Entron EN7000-TS User manual

EN7000-TS
Touch-screen programming
User Guide
This user guide demonstrates the use of the EN7000 touchscreen. Reference the
EN7000 Technical Manual for further details of parameters.
Forfirmwareversion1.12
Documentrevision1

2|Page
Contents
Page
Section 1
How to use the Touch Screen……..3
Section 2
Editing Parameters…………………..6
Section 3
Menus…………………………………..8
Section 4
Quick Start……………………..…….39

Section 1 – How to use the touch-screen
3|Page
Note: Not all parameters are visible at any one time. Many parameters are
dependent on other parameters. Only relevant parameters are displayed
as this reduces clutter on the screen. The screens shown here are typical
and may not be exactly what you will see.
1.1 Start-up
On Start-up, the display will show the splash screen.
Proceed to the Main Menu by tapping the Home icon (bottom right).

Section 1 – How to use the touch-screen
4|Page
1.2 Menu screen
The items described below are common to every menu screen.
UseProgram
DiscreteI/O ˄
2
HistoryLog System ˅
12
3
4
5
6
Program BusI/O
Electrode AnalogI/O
i
MainMenu
1 Tapping the i in the center of the banner will display the Status screen.
Tappin
g
it from the Status screen will return to the previous screen.
2 Tappin
g
the Home icon will return to the previous screen.
3 Tappin
g
the UP ar
r
ow scrolls the displa
y
up one line at a time.
4 The size of the scroll bar handle indicates how many additional items
there are in the menu. The smaller the handle, the more items there are
in the entire menu to be displa
y
ed.
5 Tapping the blue area in the scroll bar will scroll the display up or down
one pa
g
e at a time.
6 Tappin
g
the DOWN arrow scrolls the displa
y
down one line at a time.
The remaining area is divided up into eight labeled buttons. Tapping one of these
buttons will either
Open the sub-menu for that function.
OR
Open an information window.
OR
If the button contains a parameter, edit that parameter.

Section 1 – How to use the touch-screen
5|Page
1.3 Status screen
This screen presents useful information regarding the status of the control and
the measurements from the last weld. Access the Status screen by tapping on
the i icon on the banner of any menu.
Pos t‐he a t
Progra m 2
Force 100lb
˄
Ready
1
2
3
4
5
6
Conducti o
n
35.5%
7
˅
2.00kA
5.00kA
1.00kA
Pre‐heat
Ma i nHe a t
i
Status
1 This field displays the control status. Tapping on this field will display
a messa
g
e screen
g
ivin
g
the option to reset the status.
2 Pre-heat current from the last weld
3 Main heat current from the last weld
4 Post-heat current from the last weld (Extended Features must be
enabled in the Confi
g
uration menu
)
5 Pro
g
ram used for the last weld
6 Force measured from the last weld
7 Percent Conduction of the SCR from the last weld
Tap the i in the center of the banner to return to the previous screen.
Tap the HOME key to go to the main menu

Section 2 – Editing parameters
6|Page
Parameters can be edited in several different ways, depending upon their nature.
2.1 Numeric
When you tap on a button showing a numeric parameter, an editor window
opens:
e.g.
1 Present value of paramete
r
2 Use the ke
y
pad to enter a new value
3 Cancel the entr
y
(
present value remains unchan
g
ed
)
4 Backspace the value in field 1
5 Enter the selected value
(
parameter is chan
g
ed to new value
)
Initially, the present value is shown. In the above example the parameter
called Use Program is set to the value 2.
Tap on the numeric buttons to enter a new value, then tap the green tick
key. The editor will close and return to the previous screen, showing the new
value entered.
If you enter an illegal value, a warning message appears and the parameter is
not changed. Close the warning message by taping on the red X key in the
top right corner.

Section 2 – Editing parameters
7|Page
2.2 Radio button
This type of parameter has only two options.
e.g.
Standard Extended
Features
The presently selected option is highlighted. In the above example the
parameter called Features is set to Standard.
Each time you tap on the button, the parameter is set to the other option.
2.3 Multi-option
This type of parameter has more than two options.
e.g.
I/OSource
DISCRETE
The presently selected option is shown. In the above example the parameter
called I/O source is set to DISCRETE.
Each time you tap on the button the parameter will change to the next option
in the list. After the final option, the list starts again with the first option.
2.4 Check box
This type of parameter is either on (box ticked) or off (box clear).
e.g.
Stop
onFault
In the above example the parameter called ‘Stop on fault’ is on.
Each time you tap on the button the parameter toggles between on (box
ticked) and off (box clear).

Section 3 – Menus
8|Page
This section describes the hierarchy of menus which allow access to the parameters.
Not all parameters are visible at any one time. Many parameters are dependent on
other parameters. Only relevant parameters are displayed as this reduces clutter on the
screen. The screens shown here are typical and may not be exactly what you will see.
Wherever you see the symbol in this section, this indicates that the
parameter is only available if Extended features is selected in the Configure menu.
The Main menu is the hub from which all sub-menus are accessed.
DiscreteI/O
BusI/O
AnalogI/O
System
0
Configure
˅
Electrode
HistoryLog
UseProgram
˄
Program
i
MainMenu
Extended

Section 3 – Menus
9|Page
3.1 Use Program (parameter)
Sets the program number selected to execute when the START signal is applied.
This parameter will not be available if the configuration parameter Program
select is set to Extern.
3.2 Program menu
The Program menu is used to configure parameters in a weld schedule. There
are settings in the Options and Configuration menus that will determine which
of these parameters are displayed.
Program
Time ˄
0
Current Force
Valves Options
Copy START
˅
Linktoprogram
1
Electrode
0
i
Programmenu
3.2.1. Program (parameter)
Select the program to edit. Subsequent program parameter edits will
apply only to the program set here.
3.2.2. Link to Program (parameter)
Select the program to link to the program being edited. Linking must be
enabled in the Options menu for this field to be displayed. The linked
program will automatically begin after the program being edited executes if
the START signal is maintained.
3.2.3. Electrode (parameter)
Select the electrode to be assigned to the program being edited. Multi
Electrodes must be selected in the Configuration menu.
Extended
Extended

Section 3 – Menus
10|Page
3.2.4. Timing menu
50~
Hold
Pre‐heat
˄
10~20~
Squeeze
Upslope
2~
Cool2
˅
Downslope
2~
20~
Post‐heat
20~
Cool1
2~
MainHeat
30~
i
Timing:Program 0
3.2.4.1. Presqueeze (parameter)
Time interval between program initiation and the start of squeeze
time. Only occurs on the first spot of a Repeat mode spot
sequence. Used to allow for large initial movements of the welding
electrodes.
3.2.4.2. Squeeze (parameter)
Time interval between end of Presqueeze time and the application
of weld current. Used to allow the electrodes to develop the desired
force.
3.2.4.3. Pre-heat (parameter)
Time interval where the Pre-heat current is applied. Pre-heat must
be enabled in the Program Options menu.
3.2.4.4. Cool1 (parameter)
Time interval between end of Pre-heat time and start of Upslope
time where no current is passed. Pre-heat must be enabled in the
Program Options menu to use this feature.
3.2.4.5. Upslope (parameter)
Time interval for the welding current to change from the Pre-heat
value to the Main Heat value.

Section 3 – Menus
11|Page
3.2.4.6. Main heat (parameter)
Time interval for the main welding current.
3.2.4.7. Cool2 (parameter)
Time interval where no current is passed. For spot mode, there
must be more than 1 Pulsation in the Program Options menu to
use this feature.
3.2.4.8. Downslope (parameter)
Time interval for the welding current to change from the Main Heat
value to the Post-heat value.
3.2.4.9. Post-heat (parameter)
Time interval where the Post-heat current is applied. To use this
feature, Post-heat must be enabled in the Program Options
menu.
3.2.4.10. Hold (parameter)
Time interval where the force is maintained and no current is
passed. Used to allow the nugget to congeal.
3.2.4.11. Off (parameter)
Time interval where the electrode force is released until the next
sequence begins. Repeat spot mode or Roll-spot mode must be
enabled in the Program Options menu to use this feature.
Extended

Section 3 – Menus
12|Page
3.2.5. Current menu
PHA CCR
PHA CCR
PHA CCR
2.00kA
LowLimit
5%
Pre‐heatmode Pre‐heat
0%
Monitor
Current(pre)
Monitor
Current(main)
Monitor
Current(post)
HighLimit
5%
Post‐heatmode Post‐heat
20%
Current(post)
Current(main)
˅
10.00kA
Mainheatmode Mainheat
0%
˄
Current(pre)
2.00kA
i
Current: Program0
3.2.5.1. Pre-heat mode (parameter)
Regulation mode for pre-heat. Phase Angle (PHA) provides no
current regulation but uses a fixed SCR firing angle. Constant
Current Regulation (CCR) provides closed loop regulation to control
the current to a specified value.
3.2.5.2. Pre-heat (parameter)
Percent heat (0 – 99.9%) to be used in PHA mode.
3.2.5.3. Current (pre) (parameter)
Current to be used in CCR mode. This parameter also serves as
the pre-heat monitor set-point for both PHA and CCR modes.
3.2.5.4. Monitor Current (pre) (parameter)
Check this box to enable current monitoring during the pre-heat
interval. Current will be monitored to be within the Low and High
Limit parameters in this menu.

Section 3 – Menus
13|Page
3.2.5.5. Main heat mode (parameter)
Regulation mode for main heat. Phase Angle (PHA) provides no
current regulation but uses a fixed SCR firing angle. Constant
Current Regulation (CCR) provides closed loop regulation to control
the current to a specified value.
3.2.5.6. Main heat (parameter)
Percent heat (0 – 99.9%) to be used in PHA mode.
3.2.5.7. Current (Main) (parameter)
Current to be used in CCR mode. This parameter also serves as
the main-heat monitor set-point for both PHA and CCR modes.
3.2.5.8. Monitor Current (main) (parameter)
Check this box to enable current monitoring during the main heat
interval. Current will be monitored to be within the Low and High
Limit parameters in this menu.
3.2.5.9. Post-heat mode (parameter)
Regulation mode for post-heat. Phase Angle (PHA) provides no
current regulation but uses a fixed SCR firing angle. Constant
Current Regulation (CCR) provides closed loop regulation to control
the current to a specified value.
3.2.5.10. Post-heat (parameter)
Percent heat (0 – 99.9%) to be used in PHA mode.
3.2.5.11. Current (post) (parameter)
Current to be used in CCR mode. This parameter also serves as
the post-heat monitor set-point for both PHA and CCR modes.
3.2.5.12. Monitor Current (post) (parameter)
Check this box to enable current monitoring during the post-heat
interval. Current will be monitored to be within the Low and High
Limits set in this menu.
3.2.5.13. Balance (parameter)
Seam welds only. Adjusts the current in the first half-cycle of any
pulse within a seam weld, to reduce transient effects.
Extended
Extended
Extended
Extended
Extended

Section 3 – Menus
14|Page
3.2.6. Force menu
If Force Profile is not selected (or not shown) in the Options menu, the
Force menu will only include the items shown below.
The Force value shown below will be used for the entire duration of the
program:
Monitor
Force
˄
LowLimit HighLimit
5% 5%
Force
500lb
˅
Waitfor
Force
i
Force:Program0
Force Menu without Force Profile
If Force Profile is selected in the Options menu, the Force menu will
include the items shown below. Using the Force Profile provides the
opportunity to use different force values in each program interval.
500lb
Post‐heat
500lb
Hold
500lb
MainHeat
450lb
Cool2
500lb
Downslope
˅
˄
LowLimit HighLimit
5% 5%
Monitor
Force
Waitfor
Force
Squeeze
500lb
Pre‐heat
600lb
Cool1
500lb
Upslope
550lb
i
Force:Program0
Force Menu with Force Profile
Extended

Section 3 – Menus
15|Page
3.2.6.1. Wait for Force (parameter)
Checking this box will cause the control to wait for the Analog Force
input to be within the High and Low Force Limits before proceeding
to weld. It can be set to occur before or after Squeeze in the
Configuration menu (see 3.5.10).
3.2.6.2. Monitor Force (parameter)
Check this box to monitor the force at the end of the main-heat
interval. The measured value is checked between the Low and
High limits.
3.2.6.3. Low Limit (parameter)
The Low Force Limit in percent used by the Force Monitor
3.2.6.4. High Limit (parameter)
The High Force Limit in percent used by the Force Monitor
3.2.6.5. Squeeze (parameter)
Force used from the start of the Squeeze interval
3.2.6.6. Pre-heat (parameter)
Force used from the start of the Pre-heat interval
3.2.6.7. Cool 1 (parameter)
Force used from the start of the Cool 1 interval
3.2.6.8. Upslope (parameter)
Force used from the start of the Upslope interval
3.2.6.9. Main Heat (parameter)
Force used from the start of the Main Heat interval
3.2.6.10. Cool 2 (parameter)
Force used from the start of the Cool 2 interval
3.2.6.11. Downslope (parameter)
Force used from the start of the Downslope interval
3.2.6.12. Post-heat (parameter)
Force used from the start of the Post-heat interval
Extended
Extended
Extended
Extended
Extended
Extended
Extended
Extended

Section 3 – Menus
16|Page
3.2.6.13. Hold (parameter)
Force used from the start of the Hold interval
3.2.6.14. Off (parameter)
Force used from the start of the Off interval
Extended
Extended

Section 3 – Menus
17|Page
3.2.7. Valves menu
Off ‐‐‐‐‐‐‐‐
Mainheat
Cool2
Downslope
Post‐heat
Hold
Cool1 ‐‐‐‐‐‐‐‐
‐‐‐‐‐‐‐‐
‐‐‐‐‐‐‐‐
‐‐‐‐‐‐‐‐
˅
Upslope
Pre‐heat ‐‐‐‐‐‐‐‐
‐‐‐‐‐‐‐‐
‐‐‐‐‐‐‐‐
‐‐‐‐‐‐‐‐
MOTOR
Squeeze
‐2‐‐‐‐‐‐
‐‐3‐‐‐‐‐
WAV 1‐‐‐‐‐‐‐
˄
i
Valves
There are eight valve outputs on the EN7000. Each valve is assignable to
a program interval as described below. To assign a valve to a program
interval, tap either button in the program interval row. In the figure above,
WAV is assigned valve 1, Motor is assigned valve 2, and the AUX output
during the Squeeze interval is assigned valve 3. The table below shows
constraints of how the valves may be assigned.

Section 3 – Menus
18|Page
Features Electrodes WAV Motor
Standard n/a AV1 n/a AV1 is
automatically
assi
g
ned
Extended
(spot)
Single AV1 n/a AV1 is
automatically
assi
g
ned
Multi AV1 – AV8 n/a Any AV output
ma
y
be assi
g
ned
Extended
(seam)
Single AV1 AV2 AV1 and AV2 are
automatically
assi
g
ned
Multi AV1 – AV8 AV1 – AV8 Any AV output
ma
y
be assi
g
ned
3.2.7.1. WAV
The WAV (Weld Air Valve) turns on at the start of the sequence
and turns off at the end of Hold. Valves not being used for the
WAV function may be used as AUX valves. WAV settings will
always override any AUX setting assigned to the same valve.
3.2.7.2. MOTOR
This feature is available in Seam mode only. For normal seam
welding, the MOTOR output turns on according to the 2nd Stage
setting in the Configuration menu and turns off at the start of the
Hold interval. If the Roll-spot option is selected, the MOTOR
output operates during the Off interval only. Valves not being used
for the MOTOR function may be used as AUX valves. MOTOR
settings will always override any AUX setting assigned to the same
valve.
3.2.7.3. AUX
An AUX valve may be programmed to turn on during any interval in
the welding sequence. Repeat mode must be enabled in the
Options menu to access the OFF interval. WAV and MOTOR
settings will always override any AUX setting assigned to the same
valve.
Extended

Section 3 – Menus
19|Page
3.2.8. Options menu
Program
Inhibit
Pre‐heat
˄
Repeat
Forceprofile
˅
Link
Pulsations
3
Post‐heat
i
Options:Program 0
3.2.8.1. Program Inhibit (parameter)
Checking this box will prevent a program from executing. If the
program is not linked, attempting to run it will produce an error
message. If the program is linked, it will be skipped and the next
linked program will run.
3.2.8.2. Pre-heat (parameter)
Checking this box will enable the Pre-heat parameters.
3.2.8.3. Post-heat (parameter)
Check this box to enable Post-heat features.
3.2.8.4. Pulsations (parameter)
This value is the number of times the Main Heat – Cool 2 interval is
repeated.
3.2.8.5. Link (parameter)
Check this box to enable linking. The linked program selected in
the Program menu will begin automatically if the START signal is
maintained. Linking cannot be used if Repeat is selected.
3.2.8.6. Repeat (parameter)
Checking this box will set repeat mode in the program. It is
available in Spot weld mode only, as set in the Configuration
menu. Repeat cannot be used if Linking is selected.
Extended
Extended

Section 3 – Menus
20|Page
3.2.8.7. Force profile (parameter)
Checking this box will enable the setting of different force values
during each interval of the schedule. This is described in the Force
menu section.
3.2.8.8. Roll-spot (parameter)
Checking this box will set roll-spot mode in the program. It is
available in Seam weld mode only, as set in the Configuration
menu.
3.2.9. Copy program
Copy parameters from the program being edited to another
program or to a range of programs.
3.2.10. START button
Initiate the program being edited. A warning message will be
displayed asking for Confirm or Abort prior to initiation. This button
is not displayed if Seam is selected as the Weld Type in the
Configuration settings.
Extended
Extended
Other manuals for EN7000-TS
2
Table of contents
Other Entron Touchscreen manuals
Popular Touchscreen manuals by other brands
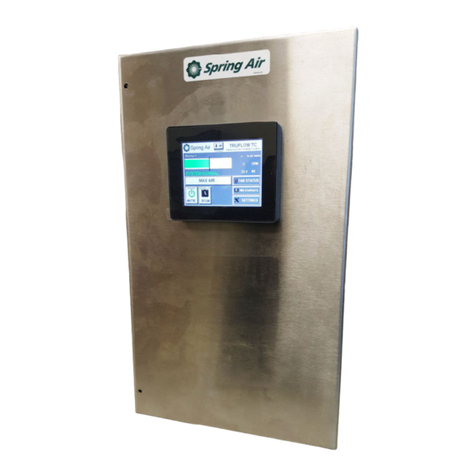
Spring Air Systems
Spring Air Systems Truflow-TC Installation and operation manual
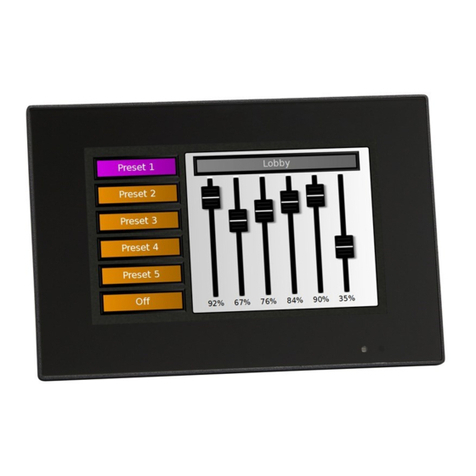
ETC
ETC Unison Paradigm P-TS7 user manual
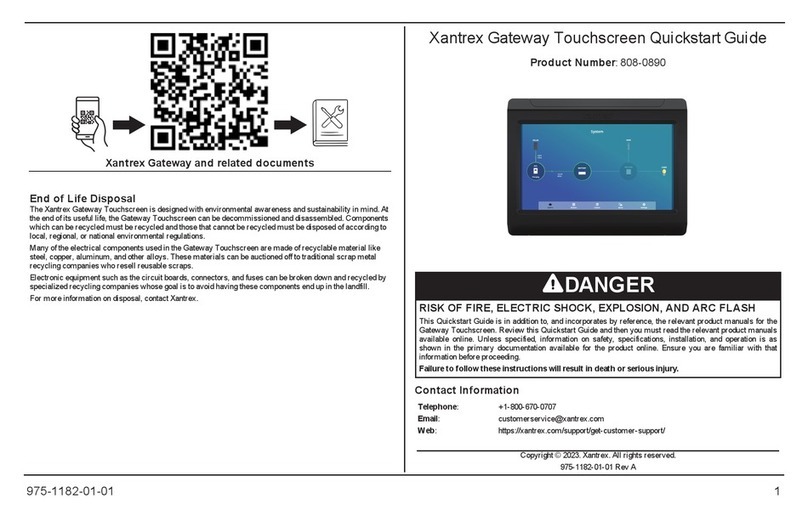
Xantrex
Xantrex 808-0890 quick start guide
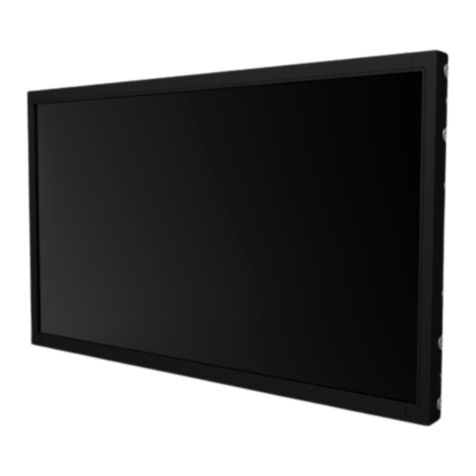
Elo Touch Solutions
Elo Touch Solutions 2740L user manual
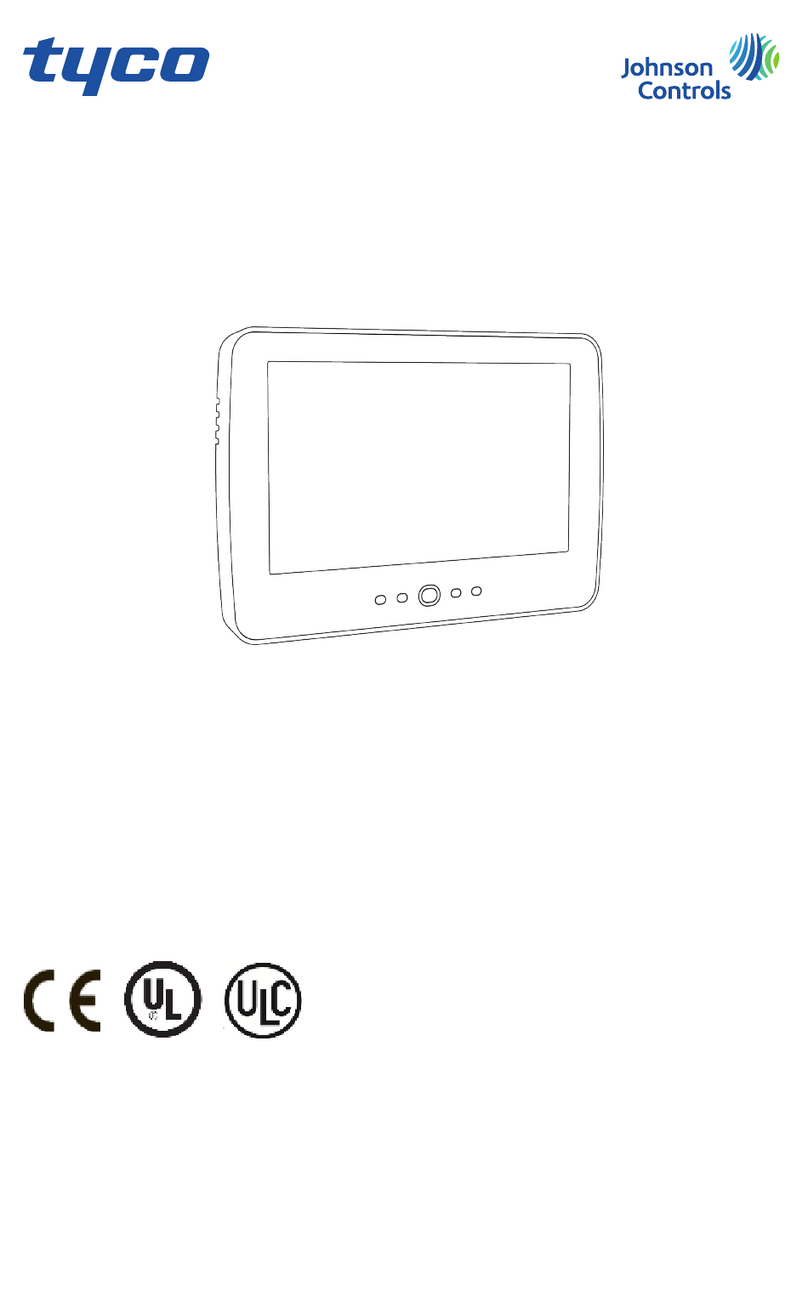
DSC
DSC HS2TCHP E user manual
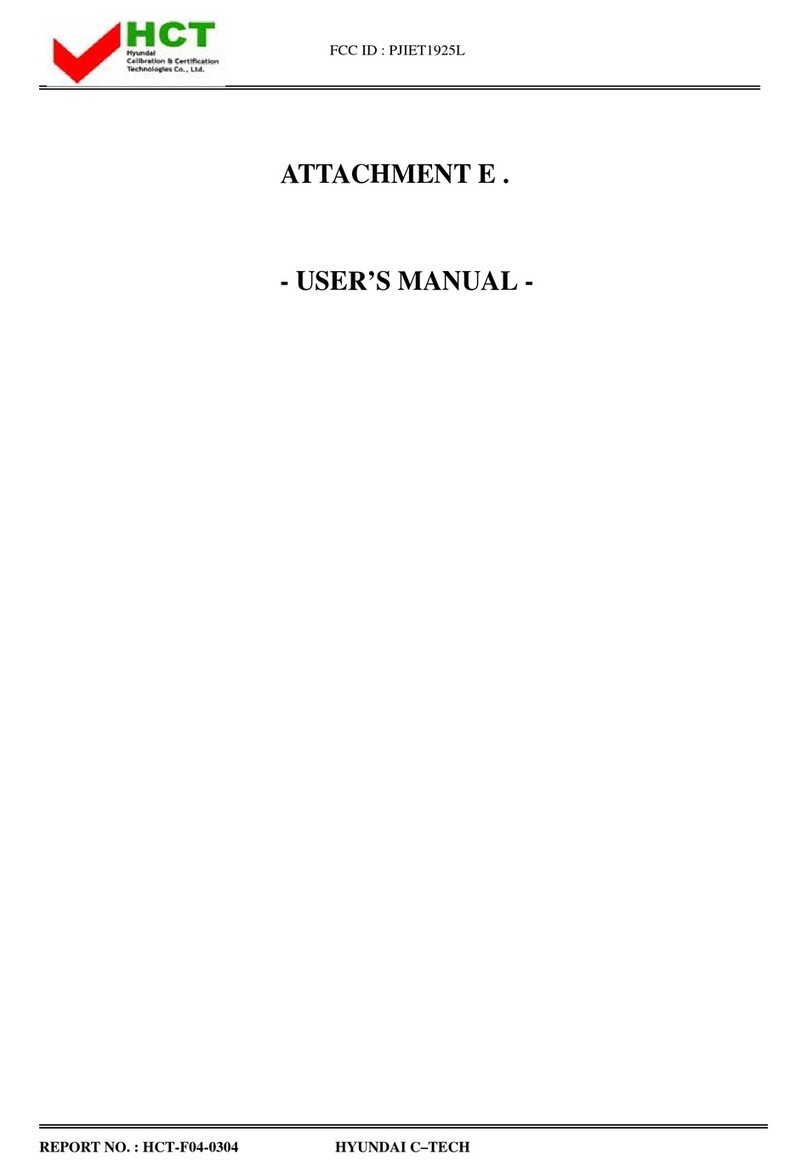
Tyco Electronics
Tyco Electronics Elo Entuitive Touchmonitor ET1925L Series user guide