Eaton URTDII Manual










This manual suits for next models
2
Other Eaton Security Sensor manuals

Eaton
Eaton MEM Watchman 180 User manual
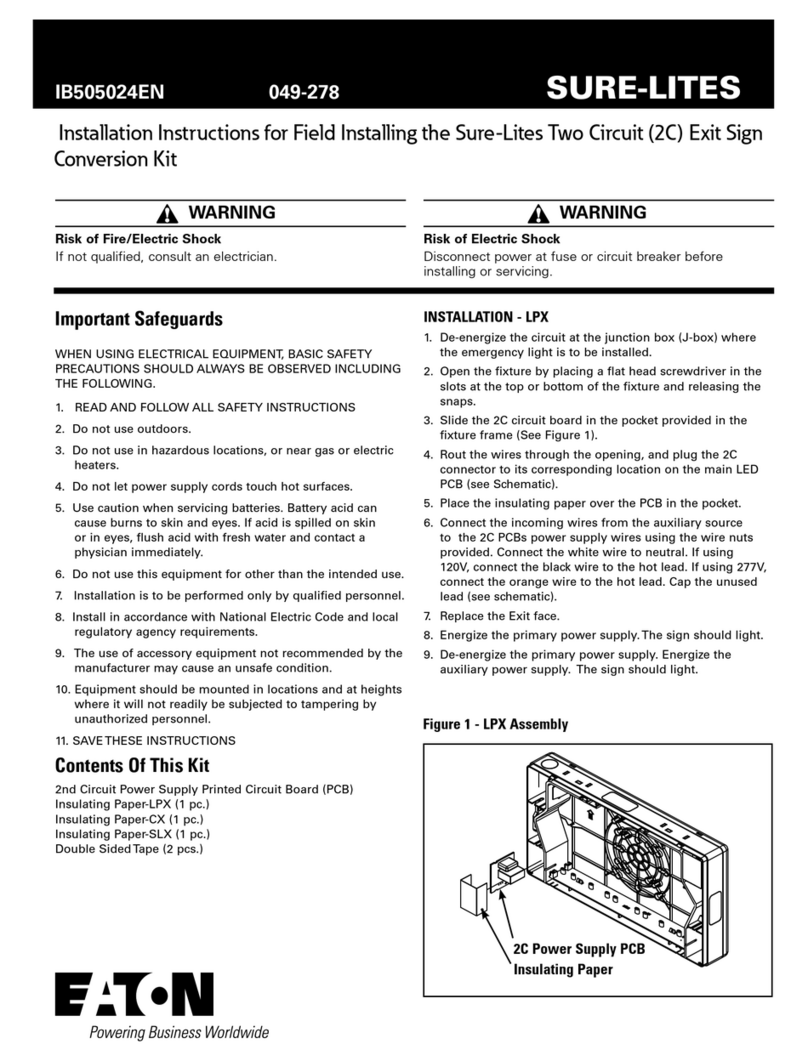
Eaton
Eaton Sure-Lites 2C User manual

Eaton
Eaton ALL-PRO MS185DW User manual
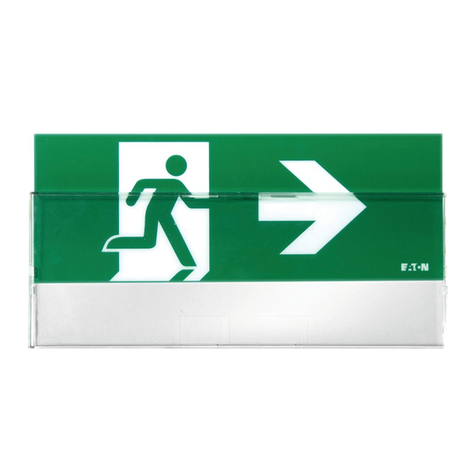
Eaton
Eaton NexiTech Series User manual
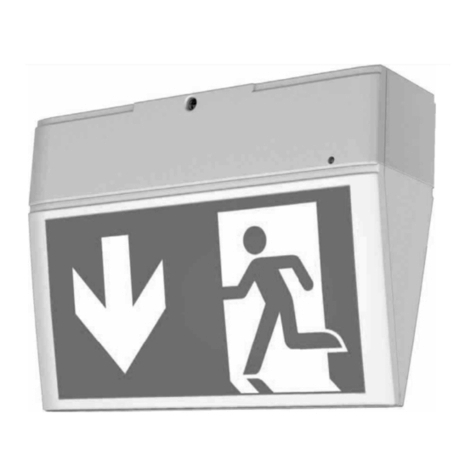
Eaton
Eaton CEAG EURO X LED Service manual
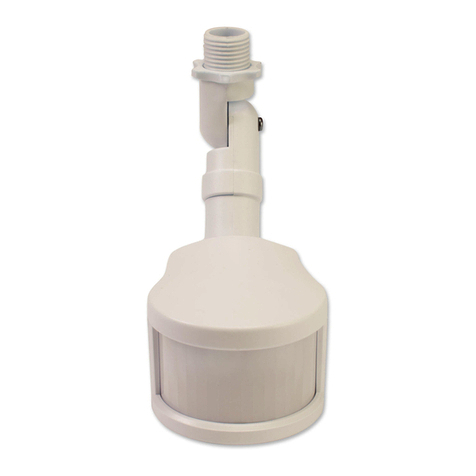
Eaton
Eaton All-Pro MS180BT User manual

Eaton
Eaton Sure-Lites UX6 User manual

Eaton
Eaton CEAG GuideLed Cinema 11011 CG-S Service manual
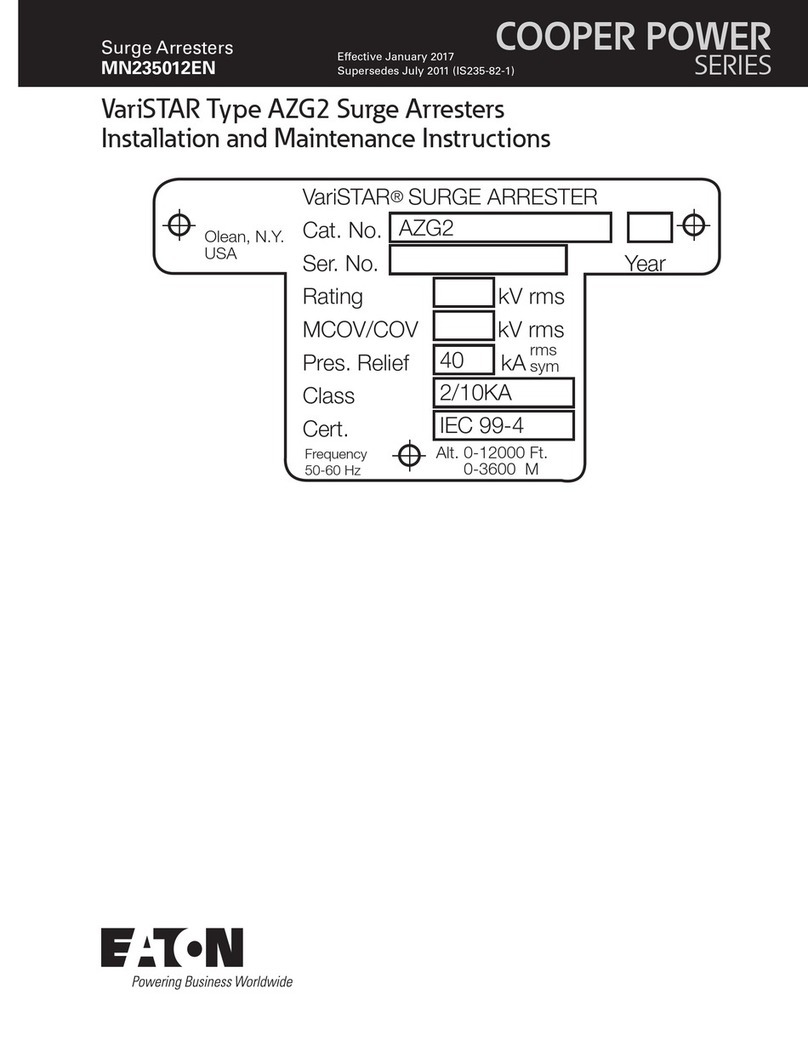
Eaton
Eaton COOPER POWER SERIES User manual
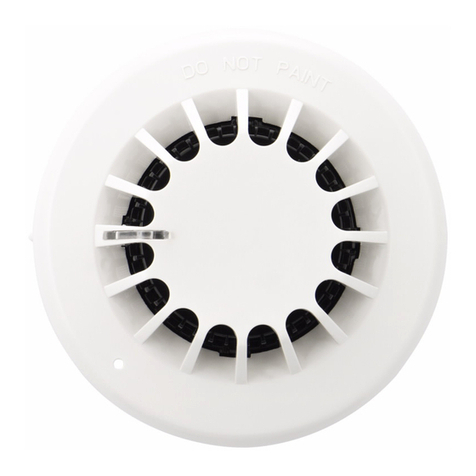
Eaton
Eaton MAP820 Instruction manual
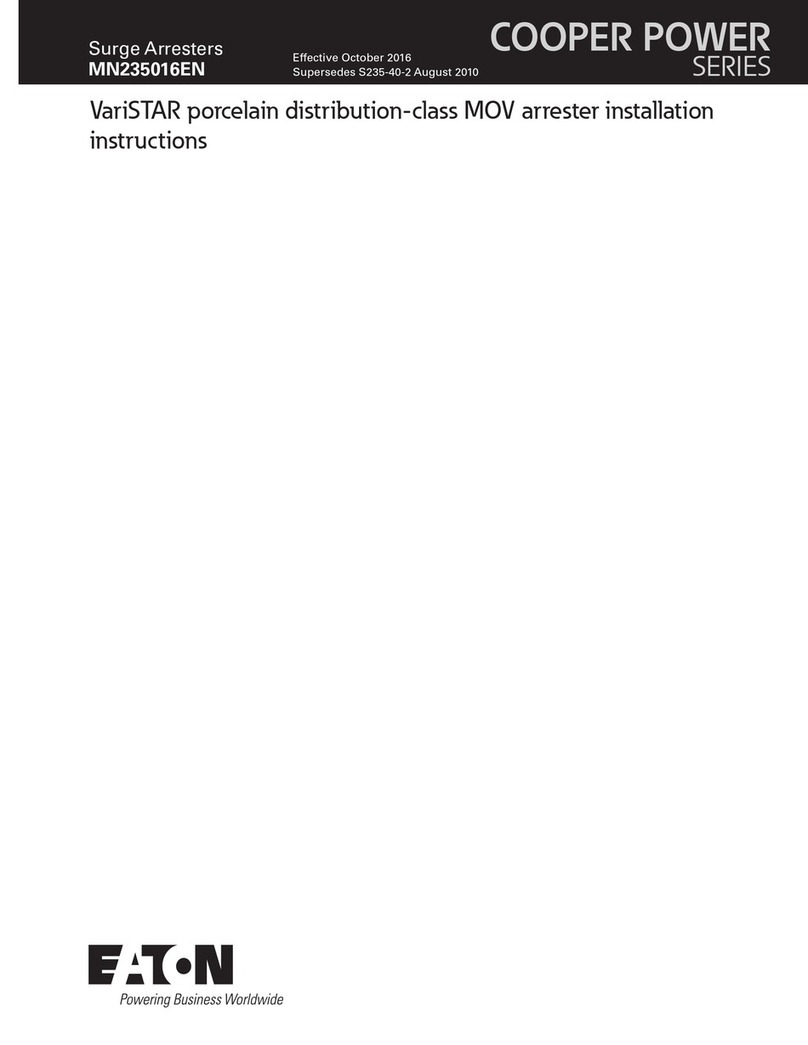
Eaton
Eaton COOPER POWER SERIES User manual
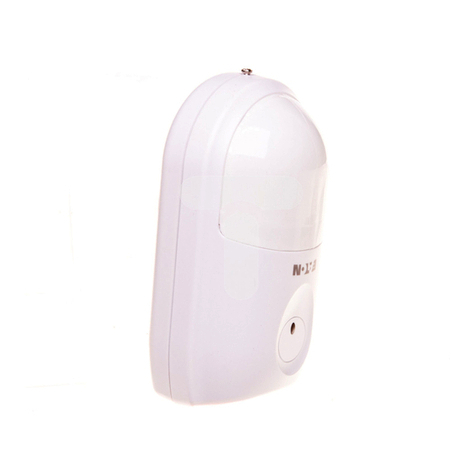
Eaton
Eaton xComfort CBMA-02/01 Manual
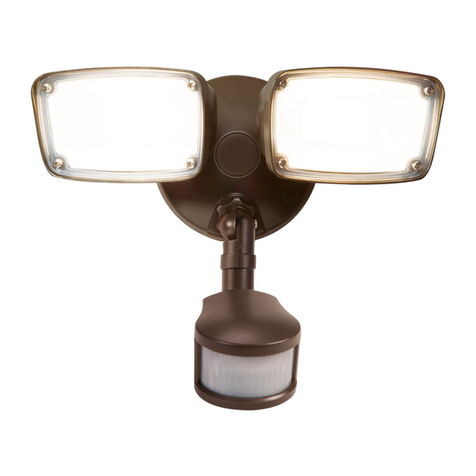
Eaton
Eaton HaloHome MST20C18W User manual

Eaton
Eaton CWGA-0 Series Manual
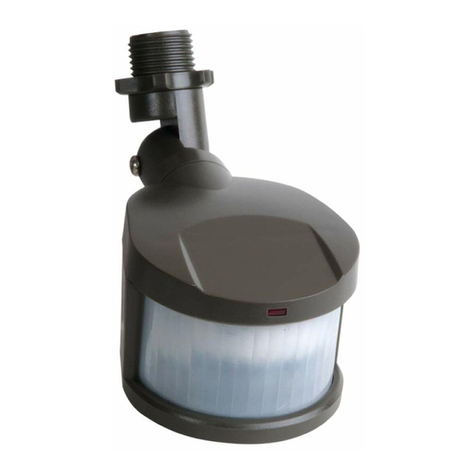
Eaton
Eaton All-Pro MS180 User manual
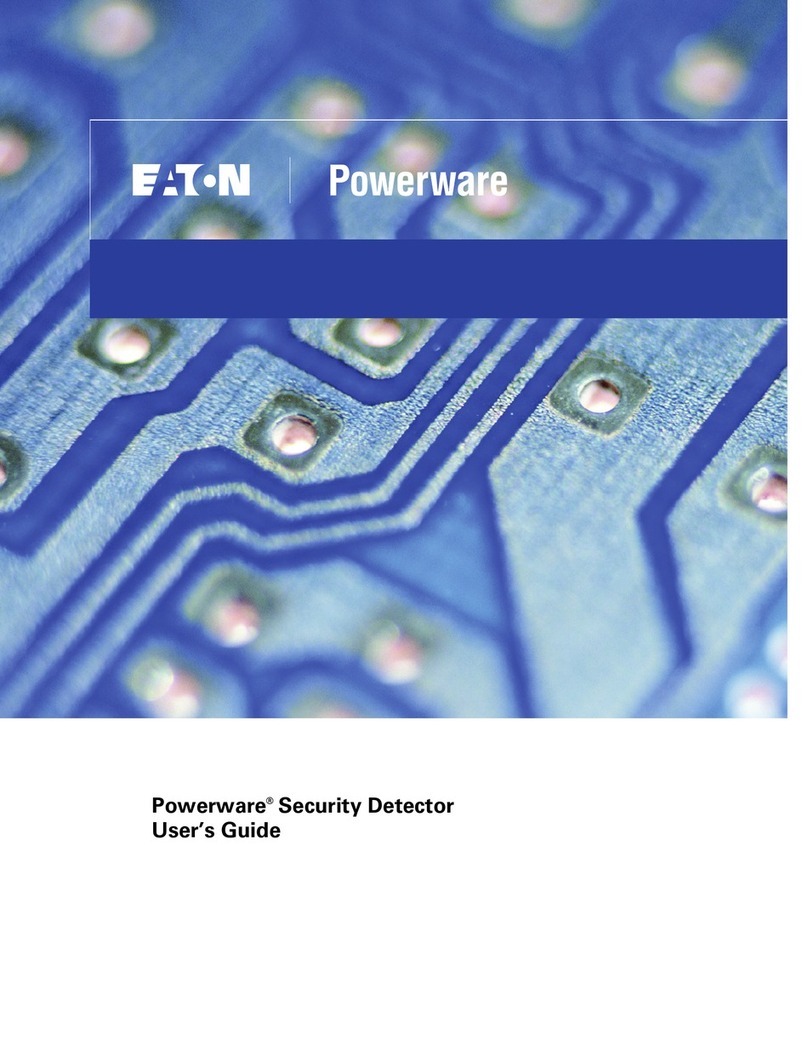
Eaton
Eaton Powerware Series User manual
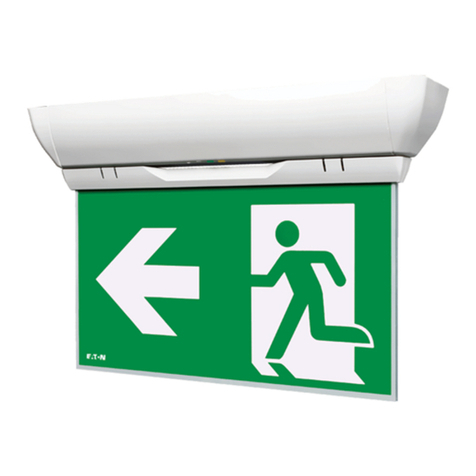
Eaton
Eaton Velos User manual
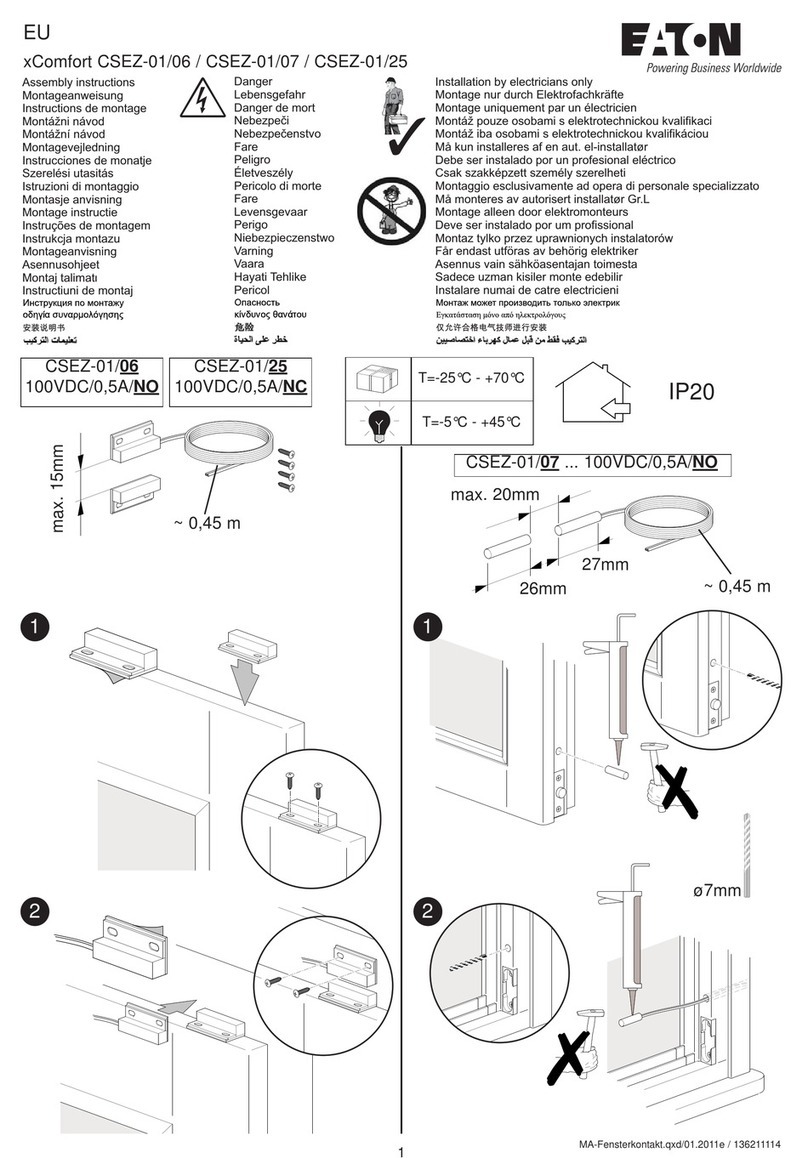
Eaton
Eaton xComfort CSEZ-01/06 User manual
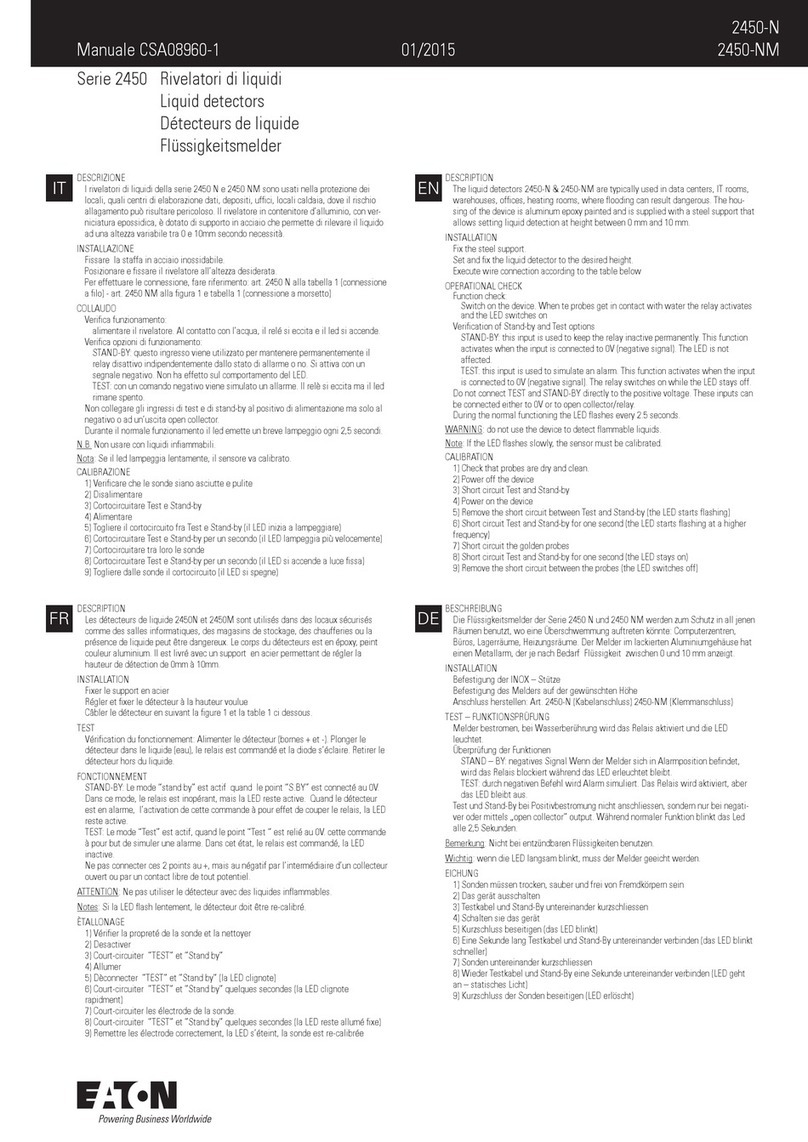
Eaton
Eaton 2450 Series User manual

Eaton
Eaton CEAG Style 22011 CG-S Service manual
Popular Security Sensor manuals by other brands
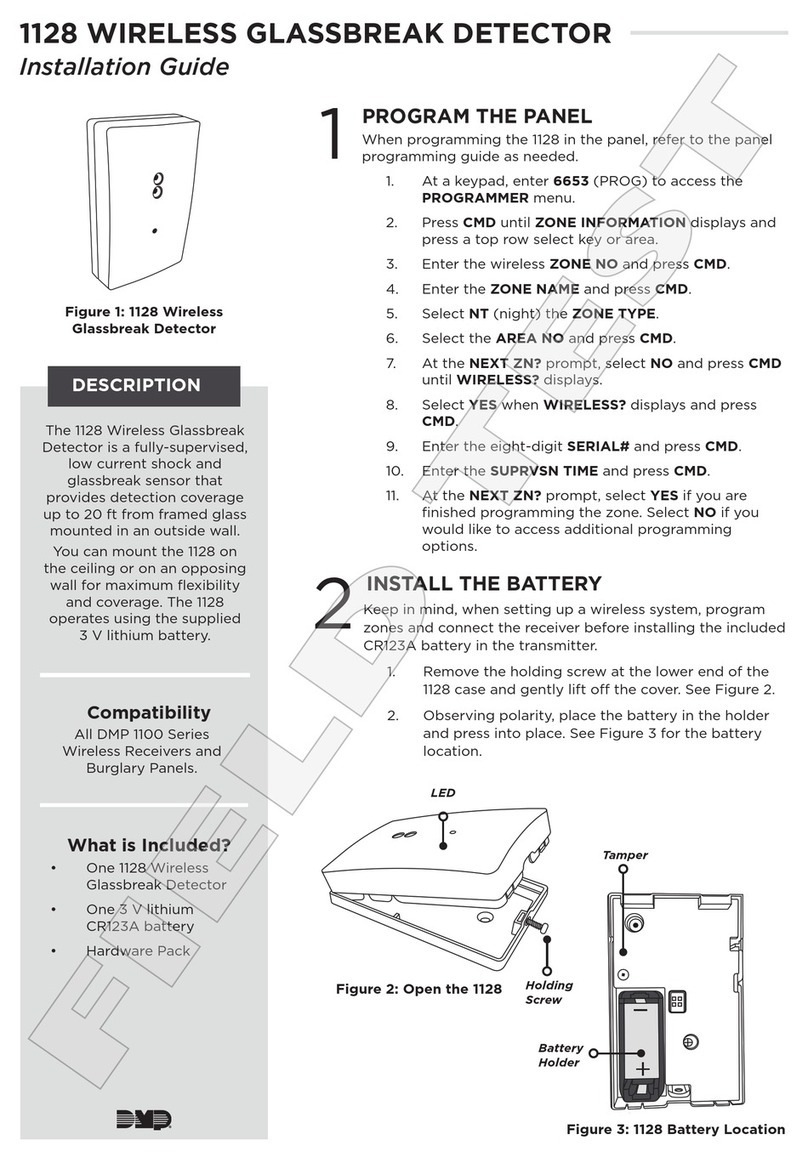
DMP Electronics
DMP Electronics 1128 installation guide

Conrad
Conrad FP500 operating instructions
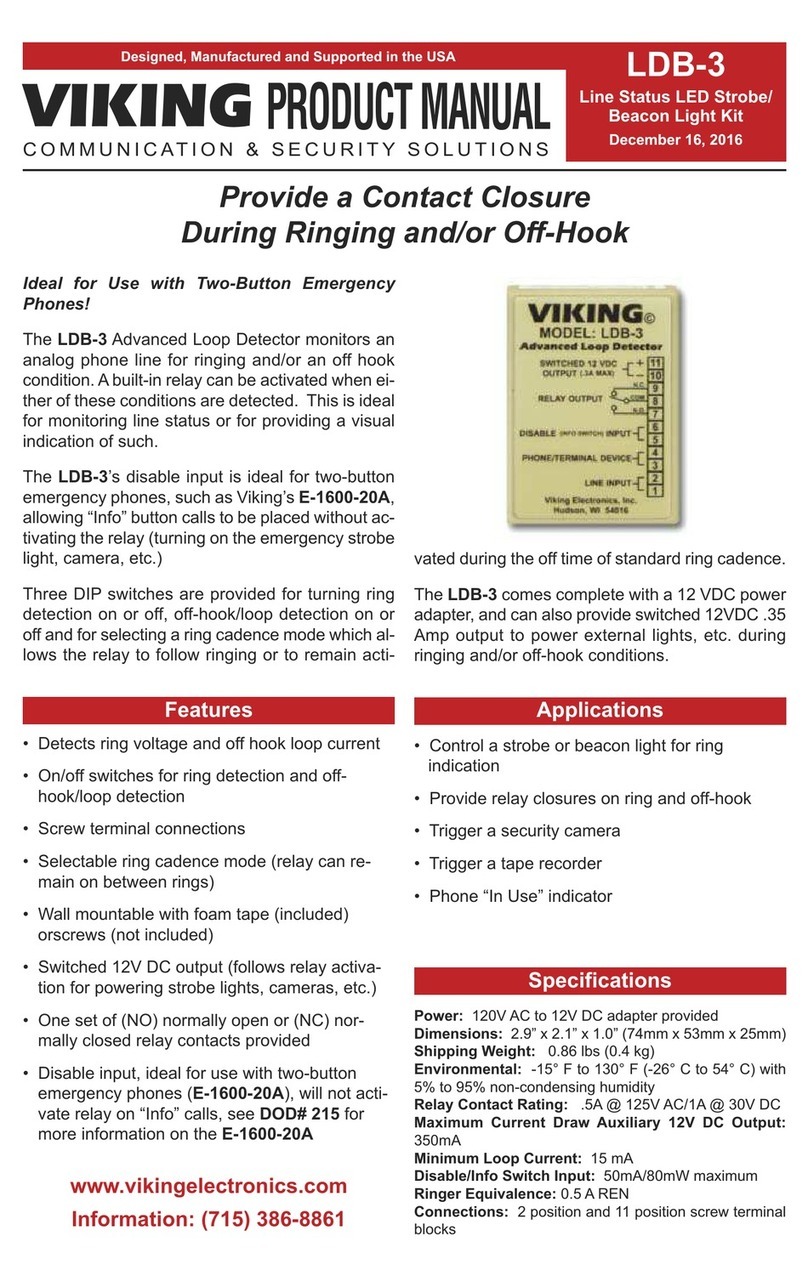
Viking
Viking LDB-3 product manual
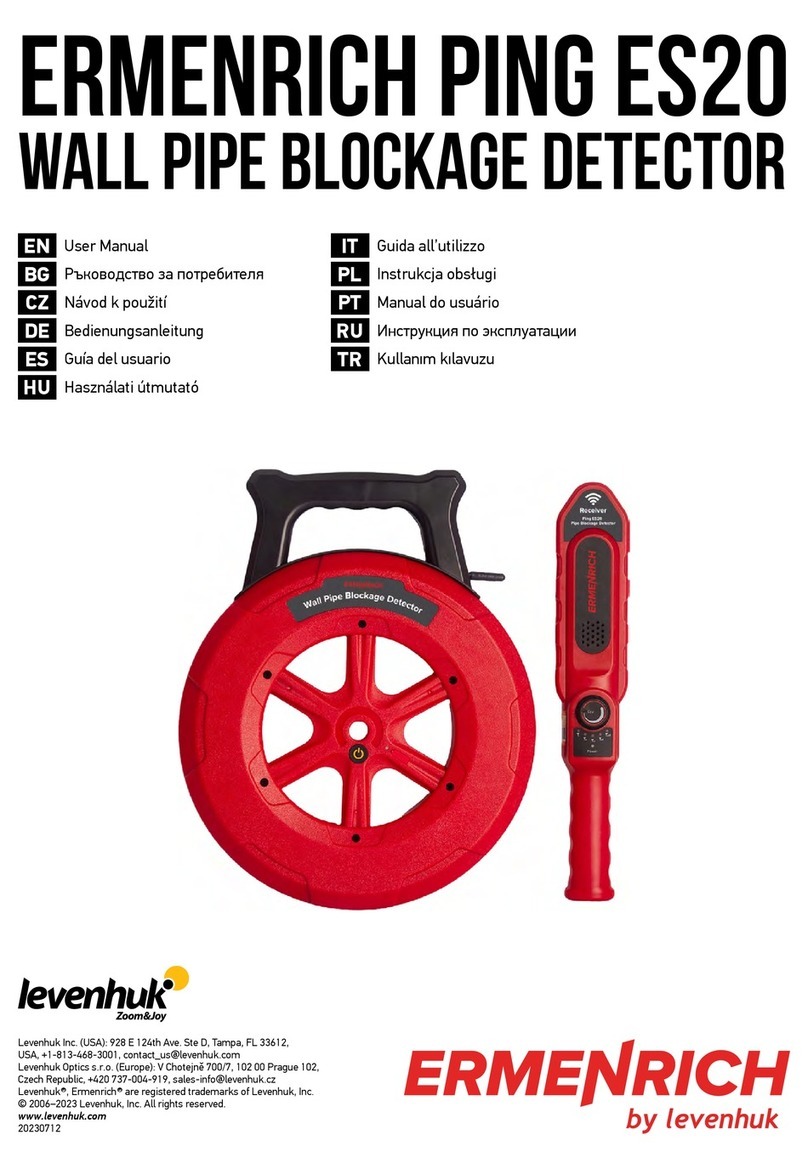
ERMENRICH
ERMENRICH Ping ES20 user manual

aci
aci A/CTA-5 Assembly, installation and operation instructions
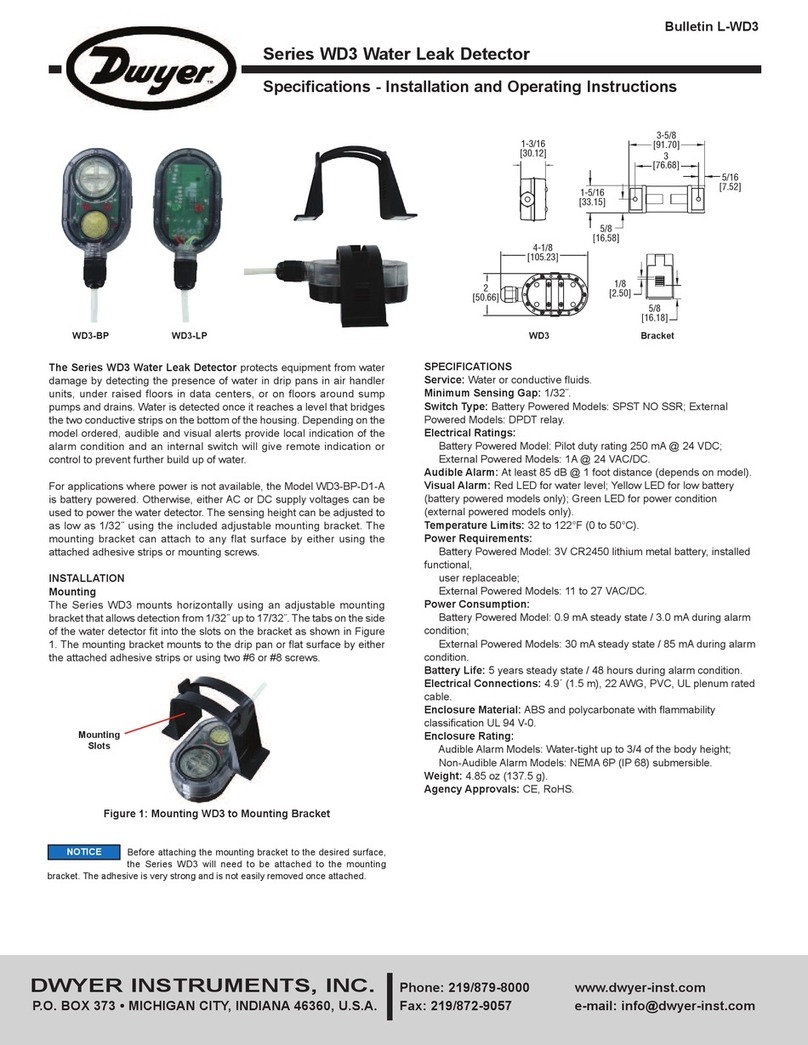
Dwyer Instruments
Dwyer Instruments WD3 Series Installation and operating instructions

Arch Environmental Equipment
Arch Environmental Equipment CTS 9000 IRRD Operation and installation manual

Homematic IP
Homematic IP HmIPW-SCTHD Installation instructions and operating manual
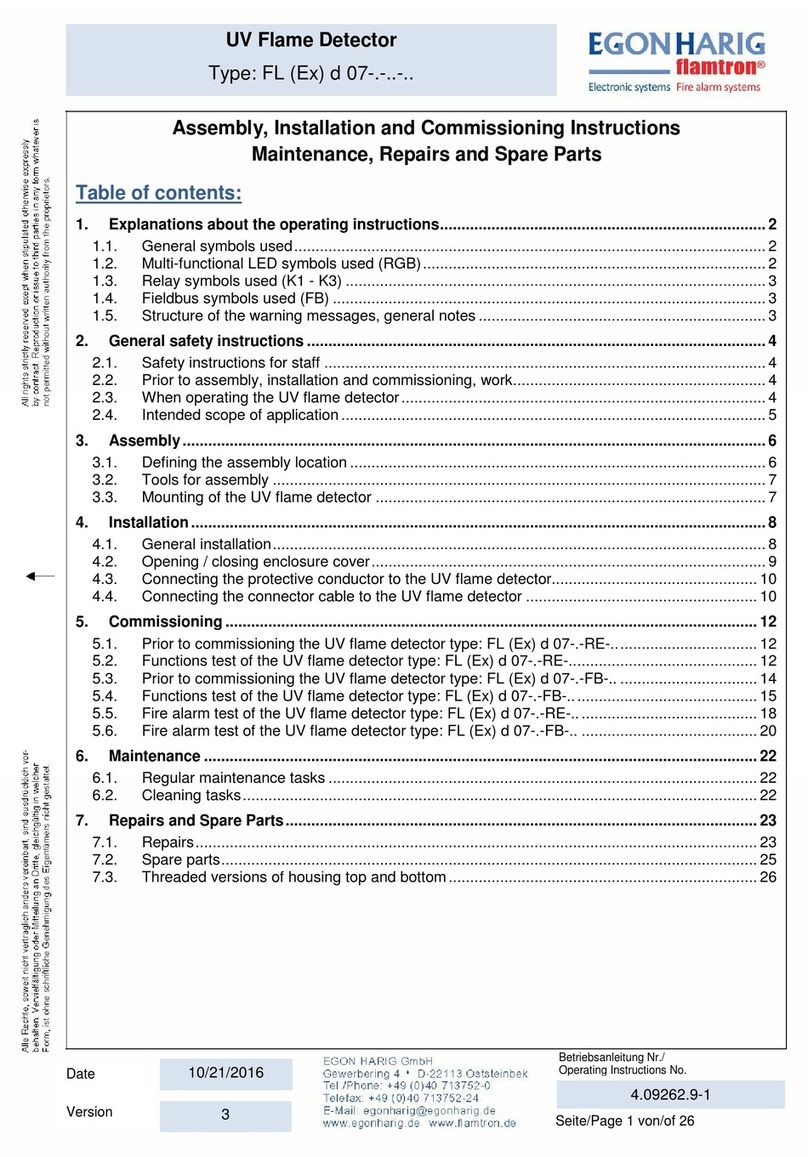
EGON HARIG
EGON HARIG flamtron FL (Ex) d 07 Series Assembly, Installation and Commissioning Instructions
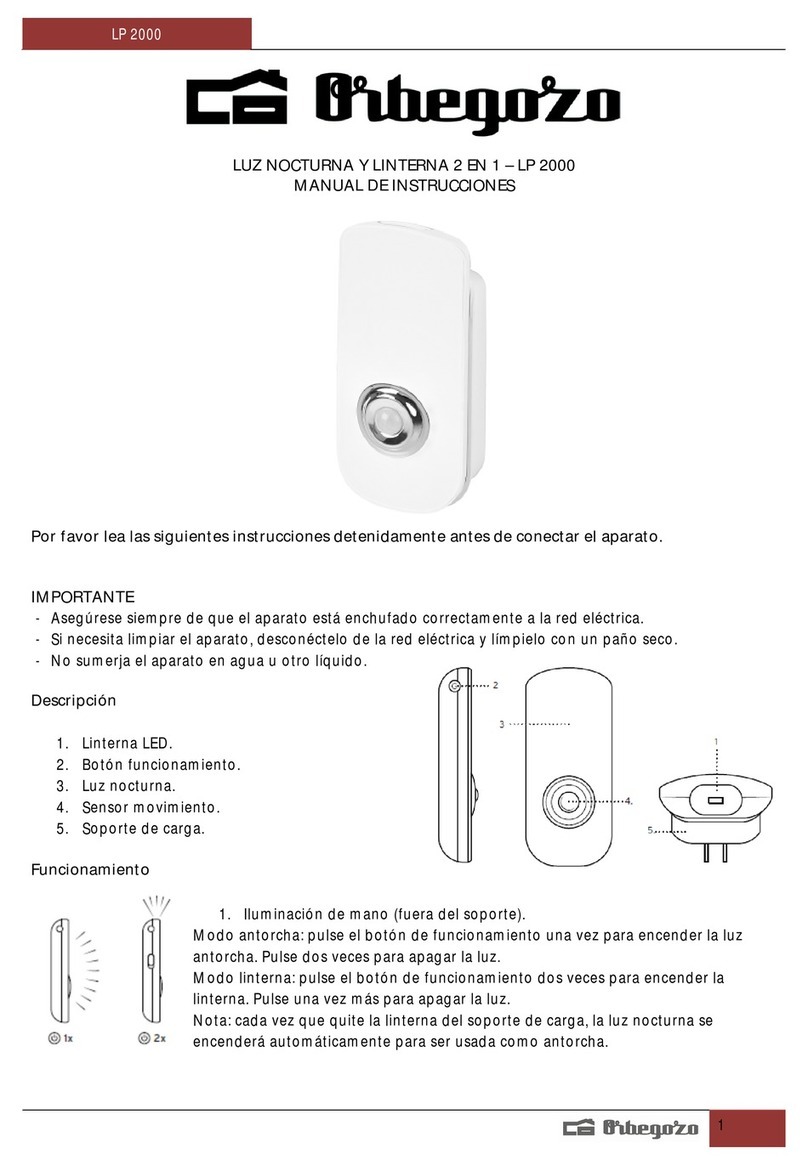
Orbegozo
Orbegozo LP 2000 instruction manual

Blaupunkt
Blaupunkt HD-S1 instructions
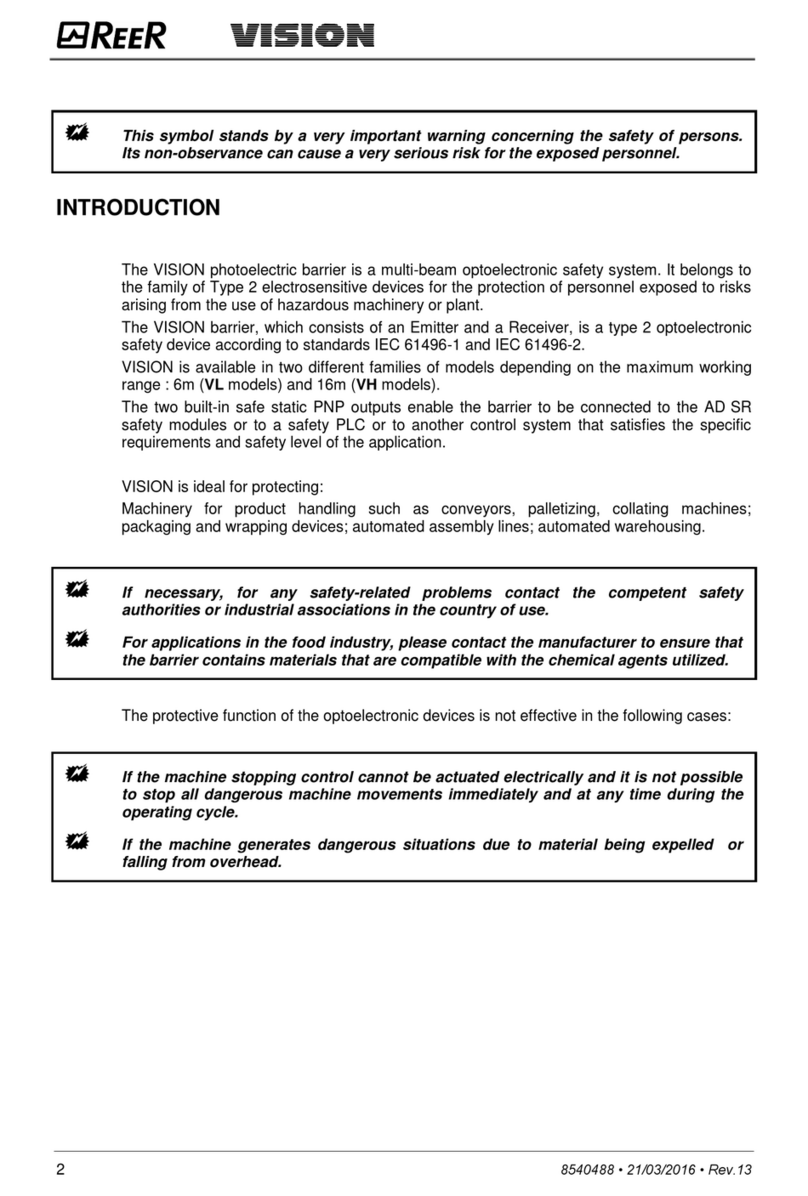
Reer
Reer VISION V3BL instructions