FTS Bubbler User manual

EXTREME ENVIRONMENTS. EXTREMELY RELIABLE.
Bubbler
User Manual
1.800.548.4264 | www.ftsinc.com
700-Bubbler-Man Rev 12 13 Feb 2020

i
Contents
1.1 INTRODUCTION.......................................................................................................................... 1
1.2 COMPLIANCE INFORMATION ................................................................................................... 2
1.3 DEFAULT VALUES ....................................................................................................................... 2
1.4 BUBBLER RESPONSE TIMES TO STAGE CHANGES ................................................................. 2
1.5 4-20mA OPTION ......................................................................................................................... 3
1.5.1 4-20MA MINIMUM/MAXIMUM, DEFAULT VALUES, AND UNITS OF MEASUREMENT ........... 4
1.6 SD CARD ...................................................................................................................................... 4
1.7 MAINTENANCE ........................................................................................................................... 4
1.8 SHIPPING THE BUBBLER ........................................................................................................... 4
1.9 DISPLAY AND KEYPAD ............................................................................................................... 5
1.10 CONFIGURING THE BUBBLER................................................................................................... 5
1.11 FIRMWARE UPDATES ................................................................................................................. 5
2.1 PRIOR TO PROCEEDING TO THE SITE ...................................................................................... 6
2.1.1 EQUIPMENT ............................................................................................................................... 6
2.2 SITE SELECTION .......................................................................................................................... 6
2.3 MOUNTING ................................................................................................................................. 6
2.4 CONNECTORS AND WIRING ..................................................................................................... 7
2.4.1 DATA LOGGER CONNECTIONS ................................................................................................. 7
2.5 DESICCATOR ............................................................................................................................... 8
2.5.1 DESICCANT HANDLING SAFETY PRECAUTIONS....................................................................... 8
2.5.2 MOUNTING THE FTS SUPPLIED DESICCANT AIR DRYER ........................................................ 9
2.5.3 REPLACING THE DESICCANT................................................................................................... 10
2.6 CONNECTING AND INSTALLING THE ORIFICE LINE............................................................. 11
2.6.1 USING THE SWAGELOK® FITTING ......................................................................................... 12
2.7 POWER CONNECTIONS ........................................................................................................... 14
3.1 KEYPAD ...................................................................................................................................... 15
3.2 SCREENS, MENUS AND OPERATING THE USER INTERFACE................................................ 15
3.2.1 EDITING A MENU ITEM ........................................................................................................... 16
3.3 STATUS SCREEN........................................................................................................................ 16
3.3.1 OFFSET...................................................................................................................................... 16

ii
3.3.2 FAULT........................................................................................................................................ 16
3.4 CONDUCTING A MANUAL PURGE.......................................................................................... 17
3.4.1 LINE HIGH DETECTED DURING PURGE.................................................................................. 17
3.4.2 BLEEDING THE TANK............................................................................................................... 17
3.5 CONFIGURING THE BUBBLER USING THE BUBBLER INTERFACE....................................... 18
3.6 SETTING THE STAGE................................................................................................................. 18
3.6.1 USING THE 4-20 MA OPTION TO CONFIGURE STAGE.......................................................... 19
3.7 SETUP MENU............................................................................................................................. 20
3.8 DIAGNOSTICS............................................................................................................................ 21
3.8.1 UPDATING FIRMWARE............................................................................................................. 21
4.1 SETUP GENERAL INFORMATION ............................................................................................ 24
4.2 SENSOR TAB.............................................................................................................................. 25
4.3 STAGE TAB................................................................................................................................. 25
4.4 SETUP TAB................................................................................................................................. 26
4.5 PURGE TAB................................................................................................................................ 27
4.6 SAVE CONFIGURATION............................................................................................................ 28
4.7 BUBBLER SENSOR SCREEN ..................................................................................................... 28
4.7.1 CONDUCT A MANUAL PURGE ................................................................................................ 29
4.7.2SET STAGE AND CALCULATE/CLEAR OFFSET ......................................................................... 29
4.8 SETTING THE BUBBLER’S TIME ............................................................................................... 32
5.1 STANDARD SDI-12 MEASUREMENT COMMANDS ................................................................ 33
5.1.1 SDI -12 MEASUREMENT COMMAND CODES......................................................................... 35
5.1.2 CONDUCTING A PURGE USING THE M7 COMMAND ........................................................... 35
5.2 EXTENDED (X) COMMANDS .................................................................................................... 36
5.2.1 REQUIRED FORMATTING ELEMENTS ..................................................................................... 36
5.2.2 SETTING THE BUBBLER’S DATE AND TIME ............................................................................ 36
5.2.3 X COMMANDS LIST.................................................................................................................. 37
B.1 MECHANICAL INDICATORS ..................................................................................................... 42
B.2 MEASUREMENT VALUE FAULT INDICATOR........................................................................... 42
B.3 DATA INDICATORS ................................................................................................................... 43
B.4 BUBBLER STATUS SCREEN FAULT INDICATORS ................................................................... 46

700-Bubbler-Man Rev 12 13 Feb 2020 Page 1/51
GENERAL
1.1 INTRODUCTION
The FTS Bubbler is an SDI-12 user configurable system for accurately measuring water stage in
streams and reservoirs using pressure differentials. It is a self-contained, sealed system that
includes an air compressor, control electronics and a high accuracy pressure sensor for measuring
water levels. It must be used with a desiccator (see section 2.5) and can be connected to any SDI-12
capable data logger or data collection platform (DCP) using the SDI-12 Data Terminal Block for data
logging capability. The FTS Bubbler also has the option to output the level value as a 4-20mA signal.
Figure 1-1: Bubbler components
The system forces air at a continuous rate through an orifice line, the end of which is mounted at a
known, fixed position. A sensor measures the pressure required to maintain the air flow down the
orifice line such that bubbles emerge from its end, compares that to atmospheric pressure, and
computes the stage level (water depth). Any change in water level causes the air pressure in the
orifice line to vary resulting in updated stage levels.
FTS’ proprietary design allows for a larger orifice (18 times larger than the standard metering valve
orifice of 0.035mm). Not only does this minimize fouling of the manifold but it also allows the purge
to flush particulates throughout the entire system from the compressor valve to the orifice line end
fitting. The purge is achieved without bypassing a portion of the system, as systems which use a
metering valve must do. This results in highly accurate readings, even in environments with high
humidity or containing airborne particulates.
Compressor Air Intake
Outlet/Orifice Line Connection
Data Terminal Block
Power Terminal Block
Mounting
plates
Display
Keypad
Part#18729: Barbed
desiccant line inlet
fitting

700-Bubbler-Man Rev 12 13 Feb 2020
Page 2/51
1.2 COMPLIANCE INFORMATION
This device complies with Part 15 of the FCC Rules. Operation is subject to the
following two conditions:
(1) this device may not cause harmful interference, and
(2) this device must accept any interference received, including interference that
may cause undesired operation.
Le présent appareil est conforme à la partie 15 des règlements de la FCC. L'exploitation est
autorisée aux deux conditions suivantes :
(1) l'appareil ne doit pas produire de brouillage, et
(2) il doit accepter toute interférence reçue, notamment celles pouvant entraîner un
dysfonctionnement.
This equipment may be operated in the USA and Canada.
This device complies with Australian and New Zealand requirements specific to EMC,
telecommunications and electrical safety.
1.3 DEFAULT VALUES
The Bubbler is shipped with the following default values:
SDI-12 address
0
Bubble rate (per minute)
60
Purge Pressure
90 psi
Stage Units
Feet
Sample period
8 seconds
Temperature
F
4mA (min)
0 feet
20mA (max)
69.2 feet
1.4 BUBBLER RESPONSE TIMES TO STAGE CHANGES
The following table shows the response time for the Bubbler to recover from a stage change at
different bubble rates. Note that response time may vary slightly under different conditions (battery
charge levels, extreme ambient temperatures, etc.)
Bubbler Rate
Response time (3 ft rise)
30 bubbles/min
28 seconds
45 bubbles/min
15 seconds
50 bubbles/min
14 seconds
60 bubbles/min
11 seconds
120 bubbles/min
7 seconds

700-Bubbler-Man Rev 12 13 Feb 2020
Page 3/51
1.5 4-20mA OPTION
The Bubbler-has an optional 16 bit 4-20mA output with a resolution of 0.37 µA. A measurement
scale is determined by inputting the minimum and maximum water levels which correspond to 4mA
and 20 mA outputs respectively. The measured current signal is translated into a level
measurement based on the linear relationship between the minimum and maximum levels and the
corresponding current output. The process variable that appears on the 4-20 mA output is the
average stage value calculated by the Bubbler. Note that the process variable (level) and 4-20mA
output are only updated when an SDI-12 measurement command is received
Example:
The Minimum level is 10 feet (4mA); the maximum level is 30 feet (20 mA). A signal output of
12mA (half way between 4 mA and 20 mA) would correspond to a level measurement of 20
feet.
Because the relationship between the level variable and the 4-20mA signal is scaled based on the
range of the minimum and maximum levels, the smaller the range the more precise the level
measurement will be.
The 4-20mA output can be connected to a 4-20mA input on a SCADA system, PLC or chart plotter.
The output from the Bubbler is connected to the SCADA equipment as shown in the following
diagram. The output is isolated from the SDI-12 power supply and relies on current loop to provide
power to the output circuitry.
The 4-20mA output can be validated using a DMM or the SCADA equipment to measure the output
current. It is recommended to use a 6 ½ digit multi-meter for best results.
The expected output current can be determined using the following equation:
Analog Output (mA) = (Analog Slope * Stage) + Analog Offset
New values for the analog slope and analog offset can be determined using the following equations:
Analog Slope = 16/(Max Stage – Min Stage)
Analog Offset = 4 – (Analog Slope * Min Stage)
In which:
Max Stage is the maximum stage expected at the site, represented by a 20mA output.
Min Stage is the minimum stage expected at the site, represented by a 4mA output.
Minimum and Maximum stage

700-Bubbler-Man Rev 12 13 Feb 2020
Page 4/51
1.5.1 4-20mA MINIMUM/MAXIMUM, DEFAULT VALUES, AND UNITS OF MEASUREMENT
The minimum and maximum default values are:
4mA
0 feet
20mA
69.2 feet
These defaults can be adjusted from the Bubbler’s front panel (section 3.6) or using SDI-12 X
Commands (section 5.2.4) to modify the analog offset and analog slope respectively.
If the units of measurement are changed, either through the Bubbler’s front panel or using SDI-12
commands, the minimum and maximum values will be automatically converted to the new unit of
measurement (e.g. the initial unit of measurement was feet with a minimum and maximum levels
of 5 and 20. Units of measurement were changed to meters. The minimum and maximum levels
will automatically be changed to 1.52 and 6.09).
1.6 SD CARD
The Bubbler has an FTS supplied internal SD card which is used for service and factory logs. This SD
card has been tested to work in the environmental conditions in which the Bubbler is designed to
operate. Replacing it with a non-FTS approved, standard SD card can cause reduced or lost data in
the service and factory logs.
The Bubbler’s SD card stores data independently from the data logger and as such, is timestamped
by the Bubbler. Transmitted data will be timestamped in accordance with the data logger’s clock.
SD card log entries will only be timestamped if the Bubbler’s date and time are set using the “Set
date and Time X-command (see section 5.2.2).
IMPORTANT! The Bubbler’s timestamp is cleared if the Bubbler has been powered off
and must be reset once power is restored.
1.7 MAINTENANCE
The Bubbler itself requires little maintenance. During site visits, inspect the Bubbler, all power and
hose fittings and periphery equipment for signs of damage and to ensure the station setup has
maintained its integrity. Inspect the colour of the desiccant in the desiccator and replace if it is
saturated. Details of the FTS supplied desiccator and desiccant are found in section 2.5. If using a
different desiccator, refer to its operating instructions. It is recommended to bring extra desiccant
on site visits. Should the Bubbler not be operating as expected, contact FTS Support for assistance
and guidance. FTS suggests Bubbler maintenance should be conducted by factory trained
personnel.
1.8 SHIPPING THE BUBBLER
Prior to shipping the Bubbler, bleed the compressor tank (Section 3.4.2) and remove the desiccant
line inlet fitting (Part # 18729). See Figure 1-1 and Section 2.5.

700-Bubbler-Man Rev 12 13 Feb 2020
Page 5/51
1.9 DISPLAY AND KEYPAD
The front panel has a display and keypad which is used to view information and perform specific
actions (purge, set stage, setup, and diagnostics). The display will normally be off in power save
mode. Pressing any key will display the status screen. The arrow keys are used to navigate through
the different functions and configuration parameters. Refer to Chapter 3 for details of menu items.
The front panel allows the user to do the following:
•Set purge pressure
•Conduct a manual purge
•Manually bleed the tank
•Set stage
•
Set stage units
•Set minimum and maximum 4-20 mA values
•Set bubble rate
•Set averaging duration
•Set temperature units
•
Set the SDI-12 address
1.10 CONFIGURING THE BUBBLER
The Bubbler can be configured through its front panel using the Set Stage and Setup sub-menus
(Chapter 3) or through a data logger. The Bubbler will retain the last input configuration whether set
through the Bubbler or the data logger. However, changes made using the Bubbler’s interface will
not be reflected in the data logger, unless it is an FTS Axiom Datalogger.
If using an FTS Axiom Datalogger, configuration can be done through the Axiom using the Bubbler
sensor extension. Configuration changes using the Bubbler’s screen will also be valid. See Chapter
4 for details.
Note that certain features, those which require a real time clock, can only be set through a data
logger. Refer to Table 1-1.
Table 1-1: Configuration using Bubbler vs data logger
FUNCTION
BUBBLER
DATA
LOGGER
Set stage
Set stage units
Set bubble rate
Set temperature units
Set averaging duration
Perform manual purge
Set scheduled purge
Set scheduled stage collection
Set date and time1
1.11 FIRMWARE UPDATES
Periodically, the Bubbler’s firmware may need to be updated. In that event, FTS will issue a
notification with instructions on how to conduct the update.
1This sets the Bubbler’s date and time which is used on the time stamp of the Bubbler’s SD card. It does not affect the time
stamp of sent data or the timing of scheduled events as those are controlled by the data logger and the telemetry in use.

700-Bubbler-Man Rev 12 13 Feb 2020
Page 6/51
INSTALLATION
2.1 PRIOR TO PROCEEDING TO THE SITE
2.1.1 EQUIPMENT
Unpack the Bubbler and conduct a visual inspection for any signs of shipping damage. If any
damage is found, contact FTS Service and Support immediately. Retain the shipping container to
transport the Bubbler to the site or to return the unit to FTS should damage have occurred during
shipping.
For the Bubbler
For mounting the air dryer
•3/32” flathead screwdriver (for the terminal block
screws)
•11/16 open-ended wrench
•5/8 open-ended wrench
•Teflon tape
•Additional tools and hardware for mounting the Bubbler
in accordance with your site characteristics.
•Drill with bits
•9/16 open-ended wrench
•Flathead screwdriver
•Teflon tape
2.2 SITE SELECTION
The Bubbler should be mounted adjacent to the body of water to be measured, typically in a
hydrology shack or gauging house. The position of the Bubbler should allow for a continuous
downward run of the orifice line to its final termination point. The water should be relatively calm
and where sediment accumulations are not likely to block the orifice.
The orifice line with a terminating orifice should be laid out into the water so that the stream ward
end will remain in a fixed position and at a depth that will not be exposed at low stage. Should the
orifice line need to be installed in an area with high currents, it should be installed in a static tube.2
2.3 MOUNTING
When mounting the Bubbler these guidelines should be followed:
•The Bubbler should be firmly bolted to a flat/even vertical surface using all four mounting
plates located on the corners of the enclosure.
•Screws for the mounting plates should be tightened until the play is gone but not to the
point that the screw is forming any kind of indentation or depression in the mounting plate.
Overtightening can cause the mounting plates to fail over time. The connectors and outlets
should be pointing down.
•The Bubbler must have a dedicated desiccator and air intake path; do not use one desiccator
for multiple Bubblers (this can cause spikes in the data). Additionally, the entire air intake
path from the desiccator’s air intake line to the Bubbler’s air intake fitting should have no
restrictions (e.g. check valves) as this can cause spikes in the data;
2Refer to USGS publications TM3-A7 Stage Measurement at Gaging Stations http://pubs.usgs.gov/tm/tm3-
a7/pdf/tm3-a7.pdf and TWRI_8-A2 “Installation and Service Manual for U.S. Geological Survey Meters”
http://pubs.usgs.gov/twri/twri8a2/html/pdf.html

700-Bubbler-Man Rev 12 13 Feb 2020
Page 7/51
•The bottom of the Bubbler should be free of obstruction so that the orifice line has a free
downward run.
•Ensure the orifice line is not bent or crimped.
•Do not mount the Bubbler so that it rests on a horizontal surface such as a tabletop or shelf
as this can bend the orifice line permitting moisture to accumulate and preventing the
correct operation of the device.
2.4 CONNECTORS AND WIRING
When installing the Bubbler connections, do not apply power until all other connections are made.
The following connections should be made:
1. Data connections (SDI-12)
2. Desiccant assembly
3. Orifice line
4. Power
.
Figure 2-1: Bubbler Connections
2.4.1 DATA LOGGER CONNECTIONS
The Bubbler’s interface allows for SDI-12 or 4-20mA connections to a data collection platform (DCP)
in accordance with the DCP’s capabilities. These connections are made using the removable data
terminal block on the bottom of the Bubbler.
Connect the leads to the data logger in accordance with the manufacturer’s directions. Connect the
flying leads from the data logger to the Bubbler’s data terminal strip as shown.
Insert the terminal block into the Bubbler’s connector port and secure.
Figure 2-2: SDI-12 Connections
SDI-12 Connections
4-20mA Connections
Pin
Description
Pin
Description
1
12 VDC
3
Ground
2
Serial data
4
4-20mA positive
3
Ground
5
4-20mA negative
6
Chassis ground
6
Chassis ground
1
2
3
4
5
6
PINS
Barbed hose fitting
for desiccant hose
Bubbler outlet
(orifice line
connection)
Bubbler air
intake fitting
Data
Power

700-Bubbler-Man Rev 12 13 Feb 2020
Page 8/51
2.5 DESICCATOR
An external desiccator must be connected to prevent the accumulation of moisture in the
compressor manifold and throughout the system. Moist air drawn into the Bubbler will degrade the
measurement accuracy and damage the compressor and manifold. Desiccant air dryers and
mounting brackets are available from FTS (see Appendix D for part numbers) and
mounting/maintenance details are found in Sections 2.5.1 and 2.5.2 respectively. For other
desiccators, follow the manufacturer’s directions with respect to handling, mounting, maintenance,
and disposal of the desiccator and desiccant.
The desiccator should be mounted close to the Bubbler to minimize the length of the output hose.
Ensure there are no kinks or bends in the output hose.
A barbed hose fitting for the desiccant hose is shipped with the Bubbler and must be attached to the
Bubbler’s air intake fitting (see Figure 2-1). Wrap Teflon tape around the Bubbler’s air intake fitting,
and then screw on the barbed hose fitting finger tight. While holding the Bubbler’s air intake fitting
steady with the 11/16 wrench, use the 5/8 wrench to tighten the barbed hose fitting (about 2 turns).
Do not turn or apply torque to the Bubbler’s air intake fitting.
IMPORTANT! Applying torque to the Bubbler’s air intake fitting can displace the O-ring
resulting in the possibility of moisture entering the manifold.
2.5.1 DESICCANT HANDLING SAFETY PRECAUTIONS
The desiccant supplied with the FTS supplied air dryer is blue silica gel. When handling observe the
following recommended safety precautions:
CAUTION:
•Inhalation may irritate the respiratory tract.
•Avoid breathing of the dust or prolonged contact with the skin.
•Use adequate ventilation.
HANDLING
•Wear gloves.
•Wear a NIOSH/MSHA approved dust mask.
•Wear long sleeved clothing.
•If transferring material into flammable solvents, use proper grounding to
avoid static electrical sparks.
FIRST AID
•
If material gets into the eyes, hold eyelids apart and flush with water for a
least 15 minutes.
•If material gets onto the skin, wash with soap and water.
•If inhaled remove to fresh air and seek medical attention for any difficulty
breathing.
•If swallowed, administer plenty of water and seek medical attention.
REGENERATION •It is NOT recommended to regenerate/reheat BLUE SILICA GEL
DISPOSAL
•Comply with local regulations for disposal.
•Store in an airtight, moisture-proof container in a cool dry place until disposal.

700-Bubbler-Man Rev 12 13 Feb 2020
Page 9/51
2.5.2 MOUNTING THE FTS SUPPLIED DESICCANT AIR DRYER
Refer to the manufacturer’s instructions for important details and safety information about the air
dryer and desiccant.
You will need the following tools to mount the air dryer:
•Drill with bits
•9/16 wrench
•Flathead screwdriver
•Teflon tape
IMPORTANT INSTALLATION POINTS:
•Observe the safety precautions when using the blue silica gel desiccant (section 2.5.1)
•Each Bubbler must have a dedicated desiccator and air intake path; do not use one
desiccator for multiple Bubblers (this can cause spikes in the data);
•The entire air intake path from the desiccator’s air intake line to the Bubbler’s air intake
fitting should have no restrictions (e.g. check valves) as this can cause spikes in the data;
•The air dryer should be installed as close as possible to the Bubbler’s air intake with the air
flow going in the direction of the arrow (see Figure 2-4);
•There should be no kinks or tight bends in the desiccant hose;
•There should be no obstruction above the mounting bracket to permit the insertion and
removal of the air dryer.
1) Using the supplied screws, mount the bracket.
2) Depress the release button on the clamp ring and rotate the housing to remove the protective
metal bowl.
3) Maintain a firm grip on the bowl and separate the top housing from the bowl.
4) Keep the central tube covered to prevent silica gel from entering it. Fill the bowl with desiccant
to 1/8” below the inner step of the bowl. Shake or tap the bowl to settle the desiccant and add
more desiccant if required. Refer to Figure 2-3.
Figure 2-3: Filling the bowl with desiccant

700-Bubbler-Man Rev 12 13 Feb 2020
Page 10/51
5) Firmly replace the top housing ensuring the bowl is evenly and fully seated. Do not tip the bowl
during this step. If any silica gel pellets lodge in the gaskets, they can prevent the bowl from
seating properly or forming a seal.
6) Wrap Teflon tape around the threads of the barbed desiccant adaptor fitting.
7) Remove the shipping plugs from the inlet and outlet sockets.
8) Screw the desiccant adaptor (part# 19469) into the air dryer’s outflow socket. Screw in finger
tight and then tighten two turns with a wrench.
9) Insert the inlet vent (part # 20625), tighten finger tight and turn 1 full turn with a screwdriver.
Figure 2-4: Air dryer with inlet vent and desiccant adaptor in place
10) Place the desiccant dryer in the mounting bracket.
11) Push the desiccant tubing firmly onto the dryer’s barbed desiccant adaptor fitting, ensuring a
tight seal.
12) Attach the desiccant hose to the barbed hose fitting on the Bubbler’s air intake (see Figure 2-2).
2.5.3 REPLACING THE DESICCANT
Observe the silica gel safety handling precautions (section 2.5.1). The silica gel desiccant, visible
through the clear polycarbonate plastic bowl, contains a colour indicator: blue indicates it is dry, and
pink indicates it is wet and needs to be replaced. The frequency of changing the desiccant is
dictated by the individual characteristics of each site and levels of humidity.
Before replacing the desiccant, the Bubbler must be powered off. You may need to remove the
desiccant hose from the air dryer in order to manipulate the top housing.
1) Remove the air dryer from the mounting bracket
2) Open the bowl following steps 2 and 3 in the preceding section.
Shipping
Plug
Inlet vent
Part # 20625
Desiccant
adaptor
Part #19469
AIR FLOW
To Bubbler

700-Bubbler-Man Rev 12 13 Feb 2020
Page 11/51
3) Cover the tube to ensure no pellets can enter, and tip the desiccant out into a clean, sealable
container.
4) Refill and replace the bowl following steps 4 and 5 in the preceding section.
5) Replace the air dryer in the mounting bracket and replace the desiccant hose, if it had been
removed.
6) Supply power to the Bubbler.
2.6 CONNECTING AND INSTALLING THE ORIFICE LINE3
The orifice line should be black polyethylene 3/8” outer diameter, 1/8” inner diameter USGS
approved.
The orifice line should be enclosed in a protective conduit to prevent damage from foot traffic,
animals, debris, etc. The run should be as straight as possible in a continuous downward path to
minimize moisture collection in catenaries. No part of the line should be lower than the line exit in
the water. The run should terminate in a calm area, ideally in the same pool as the outside gauge,
and secured so that the stream ward end with the line outlet will remain in a fixed position and at a
depth that will not be exposed at low stage. The stream ward end should be positioned
perpendicular to the direction of the flow at a slight downward angle.
The use of an orifice fitting on the terminal end of the orifice line is recommended to aid in securing
the line in a fixed position. There are a variety of orifice options available to the consumer
depending on site characteristics and specific agency requirements. FTS offers the USGS Standard
Orifice Fitting (Part #19063) as an accessory.
If the area has high currents, the orifice line should be installed in a static tube. If the waters are
turbulent, a muffler should be used.
Once the orifice line run is securely laid out, connect the orifice line to the Bubbler outlet (refer to
Figure 2-5) and secure it with the provided Swagelok® fitting.
3For a detailed explanation of the installation of an orifice line and static tube, refer to USGS publications:
TWRI_8-A2: Craig, J.D, 1983, “Installation and service manual for U. S. Geological Survey manometers”: U.S. Geological Survey
Techniques of Water-Resources Investigations, book 8, chap. A2. http://pubs.usgs.gov/twri/twri8a2/html/pdf.html
TM3-a7: Sauer, V.B. and Turnipseed, D.P., 2010 “Stage Measurement at Gaging Stations”: U.S. Geological Survey Techniques
and Methods, book 3, chap 7, sect A http://pubs.usgs.gov/tm/tm3-a7/pdf/tm3-a7.pdf

700-Bubbler-Man Rev 12 13 Feb 2020
Page 12/51
DO:
•Use only USGS approved line
•Encase the orifice line in a conduit
•Ensure the line’s run is continuously downward with no dips or swells and no part of the
line’s run is lower than the line outlet
•Place the line outlet in calm water (when possible)
•Ensure the line outlet is secured in place and has a slight downwards tilt
•Install the line outlet perpendicular to the flow in flowing water
•Use a muffler if water is turbulent
DO NOT:
•Splice the orifice line
•Face the stream ward end of the orifice line facing upstream, downstream or upwards in
flowing water
•Mount the line outlet in the wake of an obstruction (boulder, bridge footing etc.)
2.6.1 USING THE SWAGELOK® FITTING4
NOTE: To maintain a tight seal, use the provided Swagelok fitting with a brass ferrule.
ASSEMBLY:
1) Place the nut and ferrules on the line as shown in Figure 2-5 and fully insert the line into the
Bubbler outlet.
IMPORTANT! Ensure the
Swagelok fitting ferrules
are oriented as shown
Figure 2-5: Swagelok fitting orientation
4For a detailed explanation of installing Swagelok fittings refer to “An Installer’s Pocket Guide for Swagelok Tube
Fittings” on the Swagelok website. https://www.swagelok.com/downloads/webcatalogs/en/ms-13-151.pdf
Tapered
section of
front ferrule
Stepped down
portion of
back ferrule

700-Bubbler-Man Rev 12 13 Feb 2020
Page 13/51
2) Screw the nut on until finger tight.
3) Mark the nut at the 6 o’clock position.
4) Use a wrench to tighten the nut one and a quarter
turns (pass the 6 o’clock position once and stop at
the 9 o’clock position).
DO NOT twist the Bubbler outlet. Only
turn the nut.
DISASSEMBLY
1) Mark a line along the back of the nut and Bubbler
outlet. These marks will be used to return the nut to
this position.
2) Use a wrench to loosen the nut.
3) Once maintenance is complete, replace the nuts
and ferrules, and re-insert the line as shown in Step 1
of the assembly instructions.
4) Tighten the nut to the marked position. At this
point, resistance will increase. Tighten the nut
slightly.

700-Bubbler-Man Rev 12 13 Feb 2020
Page 14/51
2.7 POWER CONNECTIONS
The Bubbler requires a dedicated +12VDC power source to operate. This is normally supplied by an
external lead-acid battery. Although the Datalogger supplies some power through the SDI port, it is
only enough to view and operate the Bubbler’s screen. It is insufficient to run the compressor.
If the Bubbler is sharing an external battery source with other equipment, the combined power
draw will need to be considered when calculating the site’s power budget and power requirements.
IMPORTANT! If not using an FTS supplied power cable (Part #18945) between
the battery and the Bubbler, an equivalent power cable should be used. The
power cable should be 14 AWG to a maximum of 8 ft with an integrated 20A
slow blow fuse.
To connect the power cable:
1) Remove the power terminal block from the port
2) Secure the power wires to the appropriate pins
(positive and negative – see Figure 2-4).
3) Connect the power cable to the power source
(positive to positive, negative to negative).
4) Re-insert and secure the power terminal block.
Figure 2-6: Power Connections

700-Bubbler-Man Rev 12 13 Feb 2020
Page 15/51
BUBBLER INTERFACE AND MENUS
The front panel has a display and keypad which is used to configure the Bubbler. When power is
supplied, the start-up screen will display for about 5 seconds before the Status Screen is displayed.
After three minutes of inactivity, the display will enter low power mode and blank out. Pressing any
button on the keypad will display the status screen.
3.1 KEYPAD
The keypad consists of the following buttons used to navigate through the different screens and
menu items:
The keypad consists of the following buttons used to
navigate through the different screens and menu items:
Figure 3-1: Keypad
3.2 SCREENS, MENUS AND OPERATING THE USER INTERFACE
The following diagram illustrates the different screens and menus.
SUB-MENUS
PRESSURE
PURGE
BLEED
STATUS SCREEN*
SITE/FAULT *
STAGE
OFFSET
TANK PSI
MAIN MENU
PURGE
SET STAGE
SETUP
DIAGNOSTICS
STAGE
UNITS
4mA
20mA
Output mA
SLOPE
SITE
ADDRESS
RATE
TEMP F/C
AVG DUR
SDCARD
BATTERY
TEMP
VERSION
UPDATE
DATE
TIME
Up
Down
Left
Right
Select/
Accept
* Normally the Status screen
will display the Site’s name. If a
fault is detected, the Site name
will be replaced with FAULT:
followed by the type of fault (see
Section 3.3.1)
Only shows when
custom units (cu)
are indicated
Figure 3-2: Menu tree
Only shows if it is
a 4-20mA model
Other manuals for Bubbler
2
This manual suits for next models
1
Table of contents
Other FTS Measuring Instrument manuals
Popular Measuring Instrument manuals by other brands
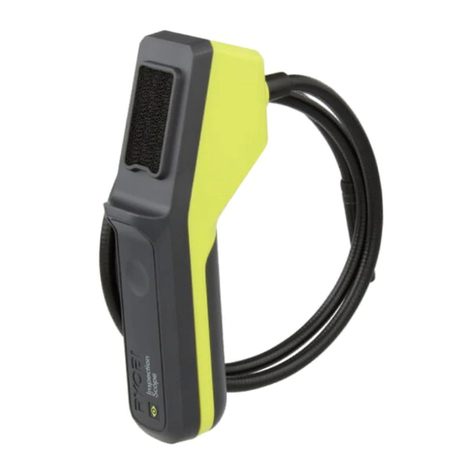
Ryobi
Ryobi ES5000 Operator's manual
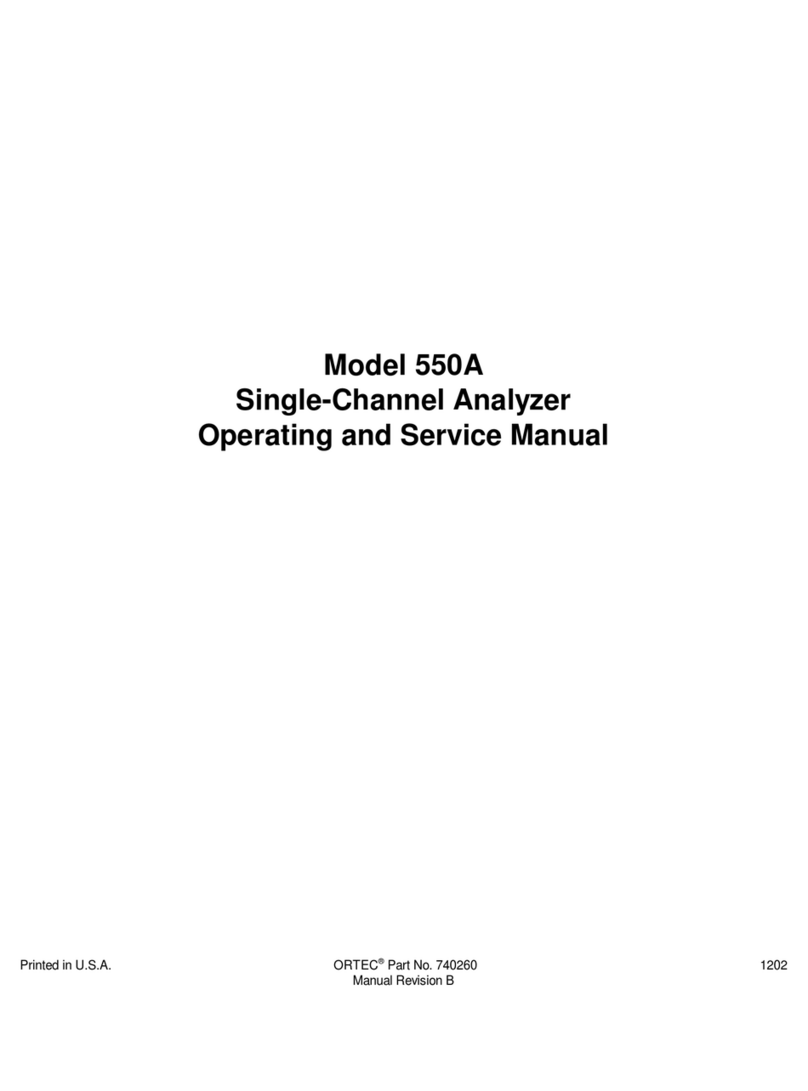
ORTEC
ORTEC 550A Operating and service manual
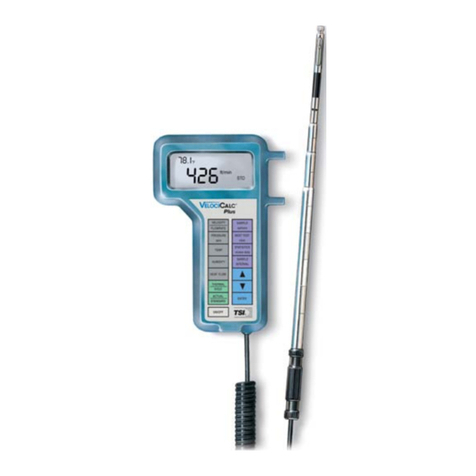
TSI Incorporated
TSI Incorporated VelociCalc Plus 8384 Operation and service manual
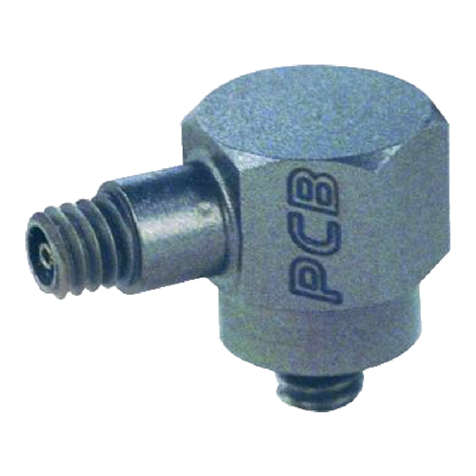
PCB Piezotronics
PCB Piezotronics JM320C15 Installation and operating manual

Kusam-meco
Kusam-meco KM 078 instructions

3am Systems
3am Systems LineScope quick start guide
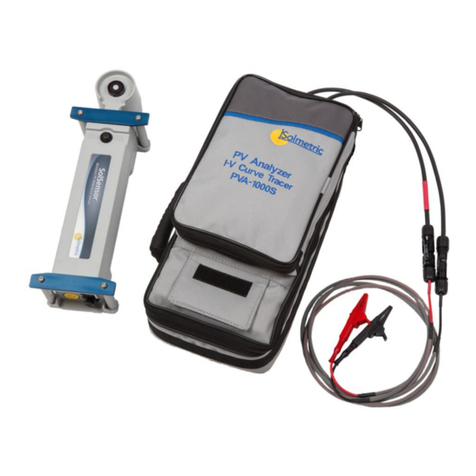
Solmetric
Solmetric PVA-1500V2 Quick reference card
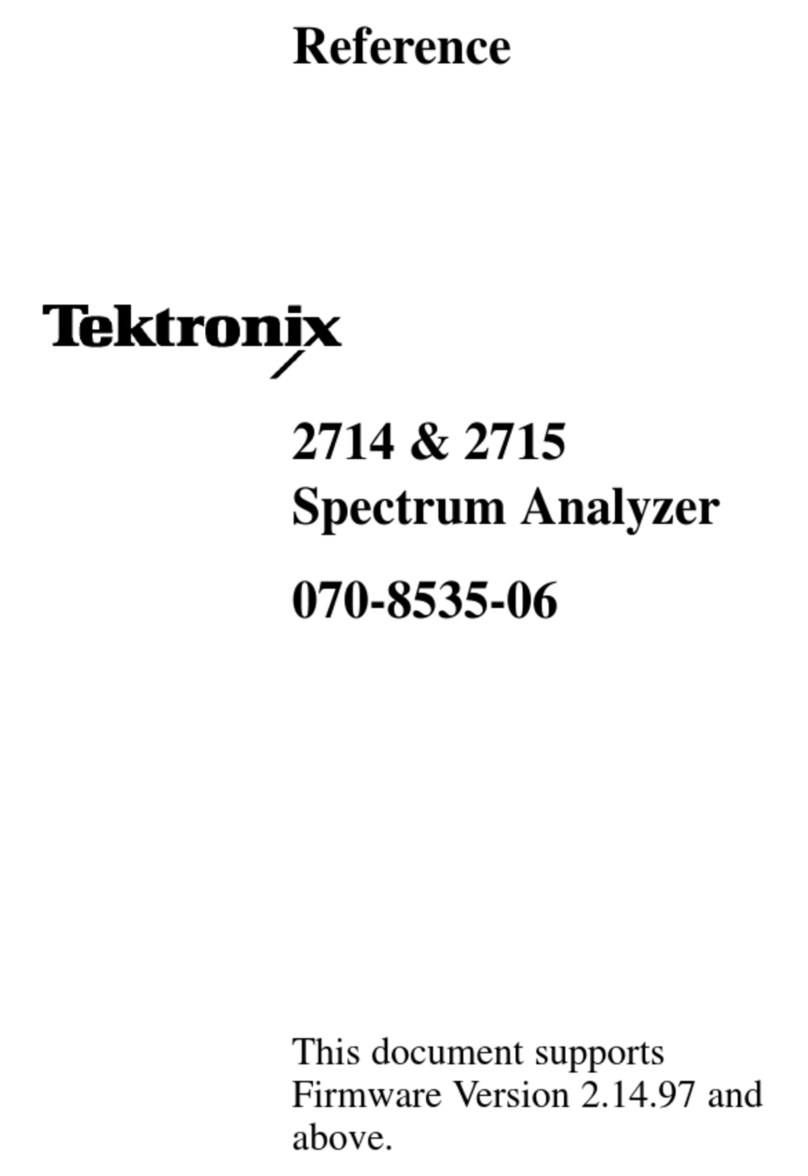
Tektronix
Tektronix 2714 Reference
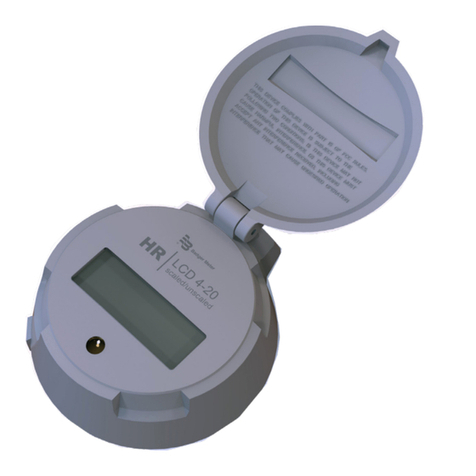
Badger Meter
Badger Meter HR-LCD 4-20 user manual
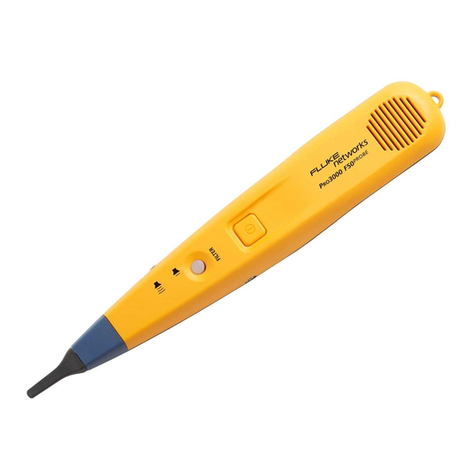
Fluke
Fluke PRO3000 user guide
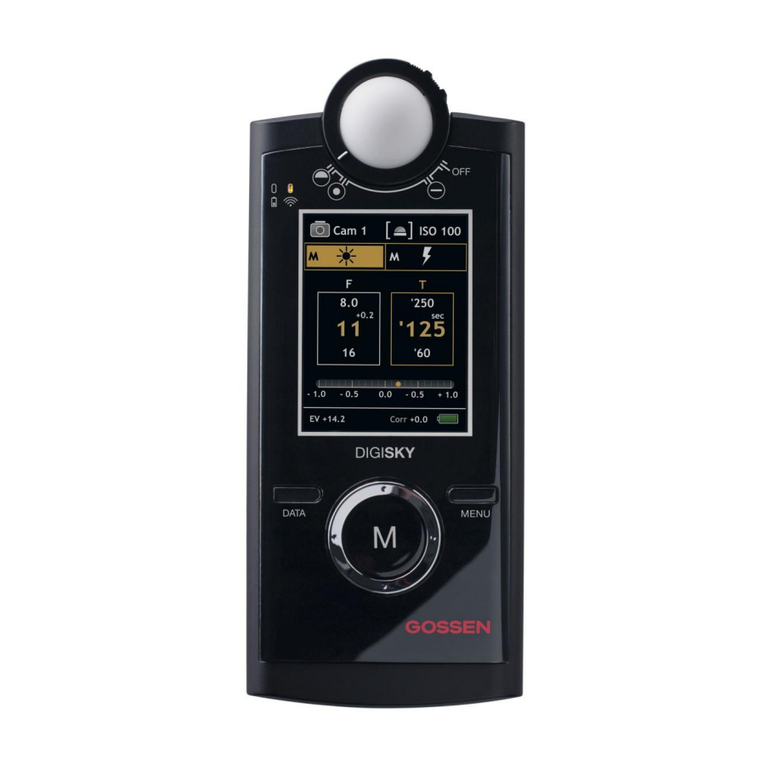
Gossen MetraWatt
Gossen MetraWatt DIGISKY Update manual
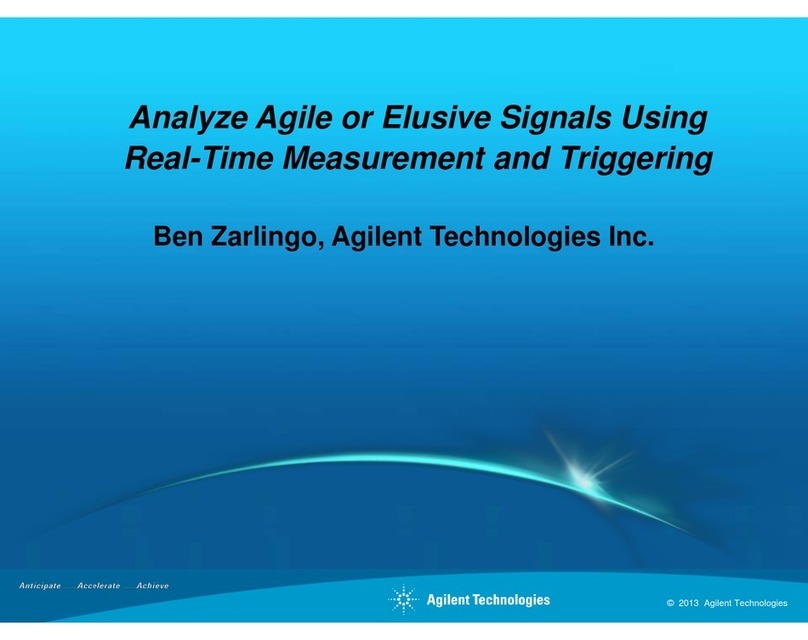
Agilent Technologies
Agilent Technologies Agile or Elusive Signals Using Information sheet