ECD 100-181 User manual

100-181 Controller Manual
Revision Date: Feb 22, 2017
ECD System
Manual

E L E C T R O N I C C I R C U I T D E S I G N S P T Y . L T D .
Operation Guide
This manual covers all versions of 1 -181 hardware
and software. Some features and operative descriptions
mentioned in this manual may differ or not be available on
earlier 1 -181 versions
Electronic Circuit Desi ns Pty. Ltd.
Factory 11/30 Perry Street • Matraville • NSW • Australia • 2036
Phone 61 2 9316 6909 • Fax 61 2 9316 6797
Email sales@ecd.com.au Web www.ecd.com.au

Table of Contents
Table of Contents............................................................................................ i
Section 1: Safety Regulations & Introduction .............................................. 4
1.2.1
Following operating instructions. ............................................ 4
1.2.2
Obligations of operator............................................................. 4
1.2.3
Obligations of personnel........................................................... 4
1.2.4
Hazards associated with the equipment. ................................. 5
1.2.5
Warranty and liability.............................................................. 5
1.2.6
Organizational measures.......................................................... 5
1.2.7
Protective equipment................................................................ 6
1.2.8
Informal safety measures. ........................................................ 6
1.2.9
Training of personnel. .............................................................. 6
1.2.10
Machine controls....................................................................... 6
1.2.11
Safety measures during normal operation. ............................. 6
1.2.12
Hazards caused by electric power............................................ 6
1.2.13
Hazards caused by hydraulic power........................................ 7
1.2.14
Special danger areas (examples). ............................................. 7
1.2.15 Controller Installation Environmental Requirements .............. 7
1.2.16 Introduction ................................................................................. 8
Section 2: EEProm Settings .......................................................................... 9
EEProm Version 4.02 Summary ................................................................. 10
EEProm Definitions (Full description)....................................................... 13
ADO - Advanced Door Opening setup.................................................. 13
ALP – Auxiliary Leveling Pump operation setup ................................ 13
ANS - Anti Nuisance setup..................................................................... 13
BCC - Bottom Car Call setup ................................................................ 13
BOT - Bottom floor setup ...................................................................... 13
BST – Brake Switch Time...................................................................... 14
CCMF - Car Call Mask (Front doors) setup ........................................ 14
CCMR - Car Call Mask (Rear doors) setup ......................................... 14
CNT - CNT Input setup ......................................................................... 14
COD – Parameter lockout function....................................................... 15
DCMF - Down Call Mask (Front doors) setup..................................... 15
DCMR - Down Call Mask (Rear doors) setup...................................... 15
DLI - Door Limit Invert setup............................................................... 15
DLM - Door Limit setup ........................................................................ 16
DRV - Drive type setup .......................................................................... 16
DT - Door Time Close setup .................................................................. 16
DTCF - Door Time Car call (Front doors) close setup ........................ 16
DTCR - Door Time Car call (Rear doors) close setup ......................... 16
DTHF - Door Time Hall call (Front doors) close setup........................ 17
DTHR - Door Time Hall call (Rear doors) close setup ........................ 17
DTL - Door Time Lobby call close setup .............................................. 17
DTRF - Door Time Recall Front setup ................................................. 17
DTRR - Door Time Recall Rear setup .................................................. 17
EQK......................................................................................................... 18
FS - Fire Service type ............................................................................. 18
HFAF - Hall Fire Alternate (Front doors) floor setup .........................18
HFAR - Hall Fire Alternate (Rear doors) floor setup .......................... 18
HFSF - Hall Fire Service (Front doors) return floor setup..................18
HFSR - Hall Fire Service (Rear doors) Return floor setup..................19
HRF – Hospital / Hall Recall Front doors.............................................19
HRR – Hospital / Hall Recall Rear doors..............................................19
LCK – Parameter lockout function .......................................................19
LOB - Lobby floor setup ........................................................................19
L.# - Lift Number setup..........................................................................19
MOD - MODE Inputs setup...................................................................20
MSL - Magnet Slowing type................................................................... 20
NR - Door Nudging setup .......................................................................20
PRK - Park/Zone with doors open.........................................................20
PRV - Proving required setup................................................................20
RLV - Re-Leveling setup ........................................................................20
RPT -
Run Protection Timer setup ...................................................21
RTM – Run Time short floor run setup ................................................ 21
SDX - Star Delta Exchange Time setup.................................................21
SDX - VF Drive setting 06,07,08 brake drop time ................................ 21
SFR - Short Floor Run setup..................................................................21
Spares.......................................................................................................22
StF - Start Fast........................................................................................22
StM - Start Medium................................................................................22
SlF - Slow Fast.........................................................................................22
SlM - Slow Medium ................................................................................22
ST2 - Star Delta Changeover Time setup.............................................. 22
ST2 - VF Drive setting 06,07,08 end run time.......................................22
TCC - Top Car Call setup ......................................................................22
TOP - Top floor setup.............................................................................23
UCMF - Up Call Mask (Front doors) setup ..........................................23
UCMR - Up Call Mask (Rear doors) setup ........................................... 23
XTM - Extend run time short floor run ................................................23
ZON - Zoning/Parking floor setup.........................................................23
ZTM - Zoning Time setup ......................................................................24
#.L - Number of Lifts setup ....................................................................24
Section 3. Group ..........................................................................................25
Group Connections and Communication..............................................25
Group Checks..........................................................................................26
Group/Duplex Faults ...........................................................................26
Section 4. Inputs – Outputs..........................................................................27
BRK - Brake relay output ......................................................................27
BSL – Bottom SLowing input ................................................................27
CBSF - Hall Button Stop (Front doors) output..................................... 27
CBSR - Hall Button Stop (Rear doors) output...................................... 27
CC - Car Call inputs/Darlington outputs .............................................. 27
CFS - Car Fire Service input..................................................................28

CFSS - Car Fire Service Start input...................................................... 28
DCBF - Door Close Button (Front doors) input................................... 28
DCBR - Door Close Button (Rear doors) input.................................... 28
DCF - Door Close (Front doors) relay output ...................................... 28
DCR - Door Close (Rear doors) relay output ....................................... 28
DDN - Direction Down output ............................................................... 28
DDO - Door Open Disable input / Toggle Switch................................. 28
DF - Down Fast relay output ................................................................. 29
DFCF - Door Fully Closed (Front doors) input.................................... 29
DFCR - Door Fully Closed (Rear doors) input..................................... 29
DFOF - Door Fully Open (Front doors) input...................................... 31
DFOR - Door Fully Open (Rear doors) input....................................... 31
DHC - Down Hall Call inputs/Darlington outputs ............................... 32
DN - Down Relay output........................................................................ 33
DOBF - Door Open Button (Front doors) input................................... 33
DOBR - Door Open Button (Rear doors) input.................................... 33
DOF - Door Open (Front doors) relay output ...................................... 33
DOR - Door Open (Rear doors) relay output ....................................... 33
DS - Down Slow relay output................................................................. 33
DUP - Direction Up output .................................................................... 33
DZ - Door Zone input............................................................................. 33
DZ – Door Zone relay output ................................................................ 33
EDPF - Electronic Door Protection (Front doors) input ..................... 33
EDPR - Electronic Door Protection (Rear doors) input ...................... 34
EP - Emergency Power input................................................................. 34
EQK – Earthquake Detection input...................................................... 34
HCB – Hall Call Bypass Input............................................................... 34
HFA - Hall Fire Alternate input............................................................ 34
HFL - Hall Fire Light output................................................................. 34
HFM Hall Fire Machine room/Hoist way input................................... 34
HFR - Hall Fire Reset Input .................................................................. 34
HFS - Hall Fire Service input ................................................................ 35
HFV - Hall Fire Visual signal output .................................................... 35
HV2 - High Voltage input ...................................................................... 35
IDN - Inspection Down input................................................................. 35
IND - Independent Service input........................................................... 35
INSP - Inspection Control input............................................................ 35
IUP - Inspection Up input...................................................................... 35
LEV - Leveling relay output .................................................................. 36
LR – Lock Relay input. ......................................................................... 36
LR – Lock Relay output......................................................................... 36
LRX – Aux LR input.............................................................................. 36
M3 - Door Locks input ........................................................................... 36
MSD – Magnetic Switch Down input .................................................... 36
MSU - Magnetic Switch Up input.......................................................... 36
NDGF - Nudging Buzzer output front doors ........................................ 37
NDGR - Nudging Buzzer output rear doors......................................... 37
NRF - Nudging output front doors ........................................................37
NRR - Nudging output rear doors .........................................................37
OS - Out of Service output .....................................................................37
PI - Position Indicator output ................................................................37
PRK - Parking function input................................................................38
PRV - Proving Circuit input ..................................................................38
PULSE – Pulse Counting input..............................................................38
SAF - Safety Circuit input......................................................................38
Sin1 - BKSW - Brake Switch Input .......................................................39
SIn3 – HR Input...................................................................................... 39
SO1 – Inspection Relay Output/Correction Run Output..................... 39
SO2 – HR Output....................................................................................39
SP1 - Multi Purpose output 1.................................................................39
SP2 - Multi Purpose output 2.................................................................39
SP3 - Multi Purpose Output 3................................................................40
SP4 - Multi Purpose output 4.................................................................40
TSL – Top SLowing input......................................................................40
UD - Up/Dn relay output ........................................................................40
UF - Up Fast relay output.......................................................................40
UHC - Up Hall Call inputs / outputs......................................................40
UP - Up relay output...............................................................................40
US - Up Slow relay output......................................................................41
Section 5. Liquid Crystal Display.................................................................42
LCD Status Line...........................................................................................42
LCD Position & Direction ......................................................................42
LCD Modes..............................................................................................42
LCD Lift Status.......................................................................................43
LCD Door Modes ....................................................................................43
LCD Control Buttons .............................................................................44
LCD Display Options..............................................................................44
Section 6. Motion .........................................................................................46
Motion Control Outputs.........................................................................46
Drive settings and their output status....................................................46
Counting Method “00” - Magnet Counting........................................... 54
Counting Method “01” - Pulse Counting. .............................................56
Counting Method “02” - Pulse Counting. .............................................65
Section 7: Faults – Fault finding.................................................................67
Upgrade Controller software. ................................................................67
Group/Duplex Faults ..............................................................................67
Leveling inhibit. LEV .............................................................................67
Run protection timer. RPT.....................................................................67
Lift won’t re-level with doors open........................................................67
On board fuse blows ...............................................................................68
Testing 24Vdc..........................................................................................68
Doors do not open ...................................................................................68
Doors close on park.................................................................................68
Doors don’t open at terminal floors....................................................... 68

Lift gets out of step ................................................................................. 68
Lift does not answer car calls................................................................. 68
Lift does not answer hall calls................................................................ 68
Lift misses hall calls................................................................................ 68
Re-leveling won’t operate....................................................................... 69
Red3 LED is not blinking....................................................................... 69
Processor errors/Lockup: ...................................................................... 69
Section 8. Upgrades, Changes & Technical Information........................... 70
Controller ID. .............................................................................................. 71
Terminal Screw Torque Settings................................................................. 72

S A F E T Y R E G U L A T I O N S & I N T R O D U C T I O N
4
Section 1: Safety Regulations & Introduction
Section 1.1 Safety Re ulations
Elevator controllers and other electrical components can cause serious harm or death if installation uides are not
met. It is the responsibility of the installer of our equipment to ensure that once installed, the equipment does not
pose any threat, dan er or hazard.
Installation of this equipment shall be done in accordance with AS1735 for Australia and with all applicable local
codes and NFPA 70 (National Electric Code) for the U.S.A. and C22.1-02 Canadian Electrical Code Part 1 for
Canada as well as ASME A17.1, CAN/CSA-B44.1.
Section 1.2 Obli ations and Liability
1.2.1 Following operating instructions.
•In order to ensure safe handlin and problem free operation of this equipment, it is absolutely
essential for the relevant personal to be fully acquainted with the relevant safety re ulations.
•These operatin instructions contain the most important information for operatin the machine correctly
and safely.
•These operatin instructions, in particular the safety re ulations, must be observed by all those persons
who work on the equipment.
•Furthermore, all locally applicable rules and re ulations relatin to accident prevention and installation
must be observed.
1.2.2 Obligations of operator.
The operator undertakes to allow only those persons to work on the equipment who
•Are fully acquainted with the basic re ulations relatin to safety in the workplace and accident prevention
and to have been trained in handlin the equipment.
•Have read the safety re ulations and the warnin notices contained in these the operatin instructions.
•Re ular checks are conducted to ensure that personnel perform their duties with safety considerations
foremost in their minds.
1.2.3 Obligations of personnel.
All personnel char ed with workin on the machine undertake prior to startin work to
•Observe the basic re ulations relatin to safety in the workplace and accident prevention.
•Read the operatin instructions, in particular the safety re ulations, and confirm by way of their si nature
that they have understood them.
Section
1

S A F E T Y R E G U L A T I O N S & I N T R O D U C T I O N
5
1.2.4 Hazards associated with the equipment.
The equipment is built with state-of-the-art technolo y and reco nized safety re ulations. Nevertheless, use of the
equipment can result in dan ers to life and limb for the installer, user or a third party and in impairments to the
equipment or to other material property. The equipment must only be used
•For its intended purpose.
•In perfect condition in terms of safety requirements.
Operate the equipment in technically perfect condition and for its intended use only while bearin in mind all
safety and hazard considerations and followin the operatin instructions. In particular, faults which restrict safety
must be rectified immediately after they have been identified and at the latest before the equipment is started up.
Compliance Testin for AS/NZS CISPR 22:2002 Class A
Compliance Testin for FCC Title 47 Part 15, Subpart B Class A
1.2.5 Warranty and liability.
Our “Sales terms and conditions” apply. These terms and conditions will have been available to the purchaser at
time of sale. Warranty and liability shall be limited to repairs and replacement to the equipment purchased from
us. Warranty and liability claims shall not be entertained if they can be traced back to one or more of the followin
causes.
•Equipment not used for its intended purpose.
•Improper installation, startup, operation and maintenance of the equipment.
•Operation of the equipment with faulty safety devices or improperly installed or non-operational safety
and protective equipment.
•Failure to observe the information, instructions and notices contained in the operatin instructions
relatin to transportation, stora e, installation, startup, operation, maintenance and settin up of the
equipment.
•Inadequate monitorin of the equipment parts which are subject to wear.
•Improperly conducted repairs.
•Catastrophes caused by the influence of forei n bodies and force majeure.
1.2.6 Organizational measures.
•The installer and or maintainer shall provide the necessary protective equipment for the personnel
•All existin safety equipment must be checked at re ular intervals.
WARNING !
This is a Class A product. In a domestic environment this product may cause radio
interference in which case the user may be required to take adequate measures.
FCC PART 15
This device complies with part 15 of the FCC rules. Operation is subject to the
followin two conditions:
1. This device may not cause harmful interference, and
2. This device must accept any interference received, includin interference that
may cause undesired operation.

S A F E T Y R E G U L A T I O N S & I N T R O D U C T I O N
1.2.7 Protective equipment.
•At all times, prior to puttin the machine into operation, all protective equipment must be correctly
installed and in proper workin condition.
•Protective equipment may only be removed
-after the machine has come to a complete stop and the machine has been disabled to ensure it
cannot be started up a ain.
-if subcomponents are delivered, the operator must install the protective equipment in
accordance with re ulations
1.2.8 Informal safety measures.
•Keep the operatin instructions and circuit dia rams permanently at the site where the equipment is
installed.
•In addition to the operatin instructions, the enerally valid and local re ulations relatin to accident
prevention and environmental protection must be provided and observed.
•Maintain all safety and dan er notices on/next to the machine in le ible condition and comply with
them.
•If the equipment is sold or transferred, the operatin instructions must be included with the equipment.
1.2.9 Training of personnel.
•Only personnel who have been trained and instructed are allowed to work on the machine.
•The responsibilities of the personnel must be clearly defined for the machine/controller installation,
startup, operation, settin -up, maintenance and repairs.
•Personnel still in the process of bein trained are only permitted to work at the machine under the
supervision of an experienced person.
1.2.10 Machine controls.
•Under no circumstances carry out any pro ram modifications to the software!
•Only properly instructed personnel are permitted to operate the controls.
•The machine must not be operated if potential electroma netic interference sources are actin on the
machine. Interference sources are e. . weldin equipment, portable phones.
1.2.11 Safety measures during normal operation.
•Only operate the machine when all protective equipment is fully operational.
•Prior to switchin on the machine, ensure that the startup can cause no harm to personnel.
•Re ularly maintain and check machine for externally identifiable dama e and check that all the safety
devices are operational.
1.2.12 Hazards caused by electric power.
•Ensure V and +24V are free from other voltages. High voltages may be superimposed on V
and 24Vdc lines as no reference to ground exists. See Warning 1.2.14
•Work on the electric power supply may only be carried out by a qualified electrician.
•Check the electrical equipment of the machine at re ular intervals.
Repair loose connections and scorched cables immediately.
•Keep the control cabinet locked at all times. Access is only permitted to authorized personnel with a key
or tool.

S A F E T Y R E G U L A T I O N S & I N T R O D U C T I O N
7
•If work has to be carried out on live parts, do this only in the presence of a second person who can
switch off the master switch in an emer ency.
•The machine causes electroma netic interference sources. For this reason, do not use any sensitive
equipment in its vicinity.
•For EMC reasons, the controller must not be modified.
1.2.13 Hazards caused by hydraulic power.
•Only personnel with special knowled e and experience in the field of hydraulics may work on hydraulic
equipment.
•Before be innin repairs, depressurize system sections and pressure lines which are to be opened.
1.2.14 Special danger areas (examples).
•When on inspection, always ensure either of the common or direction control buttons stops the lift.
•The common button shall break the safety line and the 0V up/down direction input.
•Never place yourself or any party in a position of dan er where relyin on any sin le safety measure.
•Automatic machines start without warnin . Care must be taken at all times.
1.2.15 Controller Installation Environmental Requirements
Controller cabinet must be installed in a location free from;
•Dust and dirt.
•Excessive heat and humidity. Ambient temperature should not exceed 40°C /104°F.
•Excessive vibrations.
•Mist or water
When mountin controller cabinet, ensure it is suitably supported.
WARNING !
Always treat terminals and conductors as dangerous. High voltages may be
superimposed on V and 24Vdc lines as no reference to ground exists. Always
meter these points to ensure correct voltage exists.

E E P R O M S E T T I N G S
1.2.16
Introduction
he 1 -181 controller enables independent control of the front and rear doors at each
floor.
The 100-181 controller can operate up to 8 floors.
The controllers can be rouped up to a 6 car roup and may be inter-connected usin 3 wire serial communication. A
separate roup controller is therefore, not required.
Processor
Under normal operation;
•The red Red3 LED blinks to confirm that the microprocessor is runnin .
•The yellow Yel3 LED comes on to confirm outputs are enabled.
•The reen Grn3 LED comes on durin power up and turns off durin normal operation. It will
also flash once when a new value has been written in to EEPROM.
When re-powerin ; ensure the lift is off for 10 seconds before turnin back on.
On power up, a delay of approximately 2 seconds is iven on start up to ensure volta es are stable prior to readin
and writin outputs.
T

E E P R O M S E T T I N G S
Section 2: EEProm Settings
EEProm How to read and modify settings
This EEProm holds settin s for the particular contract data includin number of
floors, door type and drive types.
The EEPRom holds values for various contract settin s which may be altered on site. Each settin has a definition
followed by its value in hex followed by its value in bit format.
To inspect the settin s from the power up state,
press the forward “>” button located to the left
below the LCD until the EEPROM settin appears.
To inspect the settin s from the power up state,
press the forward “>” button located to the left
below the LCD until the EEPROM settin appears.
Now you can use the up “∧” and down “∨”buttons
to scroll throu h the settin s. If you want to chan e
a settin press the enter “ENT” button and a * shall
appear on the screen to indicate you are in edit mode.
Now use the up “∧” and down “∨” buttons to
chan e the settin . When you are at the required
value press the enter “ENT” button a ain and the *
shall disappear.
EEProm Security
A special write sequence has been added to ensure unauthorized writes to the EEProm are not made. Only
operates with EEProms with this capability. These EEproms are recommended and identified by a “contract data
secure” label.
Section
2
01- NOR IDL ][
ECD Aust. V-4.02
01- NOR IDL ][
TOP: 08:00001000
01- NOR IDL ][
TOP:*08:00000010
01- NOR IDL ][
TOP: 06:00000010

E E P R O M S E T T I N G S
EEProm Version 4. 2 Summary
The EEProm holds values for various contract settin s which may be altered on site. Each settin has a definition
followed by its value in hex and then its value in bit format.
Note: Refer to EEProm Definitions (Full description) for more information.
BOT Bottom floor number (VALUE)
Settin example:- BOT 01: 00000001 (Level 1)
TOP Top floor number (VALUE)
Settin example:- TOP 06: 00000110 (Level 6 is top floor)
BCC Bottom car call for “BOT CALL” button on the circuit board (MASK)
Settin example:- BCC 80: 10000000 (Bottom call Level 1)
TCC Top car call for “TOP CALL” button on the circuit board (MASK)
Settin example:-TCC 04: 00000100 (Top call to level 6)
CCMF Car call mask. Front doors floors allowed. (MASK)
Settin example:-CCMF FC: 11111100 (Front doors, levels 1-6)
CCMR Car call mask. Rear doors floors allowed. (MASK)
Settin example:-CCMR F8: 11111000 (Rear doors, levels 1-5)
UCMF Up call mask. Front doors floors allowed. (MASK)
Settin example:- UCMF F8: 11111000 (Front doors, levels 1U-5U)
UCMR Up call mask. Rear doors floors allowed. (MASK)
Settin example:- UCMR F0: 11110000 (Rear doors, levels 1U-4U)
DCMF Down call mask. Front doors floors allowed. (MASK)
Settin example:- DCMF 7C: 01111100 (Front doors, levels 2D-6D)
DCMR Down call mask. Rear doors floors allowed. (MASK)
Settin example:- DCMR 78: 01111000 (Rear doors, levels 2D-5D)
LOB Lobby floor. (MASK)
Settin example:- LOB 40: 01000000 (Level 2 is the master zonin floor)
ZON Zone floor. (MASK)
Settin example:-ZON 10: 00010000 (Zone to Level 4)
ZTM Zonin time. (VALUE)
Settin example:-ZTM 06: 00000110 (= 60seconds)
HFSF Hall fire service floor. Front doors floors (MASK)
Settin example:-HFSF 80: 10000000 (Front doors, level 1)
HFSR Hall fire service floor. Rear doors floors (MASK)
Settin example:-HFSR 00: 00000000 (Rear doors, no settin )
SFR Short Floor Run (MASK)
Settin example:- SFR 9F: 10011111 (Short floor between 2&3)
L.# Lift Number (VALUE)
Settin example:- L.# 02: 00000010 (Lift #2)
#.L Number of Lifts (VALUE)
Settin example:- #.L 03: 00000011 (3 Lifts in roup)
MOD Mode inputs (MASK)
Settin example:- MOD 02: 00000010 (CFS input inverted)
CNT CNT inputs (MASK)
Settin example:- CNT 02: 00000010 (DOB input inverted)
HFAF Hall fire alternate floor. Front doors floors. US only (MASK)
Settin example:- HFAF 00: 00000000 (Front doors, no settin )
HFAR Hall fire alternate floor. Rear doors floors. US only (MASK)
Settin example:- HFAR 40: 01000000 (Rear doors, level 2 alt. fire floor)
PRV If set to "1" requires PRV on all DRV settin s

E E P R O M S E T T I N G S
RPT Run protection timer
Settin example:-RPT 01: 00000001 (25s)
DRV Drive control type.
Settin example:-DRV 02: 00000010 (3010/2CH/S block)
ST2 Star Delta time. (VALUE)
Settin example:-ST2 08: 00001000 (= 800ms)
SDX Star Delta Exchan e time. (VALUE)
Settin example:-SDX 01: 00000001 (= 100ms)
MSL Ma net slowin type.
Settin example:- MSL 00: 00000000 (MSU/MSD slowin )
MSL 01: 00000001 (Pulse slowin )
RTM Extend run time. – If slowin is obtained less than this time, then add the value
of in XTM on before droppin hi h speed.
Settin example:-RTM 00: 00000000 (No extended run time.)
XTM Extend run time. – If a short floor determined by RTM then add this amount of
Time on before droppin hi h speed.
Settin example:-XTM 00: 00000000 (No extended run time.)
StF Start Fast. - Number of pulses it takes to reach fast speed.
StM Start Medium.- Number of pulses it takes to reach medium speed.
SlF Slow Fast. - Number of pulses it takes to slow from fast speed.
SlM Slow Medium.- Number of pulses it takes to slow from medium speed.
RLV Re-levelin . Turn re-levelin on/off.
Settin example:-RLV 00: 00000000 (No Re-level.)
RLV 01: 00000001 (Re-levelin on.)
DLM Door limit mask.
Settin example:-DLM 00: 00000000 (Sin le doors.)
DLM 01: 00000001 (Multi doors.)
DLM 02: 00000010 (Door cam.)
DLI Door limit invert. (MASK)
Settin example:-DLI 00: 00000000 (Limits not inverted.)
NR Nud in Relay for door nud in /Passin tone (MASK)
Settin example:-NR 00: 00000000 (Nud in off.)
ADO Advanced Door Openin .
Settin example:-ADO 00: 00000000 (Off )
DTCF Door time car call for front doors. (VALUE)
Settin example:-DTCF 32: 00110010 (= 5000ms, “5 seconds”)
DTCR Door time car call for rear doors. (VALUE)
Settin example:-DTCR 32: 00110010 (= 5000ms, “5 seconds”)
DTHF Door time hall call for front hall. (VALUE)
Settin example:-DTHF 32: 00110010 (= 5000ms, “5 seconds”)
DTHR Door time hall call for rear hall. (VALUE)
Settin example:-DTHR 32: 00110010 (= 5000ms, “5 seconds”)
DTL Door time lobby. (VALUE)
Settin example:-DTL 32: 00110010 (= 5000ms, “5 seconds”)
ANS Anti Nuisance EDP. (VALUE)
Set to the number of times a car call is answered without EDP activation before calls are cancelled.
PRK Park/Zone with doors closed/open. Set to 00 – doors closed.
FS Fire service type
Settin example:-FS 00: 00000000 (Australian fire service.)
FS 01: 00000001 (Code 17.1 U.S.A..)
DT Door Time Close Setup. Door Time Cancelin Function
Settin example:-DT 01: 00000001 (Door Timin Cancelin Activated)
BST Brake Switch Time
Settin example:-BST 03: 00000011 (3s)

E E P R O M S E T T I N G S
DTRF Door time HR recall . (VALUE)
Settin example:-DTRF 32: 00110010 (= 5000ms, “5 seconds”)
DTRR Door time HRR recall . (VALUE)
Settin example:-DTRR 32: 00110010 (= 5000ms, “5 seconds”)
HRF Hosp / Hall recall mask.
Settin example:-HRF 40: 01000000
HRR Hosp / Hall recall mask.
Settin example:-HRR 40: 01000000
ALP Auxiliary Levelin Pump. Turns on Auxiliary Levelin Pump, for Up Re Level operation.
Settin example:- ALP FF:11111111 (No Auxiliary pump Re-level.)
ALP 01: 00000001 (Re-levelin with Auxiliary pump)
LCK EEProm Lock (Unlock default 67)
COD Lock code (Unlock default 89)
EQK N/A. Do not adjust

E E P R O M S E T T I N G S
EEProm Definitions (Full description)
ADO - Advanced Door Opening setup
Sets the doors to open whilst travelin into the floor. The doors shall commence openin when the lift is within the
door zone and the MSU or MSD vane pendin direction.
ADO EEPROM Advanced Door Openin .
00: 00000000 “Off – Default”
01: 00000001 ”On”
ALP – Auxiliary Leveling Pump operation setup
For hydraulic lifts, ALP can be set to control SP3 relay to allow Up Re-Levelin usin the Auxiliary Pump motor.
For “SP3” relay to ener ise when performin an Up Re level set ALP to “01” and DRV to “00”, “02” or “05”.
The contacts of SP3 may also be used to stop a secondary pump startin when Up Re-Levelin
If ALP is set to “01”, SP3 shall NOT turn on for inspection.
ALP EEPROM Auxiliary Levelin Pump.
FF: 11111111 “Off”
01: 00000001 “On – operates SP3 for Up Re-Level or inspection”
ANS - Anti Nuisance setup
Set to the number of times a car call is answered without EDP (Electronic Doors Protection) activation before calls
are cancelled. Counter is reset to zero if either EDPF or EDPR is activated. If a hall call is present as well as a car
call, the counter will not increment.
ANS EEPROM Anti Nuisance.
00: 00000000 “Off”
03: 00000011 ”On – operates after 3 car calls of no EDP in a row.”
1e: 00011110 ”On – operates after 30 car calls of no EDP in a row - Default”
BCC - Bottom Car Call setup
BCC EEPROM Bottom car call for the “BOT CALL” button on the circuit board (MASK)
First floor served for this lift only.
The controller shall enter a car call to this settin when the “BOT CALL’ button on the circuit board is pressed.
80: 10000000 (Level 1)
40: 01000000 (Level 2)
20: 00100000 (Level 3)
10: 00010000 (Level 4)
08: 00001000 (Level 5)
BOT - Bottom floor setup
BOT EEPROM Bottom number (VALUE)
Set value to lowest floor served. (01 to 05 valid values)
Lift resets to “BOT” value when BSL limit is activated.

E E P R O M S E T T I N G S
This si nal can be used when a lift in the roup doesn’t o all the way to the bottom.
01: 00000001 (Level 1)
02: 00000010 (Level 2)
03: 00000011 (Level 3)
04: 00000100 (Level 4)
05: 00000101 (Level 5)
BST – Brake Switch Time
For brake switch monitorin .
BST sets the time that the BKSW input must be turned on (to prove the brake has lifted) once the brake lift
command (BRK relay pulled in) has been initiated.
Settin example:
01: 00000001 = 1s
02: 00000010 = 2s
03: 00000011 = 3s
04: 00000100 = 4s
05: 00000101 = 5s
FF: 11111111 = OFF. BKSW not monitored.
Any other settin than 01-05 will turn the brake switch monitorin OFF.
BST is a fatal error. Reset is only via a processor POR.
See also Input - Output, Sin1- BKSW.
CCMF - Car Call Mask (Front doors) setup
CCMF EEPROM Car call mask. Front doors floors allowed. (MASK). For this lift only.
This settin lets you define the floors which the lift serves via the front doors.
Set bits to a “1” car call allowed or a “0” for not allowed.
C0: 11000000 (1c,2c)
E0: 11100000 (1c,2c,3c)
F0: 11110000 (1c,2c,3c,4c)
F8: 11111000 (1c,2c,3c,4c,5c)
FC: 11111100 (1c,2c,3c,4c,5c,6c)
Note: This maskin feature shall not to be used as a means providin of floor security, as it shall disable the car
calls in Fire Service and other modes of operation.
CCMR - Car Call Mask (Rear doors) setup
CCMR EEPROM Car call mask. Rear doors floors allowed. (MASK). For this lift only.
This settin lets you define the floors which the lift serves via the rear doors.
Set bits to a “1” car call allowed or a “0” for not allowed.
C0: 11000000 (1c,2c)
E0: 11100000 (1c,2c,3c)
F0: 11110000 (1c,2c,3c,4c)
F8: 11111000 (1c,2c,3c,4c,5c)
FC: 11111100 (1c,2c,3c,4c,5c,6c)
Note: This maskin feature shall not to be used as a means providin of floor security, as it shall disable the car
calls in Fire Service and other modes of operation.
CNT - CNT Input setup
Enables the followin CNT inputs to be inverted; DCBF, DOBF, EDPF, DCBR, DOBR, EDPR.
CNT EEPROM (MASK)
00: 00000000 No inputs inverted.
01: 00000001 DCBF. Door close front input inverted
02: 00000010 DOBF. Door open front input inverted
04: 00000100 EDPF. Li ht ray front input inverted

E E P R O M S E T T I N G S
08: 00001000 Not used. Default to 0.
10: 00010000 Not used. Default to 0.
20: 00100000 DCBR. Door close rear input inverted
40: 01000000 DOBR. Door open rear input inverted
80: 10000000 EDPR. Li ht ray rear input inverted
e . 42: 01000010 = Both DOBF and DOBR door open button inputs inverted.
COD – Parameter lockout function
To stop unauthorised adjustments to the EEprom parameters the COD and LCK parameters are used.
COD and LCK must both be set to default values to allow other parameters to be adjusted.
See also Eeprom settin LCK
COD default. 89: 10001001
LCK default. 67: 01100111
DCMF - Down Call Mask (Front doors) setup
DCMF EEPROM (MASK) Front doors down hall calls allowed for this lift only.
This settin lets you define the DOWN front doors floors which the lift can serve via DOWN HALL CALLS
Set bits to a “1” hall call allowed or a “0” for not allowed.
40: 01000000 (2d)
60: 01100000 (2d,3d)
70: 01110000 (2d,3d,4d)
78: 01111000 (2d,3d,4d,5d)
7C: 01111100 (2d,3d,4d,5d,6d)
DCMR - Down Call Mask (Rear doors) setup
DCMR EEPROM (MASK) Rear doors down hall calls allowed for this lift only.
This settin lets you define the DOWN rear doors floors which the lift can serve via DOWN HALL CALLS
Set bits to a “1” hall call allowed or a “0” for not allowed.
40: 01000000 (2d)
60: 01100000 (2d,3d)
70: 01110000 (2d,3d,4d)
78: 01111000 (2d,3d,4d,5d)
7C: 01111100 (2d,3d,4d,5d,6d)
DLI - Door Limit Invert setup
DLI is only valid when DLM is set to 00, 03 or 04. See also EEprom settin DLM.
DLI settin is used to invert the DFOF/DFOR and DFCF/DFCR inputs when normally open (n/o) door limit
contacts are used.
DLI EEPROM Door limit invert. (MASK)
DLI: 00 “Limits not inverted.”
DLI: 01 “ Limits inverted.” Any settin other than 00 shall default to inverted limits.
DLI set to - Limits not inverted. Using n/c limits.
Doors fully open – DFCF/DFCR LED will be on. DFOF/DFOR LED will be off
Doors fully closed – DFCF/DFCR LED will be off. DFOF/DFOR LED will be on
Doors midway – DFCF/DFCR LED will be on. DFOF/DFOR LED will be on
DLI set to 1 - Limits inverted. Using n/o limits.
Doors fully open – DFCF/DFCR LED will be off. DFOF/DFOR LED will be on
Doors fully closed – DFCF/DFCR LED will be on. DFOF/DFOR LED will be off

E E P R O M S E T T I N G S
Doors midway – DFCF/DFCR LED will be off. DFOF/DFOR LED will be off
DLM - Door Limit setup
This si nal sets up the door limits inputs.
See also EEprom setting DLI, DFCF/DFCR, DFOF/DFOR.
DLM EEPROM Door limit mask.
Settin example:
DLM 00: 00000000 (Door open and close limits oin to DFOF/DFOR, DFCF/DFCR
inputs which drop DOF/DOR and DCF/DCR relays).
DLM 01: 00000001 N/A
DLM 02: 00000010 (Door cam control) DC relay output used to control Cam operation.
Nb: 1 sec delay from DO pickin up after DC has dropped. (to allow time for cam
to drop and locks to break, to avoid lock “sna in ”).
See also Input - Output, DFCF/R.
DLM 03: 00000011 (As per settin “00” but DOF/DOR and DCF/DCR relays are held up)
DLM 04: 00000100 (As per settin “00” but DCF/DCR relay picks up whilst runnin ).
DRV - Drive type setup
This sets the drive output type. Relay output confi urations are chan ed to suit equipment installed.
Refer to operation section for motion outputs.
DRV…EEPROM…Drive control type.
00: 00000000 “Standard hyd. block valve. 3010EN”
01: 00000001 ”DA DynaHyd valve.”
02: 00000010 “Soft valve. 3010/2CH/S”
03: 00000011 “VF type 1; Keb VF drive, Zetadyn VF drive”
04: 00000100 “1,2 speed AC”
05: 00000101 “GMV 3010/S, Blain EV100”, Maxton, Bucher LRV, EECO
06: 00000110 “VF type 2”
07: 00000111 “VF type 3; ABB VF drive”
DT - Door Time Close setup
This settin allows the door fully open time NOT to be canceled when a car-call or door closed button
(DCBF/DCBR) is pressed.
Settin example:
DT 00: 00000000 (NOT ALLOW pressin a car-call or door close button to cancel door timin ).
DT 01: 00000001 (ALLOW pressin a car-call or door close button to cancel door timin ).
DTCF - Door Time Car call (Front doors) close setup
Sets the amount of time before the front doors close for a car call whilst on normal operation.
DTCF EEPROM Front doors time close. (VALUE)
Set value for front door close time.
The time is set in 100ms increments.
1e: 00011110 = 3000ms, “3 seconds”
32: 00110010 = 5000ms, “5 seconds”
90: 10010000 = 14400ms, “14.4 seconds”
(01 to FF valid values.)
DTCR - Door Time Car call (Rear doors) close setup
Sets the amount of time before the rear doors close for a car call whilst on normal operation.
DTCR EEPROM Rear door time close. (VALUE)
Set value for rear door close time.
The time is set in 100ms increments.
1e: 00011110 = 3000ms, “3 seconds”

E E P R O M S E T T I N G S
32: 00110010 = 5000ms, “5 seconds”
90: 10010000 = 14400ms, “14.4 seconds”
(01 to FF valid values.)
DTHF - Door Time Hall call (Front doors) close setup
Sets the amount of time before the front doors close for a hall call whilst on normal operation.
Lobby time (DTL) overrides this settin when lift is at the lobby floor.
Recommend DTHF is set equal to or reater than DTCF.
DTHF EEPROM Front door hall call time close. (VALUE)
Set value for front door close time.
The time is set in 100ms increments.
1e: 00011110 = 3000ms, “3 seconds”
32: 00110010 = 5000ms, “5 seconds”
90: 10010000 = 14400ms, “14.4 seconds”
(01 to FF valid values.)
DTHR - Door Time Hall call (Rear doors) close setup
Sets the amount of time before the rear doors close for a hall call whilst on normal operation.
Lobby time (DTL) overrides this settin when lift is at the lobby floor.
Recommend DTHR is set equal to or reater than DTCR.
DTHR EEPROM Rear door hall call time close. (VALUE)
Set value for rear door close time.
The time is set in 100ms increments.
1e: 00011110 = 3000ms, “3 seconds”
32: 00110010 = 5000ms, “5 seconds”
90: 10010000 = 14400ms, “14.4 seconds”
(01 to FF valid values.)
DTL - Door Time Lobby call close setup
Sets the amount of time before the doors close after a lobby call is answered when on normal operation.
DTL value overrides DTHF/DTHR value when answerin a hall call at the lobby floor.
Recommend DTL is set equal to or reater than DTHF/DTHR and DTCF/DTCR.
DTL EEPROM Door time close. (VALUE)
Set value for door close time.
The time is set in 100ms increments.
1e: 00011110 = 3000ms, “3 seconds”
32: 00110010 = 5000ms, “5 seconds”
90: 10010000 = 14400ms, “14.4 seconds”
(01 to FF valid values.)
DTRF - Door Time Recall Front setup
Sets the amount of time before the front doors close after returnin to HR or HR1 floor and lift not bein
switched to IND or CFS.
The time is set in 100ms increments.
E . 32: 00110010 = 5000ms, “5 seconds”
See also Inputs-Outputs SIN3
DTRR - Door Time Recall Rear setup
Sets the amount of time before the rear doors close after returnin to HR or HR1 floor and lift not bein switched
to IND or CFS.
The time is set in 100ms increments.
E . 32: 00110010 = 5000ms, “5 seconds”
See also Inputs-Outputs SIN3

E E P R O M S E T T I N G S
EQK
N/A. Do not adjust.
FS - Fire Service type
Australia: Set to 00: 00000000
USA Only. Fire Service Code 17.1. FS EEprom settin must be set to 01: 00000001
HFAF - Hall Fire Alternate (Front doors) floor setup
USA Only. Fire Service Code 17.1. FS EEprom settin must be set to 01
When the desi nated floor smoke alarm is activated, the lift shall return to the HFAF floor if there is a settin floor.
See also Inputs-Outputs HFAF
HFAF…EEPROM Hall Fire Alternate (Front doors) floor. (MASK)
00: 00000000 (No settin floor)
80: 10000000 (Level 1)
40: 01000000 (Level 2)
20: 00100000 (Level 3)
10: 00010000 (Level 4)
08: 00001000 (Level 5)
04: 00000100 (Level 6)
Note: Set either HFAF OR HFAR. DO NOT set both of them.
HFAR - Hall Fire Alternate (Rear doors) floor setup
USA Only. Fire Service Code 17.1. FS EEprom settin must be set to 01
When the desi nated floor smoke alarm is activated, the lift shall return to the HFAR floor if there is a settin
floor.
See also Inputs-Outputs HFAR
HFAR…EEPROM Hall Fire Alternate (Rear doors) floor. (MASK)
00: 00000000 (No settin floor)
80: 10000000 (Level 1)
40: 01000000 (Level 2)
20: 00100000 (Level 3)
10: 00010000 (Level 4)
08: 00001000 (Level 5)
04: 00000100 (Level 6)
Note: Set either HFAF OR HFAR. DO NOT set both of them.
HFSF - Hall Fire Service (Front doors) return floor setup
This sets the hall fire service return front doors floor activated when HFS input is active whilst in normal mode and
HFSF has a settin floor.
HFSF…EEPROM Hall Fire Service (Front doors) floor. (MASK)
00: 00000000 (No settin floor)
80: 10000000 (Level 1)
40: 01000000 (Level 2)
20: 00100000 (Level 3)
10: 00010000 (Level 4)
08: 00001000 (Level 5)
04: 00000100 (Level 6)
Note: Set either HFSF OR HFSR. DO NOT set both of them.
Table of contents
Other ECD Controllers manuals
Popular Controllers manuals by other brands
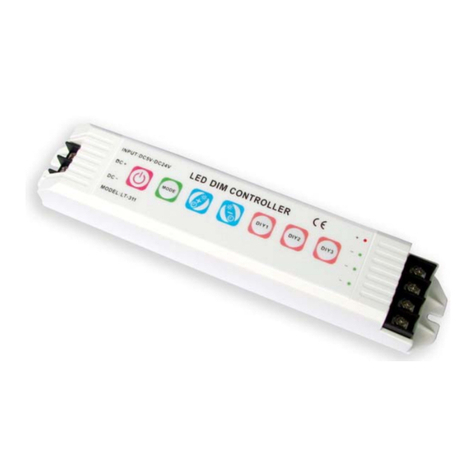
Ltech
Ltech LT-311 User instructions
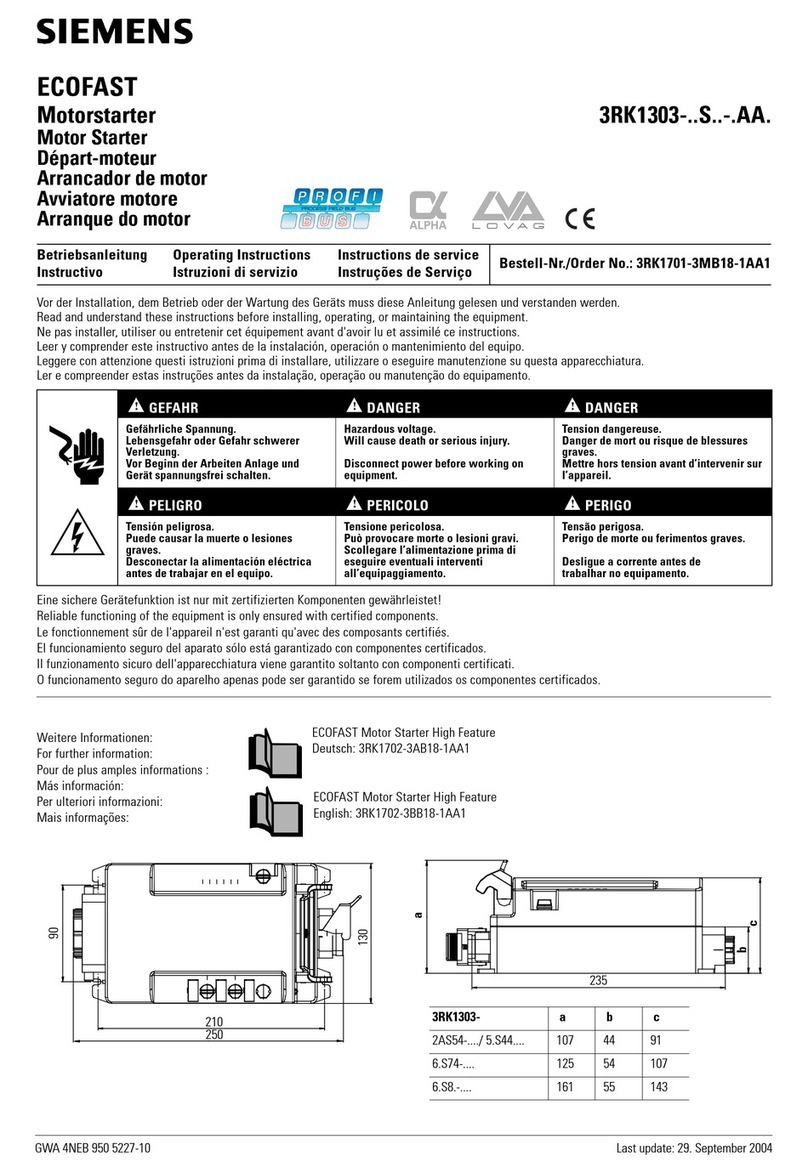
Siemens
Siemens ECOFAST 3RK1303 S AA Series operating instructions
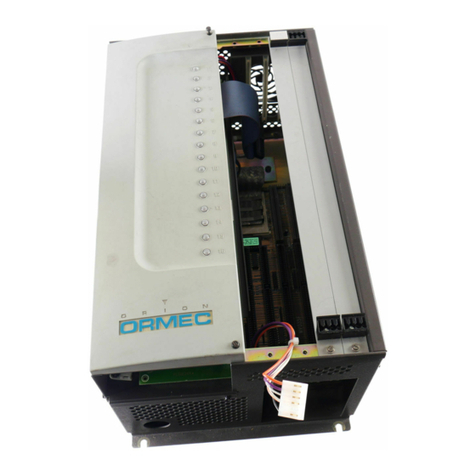
Ormec
Ormec ORION Quick reference guide
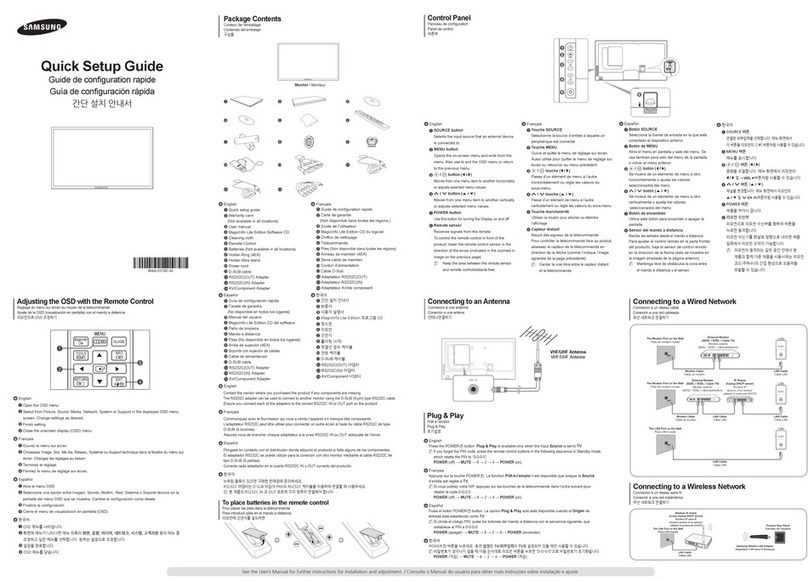
Samsung
Samsung RS232C Quick setup guide
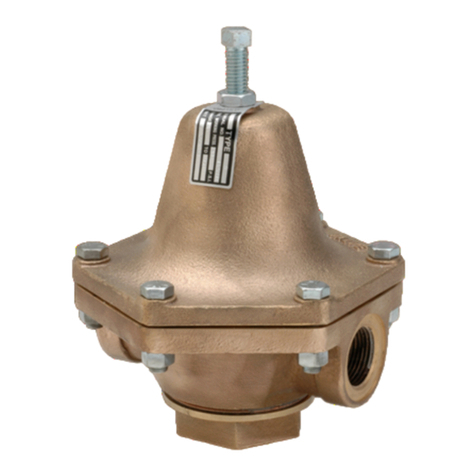
Emerson
Emerson CASH VALVE B Series Installation, operation and maintenance instructions
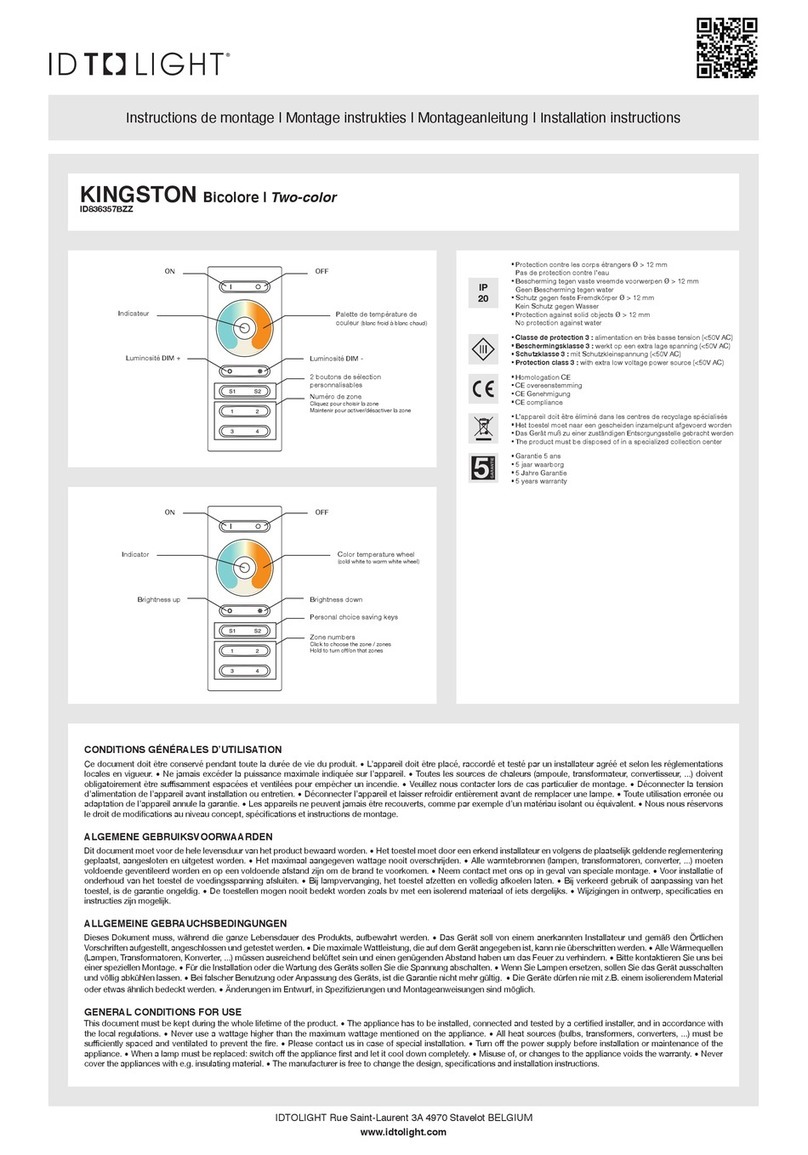
IDTOLIGHT
IDTOLIGHT KINGSTON installation instructions
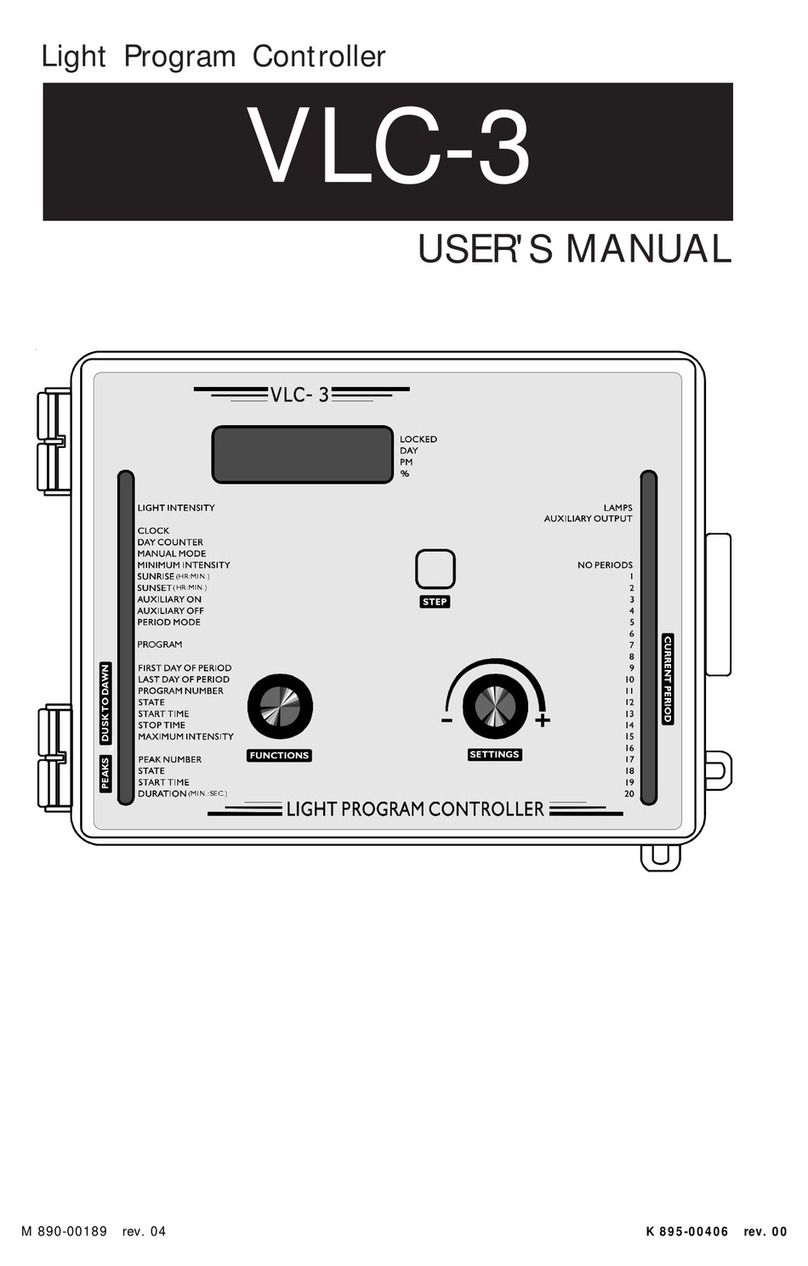
Thevco
Thevco VLC-3 user manual

ATA
ATA OACIS-2XC Installation instruction
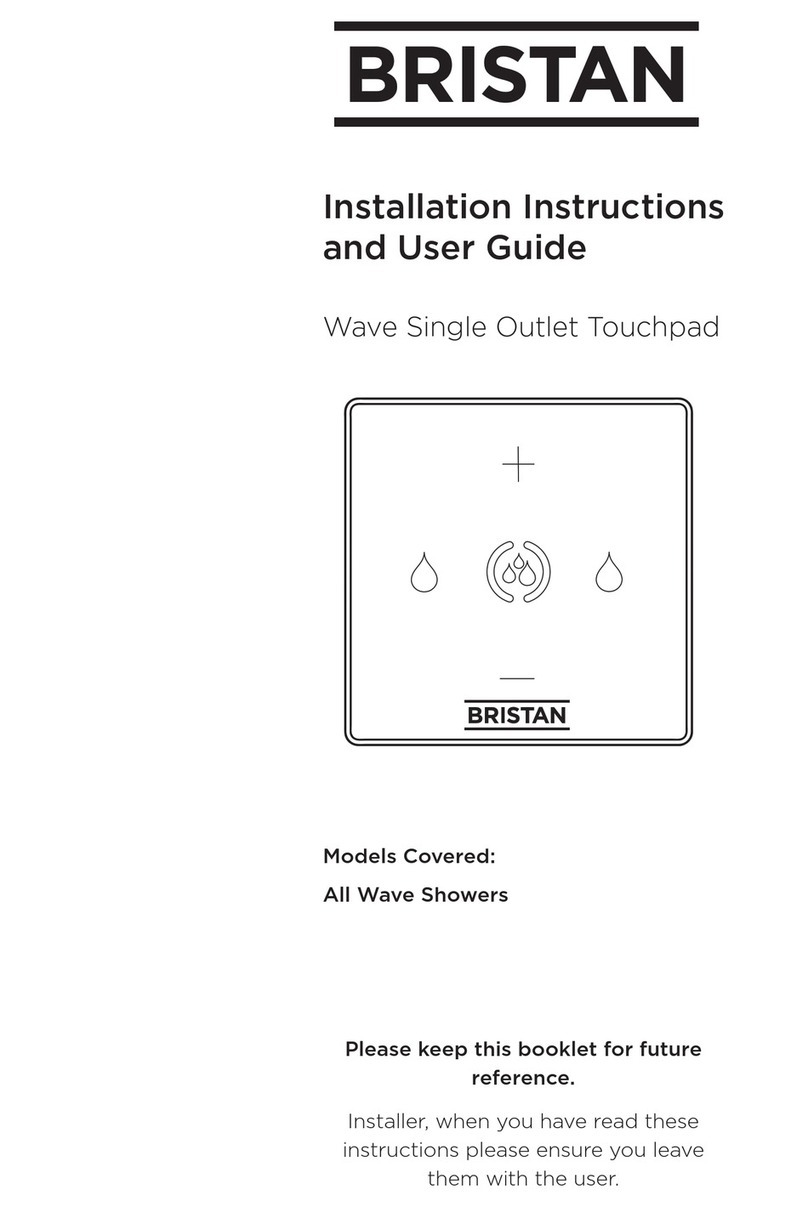
Bristan
Bristan Wave Single Outlet Touchpad Installation instructions and user guide
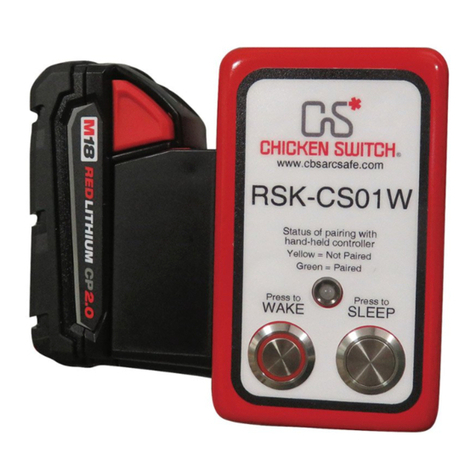
CBS ArcSafe
CBS ArcSafe RSK-CS01W instruction manual
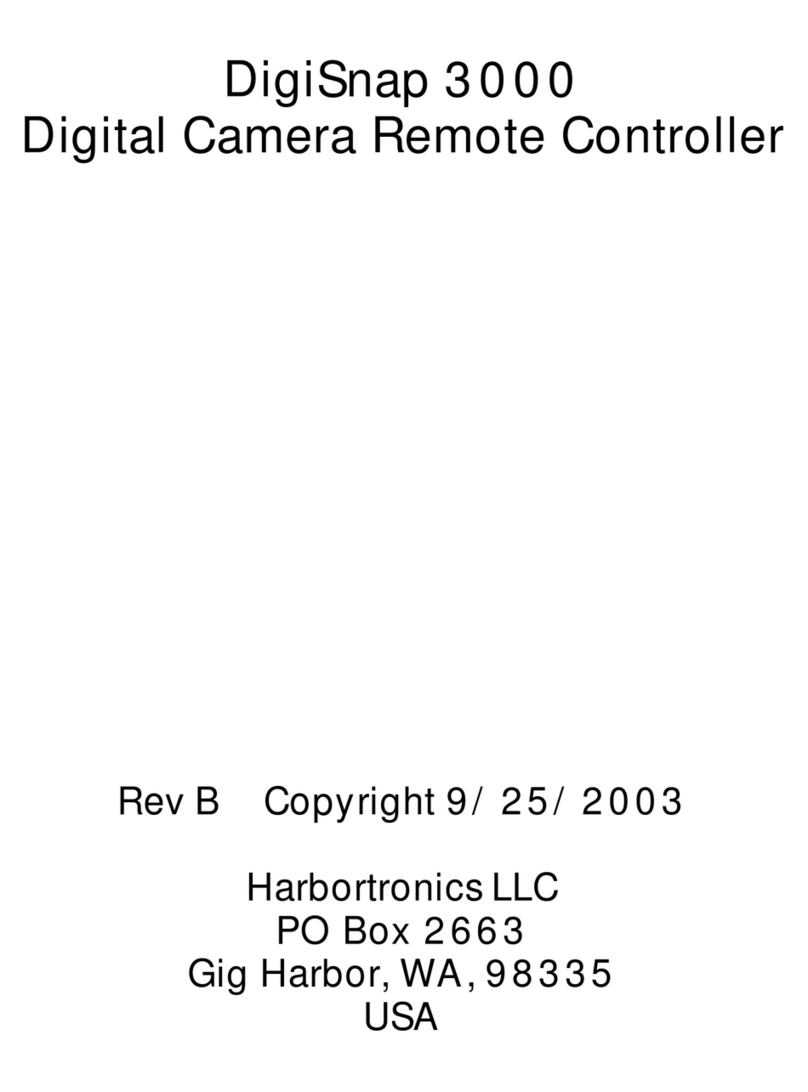
Harbortronics
Harbortronics DigiSnap 3000 user manual

Mitsubishi Electric
Mitsubishi Electric Central Controller G-50A Instruction book