ElectroDacus SBMS100 User manual

1
user manual
user manual
v0.9
www.ElectroDacus.com
www.ElectroDacus.comSBMS100 / SBMS60
SBMS100 / SBMS60

2www.ElectroDacus.com
www.ElectroDacus.comSBMS100 / SBMS60
SBMS100 / SBMS60
Table of contents
Table of contents
Simplified diagram 3
Specifications 4
1. Install instructions 5
2. Thermal management 9
3. Cable selection 11
4. E ternal Load 12
5. Battery temperature 14
6. The 20pin connector 15
7. Selecting the battery and PV panels 16
8. WiFi
9. Internal data logging
18
20
10. User interface 23

3SBMS100 / SBMS60
SBMS100 / SBMS60
www.ElectroDacus.com
www.ElectroDacus.com
1
1
2
2
3
3
4
4
5
5
6
6
7
7
8
8
Brown
Brown Red
Red Orange
Orange Yellow
Yellow Green
Green Blue
Blue
Grey
Grey Black
Black&
&Whi e
Whi e
Purple
Purple
Simplified circuit diagram for the SBMS100 with max configuration.
(Two PV arrays each with x 250W PV panels for a total of 3kW).

4SBMS100 / SBMS60
SBMS100 / SBMS60
www.ElectroDacus.com
www.ElectroDacus.com
Specication
Specication
Battery type
Battery type any type of Lithium cells and Supercapacitors
any type of Lithium cells and Supercapacitors
Number of cells
Number of cells 3 to 8 cells
3 to 8 cells
Battery voltage limits min/max)
Battery voltage limits min/max) 8V to 32V
8V to 32V
Battery/PV recommandation 12V
Battery/PV recommandation 12V 4 cell LiFePO4 / 32 or 36 cells PV panel
4 cell LiFePO4 / 32 or 36 cells PV panel
Battery/PV recommandation 24V
Battery/PV recommandation 24V 8 cell LiFePO4 / 60 cells PV panels
8 cell LiFePO4 / 60 cells PV panels
Max PV Open Circuit voltage
Max PV Open Circuit voltage 47V mono or polycristaline panels with up to 72 cells)
47V mono or polycristaline panels with up to 72 cells)
Dual PV input
Dual PV input PV1+ and PV2+ with separate current measurement and ideal diode
PV1+ and PV2+ with separate current measurement and ideal diode
PV1 or PV2 max current
PV1 or PV2 max current SBMS60 72A ) / SBMS100 72A )
SBMS60 72A ) / SBMS100 72A )
PV1 + PV2 max current
PV1 + PV2 max current SBMS60 72A ) / SBMS100 120A )
SBMS60 72A ) / SBMS100 120A )
Load+ overcurrent limit
Load+ overcurrent limit SBMS60 72A ) / SBMS100 120A )
SBMS60 72A ) / SBMS100 120A )
Cell balancing current
Cell balancing current max 200mA
max 200mA
Power terminal max wire size / recommended
Power terminal max wire size / recommended 35mm2 #2 AWG) / 16mm2 #6 AWG) 200C silicone
35mm2 #2 AWG) / 16mm2 #6 AWG) 200C silicone
Battery temperature sensor
Battery temperature sensor Thermistor optional)
Thermistor optional)
20pin connector
20pin connector Includes Ext IO, 16bit ADC, external current shunt input 500A max
Includes Ext IO, 16bit ADC, external current shunt input 500A max
Data logging to internal Flash memory
Data logging to internal Flash memory 128Mbit 16Mbyte) 2 minute interval for one year of data
128Mbit 16Mbyte) 2 minute interval for one year of data
WiFi
WiFi WiFi used for remote monitoring SBMS acts as AP )
WiFi used for remote monitoring SBMS acts as AP )
Display
Display 2.2” Color LCD 320x240
2.2” Color LCD 320x240
Weight
Weight 255g
255g
Dimensions
Dimensions 100mm x 90mm x 26mm
100mm x 90mm x 26mm
Self consumption
Self consumption 250mW to 700mW WiFi and Backlight ON)
250mW to 700mW WiFi and Backlight ON)
Max TDP
Max TDP SBMS100 22W) / SBMS60 14W)
SBMS100 22W) / SBMS60 14W)

5SBMS100 / SBMS60
SBMS100 / SBMS60
www.ElectroDacus.com
www.ElectroDacus.com
1 Install Instructions
1 Install Instructions
*before starting with electrical installation take a look at the thermal management the SBMS needs a heatsink in most cases)
Step 1
Step 1
Connect the Batt+ power connector to battery positive terminal with a ma 2m of 16mm2 (#6AWG) fle ible copper wire with 200°C
silicone insulation (check page 11 for more details about the recommended cable).
Make sure this is the first connected and the last to be removed.
Step 2
Step 2
Connect the 10pin monitor and balancing cable. Make sure this is the second one to be connected after Batt+ and never disconnect
while anything else is connected except for Batt+. (see details on page 3 or Parameter Settings on how this has to be connected to
individual cells).

6SBMS100 / SBMS60
SBMS100 / SBMS60
www.ElectroDacus.com
www.ElectroDacus.com
Step 3
Step 3
Go to Parameter Settings menu and select the type of cell, number of cells and battery capacity then push Store Parameters button to
save data to SBMS. Then remove the 10pin connector and reconnect for the new stored parameters to be accepted.
*you need to be connected to battery to Store Parameters will not work on USB power since ISL94203 is not powered.
Step 4
Step 4
Go to monitoring menu page 3 and push ok button then a small sub menu will be displayed in the top left corner. Use down key to select
Load OFF and then push OK to enable this.
You should see CFET and DFET flags change state from highlighted to not being highlighted meaning that load+, PV1 and PV2 are
disconnected internally.

7SBMS100 / SBMS60
SBMS100 / SBMS60
www.ElectroDacus.com
www.ElectroDacus.com
Step 5
Step 5
Connect Load+ using the same type of cable mentioned in step1 to a 125A circuit breaker in OFF position and from there to your load.
Step 6
Step 6
Connect the PV1 and or PV2 to your PV array to appropriate size circuit breaker in OFF position.
See the page 16 for the type of PV panels recommended based on the number of cells and battery voltage.

8SBMS100 / SBMS60
SBMS100 / SBMS60
www.ElectroDacus.com
www.ElectroDacus.com
Step 7
Step 7
Switch the Load and PV breakers to ON position and then go again to page 3 of the monitoring menu and select Load ON this time.
The CFET and DFET should be highlighted and the Load should now have power also the PV1 and PV2 should provide charging
current.
Step 8
Step 8
Check the first page of the Monitoring Menu to see if all works correctly. You are done. Make sure you follow the install procedure in
reverse when you want to remove the SBMS. Never remove the Batt+ or 10pin cell monitoring connector while PV1, PV2 or Load+ is
connected.

9SBMS100 / SBMS60
SBMS100 / SBMS60
www.ElectroDacus.com
www.ElectroDacus.com
2 Thermal Management
2 Thermal Management
The SBMS60 and SBMS100 will need to be mounted on an appropriate size heatsink able to dissipate the ma TDP (Total Dissipated
Power) that is as high as 22W for SBMS100 and 14W for the SBMS60 at full load (charge and discharge at the same time).
The SBMS has two ( 5mm ) mounting holes as you see in the below drawing.

10 SBMS100 / SBMS60
SBMS100 / SBMS60
www.ElectroDacus.com
www.ElectroDacus.com
The SBMS100 without any heatsink or fan can at most dissipate 4W to 5W so below is an e ample with lower power to allow this.
E ample SBMS100 with ma 40A load and 24A on each PV
on Load+ TDP = 40A 40A 0,001Ω = 1,6W
on PV TDP = 24A 24A 0,0024Ω = 1,38W
Total 1,6W + 1,38W + 1,38W = 4,36W
So 40A load and 48A charging is around ma supported by SBMS100 without a heatsink.
The SBMS has an internal 10k thermistor installed on the power board and will measure and
display the temperature of that board. If temperature e ceeds +60°C the charging and
discharging will be turned off and only turn on the charging and discharging when
temperature drops below +50°C.
If size and weight is of great concern in your installation a low speed fan can be used to cool the back of the SBMS.
If SBMS is not used with full configuration then a smaller heatsink can be used or even no heatsink at all.
You can use the simple formula below to calculate the TDP.
TDP[W] = I[A] I[A] R[Ω]
For e ample you need to know the R for Load+ and PV1/PV2. Load+ resistance path on SBMS100 is 1mΩ and SBMS60 is 1,5mΩ
where PV input on SBMS100 is 2,4mΩ and on SBMS60 is 3mΩ.
For ma configuration on SBMS100 you have:
on Load+ TDP = 100A 100A 0,001Ω = 10W
on PV TDP = 50A 50A 0,0024Ω = 6W
So total 10W + 6W + 6W = 22W on full load SBMS100

11 SBMS100 / SBMS60
SBMS100 / SBMS60
www.ElectroDacus.com
www.ElectroDacus.com
3 Cable Selection
3 Cable Selection
SBMS requires flexible copper cables. For full load configuration I recommend using high quality 16mm2 (sold as #6 AWG even if is
much closer to #5 AWG) fle ible tinned copper cable with 3200 strands of 0,08mm and 200°C silicone insulation.
I measured 1,125mΩ/m for this cable and you will want to keep the resistance of cable between battery positive terminal and SBMS
Batt+ connector below 2,5 mΩ so around 2m ma is recommended for this particular cable.
No fuse or breaker is allowed between Batt+ and battery positive terminal. Use the same cable between Load+ and a DC circuit
breaker.
The same cable can be also used between PV and a DC circuit breaker.
The circuit breakers on PV and Load+ will allow for a way to manually disconnect the circuit and offer redundant
overcurrent protection.
When you connect the cable to the SBMS power connectors please do not use to much torque. Since you will probably using a 4mm he
allen key the force pushing on the cable will be multiplied 628 times even with just a 10cm long key.
Excessive force can break the connectors from the PCB.

12 SBMS100 / SBMS60
SBMS100 / SBMS60
www.ElectroDacus.com
www.ElectroDacus.com
4 External Load
4 External Load
On both SBMS60 and SBMS100 an E ternal Load can be connected allowing large loads of up to 500A to be connected.
01 02
03 04
05 06
07 08
09 10
11 12
13 14
15 16
17 18
19 20
1
1
2
2
3
3
4
4
5
5
6
6
7
7
8
8
470Ω
Remo e ON/OFF
Curren shun (10A o 500A 75mV)
USART TX USART RX
SDA / EXT IO1
BOOT 0
ESP FLASH
GND
USBN / EXT IO3
USBP / EXT IO4
ADC1N
EXT ADC2
EXT ADC4
EXT IO2 / SCL
EXT IO5 / SWK
EXT IO6 / SWD
GND
XT1 EXT Temp
3.3V-100Ω
ADC1P
EXT ADC3
GND
SBMS100 / SBMS60

13 SBMS100 / SBMS60
SBMS100 / SBMS60
www.ElectroDacus.com
www.ElectroDacus.com
All you need for an e ternal load connection is a 75mV current shunt. Can be 10A up to 500A and the load needs to support remote
ON/OFF and optoisolation is required between EXT IO pin and inverter remote ON/OFF port.
Most large power inverters have a digital remote ON/OFF input signal. The e ample inverter in the above diagram is the TRIPP-Lite
PV2400FC (is a modified sine inverter that I happen to own) that has a 15V signal that if pulled to GND will power the inverter and the
amount of current when that 15V signal is pulled to GND is around 13mA so most optoisolators will be able to handle that.
If you are not using the inverter 24h/day then you can add a normal mechanical switch in series with the optoisolator output so that you
can manually turn OFF the inverter. I will do that since I only use the inverter occasionally most of my loads are DC.
The EXT IO pins supply 3.3V and up to 20mA can be draw from them. With normal optoisilator with infrared LED the voltage drop on
that LED is around 1.2 to 1.3V so about 2V will drop on e ternal resistor you need to add for current limiting (in the above e ample a
470Ω resistor was used that will limit the LED current to 2V / 470Ω = 4.25mA more than sufficient for the optoisolator).
An appropriate circuit breaker or fuse is also needed for overcurrent protection.
The current sense output from the current shunt gets connected on pins 15 and 16 on the 20pin connector.
The pin16 (ADC1P) will be on the battery positive side of the current shunt resistor and pin15 (ADC1N) on the side going to your
e ternal load presumably a DC to AC power inverter as in the above diagram.
The e ternal load will need to support remote ON/OFF capabilities and that will be connected to one of the 4 EXT IO pins.
The EXT IO pin you decide to use (EXT IO3 used in the above e ample) will need to be programmed in the EXT IO submenu as type 2
(Low Voltage Disconnect) or as type 4 if you want the load (inverter) to be disconnected when battery gets below a certain SOC level
(user programmable).
Another setting you will need to do is in the ADC (E tLoad settings) submenu where you will be turning the E tLoad ON and providing
the E tLoad shunt resistance value in [mΩ] so that SBMS is able to calculate and display current correctly.
E ample 1) 500A 75mV shunt will have a resistance value of 75mV / 500A = 0.1500mΩ.
E ample 2) 75mV / 200A = 0.3750mΩ
E ample 3) 75mV / 10A = 7.5000mΩ.

14 SBMS100 / SBMS60
SBMS100 / SBMS60
www.ElectroDacus.com
www.ElectroDacus.com
5 Battery Temperature
5 Battery Temperature
It is possible to add e ternal temperature sensor but in most cases not needed and so is optional.
All Lithium batteries require temperature above freezing > +5°C) during charging otherwise they will be damaged.
Best way when possible is to have the battery inside the living space where temperature is ideal for battery operation.
The SBMS is designed to accept a thermistor as temperature sensor connected between pin 12 and one of the GND pins (like pin 10 on
the 20 pins connector).
01 02
03 04
05 06
07 08
09 10
11 12
13 14
15 16
17 18
19 20
USART TX USART RX
SDA / EXT IO1
BOOT 0
ESP FLASH
GND
USBN / EXT IO3
USBP / EXT IO4
ADC1N
EXT ADC2
EXT ADC4
EXT IO2 / SCL
EXT IO5 / SWK
EXT IO6 / SWD
GND
XT1 EXT Temp
3.3V-100Ω
ADC1P
EXT ADC3
GND
The SBMS is calibrated for a particular 10kΩ thermistor made by Murata NCP21XV103J03RA (this same thermistor type is used
internally to measure the power board temperature).
The low and high temperature limits for this e ternal temperature sensor can be set from the Advanced Parameter Setting submenu
parameter 29 and 30.
Value is a 12bit binary number and if you use the recommended thermistor the 0°C=3144b,+5°C=3000b, +50°C=1338b,
+55°C=1182b, +60°C=1040b.
You can see the actual temperature in Monitoring menu and the raw binary value in Diagnostic menu.
NCP21XV103J03RA

15 SBMS100 / SBMS60
SBMS100 / SBMS60
www.ElectroDacus.com
www.ElectroDacus.com
6 The 20pin connector
6 The 20pin connector
There is a 20pin connector on the left side of the LCD on SBMS and it is used for different functionality described below.
01 02
03 04
05 06
07 08
09 10
11 12
13 14
15 16
17 18
19 20
USART TX USART RX
SDA / EXT IO1
BOOT 0
ESP FLASH
GND
USBN / EXT IO3
USBP / EXT IO4
ADC1N
EXT ADC2
EXT ADC4
EXT IO2 / SCL
EXT IO5 / SWK
EXT IO6 / SWD
GND
XT1 EXT Temp
3.3V-100Ω
ADC1P
EXT ADC3
GND
01 & 02 UART TX and RX pins are used for the WiFi module so if you want to use the USART for
something else then WiFi will be disabled (voltage levels 0 to 3.3V).
03 & 04 This two pins are reserved as I2C port for a future addon to SBMS (Digital MPPT heat
controller) and maybe some other future addons.
05 Boot 0 connected to pin 14 will put the STM32F373 microcontroller in programing mode.
06 & 08 This pins have dual function as programmable EXT IO5 and IO6 (0 to 3.3V 20mA ma )
and as SWK and SWD programing interface for the STM32F373.
05 ESP Flash connected to GND will put the ESP8266 WiFi module in programing mode.
11 & 13 This pins have dual function as programmable EXT IO3 and IO4 (0 to 3.3V 20mA ma )
and as USB or CAN port not used in the software as of now. USB can probably be used in
firmware upload mode for the STM32F373 (not tested).
14 This is a 3.3V supply from the internal DC-DC converter trough a 100Ω series resistor
mostly to be used to pull up BOOT 0 pin to enter programing mode.
15 & 16 E ternal current shunt input with a 0 to 90mV input range see page 11 for more details.
17, 18 & 19 E t ADC inputs 2,3,4 with analog input range of 0 to 1.8V that will be logged in the internal SBMS memory at 2 minute
intervals but not used in any automation with the latest firmware version. This are good if you want to log some other analog signals.

16 SBMS100 / SBMS60
SBMS100 / SBMS60
www.ElectroDacus.com
www.ElectroDacus.com
7.1 Selecting the battery and PV panels
7.1 Selecting the battery and PV panels
I always recommend going with 24V since that will be the least e pensive option (mostly because of the lower cost PV panels).
There are just two main type of PV cells the 125 125mm (5”) and 156 156mm (6”) cells (6” cells are by far more common and panels
made with them are usually lower cost per Watt).
Each cell will have a current output based on surface area of the cell and cell efficiency so the 5” will have around 5 to 6A output with
STC (Standard Test Conditions) and the 6” will have a 8 to 9A output in the same conditions.
The output voltage is not dependent of the amount of sun power or cell size and open circuit voltage is around 0.6V to 0.65V / cell and
ma power point voltage at STC is around 0.5V / PV cell a bit lower as cells get hotter.
The PV cells are connected in series in most solar PV panels and there are just a few standard PV panels with by far the most common
in recent years being the 60 cell PV panels rated from 240 to 270W depending on the cell efficiency.
This 60 cell panels made with 6” cells are the most common representing probably close to 80% of the world production and that is why
they are the least e pensive as in $/Watt and ideal for 24V LiFePO4 battery charging.
For 12V battery the 32 or 36 cells panels are ideal do to ma power point voltage being closer to battery voltage but since they are less
common they will cost more per Watt than the 60 cell ones almost to the point that it cost about the same to get a 36 cell 5” panel or a
60 cell 6” panel. The down side will be the size so where space reserved for PV is limited and you want a 12V battery there is no choice
than to get the more e pensive 32 or 36 panels.
For battery you will need 4 cells in series for 12V and 8 cells in series for 24V (that is for LiFePO4 most cost effective batteries for
stationary energy storage). Any number of cells in parallel will be equivalent to a larger capacity cell but is till easier to have a single
large cell than multiple smaller parallel cells. All cells need to be new and the same model/capacity.
In case LiCoO2 or other Lithium Cobalt variants mostly used in consumer electronics and electric vehicles for their higher energy
density 7 cells in series will give you the best 24V equivalent and you will select battery Type 2 on the SBMS.
But LiCoO2 will in most cases be more e pensive than LiFePO4 over the life of the battery so unless you find like new cells from a
damaged EV for less than $100/kWh as of 2016 is best to get LiFePO4 that is around $400/kWh new but also lasts at least 4 longer
and is safer to use.

17 SBMS100 / SBMS60
SBMS100 / SBMS60
www.ElectroDacus.com
www.ElectroDacus.com
7.2 Selecting the battery and PV panels
7.2 Selecting the battery and PV panels
Another important aspect in sizing the system will be your location and the amount of energy needed.
See three system size e ample a large a medium and a small system with three different locations.
Ideal charge rate is 0.25 to 0.3C for long life LiFePO4 and as you can see below the selected battery capacity and PV array size respect
this rule.
SBMS100
SBMS100 SBMS60
SBMS60 SBMS60
SBMS60
PV array size STC power (STC curren )
PV array size STC power (STC curren ) 3000W
3000W
(100A)
(100A)
1820W
1820W
(60A)
(60A)
200W
200W
(12A)
(12A)
LiFePO4 ba ery capaci y (vol age)
LiFePO4 ba ery capaci y (vol age) 400Ah
400Ah
(24V)
(24V)
200Ah
200Ah
(24V)
(24V)
40Ah
40Ah
(12V)
(12V)
Min/Max
Min/Max
[kWh/mon h]*
[kWh/mon h]*
Phoenix/AZ/USA, Dubai/UAE, Alice Springs/Aus ralia 300/360 180/220
180/220 18/22
18/22
Regina/SK/Canada, San Francisco/CA/USA, Sydney/Aus ralia
Regina/SK/Canada, San Francisco/CA/USA, Sydney/Aus ralia 200/320
200/320 120/190
120/190 12/19
12/19
London/UK, Berlin/Germany, Ams erdam/Nea herlands
London/UK, Berlin/Germany, Ams erdam/Nea herlands 50/260
50/260 30/160
30/160 3/16
3/16
*Min refers to the worst winter month and that should be the targeted power consumption is you are completely off-grid and there is no
other energy source. The numbers are based on the http://pvwatts.nrel.gov/ online calculator and correlated with my 3 years offgrid
e perience in Regina/SK/Canada. Panels should be tilted ideally for the best output in winter when is needed most since in summer you
will have a lot of e cess energy anyway.
There are 3 locations for each group and they are with in 10% of each other so it made sense to group them to keep the table clean.

18 SBMS100 / SBMS60
SBMS100 / SBMS60
www.ElectroDacus.com
www.ElectroDacus.com
8 WiFi
8 WiFi
Both SBMS100 and SBMS60 include a WiFi module that can be used for remote monitoring. The SBMS acts as an AP (Access Point)
and will deliver data to a WiFi enabled computing device that supports a HTML5 capable web browser (a smart phone, tablet or
laptop/desktop computer).
All you need to do is download and decompress this html file http://electrodacus.com/SBMS100/SW/SBMS.zip and copy to your device
then connect to SBMS-100 or SBMS-60 named AP and open that file with your preferred web browser.

19 SBMS100 / SBMS60
SBMS100 / SBMS60
www.ElectroDacus.com
www.ElectroDacus.com
The raw data over WiFi are transmitted in a compressed format and if you want to see the raw data you can just write in your web
browser address window the following IP address while connected to SBMS 192.168.4.1 then you will see something similar as below.
var PV1="################################################################################################################################################################################################################################################";
var PV2="###################################################################################A\\_ky}vnM#L$##@*###=###D###L$###I2#-;}xtqp ######################MnoqpoligU############:VUUTSSRQP||||||||||||{|||||{||{||||||||||||||{||{{{{||||{{{{|{|{{|||{";
var Btp="###################################################################################?X\\iy}vmI#G###9#### ###?###H####<$##4}vqoo'######################0Y[\\\\ZWTR<#############<<GJIHHFFx}vuvwvvwwww{|{|vu{tu|uvwwvvvuv{zvutyzttuvw{uuttt{uwvvvvwvvu";
var Btn="############################################################################################,#*,,##,,,#,,,#,,,#*,,,##3(####### 7 77 77777778:##########GGGGGGGGGGHH*#####################################################################";
var Ld ="%$$$$$$$%$%$$$$$%%%%%%%$$$$%$%$%$%%%$$$$$$$$$%$%&&&&&%%&%&&&%%&&&&%&%%&'(''''&%%&%&>QRSSRRQQTSUTUSTUUUSTTTRTTTPRSTW|z}|UOOPNMQRQQRRRRSRSSSRSTTTSTTUZ}{z{{zzyxxzzz{{{{|{{||zzz^TSSQSRvly{yxxzwwwxnnomxzn|zmzzvwyzyzypryz}rp|
zywuo{z{zznywwxvwwxxz";
var ELd="################################################################################################################################################################################################################################################";
var sbms="3';2LD$,I)I*I+I+H}I%I+I**h##+#)P####->##################%N(";
var xsbms="#&lL >N$##5";
var gsbms="#Kc#7?#-L#Hp#*+#)r#)|#&|";
var eA="####.(##########K2empty-####K2####3i######";
var eW="####&%##########-xempty-####-x####'X######";
var s1=['Ah','A','SBMS100'];
var s2=[0,0,0,0,0,0,0,0,3,5,1,1];
The small print above is an e ample of what you will get if you look at the raw data. The data is compressed using my proprietary base
91 encoding using the ascii characters from 35 "#" to 125 "}" this was a simple and efficient way for me to compress data.
The first 6 variables in that raw data are the data for displaying the 6 graphs (3 graphs windows each containing 2 graphs or in the
case of battery a separate graphs for charging and discharging)
It will be simple to deduce each of those variables and what they contain by looking at the java script code inside the html file
mentioned above.
Since this are just raw data representing measurements made by the SBMS you can modify the html page so that you can get a better
nicer user interface or more tailored to your needs.
The sbms variable is the one containing the most important data and I will go in to more details about that one in the ne t chapter
related to SBMS internal data logging.

20 SBMS100 / SBMS60
SBMS100 / SBMS60
www.ElectroDacus.com
www.ElectroDacus.com
9 Internal data logging
9 Internal data logging
The SBMS has an internal 128Mbit (16Mbyte) SPI Flash memory that can log data at a fi ed 2 minute interval.
The memory is capable of storing a full year (12months) of data in a circular type buffer so you always have the last 12 months worth of data in
that internal Flash memory.
In order for the data logging to start you will need to set the Date and Time and you will notice the small “mem” symbol in the lower right side of
the SBMS LCD being highlighted.
The data is also stored compressed in the memory same base 91 compression mentioned in the WiFi chapter and contains the data sent also over
WiFi in the sbms variable.
Here is an e planation of what is contained there and what it is logged in the internal memory.
var sbms="YMDHMS%%C1C2C3C4C5C6C7C8ITET+BATPV1PV2EXTAD2AD3AD4ht1ht2ERR"
Y-year last two digit (limited to 2090); ( sorry if you read this in 2091 I will not e pect a software update :) ).
M-month
D-day
H-hour
M-minute
S-seconds
%% - SOC 0 to 100%
C1 to C8 - cell voltage in mV
IT and ET - internal and e ternal temperature in hundreds of a degree 0 is -45C and 1449 is 99.9C so you need to subtract 450 from the
result and divide by 10 (e ample 689 as result of the decompression will be (689-450)/10=23.9C)
+ - sign for battery charging (+) and discharging (-) used as it is no compression.
BAT - Battery current in mA from -750000mA to +150000mA
PV1 - PV1 input current in mA
PV2 - PV2 input current in mA
This manual suits for next models
1
Table of contents
Popular Control Unit manuals by other brands
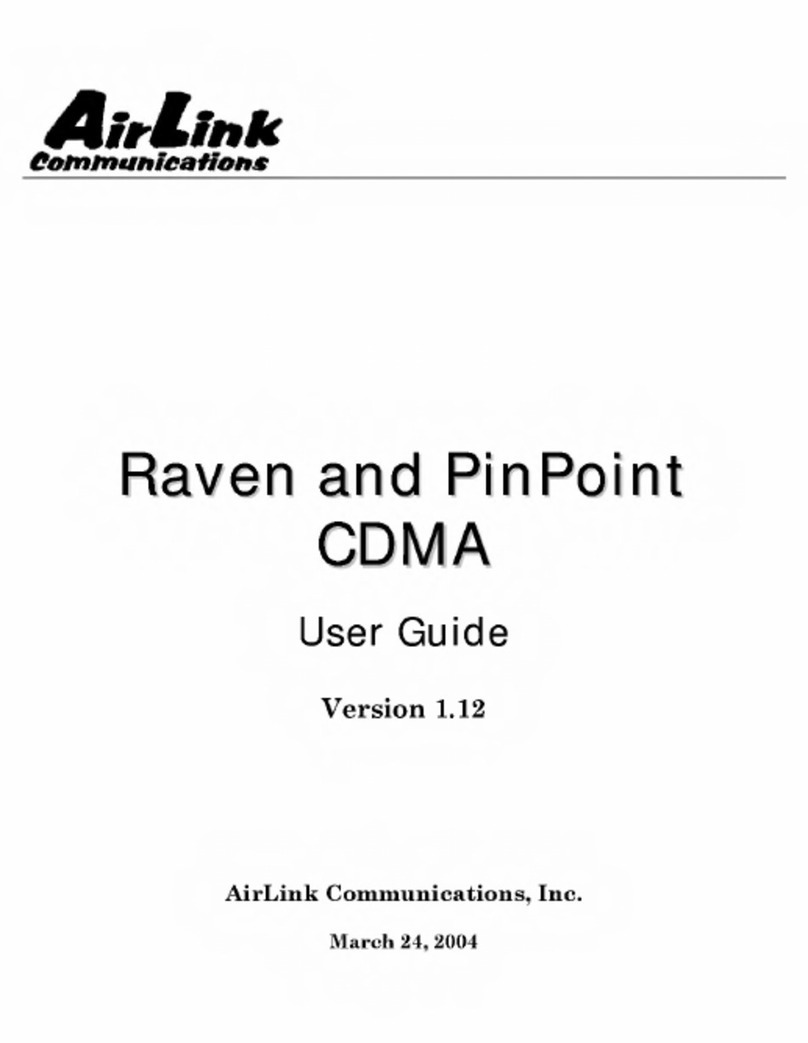
Airlink101
Airlink101 Raven user guide
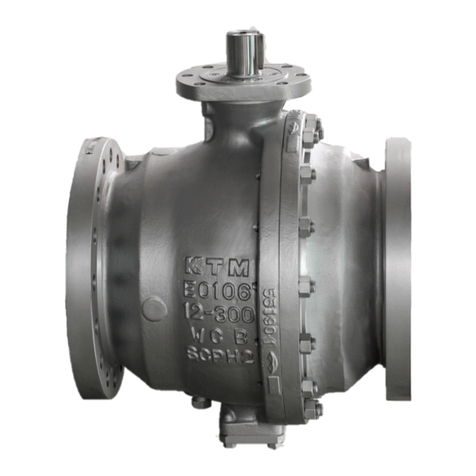
Emerson
Emerson KTM Series Operating and safety instructions
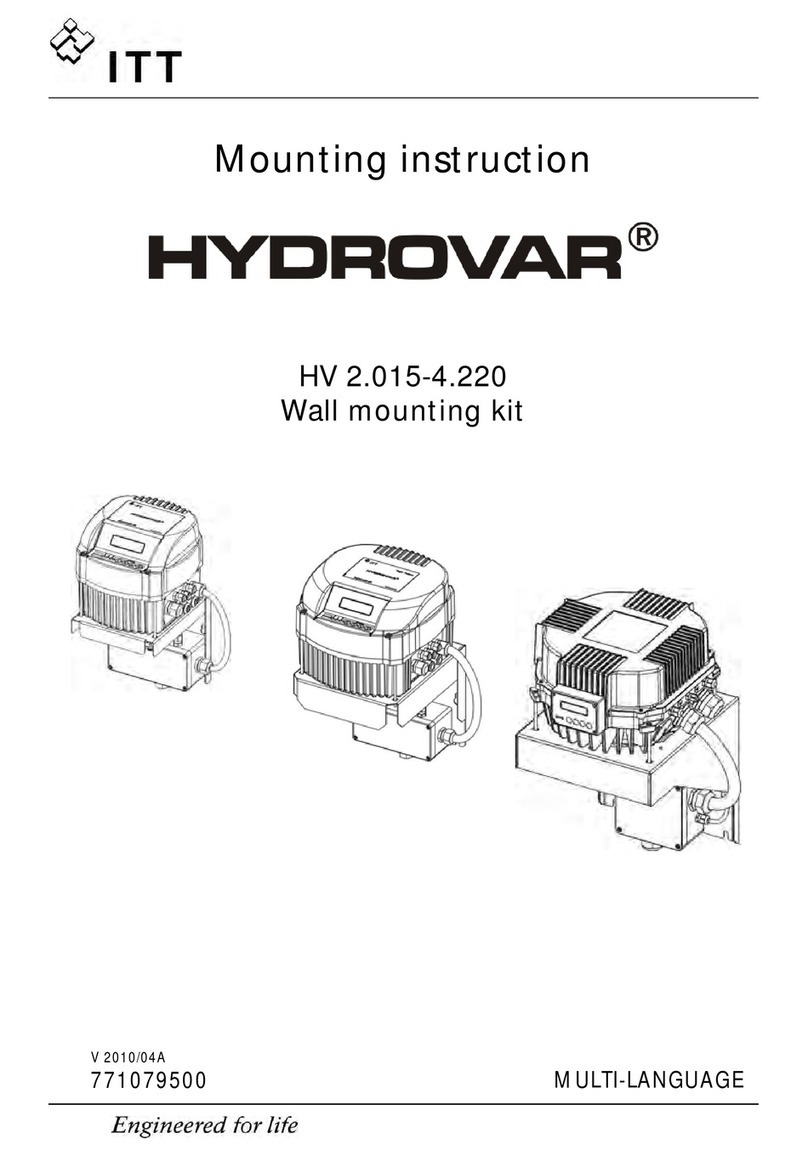
ITT
ITT HYDROVAR HV 4.040 Mounting instruction
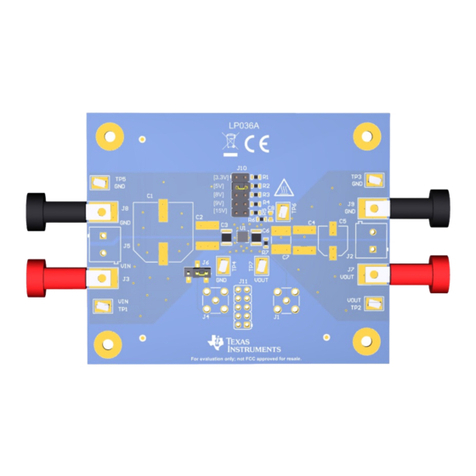
Texas Instruments
Texas Instruments TPS7B8401EVM user guide
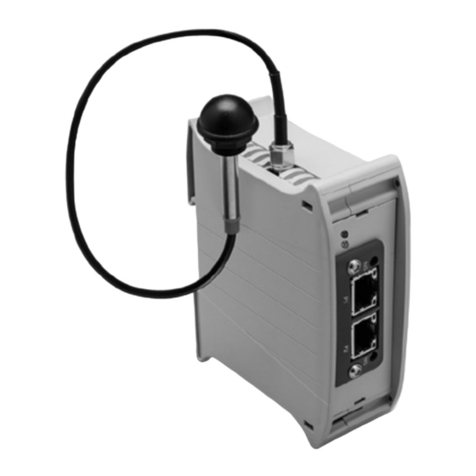
Elesa
Elesa UC-RF operating instructions
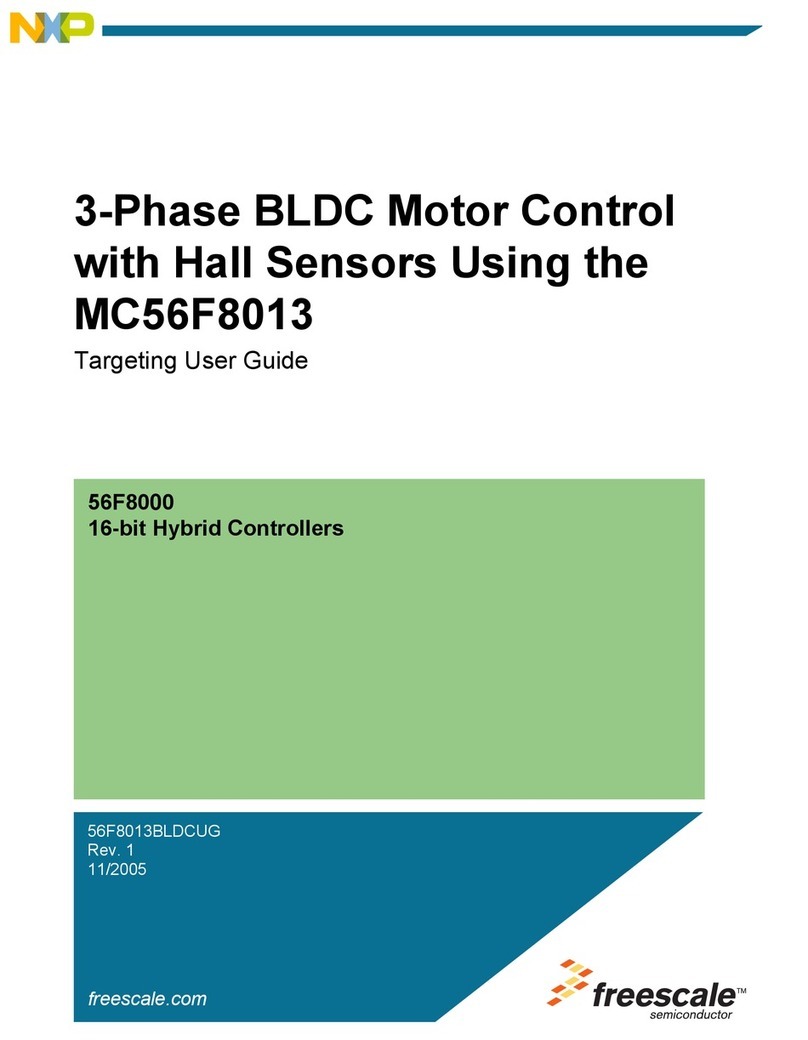
NXP Semiconductors
NXP Semiconductors MC56F8013 Targeting User Guide