Evolution Micro Fusion II User manual

0
Micro Fusion II Instruction
Manual
FEATURES
Precision Laser Cut Parts
Lightweight Strong Airframe
Excellent Low Speed Stability
Comprehensive Instruction Manual
High Quality Balsa Ply and Depron parts
Excellent Precise Handling Characteristics
High Quality Comprehensive Hardware Pack

1
Introduction
The New Micro Fusion has takes those comments made by our customers and develops them into the
Fusion package. These comments along with hours of testing and development we have improved the
strength, durability and overall performance of the model. For those who owned the original Fusion you will
note the changes, some of them are only minor, such as the length of Tail moment and others like the
battery hatch provide a better all round model. We listen to our customers to improve our products, so if you
have anything you wish to share please let us know.
The Evolution Fusion has been designed predominantly for the Fun Fly enthusiast and the club flyer. The
Fusion will loop on the spot, roll in the blink of an eye and inspire confidence as it remains rock solid and
stable. This model that has been designed to be highly manoeuvrable, but also to be attractive with style
and flair.
The laser cut parts simply slot together to provide a lightweight structure without compromising strength.
The Fusion is simple and satisfying to build for the amateur and experienced builder.
Each kit contains a comprehensive hardware pack that includes the closed loop systems, hinges, hatch latch
and horns to name but a few, we even include fuel tubing (Glow Version)!
The Evolution Fusion has been designed to meet the needs of the Fun Fly competition pilot in an attractive
package. We hope that you have as much fun building and flying it as we have had developing it!
Building Recommendations
Check all parts from the box to ensure that they are present; if not then please contact us at the e-mail
address at the back of the instructions. We do from time to time make mistakes!!
Ensure that you use a completely flat base on which to build the model, this should be large enough the build
the wing 50” (1270mm) x 16” (400mm) as a minimum.
Read through the instructions before starting to build, understand each step before applying glue.
The glue detailed in the instructions is for a guide only, this is what we used for the prototypes, it is at the
builder discretion which glue is used, but ensure that it is suitable for the intended purpose. Always read the
application instructions to ensure you achieve a strong joint. Depron is a foam material; Standard Cyano will
attack and melt it, always use foam safe glue. Always read the safety instructions supplied with the glue.
Take your time building the model, build a straight and strong model, this will ensure the model will fly well!
Enjoy. Building is part of aero modelling!
This radio controlled model is not a toy. It can cause serious injury to the operator, public and property if
misused or abused. Ensure that you read all the instructions supplied with this kit and instructions provided
with the engine and radio control system or any other components purchased separately carefully. Also
make sure that any parts bought separately are suitable for their application.
The kit contains small and potentially sharp parts, keep away from children.
Additional Materials Required
Recommended Tools
Uhu Por
Foam Safe Cyano
Standard Thin or Medium Cyano
White Wood Glue
Epoxy Resin
Tinned Copper Wire (For Undercarriage)
Solder
Heat Shrink Covering Material
Engine Mount
Radio Gear
Modelling Knife
Razor Plane
Set Square
Sand Paper
Sanding Block
Blow Torch
Drill
Drill Bits
Building Board – Completely flat 1300 x 400mm Min
Bradawl

2
Micro Fusion Part List
Wood Pack
Hardware Pack
Description Quantity
Piano Wire Aileron Pushrods 2
Aileron Pushrod adaptors 2
Single Saddle Cl
amp 12
swg
4
Undercarri
age Screws
8
200mm Mylar Strip 1
Closed Loop Kit (4 adaptors, 4 Ferrules, 1.8m Wire) 1
Magnet and washer 1
¼ x ¼ x 1 Spruce bearer 2
Description
Sheet Size
Quantity
Metric
Imperial
Web
bing Sheet
1.5 x
75
x
457
mm
1/16 x 3 x 18
”
1
Leading and Trailing Edge Sheet 1.5 x 75 x 915mm 1/16 x 3 x 36” 2
Leading Edge
4.5
x
18
x
915
mm
3/16
x
3/4
x
36
”
1
Wing Spars and Trailing Edge Spar 4.5 x 4.5 x 915mm 3/16 x 3/16 x 36” 3
Wing Centre Section S
heet
1.5 x 75 x
457
mm
1/16 x 3 x
18
”
1
Fuselage Bottom and Front Deck Sheet 3 x 75 x 457mm 1/8 x 3 x 18” 1
Rib Capping Strips
1.5 x 6 x 915mm
1/16 x ¼ x 36”
5
Aileron/
Rudder
/
Elevator
/
Tail
Plane
Strip
4
.5 x 6 x 915mm
3/16
x ¼ x 36”
2
Fuselage Triangular Fillet 6 x 6 x 915mm 1/4 x 1/4 x 36” 3

3
Laser Cut Parts
27
1 2
1
3
4
5 6 7 8
10
11
9
12
13
15
17
14
18
19
20
21
22
23
24
25
26
29
30
28
31
32
33
34
35
W1
W2
W3
W4
16

4
Part No. Description Sheet Material
1 Left and Right Fuselage Sides (2) 3mm (1/8”) Balsa
2 UC centre spacer Plate 3mm (1/8”) Balsa
3 Tail Plane Tips (2) 4.5mm (3/16) Balsa
4 Elevator Tips (2) 4.5mm (3/16) Balsa
5 Aileron Outer Tips (2) 4.5mm (3/16) Balsa
6 Rudder Leading Edge 4.5mm (3/16) Balsa
7 Rudder Bottom Frame 4.5mm (3/16) Balsa
8 Rudder Top Frame 4.5mm (3/16) Balsa
9 Rudder trailing Edge 4.5mm (3/16) Balsa
10 Wing tips (2) 4.5mm (3/16) Balsa
11 Fin Main Section 4.5mm (3/16) Balsa
12 Fin Front Section 4.5mm (3/16) Balsa
13 Elevator Centre Section 4.5mm (3/16) Balsa
14 Aileron Leading Edge (2) 4.5mm (3/16) Balsa
15 Aileron Horn Supports (2) 4.5mm (3/16) Balsa
16 Aileron Trailing Edge (2) 4.5mm (3/16) Balsa
17 Elevator trailing Edge 4.5mm (3/16) Balsa
18 Tail Plane Leading Edge 4.5mm (3/16) Balsa
19 Tail Plane Trailing Edge 4.5mm (3/16) Balsa
20 Elevator Leading Edge 4.5mm (3/16) Balsa
21 Aileron Inner Tips (2) 4.5mm (3/16) Balsa
22 Top Rear Deck 4.5mm (3/16) Balsa
23 Tail Plane Centre Section 4.5mm (3/16) Balsa
24 Tail Skid 3mm (1/8) Ply
25 Hatch magnet support 3mm (1/8) Ply
26 U/C Front Mount 3mm (1/8) Ply
27 F1 - Firewall 3mm (1/8) Ply
28 U/C Rear Mount 3mm (1/8) Ply
29 F2 – Servo Tray 3mm (1/8) Ply
30 Wing Aileron Servo Mounts (2) 3mm (1/8) Ply
31 Wing Band Support 1mm (1/32) Ply
32 Fuselage Doublers (2) 1mm (1/32) Ply
33 Hatch Floor 1mm (1/32) Ply
34 Aileron Horn set 1mm (1/32) Ply
35 Elevator and rudder closed loop horn sets 1mm (1/32) Ply

5
Description
Quantity
Undercarriage Front Leg 1
Undercarriage Rear Leg 1
Undercarriage Support 2
Tail Skid 1
Front Leg 12 swg
Rear Leg 12 swg
Piano Wire U/C
Fusion Parts List
Supports 12 swg
Tail Skid 16 swg

6
Building Instructions
Fin and Rudder
Take the six parts that form the Fin and Rudder (Parts 12, 11, 6, 8, 7 and 9), trial fit before gluing together
using Cyano or white wood glue. With the supplied strip of 4.5 x 6mm (3/16” x 1/4”) cut to length to form the
centre ribbing pieces. Mark a centre line on the Rudder leading edge and chamfer to a 45° angle with a
razor Plane.
Place the parts on a bench like so Glue together Add the two ribbing pieces
With a sharp knife cut the slots for two hinges 10mm (3/8”) from the top and bottom. This gap should be
parallel for the full length of the Rudder. Cut 10mm (3/8”) strips from the supplied Mylar hinge material and
insert into the hinge slots; 50% in the Rudder and 50% into the Fin. Ensure that you get at least 45° free
movement either way. Do not glue the hinges in at this stage! Cover both parts with your chosen covering
first.
Sand all parts to a smooth Finish and round off the leading edge of the Fin ready for covering. !!! Warning.
Ensure that you are wearing an appropriate mask for sanding balsa and are in a well ventilated area. We
recommend sanding in free air (outside).!!!
Tail Plane and Elevator
Take the five pre-cut parts (Parts 3(2), 4(2), 13, 17, 18, 19, 20 and 23) which form the Tail Plane and
Elevator, trial fit, ensure the tips are at 90° to the leading and trailing edge before gluing with Cyano or white
wood glue. With the supplied strip of 6 x 9.5mm (1/4” x 3/16”) cut to length to form the eight ribbing pieces,
glue in place with Cyano or white wood glue. Do not glue the Elevator to the Tail Plane; theses should be 2
separate pieces!
With a pencil mark the centre line of the leading edge of the Elevator and chamfer to a 45° angle with a razor
Plane ready to receive the hinges.
Tail Plane parts laid out Glue Tail Plane and Elevator parts separately.
Rib pieces inserted

7
Wit h a sharp knife cut the slots for four hinges 10mm in from either end and evenly spaced, ensure that the
Elevator sits centrally on the Tail Plane. Cut 3/8” (10mm) strips from the supplied Mylar hinge material and
insert into the hinge slots, 50% in the Elevator and 50% into the Tail Plane. Ensure that you get at least 45°
free movement either way. Do not glue the hinges in at this stage! Cover both parts with your chosen
covering first.
Sand all parts to a smooth Finish and round off the leading edge of the Tail Plane ready for covering.
!!! Warning. Ensure that you are wearing an appropriate mask for sanding balsa and are in a well ventilated
area. We recommend sanding in free air (outside).!!!
Fuselage
Lay the two Fuselage sides (Parts 1(2)) on the work bench ensuring that you have a left and right hand side.
With a thin layer of epoxy or white wood glue attach the 1mm (1/32”) ply doubler (Part 32(2)). Weigh down
to ensure that the parts cannot ‘curl’ and to allow dry.
Using the 6mm (1/4”) triangular fillet, glue with Cyano or white wood glue to the outer edge of the Fuselage
shown hatched below, excluding the wing seat, section above the Tail Plane and small rear section between
the Fuselage bottom and Tail Plane. Make cuts in the fillet to allow it to follow the bottom curve of the
Fuselage. Set the triangular fillet 3mm (1/8”) back from the front of the Fuselage to allow F1 (Part (27)) to sit
flush with the Fuselage side; see the diagram on the next page.
Cut servo holes in F2 (Part 29) to suit the servos you have chosen for this model. Carefully mark the
position of F2 in the Fuselage to ensure that your chosen servos have the depth to fit, and the higher (front)
servo fits below the wing seat. The rear of F2 lines up with the rear of the wing seat. The front servo sits on
the two pieces of 6 x 6mm (¼ x ¼) spruce supplied in the hardware pack. These can be glued in place now
or when fitting the servo later.

8
Glue the excess triangular fillet to the underside of F2 and dry fit between the Fuselage sides, ensure that F1
fits in the 3mm (1/8”) recess left at the front. If you are building the electric version carefully drill holes at the
top and the bottom of the former to allow air to enter the Fuselage for cooling.
F1 should be placed with the pre cut hole set towards the bottom of the Fuselage, once glued in place
chamfer the top and bottom to follow the Fuselage sides.
With F1 and F2 in place the Fuselage sides should taper back so that the triangular fillet at the rear just
touches. Once satisfied that the part fits correctly glue in place using epoxy. We have found this easier by
gluing F2 to one side of the Fuselage first and allowing to dry before offering the other side and inserting F1.
Ensure that F1 is 90° to the centre line of the Fuselage.
We have shown standard servos fitted in the Fuselage, but recommend that you use a good quality
mini/micro servo to reduce weight. Ensure the mini/micro servo is of the same or better specification as a
standard servo.
Once the epoxy has set, the top rear deck (Part 22) to the Fuselage, ensuring the rear Fuselage remains
square and the cut out for the Fin remains along the Fuselage centre line.
With epoxy glue the front ply (Part 26), centre balsa (Part 2) and rear ply (Part 28) undercarriage plates into
position.
With the supplied the sheet of 3mm (1/8”) balsa plank the front top deck of the Fuselage. If you are building
the glow version continue to plank the whole of the bottom. The planking grain should run from side to side
to provide maximum strength.
CL
F1 F2
F1 set flush with front of
fuselage, triangular fillet set
back 3mm to allow this.
3mm

9
If you are building the electric version take the battery hatch floor (Part 33) and place the tab under the ply
U/C mount and mark the ends as shown below.
Remove the section of triangular balsa and plank with the 3mm (1/8”) from this point to the back of the
Fuselage.
Plank the bottom of the hatch floor (part 33) with 3mm (1/8”) balsa except for the tab that fits under the U/C
mount. Glue the supplied washer as shown below. Insert the magnet in to the hatch magnet support (Part
25) and glue the 1mm (1/32nd) disc on the upper side. Glue the hatch magnet support at the rear hatch
opening so that the magnet projects into the opening and the magnet locks onto the washer.
Sand the Fuselage to shape rounding off the top and bottom decking and sand the top deck at the front
down to 1mm (1/16”) where it meets the wing. !!! Warning. Ensure that you are wearing an appropriate
mask for sanding balsa and are in a well-ventilated area, we recommend sanding in free air (outside).!!!
Lay the Tail skid (Part 24) on the bottom of the Fuselage and mark the distance from the rear, cut a slot
3mm (1/8”) wide to accept the skid along the centre line of the Fuselage. Slot the Fin in from the top and
ensure that the parts mate within the Fuselage. Glue scrap pieces of ply either side of the Tail skid slot to
prevent the Tail skid wire rotating as in the picture below. Ensure that they are not too large to slide into the
Fuselage.
Draw line here
Remove triangular strip

10
Adjust to suit before gluing in the skid with epoxy. Do not glue the Fin in at this stage. Ensure that the Tail
Plane can fit into the Fuselage slot and the Fin slot without fouling.
Wing and Aileron
We recommend building the entire wing with Aliphatic Wood Glue. It is generally fast setting and can be
sanded at the same rate as balsa.
Cut each piece of webbing from the supplied sheet of 1.5mm x 75mm x 457mm (1/16” x 4” x 18”) as per the
spacing shown below, making sure that all the webbing is perfectly square. Each webbing piece should be
approximately 40mm high, for example cut 8 No. webbing pieces 75 x 40mm (3” x 1 9/16”), 2 No. at 45 x
40mm (1 3/4” x 1 9/16”) etc.
The webbing should sit on the front of the spars, do not glue in place at this time, just use as a guide for rib
spacing. Carefully cut the ribs from the Depron sheet.
Dimensions shown in mm
Pin the main and trailing edge spars 4.5mm x 4.5mm x 915mm (3/16” x 3/16” x 36”) to the surface. Use a
straight edge to ensure that it is completely straight and both parts are parallel. Mark the centre of the spar
and the centre of the centre webbing; pin the centre webbing to the spar and place each rib in turn working
equally on both sides, separating each rib with a webbing piece previously cut to size as directed in the
drawing above. Push the rib down onto the spar so that the rib is flush with the board. N.B. It is important
that the bottom of the rib sits flush with the spar. (Please note the internal light look different to those
photographed)
40
24
24
W4
W4
W4
W4
W4
W4
W4
W4
W3
W3
W2
W2
W1
W1
W1
W1
24
24

11
As you install W2 take a piece of paper and roll into a tube to carry the servo wires to the centre section, this
is optional, but we Find this makes the installation look tidier. These need to be inserted as work proceeds
as it is impossible to insert after all the ribs are in place. Once the tube is in position wrap it with Sellotape to
seal the edge once in position.
Continue to place the ribs, you may Find that the Final rib is approximately 3mm (1/8”) short of the end of the
spar, cut the excess spar off later. Ensure that you place the correct rib in the correct position as per the
diagram above. Once dry, place the upper spar into position and glue in place. Glue the ribs in place, check
to make sure that the ribs are all vertical and at 90°. Once dry, glue the webbing in place.
Glue the 4.5mm x 18mm x 915mm (3/16” x 3/4” x 36”) leading edge (LE) strip on to the front of the ribs. Pin
in place and allow to dry.
Cut the 1.5mm x 75 x 915mm (1/16” x 3” x 36”) leading and trailing edge sheet into two pieces each
measuring 1.5mm x 60mm x 915mm (1/16” x 2 5/16” x 36”) and 1.5mm x 15 x 915mm (1/16” x 9/16 x 36”)
Chamfer the LE as shown below before gluing on the 1.5mm x 60mm x 915mm (1/16” x 2 7/16 x 36”) LE
sheet and 1.5mm x 15mm x 915mm (1/16” x 9/16” x 36”) Trailing Edge (TE). The LE sheet should be glued
to the centre of the spar first, then when dry place glue on the ribs and LE and pin into position.
Un-pin from the board and repeat the sheeting process to the underside of the wing. Once completed cut off
any excess spar, leading, trailing edge and sheeting, leave flush with the end ribs.
Take the 1.5mm x 75mm x 457mm (1/16” x 3” x 18”) sheeting supplied and sheet across the 4 centre ribs to
both top and bottom of the wing, glue to the ribs. Cut a hole in the underside of the sheeting between the
two centre ribs to allow the servo leads to exit.

12
Cut the 1.5mm x 6mm x 915mm (1/16” x ¼” x 36”) capping strips to length and glue in place. Ensure good
bond with the leading and trailing edge sheeting to prevent these pieces moving independently as this will
cause problems when sanding, repeat to the bottom of the wing.
Take the servo mounting plates (Parts) from the birch ply and cut holes to suit your chosen servos. Once
satisfied the servo is a good fit, glue this piece into the wing. With scrap pieces of 9.5mm x 4.5mm (3/8” x
3/16”) glue packing pieces from the servo tray to the wing capping surface to allow provide a surface for the
covering to Finish.
Take the two wing tip pieces (Part (10(2)) and glue onto the tips of the wing using foam safe Cyano or UHU
Por. The tip should be lined up with the centre of the leading edge and the centre of the trailing edge. With
some scrap 3mm (1/8”) sheeting make the triangular fillet pieces to support the wing tip. We generally only
install the supports to the upper side of the wing, but you may wish to support on both sides. Position the
fillets as set out below. The TE fillet will have to be ‘cranked’ to allow the covering to follow the wing contour
neatly.
Example of cranked TE fillet

13
Where the tip extends past the trailing edge of the wing make a fillet with scrap 1/8” (3mm) balsa as shown
in the right hand picture above.
Shape the leading edge roughly with a razor Plane before Finishing with sand paper as shown in the
diagram on page 11, continually checking the fit to the Fuselage.
Sand the entire wing to provide a smooth, blemish free surface ready for covering. !!! Warning. Ensure that
you are wearing an appropriate mask for sanding balsa and are in well ventilated area, we recommend
sanding in free air (outside).!!! Check the fit with the Fuselage.
At this point if you would prefer you may cut off the front sheeting that passes over the wing and glue it onto
the wing itself. In the event of a hard landing it is more likely to allow the wing to ‘shift’. We have not done
this with the prototype models and it is left to the builder’s discretion.
Glue the 1mm (1/32”) ply doubler (Part 31) to the rear of the wing to protect the trailing edge when the rubber
bands are fitted
Ailerons
Take the five pre-cut parts (Parts 5, 15, 15, 16 and 21) which form the ailerons, trial fit, ensure the tips are at
90° to the leading edge, fit the trailing edge, when satisfied glue with Cyano or white wood glue. With a
supplied strip of 4.5mm x 6mm x 915mm (3/16” x 1/4” x 36”) cut to length to form the ten ribbing pieces, glue
in place.
With a pencil mark the centre line of the leading edge and chamfer to a 45° angle with a razor Plane. With a
sharp knife cut slots for four hinges 10mm in from either end and evenly spaced. Cut 10mm (3/8”) strips
from the supplied Mylar hinge material and insert into the hinge slots, 50% in the Aileron and 50% into the
wing.
Repeat the above stages for the second aileron.
Ensure that you get at least 45° free movement either way. Do not glue the hinges in at this stage! Cover
both parts with your chosen covering first.
Sand to provide a smooth, blemish free surface ready for covering. !!! Warning. Ensure that you are
wearing an appropriate mask for sanding balsa and are in well ventilated area, we recommend sanding in
free air (outside).!!!

14
Covering
Before covering seat the wing, Tail Plane and Fin and make sure that all fit. Make any alterations as
necessary with Fine sandpaper and a block. Finally sand all parts to provide a smooth, blemish free surface
ready for covering. !!! Warning. Ensure that you are wearing an appropriate mask for sanding balsa and
are in well ventilated area, we recommend sanding in free air (outside).!!!
This is your chance to express yourself; unlike the ARTF models on the market you can now choose your
own colour scheme. The prototype models were covered in Solarfilm or Profilm, but the choice is yours.
Just make sure that you follow the manufactures recommendations when applying the film. We would
recommend applying a surface sealant to the area around F1 so that the film adheres better in areas where
it is likely to be exposed to glow fuel (glow version). We also recommend that you apply a glow fuel sealant
to the radio compartment of the Fuselage. Follow the manufactures recommendations when applying.
Ensure when you cover the model you do not introduce any warps, cover each section and evenly tighten
the covering on both sides. Ensure when you have Finished covering all parts they are straight and true.
Tail Skid and Undercarriage
Draw two lines on a piece of scrap ply 65mm (2 ¾”) apart. Place the front leg and rear leg on each of the
lines and screw down using the supplied 10swg saddle clamps and screws. Make any minor adjustments
with pliers to make sure that the legs are parallel where they are to be bound.
Clean the tops of the legs with sandpaper or wire wool to remove any dirt or lubricants ready to solder. Pull
the legs together so that they join as shown in the photograph. Bind together using tinned copper wire.
Heat the wire using a blowtorch and feed solder into the joint, ensuring that you flood the joint to make it
strong. Clean off the excess with a damp cloth; do not touch the leg as it will be extremely hot. We advise
wearing gauntlets at this point. Repeat for both sides. Once cool remove from the scrap ply. Save the
clamps and screws.
With the two support pieces, offer these up to the main U/C legs and Find the point at which they best fit,
make minor adjustments as before. Bind and solder as before. Repeat for the second side, ensuring that
the supports are positioned symmetrically.

15
Once the Fuselage has been covered, line the undercarriage up with the centre of the two mounting plates.
Ensure that it is placed square to the Fuselage. Place the saddle clamps over the wire screw into the pre-
drilled holes. Make sure the axles are at 90° to the centreline of the Fuselage. Minor adjustments can be
made with pliers or mole grips, just ensure that you hold the undercarriage legs when doing this to prevent
damaging the Fuselage.
Place on the supplied 1 ½” (38mm) wheel followed by collet. Ensure that the wheel rotates freely and tighten
the second grub screw. Cut off any excess piano wire.
Take the pre-bent 2mm (16 swg) wire and attach to the Tail skid using cotton, looping through each of the
pre-drilled holes several times before securing with Cyano. Ensure the Cyano penetrates through the cotton.
Final Assembly
If you have any queries about the Final assembly then please contact us at suppo[email protected]om
where we will be happy to discuss your problem and send you a photo to two to illustrate our solution.
Wing
Take the fully covered wing and ailerons, glue the hinges 50% into the aileron using a thin Cyano and ensure
that it penetrates into the slots both top and bottom. Slot the hinges into the corresponding slots on the wing.
Move the aileron full travel (min 45°) to ensure that there is no resistance and repeat the gluing process.
Repeat this for the second aileron. Due to the large control surfaces we would recommend pinning the
hinges. This is left to the builder’s discretion.
Install the servos in to the wing and feed the wires through the tubes. Pull the wires out at the centre section
where the sheeting was cut earlier. Drill pilot holes and securely screw the servos into place using the
fixings supplied with the servo. Centre the servo and attach a single arm horn as shown in the attached
picture.
Make up the horn as indicated below (Parts 34) and cut a slot in the aileron 1/32” (1mm) wide. Cut the
covering the same size as the base and securely glue in place making sure the horn remains at 90° aileron
leading edge. Repeat this for the second aileron.

16
With the supplied pushrods rods make a ‘Z’ bend using ‘Z’ bend pliers or needle nose pliers as shown in the
diagram below. Push the ‘Z ‘ bend through the horn and the servo adaptor as per the diagram below. Make
sure all the joints are secure; failure will result in the loss of a control surface!!! Use lock tight on the
screw.
Not to scale
Fuselage
Take the fully covered parts for the Fuselage and insert the 8mm (5/16”) dowels provided. Glue in place with
white wood glue or Cyano. Fit the wing to the Fuselage and hold in place with an elastic band so that it is
firmly seated, but able to move for adjustment. With a tape measure check that the Fuselage is square to
the wing as per the diagram. Ensure A1 = A2.
Insert the Tail Plane into its slot and check the measurement B1 = B2. Once satisfied that the Tail Plane is
square, mark with a pencil both top and bottom along the edge of the Fuselage. Remove the Tail Plane from
its slot and carefully cut 1.5mm (1/16”) on the inside of the line to remove the covering film from both the top
and bottom.
Take the Fin and insert into the slot. With a pencil mark along the Fuselage as with the Tail Plane, remove
the Fin and remove the covering from 1.5mm (1/16”) below the line.
!!! Warning. Only cut through the film while undertaking the tasks above, do not cut into the balsa as this will
weaken the Fin and may cause it to fail in flight!!!
Re-insert the Fin and make sure that the cut-out in the base of the Fin lines up with the Tail Plane slot.
Insert the Tail Plane to confirm. One satisfied with the fit, glue the Fin into position using epoxy on the base
where it joins to the Tail skid and Cyano or white wood glue at the junction with the top deck. Ensure that
the Fin is vertical, with the wing seated; also check that the Fin is at 90° by viewing it from the front.
A2
A1
B2
B1
90
o
90
o

17
Glue the Tail Plane into position, apply the glue inside the slot, top and bottom, and with help carefully open
the slot while inserting the Tail Plane and release the Fuselage to clamp back down. Only apply slight
pressure so as not to break the rear of the Fuselage. When inserting the Tail Plane be careful not to get
glue onto the covering. Make sure the Tail Plane is parallel to the wing by viewing from the front as before.
Take the fully covered Fuselage with Fin and Tail Plane fitted and glue the hinges 50% into the Rudder and
Elevator. Glue using a thin Cyano and ensure that it penetrates into the slots both top and bottom. Slot the
hinges into the corresponding slots on the Fin and Tail Plane. Move the control surfaces full travel (min 45°)
to ensure that there is no resistance and repeat the gluing process. Due to the large control surfaces we
would recommend pinning the hinges, this is left to the builder’s discretion.
Fit the Elevator servo (rear servo), Rudder servo (front servo) and 9g Throttle servo (glow version) using the
screws supplied with the servos, if you haven’t already, fit the 6 x 6mm (¼” x ¼”) spruce to the front servo.
Pilot drill the holes first to prevent the ply and spruce splitting.
Make up the two horns (Parts 35), cut a slot in the rudder and elevator to accept them. The elevator horn
sits at in centre of the elevator and the rudder horn sits 3/8” (9mm) from the bottom of the rudder parallel with
the bottom rail.
With a Bradawl make holes for the closed loop system to exit the Fuselage as shown below. Start by making
a hole at 90° to the surface, then increase the angle while twisting the Bradawl to about 5°. Make the holes
in the positions as shown on the diagram. We have found it neater to insert tubes into the holes, and have
used old pen inners (Biro) or excess Bowden outer glued in place with Cyano. Ensure Cyano does not enter
the tube or it will glue the cable fast. The hole for the upper Elevator closed loop cable will be placed
centrally on the rear deck, but needs to be inserted at an angle so that the cable can be run past the Fin
post.

18
Make up the closed loop systems to the Elevator and Rudder as shown below.
Ensure the crimps hold the wire tightly, place a drop of Cyano to make sure the wires cannot move.
Motor Mount
Mount the motor using the recommended motor mount ensuring that it is securely attached to the firewall, do
not use screws, only use lock nuts, bolts and washers suitable for this application.
Electronic Speed Controller (ESC)
On the prototypes we mounted the ESC under the Fuselage between the undercarriage mounts, this
provided constant cooling which is essential to prevent the ESC from cutting out. Carefully drill holes through
the bottom of the Fuselage for the wires to pass into the radio bay. Stick the ESC to the bottom of the
Fuselage using double sided tape or hook and loop strips.
Motor Battery
We would recommend using a Lithium Polymer (Li-Po) battery for this model, use extreme caution when
using Li-Po batteries and always read the manufacturers or suppliers instructions when handling and
charging this type of battery. The battery sits at the front of the Fuselage and can be moved forward or back
to alter the centre of gravity (Explained later). Once the centre of gravity is achieved ensure that the battery
is unable to move during flight or foul the servos.
Receiver and Battery Position
The battery and receiver are to be located between the servo tray and tank or flight battery. For the Electric
version mount as close to the servos as possible to allow maximum space in the battery compartment.
Ensure that both components are isolated from airframe vibration and that they are not able to move when
the model is in flight.

19
Control Throws
We only recommend setting the model up with sport flying throws unless you are an experienced flyer.
Increasing the control rates will make the model extremely responsive!
For test flying and sports flying, set the control throws up as shown below:
Ailerons - 30mm Up and Down measured at the tip
Elevator – 30mm Up and Down measured at the tip
Rudder – 65mm Left and Right measured at the top
These control throws will provide docile flight characteristics, suitable for test flying. Once confident in the
models performance increase the rates. At Evolution we fly our display models with the following settings on
the transmitter high rate settings:
Ailerons - 45mm Up and Down measured at the tip
Elevator – 40mm Up and Down measured at the tip
Rudder – As much as possible!
When you are content with the control setup, use some heat shrink tubing or excess fuel tube over the clevis
to ensure that it cannot open.
Flap Mix
If your transmitter has the ability to mix in flaps, we have used this function to make the model loop and pitch
much tighter. Flap is when the ailerons move in the same direction (up or down) together.
To set this mix up increase the Elevator movement until the model begins to screw out of loops with
movement, once this begins to happen back off the movement slightly. Repeat this with the flaps, with full
up Elevator and full flap the model should be able to perform a tight loop without screwing out. We highly
recommend this mix as it makes the model more stable in loops and at slower speeds.
The flaps should be set as below:
Elevator up – Flaps (Ailerons) Down
Elevator Down – Flaps (Ailerons) Up
(Flap mix shown with high rates switched on)
Centre of Gravity (CoG)
Once you have completed the model, and all components, including receiver and batter have been installed
check the balance of the model with the fuel tank empty. With a helper place a Finger under the wing to see
where the CoG sits. The Fusion has a huge CoG range, but we recommend starting about 25mm (1”)
behind the spar. When you and your helper lift the model it should balance on this point, if it does not then
Table of contents
Other Evolution Toy manuals
Popular Toy manuals by other brands

Eduard
Eduard 49 1198 manual
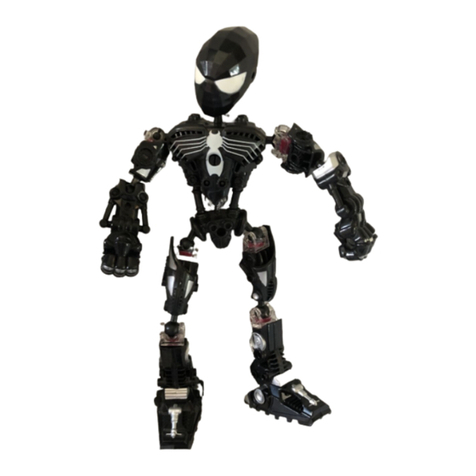
Mega Bloks
Mega Bloks MARVEL Super Tech Heroes THE AMAZING SPIDER-MAN... manual
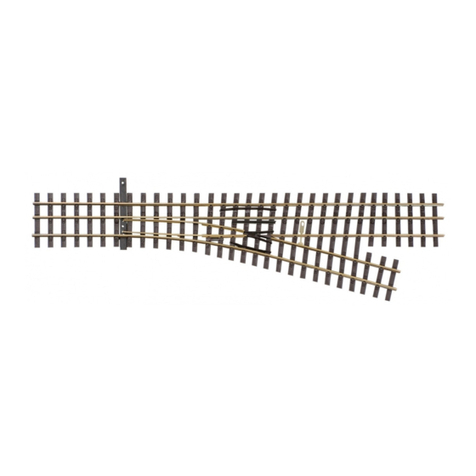
TILLIG BAHN
TILLIG BAHN 85191 quick start guide
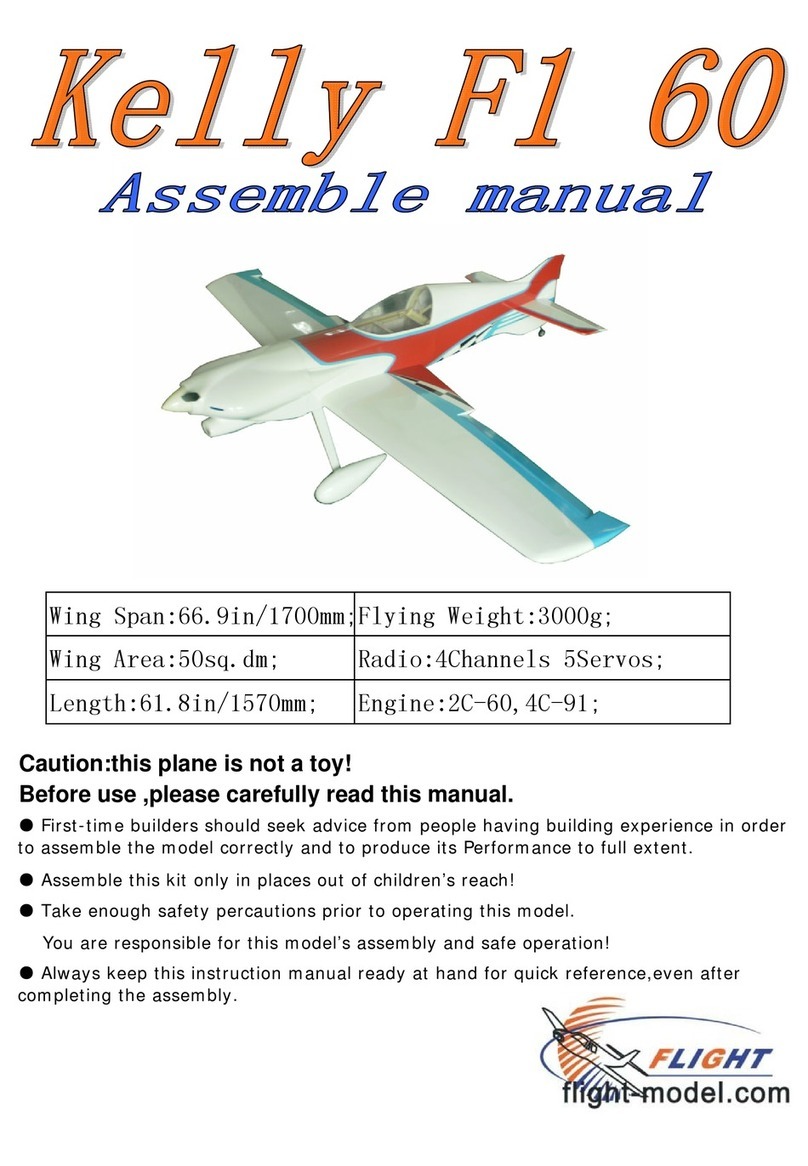
Flight Model
Flight Model F131 Kelly F1 60 Assemble manual

Thames & Kosmos
Thames & Kosmos 659240 Experiment manual

TP Toys
TP Toys TP614 Instructions for assembly, maintenance and safe use