Ransburg Pulsetrack 2 User manual

SERVICE MANUAL
LN-9248-05.3
(Replaces LN-9248-05.2)
March - 2013
MODEL: A11515-XXXXX
IMPORTANT: Before using this equipment,
carefully read SAFETY PRECAUTIONS, starting
on page 1, and all instructions in this manual.
Keep this Service Manual for future reference.
Service Manual Price: €25.00 (Euro)
$30.00 (U.S.)
PULSETRACK
SPEED CONTROL AND
MONITOR SYSTEM
Ransburg

NOTE: This manual has been changed from revision LN-9248-05.2 to revision LN-9248-05.3.
Reasons for this change are noted under “Manual Change Summary” on page 53 of
this manual.

SAFETY:
SAFETY PRECAUTIONS...........................................................................................................
HAZARDS / SAFEGUARDS......................................................................................................
PAGE
INTRODUCTION:
CONTENTS
GENERAL DESCRIPTION.........................................................................................................
A11515 PULSETRACK 2 SPEED CONTROL AND
MONITOR SYSTEM MODEL IDENTIFICATION......................................................................
SPECIFICATIONS......................................................................................................................
TYPICAL TURBODISK 2 INSTALLATION WITH
TEMPERATURE HUMIDITY CARDS........................................................................................
ELECTRICAL NOISE..................................................................................................................
INSTALLATION:
LOCATION..................................................................................................................................
INPUT POWER...........................................................................................................................
FIBER OPTIC CABLE.................................................................................................................
PNEUMATIC CONNECTIONS..................................................................................................
ELECTRICAL I/O........................................................................................................................
DIP SWITCH SETTINGS...........................................................................................................
1-5
6-10
11-26
1
2-6
6-7
7
8
9
10
11-12
12-13
13
13-15
16-23
24-26
OPERATION:
THEORY OF OPERATION........................................................................................................
FRONT PANEL CONTROLS.....................................................................................................
ATOMIZER CARD CONTROLS................................................................................................
OPTIONAL TEMPERATURE / HUMIDITY
CARD CONTROLS.....................................................................................................................
TO ENABLE SPEED CONTROL...............................................................................................
TO DISABLE SPEED CONTROL..............................................................................................
FAULT DESCRIPTIONS............................................................................................................
27-32
27
27
28-29
29
30
30-31
31-32
(Continued On Next Page)
MAINTENANCE:
GENERAL...................................................................................................................................
SCHEDULED MAINTENANCE..................................................................................................
REPLACEMENT PROCEDURES.............................................................................................
TROUBLESHOOTING...............................................................................................................
33-44
33
33
33-37
38-44

PARTS IDENTIFICATION: 45-52
CONTROL PANEL - FRONT VIEW / PARTS LIST...................................................................
CONTROL PANEL - INSIDE DOOR VIEW / PARTS LIST.......................................................
CONTROL PANEL - INSIDE CABINET VIEW / PARTS LIST..................................................
RECOMMENDED SPARE PARTS LIST...................................................................................
45-46
47-48
49-50
51
WARRANTY POLICIES: 52
LIMITED WARRANTY.................................................................................................................52
PAGE
CONTENTS (Cont.)

W A R N I N G
!
W A R N I N G
!
SAFETY
SAFETY PRECAUTIONS
Before operating, maintaining or servicing any
Ransburg electrostatic coating system, read and
understand all of the technical and safety liter-
ature for your Ransburg products. This manual
contains information that is important for you to
know and understand. This information relates to
USER SAFETY and PREVENTING EQUIPMENT
PROBLEMS. To help you recognize this informa-
tion, we use the following symbols. Please pay
particular attention to these sections.
A WARNING! states information to alert you
to a situation that might cause serious injury
if instructions are not followed.
A CAUTION! states information that tells how
to prevent damage to equipment or how to
avoid a situation that might cause minor injury.
A NOTE is information relevant to the proce-
dure in progress.
While this manual lists standard specications
and service procedures, some minor deviations
may be found between this literature and your
equipment. Differences in local codes and plant
requirements, material delivery requirements,
etc., make such variations inevitable. Compare
this manual with your system installation draw-
ings and appropriate Ransburg equipment man-
uals to reconcile such differences.
Careful study and continued use of this manual will
provide a better understanding of the equipment
and process, resulting in more efcient operation,
longer trouble-free service and faster, easier
troubleshooting. If you do not have the manuals
and safety literature for your Ransburg system,
contact your local Ransburg representative or
Ransburg.
The hazards shown on the following pag-
es may occur during the normal use of this
equipment. Please read the hazard chart be-
ginning on page 2.
The user MUST read and be familiar with
the Safety Section in this manual and the
Ransburg safety literature therein identied.
This manual MUST be read and thor-
oughly understood by ALL personnel who
operate, clean or maintain this equipment!
Special care should be taken to ensure that
the WARNINGS and safety requirements for
operating and servicing the equipment are
followed. The user should be aware of and
adhere to ALL local building and re codes
and ordinances as well as NFPA-33 SAFE-
TY STANDARD, LATEST EDITION, prior
to installing, operating, and/or servicing this
equipment.

Spray Area
AREA
Tells where hazards
may occur.
HAZARD
Tells what the hazard is.
SAFEGUARDS
Tells how to avoid the hazard.
Fire Hazard
Improper or inadequate
operation and maintenance
procedures will cause a re
hazard.
Protection against inadver-
tent arcing that is capable of
causing re or explosion is
lost if any safety interlocks
are disabled during opera-
tion. Frequent Power Supply
or Controller shutdown indi-
cates a problem in the system
requiring correction.
Fire extinguishing equipment must be present in
the spray area and tested periodically.
Spray areas must be kept clean to prevent the
accumulation of combustible residues.
Smoking must never be allowed in the spray
area.
The high voltage supplied to the atomizer must
be turned off prior to cleaning, ushing or main-
tenance.
When using solvents for cleaning:
•Those used for equipment ushing should
have ash points equal to or higher than
those of the coating material.
•Those used for general cleaning must have
ash points above 100°F (37.8°C).
Spray booth ventilation must be kept at the rates
required by NFPA-33, OSHA, country, and local
codes. In addition, ventilation must be main-
tained during cleaning operations using am-
mable or combustible solvents.
Electrostatic arcing must be prevented. Safe
sparking distance must be maintained between
the parts being coated and the applicator. A dis-
tance of 1 inch for every 10KV of output voltage
is required at all times.
Test only in areas free of combustible material.
Testing may require high voltage to be on, but
only as instructed.
Non-factory replacement parts or unautho-
rized equipment modications may cause re or
injury.
If used, the key switch bypass is intended for
use only during setup operations. Production
should never be done with safety interlocks dis-
abled.
Never use equipment intended for use in water-
borne installations to spray solvent based ma-
terials.
The paint process and equipment should be
set up and operated in accordance with NFPA-
33, NEC, OSHA, local, country, and European
Health and Safety Norms.

AREA
Tells where hazards
may occur.
HAZARD
Tells what the hazard is.
SAFEGUARDS
Tells how to avoid the hazard.
Spray Area
Improper operation or mainte-
nance may create a hazard.
Personnel must be properly
trained in the use of this equip-
ment.
Explosion Hazard
Improper or inadequate oper-
ation and maintenance proce-
dures will cause a re hazard.
Protection against inadvertent
arcing that is capable of caus-
ing re or explosion is lost if
any safety interlocks are dis-
abled during operation.
Frequent Power Supply or
Controller shutdown indicates
a problem in the system requir-
ing correction.
General Use and
Maintenance
Electrostatic arcing must be prevented. Safe
sparking distance must be maintained between
the parts being coated and the applicator. A dis-
tance of 1 inch for every 10KV of output voltage
is required at all times.
Unless specically approved for use in hazard-
ous locations, all electrical equipment must be
located outside Class I or II, Division 1 or 2
hazardous areas, in accordance with NFPA-33.
Test only in areas free of ammable or combus-
tible materials.
The current overload sensitivity (if equipped)
MUST be set as described in the correspond-
ing section of the equipment manual. Protec-
tion against inadvertent arcing that is capable
of causing re or explosion is lost if the current
overload sensitivity is not properly set. Fre-
quent power supply shutdown indicates a prob-
lem in the system which requires correction.
Always turn the control panel power off prior to
ushing, cleaning, or working on spray system
equipment.
Before turning high voltage on, make sure no
objects are within the safe sparking distance.
Ensure that the control panel is interlocked with
the ventilation system and conveyor in accor-
dance with NFPA-33, EN 50176.
Have re extinguishing equipment readily avail-
able and tested periodically.
Personnel must be given training in accordance
with the requirements of NFPA-33, EN 60079-0.
Instructions and safety precautions must be
read and understood prior to using this equip-
ment.
Comply with appropriate local, state, and na-
tional codes governing ventilation, re protec-
tion, operation maintenance, and housekeep-
ing. Reference OSHA, NFPA-33, EN Norms
and your insurance company requirements.

AREA
Tells where hazards
may occur.
HAZARD
Tells what the hazard is.
SAFEGUARDS
Tells how to avoid the hazard.
Spray Area /
High Voltage
Equipment
Electrical Discharge
There is a high voltage device
that can induce an electrical
charge on ungrounded objects
which is capable of igniting
coating materials.
Inadequate grounding will
cause a spark hazard. A
spark can ignite many coating
materials and cause a re or
explosion.
Parts being sprayed and operators in the spray
area must be properly grounded.
Parts being sprayed must be supported on con-
veyors or hangers that are properly ground-
ed. The resistance between the part and earth
ground must not exceed 1 meg ohm. (Refer to
NFPA-33.)
Operators must be grounded. Rubber soled in-
sulating shoes should not be worn. Grounding
straps on wrists or legs may be used to assure
adequate ground contact.
Operators must not be wearing or carrying any
ungrounded metal objects.
When using an electrostatic handgun, operators
must assure contact with the handle of the ap-
plicator via conductive gloves or gloves with the
palm section cut out.
NOTE: REFER TO NFPA-33 OR SPECIFIC
COUNTRY SAFETY CODES REGARDING
PROPER OPERATOR GROUNDING.
All electrically conductive objects in the spray
area, with the exception of those objects re-
quired by the process to be at high voltage, must
be grounded. Grounded conductive ooring
must be provided in the spray area.
Always turn off the power supply prior to ush-
ing, cleaning, or working on spray system equip-
ment.
Unless specically approved for use in hazard-
ous locations, all electrical equipment must be
located outside Class I or II, Division 1 or 2 haz-
ardous areas, in accordance with NFPA-33.

Toxic Substances Certain material may be harmful
if inhaled, or if there is contact
with the skin.
Follow the requirements of the Material Safety
Data Sheet supplied by coating material manu-
facturer.
Adequate exhaust must be provided to keep the
air free of accumulations of toxic materials.
Use a mask or respirator whenever there is a
chance of inhaling sprayed materials. The mask
must be compatible with the material being
sprayed and its concentration. Equipment must
be as prescribed by an industrial hygienist or
safety expert, and be NIOSH approved.
AREA
Tells where hazards
may occur.
HAZARD
Tells what the hazard is.
SAFEGUARDS
Tells how to avoid the hazard.
Electrical
Equipment
Electrical Discharge
High voltage equipment is uti-
lized in the process. Arcing
in the vicinity of ammable or
combustible materials may oc-
cur. Personnel are exposed to
high voltage during operation
and maintenance.
Protection against inadvertent
arcing that may cause a re or
explosion is lost if safety circuits
are disabled during operation.
Frequent power supply shut-
down indicates a problem in the
system which requires correc-
tion.
An electrical arc can ignite coat-
ing materials and cause a re or
explosion.
Unless specically approved for use in hazard-
ous locations, the power supply, control cabinet,
and all other electrical equipment must be locat-
ed outside Class I or II, Division 1 and 2 hazard-
ous areas in accordance with NFPA-33 and EN
50176.
Turn the power supply OFF before working on
the equipment.
Test only in areas free of ammable or combus-
tible material.
Testing may require high voltage to be on, but
only as instructed.
Production should never be done with the safety
circuits disabled.
Before turning the high voltage on, make sure no
objects are within the sparking distance.
Explosion Hazard –
Incompatible Materials
Halogenated hydrocarbon sol-
vents for example: methylene
chloride and 1,1,1,-Trichlo-
roethane are not chemically
compatible with the aluminum
that might be used in many sys-
tem components. The chemical
reaction caused by these sol-
vents reacting with aluminum
can become violent and lead to
an equipment explosion.
Aluminum is widely used in other spray appli-
cation equipment - such as material pumps,
regulators, triggering valves, etc. Halogenated
hydrocarbon solvents must never be used with
aluminum equipment during spraying, ushing,
or cleaning. Read the label or data sheet for the
material you intend to spray. If in doubt as to
whether or not a coating or cleaning material is
compatible, contact your coating supplier. Any
other type of solvent may be used with aluminum
equipment.
Spray Area

INTRODUCTION
GENERAL DESCRIPTION
The PulseTrack 2TM system is designed to contin-
uously monitor and maintain the program-mable
speed of up to six rotary atomizers and monitor tem-
perature and humidity for one or more zones. The
PulseTrack 2 system is a micro-processor-based
design that optimizes control of rotator speed
by utilizing proven proprietary software based
on many years of experience. This system can
monitor and control the speed of rotators offered
by Ransburg such as the TurboDiskTM,AerobellTM
and Aerobell 33TM family of applicators. The Pul-
seTrack 2 system is designed to be versatile and
adapt easily to system requirements.
Each PulseTrack 2 system includes a Control
Card and up to six Atomizer Cards for control of
rotator speed. There is one Atomizer Card for
each rotator. Each Atomizer Card includes a dig-
ital display for speed and diagnostic readout and
the necessary manual control switches required
to operate each rotator. Optional Temperature/
Humidity Cards display temperature and relative
humidity for signals received from remote mounted
probes. Additionally, discreet as well as analog
inputs and outputs are available for use in oper-
ating the system.
The basic components of the PulseTrack 2 system
are described below.
Control Card
The Control Card is a microprocessor-based
printed circuit board that performs the following
functions:
1. Communicates to each Atomizer Card through
a high-speed serial I/O data bus.
2. Receives external digital and analog control
signals from a system PLC or host controller and
processes the commands.
3. Receives the rotational feedback signals from
the integrated ber optic receiver(s).
4. Receives analog signal feedback representing
temperature and relative humidity from a probe
located in a desired zone. The feedback signals
are scaled as needed and sent to each Tempera-
ture/Humidity Card to be displayed.
5. Performs the closed-loop rotational speed
computations for each atomizer. An output control
signal is generated and sent to the current-to-pres-
sure (I/P) transducers as needed to maintain the
desired speed.
6. Determines if there is a possible unsafe or
abnormal condition and automatically shuts down
the rotator and alerts the operator.
7. Supplies the signals to control each brake
solenoid for bell applications utilizing the brake
function.
8. The red LED1 ashing at upper left corner of
control card indicates the microprocessor is active.
Atomizer Card
The Atomizer Card (one per atomizer) provides
the operator controls necessary for basic speed
control operation of a given applicator and dis-
plays the speed and diagnostic information for
that atomizer.
Temperature/Humidity Card
(Optional)
The Temperature/Humidity Card provides a user
selectable display of temperature or relative hu-
midity for each remotely mounted probe. Degrees
Fahrenheit or Celsius can be selected.
Current-to-Pressure Transducer
A current-to-pressure (I/P) transducer is required
for control of each rotator. Based upon the error
between the present speed and the setpoint, an
electrical analog signal is generated from the Con-
trol Card. Each electrical signal is converted to a

pneumatic pressure signal by the I/P transducer.
The pneumatic signal is then supplied to a 1:1 air
piloted regulator (volume booster) located near
the atomizer.
Fiber Optic Receiver Module
A ber optic transmitter assembly, located on each
atomizer, sends pulses of light through a ber optic
cable to the Fiber Optic Receiver Module. The
Fiber Optic Receiver Module converts the light
pulses to an electrical signal which is then sent
to the Control card for processing.
Brake Solenoids (Optional)
Brake solenoids supply pilot air to the brake valves
in order to minimize the time required for transitions
from higher speeds to lower speeds. Braking is
not used on Turbodisk rotators.
Brake Air Valves (Optional)
The brake air valve is an air piloted three way
valve that supplies the necessary volume across
the rotator motor vanes in reverse direction to
produce quick reduction in speed. Brake valves
are not used for Turbodisk rotators.
Number of Temperature/Humidity Cards:
0, 1, 2, 3, 4, or 5
Model No. A11515 - A B C D E
Number of Atomizer Cards (Rotators):
0, 1, 2, 3, 4, 5, or 6
115 or 230 VAC Input:
0 - 115 VAC
1 - 230 VAC
Rotator Type:
0 - No rotator 6 - 10" unidisk
1 - 6" conical disk 7 - 12" unidisk / 12" conical
2 - Standard Aerobell disk
3 - Aerobell 33 8 - Standard Aerobell w/brake
4 - 6" unidisk option
5 - 8" unidisk / 9 - Aerobell
33 w/brake option
9" conical disk
Cable/Tubing Length:
0 - None 3 - 75 ft. (22.86 m)
1 - 25 ft. (7.62 m) 4 - 100 ft. (30.48 m)
2 - 50 ft. (15.24 m)
When ordering, use A11515-ABCDE:
A11515 PULSETRACK 2 SPEED CONTROL AND
MONITOR SYSTEM MODEL IDENTIFICATION

SPECIFICATIONS
Operating
Temperature: 0°C to 50°C
Storage
Temperature: -20°C to 85°C
Humidity: 0 to 95% non-condensing
Size: 20" H x 16" W x 8" D
(50.8 cm X 40.6 cm X 20.3 cm)
Weight: 52 lbs. (23.6 kg)
Electrical
AC Input: A11515-XX0XX Models
100-120 VAC, 50/60 Hz
2.1 A rms
Fused at 3 Amps
A11515-XX1XX Models
200-240 VAC, 50/60 Hz
1.1 A rms
Fused at 1.5 Amps
Analog Inputs: Remote Speed Setpoint
0-10 VDC or 4-20mA
Switch Selectable
T
emp./Humidity Inputs 4-20mA
250 ft. (76.2m) maximum
cable length
Analog Outputs:
Speed Feedback
0-10 VDC or 4-20mA
Switch Selectable
Discreet Inputs:
Master Enable, Master
Reset, Rotator Enable
Sourced 24 VDC @ 2.3mA
Active Low - connect input
to ground to activate
Discreet
Outputs: Temperature/Humidity,
Master Overspeed, Master
Underspeed, Master Loss
of Feedback, Master Fault,
Rotator Active, Rotator
Fault, Brake Control Active
High - put out 24 VDC when
active, 0.25A maximum per
output
Pneumatic
Inputs
Supply Air: 1/4" ID x 3/8" OD
110 psi (7.6 bar) maximum,
operating
80 psi (5.5 bar) minimum,
operating
40 micron ltration
Pressure Switches
(Enable Inputs): 15 psi (1.03 bar) minimum
to activate
150 psi (10.3 bar) maximum
Outputs
Control Outputs*: 0.106" ID by 5/32" OD
100 ft. (30.5m) maximum
length to volume booster
Brake Control*: 0.170" ID x 1/4" OD
100 ft. (30.5m) maximum
length to brake valve
assembly
Brake Supply*: 1/4" ID x 3/8" OD
100 psi maximum
100 ft. (30.5m) maximum
length from brake valve
assembly to rotator
General
Fiber Optic
Cable: Maximum length is 150 ft.
(45.7m)
Temperature / Humidity Probe
Temperature
Range: 0-100°C (32-212°F)
Accuracy: ± 0.6°C (± 1°F)
Repeatability: ± 0.3°C (± 0.5°F)
Humidity
Range: 3-95% RH
Accuracy (@ 72°F):
± 2.5% from 20% to 80%
± 3.1% <20%, >80%
Drift: ± 0.1% / °F
Repeatability: ± 1% RH
* Longer tubing lengths may be acceptable de-
pending on overall total lengths of pilot signals
and supply signals and the specic application.
However, longer lengths may degrade overall
speed control performance.
Environmental / Physical

Figure 1: Typical Turbodisk 2 Installation With Temperature Humidity Cards

ELECTRICAL NOISE
Electrical noise refers to stray electrical signals
in the atmosphere at various signal strengths
and frequencies that can affect the operation
of equipment. One of the best ways to prevent
this is to shield the equipment and cables within
a continuous ground envelope, such that any
incident noise will be conducted to earth ground
before it can affect the circuit conductors.
For conductors inside the control panel the ground-
ed enclosure provides this envelope.
For factory supplied control cables shielded cable
has been used. The shield typically consists of an
overall foil shield in combination with an overall
braided shield. This provides the most effective
shielding, as the foil covers the "holes" in the braid,
and the braid allows for practical 360°termination
at both ends of the cable.
The AC input cord is not shielded, but instead is
directed to an AC line lter as soon as it enters the
cabinet. This lter lters out any noise that comes
in on the AC line. For maximum noise immunity
the AC line should connect to the lter as soon
as it enters the cabinet with as short of leads as
pos-sible. Additional noise protection is provided
by running the AC input line to the control panel
in grounded conduit, which is the recommended
method and is required by most codes.
For maximum noise protection any user supplied
input/output (I/O) wiring should be made using
shielded cable or conduit which is connected to
earth ground in a continuous 360°fashion at both
ends. The best way to do this is to use a connector/
tting at each end of the cable/conduit that makes
contact to the grounded enclosure in this manner.
Connecting the drain wire of a shield to a ground
point on or in the cabinet (usually referred to as
pigtailing) is not an effective method of shielding
and actually making things worse (see Figure 2).
Cable is recommended for the DC I/O. Again, for
maximum noise immunity the cabling must contain
overall foil and braided shields and be terminated
in a continuous 360°manner as previously de-
scribed. Special ttings have been provided on
the control panel for termination of these cables
where they enter the cabinet. The use of these
ttings is described under "Electrical I/O" in the
"Installation" section of this manual.
Figure 2: Cable Connection Examples

INSTALLATION
LOCATION
Control Panel
> The PulseTrack 2 Control Panel MUST
be located outside the hazardous area (see
NFPA-33).
> This manual MUST be read and thor-
oughly understood by ALL personnel who
operate, clean, or maintain this equipment.
Special care should be taken to ensure that
the WARNINGS and requirements for oper-
ating and servicing safely, are followed.
W A R N I N G
!
Install the control panel in a convenient area
outside the hazardous location, where it will be
protected from the possibility of any contact with
water, vapor or high humidity, and ambient tem-
peratures do not exceed 120°F (49°C). The area
should be clean, dry and well ventilated.
Brake Valve(s)
(Bells Only - Optional)
If a bell system is ordered with the brake option
an A11547 Brake Valve Assembly will be supplied
for each bell. Install the brake valve assembly(s)
on the LA0042 Air Manifold Assembly (supplied
separately) as follows (see Figure 3):
1. Remove the turbine air volume booster from
the manifold by loosening the swivel tting.
2. Attach the swivel tting of the brake valve
assembly to the manifold tting.
3. Attach the swivel tting of the turbine air volume
booster to the brake valve tting.
The LA0042 Air Manifold should be mounted in a
convenient location such that the maximum tubing
lengths from the control panel to the brake valve
and the brake valve to the rotator do not each
exceed 100 ft. (30.5m).
> Do not locate the control panel near
or adjacent to heat producing equipment
such as ovens, high wattage lamps,
steam pipes, etc.
C A U T I O N
!
Bolts or screws used for mounting must be at
least 3/8" (9.5mm) in diameter. If mounting to a
non-metallic wall, the mounting screws must be
secured to studs in the wall. If mounting to a metal
wall, the wall must be at least 0.100" (2.5mm) thick.

Figure 3: Optional Brake Control Valve Assembly (Bell Systems Only)
TB3-N
TB3-L
TB3-Ground
TABLE 1 - AC INPUT POWER
CONNECTIONS
Description
AC Neutral
AC Line (Hot)
Earth Ground
Connection Point
INPUT POWER
TheAC Input power routing and connections to the
control panel should be supplied from a FUSED
DISCONNECT rated 10Amps/240VAC or great-
er, and should meet all guidelines of applicable
electrical codes and any other requirements as
suitable for the location. LOCKOUT/TAGOUT
procedures should be put in place for the fused
disconnect. Using conduit, route the input power
wiring, 14 AWG (2mm2/ 300V minimum) through
Temperature/Humidity Probe(s)
(Optional)
the AC Power opening in the top left corner of the
control panel. For greatest noise immunity the AC
input should be located as close as possible to the
AC line lter (see Figure 4). For this reason it is
recommended that the AC input not be relocated
to another position on the control panel. Route
the input power wiring through the conduit and
attach to terminal block TB3 as shown in Table 1
and Figure 4.
> After making the input power con-
nections, double-check to ensure that
the control panel is properly grounded by
measuring the resistance from one of the
Remote I/O connectors on the top of the
panel to an external ground reference.
The resistance should be less than 0.1
ohms.
C A U T I O N
!
> The temperature/humidity probes MUST
be located outside the hazardous area (see
NFPA-33).
W A R N I N G
!
Install the optional temperature/humidity probe(s)
in a desired area outside the hazardous location
such that the maximum length of cable from the
probe to the control panel does not exceed 250
ft. (76.2m). A 50 ft. (15.2m) cable assembly
is supplied with each probe. Additional 50 ft.
(15.2m) cable assemblies (p/n 77220-00) may be
purchased separately to extend this length up to
the 250 ft. (76.2m) maximum.

FIBER OPTIC CABLE
(See Figure 5)
Remove the tting from the ber optic input port
(FO1 - FO6) on the side of the control panel and
slide over one end of the ber optic cable. Open
the control panel door. Insert the end of the ber
optic cable through the input port tting and into
the hole of the black rectangular ber optic recep-
tacle on the ber optic receiver module. Tighten
the screw of the ber optic receptacle onto the at
of the cable extension and secure the tting on
the side panel. Route the ber optic cable to the
rotator and connect the other end of the cable to
the ber optic input tting of the rotator.
Figure 4: AC Input Power Connections
The ber optic cables are integrated into ¼” tubing
for mechanical protection. Aminimum bend radius
of 3" is required. Care must be taken to prevent
kinking for protection of the ber optic cables.
Avoid exposure of the cable ends to chemicals
such as paint or solvents. Exposing the cable
ends to such chemicals will cause damage and
can severely reduce the ability of the cable to
transmit light.
The control panel is precongured for 115 VAC or
230 V AC depending on the model number. Refer
to the "Parts Identication" section of this manual
and the product specication label located on the
control panel.
PNEUMATIC
CONNECTIONS
(See Table 2)
All pneumatic connections are made to the right
side of the PulseTrack 2 control panel. System
components should be installed to minimize the
length of pneumatic control lines. This will max-
imize the rotator speed control response. Tubing
may exceed the maximum lengths as indicated in
the "Specications" in the "Introduction" section of
this manual dependent on the specic installation
requirements; however, this could degrade overall
speed control performance.
Figure 5: Fiber Optic Cable Installation

Supply Air
Using the supplied 3/8" OD tubing connect the
Supply air inlet to a source of clean, dry factory
air having an operating pressure of 80 psi (5.5
bar) minimum and 110 psi (7.6 bar) maximum.
For optimal speed control response ensure the
supply air is at least 100 psi minimum operating
pressure.
Control Output(s) (CL1-CL6)
Using the supplied 5/32" OD tubing, connect the
control output(s) to the pilot signal port(s) of the
volume booster(s) which are supplying turbine air
to the rotator(s). It may be necessary to install
a 5/32" adapter tting in the volume booster pilot
port. DO NOT replace this tubing with larger
diameter tubing or speed response may be ad-
versely affected.
Enable Input(s) (EN1-EN6)
The enable input is an interlock which must be
made active in order for speed control to occur
on a given channel. This can be done pneu-
matically by using the enable inputs on the right
side of the control panel or electrically by using a
remote switch across the enable input contacts
(see Electrical I/O later in this section).
For pneumatic activation, connect the supplied
1/4" OD tubing from the activation source to the
Enable input on the right side of the control panel.
Typically, the pneumatic Enable input is used
to interface with an Ransburg Air Logic Panel.
(See the appropriate service manual for further
information.)
Optional Brake Control Output(s)
(BR1-BR6) (Bells Only - See Figure
3)
Using the supplied 1/4" OD tubing, connect the
brake control output(s) to the pilot air input(s) of
the supplied brake valve assembly(s). Using the
supplied 3/8" OD tubing, connect the output port
of the brake valve assembly(s) to the brake air
input of the bell applicator(s).
When a lower speed is requested than the speed
the bell is currently spinning at, the brake valve will
turn on and apply air against the rotator vanes to
assist in a more rapid transition to the lower speed.
Once the new speed is reached, the brake valve
will turn off. Additionally, it is possible to congure
the system so that the brake turns on when the bell
speed is disabled, to assist in bringing the bell to
a full stop more quickly. This is explained further
under "Dip Switch Settings" in the "Installation "
section of this manual.

Factory Air (clean and dry)
Rotator 1 Volume Booster Pilot
Rotator 2 Volume Booster Pilot
Rotator 3 Volume Booster Pilot
Rotator 4 Volume Booster Pilot
Rotator 5 Volume Booster Pilot
Rotator 6 Volume Booster Pilot
Rotator 1 Enable Air Source
Rotator 2 Enable Air Source
Rotator 3 Enable Air Source
Rotator 4 Enable Air Source
Rotator 5 Enable Air Source
Rotator 6 Enable Air Source
Rotator 1 Brake Valve Assy. Pilot
Rotator 2 Brake Valve Assy. Pilot
Rotator 3 Brake Valve Assy. Pilot
Rotator 4 Brake Valve Assy. Pilot
Rotator 5 Brake Valve Assy. Pilot
Rotator 6 Brake Valve Assy. Pilot
TABLE 2 - PNEUMATIC CONNECTIONS
From
Supply
CL1
CL2
CL3
CL4
CL5
CL6
EN1
EN2
EN3
EN4
EN5
EN6
BR1
BR2
BR3
BR4
BR5
BR6
To
Supply Air to PulseTrack 2
Rotator 1 Transducer Output Control Signal
Rotator 2 Transducer Output Control Signal
Rotator 3 Transducer Output Control Signal
Rotator 4 Transducer Output Control Signal
Rotator 5 Transducer Output Control Signal
Rotator 6 Transducer Output Control Signal
Rotator 1 Speed Control Interlock
Rotator 2 Speed Control Interlock
Rotator 3 Speed Control Interlock
Rotator 4 Speed Control Interlock
Rotator 5 Speed Control Interlock
Rotator 6 Speed Control Interlock
Rotator 1 Brake Output Control Signal
Rotator 2 Brake Output Control Signal
Rotator 3 Brake Output Control Signal
Rotator 4 Brake Output Control Signal
Rotator 5 Brake Output Control Signal
Rotator 6 Brake Output Control Signal
Description

ELECTRICAL I/O
(See Table 5)
Electrical I/O terminals are available from a
breakout board inside the PulseTrack 2 control
Panel (see Figures 6 and 7). For maximum noise
immunity all electrical I/O should be run in cable
having a foil shield with an overall braided shield.
Special noise reduction connectors have been
provided at the top of the PulseTrack 2 control
panel for routing of all electrical I/O (see Figure
8). Signals specic to an individual rotator can be
routed through that rotator'sATM connector, while
common signals can be routed through the SYS
connector. To make electrical I/O connections
using these connectors, perform the following:
1. Remove the cable grommet hardware from the
desired connector (see Figure 9A).
2. Route desired length of cable through connector
housing and mark 1" span of cable that passes
through connector housing as shown in Figure
9B.
3. Remove cable and strip marked 1" section to
the cable braid.
4. Slide the cable grommet hardware onto the
cable in the order shown in Figure 9A.
5. Route the cable back through the cable housing
and make the appropriate I/O terminal connections
(see Table 5).
6. Tighten the cable grommet ensuring the grom-
met spring makes 360° contact with the exposed
cable braid.
7. For maximum noise immunity, connect the braid
of the cable to earth ground at the end opposite
the control panel.
NOTES
Table of contents
Popular Control System manuals by other brands
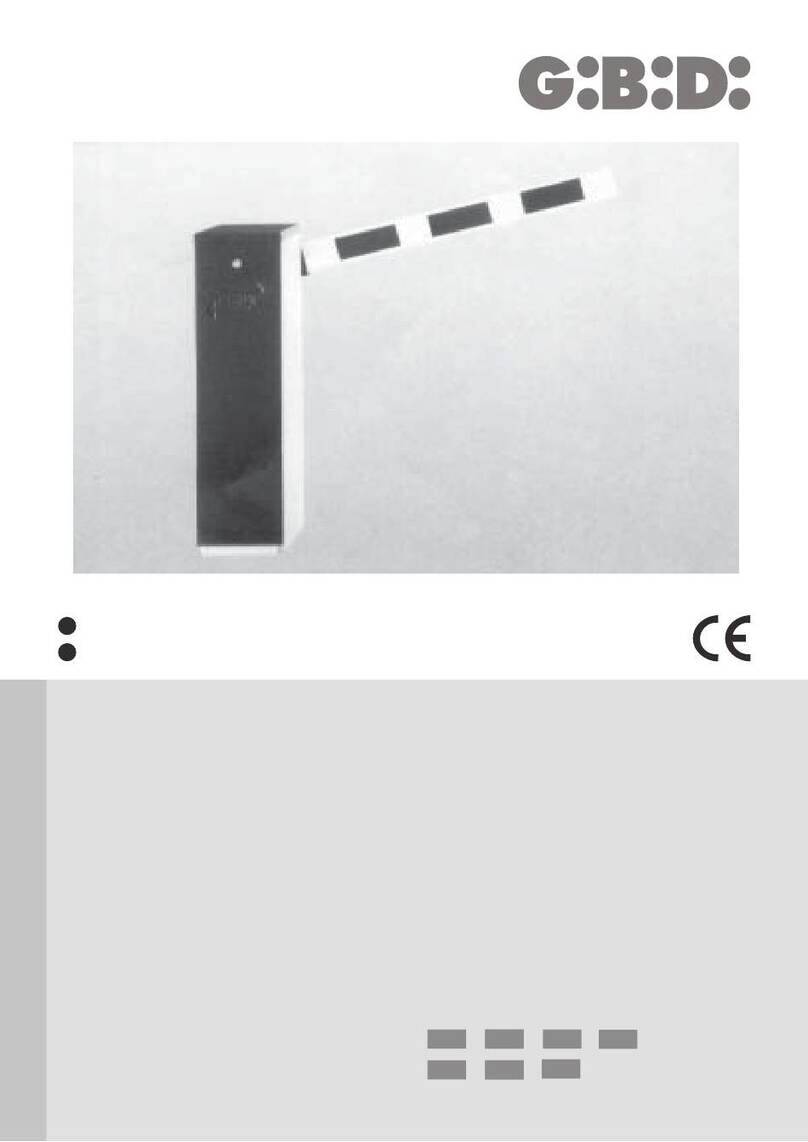
GiBiDi
GiBiDi BARR 600 Instructions for installation
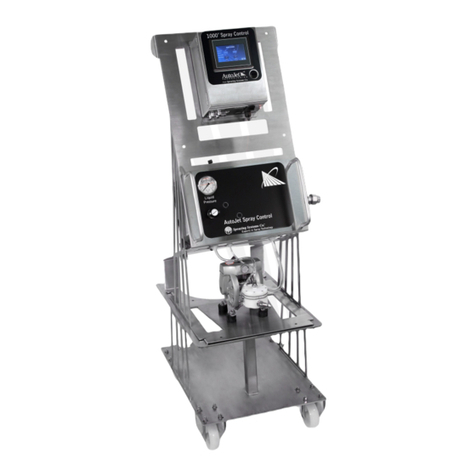
Spraying Systems
Spraying Systems AutoJet SCS Series owner's manual
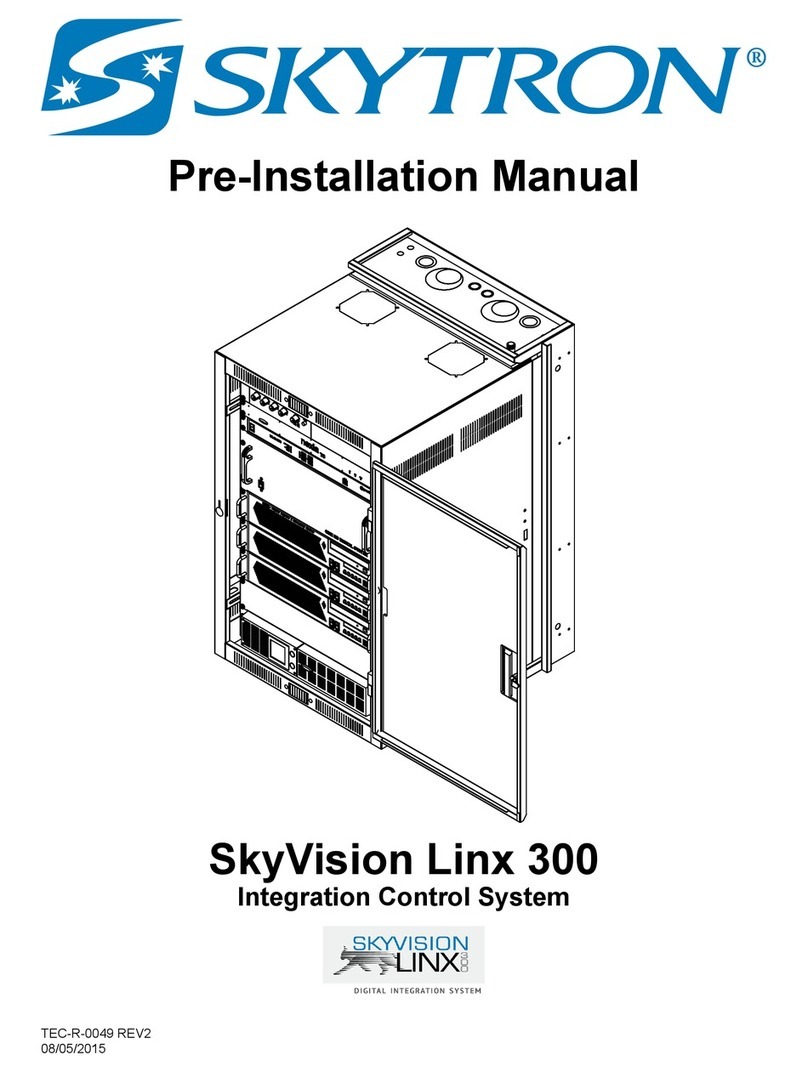
sky vision
sky vision Linx 300 Preinstallation manual
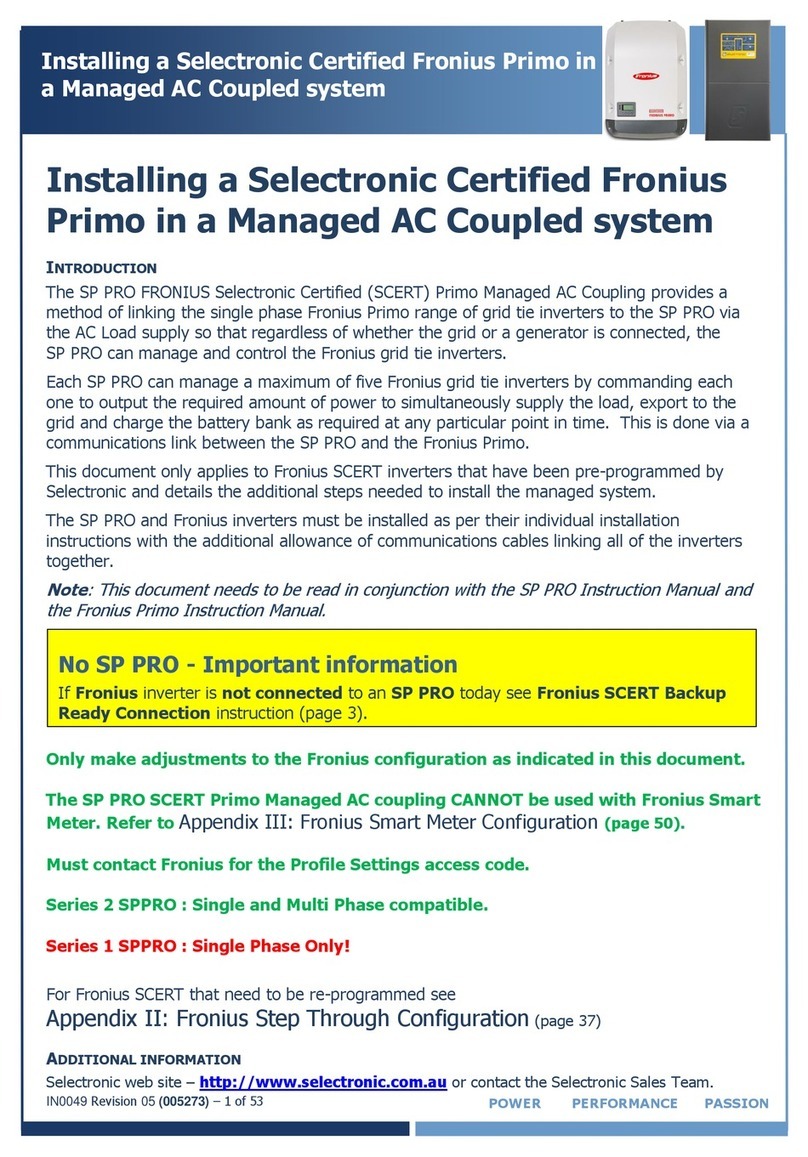
FRONIUS
FRONIUS SP PRO Series 1 instruction manual
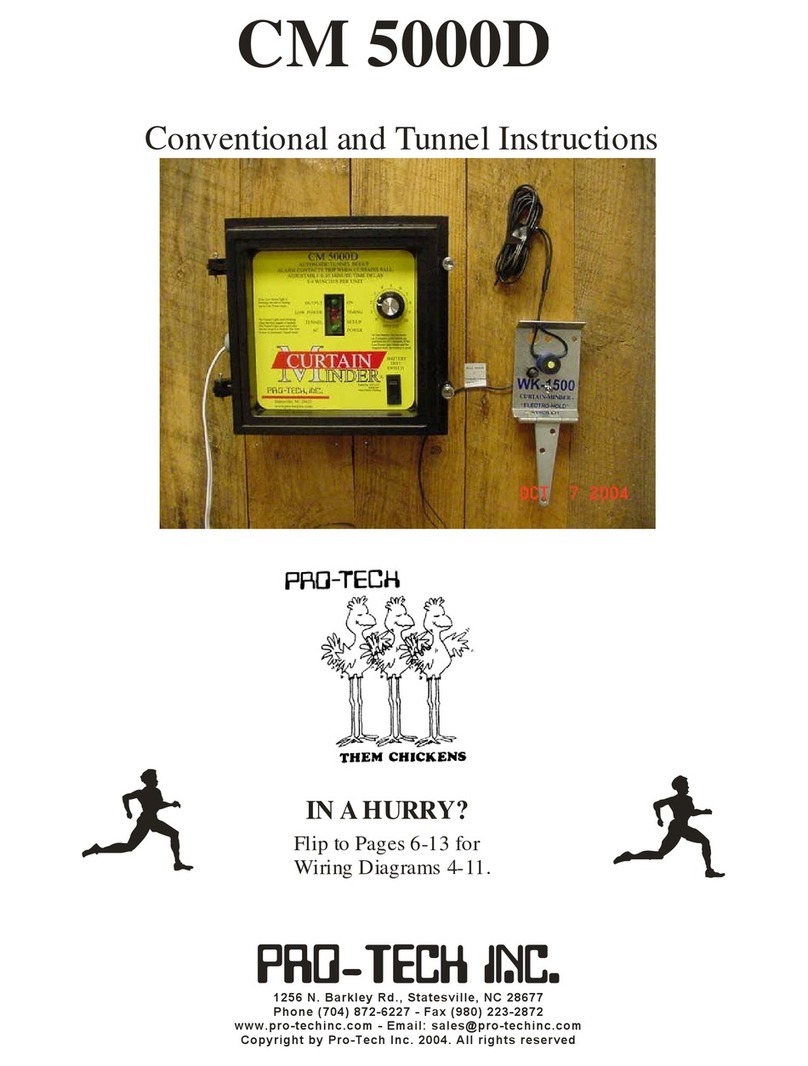
protech
protech CM 5000D instructions
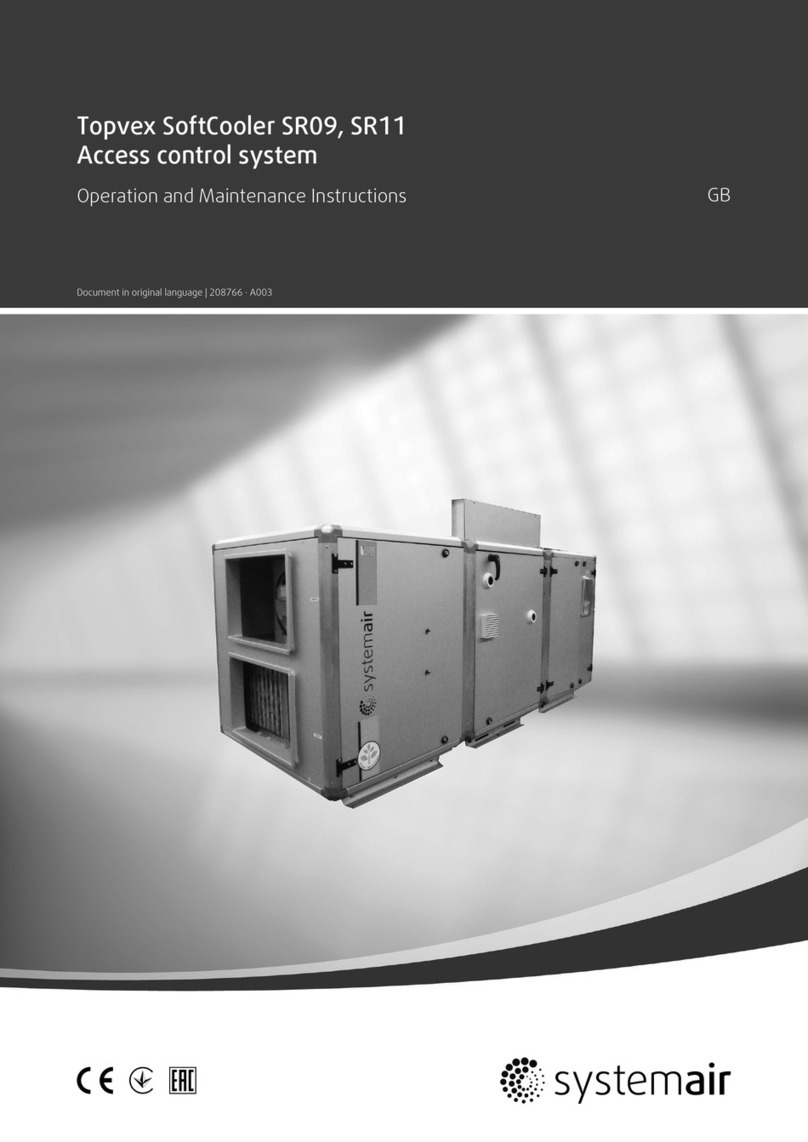
System air
System air Topvex SoftCooler SR11-L manual

HIK VISION
HIK VISION DS-K260X-G Quick setup guide
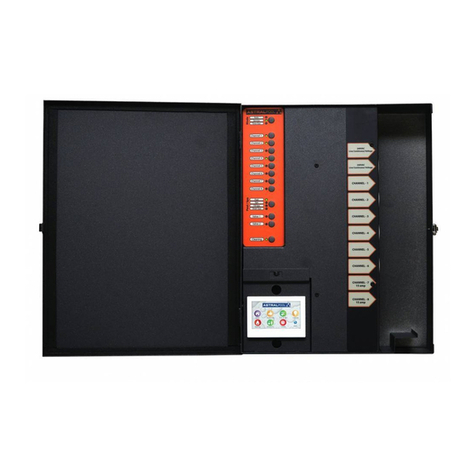
Astral Pool
Astral Pool Viron Connect 10 Installation and operating instructions
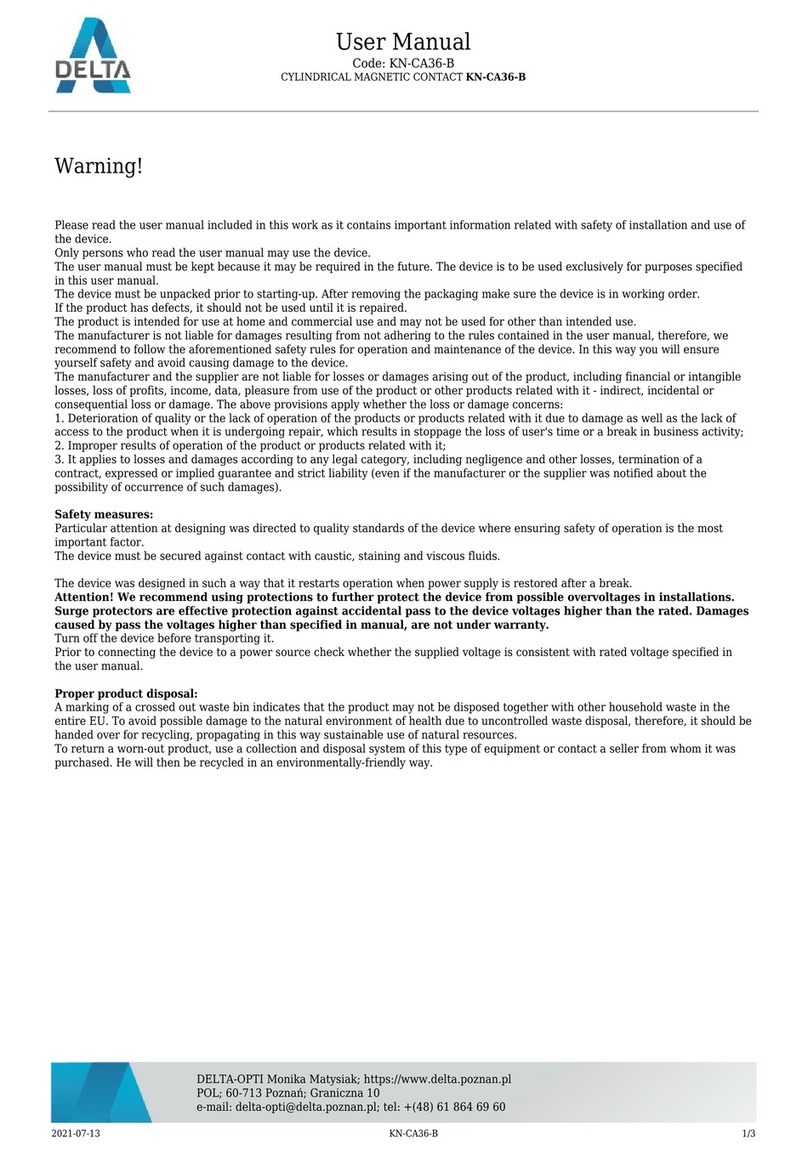
Delta
Delta KN-CA36-B user manual

Samson
Samson Trovis 6400 Mounting and operating instructions
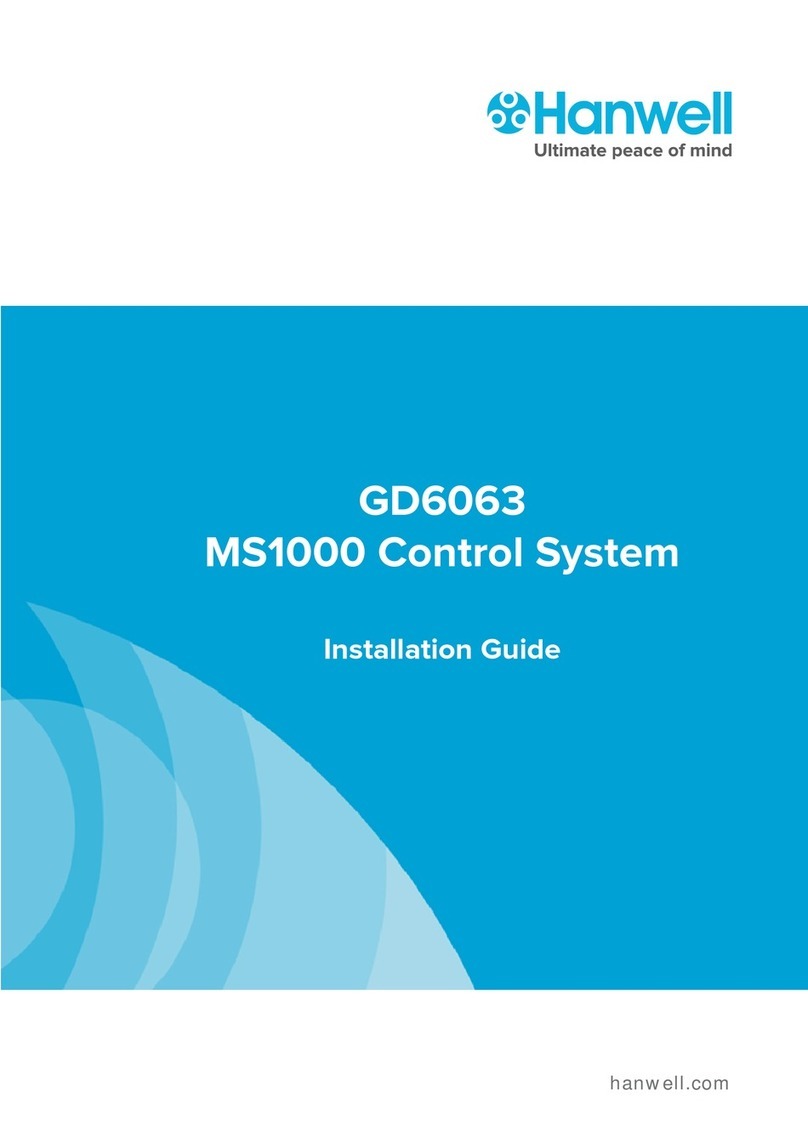
Hanwell
Hanwell MS1000 installation guide
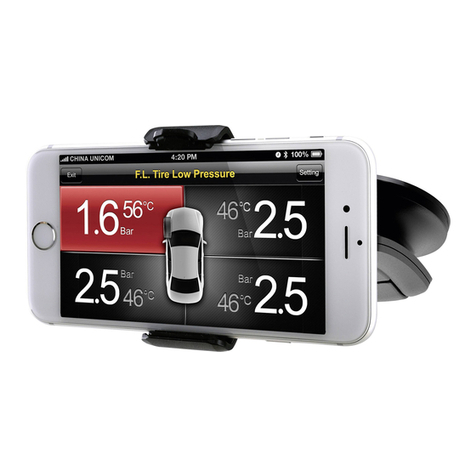
Conrad
Conrad TPMS-8886 operating instructions