Festo PDAD Series Installation and operating instructions

100152
Application note
Energy management function at
adsorption dryer PDAD
Application note for use of the energy management function at
adsorption dryer PDAD. Explanation, use and layout of purge air
regulation for reducing air consumption.
PDAD-…-…

Title ...................................................................................Energy management function at adsorption dryer PDAD
Version.............................................................................................................................................................. 1.10
Document number ....................................................................................................................................... 100152
Original ................................................................................................................................................................ de
Author ..............................................................................................................................................................Festo
Last saved on ........................................................................................................................... 20. September 2017
Copyright notice
This documentation is the intellectual property of Festo AG & Co. KG, which also holds exclusive copyrights. Any
modification of the content, duplication or reprinting of this documentation, as well as distribution to third parties,
are only permissible with the express consent of Festo AG & Co. KG.
Festo AG & Co KG reserves the right to make modifications to this document in whole or in part. All brand names
and product names are trademarks or registered trademarks of their respective owners.
Legal notice
Hardware, software, operating systems and drivers may only be used for the applications described and only in
conjunction with components recommended by Festo AG & Co. KG.
Festo AG & Co. KG does not accept any liability for damages arising from the use of any incorrect or incomplete
information contained in this documentation or any information missing therefrom.
Defects resulting from improper handling of devices and modules are excluded from the warranty.
The data and information specified in this document should not be used for the implementation of safety-relevant
functions for the protection of personnel and machinery.
No liability is accepted for claims for damages arising from failure or malfunctioning. Otherwise, the stipulations
concerning liability set forth in the terms and conditions of delivery, payment and use of software of Festo AG &
Co. KG, which can be found at www.festo.com or can be supplied upon request, shall apply.
None of data contained in this document represent guaranteed characteristics in the legal sense, particularly with
regard to functionality, condition or quality,.
The information in this document serves only as basic information for the implementation of a specific,
hypothetical application and is in no way intended as a substitute for the operating instructions of the respective
manufacturers or design and testing of the respective application by the user.
The respective operating instructions for Festo products can be found at www.festo.com/sp.
Users of this document (function and application) must themselves verify that all of the functions described herein
also work correctly within the application. Even after examining this document and using the specifications
contained herein, users are nevertheless solely responsible for their own applications.
(Festo AG & CO. KG, D-73726 Esslingen, Germany, 2017)
Internet: http://www.festo.com
E-mail: service_international@festo.com

Table of contents
Application Note –Energy management function at adsorption dryer PDAD –1.10 Page 3 of 17
Table of contents
1Utilised components, documentation......................................................................................................... 4
1.1 Utilised components.................................................................................................................................... 4
1.2 Documentation............................................................................................................................................ 4
2 Description and purpose of the application note ......................................................................................... 5
2.1 Introduction to the subject matter............................................................................................................... 5
2.2 PDAD functions............................................................................................................................................ 6
2.3 Reasonably foreseeable misuse.................................................................................................................. 7
2.4 Environment used in.................................................................................................................................... 7
2.5 User groups................................................................................................................................................. 7
2Layout of purge air regulation for reducing air consumption..................................................................... 8
3.1 Nature of the task........................................................................................................................................ 8
2.2 Use of a manual switch for purge regulation ............................................................................................... 9
2.3 User of a dew point transmitter and a process regulator for purge regulation .......................................... 10
2.4 Use of a simple pressure switch for purge regulation ............................................................................... 11
2.5 Use of a pressure sensor for purge regulation .......................................................................................... 13
2.6 Establishing a connection between switching device and the energy management contact at the PDAD . 14
3Safety........................................................................................................................................................ 17

Utilised components, documentation
Application Note –Energy management function at adsorption dryer PDAD –1.10 Page 4 of 17
1Utilised components, documentation
1.1 Utilised components
Type/name
Software/firmware version
Date of manufacture
PDAD-…-…
All
All
Manual electric switch
--
--
dew point sensor/transmitter
--
--
Pressure switch
--
--
Pressure sensor
--
--
Table 1: Utilised components
1.2 Documentation
This application note is intended to supplement existing documents to include the energy management function.
Catalogue documentation
https://www.festo.com/cat/en-gb_gb/data/doc_engb/PDF/EN/PDAD_EN.PDF
Operating instructions:
https://www.festo.com/net/en-gb_gb/SupportPortal/Downloads/385765/464376/PDAD_2017-
01g_8068816g1.pdf
Animation:
https://www.festo.com/net/en-gb_gb/SupportPortal/Flash/378325/376353/en/index.htm
--> Further documents and publications regarding this subject can be found at the Support Portal operated by
Festo AG & Co. KG.

Description and purpose of the application note
Application Note –Energy management function at adsorption dryer PDAD –1.10 Page 5 of 17
2 Description and purpose of the application note
2.1 Introduction to the subject matter
The adsorption dryer PDAD is used to reduce the pressure dew point to -70° C for corresponding use, e.g. handling
powders, in climatised rooms and in the pharmaceuticals and chemicals industries.
Brief explanation:
Adsorption (from the Latin adsorpio, from adsorbere (“draw in”) is the designation for the enrichment of
substances from gases or liquids at the surface of a solid, generally at the interface (matter) between two phases.
Adsorption dryers draw the moisture out of the compressed air through the use of a drying agent. While
adsorption takes place in the first container, regeneration takes place in the second container at the same time.
The cycle times are stored in the electronic controller. Pressure dew points within a range of -20 to -70 °C are
achieved with standard products. Various hot and cold processes are available for regeneration.
The cold regeneration process is used by the adsorption dryer PDAD:
For the purpose of regeneration, a portion of the already dried compressed air is caused to flow through the
previously used container cartridge and is then vented to the atmosphere.
+Simple technology
+Minimal investment costs
- Compressed air consumption
-High operating costs

Description and purpose of the application note
Application note –Energy management function at adsorption dryer PDAD –1.10 Page 6 of 17
2.2 PDAD functions
Due to requirements for minimal power consumption, the PDAD is equipped with an energy management function.
This makes it possible to set up purge air regulation with corresponding interconnection in order to reduce air
consumption. The PDAD also includes an RJ45 interface for connecting a PC directly via a network cable (Ethernet).
With the help of software matched to the serial number, the dryer’s setting can be accessed and changed, and
errors can be read out if applicable.
These functions are integrated, but they’re not described in the operating instructions. The software is neither
provided by Festo nor is it available, because the device can be damaged in the event of incorrect settings.
The PDAD is also equipped with an alarm connection which is described in the operating instructions. A visual or
acoustic remote alarm system can be connected outside of the dryer via this connection (type C DIN plug). In the
event of a malfunction or if service is required, the alarm relay is switched (NO contact) and red LEDs
simultaneously indicate the error at the display panel. The alarm relay is reset when the error has been eliminated,
but only after the current switching cycle has been completed or the control device has been reset after a cartridge
change.
Figure 0: PDAD functions –overview of connections at the controller
Connection for energy
management function
Controller serial number
Connection for alarm function
Service interface connection

Description and purpose of the application note
Application note –Energy management function at adsorption dryer PDAD –1.10 Page 7 of 17
2.3 Reasonably foreseeable misuse
This application note describes the layout and the benefits of the energy management function. It can be used to
shut down the purge air function when little or no air is required.
It’s very important to understand that the purge function can only be shut down at times when little or no air is
required. If this function is shut down at any other time, the drying agent cartridges may be permanently damaged
thus resulting in the loss of drying performance, and possibly a mechanical defect as well. The cartridges may
never be entirely saturated!
In any case, checking must be conducted for continuously flawless functioning because the dryer might
otherwise fail, or errors might occur within the process or the application!
The function of the RJ45 interface for direct connection of a PC via a network cable (Ethernet) is not described
because the software is not supplied with the product, and there are too many hazards associated with incorrectly
configured device parameters. The function and use of the alarm connection are described in the official operating
instructions.
2.4 Environment used in
•Industrial environment
•Applications with minimal or sporadic air consumption with correspondingly specified
pressure dew points, e.g. in laboratories
2.5 User groups
•Specialists in the field of pneumatics
•Specialists in field of electrical engineering
•Sales engineers at Festo AG & Co. KG

Layout of purge air regulation for reducing air consumption
Application Note –Energy management function at adsorption dryer PDAD –1.10 Page 8 of 17
2Layout of purge air regulation for reducing air consumption
3.1 Nature of the task
Regenerative dryers have to eject a portion of the process air in order to remove the moisture which accumulates
inside them. During times when only small amounts of air are required, this loss is unnecessary and thus
undesirable. In many cases the compressor runs nearly uninterruptedly in order to compensate for the dryer’s
purge air loss.
Example: The compressor for central compressed air preparation is started up again and again due to the purge
air function and the associated pressure drop, although no air consumption is required for the application.
Compressor start-up results in noise –in some cases disagreeably at night. The temperature in the room might
also rise, so that applications with low pressure dew points may be influenced.
The adsorption dryer PDAD is equipped with an energy management function by means of which the purge
function can be shut down during times when little or no air is required. The dryer’s regulator is equipped with a
set of easily accessible contacts with which the solenoid valves (which regulate the dryer’s purge function) can be
shut down, thus resulting in zero air loss at via dryer.
In order to makes use of this function, the operator must provide a switching system with acceptable logic which
informs the dryer when little or no air is required. Several examples of frequently used switching systems are
provided in the following pages (with varying complexity).

Layout of purge air regulation for reducing air consumption
Application note –Energy management function at adsorption dryer PDAD –1.10 Page 9 of 17
2.2 Use of a manual switch for purge regulation
This is the simplest setup. When air is not used downstream from the dryer, the purge function is shut down by
means of a manual switch. This layout is frequently used in systems which act upon the point of consumption
(point-of-use or POU systems). For example, if the dryer is only used to supply suitably dried air to a certain
machine or application, the dryer is only needed when the machine is running and can be shut down either
manually or possibly via additional contacts in the machine’s on/off switch.
It’s very important to understand that the purge function can only be shut down at times when little or no air is
required. If this function is shut down at any other time, the drying agent cartridges may be permanently damaged
thus resulting in the loss of drying performance, and possibly a mechanical defect as well. The cartridges may
never be entirely saturated!
The following drawing (figure 2) shows how the above mentioned components might be connected for regulation
of a dryer’s purge function. Please note that specific details regarding the components are manufacturer-
independent –the manufacturer’s specifications must be complied with in any case.
Figure 2: Use of a manual switch for purge air regulation
Dryer
regulator
Pin 2
Pin 1 (reads out +5 V DC signal)
Manual switch
(installed in the field)
Signal output
Return signal
* Current-free when closed –open to deactivate the purge function
Current-free
when closed *

Layout of purge air regulation for reducing air consumption
Application note –Energy management function at adsorption dryer PDAD –1.10 Page 10 of 17
2.3 User of a dew point transmitter and a process regulator for purge regulation
The best alternative for purge regulation when the degree of dryness (pressure dew point) of the air from the
dryer is critical. When the air is adequately dry, the purge function can be shut down until moisture in the air
increases once again. When the purge function is shut down, it must be assured that the drying agent beds don’t
become too wet before purge function is restarted. When the purge function is switched back on again, the air’s
pressure dew point may continue to climb a bit before it drops off again. This must be taken into consideration in
order to assure that the flow of air remains adequately dry.
It’s very important to understand that the purge function can only be shut down at times when little or no air is
required. If this function is shut down at any other time, the drying agent cartridges may be permanently damaged
thus resulting in the loss of drying performance, and possibly a mechanical defect as well. The cartridges may
never be entirely saturated!
The following drawing shows how the above mentioned components might be connected for regulation of a
dryer’s purge function. Please note that specific details regarding the components are manufacturer-independent
–the manufacturer’s specifications must be complied with in any case.
Figure 6: Use of a dew point sensor and a process regulator for purge regulation (this setup is only an example and the configuration
can be changed depending on the application)
Dryer
regulator
Pin 2
Pin 1 (reads out
+5 V DC signal)
Signal output
Return signal
* Current-free when closed –open to deactivate the purge function
DC supply power
Electronic
pressure switch
Dew point transmitter
Relay
Signal output
COM
Return signal

Layout of purge air regulation for reducing air consumption
Application note –Energy management function at adsorption dryer PDAD –1.10 Page 11 of 17
2.4 Use of a simple pressure switch for purge regulation
Many compressors are furnished with pressure switches which include additional contacts, by means of which the
dryer’s purge function can be shut down when the compressor is in the discharged state. Unfortunately, many of
these switches have considerable dead zones or a large hysteresis (difference or reset point between the charge
(on) and discharge (off) settings, which in most cases cannot be changed). The amount of air which can flow
through the dryer while the compressor is being discharged must be taken into consideration, because it may be
considerable (in particular if the hysteresis is large or the receiver is very moist.
A separate pressure switch is often a better alternative, because the user can adjust it independently of the
compressor’s pressure switch. The following applies when selecting a separate pressure switch: the smaller the
hysteresis the better. If a separate pressure switch is used, the dryer is wired to the contacts at the pressure switch
which are closed in the absence of current. When the switch is activated (figure 3: e.g. at an overpressure of
6.55 bar or 95 psi), the purge function is shut down until the pressure switch is once again released (in this
example at an overpressure of 6.2 bar or 90 psi). The point at which the switch is released can be adjusted in
accordance with the system.
If it’s determined that the dew point drops to an unacceptable level, the point at which the switch is released must
be increased. Please note that many pressure switches have a fixed hysteresis value, in which case the activation
and deactivation points change in correspondence to each other.
It’s very important to understand that the purge function can only be shut down at times when little or no air is
required. If this function is shut down at any other time, the drying agent cartridges may be permanently damaged
thus resulting in the loss of drying performance, and possibly a mechanical defect as well. The cartridges may
never be entirely saturated! Fundamentally, the solution with a simple pressure switch is critical with regard to
constant dew point reduction.
Figure 4 on page 11 shows how the above mentioned components might be connected for regulation of a dryer’s
purge function. Please note that specific details regarding the components are manufacturer-independent –the
manufacturer’s specifications must be complied with in any case.
Figure 3: Adjustment of the simple pressure switch or pressure sensor
Purge function off (switch activated)
Purge function off (switch activated)
Purge function on (switch deactivated)
Purge function on
Adjust depending on system
(pressure switch deactivation point)
System pressure (psig)

Layout of purge air regulation for reducing air consumption
Application note –Energy management function at adsorption dryer PDAD –1.10 Page 12 of 17
Figure 4: Use of a simple pressure switch for purge regulation
Dryer
regulator
Pin 1 (reads out +5 V DC signal)
Pressure switch
(installed in the field)
Signal output
Return signal
* Current-free when closed –open to deactivate the purge function
Current-
free
when
closed *
Current-
free
when
open
Pin 2

Layout of purge air regulation for reducing air consumption
Application note –Energy management function at adsorption dryer PDAD –1.10 Page 13 of 17
2.5 Use of a pressure sensor for purge regulation
If a pressure sensor is used, it’s best to use a programmable variant. In the final analysis, this type of pressure
sensor is a pressure transmitter and a process regulator in a single component. Although a programmable
pressure sensor is a bit more expensive than a simple mechanical pressure switch, it can be much more
favourably configured. Hysteresis can typically be reduced or eliminated, which permits immediate reaction to
changes in system pressure which determine air flow.
If a pressure sensor is used, the dryer is wired to the contacts of a switching relay which are closed in the
absence of current. When the pressure sensor is activated (figure 3, page 10: e.g. at an overpressure of 6.55 bar
or 95 psi), the purge function is shut down via the relay contact until the pressure sensor’s output drops out
again at the selected pressure value (in this example at an overpressure of 6.2 bar or 90 psi). The point at which
the switch is released can be adjusted in accordance with the system.
It’s very important to understand that the purge function can only be shut down at times when little or no air is
required. If this function is shut down at any other time, the drying agent cartridges may be permanently
damaged thus resulting in the loss of drying performance, and possibly a mechanical defect as well. The
cartridges may never be entirely saturated! Fundamentally, the solution with a pressure sensor is critical with
regard to constant dew point reduction.
The following drawing shows how the above mentioned components might be connected for regulation of a
dryer’s purge function. Please note that specific details regarding the components are manufacturer-
independent –the manufacturer’s specifications must be complied with in any case.
Figure 6: Use of a pressure sensor for purge regulation (this setup is only an example and the configuration can be changed depending
on the application)
Dryer
regulator
Pin 2
Pin 1 (reads out
+5 V DC signal)
Signal output
Return signal
* Current-free when closed –open to deactivate the purge function
DC supply power
Electronic
pressure switch
Relay
Signal out
COM

Layout of purge air regulation for reducing air consumption
Application note –Energy management function at adsorption dryer PDAD –1.10 Page 14 of 17
2.6 Establishing a connection between switching device and the energy management
contact at the PDAD
The adsorption dryer is shipped with activated purge air function as a default setting, i.e. purge air is also active
at times when little or no purge air is required. There’s a plug inserted into the socket for the energy management
function (EM) to this end with pre-set jumper (see figures 7 and 8).
This jumper establishes a permanent connection between terminals 1 and 2 at the DIN plug which corresponds to
an activated purge air function.
Figure 7: PDAD default status –DIN plug with pre-set jumper connected to EM contact
Figure 8: PDAD default status –jumper between terminals 1 and 2 in the insert of the DIN plug

Layout of purge air regulation for reducing air consumption
Application note –Energy management function at adsorption dryer PDAD –1.10 Page 15 of 17
The jumper must be removed in order to use the EM function. Terminals 1 and 2 at the EM socket are then
connected to the NC contact of the corresponding switching device (manual switch, directly to a pressure switch
or a relay). When the manual switch, the pressure switch or the relay contact is opened, purge air is deactivated.
The dryer should be removed from service before conversion or integration. In order to remove the device from
service, disconnect it from supply power and compressed air supply, and fully depressurise it.
Connection procedure:
1. Remove the DIN plug from the EM contact.
2. Insert a small screwdriver into the small depression at the edge of the insert and press the insert out of
the external sleeve of the DIN plug (see figure 9).
Figure 9: Removing the insert from the DIN plug
3. Remove the jumper between terminals 1 and 2 (see figure 10).
Figure 10: Removing the jumper from the DIN plug

Layout of purge air regulation for reducing air consumption
Application note –Energy management function at adsorption dryer PDAD –1.10 Page 16 of 17
4. Connect external switching logic (NC contact of the manual switch, the pressure switch or on the relay) to
terminals 1 and 2 in the plug insert of the DIN plug. Make sure that the wires and cables are correctly
stripped and that good insulation is assured through the cable gland!
5. Measure continuity between the two wires if possible with a measuring instrument, in order to ensure
that the switch is current-free in the closed position. Check for correct switching function if possible as
well. A 5 V DC signal is read out from terminal 1 during operation which is fed to terminal 2 via the NC
contact, by means of the EM function can be activated or deactivated.
6. Carefully pull the cable back through the sleeve until the insert snaps back into the housing of the DIN
plug. Observe the direction in which the cable throughfeed must point.
7. Insert the DIN plug back into the energy management connection at the dryer and screw it tight, making
sure that the sealing ring is correctly seated. The protective conductor terminal is somewhat wider than
terminals 1 and 2. Make sure that the socket plug is correctly aligned.
The selected cable to the switching logic …
•must have at least 2 conductors. Additional conductors may be useful in the event that a conductor is
broken. Conductors can be changed without having to lay a new cable.
•may not have a wire cross-section of any greater than 1.5 sq. mm (recommended) in order to freely fit
into the DIN plug insert.
• should have an outside diameter of no more than 6 mm. Larger diameters don’t fit well into the cable
gland of the DIN plug for the energy management function.
•should demonstrate insulation characteristics which are suitable for the conditions of use.
8. Restart the dryer in accordance with the operating instructions.
9. Test the energy management function (switch manually or by adjusting the switching points) without yet
discharging compressed air! Recommendation: shut-off device (2/2 function) downstream from the PDAD
10. If reliable functioning is assured, slowly open the shut-off device and release compressed air to the
application.
11. Renewed testing and long-term observation of the EM function, as well as adjustment of the switching
points during normal operation. Pressure, as well as the pressure dew point, should not drop to below
the minimum requirement!
Supplementary notes for the operating instructions:
The use of an ideal air reservoir downstream from the PDAD smooths pulsation caused by discharging air.
The pressure dew point to be achieved is based on the flowing quantity of air. Consequently, a higher pressure
dew point is achieved with a lower flow velocity. On the other hand, a higher or excessively high flow rate may
result in a reduced pressure dew point. For this reason, the table values listed in the catalogue should always be
complied with. The dischargeable flow rate is listed there depending on the size of the PDAD, operating pressure,
the available amount of air and the required pressure dew point.

Safety
Application Note –Energy management function at adsorption dryer PDAD –1.10 Page 17 of 17
3Safety
Festo expressly excludes any and all liability or responsibility for damages and/or injuries which result from
disregarding these operating instructions.
The device may only be used for its intended purpose. The cold regenerative adsorption dryer may only to be used
for the intended purpose of drying pressurised air under the conditions described in section 11 of these operating
instructions.
Any other use of the device is deemed use for other than the intended purpose. Festo is not liable for damages
which result from use for other than the intended purpose.
The following safety regulations must be adhered to strictly:
•These operating instructions must be kept at the product’s installation site as a print-out or copy.
•Repair work conducted on the device may only be carried out by personnel authorised by Festo.
•Operating, repair and maintenance personnel must be familiar the following information:
- Accident prevention regulations
- Safety information (general and device-specific)
- Device safety equipment
- Measures to be implemented in case of emergency
•It’s the responsibility of the installation technician to ensure that the cables to and from the dryer are
suitable for the task, correspond to all applicable laws and have been subjected to visual inspections and
testing before commissioning. All cables must be secured in an appropriate manner.
•The device must be removed from service before conducting any maintenance or repair work. Operators
and other personnel are exposed to hazards if work is carried out on a running device. In order to remove
the device from service, disconnect it from supply power and compressed air supply, and fully
depressurise it.
•Only trained specialists who are familiar the electrical requirements of the device as described in these
operating instructions, and the respective safety rules and regulations, are permitted to conduct work on
the device’s electrical components and power supply.
•Use suitable, correctly dimensioned tools that are in good condition to carry out any work on the device.
•Use accessories and spare parts from the manufacturer only. There is no guarantee that non-original
spare parts are designed and manufactured to correspond to the safety and operating requirements of
the device. Festo assumes no liability for device faults which result from the use of unapproved spare
parts.
•Use suitable, safe work platforms or other secure work access options to carry out installation work above
head height.
•Do not make any design changes to the product. Changes and modifications may only be carried out by
Festo.
•All faults or defects which might impair safety must be eliminated before using the device.
•Utilised objects and materials must be correctly disposed of in accordance with local laws and
regulations. This applies in particular to the drying agent cartridges.
Other manuals for PDAD Series
1
Table of contents
Other Festo Dryer manuals
Popular Dryer manuals by other brands

Miele
Miele PDR 514 Operating and installation instructions
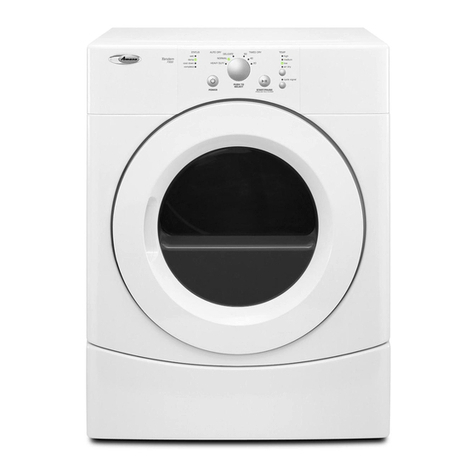
Whirlpool
Whirlpool W10240579C installation instructions
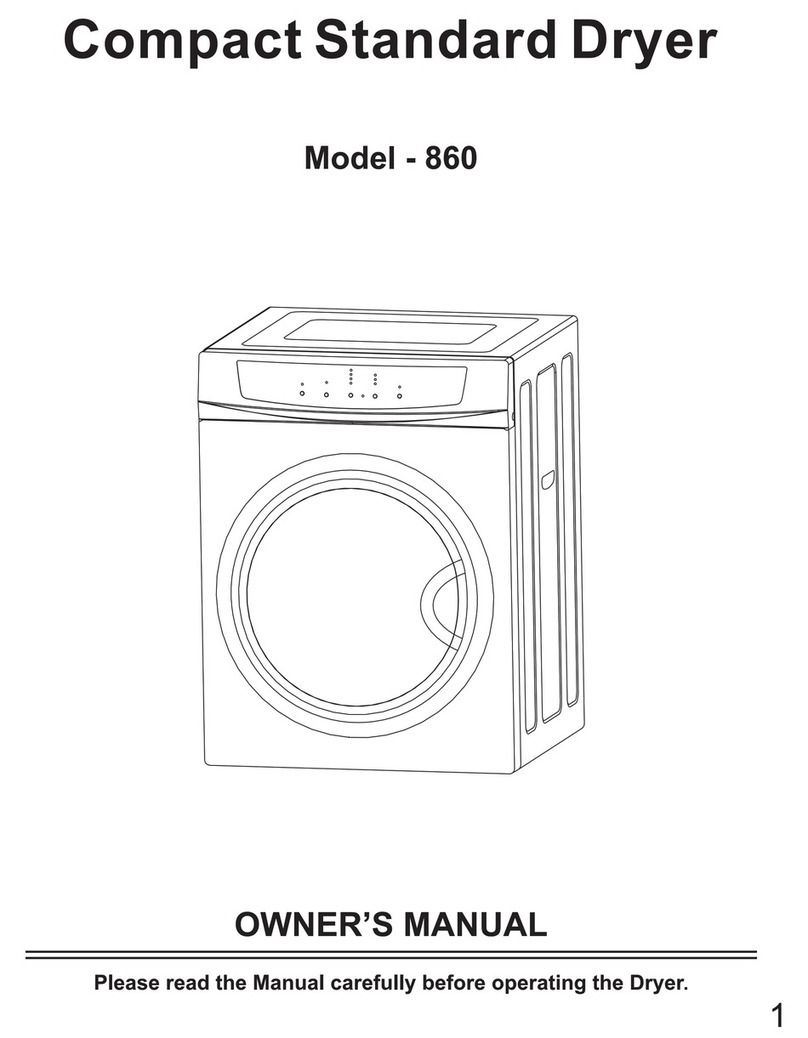
Consolidated Brands
Consolidated Brands 860 owner's manual
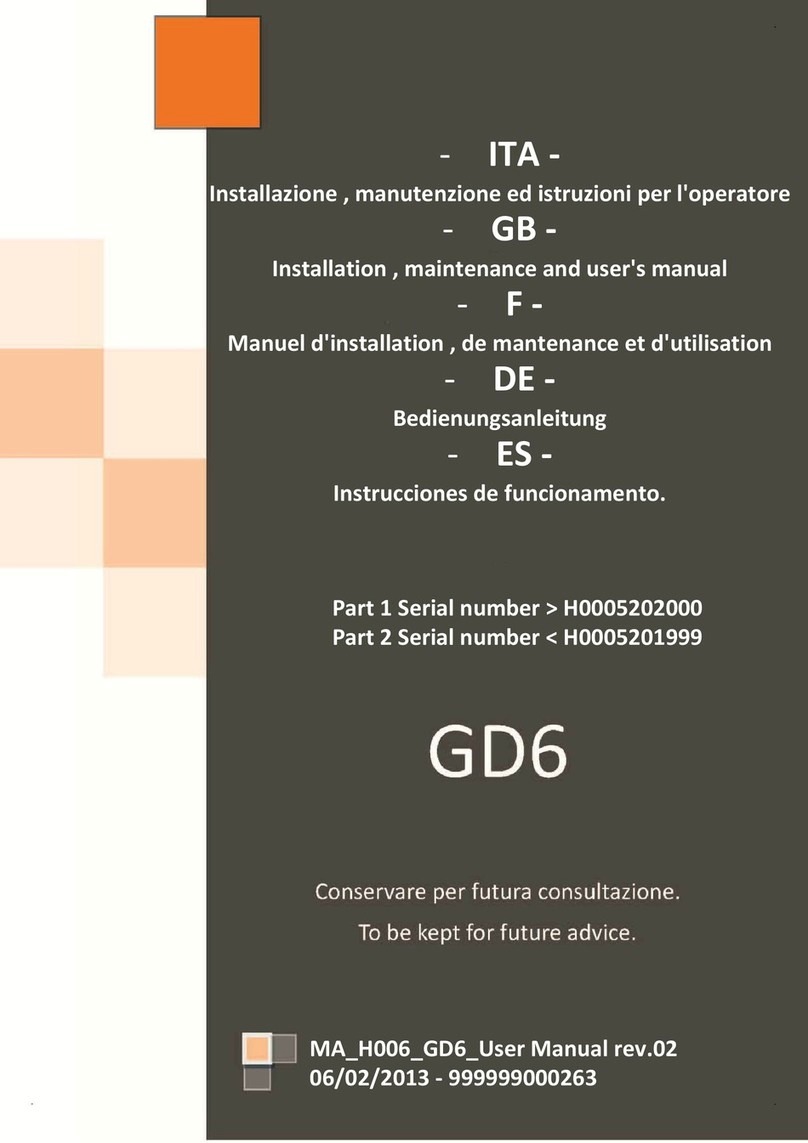
grandimpianti
grandimpianti DG6 Installation, maintenance and user manual
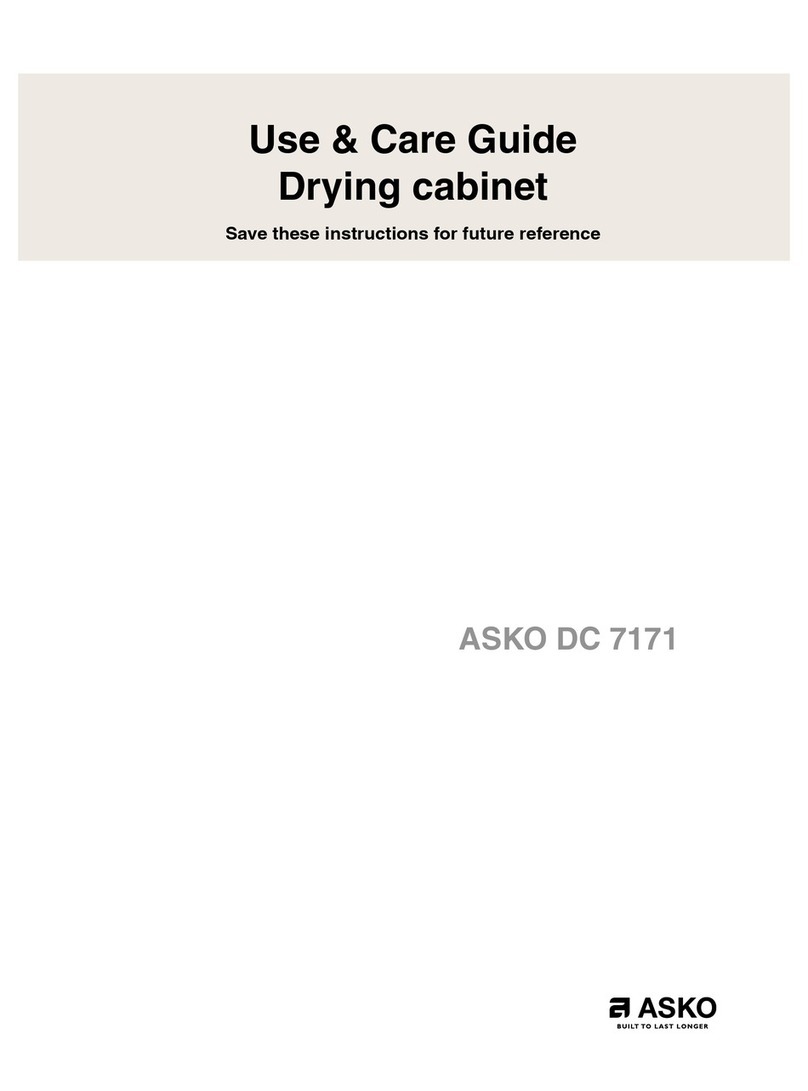
Asko
Asko DC 7171 Use and care guide
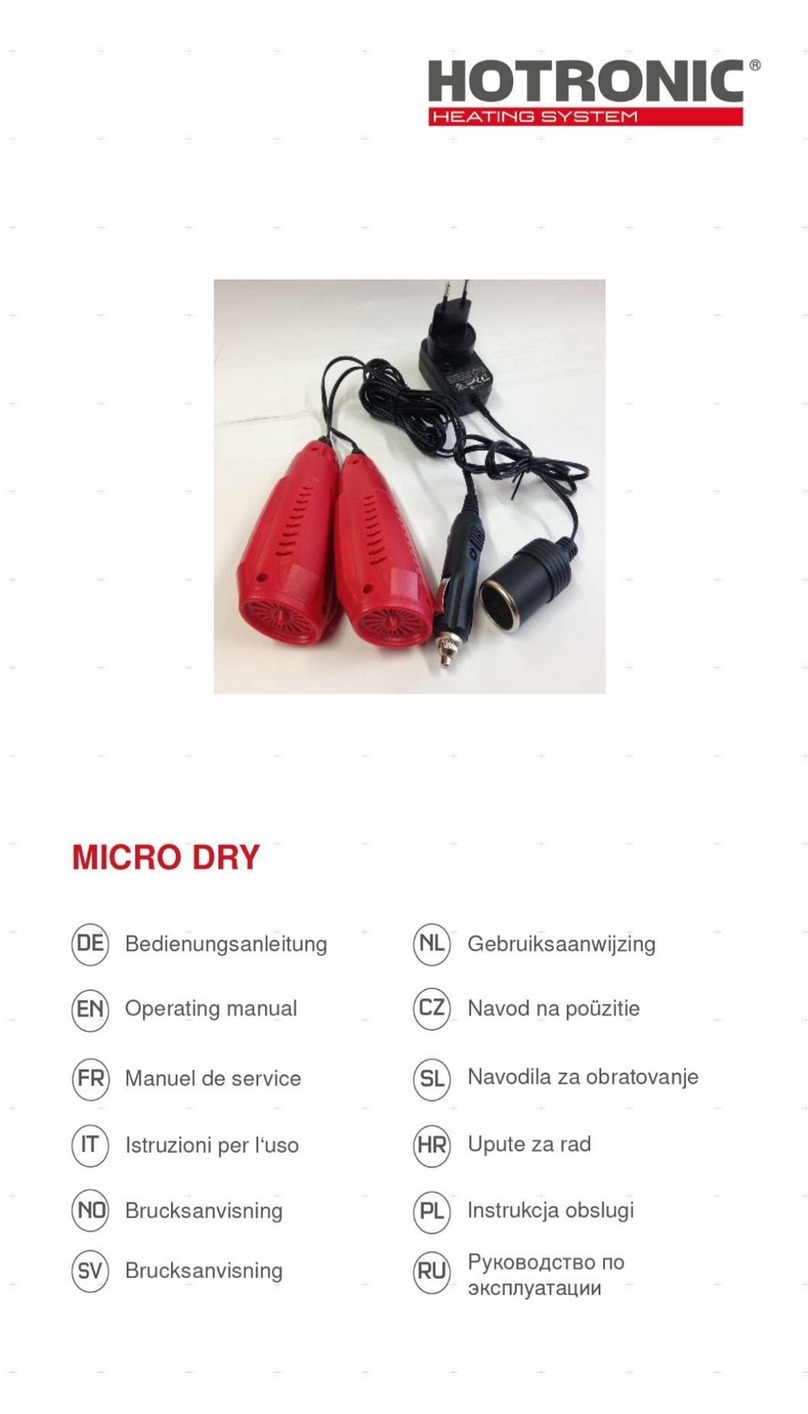
Hotronic
Hotronic Micro Dry operating manual
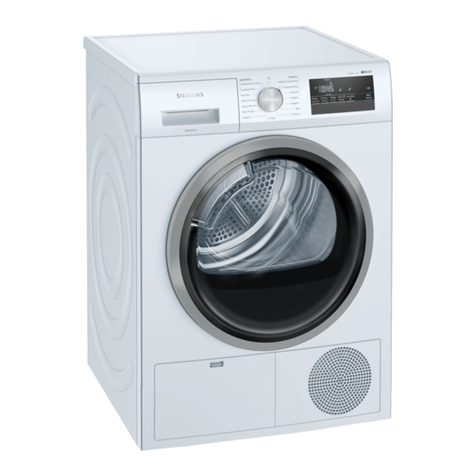
Siemens
Siemens WT46N203IN Installation and operating instructions

Kenmore
Kenmore 7965 - 600 5.9 cu. Ft. Capacity Gas Flatback... installation instructions

Beko
Beko B5T60230M user manual

AEG Electrolux
AEG Electrolux SV4028 user manual

Asko
Asko T411HSW installation instructions
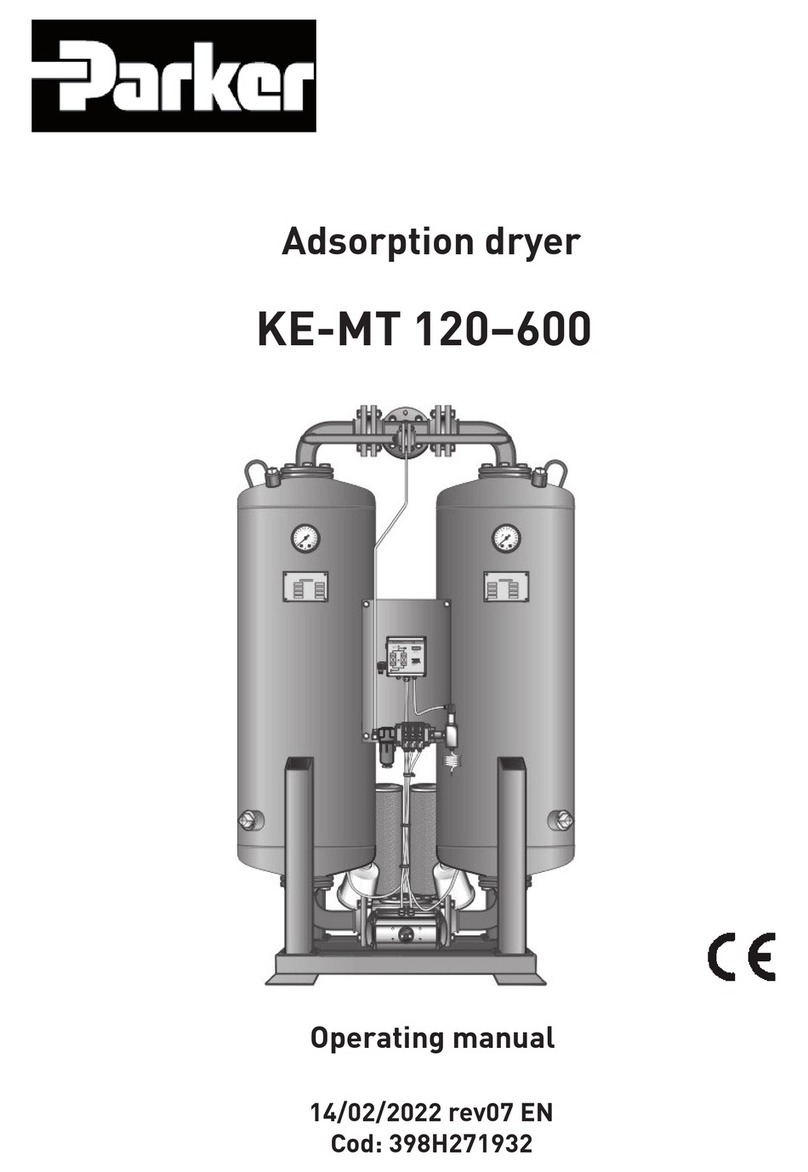
Parker
Parker KE-MT Series operating manual