FORSTA FILTERS 180 Series User manual

TABLE OF CONTENTS
FILTER BASICS ............................................................................................................ 1
Figure 1: 180 Series Filter –General Layout .................................................................................. 1
Figure 2: 180 Series Filter –Assembled View ................................................................................. 1
Figure 3: 180 Series Filter –Exploded View ................................................................................... 1
QUICK START GUIDE ................................................................................................... 2
Figure 4: 180 Series Filter –Quick Start Guide................................................................................ 2
INSTALLATION REQUIREMENTS ................................................................................... 3
Figure 5: 180 Series Filter –Installment Layout.............................................................................. 3
Couplings ......................................................................................................................................................... 3
Flush Line......................................................................................................................................................... 3
Hydraulic Connections..................................................................................................................................... 4
Hydraulic Piston............................................................................................................................................... 4
FILTER PERFORMANCE ................................................................................................ 4
Normal Operation............................................................................................................................................ 4
Figure 6: 180 Series Filter –Normal Operation............................................................................... 4
Backwash Cycle................................................................................................................................................ 5
Figure 7: 180 Series Filter –Backwash Cycle .................................................................................. 5
FLOW & PRESSURE REQUIREMENTS ............................................................................. 6
Figure 8: 180 Series Filter –Valve Flow Rates................................................................................. 6
MAINTENANCE & SPARE PARTS ................................................................................... 6
Startup............................................................................................................................................................. 6
Shutdown......................................................................................................................................................... 6
Periodic Maintenance ..................................................................................................................................... 7
Figure 9: 180 Series Filter –Inspection ........................................................................................... 7
Particle Remover ............................................................................................................................................. 8
Figure 10: 180 Series Filter –Particle Remover .............................................................................. 8
Spare Parts....................................................................................................................................................... 9
Figure 11: 180 Series Filter –2- 5-year Parts Maintenance............................................................ 9
Hydraulic Piston............................................................................................................................................. 10
Figure 12: 180 Series Filter –Hydraulic Piston.............................................................................. 10
Piston Seal Replacement Instructions........................................................................................................... 11
Figure 13: 180 Series Filter –Piston Seal Replacement ................................................................ 11
Troubleshooting Guide.................................................................................................................................. 12
Figure 14: 180 Series Filter –Trouble Shooting ............................................................................ 12
Screen Removal/Installation Instructions ..................................................................................................... 13
Figure 15: 180 Series Filter –Screen Removal .............................................................................. 13
Figure 16: 180 Series Filter –Screen Installation .......................................................................... 14
INSTALLATION & WIRING.................................................................................................... 15
180 Series Filters Wiring................................................................................................................................ 15
Figure 17: 180 Series Filter –EC-2 Wiring..................................................................................... 15
2x180 Series Filters in Parallel....................................................................................................................... 16
Figure 18: 180 Series Filter –2x180 in Parallel ............................................................................. 16
WARRANTY ..............................................................................................................17

1
1: Filter Housing
4: Bushing
Figure 2: 180 Series Filter - Assembled View
Figure 1: 180 Series Filter - General Layout
11: Coarse Screen
Figure 3: 180 Series Filter - Exploded View
5: Housing Seal 6: Screen O-Ring 6: Screen O-Ring 3: Particle Remover 7: Hex Spacer
1: Filter Housing 1.7: HMC Bushing 8: Hydraulic Piston
N5: Coupling
N1: Inlet
2: Filter Screen
1.8: HMC O-Ring
Pressure Gauge Plug
Hydraulic Piston Fitting
Fitting
Pressure Gauge N4: Service Port
K1: Hydraulic Connection
N5: Coupling
K2: Hydraulic Connection
N2: Outlet
N3: Flush Outlet
K3: Hydraulic Connection
N4: Service Port
1: Filter Housing
4: Bushing
11: Coarse Screen 1.7: HMC Bushing 8: Hydraulic Piston
5: Housing Seal 6: Screen O-Ring 6: Screen O-Ring 3: Particle Remover 7: Hex Spacer
1: Filter Housing
2: Filter Screen
1.8: HMC O-ring
FILTER BASICS
The Forsta 180 Series is a self-cleaning screen water filter. The major components include the Filter Housing
(1), Coarse Screen pre-filter (11), Fine Screen filter element (2), Particle Remover (3), Hydraulic Piston (8), and
Backwash Valve (12).
Figure 1: 180 Series Filter –General Layout
Figure 2: 180 Series Filter –Assembled View
Figure 3: 180 Series Filter - Exploded View

2
psi
0
20
40
60
80
100
120
140
160
2.00
3. INSTALLATION OF ISOLATION AND BYPASS
VALVES STRONGLY RECOMMENDED
2.00
3.00 +
2.00
1.50
1.50
2.00 +
1.50
FLUSH
CONTROL PANEL
Filter
INLET OUTLET
Isolation
Valve Isolation
Valve
Bypass
Valve
2' Valve 1.5' Valve
2. INLET PRESSURE MUST REMAIN
ABOVE 40 PSI (2.5 BAR) DURING BACKWASH
1. FLUSH PIPING MUST BE
OVERSIZED
TO PREVENT BACK-PRESSURE IN
THE HYDRAULIC MOTOR CHAMBER.
AVOID EXCESSIVE ELBOWS AND
ELEVATION GAIN. PIPE FITTING AND
NIPPLE CANNOT BE PLASTIC,
PREFERRED STAINLESS STEEL
FOR MAX INTERNAL DIAMETER
QUICKSTART GUIDE
Figure 4: 180 Series Filter –Quick Start Guide

3
Filter
INLET OUTLET
Differential
Pressure
Gauge
Isolation
Valve Isolation
Valve
FLUSH
Bypass
Valve
Figure 4: 180 Series Filter - Installation Layout
INSTALLATION REQUIREMENTS
180 Series filters may be mounted directly on the inlet (N1) and outlet (N2) flanges, and positioned in any
orientation. As shown below in figure 4, isolation valves should be installed at the inlet and outlet, and a
bypass valve should be installed between the flanges. This will allow the filter to be taken offline without
disruption to water flow.
Figure 5: 180 Series Filter –Installment Layout
There should be adequate clearance around the filter to allow for easy maintenance access, including a
minimum of 24” from the back (piston side). The minimum clearance on the front (cover) depends on the
model. There must be enough room to remove the coarse screen and fine screen periodically.
Couplings
It is recommended to use the 1” threaded half couplings (N5) for air bleed-off during startup, and draining
when taking the filter offline. Valves may be installed at both locations, otherwise the couplings remain
plugged.
Flush Line
The piping for the flush valve must have no backpressure. It is strongly recommended to use oversized piping
to accommodate this requirement. For example, if the 180 Series filter uses a 2” valve, the recommended pipe
is a minimum of 3”. For a 1” valve, 1.5” or 2” pipe must be used.
To minimize backpressure on the flush line, it is also important to avoid elevation gain in the flush line. Even
small elevation gains will reduce the filter’s ability to perform an effective backwash cycle. If flush water must
be transported to higher elevation, it is recommended to pipe the flush line to a storage tank first, and then
pump it out to higher elevation. Additionally, avoid any sharp bends and shifts of direction to allow a smooth
flow of water during backwash.

4
Hydraulic Connection
Each flanged connection nozzle (N1 & N2) on the 180 Series filter has two ¼” threaded couplings. One may be
used to install a pressure gauge or other sensor equipment. The other ¼” coupling will be used to connect
hydraulic tubing from the differential pressure switch to the filter. The high-pressure line is fitted to the inlet,
and low pressure fitted to the outlet.
Hydraulic Piston
The piston (8) is mounted on the domed end of the filter. ¼” tubing must be installed from the fitting located
on the back of the piston to the hydraulic connection (K3) on the flush outlet (N3). A filter is installed on the
hydraulic tubing to protect the piston.
FILTER PERFORMANCE
Normal Operation
During normal operation of the filter, dirty water enters through the inlet and passes through the coarse
screen. Any abnormally large debris is caught here and prevented from possibly damaging the fine screen or
particle remover.
Water then travels down the center of the filter and is strained across the fine screen. As water passes from
inside the screen to outside, suspended particles are trapped on the fine screen and continue to buildup,
eventually creating a drop in pressure at the outlet of the filter.
Figure 6: 180 Series Filter –Normal Operation
This drop in outlet pressure is monitored by the differential pressure gauge, which at seven PSID (pounds per
square inch differential) sends a signal to the controller to initiate a backwash cycle.

5
Filter
HYDRAULIC MOTOR CHAMBER
(LOW PRESSURE)
INTERIOR OF FILTER
(HIGH PRESSURE)
Backwash Cycle
The controller opens the flush valve, which causes a drop in pressure in the hydraulic motor chamber. This
creates a low-pressure path inside the particle remover, which acts as a vacuum at the end of the suction
nozzles, removing the built-up debris from the inside of the fine screen.
Figure 7: 180 Series Filter –Backwash Cycle
Water flows through the suction nozzles, down the interior of the particle remover, and out the hydraulic
motor. The rapid flow of water through the hydraulic motor forces the entire particle remover to rotate,
enabling each suction nozzle to cover a radial strip of screen. And the pressure difference between the interior
of the filter and the hydraulic motor chamber drives the particle remover toward the hydraulic piston.
The piston depressurizes during the backwash cycle, and expels the volume of water from its chamber. This
acts as a timer, gradually allowing the particle remover to drive the piston rod into the piston, assuring that
the suction nozzles cover the entire surface of the fine screen. When the piston reaches the end of its stroke,
the backwash cycle is complete, and the flush valve closes. Pressure inside the hydraulic motor chamber
normalizes with the rest of the filter, and the piston pushes the particle remover back to its original position.
After the piston and particle remover move back to their original positions, the filter returns to normal
operation. During the entire backwash cycle, the main flow through the filter is never disrupted.

6
FLOW & PRESSURE REQUIREMENTS
Forsta 180 Series filters have a minimum pressure requirement of 40 PSI. This includes any pressure loss
incurred during the backwash cycle. Therefore, the pump performance is a crucial component in determining
whether the filter will perform correctly.
Pump manufacturers will provide the performance data in the form of a pump curve. This is a graph that plots
pressure vs. flow rate. A pump is considered adequate for an application if it can maintain a minimum of 40
PSI while pumping the normal system flow AND the additional flow required during backwash. The additional
flow depends on the filter model and what valve is used.
Valve
Flow Rate
1.5”
100 gpm
2”
220 gpm
Figure 8: 180 Series Filter –Valve Flow Rates
MAINTENANCE & SPARE PARTS
Startup
When pumping water through the Forsta 180 Series for the first time or after it has been empty, it is
important to follow a correct sequence of valve actuation in order to prevent damage to the filter
components.
With both isolation valves closed and the bypass valve open, the correct sequence is:
1. Slowly open the inlet isolation valve letting water flow into the filter. If installed, bleed out the air
through a valve on the top of the filter body. Let the entire filter fill with water before moving to the
next step.
2. Close the bypass valve.
3. Open the outlet isolation valve.
If it is not an option to close the bypass valve momentarily before opening the outlet valve, then both may be
actuated simultaneously.
Shutdown
To remove the filter from operation, reverse the steps used for startup.
1. Close the outlet valve.
2. Open the bypass valve
3. Close the inlet valve, and slowly open the drain valve on the bottom of the filter housing. There will be
residual pressure in the tank still, so use caution when draining.
If it is not an option to close the outlet valve momentarily before opening the bypass, then both may be
actuated simultaneously.

7
Periodic Maintenance
Once a year, or whenever pumps or water flow is shutdown, it is recommended to open and inspect the filter
components. Access to the internal components is through the front cover and service port (N4).
Remove the piston from the back plate and drain the water from the piston chamber. Verify that the piston
rod is moving smoothly in and out, and inspect the piston tip for wear.
3
Figure 9: 180 Series Filter - Inspection
Remove the hydraulic motor from the rest of the particle remover by accessing it through the service port. It
has a left-hand thread, so it must be turned to the right to loosen it.
Remove the screen and particle remover, using the front cover for access. Both should be extracted in one
piece. Separate the two items and inspect both for damage. The screen mesh and bushing should be
inspected for wear.
Also inspect the particle remover rod and suction nozzles for wear.
When taking care of the filter, also perform the same periodic maintenance on the piston itself. A step-by-step
description of disassembling the piston for maintenance and replacement of parts is displayed on page 12 of
the manual. Furthermore, an animated video of the individual parts being assembled and disassembled will be
provided in the “180 series” link on our website

8
3.8 Retainer
3.2 Rod Counter-Nut
3.5 Suction Nozzle
3.1 Rod
3.3 Casing 3.4 Hydraulic Motor
7 Hex Spacer
3.7 End-Cap
Particle Remover
Figure 10: 180 Series Filter –Particle Remover

9
Spare Parts
Spare parts for maintenance
for two years include:
Spare parts for maintenance
for five years include:
Figure 11: 180 Series Filter –2- and 5-Year Parts Maintenance
Part Number
Description
Qty
1.7-180-UHMWPE
Hydraulic Motor Chamber
Bushing
1
1.8-180/LP180
Hydraulic Motor Chamber
Bushing O-Ring
1
16-1/4
Mini Filter
1
17-Fitting/Tubing
Fitting Tube
1
18-D/P-MW-522A
Pressure Differential Switch
1
3.5-180
Suction Nozzles
4-7
4-180-316L/PE
Stainless Steel Bushing
1
5-180/LP180
Housing Seal
1
6-180/LP180
Screen O-Ring
2
7-180-316L-VES
Stainless Steel Spacer
1
8.9-180-316
Piston Shaft Tip
1
8K-180
Piston Repair Kit
1
Part Name
Qty
Plate bushing (1.7)
2
Plate bushing o- ring (1.8)
2
Fine Screen (2)
1
Particle Remover (3)
1
Particle Remover rod (3.1)
1
Suction Nozzles (3.5)
2 Sets
Bushing (4)
2
Cover Seal (5)
2
Screen O-rings (6)
4
Hex Spacer (7)
2
Hydraulic piston (8)
1
Shaft tip (8.9)
2
Piston Seal Kit (8K)
2
Valve (12)
1
Mini-Filter (16)
2
Differential Pressure Gauge (18)
2
Tubing & fitting
2

10
8
8.15
8.11
8.10
8.9
8.8
8.4
8.3
8.2
8.1
8.16 8.14
8.7
8.6
8.12
PART NUMBER
8
8.1
8.2
8.3
8.4
8.6
8.7
8.8
8.9
8.10
8.11
8.12
8.14
8.15
8.16
PART NAME
Hydraulic Piston
Snap Ring
Head Ring
Shaft U-Cup
Head O-Ring
Shaft O-Ring
Pin Holder
Position Pin
Shaft Tip
Piston Shaft
U-Cup Holder
Casing U-Cup
Casing
Casing Cap
Piston Head
180 SERIES PISTON - PART LIST
Head Gasket 8.17
8.17
8
8.15
8.11
8.10
8.9
8.8
8.4
8.3
8.2
8.1
8.16 8.14
8.7
8.6
8.12
PART NUMBER
8
8.1
8.2
8.3
8.4
8.6
8.7
8.8
8.9
8.10
8.11
8.12
8.14
8.15
8.16
PART NAME
Hydraulic Piston
Snap Ring
Head Ring
Shaft U-Cup
Head O-Ring
Shaft O-Ring
Pin Holder
Position Pin
Shaft Tip
Piston Shaft
U-Cup Holder
Casing U-Cup
Casing
Casing Cap
Piston Head
180 SERIES PISTON - PART LIST
Head Gasket 8.17
8.17
Hydraulic Piston
Figure 12: 180 Series Filter –Part List –Hydraulic Piston

11
123
4
7865
9
1. Drain filter body, remove the hex nuts, remove the piston from the filter
2.Unscrew the piston pin and pull out
3. Unscrew the casing cap (8.15) and remove
4.Remove internal piston assembly which consists of parts 8.6 - 8.12
5. Replace casing U-cup (8.12)
6.Replace shaft O-ring (8.6)
7. Replace shaft U-cup (8.3)
8. Replace head O-ring (8.4)
9. Before reassembling, lubricate internal surfaces using silicone grease
10.Ensure everything is clean and lubricated before reversing the steps to
assemble
Piston Seal Replacement Guide
Figure 13: 180 Series Filter –Piston Seal Replacement

12
3. FLUSH PORT
a) Re-pipe the flush line to prevent back-pressure.Remove elbows,
gain, and oversize the pipe.
b) Flush directly to a nearby tank.
c) Increase flush valvesize.
Solution
4. MINI FILTER
Solution
a) Wash the mini-filter.
5. HYDRAULIC PISTON
Solution
a) Open the brass hex caps and inspect therubberseals forwear.They
need to be replaced.
b) Check that the hex cap (8.15) has a small hole through it to allow water
flow out of the positon. If this orifice isobstructed,remove debris.
6. PARTICLE REMOVER
Solution
a) Bypass the filter and relieve pressure. Open the connection clamp,and
remove the top section of the filter. The particle remover should rotate
inside the center oftheplate.
b) Remove the plate and inspect the particleremover.The rod should be
inserted into the bushing near the inlet ofthe filter.There should be
clearance between the suction nozzles and the screen.
c) Check for any severe damage or wearon anyofthe components.
6
3
5
015
7
015
7
7 PSID
0 PSID
015
7
0 PSID
1
2
1
6b
6b
5b
During normal operation, record the pressure reading at inletconnection K1.
35psi, this is yourproblem.
During backwash, record the pressure reading atinletconnection K1(flush
valve open). If the pressure is below 35 psi,thisisyour problem.
Record the pressure reading at flush outletconnectionK3 duringbackwash.
If no pressure gauge is installed on K3, add a tee("T")connectiontoinstallgauge.
If the pressure does not read 0 psi duringbackwash,thisisyourproblem.
Inspect mini-filter located on the piston tubing line.Ifthe mini-filterisclogged,
this is yourproblem.
Inspect the hydraulic piston (8). Verify thatthe rod can smoothly move back
and forth, and that the pin moves the entire length ofthe slot.
Inspect the internal components for smooth operation.If the particle remover
is jammed, this is your problem.
1. PRESSURE / 2. BACKWASHPRESSURE
Increase system pressure by:
a) Choking the outlet ofthefilter.
b) Ramping up pump.
c) Replacing pressure gauge if itisdefective.
Solution
4
Filter
HYDRAULIC MOTOR CHAMBER
(LOW PRESSURE)
INTERIOR OF FILTER
(HIGH PRESSURE)
180 SERIES FILTER - BACKWASH CYCLE
Filter
180 SERIES FILTER - NORMAL OPERATION
If the pressure is below
elevation
may
freely
to
Troubleshooting Guide
Figure 14: 180 Series Filter –Troubleshooting

13
34
5
6
1
2
7
1. Relieve any static pressure in the filter body by running a
backwash cycle and turning off the system once the gauge
reads 0 psi. Once at 0psi, open the Coupling (N5). Verify
an internal pressure lowered to atmosphere by looking at
the gauges on the inlet and flush outlet.
2. Drain all excess water from the system through the
hydraulic connection ports, piston connection or service
ports
3. Remove the front plate from the body once all water is
removed
4. Remove the coarse screen from inside the filter body and
set aside for observation later
5. Open the service port furthest to the end of the body and
unscrew the hydraulic motor. For this you will need to brace
the particle remover and rotate the motor clockwise to
remove. The motor is screwed in with left-hand-threading
so ensure you are not tightening the motor even further
6. Remove the fine screen and particle remover all together
by pulling on the screen bar
7. Separate the fine screen and particle remover by sliding
the particle remover out of the screen
Screen Removal Instructions
Figure 15: 180 Series Filter –Screen Removal

14
5
7
4
6
8
8
3
21
1. Insert the particle remover into the screen,
guiding the rod into the screen bushing.
2. Lubricate the screen O-rings with NSF 61
approved silicone grease before installation .
3. Lift the fine screen with the particle remover as
one unit and insert into the filter body. Guide
the particle remover though the internal
bushing at the opposite end of the filter body.
Lift the screen as you guide it, end of the filter
body
4. Hold the screen by the screen handles and
rotate the screen 180 degrees as you push the
screen into the body, allowing the screen to
center itself. Once aligned, push the screen
until it seals
5. Rotate the particle remover by hand ensuring
unobstructed rotation
6. Install the hydraulic motor sprinkler by
threading (left hand thread) it back into the
particle remover through the service port.
Close and secure the service port
7. Verify the cover seal is properly installed on
the cover O-ring groove and secure the cover
onto the studs with the washers and hex nuts.
Follow a star pattern of fastening nuts
8. Reinstall the unplugged service ports, tighten
down, verify they are all secure, and bring the
filter back online. Inspect for any leaks.
Screen Installation Instructions
Figure 16: 180 Series Filter –Screen Installation

15
Filter
INLET OUTLET
Differential
Pressure
Gauge
Isolation
Valve Isolation
Valve
Bypass
Valve
R W R 1
CPDAM2
DP WIRING
1: P
2: D
180 SERIES FILTER - EC-2 WIRING
VALVE CONNECTIONS
R(left). ------- RED
R(right). ----- BLACK
1. -------------- WHITE
DP CONNECTIONS
H - K1 (High Pressure Inlet)
L - K2 (Low Pressure Outlet)
HL
DP WIRING
1: P
2: D
EC-2-110/220
6
8
12
18
24
2
30 4
10
8
6
12
14
16
18
20
25
2
5
10
15
20
30
40
50
60
75
90 0
P
E
R
I
O
D
I
C
(HOURS)
F
L
U
S
H
(SEC)
(SEC)
D
W
E
L
L
R W R 1
CPDAM2
PD DWELL 1 2 ALARM
MANUAL
START/
ADVANCE
COUNTER
RESET
ALARM
RESET
BACKWASH
COUNT
POWER
OFF
ON
OFF 1/4
1/2
1
2
3
4
FLUSH
INSTALLATION & WIRING
180 Series Filters Wiring
Figure 17: 180 Series Filter –EC-2 Wiring

16
FLUSH
Bypass
Valve
INLET
OUTLET
VALVE CONNECTIONS
R(left). ------- RED
R(right). ----- BLACK
1. -------------- WHITE
VALVE CONNECTIONS
R(left). ------- RED
R(right). ----- BLACK
2. -------------- WHITE
DP CONNECTIONS
H - K1 (High Pressure Inlet)
L - K2 (Low Pressure Outlet)
HL
DP WIRING
1: P
2: D
Differential
Pressure
Gauge
VALVE CONNECTIONS
R(left). ------- RED
R(right). ----- BLACK
1. -------------- WHITE
EC-2-110/220
R W R 1
CPDAM2
R W R 1C PDAM2
PD DWELL 1 2 ALARM
MANUAL
START/
ADVANCE
COUNTER
RESET
ALARM
RESET
BACKWASH
COUNT
POWER
OFF
ON
Filter
Isolation
Valve Isolation
Valve
DP WIRING
1: P
2: D
OFF 1/4
1/2
1
2
3
4
6
8
12
18
24
2
30 4
10
8
6
12
14
16
18
20
25
2
5
10
15
20
30
40
50
60
75
90 0
P
E
R
I
O
D
I
C
(HOURS)
F
L
U
S
H
(SEC)
(SEC)
D
W
E
L
L
2x180 Series Filters in Parallel
Figure 18: 180 Series Filter –2x180 in Parallel

17
WARRANTY
Forsta Filters guarantees all self-cleaning water filters, components, and accessories free of defects
for one year from the date of installation, or 18 months from the date of original shipment. Forsta will
replace any part found defective during the warranty period, provided the equipment in question was
handled, installed, and operated in accordance with the operation and maintenance manual and
sound engineering practices. Forsta Filters assumes no liability for incidental or consequential
damage resulting from the use of its products, services, or data. Liability is limited to replacement or
repair of products provided by Forsta Filters, and no agent or sales representative has authority to
extend the warranty period without the express written consent of Forsta Filters, Inc. Shipping
charges for returned equipment will be at the expense of the purchaser, and all returned equipment
must be sent to Forsta Filters
Table of contents
Popular Water Filtration System manuals by other brands
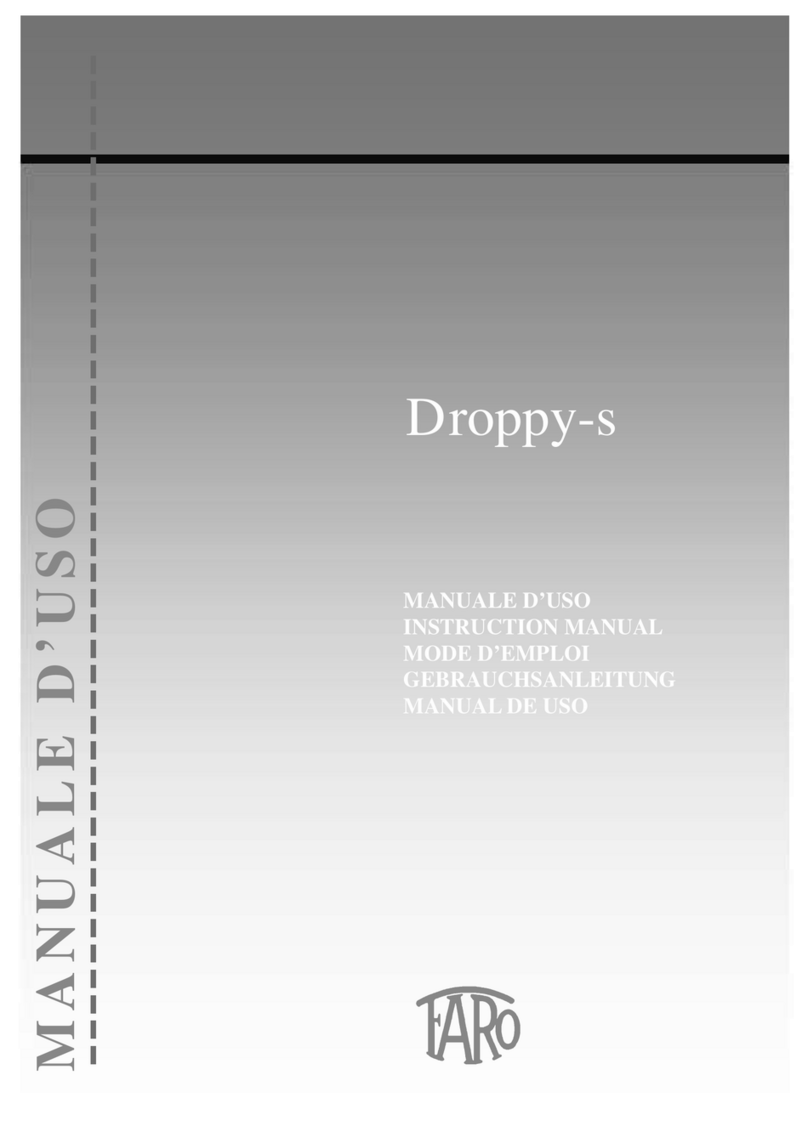
Faro
Faro Droppy-s instruction manual

Dupla
Dupla Perfect Clean PC 1 Instructions for use
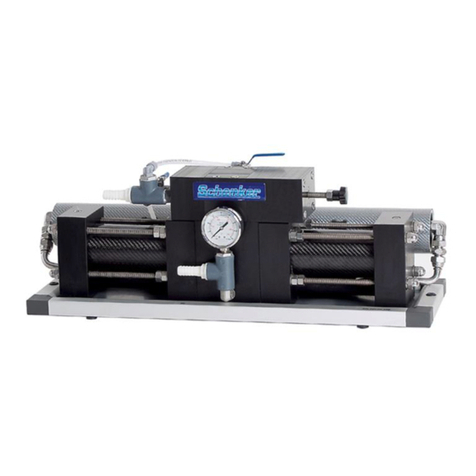
Schenker
Schenker SMART 30 Installation, use and maintenance manual

Watts
Watts OneFlow OF110 Installation, operation and maintenance manual
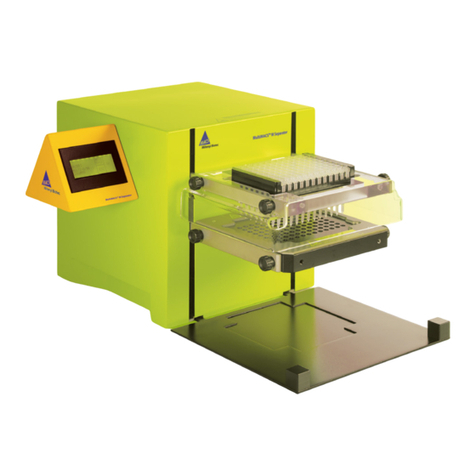
Miltenyi Biotec
Miltenyi Biotec MultiMACS M96 user manual
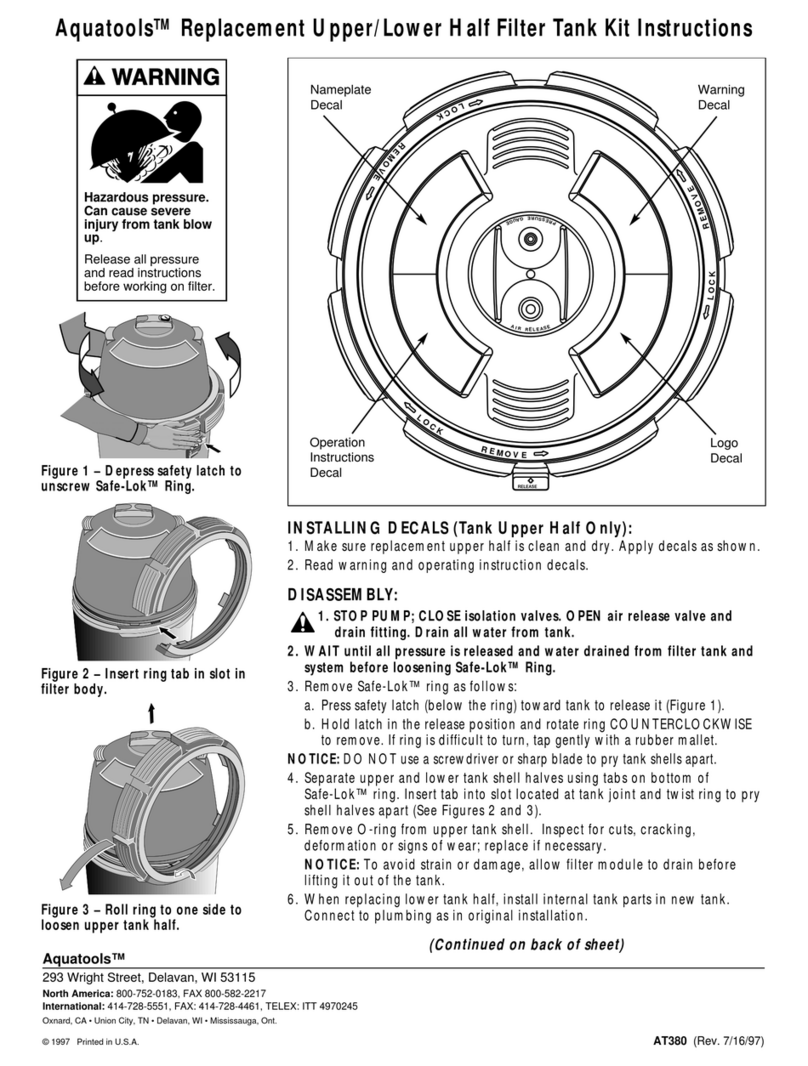
AquaTools
AquaTools Filter Tank Kit manual