GE Multilin MM300 Use and care manual

LISTED
52TL
IND.CONT. EQ.
E83849
Title page
GE Multilin's Quality
Management System is
registered to ISO9001:2000
QMI # 005094
GE Digital Energy
Multilin
GE Multilin
215 Anderson Avenue, Markham, Ontario
Canada L6E 1B3
Tel: (905) 294-6222 Fax: (905) 201-2098
Internet: http://www.GEmultilin.com
MM300 revision: 1.5x
Manual P/N: 1601-9025-A6
GE publication code: GEK-113392E
Copyright © 2010 GE Multilin
IISO9001:2000
G
E
M
U
L
T
I
L
I
N
R
E
G
I
S
T
E
R
E
D
*1601-9025-A6*
MM300
Motor Management System
Communications Guide

© 2010 Multilin Incorporated. All rights reserved.
GE Multilin MM300 Motor Management System Communications Guide for revision 1.5x.
MM300 Motor Management System, EnerVista, EnerVista Launchpad, EnerVista MM300
Setup, and FlexLogic are registered trademarks of GE Multilin Inc.
Allen-Bradley, RSLinx DeviceNet-3, RSNetWorx for DeviceNet, EDS Wizard, Allen-Bradley
1770-KFD Driver, and 1747-SDN Scanner Module, are registered trademarks of Rockwell
Automation, Inc.
The following screens are captured from ProfiCaptain v1.0 - ©2005 Profibus Center,
Netherlands:
– Figure 2 - Profibus configuration menu
– Figure 3 - Profibus I/O data - 87 words in, 1 word out
– Figure 4 - Profibus configuration menu
– Figure 5 - Profibus I/O data - 3 words in, 1 word out
The following screens are captured from ProfiTrace v1.4 - ©2005 Profibus Center,
Netherlands:
– Figure 6 - Profibus - extended diagnostic data
– Figure 7 - Profibus - no extended diagnostic data
The following screen is captured from DeviceNet Master Simulator. HMS Industrial
Networks. Version 1.7.4. ©2001, Bihl+Wiedemann GmbH
– Figure 8 - DeviceNet polled I/O data
The contents of this manual are the property of GE Multilin Inc. This documentation is
furnished on license and may not be reproduced in whole or in part without the permission
of GE Multilin. The content of this manual is for informational use only and is subject to
change without notice.
Part number: 1601-9025-A6 (April 2010)

MM300 MOTOR MANAGEMENT SYSTEM – COMMUNICATIONS GUIDE i
Table of Contents
Communications interfaces .................................................................................................... 1
RS485 interface (Modbus RTU) ............................................................................................... 2
Modbus Protocol................................................................................................................................... 2
Electrical Interface .............................................................................................................................. 2
Data Frame Format and Data Rate ............................................................................................ 2
Data Packet Format ........................................................................................................................... 2
Error Checking....................................................................................................................................... 3
CRC-16 Algorithm ................................................................................................................................ 3
Timing........................................................................................................................................................ 4
MM300 supported functions .......................................................................................................... 4
Modbus Functions................................................................................................................................ 4
Function Code 03H ............................................................................................................................. 4
Function Code 04H ............................................................................................................................. 5
Function Code 05H ............................................................................................................................. 6
Function Code 06H ............................................................................................................................. 7
Function Code 07H ............................................................................................................................. 8
Function Code 08H ............................................................................................................................. 8
Function Code 10H ............................................................................................................................. 9
Error Responses..................................................................................................................................10
Modbus memory map..................................................................................................................... 11
Format codes ...................................................................................................................................... 41
Performing Commands Using Function Code 10H ........................................................... 67
Using the User Definable Memory Map ..................................................................................68
Ethernet interface.......................................................................................................................69
Fieldbus interface.......................................................................................................................70
Configurable Fieldbus input data............................................................................................... 70
Profibus DP ........................................................................................................................................... 71
Profibus power supply configuration.......................................................................................72
Profibus DP-parameterization.....................................................................................................73
Profibus DP-configuration .............................................................................................................73
Profibus Input Data...........................................................................................................................76
Profibus Output Data .......................................................................................................................78
Profibus DPV0-Diagnostics ...........................................................................................................78
Profibus DPV1...................................................................................................................................... 89
Profibus DPV1-Acyclic read/write data...................................................................................89
Profibus DPV1-Diagnostics ...........................................................................................................92
I&M (Identification & Maintenance) records.......................................................................103
DeviceNet protocol.........................................................................................................................105
DeviceNet power supply configuration................................................................................106
DeviceNet setup and configuration (typical)......................................................................107
DeviceNet setup and configuration (ADR)...........................................................................122
DeviceNet Communications......................................................................................................125
Poll data ..............................................................................................................................................125
Identity Object (Class Code 01H)..............................................................................................126
Message Router (Class Code 02H) ..........................................................................................127
DeviceNet Object (Class Code 03H)........................................................................................127
DeviceNet Connection Object (Class Code 05H) ..............................................................127
DeviceNet Motor Data - Explicit Object (Class Code A0H) ...........................................128
DeviceNet - Explicit Configuration Data Object (Class Code A1H, Services) .......130
DeviceNet - Explicit Motor Analog Data Object (Class Code A2H, Services) .......133
DeviceNet - Explicit Motor Analog Data Object, Class Code B0H, Services.........135
DeviceNet - Explicit Motor Object, Class Code B1H........................................................138
Change notes ............................................................................................................................141
Revision history.................................................................................................................................141

ii MM300 MOTOR MANAGEMENT SYSTEM – COMMUNICATIONS GUIDE

MM300 MOTOR MANAGEMENT SYSTEM – COMMUNICATIONS GUIDE 1
MM300 Motor Management System
Communications Guide
Digital Energy
Multilin
Communicatio ns Guide
Communications interfaces
The MM300 has three communications interfaces. These can be used simultaneously:
• RS485
• 10/100Base-T Ethernet
•Fieldbus
NOTE
NOTE: Setpoint changes related to DeviceNet, Profibus, and Ethernet, require a power cycle to be
activated.
NOTE
NOTE: External power must be present on the Fieldbus port at power-up, in order to correctly
initialize and operate.
NOTE
NOTE: For full details, please refer to the MM300 Communications Guide, to be found on the GE
Multilin web site.

2 MM300 MOTOR MANAGEMENT SYSTEM – COMMUNICATIONS GUIDE
RS485 INTERFACE (MODBUS RTU) CHAPTER 1: COMMUNICATIONS GUIDE
RS485 interface (Modbus RTU)
The RS485 interface is a serial two-wire port intended for use as a Modbus RTU slave. The
RS485 port has the following characteristics.
•Address:1to254
• Baud rate: 9600 to 115200 bps
• Supported Modbus function codes: 3, 4, 5, 6, 7, 8, 16
Modbus Protocol
The MM300 implements a subset of the Modicon Modbus RTU serial communication
standard. The Modbus protocol is hardware-independent. That is, the physical layer can be
any of a variety of standard hardware configurations. This includes RS232, RS422, RS485,
fibre optics, etc. Modbus is a single master / multiple slave type of protocol suitable for a
multi-drop configuration as provided by RS485 hardware. The MM300 Modbus
implementation employs two-wire RS485 hardware. Using RS485, up to 32 MM300s can be
daisy-chained together on a single communication channel.
The MM300 is always a Modbus slave. It can not be programmed as a Modbus master.
Computers or PLCs are commonly programmed as masters.
Both monitoring and control are possible using read and write register commands. Other
commands are supported to provide additional functions.
Electrical Interface The hardware or electrical interface in the MM300 is two-wire RS485. In a two-wire link,
data is transmitted and received over the same two wires. Although RS485 two wire
communication is bi-directional, the data is never transmitted and received at the same
time. This means that the data flow is half duplex.
RS485 lines should be connected in a daisy chain configuration with terminating networks
installed at each end of the link (i.e. at the master end and at the slave farthest from the
master). The terminating network should consist of a 120 Ohm resistor in series with a 1 nF
ceramic capacitor when used with Belden 9841 RS485 wire. Shielded wire should always
be used to minimize noise. The shield should be connected to all of the MM300s as well as
the master, then grounded at one location only. This keeps the ground potential at the
same level for all of the devices on the serial link.
NOTE
NOTE: Polarity is important in RS485 communications. The '+' (positive) terminals of every device
must be connected together.
Data Frame Format
and Data Rate
One data frame of an asynchronous transmission to or from a MM300 typically consists of
1 start bit, 8 data bits, and 1 stop bit. This produces a 10 bit data frame. This is important
for transmission through modems at high bit rates (11 bit data frames are not supported
by Hayes modems at bit rates of greater than 300 bps).
Modbus protocol can be implemented at any standard communication speed. The
MM300supports operation at 9600, 19200, 38400, 57600, and 115200 baud.
Data Packet Format A complete request/response sequence consists of the following bytes (transmitted as
separate data frames):
Master Request Transmission:
SLAVE ADDRESS: 1 byte
FUNCTION CODE: 1 byte
DATA: variable number of bytes depending on FUNCTION CODE
CRC: 2 bytes

CHAPTER 1: COMMUNICATIONS GUIDE RS485 INTERFACE (MODBUS RTU)
MM300 MOTOR MANAGEMENT SYSTEM – COMMUNICATIONS GUIDE 3
Slave Response Transmission:
SLAVE ADDRESS: 1 byte
FUNCTION CODE: 1 byte
DATA: variable number of bytes depending on FUNCTION CODE
CRC: 2 bytes
SLAVE ADDRESS: This is the first byte of every transmission. This byte represents the user-
assigned address of the slave device that is to receive the message sent by the master.
Each slave device must be assigned a unique address and only the addressed slave will
respond to a transmission that starts with its address. In a master request transmission the
SLAVE ADDRESS represents the address of the slave to which the request is being sent. In a
slave response transmission the SLAVE ADDRESS represents the address of the slave that is
sending the response.
FUNCTION CODE: This is the second byte of every transmission. Modbus defines function
codes of 1 to 127.
DATA: This will be a variable number of bytes depending on the FUNCTION CODE. This may
be Actual Values, Setpoints, or addresses sent by the master to the slave or by the slave to
the master.
CRC: This is a two byte error checking code.
Error Checking The RTU version of Modbus includes a two byte CRC-16 (16 bit cyclic redundancy check)
with every transmission. The CRC-16 algorithm essentially treats the entire data stream
(data bits only; start, stop and parity ignored) as one continuous binary number. This
number is first shifted left 16 bits and then divided by a characteristic polynomial
(11000000000000101B). The 16 bit remainder of the division is appended to the end of the
transmission, MSByte first. The resulting message including CRC, when divided by the
same polynomial at the receiver will give a zero remainder if no transmission errors have
occurred.
If a MM300 Modbus slave device receives a transmission in which an error is indicated by
the CRC-16 calculation, the slave device will not respond to the transmission. A CRC-16
error indicates than one or more bytes of the transmission were received incorrectly and
thus the entire transmission should be ignored in order to avoid the MM300 performing
any incorrect operation.
The CRC-16 calculation is an industry standard method used for error detection. An
algorithm is included here to assist programmers in situations where no standard CRC-16
calculation routines are available.
CRC-16 Algorithm Once the following algorithm is complete, the working register “A” will contain the CRC
value to be transmitted. Note that this algorithm requires the characteristic polynomial to
be reverse bit ordered. The MSBit of the characteristic polynomial is dropped since it does
not affect the value of the remainder. The following symbols are used in the algorithm:
—>: data transfer
A: 16 bit working register
AL: low order byte of A
AH: high order byte of A
CRC: 16 bit CRC-16 value
i, j: loop counters
(+): logical exclusive or operator
Di: i-th data byte (i = 0 to N-1)
G: 16 bit characteristic polynomial = 1010000000000001 with MSbit dropped and bit order
reversed
shr(x): shift right (the LSbit of the low order byte of x shifts into a carry flag, a '0' is shifted
into the MSbit of the high order byte of x, all other bits shift right one location

4 MM300 MOTOR MANAGEMENT SYSTEM – COMMUNICATIONS GUIDE
RS485 INTERFACE (MODBUS RTU) CHAPTER 1: COMMUNICATIONS GUIDE
The algorithm is:
1. FFFF hex —> A
2. 0 —> i
3. 0 —> j
4. Di (+) AL —> AL
5. j+1 —> j
6. shr(A)
7. is there a carry? No: go to 8. Yes: G (+) A —> A
8. is j = 8? No: go to 5. Yes: go to 9.
9. i+1 —> i
10. is i = N? No: go to 3. Yes: go to 11.
11. A —> CRC
Timing Data packet synchronization is maintained by timing constraints. The receiving device
must measure the time between the reception of characters. If 3.5 character times elapse
without a new character or completion of the packet, then the communication link must
be reset (i.e. all slaves start listening for a new transmission from the master). Thus at 9600
baud a delay of greater than 3.5 x 1 / 9600 x 10 x = x 3.65 x ms will cause the
communication link to be reset.
MM300 supported
functions
The following functions are supported by the MM300:
• FUNCTION CODE 03 - Read Setpoints and Actual Values
• FUNCTION CODE 04 - Read Setpoints and Actual Values
• FUNCTION CODE 05 - Execute Operation
• FUNCTION CODE 06 - Store Single Setpoint
• FUNCTION CODE 07 - Read Device Status
• FUNCTION CODE 08 - Loopback Test
• FUNCTION CODE 10 - Store Multiple Setpoints
Modbus Functions
Function Code 03H Modbus implementation: Read Holding Registers
MM300 implementation: Read Setpoints
For the MM300 implementation of Modbus, this function code can be used to read any
setpoints (“holding registers”). Holding registers are 16 bit (two byte) values transmitted
high order byte first. Thus all MM300 Setpoints are sent as two bytes. The maximum
number of registers that can be read in one transmission is 125.
The slave response to this function code is the slave address, function code, a count of the
number of data bytes to follow, the data itself and the CRC. Each data item is sent as a two
byte number with the high order byte sent first.
For example, consider a request for slave 17 to respond with 3 registers starting at address
006B. For this example the register data in these addresses is as follows:

CHAPTER 1: COMMUNICATIONS GUIDE RS485 INTERFACE (MODBUS RTU)
MM300 MOTOR MANAGEMENT SYSTEM – COMMUNICATIONS GUIDE 5
The master/slave packets have the following format:
Table 1: Master/slave packet format for Function Code 03H
Function Code 04H Modbus Implementation: Read Input Registers
MM300 implementation: Read Actual Values
For the MM300 implementation of Modbus, this function code can be used to read any
actual values (“input registers”). Input registers are 16 bit (two byte) values transmitted high
order byte first. Thus all MM300 Actual Values are sent as two bytes. The maximum
number of registers that can be read in one transmission is 125.
The slave response to this function code is the slave address, function code, a count of the
data bytes to follow, the data itself and the CRC. Each data item is sent as a two byte
number with the high order byte sent first.
For example, request slave 17 to respond with 1 register starting at address 0008. For this
example the value in this register (0008) is 0000.
Table 2: Master/slave packet format for Function Code 04H
Address Data
006B 022B
006C 0000
006D 0064
MASTER TRANSMISSION BYTES EXAMPLE DESCRIPTION
SLAVE ADDRESS 1 11 message for slave 17
FUNCTION CODE 1 03 read registers
DATA STARTING ADDRESS 2 00 6B data starting at 006B
NUMBER OF SETPOINTS 2 00 03 3 registers = 6 bytes
total
CRC 2 76 87 CRC error code
SLAVE RESPONSE BYTES EXAMPLE DESCRIPTION
SLAVE ADDRESS 1 11 message from slave
17
FUNCTION CODE 1 03 read registers
BYTE COUNT 1 06 3 registers = 6 bytes
DATA 1 (see definition above) 2 02 2B value in address
006B
DATA 2 (see definition above) 2 00 00 value in address
006C
DATA 3 (see definition above) 2 00 64 value in address
006D
CRC 2 54 83 CRC error code
MASTER TRANSMISSION BYTES EXAMPLE DESCRIPTION
SLAVE ADDRESS 1 11 message for slave 17
FUNCTION CODE 1 04 read registers
DATA STARTING ADDRESS 2 00 08 data starting at 0008
NUMBER OF ACTUAL VALUES 2 00 01 1 register = 2 bytes
CRC 2 B2 98 CRC error code

6 MM300 MOTOR MANAGEMENT SYSTEM – COMMUNICATIONS GUIDE
RS485 INTERFACE (MODBUS RTU) CHAPTER 1: COMMUNICATIONS GUIDE
Function Code 05H Modbus Implementation: Force Single Coil
MM300 Implementation: Execute Operation
This function code allows the master to request a MM300 to perform specific command
operations.
For example, to request slave 17 to execute operation code 1 (reset), we have the following
master/slave packet format:
Table 3: Master/slave packet format for Function Code 05H
The commands that can be performed by the MM300 using function code 05 can also be
initiated by using function code 10.
SLAVE RESPONSE BYTES EXAMPLE DESCRIPTION
SLAVE ADDRESS 1 11 message from slave
17
FUNCTION CODE 1 04 read registers
BYTE COUNT 1 02 1 register = 2 bytes
DATA (see definition above) 2 00 00 value in address
0008
CRC 2 78 F3 CRC error code
MASTER TRANSMISSION BYTES EXAMPLE DESCRIPTION
SLAVE ADDRESS 1 11 message for slave 17
FUNCTION CODE 1 05 execute operation
OPERATION CODE 2 00 01 operation code 1
CODE VALUE 2 FF 00 perform function
CRC 2 DF 6A CRC error code
SLAVE RESPONSE BYTES EXAMPLE DESCRIPTION
SLAVE ADDRESS 1 11 message from slave
17
FUNCTION CODE 1 05 execute operation
OPERATION CODE 2 00 01 operation code 1
CODE VALUE 2 FF 00 perform function
CRC 2 DF 6A CRC error code

CHAPTER 1: COMMUNICATIONS GUIDE RS485 INTERFACE (MODBUS RTU)
MM300 MOTOR MANAGEMENT SYSTEM – COMMUNICATIONS GUIDE 7
Function Code 06H Modbus Implementation: Preset Single Register
MM300 Implementation: Store Single Setpoint
This command allows the master to store a single setpoint into the memory of a MM300
The slave response to this function code is to echo the entire master transmission.
For example, request slave 17 to store the value 2 in setpoint address 04 5C. After the
transmission in this example is complete, setpoints address 04 5C will contain the value
01F4. The master/slave packet format is shown below:
Table 4: Master/slave packet format for Function Code 06H
Operation Code Description
1Reset
2LockoutReset
3Stop
4StartA
5StartB
96 Clear Last Trip Data Prompt
97 Reset MWh and Mvarh Meters
99 Clear Counters
100 Clear Event Records
102 Clear Maintenance Info
103 Clear Datalog
112 Clear RTD Maximums
113 Reset Motor Information
114 Auto Mode
115 Manual Mode
121 Start Datalog
122 Stop Datalog
MASTER TRANSMISSION BYTES EXAMPLE DESCRIPTION
SLAVE ADDRESS 1 11 message for slave 17
FUNCTION CODE 1 06 store single setpoint
DATA STARTING ADDRESS 2 04 5C setpoint address 04
5C
DATA 2 00 02 data for setpoint
address 04 5C
CRC 2 CB B9 CRC error code
SLAVE RESPONSE BYTES EXAMPLE DESCRIPTION
SLAVE ADDRESS 1 11 message from slave
17
FUNCTION CODE 1 06 store single setpoint
DATA STARTING ADDRESS 2 04 5C setpoint address 04
5C
DATA 2 00 02 data stored in
setpoint address 04
5C
CRC 2 CB B9 CRC error code

8 MM300 MOTOR MANAGEMENT SYSTEM – COMMUNICATIONS GUIDE
RS485 INTERFACE (MODBUS RTU) CHAPTER 1: COMMUNICATIONS GUIDE
Function Code 07H Modbus Implementation: Read Exception Status
MM300 Implementation: Read Device Status
This is a function used to quickly read the status of a selected device. A short message
length allows for rapid reading of status. The status byte returned will have individual bits
set to 1 or 0 depending on the status of the slave device. For this example, consider the
following MM300 general status byte:
The master/slave packets have the following format:
Table 5: Function code 7 bitmask
Table 6: Master/slave packet format for Function Code 07H
Function Code 08H Modbus Implementation: Loopback
Test MM300 Implementation: Loopback Test
This function is used to test the integrity of the communication link. The MM300 will echo
the request.
For example, consider a loopback test from slave 17:
Table 7: Master/slave packet format for Function Code 08H
Bit Function
0Alarm
1Trip
2 Internal fault
3Auto
4 Contactor A
5 Contactor B
6 Contact output 3
7 Drive available (communications control)
MASTER TRANSMISSION BYTES EXAMPLE DESCRIPTION
SLAVE ADDRESS 1 11 message for slave 17
FUNCTION CODE 1 07 read device status
CRC 2 4C 22 CRC error code
SLAVE RESPONSE BYTES EXAMPLE DESCRIPTION
SLAVE ADDRESS 1 11 message from slave
17
FUNCTION CODE 1 07 read device status
DEVICE STATUS (see definition
above)
1 2C status = 00101100 (in
binary)
CRC 2 22 28 CRC error code
MASTER TRANSMISSION BYTES EXAMPLE DESCRIPTION
SLAVE ADDRESS 1 11 message for slave 17
FUNCTION CODE 1 08 loopback test
DIAG CODE 2 00 00 must be 00 00
DATA 2 00 00 must be 00 00
CRC 2 E0 0B CRC error code

CHAPTER 1: COMMUNICATIONS GUIDE RS485 INTERFACE (MODBUS RTU)
MM300 MOTOR MANAGEMENT SYSTEM – COMMUNICATIONS GUIDE 9
Function Code 10H Modbus Implementation: Preset Multiple Registers
MM300 Implementation: Store Multiple Setpoints
This function code allows multiple Setpoints to be stored into the MM300 memory. Modbus
“registers” are 16-bit (two byte) values transmitted high order byte first. Thus all MM300
setpoints are sent as two bytes. The maximum number of Setpoints that can be stored in
one transmission is dependent on the slave device. Modbus allows up to a maximum of 60
holding registers to be stored. The MM300 response to this function code is to echo the
slave address, function code, starting address, the number of Setpoints stored, and the
CRC.
For example, consider a request for slave 17 to store the value 00 02 to setpoint address 04
5C and the value 01 F4 to setpoint address 04 5D. After the transmission in this example is
complete, MM300 slave 17 will have the following setpoints information stored:
The master/slave packets have the following format:
Table 8: Master/slave packet format for Function Code 10H
SLAVE RESPONSE BYTES EXAMPLE DESCRIPTION
SLAVE ADDRESS 1 11 message from slave
17
FUNCTION CODE 1 08 loopback test
DIAG CODE 2 00 00 must be 00 00
DATA 2 00 00 must be 00 00
CRC 2 E0 0B CRC error code
Address Data
04 5C 00 02
04 5D 01 F4
MASTER TRANSMISSION BYTES EXAMPLE DESCRIPTION
SLAVE ADDRESS 1 11 message for slave 17
FUNCTION CODE 1 10 store setpoints
DATA STARTING ADDRESS 2 04 5C setpoint address 04
5C
NUMBER OF SETPOINTS 2 00 02 2 setpoints = 4 bytes
total
BYTE COUNT 1 04 4 bytes of data
DATA 1 2 00 02 data for setpoint
address 04 5C
DATA 2 2 01 F4 data for setpoint
address 04 5D
CRC 2 31 11 CRC error code
SLAVE RESPONSE BYTES EXAMPLE DESCRIPTION
SLAVE ADDRESS 1 11 message from slave
17
FUNCTION CODE 1 10 store setpoints
DATA STARTING ADDRESS 2 04 5C setpoint address 04
5C
NUMBER OF SETPOINTS 2 00 02 2 setpoints
CRC 2 82 7A CRC error code

10 MM300 MOTOR MANAGEMENT SYSTEM – COMMUNICATIONS GUIDE
RS485 INTERFACE (MODBUS RTU) CHAPTER 1: COMMUNICATIONS GUIDE
Error Responses When a MM300 detects an error other than a CRC error, a response will be sent to the
master. The MSBit of the FUNCTION CODE byte will be set to 1 (i.e. the function code sent
from the slave will be equal to the function code sent from the master plus 128). The
following byte will be an exception code indicating the type of error that occurred.
Transmissions received from the master with CRC errors will be ignored by the MM300.
The slave response to an error (other than CRC error) will be:
SLAVE ADDRESS: 1 byte
FUNCTION CODE: 1 byte (with MSbit set to 1)
EXCEPTION CODE: 1 byte
CRC: 2 bytes
The MM300 implements the following exception response codes:
01 - ILLEGAL FUNCTION
The function code transmitted is not one of the functions
supported by the MM300.
02 - ILLEGAL DATA ADDRESS
The address referenced in the data field transmitted by the
master is not an allowable address for the MM300.
03 - ILLEGAL DATA VALUE
The value referenced in the data field transmitted by the
master is not within range for the selected data address.

CHAPTER 1: COMMUNICATIONS GUIDE RS485 INTERFACE (MODBUS RTU)
MM300 MOTOR MANAGEMENT SYSTEM – COMMUNICATIONS GUIDE 11
Modbus memory map
Modbus Hex Description Min Max Step Units Format Default Size in
Words
ACTUAL VALUES
PRODUCT INFORMATION
30001 0000 Product Device Code --- --- --- --- F22 N/A 1
30002 0001 Hardware Revision --- --- --- --- F15 N/A 1
30003 0002 Firmware Version --- --- --- --- F3 N/A 1
30004 0003 Display Software Version --- --- --- --- F3 N/A 1
30005 0004 Modification Number --- --- --- --- F1 N/A 1
30006 0005 Boot Version --- --- --- --- F3 N/A 1
30007 0006 Boot Modification # --- --- --- --- F1 N/A 1
30008 0007 Serial Number --- --- --- --- F22 N/A 6
30014 000D Order Code --- --- --- --- F22 N/A 16
30030 001D MAC Address --- --- --- --- F22 N/A 6
30036 0023 Database Version 0 0xFFFF F3 719 1
30037 0024 Build Date --- --- --- --- F22 N/A 6
30043 002A Build Time --- --- --- --- F22 N/A 4
30047 002E Original Calibration Date --- --- --- --- F18 N/A 2
30049 0030 Last Calibration Date --- --- --- --- F18 N/A 2
30051 0032 Communications Build Date --- --- --- --- F22 N/A 6
30057 0038 Communications Build Time --- --- --- --- F22 N/A 4
30061 003C Communications Revision --- --- --- --- F3 N/A 1
30062 003D Platform Version 0 0xFFFF 1 F3 120 1
30063 003E Reserved --- --- --- --- --- --- 1
▼▼▼ ▼ ▼ ▼▼▼▼ ▼
30185 00B8 Reserved 1
LAST TRIP DATA
30186 00B9 Cause of Last Trip --- --- --- --- FC134 N/A 1
30187 00BA Time of Last Trip 2 words --- --- --- --- F19 N/A 2
30189 00BC Date of Last Trip 2 words --- --- --- --- F18 N/A 2
30191 00BE Motor Speed During Trip --- --- --- --- FC135 N/A 1
30192 00BF Pre Trip Ia --- --- --- A F10 N/A 2
30194 00C1 Pre Trip Ib --- --- --- A F10 N/A 2
30196 00C3 Pre Trip Ic --- --- --- A F10 N/A 2
30198 00C5 Reserved --- --- --- --- --- --- 1
30199 00C6 Reserved --- --- --- --- --- --- 1
30200 00C7 Reserved --- --- --- --- --- --- 1
30201 00C8 Pre Trip Motor Load 0 2000 1 % F1 0 1
30202 00C9 Pre Trip Current Unbalance --- --- --- % F1 N/A 1
30203 00CA Pre Trip Ig --- --- --- A F10 N/A 2
30205 00CC Pre Trip Vab --- --- --- V F1 N/A 1
30206 00CD Pre Trip Vbc --- --- --- V F1 N/A 1
30207 00CE Pre Trip Vca --- --- --- V F1 N/A 1
30208 00CF Pre Trip Van --- --- --- V F1 N/A 1

12 MM300 MOTOR MANAGEMENT SYSTEM – COMMUNICATIONS GUIDE
RS485 INTERFACE (MODBUS RTU) CHAPTER 1: COMMUNICATIONS GUIDE
30209 00D0 Pre Trip Vbn --- --- --- V F1 N/A 1
30210 00D1 Pre Trip Vcn --- --- --- V F1 N/A 1
30211 00D2 Pre Trip System Frequency --- --- --- Hz F3 N/A 1
30212 00D3 Pre Trip Real Power --- --- --- kW F13 N/A 2
30214 00D5 Pre Trip Reactive Power --- --- --- kvar F13 N/A 2
30216 00D7 Pre Trip Apparent Power --- --- --- kVA F2 N/A 1
30217 00D8 Pre Trip Power Factor --- --- --- --- F21 N/A 1
30218 00D9 Reserved --- --- --- --- --- --- 1
▼▼▼ ▼ ▼ ▼▼▼▼ ▼
30222 00DD Reserved --- --- --- --- --- --- 1
REAL-TIME CLOCK
30223 00DE Weekday --- --- --- --- FC171 N/A 1
30224 00DF Date Read Only --- --- --- --- F18 N/A 2
30226 00E1 Time Read Only --- --- --- --- F19 N/A 2
30228 00E3 Daylight Savings Active --- --- --- --- FC126 N/A 1
30229 00E4 Reserved --- --- --- --- --- --- 1
TRIP COUNTERS
30230 00E5 Total Number of Trips --- --- --- --- F1 N/A 1
30232 00E7 Overload Trips --- --- --- --- F1 N/A 1
30233 00E8 Mechanical Jam Trips --- --- --- --- F1 N/A 1
30234 00E9 Undercurrent Trips --- --- --- --- F1 N/A 1
30235 00EA Current Unbalance Trips --- --- --- --- F1 N/A 1
30236 00EB Ground Fault Trips --- --- --- --- F1 N/A 1
30237 00EC Motor Acceleration Trips --- --- --- --- F1 N/A 1
30238 00ED Undervoltage Trips --- --- --- --- F1 N/A 1
30239 00EE Overvoltage Trips --- --- --- --- F1 N/A 1
30240 00EF Voltage Phase Reversal Trips --- --- --- --- F1 N/A 1
30241 00F0 Voltage Freq Trips --- --- --- --- F1 N/A 1
30242 00F1 Underpower Trips --- --- --- --- F1 N/A 1
30243 00F2 Reserved --- --- --- --- --- --- 1
▼▼▼ ▼ ▼ ▼▼▼▼ ▼
30256 00FF Reserved 1
GENERAL TIMERS
30257 0100 Number of Motor Starts --- --- --- --- F1 N/A 1
30258 0101 Number of UV Restarts --- --- --- --- F1 N/A 1
30259 0102 Motor Running Hours --- --- --- hrs F9 N/A 2
30261 0104 UVR Timer --- --- --- s F1 N/A 1
30262 0105 Start Timer 1 --- --- --- s F1 N/A 1
30263 0106 Start Timer 2 --- --- --- s F1 N/A 1
30264 0107 Start Timer 3 --- --- --- s F1 N/A 1
30265 0108 Start Timer 4 --- --- --- s F1 N/A 1
30266 0109 Start Timer 5 --- --- --- s F1 N/A 1
30267 010A TransferTimer --- --- --- s F1 N/A 1
30268 010B Power Loss Time 0 0xFFFF 1 ms F1 0 1
30269 010C Motor Stopped Hours --- --- --- hrs F1 N/A 1
START BLOCKS
Modbus Hex Description Min Max Step Units Format Default Size in
Words

CHAPTER 1: COMMUNICATIONS GUIDE RS485 INTERFACE (MODBUS RTU)
MM300 MOTOR MANAGEMENT SYSTEM – COMMUNICATIONS GUIDE 13
30270 010D Overload Lockout --- --- --- --- F1 N/A 1
30271 010E Starts/Hour Block --- --- --- s F1 N/A 1
30272 010F Time Between Starts 0 3601 1 s F1101
30273 0110 Restart Block --- --- --- s F1 N/A 1
30274 0111 Reserved --- --- --- --- --- --- 1
30275 0112 Pre-Contactor Timer --- --- --- s F1 N/A 1
30276 0113 Long Power Loss Time 0 0xFFFFFFFF 1 s F9 0 2
30277 0114 Reserved --- --- --- --- --- --- 2
▼▼▼ ▼ ▼ ▼▼▼▼ ▼
30282 0119 Reserved --- --- --- --- --- --- 1
CONTACT/VIRTUAL INPUTS/OUTPUTS STATUS
30283 011A Contact Input 64-33 (Bit Field) --- --- --- --- FC168 N/A 2
30285 011C Contact Input 32-1 (Bit Field) --- --- --- --- FC167 N/A 2
30287 011E Reserved --- --- --- --- --- --- 1
30288 011F Virtual Input 32-1 (Bit Field) --- --- --- --- FC167 N/A 2
30290 0121 Virtual Output 32-1 (Bit Field) --- --- --- --- FC167 N/A 2
30292 0123 Reserved --- --- --- --- --- --- 2
▼▼▼ ▼ ▼ ▼▼▼▼ ▼
30297 0128 Reserved --- --- --- --- --- --- 1
30298 0129 Contact Output 32-1 (Bit Field) --- --- --- --- FC167 N/A 2
30300 012B Reserved --- --- --- --- --- --- 1
30301 012C Reserved --- --- --- --- --- --- 1
SECURITY
30302 012D Current Security Access Level --- --- --- --- F1 N/A 1
30303 012E Reserved --- --- --- --- --- --- 1
30304 012F Reserved --- --- --- --- --- --- 1
STATUS - MOTOR
30305 0130 Motor Status --- --- --- --- FC129 N/A 1
30306 0131 Extended Status --- --- --- --- FC178 N/A 1
30307 0132 Thermal Cap Used --- --- --- % F1 N/A 1
30308 0133 Time to Overload Trip --- --- --- s F20 N/A 2
30310 0135 Drive Status --- --- --- --- FC143 N/A 1
30311 0136 Reserved --- --- --- --- --- --- 1
30312 0137 Command Status --- --- --- --- FC128 N/A 1
30313 0138 Time To Reset --- --- --- min F1 N/A 1
30314 0139 Reserved --- --- --- --- --- --- 1
▼▼▼ ▼ ▼ ▼▼▼▼ ▼
30327 0146 Reserved 1
CURRENT METERING
30328 0147 Ia --- --- --- A F10 N/A 2
30330 0149 Ib --- --- --- A F10 N/A 2
30332 014B Ic --- --- --- A F10 N/A 2
30334 014D Iavg --- --- --- A F10 N/A 2
30336 014F Motor Load --- --- --- % F1 N/A 1
30337 0150 Current Unbalance --- --- --- %Ub F1 N/A 1
30338 0151 Ig --- --- --- A F10 N/A 2
Modbus Hex Description Min Max Step Units Format Default Size in
Words

14 MM300 MOTOR MANAGEMENT SYSTEM – COMMUNICATIONS GUIDE
RS485 INTERFACE (MODBUS RTU) CHAPTER 1: COMMUNICATIONS GUIDE
VOLTAGE METERING
30340 0153 Va1 Angle --- --- --- ° F1 N/A 1
30341 0154 Vb1 Angle --- --- --- ° F1 N/A 1
30342 0155 Vc1 Angle --- --- --- ° F1 N/A 1
30343 0156 Ia Angle 0 359 1 ° F1 0 1
30344 0157 Ib Angle 0 359 1 ° F1 0 1
30345 0158 Ic Angle 0 359 1 ° F1 0 1
30346 0159 Reserved --- --- --- --- --- --- 1
▼▼▼ ▼ ▼ ▼▼▼▼ ▼
30357 0164 Reserved 1
30358 0165 Vab --- --- --- V F1 N/A 1
30359 0166 Vbc --- --- --- V F1 N/A 1
30360 0167 Vca --- --- --- V F1 N/A 1
30361 0168 Average Line Voltage --- --- --- V F1 N/A 1
30362 0169 Van --- --- --- V F1 N/A 1
30363 016A Vbn --- --- --- V F1 N/A 1
30364 016B Vcn --- --- --- V F1 N/A 1
30365 016C Average Phase Voltage 0 20000 1 V F1 0 1
30366 016D Freq --- --- --- Hz F3 N/A 1
30367 016E Reserved --- --- --- --- --- --- 1
▼▼▼ ▼ ▼ ▼▼▼▼ ▼
30375 0176 Reserved --- --- --- --- --- --- 1
30376 0177 VAux --- --- --- V F1 N/A 1
30377 0178 Voltage Unbalance 0 100 1 %Ub F1 0 1
30378 0179 IO Voltage 0 0xFFFF 1 V F1 0 1
30379 017A Reserved --- --- --- --- --- --- 1
▼▼▼ ▼ ▼ ▼▼▼▼ ▼
30383 017E Reserved --- --- --- --- --- --- 1
POWER METERING
30384 017F Power Factor --- --- --- --- F21 N/A 1
30385 0180 Real Power --- --- --- kW F13 N/A 2
30387 0182 Reserved --- --- --- --- --- --- 1
30388 0183 Reserved --- --- --- --- --- --- 1
30389 0184 Reactive Power --- --- --- kvar F13 N/A 2
30391 0186 Apparent Power --- --- --- kVA F2 N/A 1
30392 0187 MWh Consumption --- --- --- MWh F17 N/A 2
30394 0189 Mvarh Consumption --- --- --- Mvarh F17 N/A 2
30396 018B Mvarh Generation 0 999999999 1 Mvarh F17 0
30398 018D Apparent Power --- --- --- kVA F10 N/A 2
30400 018F Reserved --- --- --- --- --- --- 1
30405 0194 Phase A Real Power -50000 50000 1 kW F2 0 1
30406 0195 Phase A Apparent Power 0 50000 1 kVA F13 0 2
30408 0197 Phase A Reactive Power -50000 50000 1 kvar F2 0 1
30409 0198 Phase A Power Factor -99 100 1 eUnitPF F21 0 1
30410 0199 Phase B Real Power -50000 50000 1 kW F2 0 1
30411 019A Phase B Apparent Power 0 50000 1 kVA F13 0 2
Modbus Hex Description Min Max Step Units Format Default Size in
Words

CHAPTER 1: COMMUNICATIONS GUIDE RS485 INTERFACE (MODBUS RTU)
MM300 MOTOR MANAGEMENT SYSTEM – COMMUNICATIONS GUIDE 15
30413 019C Phase B Reactive Power -50000 50000 1 kvar F2 0 1
30414 019D Phase B Power Factor -99 100 1 eUnitPF F21 0 1
30415 019E Phase C Real Power -50000 50000 1 kW F2 0 1
30416 019F Phase C Apparent Power 0 50000 1 kVA F13 0 2
30418 01A1 Phase C Reactive Power -50000 50000 1 kvar F2 0 1
30419 01A2 Phase C Power Factor -99 100 1 eUnitPF F21 0 1
30420 01A3 Reserved 1
▼▼▼ ▼ ▼ ▼▼▼▼ ▼
30425 01A8 Reserved 1
TEMPERATURE METERING
30426 01A9 Internal Temp -40 125 1 °C F4 0 1
30427 01AA Hottest Stator RTD --- --- --- --- F1 N/A 1
30428 01AB Hottest Stator RTD --- --- --- °C F4 N/A 1
30429 01AC RTD 1 Temp --- --- --- °C F4 N/A 1
30430 01AD RTD 2 Temp --- --- --- °C F4 N/A 1
30431 01AE RTD 3 Temp --- --- --- °C F4 N/A 1
30432 01AF RTD 4 Temp --- --- --- °C F4 N/A 1
30433 01B0 RTD 5 Temp --- --- --- °C F4 N/A 1
30434 01B1 RTD 6 Temp --- --- --- °C F4 N/A 1
30435 01B2 Thermistor --- --- --- ohms F1 N/A 1
30436 01B3 Internal Temp Max -40 125 1 °C F4 0 1
30437 01B4 Reserved --- --- --- --- --- --- 1
30438 01B5 Reserved --- --- --- --- --- --- 1
30439 01B6 Reserved --- --- --- --- --- --- 1
DEMAND METERING
30440 01B7 Current Demand 0 100000 1 A F10 0 2
30442 01B9 Real Power Demand -50000 50000 1 kW F13 0 2
30444 01BB Reactive Power Demand -50000 50000 1 kvar F13 0 2
30446 01BD Apparent Power Demand 0 50000 1 kVA F2 0 1
30447 01BE Peak Current Demand 0 100000 1 A F10 0 2
30449 01C0 Peak Real Power Demand -50000 50000 1 kW F13 0 2
30451 01C2 Peak Reactive Power Demand -50000 50000 1 kvar F13 0 2
30453 01C4 Peak Apparent Power Demand 0 50000 1 kVA F2 0 1
30454 01C5 Reserved 1
▼▼▼ ▼ ▼ ▼▼▼▼ ▼
30466 01D1 Reserved 1
MOTOR STARTING LEARNED DATA
30467 01D2 Learned Acceleration Time --- --- --- s F2 N/A 1
30468 01D3 Learned Starting Current --- --- --- A F10 N/A 2
30470 01D5 Learned Starting Capacity --- --- --- % F1 N/A 1
30471 01D6 Reserved --- --- --- --- --- --- 1
▼▼▼ ▼ ▼ ▼▼▼▼ ▼
30483 01E2 Reserved --- --- --- --- --- --- 1
30484 01E3 Average Motor Load Learned --- --- --- %FLA F3 N/A 1
RTD MAXIMIUM TEMPERATURE
30485 01E4 RTD 1 MAX Temp --- --- --- °C F4 N/A 1
Modbus Hex Description Min Max Step Units Format Default Size in
Words

16 MM300 MOTOR MANAGEMENT SYSTEM – COMMUNICATIONS GUIDE
RS485 INTERFACE (MODBUS RTU) CHAPTER 1: COMMUNICATIONS GUIDE
30486 01E5 RTD 2 MAX. Temp --- --- --- °C F4 N/A 1
30487 01E6 RTD 3 MAX. Temp --- --- --- °C F4 N/A 1
30488 01E7 RTD 4 MAX. Temp --- --- --- °C F4 N/A 1
30489 01E8 RTD 5 MAX. Temp --- --- --- °C F4 N/A 1
30490 01E9 RTD 6 MAX. Temp --- --- --- °C F4 N/A 1
HMI
30495 01EE Current Menu Page Displayed 0 2 1 F1 0 1
30496 01EF Current Highlight Item Index 0 24 1 F1 0 1
30497 01F0 Current Display Page 0 39 1 F1 0 1
30498 01F1 Current Display Item Index 0 40 1 F1 0 1
30499 01F2 Reserved --- --- --- --- --- --- 1
▼▼▼ ▼ ▼ ▼▼▼▼ ▼
30504 01F7 Reserved --- --- --- --- --- --- 1
LED STATUS FOR GRAPHICAL AND BASIC CONTROL PANEL
30505 01F8 LED Status --- --- --- --- FC144 N/A 2
30507 01FA LED Flash --- --- --- --- FC130 N/A 1
30508 01FB Reserved --- --- --- --- --- --- 1
GCP FACTORY TEST
30509 01FC LCD Test Color --- --- --- --- FC212 N/A 1
30510 01FD Reserved --- --- --- --- --- --- 1
▼▼▼ ▼ ▼ ▼▼▼▼ ▼
30523 020A Reserved --- --- --- --- --- --- 1
USER MAP VALUES
30524 020B User Map Value 1 --- --- --- --- F1 N/A 1
30525 020C User Map Value 2 --- --- --- --- F1 N/A 1
30526 020D User Map Value 3 --- --- --- --- F1 N/A 1
30527 020E User Map Value 4 --- --- --- --- F1 N/A 1
▼▼▼ ▼ ▼ ▼▼▼▼ ▼
30645 0284 User Map Value 122 --- --- --- --- F1 N/A 1
30646 0285 User Map Value 123 --- --- --- --- F1 N/A 1
30647 0286 User Map Value 124 --- --- --- --- F1 N/A 1
30648 0287 User Map Value 125 --- --- --- --- F1 N/A 1
30649 0288 Reserved --- --- --- --- --- --- 1
▼▼▼ ▼ ▼ ▼▼▼▼ ▼
30656 028F Reserved --- --- --- --- --- --- 1
SELF TEST
30657 0290 Internal Fault Cause --- --- --- --- FC188 N/A 2
EVENT RECORDER
30659 0292 Event Recorder Last Reset 2
words
--- --- --- --- F18 N/A 2
30661 0294 Total Number of Events Since
Last Clear
--- --- --- --- F1 N/A 1
30662 0295 Cause --- --- --- --- FC134 N/A 1
30663 0296 Contactor --- --- --- --- FC136 N/A 1
30664 0297 Time --- --- --- --- F19 N/A 2
30666 0299 Date --- --- --- --- F18 N/A 2
30668 029B Ia --- --- --- A F10 N/A 2
Modbus Hex Description Min Max Step Units Format Default Size in
Words
Table of contents
Popular Control Unit manuals by other brands
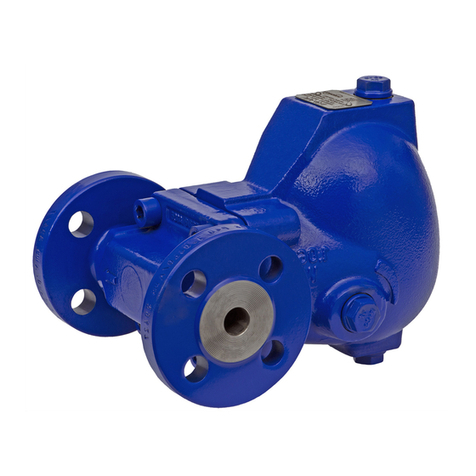
GESTRA
GESTRA UNA 43 Original Installation Instructions

Weidmüller
Weidmüller DPA/MAS operating instructions
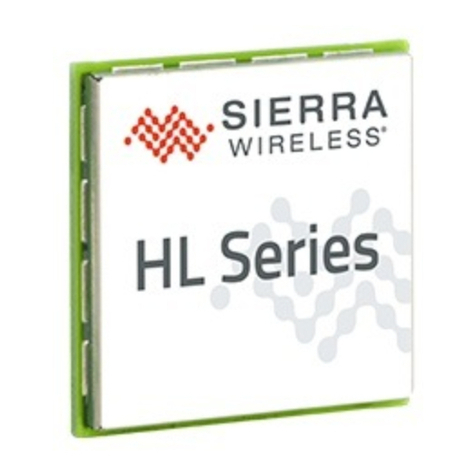
Sierra Wireless
Sierra Wireless AirPrime HL7519 user guide
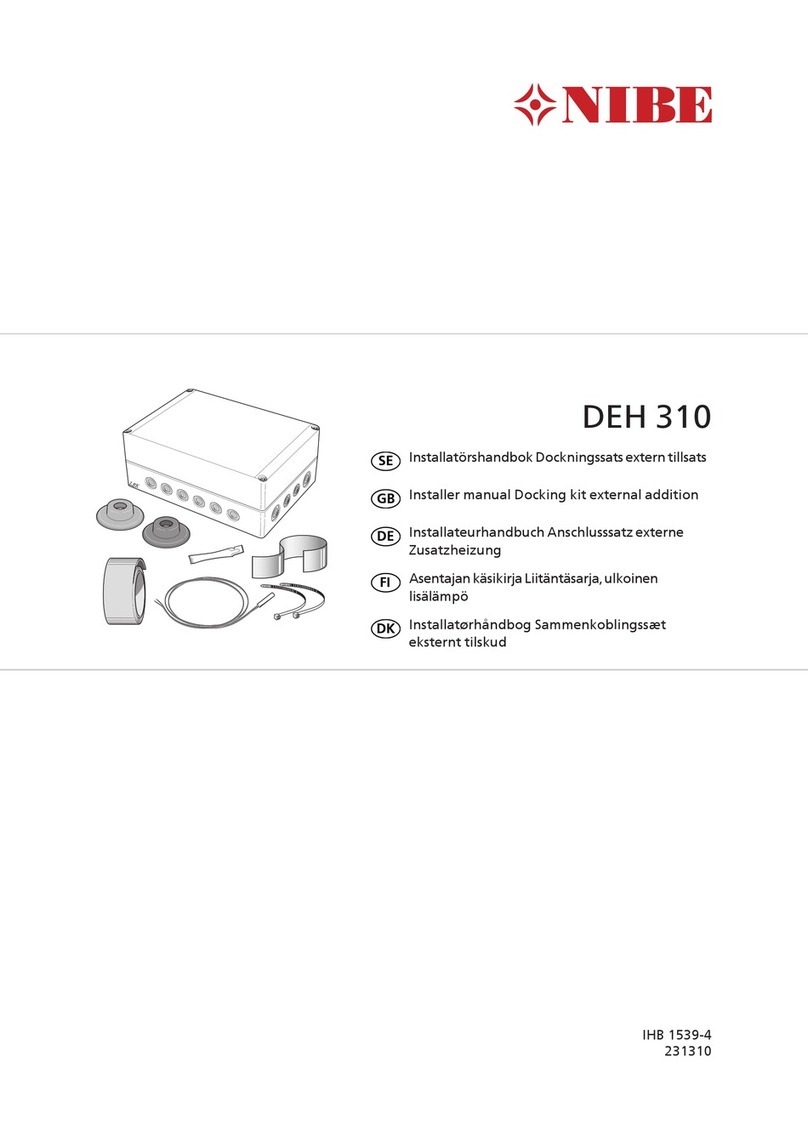
Nibe
Nibe DEH 310 Installer manual
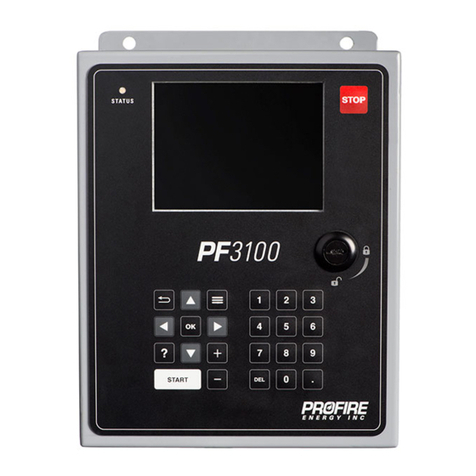
Profire Energy
Profire Energy PF3100 Series Operator's guide
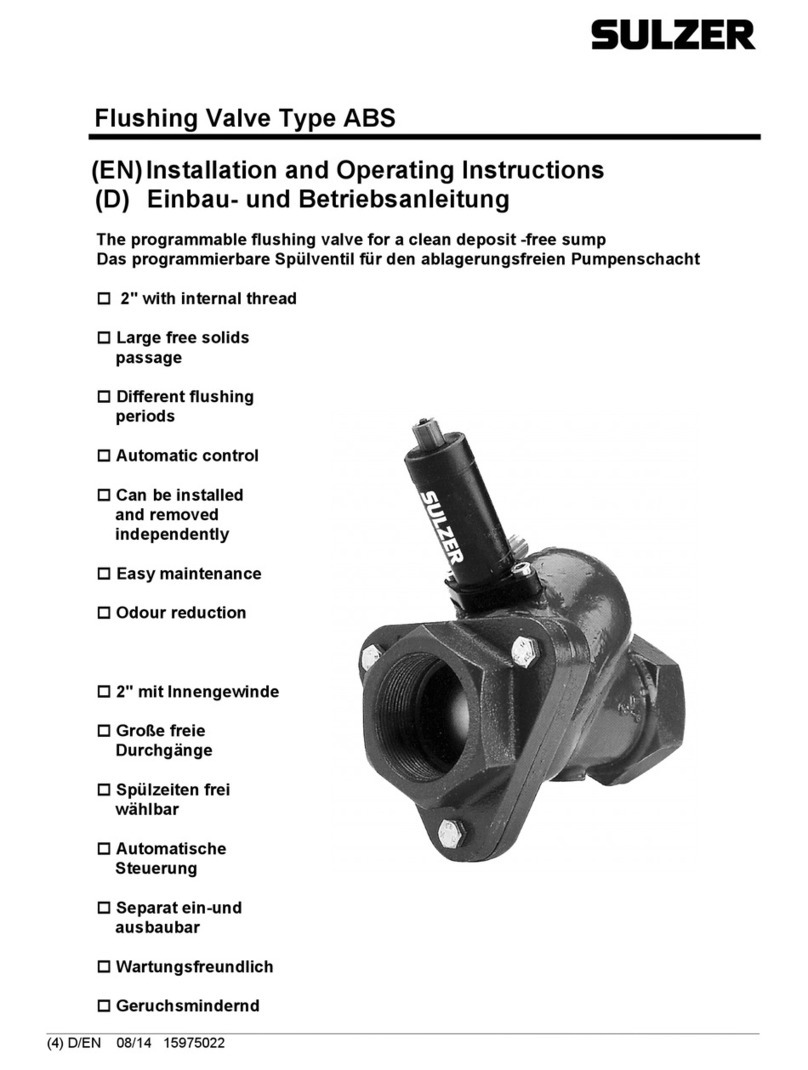
Sulzer
Sulzer ABS Installation and operating instructions

Keysight Technologies
Keysight Technologies 11713B Operating and service manual

Aetina
Aetina AIE-KO21 user manual
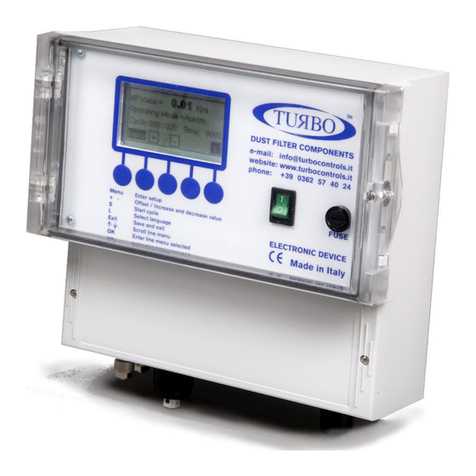
Turbo
Turbo Eco-Net 128 Use and maintenance instructions
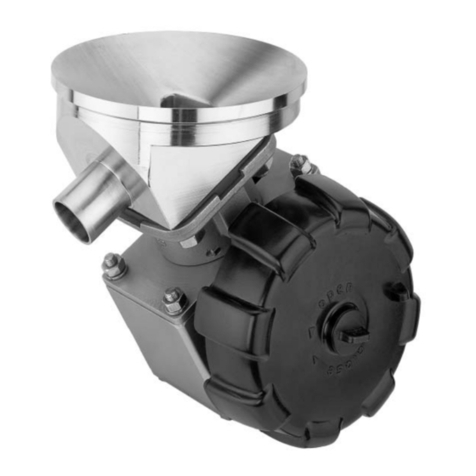
GEM
GEM 643 Series Installation, operating and maintenance instructions
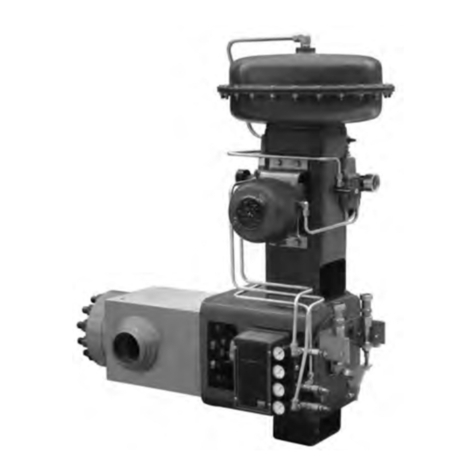
Emerson
Emerson Fisher Vee-Ball SS-84PSV4 instruction manual
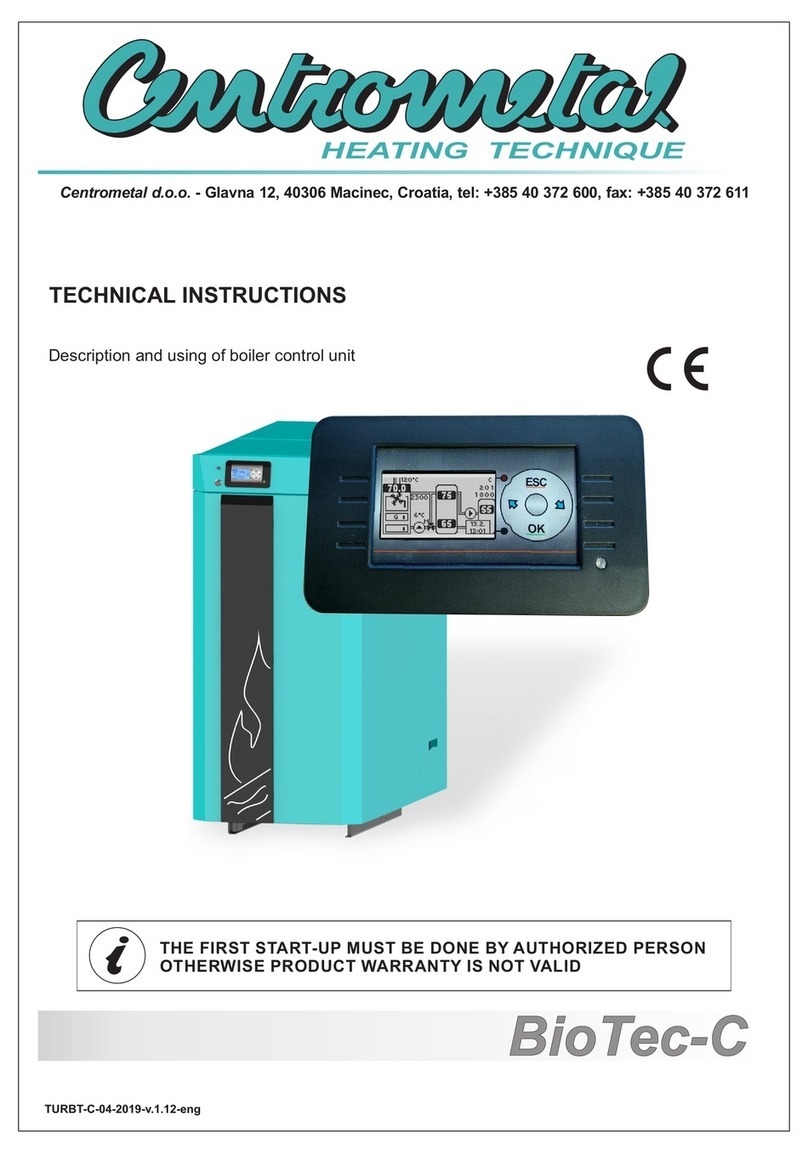
Centrometal
Centrometal BioTec-C Technical instructions