EMC 880 User manual

EMC 880
Kiln Controller
880 Operation Manual Issue 7 EMC INDUSTRIAL GROUP LTD
Operation Manual
Software Revision 2.0 to 2.7

880 Operation Manual Issue 7 EMC INDUSTRIAL GROUP LTD Page 2 of 25
COPYRIGHT © 2001 by EMC Industrial Group Ltd
56 Tarndale Grove, Albany, Auckland
PO Box 101 444 NSMC, Auckland, New Zealand
Telephone +64-9-415 5110, Facsimile +64-9-415 5115
E-mail [email protected]z
Web http://www.emc.co.nz/
As we are continuously improving our products, changes to this specification
may occur without notice.

Contents
880 Operation Manual Issue 7 EMC INDUSTRIAL GROUP LTD Page 3 of 25
Contents
Contents .................................................................................................................. 3
Introduction............................................................................................................. 5
About this manual........................................................................................... 5
Please Read................................................................................................... 5
Quick Firing Guide.................................................................................................. 6
Establish Firing Program ................................................................................ 6
Store a Bisque Firing as Program 1 ............................................................... 6
Start Bisque Firing Instantly ........................................................................... 6
Delay Start Bisque Firing By 3 Hours............................................................. 6
Operation of Controller .......................................................................................... 7
Operation Overview........................................................................................ 7
Enter a Program ............................................................................................. 7
Select a Program ................................................................................. 7
Set Ramp 1 .......................................................................................... 7
Set Temperature 1 ............................................................................... 8
Set Hold 1............................................................................................. 8
Set Stage 2 Through To Stage 6 ......................................................... 8
Set Vent Close Set Point...................................................................... 8
Set Vent Open Set Point...................................................................... 9
Start a Firing................................................................................................... 9
Instant Start.......................................................................................... 9
Delayed Start........................................................................................ 9
Stage Start ......................................................................................... 10
During a Firing.............................................................................................. 10
Keys.............................................................................................................. 11
RUN STOP Key.................................................................................. 11
Menu (Next) Key ................................................................................ 11
Control Temp (Down) Key.................................................................. 11
Time To Go (Up) Key......................................................................... 11
Alarm Cancel (Exit) Key..................................................................... 12
Indicator Lights ............................................................................................. 12
Heat Light........................................................................................... 12
Vent Light ........................................................................................... 12
Run Stop Light.................................................................................... 12
Menu Light.......................................................................................... 12
Alarm Light ......................................................................................... 12
°C/h Ramp Light................................................................................. 12
°C Temp Light .................................................................................... 12
h.m Hold Light .................................................................................... 12
Display.......................................................................................................... 12
Large Display ..................................................................................... 12
Small Display...................................................................................... 13
Beeper .......................................................................................................... 13
Power Up Test.............................................................................................. 13
Power Failure ............................................................................................... 13
Firing Auto Continues When Power Returns ..................................... 14
Firing Does Not Resume When Power Returns ................................ 14
Alarms.................................................................................................................... 15
Alarm List...................................................................................................... 15
Fault Diagnostics.......................................................................................... 17

Contents
880 Operation Manual Issue 7 EMC INDUSTRIAL GROUP LTD Page 4 of 25
Typical Faults List......................................................................................... 17
Installation............................................................................................................. 19
Dimensions................................................................................................... 19
Mounting....................................................................................................... 19
Wiring ........................................................................................................... 19
Cable Separation.......................................................................................... 19
Power Supply ..................................................................................... 20
Electrical Interference Suppression of Relay Outputs ....................... 20
Heat Relay.......................................................................................... 20
Heat Logic for Solid State Relay ........................................................ 20
Run Relay (Option) ............................................................................ 20
Vent Relay (Option)............................................................................ 20
Alarm Relay (Option).......................................................................... 21
Thermocouple .................................................................................... 21
Resistance Thermometer – 3 Wire .................................................... 21
Resistance Thermometer – 2 wire ..................................................... 21
Field Settings ........................................................................................................ 22
Enter Field Setting Mode.................................................................... 22
Field Settings Table ........................................................................... 22
Input Sensor ................................................................................................. 22
Set Input Sensor Type Code Number Step 01 .............................. 22
Demo Mode.................................................................................................. 23
Set Demo Mode Step 02 ............................................................... 23
Auto-Continue............................................................................................... 23
Set Auto-Continue Step 21 ............................................................ 23
Hold Temperature Setting Limits.................................................................. 23
Set Maximum Hold Temperature Step 23 ..................................... 23
Set Minimum Hold Temperature Step 24 ....................................... 23
Loss of Control Timeout ............................................................................... 24
Set Loss of Control Timeout Step 25.............................................. 24
Auto Simmerstat........................................................................................... 24
Automatic Simmerstat Temperature For Full Power Step 44......... 24
SPECIFICATIONS ..................................................................................... 25
Program Settings.......................................................................................... 25
Field Settings................................................................................................ 25
Inputs.................................................................................................. 25
Other Settings .................................................................................... 25
Outputs......................................................................................................... 25
General......................................................................................................... 25
ORDERING..................................................................................................... 25

Introduction
880 Operation Manual Issue 7 EMC INDUSTRIAL GROUP LTD Page 5 of 25
Introduction
About this manual
This manual is divided into several main sections to help find specific information
quickly. For example, to find detailed information about the different methods of
starting a firing see Start a Firing,page 9.
A good way to know the EMC 880 once the controller has been installed, as de-
tailed in section Installation, page 19, is simply to try it.
Turn on power and follow the simple step by step procedure in the section called
Quick Firing Guide,page 6.
As questions arise about the controllers operation refer to the appropriate section
in this manual.
Please Read
Before the kiln is fired for the first time it is very important to check the input of the
controller matches the thermocouple used.
If these do not match the kiln may over fire and cause a melt down. For instance
the kiln will over fire if the controller is set for a type K thermocouple but a type R
thermocouple is used.
To check controller:
Watch the display for the input sensor type when power is turned on as de-
tailed in Power Up Test, page 13. To change the controller to another input
sensor type refer to Field Settings, page 22.
To check thermocouple:
See if the type code is written on the probe, i.e. look under the terminal cover,
otherwise consult kiln supplier.
Check ambient temperature:
After the power up test sequence check controller is showing ambient air tem-
perature, which normally is about 20°C to25°C.
As a precautionary measure the first firing should be observed to ensure firing pro-
gresses as expected.

Quick Firing Guide
880 Operation Manual Issue 7 EMC INDUSTRIAL GROUP LTD Page 6 of 25
Quick Firing Guide
Follow the procedure below to program the controller for a Bisque firing, stored as
Program 1, and then start the firing.
Establish Firing Program
Draw the temperature profile required and write down program values as shown on
the diagram and chart below, and then enter these values into the controller.
Store a Bisque Firing as Program 1
Step Action Display
1. Press MENU key. Display shows currently selected program. ?
2. Set program number in large display with the UP or DOWN keys.
3. Press NEXT key and set Stage 1 Ramp to .
4. Press NEXT key and set Stage 1 Temperature to .
5. Press NEXT key and set Stage 1 Hold to .
6. Press NEXT key and set Stage 2 Ramp to .
7. Press NEXT key and set Stage 2 Temperature to .
8. Press NEXT key and set Stage 2 Hold to .
9. Press NEXT key and set Stage 3 Ramp to .
10. Press NEXT key and set Stage 3 Temperature to .
11. Press NEXT key and set Stage 3 Hold to .
12. Press EXIT to return to normal operation and show ambient temperature.
Start Bisque Firing Instantly
1. Check small display shows program you want to use, in this case program 1.
2. Press RUN STOP key to start firing.
Delay Start Bisque Firing By 3 Hours
1. Check small display shows program you want to use, in this case program 1.
2. Press RUN STOP key and while light is flashing set large display to .
Firing Type Bisque Program Number 1
RAMP TEMP HOLD
STAGE 1 50°C per hr 150°C none
STAGE 2 100°C per hr 650°C none
STAGE 3 150°C per hr 950°C 15 min
RAMP
RAMP 150°C/hr
RAMP 50°C/hr
TEMP 150°C
TEMP 650°C
TEMP 950°C
STAGE 1
STAGE 2
STAGE 3
TEMPERATURE
TIME
HOLD 15 minutes

Operation of Controller
880 Operation Manual Issue 7 EMC INDUSTRIAL GROUP LTD Page 7 of 25
Operation of Controller
This section gives an overview on how to operate the controller, describes in detail
how to enter programs into the controller, how to start a firing and what can be
done while firing is in progress, explains the function of keys, indicator lights, dis-
play and the internal beeper, describes what to look for when power is turned on
and finally how the controller recovers from a power failure.
Operation Overview
The Kiln Controller is very easy to use.
When power is applied the display sequentially shows a display test to verify the
controller is working correctly. See Power Up Test, page 13.
Before firing can commence the correct program values must be entered into at
least one of the nine program storage containers.
A program has up to six stages. Each stage has a ramp setting, a temperature set-
ting and a hold setting. When firing is started the temperature climbs at the ramp
rate to the Hold Temperature and is maintained there for the Hold Time before ad-
vancing to the next stage.
If a ramp rate is not required, the ramp setting can be set to . The controller
will then bring the kiln to the Hold Temperature as fast as possible.
If a stage needs to be kept at the Hold Temperature indefinitely, the hold setting
can be set to . The controller will then maintain temperature until stopped
with the RUN STOP key.
If a stage is not required, the temperature setting can be set to . The pro-
gram will then skip onto the next stage.
To jump to the end of a program and skip all remaining unused stages set the
ramp setting of the next stage after the last programmed stage to .
To commence a firing ensure the correct program number is showing in the small
display, for example is program one, then press the RUN STOP key. The firing
can also be delay started or stage started, see Start a Firing, page 9.
Once started, the kiln temperature will follow the temperature profile of the selected
program. See During a Firing, page 10.
During the firing, settings of the program can be checked and changed, other
stored programs can be changed or new programs can be entered.
When completed the alarm beeps five times and shuts power off to the kiln.
Enter a Program
How to select a program and enter a program value is explained in the following
sections. Enter program mode by pressing the MENU key. Return to normal mode
by pressing the EXIT key.
Select a Program
Press MENU key.
Large display shows current program number.
Use UP or DOWN keys to select a new program number.
Set Ramp 1 Press and release MENU key until the small display flashes .
Large display shows the ramp rate for stage 1 or shows or .
means the kiln temperature will ramp as fast as possible to the set tem-
perature.
means the controller will skip to the end of the program bypassing the re-
maining stages and will not display other stage settings past this point except the
vent close and vent open settings, and .

Operation of Controller
880 Operation Manual Issue 7 EMC INDUSTRIAL GROUP LTD Page 8 of 25
Use UP or DOWN keys to set the required ramp rate, or hold down the UP key un-
til display shows . Press DOWN once to set it to or press it twice to
select 3200, which is the largest ramp number that can be set.
Alternatively, pressing the UP and DOWN keys together will cycle between a ramp
rate of 100°C/h, the setting and the setting .
Set Temperature 1
Press and release MENU key until the small display flashes .
Large display shows either the maximum temperature kiln will climb to during stage
1 or show . means bypass stage 1 completely.
Use UP or DOWN keys to set the required temperature value, which must be be-
tween the setting limits, see Hold Temperature Setting Limits, page 23, or hold
down the UP key until display shows .
Alternatively, pressing the UP and DOWN keys together will cycle between a value
of half the Maximum Hold Temperature, see Hold Temperature Setting Limits,
page 23, and the setting .
Set Hold 1 Press and release MENU key until the small display flashes .
Large display shows length of time kiln temperature will be held for at stage 1 tem-
perature setting or show the word . means the kiln will be held at
stage 1 temperature setting until the START/STOP key is pressed to stop the fir-
ing.
Use UP or DOWN keys to set required hold period, up to a maximum of 54 hours,
or set to by holding down the UP key until display shows .
Alternatively, pressing the UP and DOWN keys together will cycle between a hold
time of 0.00 and the setting .
Set Stage 2 Through To Stage 6
Entering setting values for Stage 2 through to stage 6 is the same as described for
stage 1.
Set Vent Close Set Point
The Vent Close Set Point value is only shown in the display if relay option card OP-
1 is fitted.
Press and release MENU key until the small display shows .
The large display shows either the close vent set point or and the VENT light
will be flashing.
If the close vent set point is exceeded by the kiln temperature the Vent light will
turn off and the Vent will shut.
The vent limits do not operate when the setting is set to .
Use UP or DOWN keys to set the required close vent temperature value, which
must be between the setting limits, see Hold Temperature Setting Limits, page
23, or set to by holding down the UP key until display shows .
Alternatively, pressing the UP and DOWN keys together will cycle between half the
Maximum Hold Temperature, see Hold Temperature Setting Limits, page 23,
and the setting .
Press EXIT key to return to normal operation.
Note At power on, the Vent is always opened. When the RUN key is
pressed (or firing is Auto Continued after a power failure) the vent re-
mains open, unless the current kiln temperature exceeds the tem-
perature.

Operation of Controller
880 Operation Manual Issue 7 EMC INDUSTRIAL GROUP LTD Page 9 of 25
Set Vent Open Set Point
The Vent Open Set Point value is only shown in the display if relay option card OP-
1 is fitted.
Press and release MENU key until the small display shows .
The large display shows either the open vent set point or and the VENT light
will be flashing.
If the kiln temperature falls below the open vent set point after the firing is com-
pleted, the Vent light will turn on and the vent will open.
The vent limits do not operate when the setting is set to .
Use UP or DOWN keys to set the required open vent temperature value, which
must be between the setting limits, see Hold Temperature Setting Limits, page
23, or set to by holding down the UP key until display shows .
Alternatively, pressing the UP and DOWN keys together will cycle between half the
Maximum Hold Temperature, see Hold Temperature Setting Limits, page 23,
and the setting .
Press EXIT key to return to normal operation.
Start a Firing
Before starting a firing, either select one of the nine programs if they have been
previously entered or enter a new program as detailed in Enter a Program,page
7.
To view the total firing duration of this program press the TIME TO GO key, before
starting the firing.
There are three ways the firing can be started.
Instant Start Starts from the beginning of a program.
Delayed Start Starts automatically after a time delay.
Stage Start Starts from any stage of the program.
Each section is described in detail below.
Note When the firing has started, the HEAT light will turn on and off at dif-
ferent times to regulate the kiln temperature.
If the kiln temperature is too low the HEAT light will turn on. This indi-
cates power has been applied to the kiln's heating elements to in-
crease the temperature.
If the kiln temperature is too high the heat light will turn off. This indi-
cates power has been cut off to the kiln’s heating elements to allow
the temperature to fall.
Instant Start This is the simplest way of starting the firing.
Press the RUN STOP key.
The small display shows and the RUN STOP light fast flashes for five seconds.
When the RUN STOP light stops flashing the small display will show the first ramp
number, the heat light will turn on, and the firing will start.
Delayed Start A delayed start allows a firing to be started after a delay of up to 99 hours and 59
minutes from when the START/STOP key was pressed.
Press the RUN STOP key.
The small display shows and the RUN STOP light fast flashes for five seconds.
During the five seconds set the large display to the delay start time required.
At the end of the five seconds the small display comes on steady and the RUN
STOP light slow flashes to indicate there is a delayed start in progress.

Operation of Controller
880 Operation Manual Issue 7 EMC INDUSTRIAL GROUP LTD Page 10 of 25
The large display shows remaining time to go before firing will commence.
The delay start time can be altered while timing out.
When the time gets to the small display will show the first ramp or tempera-
ture stage number, the heat light will turn on, the RUN STOP light will come on
steady and the firing will start.
To cancel a delayed start when in progress, press the RUN STOP key.
NOTE If power fails during this delay period and the Auto Continue feature
has been enabled, the countdown to the start of firing will continue
when power is restored, but the start time will be extended by the time
power was off.
Stage Start The Stage Start method allows a firing to be started instantly from any point within
the program.
Use the MENU key to step through the program until the small display shows the
desired starting point.
The MENU light will be on and the small display will be fast flashing.
Press the RUN STOP key.
The MENU light will be on and the START/STOP light will fast flash for five sec-
onds.
Press the RUN STOP key again during the five-second time out. Two long beeps
will sound, the heat light will turn on, and the small display and the RUN STOP light
will come on steady indicating the firing has started.
Warning If the key is not pressed, during this time out, the firing will start from
the beginning of the program.
Check the small display is showing the correct starting point in the program.
During a Firing
Once the firing is started, the kiln controller generates a temperature profile calcu-
lated from the ramp, temperature and hold settings of each stage.
Any of these settings can be adjusted during the firing to change the temperature
profile.
As the program advances, the Control Temperature follows the temperature profile
exactly.
The Heat output is turned on and off to make the kiln temperature follow the Con-
trol Temperature.
If the kiln temperature is less than the Control Temperature, heating is switched on,
if the kiln temperature is higher heating is switched off.
To see the current Control Temperature press the CONTROL TEMP key at any
time during a firing.
To view the remainder of the total firing time press and hold the TIME TO GO key
for longer than 3 seconds.
When the small display shows … the kiln temperature is ramping up to the set
temperature and the time to finish this ramp can be viewed by pressing the TIME
TO GO key.
At lower temperatures, the kiln temperature will follow the Control Temperature
very closely, but at higher temperatures the kiln temperature may fall behind the
Control Temperature, especially if the ramp rate is too high or the heating elements
are getting old.
If the Control Temperature reaches the set temperature and the kiln temperature is
lagging behind, the mnemonic … will show in the small display indicating the pro-
gram is paused while waiting for the kiln temperature to catch up.

Operation of Controller
880 Operation Manual Issue 7 EMC INDUSTRIAL GROUP LTD Page 11 of 25
If the TIME TO GO key is pressed, when … is showing, the display will show
.
When the kiln temperature is within 5°C of the Hold Temperature the kiln will either
be held at this temperature for the hold period or will move into the start of the next
stage if no Hold Time has been set for this stage.
To view how much time remains to the end of the current hold period, press the
TIME TO GO key while the small display is showing ….
When all stages of the program have been completed the firing will be stopped and
five long beeps indicate the program is finished.
Keys There are two basic modes of operation, normal mode and programming mode.
•The controller is in programming mode after the MENU key has been pressed,
and up until the EXIT key is pressed. In this mode key functions are identified
by the blue captions.
•All other times the controller is considered to be in normal mode and functions
are identified by the caption on the key except when using the UP and DOWN
keys to set the delayed start time.
RUN STOP Key
Starts or stops a firing when pressed. When started the light fast flashes for five
seconds to allow setting (with the UP or DOWN keys) the delay start period. If a
delay start period is set, after the five-second-entry time, the RUN STOP light will
change to slow flashing to indicate the controller is waiting to start at the end of this
period. The delay time can be altered while waiting to start.
Menu (Next) Key
Used to go into the programming mode.
First press will display the current program number, further presses step through
each setting of the current program.
During a firing this key can be used to view or change settings of the current pro-
gram and also to view or changed settings of other stored programs or enter new
programs.
Control Temp (Down) Key
This key has two functions;
•When programming or setting the Delayed Start Time, press to decrease the
value of the selected setting. Alternatively to toggle between preset values
and the instruction words press the UP and DOWN keys together.
Toggle settings are;
Ramp Rate 100°C/hr, FAST and End,
Temperature Half the Maximum Hold Temperature of a stage, see Hold
Temperature Setting Limits, page 23, and PASS,
Hold 0hr 00min and Hold.
•When firing, press to display the Control Temperature.
Time To Go (Up) Key
This key has six functions.
•When programming or setting the Delayed Start Time, press to increase the
value of the selected setting. Alternatively to toggle between preset values
and the instruction words press the UP and DOWN keys together.
Toggle settings are the same as for the CONTROL TEMP (DOWN) key.
•When not firing, press to show the total firing time.
•When firing press and hold key down for three seconds to show the remaining
firing time.

Operation of Controller
880 Operation Manual Issue 7 EMC INDUSTRIAL GROUP LTD Page 12 of 25
•When firing and small display shows … press to show how much time re-
mains to the end of the current ramp.
•When firing and small display shows … press to show how much time re-
mains to the end of the current hold period.
•When firing and small display shows … pressing this key will show in
the large display.
… indicates the Control Temperature has reached the set temperature and
the kiln temperature is lagging behind because there is not enough power go-
ing in to the kiln to keep its temperature up with the ramp rate setting.
Alarm Cancel (Exit) Key
This key performs two functions, alarm cancel and exit programming.
•When an alarm has occurred press to acknowledge the alarm and mute the
internal beeper and display the alarm number. See Alarm List, page 15 for
alarm numbers.
•Press to return to normal operation after programming.
Indicator Lights
Heat Light Turns on when heat is being applied to the kiln.
Vent Light Turns on when kiln is venting. The Vent output is available only if option OP-1 relay
card has been fitted. If the Close Vent and Open Vent settings are both set
to , see Set Vent, page 8, the vent light will remain off.
Run Stop Light
Turns on when controller is running a program. If the controller has been set for a
delayed start, the Run Stop light will flash slowly during the delay countdown.
Menu Light Turns on when controller is in programming mode and indicates keys marked with
blue captions are used to select and change settings.
Alarm Light The Alarm light flashes’ indicating the controller has detected a problem. When the
ALARM CANCEL key is pressed, the internal beeper is muted, and, if the problem
is still present, the Alarm light becomes steady, or goes off if the problem has
gone.
°C/h Ramp Light
Turns on when large display is showing a ramp rate.
°C Temp Light Turns on when large display is showing a temperature.
h.m Hold Light
Turns on when large display is showing time in hours and minutes.
Display
Both Displays
•After a power failure both displays flash indicating firing has not resumed. See
Firing Does Not Resume When Power Returns, page 14.
Large Display
•In normal operation it shows the kiln temperature.
•When programming, it shows the value of the selected setting.

Operation of Controller
880 Operation Manual Issue 7 EMC INDUSTRIAL GROUP LTD Page 13 of 25
•When an alarm occurs, the alarm number mnemonic is shown if the ALARM
CANCEL key is pressed. See Alarm List, page 15.
Small Display
•When the controller is stopped it shows the program number.
•When the controller is running, it shows the current stage number. For exam-
ple, if the program has got to the ramp of stage 2, the display shows r2.
•When programming, it flashes and shows the stage number of the setting
value shown in the large display.
•When an alarm occurs, the alarm number is shown if the ALARM CANCEL
key is pressed. See Alarm List, page 15.
Beeper The internal beeper is used as an audible indication for three events.
•When any key is pressed a single beep indicates a valid key press has been
entered.
•Five long beeps indicate the firing is completed.
•If any alarm occurs bursts of five fast beeps are repeated until the ALARM
CANCEL key is pressed to acknowledge the presence of an alarm.
Power Up Test
When the controller is powered up, the displays sequentially show a display test,
the software revision number and model number, the code of an option card if fitted
and finally shows the sensor code and type of sensor the controller has been set
for.
Power Up
Sequence
Description of Displayed Information
1 All display segments and indicator lights turn on normally but if unit
has been set to Demo Mode, see Demo Mode, page 23, the large
display shows !with all indicator lights on.
2 Small display shows software revision number and large display
shows model number. eg "
##.
3 If option card OP-1 is fitted large display shows $.
4 Small display shows input sensor code number and large display
shows sensor type.
Input Sensor Type Displayed Code Number & Mnemonic
J T/C %
K T/C
N T/C &
R T/C "'
T T/C
PT100 RTD '
5 Normal operating display. Small display shows program number and
large display shows kiln temperature. eg
If any segment or light does not turn on or the display is blank and the beeper
sounds or the display shows (, the unit is faulty and should be returned
for service.
Power Failure
If power fails during a firing, the controller remembers what it was doing at that
time.
The controller has been factory set to automatically continue the firing from the
point in the temperature profile at which power failed.

Operation of Controller
880 Operation Manual Issue 7 EMC INDUSTRIAL GROUP LTD Page 14 of 25
Alternatively the controller can be set to stop firing when power returns and show
at what stage during the firing power failed. The firing must then be either manually
restarted, or cancelled.
Firing Auto Continues When Power Returns
To automatically resume firing when power is restored, the Auto Continue field set-
ting must be set &. See Auto-Continue page 23.
If power failed during the delay start count down or at any other time during the fir-
ing, the program will automatically resume and continue from where it left off when
power returns. The ALARM light flashes to indicate there has been a power failure.
Note this is the only alarm where the internal beeper does not sound and, if option
OP-1 relay card is fitted, the Alarm Relay contacts do not close.
Press the ALARM CANCEL key to clear the alarm. When this key is pressed and
held, the display will show the alarm number )* confirming a power failure
occurred.
NOTE If power failed during the hold period of a stage, the controller auto-
matically resumes firing in the ramp section of that stage. This en-
sures that the kiln temperature is brought back to the hold tempera-
ture at a controlled rate. Once the kiln is back at hold temperature, the
controller resumes holding for the remaining hold time.
Firing Does Not Resume When Power Returns
To prevent firing resuming when power is restored, the Auto Continue field setting
must be set . See Auto-Continue,page 23.
When power returns, the ALARM light and display flash and the internal beeper
sounds to indicate that a power failure occurred. The small display shows during
which program stage power failed, eg for Hold 2, or will show if it happened
through the delayed start. The large display shows the current kiln temperature.
If option OP-1 relay card is fitted, the Alarm Relay contacts close to sound an ex-
ternal alarm device if fitted.
Press the ALARM CANCEL key to mute the beeper and open the Alarm Relay
contacts. While pressing this key, the display will show alarm number )*
confirming fault was a power failure.
To continue with the firing, press the RUN STOP key. To cancel the firing, press
the RUN STOP key a second time.
NOTE If the MENU key is pressed, from the time power is restored after a
failure up until the RUN STOP key is pressed, its function will be ig-
nored and if the CONTROL TEMP key is pressed during this time the
large display will show .

Alarms
880 Operation Manual Issue 7 EMC INDUSTRIAL GROUP LTD Page 15 of 25
AlarmsEMC kiln controllers have proven over a number of years to be very reliable. How-
ever there are times when things do go wrong with an installation.
The controller has an inbuilt comprehensive monitoring system designed to avoid
kiln melt down.
If a fault occurs an internal audible beeper is sounded and the firing cycle will either
be paused, allowing the cycle to continue if the fault can be cleared, or the firing
cycle will be stopped. The Alarm light flashes to indicate that the controller has de-
tected a problem.
If option OP-1 relay card is fitted the ALARM contact, which can be used to sound
an external alarm device, will close until the alarm is acknowledged and the RUN
contact is opened and remains open until the firing is re started.
To acknowledge the alarm press the ALARM CANCEL key.
When the ALARM CANCEL key is pressed, the internal beeper is muted, and the
Alarm light turns on steady if the problem is still present, or turns off if the problem
has gone. While the ALARM CANCEL key is held down, the alarm number and
alarm mnemonic are shown in the display.
The Alarm List below shows, for each alarm number, what the large and small dis-
plays are showing, what state the controller is in, the likely cause of the fault and
the fault remedy.
To help short cut other problems not detected by the alarm system, a Typical
Faults List has been compiled of common faults, with separate columns for easy
identification of the Fault, the Cause and the Remedy.
Alarm List
SMALL DISPLAY Shows
point in program where
power failed (eg )
LARGE DISPLAY
Shows current kiln tempera-
ture
CONTROLLER STATE
Controller is paused (only
if Auto Continue is set to
). Heat is OFF
CAUSE Mains power failed during a firing or delayed start.
ALARM
NUMBER
Press alarm
key to view
)*
REMEDY Press RUN STOP once to continue firing, or twice to cancel firing.
SMALL DISPLAY Not af-
fected LARGE DISPLAY
Shows (over-range)
CONTROLLER STATE
Heat is OFF
CAUSE Thermocouple burnout or thermocouple wiring break
ALARM
NUMBER
Press alarm
key to view
REMEDY Check the thermocouple and wiring by turning power off to the controller and
strap terminals 14 and 15 together with a wire link. Turn power on. If the display shows
ambient temperature, i.e. approximately 25°C, the thermocouple probe or it’s wiring is
faulty. If the display still shows the controller is faulty and should be returned to the
supplier with a written description of the fault.
SMALL DISPLAY Not af-
fected LARGE DISPLAY
Shows (under-range) CONTROLLER STATE
Heat is OFF
CAUSE Thermocouple reverse connected
ALARM
NUMBER
Press alarm
key to view
REMEDY Check thermocouple connections. See Thermocouple,page 21.

Alarms
880 Operation Manual Issue 7 EMC INDUSTRIAL GROUP LTD Page 16 of 25
SMALL DISPLAY Shows
point in program where over-
load detected (eg )
LARGE DISPLAY
Shows current kiln tempera-
ture
CONTROLLER STATE
Controller is paused,
Heat is OFF
CAUSE Kiln temperature is greater than the Maximum Hold Temperature setting. Possi-
bly due to welded contacts on the kiln’s contactor
ALARM
NUMBER
Press alarm
key to view
REMEDY Check and repair kiln contactor. Press RUN STOP once to continue firing, or
twice to cancel firing.
SMALL DISPLAY Shows
point in program where loss
of control detected (eg )
LARGE DISPLAY
Shows current kiln tempera-
ture
CONTROLLER STATE
Controller is paused,
Heat is OFF
CAUSE Kiln temperature has been higher than the Control Temperature for more than
1 hour1and is rising at more than 20°C per hour. Possibly due to welded contacts on the
kiln’s contactor.
ALARM
NUMBER
Press alarm
key to view
REMEDY Check and repair kiln contactor. Press RUN STOP once to continue firing, or
twice to cancel firing.
SMALL DISPLAY Shows
point in program where loss
of control detected (eg )
LARGE DISPLAY
Shows current kiln tempera-
ture
CONTROLLER STATE
Controller is paused,
Heat is OFF
CAUSE Kiln temperature has been higher than the Control Temperature for more than
1 hour1and is not falling and is still rising. Possibly due to welded contacts on the kiln’s
contactor.
ALARM
NUMBER
Press alarm
key to view
REMEDY Check and repair kiln contactor. Press RUN STOP once to continue firing, or
twice to cancel firing.
SMALL DISPLAY Shows
point in program where loss
of control detected (eg )
LARGE DISPLAY
Shows current kiln tempera-
ture
CONTROLLER STATE
Controller is paused,
Heat is OFF
CAUSE Kiln temperature has been lower than the Control Temperature for more than
1 hour1and is rising at less than 20°C per hour. Due to weak elements, low mains volt-
age, probe not fully inserted into the kiln or kiln overloaded.
ALARM
NUMBER
Press alarm
key to view
REMEDY Check and replace faulty elements, check mains voltage, push probe fully into
the kiln, remove some work from the kiln. Press RUN STOP once to continue firing, or
twice to cancel firing.
SMALL DISPLAY Shows
point in program where loss
of control detected (eg )
LARGE DISPLAY
Shows current kiln tempera-
ture
CONTROLLER STATE
Controller is paused,
Heat is OFF
CAUSE Kiln temperature has been lower than the Control Temperature for more than
1 hour1and is falling at more than 20°C per hour. Due to failed elements, low mains volt-
age.
ALARM
NUMBER
Press alarm
key to view
REMEDY Check and replace faulty elements, check mains voltage. Press RUN STOP
once to continue firing, or twice to cancel firing.
1This time period can be altered or the alarm turned off. See Loss of Control Timeout on page 24.

Alarms
880 Operation Manual Issue 7 EMC INDUSTRIAL GROUP LTD Page 17 of 25
SMALL DISPLAY Shows
program number (eg )
LARGE DISPLAY Shows
current kiln temperature CONTROLLER STATE
Controller is stopped
CAUSE Electrical interference disrupted operation of controller or controller is faulty.
ALARM
NUMBER
Press alarm
key to view
REMEDY Check Thermocouple is separated from power cabling as described in
Cable Separation, page 19 or, if fault cannot be cleared, return to supplier with a written
description of fault and the fault alarm number.
Clock fail reset
Watch dog reset
Bad instruction reset
"
Unexpected interrupt reset
A/D fail
+
EEPROM fail
, Requires factory calibration
Fault Diagnostics
When a fault occurs there are several values that should be looked at before the
firing is stopped or power is turned off.
This information will be useful to a service person to help with fault location at a
later date.
•Check program is correct.
•Note what stage firing is at. This is shown in small display.
•Note kiln temperature.
•Note control temperature by pressing the CONTROL TEMP key.
•Check if heat light is on or is being turned on and off.
•Check, if possible, power is applied to the elements when heat light is on.
•Note alarm number by pressing ALARM key. See Alarms, page 15.
•Note current kiln temperature ramp rate by pressing together the DOWN and
the ALARM keys.
•Check and apply remedy if fault is listed in Typical Faults List below.
Typical Faults List
FAULT CAUSE REMEDY
Kiln over fires by up to
100°C. Thermocouple com-
pensating lead re-
verse connected.
Check the thermocouple connection. See
Thermocouple, page 21.
Displays and lights frozen
and no response from
any key press.
Electrical interfer-
ence or component
failure has locked out
the controller.
Check Thermocouple is separated from power
cabling as described in Cable Separation,page
19. Turn power off then on to restart controller. If
controller does not respond return to supplier with
a description of fault.
Heat light is on but kiln
temperature is not in-
creasing.
Mains power not
connected to heating
elements.
Check kiln door is closed properly, heating con-
tactor has operated, main supply switch is on and
the heater fuses are okay.
None of the indicator
lights illuminate and the
display remains blank
after mains power is
switched on.
Mains power is not
connected to control-
ler.
Check supply fuse and that power is on the con-
troller terminals. If power is okay the controller
may be faulty and should be returned to the sup-
plier with description of fault.

Alarms
880 Operation Manual Issue 7 EMC INDUSTRIAL GROUP LTD Page 18 of 25
On power up, both dis-
plays are blank, the alarm
light is on and the beeper
sounds.
Controller is faulty. Return to supplier with a description of fault.
On power up some of the
display segments or
some of the indicator
lights do not turn on as
described in Power Up
Test, page 13.
Controller is faulty. Return to supplier with a description of fault.

Installation
880 Operation Manual Issue 7 EMC INDUSTRIAL GROUP LTD Page 19 of 25
Installation
This section provides information on mounting the controller, and wiring require-
ments, including details of good wiring practice to avoid the controller malfunction-
ing from electrical interference.
Take particular note of the two WARNING paragraphs in the wiring section.
EMC recommends that a qualified electrician install the unit to ensure all electrical
safety requirements are met.
Dimensions
Mounting The controller has plug-in screw terminals at the rear.
Install the unit in a 92 x 45 mm cut out in a position where it is easy to read and
operate, and where the case temperature will not rise above 45°C.
Wiring
Cable Separation
WARNING Power and Thermocouple cabling must be separated by at least 50mm.
To avoid malfunction of the controller it is essential that all power and control ca-
bling is run separately and at least 50mm away from the thermocouple wiring.
PANEL CUT OUT
92 x 44 +0.6
–
0.0mm
TOP
VIEW
100mm
8mm
48mm
FACIA
96mm
RUN
VENT
AC SUPPLY
5VA max
ALARM
T/C
+5V
-
+
24
23
16
17
18
19
20
21
22
L
N
8
9
10
11
12
13
14
15
0V
With Solid State Switch
HEAT
LOGIC
-
+
+
-
Kiln door
safety interlock
Kiln
Fuse
Isolator
L
N
230Vac Supply
Solid State
Switch
+
-
50mm cable separation
Fuse
With Contactor
0.1uF + 100E
suppression
capacitor
Kiln
door
safety interlock
Contactor
50mm cable
separation
HEAT
LOGIC
-
+
+
-
Kiln
Fuse
Isolator
L
N
230Vac Supply
Fuse
RUN
VENT
AC SUPPLY
5VA max
ALARM
T/C
+5V
-
+
24
23
16
17
18
19
20
21
22
L
N
8
9
10
11
12
13
14
15
0V

Installation
880 Operation Manual Issue 7 EMC INDUSTRIAL GROUP LTD Page 20 of 25
Power Supply Connect supply phase to terminal L and supply neutral to terminal N.
Power requirement is 5VA maximum.
WARNING Before switching power on to controller, check supply voltage rating
shown on the back panel, is correct for your mains power supply.
Electrical Interference Suppression of Relay Outputs
Inductive loads, such as the heat contactor coil used to switch power to kiln ele-
ments, connected to any of the relay contacts must have a suppression capacitor
fitted across the coil.
This is to suppress the large back EMF randomly generated when switching off the
contactor.
The fast changing back EMF voltage can couple into the controllers wiring which
may crash the microcontroller causing an alarm, to or (. See
Alarm List, page 15.
Use supplied suppression capacitor, RS Components Part Number 238-299 or an
equivalent connected across the heat contactor coil.
Warning Do not connect capacitor across output relay contacts.
If relay option card OP-1 is fitted any inductive loads connected to the outputs
should have suppression capacitors fitted.
Heat Relay Link terminal 8 to supply phase, terminal L, and connect terminal 9 via the door in-
terlock micro switch to the contactor coil. The other end of the coil connects to neu-
tral.
The contacts close if the kiln temperature is lower than the Control Temperature by
more than 2°C any time the program is running other than when there is an alarm.
Heat Relay contacts are on terminals 8 and 9 and are rated 240Vac, 2 amp load.
Link terminal 8 to supply phase, terminal L, and connect terminal 9 via the door in-
terlock micro switch to the contactor coil. The other end of the coil connects to neu-
tral.
Heat Logic for Solid State Relay
Out 1 Logic signal (5V at 20mA max) are on terminals 11 and 12.
Terminal 11 is positive and terminal 12 is negative.
This output, which operates when heat is called for, can be used for connection to
solid-state relays.
Run Relay (Option)
Run Relay contacts are on terminals 16 and 17 and are rated at 240Vac, 2 amp
load.
When firing starts, the contacts close and remain closed (except during a power
failure or alarm) for the duration of the firing. At the end of firing the contacts open.
This output may be used as the master cut-off control switch in gas fired kilns.
Vent Relay (Option)
Vent Relay contacts are on terminals 18 and 19 and are rated at 240Vac, 2 amp
load.
When the kiln temperature exceeds the programmed value , the contacts close
to close the vent. The contacts will only open again to open the vent when the firing
has ended and the kiln temperature has dropped below the programmed value
.
Note At power on, the Vent is always open. When the RUN key is pressed
(or firing Auto Continues) the vent is opened, unless the current kiln
temperature has exceeded the temperature.
Table of contents
Other EMC Controllers manuals
Popular Controllers manuals by other brands
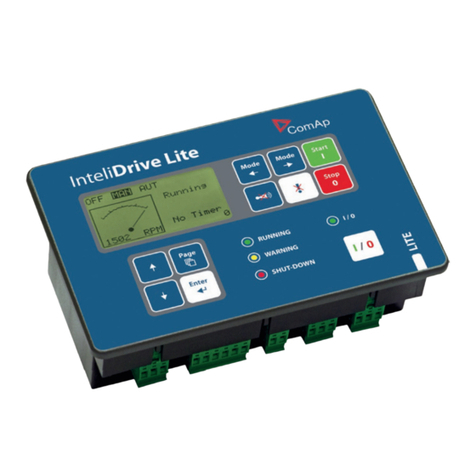
ComAp
ComAp InteliDrive Lite user guide

Enerpac
Enerpac RFL-102 instruction sheet
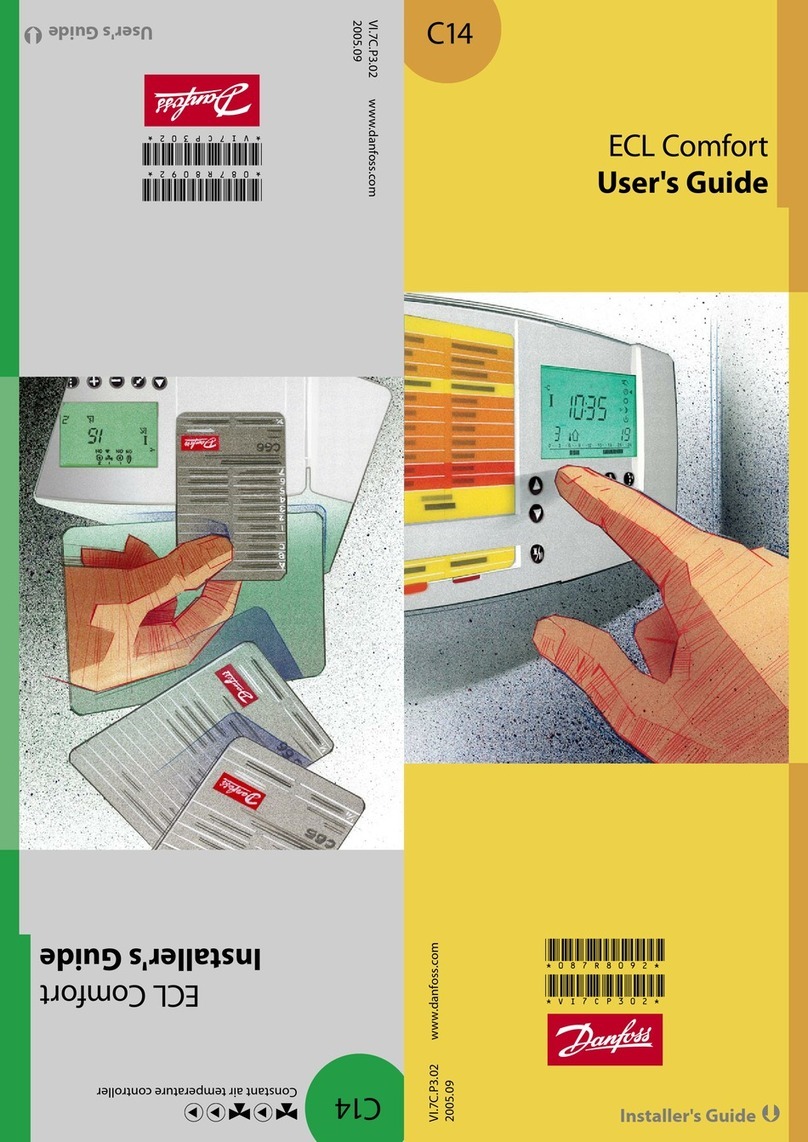
Danfoss
Danfoss ECL Comfort 100M user guide
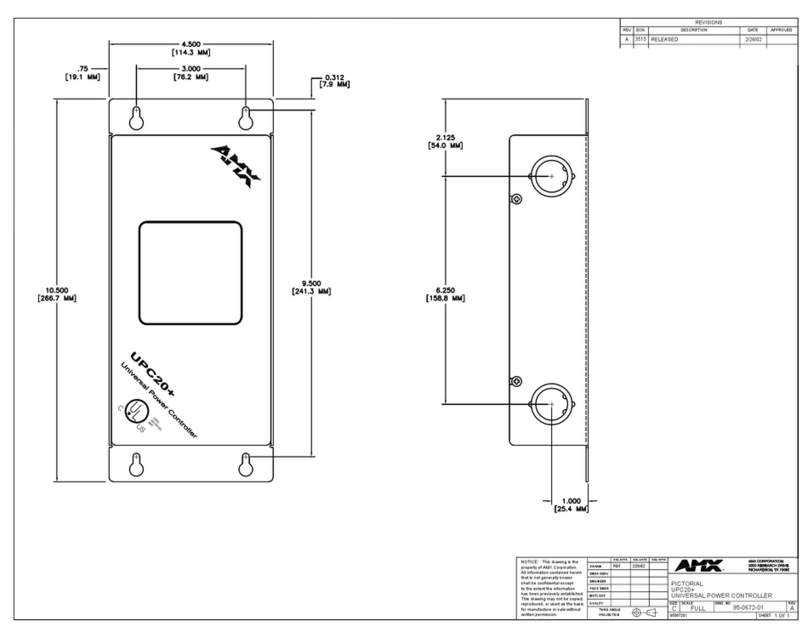
AMX
AMX UPC20 Plus Dimensional drawing

Highway Equipment Company
Highway Equipment Company New Leader MARK V DGPS-Ready General manual
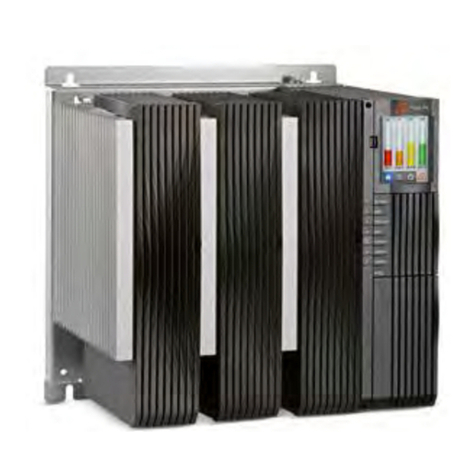
Advanced Energy
Advanced Energy Thyro-PX user manual