FineTek JTR Series Technical manual

2
Contents
1.Operation manual use ...................................................................................................4
2.Product warranty ...........................................................................................................5
2.1 New product warranty................................................................................................................. 5
2.2 Repair warranty......................................................................................................................... 6
2.3 Service Network........................................................................................................................... 7
3. Product...........................................................................................................................8
3.1 Configuration................................................................................................................................ 8
3.1.1 Model Label............................................................................................................................... 8
3.1.2 Product Contents...................................................................................................................... 8
3.2 Safety Inspection......................................................................................................................... 8
4. Principles .......................................................................................................................9
4.1 Product Principles..................................................................................................................... 9
4.2 Bottom Tracking Probe Technology....................................................................................... 9
4.2.1 Bottom Tracking Probe Technology....................................................................................... 9
4.2.2 Function Principle –Dual-Level Interface Measurement................................................. 10
5. Features........................................................................................................................ 11
6. Specification................................................................................................................12
7. Installation....................................................................................................................13
7.1 General Instructions............................................................................................................... 13
7.1.1 Lock Instrument...................................................................................................................... 13
7.1.2 Moisture Proof Instructions................................................................................................... 13
7.1.3 Operating Conditions............................................................................................................. 13
7.2 Installation Instruments.......................................................................................................... 14
7.2.1 Installation Site ....................................................................................................................... 14
7.2.2 Feeding Tank Installation Precautions................................................................................ 16
7.2.3 Measurement Scope.............................................................................................................. 16
8 Wiring Instruction.........................................................................................................17
8.1 Preparations............................................................................................................................... 17
8.1.1 Please Note the Following Safety Precautions before Use:............................................ 17
8.1.2 Connecting Cable................................................................................................................... 17
8.1.3 Power Supply.......................................................................................................................... 18
8.2 Wiring Instructions:.................................................................................................................... 18
8.2.1 Connection Skills.................................................................................................................... 18
8.2.2 Wiring Steps............................................................................................................................ 18
8.3 Startup Instructions.................................................................................................................... 19

3
9. Display Module Adjustment and Setting ....................................................................20
9.1 Operation Steps:........................................................................................................................ 20
9.1.1 Adjustment............................................................................................................................... 21
9.2 Menus.......................................................................................................................................... 21
9.2.1 Measurement Settings Menu ............................................................................................... 22
9.2.2 Display settings Menu ........................................................................................................... 24
9.2.3 Diagnostics.............................................................................................................................. 26
9.2.4 Additional Settings Menu ...................................................................................................... 27
9.2.5 Machine Information Menu................................................................................................... 28

4
1. Operation manual use
Thank you for purchasing this FineTek product. This operation manual describes the product
features, operating principle, operation and maintenance methods, as well as precautionary
measures that should be taken during the installation, operation or maintenance of this product.
This manual is designed to prevent dangerous situations that can result in damage to the
product or injury to an installer or operator.
Please read this operation manual completely and carefully before installing the product.
Please contact FineTek if this operation manual does not answer your questions.
The content of this operation manual may be updated from time to time. Updates are
Maintained on the FineTek website www.fine-tek.com for your easy access.
Do not disassemble or attempt to repair the product as this will void the product
warranty.Please return the product to FineTek for repair and calibration if required.
This manual may utilize warning symbols. An explanation of these symbols is as follows:
Danger→this symbol indicates an incorrect operation will result in major accidents and
death.
Note→this symbol an incorrect operation will result in injury to personnel and some
damage to the product.
Electric shock→this symbol warns of a possible electric shock hazard.
Fire→this symbol warns of a possible fire hazard.
Prohibited→this symbol indicates the action is prohibited.

5
2. Product warranty
2.1 New product warranty
Each FineTek Guided Wave Radar Level Sensor is backed by 1-year limited warranty.
Should you experience a problem with one of our products deemed by our factory to be a
product failure covered by our warranty, for a period of 1-year from the delivery date we
will repair the unit at our factory or provide you with a replacement unit or sub-assembly
at our discretion. A return authorization number must be obtained from FineTek before
returning any unit.
If the Guided Wave Radar Level Sensor product failed to operate out-of-the-box, and this
failure was not due to transportation, handling or incorrect Installation, then you can
request a replacement unit within 7 days from the delivery date.
When returning a product to the factory, return the entire device and do not disassemble
the unit as previously mentioned. In addition, wherever possible please returning the
device please ensure it is packed to avoid damage during transportation.
When returning a product to the factory, return the entire device and do not disassemble
the unit as previously mentioned. In addition, wherever possible please returning the
device please ensure it is packed to avoid damage during transportation.
The product is not warranted in the following situations or conditions, therefore charges
will result for repair of product:
The product is beyond its warranty term.
The defect or damage to the product is caused by the incorrect operation or by not
following the installation and operation instructions contained within the operation
manual.
The product damage is a result of force majeure factors, including but not limited to
natural disasters, floods, fires, earthquakes, lightning, severe weather conditions such
as hurricanes, typhoons, tornadoes etc., human error such as use of improper voltage,
high-humidity, water leakage, stains, corrosion, loss, improper storage etc. and other
abnormal factors.
The damage is caused by installation, addition, expansion, modification and repair of
parts not authorized specifically or certified by FineTek.
If the data label information on the product is incorrect or unclear so as to not be able
to read or confirm the product serial number.

6
2.2 Repair warranty
Repaired product is warranted for 6 months from the delivery date. The warranty is
limited to the part(s) replaced or repaired during the repair. If the repaired or replaced part
is defective within this term the same part(s) will be repaired or replaced free of charge.

7
2.3 Service Network
Company
Address
Telephon
Fax
Taipei Headquarters
(Taiwan)
No.16, Tzuchiang St., Tucheng
Industrial Park, New Taipei City
23678
+886 2 2269 6789
+886 2 2268 6682
Taichung
Sales office
(Taiwan)
+886 4 2465 2820
+886 4 2463 9926
Kaohsiung
Sales office
(Taiwan)
+886 7 333 6968
+886 7 536 8758
Fine automation
Co., Ltd.
(China)
No. 451, Duhui Road,
Zhuanqiao Township, Minhang
District, Shanghai City 201109
+86 021 64907260
+86 021 6490 7276
Aplus FineTek
Sensor Inc.
(US Office)
355 S. Lemon Ave, Suite D,
Walnut, CA 91789
1 909 598 2488
1 909 598 3188
FineTek GmbH
(Germany Branch)
Frankfurter Str. 62, OG
D-65428
Ruesselsehim, Germany
+49 (0)6142 17608 0
+49 (0)142 17608 20
FineTek Pte Ltd.
(Singapore Branch)
No. 60 Kaki Bukit Place,
#07-06 Eunos
Techpark 2 Lobby B,
Singapore 415979
+65 6452 6340
+65 6734 1878
FineTek Co., Ltd.
(Indonesia Branch)
Ruko Golden 8 Blok H No.40
Gading Serpong, Tangerang,
Indonesia
+62 (21) 2923 1688
+62 (21) 2923 1988
FineTek Co., Ltd.
(Malaysia Branch)
8-05, Plaza Azalea, Persiaran
Bandaraya,
Seksyen 14, 40000 Shah
Alam, Selangor, Malaysiac
+603 5524 7168
+603 5524 7698

8
3. Product
3.1 Configuration
3.1.1 Model Label
The model label includes the product specification such as type, power supply,
output mode, ambient temperature, process temperature and process pressure.
3.1.2 Product Contents
1. Sensor
2. Documents
Operation Manual
Inspection Certificate of Measurement Accuracy (Optional)
3.2 Safety Inspection
a. Unpack and open the box
b. Please check whether the external package is deformed or damaged. Please
remember to take a picture for evidence in case you want to file for payment refund
later.
c. After unpacking, please check whether the content is deformed or damaged, or has any
quality problem. Please remember to take a picture for evidence in case you want to file
for payment refund later.
d. After unpacking, please check whether the content is consistent with the ordering info,
and whether the quantity is right.
e. Please contact the company within 7 days for any of the above situations (with picture
attached). Otherwise, we won’t refund, change or repair the product.

9
4. Principles
4.1 Product Principles
The guided wave radar emits a high-frequency pulse wave to be transmitted along with the
detection component (steel rope or connecting rod). When it comes in contact with the
object to be measured, the pulse wave will be reflected and some of the energy will be
reflected as well due to the different dielectric constant of air and the material. The time
difference between the reflection wave and the emission wave can be used to calculate
the distance between the surface of the measured object and the guided wave radar level
sensor.
4.2 Bottom Tracking Probe Technology
4.2.1 Bottom Tracking Probe Technology
The product is equipped with a bottom tracking probe technology. This function is very
useful in increasing the sensitivity when the dielectric constant of the measured object is
low, such as the plastic particles, material fragments or that in the liquefaction container.
When the dielectric constant is 3~10, the bottom tracking probe function will be enabled
automatically as long as the echo signal is not detected. The measurement value is
calculated based on the dielectric constant recorded the last time. In this case, the
instrument accuracy depends on the stability of the dielectric constant.
If the dielectric constant of the media is lower than 3, the bottom tracking probe function
will be enabled all the time. Under this circumstance, you must input the dielectric constant
of the media, which is quite important for measurement.
Distance
Material Height

10
4.2.2 Function Principle –Dual-Level Interface Measurement
The high-frequency micro wave pulse travels along the steel rope or the connecting rod.
When it reaches the media surface, a part of the micro wave pulse will be reflected.
Another part will penetrate the media in the upper layer (L1), and the second reflection will
take place on the interface between the upper (L2) and lower (L1) interface layers. The two
periods of pulse running will be calculated by the PCB inside the instrument, which also
outputs two levels.
※Measurement condition of dual-level interface:
Media on the upper layer (L2):
L2 must be non-conducting media. The dielectric constant of the media in L2 or the actual
distance towards the interface is known. The dielectric constant of the media in L2 must be
larger than 1.6. The media must be stable without change or mixture. Moreover, it must be
uniform. The minimum thickness of the media in L2 should be larger than 50mm
(1.97-inch), and L2 must be clearly separated from the lower layer (L1). In case of
emulsion phase or chipping layer, the maximum thickness should be 50mm (1.97-inch). It
should be without foam on the surface if possible, so it will get better measurement results.
Media on lower layer (L1):
The dielectric constant of L1 must be 10 larger than that of L2 at minimum, and the
conducting media is recommended. For example, if the dielectric constant of L2 is 2, the
dielectric constant of L1 should be 12 at least.
Gas layer (L3): It is the mixture of air or gas.
Output signal setting of dual-level interface measurement:
This instrument requires applying the setting in “level measurement”, which should be
applied in dual-level interface measurement. You may select dual-analog output version
and adjust the settings.
Distance of
the 1st Level
Height of
the 1st Level
Distance of 2nd
Height of 2nd

11
5. Features
It meets the measurement requirements of different temperatures, pressures and
media.
Based on the contact measurement, it can overcome the effects from steam,
foam and stirring.
2-wire loop power for simple wiring
Local LCM display for convenient on-site adjustment.
Unique algorithm and echo processing technology can be applied in various
complicated conditions.
Echo wave graphics display function, to show the signal waveform inside the
tank,can be used for background noise processing.

12
6. Specification
Model
JTR302
JTR30A
JTR301
JTR305
Applicable
Environment
Solid/Powder/Particle
Liquid/solid
Liquid
Low Dielectric
Liquid
MeasuringScope
Rod type:6m
Steel wire cable type:20m
Rod type:6m
Rod type:6m
Steel wire cable type:20m
Coaxial type:6m
Connection
1"PF
1"(3A)
3/4"PF
Min. Dielectric
coefficient
2.0
1.6
Ambient
Temperature
-40~80℃
-40~80℃
Operating
temperature
-40~150℃(Max.230℃)
-40~150℃(Max.230℃)
Operating
pressure
0~60 bar(25℃)
0~60 bar(25℃)
Accuracy
±5 mm
±5 mm
Analog
output
4~20 mA
4~20 mA
Power supply
16~30 Vdc Loop Power,16~30 Vdc
4-wire
16~30 Vdc Loop Power,16~30
Vdc 4-wire
Digital
communication
HART 7.3 for 2-Wire,
Modbus for 4-Wire
HART 7.3 for 2-Wire,
Modbus for 4-Wire
Housing material
Aluminum alloy
Aluminum alloy
Load Impedance
(VS-16)/0.022A Ohm for
2-wire;300 Ohm for 4-wire>16V
(VS-16)/0.022A Ohm for 2-wire;
300 Ohm for 4-wire>16V
IP Protection rating
IP67

13
7.Installation
7.1 General Instructions
7.1.1 Lock Instrument
When locking the instrument and the tank, the suitable hex wrench should be used to
fasten it.
Note! During the installation, please apply force on the hex screw to fasten it.
Don’t apply force on the instrument housing because it may damage the internal
parts.
7.1.2 Moisture Proof Instructions
During the installation, you may take the following measures to protect the instrument from
moisture:
Use the appropriate cable (The standard cable for this instrument is 1/2"PF cable connector)
Fasten the cable connector
Direct the cable connector downwards when installing, so as to prevent moisture
When connecting with the cable, leave a small segment of cable hanging down
in front of the fixing header.
Prevent moisture from entering the housing along the cable.
Please pay special attention to moisture proofing when the product is applied
in the following environments:
Outdoor installation
Installation in areas with estimated high moisture (such as cleaning process equipment)
Installation in cooling or heating containers
7.1.3 Operating Conditions
When using the instrument, please check whether the specification of all parts meets the
operating environment where it is exposed, including:
Measuring sensor
Connecting or fixing thread or flange
Sealing material
Especially the following conditions in the specification:
Operating pressure
Operating temperature
Properties of chemical media
Abrasion and mechanical effects
Note! If the instrument is applied in the pressure tank or the low-pressure container, it must be
sealed when fixing during the installation. Before usage, it must be checked as to whether the
operating temperature of the sealing material meets the ambient temperature.

14
7.2 Installation Instruction
7.2.1 Installation Site
Pay attention to the following when installing JTR3 series products. When it is installed in a
metal container, the distance between the container parts and the inner wall should be at
least over 300mm. For non-metal containers, the distance to the inner wall should be at
least over 500mm. During the operation, make sure the sensor doesn’t get into contact
with any device or tank wall. When using the sensor of a steel rope, it is recommended
fixing the sensor bottom in the tank to reduce the vibration to the sensor. For the tanks with
core shape at the lower part, it is recommended installing the product in the center of the
container to measure the lowest point at the bottom.
※Please note the upper/lower blind area of the instrument. It can’t measure the lowest point of
the sensor.
Note! When welding is required for the installation, please remove the electronic module of
the sensor from the junction box before welding. It can prevent the damage on the
electronic device due to the inductive coupling or other abnormalities.
Plastic container/glass container
The measuring principle of guided wave radar requires a metal plane at the process junction
point. Therefore, when it is used in the plastic container, it requires an instrument with flange
(since DN 50) or a metal plate (ø > 200 mm/8 in) placed under the process connection.
Note, the metal plate should be connected with the process connection directly. When installing
the measuring sensor of the connecting rod or steel rope in the plastic container without a metal
wall, the measuring value will be affected by the strong electromagnetic field (The interference
emission based on EN 61326: Class A). In this case, please use the co-axis measuring sensor.
Metal Tank
D>300mm
Non-metal Tank
D>500mm

15
.
During the installation, don’t use extension pipe on the container. Kindly install the sensor and
the container cap flush with the ground.
※When welding the connector of the extension pipe, please make the edge of the
extension pipe connector flush with container cap.
1. Flange
2. Metal plate

16
7.2.2 Feeding Tank Installation Precautions
Please don’t install the instrument at the feeding port. The instrument must be in a position
with stable media rather than a position with liquid flow. It can’t provide accurate measurement
when the liquid flows in.
7.2.3 Measuring range
The measuring range is from the bottom of flange or hread.
※Note, t he measuring range is from the reference to the bottom of the sensor, but not
including the upper/lower blind areas. For the default measuring range of the instrument, it is
set based on the media, “water”.
Measurement
scope
Lower blind area
Bottom of flange/ thread
Upper blind area

17
8 Wiring Instruction
8.1 Preparations
8.1.1 Please Note the Following Safety Precautions before Use:
The instrument wiring is only permitted when it is powered OFF.
If overvoltage occurs to the wire, please install overvoltage protection device to protect the
instrument.
8.1.2 Connecting Cable
The instrument can be connected with the general 2-core wire without the shielding layer
available on the market.
If electromagnetic coupling phenomenon occurs to the installation and wiring environment, and
the value exceeds the inspection value of EN61326-1 Standards applicable to the industrial
field, the cable with shielding cable should be used. For the instrument with housing and cable
screw thread connector, please use the cable with circular cross-section. Please check the
external diameter of the cable applicable to the cable screw thread connector, so as to ensure
the sealing on the cable screw thread connector (IP protection method). Please use the cable
screw thread connector matching with the cable diameter.
Note!
When wiring, please follow the requirements of DIN EN 61140 VDE 0140-1(Protection against
electric shock - Common aspects for installation and equipment), to guarantee the safety
isolation between the power circuit and the grid circuit.
When the cable with shielding isolated mesh is used, it is recommended setting up the
shielding isolated mesh on both sides of earth potential. In the sensor, the shielding isolated
mesh must be directly connected with the internal grounding terminal. The external grounding
terminal on the housing must be connected with the low impedance of the earth potential. For
explosion-proof equipment, it should perform grounding based on the requirements on the
license.
For the electroplating and KKS equipment (cathodic anticorrosion protection), the great
potential difference should be considered. When the shielding isolated mesh is grounded on
both sides, it may cause the current of the shielding isolated mesh to exceed the permitted
scope.

18
8.1.3 Power Supply
The product is connected with a 2-core wire to supply power and send current signal
Working voltage (Vs):
Without display adjustment module: 16~36VDC
With display adjustment module: 18~36VDC
Load impedance:(Vs-Vmin)/0.022A
For example: When supplying 24VDC for the instrument with display adjustment module:
(24-18)/0.022 = 272Ω
8.2 Wiring Instructions:
8.2.1 Connection Methods
When wiring, make the 2-core wire go through the enclosure, and make a connection
based on the positive/negative power supply as marked on the nameplate. A flathead
screwdriver may be used for connection.
8.2.2 Wiring Steps
Please follow the steps below:
1. Remove the cover on the housing.
2. Remove the display module by rotating it counterclockwisely.
3. Loosen the fixing screw on the cable screw thread connector
4. Remove the jacket of about 10cm (4in) on the cable, and remove the insulation of 1cm
(0.4in) at the core wire end.
5. Make the cable go through the cable connector, and insert it inside the housing.
6. Connect the wire to the terminal according to the wiring diagram
7. Pull it gently to check whether the wire is fixed firmly on the terminal
8. Connect the shielding with the terminal of the internal grounding wire, and connect the
terminal of the external grounding wire with the electric potential compensation.
9. Fasten the fixing screw of the cable screw thread connector, and make sure the sealing
ring is completely surrounding the cable
10.Re-assemble the display module.
11.Put on the housing cover to complete the electric connection

19
Note!
The product is of 2-wire loop power power supply. When it is applied for two analog
outputs, the current for each circuit should be measured individually. Parallel connection of the
two circuits will cause abnormal current output.
8.3 Startup Instructions
After the instrument is connected with the power supply and powered ON again, it will start
system initialization and self-diagnosis for about 30 seconds:
Internal inspection of the electronic parts.
It will show the model type, hardware and software version on the display module.
Wiring Diagram for Single
Analog Output
Wiring Diagram for two Analog
Outputs

20
9. Display Module Adjustment and Setting
9.1 Operation Steps:
1. Rotate the housing cover counterclockwisely to remove it.
2. Adjust the display module on the electronic part at the required direction, rotate clockwisely
to fix it.
3. Fasten the housing cover. The disassembly should follow the reverse direction.
[ ENT ] button:–Enter the menu–Confirm the selected content–Save the value
[ > ]button:–Select item in the menu –Select the edit field
[ ^]button:–Add setting parameter value
[ ESC ]button:–Go back to the previous menu layer
This manual suits for next models
4
Other FineTek Measuring Instrument manuals
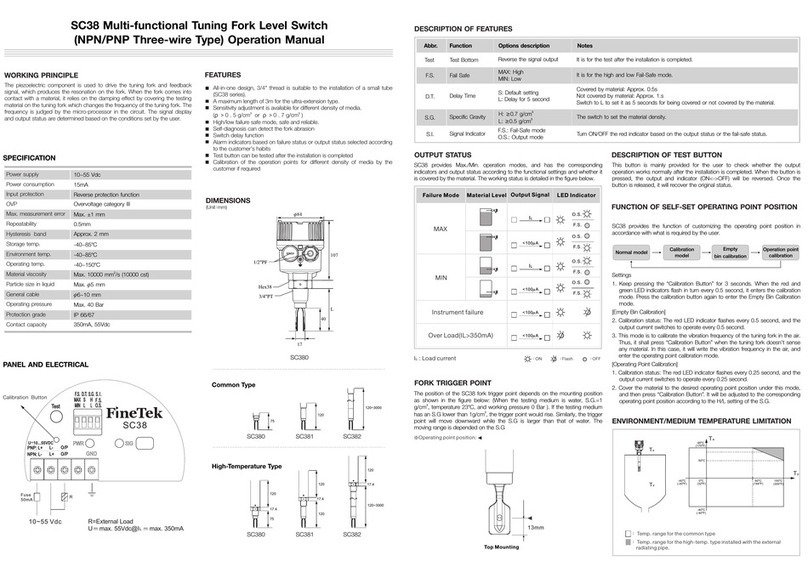
FineTek
FineTek SC38 User manual
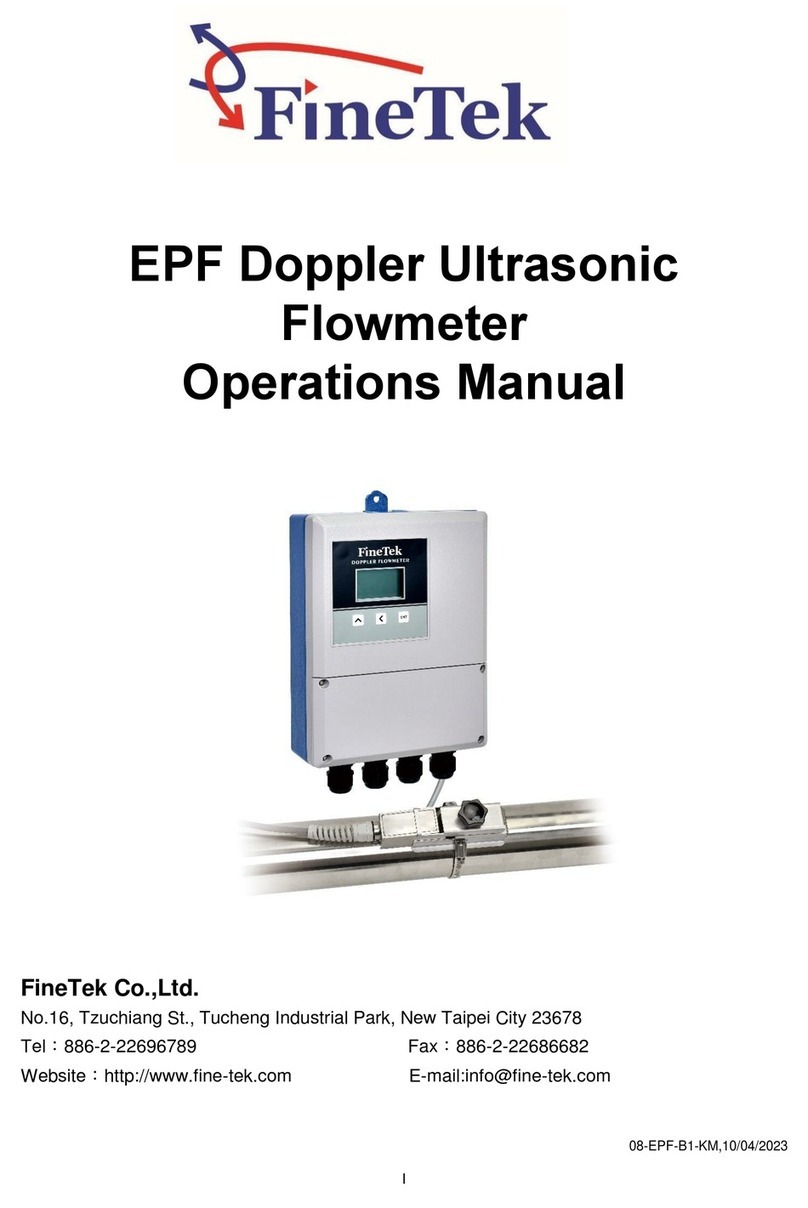
FineTek
FineTek EPF Series User manual
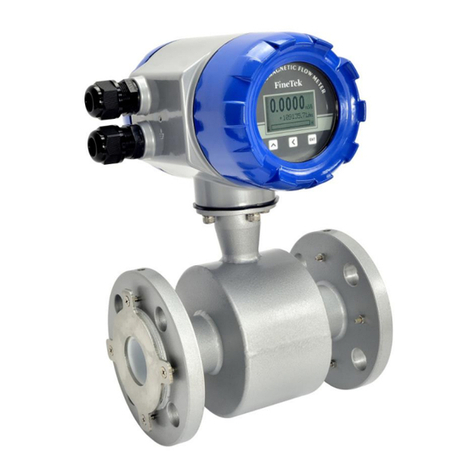
FineTek
FineTek EPD30 Technical manual
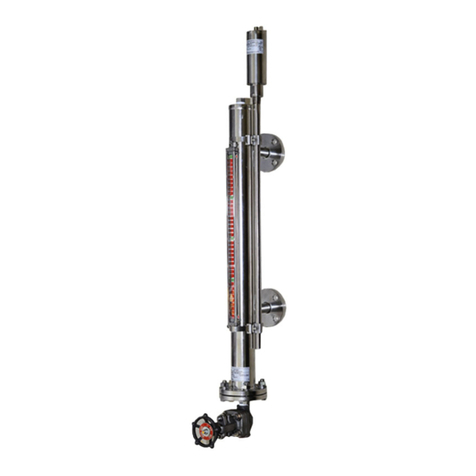
FineTek
FineTek EF Technical manual

FineTek
FineTek EDX2 User manual
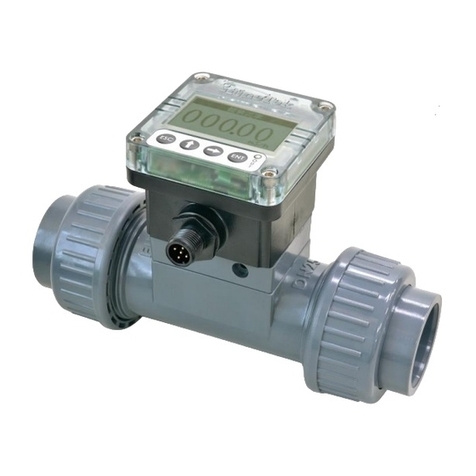
FineTek
FineTek EPR1 Series Technical manual

FineTek
FineTek EPD36 Technical manual
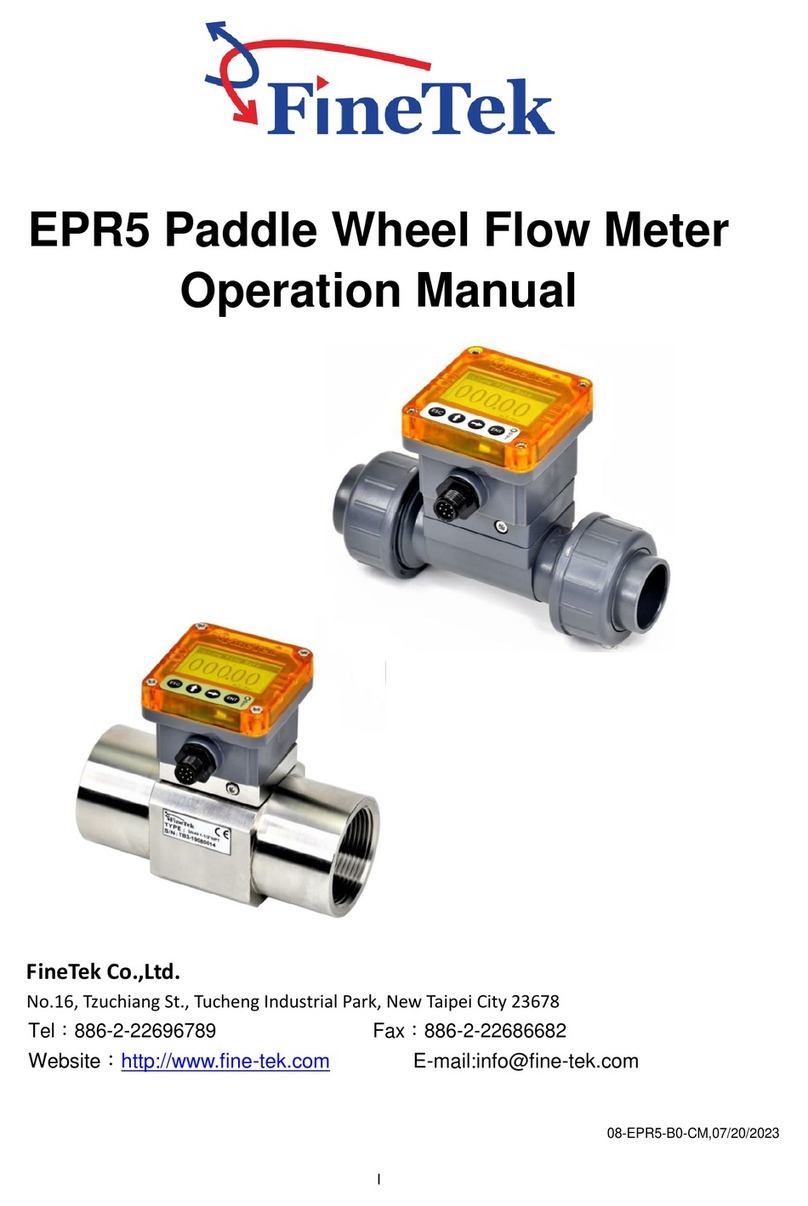
FineTek
FineTek EPR5 User manual
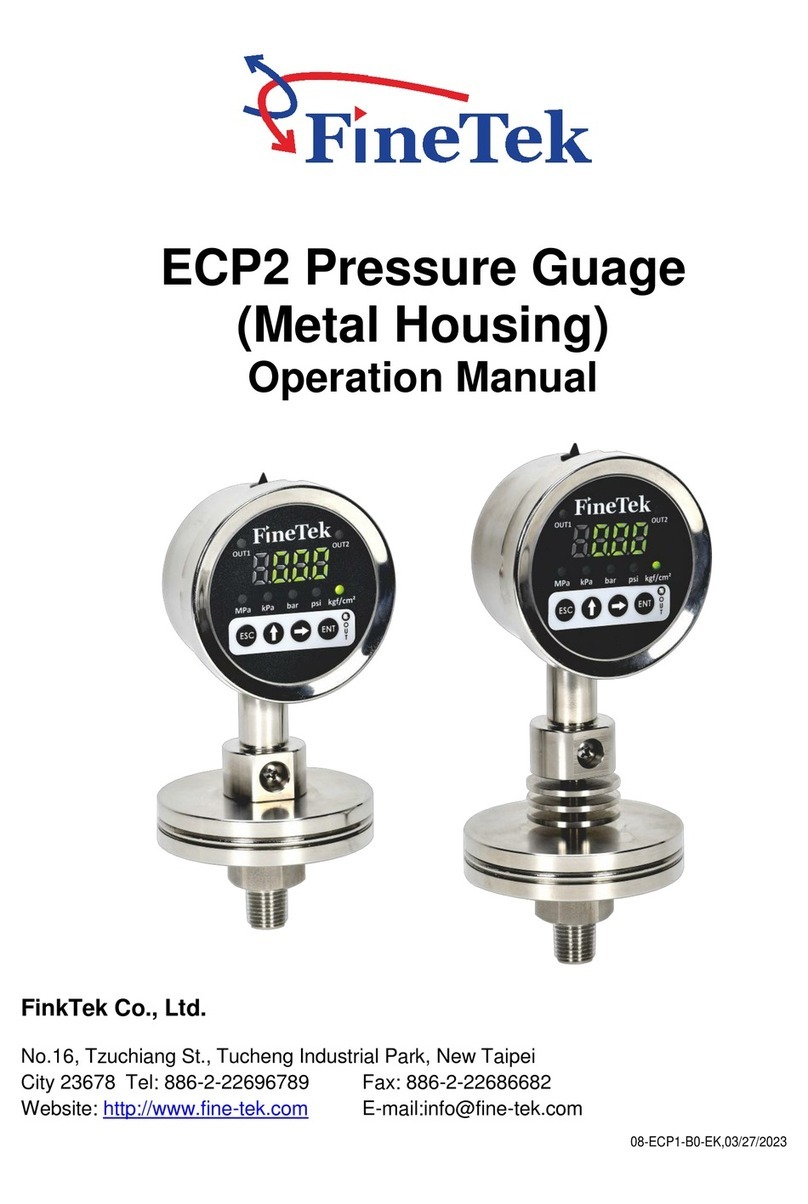
FineTek
FineTek ECP2 User manual
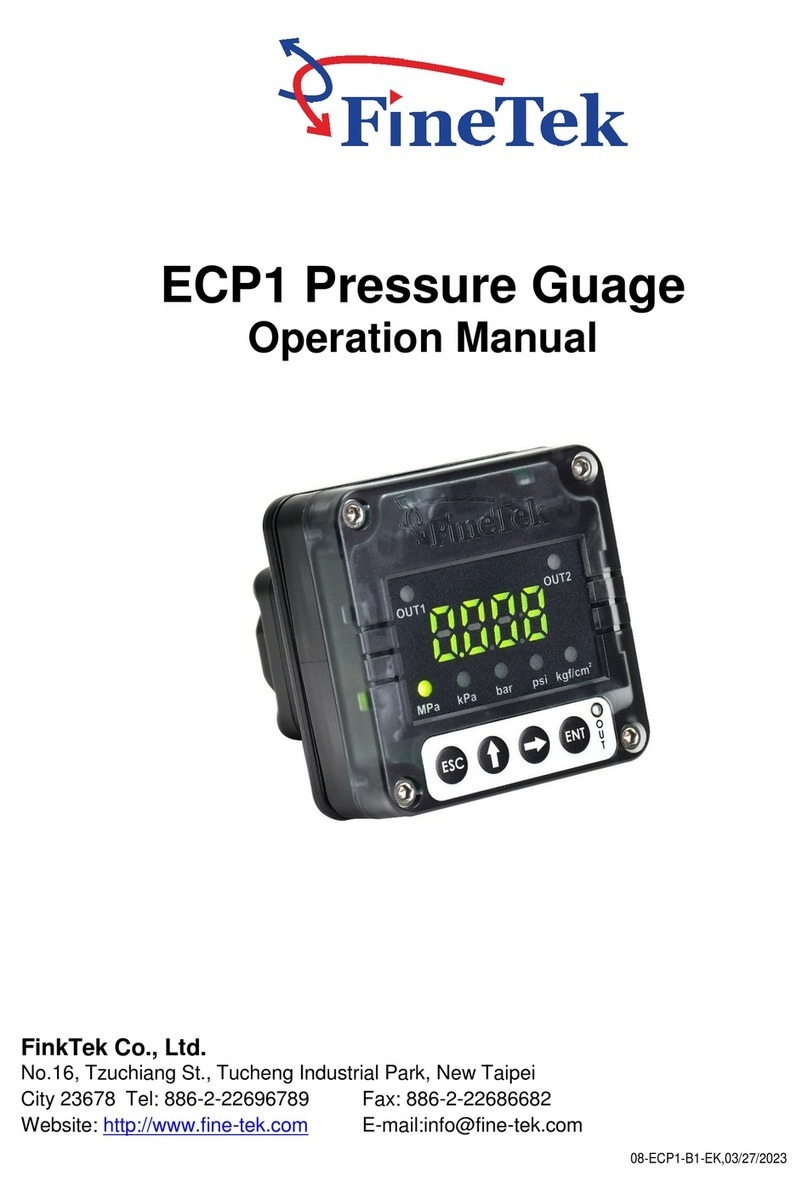
FineTek
FineTek ECP1 User manual