Megmeet MC160 PLC Series User manual

MC160 series PLC user quick reference
manual
Thank you for using MC160 series PLC of Megmeet. Before using the
PLC product, please carefully read this booklet so as to better
understand it, fully use it, and ensure safety.This user manual is to offer
you a quick guide to the design, installation, connection and
maintenance of MC160 PLC.This quick reference manual is used for
the design, installation, connection and maintenance of the MC160
series PLC. It is convenient for users to consult the required
information on the spot, as well as the introduction of the relevant
optional accessories, FAQ, etc., for easy reference.
This manual for the following members:
MC160-0806BTD1-2
MC160-1206BTD1-2
MC160-0806BTD7-2
MC160-1214BMD1-2
MC160-1414BTD1-2
Version 1.0
Revision date Sep 09, 2019
BOM
1. Appearance and parts name
MC160-0806BTD1-2
MC160-1206BTD1-2
MC160-0806BTD7-2

MC160-1214BMD1-2
MC160-1414BTD1-2
2. Model specification
3. Installation
3.1 Environment temperature
1. Ambient temperature range: -5℃~ 55℃.
2. Humidity: <85%RH, no condensation.
3. When the ambient temperature exceeds 55℃for a long time, it is
better to choose a well-ventilated place.
3.2 Installations
Places free from corrosion, flammable and explosive gases and
liquids.
A firm, vibration-free place.
The PLC is designed for the application of installing environment
II standard and pollution level 2.
3.3 Installation method
The PLC must be installed horizontally on the back panel of the
electrical cabinet. Install it up and down and keep the distance between
the PLC and the equipment or cabinet wall above and below not less
than 20cm. Installation in other directions is not conducive to heat
dissipation of the PLC, and there should be no heating equipment
under the PLC.
DIN slot installation and fixation
In low vibration environment, the DIN slot width of 35mm can be used
for installation. Open the DIN buckle at the bottom of the module and
clamp the bottom of the module on the DIN rail; The rotating module is
close to DIN guide rail and close DIN buckle. Carefully check whether
the DIN buckle on the module is tightly fixed to the DIN guide rail.
Install and fix with screws
In case of large vibration, screws must be used to fix the module. M3
screws can be selected to fix the module on the back plate.
The external dimensions and installation hole size of this module
are shown in the figure below.

3.4 Cable connections and specifications
When wiring products, it is recommended to use multiple copper wires
and prefabricate insulated terminals to ensure the quality of wiring. The
sectional area and type of the recommended conductor are shown in
the table below.
Cable
Position
Allow
wire
number
Recommended
stripping
length
Install
method
Power
terminal(3PIN)
Side
12 ~
30AWG
6.5mm
Screws
Communication
terminal(2PIN)
Side
12 ~
30AWG
6.5mm
Screws
DA output
terminal(3PIN)
Side
12 ~
30AWG
6.5mm
Screws
AD input
terminal(5PIN)
Side
12 ~
30AWG
6.5mm
Screws
Digital input
terminal(9PIN)
Top
12 ~
30AWG
6.5mm
Screws
Digital output
terminal(8PIN)
Top
12 ~
30AWG
6.5mm
Screws
Analog input
terminal(6PIN)
Top
12 ~
30AWG
6.5mm
Screws
Analog output
terminal(6PIN)
Top
12 ~
30AWG
6.5mm
Screws
Digital input
terminal(5PIN)
Top
12 ~
30AWG
6.5mm
Screws
For security (to prevent electric shock and fire accident), and reduce
the noise, the module of grounding terminal shall be in strict
accordance with the national electrical code requirements, grounding
resistance should be less than 0.1 Ω. When grounding multiple
modules, single point grounding should be adopted, and the ground
wire cannot form a circuit. As shown in the figure below:
Error Correct
4. Power supply
Item
Uni
t
Mix.
value
Type
value
Max.
value
Remark
The range of
input voltage
Vdc
20.4
24
30
Normal start-up
and working range
Input current
A
0.25
0.18
0.14
Normal
temperature rated
full load

5. Terminal
5.1 User terminal
User terminal definition table
Remark
Explanation
24V+,24V-
Input power supply DC24V
Ground
485+,485-
RS485(COM0)
S/S0,X0~X7
Switch input common terminal, input port
Y0~Y3,COM0
Switching output channel 0 ~ 3 output
common end 0
Y4~Y5,COM1
Switching output channel 4 ~ 5 output
common end 1
AVI1+,AVI2+,AVI3+,AVI
4+,AI-
The channel of analog input 1~4(voltage
and current compatible)
AIO2+,AIO1+,AO-
Analog output channel1,channel 2(current
type)
AVO2+,AVO1+,AO-
Analog output channel1,channel 2(voltage
type)
AVO3+,AIO3+,AO3-
Analog output channel 3(voltage and
current compatible)
AVO4+,AIO4+,AO4-
Analog output channel 4(voltage and
current compatible)
AVO5+,AIO5+,AO5-
Analog output channel 5(voltage and
current compatible)
AVO6+,AIO6+,AO6-
Analog output channel 6(voltage and
current compatible)
X10,X11,X12,X13,
S/S1
Switch input common terminal, input port
L1+ L1- LR1-
PT100 thermal resistance input channel 1
L2+ L2- LR2-
PT100 thermal resistance input channel2
L3+ L3- LR3-
PT100 thermal resistance input channel3
L4+ L4- LR4-
PT100 thermal resistance input channel4
Y6,Y7,COM2
Relay output 6,7
input common terminal 2
Y10,Y11,COM3
Relay output 10.11
input common terminal 3
Y12,Y13,COM4
Relay output 12.13
input common terminal 4
Y14,Y15,COM5
Relay output 14.15
input common terminal 5
S/S1,X10~X13
Digital input port common end, input port
5.2 Communication port
Name
Supported
protocols
Position
Physical layer
Communication
Modbus slave
COM0
RS485

port 0
(485+ ,485-)
6. Switching characteristics of input and output
6.1 Switching input characteristics and signal
specifications
The counter input port has a maximum frequency limit. If the limit is
exceeded, the count may be inaccurate or the system may not function
properly. Please arrange the input port reasonably and select the
appropriate external sensor. The PLC provides port "S/S" for selecting
whether the input signal is source input or leak input. Leaky input:
connect S/S terminal to +24V terminal. NPN sensors can be connected
in this way. The internal equivalent circuit and external connection
mode of leakage input mode are shown in the figure below.
Source input: Short connect S/S terminal to COM terminal. This mode
can be connected to the PNP sensor. The internal equivalent circuit
and external connection mode of source input mode are shown in the
figure.
6.2 Transistor output
The output terminals are divided into several electrically isolated
groups, and different groups can be connected to different power
circuits. Transistor output can only be used in DC 24V load circuit. Pay
attention to power polarity. The inductive load of DC circuit should be
considered to increase the continuation diode.
Relay output
Item
Specification
Contact load (resistive)
5A 250VAC/30VDC
Switching voltage
250VAC/30VDC
Switching current
5A
Switching power
1250VA/150W
7. Analog input characteristics
7.1 Wiring method
The specific connection method is shown below.
* Double stranded shielded cable access is recommended. Cables
should be kept away from power lines or other wires, user terminals,
extension cables and interface extension cables that may cause
electrical interference.
* If the input signal fluctuates or there is electrical interference in the
external wiring, it is recommended to connect a smooth capacitor
(0.1uf ~ 0.47uF/25V).

* It is recommended to use connection cables of less than 100m in
length to reduce measurement errors and noise interference.
7.2 Performance
7.2.1 Voltage/Current input channel index
Item
Index
Conversion speed
15ms/channel(Normal),6ms/channel(high-sp
eed)
Analog
input range
Voltage
input
0VDC~+10VDC,
input resistance
1MΩ
The attributes of each
channel can be set
individually through the
X-Builder programming
software
Current
input
0mA ~+20mA ,
input resistance
250Ω
Digital output
Scope:0~+2000
Resolution
Voltage
input
5mV
Current
input
10uA
Accuracy
Full load ±1%
Isolation
Analog and digital circuits are isolated,
analog channels are not isolated.
7.2.2 Analogy output channel index
Item
Index
Conversion speed
2ms/channel
Analog
output
Voltage output
0 ~ + 10 VDC, external load
impedance ≥2 k Ω
Current output
0 ma ~ + 20 ma, external load
impedance ≤500 Ω
Digital
output
Voltage output
Default setting: 0 ~ +2000
Current output
Default setting: 0 ~ +2000
Resolution
Voltage input
5mV
Current input
10uA
Accuracy
Full load ±1%
Isolation
Analog and digital circuits are isolated,
analog channels are not isolated.
8. Common problems and solutions
phenomenon
Possible reason
Countermeasures
Power and
other LED
light are OFF
Out of voltage or low voltage
Check power supply
condition and
exclude
The power switch is off or
the fuse is blown
Check the condition
of switches, wires or
fuses to exclude
them
Abnormal power connection
Power plate damage
Check and confirm
whether the voltages
between 24V+ and
24V- terminals are in
normal range
The POWER
lights flashed
intermittently
The power supply is
unstable
The module is damage
RUN LED
light is OFF
Shut down remotely by
upper computer equipment
Make the upper
computer start up
remotely
System error outage
Check with the
Thermostat Assistant
COMM single
light is OFF
Bad cable connection, or the
signal attribute of the
connection line is wrong,
such as 485+ and 485-
connection
Connect the signal
lines together
Communication master and
slave machine
characteristics set
inconsistent, such as baud
rate, calibration, data
number, address
Set the
communication
parameters to be
consistent
ERR single
light is ON
System error outage
Check with
temperature control
assistant and consult
corrigendum manual
1. Warranty scope refers to the programmable controller body.
2. The warranty period is 18 months. If the product breaks down or is
damaged during normal use, our company will repair it free of charge.
3. The warranty period starts from the date the product is manufactured.
Machine code is the only basis for judging the warranty period.
Equipment without machine code shall be treated as under warranty.
4. Even within the warranty period, a maintenance fee will be charged
if:
Failure of the machine caused by failure to operate in
accordance with the user's manual.
Damage to machinery caused by fire, flood, abnormal voltage,
etc.
Damage caused when a programmable controller is used for

abnormal functions.
Self-disassemble the programmable controller.
5. The service fee shall be calculated according to the actual cost. If
there is another contract, the contract shall take precedence.
6. If you have any questions, please contact the agent or our company
directly.
SHENZHEN MEGMEET CONTROL TECHNOLOGY CO.,LTD
Add:floor 5, tower B, qinghua information port, langshan road, north
district, science and technology park, nanshan district, shenzhen
Tel:400-6662163
Fax:(+86)0755-26897197
Zip code:518067
Web:www.megmeet.com
This manual suits for next models
5
Table of contents
Other Megmeet Controllers manuals
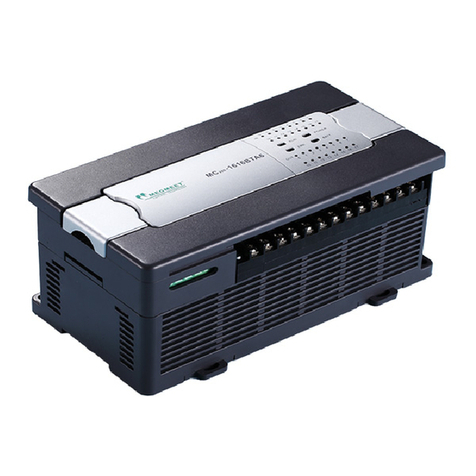
Megmeet
Megmeet MC200E Series Manual
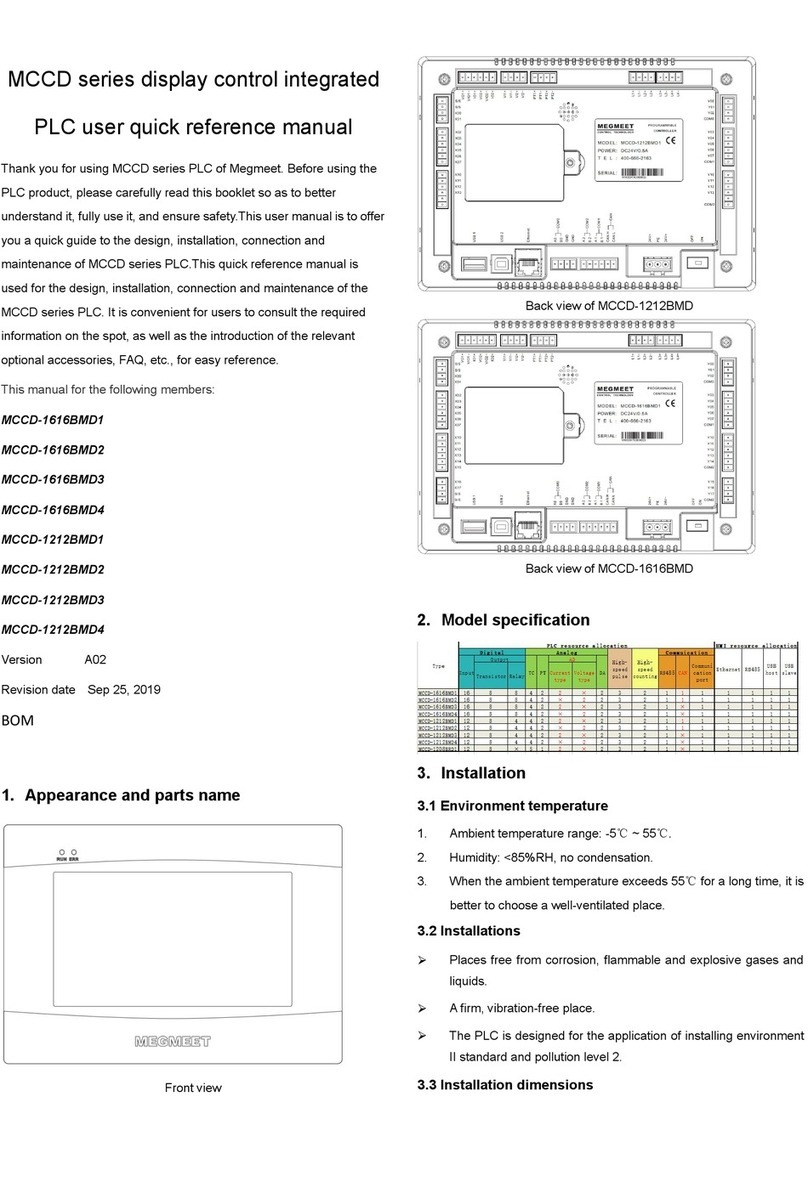
Megmeet
Megmeet MCCD Series Service manual

Megmeet
Megmeet MV820 User manual
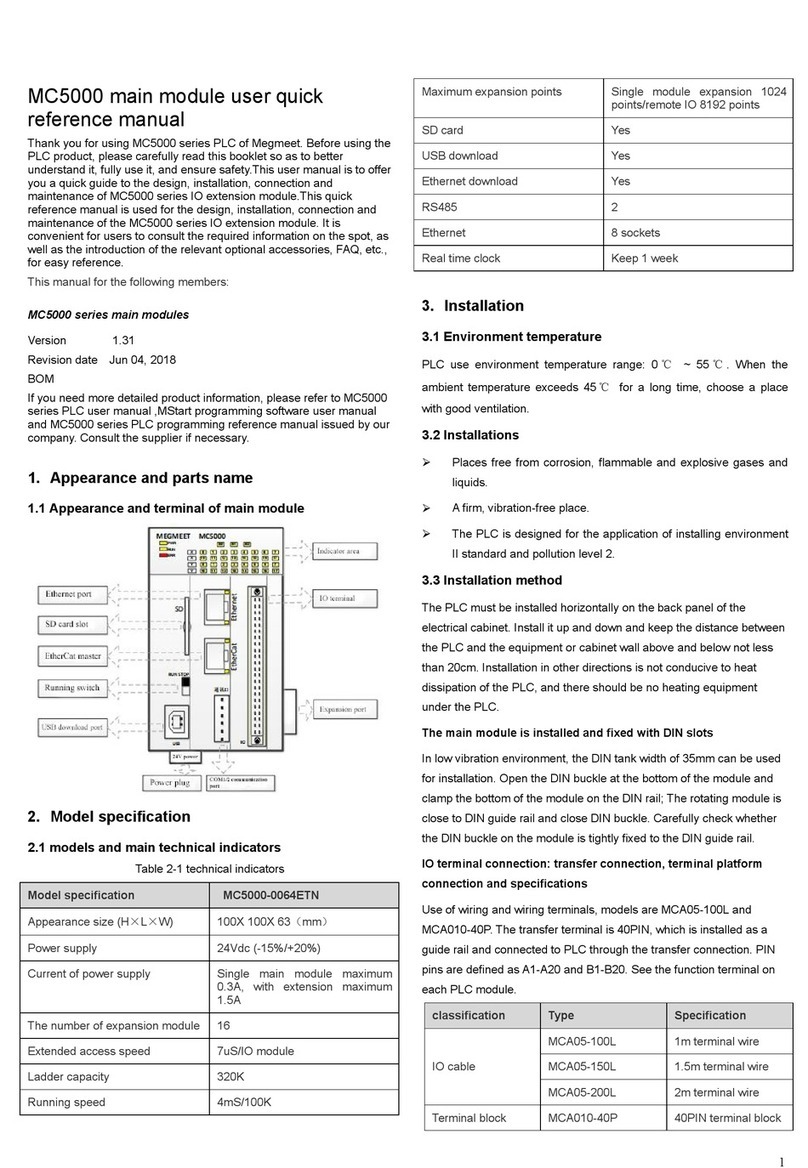
Megmeet
Megmeet MC5000 Series User manual
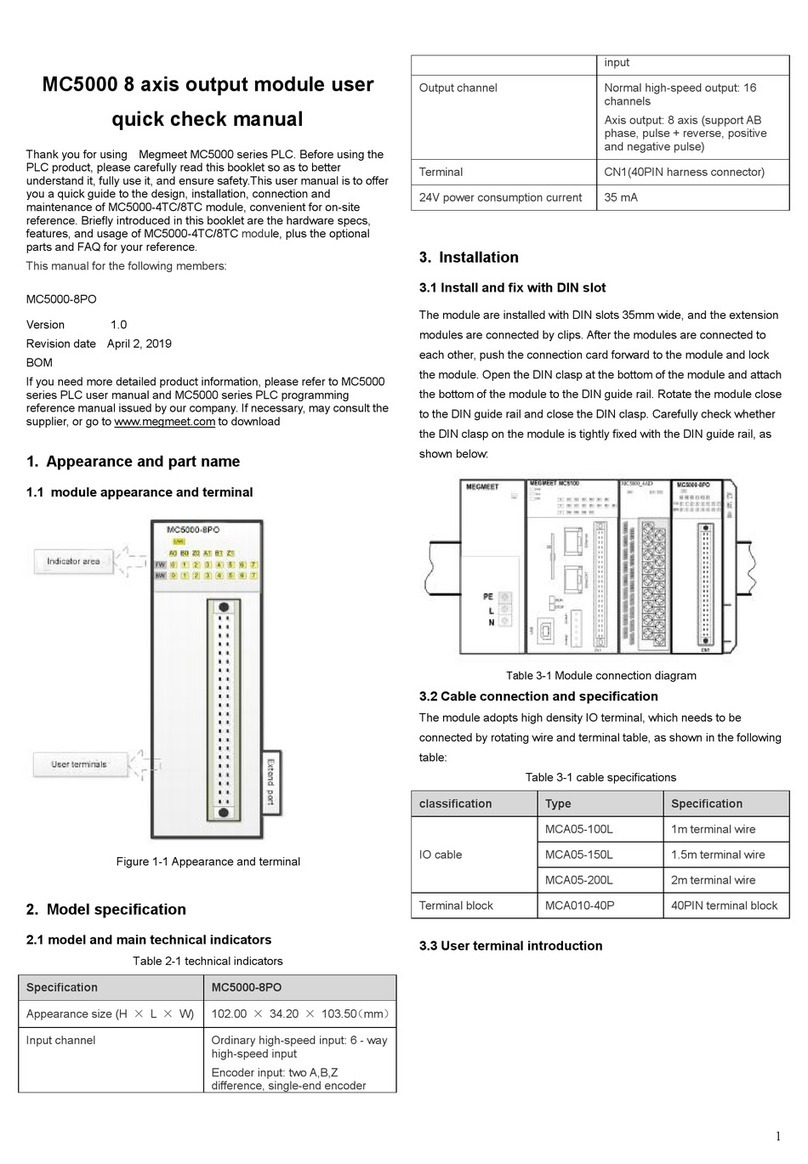
Megmeet
Megmeet MC5000 Series User manual
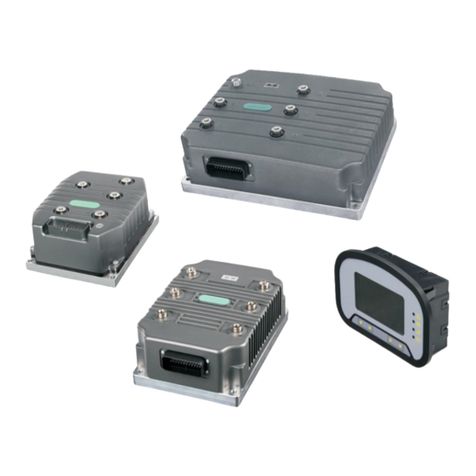
Megmeet
Megmeet L6 Series User manual
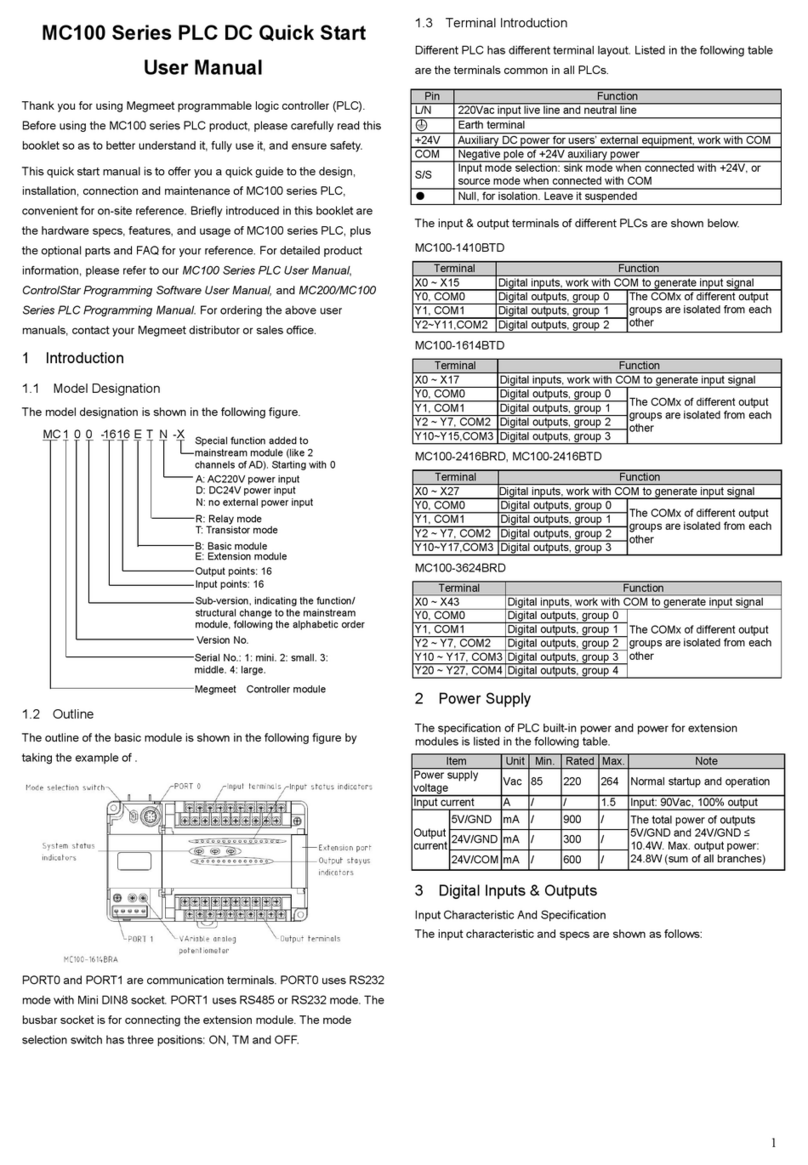
Megmeet
Megmeet MC100 Series User manual
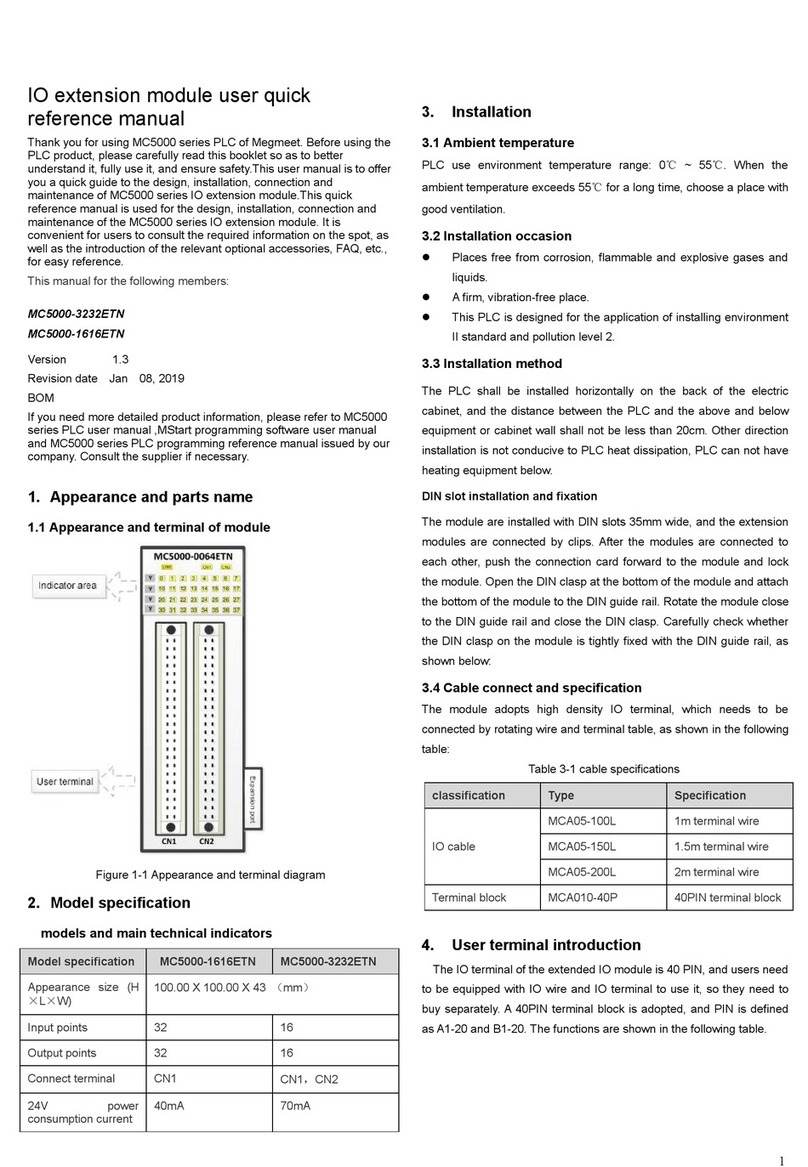
Megmeet
Megmeet MC5000 Series User manual
Popular Controllers manuals by other brands
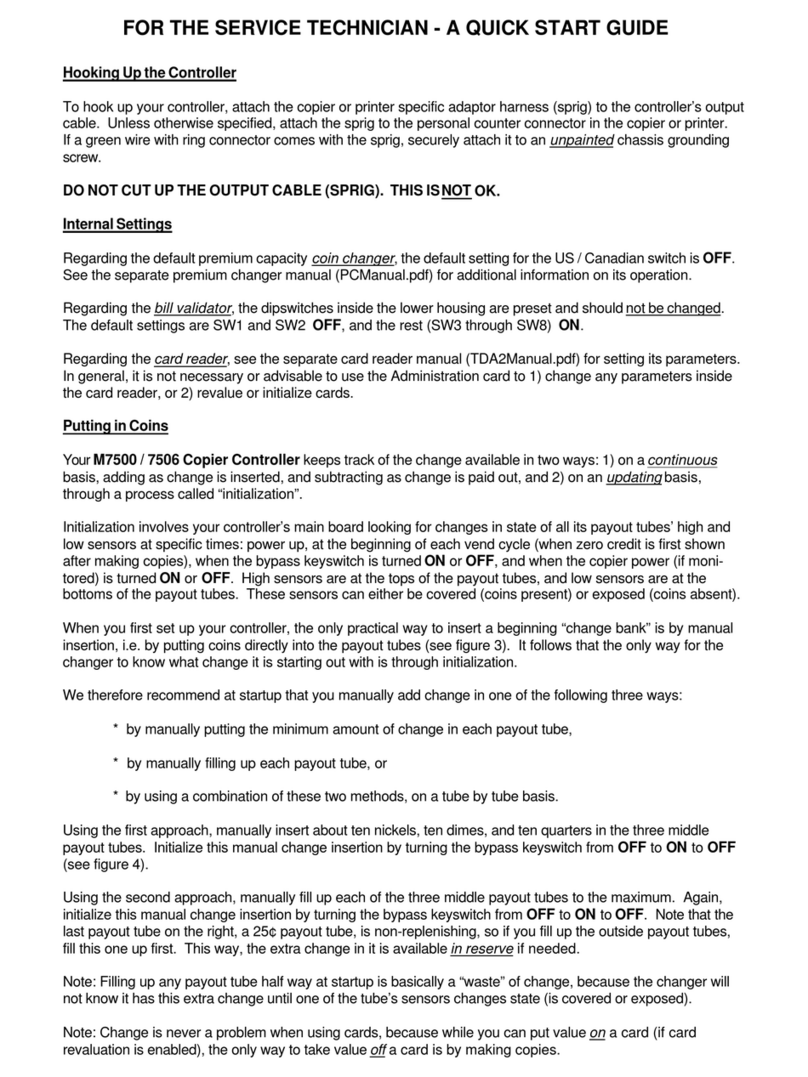
Advanced Technologies
Advanced Technologies M7000 Series User and technical manual
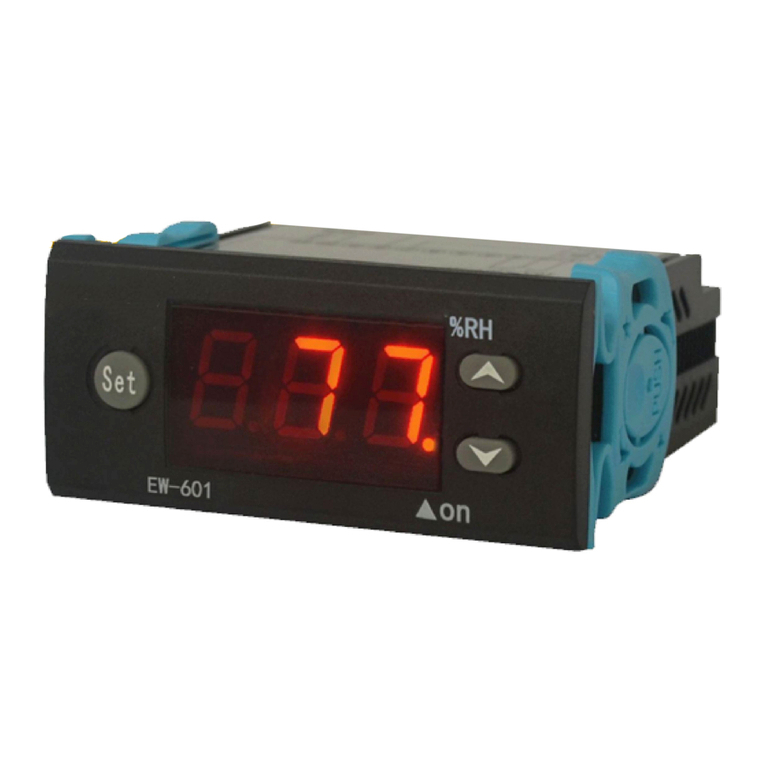
Eliweli
Eliweli EW-601 user manual
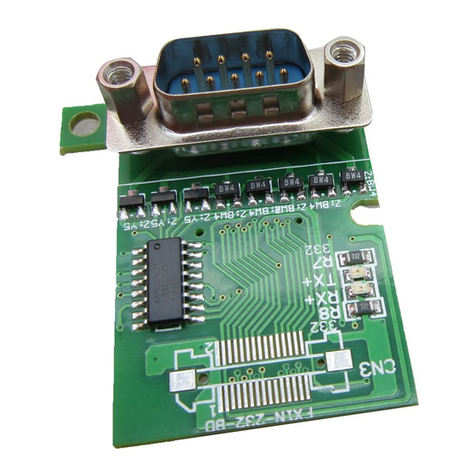
Mitsubishi
Mitsubishi FX3U-232-BD user manual
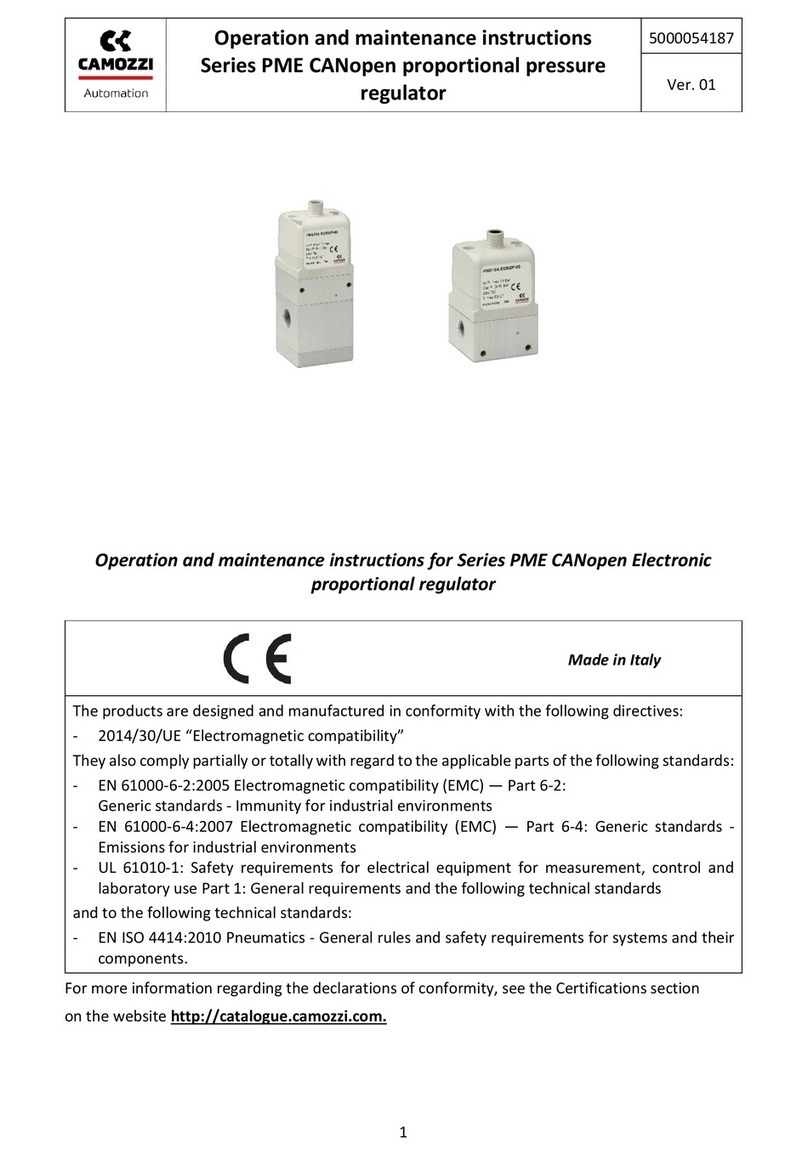
Camozzi
Camozzi PME Series Operation & maintenance instructions
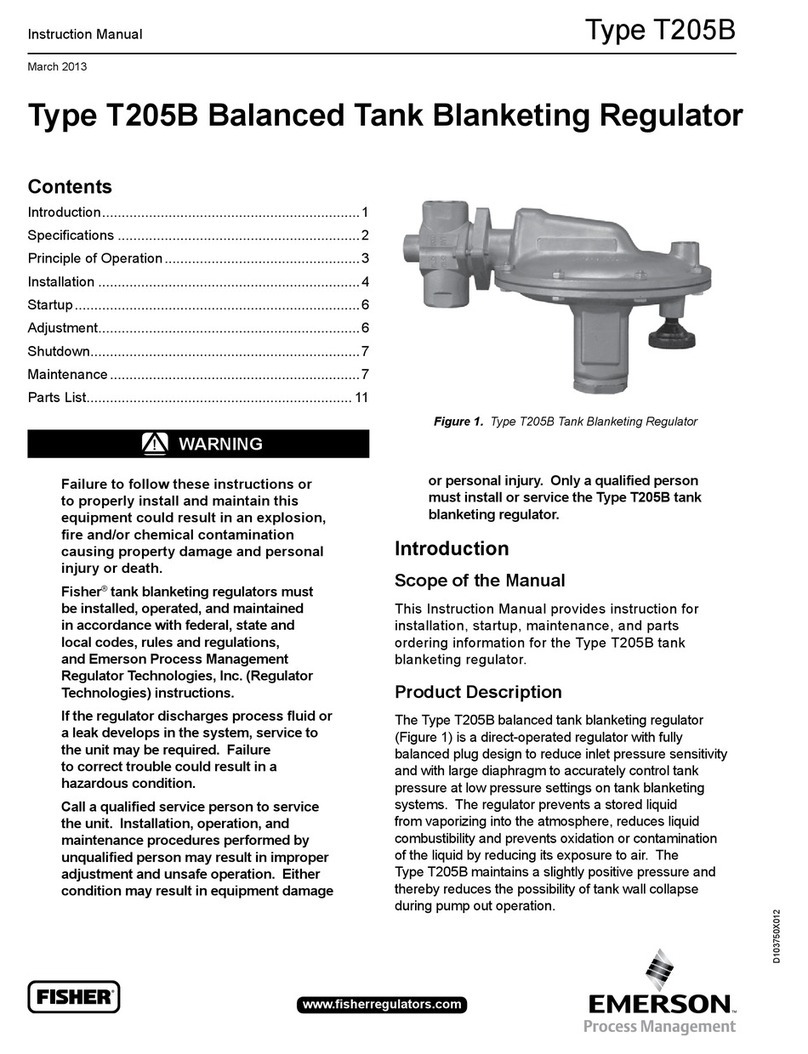
Emerson
Emerson FISHER T205B instruction manual
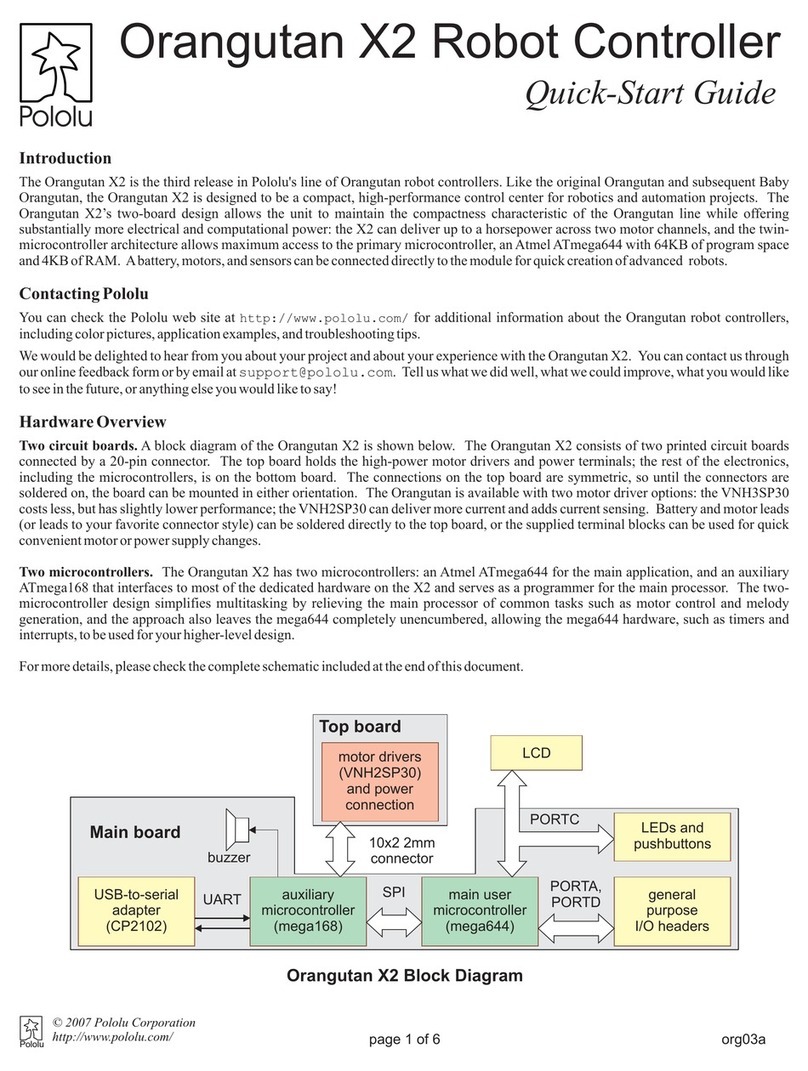
Pololu
Pololu Orangutan X2 quick start guide