Emerson Spence K3 User manual












Other Emerson Control Unit manuals
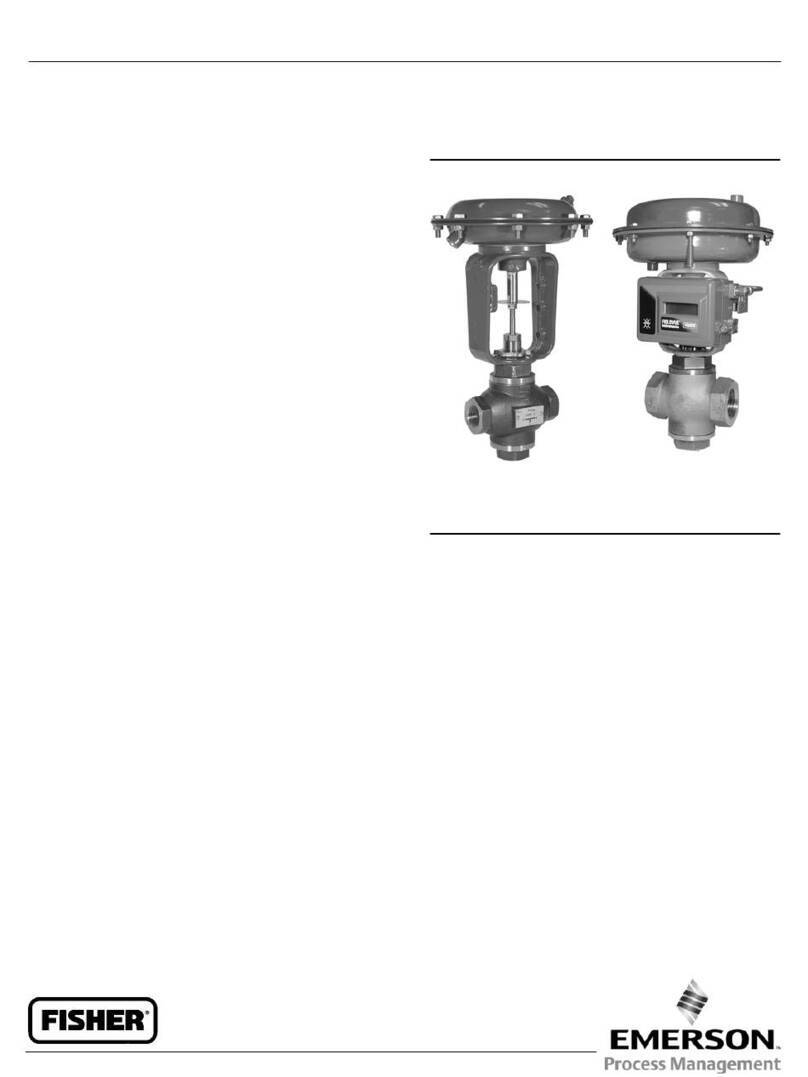
Emerson
Emerson Fisher Baumann 24003 User manual
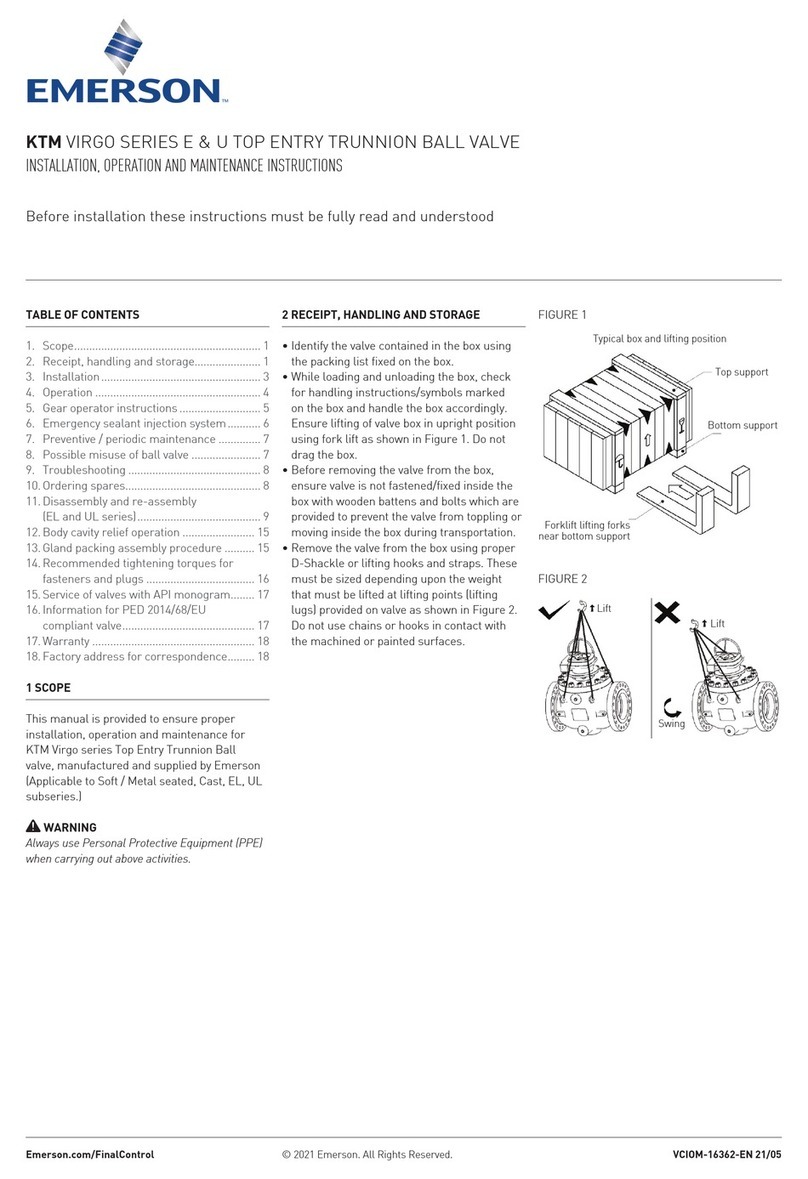
Emerson
Emerson KTM VIRGO E Series Manual

Emerson
Emerson Anderson Greenwood 400 Series Quick guide
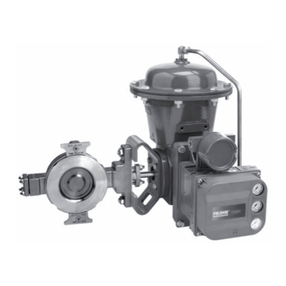
Emerson
Emerson Fisher 8580 User manual
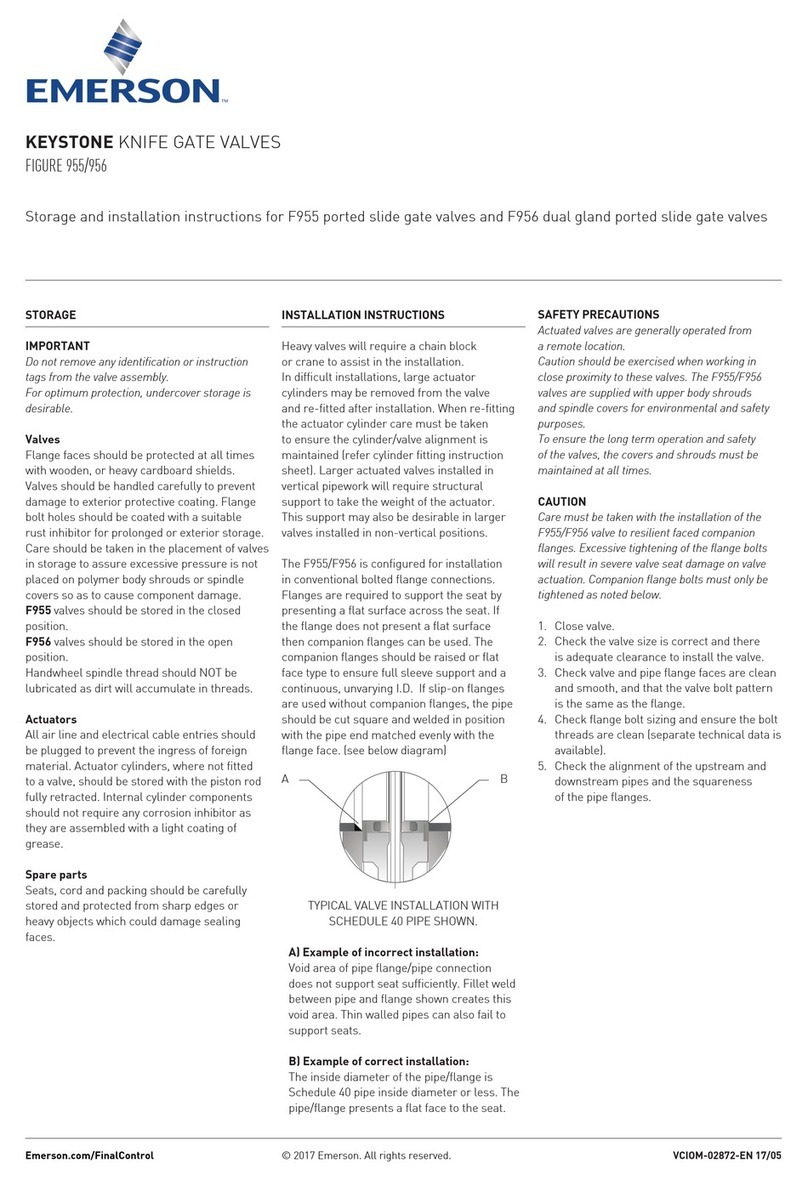
Emerson
Emerson KEYSTONE FIGURE 955 User manual
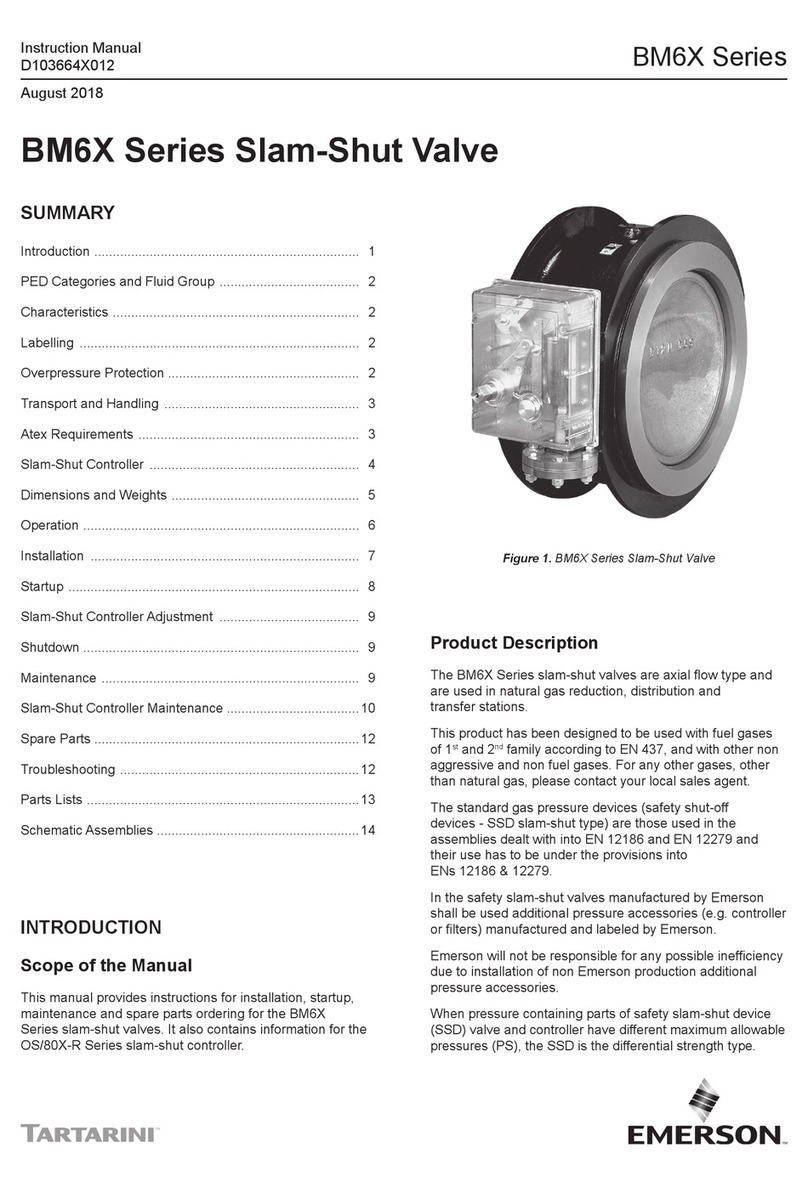
Emerson
Emerson BM6X Series User manual
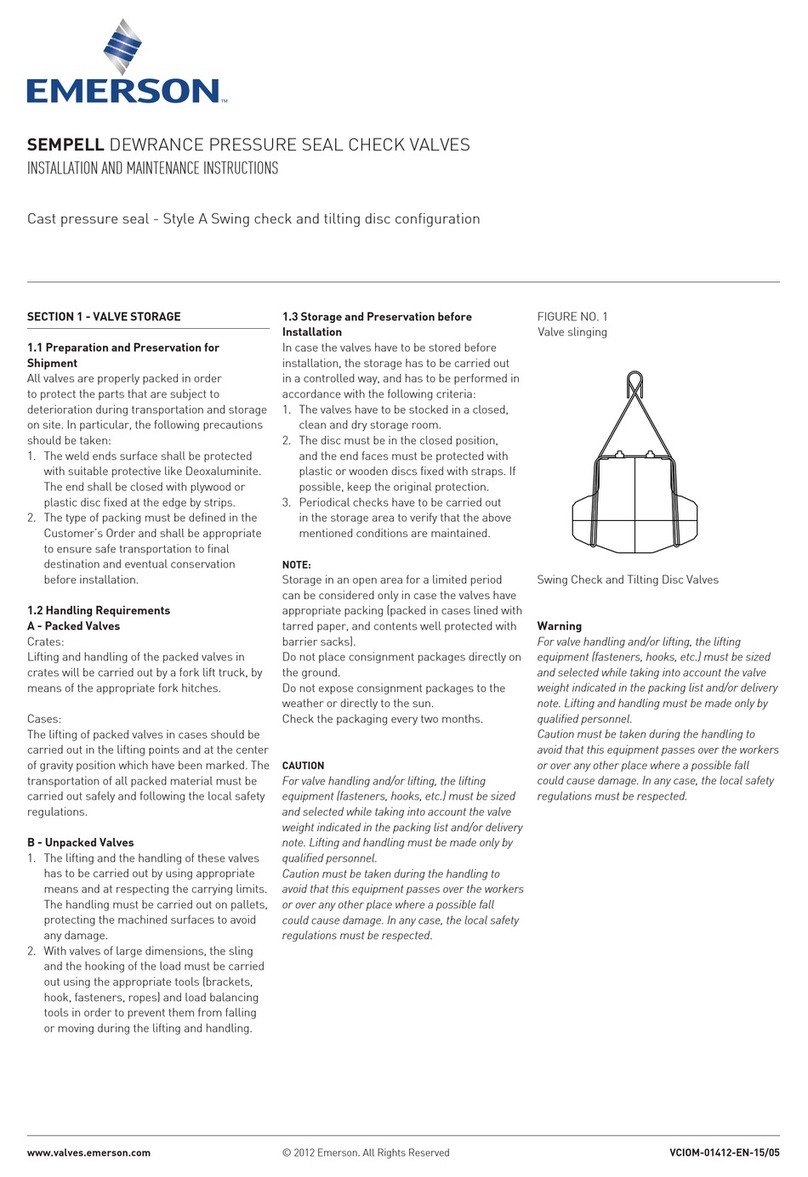
Emerson
Emerson Sempell series User manual
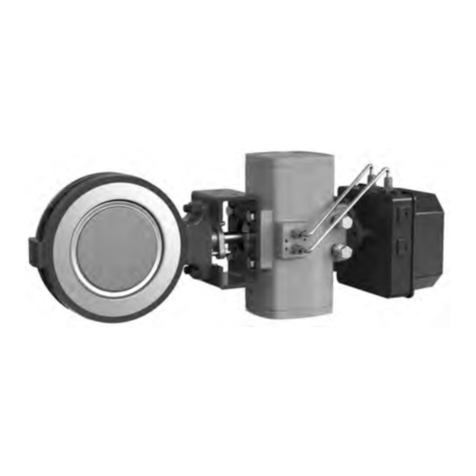
Emerson
Emerson Fisher 8540 User manual
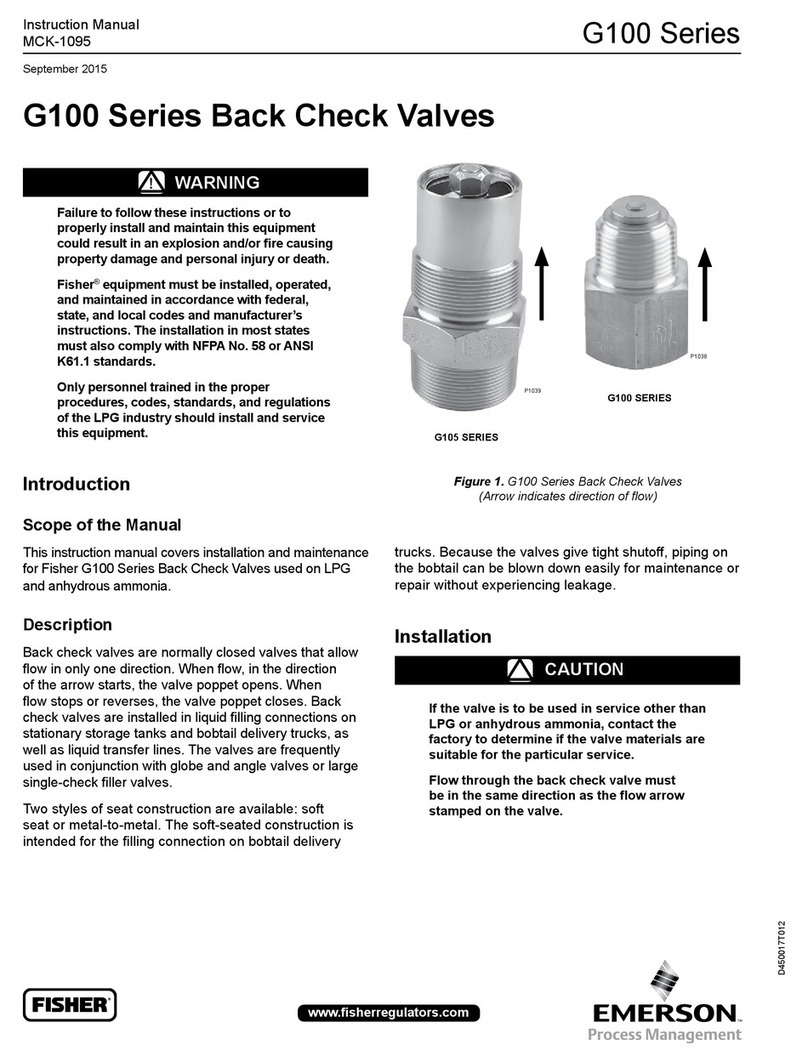
Emerson
Emerson Fisher G101 Series User manual

Emerson
Emerson Fisher Operating and maintenance manual
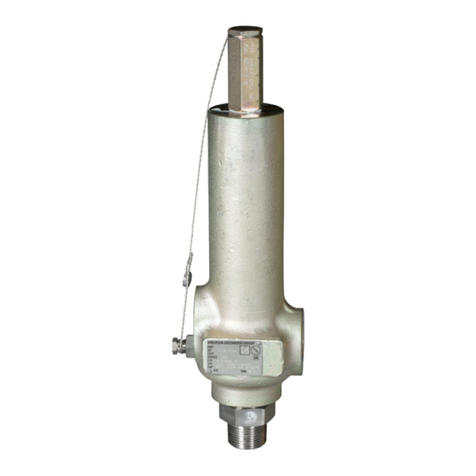
Emerson
Emerson Anderson Greenwood 81P Technical specifications
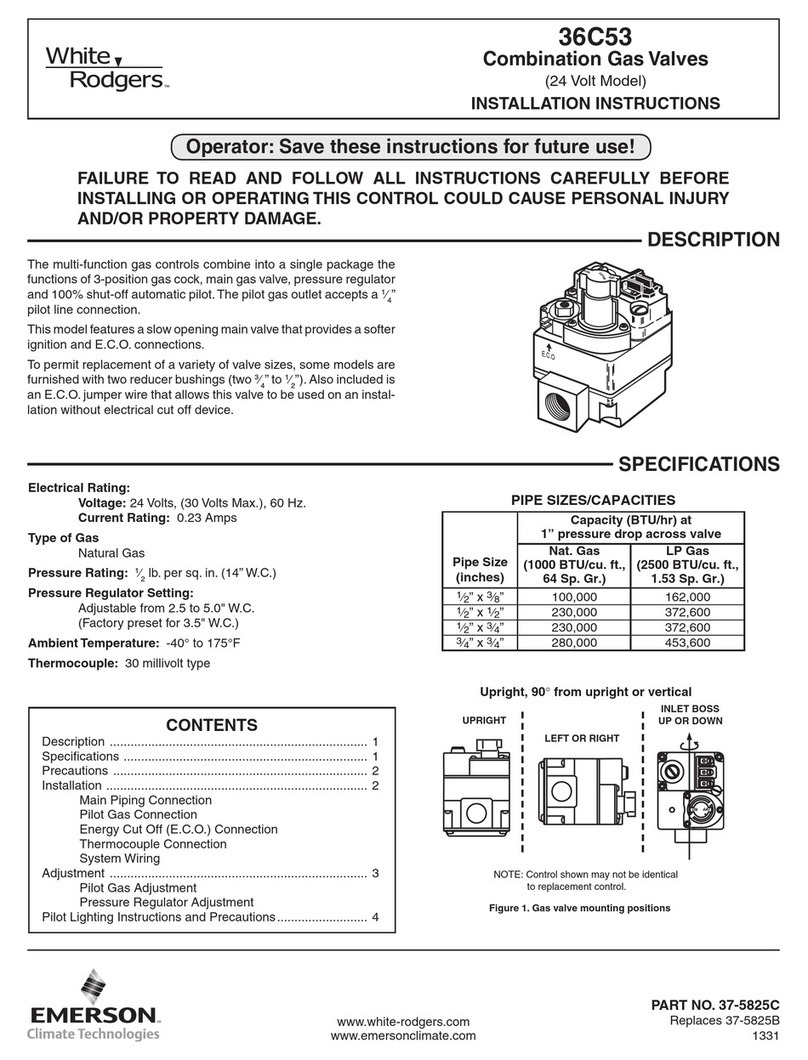
Emerson
Emerson White Rodgers 36C53 Series User manual

Emerson
Emerson Rosemount RM5800 User manual
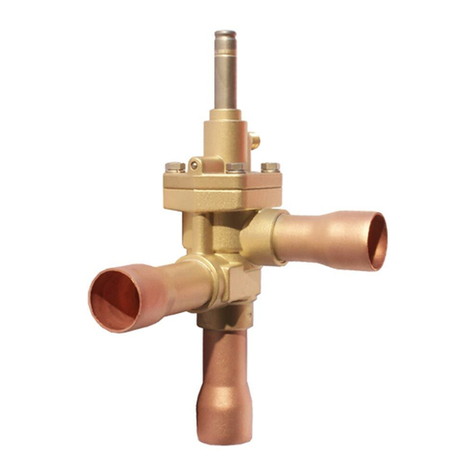
Emerson
Emerson Alco Controls M36 Series User manual

Emerson
Emerson Dixell XEC Supercap Wiring diagram
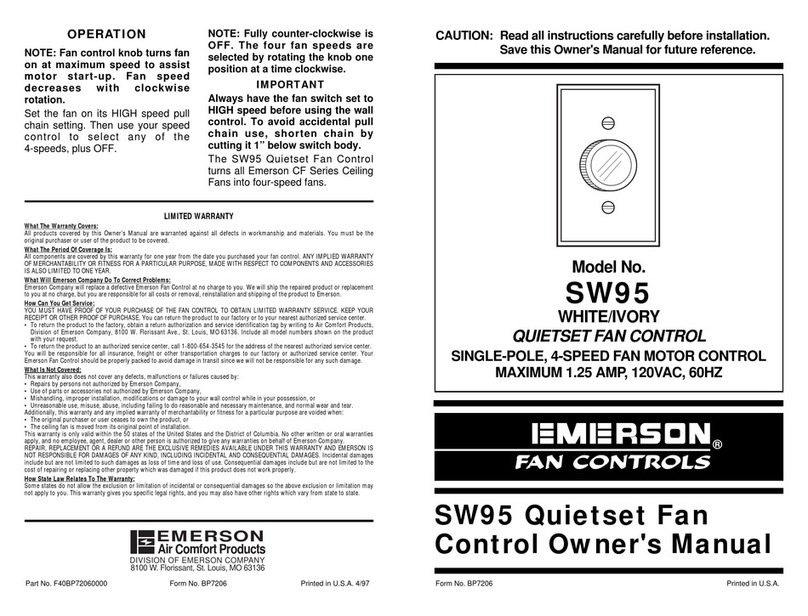
Emerson
Emerson SW95 User manual
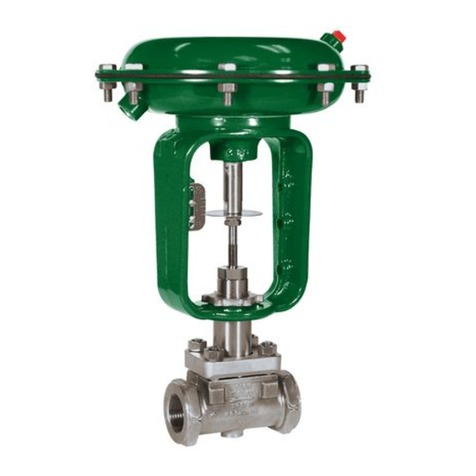
Emerson
Emerson Fisher Baumann 24000S User manual

Emerson
Emerson Fisher V150S Slurry Vee-Ball User manual
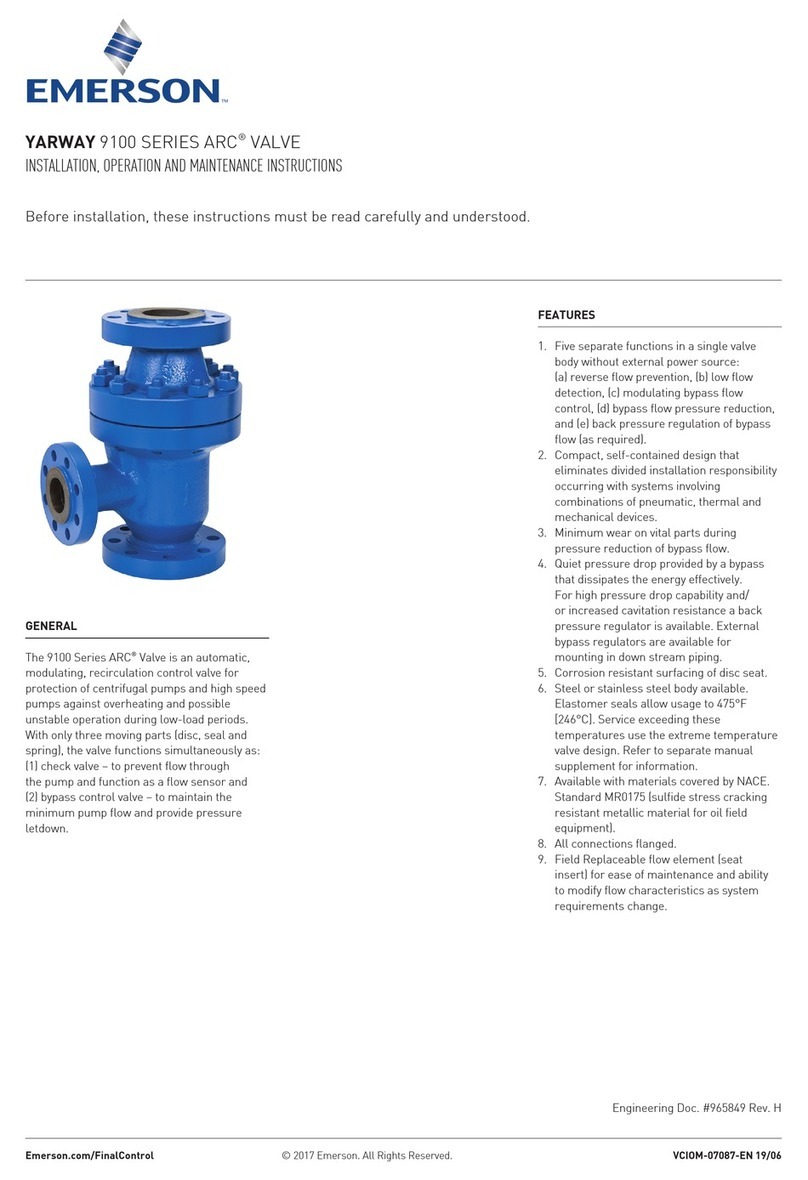
Emerson
Emerson YARWAY 9100 ARC Series Manual
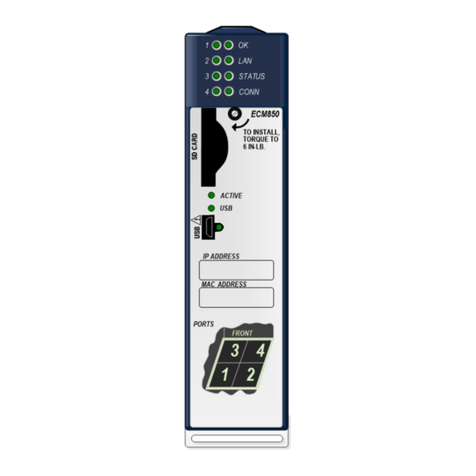
Emerson
Emerson PACSystems RX3i IEC 61850 User manual
Popular Control Unit manuals by other brands
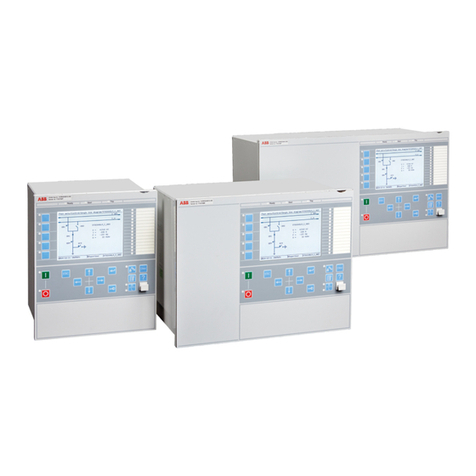
ABB
ABB Relion REC670 Applications manual
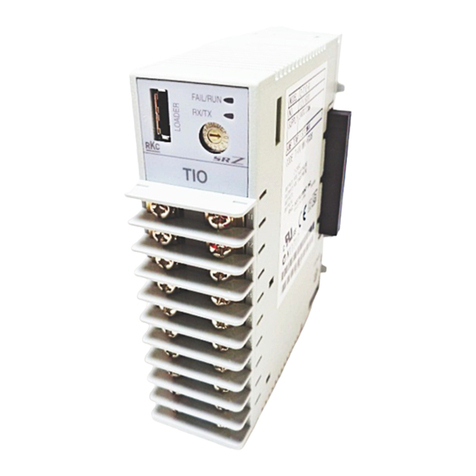
RKC INSTRUMENT
RKC INSTRUMENT Z-TIO-G instruction manual

BFT
BFT RIGEL 6 installation manual

ChemValve-Schmid
ChemValve-Schmid ChemBall CSB Installation & operating instructions
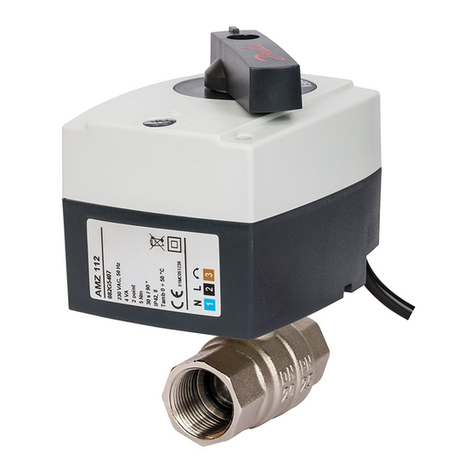
Danfoss
Danfoss AMZ 112 installation guide

IFM Electronic
IFM Electronic Ecomat 300 AL1030 Device manual