Fluke 8270A User manual

July 2018
© 2018 Fluke Corporation. All rights reserved. Specifications are subject to change without notice.
All product names are trademarks of their respective companies.
8270A/8370A
High-Pressure Modular Controller
Operators Manual

LIMITED WARRANTY AND LIMITATION OF LIABILITY
Each Fluke product is warranted to be free from defects in material and workmanship under normal use and
service. The warranty period is one year and begins on the date of shipment. Parts, product repairs, and
services are warranted for 90 days. This warranty extends only to the original buyer or end-user customer of
a Fluke authorized reseller, and does not apply to fuses, disposable batteries, or to any product which, in
Fluke's opinion, has been misused, altered, neglected, contaminated, or damaged by accident or abnormal
conditions of operation or handling. Fluke warrants that software will operate substantially in accordance
with its functional specifications for 90 days and that it has been properly recorded on non-defective media.
Fluke does not warrant that software will be error free or operate without interruption.
Fluke authorized resellers shall extend this warranty on new and unused products to end-user customers
only but have no authority to extend a greater or different warranty on behalf of Fluke. Warranty support is
available only if product is purchased through a Fluke authorized sales outlet or Buyer has paid the
applicable international price. Fluke reserves the right to invoice Buyer for importation costs of
repair/replacement parts when product purchased in one country is submitted for repair in another country.
Fluke's warranty obligation is limited, at Fluke's option, to refund of the purchase price, free of charge repair,
or replacement of a defective product which is returned to a Fluke authorized service center within the
warranty period.
To obtain warranty service, contact your nearest Fluke authorized service center to obtain return
authorization information, then send the product to that service center, with a description of the difficulty,
postage and insurance prepaid (FOB Destination). Fluke assumes no risk for damage in transit. Following
warranty repair, the product will be returned to Buyer, transportation prepaid (FOB Destination). If Fluke
determines that failure was caused by neglect, misuse, contamination, alteration, accident, or abnormal
condition of operation or handling, including overvoltage failures caused by use outside the product’s
specified rating, or normal wear and tear of mechanical components, Fluke will provide an estimate of repair
costs and obtain authorization before commencing the work. Following repair, the product will be returned to
the Buyer transportation prepaid and the Buyer will be billed for the repair and return transportation charges
(FOB Shipping Point).
THIS WARRANTY IS BUYER'S SOLE AND EXCLUSIVE REMEDY AND IS IN LIEU OF ALL OTHER
WARRANTIES, EXPRESS OR IMPLIED, INCLUDING BUT NOT LIMITED TO ANY IMPLIED WARRANTY
OF MERCHANTABILITY OR FITNESS FOR A PARTICULAR PURPOSE. FLUKE SHALL NOT BE LIABLE
FOR ANY SPECIAL, INDIRECT, INCIDENTAL, OR CONSEQUENTIAL DAMAGES OR LOSSES,
INCLUDING LOSS OF DATA, ARISING FROM ANY CAUSE OR THEORY.
Since some countries or states do not allow limitation of the term of an implied warranty, or exclusion or
limitation of incidental or consequential damages, the limitations and exclusions of this warranty may not
apply to every buyer. If any provision of this Warranty is held invalid or unenforceable by a court or other
decision-maker of competent jurisdiction, such holding will not affect the validity or enforceability of any other
provision.
Fluke Corporation
P.O. Box 9090
Everett, WA 98206-9090
U.S.A.
Fluke Europe B.V.
P.O. Box 1186
5602 BD Eindhoven
The Netherlands
11/99

i
Table of Contents
Title Page
Introduction ............................................................................................ 1
Contact Fluke Calibration ...................................................................... 1
Safety Information ................................................................................. 2
Symbols ................................................................................................. 3
The Product Manual Set ........................................................................ 3
Specifications ........................................................................................ 4
Unpack the Product ............................................................................... 4
Product Placement ................................................................................ 5
Connect to Mains Power ....................................................................... 6
Mains Voltage ........................................................................................ 6
Access the Module Bay ......................................................................... 7
PMM Installation .................................................................................... 8
PCM Installation .................................................................................... 11
Barometer Module ................................................................................. 11
Rear-Panel Manifold Pressure Connections ......................................... 12
SUPPLY Port ..................................................................................... 15
EXHAUST Port (Vacuum Pump if Required) ..................................... 15
TEST Port .......................................................................................... 16
REF Port ............................................................................................ 16
VENT Port ......................................................................................... 17
Controller Settings (Setup Menu) .......................................................... 17
Setup Menu ....................................................................................... 17
Instrument Setup Menu ..................................................................... 18
Instrument Settings Menu .............................................................. 18
Remote Port Menu ........................................................................ 21
Front-Panel Features ............................................................................ 22
Rear-Panel Features ............................................................................. 24
Turn on the Product ............................................................................... 26
Main Menu ............................................................................................. 26
Operation ............................................................................................... 32
Operating Modes ............................................................................... 32
Set Target Pressure (Setpoint) .......................................................... 32
Step Pressure Up or Down ................................................................ 32
Jog Pressure ..................................................................................... 33
Vent and Abort ................................................................................... 33
Pressure Measurement ..................................................................... 34

8270A/8370A
Operators Manual
ii
Pressure Control Settings ..................................................................... 34
Control Modes ................................................................................... 34
Dynamic Control Modes .................................................................... 35
Static Control
Mode
........................................................................... 36
Slew Rate (Rate of Pressure Change) .............................................. 36
Safety Limits ...................................................................................... 37
Upper Limit .................................................................................... 37
Lower Limit .................................................................................... 37
Auto Vent ....................................................................................... 37
Pressure Measurement Settings ........................................................... 37
Unit and Custom Units ....................................................................... 37
Measurement Modes ......................................................................... 39
Measurement Resolution ................................................................... 39
Module Selection ............................................................................... 40
Pressure Filter ................................................................................... 40
AutoZero ............................................................................................ 40
Gauge Mode .................................................................................. 40
Absolute Mode ............................................................................... 40
Atmosphere ....................................................................................... 41
Head Height ....................................................................................... 42
PM500 Absolute Zeroing ....................................................................... 43
Required Equipment .......................................................................... 43
PM500 Full Scale 700 kPa Absolute Zeroing .................................. 44
PM500 Full Scale >700 kPa Absolute Zeroing .................................. 46
Tasks ..................................................................................................... 46
Leak Test ........................................................................................... 46
Switch Test ........................................................................................ 47
Exercise ............................................................................................. 48
Program ............................................................................................. 48
External Driver Communication ............................................................. 50
Configure the Driver .............................................................................. 51
Driver Electrical Connections ................................................................ 53
External Abort and Isolation Valves ...................................................... 54
System Mode ........................................................................................ 54
Maintenance .......................................................................................... 54
Fuse Replacement ............................................................................ 54
Clean the Exterior
.............................................................................. 55
Reset Controller Settings ....................................................................... 56
Diagnostics ............................................................................................ 56
System ............................................................................................... 56
Measure ............................................................................................. 57
Control ............................................................................................... 57
Remote Interface ............................................................................... 58
Troubleshooting ..................................................................................... 58
Error Codes ........................................................................................... 61
User-Replaceable Parts and Accessories ............................................. 63

1
Introduction
The Fluke Calibration 8270A/8370A High-Pressure Modular Controller (the
Product) precisely measure and control pneumatic pressures up to 44 MPa
(6300 psi) and 107 MPa (15 500 psi), respectively. Use the Product to calibrate,
characterize, or test a wide variety of pressure measurement devices that include
transmitters, gauges, and switches.
The Product uses interchangeable Pressure Measurement Modules (PMMs) and
a Pressure Control Module (PCM) to regulate pressure output. The touchscreen
display features a multi-language user interface (UI). See Instrument Setup Menu
for more information.
Contact Fluke Calibration
To contact Fluke Calibration, call one of the following telephone numbers:
Technical Support USA: 1-877-355-3225
Calibration/Repair USA: 1-877-355-3225
Canada: 1-800-36-FLUKE (1-800-363-5853)
Europe: +31-40-2675-200
Japan: +81-3-6714-3114
Singapore: +65-6799-5566
China: +86-400-810-3435
Brazil: +55-11-3759-7600
Anywhere in the world: +1-425-446-6110
To see product information or download manuals and the latest manual
supplements, visit Fluke Calibration’s website at www.flukecal.com.
To register your product, visit http://flukecal.com/register-product.

8270A/8370A
Operators Manual
2
Safety Information
A Warning identifies conditions and procedures that are dangerous to the user.
A Caution identifies conditions and procedures that can cause damage to the
Product or the equipment under test.
XWWarnings
To prevent possible electrical shock, fire, or personal injury:
Only assemble and operate high-pressure systems if you
know the correct safety procedures. High-pressure liquids
and gases are hazardous and the energy from them can be
released without warning.
Read all safety information before you use the Product.
Carefully read all instructions.
Do not use the Product around explosive gas, vapor, or in
damp or wet environments.
Do not operate the Product with covers removed or the case
open. Hazardous voltage exposure is possible. Pressure
modules may be exchanged through the front panel while
the Product is turned on.
Use this Product indoors only.
Do not put the Product where access to the mains power
cord is blocked.
Use only the mains power cord and connector approved for
the voltage and plug configuration in your country and rated
for the Product.
Make sure the ground conductor in the mains power cord is
connected to a protective earth ground. Disruption of the
protective earth could put voltage on the chassis that could
cause death.
Replace the mains power cord if the insulation is damaged
or if the insulation shows signs of wear.
Use the Product only as specified, or the protection
supplied by the Product can be compromised.
Before the Product is used to apply pressure, ensure the
integrity of all components to be pressurized and make sure
they are rated to adequate working pressure.
Do not apply more than the rated voltage, between the
terminals or between each terminal and earth ground.
Do not touch voltages >30 V ac rms, 42 V ac peak, or
60 V dc.

High-Pressure Modular Controller
Symbols
3
Do not use the Product if it operates incorrectly.
Disable the Product if it is damaged.
Use only specified replacement parts.
Have an approved technician repair the Product.
Do not disable safety interlocks or pressure-relief devices.
Use two handles to lift and carry the Product.
Symbols
The symbols shown in Table 1 can be found in this manual or on the Product.
Table 1. Symbols
Symbol Description Symbol Description
X Hazardous voltage. Risk of electric
shock. ) Certified by CSA Group to North
American safety standards.
W Risk of Danger. Important
information. See Manual. P Conforms to European Union
directives.
Consult user documentation. Conforms to relevant Australian EMC
standards.
Fuse Conforms to relevant South Korean
EMC Standards.
Earth Terminal ~
This product complies with the WEEE
Directive marking requirements. The
affixed label indicates that you must not
discard this electrical/electronic product
in domestic household waste. Product
Category: With reference to the
equipment types in the WEEE Directive
Annex I, this product is classed as
category 9 "Monitoring and Control
Instrumentation" product. Do not
dispose of this product as unsorted
municipal waste.
The Product Manual Set
The Product manuals are:
8270A/8370A Safety Information
8270A/8370A Operators Manual (provided at www.Flukecal.com.)
6270A, 8270A, 8370A Remote Programmers Guide (provided at
www.Flukecal.com)
To order, refer to the Fluke Calibration Catalog or contact a Fluke Calibration
sales representative. See Contact Fluke Calibration.
This manual provides complete information to install and operate the Product
from the front panel.

8270A/8370A
Operators Manual
4
Calibration and Repair Information
If calibration or repair is needed during the warranty period, contact an
authorized Fluke Calibration Service Center to arrange for repair (see Contact
Fluke Calibration). Please have the Product information ready such as the
purchase date and serial number to schedule the repair.
Specifications
Safety specifications are located in the printed 8270A/8370A Safety Information.
Full specifications are located online in the 8270A/8370A Specifications.
Unpack the Product
The Product is delivered in a corrugated container with foam inserts. An optional
molded shipping case with custom foam inserts is also available, see User-
Replaceable Parts and Accessories.
Remove the Product and its accessories from the shipping container and remove
each element from its protective plastic bag. Check that all items listed in Table 2
are present and have no visible damage.
If it is necessary to reship the Product, use the original container. To order a new
container, see Contact Fluke Calibration.
Table 2. Standard Equipment
Item Model or Part Number
The Product 8270A/8370A
Mains Power Cord See Table 3.
PMM (Pressure Measurement Module,
ordered separately)
Assorted ranges and Barometer modules are also
available. See Flukecal.com.
PCM (Pressure Control Module, ordered
separately) PCM-STD-40M/PCM-STD-100M
8270A/8370A Safety Information 4938183
Module Installation Tool 5010562 (6 mm hex bit), 5013218 (handle)
8270A Seals Kit SK-8270-SERVICE [1]
8370A Seals Kit SK-8370-SERVICE [1]
1. For detailed information on installation of replacement seals, consult the 8270A/8370A Service
Manual.

High-Pressure Modular Controller
Product Placement
5
Product Placement
XWWarnings
To prevent possible electrical shock, fire, or personal injury, do
not restrict access to the Product mains power cord. The mains
power cord is the mains disconnecting device. If access to the
power cord is inhibited by rack mounting, a properly-rated
accessible mains disconnecting switch must be provided within
reach as part of the installation.
To prevent possible personal injury:
Use good lifting practices when lifting or moving the
Product. The Product is an unbalanced load and can weigh
as much as 20 kg (44 lb).
Use two handles to lift and carry the Product.
Use the Product on a bench or in a standard 19 inch equipment rack. Purchase a
rack mount kit to install the Product into an equipment rack. For bench-top use,
install the Product on a flat, stable surface at a convenient height. The front feet
can be extended to incline the Product for easier viewing.
Minimize the distance between the Product and the device or system under test
to enhance control performance and reduce pressure settling times.
For installation, the Product requires:
An electrical power source of 100 V ac to 240 V ac, 47 Hz to 63 Hz.
A continuous, regulated pressure supply of clean, dry, non-corrosive gas at
10 % greater than the highest pressure range should be connected to the
Product SUPPLY port. For optimal control performance, the supply pressure
should be no greater than 100 times the full scale of the active measurement
range. Never exceed the maximum pressure of the Product chassis.
A vacuum source of 7 kPa (1 psi) absolute and with a displacement of at
least 90 L/min (3 cfm) if controlling pressures <7 kPa (1 psi) gauge (8270A
only).

8270A/8370A
Operators Manual
6
Connect to Mains Power
XWWarning
To prevent shock hazard, connect the factory-supplied three-
conductor mains power cord to a properly-grounded power
outlet. Do not use a two-conductor adapter or extension cord,
as it will break the protective ground connection.
Mains Voltage
To power the Product, mains voltage ranging from 100 V ac to 240 V ac with
frequencies from 47 Hz to 63 Hz is required.
The Product comes with the appropriate line power plug for the country of
purchase. If a different type is necessary, refer to Table 3 for a list that shows the
mains line power plug types available from Fluke Calibration.
Table 3. Line Power Cord Types Available from Fluke Calibration
LC-1 LC-3 LC-4 LC-5
LC-6 LC-7 LC-42
hhp004.eps
Type Fluke Calibration Option Number
North America LC-1
Universal Euro LC-3
United Kingdom LC-4
Switzerland LC-5
Australia LC-6
South Africa LC-7
Brazil LC-42

High-Pressure Modular Controller
Access the Module Bay
7
Access the Module Bay
After the Product is properly placed (in a standard 19 inch rack or on a bench
top) install the modules in the Module Bay. Before use, install the Pressure
Control Module (PCM) and Pressure Measurement Module(s) (PMM). See PCM
Installation for PCM bolt torque values.
Note
The Product rear-panel power switch can be on or off during PMM
exchange or installation.
W Warning
To prevent personal injury, vent the supply pressure before you
remove the PCM.
To access the Module Bay, see Figure 1:
1. Pull out the handle () located directly below the numeric keypad. This
unlocks the front panel.
2. Pull the handle to slide out front panel and access the Module Bay ().
Note
For safety, the Product automatically vents to atmosphere when the
front panel is unlatched and opened. When the front panel is open,
the system stays in the Vent mode until closed.
For service activity, see the Service Manual for detailed service
processes.
For standard operations, the system pneumatic valves are a
normally closed type. Depending on the chassis power/pressure
down process, differing levels of trapped pressure are possible.
If power is lost to the product, while at high pressure, remove
pressure supply to allow system to mostly depressurize. If possible,
power on system to perform a vent.
Before you open the front panel, remove sensitive, low pressure
devices from the test port. Use the optional Isolation Valve to
improve protection for sensitive pressure devices.

8270A/8370A
Operators Manual
8
1
2
ifb001.eps
Figure 1. Module Bay
PMM Installation
The PMMs are delivered in a separate box. Install the PMMs with the Product
turned on or off. For the 8270A, the PMMs can be installed in any order without
the need to plug any of the unused slots. For the 8370A, the measure module to
the far right (closest to the control module) must have a full scale of 70 MPa
(10 000 psi) or greater. A module must be installed in this slot for the system to
properly operate. When the front panel is opened, information such as the
pressure range of each module is shown after it is connected. The Product
detects the PMM information when installed and shows the information in the
Modules menu (see Modules).

High-Pressure Modular Controller
PMM Installation
9
To install the PMMs:
WCaution
To prevent damage to the sensors inside the modules, do not
drop the modules.
1. Remove the PMM from its shipping box.
2. Remove the protective plastic cover from the PMM test and reference port.
3. Confirm that the test port and reference port O-rings are properly installed on
the module and are not torn or damaged. Additional O-rings are available in
case they become lost or damaged.
4. Open the front panel to access the Module Bay as described in the Access
the Module Bay section.
5. The PMM has a slot on the bottom of it that fits into the track that lies on the
bottom of the inner Product case, see Figure 1 (). Line the track up with the
slot and slide the PMM into the bottom case until it stops. See Figure 2.
6. Turn the knob on the PMM clockwise until it clicks one time to tighten it,
modules less than or equal to 44 MPa (6300 psi). High-pressure modules,
with full scales greater than 44 MPa (6300 psi), use a standard hex bolt for
tightening the pressure connection. A 6 mm hex head wrench is required to
connect the module (provided with the chassis). There is no torque limiting
feature on these high pressure modules. The recommended torque is
10-14 N ꞏ m (7 - 10 lbf ꞏ ft).
Note
The PMM knob is a torque-limiting knob that slips once the proper
amount of torque is applied. This prevents accidental over-tightening
that can damage the manifold.
7. After tightening the PMM to the manifold, the module should automatically
appear on the display. Check the main display to see if the PMM is properly
installed.
Note
When the Module Bay is opened, the front-panel display shows the
slots and visually displays the PMMs installed. This provides a
method to quickly ensure the newly installed PMM is connected and
communicating.
8. Repeat this procedure for any other PMMs.
9. Close and latch the front panel.

8270A/8370A
Operators Manual
10
ifb011.eps
Figure 2. PMM Installation

High-Pressure Modular Controller
PCM Installation
11
PCM Installation
Depending upon how the Product is ordered, the PCM may come installed in the
unit or be delivered in a separate box.
To install the PCM:
WCaution
To prevent damage to the sensors inside the modules, do not
drop the modules.
1. Remove the PCM from its shipping box.
2. Remove any protective plastic covers from the PCM pressure ports.
3. Open the Module Bay as described in the Access the Module Bay section.
4. The PCM location in the Module Bay is on the far right. Align the track on the
bottom of the PCM with the PCM slot inside the Module Bay. See Figure 3.
5. Slide the PCM into place.
6. Tighten the two bolts on the front of the PCM using a 6 mm hex head wrench.
The recommended torque is 10-14 N ꞏ m (7 - 10 lbf ꞏ ft).
WCaution
To prevent damage to the internal manifold, do not over torque.
7. Close and latch the front panel.
ifb021.eps
Figure 3. PCM Installation
Barometer Module
For absolute measurements with gauge mode modules, a barometer module
(PM200-A100K, PM500-A120K, PM500-BA120K, PM500-A200K, or BRM600-
BA100K) must be installed, see Atmosphere. The module can also be selected
as an Autozero reference, see Autozero - Absolute Mode.

8270A/8370A
Operators Manual
12
Rear-Panel Manifold Pressure Connections
The 8270A comes with one of three types of manifolds installed:
NPT
BSP
SAE
The type of manifold is marked on its lower right corner. Table 4 lists the different
manifolds and port sizes. Manifold installation is explained in the Maintenance
section.
Table 4. 8270A Rear-Panel Manifolds
Manifold SUPPLY EXHAUST TEST Reference
(REF) VENT
NPT [1] 1/4 inch
NPT
1/4 inch
NPT
1/4 inch
NPT
1/4 inch
NPT
1/8 inch
NPT
BSP [2] 1/4 inch
BSP
1/4 inch
BSP
1/4 inch
BSP
1/4 inch
BSP
1/8 inch
BSP
SAE [3] 7/16-20
SAE
7/16-20
SAE
7/16-20
SAE
7/16-20
SAE
7/16-20
SAE
[1] Requires the use of PTFE tape on the male adapter to ensure a good seal.
[2] Bonded seal is required to ensure a good seal.
[3] O-ring is required (which is normally included on the fitting) to ensure a good seal.
A lines and fittings kit can be purchased to supply the common adapters used to
connect to the manifolds. See User-Replaceable Parts and Accessories for more
information.
The 8370A is available with only one type of manifold block. The pressure
connection types are:
Supply DH500
Test DH500
Reference 1/4 inch NPT
Exhaust 1/4 inch NPT
Vent 1/8 inch NPT
DH500 is a cone and threaded high-pressure connection equivalent to AE F250C
or HiP HF4.
Pneumatic schematics are shown in Figures 4 and 5.

High-Pressure Modular Controller
Rear-Panel Manifold Pressure Connections
13
MPa MPa MPa MPa MPa
ifb036.eps
Figure 4. 8270A Pneumatic Schematic

8270A/8370A
Operators Manual
14
MPa MPa MPa MPa MPa MPa
ifb035.eps
Figure 5. 8370A Pneumatic Schematic

High-Pressure Modular Controller
Rear-Panel Manifold Pressure Connections
15
SUPPLY Port
The pressure SUPPLY port must be connected to a regulated source of clean,
dry air or nitrogen as directed in Specifications. Fluke Calibration recommends
that tubing be at least 2 millimeters (0.083 inch) inside diameter and properly
rated for the pressure. Length in excess of 3 meters (10 ft) may increase
readiness time in some situations.
A continuous, regulated pressure supply of clean, dry, non-corrosive gas at 10 %
greater than the highest pressure range should be connected to the Product
SUPPLY port. For optimal control performance, the supply pressure should be no
greater than 100 times the full scale of the active measurement range. Never
exceed the maximum pressure of the Product chassis. The supply pressure can
be viewed under the diagnostics Setup>Diagnostic>Control.
WCaution
To prevent damage to the system, make sure to select the
correct size adapter fitting with the correct thread type. Ensure
that all hardware used is rated to adequate working pressure,
and that all equipment is in proper working order (for example,
no cracks or stripped threads).
To prevent damage to the Product, be sure to connect the
pressure supply to the SUPPLY port. Connecting to another
port can damage the Product.
To prevent damage to the system and to prevent waste of
supply gas, install the PCM prior to connecting the supply
pressure to the system.
EXHAUST Port (Vacuum Pump if Required)
Typical operation is with the EXHAUST port open to atmosphere (no restriction).
A vacuum pump is required to control pressure below atmosphere. Control
performance below 7 kPa (1 psi) gauge may be degraded if a vacuum pump is
not used. Tubing should have a minimum inside diameter of 6 millimeters
(1/4 inch). In confined areas, pipe the exhaust port outside to prevent an
accumulation of nitrogen (or other supply gas). It is acceptable to add tubing to
the exhaust port for the primary purpose of reducing noise. Do not block the
exhaust tube.
WCaution
To prevent damage to the Product:
Never connect a pressure supply to or plug the Product
EXHAUST port.
To avoid building up pressure on the EXHAUST port or on a
vacuum pump connected to the EXHAUST port, the vacuum
source should either be continuously ON or the EXHAUST
port should be bypassed to atmosphere when the vacuum
source is OFF. This is because when a supply pressure is
applied to the Product SUPPLY port and the Product is not
in the vent ON condition, there is typically a constant gas
exhaust through the Product EXHAUST port.

8270A/8370A
Operators Manual
16
When controlling down in pressure, the Product will exhaust
gas through the EXHAUST port. The flow of this gas can be
greater than what the vacuum pump can support. When
working at higher pressures, Fluke Calibration recommends
that the vacuum pump be turned off and equipped with an
auto-vent valve.
TEST Port
Pressure instruments and devices to be tested are connected to the TEST port.
Tubing connected from the Test port to the load volume should have an internal
diameter >2 millimeter (0.083 inch). For optimal performance, tubing should be
<5 meters (15 feet) when minimum diameter tubing is used.
To prevent oils, grease, solvents, and water that could be present in a Device
Under Test (DUT) from contaminating the Product, a Contamination Prevention
System (CPS) is available for use with the Product. The CPS sits on the bench
and provides a platform to test pressure instruments and devices. The CPS
connects directly to the TEST port. For more information, see the CPS-40M-
HC40/CPS-100M Instructions.
Note
Excessive leaks in the test volume affect control stability and can
cause measurement errors in the DUT.
WCaution
To prevent damage to the Product, when the Product is
connected to a system with liquid contaminants, take proper
precautions to purge the system and test line. Not doing so can
cause Product contamination and result in a need for non-
warranty service.
Note
Minimize the length of the test connection tubing to enhance control
performance and reduce pressure setting time.
The Product pressure control will not operate properly if there are
excessive leaks in the test system. The maximum acceptable leak
rate for optimal automated pressure control operation and to ensure
in tolerance measurements with default pressure control parameters
is
0.5 % of set pressure/minute. In DYNAMIC CONTROL modes
(Dynamic A and Dynamic B), to handle higher test system leak
rates, use Control Settings to increase the ready tolerance.
REF Port
The REF port (Reference port) is open to atmosphere for gauge measurements
or it can be connected to the reference port of the pressure instruments and
DUTs.
Instruments with a low full-scale pressure range require special handling to
assure their performance. These instruments are sensitive to atmospheric
pressure changes, including disturbances in the atmospheric pressure. The
reference side must be carefully controlled or changes due to wind, air handlers,
doors shutting, and more will cause major variations in the readings. The Product
tracks these changes but it may not track in the same way as the DUT. To
control these changes, Fluke Calibration recommends that the reference port
(also referred to as the "test-(test minus)" or "low" port of all relevant DUTs be
tied to the REF port of the Product.
This manual suits for next models
16
Table of contents
Other Fluke Controllers manuals
Popular Controllers manuals by other brands
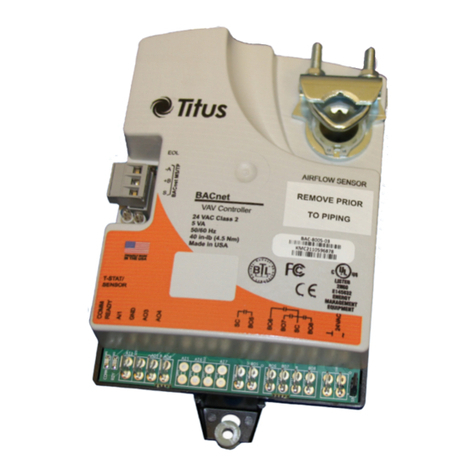
Titus
Titus BAC-8007 Installation & operation manual
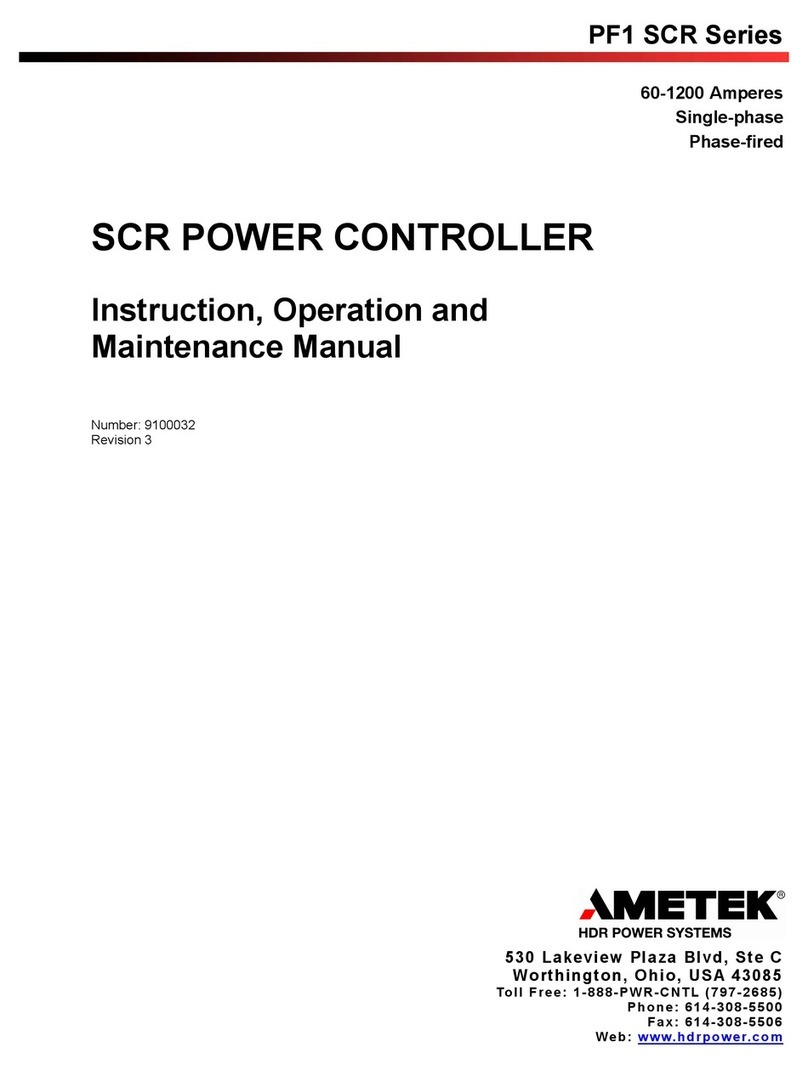
Ametek
Ametek PF1 SCR Series Instruction, Operation and Maintenance Manual

Centork
Centork 480 Series TECHNICAL REPORT
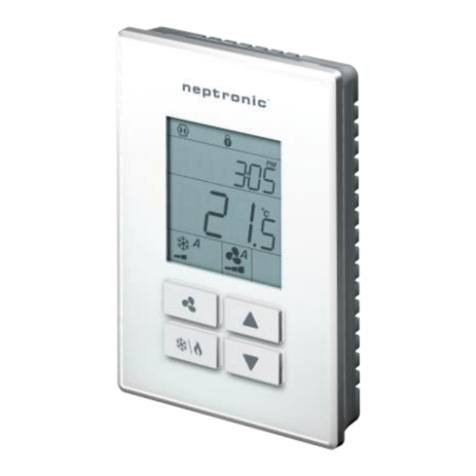
Neptronic
Neptronic TSUB00 Series Specification and installation instructions
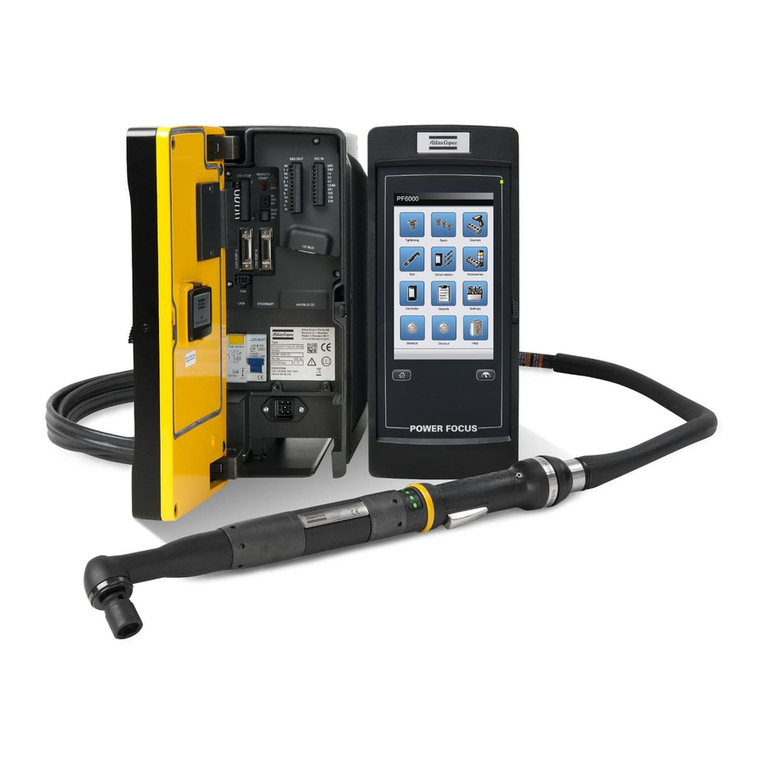
Atlas Copco
Atlas Copco POWER FOCUS 6000 Pocket guide
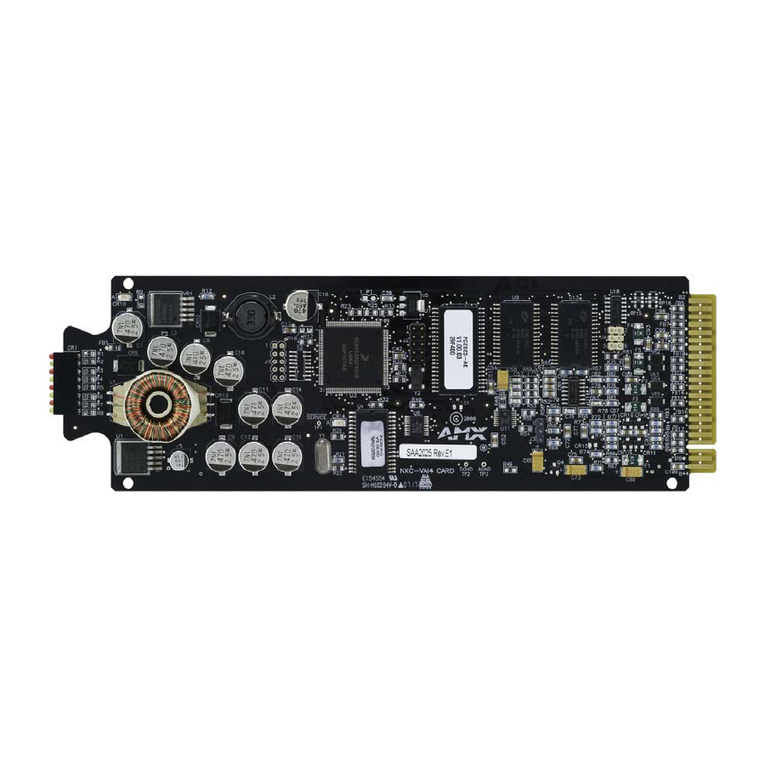
AMX
AMX NXC-VOL4 installation guide