Electro-Craft MAX-430 User manual

MAX-430
PWM Servo Drive
Instruction Manual
Rockwell Automation/Electro-Craft
6950 Washington Avenue South
Eden Prairie, MN 55344
THE RIGHT COMPANY. THE RIGHT SOLUTION.
Click to Go Back to OEM Menu

P/N 0013-1025-001 Rev F
© 1998 Rockwell International Corporation. All rights reserved.
Printed in the United States of America.
Information contained in this manual is subject to change without notice.
Electro-Craft is a trademark of Rockwell Automation.
UL and cUL are registered trademarks of Underwriters Laboratories.
Other trademarks cited are the property of their respective owner.
Intro
!
WARNING Only qualified electrical personnel familiar with the construction and operation
of this equipment and the hazards involved should install, adjust, operate or
service thisequipment. Readand understandthis manual and other applicable
manuals in their entirety before proceeding. Failure to observe this precaution
could result in severe bodily injury or loss of life.
Intro
!
WARNING The user must provide an external, hardwired emergency stop circuit outside
the controller circuitry. This circuit must disable the system in case of improper
operation. Uncontrolled machine operation may result if this procedure is not
followed. Failure to observe this precaution could result in severe bodily injury.

Instruction Manual
Contents
IntroContents
Contents Intro-3
List of Figures Intro-5
List of Tables Intro-7
Pictorial Index Intro-8
CHAPTER 1 Introduction
HowtoUseThisManual......................................1-1
Safety.................................................1-1
IntroductiontotheMAX-430....................................1-1
FunctionalDescription .......................................1-2
CHAPTER 2 Installation
Installation..............................................
2-1
InternalAdjustments ........................................2-1
Jumpers...............................................2-1
Mounting...............................................2-3
TransformerSizing..........................................2-3
ACandDCPowerConnections..................................2-4
AuxiliaryLogicSupplyPower...................................2-8
ConnectingTheMotor........................................2-8
LogicInputsandOutputs......................................2-8
ConnectingInputs......................................... 2-10
VelocityCommandSignal(VCS)............................... 2-10
AuxiliaryInput ......................................... 2-10
Inhibit(INH)........................................... 2-10
ForwardandReverseAmplifierClamps(FAC,RAC) ................... 2-10
InternalConnections(FAC,RACandINH)........................... 2-11
VelocityClamp(TorqueMode)................................ 2-12
External Current Limit (Optional). . . . . . . . . . . . . . . . . . . . . . . . . . . . . . . 2-12
ConnectingOutputs........................................ 2-13
SystemStatusOutput(SSO).................................. 2-13
MotorCurrentOutput(MCO0-10V) .............................. 2-15
Motor Current Output (MCO ±10V) . . . . . . . . . . . . . . . . . . . . . . . . . . . . . 2-15
MotorVelocityOutput(MVO)................................. 2-15
±15VDCPowerOutput.................................... 2-15
TypicalWiringExamples..................................... 2-16

Intro-4 Contents
P/N 0013-1025-001 Rev F
CHAPTER 3 Applying Power for the First Time
SetupChecklist........................................... 3-1
Start-up Procedure with Tach (Velocity Mode) . . . . . . . . . . . . . . . . . . . . . . . . 3-2
InternalCurrentLimit(ILIM)................................... 3-3
BalanceControl(BAL)....................................... 3-3
ServoCompensation(COMP)................................... 3-3
TachGain(TACH)......................................... 3-3
VCSGain(VCS)........................................... 3-4
VCSSignalandScaling(VCS)................................... 3-4
VCSSignalInput......................................... 3-4
VCSGainSetting......................................... 3-4
VCSSignalScaling........................................ 3-4
Start-upProcedurewithoutTach(TorqueMode) ....................... 3-6
TorqueModeOperation...................................... 3-7
CHAPTER 4 Diagnostics/Troubleshooting
MonitoringOutputs ........................................ 4-1
Motor Current Output (MCO 0-10V) . . . . . . . . . . . . . . . . . . . . . . . . . . . . . 4-1
Motor Current Output (MCO ±10V) . . . . . . . . . . . . . . . . . . . . . . . . . . . . . . 4-1
MotorVelocityOutput(MVO)................................. 4-1
ScheduledMaintenance...................................... 4-2
CheckingandReplacingtheFuses................................ 4-2
MalfunctionDiagnosis....................................... 4-3
LightEmittingDiodes....................................... 4-4
Power LED (Green) . . . . . . . . . . . . . . . . . . . . . . . . . . . . . . . . . . . . . . . 4-4
TestOutputs ............................................ 4-5
CHAPTER 5 Specifications
Inrush Currents . . . . . . . . . . . . . . . . . . . . . . . . . . . . . . . . . . . . . . . . . . . 5-2
CHAPTER 6 Component Ordering Information
CHAPTER 7 Reference Drawings
APPENDIX A Differences from the MAX-400
MAX-400toMAX-430Replacements............................... A-1
PowerConnector......................................... A-1
Foldback.............................................. A-1
Motor Current Output. . . . . . . . . . . . . . . . . . . . . . . . . . . . . . . . . . . . . . A-1
Multi-AxisPowerWiring.................................... A-1
Index of Topics Help-1
Documentation Improvement Form Help-3
Product Support Help-5

Instruction Manual
List of Figures
IntroList of Figures PictorialIndex...........................................Intro-8
CHAPTER 1 Introduction
SystemFunctionalDiagram...................................1-2
CHAPTER 2 Installation
Jumper Locations.........................................2-2
115 VACInput Power/MotorWiring.............................2-4
230 VACInput Power/MotorWiring.............................2-5
+(30-120)VDCInput Power/MotorWiring......................... 2-5
Multiple Axis Power Wiring (Individual Secondaries)
(Recommended Method)...................................2-6
Multiple Axis Power Wiring (One Secondary)
(AlternativeMethod).....................................2-7
ExternalInterfaceConnections.................................2-9
Sourcing Opto’s with Internal Power (P8A: pins 1-2 and P8:pins 1-2)..........2-11
Sourcing Opto’s with External Power (P8A: pins 2-3 and P8: pins 2-3)..........2-11
Sinking Opto’s with Internal Power (P8A: pins 2-3 andP8: pins 1-2)...........2-11
Sinking Opto’s with External Power (P8A: pins 2-3 and P8:pins 2-3)...........2-12
SSO-OpenCollectorSourcing.................................2-13
SSO-OpenCollectorSinking..................................2-13
SSO-NormallyClosedRelaywithInternalPower.....................2-14
SSO - Normally Closed Relay using External Power
withFAULTCondition=LogicLevel“1”.........................2-14
SSO - Normally Closed Relay using External Power
withDriveREADY=LogicLevel“1”............................2-14
IsolatedLogicInterfaceConnections.............................2-16
LimitSwitchWiring.......................................2-16
CWRemoteVCSControl....................................2-17
CW/CCWRemoteVCSControl................................2-17
CCWRemoteVCSControl...................................2-17
TorqueControl..........................................2-18
Master SlaveWiring.......................................2-18
CHAPTER 3 ApplyingPower for theFirst Time
SystemResponsetoaStepVCSInput.............................3-5
VCSTorqueMode ScalingExamples.............................3-7
CHAPTER 4 Diagnostics/Troubleshooting
LocationofFuses.........................................4-2
Excessive Current Timeout Diagram.............................4-4
TestOutputs...........................................4-5
CHAPTER 5 Specifications
Inrush Current Measurements.................................5-2

Intro-6 List of Figures
P/N 0013-1025-001 Rev F
CHAPTER 6 Component Ordering Information
0.625 kVA Transformer, Part Number 9077-0640 . . . . . . . . . . . . . . . . . . . . . . . 6-2
1.8kVATransformer,PartNumber9077-0639........................ 6-3
3.6kVATransformer,PartNumber9077-0638........................ 6-4
3.6kVATransformer,PartNumber9077-0637........................ 6-5
CHAPTER 7 Reference Drawings
Outline,MountingandAdjustmentsDiagram........................ 7-1
SimplifiedCircuitDiagram................................... 7-2
APPENDIX A Differences from the MAX-400

Instruction Manual
List of Tables
IntroList of Tables
CHAPTER 1 Introduction
CHAPTER 2 Installation
Inputs and Outputs with Jumpers P6 through P9A .........................2-1
CHAPTER 3 Applying Power for the First Time
CHAPTER 4 Diagnostics/Troubleshooting
MAX-430 System Problem Symptoms and Possible Causes ....................4-3
LED Fault Conditions ...........................................4-4
CHAPTER 5 Specifications
Performance Specifications ........................................5-1
Electrical Specifications ..........................................5-1
Input Power Requirements ........................................5-1
Physical Specifications...........................................5-1
CHAPTER 6 Component Ordering Information
Ordering PWM Servo Drive .......................................6-1
Ordering Transformers ..........................................6-1
CHAPTER 7 Reference Drawings
Listing of Drawings ............................................7-1
APPENDIX A Differences from the MAX-400

Intro-8 Pictorial Index
P/N 0013-1025-001 Rev F
IntroPictorial Index
Intro
Pictorial Index
page 4-4
page 4-5
page 2-4,
page 2-8
page 2-4,
page 2-8
page 2-4,
page 2-8
page 2-4,
page 2-8
page 3-3
page 4-5
page 2-10
page 2-10
page 2-10
page 2-13
page 2-13
page 2-12
page 2-10
page 2-10
page 2-10
page 2-12
page 2-12
page 2-15
page 2-15
page 2-15
page 2-15
page 2-15
page 2-12

Instruction Manual
CHAPTER 1: Introduction
How to Use This Manual
This manual describes the function, theory and application of the Electro-Craft MAX-430 servo
drivesandprovidesinformation related totheirperformance,operation andmaintenance. This
manual is addressed to the customerengineer or technician involved inthe installation ormain-
tenance of the MAX-430 drive. It is assumed that the reader is trained in the use of mechanical
and electrical test equipment and is familiar with basic servo system maintenance procedures.
Safety It is necessary to wait at least 60 seconds before working on the drive when main power has
been turned off and auxiliary power is not being supplied to the drive. When there is 24 volts
being supplied to the auxiliary power input, main power will dissipate immediately on power
down. However, if there is no power being supplied to the auxiliary power input, main power
must dissipate through a resistor, and it will take at least 60 seconds before the voltage is at a
safe level.
Introduction to the MAX-430
The“SystemFunctionalDiagram”oftheElectro-CraftMAX-430driveisshownonthefollowing
page. MAX-430 series drives are designed to drive permanent magnet, brushtype, DC servo
motors. The drives and motors are intended for use in a broad range of industrial servo appli-
cations, including machine tool and robotic applications, and are used in torque, velocity and
positiontypeservosystems.Eachdriveisaself-containedunit,readyformechanicalinstallation
and electrical interconnections to the AC power transformer, motor-tachometer, and controller.
TIP If replacinga MAX-400 with a MAX-430, refer to Appendix A, “Differences from
the MAX-400” for a list of changes to be aware of.

1-2 Introduction
P/N 0013-1025-001 Rev F
Functional Description
The Electro-Craft MAX-430 is a controllable power source for brushtype, DC servo motors.
Usually configured as a controlled velocity system, the drive interfaces with a controller which
provides an analog voltage signal proportional to the desired motor velocity. The MAX-430
drive can also operate in torque mode (or current mode), such that a controller provides an
analog voltage signal proportional to the desiredmotor torque.Refer to the “System Functional
Diagram” shown below. The MAX-430 drivecontains circuitry for protection of both motor and
drive from effects of various overload and short circuit conditions. The command signal to the
power drive can be monitored at the ICMD output. The MAX-430 is a 16 kHz pulse-width
modulation (PWM), switching type drive that reduces system power losses. Motor speed is
precisely controlled down to a maximum torque, low velocity condition.
Intro
FIGURE 1.1 System Functional Diagram

Instruction Manual
CHAPTER 2: Installation
Installation All wiring and mechanical instructions described in this section should be made with reference
to the “Simplified Circuit Diagram” on page 7-2 and the “Outline, Mounting and Adjustments
Diagram” on page 7-1. Also see “Input Power/Motor Wiring” diagrams starting on page 2-4.
Internal Adjustments
Jumpers
There are jumpers onthe velocity regulatorboard ofthe MAX-430 to indicate desired operation
of the Forward and Reverse Amplifier Clamps and the System Status Output (FAC, RAC, and
SSO). There are also jumpers used to indicate desired operation of the optically isolated tran-
sistors on FAC, RAC andinhibit (INH) inputs. Refer toTable 2.1 for operation of theinputs and
outputs with jumpers P6 through P9A in the different positions. Also see on “Forward and
Reverse Amplifier Clamps (FAC, RAC)” on page 2-10.
Intro
!
CAUTION If replacinga MAX-400 with a MAX-430, refer to Appendix A, “Differences from
the MAX-400” for a list of changes to be aware of.
TABLE 2.1 Inputs and Outputs with Jumpers P6 through P9A
Jumper Pins Position Operation Page
P6 1-2 FAC ILIMIT Current reduced to 5% of peak current in
the forward direction when FAC is clamped. 2-10
2-3 ∗FAC DISABLE No tor
q
ue in the forward direction when
FAC is clamped. 2-10
P7 1-2 RAC ILIMIT Current reduced to 5% of peak current in
the reverse direction when RAC is
clamped.
2-10
2-3 ∗RAC DISABLE No tor
q
ue in the reverse direction when
RAC is clamped. 2-10
P8 1-2 ∗Internal Opto Power Opticall
y
isolated transistors
(
opto’s
)
on
FAC, RAC and INH inputs are powered
internall
y
b
y
the drive.
2-11
P8A 1-2 ∗Internal Sourcin
g
Opto’s Opto’s are sourcin
g
inputs
(
pulled up to 24V
b
y
internal power when true
)
.2-11
P8A 2-3 Internal Sinkin
g
Opto’s Opto’s are sinkin
g
inputs
(
pulled down to
0V b
y
internal power when true
)
.2-11

2-2 Installation
P/N 0013-1025-001 Rev F
* Indicates Factory Setting
P8 2-3 External Opto Power Customer supplies power
(
24V
)
to opto’s on
FAC, RAC and INHibit inputs. 2-11
P8A 2-3 External Sourcin
g
Opto’s Opto’s are sourcin
g
inputs
(
pulled up to 24V
b
y
external power when true
)
.
NOTE: External power polarit
y
connec-
tions define circuit as sourcin
g
.
2-11
P8A 2-3 External Sinkin
g
Opto’s Opto’s are sinkin
g
inputs
(
pulled down to
0V b
y
external power when true
)
.
NOTE: External power polarit
y
connec-
tions define circuit as sinkin
g
.
2-12
P9 & P9A 1-2 SSO Rela
y
S
y
stem Status Output is controlled b
y
a
rela
y
2-13
2-3 ∗SSO Open Collector S
y
stem Status Output is controlled b
y
an
open collector transistor 2-13
Intro
FIGURE 2.1 Jumper Locations
TABLE 2.1 Inputs and Outputs with Jumpers P6 through P9A (continued)
Jumper Pins Position Operation Page
NOTE: Figure depicts factory jumper settings. Refer to the “Internal Connections (FAC, RAC
and INH)” on page 2-11 for diagrams to connect externally powered opto’s.
123
VERR
EN INTG
+15V-15V
C22C21
P2
P1
ICMD
VCS
TACH
COMP
BAL
ILIM
P6 P7
P8 P8A
P9 P9A
P7 2-3 = RAC DISABLE
123
P6 2-3 = FAC DISABLE
3
2
1
P8A
1-2 = SOURCING OPTO’S
1
2
3
P9A
1
2
3
P9
3
2
1
P8
1-2 = INTERNAL OPTO POWER
2-3 =
SSO OPEN
COLLECTOR
OUTPUT

Installation 2-3
Instruction Manual
Mounting The drive must be mounted in the vertical position (heat sink fins must be vertical) away from
other heat producing devices. In multiple axis applications, a minimum of 1 inch separation
between each chassis is recommended. See Figure 7.1 on page 7-1.
Transformer Sizing
The MAX-430 requires an isolation/step-down transformer. To size a transformer for a MAX-
430 the power output (KVA) of each axis must be known. This can be derived by calculating the
horsepower for each axis.
Transformer single phase KVA rating = (Sum of each motor’s average output power) x 2.0
IfyouareusingtheElectro-Craftsystemsizingprogram(Systex),theaveragespeedandaverage
torque data has already been calculated and can be used in the above equation.
Example:
You are using a MAX-430 drive and 0644-35-021 motor, and you are unsure of the exact speed
and torque in your application. Look at the speed/torque curve for your drive/motor combi-
nation as shown in the Electro-Craft catalog and use the values for the worst case continuous
speed and torque.
Transformer single phase KVA rating = (Sum of each motor’s average output power) x 2.0
KVA =
Selectatransformerthatcanprovideenoughvoltagefortheapplication.Thiscanbedetermined
by looking at the maximum speed ofthe application and the voltage constant (KE) of the motor
selected.
TIP The factor of 2.0 is used as an estimate of drive module and motor losses.
KVA Speed Torque
×
63 025
,
--------------------------------------746 Watts
HP
------------------------
×KVA
1,000 Watts
-----------------------------
×2.0
×
=
Speed is in units of RPM
Torque is in units of lb-in
2000 RPM 6.2 lb-in
×
63 025
,
-----------------------------------------------------746 Watts
HP
------------------------
×KVA
1,000 Watts
-----------------------------2.0
××
Transformer size = 0.294 KVA
KEMax Speed
×1000
,
----------------------------------------
Motor Winding Resistance Peak Current
×()
+1.5
×DC bus voltage=
KE= Volts/krpm
Max. Speed = krpm
Motor Windin
g
Resistance = Ohms
Peak Current = Amps
1.5 = 50% safet
y
and losses
Tapped voltage from transformer DC bus voltage
2
-------------------------------------
≥

2-4 Installation
P/N 0013-1025-001 Rev F
AC and DC Power Connections
AC input power to the MAX-430 must be supplied by an isolation transformer with an output
of 20-85 VAC. Refer to “Transformer Sizing” on page 2-3. Alternatively the MAX-430 may be
supplied with 30-120 VDC.
ThegroundingconnectionforACandDCpower,chassisandmotormustbeconnectedasshown
in the following wiring diagrams.
Intro
!
CAUTION All TB1 terminals must be tightened to 9 lb-in. All wiring must be a minimum of
60°C insulation rating.
Intro
FIGURE 2.2 115 VAC Input Power/Motor Wiring

Installation 2-5
Instruction Manual
The isolated AC supply may be commonto more thanone drive as shown inthe “Multiple Axis
Power Wiring” diagrams below. The power leads from each drive should terminateat the trans-
former terminals as shown on the drawing. When powering more than one drive, it is
recommended, but not required, that individual secondaries of a transformer be used, so that
the power inputs of the drives are completely isolated.
Intro
FIGURE 2.3 230 VAC Input Power/Motor Wiring
Intro
FIGURE 2.4 +(30-120) VDC Input Power/Motor Wiring

2-6 Installation
P/N 0013-1025-001 Rev F
Intro
FIGURE 2.5 Multiple Axis Power Wiring (Individual Secondaries)
(Recommended Method)

Installation 2-7
Instruction Manual
Intro
FIGURE 2.6 Multiple Axis Power Wiring (One Secondary)
(Alternative Method)

2-8 Installation
P/N 0013-1025-001 Rev F
Auxiliary Logic Supply Power
Supplying power separately to the logic supply is useful if the MAX-430 logic power must stay
ON when the motor power must be turned OFF. When DC power (24 VDC) is supplied to the
Auxiliary power input at TB1 pins 9 and 10, only the logic supply is powered. This is useful
whentheoperationalstatusoftheMAX-430driveisneededattheSSOoutput(P1pin6)without
applying main power. See “AC and DC Power Connections” on page 2-4.
Connecting The Motor
When a positive voltage is applied to VCS+ with respect to VCS- (P1 pins 1 and 2), and the
motor and tachometer leads are connected to the drive as explained below, there will be clock-
wise (CW) motor shaft rotation as viewed from the shaft end of the motor. Likewise, there will
be counterclockwise rotation when a negative voltage is applied to VCS+. To reverse direction,
whilekeepingthevoltagepolarityonVCS+andVCS-thesame,bothmotorleadsandtachometer
leads need to be reversed. To reduce the effect of radiated electrical noise it is suggested that the
motor leads and the supply leads be run as twisted pair shielded cable. It is also advisable to
keep the motor and power leads away from any signal leads. See “AC and DC Power Connec-
tions” on page 2-4.
Motor Connection
TB1 pin 5 is MT+
TB1 pin 4 is MT-
Tachometer Connection
TB1 pin 2 is TG+
TB1 pin 1 is TG-
Logic Inputs and Outputs
The diagram below illustrates the suggested method of connecting the inputs and outputs on
P1andP2.Thefollowingthreesections(“ConnectingInputs”,“InternalConnections(FAC,RAC
and INH)” and “Connecting Outputs”) explain the function of each input and output in more
detail.

Installation 2-9
Instruction Manual
Intro
FIGURE 2.7 External Interface Connections
1
2
Proper shielding is recommended. The shield may be connected to common (P1 pin 4) or to common
on controller end of wire.
The connections shown are with factory default jumper settings. See “Internal Connec-
tions (FAC, RAC and INH)” on page 2-11, for details on connections for other jumper set-
tings.

2-10 Installation
P/N 0013-1025-001 Rev F
Connecting Inputs
Velocity Command Signal (VCS)
Function
This input controls motor speed and direction. When a positive voltage is applied to pin 1 with
respect to pin 2, the motor shaft will rotate CW as viewed from the shaft end of the motor. A
negative voltage applied to pin 1 with respect to pin 2 will result in counterclockwise (CCW)
rotation.
This input signal is conditioned through a differential drive to reduce noise. Proper shielding
is recommended, as shown in Figure 2.7.
Input signal range is ± 10 VDC.
Connection
P1 pin 1 is VCS+
P1 pin 2 is VCS-
Auxiliary Input
Function
The auxiliary input signal (AUX) may be used, in addition to VCS, as a velocity signal.
Refer to the Figure 1.1 on page 1-2.
Input signal range is ±10 VDC.
Connection
P1 pin 3
Inhibit (INH)
Function
This input signal inhibits or enables the output stage. The input can be either active high or
active low, depending on the position of jumper P8A. (Location of the jumpers on the velocity
regulatorboardis shown inFigure 2.1.)Thisinput isalso usedto resettheSystemStatusOutput
(SSO) fault circuit. The INHibit input must be activated to clear the SSO fault.
Connection
P1 pin 8
(Refer to “Internal Connections (FAC, RAC and INH)” on page 2-11.)
Forward and Reverse Amplifier Clamps (FAC, RAC)
Function
The forward amplifier clamp (FAC) and reverse amplifier clamp (RAC) are directional clamps
that will operate in one of two ways, depending on the position of jumpers P6 and P7. With P6
and P7 in the FAC ILIMIT and RAC ILIMIT positions, the drive will limit the current to 5% of
peakcurrent inthe correspondingdirection,allowingoperationintheopposite direction,when
either clamp is activated. With P6 and P7 in the FAC DISABLE and RAC DISABLE positions,
there will be no torque in the corresponding direction when either clamp is activated.
Forward is defined as CW motor shaft rotation as viewed from the shaft end of the motor.
Reverse is defined as CCW motor shaft rotation as viewed from the shaft end of the motor.
The FAC and RAC inputs can be either active high or active low, depending on the position of
jumper P8A. Refer to the sourcing and sinking diagrams below for the operation of the jumper
settings. (Location of each jumper on the velocity regulator board is shown in Figure 2.1.)
Table of contents
Other Electro-Craft Servo Drive manuals
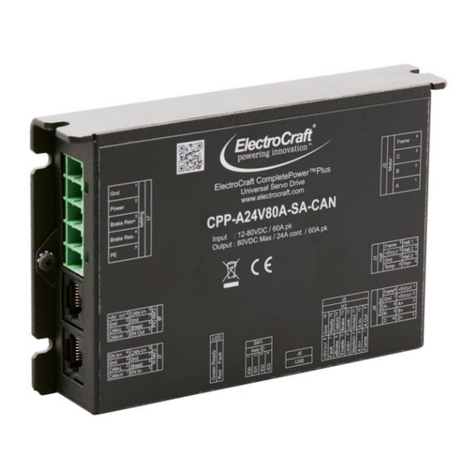
Electro-Craft
Electro-Craft CompletePower Plus CPP-A24V80A-SA-CAN User manual
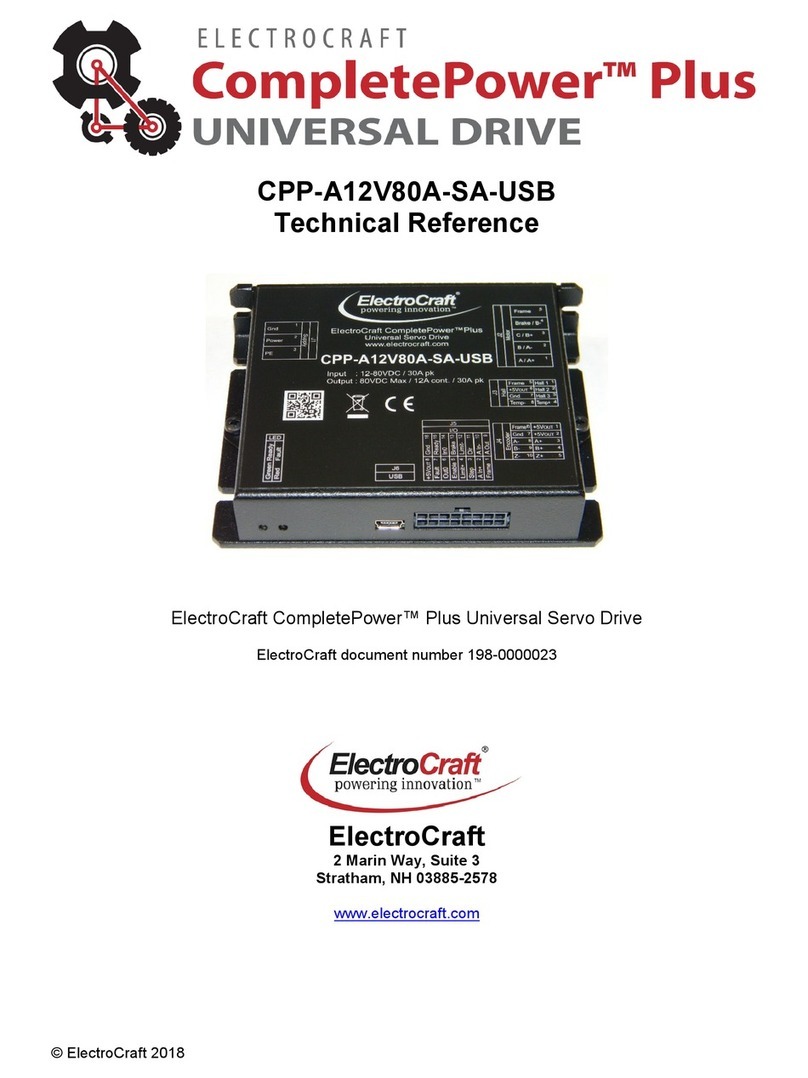
Electro-Craft
Electro-Craft CompletePower Plus CPP-A12V80A-SA-USB Use and care manual
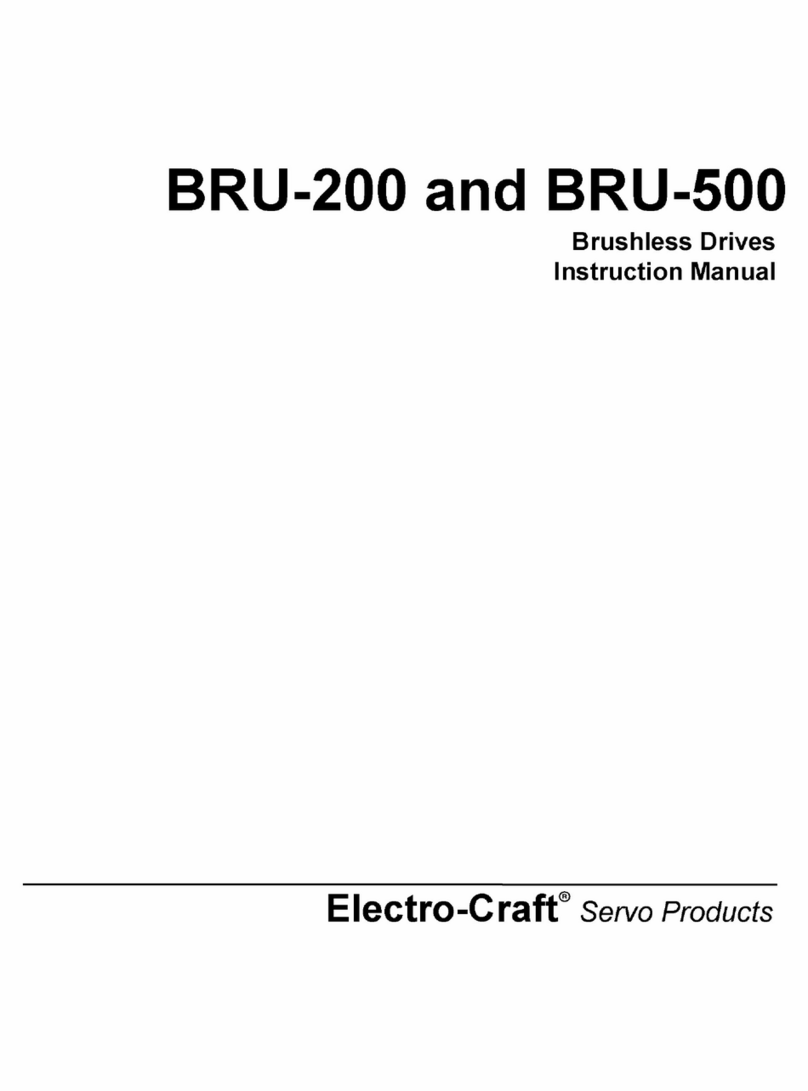
Electro-Craft
Electro-Craft BRU-200 User manual
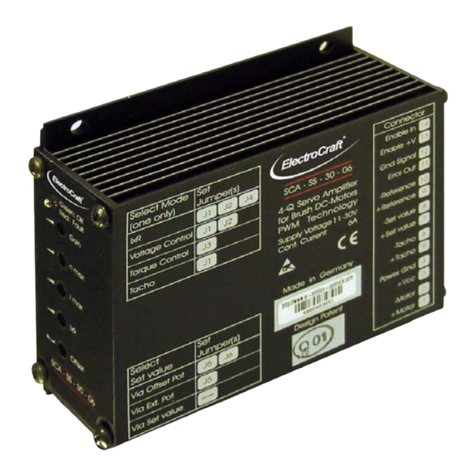
Electro-Craft
Electro-Craft SCA-SE-30-06 User manual
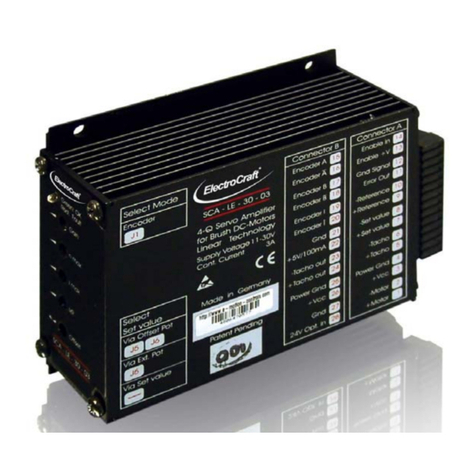
Electro-Craft
Electro-Craft SCA-LE-30-03 User manual
Popular Servo Drive manuals by other brands
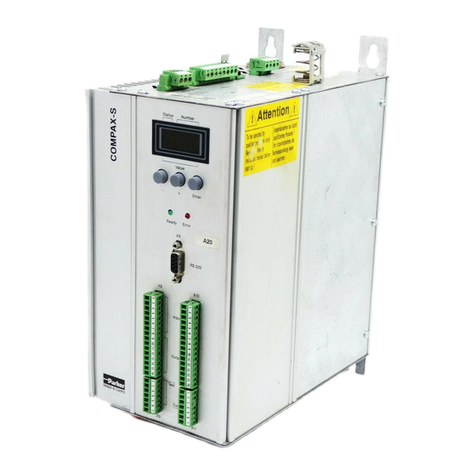
Parker
Parker Hauser COMPAX 25 S F1 Series operating instructions
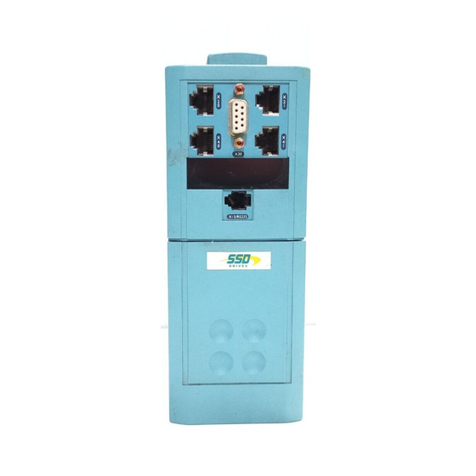
Eurotherm Drives
Eurotherm Drives 631 product manual
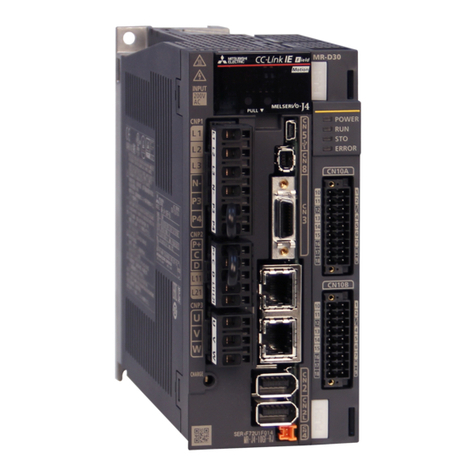
Mitsubishi Electric
Mitsubishi Electric MR-D30 instruction manual
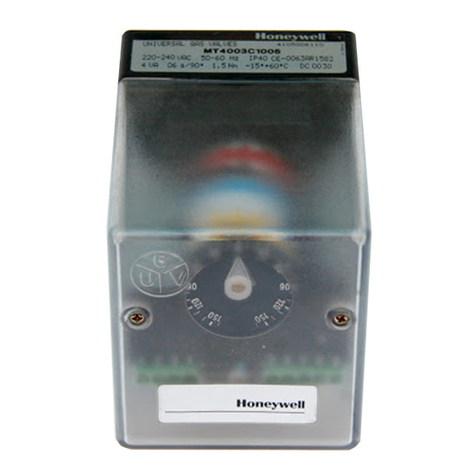
Honeywell
Honeywell MT4000 Series instruction sheet
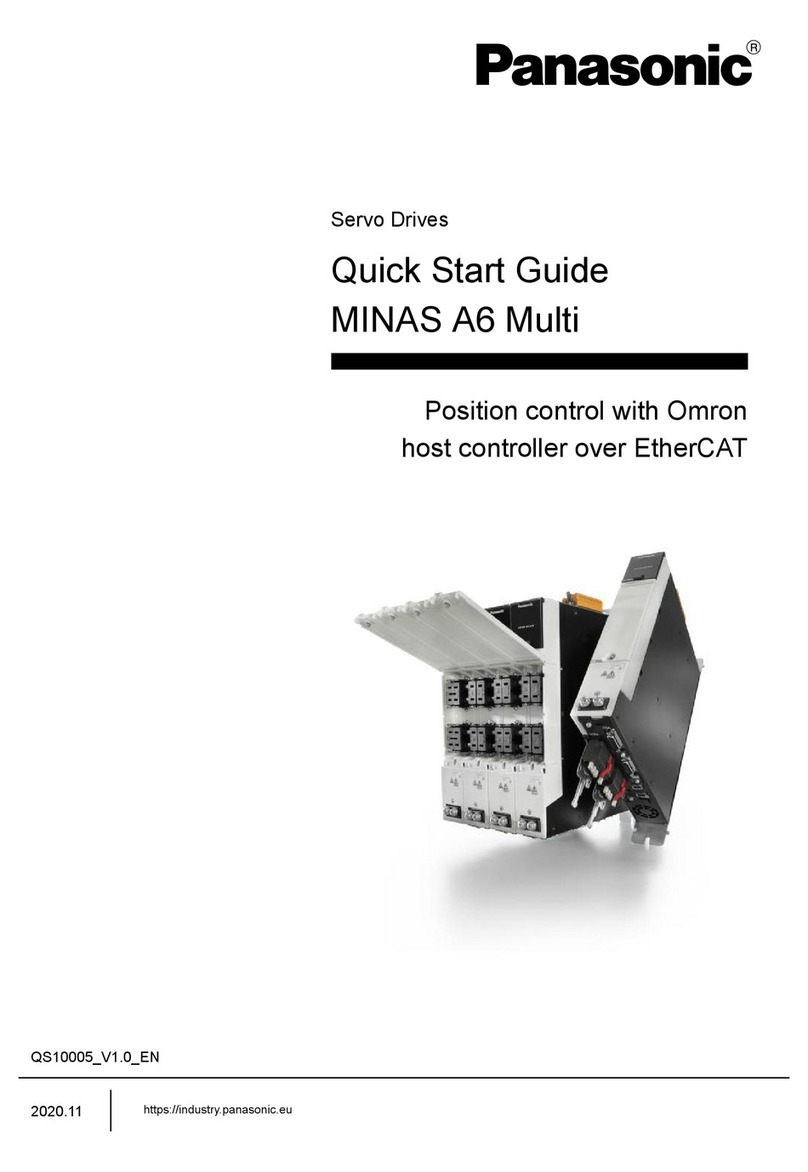
Panasonic
Panasonic MINAS A6 Series quick start guide
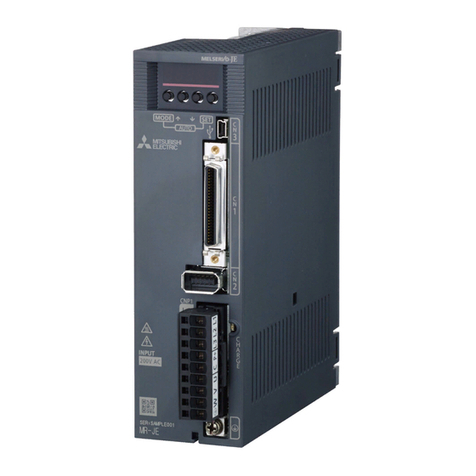
Mitsubishi
Mitsubishi MR-JE series instruction manual