GCS Basyx VAV User manual

Basyx VAV / VVR
Variable Air Volume Controller
Installation Manual
VAV/VVR-IM Revision 3.3
10/07/2020
Global Control Solutions
GCS

Page 2
BASYX VAV / VVR
Variable Air Volume Controller
Table of Contents
Before Installing
3
VAV Board Layout
4
Mounting the Unit
5
New Construction
5
Retrofit
7
Connecting the Power
10
Communications Bus Wiring
11
Setting The Device Address
13
Connecting Temperature Sensors
14
Room Sensor
15
Duct Sensor
16
Connecting Digital Inputs
16
Connecting Digital Outputs
17
Pilot Relays
17
Fan Powered Box Outputs
18
Connecting Analog Output
19
Connecting the Velocity Sensor
20
Operation
21
Basic Troubleshooting
21
Specifications
22
About the BASYX Product Line
23
Appendix 1: BASYX Address Switch Settings
24
Appendix 2: Manufacturer Box Constants
26
Appendix 3: Recommended Cable
32
Warning ( For your Safety )
All electrical connections must be in agreement with local codes ordinances, or the National Electric Code (NEC).
Do not install in areas that experience high levels of electrical interference, moisture or exposure to water.

Page 3
BEFORE INSTALLING
Check contents for any sign of damage. If the VAV assembly is damaged in any way, contact the dealer or seller
immediately.
The BASYX VAV comes ready to mount directly onto the damper shaft using the attached V-Clamp. The VAV
electronics board is housed within the clamshell type enclosure and the entire assembly is attached to the duct with
one sheet metal screw.
If using the BASYX VVR board with a motor other than a BELIMO, contact your GCS dealer to verify compatibility and
power requirements.
Figure 1:
BASYX VAV controller assembly
Figure 2:
BASYX VVR retrofit controller
The VAV controller assembly is designed for use on new construction projects or retrofit of existing variable air
volume terminals where actuators are replaced, i.e. pneumatic conversion, etc. The controller is a self-contained unit
which consists of a plastic enclosure and 3-wire floating damper actuator.
The VVR retrofit controller is used on existing variable air volume terminals where existing 3-wire floating actuators
may be reused. The unit is a snap-track mounted unit, and may be installed in existing VAV unit control enclosures.
Figure 1
shows the VAV controller assembly and
Figure 2
shows the VVR retrofit controller.
Contact Global Control Solutions or your local dealer/distributor if unsure about the compatibility of any existing
actuator or box type.

Page 4
VAV / VVR BOARD LAYOUT
Figure 3:
VAV / VVR Board Layout
The VAV is a single board controller with plug-on terminal strips for all input and output connections.
The board is under the black clamshell cover on the VAV unit, with the right side terminal strips exposed along the
right side of the controller. Remove the cover to expose the entire board, and to make connections to the left
terminals.
The board is a snap-track mounted unit on the VVR, and provides complete access to all terminal strips when
mounted in an existing control enclosure or other NEMA 1 type box.
L
1
L
2
N
O
C
N
O
C
N
O
C
N
O
C
+
-
+
-
+
-
+
-
+
-
R
E
F
4
3
2
1
2
4
V
A
C
H
E
A
T
I
N
G
R
E
L
A
Y
O
U
T
P
U
T
S
A
O
1
1
2
A
N
A
L
O
G
I
N
P
U
T
S
R
S
4
8
5
C
O
M
M
B
U
S
C
W
C
O
M
C
C
W
D
A
M
P
E
R
+
-
+
-
2
1
D
I
G
I
T
A
L
I
N
P
U
T
S
+
-
S
P
A
D
J
+
-
3
F
D
B
K
O
U
T
I
N
G
N
D
G
N
D
+
2
8
A
O
2
+
-
3
R
S
2
3
2
S
E
R
V
I
C
E
P
O
R
T
A
O
2
VELOCITY SENSOR
NOT USED
DIRECT CONNECTION PORT
(
RJ
11
ON ROOM SENSOR
)
OPTIONAL
0
-
10
K DAMPER FEEDBACK
SETPOINT ADJUSTMENT
(
SLIDEBAR ON ROOM SENSOR
)
OVERRIDE BUTTON ON ROOM SENSOR
DIGITAL INPUT
2
DAMPER ACTUATOR
POWER CONNECTION
(
24
VAC
/
DC
)
DIGITAL OUTPUT RELAYS
(
4
SPST
/
N
.
O
.)
MODULATING REHEAT VALVE
(
0
-
10
VDC
)
ROOM
&
DUCT TEMPERATURE
RS
485
COMMUNICATION BUS
V
A
V
/
V
V
R
C
O
N
T
R
O
L
L
E
R
B
O
A
R
D

Page 5
MOUNTING THE UNIT
VAV NEW CONSTRUCTION INSTALLATION
The VAV must be mounted in a relatively clean environment, free from major airborne dust and contaminants
(moisture, oil, etc.). Keep the VAV away from high voltage equipment that might disrupt communications and away
from high vibration equipment. Do not mount the unit near any sources of electromagnetic interference (EMI) or
flammable vapors.
Install the VAV controller on the VAV terminal by placing the opening of the actuator over the damper shaft extended
from the box as shown in
Figure 4
. Make sure that the terminal end of the enclosure is over a flat area of the box, or
a mounting bracket must be used.
Figure 4:
Typical VAV Box Installation
VAV
H
L
ROOM SENSOR
DUCT SENSOR
FLOW
RING
FLOW TAPS
AIR FLOW
AIR FLOW
¼” OD TUBING
3
PAIR CABLE
2
PAIR CABLE
1
PAIR CABLE
VARIABLE AIR VOLUME TERMINAL

Page 6
NEW INSTALLATION CW OPEN DAMPER
The VAV assembly operates whereas the Belimo actuator rotates
CLOCKWISE
to open the damper. To connect the
actuator to the damper shaft:
1.
Turn the damper to the closed position.
2.
Press the black triangular shaped clutch on the right edge of the actuator and
rotate the actuator fully counter-clockwise.
3.
Place the assembly over the damper shaft and hand-tighten the nuts on the
actuator V-clamp.
4.
Attach the assembly to the box or mounting plate by driving a sheet metal screw
through the eyelet on the terminal strip end of the assembly.
3.
Lock the actuator to the shaft by tightening the nuts on the V-clamp.
5.
Remove the VAV cover and set the address DIP switch as required per
Appendix 1
.
6.
Connect the low voltage power to the unit per the next section.
7.
Connect temperature sensors per additional sections of this manual.
8.
Connect fan or heating stages per additional sections of this manual.
9.
Connect modulating reheat valves per additional sections of this manual
NEW INSTALLATION CCW OPEN DAMPER
If the VAV is installed on a box which requires that the damper rotates
COUNTER-CLOCKWISE
to open, connect as
follows:
1.
Turn the damper to the closed position.
2.
Press the black triangular shaped clutch on the right edge of the actuator and
rotate the actuator fully clockwise.
3.
Place the assembly over the damper shaft and hand-tighten the nuts on the
actuator V-clamp.
4.
Attach the assembly to the box or mounting plate by driving a sheet metal screw
through the eyelet on the terminal strip end of the assembly.
5.
Remove the VAV cover and set the address DIP switch as required per
Appendix 1
.
6.
Connect the low voltage power to the unit per the next section.
7.
Remove and reverse connection of the RED and BLACK wires on the Belimo
actuator, where RED is connected to terminal 2 (CCW) and BLACK is connected
to terminal 3 (CW).
8.
Connect temperature sensors per additional sections of this manual.
9.
Connect fan or heating stages per additional sections of this manual.
10.
Connect modulating reheat valves per additional sections of this manual

Page 7
VVR RETROFIT INSTALLATION
The VVR must be mounted in a relatively clean environment, free from major airborne dust and contaminants
(moisture, oil, etc.). Keep the VVR away from high voltage equipment that might disrupt communications and away
from high vibration equipment. Do not mount the unit near any sources of electromagnetic interference (EMI) or
flammable vapors.
Install the VVR controller by attaching the provided snap-track into the unit control enclosure. If no enclosure is
provided, mount in standard NEMA 1 box as shown in
Figure 5
.
Figure 5:
Typical VVR Box Installation
H
L
ROOM SENSOR
DUCT SENSOR
FLOW
RING
FLOW TAPS
AIR FLOW
AIR FLOW
¼” OD TUBING
3
PAIR CABLE
2
PAIR CABLE
1
PAIR CABLE
VARIABLE AIR VOLUME TERMINAL
VVR
EXISTING
ACTUATOR
2
PAIR CABLE

Page 8
RETROFIT CW OPEN DAMPER
The VVR default logic operates whereas the board activates the
CCW
board output to open the damper. To connect
the actuator to the damper shaft to open in a
CLOCKWISE
rotation:
1.
Make sure the damper is closed, and the existing actuator is in the full
counter-clockwise position.
2.
Connect the existing 3-wire floating actuator with 2-pair cable as shown in
Figure 6
.
3.
Set the address DIP switch as required per
Appendix 1
.
4.
Connect the low voltage power to the unit per the next section.
5.
Connect temperature sensors per additional sections of this manual.
6.
Connect fan or heating stages per additional sections of this manual.
7.
Connect modulating reheat valves per additional sections of this manual
Figure 6:
Wiring of Existing Actuator for Clockwise to Open
Actuator Wiring Connections for
CLOCKWISE
to open:
VVR COM
to
ACTUATOR COMMON
VVR CCW
to
ACTUATOR CW
VVR CW
to
ACTUATOR CCW
C
W
C
O
M
C
C
W
D
A
M
P
E
R
VVR BOARD
RED
WHITE
BLACK
RED
BLACK
WHITE
EXISTING
3
-
WIRE
ACTUATOR
C
O
M
C
C
W
C
W
2
PAIR CABLE
REFER TO ACTUATOR MANUFACTURER’S
INSTALLATION INSTRUCTION FOR SPECIFIC
DETAILS
IMPORTANT NOTE
THE SILKSCREEN ON THE VVR BOARD IS
INCORRECT
.
TO VERIFY
-
THE CCW
OUTPUT ENERGIZES ON A CALL TO OPEN
,
AND THE CW OUTPUT ENERGIZES TO
CLOSE
.

Page 9
RETROFIT CCW OPEN DAMPER
If the VVR is installed on a box which requires that the damper rotates
COUNTER-CLOCKWISE
to open, connect as
follows:
1.
Make sure the damper is closed, and the existing actuator is in the full
clockwise position.
2.
Connect the existing 3-wire floating actuator with 2-pair cable as shown in
Figure 7
.
3.
Set the address DIP switch as required per
Appendix 1
.
4.
Connect the low voltage power to the unit per the next section.
5.
Connect temperature sensors per additional sections of this manual.
6.
Connect fan or heating stages per additional sections of this manual.
7.
Connect modulating reheat valves per additional sections of this manual.
Figure 7:
Wiring of Existing Actuator for Counter-Clockwise to Open
Actuator Wiring Connections for
COUNTER
-
CLOCKWISE
to open:
VVR COM
to
ACTUATOR COMMON
VVR CCW
to
ACTUATOR CCW
VVR CW
to
ACTUATOR CW
C
W
C
O
M
C
C
W
D
A
M
P
E
R
VVR BOARD
BLACK
WHITE
RED
RED
BLACK
WHITE
EXISTING
3
-
WIRE
ACTUATOR
C
O
M
C
C
W
C
W
2
PAIR CABLE
REFER TO ACTUATOR MANUFACTURER’S
INSTALLATION INSTRUCTION FOR SPECIFIC
DETAILS
IMPORTANT NOTE
THE SILKSCREEN ON THE VVR BOARD IS
INCORRECT
.
TO VERIFY
-
THE CCW
OUTPUT ENERGIZES ON A CALL TO OPEN
,
AND THE CW OUTPUT ENERGIZES TO
CLOSE
.

Page 10
CONNECTING THE POWER
The VAV / VVR must be powered by 24VAC Class 2 low voltage transformers. To connect the power wiring to the
VAV / VVR, locate the terminals on the outside edge of the VAV / VVR terminal strip and connect to the 24VAC power
source.
Figure 8
illustrates the VAV / VVR assembly showing the location of the 24VAC terminal block
.
NOTE:
For 24 VAC power, use only power supplies with a Class 2 transformer rating.
Do not power with any voltage other than the 24VAC low voltage listed. Connect power to the VAV / VVR by
connecting wires from the transformer to the 24VAC terminals L1 and L2. The terminals are labeled on the edge of
the VAV / VVR. The red indicator LED under the board clam shell cover will illuminate when the power is properly
connected.
For connections to the VAV / VVR, strip the wire back approximately 3/16" and insert into the terminal block. Back
out the screw on the terminal block until the bare wire inserts fully, and turn the screw back down until there is firm
tension on the wire. Make sure that the clamp secures the stripped portion of the wire, and that no insulation is under
the clamp.
Figure 8:
BASYX VAV / VVR power connections
L
1
L
2
N
O
1
2
4
V
A
C
24
VAC
+
-
24
VAC
TRANSFORMER
VAV
/
VVR BOARD
120
VAC CIRCUIT
MULTIPLE CONTROLLERS MAY BE POWERED
FROM A SINGLE TRANSFORMER
,
USE
5
VA
PER VAV
/
VVR FOR TRANSFORMER SIZING
.
THE VAV
/
VVR MAY BE POWERED FROM
THE EXISTING CONTROL
TRANSFORMER IN A FAN POWERED OR
REHEAT BOX IF AVAILABLE
.

Page 11
NOTE:
Multiple controllers may be powered from a single transformer. Recommend 5VA for
transformer sizing when designing power configurations. It is recommended that zones
or specific areas are powered in groups, and that not all controllers within the system
are powered from a single transformer.
COMMUNICATIONS
BUS WIRING
The BASYX VAV / VVR can be used in a stand alone configuration with a wall mounted sensor, with a PSC in smaller
applications, or in an array utilizing hundreds of units. When used in an application smaller than 32 total units, a
minimum of one (1) PSC must be installed. If used in a large array they must be used in conjunction with the BASYX
SCM Supervisor System and the required number of BASYX UBE Communications Expanders. Up to 32 BASYX
UBE expander boards can be connected to the BASYX Supervisor. In turn up to 32 BASYX VAV / VVR or other
system controllers can be connected to each communication expander providing great flexibility to conform to any
building’s physical installation requirements.
All communication wiring consists of a shielded, plenum rated cable (See
Figures 9
& 10
). Use 22 AWG, twisted pair,
stranded, shielded, plenum rated cable (Recommended Belden 6500FE) for all communications wiring. In lieu of the
6500FE cable, a stranded 2 pair cable with individually paired shields may be used. When connecting a channel of
controllers, connect communications in a daisy chain configuration.
Communication is via EIA RS-485 protocol. This requires that the system be wired according to the following
methods and rules:
•
Communications cable must be 1 twisted pair (Belden 6500FE), 22 AWG, plenum rated.
•
The total distance from the UBE expander to the last VAV / VVR in the daisy chain must
not exceed 4000 feet.
•
The drain wire of the communication cable must
NOT
be connected to the
VAV / VVR controller, twist shield wires together to create single shield for the entire daisy chain
and connect to ground at one end only (suggest at the UBE location).
•
Connection of the REF terminal on the VAV / VVR controller is
NOT
required.
•
Each VAV / VVR in the daisy chain must have a unique address. Refer to the
instructions below for setting the Device Address (ADDR) dip switch.
Connect the communications wiring to the terminal blocks on the edge of the VAV / VVR assembly marked +, -,
and REF as shown in
Figure 9
.
CAUTION:
All communication wiring must be connected such that the plus (+)
terminal is wired to a plus terminal and the minus terminal (-) is
wired to a minus terminal. Do not install communications cables near
power cables or in power conduits. Isolate all communications wiring
from large motors, fluorescent lighting fixtures or other sources of
high intensity electromagnetic interference (EMI).

Page 12
BASYX SCE
U
B
E
#
1
U
B
E
#
2
U
B
E
#
3
U
B
E
#
4
VAV
1
-
1
VAV
1
-
2
VVR
1
-
3
VVR
2
-
1
VVR
2
-
2
VVR
2
-
3
VAV
3
-
1
VVR
3
-
2
VAV
3
-
3
VVR
4
-
1
VAV
4
-
2
VVR
4
-
3
BASYX SCM SUPERVISOR
BASYX UBE EXPANDERS
BASYX VAV
/
VVR CONTROLLERS
UP TO
32
TOTAL
CHANNEL
1
VAV
/
VVR
CONTROLLERS
UP TO
32
TOTAL UBE CONTROLLERS
UP TO
32
TOTAL
CHANNEL
2
VAV
/
VVR
CONTROLLERS
UP TO
32
TOTAL
CHANNEL
3
VAV
/
VVR
CONTROLLERS
UP TO
32
TOTAL
CHANNEL
4
VAV
/
VVR
CONTROLLERS
MAIN RS
485
COMMUNICATIONS BUS
CHANNEL RS
485
COMMUNICATIONS BUS
COMPLEX COMMUNICATIONS BUS WITH EXPANDER MODULES
Figure 9:
BASYX Typical Communications Loop Configurations
Communications loops may contain any mixture of BASYX controllers. Each controller must have a unique address
setting for proper operation.
Smaller systems may not require the BASYX SCM Supervisor or the UBE Unitary Bus Expanders. A Single loop
containing a minimum of (1) PSC and up to 31 additional controllers may be used.

Page 13
+
-
+
-
+
-
+
-
R
E
F
1
2
R
S
4
8
5
C
O
M
M
B
U
S
RED
BLACK
RED
BLACK
TWISTSHIELDWIRES
TOGETHER
-
DO
NOT
CONNECTTOBOARD
A
N
A
L
O
G
I
N
P
U
T
S
+
-
+
-
+
-
+
-
R
E
F
1
2
R
S
4
8
5
C
O
M
M
B
U
S
RED
BLACK
RED
BLACK
TWISTSHIELDWIRES
TOGETHER
-
DO
NOT
CONNECTTOBOARD
A
N
A
L
O
G
I
N
P
U
T
S
VAV
/
VVR
1
-
1
VAV
/
VVR
1
-
2
CHANNELRS
485
COMMUNICATIONSBUS
CHANNEL
1
CONTROLLERS
3
-
64
FROMBASYXUBEEXPANDERS
Figure 10:
Typical VAV / VVR Communications Connection Details
SETTING THE DEVICE ADDRESS
If the VAV / VVR is used as a stand alone controller make sure that the address is set to #1.
If more than one VAV / VVR is used on the same communications bus then each device must have a different
address for proper communication. Removing the clam shell cover from the BASYX VAV assembly will expose the dip
switch which sets the individual controller address. Refer to
Appendix 1
for setting the device address to a number
between 1 and 64. The communication address for each device must be unique.
NOTE:
Do not skip addresses in a daisy chain; begin at 1 and count up. The boards do not
have to be in consecutive order, however all addresses must be included.

Page 14
CONNECTING THE TEMPERATURE SENSORS
The BASYX VAV / VVR provides predetermined analog and digital inputs for variable air volume terminal control.
Please refer to the
TYPICAL VAV INSTALLATION DRAWING
at the end of this document for details on complete
wiring of the VAV / VVR controller inputs and outputs.
Use 1 pair, shielded plenum cable for all input and output wiring. This cable should be 18 AWG, and should consist of
a stranded, twisted-pair, shielded cable with less than 20 pF capacitance per foot.
NOTE:
Connect all sensor and output cable drain wires to earth ground.
CAUTION:
Do not run sensor or output wires near power cables or in power
conduits. Isolate all sensor and output wires from large contactors
or motors, fluorescent light fixtures and other sources of high
intensity electromagnetic interference (EMI).
SENSOR INPUT DESIGNATIONS
The VAV / VVR analog inputs are thermistor type II only, with inputs dedicated as follows:
Analog Input 1:
Space temperature sensor
Analog Input 2:
Entering supply air temperature sensor
Analog Input 3:
Setpoint adjustment slidebar
Analog input 1 is dedicated for space temperature, and is used for temperature control of the conditioned space, and
is used for air flow calculation reset.
Analog input 2 is dedicated to supply air temperature from the corresponding air handling unit. This is used for
reversing of damper logic on high supply temperature (morning warmup, etc.), and makes the box a variable air
volume heating device based on the adjustable setpoint.
Analog input 3 is the setpoint adjustment slidebar on the ACI/10K-CP-R series room sensor if selected. This is a 0-
400 ohm resistance input and will automatically adjust the normal space setpoint by +/- 2 degrees.

Page 15
CONNECTING THE ROOM SENSOR
The room sensor monitors the space ambient temperature, as well as optional setpoint adjustment and system
override function. In addition, the sensor can be provided with an RJ11 jack, which allows connection to the individual
controller with a laptop through the room sensor.
Mount the room sensor according to the manufacturer’s instructions. Make sure that the sensor is not mounted so
that diffuser air is directly hitting the sensor, and that no heat producing equipment is nearby (coffee pots, etc.).
Connect the room sensor as shown in
Figure 11.
Figure 11:
Typical Room Sensor Wiring with Setpoint Adjustment, Override & Direct Connection
L
1
L
2
N
O
C
N
O
C
N
O
C
N
O
C
4
3
2
1
2
4
V
A
C
H
E
A
T
I
N
G
R
E
L
A
Y
O
U
T
P
U
T
S
C
W
C
O
M
C
C
W
D
A
M
P
E
R
+
-
+
-
2
1
D
I
G
I
T
A
L
I
N
P
U
T
S
+
-
S
P
A
D
J
+
-
3
F
D
B
K
RED
BROWN
BLUE
BLACK
GREEN
WHITE
GREEN
RED
BLACK
2
PAIR CABLE
+
-
+
-
+
-
A
O
1
1
2
A
N
A
L
O
G
I
N
P
U
T
S
RED
BLACK
O
U
T
I
N
G
N
D
G
N
D
+
2
8
R
S
2
3
2
S
E
R
V
I
C
E
P
O
R
T
1
2
3
4
5
6
+
-
SET
O
/
R
SHORT SENSOR
SEPARATE INPUT
SENSOR
RJ
11
JUMPERS MUST BE SET
FOR SEPARATE INPUT
-
JUMP LOWER
2
PINS OF
EACH VERTICAL SET
SETPOINT ADJUSTMENT SLIDEBAR
RED
BLACK
BLUE
BROWN
GREEN
WHITE
GREEN
RED
BLACK
SPACE TEMPERATURE SENSOR
OVERRIDE BUTTON
ACI
/
10
K
-
CP
-
RSO
-
RJ
6
AUTOMATION COMPONENTS
,
INC
.
RED
BLACK
WHITE
GREEN
BROWN
BLUE
3
PAIR CABLE
V
A
V
/
V
V
R
C
O
N
T
R
O
L
L
E
R
B
O
A
R
D

Page 16
CONNECTING THE DUCT SENSOR
The duct sensor monitors the incoming supply air temperature, and allows the reverse operation of the damper upon
a high entering duct temperature. This is typically used on air handling equipment with morning warmup function.
The reversing function will reverse the operation of the damper i.e. open on a call for heat.
Mount the sensor upstream from the VAV box in the branch duct according to the manufacturer’s installation
instructions. Make sure that the sensor is in a straight section of duct, and install at least 5 duct diameters ahead of
box and away from elbows.
Connect the duct sensor as shown in
Figure 12.
Figure 12:
Duct Sensor Wiring
CONNECTING THE DIGITAL INPUTS
The VAV / VVR contains two (2) digital inputs:
Digital Input 1 is dedicated for the override button on the room sensor as shown in
Figure 10.
Digital Input 2 is a free input, and may be used for monitoring of any dry-contact input. This point may be used to
monitor flow switches, current switches, filter switches, etc. and is connected directly next to the override input as
shown in
Figure 11.
L
1
L
2
N
O
C
N
O
C
N
O
C
N
O
C
4
3
2
1
2
4
V
A
C
H
E
A
T
I
N
G
R
E
L
A
Y
O
U
T
P
U
T
S
RED
BLACK
2
PAIR CABLE
+
-
+
-
+
-
A
O
1
1
2
A
N
A
L
O
G
I
N
P
U
T
S
RED
BLACK
V
A
V
/
V
V
R
C
O
N
T
R
O
L
L
E
R
B
O
A
R
D
GREEN
WHITE
BUTT SPLICES
-
DO
NOT
USE WIRE NUTS
INSTALL SENSOR UPSTREAM IN
ENTERING AIR DUCT
A
C
I
/
1
0
K
-
C
P
-
D
4
DUCT SENSOR
RED
BLACK
A
U
T
O
M
A
T
I
O
N
C
O
M
P
O
N
E
N
T
S
,
I
N
C
.

Page 17
L
1
L
2
N
O
C
N
O
C
N
O
C
N
O
C
+
4
3
2
1
2
4
V
A
C
H
E
A
T
I
N
G
R
E
L
A
Y
O
U
T
P
U
T
S
HEAT
4
RELAY
PILOT RELAYS
HEAT
3
RELAY
HEAT
2
RELAY
FAN
/
HEAT
1
RELAY
24
VAC
+
-
24
VAC TRANSFORMER
V
A
V
/
V
V
R
C
O
N
T
R
O
L
L
E
R
B
O
A
R
D
CONNECTING THE DIGITAL OUTPUTS
The VAV / VVR provides four (4) SPST relay outputs for control of box fans and/or electric heat strips. The outputs
provide a normally open contact, and will interface with most box manufacturer control sequences.
Figure 13
shows
output wiring utilizing external pilot relays.
NOTE:
The maximum current for each digital output is 1 amp at 24V (AC or DC).
CAUTION:
The digital outputs on the VAV / VVR are for low voltage, pilot duty switching.
DO NOT ATTEMPT TO SWITCH LINE VOLTAGE
(120V or higher)
through the digital outputs, serious damage may be done to the VAV / VVR
controller.
Figure 13:
Typical VAV Pilot Relay Output Wiring

Page 18
Figure 14
shows typical wiring of a fan-powered reheat box which uses the 24VAC transformer in the VAV box
controls to power the VAV / VVR board. This is a typical view, and the box manufacturer instructions should be
referenced for exact wiring details.
Figure 14:
Typical Fan-Powered Box Output Wiring
INSTALLING THE VARISTORS
Each VAV or VVR is shipped with four (4) varistors for installation on existing fan or electric heat contactors. The
devices clamp on electrical noise typically associated with drop-out of contactor coil voltage, which may cause the
VAV controller to malfunction. To install the varistors, connect in parallel with contactor coil wiring as shown in
Figure 15
.
Figure 15:
Varistor Installation Details
L
1
L
2
N
O
C
N
O
C
N
O
C
N
O
C
+
4
3
2
1
2
4
V
A
C
H
E
A
T
I
N
G
R
E
L
A
Y
O
U
T
P
U
T
S
BOX TERMINAL STRIP
H
O
T
C
O
M
M
O
N
F
A
N
/
H
E
A
T
1
H
E
A
T
2
H
E
A
T
3
H
E
A
T
4
V
A
V
/
V
V
R
C
O
N
T
R
O
L
L
E
R
B
O
A
R
D
VARISTOR
L
1
L
3
L
2
L
1
L
2
L
3
LOAD
EXISTING CONTROL
CIRCUIT
EXISTING CONTACTOR

Page 19
CONNECTING THE ANALOG OUTPUT
One 0-10vdc analog device may be controlled by the VAV / VVR, and is used to control hot water reheat or
baseboard heating valves.
Figure 16
illustrates typical device connections. When connecting the actuator, make
sure to be consistent with L1 (HOT) and L2 (COMMON) connections within the system.
Figure 16:
Typical VAV Analog Output Wiring
DANGER:
The VAV / VVR analog output is designed for use with an actuator using full-wave power.
Serious damage will occur to the VAV / VVR board if connected to a half-wave device. If unsure
about your selected actuator, call Global Control Solutions technical support.
L
1
L
2
N
O
C
N
O
C
N
O
C
N
O
C
+
-
+
-
+
-
+
-
+
-
R
E
F
4
3
2
1
2
4
V
A
C
H
E
A
T
I
N
G
R
E
L
A
Y
O
U
T
P
U
T
S
A
O
1
1
2
A
N
A
L
O
G
I
N
P
U
T
S
R
S
4
8
5
C
O
M
M
B
U
S
24
VAC
+
-
C
O
M
M
O
N
(
1
)
H
O
T
(
+
)
S
I
G
N
A
L
(
Y
1
)
F
E
E
D
B
A
C
K
(
Y
2
)
BELIMO or OTHER ACTUATOR
24
VAC TRANSFORMER
IMPORTANT
!!
WHEN POWERING THE ACTUATOR
FROM THE POWER SUPPLY
,
MAKE
SURE THAT THE POWER IS
CONNECTED CONSISTENTLY WITH THE
VAV CONNECTION
(
HOT
-
HOT
)
AND
(
GROUND
-
GROUND
)
SERIOUS DAMAGE
WILL
OCCUR TO
THE VAV BOARD IF NOT CONNECTED
CORRECTLY
!
V
A
V
/
V
V
R
C
O
N
T
R
O
L
L
E
R
B
O
A
R
D

Page 20
1
3
2
CW
COM
CCW
HIGH
LOW
HIGH PRESSURE TAP ON BOX FLOW RING
or FLOW SENSOR
LOW PRESSURE TAP ON BOX FLOW RING
or FLOW SENSOR
¼” OD TUBING
VELOCITY SENSOR
/
TUBING CONNECTIONS
INTERNAL TUBING FROM BOARD
VELOCITY SENSOR TO EXTERNAL
PRESSURE TAPS FACTORY INSTALLED
CONNECTING THE VELOCITY SENSOR
The VAV / VVR uses an on-board differential pressure sensor for monitoring of air flow and velocity of the box
discharge to the conditioned space. On the VAV, the sensor is connected with flexible tubing to external taps on the
lower edge of the enclosure marked “HIGH” and “LOW”. On the VVR, the tubing is connected directly to the velocity
sensor at the top of the VVR controller board.
IMPORTANT:
When connecting tubing directly to the on-board velocity sensor, the lower
(closest to the board) connection is the “LOW” pressure, and the upper
connection is the “HIGH”.
NOTE:
On the VAV assembly, the external taps accept a 1/4" OD tubing.
On the VVR retrofit board, the sensor taps are 3/8" OD.
Figure 17
shows the connection to the box flow ring (see box manufacturers installation manual) or the SSS series
flow sensor, which is provided for older boxes without a flow ring, or damper blade only type installations.
Figure 17:
Typical VAV Velocity Sensor Tubing Connections
NOTE:
See
Appendix 2
for box constant values for major manufacturers
This manual suits for next models
1
Table of contents
Popular Controllers manuals by other brands
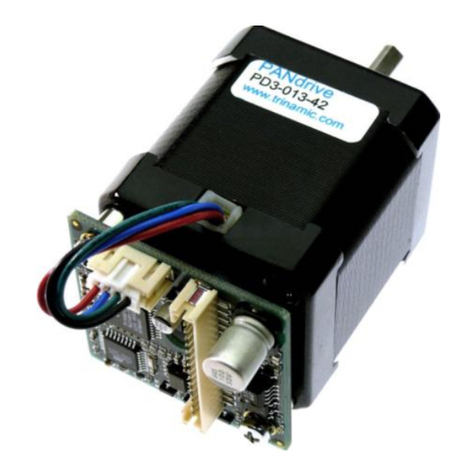
Trinamic
Trinamic TMCM-013-42 Hardware manual

Nordson EFD
Nordson EFD PICO Touch Series operating manual
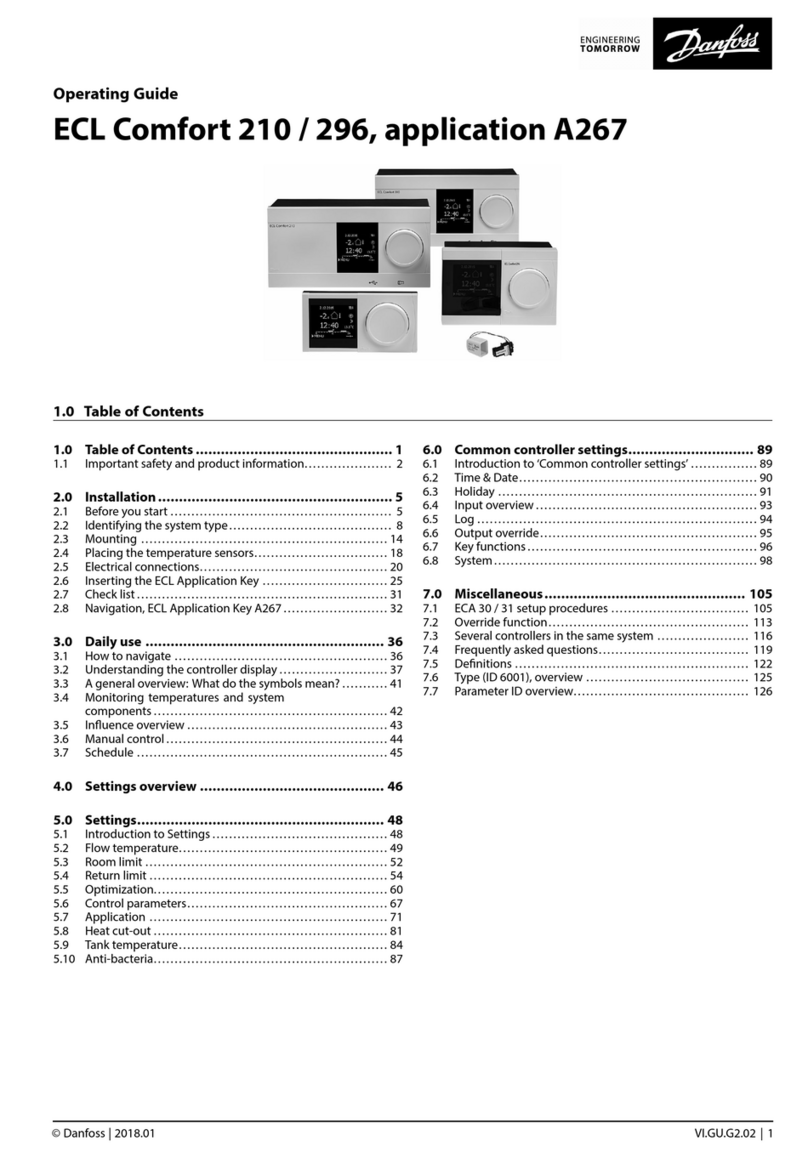
Danfoss
Danfoss ECL Comfort 296 operating guide
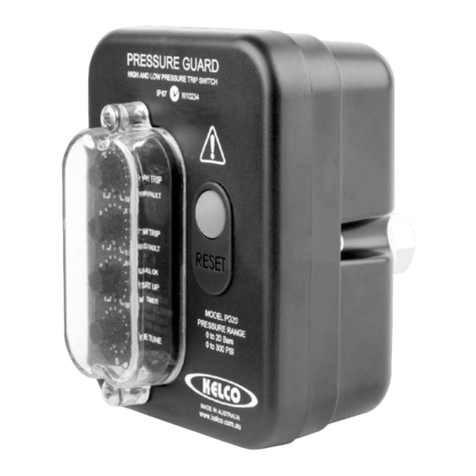
KELCO
KELCO PG20 Series Instructions for installing and using
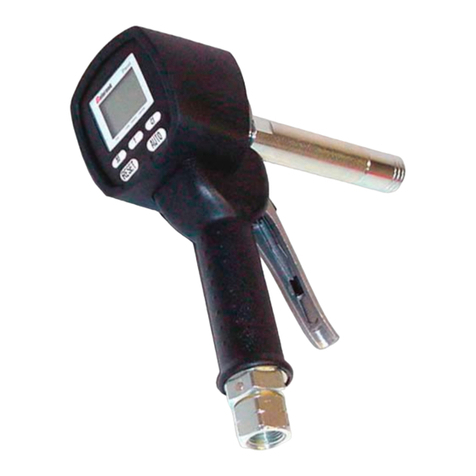
Balcrank
Balcrank 3331-014 Operation, installation, maintenance and repair guide

LenelS2
LenelS2 LNL-X2210 manual
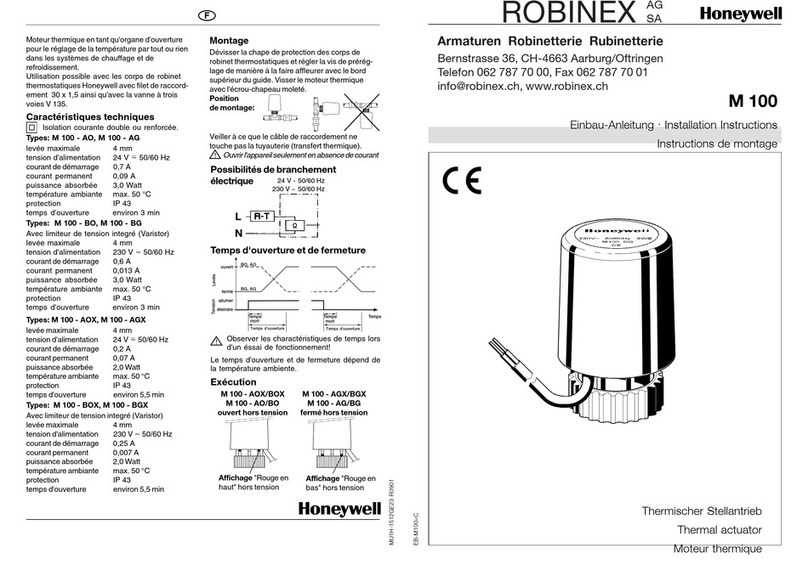
Honeywell
Honeywell ROBINEX M 100 installation instructions
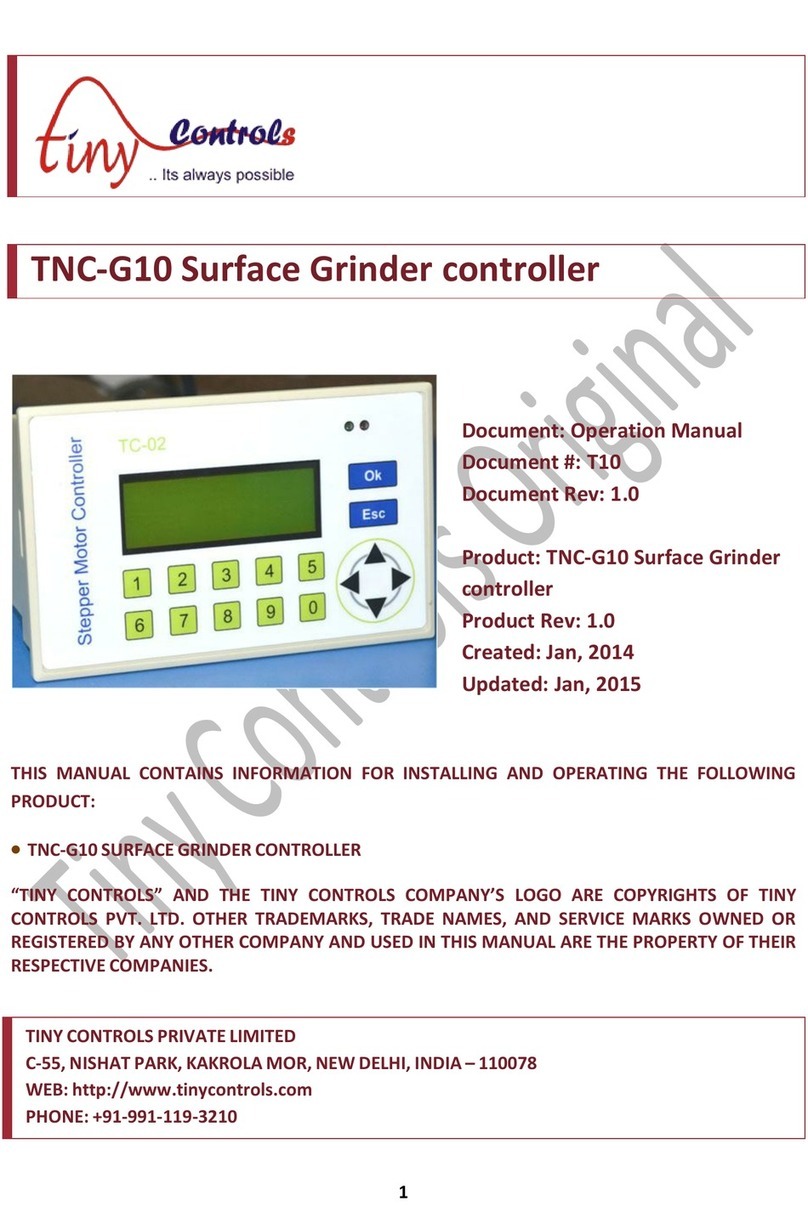
TINY
TINY TNC-G10 Operation manual
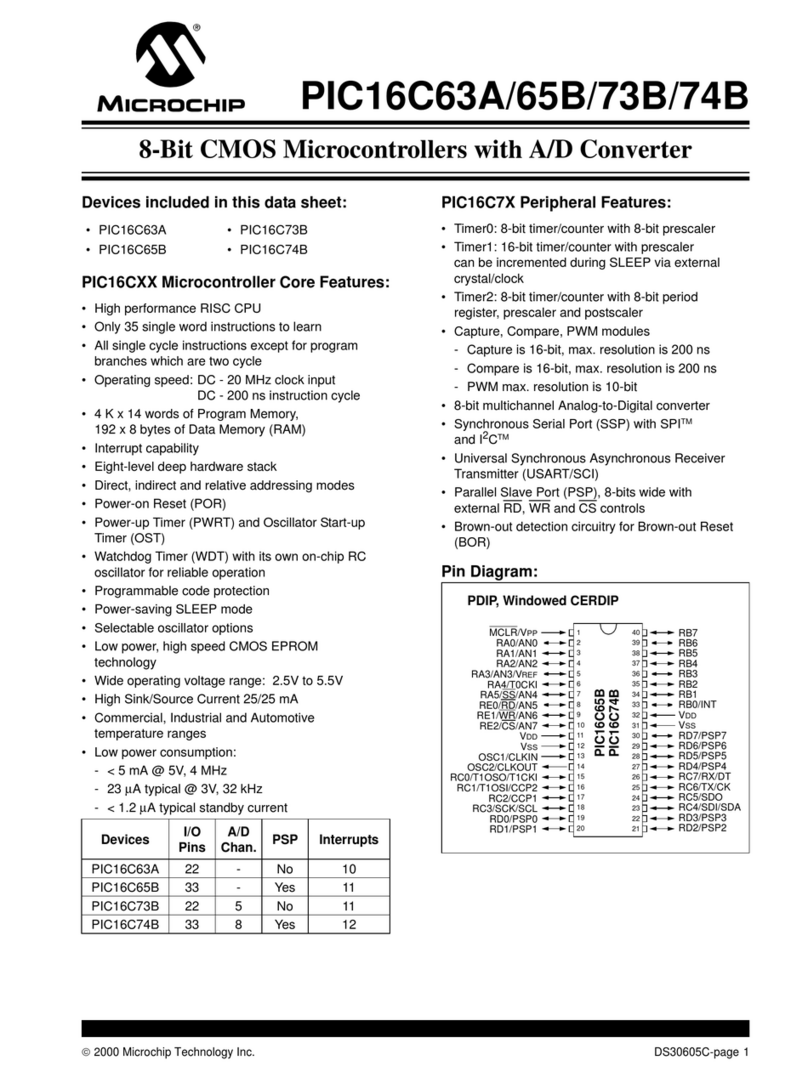
Microchip Technology
Microchip Technology PIC16C63A Operator's manual

Xerox
Xerox FREEFLOW ACCXES FIRMWARE 12.7 B 114 Firmware release notes
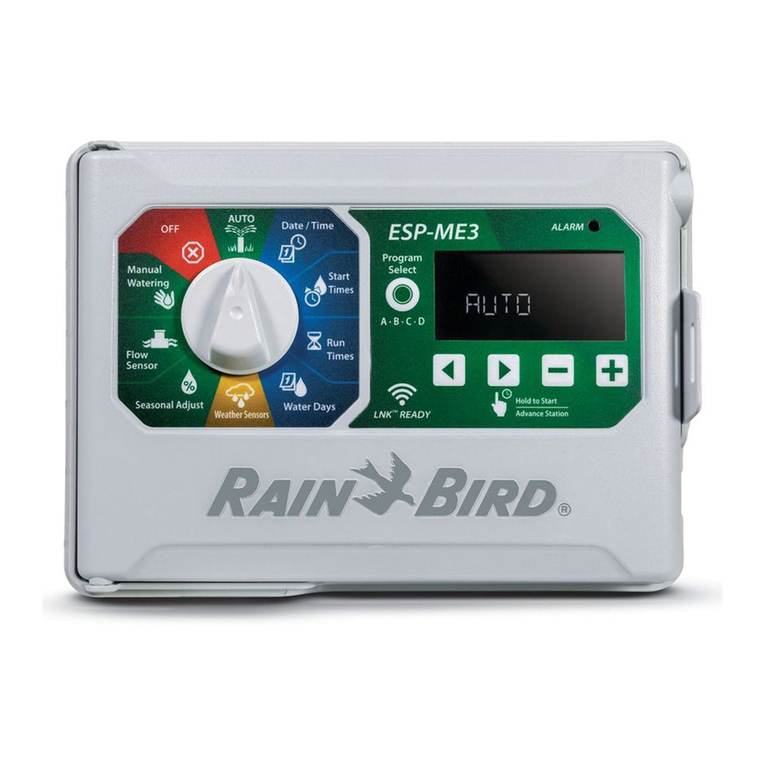
Rain Bird
Rain Bird ESP-ME3 user manual

ITRON
ITRON RB 4000 Installation and start-up instructions