Dynafile 14000 User manual

WMV-Dresden
WMV-Dresden
WMV-Dresden
WMV-Dresden
WMV-Dresden
WMV-Dresden
WMV-Dresden
WMV-Dresden
WMV-Dresden
WMV-Dresden
WMV-Dresden
WMV-Dresden
WMV-Dresden
WMV-Dresden
WMV-Dresden
WMV-Dresden
WMV-Dresden
WMV-Dresden
WMV-Dresden
WMV-Dresden
WMV-Dresden
WMV-Dresden
WMV-Dresden
WMV-Dresden
WMV-Dresden
WMV-Dresden
WMV-Dresden
WMV-Dresden
WMV-Dresden
WMV-Dresden
WMV-Dresden
WMV-Dresden
SAFETY INSTRUCTIONS
Carefully Read all instructions before operating or servicing any Dynabrade®Abrasive Power Tool.
Products offered by Dynabrade are not to be modified, converted or otherwise altered from the original design without expressed written consent from Dynabrade, Inc.
Tool Intent: Dynafile®abrasive belt machine replaces tedious hand filing and sanding and can be used for grinding, deburring, blending and polishing. Tool can be used on most
materials including metal, plastic, fiberglass, composites, rubber, glass and stone.
Do not use tool for anything other than its intended applications.
This power tool is not intended for use in potentially explosive atmospheres and is not insulated against contact with electrical power.
Training: Proper care, maintenance, and storage of your tool will maximize its performance.
• Employer's Responsibility – Provide Dynafile®operators with safety instructions and training for safe use of tools and accessories.
Accessory Selection:
• Abrasive/accessory RPM (speed) rating MUST be approved for AT LEAST the tool RPM rating.
• Before mounting an accessory, visually inspect for defects. Do not use defective accessories.
• Mount only recommended accessories. See manual and Dynabrade catalog.
• Follow tool specifications before choosing size and type of accessory.
• Only use recommended fittings and air line sizes. (See tool Machine Specifications table.)
OPERATING INSTRUCTIONS
Warning: Always wear eye protection. Operator of tool is responsible for following: accepted eye, face, respiratory, hearing and body protection.
Caution: Hand, wrist and arm injury may result from repetitive work, motion and overexposure to vibration.
• Only use recommended fittings and air line sizes. Air supply hoses and air hose assemblies must have a minimum working pressure rating of 150 PSIG
(10 Bars, g) or 150 percent of the maximum pressure produced in the system, whichever is higher. (See tool Machine Specifications table.)
(continued on next page)
PD05•13R
November, 2016
Supersedes PD05•13
Dynafile
®
Air Tool Manual – Safety, Operation and Maintenance
Models:
14000 – 20,000 RPM
14010 – Versatility Kit
SAFETY LEGEND
WARNING
WARNING
Read and understand tool manual before
work starts to reduce risk of injury to
operator, visitors, and tool.
WARNING
Eye protection must be worn at all times,
eye protection to conform to ANSI Z87.1.
WARNING
Respiratory protection to be used when exposed to
contaminants that exceed the applicable threshold
limit values required by law.
WARNING
Practice safety requirements. Work alert,
have proper attire, and do not operate tools under
the influence of alcohol or drugs.
WARNING
Ear protection to be worn when exposure to sound,
exceeds the limits of applicable Federal, State or
local statues, ordinances and/or regulations.
WARNING
Air line hazard, pressurized supply lines and flexible
hoses can cause serious injury. Do not use damaged,
frayed or deteriorated air hoses and fittings.
Read and understand this tool manual before operating your air tool. Follow all safety rules for the protection of operating personnel
as well as adjacent areas. Always operate, inspect and maintain this tool in accordance with the American National Safety Institute
(ANSI) Safety Code for Portable Air Tools – B186.1. For additional safety information, refer to Safety Requirements for the Use, Care
and Protection of Abrasive Wheels – ANSI B7.1, Code of Federal Regulation – CFR 29 Part 1910, European Committee for Standards
(EN) Hand Held Non-Electric Power Tools – Safety Requirements and applicable State and Local Regulations.
SAVE THIS DOCUMENT, EDUCATE ALL PERSONNEL
For Serial No. 4A1000 and Higher
WMV-Dresden, Ersatzteilservice für Elektrowerkzeuge, Motor- und Gartengeräte
WMV-Dresden, Ersatzteilservice für Elektrowerkzeuge, Motor- und Gartengeräte
WMV-Dresden, Ersatzteilservice für Elektrowerkzeuge, Motor- und Gartengeräte

WMV-Dresden
WMV-Dresden
WMV-Dresden
WMV-Dresden
WMV-Dresden
WMV-Dresden
WMV-Dresden
WMV-Dresden
WMV-Dresden
WMV-Dresden
WMV-Dresden
WMV-Dresden
WMV-Dresden
WMV-Dresden
WMV-Dresden
WMV-Dresden
WMV-Dresden
WMV-Dresden
WMV-Dresden
WMV-Dresden
WMV-Dresden
WMV-Dresden
WMV-Dresden
WMV-Dresden
WMV-Dresden
WMV-Dresden
WMV-Dresden
WMV-Dresden
WMV-Dresden
WMV-Dresden
WMV-Dresden
WMV-Dresden
Contact Arm Assembly/Disassembly Instructions
Abrasive Belt Exchange Instructions
11275 CONTACT WHEEL SHAFT
REMOVAL TOOL
11271 WHEEL POSITION BLOCK 11271 WHEEL POSITION BLOCK
11276 BEARING REMOVAL TOOL
FOR 1/4" ID CONTACT WHEEL
11277 BEARING REMOVAL TOOL FOR
3/8" ID CONTACT WHEEL
11274 CONTACT WHEEL BEARING
MOUNT TOOL
11279 CONTACT WHEEL SHAFT
ADHESIVE CONTACT WHEEL SHAFT
SLIP FIT
PRESS
FIT HERE
BEARING
PRESS FIT
SLIP FIT CONTACT WHEEL CONTACT WHEEL
REMOVE OLD BEARING FROM WHEEL
PRESS BEARING INTO EACH SIDE OF WHEEL
INSTALL NEW SHAFT
REMOVE CONTACT ARM FROM MACHINE.
PRESS CONTACT WHEEL SHAFT OUT OF CONTACT ARM.
MOISTEN TIP OF PIPE CLEANER WITH CONTACT WHEEL
SHAFT ADHESIVE AND APPLY TO ID OF BEARINGS BEFORE
INSTALLING PROPER SHAFT.
DO NOT GET ADHESIVE ON FACE OF BEARING.
INSERT INTO
BORE OF BEARING
PIPE CLEANER
11271 WHEEL POSITION BLOCK
5
4
123
2
OPERATING INSTRUCTIONS (continued)
• Keep hand and clothing away from working end of the air tool.
• Be sure that any loose clothing, hair and all jewelry is properly restrained.
• Secure inlet bushing on air tool with a wrench before attempting to install the air fitting to avoid damaging housing assembly.
• Check tool RPM (speed) with tachometer with air pressure set at 90 PSIG while the tool is running. If tool is operating at a higher speed than the RPM marked on the tool
housing, or operating improperly, the tool must be serviced and corrected before use.
Caution: Tool RPM must never exceed abrasive/accessory RPM rating. Check accessory manufacturer for details on maximum operating speed or special
mounting instructions.
• Disconnect air hose from tool when changing belts and contact arms.
• Connect air tool to power source. Be careful NOT to depress throttle lever in the process. Do not expose air tool to inlet pressure above 90 PSIG or (6.2 Bars).
Caution: After installing the accessory, before testing or use and/or after assembling tool, the Dynafile®must be started at a reduced speed to check for good balance.
Gradually increase tool speed. DO NOT USE if tool vibration is excessive. Correct cause, and retest to insure safe operation.
• Make sure that work area is uncluttered, and visitors are at a safe range from the tools and debris.
• Use a vise or clamping device to hold work piece firmly in place.
• Do not apply excessive force on tool or apply “rough” treatment to it.
• Always work with a firm footing, good posture and proper lighting.
• Make sure that work area is uncluttered, and visitors are at a safe range from the tools and debris. Potentially explosive atmospheres can be caused by dust and fumes
resulting from sanding or grinding. Always use dust extraction or suppression systems which are suitable for the material being processed.
Report to your supervisor any condition of the tool, accessories, or operation you consider unsafe.
12
45
3
With your thumb, pull and slide
guard open in a clockwise direction.
Form a loop in belt keeping the belt splice
between fingers as shown in photo above.
Slip lower loop of belt under the drive wheel.
Depress idler arm lever and pull belt
toward the contact wheel.
Slip belt over contact wheel. Release
idler arm lever. Operate on the contact
wheel or on the return side of the belt.
Completely close the guard.
WMV-Dresden, Ersatzteilservice für Elektrowerkzeuge, Motor- und Gartengeräte
WMV-Dresden, Ersatzteilservice für Elektrowerkzeuge, Motor- und Gartengeräte
WMV-Dresden, Ersatzteilservice für Elektrowerkzeuge, Motor- und Gartengeräte

WMV-Dresden
WMV-Dresden
WMV-Dresden
WMV-Dresden
WMV-Dresden
WMV-Dresden
WMV-Dresden
WMV-Dresden
WMV-Dresden
WMV-Dresden
WMV-Dresden
WMV-Dresden
WMV-Dresden
WMV-Dresden
WMV-Dresden
WMV-Dresden
WMV-Dresden
WMV-Dresden
WMV-Dresden
WMV-Dresden
WMV-Dresden
WMV-Dresden
WMV-Dresden
WMV-Dresden
WMV-Dresden
WMV-Dresden
WMV-Dresden
WMV-Dresden
WMV-Dresden
WMV-Dresden
WMV-Dresden
WMV-Dresden
Maintenance Instructions
Important: A Preventative Maintenance Program is recommended whenever portable power tools are used.
•
Use only genuine Dynabrade replacement parts to insure quality. To order replacement parts, specify Model #, Serial # and RPM
of your air tool.
•
It is strongly recommended that all Dynabrade rotary vane air tools be used with a Filter-Regulator-Lubricator to minimize the possibility
of misuse due to unclean air, wet air or insufficient lubrication. Dynabrade recommends the following: 11405 Air Filter-Regulator-
Lubricator (FRL) – Provides for air pressure regulation, two stage filtration of water and contaminants.
Operates 40 SCFM/1,133 LPM @ 100 PSIG with 3/8" NPT female ports.
•
Dynabrade recommends one drop of air lube per minute for every 10 SCFM (example: if the tool specification states 40 SCFM, set the
drip rate on the filter-lubricator to 4 drops per minute). Dynabrade Air Lube (P/N 95842: 1 pt 473 ml) is recommended.
Routine Preventative Maintenance: Check free speed of Dynafile®using a tachometer.
•
Mineral spirits are recommended when cleaning the tool and parts. Do not clean tool or parts with any solvents or oils containing acids,
esters, ketones, chlorinated hydrocarbons or nitro carbons.
•
DO NOT clean or maintain tools with chemicals that have a low flash point (example: WD-40®).
•
A Motor Tune-Up Kit (P/N 95600) is available which includes high wear and medium wear motor parts.
•
Air tool labels must be kept legible at all times, if not, reorder label(s) and replace. User is responsible for maintaining specification
information i.e.: Model #, S/N, and RPM. (See Assembly Breakdown)
•
Blow air supply hose out prior to initial use.
•
Visually inspect air hoses and fittings for frays, visible damage and signs of deterioration. Replace damaged or worn components.
•
Refer to Dynabrade's Warning/Safety Operating Instructions Tag (Reorder No. 95903) for safety information.
After maintenance is performed on tool, add a few drops of Dynabrade Air Lube (P/N 95842) to the air line and start the tool a few times to
lubricate air motor. Check for excessive tool vibration.
Handling and Storage:
•
Use of tool rests, hangers and/or balancers is recommended.
•
Protect tool inlet from debris (see Notice below).
•
DO NOT carry tool by air hose.
•
Protect abrasive accessories from exposure to water, solvents, high humidity, freezing temperature and extreme temperature changes.
•
Store accessories in protective racks or compartments to prevent damage.
Notice
All Dynabrade motors use the highest quality parts and metals available and are machined to exacting tolerances. The failure of quality
pneumatic motors can most often be traced to an unclean air supply or the lack of lubrication. Air pressure easily forces dirt or water contained
in the air supply into motor bearings causing early failure. It often scores the cylinder walls and the rotor blades resulting in limited efficiency
and power. Our warranty obligation is contingent upon proper use of our tools and cannot apply to equipment which has been subjected to
misuse such as unclean air, wet air or a lack of lubrication during the use of this tool.
Machine Specifications
3
Model Motor Motor Sound Abrasive Belt Size Maximum Air Flow Max. SFPM Weight Length Height
Number HP (W) RPM Level Inch (mm) CFM/SCFM (LPM) (SMPM) Pound (kg) Inch (mm) Inch (mm)
All Models .5 (373) 20,000 77 dB(A) 1/8-1/2 (3-13) W x 24 (610) L 4/31 (878) 5,800 (1,762) 3.1 (1.4) 14.6 (371) 4.6 (116)
Additional Specifications: Air Inlet Thread 1/4" NPT • Hose I.D. Size 3/8" or 10mm • Air Pressure 90 PSIG (6.2 Bars)
LIFETIME WARRANTY
To validate Dynabrade Lifetime Warranty, you must register each tool at: www.dynabrade.com. Registration of each tool
at website is required. Dynabrade will not honor Lifetime Warranty on unregistered tools. Please view the entire Lifetime
Warranty Policy at : www.dynabrade.com.
American National Standards Institute (ANSI)
25 West 43 Rd St., 14th Floor • New York, NY 10036 • Tel: 1 (202) 293-8020
Compressed Air & Gas Institute
1300 Sumner Ave.• Cleveland, OH 44115-2851
Tel: 1 (216) 241-7333 • Fax.(216) 241-0105
European Committee for Standardization
Rue de Stassart 36 • B - 1050 Brussels, Belgium
International Organization of Standards
Case postale 56 • CH-1211 Geneva20
Tel: + 41 22 749 01 11 • Fax: + 41 22 749 09 47
Government Printing Office
Superintendent of Documents • Attn: New Orders
P.O.Box 371954 • Pittsburgh, PA 15250-7954
Tel: 1 (202) 512-1803
REFERENCE CONTACT INFORMATION
WMV-Dresden, Ersatzteilservice für Elektrowerkzeuge, Motor- und Gartengeräte
WMV-Dresden, Ersatzteilservice für Elektrowerkzeuge, Motor- und Gartengeräte
WMV-Dresden, Ersatzteilservice für Elektrowerkzeuge, Motor- und Gartengeräte

WMV-Dresden
WMV-Dresden
WMV-Dresden
WMV-Dresden
WMV-Dresden
WMV-Dresden
WMV-Dresden
WMV-Dresden
WMV-Dresden
WMV-Dresden
WMV-Dresden
WMV-Dresden
WMV-Dresden
WMV-Dresden
WMV-Dresden
WMV-Dresden
WMV-Dresden
WMV-Dresden
WMV-Dresden
WMV-Dresden
WMV-Dresden
WMV-Dresden
WMV-Dresden
WMV-Dresden
WMV-Dresden
WMV-Dresden
WMV-Dresden
WMV-Dresden
WMV-Dresden
WMV-Dresden
WMV-Dresden
WMV-Dresden
Dynafile
®
Complete Assembly Breakdown
4
01197 Air Motor with 01111 Drive Wheel
Note: 50971 Lock Ring Wrench is available for removal/installation of 04087 Lock Ring.
See inside for Important Operating, Maintenance and Safety Instructions before operating tool.
1
Contact Arm Assembly
(See pages 8-11)
2 95218 Knob Assembly
3* 11420 Idler Arm Assy., Includes:
95070 Threaded Insert
11040 Spring
4 11359 Tension Spring
5* 95162 Screw (2)
6* 11011 Idler Wheel Assy. (2) Includes:
95162 Screw
11013 Bearing
11006 Idler Wheel
7 95216 Pivot Pin
8 11418 Housing
9 95311 Screw
10 40029 Motor Lock
11 11419 Cover
12 11424 Wave Spring
13 01197 Air Motor
14 01111 Drive Wheel
15 10295 Screen
16 04087 Lock Ring
17 04078 Felt Silencer
18 04084 Air Control Ring
19 04081 Rotor Nut
20 01007 Bearing
21 01121 Shim Pack (3/pkg.)
22 01008 Bearing Plate
23 50767 Pin (2)
24 01010 Rotor Spacer
25 01013 Cylinder
26 01011 Blade (4) (4/pkg.)
27 01120 Rotor
28 01244 Bearing Plate
29 01015 Bearing
30 95558 Retaining Ring
31 30420 Housing
32 01477 Valve Stem
33 95730 O-Ring
34 01024 O-Ring
35 01247 Speed Regulator Assembly
36 01953 Safety-Lock Throttle Lever
37 01017 Pin
38 01464 Seal
39 01472 Tip Valve
40 01438 Spring
41 53190 Block Plate
42 96065 O-Ring
43 01494 Inlet Adapter
Index Key
No. Part # Description
T
G
A
O
Adhesive: A3= Loctite #242
A8= Loctite #567
Torque: N•m x 8.85 = In. - lbs.
KEY
14
10
12
11
8
6*
13*
13
15 17 18
19
20 22 25 27
26
23
28 29
30
36
37 40 41 42 43
393823 32
33
34 35
21 24
23 N•m
T
17 N•m
T
23 N•m
TO1
O1
A8
G2
G2
A3
A8
Oil: O1= Air Lube
Grease: G2= Loctite #771
31
16
9
2
*Asterisk indicates parts that are
included in 11421 Idler Arm Assembly.
Note: All Boxed index numbers represent
11431 Housing Assembly.
5*
4
7
WMV-Dresden, Ersatzteilservice für Elektrowerkzeuge, Motor- und Gartengeräte
WMV-Dresden, Ersatzteilservice für Elektrowerkzeuge, Motor- und Gartengeräte
WMV-Dresden, Ersatzteilservice für Elektrowerkzeuge, Motor- und Gartengeräte

WMV-Dresden
WMV-Dresden
WMV-Dresden
WMV-Dresden
WMV-Dresden
WMV-Dresden
WMV-Dresden
WMV-Dresden
WMV-Dresden
WMV-Dresden
WMV-Dresden
WMV-Dresden
WMV-Dresden
WMV-Dresden
WMV-Dresden
WMV-Dresden
WMV-Dresden
WMV-Dresden
WMV-Dresden
WMV-Dresden
WMV-Dresden
WMV-Dresden
WMV-Dresden
WMV-Dresden
WMV-Dresden
WMV-Dresden
WMV-Dresden
WMV-Dresden
WMV-Dresden
WMV-Dresden
WMV-Dresden
WMV-Dresden
Disassembly/Assembly Instructions – Dynafile
®
Important: The manufacture warranty is void if the tool is disassembled before the warranty expires, by anyone other than a Dynabrade approved
repair technician. Notice: A complete Motor Tune-Up Kit, part number 95600 is available. Also, the special repair tooling referred to in these
instructions can be ordered through your Dynabrade Distributor. Please refer to this tool manual for correct part number identification.
Motor Disassembly:
1. Shut off the air supply, and depress throttle lever to dissipate the remaining air. Carefully disconnect the tool from the air supply hose.
2. Remove the abrasive belt and contact arm assembly.
3. Carefully hold the 11418 Housing in a vise with aluminum or bronze jaws.
4. Use a 9/64" hex key to loosen the 95311 Screw. Remove the 01197 Air Motor along with the 11424 Wave Spring and the 11419 Cover.
5. Hold the 01243 Housing of the 01197 Air Motor in a vise with aluminum or bronze jaws so that the drive wheel is pointing up. Fasten the flats near
the inlet area of the housing.
6. Insert a 3/16" hex key through the 01111 Drive Wheel and into the end of the 01120 Rotor to hold it stationary. Grasp the drive wheel and turn it
counterclockwise to remove. Remove the 10295 Screen.
7. Use the 50971 Lock Ring Wrench to remove the 04087 Lock Ring, turning it counterclockwise. Remove the 04084 Air Control Ring and the 04078 Felt
Silencer. Pull the motor out of the housing.
8. Fasten the 96346 2" Bearing Separator around the portion of the 01013 Cylinder closest to the 01244 Bearing Plate. Place the separator and the motor
on the table of the 96232 #2 Arbor Press so that the threaded end of the rotor is pointing down.
9. Use a 3/16" or 5mm diameter flat end drive punch as a press tool and push the rotor out of the 01015 Bearing.
10. Remove the 01011 Blades (4).
11. The 01015 Bearing can be removed from the 01244 Bearing Plate with the 96211 Bearing Removal Tool and the arbor press.
12. Hold the blade portion of the 01120 Rotor in a vise with aluminum or bronze jaws and remove the 04081 Rotor Nut with an adjustable wrench,
turning it counterclockwise.
13. The 01007 Bearing, 01008 Bearing Plate, 01121 Shims, and 01010 Spacer can now be removed from the 01120 Rotor.
Motor Disassembly Complete.
Valve Disassembly:
1. Hold the 01243 Housing in a vise with aluminum or bronze jaws. Fasten the flats near the inlet area of the housing so that the air inlet is pointing up.
2. Hold the 01494 Inlet Adapter stationary with a wrench and remove the air fitting with another wrench.
Important: The 01494 Inlet Adapter must be held stationary to prevent damage to the 01243 Housing.
3. Remove 01494 Inlet Adapter to access the 01438 Spring, 01472 Tip Valve, and 01464 Seal.
4. Use a 2.5mm drive punch to remove the 01017 Pin and the throttle lever.
5. The 01477 Valve Stem can be pulled out of the 01247 Speed Regulator Assembly.
6. Use retaining ring pliers to remove the 95558 Retaining Ring and then push the 01247 Speed Regulator Assembly out of the 01243 Housing.
Valve Body Disassembly Complete.
Idler Arm Disassembly:
1. Use a 1/8" or 3mm diameter drive punch to remove the 95216 Pivot Pin along with the 11420 Idler Arm Assembly and 11359 Tension Spring.
2. Use a 3/32" hex key to remove the 11011 Idler Wheel Assembly (2).
Idler Arm Disassembly Complete.
Important: Clean and inspect all parts before assembling.
Valve Assembly:
1. Hold the 01243 Housing in a vise with aluminum or bronze jaws. Fasten the flats of the housing near the inlet area so that the air inlet is pointing up.
2. Install the 01247 Speed Regulator Assembly (o-rings included) into the 01243 Housing and hold it in place with the 95558 Retaining Ring.
3. Insert the 01477 Valve Stem so that the end with the hole fits into the 01247 Speed Regulator Assembly.
4. Install the 01464 Seal into the air inlet so that it is laying flat.
5. Use a needle nose pliers to grasp the white nylon portion of the 01472 Tip Valve and insert the metal pin of the tip valve into the hole in the
01477 Valve Stem.
6. Install the 01438 Spring so that the smaller end of the spring fits against the center of the tip valve.
7. Install the 96065 O-Ring onto the 53190 Block Plate and install the block plate along with the o-ring so that the flat side of the block plate is positioned
against the 01243 Housing.
8. Apply a small amount of the #567 Loctite®(or equivalent) to the threads of the 01494 Inlet Adapter and install the adapter into the housing.
Torque to 23 N•m/200 lbs. in.
9. Install the throttle lever and fasten it with the 12132 Pin.
Valve Assembly Complete.
Idler Arm Assembly:
1. Apply a small amount of the Loctite®#242 (or equivalent) to the 95162 Screw (2) and install the 11011 Idler Wheel Assembly (2).
2. Install the 11359 Tension Spring into the 11418 Housing. Install the 11420 Idler Arm Assembly and fasten it into housing with the 95216 Pivot Pin.
Idler Arm Assembly Complete.
Motor Assembly:
1. Install the 01010 Spacer onto the rotor.
2. Select .003" (0.80mm) thickness in shims from the 01121 Shim Pack and place these into the 01008 Bearing Plate.
3. Install the 01007 Bearing into the bearing plate.
WMV-Dresden, Ersatzteilservice für Elektrowerkzeuge, Motor- und Gartengeräte
WMV-Dresden, Ersatzteilservice für Elektrowerkzeuge, Motor- und Gartengeräte
WMV-Dresden, Ersatzteilservice für Elektrowerkzeuge, Motor- und Gartengeräte

WMV-Dresden
WMV-Dresden
WMV-Dresden
WMV-Dresden
WMV-Dresden
WMV-Dresden
WMV-Dresden
WMV-Dresden
WMV-Dresden
WMV-Dresden
WMV-Dresden
WMV-Dresden
WMV-Dresden
WMV-Dresden
WMV-Dresden
WMV-Dresden
WMV-Dresden
WMV-Dresden
WMV-Dresden
WMV-Dresden
WMV-Dresden
WMV-Dresden
WMV-Dresden
WMV-Dresden
WMV-Dresden
WMV-Dresden
WMV-Dresden
WMV-Dresden
WMV-Dresden
WMV-Dresden
WMV-Dresden
WMV-Dresden
Disassembly/Assembly Instructions – Dynafile
®
4. Slip the bearing and plate onto the rotor.
5. Install the 04081 Rotor Nut and check the clearance between the rotor and plate with a .001" (0.03mm) feeler gauge. The clearance should be
.001"-.0015" (0.03-0.04mm). If the rotor/plate clearance needs adjustment, repeat steps 2-5 and remove or add shims as required to establish
the correct clearance.
6. Apply the 95842 Dynabrade®Air Lube, 10W/NR (or equivalent) to the 01011 Blades (4) and install these into the rotor.
7. Install the 01013 Cylinder over the rotor so that the air inlet opening of the cylinder will align with the air inlet opening of the 01244 Bearing Plate.
8. Use the 96241 Bearing Press Tool (position the raised outside diameter against the outside diameter of the bearing) and 96232 Arbor Press to install
the 01015 Bearing into the bearing plate.
9. Use the 96241 Bearing Press Tool (position the raised inside diameter against the inside diameter of the bearing) and the 96232 Arbor Press to install
the bearing and plate onto the rear bearing journal of the rotor.
Important: Press the bearing and plate down onto the rotor until the 01244 Bearing Plate just touches the 01013 Cylinder. This fit will establish a
preload on the motor bearings producing a “snug fit” between the bearing plates and the cylinder. If the fit is too tight it will cause the bearings to wear
prematurely, too loose and the desired preload will not be achieved. If an adjustment is required, remove the bearing and plate. Repeat steps 7-9.
10. Orient the motor assembly so that the air inlet passage in the housing aligns with the air passage in the 01244 Bearing Plate and install
the motor assembly.
11. Wrap the 04078 Felt Silencer around the 04084 Air Control Ring and install these into the 04087 Lock Ring.
12. Apply a small amount of the Loctite®#567 (or equivalent) on the threads of the 04087 Lock Ring. Install the lock ring along with the air control ring
and felt silencer onto the 01243 Housing. Torque to 23 N·m/200 lbs. in.
13. Install the 11424 Wave Spring and the 11419 Cover onto the 01197 Air Motor.
14. Insert the 01197 Air Motor into the 11418 Housing. Use a 9/64" hex key to fasten the motor in place with the 40029 Cam Lock and the 95311 Screw.
15. Install a contact arm assembly and an abrasive belt onto the idler arm assembly.
16. Adjust and Track the abrasive belt by hand. Close the 11419 Cover.
17. Connect the Dynafile to the air supply hose. Open the air supply valve to charge the hose with air.
18. Run the tool and check for proper operation.
Motor Assembly Complete. Tool Assembly Complete. Please allow 30 minutes for adhesives to cure before operating tool.
Important: Motor should now be tested for proper operation at 90 PSIG. If motor does not operate properly or operates at a higher RPM than marked on
the tool, the tool should be serviced to correct the cause before use. Before operating, place 2-3 drops of Dynabrade Air Lube (P/N 95842) directly into air
inlet with throttle lever depressed. Operate tool for 30 seconds to determine if tool is operating properly and to allow lubricating oils to properly penetrate motor.
Loctite®is a registered trademark of Loctite Corp.
Abrasive Belt Change and Removal:
To Remove Belt:
1. Open 11419 Cover.
2. Depress idler arm lever and pull belt away from the contact wheel.
3. Slip belt off drive wheel.
To Replace Belt:
1. Create a loop with belt by pinching together the sides of belt in the middle.
2. Slip one loop under the 01111 Drive Wheel and around the idler arm.
3. Depress idler arm lever and pull belt toward the contact wheel.
4. Slip belt over contact wheel.
5. Connect tool to power source.
6. Adjust belt tracking using 95218 Knob.
14000 Dynafile
®
Safety Throttle
Lever (Optional)
Idler Arm
Assembly
Speed
Control
Screw
Air Motor Drive
Wheel
Wave
Spring
Idler Wheel
Assembly
Tracking
Adjustment Knob
Idler Arm Contact
Arm Assembly
(See pages 8-11)
6
01089 11421 11011 11420 11218
9521801111
Housing
11418114240119701247
WMV-Dresden, Ersatzteilservice für Elektrowerkzeuge, Motor- und Gartengeräte
WMV-Dresden, Ersatzteilservice für Elektrowerkzeuge, Motor- und Gartengeräte
WMV-Dresden, Ersatzteilservice für Elektrowerkzeuge, Motor- und Gartengeräte

WMV-Dresden
WMV-Dresden
WMV-Dresden
WMV-Dresden
WMV-Dresden
WMV-Dresden
WMV-Dresden
WMV-Dresden
WMV-Dresden
WMV-Dresden
WMV-Dresden
WMV-Dresden
WMV-Dresden
WMV-Dresden
WMV-Dresden
WMV-Dresden
WMV-Dresden
WMV-Dresden
WMV-Dresden
WMV-Dresden
WMV-Dresden
WMV-Dresden
WMV-Dresden
WMV-Dresden
WMV-Dresden
WMV-Dresden
WMV-Dresden
WMV-Dresden
WMV-Dresden
WMV-Dresden
WMV-Dresden
WMV-Dresden
This service chart is published as a guide to expectant life of component parts. The replacement levels are based on average tool
usage over one year. Dynabrade Inc. considers one year usage to be 1,000 hours.
Parts Common to all Models:
Preventative Maintenance Schedule
For All Dynafile
®
Models
LEGEND
T Included in Tune-Up Kit
X Type of wear, no other
comments apply.
L Easily lost. Care during
assembly/disassembly.
D Easily damaged during
assembly/disassembly.
R Replace each time tool is
disassembled.
Note: Please refer to pages 8-10 of tool manual for specific part number.
Index Part Description Number High Wear Medium Wear Low Wear Non-Wear
# Number Required 100% 70% 30% 10%
1 See Note Contact Arm Assembly 1
2 95218 Knob Assembly 1 X
3 11420 Idler Arm 1 X
(Incl. 95070 Threaded Insert)
4 11359 Tension Spring 1 X
5 95162 Screw 2 X
6 11011 Idler Wheel Assembly 2 X
(Incl. 95162 Screw, 11013
Bearing & 11006 Idler Wheel)
7 95216 Pivot Pin 1 X
8 11418 Housing 1 X
9 95311 Screw 1 X
10 40029 Motor Lock 1
L
11 11419 Cover 1 X
12 11424 Wave Spring 1 X
13 01197 Air Motor 1 X
14 01111 Drive Wheel 1 X
15 10295 Screen 1
T
16 04087 Lock Ring 1 X
17 04078 Felt Silencer 2 T
18 04084 Air Control Ring 1 X
19 04081 Rotor Nut 1 X
20 01007 Bearing 1 T
21 01121 Shim Pack (3/pkg.) 1 T
22 01008 Bearing Plate 1 X
23 50767 Pin 1 X
24 01010 Rotor Spacer 1 T
25 01013 Cylinder 1 X
26 01011 Blade (4/pkg.) 1 T
27 01120 Rotor 2 X
28 01244 Bearing Plate 1 X
29 01015
Bearing
1 T
30 95558 Retaining Ring 1 T
31 30420 Housing 1 X
32 01477 Valve Stem 2 T
33 95730 O-Ring 1 X
34 01024 O-Ring 1 X
35 01247 Speed Regulator Assembly 1 T
36 01953 Safety-Lock Throttle Lever 1 X
37 01017 Pin 1 T
38 01464 Seal 1 T
39 01472 Tip Valve 1 T
40 01438 Spring 1
T
41 53190 Block Plate 1 X
42 96065 O-Ring 1
T
43 01494 Inlet Adapter 1
X
7
95600 – Motor Tune-Up Kit
WMV-Dresden, Ersatzteilservice für Elektrowerkzeuge, Motor- und Gartengeräte
WMV-Dresden, Ersatzteilservice für Elektrowerkzeuge, Motor- und Gartengeräte
WMV-Dresden, Ersatzteilservice für Elektrowerkzeuge, Motor- und Gartengeräte

WMV-Dresden
WMV-Dresden
WMV-Dresden
WMV-Dresden
WMV-Dresden
WMV-Dresden
WMV-Dresden
WMV-Dresden
WMV-Dresden
WMV-Dresden
WMV-Dresden
WMV-Dresden
WMV-Dresden
WMV-Dresden
WMV-Dresden
WMV-Dresden
WMV-Dresden
WMV-Dresden
WMV-Dresden
WMV-Dresden
WMV-Dresden
WMV-Dresden
WMV-Dresden
WMV-Dresden
WMV-Dresden
WMV-Dresden
WMV-Dresden
WMV-Dresden
WMV-Dresden
WMV-Dresden
WMV-Dresden
WMV-Dresden
Part Abrasive Contact Wheel Contact Wheel Contact Wheel Bearing
Number Belt Size Description Comments Assembly Only (2) Req. Shaft
11178 1/2" x 34" 5/16" Dia. x 3/8" W Steel 9" Reach 11068 11067 11051 11054
11179 1/2" x 34" 5/8" Dia. x 3/8" W Rubber 9" Reach 11078 11077 11052 11054
11212 1/4" x 24" 5/16" Dia. x 1/8" W Steel 1/4" W Platen 11066 11065 11051 (1) 11056
11213 1/2" x 24" 5/16" Dia. x 3/8" W Steel 1/2" W Platen 11068 11067 11051 11054
11214 1/2" x 24" 7/16" Dia. x 3/8" W Rubber 1/2" W Platen 11070 11069 11051 11054
11215 1/4" x 24" 7/16" Dia. x 1/8" W Brass 1/4" W Platen 11072 11071 11052 (1) 11053
11216 1/4" x 24" 5/8" Dia. x 1/8" W Rubber 1/4" W Platen 11074 11073 11052 (1) 11053
11217 1/2" x 24" 1/2" Dia. x 3/8" W Steel 1/2" W Platen 11076 11075 11052 11054
11218 1/2" x 24" 5/8" Dia. x 3/8" W Rubber 1/2" W Platen 11078 11077 11052 11054
11219 1/4" or 1/2" x 24" 1" Dia. x 3/8" W Radiused Rubber No Platen 11080 11079 11052 11054
11228 1/2" x 24" 5/8" Dia. x 3/8" W Rubber H.D. Version of 11218 Arm 11078 11077 11052 11054
11231 1/2" x 24" 3/4" Dia. x 1/2" W Rubber 1/2" W Platen 11084 11083 11052 11055
11232 1/8" or 1/4" x 24" 1" Dia. x 3/8" W Tapered Urethane No Platen 11086 11085 11052 11054
11234 1/2" x 34" 1" Dia. x 3/8" W Radiused Rubber Double Burrer Arm 11080 (2) 11079 (2) 11052 N/A
11237 5/16" x 24" 5/16" Dia. x 1/8" W Steel Polish Turbine Blades 11066 11065 11051 (1) 11053
11238 1/2" x 24" 1/4" Dia. x 3/8" W Steel Polish Turbine Blades 11051 (3) and 11054 11051 (3) N/A 11054
11239 1/2" x 24" 5/16" Dia. x 3/8" W Steel H.D. Version of 11213 Arm 11068 11067 11051 11054
11240 1/2" x 34" 5/8" Dia. x 3/8" W Rubber 1/2" W Platen - 9" Reach 11078 11077 11052 11054
11241 1/4" x 34" 5/8" Dia. x 1/8" W Rubber 1/4" W Platen - 9" Reach 11074 11073 11052 (1) 11053
11243 1/2" x 24' 3/4" Dia x 1/2" W Rubber H.D. Version of 11231 Arm 11084 11083 11052 11055
11244 1/2" x 44" 5/8" Dia. x 3/8" W Rubber 1/2" W Platen - 14" Reach 11078 11077 11052 11054
11245 1/4" x 44" 5/8" Dia. x 1/8" W Rubber 1/4" W Platen - 14" Reach 11074 11073 11052 (1) 11053
11254 1/2" or 1/4" x 34" 4-3/4" or 2-1/8" Dia. to 1/4" or 1/2" W Grind in Deep Narrow Slots Variable Variable 11013 (1) 95162
11255 1/2" x 34" 5/8" Dia. x 3/8" W Rubber Deburr I.D. 1" to 4" 11078 11077 11052 11054
11257 1/2" Wide 5/16" Dia. x 3/8" W Steel or 5/8" Dia. x 3/8" W Rubber “Spear-Arm” - Specify length up to 32" 11068 Steel 11067 Steel 11051 Steel 11054
11078 Rubber 11077 Rubber 11052 Rubber
11258 1/2" x 24" 1/2" Dia. x 3/8" W Steel and 5/8" Dia. x 3/8" W Rubber Platen Between 2 Contact Wheels 11076 Steel 11075 Steel 11052 (4) 11054 (2)
11078 Rubber 11077 Rubber
11261 1/2" x 24" 5/8" Dia. x 3/8" W Rubber “Banana Arm” – For in-line scratch pattern. 11078 11077 11052 11054
11262 1/2" x 24" 5/8" Dia. x 3/8" W Rubber “Offset Arm” – Contact wheel is offset to prevent gouging. 11078 11077 11052 11054
11297 1/2" x 24" 5/8" Dia. x 3/8" W Rubber Contains two 11395 Guide Wheels. Prevents undercutting. 11090 11077 11052 95610
Dynafile
®
Standard Contact Arm Assemblies
11288 Dynafile Contact Arm and Idler Wheel Repair Kit
•
Contains special tools to assist in the replacement
of contact wheels and bearings.
See next page for a complete guide to contact arms. Also see page 11 for contact arm disassembly and assembly instructions.
WMV-Dresden, Ersatzteilservice für Elektrowerkzeuge, Motor- und Gartengeräte
WMV-Dresden, Ersatzteilservice für Elektrowerkzeuge, Motor- und Gartengeräte
WMV-Dresden, Ersatzteilservice für Elektrowerkzeuge, Motor- und Gartengeräte

WMV-Dresden
WMV-Dresden
WMV-Dresden
WMV-Dresden
WMV-Dresden
WMV-Dresden
WMV-Dresden
WMV-Dresden
WMV-Dresden
WMV-Dresden
WMV-Dresden
WMV-Dresden
WMV-Dresden
WMV-Dresden
WMV-Dresden
WMV-Dresden
WMV-Dresden
WMV-Dresden
WMV-Dresden
WMV-Dresden
WMV-Dresden
WMV-Dresden
WMV-Dresden
WMV-Dresden
WMV-Dresden
WMV-Dresden
WMV-Dresden
WMV-Dresden
WMV-Dresden
WMV-Dresden
WMV-Dresden
WMV-Dresden
Belt Size: 1/4" W x 24" L.
11066 Contact Wheel: 5/16" diameter x 1/8" wide, steel.
11034 Platen: 1/4" wide.
11212 File round openings as small as 7/16".
45 PSIG maximum.
Belt Size: 1/2" W x 24" L.
11068 Contact Wheel: 5/16" diameter x 3/8" wide, steel.
11027 Platen: 1/2" wide.
11213 See 11239 for heavy-duty version.
45 PSIG maximum.
Belt Size: 1/2" W x 24" L.
11070 Contact Wheel: 7/16" diameter x 3/8" wide, rubber.
11025 Platen: 1/2" wide.
11214 Work on contact wheel or Dynapad
®
.
45 PSIG maximum.
Belt Size: 1/4" W x 24" L.
11072 Contact Wheel: 7/16" diameter x 1/8" wide, brass.
11034 Platen: 1/4" wide.
11215 Enter 1/2" x 1/2" openings.
Belt Size: 1/4" W x 24" L.
11074 Contact Wheel: 5/8" diameter x 1/8" wide, rubber.
11032 Platen: 1/4" wide
.
11216 Enter 5/16" x 3/4" openings.
Belt Size: 1/2" W x 24" L.
11076 Contact Wheel: 7/16" diameter x 3/8" wide, steel.
11027 Platen: 1/2" wide.
11217 Enter channels as narrow as 9/16".
11218 Standard arm on model 14000.
See 11228 for heavy-duty version.
Dynafile
®
Standard Contact Arms
Standard Contact Arms allow for a 4" workable reach.
9
Belt Size: 1/2" W x 24" L.
11078 Contact Wheel: 5/8" diameter x 3/8" wide, rubber.
11025 Platen: 1/2" wide.
Belt Size: 1/4" or 1/2" W x 24" L.
11080 Contact Wheel: 1" diameter x 3/8" wide, radiused rubber.
No Platen
11219 No platen due to offset design.
Grind radiuses, slack polish.
Offset for slack polishing
Belt Size: 1/2" W x 24" L.
11078 Contact Wheel: 5/8" diameter x 3/8" wide, rubber.
11025 Platen: 1/2" wide.
11228 Heavy-Duty Steel Optional 11028 Steel Platen
available for grinding.
Belt Size: 1/2" W x 24" L.
11084 Contact Wheel: 3/4" diameter x 1/2" wide, rubber.
11135 Platen: 1/2" wide.
11231 See 11243 for heavy-duty version.
Belt Size: 1/8" or 1/4" W x 24" L.
11086 Contact Wheel: 1" diameter x 3/8" wide, tapered urethane.
No Platen.
11232 For 1/8" Wide Belts No platen due to offset design.
Grind corners, strap polish.
V-Tapered
Belt Size: 1/2" W x 24" L.
11068 Contact Wheel: 5/16" diameter x 3/8" wide, steel.
11027 Platen: 1/2" wide.
Belt Size: 1/2" W x 24" L.
11084 Contact Wheel: 3/4" diameter x 1/2" wide, rubber.
11135 Platen: 1/2" wide.
11243 Heavy-Duty Grind over contact wheel or Dynapad®.
11239 Heavy-Duty Steel Grind in narrow areas.
45 PSIG maximum.
Belt Size: 1/2" W x 24" L.
11078 Contact Wheel: 5/8" diameter x 3/8" wide, rubber.
11026 Platen: 1/2" wide.
11262 "Offset Arm" For flat grinding using platen at or near corners
and edges of large radius round. Contact wheel
is offset to prevent gouging.
WMV-Dresden, Ersatzteilservice für Elektrowerkzeuge, Motor- und Gartengeräte
WMV-Dresden, Ersatzteilservice für Elektrowerkzeuge, Motor- und Gartengeräte
WMV-Dresden, Ersatzteilservice für Elektrowerkzeuge, Motor- und Gartengeräte

WMV-Dresden
WMV-Dresden
WMV-Dresden
WMV-Dresden
WMV-Dresden
WMV-Dresden
WMV-Dresden
WMV-Dresden
WMV-Dresden
WMV-Dresden
WMV-Dresden
WMV-Dresden
WMV-Dresden
WMV-Dresden
WMV-Dresden
WMV-Dresden
WMV-Dresden
WMV-Dresden
WMV-Dresden
WMV-Dresden
WMV-Dresden
WMV-Dresden
WMV-Dresden
WMV-Dresden
WMV-Dresden
WMV-Dresden
WMV-Dresden
WMV-Dresden
WMV-Dresden
WMV-Dresden
WMV-Dresden
WMV-Dresden
11237 and 11238 Turbine Blade Arms 45 PSIG maximum.
11257, 11178 and 11179 Spear Arms
1-1/2"
11234 Double-Burrer Arm
•Deburrs both edges of
workpiece simultaneously.
•Contact wheels adjust for
material 1/8" to 5/8" thick.
Belt Size: 1/2" wide x 34" long.
11080 Contact Wheels: 1" diameter x 3/8" wide, rubber.
11240, 11241, 11244 and 11245 Extra-Length Arms
11254 Big Wheel Arm
•Grinds and polishes deep
slots or narrow groves.
•1/4" to 1/2" wide wheels,
2-1/8" to 4-3/4" diameter
(specify size).
Belt Size: 1/4" to 1/2" W x 34" L.
11253 Arms (specify width)
11377 Contact Wheel: 2-1/8" dia. x 1/2" wide, urethane.
11378 Contact Wheel: 2-1/8" dia. x 1/4" wide, urethane.
11254 Arms (specify width)
11375 Contact Wheel: 4-3/4" dia. x 1/2" wide, urethane.
11375 Contact Wheel: 4-3/4" dia. x 1/4" wide, urethane.
11255 Cross-Bow Arm
•I.D. polishing or deburring
with one 180° wrist turn.
•Deburr leading radius of
1" to 4" round openings.
Belt Size: 1/2" W x 34" L.
Dynafile
®
Specialized Contact Arms
Designed to solve tough production problems.
11237: 1/4" wide x 24" long belts.
11066 Contact Wheel: 5/16" dia. x 1/8" wide steel wheel.
11238: 1/2" wide x 24" long belts.
Contact Wheel: 1/4" dia. x 3/8" wide steel wheel.
Strap Polish Area
9" Workable Reach:
11240 Arm: 11241 Arm:
Belt Size: 1/2" W x 34" L belts. Belt Size: 1/4" W x 34" L belts.
11078 Contact Wheel: 11074 Contact Wheel:
5/8" dia. x 3/8" wide, rubber. 5/8" dia. x 1/8" wide, rubber.
14" Workable Reach:
11244 Arm: 11245 Arm:
Belt Size: 1/2" W x 44" L belts. Belt Size: 1/4" W x 44" L belts.
11078 Contact Wheel: 11074 Contact Wheel:
5/8" dia. x 3/8" wide, rubber. 5/8" dia. x 1/8" wide, rubber.
10
11257: Custom-made. Specify usable length up to 32".
Specify 11068 - 5/16" diameter steel or 11078 - 5/8" diameter rubber
contact wheel.
11178: Has 9" reach with 11068 - 5/16" diameter steel contact wheel.
Belt Size: 1/2" W x 34" L (45 PSIG Max.).
11179: Has 9" reach with 11078 - 5/8" diameter rubber contact wheel.
Belt Size: 1/2" W x 34" L.
Belt Size: 1/2" W x 24" L.
11078 Contact Wheel: 5/8" diameter x 3/8" wide, rubber.
Platen: 1/2" W x 7/8" L.
11258 Stroke Sander Arm Blend stainless steel.
Belt Size: 1/2" W x 24" L, 60 to 80 grit.
11090 Contact Wheel: 5/8" diameter x 3/8" wide rubber.
•Guide wheels
prevent undercutting.
•Removes raised material
within .020" or less.
•Use 60 to 80 grit abrasive
belts with this arm.
11297 Guide-Cut Arm
WMV-Dresden, Ersatzteilservice für Elektrowerkzeuge, Motor- und Gartengeräte
WMV-Dresden, Ersatzteilservice für Elektrowerkzeuge, Motor- und Gartengeräte
WMV-Dresden, Ersatzteilservice für Elektrowerkzeuge, Motor- und Gartengeräte

WMV-Dresden
WMV-Dresden
WMV-Dresden
WMV-Dresden
WMV-Dresden
WMV-Dresden
WMV-Dresden
WMV-Dresden
WMV-Dresden
WMV-Dresden
WMV-Dresden
WMV-Dresden
WMV-Dresden
WMV-Dresden
WMV-Dresden
WMV-Dresden
WMV-Dresden
WMV-Dresden
WMV-Dresden
WMV-Dresden
WMV-Dresden
WMV-Dresden
WMV-Dresden
WMV-Dresden
WMV-Dresden
WMV-Dresden
WMV-Dresden
WMV-Dresden
WMV-Dresden
WMV-Dresden
WMV-Dresden
WMV-Dresden
11
MAINTENANCE INSTRUCTIONS
Important: To keep tool safe, a Preventative Maintenance Program is
recommended. The program should include inspection of the tool and all
related accessories and consumables, including air lines, pressure regulators,
filters, oilers, etc. (refer to CAGI B186.1 for additional maintenance
information). If accessory or tool breakage occurs, investigate failure to
determine the cause and correct before issuing tool for work. Use the following
schedule as a starting point in developing a Preventative Maintenance
Program. If tool does not operate properly (RPM, vibration, start/stop) after
these scheduled checks or at any time, the tool must be repaired and
corrected before returning tool to use.
INSTALLATION
• To ensure long life and dependable service, use a Closed Loop Air System
and Filter-Regulator-Lubricator (FRL) as diagramed below.
• Each tool should have its own dedicated hose connected to an air supply
FRL. Quick disconnects should be installed at the FRL in an effort to reduce
contamination into the tool. Securely affix all fittings and hose assemblies.
• It is strongly recommended that all Dynabrade rotary vane air tools be used
with a Filter-Regulator-Lubricator to minimize the possibility of misuse due
to unclean air, wet air or insufficient lubrication. Dynabrade recommends
the following: 10690 Air Line Filter-Regulator-Lubricator — Provides
accurate air pressure regulation, two-stage filtration of water contaminants
and micro-mist lubrication of pneumatic components.
• Dynabrade recommends 1 drop of air lube per minute for each 20 SCFM
(example: if the tool specification states 40 SCFM, set the drip rate
on the filter-lubricator to 2 drops per minute). 95842 Dynabrade Air Lube
is recommended.
MAINTENANCE SCHEDULE
Maintenance schedules depend on the type and style of tool. Refer to page
3 to reference symbols associated with specific maintenance items/areas.
Match maintenance schedules accordingly. See page 4 for any additional
maintenance information.
Note: Turbine style air motors do not require oil.
Daily (every 8 hours):
• Inspect tool and accessories for damage or broken parts. Replace items
as necessary to ensure proper operation and safety.
Lubricate motor as recommended. Use 95842 Dynabrade Air Lube
(10W/NR). Apply 1 drop/minute of air lube per 20 SCFM.
• Check air line pressure with a gage. (MAX. 90 PSIG or 6.2 Bar operating
pressure at the air inlet of the tool.)
Lubricate wick system and right angle gears through gear case
fitting. Apply 3 plunges of 95848 Gear Oil. Use 95541 Lubricant Gun
(Prime lubricant gun before use).
• Check tool for proper operation: If operating improperly or demonstrates
unusual vibration, the tool must be serviced and problem corrected before
further use.
Every 20 Hours/Once a Week (which ever comes first):
For tools without "wick system", lubricate right angle gears through
lubricant fitting. Apply 1 plunge of 95544 Grease. Use 95541
Lubricant Gun. (Prime lubricant gun before use).
• Measure RPM (speed) by setting air pressure to 90 PSIG (6.2 Bar) at
tool inlet, without accessory mounted, while the tool is running. Using
tachometer, check spindle speed of the tool. Unless otherwise stated the
no-load speed may not exceed the rated speed. If tool speed exceeds
maximum rated RPM, service as required and correct before use.
• If tool is running too fast: look for worn, damaged or missing governor, air
control rings and silencer(s). Service as required.
• If tool is running too slow: look for malfunctioning governor, clogged inlet
screen, silencer(s) or air stream. Service as required.
Note: Special care must be taken when servicing governors. Refer to specific
tool manual for governor instructions and/or speed control devices. Governor
assemblies made from molded plastic components are non-serviceable and
must be replaced.
Every 50 Hours:
Lubricate planetary gears through gear case fitting with 3 plunges
of 95544 Grease. Use 95541 Lubricant Gun. (Prime lubricant gun
before use).
REPAIR
• Use only genuine Dynabrade replacement parts to ensure quality. To order
replacement parts, specify Model#, Serial# and RPM of your air tool.
• Mineral spirits are recommended when cleaning the tool and parts. Do
not clean tool or parts with any solvents or oils containing acids, esters,
ketones, chlorinated hydrocarbons or nitro carbons.
• A Motor Tune-Up Kit is available which includes high wear and medium
wear motor parts.
• Air tool markings must be kept legible at all times, if not, reorder housing
and replace. User is responsible for maintaining specification information.
After maintenance is performed on tool, add a few drops of 95842
Dynabrade Air Lube to the tool inlet and start the tool a few times to
lubricate air motor. Verify RPM (per 20 hr maintenance schedule),
vibration and operation.
HANDLING & STORAGE
• Use of tool rests, hangers and/or balancers is recommended.
• Protect tool inlet from debris (see Notice below).
•Do Not carry tool by air hose or near the tool throttle lever.
• Store accessories in protective racks or compartments to prevent damage.
• Follow the handling instructions outlined in the operating instructions when
carrying the tool and when changing accessories.
• Protect accessories from exposure to water, solvents, high humidity,
freezing temperature and extreme temperature changes.
END OF USE/ DISPOSAL
When tool has reached its end of useful service, disassemble tool into its
primary components (i.e. steel, aluminum and plastic) and recycle or discard
per local, state and/or federal regulations as to not harm the environment.
NOTICE
All Dynabrade air motors use the highest quality parts available and are
manufactured to exacting tolerances. Air motor failures are often traced to lack
of lubrication or unclean air supply. Compressed air can force dirt and other
contaminants into motor bearings causing early failure. Contaminants can score
cylinder wall and vanes resulting in reduced efficiency and power. Our warranty
obligation is contingent upon proper use of our tools. Air motors which have been
subjected to misuse, contaminated air or lack of lubrication will void warranty.
Filter
Regulator
Lubricator
Lubricator Setting
90 PSIG
(6.2 Bar)
Air Flow to Tool Station
Ball
Valve
Ball
Valve
Air Flow
Drain
Valve
Drain
Valve
Air Tool
Air Compressor and Receiver
Drain Valve
Air Hose
90 PSIG Max.
(6.2 Bar)
Air Flow
Refrigerated
Air Dryer
• Dynabrade Air Power Tools
are designed to operate at 90
PSIG (6.2 Bar) maximum air
pressure at the tool inlet,
when the tool is running. Use
recommended regulator to
control air pressure.
• Ideally the air supply should
be free from moisture. To
facilitate removing moisture
from air supply, the installation
of a refrigerated air dryer after
the compressor and the use of
drain valves at each tool
station is recommended.
®®
®
®
®
®
CLOSED LOOP AIR SYSTEM
Sloped in Direction of Air Flow
O
W
G
O
2
®
~
1 Drop/Minute per 20 SCFM
G
WMV-Dresden, Ersatzteilservice für Elektrowerkzeuge, Motor- und Gartengeräte
WMV-Dresden, Ersatzteilservice für Elektrowerkzeuge, Motor- und Gartengeräte
WMV-Dresden, Ersatzteilservice für Elektrowerkzeuge, Motor- und Gartengeräte

WMV-Dresden
WMV-Dresden
WMV-Dresden
WMV-Dresden
WMV-Dresden
WMV-Dresden
WMV-Dresden
WMV-Dresden
WMV-Dresden
WMV-Dresden
WMV-Dresden
WMV-Dresden
WMV-Dresden
WMV-Dresden
WMV-Dresden
WMV-Dresden
WMV-Dresden
WMV-Dresden
WMV-Dresden
WMV-Dresden
WMV-Dresden
WMV-Dresden
WMV-Dresden
WMV-Dresden
WMV-Dresden
WMV-Dresden
WMV-Dresden
WMV-Dresden
WMV-Dresden
WMV-Dresden
WMV-Dresden
WMV-Dresden
Optional Accessories
Composite Dynaswivel®
Swivels 360° at two locations which
allows an air hose to drop straight to
the floor, no matter how the tool is held.
•
94300: 1/4" NPT.
95600 Motor Tune-Up Kit:
•
Includes assorted parts to help maintain
and repair motor.
50971 Lock Ring Tool
•
Lock Ring Tool has a 3/8 in. square socket
for use with 3/8 in. drive; breaker bar,
ratchet head, or torque wrenches.
96241 Bearing Press Tool
•
This tool is designed to safely press a bearing
into a bearing plate and onto a shaft.
96211 Bearing Removal Tool
•
This tool is designed yo pass through the
I.D. of the bearing plate and push against
the I.D. of the bearing.
Dynabrade Air Lube
•
Formulated for pneumatic equipment.
•
Absorbs up to 10% of its weight in water.
•
Prevents rust and formation of sludge.
•
Keeps pneumatic tools operating longer
with greater power and less down time.
95842: 1pt. (473 ml)
95843: 1gal. (3.8 L)
11288 Dynafile Contact Arm and Idler Wheel Repair Kit
•
Contains special tools to assist in the replacement
of contact wheels and bearings.
WMV-Dresden, Ersatzteilservice für Elektrowerkzeuge, Motor- und Gartengeräte
WMV-Dresden, Ersatzteilservice für Elektrowerkzeuge, Motor- und Gartengeräte
WMV-Dresden, Ersatzteilservice für Elektrowerkzeuge, Motor- und Gartengeräte
This manual suits for next models
1
Table of contents
Popular Tools manuals by other brands

T&S
T&S B-7245 Series Installation and maintenance instructions
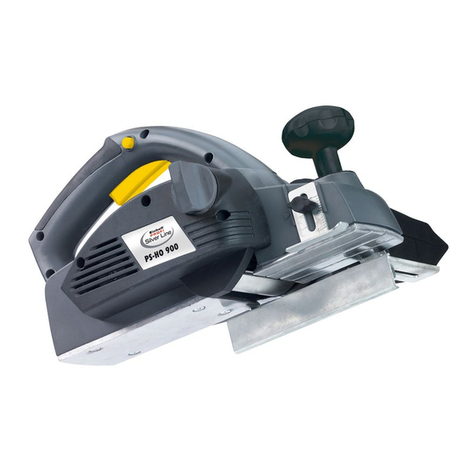
EINHELL PROFI
EINHELL PROFI SILVER LINE PS-HO 900 operating instructions

BGS technic
BGS technic 70952 instruction manual
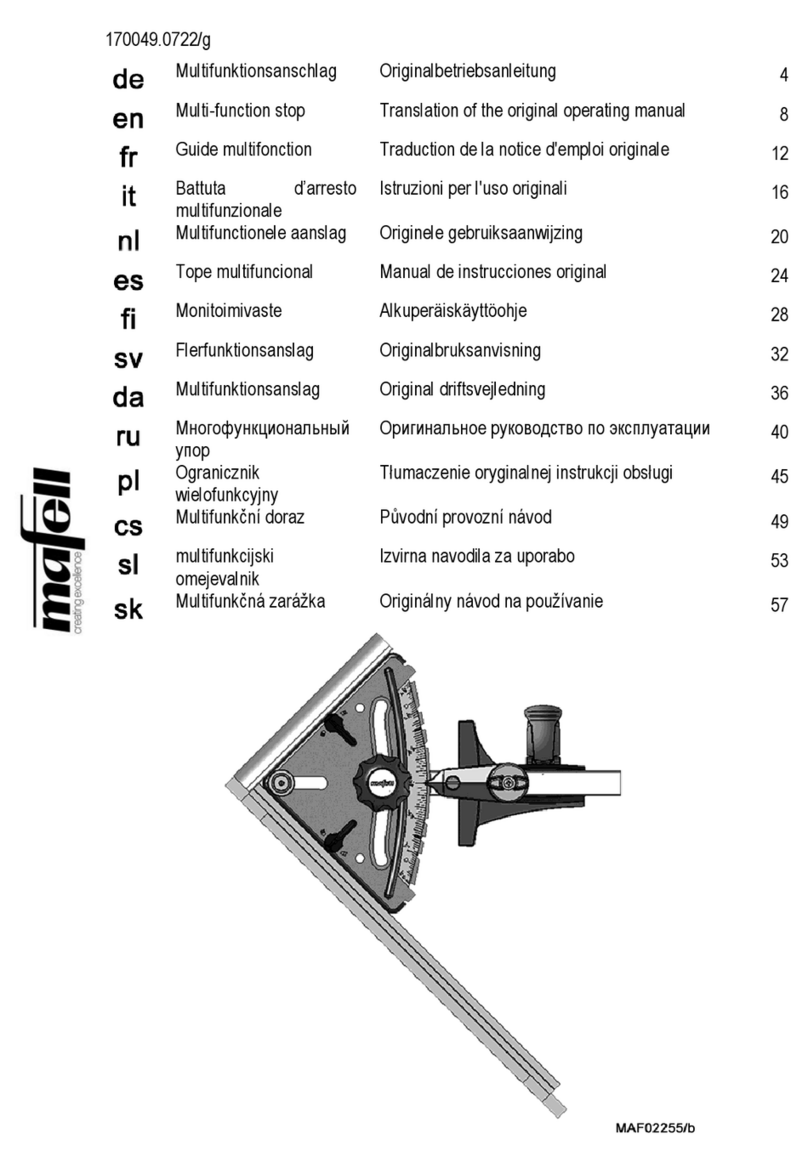
Mafell
Mafell 207910 Translation of the original operating manual
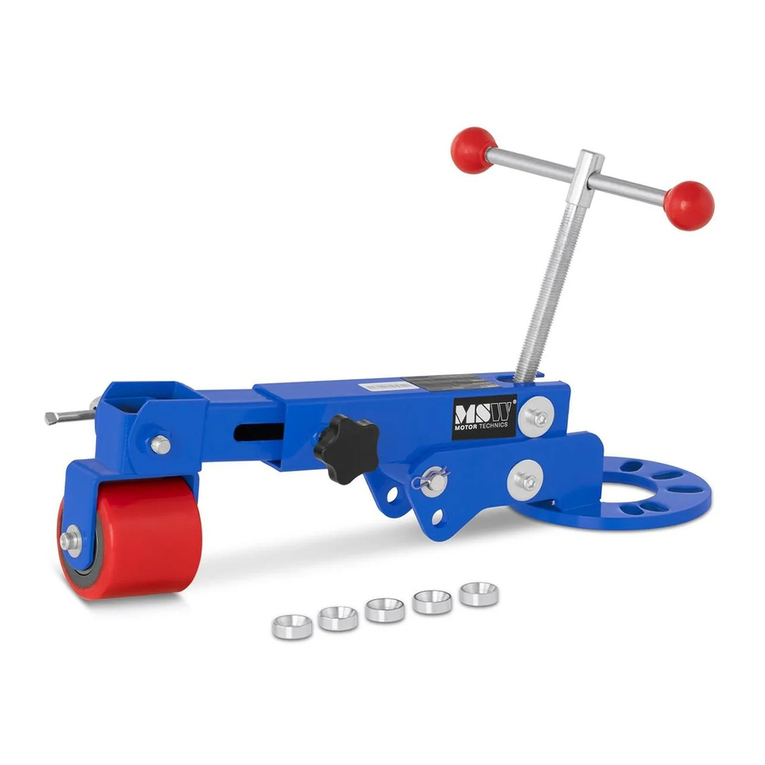
Expondo
Expondo MSW-BG-655 user manual

Wetekom
Wetekom 19 23 02 instruction manual