Estun ERSA-4C User manual

ESTUN ERSA-4C Cabinet
(E-0301EN/01)
MAINTENANCE MANUAL

ESTUN ERSA-4C Cabinet
MAINTENANCE MANUAL
E-0301EN/01

Thank you for purchasing ESTUN Robot.
Before using the robot, be sure to read the SAFETY PRECAUTION and understand the content.
ESTUN endeavor to improve the products. All specifications and designs are subject to change without notice.
In this manual, all specifications and information are checked on a regular basis. Nevertheless, discrepancies
cannot be precluded, for which reason we are not able to guarantee total conformity. ESTUN assumes no
responsibility for any direct or indirect losses arising from use of this manual and products described herein.
The information contained in this manual is the property of ESTUN Robotics Co., Ltd.
No part of this manual may be reproduced in any form.
ESTUN Robotics@2017, All Rights Reserved Copyright
Service Line: 400-025-3336
ADD: No.178, Yanhu Road, Jiangning Area, Nanjing, China Post Code: 211102
TEL: 025-81031813
FAX: 025-85097089
WEB: www.estun.com
E-mail: [email protected]

SAFETY PRECAUTION
s-1
SAFETY PRECAUTION
This chapter describes the precautions which must be followed to ensure the safe use of the robot. Before using the robot, be
sure to read this chapter thoroughly.
ESTUN robots must be transported, mounted and operated in accordance with the applicable national laws, regulations and
standards. Appropriate safeguards must be correctly situated to protect the users. Before using (mounting, operating, maintaining,
repairing) the robot, be sure to read and understand this manual and its relevant manuals. Be sure to have familiarization with the
knowledge of robot system and the safety precaution. Even if all instructions are followed, this is not a guarantee that the robot will
not cause personal injuries or material damage.
DEFINITION OF USER
The personnel can be classified as follows.
Operator
Turns the robot controller power on/off.
Starts the robot program from operator panel.
Programmer
Operates the robot.
Teaches the robot inside the safety zone.
Maintenance engineer
Operates the robot.
Teaches the robot inside the safety zone.
Maintenance (repair, adjustment, replacement)
Operator is not allowed to work in the safety zone.
Programmer and maintenance engineer is allowed to work in the safety zone.
During the operation, programming, and maintenance of the robot system, the programmer, operator and maintenance
engineer should take additional care of their safety by wearing the following safety items.
Adequate clothes for operation
Safety shoes
A helmet
SPECIAL TRAINING
Tasks in the safety zone including transportation, teaching, calibrating, repairing, etc.. Have the operator attending the
training courses before using the robot system.
For more information of training courses, contact ESTUN sales office.
DEFINITION OF SAFETY NOTATIONS
This manual indicates each precaution on safety with “WARNING”or “CAUTION”according to its severity. Supplementary
information is indicated by “INFO”. Read the contents of each notation before using the robot.

SAFETY PRECAUTION
s-2
Symbol
Definitions
WARNING
!
Danger notation
Death or serious injury will be expected to occur if the user fails to follow the approved procedure.
CAUTION
!
Caution notation
Minor or moderate injury of the user or equipment damage will be expected to occur if the user fails to
follow the approved procedure.
INFO
Information
A supplementary explanation help users operating the robot more efficiently.
SAFETY OF THE USER
(1) The robot should be transported and installed by accurately following the procedures recommended by ESTUN. Wrong
transportation or installation may cause the robot to fall, resulting in severe injury or damage.
(2) Draw an outline on the floor, clearly indicating the range of safety zone before install the robot. If necessary, install a safety
fence or warning board to ensure the safety operation of the robot and keep unauthorized person outside the safety zone.
(3) Never hang any items above the robot. Failure to observe this caution may result in injury or equipment damage.
(4) Never lean on the controllers, and avoid inadvertently pushing buttons. Failure to observe this caution may result in injury or
damage by unexpected movement of the manipulator.
(5) Take precaution for falling parts when disassemble the robot.
(6) When adjusting each peripheral equipment independently, be sure to turn off the power of the robot.
(7) The peripheral equipment must be grounded.
(8) In the first operation of the robot after installation, the operation should be restricted to low speed. Then, the speed should be
gradually increased to check the operation of the robot.
(9) Operators should be ungloved while manipulating the operator panel or teach pendant. Operation with gloved fingers could
cause an operation error.
(10) Programs, system variables, and other information can be saved on memory card or USB memories. Be sure to save the data
periodically in case the data is lost in an accident.
(11) Never forcibly move the robot axes. Failure to observe this caution may result in injury or equipment damage.
(12) Take precaution when wiring and piping between the controller, the robot and the peripheral equipment. Run the piping,
wiring, or cables through a pit or use a protective cover, so that they are not stepped on by personnel or run over by folklift.
(13) Any robot in working condition may cause severe personnel injury or equipment damage due to unexpected moving. Test
must be performed on each safety measure (safe door, brake, safe indicators, etc.). Before turn on the system, make sure that
no one is in the working space.
(14) Never set motion range or load condition that exceeds the range indicated in specification table. Incorrect setting may result
in personnel injury and equipment damage.
(15) Observe the following precautions when performing teaching operations within the working space of the robot:
Do not enable the system unless the mode is switched to manual, and make sure that all auto-control is cut off.
Speed must be limited under 250mm/s at manual mode. Only authorized person with fully understand of the risks can
adjust the robot to rated speed manually.
Be careful about rotating joints to prevent hair and clothes involved. Take precautions of injury or damage caused by the
manipulator or other auxiliary devices.
Check the motor brake to avoid personnel injuries caused by unexpected situation.
Always have an escape plan in mind in case the robot comes towards you unexpectedly.
Ensure that there is a place to retreat to in case of emergency.

SAFETY PRECAUTION
s-3
WARNING
!
Never stand beneath the manipulator in case that the robot move unexpectedly or the system be turned
on inadvertently.
CAUTION
!
Make sure that a CO2 fire extinguisher is always available in case of fire.
SAFETY OFTHE OPERATOR
(1) Before operating the robot, check that the SERVO ON indicator goes out when the EMERGENCY STOP button on the right
of the front door of the controller and the pendant are pressed. And confirm that the power is turned off.
(2) Never allow unauthorized personnel to touch the controller during operation. Failure to observe this precaution may result in
unexpected movement of the robot, severe injuries and material damage.
(3) When attaching a equipment such as a welding torch to the robot, be sure to turn off the power of the controller and the
peripheral equipment, and display a warning sign. Turning the power on during equipment installation may cause electric
shock or injury due to unexpected movement of the robot.
(4) Emergency stop
Emergency stop is an external button of the controller that can stop the robot operation.
When emergency button is pressed, the power of the robot (except the power of the servo) is cut off. The system will not run
unless the pressed emergency button being released and the system being turned on.
There may be several emergency stop buttons in a robot system to stop the robot in case of emergencies.
The red button, as shown in the left figure, shall be mounted on the teach pendant. Certainly, emergency
buttons can be mounted by your requirement.
Emergency stop button shall be located on the place where is easy to reach, so that the buttons can be
pressed down immediately in case of emergencies.
CAUTION
!
Emergency button is used in case of emergency only. It cannot be used to stop the manipulator for
normal operation.
WARNING
!
Operators must take precautions to avoid high voltage from cables of servo motors, grippers and other
devices.
SAFETY OFTHE PROGRAMMER
While teaching the robot, the programmer must enter the robot operation area. The programmer must ensure the safety
especially.
CAUTION
!
Turn on or off the system by press or release Mot button on the teach pendant.
To use the teach pendant safely, the following precautions should be taken.

SAFETY PRECAUTION
s-4
Be sure that the enable switch is effective at any time.
Enable switch must be turned off when pausing, programming or testing the system.
Teach pendant must be taken with the programmer when performing teaching jobs in the work space, to avoid
inadvertent operation by unauthorized person.
Teach pendant must not be left within the work space of the robot, as injury or damage can occur if the robot comes in
contact with the teach pendant.
SAFETY OFTHE MAINTENANCE ENGINEER
(1) Heated parts
Some parts of the robot are heated when the robot is operating, especially the servo motor and reducer. If a maintenance user
needs to touch such a part in the heated state, the user should wear heat-resistant gloves or use other protective tools.
CAUTION
!
Try to feel the temperature of heated parts before touching them, to avoid burn injuries.
After turning off the power supply, wait until the heated parts cool down before performing any
maintenance.
(2) Disassembly parts
Open the cover or shell only after interior parts such as gears are not moving any more. Never open the cover or shell when
the gear or bearing is moving. Use auxiliary device to keep interior part to its position.
Observe the following precaution when performing the first test after installation, inspection or maintenance:
a) Clear tools to proper locations outside of the working space of the robot.
b) Make sure that all precaution measures are available.
c) Make sure that there is no one in the working space of the robot.
d) Pay special attention to working condition of the maintenance parts when performing test.
Never use the manipulator as a ladder when performing maintenance. Never climb on the manipulator. Failure to observe this
caution may result in injury.
(3) Pneumatic / hydraulic pressure
There may be air/liquid residue in the system when the air pump or hydraulic pump is turned off. Before checking the
pneumatic or hydraulic parts, release remaining pressure from the system to avoid personnel injury or equipment damage.
CAUTION
!
Install a safety valve in case of accident.
(4) Although the power supply need to be turned on during fault diagnosis, it must be turned off when perform maintenance.
(5) Brake inspection
Brake may be wearing in daily operation. So brake inspection should be performed by the following procedure:
a) Move each joint to the position where the joint bears maximum load.
b) Turn off the robot. The brake works.
c) Mark each joint.
d) Check if the joint moves unduly after a period of time.
(6) Greasing
Personnel injury or equipment damage may occur during greasing. Observe the following precautions before greasing.
Take additional care of safety by wearing safety items (such as gloves) to avoid injury from heated oil or reducer..
Open the oil chamber with special caution and keep away from the opening. Oil may spray due to oil pressure.
Feed the oil according to required quantity and never fill up the oil chamber. Check the oil indicator when finished.
Never mix different types of oil into one reducer. Clean remained oil thoroughly before changing another type.

SAFETY PRECAUTION
s-5
Oil draining must be performed thoroughly. Check the oil indicator when finished.
INFO
Operate the robot for a short period of time before oil draining to heat the oil.
SAFETY OF THE TOOLS AND PERIPHERAL EQUIPMENT
Peripheral device may still be running even after the system has been turned off. Personnel injury may occur due to damaged
power lines.
SAFETY OF THE ROBOT MECHANICAL UNIT
For abnormal or emergency situations, e.g. persons trapped in or pinched by the robot, the robot axes should be moved.
(Contact ESTUN for more details about dismantling).
Small arms can be moved by hand. Lager arms should be moved by crane or other handling equipment.
Fasten the arms of the manipulator firmly before releasing the brake to avoid secondary injury caused by falling arms.
STOP TYPE OF ROBOT
The following three robot stop types exist:
Power-off stop
Servo power is turned off and the robots stops immediately. Servo power is turned off when the robot is moving, the path of
the deceleration in uncontrolled.
The following processing is performed at Power-off stop:
An alarm is generated and servo power is turned off immediately.
Execution of the program is paused.
Frequent Power-off stop of the robot during operation can cause failures of the robot. Avoid system designs that require
routine or frequent Power-off stop conditions.
Alarm stop
The robot system sends alarm (not include power-off alarm), and the robot is decelerated until it stops by control instructions.
The following processing is performed at Alarm stop:
An alarm (not include power-off alarm) is generated due to overload, system faulty, etc.
Control instruction is send from servo system. The robot operation is decelerated until it stops. Execution of the program
is paused.
Servo power is off.
Hold
The robot is decelerated until it stops, and servo power remains on.
The following processing is performed at Hold:
The robot operation is decelerated until it stops. Execution of the program is paused.

SAFETY PRECAUTION
s-6
LABELS
(1)Electric Shock Warning
Fig 0.1 Electric Shock Warning
This label indicates hazardous voltage or electric shock.
(2)High-temperature Warning
Fig 0.2 High-temperature Warning
Be cautious about a section where this label is affixed, as the section generates heat. If you have to inevitably touch such a
section when it is hot, use a protection provision such as heat-resistant gloves.

SAFETY PRECAUTION
s-7
(3)No Step-on Warning
Fig 0.3 Step-on prohibitive Warning
Never step on or climb the robot or controller as it may adversely affect the robot or controller and may get hurt if you lose
your footing as well.
(4)Personal Injury Warning
Fig 0.4 Personal Injury Warning
Never enter the operation area while the Manipulator is moving. This is extremely hazardous and may result in serious safety
problems.

SAFETY PRECAUTION
s-8
(5)Energy Storage Warning
Fig 0.5 Energy Storage Warning
Balance cylinder contains spring, high-pressure gas or liquid. Never dismantle a balance cylinder without permission from
ESTUN.
(6)No Disassembly Warning
Fig 0.6 No Disassembly Warning
Never perform disassembly arbitrarily where the warning is affixed. Contact ESTUN for disassembly.

PREFACE
p-1
PREFACE
This manual describes the following manipulators:
Manipulator Type
Load Capacity
ERS6-500
6kg
ERS6-600
6kg
ERS6-700
6kg
Related manuals
ESTUN Robot ERS Series Mechanical Unit Operator’s Manual
ESTUN Robot ERSA-4C Cabinet Maintenance Manual
ESTUN Robot ERC20 System Operator’s Manual

CONTENT
c-1
CONTENT
SAFETY PRECAUTION.....................................................................................................................................s-1
PREFACE............................................................................................................................................................ p-1
CONTENT...........................................................................................................................................................c-1
1. EQUIPMENT CONFIGURATION................................................................................................................ 1
1.1. Configuration.................................................................................................................................. 1
1.2. Arrangement of Units..................................................................................................................... 4
2. CHECKAND MAINTENANCE................................................................................................................... 6
2.1. Maintenance of the Cabinet............................................................................................................ 6
2.2. Periodic Checks.............................................................................................................................. 8
3. POWER UNIT ............................................................................................................................................... 9
4. CONTROL UNIT......................................................................................................................................... 11
4.1. Introduction.................................................................................................................................. 11
4.2. Interface........................................................................................................................................ 11
4.3. Notes............................................................................................................................................. 12
5. SERVO-DRIVE UNIT................................................................................................................................. 13
6. INPUT / OUTPUT UNIT............................................................................................................................. 15
6.1. Coupler: EE-R00.......................................................................................................................... 15
6.1.1. Functions.............................................................................................................................. 15
6.1.2. Signal Definition .................................................................................................................. 15
6.1.3. Technical Parameters............................................................................................................ 16
6.2. Digital Input: ER-1311................................................................................................................. 17
6.2.1. Functions.............................................................................................................................. 17
6.2.2. Signal Definition .................................................................................................................. 17
6.2.3. Technical Parameters............................................................................................................ 19
6.3. Digital Output: ER-2341 .............................................................................................................. 19
6.3.1. Functions.............................................................................................................................. 19
6.3.2. Signal Definition .................................................................................................................. 20
6.3.3. Technical Parameters............................................................................................................ 21
6.4. Mounting and Networking of I/O Sub-station.............................................................................. 22
6.4.1. Mounting Method................................................................................................................. 22
6.4.2. Mounting.............................................................................................................................. 22
6.4.3. Notes for Mounting .............................................................................................................. 23
6.4.4. Dismounting......................................................................................................................... 24
6.4.5. ID Set.................................................................................................................................... 25
6.4.6. Wiring................................................................................................................................... 25
6.4.7. Notes..................................................................................................................................... 26
6.4.8. Module Dimensions.............................................................................................................. 27
7. RELAY MODULE UNIT............................................................................................................................. 28
8. REPLACING ............................................................................................................................................... 29
8.1. Replacing Fuses............................................................................................................................ 29
9. BLOCK DIAGRAM .................................................................................................................................... 30

CONTENT
c-2
10. COMMUNICATION CONNECTION................................................................................................. 31
11. PERIPFIRAL DEVICE INTERFACE.................................................................................................. 32
12. HANDLING AND INSTALLATION .................................................................................................. 36
12.1. Handling Procedure...................................................................................................................... 36
12.1.1. Using a Crane to Move the Cabinet...................................................................................... 36
12.1.2. Using a Forklift to Move the Cabinet................................................................................... 36
12.2. Place of Installation...................................................................................................................... 36
12.3. Location........................................................................................................................................ 36
12.4. Connection.................................................................................................................................... 37
12.4.1. Notes on Cable Junctions ..................................................................................................... 37
12.4.2. Connection Methods............................................................................................................. 38
12.5. Adjustment and Confirmation...................................................................................................... 38
APPENDIX ALARM DISPLAY ...................................................................................................................... 39
Revision Record................................................................................................................................................... 41

EQUIPMENT CONFIGURATION
1
1. EQUIPMENT CONFIGURATION
1.1. Configuration
Configurations are subject to change according to different types of manipulators, options and applications.
Fig 1.1 Exterior View(1)

EQUIPMENT CONFIGURATION
2
Tab 1.1 Specifications
Model
ERSA-4C
Size
400*210*510 (mm)
Location
Ventilated, unsealed
Min. Range: 900×700×1000 (mm, length*width*height)
Weight
20kg
Protection Level
IP20
Ambient Temperature
0℃~45℃(Need cooling equipment when ambient temperature exceed 45℃)
Input Power Supply
Single-phase three wire AC220V 50Hz
Max. Power
1kW
Communication interface with
peripheral device
TCP/IP, Serial Port
Cables connect to robot
3 m
Noise
50-63dB

EQUIPMENT CONFIGURATION
3
Fig 1.2 Configuration of Teach Pendant
1. LCD display, 2. Emergency button, 3. Mode switch, 4. Keyboard, 5. Indicators, 6. Enable switch 7. Hanger bracket, 8. Cable
connection joint, 9. USB interface, 10. Pen
Tab 1.2 ESTUN Teach Pendant Parameters
Teach pendant type
ESTUN Teach pendant ERT72
Size (length*width*height)
265*210*110mm
CPU
800MHZ
Memory
128M
Operation system
Linux
Color touch screen
7 inches
Protection level
IP65
Length of cable
8m (extensible to 20m)
Communication interface
Ethernet
Data storage
NandFlash
Power consumption
<8W
CAUTION
!
Teach pendant is not included in the product. If you need one, contact us.

EQUIPMENT CONFIGURATION
4
1.2. Arrangement of Units
Fig 1.3 Upper Layer Arrangement
温皓 布置图
机器人控制柜 ERS6-E2C-P-A 温皓 布置图
机器人控制柜 ERS6-E2C-P-A
温皓 布置图
机器人控制柜 ERS6-E2C-P-A 温皓 布置图
机器人控制柜 ERS6-E2C-P-A
WARNING
!
Regenerative resistor reaches extremely high temperature (max. 100-200℃) during system
operation. Never touch the regenerative resistor.

EQUIPMENT CONFIGURATION
5
Fig 1.4 Sub layer Arrangement
(1) Power supply filter: Filter for power supply to guarantee its quality.
(2) Main circuit servo driver on-off unit: Turn on or off the main circuit of servo driver. Turn off automatically when high
current occurs to protect the servo driver circuit.
(3) Servo driver unit: control the 4 servo motors of the manipulator by 2 servo drivers in this unit. One of them is
triple-servo driver, the other is single-servo driver.
(4) Main controller: Programmable unit, achieve functions such as motion control of manipulator and peripheral device,
security safeguard, fault alarm, emergency stop, etc..
(5) Fan unit: One fan is used to cool interior units. The filter fixed at the air inlet, which is used to keep the interior cabinet
clean, needs to be replaced in daily maintenance.
(6) Connection port: Reserved for safe door and external emergency stop.
(7) Relay module: Integrated with 18 intermediate relay to realize circuit interlock, 18 LED indicators to indicate current
condition, which is important to protect the internal circuit.
(8) Connector unit: The interface between the cabinet and external equipment.
(9) Filter, transformer, switching power supply unit: This unit transform the power to AC power with required voltage,
then transform it to DC power. Also the filter and protection is provided.
(10) Regeneration resistor: A regeneration resistor on the servo driver is needed to release inverse electric field strength.
温皓 布置图
机器人控制柜 ERS6-E2C-P-A 温皓 布置图
机器人控制柜 ERS6-E2C-P-A
温皓 布置图
机器人控制柜 ERS6-E2C-P-A 温皓 布置图
机器人控制柜 ERS6-E2C-P-A

CHECK AND MAINTENANCE
6
2. CHECK AND MAINTENANCE
Please check the following items in daily operation:
Check that the cable of teach pendant is not extraordinarily bendy. Check that the controller and peripheral devices are in
normal condition.
Check that the air outlet of the cabinet is not dirty. If it is dirty, immediately clean up dirt.
Check the cooling fans every month. If the cooling fans are dirty, clean up the dirt.
Daily or periodic check and maintenance is essential to keep robot system reliable.
2.1. Maintenance of the Cabinet
(1)Check if the Breaker on the Cabinet is Firmly Closed
The ERSA-4C cabinet has a fully sealed construction, designed to keep external air containing oil mist out of the cabinet. The
breaker must be turned to off before maintenance.
(2)Check for Gaps or Damage in the Sealed Construction Section
Check the seal around the door is undamaged.
Check that the inside of the cabinet is not excessively dirty. If it is dirty, determine the cause, take measures to correct the
problem and immediately clean up dirt.
Fully close each door lock and check that no excessive gaps exist around the edge of the door.
(3)Cooling Fan Inspections
A defective fan can cause the cabinet to malfunction because of excessive high temperature inside.
The interior circulation fan and backside duct fan normally operate while the power is turned on. Check if the fans are
operating correctly by visual inspection and by feeling air moving into the air inlet and from the outlet.
(4)Emergency Stop Button Inspections
The emergency stop button is located on the teach pendant. Confirm the servo power is off by pressing the emergency stop
button after the servo on, before the manipulator is operated.
(5)Enable Switch Inspections
The teach pendant is equipped with a three-position enable switch. Perform the following operation to confirm the enable
switch operates.
a) Set the mode switch on the teach pendant to “TEACH”.
b) Press [Mot] on the teach pendant, the [Motion] lamp blinks.
c) When the enable switch is grasped lightly, the servo power is turned on. When the enable switch is grasped firmly or
released, the servo power is turned off.
CAUTION
!
If the [Motion] lamp does not light in previous operation b), check the following:
The emergency stop button on the teach pendant is pressed.
The emergency stop signal is input from external.
CAUTION
!
If the servo is not turned on in a previous operation c), check the following:
The overrun limited switch is operating
If a major alarm is occurring
(6)Power Supply Voltage Confirmation
Check the voltage of power input terminal of the circuit breaker (QF1) with an electric tester.
Table of contents
Other Estun Control System manuals
Popular Control System manuals by other brands
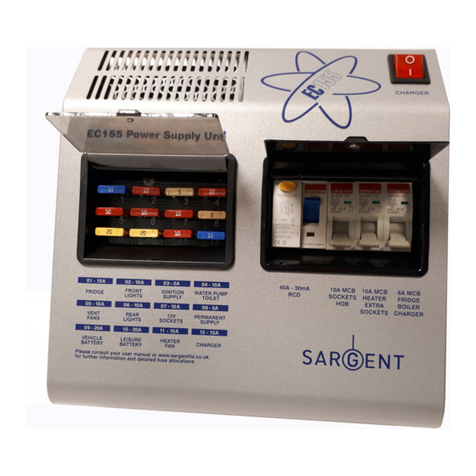
Sargent
Sargent EC155 user manual

Motorline professional
Motorline professional PHOTOCELLS MF101 Operation manual
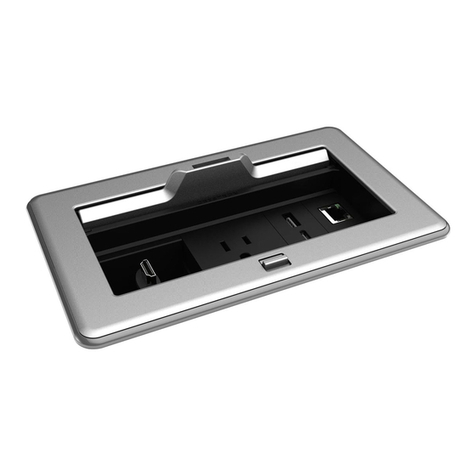
Crestron
Crestron FlipTop FT2-202-ELEC Series manual
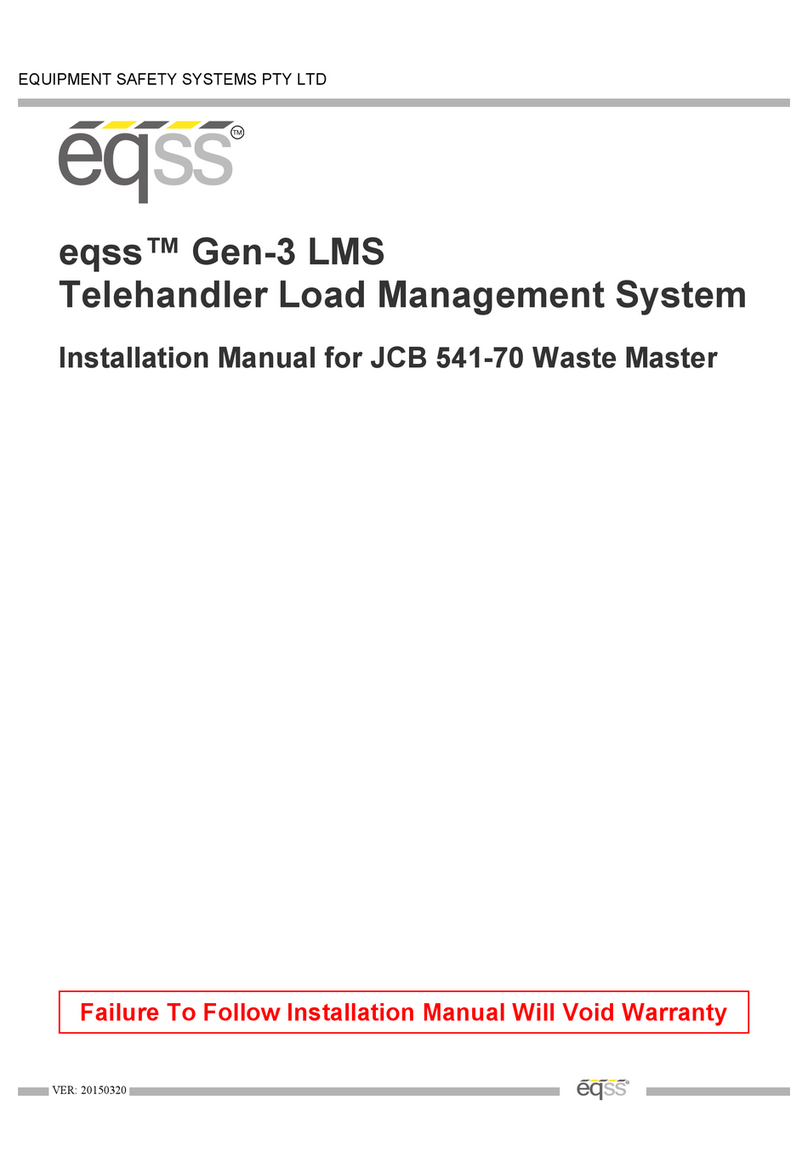
eqss
eqss Gen-3 LMS installation manual
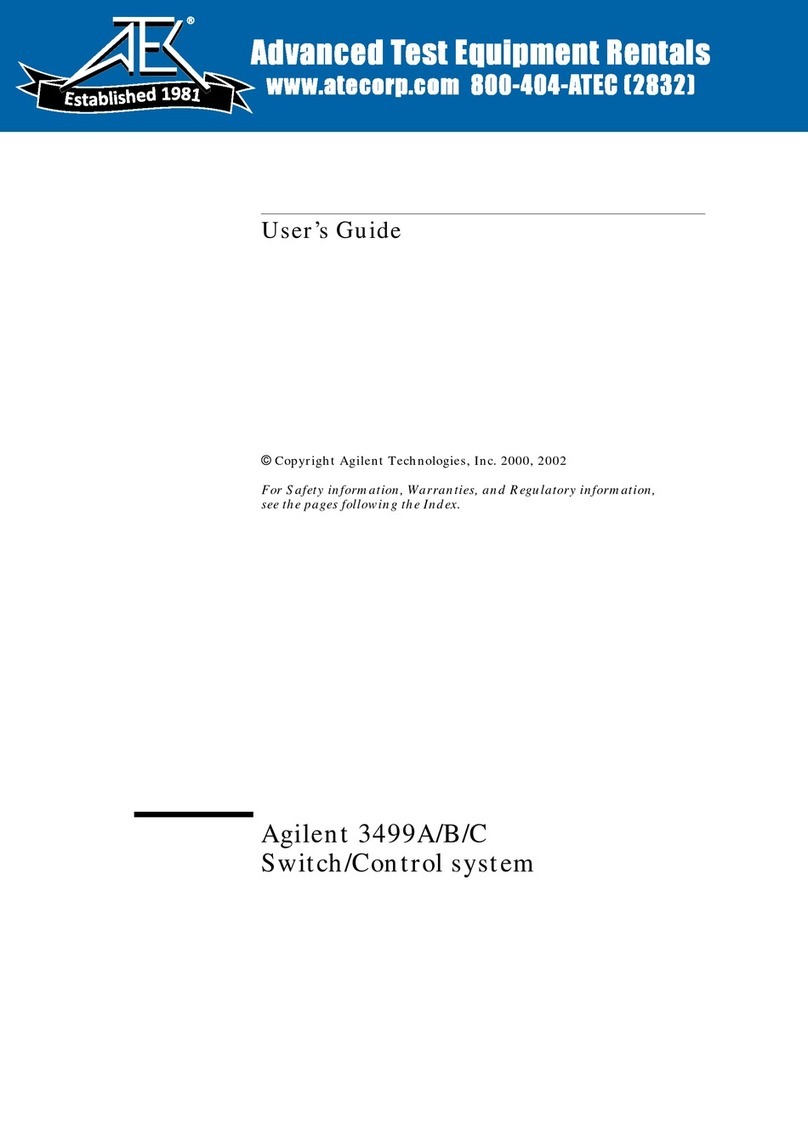
Agilent Technologies
Agilent Technologies Agilent 3499A user guide
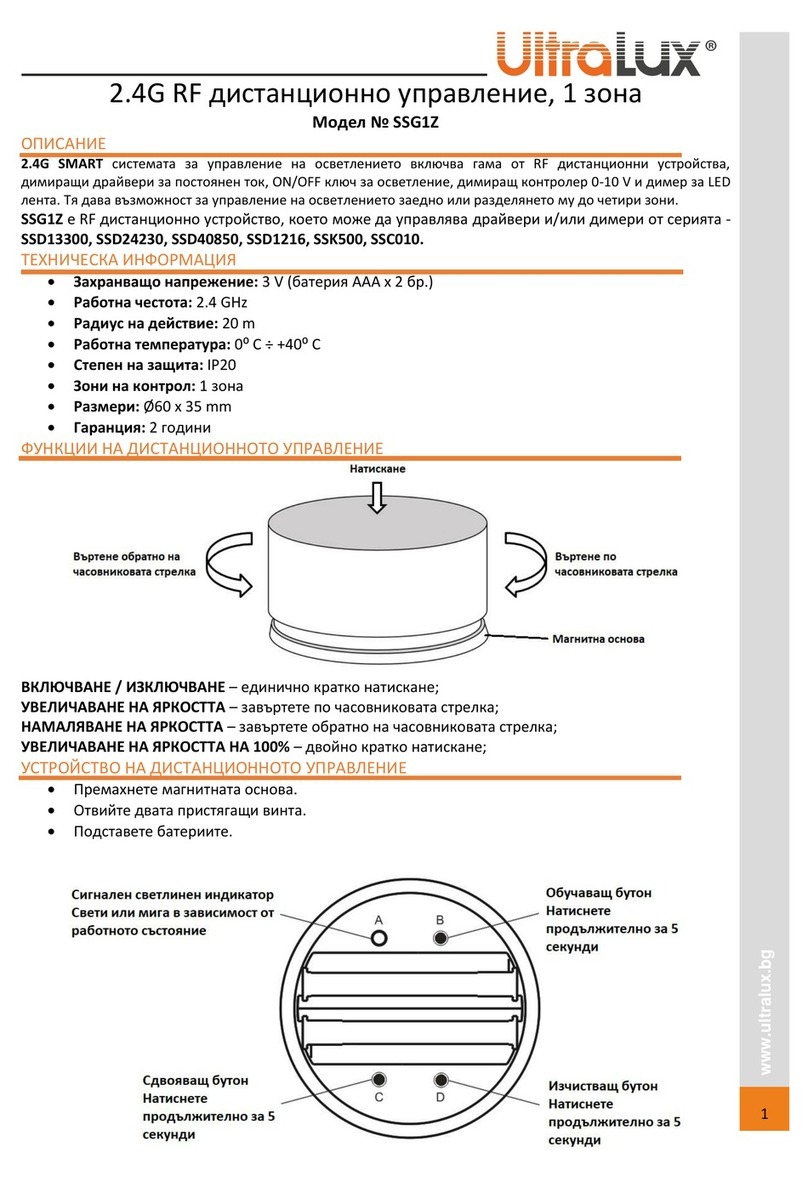
UltraLux
UltraLux SSG1Z instruction manual