Emtron ELC1 User manual

Z
ELC1/ ELC2/ ELC2M
USER
MANUAL
Rev 1.1
Emtron Lambda to
CAN

EMTRON ELC USER MANUAL
WWW.EMTRON.WORLD
© EMTRON AUSTRALIA PTY LTD MARCH 2018
1
Kit Contents
When purchasing an ELC1/ELC2 the following items are included:
▪ELC1/2 Device with Flying Harness
▪Deustch DTM 4-way mating connector with female pins (DTM06-4S)
ELC2 kit pictured.
When purchasing an ELC2M the loom side mating Autosport connector is not included but
can be purchased separately.

EMTRON ELC USER MANUAL
WWW.EMTRON.WORLD
© EMTRON AUSTRALIA PTY LTD MARCH 2018
2
Contents
1.0 Description ...........................................................................................................................3
2.0 Specification.........................................................................................................................5
3.0 Installation ...........................................................................................................................6
3.1 ELC1/2 Wiring...................................................................................................................6
3.2 ELC2M Wiring...................................................................................................................7
3.3 Bosch LSU4.9 Sensor Wiring ............................................................................................8
3.4 CAN Bus Wiring ................................................................................................................9
3.5 ELC CAN Bus ...................................................................................................................10
3.6 Noise Immunity..............................................................................................................11
4.0 Lambda Sensor Installation................................................................................................12
5.0 Heater Control and Sensor Calibration..............................................................................13
5.1 Heater Control ...............................................................................................................13
5.2 Sensor Calibration..........................................................................................................13
6.0 Exhaust Back Pressure (EMAP) Compensation..................................................................14
7.0 ELC Device Configuration...................................................................................................15
7.1 ELC Single Device Setup .................................................................................................15
7.11 ELC Device Detection ...............................................................................................15
7.12 ECU CAN Channel Configuration for Single Device..................................................16
7.2 ELC Multiple Device Setup .............................................................................................17
7.21 ELC Multiple Device Detection.................................................................................17
7.22 ELC CAN Base Address ID Reprogramming..............................................................18
7.23 ECU CAN Configuration for Multiple Devices ..........................................................19
8.0 ECU Channel Configuration................................................................................................20
9.0 ELC Custom Device Settings...............................................................................................22
10.0 Ordering Information.......................................................................................................23
Appendices...............................................................................................................................24
Appendix 1 –CAN Bus Data Packaging ................................................................................24

EMTRON ELC USER MANUAL
WWW.EMTRON.WORLD
© EMTRON AUSTRALIA PTY LTD MARCH 2018
3
1.0 Description
The Emtron Lambda to CAN devices are available in both Standard and Mil Spec versions.
ELC2M
The ELC2M is a Mil Spec Dual Channel Lambda to CAN device
using the Motorsport proven Deutsch Autosport connector
system(Green). The enclosure is made from billet 6061
aluminium and is waterproof, allowing for use in extreme
environments.
ELC1
The ELC1 is a Single Lambda to CAN device with a
concentric twisted flying loom system,
terminated with the reliable and environmentally
sealed Deutsch DTM connector. The water proof
enclosure is extremely compact and made from
billet 6061 aluminium.

EMTRON ELC USER MANUAL
WWW.EMTRON.WORLD
© EMTRON AUSTRALIA PTY LTD MARCH 2018
4
ELC2
The ELC2 is a Dual Channel Lambda to CAN device with
a concentric twisted flying loom system, terminated
with the reliable and environmentally sealed Deutsch
DTM connector. The waterproof enclosure is extremely
compact and made from billet 6061 aluminium.
All devices control the Bosch LSU4.9 Lambda Sensor and are compatible with all Emtron
ECUs. Bosch proven integrated circuit technology is used for sensor control, Nernst Cell
temperature measurement with advanced PID algorithms for precise heater control.
Exhaust Pressure compensation is available when enabled. The device is connected to the
ECU via CAN bus and will be automatically detected, significantly minimising configuration
time.

EMTRON ELC USER MANUAL
WWW.EMTRON.WORLD
© EMTRON AUSTRALIA PTY LTD MARCH 2018
5
2.0 Specification
Power Supply
▪Operating Voltage: 7.0 to 22.0 Volts DC
▪Operating Current Standby: 38mA at 14.0V
▪Operating Current Average: 3A at 14.0V (Peak 8A Warmup)
▪Reverse Battery Protection: 0mA current draw
▪Battery Transient/Over Current Protection
Internal
▪64MHz 16-bit Automotive Processor
Inputs
▪Bosch LSU4.9. Supports Single or Dual Channel
▪Resolution: 0.001 Lambda
▪Range: 0.580 Lambda to open air.
▪Lambda Signal sampling rate: 100 Hz
▪Exhaust Pressure Pump Current Compensation
Communications
▪CAN 2.0B Baud Rate: 250kBaud, 500kBaud or 1Mbaud Auto Detect
▪CAN Transmit Rate 100Hz
Operating Temperature
▪Operating Temperature Range: -30 to 85°C (-22 to 185°F)
Physical
ELC2M
▪Enclosure Size 52 mm x 74 mm x 18 mm
▪125g (Excludes loom)
ELC1/ ELC2
▪Enclosure Size 63mm x 54 mm x 20mm
▪ELC1 165g, ELC2 200g (includes flying loom)

EMTRON ELC USER MANUAL
WWW.EMTRON.WORLD
© EMTRON AUSTRALIA PTY LTD MARCH 2018
6
3.0 Installation
Each device has a M4 x 1.5 thread tapped into the base of the enclosure and can be used for
mounting. In high vibration applications rubber mounting is recommended.
CAUTION: When mounting the device inside the engine compartment, it should be
positioned in cooler areas and away from heat sources such as exhaust manifolds. Any
unnecessary radiated heat may affect device performance.
3.1 ELC1/2 Wiring
The pinouts are shown below in Table 3.0 and Table 3.1.
Power and CAN Flying Loom Connector: DTM
4 pin (M).
Pin
Function
Wire Colour
1
Ground
Black
2
CAN Lo
Green
3
CAN Hi
Yellow
4
12V Supply
Red
Table 3.0. ELC Power and CAN Deustch
Connector Pinout
Lambda Flying Loom Connector: Bosch LSU 4.9 (F)
Pin
Function
Wire Colour
1
Pump Current
Red
2
Virtual Ground
Yellow
3
Heater Ground
White
4
Heater 12 Supply
Grey
5
Cal Resistor
Orange
6
Nernst Cell Voltage
Black
Table 3.1 ELC1/2 LSU 4.9 Connector Pinout

EMTRON ELC USER MANUAL
WWW.EMTRON.WORLD
© EMTRON AUSTRALIA PTY LTD MARCH 2018
7
3.2 ELC2M Wiring
Mating Connector Loom Side
(Deutsch Autosport AS Series)
AS612-35PD (Green)
Pin
Function
Bosch Datasheet Reference
1
14 V Supply
2
Ground
3
CAN Hi
4
CAN Lo
5
Lambda 1 Pump Current
APE
6
Lambda 1 Nernst Cell Voltage
RE
7
Lambda 1 Cal Resistor
8
Lambda 1 Virtual Ground
IPN
9
Lambda 2 Pump Current
APE
10
Lambda 2 Nernst Cell Voltage
RE
11
Lambda 2 Cal Resistor
12
Lambda 2 Virtual Ground
IPN
13
Lambda 1 Heater Ground
14
Lambda 2 Heater Ground
15
Lambda 1 Heater 14V Supply (Protected)
16
Lambda 2 Heater 14V Supply (Protected)
17
(Not used)
18
(Not used)
19
(Not used)
20
(Not used)
21
(Not used)
22
(Not used)
Table 3.2. ELC2M Pinout

EMTRON ELC USER MANUAL
WWW.EMTRON.WORLD
© EMTRON AUSTRALIA PTY LTD MARCH 2018
8
3.3 Bosch LSU4.9 Sensor Wiring
Lambda Connector: Bosch LSU 4.9 (F)
Pin
Function
Wire Colour
1
Pump Current
Red
2
Virtual Ground
Yellow
3
Heater Ground
White
4
Heater 12 Supply
Grey
5
Cal Resistor
Orange
6
Nernst Cell Voltage
Black
Table 3.3. Bosch LSU 4.9 Sensor Pinout
Figure 3.0. LSU4.9 Connector Pinout
NOTE: To avoid signal errors and loss of accuracy, a cable of a maximum length of 1.5 m
between sensor and ELC is recommended.

EMTRON ELC USER MANUAL
WWW.EMTRON.WORLD
© EMTRON AUSTRALIA PTY LTD MARCH 2018
9
3.4 CAN Bus Wiring
▪CAN Bus High and Low are differential signals, so twisted pair MUST be used. Failing to
do so will compromise the entire CAN Bus System.
▪In some extreme environments, shielded twisted pair may be required to help with
reliability and data integrity.
▪The less connectors in any transmission system the better. Unnecessary connectors are
almost guaranteed to present an impedance discontinuity and hence may cause
reflections and data loss.
▪CAN Bus termination must be done correctly by using a 120 ohm 0.25W resistor at each
END of the bus system.
▪Maximum Stub length to a device from the main Bus is recommended at 0.3m, in
accordance with High-Speed ISO 11898 Standard specification. See Figure 3.3.
The ELC devices do not include an on-board CAN termination resistor, allowing the device to
be wired at any position on the Bus. CAN Bus termination must be done correctly by using a
120 ohm 0.25W resistor at each end of the bus system as mentioned above. Figures 3.1 and
3.2 show possible CAN Bus Implementation examples
Figure 3.1. CAN Bus Wiring Example. ECU and Dash at each end with 120 Ohm Termination
Figure 3.2. CAN Bus Wiring Example. ECU and ELC2 at each end with 120 Ohm Termination

EMTRON ELC USER MANUAL
WWW.EMTRON.WORLD
© EMTRON AUSTRALIA PTY LTD MARCH 2018
10
Figure 3.3. CAN Bus Wiring Example. Stub Length less than 0.3m
3.5 ELC CAN Bus
The ELC devices can be connected to the ECUs CAN Bus 1 or 2.
All devices on the CAN Bus must be configured to use the same baud rate. For this reason,
all Emtron CAN devices will Auto-scan the CAN bus until a successful baud rate has been
detected. Once detected this rate will be stored and used at the next power up.
The device will scan 3 different Baud rates at 500ms intervals moving from 1Mbaud ->
500kBaud -> 250k Baud -> 1Mbaud and so on.
NOTE: For this process to function effectively, when new devices are introduced to the CAN
bus, they should initially be connected one at a time. This allows each device to sync up to
the CAN Bus baud rate and store that setting. This typically takes 3-5 seconds.
The ELC devices leave the factory programmed with individual serial numbers, but all have
the same Base CAN Address ID used to transmit data over the Bus. The CAN Base address
can be adjusted from the factory setting using the ID Reprogramming Tool. This is required
when 2 or more of the same devices are connected to the CAN Bus (See section 4.2).
▪Factory CAN Base Address of 671. Transmits data sequentially on the next ID. Total
CAN ID Range is therefore 671 –672.
▪Up to 6x ELC devices (ELC or ELCM) can be used on the CAN Bus giving a total of 12
available Lambda Channels.

EMTRON ELC USER MANUAL
WWW.EMTRON.WORLD
© EMTRON AUSTRALIA PTY LTD MARCH 2018
11
3.6 Noise Immunity
To minimise signal contamination and maximise noise immunity, the wire pairs shown in
Table 3.2 must be twisted. It is recommended to twist the wire pairs at a minimum one twist
per 40mm of cable. This is very important and should always be implemented on both CAN
Bus and LSU Sensor wiring.
Pair 1
Pair 2
CAN High
<------->
CAN Low
Pump Current
<------->
Cal Resistor
Nernst Cell
Voltage
<------->
Virtual Ground
Table 3.4. Wire pairing for twisting

EMTRON ELC USER MANUAL
WWW.EMTRON.WORLD
© EMTRON AUSTRALIA PTY LTD MARCH 2018
12
4.0 Lambda Sensor Installation
Installation angle must be inclined at least 10° towards horizontal, (electrical connection
upwards) up to a maximum of 75°. This prevents the collection of liquids between sensor
housing and sensor element during the cold start phase.
The angle against the exhaust gas stream should be aimed as 90°. Maximum inclination
should be 90°+15° (protection tube towards gas stream) or 90°-30°.
NOTE: NEVER mount the sensor directly on the horizontal or within 10 degrees of the
horizontal. Doing so will result in intermittent sensor shutdown.
Also route the sensor cable to avoid high moisture locations –just a small amount of
moisture is enough to provide a conductive path within the connector that will upset
measurement from the sensor.
Winter and salted roads compound this issue. Always check for a cracked or broken
connector when strange results occur.

EMTRON ELC USER MANUAL
WWW.EMTRON.WORLD
© EMTRON AUSTRALIA PTY LTD MARCH 2018
13
5.0 Heater Control and Sensor Calibration
5.1 Heater Control
During engine start-up, condensation forms in the exhaust which may damage the sensor. It
is recommended to only start heating the LSU sensor after the engine is running and the
moisture content in the exhaust has evaporated. ELC settings allow the ECU to control
heater setup if enabled.
For maximum sensor life the ECU should control heater start-up. It does this by
communicating with the ELC over CAN Bus. For setup options see Config View ->
Communications Tab -> Emtron CAN Device -> Emtron Lambda to CAN (ELC/ELCM) Setup.
See Figure 5.0.
Figure 5.0. Emtune ELC Setup menu - Heater Control
Once changed, the settings are automatically stored by the ELC and therefore used on the
next power cycle. If the CAN bus is not used to control the heater (Enable Heater Override =
OFF), then by default the heater remains OFF for 15 seconds after the device is powered up.
5.2 Sensor Calibration
The sensor is calibrated by the ELC on power up. During the Calibration process two
important pieces of data are read:
▪The optimal Nernst Cell Temperature which is used for sensor heater control. The
ELC applies duty cycle and a PID routine to maintain a constant and accurate heater
temperature which results in a very stable and accurate Lambda value.
▪The Pump Current that corresponds to a Lambda reading of 1.000 Lambda.
NOTE: A Free-Air Calibration is NOT required on the LSU4.9. The sensor uses a reference
pump current instead of reference air. The big advantage with this is that the reference is a
calibrated electrical signal and remains constant.

EMTRON ELC USER MANUAL
WWW.EMTRON.WORLD
© EMTRON AUSTRALIA PTY LTD MARCH 2018
14
6.0 Exhaust Back Pressure (EMAP) Compensation
Wideband Lambda sensors primarily count oxygen atom numbers through measuring the
oxygen ion current within the sensors pump cell. The exhaust gas pressure affects this
oxygen ion current. The more pressure means more atoms per unit volume and a higher
pump current at the same Lambda i.e. this will cause the sensor to read farther from
stoichiometric.
A rich reading will appear richer than it really is.
A lean reading will appear leaner than it really is.
This predominantly becomes an issue in Turbocharged applications. This is the main reason
you should position the sensor after the turbo where exhaust back-pressure is lowest.
Excessive Exhaust Back Pressure (EMAP) can also damage the sensor. The following rule
should be observed:
Exhaust Back Pressure < 2.5 Bar
When measuring Exhaust Back Pressure, an Absolute Pressure Sensor MUST be used. (i.e.
do not use a Gauge Pressure Sensor). The ECU MUST have the Exhaust Manifold Pressure
channel configured so data transmitted from ECU to ELC is valid.
The EMAP setting can be enabled by going to the the Config View -> Communications Tab ->
Emtron CAN Device -> Emtron Lambda to CAN (ELC/ELCM) Setup and selecting the “Enable
EMAP”setting to ON (Figure 6.0). Once enabled to ECU will transmit the EMAP value over
the CAN Bus and the ELC will received this value so the correction can be applied.
Figure 6.0. Emtune ELC setup menu - EMAP Enable
NOTE: Once changed, the setting is automatically stored by the ELC and therefore used on
the next power cycle.

EMTRON ELC USER MANUAL
WWW.EMTRON.WORLD
© EMTRON AUSTRALIA PTY LTD MARCH 2018
15
7.0 ELC Device Configuration
Once the ELC is powered and connected to the ECU’s CAN bus, the following steps should be
taken to complete the setup. All setup and device monitoring is done using Emtune so this
software needs to be installed and connected to the ECU.
7.1 ELC Single Device Setup
This section outlines the setup procedure for a single device and involves 2 steps:
1. Device Detection by the ECU
2. ECU CAN Bus configuration
7.11 ELC Device Detection
To confirm the ELC device has been detected, connect to the ECU using Emtune. Open the
ECU Runtime menu (F3) and select the Communications Tab. Within this tab there will be a
list of Emtron CAN devices the ECU has detected. It will list:
1. CAN Device Model
2. Device Serial Number
3. Device Firmware Version
4. Device Hardware Version
5. CAN Base Address ID
With a single ELC device connected, the data should look as shown in Figure 7.0/7.1.
Important:
▪At this stage the ECU has only detected the device. It has not been configured to an ECU
CAN Channel so the ELC data is not yet available.
▪Note the CAN Base Address ID. This is required in the ECU CAN setup. The factory setting
is ID 671 for the ELC and ELC2M.

EMTRON ELC USER MANUAL
WWW.EMTRON.WORLD
© EMTRON AUSTRALIA PTY LTD MARCH 2018
16
Figure 7.0. Example ELC2M device detected by the ECU.
Figure 7.1. Example ELC2 device detected by the ECU
7.12 ECU CAN Channel Configuration for Single Device
The next step is to configure an ECU CAN channel, allowing the ECU to decode the ELC CAN
packets.
For this example, CAN 1- Channel 1 has been selected.
1. Set "Enable" to (ON)
2. Set "CAN Base Address" to the ID shown in Figure 7.0/7.1 In this example its ID 671.
3. Set "DATA Set" to 50 (ELC/ELC2M 1x Device). See Figure 7.2.
The ECU in now configured and reading the data from the ELC Device.
Figure 7.2. ELC CAN Configuration

EMTRON ELC USER MANUAL
WWW.EMTRON.WORLD
© EMTRON AUSTRALIA PTY LTD MARCH 2018
17
7.2 ELC Multiple Device Setup
As mentioned in section 3.5, the Base CAN Address ID used to transmit Data over the Bus by
default is the same for each device type. The ELC has a factory CAN Base Address of 671.
When multiple ELC devices are installed on the same CAN Bus, each device MUST have a
unique CAN Base Address to avoid Bus conflicts. This means the CAN Base Address ID will
need to be reprogrammed which is a simple task using the ID Reprogramming Tool as
outlined in section 7.22.
REMEMBER: For this process to function effectively, when multiple new devices are
introduced to the CAN bus, they should initially be connected one at a time. This allows
each device to sync up to the CAN Bus baud rate and store that setting. This usually takes 3-
5 seconds.
7.21 ELC Multiple Device Detection
To confirm the ELC device has been detected, connect to the ECU using Emtune. Open the
ECU Runtime menu (F3) and select the Communications Tab. Within this tab there will be a
list of Emtron CAN devices the ECU has detected. It will list:
1. CAN Device Model
2. Device Serial Number
3. Device Firmware Version
4. Device Hardware Version
5. CAN Base Address
With multiple ELC devices connected, the CAN Summary List should look as shown in Figure
7.3. In this example x2 ELC2 devices are connected to the BUS. Device 1 with SN 1241 and
Device 2 with SN 1242.
Figure 7.3. Example show two ELC2 Devices detected by the ECU

EMTRON ELC USER MANUAL
WWW.EMTRON.WORLD
© EMTRON AUSTRALIA PTY LTD MARCH 2018
18
Note: ALL devices have the same Base Address of ID 671, which is the factory setting for a
single device. To avoid Bus conflicts, the factory base address needs to be changed when
multiple devices are used, to ensure each device has its own unique ID. When re-
programming the Base Address for each device the IDs MUST be:
1) Sequential in order.
2) Have a gap of 2 numbers between each ELC device.
The Base Address ID can be any number but Emtron recommends the following:
•ELC Device 1: ID Base Address 671. (CAN ID Range 671-672)
•ELC Device 2: ID Base Address 722. (CAN ID Range 673-674)
•ELC Device 3: ID Base Address 722. (CAN ID Range 675-676)
•ELC Device 4: ID Base Address 722. (CAN ID Range 677-678)
•ELC Device 5: ID Base Address 722. (CAN ID Range 679-680)
•ELC Device 6: ID Base Address 722. (CAN ID Range 681-682)
7.22 ELC CAN Base Address ID Reprogramming
To ensure each ELC device has a unique ID from the example in Figure 7.3, ELC2 Device 2
(SN 1242) needs a new Base Address of 673.
This is easily done using Emtune from the Config view -> Communications Menu -> Emtron
CAN Devices -> Emtron CAN Device Programming menu
In this example, ELC Device 2 will need to have its Base Address re-programmed to 673. This
is easily done using Emtune from the Config view -> Communications Menu -> Emtron CAN
Devices -> Emtron CAN Device Programming menu. In this example select:
Device 2 ID Reprogramming
Enter in Serial Number = 1242
Enter in Custom Address = 673
Make sure the “Program
Address” checkbox is ticked.
Select the “Program” button and the new Custom Address ID will be programmed into the
device.

EMTRON ELC USER MANUAL
WWW.EMTRON.WORLD
© EMTRON AUSTRALIA PTY LTD MARCH 2018
19
To check the device has been correctly programmed with the new CAN Base Address, open
the F3 menu -> Communications Tab. CAN device 2 with SN 1242 should have a new Base
Address of 673. See Figure 7.5
Figure 7.5. 2x ELC Devices detected by the ECU with reprogrammed IDs
7.23 ECU CAN Configuration for Multiple Devices
The next step is to configure an ECU CAN channel, allowing the ECU to decode the ELC CAN
packets.
Only 1 CAN Channel is required for multiple devices. CAN 1 - Channel 4 has been selected.
Config as follows:
1. Set “Enable" to 1(ON)”
2. Set "CAN Base Address" to the
Lowest Base Address ID shown
in Figure 7.5. In this example
its 671.
3. Set "DATA Set" to 51 -Emtron
ELC/ELCM 2x Devices (CAN PID
671/673).
The ECU is now configured and will receive data from all devices on IDs 671-672, 673-674.
NOTE: You only need to program in the lowest Base Address . The ECU automatically
configures the remaining IDs based on the assumption that the IDs are sequential in order.
This manual suits for next models
2
Table of contents
Other Emtron Cables And Connectors manuals
Popular Cables And Connectors manuals by other brands
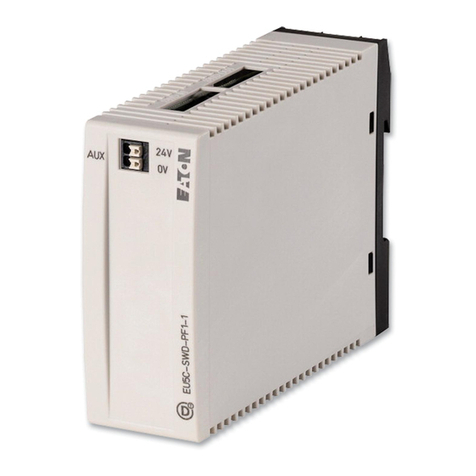
Eaton
Eaton Moeller SmartWire-Darwin Series Hardware and engineering
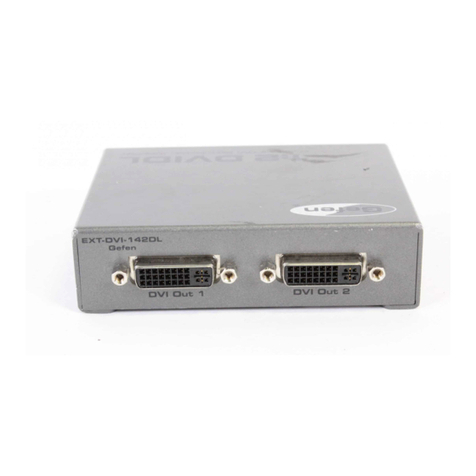
Gefen
Gefen EXT-DVI-142DL user manual

Philips
Philips SWA3605W Specification sheet
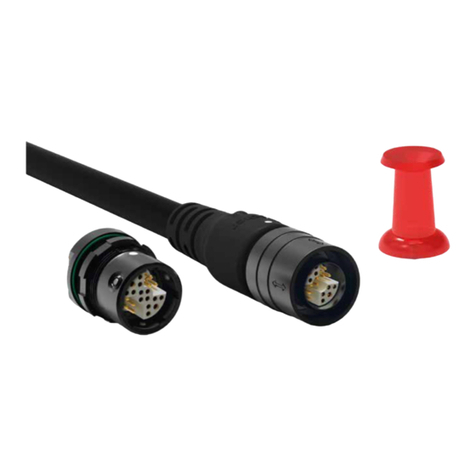
Fischer Connectors
Fischer Connectors MINIMAX SERIES Assembly instructions
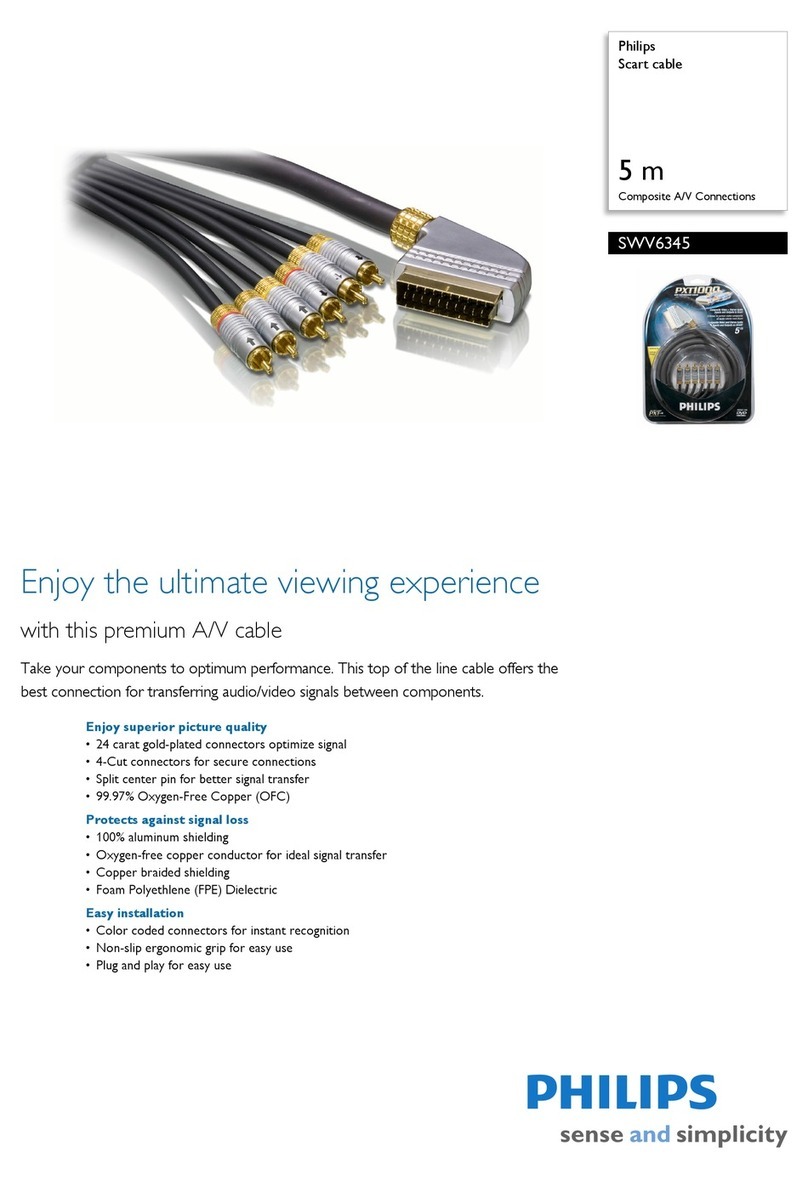
Philips
Philips SWV6345 Specifications
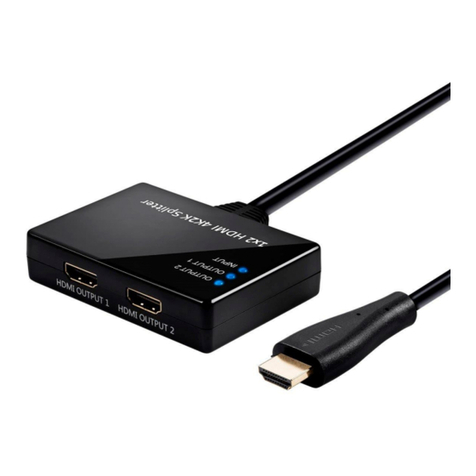
Monoprice
Monoprice Blackbird 12522 user manual