Egger UNIfit! User manual

Installation instructions
for Egger Laminate and
Comfort flooring with
UNIfit! installation system

2
. Obligatory testing and exercise of due care
EGGER Laminate and Comfort flooring are manufactured using the latest technology in modern production plants. Stringent quality
control checks are carried out regularly both during and at the end of the manufacturing process. There may be occasions, however,
when damage to individual boards may occur. It is important therefore, to visually check each flooring board before and during
installation. Damaged flooring boards or those that vary from the norm should not be installed but returned to the supplier to be
replaced.
. Sub-floors
2.1
All sub-floors must be prepared for installation in accordance with regular sub-floor preparation procedures and accepted
tolerances within the flooring industry. When assessing whether EGGER Laminate and Comfort flooring is ready to install, attention
should be paid, in particular, to the points below. In the case of failure to comply, all guarantee and warranty claims will become
void.
Check the moisture level in the sub-floor:
Use a CM device to make sure the following levels are not exceeded:
For cement-based screed ≤ 2CM % – heated screed ≤1.8CM%
For calcium sulphate screeds/calcium sulphate floating screeds ≤0.5CM % – heated screeds ≤0.3CM %
These values apply to screeds without additives. With the use of additives and in case of fast-setting screed, the measurements
and limits specified by the respective manufacturer shall apply. The test material must be obtained from the lower one-third of the
screed. During this process, the thickness of the screed must be measured and documented.
Check if the sub-floor is level:
The evenness test is based on common standards and takes place by placing a yardstick/ straight-edge on the high points of the
surface and determining the gauge at the deepest location in relation to the bearing surfaces (measuring point intervals). Use a
max. 2mm gauge (vertical deviation) at 100 cm intervals. Larger deviations should be addressed by suitable measures (e.g. with
self-levelling compounds).
Check the load-bearing capacity of the sub-floor:
The sub-floor must be a sealed, self-supporting layer.
Check if the sub-floor is clean:
The sub-floor must be vacuum cleaned.
Check atmospheric conditions:
The following conditions should be met before, during and after installation:
An air temperature of at least 18° C
A floor surface temperature of at least 15° C
A relative air humidity of between 40% and 70%.
Obligatory testing and exercise of due care/Sub-floors

3
2.2
All sub-floors, which are deemed to be ready for installation and meet the requirements previously listed, are suitable for installing
EGGER Laminate and Comfort flooring as a floating installation. This includes:
All types of screed including hot water-heated screed
Chipboard constructions
Fibreboards
Existing floor coatings such as PVC, linoleum, natural stone slabs and ceramic tiles.
Unsuitable sub-floors:
EGGER Laminate and Comfort flooring must never be installed on textile floor coverings (e.g. carpet) or sub-floors that are not ready
for installation. In the case of failure to comply, all guarantee and warranty claims will become void.
Sub-floors of limited suitability include:
Electrically operated underfloor heating (controlling the surface temperature).
Electrical underfloor heating systems are classified as sub-floors with limited suitability. This is because a range of film-based,
electrical heating systems are able to generate surface temperatures that significantly exceed 28°C. EGGER approves the use of
an electrically operated underfloor heating system if it can be controlled digitally and the surface temperature can never exceed
28° C. The technical approval must have been granted by the manufacturer of the heating system for EGGER Laminate and Comfort
flooring.
Screed
When installing EGGER Laminate and Comfort flooring as a floating installation on screeds, it should be noted that rising damp must
be expected. Consequently, all types of screed (with the exception of mastic asphalt) require, prior to the installation of a system-
specific insulating layer (see section: Attention! underlay materials), a moisture protection film, SD value ≥ 75m, to be installed over
the whole area in a trough shape as a moisture barrier. When professionally installed, the strips of the moisture protection film must
overlap by 5-20cm at the joints depending on the version.
Screeds with hot water floor heating
When preparing a heated flooring design, all those involved (builder, architect, specialist heating planner, heating engineer,
installer, floor covering manufacturer) must work together in a coordinated manner. All surface-heated flooring requires appropriate
planning and coordination of the heating system and screed in order to ensure maximum long-term performance without causing
any damage. Alongside the usual checks on the installation sub-floor, the underfloor heating/cooling function must be checked
(functional heating/cooling). This evidence of the screed construction being properly heated up and cooled down must be provided
each season and be documented.
When heating the load and heat distribution layer, a distinction is made between functional heating and floor curing heating.
Functional heating is the heating engineer’s evidence of preparing a job free of defects and is used to review the proper
functioning of the heating floor structure.
Floor curing heating is the expelling of the residual moisture in the screed until installation suitability is reached.
Attention! Functional heating does not guarantee that the screed has reached the residual moisture required for installation
suitability. Accordingly, floor curing heating is necessary as a rule.
Attention! The surface temperature of a heated floor structure may not exceed 28°C (83°F). EGGER Laminate and Comfort flooring is
generally laid as a “floating” installation. On mineral sub-floors it is essential to install a moisture protection film, SD value ≥ 75m,
over the whole area in a trough shape as a moisture barrier before the insulating underlay. When installing laminate flooring as a
floating installation, attention should be paid to the heat conductivity values of the laminate flooring and the insulating underlay.
The total of the heat conductivity values for all components must be ≤ 0.15 m²K/W according to the CE requirement. When using
insulating underlays that are not from the EGGER range of accessories, any guarantee is rejected with regards to compliance with the
effective maximum permitted heat conductivity of the overall structure for a floating installation on heated screeds. When installing
EGGER Laminate flooring with Silenzio underlay laminated to the back and Comfort flooring, no other insulating underlay must be
installed.
Sub-floors

4
Natural stone and ceramic tiles
Possible residual moisture in the sub-floor may rise to the surface and consequently, before installing the system-specific insulating
underlay (see section: Attention! underlay materials), a moisture protection film, SD value ≥ 75m, must be installed over the whole
area in a trough shape as a moisture barrier. When installing EGGER Laminate flooring with Silenzio underlay laminated to the back
and Comfort flooring, no other insulating underlay must be installed.
Woodchip and fibreboard
To improve impact sound, before installing laminate flooring a system-specific insulating underlay (see section: Attention! Underlay
materials) should be installed. A moisture protection film (vapour barrier) should not be fitted. EGGER Laminate flooring with
Silenzio underlay laminated to the back and Comfort flooring can be directly installed on wooden boards.
Wooden boards
Any loose boards should be properly screwed down. To improve impact sound, before installing laminate flooring a system-specific
insulating underlay (see section: Attention! Underlay materials) should be installed. A moisture protection film (vapour barrier)
should not be fitted. EGGER Laminate flooring with Silenzio underlay laminated to the back and Comfort flooring can be directly
installed on floorboards. Please note that the laminate flooring and Comfort flooring elements are installed at right angles to the
floorboards.
Elastic flooring surfaces (PVC, linoleum, vinyl)
The use of flexible floor coverings meets the damp-proofing requirements and thus eradicates the need for a moisture protection
film. To improve impact sound, before installing laminate flooring, a system-specific insulating underlay should be installed. EGGER
Laminate flooring with Silenzio underlay laminated to the back and Comfort flooring, can be directly installed on the elastic flooring.
(see section: Attention! Underlay materials)
Wet rooms/ wet areas
Attention! EGGER Laminate and Comfort flooring may not be installed in wet and damp rooms such as bathrooms, saunas or similar
spaces. In the case of failure to comply, all guarantee and warranty claims will become void.
Attention! Underlay materials
On mineral sub-floors, a moisture protection film, SD value ≥ 75m, must be installed over the whole area in a trough shape.
The exception to this is when using EGGER Silenzio Duo (2 in 1 insulating underlay with integrated moisture protection) or a
comparable 2 in 1 underlay. In these cases, a separate moisture protection film is not necessary.
A system-specific EGGER Silenzio underlay must be used under EGGER laminate flooring. Alternative underlayer boards are
available at www.egger.com.
The exception to this is when using EGGER laminate flooring with Silenzio underlay laminated to the back and Comfort
flooring. No other insulating underlay must be used in this case.
Sub-floors

5
. Before the installation
Conditioning the boards
Before starting the installation, the packs of laminate and Comfort flooring should be stored/acclimatised in the room where they
are going to be installed or in a room with an equivalent climate. Acclimatisation takes place in the following conditions:
The flooring is in its packaging
It is stored/acclimatised for a period of at least 48 hours
It is laid flat with a minimum of 50cm distance from all walls
The room temperature is at least 18°C
The surface temperature of the floor is at least 15° C
The relative atmospheric humidity is between 40% and 70%.
Direction of installation
Laminate and Comfort flooring looks best when the panels are installed parallel to the light coming in through the windows.
However, there are binding requirements for the direction of installation for sub-floors made of board flooring, or strip
parquet/ wooden floors on ships. In those cases, installation must be done at right angles to the boarding or the direction of the
strip parquet/ wooden floor.
Planning the first row
First, the room must be measured to determine whether the width of the first row should be reduced. This is always necessary if the
last row being installed works out to be narrower than 5cm.
Attention! The flooring elements (floor boards) must be cut lengthways from the tongue side (red inlay).
Planning expansion gaps
EGGER Laminate and Comfort flooring are subject – like all organic materials – to a certain movement behaviour
(shrinking/swelling) due to the changing indoor climatic conditions. Movement of the finished, installed floor is not affected if
allowance is made with sufficiently dimensioned expansion joints to all fixed objects.
Expansion gaps 8 to 10 mm wide should be left around all fixed objects such as walls, door frames, pipes, pillars, stairs etc.
Planning movement profiles
Due to the movement behaviour of laminate and Comfort flooring, movement profiles must always be installed in the following
applications and areas:
Door thresholds
Passageways
Angled areas
Room lengths and/ or widths of more than 10m
Before the installation

6
. Installation
Check the flooring boards for visible damage/ defects. Determine which is the tongue and which is the groove (Figure 1/Figure 2).
Start installing the first two rows in the left-hand corner of the room, ensuring that both tongue sides of the first board face the
wall and both groove sides face the fitter (Figure 1/Figure 2).
The boards in the first two rows can be installed simultaneously, which means constantly alternating them whilst complying with the
minimum offset of the end joints of 200mm (Attention! In the case of Long format boards, a minimum offset of 500mm applies, as
shown and described below.
Wall8 - 10 mm
8 - 10 mm
Board 1 = Lay in a left-hand corner of the room
Board 2 = Longitudinal angling of this shortened board. To do so, place the longitudinal tongue diagonally from above into the
longitudinal groove of Board 1 and lower Board 2 until it is lying flat. (see Figure 3)
Board 3 = Longitudinal angling & pressing in the short side. To begin with, return the longitudinal tongue at a slight angle from
above into the longitudinal groove of Board 1. Now push Board 3 in this slanted position towards the front of Board
2, until the short sides of both elements push against each other and fits perfectly. Once again lock the longitudinal
connection by lowering and at the same time the frontal connection by pushing until you can feel them snap into place.
(see Figure 4)
Board 4 = Longitudinal angling on the opposite side and pressing in the short side as before. Place the longitudinal groove at a
slight angle under the longitudinal tongue of Board 3. Push Board 4 in this slanted position towards the front of Board
1, until the short sides of both boards push against each other and fit perfectly. Now once again lock the longitudinal
connection by lowering and at the same time the frontal connection by pushing until you can feel them snap into place.
(see Figure 5)
Board 5 = Longitudinal angling and pressing on the short side (see Board 3).
Board 6 = Longitudinal angling and pressing on the short side (see Board 4)
Board 7 = Longitudinal angling and pressing on the short side (see Board 3)
Board 8 = Longitudinal angling and pressing on the short side (see Board 4).
Install all remaining boards for the first and the second row as described above, and cut the last boards to fit (Figure 6)
Finally, orientate the first two rows to face the walls, as required, check the wall distance (8-10mm) from the wall and position the
spacers. (Figure 7 to Figure 10)
a
b
c
a
b
c
a
b
c
Installation

7
Installation
Attention! Make sure that the short ends are staggered at least 200mm (8”). Attention! When installing Long format floor boards,
the short ends must be staggered by at least 500mm.
In the case of products supplied with a bevel and/ or with a special pattern (e.g. tiles decor), ensure the offset is even according
to the bevel and/ or pattern.
You install the first board of the third row by inserting the tongue on the long side into the groove on the long side of the second
row diagonally from above. Then, lower the board until it is lying flat. To install the second board of the third row, once again tilt
the long edge with the tongue down and slide it into the groove on the long side of the second row. With the board in this tilted
position, now slide it towards the end of the first board in the third row until the frontal connection mechanisms are above each
other so they fit perfectly. Once again, lock the long edge by lowering the board and the front by pushing until you can feel it lock.
Install all remaining boards for the third row as described above, and cut the last board to fit.
All the following rows can be started with the leftover piece of the previous row if this is at least 200 mm long or 500 mm for Long
format floor boards.
You can continue to install board after board now.
In order to prepare the last row of boards for installation, take the board and place it exactly on top of the row before last. By means
of a residual board (board width), it is possible to transfer the wall structures to the board within a pre-chosen distance.
Class , and Commercial Applications
GLUE
GLUE
Commercial areas are exposed to various levels of moisture and because of this, additional sealing with PVAC glue (D3), is
mandatory in such applications. The sealing glue should be applied on the long and short side of the tongue of the board being
installed so that it can leak out along the full length of the connection at the top when the boards are joined together. Make sure
that there is no gap in the flooring joints under the glue which has oozed out. Excess sealing glue is easy to remove from the surface
immediately or after a short drying period.
(Attention! Due to the profile geometry, a proportionate amount of glue is to be applied, particularly on the short side.)
Built-in kitchens/ built-in cabinets
It is recommended to assemble built-in kitchens and cabinets before installation and to install the laminate or Comfort flooring to
just behind the plinth panel.

8
Installation
Pipes
Measure the position of the pipes and mark it on the panel (allow for edge joint).
Drill at least 16 mm more than the diameter of the pipe.
Saw the holes at a 45° angle.
Fit and glue the sawn piece.
Door frames
a b c
= + 16 mm
a
b
c
If there are wooden door frames, it is recommended to shorten these by the installation height (flooring plus underlay materials)
in consultation with the customer. (Figure 1a)
Then install laminate or Comfort flooring under the frame with an appropriate expansion joint. In case the installation takes you to
a door frame, the respective board can be angled longitudinally and lowered. Subsequently, the element placed flat on the floor
is pushed under the door frame and the frontal connection is locked through horizontal knocking with a hammer and tapping
block. (Figure 1b + 1c)
On door frames that cannot be shortened, e.g. made of metal, the fitted expansion joint must be sealed or covered with an elastic
jointing material or suitable end profiles. (Figure 2)
Flooring profiles and skirting boards
After finishing the professional installation of the laminate or Comfort flooring, both the necessary flooring profiles and skirting
boards are fitted. Simple assembly instructions are enclosed with all the accessories.
Attention! With most types of profile, it is necessary to fit the base (sub-profile) to take the cover profile before installing laminate
and Comfort flooring.
Removal/Dismantling of Boards
To replace boards already installed without damaging them, you must firstly loosen the entire row on the long side from the locking
mechanism by bending it and then pushing the boards parallel against each other on the short side whilst they are flat on the
ground. Proceed with due care in order to avoid damaging the tongue and groove.
ab c

9
Cleaning and maintenance
. Cleaning and maintenance
Entrance areas are to be equipped with a reasonably sized dirt-trapping zone / mat.
For commercial applications where the flooring area directly adjoins the outdoor area, a recessed and reasonably sized dirt-
trapping zone is to be fitted in the flooring design.
Attach felt pads to the feet of furniture, including chairs and tables. Clean these regularly, check for proper functionality, and
replace if required.
Lift furniture when moving, rather than pushing or dragging.
On office chairs and all other furnishings on rollers, soft castors (type W) are to be used. The office chair and furniture rollers are
to be cleaned at regular intervals, tested for functionality and replaced if necessary.
Remove any moisture/ wetness resting on the laminate and Comfort flooring immediately.
Steam cleaners should not be used, the exception being on Aqua+Laminate Flooring.
Only clean laminate and Comfort flooring with a damp cloth.
Never use scouring or abrasive materials on laminate and Comfort flooring.
Do not use cleaning products that may leave a residue. We recommend our system-related flooring cleaner, Clean-it, from EGGER.
Waxing and/or polishing is neither necessary nor permitted.
Subsequent sealing of the surface on laminate and Comfort flooring is not necessary and must not be done.
Use the hard floor nozzle (brush accessory) when vacuum cleaning.
If, despite its robustness, a flooring board gets damaged, then minor damage can be rectified with the system-specific repair paste,
EGGER Decor Mix & Fill. If the damage is more serious, a professional installer will be able to replace an entire panel. Separate
instructions are available upon request.
In case of special installations, such as on stairs, or if you have any other questions, please contact your dealer.

www.egger.com
EGGER Holzwerkstoffe Wismar
GmbH & Co. KG
Am Haffeld 1
23970 Wismar
Germany
T +49 3841 301-0
F+49 3841 301-20222
flooring@egger.com
EGGER Drevprodukt Gagarin
Ezhvinsky proezd, 1
215010 Gagarin
Oblast Smolensk
Russia
T +7 48135 79-300
F+7 48135 79-311
info-ru@egger.com
EN_EGGER_flo_installation_instruction_UNI fit!_04/2018_SCG
Subject to technical modifications and printing errors.
Advice, service and more:
Table of contents
Other Egger Other manuals
Popular Other manuals by other brands

Redi-Chek
Redi-Chek ET-808C instruction manual

Blue Ox
Blue Ox BX2164 installation instructions
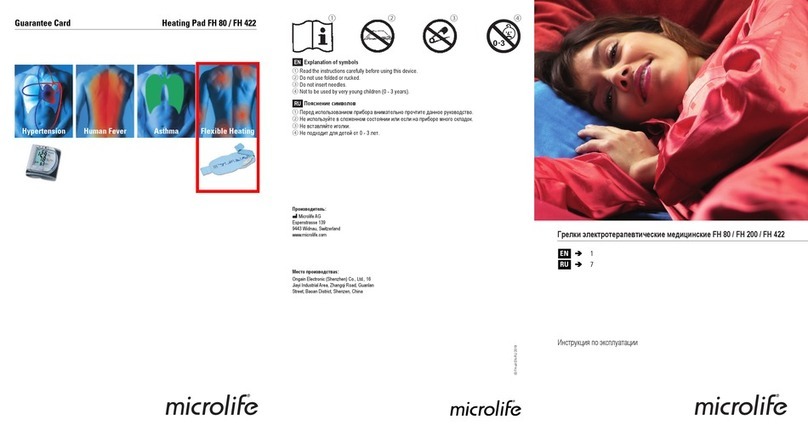
Microlife
Microlife FH 80 manual
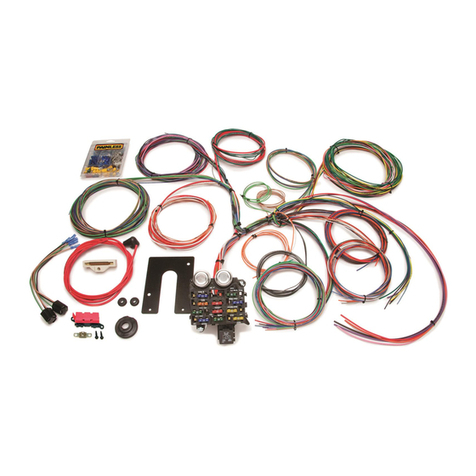
Painless Performance Products
Painless Performance Products 10106 installation instructions
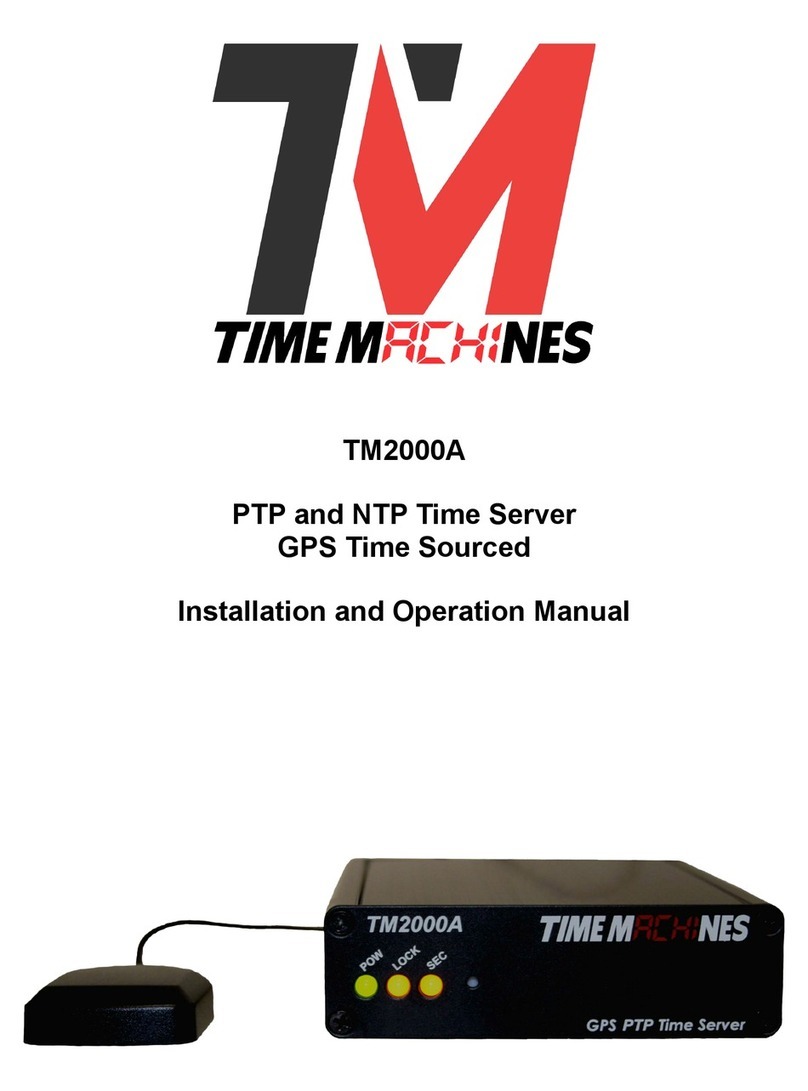
Time Machines
Time Machines TM2000A Installation and operation manual
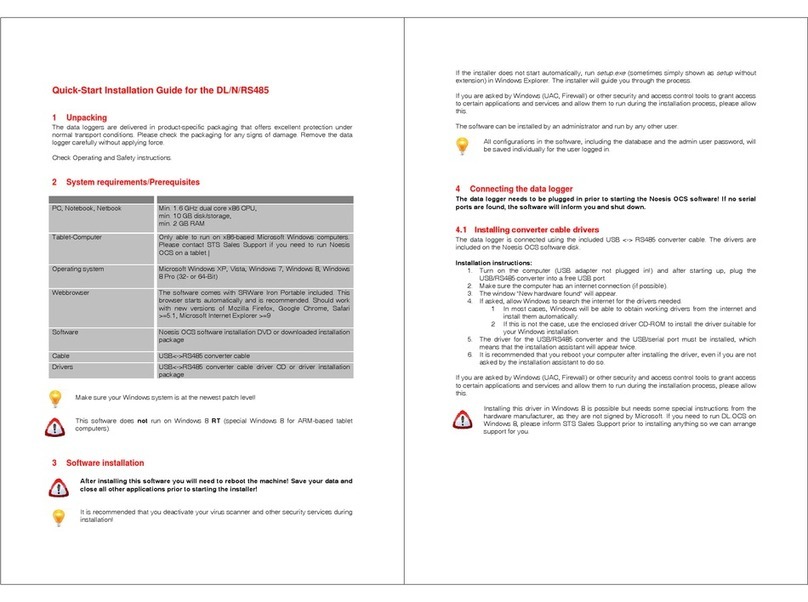
STS
STS DL/N/RS485 Quick start installation guide