GE IBCG51E21 User manual

GEE-2022
Ground Relay Type
Front View
Rear View
Fig. I
Relay Removed Case
2
Directional
Overcurrent
IBCG
TAP
-
i
-
TAP
PLUG
BLOCK
TARGET
TIME
OVERCURRENT
UNIT
TAP
SCREW
SEAL
-
IN
UNIT
-
DRAG
MAGNET
DISK
SPRING
ADJUSTMENT
RING
LOW
GRADIENT
CONTACT
(
STATIONARY
)
-
.
LOW
BACKSTOP
SCREW
GRADIENT
CONTACT
(
MOVING
)
DIRECTIONAL
UNIT
TIME
OVER
-
'
CURRENT
UNIT
MAGNET
AND
COIL
4
ASSEMBLY
THYRlTE
—
CRADLE
TRANSFORMER
Type
IBCG
5
IE
Courtesy of NationalSwitchgear.com

,INTRODUCTION
Type relays are ground directional
current relays used primarily for the protection of
feeders and transmission lines. They are available
with either inverse, very inverse or extremely in-
verse time characteristics.
They consist of two units, a time overcurrent unit
(top) of induction disk type, and an instantaneous
power unit
(bottom)
of the induction cup
type.
The directional unit is either potential or cur-
rent polarized or both and, by means of its closing
contacts, directionally control,: the operation of the
time overcurrent unit.
Type relays are used for
of a single line. They low-range
coil which may be rated or am-
peres, although the ampere rating is also
available. Under normal conditions,
in either the or current polarizing coils;
nor is there any voltage
coils.
Fig. 9 shows the external connections when the
relay used in conjunction with phase
relays polarized from wye-wye
The polarizing voltage for the ground relay is
obtained by means of an auxiliary wye-broken-delta
potent&l transformer.
Fig.
10 shows the external connections for the
Type
ground relay when current
from a local source of ground current.
On some applications, system conditions may
at such that potential polarization is
desirable, and at other times be such that current
polarization would be preferred. The Type
relay, with its dual polarization feature, is well suit-
ed for such applications. The curves 2
the
its performance when either potential or current
polarized alone. The simultaneous use of both sets
of polarizing coils is advantageous on applications
where current and potent&l polarizing sources are
available and there is a possibility that one or the
other source may temporarily lost.
The differences between the various models
covered by this instruction book are shown Table 1.
Inverse time relays should be used on systems
where the fault current flowing through a given relay
is
by the
system generating cap-
acity at the time of the fault. Very inverse time and
extremely inverse time relays should be used in
cases where the fault current magnitude is depend-
ent mainly upon the location of the fault in relation to
the relay, and only slightly or not at all upon tbe
system generating setup. The reason for this is that
relays must
be
set to
be
selective with maximum
fault current flowing. For fault currents below this
value, the operating time becomes greater as the
current is decreased. If there is a wide range in
generating capacity, together in
circuit current with fault position, the operating time
with minimum fault current may
be
exceedingly long
with very inverse time relays and even longer with
extremely inverse time relays. For such cases, the
inverse time relay is more applicable.
The choice between very inverse and extremely
inverse time relays is more limited than between
them and the inverse time relay as they are more
nearly in their time-current characteristic
curves.
For grading with fuses the extremely in-
verse time relay should
be
chosen as the time-cur-
rent curves more nearly match the fuse curve.
Another advantage of the extremely inverse relay
is that
it is
better
suited than both the inverse and
very inverse relays for picking up cold load. For
any cold load pick-up capability, the resulting
settings will provide faster protection at high fault
currents with the extremely inverse relay than with
the less inverse relays.
TABLE I
Time Circuit
teristic
contacts
Inverse
One
Inverse
Very Inverse
Fig. 4
Very Inverse
Fig. 5
Inverse
Inverse Two
Fig. 6
PICKUP
When potential polarized, the directional unit
will operate at 3.6 volt-amperes at the
GROUND
DIRECTIONAL
OVERCURRENT
RELAY
TYPE
IBCG
IBCG
influenced
-
largely
over
-
the
directional
with
variation
short
-
APPLICATION
IBCG
ground
fault
pro
-
oper
-
tection
ating
have
a
0.5
/
2
1.5
/
6
4
/
16
no
cur
rent
flows
operating
alike
across
the
potential
polariz
-
ing
Type
IBCG
is
potential
transform
-
ers
.
given
IBCG
polarized
Internal
Connections
one
time
be
Relay
Model
Charac
-
Closing
IBCG
IBCG
51
E
IBCG
52
E
IBCG
53
E
IBCG
54
E
IBCG
77
E
Extr
.
IBCG
78
E
Extr
.
Fig
.
3
inFi
£
.
com
-
performance
of
the
relay
when
dual
polarized
Two
pare
with
One
Two
Fig
.
6
Fig
.
7
One
i
be
OPERATING
CHARACTERISTICS
in
maximum
3
Courtesy of NationalSwitchgear.com

Ground Directional Relay Type IBCG
Fig. 2
Typical Comparison of Current, Potential or Dual Polarization of Type Relay
Showing Effect of Local Ground Impedance
torque angle of degrees
When current polarized, it operate at approxi-
mately 0.5 ampere with operating and polarizing
coils connected in series. The performance of the
unit with simultaneous current and potential polar-
ization is typified Fig. 2.
The maximum operating current required to
close time overcurrent unit contacts, at any
time-dial position, be within five per cent of
the tap plug setting.
RESET
The minimum percentage of minimum closing
current
at which the time overcurrent reset
is 90% for inverse-time relays and 85% for very in-
verse extremely inverse time relays. When the
relay is de-energized, the time required for the disk
to completely reset to the number posi-
tion is approximately 6 seconds for inverse time re-
lays and 60
seconds for very inverse and extremely
inverse time relays.
OPERATING TIME
The time curves of the time overcurrent
are shown in Figs. 16, 17 and 18 respectively for
inverse-time, very inverse-time and extremely in-
verse-time relays.
For the same operating condi-
tions, the relay will operate repeatedly within one
or two per cent of the same time.
CURRENT COILS
The continuous and short time ratings of the
4
operating coil circuits are shown in Table The
current polarizing coils have a rating of
5 amperes and a one (1) second rating of 150 amperes.
RATINGS OF OPERATING COIL CIRCUITS
Ratings
* Cont.
One Sec.
Rating
(Amps)
1.5 100
l
*
1.5, 2, 2.5, 3, 4, 5, 6 5
200
4, 5, 6, 8, 10, 12, 16 10
220
l
The continuous rating of the operating circuit
limited by the directional operating coil.
Applies to very inverse and extremely inverse
time relays only.
The one second rating of in-
verse time relays is 65 amperes.
POTENTIAL COILS
The potential polarizing coils withstand 120
volts for
20 minutes and 360 volts for
10
seconds.
UNIT
The rating and impedance of the seal-in unit
for the 0.2
and
2 ampere taps are given in
The
tap used
by the trip coil.
GEH
-
2032
Overcurrent
tn
1
.
4
a
.
/
X
o
e
>
w
*
1
2
irt
-
‘
a
.
ui
Z
>
«
1
I
1.0
*
o
a
.
—
x
^
.
8
•
X
o
3
X
-
J
o
.
6
X
o
o
ui
—
m
O
CD
UJ
.
4
QC
a
.
2
0
<
<
(
±
KN
«
•
90
ft
'
*
ft
X
«
r
\
NO
r
-
(
090
o
©
o
oooooo
m
-
±
c
\
«
N
m
r
o
«
•
•
t
N
o
O
O
OO
O
Or
4
o
•
H
LOCAL
GROUND
SOURCE
IHPEDENCE
-
SEC
.
OMNS
I
BCG
60
lag
(
current
lags
voltage
)
,
will
n
.
continulus
the
TABLE
n
in
the
Tap
Tap
will
Range
(
Amps
)
Rating
(
Amps
)
(
Amps
)
0.5
,
0.6
,
0.8
,
1.0
1.2
,
1.5
,
2.0
0.5
/
2
1.5
/
6
uritwill
4
/
16
and
10
time
dial
is
unit
*
*
unit
will
SEAL
-
IN
RATINGS
Table
m
.
will
depend
on
the
current
drawn
setting
Courtesy of NationalSwitchgear.com

Ground Directional Relay Type IBCG
GEH-2032
Tbe 0.2 ampere tap is for use with trip coils
operate on currents ranging from 0.2 up to
2.0 amperes at the control voltage. this
tap is used with trip coils requiring more than
2 amperes, there is a possibility that the resistance
of ohms will reduce the current to so low a value
that the breaker not be tripped.
The tap should be used with trip
that take 2 amperes or more at minimum
control voltage, provided the current does not exceed
30 amperes at the control voltage.
the tripping current exceeds 30 amperes, the con-
nections should be arranged so the induction
unit contacts will operate an auxiliary relay which
in turn energizes the trip coil or coils. such
TABLE
UNIT RATINGS
0.2 AMP
TAP TAP
Res.
Inverse
8.00
Inverse
1.00
Inverse
0.32
Very
2.20
Very Inverse
0.36
Very Inverse
0.26
1.12
Inverse
0.13
Inverse
0.36
an application, it may be necessary to connect a
loading resistor parallel auxiliary
relay coil to allow enough current to operate the
target seal-in unit.
CONTACTS
The current-closing rating of induction unit
contacts is 30 amperes for voltages not exceeding
250 volts. Their current-carrying rating is limited
by the tap rating of the seal-in unit.
BURDENS
The capacitive burden of
circuit of the directional unit at GO cycles and 12
volts is 19.6 volt-amperes at 0.78 power factor.
The burden of the current polarizing circuit of the
directional unit at 80 cycles and 5 amperes is 8.6
volt-amperes at 0.95 power factor. Table IV
the current circuit burdens of the directiona
and
overcurrent unit operating coils (studs 5-6).
Ordinarily, the potential is in the open
corner of broken delta potential transformers and
current circuits are the residual circuits of
current transformers. The burden is, therefore,
only imposed for duration the ground fault
and need be considered only for this brief period.
TABLE IV
CIRCUIT OF DIRECTIONAL AND OVERCURRENT
UNIT OPERATING COILS AT GO CYCLES
BURDENS AT
MINIMUM PICKUP
I
React.
Ohms)
20.0
2.65
0.76
5.10
0.17
0.44
1.40
0.16
0.042
+ Volt-
3
Factor
Min.
22.5
5.60
2.90
0.83 13.3
5.60 1.40
0.85
0.96
0.51 8.15
1.80
0.46
0.21
0.41
0.053
0.88
0.36
0.35
0.38
0.40
0.43
0.51
0.62
0.62
0.65
IMPEDANCE Al
13.4
7.80
1.70
1.00
0.65
0.49
5.30
4.50
0.81
0.88
0.51
0.46
1.80
1.79
0.21
0.20
0.055 0.054
At Five
560.0
13.0
20.7
140.0
22.0
12.1
46.0
5.2
1.38
1
The impedance values are those for the minimum tap of each relay. The impedance for other taps,
at pick-up current (tap rating), varies inversely approximately as the square of the current rating.
Example: for the Type relay, amperes theimpedance of the 0.5 ampere tap is 22.5 ohms.
The impedance of 1 ampere tap, at 1 ampere, is approximately X 22.5 5.63 ohms.
+ Some companies list relay burdens only as the volt-ampere to operate at minimum pickup.
column is included so a direct comparison can be made. It should not be used in calculating volt-ampere
burdens in a CT secondary circuit, since the burden at 5 amperes is used for this purpose.
Calculated from burden at minimum pickup.
5
Overcurrent
with
the
in
which
If
minimum
7
will
the
2
-
ampere
coils
If
maximum
that
the
potential
polarizing
On
m
SEAL
-
IN
p
ves
2
AMP
circuit
3
Amps
0.3
Amps
7
Ohms
52
Ohms
30
Amps
3
Amps
0.13
Ohms
0.53
Ohms
Carry
-
Tripping
Duty
Carry
Continuously
D
-
C
Resistance
Impedance
(
60
cycles
)
the
in
the
of
CURRENT
BURDENS
OHMS
Tap
*
VA
Time
Character
-
istic
Power
L
0
Times
Ain
.
P
.
U
.
Times
P
.
U
.
Range
(
Amps
)
Eff
.
1
Imped
.
(
Ohms
)
(
Ohms
)
Amperes
(
Amperes
0.5
/
2
1.5
/
6
6.50
4
/
16
0.5
/
2
1.5
/
6
Inverse
4
/
16
0.5
/
2
1.5
/
6
Extr
.
‘
Inverse
Extr
.
4
/
16
Extr
.
*
given
0.5
/
2
IBCG
51
E
(
0.5
/
1
)
2
the
This
input
Courtesy of NationalSwitchgear.com

Fig. Internal Connections
(Front View)
Fig. 3
Internal Connections Relay
(Front View)
r
Fig. 5
Internal Connections Relay
(Front View)
8
Fig. 6
Internal Connections Relay
(Front View)
GEH
-
2032
Ground
Directional
Overcurrent
Relay
Type
IBCG
l
T
3
°
C
2
^
OPER
.
i
.
Cl
•
586
c
TOC
SHAD
11
C
COILS
C
2
*
)
UND
SHADING
COILS
T
i
:
c
2
i
Cl
D
“
-
C
2
—
pSVrn
D
RT
^
x
_
s
CL
^
^
POC
CURR
.
POL
.
TO
RITE
TOC
TNYRITE
»
>
TOC
P
3
D
1
POT
.
tr
Pi
ZlSI
POL
.
PS
^
.
D
n
u
POI
rmrv
^
s
,
•
S I
V
*
v
*
y
>
'
*
>
:
*
y
,
>
^
>
'
'
'
>
'
t
v
r
7
I
1
i
~
“
V
V
I
1
v
5
3
9
5
7
9
O
*
o
o
o
to
2
6
6
8
10
6
SI
-
SEAL
-
IN
UNIT
TOC
-
TIME
WERCURREMT
UNIT
D
-
DIRECTIONAL
UNIT
SI
-
SEAL
-
IN
UNIT
TOC
-
TIME
OVERCURRENT
UNIT
D
-
DIRECTIONAL
UNIT
*
m
SHORT
FfUGER
«
=
•
SHORT
FINGER
-
IBCG
5
IE
4
-
IBC
52
E
Relay
Cl
D
C
2
1
°
OPER
.
C
2
Cl
D
1
(
P
2
Vpi
PER
.
Cl
D
SI
C
2
7
>
TOC
:
:
c
2
WOUND
SHADING
COILS
D
D
D
C
3
^
C
4
CURR
.
POL
.
THYRITt
C
3
VC
4
CURR
.
POL
.
THYRITE
r
*
TX
*
TOC
1
TX
Os
I
Os
P
3
UJJJ
mrr
u
:
<
I
>
0
*
,
D
$
<
PCT
5
ocli
si
::
TX
rrrn
POT
.
P
4
POL
u
.
POL
.
<
o
ct
ar
<
Q
:
^
Sl
::
si
i
!
>
%
*
X
X
'
/
V
——
V
—
-
v
\
f
—
—
~
N
1
\
f
V
V
V
S
'
w
—
\
/
\
'
\
r
“
V
"
V
\
1
l
l
i
l
/
i
v
9
5
7
3
I
7
o
o
o
*
0
6
0
10
8
6
4
2
4
6
8
10
*
s
SHORT
FINGER
SI
-
SEAL
-
IN
UNIT
TX
-
TIME
OVERCURRENT
UNIT
D
-
DIRECTIONAL
UNIT
SI
-
SEAL
-
1
N
UNIT
TX
-
T
.
IME
OVERCURRENT
UNIT
D
-
DIRECTIONAL
UNIT
*
«
SHORT
FINGER
-
IBCG
53
E
-
IBCG
54
E
Courtesy of NationalSwitchgear.com

Ground Directional Overcurrent Relay Type
GEH-2032
Fig. B
Internal
(Front
Fig. 7
Internal Connections
(Front View)
Fig. 9 External Connections for IBCB
Fig. External for
for Directional Fault Protection of Single
for Ground Fault Of
Line Using Potential Polarization Line Using Current Polarization
IBCG
ci
C
2
IZC
2
S
-
TOC
~
z
si
i
:
TOO
-
:
C
2
WOUND
SHAOING
COILS
TOC
3
»
COILS
©
C
3
?
C
4
CURR
.
POL
.
THYRITE
co
*
>
TOC
CM
CURR
.
POL
-
THYRITE
-
TC
4
<
0
r
-
TOC
CM
i
o
fe
-
rc
4
TOC
P
3
o
1
#
r
*
.
^
POT
.
rVYYI
Lk
P
4
rr
~
i
it
Tociisi
it
TOC
POL
.
P
3
rVvr
,
9
D
5
:
>
POT
.
u
.
*
P
4
POL
.
z
<
CC
it
SI
SI
—
*
^
SI
X
*
I
*
\
f
\
F
V
V
V
o
f
'
f
V
V
'
*
X
9
9
'
9
—
1
'
I
\
9
V
'
V
111
1
3
V
r
V
"
i
CM
0
o
O
)
9
7
5
9
7
5
1
o
o
CM
o
To
o
D
10
8
o
6
4
2
o
8
6
4
2
*
*
SH
0
RT
FINGER
SI
=
SEAL
-
1
N
UNIT
TOC
-
TIME
OVERCURRENT
UNIT
D
-
OIRECTIONAL
UNIT
SI
-
SEAL
-
IN
UNIT
TOC
=
41
ME
OVERCURRENT
UNIT
D
-
OIRECTIONAL
UNIT
SHORT
FINGER
QO
9
Connections
-
IBCG
78
E
Relay
View
)
-
IBC
677
E
Relay
A
-
C
us
1
2
A
-
C
BJS
3
TO
NBJTRAL
OF
P
0
«
*
TRANSFORMER
WASE
RELAYS
U
>
Li
Ur
1
raca
^
V
1
CO
RUSE
RELAYS
1
^
CO
o
>
TO
%
10
XI
Hi
RUSE
QO
9
^
L
RELAYS
«
1
*
1
^
p
""
LA
^
7
LAJ
L
o
>
-
L
52
M
ejToc
*
9
TRIP
US
'
!
>
u
.
32
W
4
1
t
32
I
SIMILAR
CIRCUITS
FORMER
1
*
0
IP
1
SPi
«
SIMILAR
CIRCUITS
FOR
OTHER
TO
RELAYS
1
±
«
*
±
«
1
i
2
3
2
1
-
J
-
52
2
ROTE
:
RELAY
OPERATES
FOR
FAULTS
IN
DIRECTION
OF
JRRCW
.
3
2
1
*
CO
a
NOTE
:
RELAY
OPERATES
FOR
FAULTS
IN
DIRECTION
OF
ARROW
.
I
52
00
TC
co
o
>
l
-
l
«
<
67
N
-
GHOUWO
DIRECTIONAL
OYE
.
tt
.
UMam
RELAY
—
—
-
nr
_
DIRECTIONAL
UNIT
OPERATING
COIL
PC
-
DIRECTIONAL
UNIT
POLARIZING
COIL
ac
(
-
)
TOC
-
TIME
OVERCURRENT
UNIT
D
-
DIRECTIONAL
UNIT
SI
-
SEAL
-
IN
WITH
TARGET
PCI
AY
K m
-
GROUP
PI
RECTI
ORAL
OMERGURROII
DIRECTIONAL
IMIT
HPEWATIHG
CQIl
PC
-
DIRECTIONAL
J
»
lT
POLARIZING
001
96
TOC
-
TIMt
UViNUJNHtal
unIT
D
-
DIRECTIONAL
UNIT
SI
-
SEAL
-
IN
WITH
TARGET
o
»
T
<
:
Ml
.
.
»
»
l
—
52
-
P
TC
-
TRIP
COIL
Ol
TC
-
TRIP
0
)
1
L
Connections
Type
I
BCG
Relays
Protection
a
Single
10
Relays
Type
Directional
Ground
a
7
Courtesy of NationalSwitchgear.com

Ground Directional Relay Type
Stationary Contact Assembly
Moving Contact Assembly
B Contact
J
C Contact Tip
Support
Brush
L Mounting Screw
D Contact An
F Contact
Fig. II Gradient Contact Assembly For The Directional Unit
RECEIVING, HANDLING AND STORAGE
These relays, when not included as a part of a
control panel will be shipped in cartons designed to packing the relay in order that none of the parts are
protect them against damage. Immediately
injured or the adjustments disturbed.
of a relay, examine it for any damage sustained
in transit. If injury or damage resultingfrom rough
If the relays are not to
be
installed
handling is evident, file a damage claim at once with
should
be stored
in their original cartons
the transportation company and promptly notify the
in a place that is free from moisture, dust and
nearest General Electric Apparatus Sales Office.
metallic chips. Foreign matter collected on the
outside of the case may find its way inside when
Reasonable care should be exercised in
the cover is removed and cause trouble in the
of the relay.
DESCRIPTION
TIME
The inverse time unit consists of a
tapped current operating coil wound on a U-magnet
iron structure.
The tapped operating coil is con-
nected to taps on the tap block. The U-magnet con-
tains wound shading coils which are connected in
series with the directional unit contacts.
When
power flow is in such a direction to close the
directional unit contacts, the shading coils act to
produce a split-phase field which, in turn, develops
torque on the operating disk.
The very inverse and extremely inverse time
units are of the type similar
to that
used
in meters except as follows:
the upper portion of the iron structure has two con-
centric windings on the middle leg of the magnetic
circuit. One of these is a tapped current winding
connected to taps on the tap block, the other is a
floating winding which is connected in series with
the directional unit contacts, a resistor, and the two
coils on the lower legs of the magnetic
When power flow is in such a direction as to close
the directional unit contacts, the unit develops torque
on the operating disk.
The disk shaft carries the moving contact which
completes the trip circuit when it touches the sta-
tionary contact or contacts. The is restrained
by a spiral spring to give the proper contact-closing
current, and its motion is retarded by a permanent
magnet acting on the disk to produce the desired
time characteristic. The variable retarding force
resulting from the gradient of the spring is
compensated by the spiral shape of the induction
disk,
which results in an increased driving force as
the spring winds up.
The directional unit is of the induction-cylinder
construction with a having eight
poles projecting inward and arranged symmetrically
GEH
-
2032
Overcurrent
M
I
A
'
•
sr
B
%
*
JET
D
H
G
'
F
E
A
-
Contact
Dial
Brush
-
Stop
Screw
K
-
Contact
Tip
G
-
Contact
Brush
Retainer
H
-
Contact
Retainer
M
-
Locknut
E
-
Contact
Brush
Low
upon
re
-
ceipt
immedi
-
ately
,
they
oper
-
ation
un
-
OVERCURRENT
UNIT
circuit
.
overcurrent
shaft
as
spiral
overcurrent
wattmetric
watthour
DIRECTIONAL
UNIT
laminated
stator
8
Courtesy of NationalSwitchgear.com

around a stationary central core.
The cup-like
aluminum induction rotor is free to rotate in the
annular air gap between the poles and the core.
The poles are fitted with current operating, current
polarizing, and potential polarizing coils.
The principle by which torque is developed is
the same that of an induction disk relay with a
wattmetric element, although, arrangement of
parts, the unit is more like a split-phase induction
motor.
The induction-cylinder construction pro-
vides higher torque and lower rotor inertia than the
induction-disk construction, resulting in a faster
and more sensitive relay.
A seal-in unit is
mounted
on the left side of the
unit as indicated in Fig. 1. This unit has
its series
and
its contacts in parallel with the
main contacts of the overcurrent unit, arranged in
such a manner when the main contacts close, the
seal-in unit picks up and seals-in around the
contacts. When the seal-in unit operates, it raises a
target into view which latches up and remains ex-
posed until manually released by pressing the button
located at the lower-left corner of the cover.
The directional unit contacts which control the
time overcurrent unit, are shown in Fig. 11. They
are of the low gradient type specially constructed to
minimize the effects of vibration. Both the stationary
and moving contact brushes are made of low gradient
material which, when subjected to vibration, tend to
follow one another, hence, they resist contact sep-
aration.
The contact d&l (A) supports the stationary con-
tact brush (B) on which is mounted a conical contact
tip (C). The moving contact arm supports the
moving contact brush (E) on which is but-
ton contact tip
end of the moving contact
brush bears against the inner face of the moving con-
tact brush retainer (G).
Similarly, the end of the
stationary contact brush bears against the inner face
of the stationary contact brush retainer (Ii). The
stop screw mounted on the contact dial, functions
to stop the motion of the contact arm by striking the
moving contact brush retainer the moving and
stationary contact members have
made contact.
stationary contact support and the contact are
assembled together
b
means of a mounting screw (L)
and the two locknuts M).
Ground Directional Overcurrent Relay Type
GEH-2032
INSTALLATION
The location should be clean and dry, free from
dust and excessive vibration and well lighted to
inspection testing.
The relay should be mounted on a
vertical
surface. The outline panel drilling diagram is
shown in Fig. 19.
The internal connection diagrams for the various
relays are shown in Figs. 3 to Typical wiring
are shown 9 and 10. Since
is important for-the correct operation of
Type relays, the rotation specified in Figs.
9 and 10 must be adhered to. Unless mounted on
a steel panel which adequately grounds the relay
case, it is recommended that the case be grounded
through a mounting stud or screw a con-
ductor not less B S gauge copper wire
or its equivalent.
At the time of the relay should
be
inspected
for
tarnished contacts, loose screws, or
other imperfections.
If trouble is found, it
should be corrected in the described under
CAUTION
Every circuit in the case has an
auxiliary brush. It is especially important on
current circuits and other circuits shorting
bars that the auxiliary brush be bent high enough
to engage connecting plug or test plug before
the main brushes do.
This CT sec-
ondary circuits from being opened.’
Fig. Section of Case Show-
ing Position of Auxiliary Brush
Before the relay is put into service, it should
be given a check to determine that factory adjust-
ments have not been disturbed. The time dial will
be set at zero before the relay leaves the factory.
It is necessary to change this setting in order to
open the time overcurrent unit contacts.
Q
IBCG
CONTACTS
as
i f
(
D
)
mounted
a
SEAL
-
IN
UNIT
(
F
)
.
The
overcurrent
coil
in
(
J
)
,
that
after
main
The
(
K
)
dial
5
LOCATION
drawout
with
and
facilitate
the
MOUNTING
will
Drevent
and
CONNECTING
°
LJG
Mi
N
BROS
*
CONNECTING
BLOCK
CONNECTIONS
8
.
phase
diagrams
sequence
IBCG
in
Figs
.
TERMlNA
.
9
^
0
C
*
>
A
„
XIL
'
ARY
BRUSH
NO
’
E
Af
TER
ENGAG
'
NS
AJXliJARY
BRUSH
,
CONNECTING
PLUG
TRAVELS
'
A
>
NCH
9
E
1
CRF
ENGAGING
THE
MA
;
\
BRUSH
ON
THE
TERMINAL
BLOCK
with
12
Cross
Drawout
than
#
12
&
OPERATION
INSPECTION
installation
,
any
manner
MAINTENANCE
.
Courtesy of NationalSwitchgear.com

Ground Directional Relay Type IBCG
ADJUSTMENTS
TARGET AND SEAL-IN UNIT
When used with trip coils operating on currents
ranging from 0.2 to 2.0 amperes at the minimum
control voltage, the target and seal-in tap screw
should be set the tap. When the trip
coil current ranges from 2 to 30 amperes at the
minimum control voltage, the tap screw should be
placed in the 2.0 ampere tap.
The seal-in tap screw is the screw holding
the right-hand stationary contact of the seal-in unit.
To change the tap setting, first remove the connect-
ing plug. Then take a screw from the left-hand sta-
tionary contact and place it in the desired tap.
Next,
remove the screw from the other tap and place it
back in the left-hand contact. This procedure is
necessary to prevent the right-hand stationary con-
tact from getting out of adjustment.
CURRENT SETTING
The minimum current at which the time
current unit will close its contacts is determined
by the position of plug in the tap block. The tap
block
IS
marked amperes, as shown
When the tap setting changed with the relay in
its case, the following procedure must be followed:
(1) remove the connecting plug; this de-energizes
the relay and shorts the current transformer sec-
ondary (2) remove the tap plug and place
it the tap marked for the desired pickup current.
(3) replace the connecting plug.
The minimum current required to rotate the
disk slowly and to close the contacts with-
in five per cent of the value marked on the tap plate
for any tap setting and time dial position. this
adjustment has been disturbed, it can be restored by
means of the spring adjusting ring. The ring can be
turned by inserting a screw driver blade in the
notches around the edge. By turning the ring, the
operating current of the unit can be brought into
agreement with the tap setting employed. This ad-
justment also permits any desired setting to be ob-
tained intermediate between the available tap settings.
Test connections for making pickup and time
checks on the time overcurrent unit are shown in
Fig. 13 and Fig. 14.
Use a source of 120 volts or
greater with good wave form and constant frequency.
transformers or phantom loads should not
be employed in testing induction relays since their
use may cause a distorted wave form.
SETTING
The operating of the time overcurrent unit
for any value of current and tap setting is
determined by the time setting. This operating
time is inversely proportional to the current magni-
tude as illustrated by the time curves in Figs. 16, 1’7
10
and 18. Note that the current values on these curves
are given as multiples of the tap setting. That is,
for a given time dial setting, the time will be the
same for 80 on the ampere tap as for 50
amperes on the 5 ampere tap, since in both cases,
the current is 10 times tap setting.
selective action of two or more relays is
required, determine the maximum possible short-
circuit current of the line and then choose-a time
value for each relay that differs sufficiently to in-
sure the proper sequence the operation of the
several circuit breakers. Allowance must be made
for the time involved in opening each breaker after
the relay contacts close. For this reason, unless
the circuit time of operation is
there should be a difference of about 0.5 second
(at the maximum current) between relays whose
operation is to be selective.
EXAMPLE OF
The time and current settings of the time
overcurrent unit can be made easily and quickly.
Each time value shown in Figs. 16, 17 and indi-
cates the time required for the contacts to close with
a particular time-dial setting when the current is a
prescribed number of times the current-tap, setting.
In order to obtain any particular time-current set-
ting, insert the removable plug in the proper tap
receptacle and adjust the time dial to the proper
position.
The following example illustrates the
procedure in making a relay setting.
Assume that the breaker is being used a cir-
cuit where the circuit breaker should trip on a sus-
tained current of approximately 450 amperes, and
that the breaker should trip in one second on a short-
circuit current of 3750 amperes. Assume further
that current transformers of ratio are used.
The current tap setting is found by dividing
minimum primary tripping current by the
transformer ratio.
equals 7.5 amperes.
this case, 450 divided
Since there is no 7.5 ampere
the B-ampere tap is used. To find the proper
time-dial setting to one second time delay al
3750 divide 3750 the transformer ratio.
This 62.5 amperes current which
is 7.3 times the &l-ampere setting. By referring to
the time-current curves 16. 17 and 113. it will
be seen that 7.3 times the operating cur-
rent gives a one second time delay for a No. 3.4
time dial setting on an inverse time relay a No. 5.3
time dial setting on a very inverse time relay and a
No. 10 time dial setting on an extremely inverse
time relay.
The above results should checked by means
of an accurate timing device. Slight readjustment of
the dial can be made until the desired time is
obtained.
Aid in making the proper selection of relay
settings may be obtained on application to the near-
est Sales of the General Electric Company.
GEH
-
Z
032
Overcurrent
TIME
OVERCURRENT
UNIT
8
amperes
in
0.2
-
ampere
If
in
unit
known
with
accuracy
,
SETTING
18
,
over
-
the
plate
on
this
in
Table
II
.
in
is
winding
.
in
in
60
/
1
should
be
If
current
by
6
C
In
tap
,
give
by
amperes
.
gives
secondary
Figs
.
minimum
Stepdown
be
TIME
time
given
dial
Office
Courtesy of NationalSwitchgear.com

Ground Directional Relay Type IBCG GEH-2032
Fig.
Test Connections for Checking Pickup and
Operating Time of the Time Overcurrent Unit Using
Current Polarization
POLARITY CHECK
The polarity of the external connections to the
directional unit, when it is potential polarized, may
be checked using load currents. The idea is to
tat” current from one current transformer and
voltage from the same phase. The voltage is
ob-
tained by phase 1 from the primary of the
wye-broken-delta transformer and shorting the
phase-one primary winding. Current is obtained by
shorting the current transformers in phases two
and three and opening their circuits to the relay.
This permits the current transformer in phase one
to supply the operating current.
Connect a phase angle meter to
read
the angle
between the current and voltage supplied to the relay.
Fig.
Test Connections for Checking Pickup and
Operating Tine of the Time Overcurrent Unit Using
Potential Polarization
The relay has maximum torque at 60 degrees fag.
With power flowing in the proper direction for oper-
ation, the relay should
in plus or of the maximum torque
angle.
If the unit is current from a current
transformer in the power transformer neutral, such
a check is not easily made. It is sometimes prac-
tical to introduce a single phase current in one
phase of the primary circuits in such a way that
current flows through both the transformer neutral
current transformer and one of the line current
transformers.
If this cannot be done, a careful
wiring check must suffice.
Fig. 15 shows the test connections for checking
the polarity of the directional unit itself.
MAINTENANCE
It is recommended that a mechanical
tion and an operational test be performed at least
These relays are adjusted at the factory and it
annually and if possible at the same time associated is advisable not to disturb the adjustments. If, for
equipment is
tested.
any reason, they have been disturbed, the following
points should
be
observed in restoring them:
The interval of may vary depending on
the relative importance of individual protective
equipment, their exposure to unfavorable conditions,
DISK AND BEARING6
such as extreme heat, moisture or fumes. Dust and
may contaminate the relay when the protective
cover is removed. The lower jewel should be turned up until the
disk is centered in the air gaps, after which it
11
Overcurrent
120
VOLT
AC
TEST
SOURCE
120
VOLT
AC
TEST
SOURCE
T
PCTENT
'
M
’
ER
43
OHMS
>
.
4
On
On
LOAD
LOAD
BOX
BOX
120
VOLTS
60
CYCLES
0
A
10
8
-
9
7
V
7
13
m
DIRECTIONAL
UNIT
operate
for
phase
angles
with
-
o
minus
60
degress
C
7
>
JO
polarized
ob
-
removing
O
)
U
-
inspec
-
TIME
OVERCURRENT
UNIT
time
dirt
Courtesy of NationalSwitchgear.com

Fig. 15 Test Connections for Checking Polarity of
the Directional Internal Connections
should be locked in this position by the set screw
provided for this purpose. The upper bearing pin
should next be adjusted so that the disk shaft has
about inch end play.
CONTACT ADJUSTMENT
The contacts should have about inch wipe.
That is, the stationary contact tip should be de-
flected about when the disk completes its
travel. Wipe is adjusted by turning the wipe adjust-
ment screw thereby adjusting the position of the
brush relative to the brush stop. On two-circuit
closing relays, the two stationary contact tips
should be in the same vertical plane.
When the time dial is moved to the position
where it holds the contacts just closed, it should
indicate on the time-dial scale. If it does not
and the brushes are correctly adjusted, shift the
dial by changing the position of the arm attached to
the shaft just below the time dial. Loosen the screw
clamping the arm to the shaft and turn the arm
relative to the shaft until the contacts just make
for time-dial setting.
BEARINGS
The lower jewel bearing should be screwed all
the way in until its head engages the end of the
12
. GEH-2032
Ground Directional Relay Type
threaded core support.
The upper bearing should
to allow about
inch end play to the
To check the clearance between the iron
and the inside of the rotor cup, press down on
contact arm near the shaft, thus depressing
spring-mounted jewel until the cup strikes the iron
The shaft should move about inch.
CUP AND
Should it be necessary to remove the
rotor from the directional unit, the following pro
cedure should be followed:
All leads to the unit should first be
and tagged for identification in reconnecting. Th
“nit can then be removed from the cradle with it;
mounting plate still attached.
The upper of the three flat-head
the “nit to the plate should now be removed. 0
some models, it may be necessary to remove
resistor or capacitor to expose this screw. Th
four corner screws clamping the “nit together
should next be removed, and the entire top
lifted off.
This gives access to the cup as
sembly and exposes the assembly,
should be protected to keep it free from dust
metallic particles until the “nit is reassembled.
To remove the shaft and rotor from the
head assembly, the spring clip at the top of the
must be pulled out and the clutch adjusting
out of the side of the molded contact
The shaft and can now be pulled out of
molding.
The rotor must be handled very
while it is out of the unit.
CONTACT ADJUSTMENTS
To
contact adjustments, refer to Fig. I
for identification of low gradient contact parts
proceed as follows:
Loosen the locknut which secures the
screw (located at the right hand corner of the uni
to its support.
Unwind the backstop screw so
the moving contact arm is permitted to
Adjust the tension of each low gradient
brush so that l-2 grams of pressure are
at the contact tip in order to cause the end of
brush to separate from the inner face of its
spective brush retainer. Adjust the spiral
until the moving contact arm is in a neutral pos
i.e., with the arm pointing directly
Loosen the locknut which secures the
contact mounting screw to the stationary
support.
Wind the mounting inward until
and contact
. Unwind the mounting screw until
stationary contact stop screw lines up with tl
moving contact brush retainer. Wind the
screw inward until the moving
and
members again just begin to touch.
the locknut of the stationary contact stop
advance this screw until it just touches the
contact brush retainer. Unwind the screw l-l
Overcurrent
IBCG
SOJRCE
OF
R
&
TED
VOlTAGE
1
/
64
be
adjusted
shaft
.
coi
50
OHM
RESISTOR
9
1
/
16
POTENTIAL
f
3
*
POLARIZING
COIL
10
STATOR
OPERATING
5
<
>
COIL
cup
-
tyi
6
A
)
POTENTIAL
POLARIZATION
120
VOLT
SOURCE
disconnect
*
OPERATING
5
screws
holdii
COIL
6
ft
50
OHM
u
RESISTOR
CURRENT
7
POLARIZING
<
>
strui
COIL
8
ture
whii
stator
8
)
CURRENT
POLARIZATION
THE
DIRECTIONAL
UNIT
CONTACTS
SHOULD
CLOSE
WHEN
THE
RELAY
IS
ENERGIZED
WITH
EITHER
C
*
THE
ABOVE
CONNECTIONS
.
aj
NOTE
:
conta
shi
scr
taken
ari
Un
i
t
11
cup
careful
1
/
64
make
ai
1
/
32
backst
1
/
32
inch
th
swing
frei
conta
requin
iy
-
t
r
spri
zero
forwar
stationa
conta
tion
,
t
:
screw
members
just
beg
.
.
.
^
moving
stationary
to
touch
.
i
«
zero
DIRECTIONAL
UNIT
backst
stationary
coi
Loos
i
screw
,
ai
movii
tact
Courtesy of NationalSwitchgear.com

Ground Directional Relay Type IBCG
GEH-2032
turns to provide contact wipe. Tighten the locknut.
Unwind the backstop screw turn and tighten the
locknut which secures the backstop screw to its
support.
Finally, adjust the tension on the
ary contact brush such that, when the contacts are
made and fully wiped in, there is approximately an
equal deflection on each brush.
TORQUE ADJUSTMENT
Connect the current operating and current
polarizing coils in series by connecting a jumper
across terminals 6 and 7. Apply current to ter-
minals 5 and 6 and adjust the directional unit
spring so that the unit picks up at 0.5 ampere.
The core of the directional unit has a small
flat portion, the of which is to minimize
the effect of bias torques produced on the rotor.
Such torques can be produced by any one of the
operating or polarizing quantities acting alone with
the other two circuits de-energized. Theadjustment
of the core is made at the factory, but may be check-
ed by observing that the unit responds as outlined
below:
Short out the potential coil (ter-
minals 9 and leaving the current polarizing
coil (terminals 7 and 8) unshorted. Supply 30 am-
peres through the operating coil (terminals 5 and 6)
and check that the unit does not operate.
If the unit does not satisfy the above condition,
rotate the core to a position which causes it to do
so. The core can be turned by loosening the large
hexagonal nut at the bottom of the unit and turning
the core by means of the slotted bearing screw.
This screw should be held securely in position when
the nut is retightened.
Keep in that 30 amperes cause the
current coils to overheat if left on too long.
There-
fore, leave the test current on only for shot inter-
vals and allow sufficient time between tests for the
coils and to cool.
CLUTCH ADJUSTMENT
The connections show” in Fig. 15 for the polar-
ity check can also used in making the clutch ad-
justment. The clutch should be
potential or current polarization, not both. The 50
ohm resistor should be replaced an adjustable
resistor capable of providing the current range
listed in Table V relay rating in question. A
screw, projecting from the side of the moving con-
tact controls the clutch pressure, and
quently
the current value at which the clutch will
slip.
With rated frequency (and at rated volts for
polarization), the clutch should be set to
slip the current values listed in Table V.
TABLE V
CLUTCH ADJUSTMENTS
Method Of
Tap Range Amperes For
Polarization
Clutch To Slip
Current 10-15
Current 10-15
Current 20-25
7-10
Potential
7-10
Potential 12-15
For cleaning fine silver contacts, a flexible
burnishing tool should be used. This consists of a
flexible strip of metal with an etched roughened
surface, resembling in effect a superfine file. The
polishing action is so delicate that no scratches are
left, yet corroded material will be removed rapidly
and thoroughly.
The flexibility the tool Insures
the cleaning of the actual points of contact.
Fine silver contacts should not be cleaned with
knives, files or abrasive paper or cloth. Knives or
files may leave scratches which increase arcing and
deterioration of the contacts. Abrasive paper or
cloth may leave minute particles of insulating ab-
rasive material in the contacts thus preventing
contact closing.
The burnishing tool described above can be
obtained from the factory.
RENEWAL PARTS
It is recommended that sufficient quantities of
nearest Sales Office of the General Electric
renewal parts be carried in stock to enable the prompt pany, specify quantity required, of partwanted,
replacement of any broken, or damaged.
and complete nameplate data. If possible, give
the Electric Company requisition number
When ordering renewal parts, address the
on which the relay was furnished.
13
Overcurrent
with
2
/
3
for
*
the
station
-
conse
-
arm
,
potential
a t
spiral
(
Amps
)
•
urpose
0.5
/
2
1.5
/
6
4
/
16
0.5
/
2
1.5
/
6
Potential
4
/
16
polarizing
10
)
,
CONTACT
CLEANING
of
will
mind
thy
rite
be
adjusted
using
either
Corn
-
name
give
General
that
are
worn
y
Courtesy of NationalSwitchgear.com

Ground
Directional
Overcurrent
Relay IBCG
GEH-2032
Fig
.
for the Very Inverse Time Overcurrent Unit and
I
Type
10
»
10
V
a
N
s
Ni
V
\
\
\
\
A
>
\
V
CO
10
*
1
X
>
I
i
9
V
\
8
>
V
V
$
UJ
.
7
\
\
7
„
-
I
f
:
4
%
:
s
QO
\
\
$
.
9
X
UJ
v
*
X
%
\
CO
3
\
V
o
X
o
V
x
r
^
2
o
CN
O
s
aQ
00
s
QO
©
oo
N
E
o
\
K
N
.
.
1
.
0
«
o
\
.
07
2
u
.
.
00
.
09
M
joa
.
02
*
11
.
01
»
—
1
.
9
—
4
S
99
r
9
0
*
+
9
*
MULTIPLES
OF
RELAY
TAP
SETTING
(
IBCG
53
BCG
5
H
)
17
Time
-
Current
Curves
15
Courtesy of NationalSwitchgear.com

Ground
Overcurrent Relay Type
I III I I
7
4
16
Fig.
Time-Current Curves for the Extremely Inverse Time
GEH
-
2032
IBCG
Directional
90
40
30
20
10
7
3
2
CO
1
o
in
o
5
UJ
CO
k
\
\
\
\
UJ
5
\
\
\
W
\
\
Ik
w
\
v
\
\
\
\
10
§
6
in
o
>
5
.
1
JO
Jl
J
7
3
a
>
.
00
(
/
)
2
.
09
O
M
Q
I
-
03
a
>
E
2
H
.
02
.
01
30
40
90
80
70
80
00
g
20
3
4
5
8
7
8
0
10
9
.
0
.
7
.
8
.
9
1
MULTI
PLES
OF
RELAY
TAP
SETTING
I
8
Overcurrent
Unit
Courtesy of NationalSwitchgear.com

Ground
Directional Overcurrent Relay Type IBCG
GEH-2032
NUMBERING OF STUDS
VIEW)
PANEL LOCATION
SEMI-FLUSH SURFACE
DRILLING FOR SEMI-FLUSH
MOUNTING (FRONT VIEW)
OUTLINE
STUD
VIEW SHOWING ASSEMBLY OF
FOR SURFACE MTG.
ON STEEL
PANEL DRILLING FOR SURFACE
MOUNTING RONT VIEW)
Fig. Outline and Panel Drilling Dimensions for Type
17
^
MTG
MTG
-
p
-
5
•
ft
-
I
*
6
8
<
5
Q
1
T
rofcS
gJ
10
ir
\
3
j
|
-
|
8
STUOS
i
*
FOR
SURFACE
MTG
.
CSJ
<
T
&
ro
13
5
7
9
Qgoop
OOOQO
—
2
4
6
8
10
(
FRONT
10
-
32
SCREW
>
(
0
R
STUO
)
n
Ai
\
-
;
10
-
32
«
4
MTG
.
8
SCREW
li
II
.
2
27
^
2
27
CASE
X
_
in
7
.
UJ
32
32
32
32
J O
i
RANEL
Jl
4
DRILL
H
6
HOLES
cc
z
O
/
ft
-
»
m
|
co
<
4
DRILL
4
,
10
HOLES
3
-
:
*
K
!
2
J
?
J
^
<
0
m
<
r
*
0
i
Ul
o
<
-
JC
/
>
CLUJ
CVJ
Ul
—
1
ro
cro
X
<
—
G
1
~
3
o
2
fls
5
b
1
>
=
<
o
5
UJ
iSM
HJ
it
JJJ
z
)
a
:
OQ
HARDWARE
7
I
fOIOJ
cvjto
»
4
T
»
t
PANELS
2
b
-
24
2
I
o
8
PANEL
5
*
(
F
19
IBCGRelays
Courtesy of NationalSwitchgear.com
This manual suits for next models
5
Table of contents
Other GE Relay manuals
Popular Relay manuals by other brands
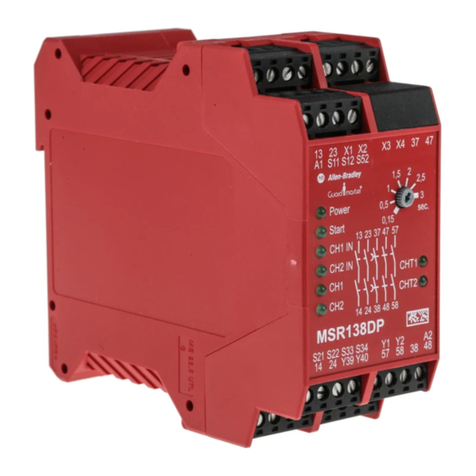
Rockwell Automation
Rockwell Automation Allen-Bradley Minotaur MSR138DP installation instructions

IFM Electronic
IFM Electronic G1502S Original operating instructions

Areva
Areva MiCom P120 Technical guide

GMI
GMI D1044S Instruction & safety manual
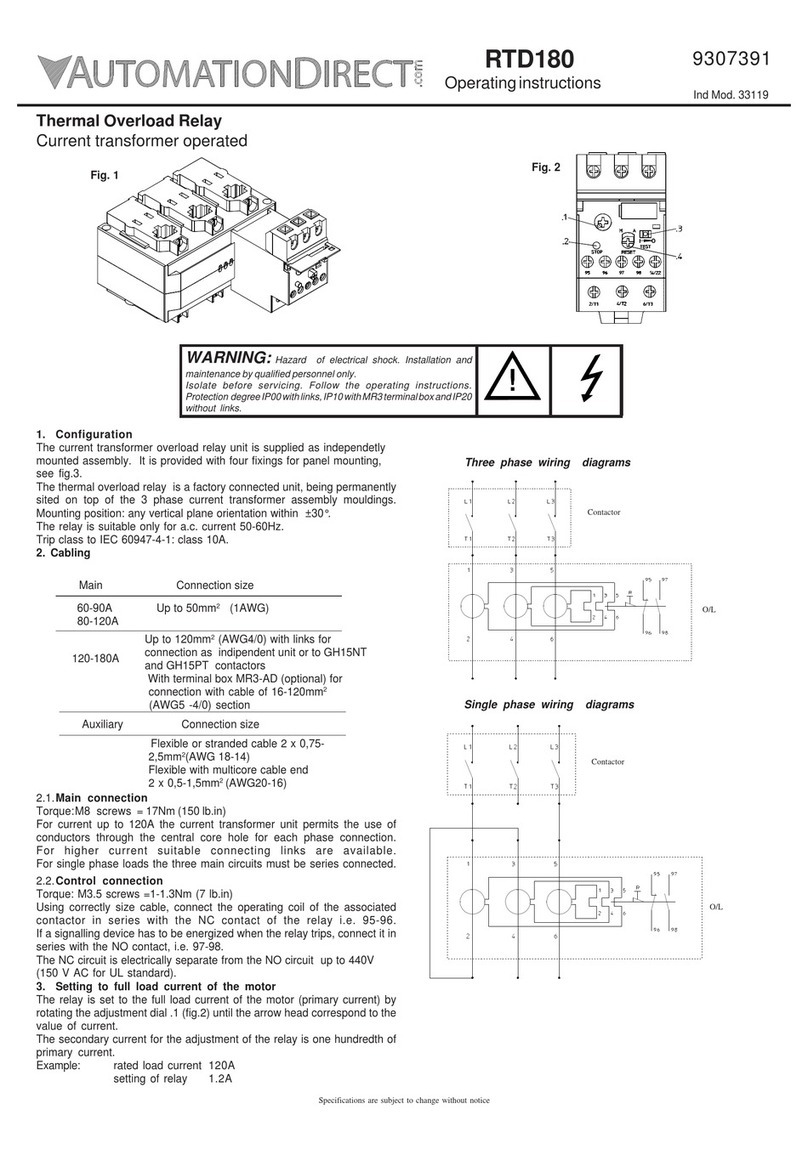
AutomationDirect
AutomationDirect RTD180 operating instructions
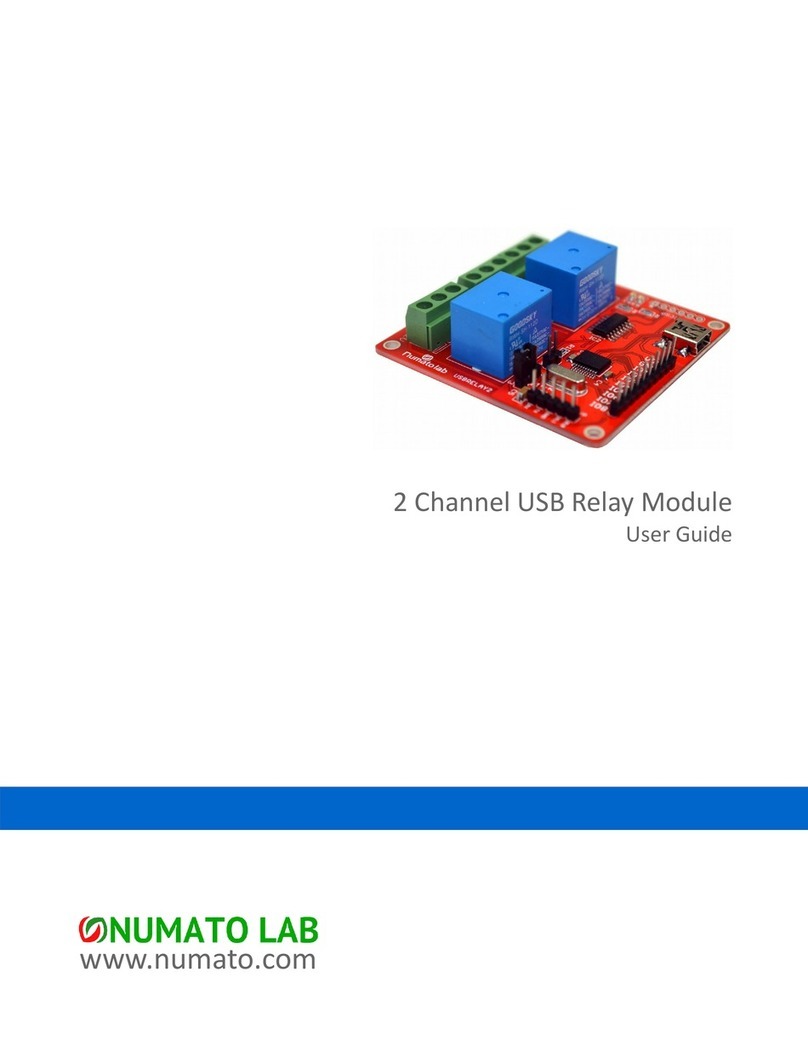
Numato
Numato 2 Channel USB Relay Module user guide