Flexiheat OXeN X2-W-1.2-V Guide

TECHNICAL DOCUMENTATION OPERATION MANUAL
OXeN X2-W-1.2-V | X2-N-1.2-V | X2-W-1.2-H | X2-N-1.2-H | X2-E-1.2-V
OXEN

2 |
TABLE OF CONTENTS
1. APPLICATION......................................................................................3
2. TECHNICAL DATA ..............................................................................4
3.1. INSTALLATION TO THE WALL.........................................................5
3.2. WATER CONNECTION.....................................................................6
3.3. SIDE COVER INSTALLATION...........................................................7
3.4. OXS INTAKE/EXHAUSTER INSTALLATION.....................................7
3.5. OXE EXPANDER INSTALLATION.....................................................9
3.6. HORIZONTAL INSTALLATION........................................................10
4. CONTROL SYSTEM ..........................................................................12
5. OPERATION.....................................................................................15
5.1. FILTERS REPLACEMENT..............................................................16
5.2. HEAT RECOVERY EXCHANGE CLEANING...................................16
6. SERVICE AND WARRANTY TERMS................................................17
7. CONFORMITY WITH WEEE DIRECTIVE 2012/19/UE .......................18

| 3
1. APPLICATION
OXeN is a ductless heat recovery unit. Two stage heat recovery in cross flow
exchangers ensure high efficiency. OXeN units are dedicated for use in medium
and large size areas where mechanical air exchange is a must. There are two
types available
X2-N-1.2-V –w/o additional heater, wall montage
X2-W-1.2-V –with additional heater (water supplied) to warm up fresh air, wall
montage
X2-E-1.2-V –with additional electric heater to warm up fresh air, wall montage
X2-N-1.2-H –w/o additional heater, ceiling montage
X2-W-1.2-H –with additional heater (water supplied) to warm up fresh air, ceiling
montage
OXeN is dedicated to operate indoor, ambient temperature in range +5ºC ÷
35ºC, maximal solid pollution 0,3 g/m3. Materials which were used: EPP,
aluminium, brass, copper, galvanized steel: substances which can cause
corrosion/damage of listed cannot be present in the room.
Water heat exchanger could be supply by water or glycol solution up to 60%.
The heat exchanger tubes are made of copper. The feed medium should not
cause corrosion of this material. In particular, the parameters as below should be
provided:
Parameter
Value
pH
7,5-9,0
Content of impurities
free of sediments/particles
Total hardness
[Ca2+, Mg2+]/[HCO3-] > 0.5
Oil and grease
<1 mg/l
Oxygen
<0.1mg/l
Bicarbonate, HCOᵌ
60-300 mg/l
Ammonium
< 1.0 mg/L
Sulphide
< 0.05 mg/L
Chloride, Cl
<100 mg/l

4 |
Max. air
stream
1200 m3/h
Air stream
range
Air flow
regulation
range
Stepless
-
Acoustic
pressure
49 dB(A)5
Max. current
consumption
1,9 A
14 A
Max. power
consumption
420 W
8,5 kW
Main
dimensions
(HxWxD)
1370 x 1180 x 760
Casing
material
Unit filled with
water
78,3 kg
-
81,3 kg
-
-
Installation
Max. solid
pollution
0,3 g/m3
Ambient
temperature
5 –45oC
Operation
position
Vertical
Horizontal
Vertical
IP
42
Filter class
EU4
Filetrs status
control
Pressure transmiter
Type of heat
recovery
exchanger
Two stage recovery, cross flow heat exchanger
Heat recovery
efficiency dry /
wet
74,7 / 80,9 % 7
Type of
additional
heater
Water heater
-
Water heater
-
electric heater
Heating
capacity
10,0 kW 8
-
10,0 kW 7
-
3,5 / 5,5 / 8,5 kW
Connection
½”
-
½”
-
-
Max. water
pressure
1,6 MPa
-
1,6 MPa
-
-
Max. water
temperature
95oC
-
95oC
-
-
Controlling
External touch panel
Anti-freeze
protection:
heat recovery
exchanger
Decrease of supplying air volume
1
Max. air flow with instal
3
Vertical range of non-isothermal stream (Δt=5°C), at velocity boundary equal to 0,2 m/s.
.
2. TECHNICAL DATA
2. DANE TECHNICZNE
2. TECHNISCHE GEGEVENS
2. ТЕХНИЧЕСКИЕ ПАРАМЕТРЫ
3.1. INSTALLATION TO THE WALL
EN X2-W-1.2-V X2-N-1.2-V X2-W-1.2-H X2-N-1.2-H X2-E-1.2-V
Power supply 230 VAC / 50 Hz 3x400 V
Unit weight
Indoor
7 According to directive 2009/125/EC measured with balanced mass flow, an indoor-outdoor air temperature difference of 20K
8At max. air flow stream, inlet/outlet water temperature 80/60°C, inlet air temperature 5oC, air volume 1200 m3/h.
led filter EU4 and wall intake/exhauster OxS.
2Horizontal range of isothermal stream, at velocity boundary equal to 0,2 m/s.
6Similar to RAL 9007
4Horizontal range of isothermal stream, at velocity boundary equal to 0,2 m/s.
5Acoustic pressure level measured in the room of average sound absorption, capacity 500m3, at distance of 5m from the unit.
Horizontal
Vertical
Horizontal
15.0 m 4.5 m 15.0 m
EPP - expanded polypropylene
Colour Grey
77.5 kg 75.1 kg 80.5 kg 78.1 kg 82.5 kg

| 5
Unit is design to be installed on the building
wall/ceiling. OxC wall transition (p.10) are
required for proper installation. Is not
recommended to use additional ducts.
Installation need keep
recommended distances.
Drill ventilation opening and
installation holes. Mounting hole
shall be prepared according to
Building Regulations.
Dismount OXeN side covers and
screw unit to the wall.
Bolts are not included.
During ventilation and heat recovery
process condensate can appear, drain
pan remove it gravity by outlet on the
bottom side of unit.

6 |
3.2. WATER CONNECTION
Regards OXeN X2-W-1.2-V/H.
The connection should be executed in a way which does not induce
stresses.
The system should be executed so that, in the case of a failure, it is
possible to disassemble the device. For this purpose it is best to use shut-
off valves just by the device.
The system with the heating medium must be protected against an
increase of the heating medium pressure above the permissible value
(1.6 MPa)
Before start up is recommended to check water connection and heating
pipeline tightness
While screwing exchanger to pipeline - connecting stubs must be hold by
wrench.
Supply
voltage
Max.
medium
temperature
120°C
Max.
operating
pressure
(A-AB)
1,6
(B-AB)
1,0
Index of
protection IP42
230VAC
2,0 bar
Connection ½”
Kvs

| 7
Prepare proper length of OxC transition. Max. wall
thickness of 190 mm, with a greater wall thickness must
be used several pieces OXC.
dd
If needed cut out ways in side cover
to pass pipelines or/and cables.
Put on the side cover.
3.3. SIDE COVER INSTALLATION
3.4. OXS INTAKE/EXHAUSTER INSTALLATION

8 |
Install OxC transition (from outside) with OXeN and seal
connection with low-expansion foam or silicone.
Dismount installation frame and side grill.
Screw frame and seal the connection with low-expansion
foam or silicone.
Install OxS to screwed frame.\
It is neccesairy to make tight connection between OxS &
OxC (rys.B)
Install side grill

| 9
3.5. OXE EXPANDER INSTALLATION
OxE –extension for OxS. It allows to dismiss air intake from air
exhaust.
Dismount side duct.
OxS should be installed on the frame already.
Install OxE expander. Max. number of OxE expanders is 4 pcs.
Ioonstall side duct and grill.

10 |
During ventilation and heat recovery process condensate can appear,
condensate pump remove it automatically by outlet on the top side of
unit.
sensor
condensate pump
connecting tube Ø9mm
Drill ventilation opening and installation holes.
Mounting hole shall be prepared according to Building Regulations.
3.6. HORIZONTAL INSTALLATION
OxS-H- roof-mounted air inlet/outlet
OxPD-H- Roof base
OxCB-H- Insulated plinth
OxE-H- Extension duct (optional)
OxC2-H- Adaptor

| 11
Insert the OxC2-H adapter into the EPP casing on the top of the
OXEN device. Niche at the dampers.
Seal the connection between OXC2-H and OXEN with the roofing
sealant around the perimeter.
Install unit under the ceiling using mounting pins, min. Ø8 mm
Install OxCB-H to the roof and seal connection
Install OxPD-H to OxCB-H using sheet metal roofing screws (every
150 mm, avoid fixing on the corner of the base), seal the contact area
from the bottom with polymer roof sealant, then install OxE-H
(optional).
OxeN can’t carry the load of OxH
The device must be horizontally levelled.

12 |
On the cleaned and degreased frame OxPD-H carefully stick the
gasket PES-15x4 in such a way that it is continuous along its entire
length, lead the gasket from the inside of the duct. Then put OxS-H on
the gasket a way from above and align the mounting frames with each
other. Be careful not to tear or fold the gasket, as this may lead to
leaks. Using M10x30 mounting bolts, enlarged washers and nuts,
screw the mounting frames together in the corners until the corner tips
are joined together. Apply a polymer sealant in the gap between the
metal frames. Then fasten the frames with clamps. Place the clamps
symmetrically along the entire length every 150 mm. After tightening
the clamps, tighten the M10 screws located in the corners. Spread the
excess of the sealant evenly in such a way that it completely fills the
place of contact between the frames. For sealing, use a silicone-free
polymer sealant, suitable for galvanized sheet metal. Using the wrong
sealant can cause leakage.

| 13
Single unit connection.
X2-W-1.2-V / X2-W-1.2-H / X2-N-1.2-V / X2-N-1.2-H
Wires size and type should be chosen by the designer.
.
X2-E-1.2-V
Wires size and type should be chosen by the designer.
COLD –OXeN X2-N-1.2-V/H
(w/o additional air heater)
HOT –OXeN X2-W-1.2-V/H
(with additional heater)
Set unit address. Each unit must have
unique number. Example:
Dipswitch SW1
Adress
1
1
0
0
0
0
2
0
1
0
0
0
6
0
1
1
0
0
31
1
1
1
1
1
1
2
4
8
16
COLD –OXeN X2-N-1.2-V/H
(bez wymiennika wodnego)
HOT –OXeN X2-W-1.2-V/H
(z wymiennikiem wodnym)
Dipswitch SW1
Adres
1
1
0
0
0
0
2
0
1
0
0
0
6
0
1
1
0
0
31
1
1
1
1
1
1
2
4
8
16
COLD - OXeN X2-N-1.2-V/H
(zonder extra luchtverwarmingselement)
HOT - OXeN X2-W-1.2-V/H
(met extra verwarmingselement)
Dipswitch SW1
Adres
1
1
0
0
0
0
2
0
1
0
0
0
6
0
1
1
0
0
31
1
1
1
1
1
1
2
4
8
16
COLD –OXeN X2-N-1.2-V/H
(без водяного теплообменника)
HOT –OXeN X2-W-1.2-V/H
(с водяным теплообменником)
Настроить адрес аппарата. Длякаждого аппарата
следует установить новый адрес.Пример:
Переключатель SW1
Адрес
1
1
0
0
0
0
2
0
1
0
0
0
6
0
1
1
0
0
31
1
1
1
1
1
1
2
4
8
16
4. CONTROL SYSTEM

14 |
Several OXeN units controlled via single T-box controller.
Connection units among themselves ensure forwarding controlling
signals. However, each unit should be supplied with power separately.
In case of chaining OXeN's (max. 31) - last unit in line
should has SW2 dipswitch in position T120. If controlling only 1 OXeN
SW2 dipswitch also has to be in T120 position.
Recommended wires*:
OXeN –> OXeN min. –LIYCY 2x2x0,5mm2,
twisted pair A and B, max 50 m.
* Wires size should be chosen by the designer

| 15
Tbox controlling touch panel shows founded OXeN units. While start
up run search procedure.
Before connecting the power supply check the correctness of
connection of the fan motor and the controllers. These connections
should be executed in accordance with their technical
documentation..
Before connecting the power supply check whether the mains
voltage is in accordance with the voltage on the unit data plate.
The electrical system supplying the fan motor should be additionally
protected with a circuit breaker against the effects of a possible
short-circuit in the system.
Starting the device without connecting the ground conductor is
forbidden.
Minimal diameter of power supply wires is 1,5mm2, final decision
make electrical designer which suit diameter to given conditions.
Wires should be finished with wire end sleeve.

16 |
It is forbidden to place any objects on the unit.
It is not allowed to make any modification in the unit. Any
modification causes in warranty loss
In the case of incorrect operation of thedevice it should be switched
off immediately.
To ensure proper operation unit should be inspected
periodically(six months), during inspection is needed to clean
heat recovery exchangers. Filters need to be replaced
according to the needs.
For the time of performing inspection or cleaning unit, power supply
should be disconnected. .
Casing can be cleaned with water and mild detergents.
The manufacturer bears no responsibility for damage of the
water heat exchanger resulting from freezing of the medium in
the exchanger. To protect water heater against freezing it is
recommended to use glycol solution as a heating medium.
5. OPERATION

| 17
5.1. FILTERS REPLACEMENT
The condition of filter is controlled by pressure transducer. When the filters are too heavily
soiled, an alarm is displayed on the T-box controller screen. In this case, replace the filters
is necessairy.
5.2. HEAT RECOVERY EXCHANGE CLEANING
Heat recovery exchanger should be cleaned with pressured air
along lamellas.
Be careful not to damage the aluminium lamellas.

18 |
6. SERVICE AND WARRANTY TERMS
Please contact your dealer in order to get acquitted with the warranty
terms and its limitation.
In the case of any irregularities in the device operation, please contact the
manufacturer’s service department.
The manufacturer bears no responsibility for operating the device in a
manner inconsistent with its purpose, by persons not authorised for
this, and for damage resulting from this!
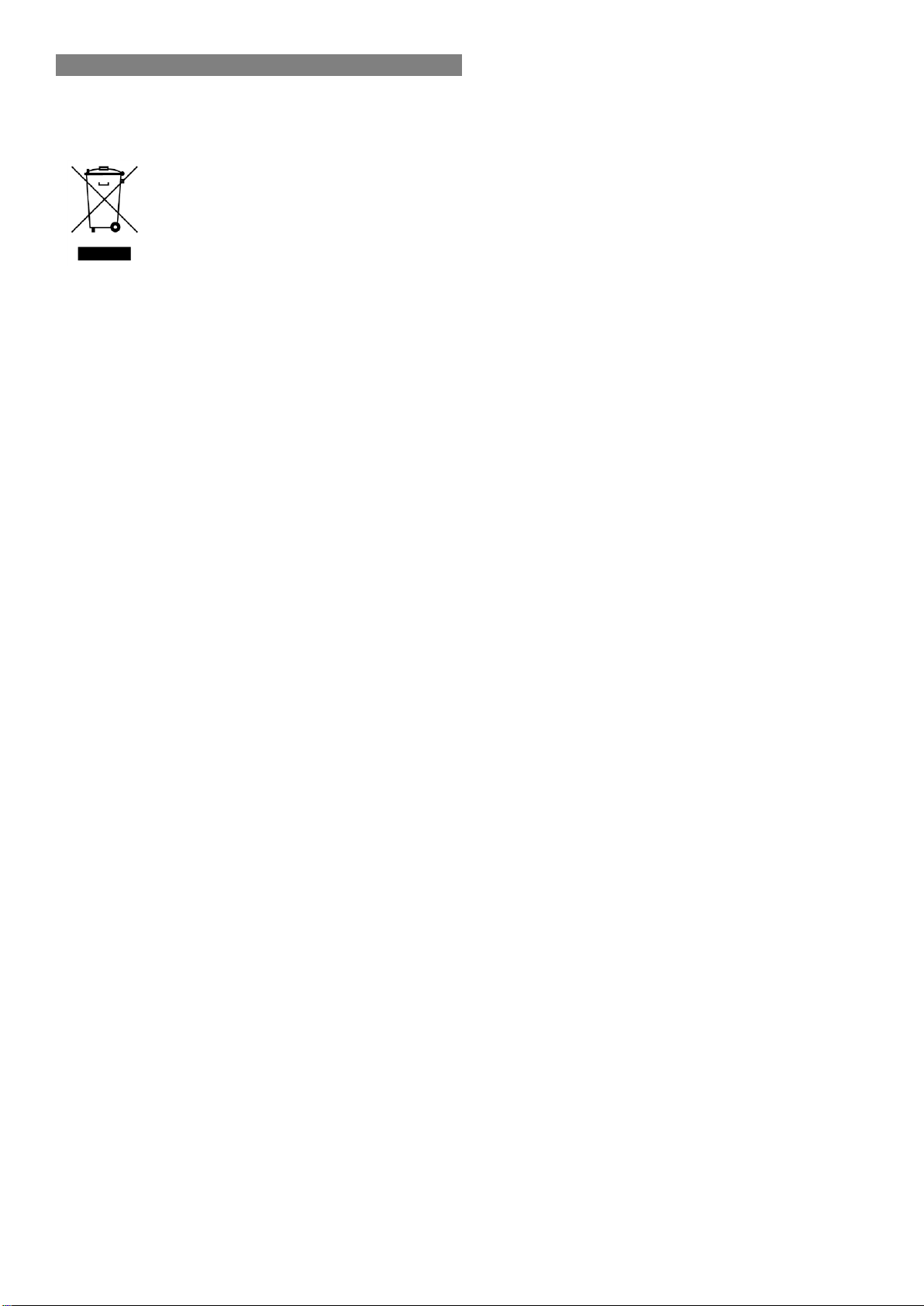
| 19
7. CONFORMITY WITH WEEE DIRECTIVE 2012/19/UE
Running a business without harming the environment and observing
the rules of proper handling of waste electrical and electronic
equipment is a priority for FLOWAIR.
The symbol of the crossed out wheeled bin placed on
the equipment, packaging or documents attached
means that the product must not be disposed of with
other wastes. It is the responsibility of the user to hand
the used equipment to a designated collection point for
proper processing. The symbol means at thesame time
that the equipment was placed on the market after
August 13, 2005.
For information on the collection system of waste electrical and
electronic equipment, please contact the distributor.
REMEMBER:
Do not dispose of used equipment together with other waste! There are
financial penalties for this. Proper handling of used equipment prevents
potential negative consequences for the environment and human
health. At the same time, we save the Earth's natural resources, reusing
resources obtained from the processing of equipment.

and harmonized norms ,with above directives:
Declaration Of Conformity
with control system and T-box controler were produced in accordance to the following Europeans Directives:
FLOWAIR hereby confirms that heat recovery units OXeN:
typ / type: X2-W-1.2-H, X2-N-1.2-H, X2-W-1.2-V, X2-N-1.2-V, X2-E-1,2-V
1. 2014/30/WE –Electromagnetic Compatibility (EMC),
2. 2006/42/WE –Machinery,
3. 2014/35/WE –Low Voltage Electrical Equipment (LVD),
4. 2009/125/WE –Energy-related products
PN-EN ISO 12100:2012 Safety Of Machinery - General Principles For Design - Risk Assessment And Risk
Reduction
Automatic electrical controls for household and similar use - Part 2-9: Particular
requirements for temperature sensing controls
PN-EN 60730-2-9:2011
Gdynia, 01.12.2021r.
Filip Konieczny
Product Manager
PN-EN 60335-2-40:2004/A2:2009E Household and similar electrical appliances - Safety - Part 2-40: Particular
requirements for electrical heat pumps, air-conditioners and dehumidifiers
PN-EN 61000-6-2:2008 Electromagnetic compatibility (EMC). Generic standards. Immunity for industrial
environments
Safety of machinery − Electrical equipment of machines − Part 1: General
requirements
PN-EN 60204-1:2010
20 |
This manual suits for next models
4
Table of contents
Other Flexiheat Fan manuals
Popular Fan manuals by other brands

Hunter
Hunter 51384 installation manual

BLAUBERG Ventilatoren
BLAUBERG Ventilatoren Moon user manual
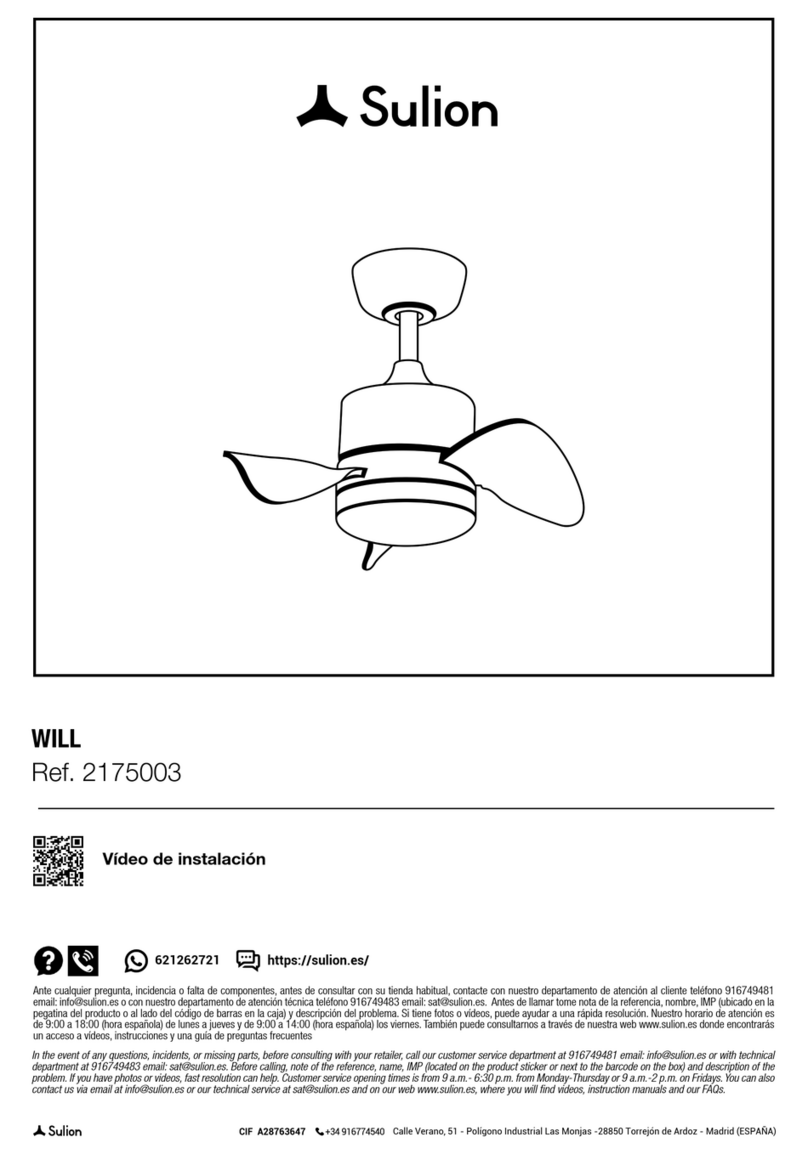
Sulion
Sulion WILL manual
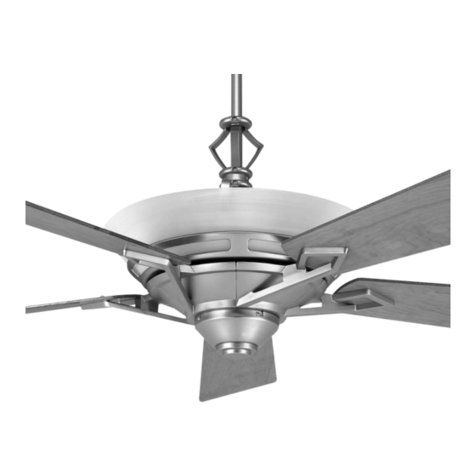
Regency Ceiling Fans
Regency Ceiling Fans Strasburg owner's manual
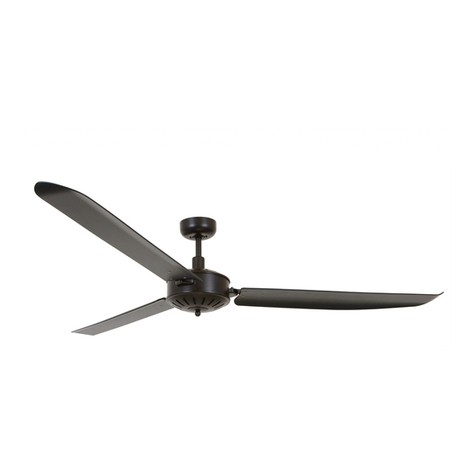
LUCCI Air
LUCCI Air AIRFUSION CAROLINA Installation and operation
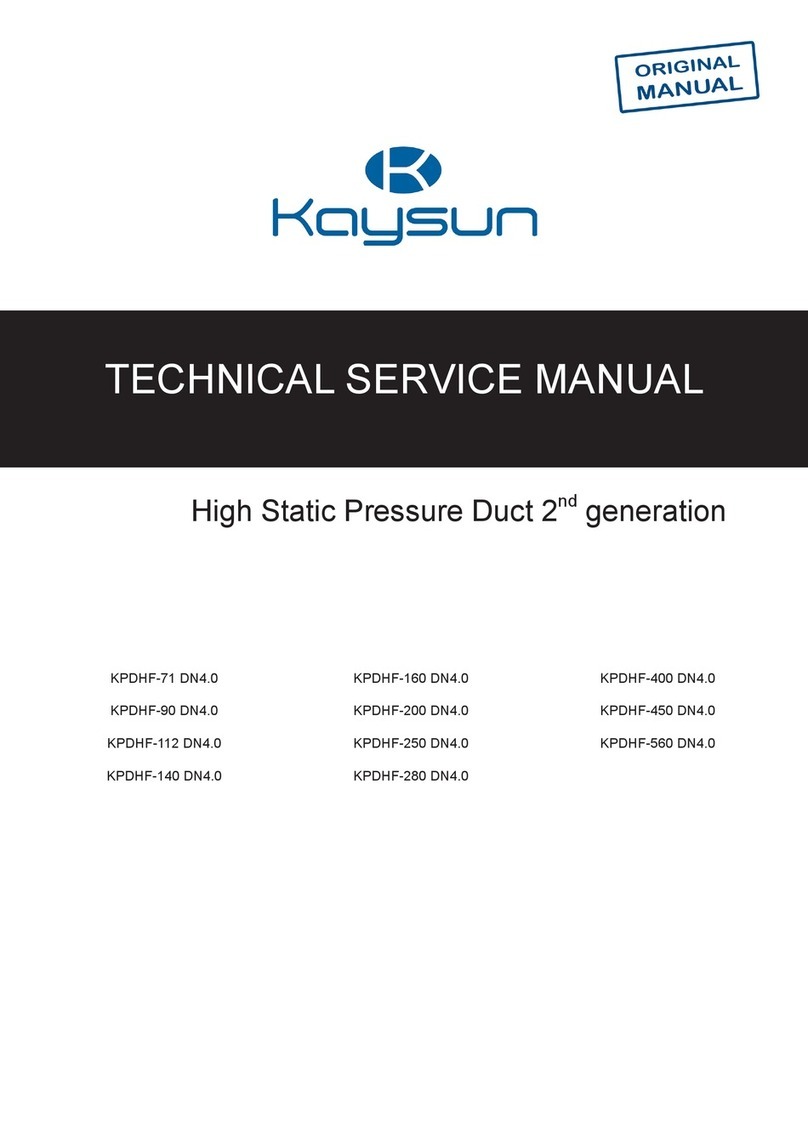
Frigicoll
Frigicoll Kaysun KPDHF-71 DN4.0 Technical & service manual