Emheater EM-GU Series User manual


Preface
Thanks for your using EMHEATER EM-GU series motor soft starter, this product is used for three-phase squirrel
cage induction motor soft starting and soft stopping control. Before using, please carefully read and understand
the contents of this manual.
In the process of using the soft starter, please note the following Safety Clauses:
Please check this user manual carefully before using the product.
Only the technical person is allowed to install the product.
To be sure that the motor is correctly matched with the soft starter.
It is forbidden to connect capacitors to the output terminals (U V W).
Please seal the terminal switch insulation glue after finishing connect them.
The soft starter and its enclosures must be fixedly earthed.
During the maintenance and repair, the input must be off-power.
PRODUCT UNPACKING INSPECTION
Please check up the products before using, if in some problems; please do not hesitate to contact us with any
request for additional information.
⚫Check-up the type of product whether it is the right one you order.
⚫Check any damage to the product because of the transport, such as the spare parts are apart from the
main body or the shell be damage etc.
⚫Check others, including the user's manual.
This user manual content may be changed due to technical reasons or modified. We reserve the updating right.
Version 1.0.0

Table of Contents
1. Products Information............................................................................................................................................... 1
1.1 Motor Soft Starter ............................................................................................................................................. 1
1.2 Technical Features............................................................................................................................................. 1
1.3 Technical Specification..................................................................................................................................... 1
2. Product Description and Installation........................................................................................................................ 2
2.1 Model Explanation............................................................................................................................................ 2
2.2 Products Model and Installation Dimension..................................................................................................... 2
2.3 Installation Environment................................................................................................................................... 3
2.4 Installation requirement .................................................................................................................................... 3
2.5 Peripheral Devices Connection Diagram.......................................................................................................... 4
2.6 Description of control circuit terminals............................................................................................................. 5
3. Operation and Display............................................................................................................................................. 6
3.1 Keypad and Operation....................................................................................................................................... 6
3.2 Description of Function Parameters.................................................................................................................. 8
3.3 Fault Diagnosis and Solution .......................................................................................................................... 14
4. Test Run and Application...................................................................................................................................... 16
4.1 Power on to Test Running............................................................................................................................... 16
5.2 SpecialApplication......................................................................................................................................... 16
5. Online Soft Starter Cabinet.................................................................................................................................... 17
5.1 Product Function............................................................................................................................................. 17
5.2 Products Structure and Installation ................................................................................................................. 17
5.3 Operation and Notice ...................................................................................................................................... 18
6. Modbus Communication Protocol......................................................................................................................... 20
6.1 About Modbus RTU protocol.......................................................................................................................... 20
6.2 Bus Structure................................................................................................................................................... 20
6.3 Abnormal Feedback ........................................................................................................................................ 21
Appendix I Function Code Table............................................................................................................................... 22

EM-GU User’s Manual 1. Products Information
1
1. Products Information
1.1 Motor Soft Starter
EM-GU motor soft starter, the use of intelligent digital control; It used to various squirrel-cage asynchronous
motor control of load, the motor can smooth starting under any working conditions, protect the drag system,
reduce the starting current impact on power grid, ensure reliable motor starting. Intelligent digital motor soft start
equipment system with the complete protection function, extend the service life of the system, reduce the cost of
system cost, improve the reliability of system and compatible with all the functions of starting equipment; It is a
new ideal alternative for traditional star triangle starter and self-coupling decompression starter.
1.2 Technical Features
●A variety of start mode can be selected to allow the motor soft starter to start different types of motor loads;
●Multiple dynamic fault memory functions for easy fault finding;
●Multiple protection functions, such as overcurrent, overheat, phase loss and thermal overload;
●Humanized design, detachable operation panel, built-in Chinese and English display interface for flexible
selection.
●Powerful software functions, rich hardware configuration, easily meet the needs of various industries.
●Compact design, easy to install and use.
1.3 Technical Specification
Input&Output
●Input voltage: AC 220-380V±15%
●Input frequency: 50/60Hz
●Output voltage: AC 220/380V±15%
Technical function
●Start mode: voltage ramp start, current limit start, torque start
●Stop mode: Soft stop, Free stop
●Starting time: 1~120s
●Stopping time: 0~60s
●Starting current limiting multiplier: 0.5~6Ie
●Starting voltage: 0.3~0.8Ue
●Pump functions
External terminal
●Remote control input
●Relay output
●Analog output
●RS485 communication output
Ambient
●Indoor location with good ventilation free from corrosive gas and conductive
dust.
●Altitude: Below 2000M. It has to rise the rate power when the altitude is more
than 2000M
●Temperature: -10 +40 oC
●Humidity: 90%RH without dew condensation.
●Vibration: <0.5G
●Cooling mode: Fans cooling.

2. Product Description and Installation EM-GU User’s Manual
2
2. Product Description and Installation
2.1 Model Explanation
Company code
GU series online soft starter
Rated voltage:
2: Three phase 220V
3: Three phase 380V
I: Cabinet
Matched motor: 045: 75kW; 160: 160kW
Diagram 2.1 Products model explanation
2.2 Products Model and Installation Dimension
Diagram 2.2 EM-GU installation dimension and mounting holes
Model
Rated
Power
Rated
Current
External Dimensions
(mm)
Installation Dimensions
(mm)
(KW)
(A)
H
W
D
H1
W1
d
EM-GU3-011
11
23
240
105
169
211
75
M6
EM-GU3-015
15
30
EM-GU3-018
18.5
37
EM-GU3-022
22
45
EM-GU3-030
30
60
EM-GU3-037
37
75
EM-GU3-045
45
90
283
135
185
244
105
M6
EM-GU3-055
55
110
EM-GU3-075
75
150
EM-GU3-090
90
180
371
190
245
322
150
M8
EM-GU3-115
115
230
EM-GU3-132
132
260
393
225
226
340
170
M8
EM-GU3-160
160
320

EM-GU User’s Manual 2. Product Description and Installation
3
Model
Rated
Power
Rated
Current
External Dimensions
(mm)
Installation Dimensions
(mm)
(KW)
(A)
H
W
D
H1
W1
d
EM-GU3-200
200
400
EM-GU3-250
250
500
586
483
296
498
340
M8
EM-GU3-280
280
560
EM-GU3-315
315
630
Note: The rated power of motor in the above form is the maximum rated value. Generally, the values of
matched motor power capacity should not be more than this value.
2.3 Installation Environment
●Power Supply: City grid power, self-provided power, diesel oil dynamotor, 3-phase alternating current
380V±15%, 50Hz or 60Hz. The power capacity of the soft start must meet the motor starting requirement.
●Matched Motor: Motor should be three phase squirrel asynchronous motor, and its power capacity must be
matched with soft starters.
●Starting Frequency: Not more than 4/hour when the motor is started with full load. The starting time is
according to the loading equipment.
●Cooling Mode: Fan cooling.
●Protective Grade: IP20
●Environment Conditions: when altitude is less than 2000m, the temperature of the environment should be
between -10oC ~ 40oC, relative humidity should be less than 95% RH, no vapor, no flammable, volatile,
corrosive gas. No electric dirt, indoor installation, ventilated, vibration is less 0.5G.
2.4 Installation requirement
he direction and distance of installation: In order to make sure that the soft starter be in good ventilation and heat
dissipation, please install the product in vertical direction, and be sure the space around the product is enough. If
the soft starter is installed in a box, please note that the ventilation is very good, as well as the above notes. (See
the following diagram 2.3)
Diagram 2.3 Ventilating duct installation dimension diagram of soft starter

2. Product Description and Installation EM-GU User’s Manual
4
2.5 Peripheral Devices Connection Diagram
EM-GU series soft starters can be connected to the motor by line mode connection or delta mode
connection.
Line Mode connection:
Diagram 2.4 EM-GU device connection diagram(Line mode)
Delta Mode connection:
Diagram 2.5 EM-GU delta mode connection diagram

EM-GU User’s Manual 2. Product Description and Installation
5
2.6 Description of control circuit terminals
Control terminal connection: That is the wire comes from 11 external terminals which including input and
output control signal and analogue output or RS485 communication signal.
Diagram 2.6 Control circuit terminal
Type
Terminal
Symbol
Terminal
Name
Description
Communication
485+
Communication
terminal
Input and output signal terminals for MODBUS-RTU protocol
communication.
485-
Digital input
IN1-24V
Run
When F49=0, there are two ways of connections for your selection;
those are 2-wire connection and 3-wire connection, as below:
IN2-24V
Stop/Reset
IN3-24V
Faul
Analog output
AO-GND
4-20mA output
The output upper and lower current limits are set by parameter F15,
default 2 times.
Relay output
TA-TB
NC terminal
Programmable relay output, the output method is set by the F13
parameter.
TA-TC
NO terminal
Note:Please make sure that external terminals are in right connection; otherwise, the product may be
damaged.

3. Operation and Display EM-GU User’s Manual
6
3. Operation and Display
The motor soft starter has five kinds of working state: Ready, starting, Running, stopping and Fault, the showing
parameter is easy to understand and modify.
3.1 Keypad and Operation
Diagram 3.1 Operation keypad
No.
Name
Function
LCD display area
LCD shows the parameter, monitoring data and Error codes.
Status indicator
area
Ready
On indicates that the soft starter is ready.
Run
On indicates that the motor is starting, running, soft stop state
Trip
On indicates that the soft starter is in a fault state, flashing indicates
that the soft starter is in warning state.
Local
On indicates that the soft starter is in keypad control mode.
Operation key area
Exit/Cancel key: Exit menu or cancel modification of parameters.
Shift key: The fault log can be cycled through while on the main
display screen, and select the digit to be modified when modifying
parameters.
UP key: Increase data or parameter code.
DOWN key: Decrease data or parameter code.
Menu/Enter key: Enter menu and confirm the parameter setting.
R/L key: For switching between keypad control and terminal control
Running key: Start the soft starter in the keypad control mode.
Stop/Reset key: When in operation, press this key for stop operation;
when in fault alarm, press this key for fault reset operation.
Start and stop operation:
The soft starter keypad screen shows “READY”, and press running key to start the motor. In the In the
process of starting, the screen shows starting current “xxxA”. When the starting is completed, can be press
UP key to check three phase current information.And press Stop/Reset key to stop the motor.

EM-GU User’s Manual 3. Operation and Display
7
Prompt:
●Only when the "READY" is displayed, the motor can be started by pressing the running key.
●When the external control terminal is wired in 3-wire mode, the external control start and stop buttons are
functionally equivalent to the running key and stop/reset key on the keypad respectively.
●During the start and stop process, you can not enter the Set Menu or Help Menu.。
Parameter modification operation:
In the “Ready” state, press MENU/ENTER key can enter the main menu.And the parameter can be
selected by UP key or DOWN key, and press MENU/ENTER key again to enter the
parameter that needs to be modified, select the option or modify the value by UP key or DOWN key,
and then press MENU/ENTER key again means that the new data has been saved and return to the menu.
If you do not want to save, please press Exit/Cancel key to return to the menu.
Prompt:
●Use the shift keys to quickly switch to the parameter to be modified.
●The keypad is designed to be super anti-interference, allowing an outward lead distance of more than 3m.
Fault enquiry operations:
The soft starter can record 12 fault logs for easy viewing, in the “Ready” state, press shift key to enter the
fault record menu. Check the fault logs by UP key or DOWN key. If you want to exit fault record
menu, please press shift key to exit the menu.

3. Operation and Display EM-GU User’s Manual
8
3.2 Description of Function Parameters
F00
Soft Starter Rated Current
Description: The default value of the parameter depends on the model, this parameter is read only and
can not be modified.
F01
Soft Starter Rated Voltage
Description: The default value of the parameter depends on the model, this parameter is read only and
can not be modified.
F02
Motor Rated Current
Description: The default value of the parameter depends on the model.
Match the starter to the rated current of the connected motor. Set the rated current is depend on the
motor nameplate
F03
Control Mode
Range: 0~7 (Default: 3)
Option: 0: Disable
1: Keypad
2: Terminal
3: Key+Term (Both keypad control and terminal control are valid)
4: Communication
5: Key+Comm (Both keypad control and communication control are valid)
6: Term+Comm (Both terminal control and communication control are valid)
7: Key+Term+Comm (Keypad control, terminal control, communication control all valid)
F04
Start Mode
Range: 0~2 (Default: 0)
Option: 0: Voltage Ramp
1: Current Limit
2: Torque Start
Select soft starter start mode.
F05
CLS Current Limited
Range: 50%~600% (Default: 300%)
Description: Set the current limit value for current-limited starting, as a percentage of motor rated
current.
F06
Initial Start Voltage
Range: 30%~80% (Default: 35%)
Description: Set initial start voltage for Voltage ramp starting.
F07
VRS Start Time
Range: 1s~120s (Default: 15s)
Description: Set start time for voltage ramp starting(Invalid for current limit starting)
F08
Stay Voltage
Range: 60%~85% (Default: 65%)
Description: Set stay voltage, valid for torque starting.
F09
Initial Ramp Time
Range: 1s~10s (Default: 5s)
Description: Set initial acceleration time, valid for torque starting.
F10
Stay Time
Range: 1s~120s (Default: 10s)

EM-GU User’s Manual 3. Operation and Display
9
Description: Set F08 hold time, valid for torque starting.
F11
End Ramp Time
Range: 1s~10s (Default: 3s)
Description: Set end acceleration time, valid for torque starting.
F12
Soft Stop Time
Range: 0s~60s (Default: 0s)
Description: Set the time required to soft stop the motor, if the value is “0”, the motor will free stop.
Note: One soft starter for 2 motor, this code should set "0".
F13
Programmable Relay
Range: 0~7 (Default: 7)
Option: 0: Disable
1: Power on
2: Starting
3: Bypass
4: Stopping
5: Running
6: StandBy(Ready)
7: Fault
Select programmable relay output method.
F14
Programmable Delay Time
Range: 0~600s (Default: 0s)
Description: Set the programmable output relay closed delay time.
F15
4-20 mA Current Limit
Range: 50%~500% (Default: 200%)
Description: Set analog current upper limit.
F16
Motor Wiring Mode
Range: 0~1 (Default: 0)
Option: 0: Line Mode
1: Delta Mode
Select motor wiring mode.
F17
ModbusAddress
Range: 1~127 (Default: 1)
Description: Set soft starter communication address.
F18
Modbus Baud rate
Range: 0~3 (Default: 2)
Option: 0:2400
1:4800
2:9600
3:19200
F19
Running Over Load(OL) Class
Range: 1~30 (Default: 10)
Description: Set different levels of overload protection。
The overload protection adopts anti-time protection control, and the formula as below:
Protection time t = 35 ∗Tp
(I/Ip)2 − 1

3. Operation and Display EM-GU User’s Manual
10
Note: t means action time, Tp means running OL class, I means running current,Ip means motor rated
current.
The table of motor overload protection characteristics is as follows:
Overload
Class
Overload capacity
1.05Ie
1.2Ie
1.5Ie
2Ie
3Ie
4Ie
5Ie
6Ie
1
∞
79.5s
28s
11.7s
4.4s
2.3s
1.5s
1s
2
∞
159s
56s
23.3s
8.8s
4.7s
2.9s
2s
5
∞
398s
140s
58.3s
22s
11.7s
7.3s
5s
10
∞
795.5s
280s
117s
43.8s
23.3s
14.6s
10s
20
∞
1591s
560s
233s
87.5s
46.7s
29.2s
20s
30
∞
2386s
840s
350s
131s
70s
43.8s
30s
Note: ∞means no action.
Motor overload protection characteristic curve diagram
F20
Starting Over Current(OC) P.C.
Range: 50%-600% (Default: 500%)
Description: Set the multiple of overcurrent for soft starter starting.
F21
Starting Over Current(OC) Time
Range: 0s-120s (Default: 5s)
Description: Set the overcurrent protection trigger delay time when the soft starter starting.
F22
Running Over Current(OC) P.C.
Range: 50%-600% (Default: 200%)
Description: Set the multiple of overcurrent for soft starter running.
F23
Running Over Current(OC) Time
Range: 0s-6000s (Default: 5s)
Description: Set the overcurrent protection trigger delay time when the soft starter running.
F24
Over Voltage P.C.
Range: 100%~140% (Default: 120%)
Description: Set the multiple of overvoltage for soft starter.
F25
Over Voltage Time
Range: 0s~120s (Default: 5s)
Description: Set soft starter overvoltage protection trigger delay time.
F26
Under Voltage P.C.

EM-GU User’s Manual 3. Operation and Display
11
Range: 50%-100% (Default: 80%)
Description: Set the multiple of undervoltage for soft starter.
F27
Under Voltage Time
Range: 0s~120s (Default: 5s)
Description: Set soft starter undervoltage protection trigger delay time.
F28
Current Unbalance P.C.
Range: 20%~100% (Default: 40%)
Description: Parameter setting for current three-phase unbalance.
F29
Current Unbalance Time
Range: 0s~120s (Default: 10s)
Description: Set soft starter three phase current unbalance protection trigger delay time.
F30
Under Load P.C.
Range: 10%~100% (Default: 50%)
Description: Set the multiple of under load for soft starter.
F31
Under Load Time
Range: 1s~120s (Default: 10s)
Description: Set soft starter under load protection trigger delay time.
F32
Phase Sequence
Range: 0~2 (Default: 0)
Option: 0: Any
1: Positive
2: Negative
F33
IA Calibration
Range: 10%~1000% (Default: 100%)
Description: Calibration of the soft starter's current monitoring circuit to match the external current
measuring device.
The formula is as follows:
Calibration (%) = Current measured by an external device / Current displayed on the soft starter
For example: 102%=102A/100A
Note: This adjustment value affects all current-based functions and protections.
F34
IB Calibration
Range: 10%~1000% (Default: 100%)
Description: The function same as parameter F33.
F35
IC Calibration
Range: 10%~1000% (Default: 100%)
Description: The function same as parameter F33.
F36
Voltage Calibration
Range: 10%~1000% (Default: 100%)
Description: Calibration of the soft starter's voltage monitoring circuit to match the external voltage
measuring device.
The formula is as follows:
Calibration (%) = Voltage measured by an external device / Voltage displayed on the soft starter
For example: 95%=380V/400V
F37
4-20mA Lower Calibration

3. Operation and Display EM-GU User’s Manual
12
Range: 0%~150.0% (Default: 20.0%)
Description: Analog output lower setting, default 4mA.
F38
4-20mA Upper Calibration
Range: 0%~150.0% (Default: 100.0%)
Description:Analog output upper setting, default 20mA.
F39
Running Over Load(OL)
Range: 0~1 (Default: 0)
Option: 0: Alarm & Stop
1: Ignore (The protection function is disabled)
F40
Starting Over Current(OC)
Range: 0~1 (Default: 0)
Option: 0: Alarm & Stop
1: Ignore (The protection function is disabled)
F41
Running Over Current(OC)
Range: 0~1 (Default: 0)
Option: 0: Alarm & Stop
1: Ignore (The protection function is disabled)
F42
Over Voltage
Range: 0~1 (Default: 0)
Option: 0: Alarm & Stop
1: Ignore (The protection function is disabled)
F43
Under Voltage
Range: 0~1 (Default: 0)
Option: 0: Alarm & Stop
1: Ignore (The protection function is disabled)
F44
Current Unbalance
Range: 0~1 (Default: 0)
Option: 0: Alarm & Stop
1: Ignore (The protection function is disabled)
F45
Under Load
Range: 0~1 (Default: 0)
Option: 0: Alarm & Stop
1: Ignore (The protection function is disabled)
F46
Over Heat
Range: 0~1 (Default: 0)
Option: 0: Alarm & Stop
1: Ignore (The protection function is disabled)
F47
Language
Range: 0~1 (Default: 1)
Option: 0:English
1:中文
Select the language in which messages and feedback are displayed on the keypad.
F48
MB Soft Version
Description: Displays the master board software version information. This parameter is read only and
cannot be modified.

EM-GU User’s Manual 3. Operation and Display
13
F49
Pump Functions
Range: 0~4 (Default: 0)
Option: 0: None (Soft starter standard functions)
1: Float Ball (IN1 on: start; IN1 off: stop)
2: Electrical Pressure Gauge (IN1 on: start; IN2 on: stop)
3: Level relay Supply(IN1 off and IN2 off: start;IN1 on and IN2 on: stop)
4: Level relay Drain(IN1 off and IN2 off: stop;IN1 on and IN2 on: start)
Note:
When F49 = 0, the IN3 function is fault output.
When F49 = 1 to 4, the IN3 function is running enable, it must be on to perform the above
operation.
F50
Display Soft Version
Description: Displays software version information. This parameter is read only and cannot be modified.

3. Operation and Display EM-GU User’s Manual
14
3.3 Fault Diagnosis and Solution
The soft start writes the protection condition into the program when it is detected and it may trip. The soft start
response depends on the protection level.
Some of these protection responses cannot be adjusted by the user. These trips are usually caused by external
events (e.g. phase loss) or may be caused by internal soft start faults. There are no parameters associated with
these trips and they cannot be set to ignored.
If the soft start trips, you will need to identify and clear the conditions that triggered the trip and reset the soft start
before it can be restarted. To reset the starter, press the (stop/reset) key on the keypad or activate the "stop/reset
remote input".
The following table shows the protection mechanisms and possible causes of tripping of the soft start. Some of the
settings can be adjusted using the protection level, while others are built-in system protections and cannot be set
or adjusted.
Fault Name
Possible causes and solutions
Input phase loss
1. When the start command is issued, soft starter one phase or multiple phases are not
powered. Check whether the main circuit is powered or whether the SCR or thyristor is
damaged and whether the signal cable has poor contact.
2. Main board is faulty.
Related parameters: No parameter adjustment.
Output phase loss
1. Check whether the SCR or thyristor is damaged.
2. Motor cable has one phase or multiple phases open circuit. Please check whether the
motor cable is open circuit.
3. Main board is faulty.。
Related parameters: No parameter adjustment.
Running OL
1.The load is too heavy. Please replace the soft start with a more powerful one.
2. The parameters are not set correctly. Please adjust the parameters.
Related parameters: F19, F39
Under Load
1.The load is too small.
2. The parameters are not set correctly. Please adjust the parameters.
Related parameters: F30, F31, F45
Over Heat
1. Please check whether the temperature switch is faulty.
2. Fan not turning, please check whether the fan is working properly.
3. The soft start has been working for too long, stop the machine and let the soft start cool
down.
Related parameters: F46
Over Volt
1. Input voltage is too high, please check the power supply voltage.
2. The parameters are not set correctly. Please adjust the parameters.
Related parameters: F24,F25,F42
Over Load
1. Input voltage is too low, please check the power supply voltage.
2. The parameters are not set correctly. Please adjust the parameters.
Related parameters: F26,F27,F43
Running OC
1.The load is too heavy. Please replace the soft start with a more powerful one.
2. The parameters are not set correctly. Please adjust the parameters.
Related parameters: F22,F23,F41
Starting OC
1.The load is too heavy. Please replace the soft start with a more powerful one.

EM-GU User’s Manual 3. Operation and Display
15
Fault Name
Possible causes and solutions
2. The parameters are not set correctly. Please adjust the parameters.
Related parameters: F20,F21,F40
External Fault
1. External fault terminal has input. Please check external input terminal.
Related parameters: No parameter adjustment.
Phase Sequence
1. The input power phase sequence is not the same as the setting, please change the power
phase sequence or adjust the parameters.
Related parameters: F32

4. Test Run and Application EM-GU User’s Manual
16
4. Test Run and Application
Please do some examinations before test running as following:
⚫Whether the rated power of soft starter is matched with the Motor.
⚫Whether the insulation of motor meets requirement.
⚫Whether the main circuit connection of input and output is correct.
⚫Whether all the screws of terminals are twisted tightly.
4.1 Power on to Test Running
●The "Ready" state is displayed when power on, press Running key to start the motor.
●Set F02 be same as motor nameplate rated current.
●After started the motor, you should examine whether the motor running direction is correct, or whether runs
normally. If not, you can press key or cut off the power to stop running.
●If the soft starter starting state is not satisfied, please select the appropriate starting mode and starting time.
●If the start torque is not enough, you can change start mode to torque start to improve start torque.
●Do not open the face cover in case of electric shock.
●If abnormal phenomena such as abnormal sound, smoke or odour are found during the trial operation of the
soft starter, the power supply should be cut off at once and the cause investigated.
●If the Trip light on after power-up or at start-up, you can check chapter 3.3 to find out reason.
●Press key or external stop button can reset the error state.
Note: When ambient temperature is less than -10oC, the starter should be power on to preheat for 30 minutes,
and then to start.
5.2 Special Application
⚫In parallel the starting of the motors: If the motors total power is less than 80% of soft starter, the motors
can be parallel connection. But at this time should be also provides for each motor thermal protection device.
⚫Double speed motor: Motor soft starter can cooperate with double speed motor starting, must go through
demagnetization delay period before change from low speed to high speed, to avoid anti-phase current
generated between the lines and motor.
⚫Too long cable: f the cable is too long, the cable voltage drop will be high, and that will increase current loss
and reduce starting torque, so please use big KW soft starter and motor.
⚫Soft starter parallel connected with one power-line: If several soft starters parallel installed in the one power
line, the input line reactor should be installed in the middle of the transformer and the soft starter circuit. Reactor
should be installed at each line input side between circuit breaker and soft starter.
⚫The application of surge protection device (SPD): The surge protection device should be considered to
installed in the application case, where is easily caused trouble by lightning or other reasons, such as over
voltage, over-current, surge interference. Please refer to SPD related documents for details.

EM-GU User’s Manual 5. Online Soft Starter Cabinet
17
5. Online Soft Starter Cabinet
EM-GU3I series online soft starter cabinet is suitable for squirrel cage asynchronous motor control with various
loads to ensure reliable start of motor. It has a complete system protection function, extend the service life of the
system, reduces the cost of the system, improves the reliability of the system and compatible with various
functions of all devices. It is a new ideal alternative for traditional star triangle starter and self-coupling
decompression starter.
5.1 Product Function
●Effectively reduce the starting current of the motor; Can reduce the distribution capacity, avoid grid
expansion investment.
●Reduce the starting stress of motor and load equipment; Prolong the service life of the motor and related
equipment.
●Soft stopping function can effectively solve the parking surge problem of inertial systems; That is a
traditional starting equipment cannot be achieved.
●With six unique starting mode; To adapt to the complex motor and load, achieve perfect priming effect.
●With complete and reliable protection function; effectively protect the safety of motor and related production
equipment.
●Intelligent motor soft starter, the application of network technology used motor control technology to adapt
to the rapid development of electric power automation technology in the higher requirements.
Conditions of Use:
●Power Supply: City grid power, self-provided power, diesel oil dynamotor, 3-phase alternating current
380V±15%, 50Hz or 60Hz. The power capacity of the soft start must meet the motor starting requirement.
●Matched Motor: Motor should be three phase squirrel asynchronous motor, and its power capacity must be
matched with soft starters.
●Starting Frequency: The starting time is according to the loading equipment.
●Cooling Mode: Naturally wind cooling.
●Protective Grade: IP20
●Environment Conditions: when altitude is less than 2000m, the temperature of the environment should be
between -10oC ~ 40oC, relative humidity should be less than 90% RH, no vapor, no flammable, volatile,
corrosive gas. No electric dirt, indoor installation, ventilated, vibration is less 0.5G.
5.2 Products Structure and Installation
Installation:
The installation adopts floor vertical installation, which can be installed on the trench slot, the cabinet body is
exposed, and the power cable and control cable are introduced into the control cabinet by the trench. The cabinet
body is made of angle steel frame and painted, and the door is opened from the front of the control cabinet
Table of contents
Other Emheater Controllers manuals
Popular Controllers manuals by other brands
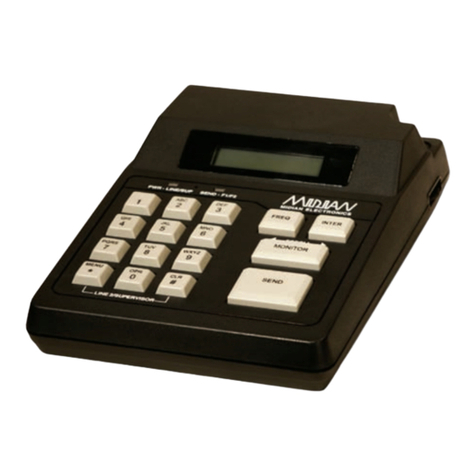
Midian Electronics
Midian Electronics TRC-1000 manual
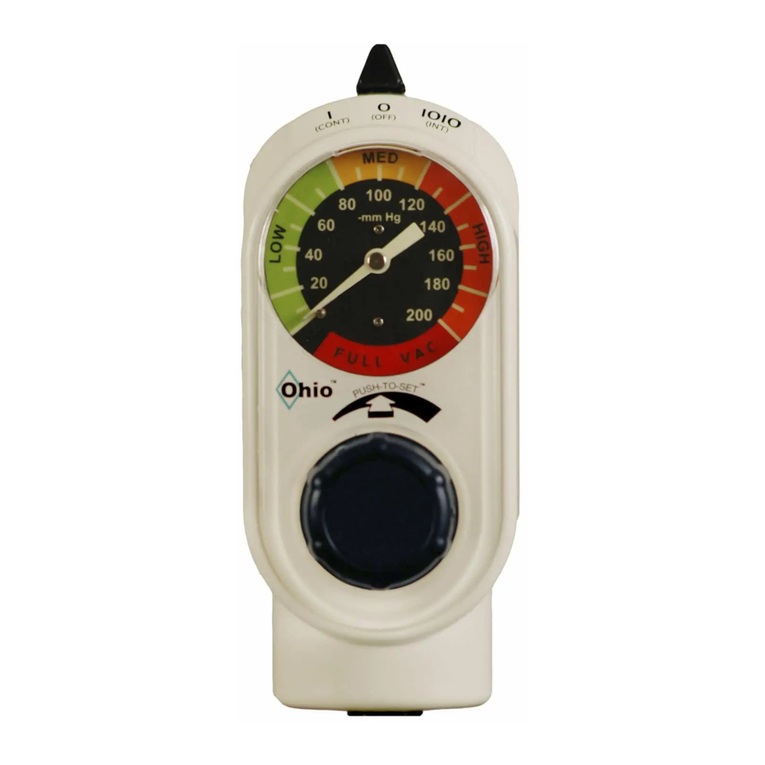
Ohio Medical
Ohio Medical Push-To-Set PTS-CVR Service manual
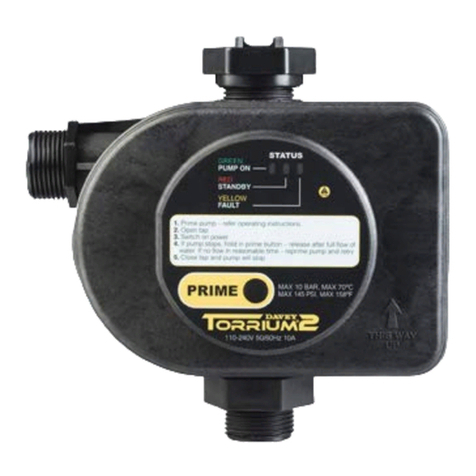
Davey Water Products
Davey Water Products Torrium 2 Installation and operating instructions
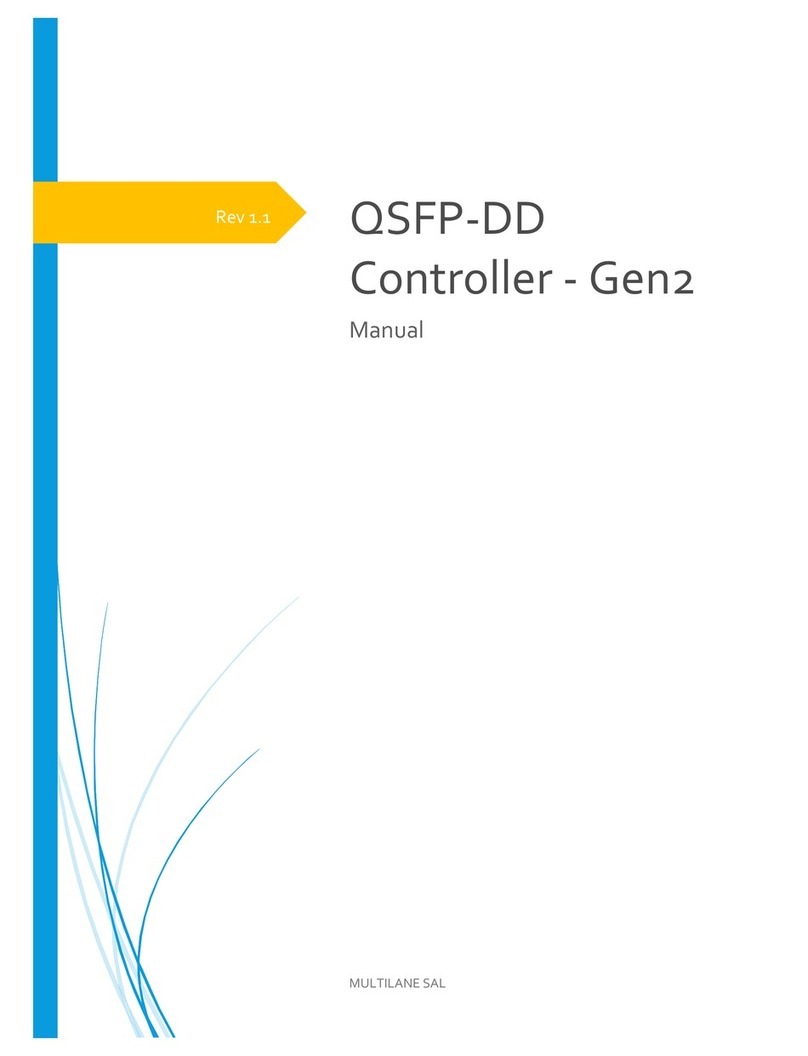
MULTILANE
MULTILANE QSFP-DD manual

RCS
RCS Eden Compact series Product guide
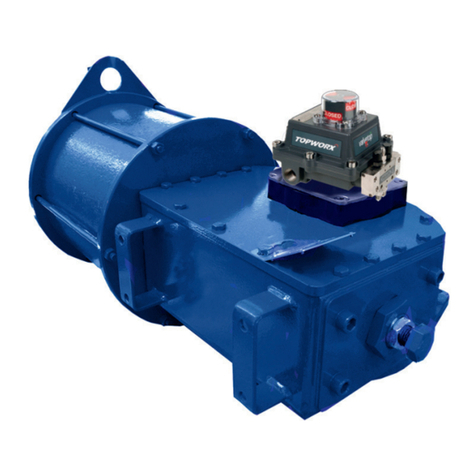
BIFFI
BIFFI ALGA-EAC Series Installation, operation and maintenance manual