Geosense LS-G6-VW User manual

User Guide V1.9
Vibrating Wire Node
5-Channel
(LS-G6-VW)
1-Channel Aluminum
Version
(LS-G6-VW-1M)
0

Table of contents
Before starting to use Vibrating Wire Data logger 2
Overview of the Loadsensing Vibrating Wire Devices 3
Vibrating Wire Logger Specifications 4
Equipment provided 5
Sensor connection 7
Powering the wireless data logger 8
Loadsensing Device Configuration 10
Safely Closing the Vibrating Wire Logger 19
Node Surge Protection 21
Maintenance and troubleshooting 28
Battery Lifespan 29
Data Storage 30
FAQs 32
CONTACT WORLDSENSING 35
1

Before starting to use Vibrating Wire Data logger
Please read these instructions carefully and ensure that the required conditions specified in this
document are met before using the product. Each of our edge devices includes this information
inside the packaging
General warnings
●
Follow these precautions to avoid a battery explosion or leakage of flammable liquid or gas:
○
Use the correct battery type. Dispose of the batteries according to instructions. Do not dispose of the
batteries by throwing them into a fire or a hot oven, or mechanically crush or cut them.
○
Do not leave the batteries in an extremely high-temperature environment.
○
Do not subject the batteries to extremely low air pressure. It may result in an explosion or leakage of
flammable liquid or gas.
○
Do not short circuit the batteries. This will blow the protection fuse.
●
Batteries and equipment to be connected via the data port must meet IEC 62368-1 ES1 and PS1 requirements.
●
Equipment to be installed in restricted access areas.
Symbol
Description
Caution. Do not proceed until the instructions are clearly understood and all required
conditions are met.
Read the instructions for use carefully before using.
Caution, hot surface.
According to the European Union WEEE Directive 2012/19/EU, this product and its batteries
should not be discarded as unsorted waste.
Please send them to separate collection facilities for recovery and recycling.
It is your responsibility to dispose of your waste equipment and batteries properly. The
correct disposal of your old equipment and batteries will help prevent potential negative
consequences for the environment and human health.
2

Overview of the Loadsensing Vibrating Wire Devices
This user guide explains the basic procedure for configuring and operating
Worldsensing’s Loadsensing LS-G6 vibrating wire nodes (LS-G6-VW, LS-G6-VW-1M). You
can find further technical details in our data sheets.
The Loadsensing Vibrating Wire data logger is a low-power, long-range wireless edge
device. Two models are available: a 5-channel vibrating wire node where up to 5
vibrating wire sensors can be connected at the same time, and a single-channel
vibrating wire node for a single sensor.
We oer metallic versions of the single-channel and multichannel nodes.
The Loadsensing Vibrating Wire data logger can also be used as a standalone logger for
manual monitoring. It can be configured easily and connected with a USB cable and an
Android phone.
Loadsensing Vibrating Wire devices are able to read most of the vibrating wire sensors of
the market. These are used for geotechnical applications in civil works, tunnel
construction, landslides and mining.
3

Vibrating Wire Logger Specifications
LS-G6-VW, LS-G6-VW-1M
VIBRATING WIRE
Measurement method: embedded algorithms increasing immunity to noise.
Excitation wave
+/- 5 V
Measurement range
300 - 7000 Hz
Resolution (-40ºC to +85 ºC)
< 0,01 Hz
*
Accuracy (-40ºC to +85 ºC)
Resolution and accuracy depends on the sweep, as follows:
Vibrating wire
sweep range
Excitation
Frequencies (Hz)
Accuracy -
Error (%)
Resolution (Hz)
Sweep A
450 - 1 125
0.013
0.002
Sweep B
800 - 2 000
0.008
0.002
Sweep C
1 400 - 3 500
0.010
0.004
Sweep D
2 300 - 6 000
0.009
0.007
THERMISTOR
Measurement range:
0 ohm to 4 Mohm
Resolution
1 ohm
Accuracy (20 ºC)
0,05ºC (0,04 % FS)
BAROMETER
Pressure range
300 to 1.100 hPa
Relative accuracy (900 to 1050 hPa at 25ºC)
+/- 0,12 hPa
* Since firmware node version 2.43 resolution and accuracy have been improved according to the
sweep frequency group. It is very important to configure the sensor according to its sweep
frequency group, as this will be aecting both parameters.
4

Equipment provided
The Loadsensing nodes are shipped with the following accessories:
●
Vibrating wire data logger.
●
Antenna.
●
Antenna adapter.
The package does not include:
●
A USB-OTG configuration cable.
●
Batteries.
●
A grounding connector.
●
Mounting support .
The vibrating wire logger comprises:
1. Casing.
2. RP N female connector.
3.
Male RP N connector to RP - SMA
male and aerial with RP - SMA
male.
4. External mini USB B female
connection
5. Gore valve for protection against
condensation.
6. A grounding screw for metallic
nodes.
7.
Cable gland.
Check the labels in the image on the right to determine the position of each component.
5

Data Logger Mounting
All vibrating wire data loggers can be deployed as follows, depending on the application
and the conditions of the site:
●
On a wall, using a metallic (LS-MEC-MP-001) or polycarbonate (LS-ACC-MP-P)
mounting support.
●
On a 35-mm or 50-mm mounting pole, using an aluminum mounting plate
(LS-ACC-POLE35-2/LS-ACC-POLE50-2). This includes nuts and U-bolts for
a
pole diameter of less than 35 mm and 50 mm.
●
Inside a manhole, with a plastic or metallic cover. No special accessories are
available for this type of mounting. Even though the data loggers are IP67
certified, if they are closed following the instructions in the chapter on Safely
closing the vibrating wire data logger from this User Guide, we strongly
recommend reading the Data Logger Installation in Manholes
guide.
You can find drawings for our supports in the Accessories List in our knowledge base.
6

Sensor connection
Most vibrating wire sensors can be connected to the Loadsensing vibrating wire data
loggers. Further information can be found in the vibrating logger specification chapter.
The data logger has a cable gland for each channel, to allow you to adjust dierent
sensor cable diameters. Each terminal block has a group of five connectors and each
group has:
●
2 vibrating wire connectors (with no polarity) VW
+/ -
●
2 thermistor connectors (with no polarity)
TH +/-
●
1 shield terminal
SHLD
The terminal blocks accept wires prepared by stripping a short length of insulation from
the end.
Wires and their pinouts must be checked with the sensor data sheet from the
manufacturer. As a workaround, pairs can be checked with a multimeter.
After you connect each terminal block, we recommend you take some sensor readings to
make sure the connections have been made correctly. Also, taking several readings will
help you check that the sensor is correctly wired to the logger and the sensor wires.
An alternative can be to compare the sensor reading at installation with a portable
readout unit.
7

Powering the wireless data logger
The Loadsensing vibrating wire nodes are shipped closed, without batteries. To power it
up, follow these steps:
1. Open the vibrating wire node using a 2.5 mm Allen key.
2. A small RTC battery was shipped inside the ½ AA size battery holder in our
multichannel data loggers in order to keep time regar dl ess of whether C-type
batteries are also inserted in the data logger.
Since serial 52594 and above, the ½ AA size battery holder and its battery have
been removed from the battery board to simplify the product installation and
maintenance and in line with our thrust to provide more environmentally
sustainable products by reducing battery waste.
Please take note that this update shall have no impact whatsoever on the
performance of the edge device, as since Gateway firmware version 1.12.1 the
Gateway is able to check if the node is on time. If it's not, a time synchronization
message is sent.
3. The data logger always uses UTC time, although data can be visualized in local
time in our gateway.
8

4. Insert C-type batteries in the battery holders. The single channel node takes only
one battery and the multichannel node has up to four (more batteries will give the
logger a longer life for a given configuration). See our LS G6 data logger
recommended batteries guide for further information.
Please note our devices have reverse battery protection but it is not safe to keep
batteries reversed in the node for a long time.
Warning: There is a risk of explosion if you use the wrong batteries. Dispose of batteries according
to instructions and refer to the General Warnings from bellow.
5. As well as batteries, the logger can be powered with external power. There is a
power mode switch on the node. Turn it to whichever power mode you are using.
Please take a look at the External power options document before using this
option.
General Warnings
● We advise during usage of the batteries to observe the following precautions:
○ Risk of explosion if the battery is replaced with an incorrect type.
○ Disposal of the battery into fire or a hot oven, or mechanically crushing or
cutting of a battery, can result in an explosion.
○ Leaving the battery in an extremely high temperature surrounding
environment can result in an explosion or the leakage of flammable liquid or
gas.
○ The battery subjected to extremely low air pressure that may result in an
explosion or the leakage of flammable liquid or gas.
○ Short-circuiting the battery will result in blowing the protection fuse.
● Batteries and equipment to be connected via the data port must meet the
requirements of ES1 and PS1 according to the IEC 62368-1.
● Equipment to be installed in restricted access areas.
9

Device Configuration
We strongly recommend configuring the device on location so you can conduct
an on-site radio coverage test at the same time.
Device configuration has to be carried out using the Worldsensing Android app (WS App),
which i s compatible with USB On-The-Go (OTG) Android devices. Please refer to the
Worldsensing app User Guide for more details. To make sure the app works properly, we
recommend purchasing one of the mobile phone models i n stock from Worldsensing.
Please contact the technical support team for more information.
WS App starts up once the Android device i s connected to the Loadsensing node using
an USB-OTG cable. It does not need to be started up manually.
The whole configuration process takes no more than five minutes. From then on, the
Loadsensing node will start taking readings and sending data to the gateway.
Please take note of the following credentials i n the Gateway Information Sheet. These
will be necessary to perform the radio coverage test:
Gateway Information Sheet
Mobile app field
Default network ID
Network ID
Default network key
Password
Default network access password
Server password
The process for configuring the vibrating wire node is the same as the other nodes and it
is detailed in the Worldsensing App user guide.
10

There are some configurations and functionalities that are particular for the vibrating
wire node, such as configuring the sweep frequency from the sensor and setting a
specific magnitude threshold to detect if the sensor has been disconnected.
User will need to add the channels that want to read, with a suitable sweep frequency
group from the sensor. There are 4 frequency groups available on the app that cover
most of the vibrating wire sensors on the market.
Frequency range
Sweep A
450-1.125 Hz
Sweep B
800-2.000 Hz
Sweep C
1.400-3.500 Hz
Sweep D
2.300-6.000 Hz
Table 1. Sweep frequencies ranges
Fig.1 Node sweep frequency configuration.
11

A sweep custom frequency is also available on the app, where a custom start and end
frequency in Hz can be added and also a custom time (in ms) for reading the sensor.
Fig.2 Sweep custom configuration.
We recommend checking this information with the datasheet from the sensor
manufacturer.
12

Algorithm refinement
From Vibrating wire Data logger firmware version 2.43, the algorithm we use is able to improve
resolution and accuracy using proper sweep configurations.
Excitation Freqs.
Accuracy - Error %
Resolution Hz
Sweep A
450-1125
0.013
0.002
Sweep B
800-2000
0.008
0.002
Sweep C
1400-3500
0.010
0.004
Sweep D
2300-6000
0.009
0.007
If you configure a custom sweep frequency within a wide range, the resolution will correspond
to the group with the lower specs. For this reason, we recommend your sweep frequency fits
the sensor range and not much more.
The chart below shows spot-weldable strain gauge readings from our previous firmware
compared to version 2.43. As you can see, the resolution with the new firmware is
significantly better and allows you to detect smaller changes.
13

Firmware readings comparison
A comparison of strain gauge readings using the previous firmware and version 2.43
Version 2.43 also includes an advanced configuration option and users can use it to
configure a magnitude threshold (see ‘Sensor detection functionality’ overleaf for more
details) to avoid recording noise or induced frequencies on the cable. If the measured
magnitude is lower than the configured threshold (for example if the cable gets cut), you
will get a ‘sensor not detected’ error message. See the next page for more details.
14

Fig.3 Magnitude threshold configuration.
15

Sensor Detection Functionality
Vibrating wire sensors may sometimes get disconnected due to a cut cable or other issues.
This can lead to data analysis challenges when you are analyzing data remotely, as it could be
interpreted as a node or a sensor failure, among other things.
To reduce noise or induced frequencies, we’ve implemented a configurable threshold. If the
magnitude of the reading is above that threshold, the reading is taken as valid. If the
magnitude of the reading is at or below the threshold, the reading is discarded and an error
code is sent.
When configuring the threshold note that:
●
Only one threshold can be configured for all the channels.
●
Dierent sensors give dierent magnitude responses.
●
The excitation sweep influences the magnitude returned, so it is important to choose
a
sweep frequency group instead configuring a custom sweep frequency within a
wider
frequency range.
●
The default threshold is set at a safe distance from noise, at 0.075 Hz, but there are
sensors that work closer to the noise level, at 0.02 and 0.01 Hz.
●
Any value beneath the threshold will trigger a ‘missing sensor’ warning.
You should consider changing the threshold when a sensor is present but reported as not
detected, or when the magnitude of noise is higher than the threshold.
When changing this setting, remember that:
●
The recommended threshold value is 0.02.
●
Most sensors have magnitude values above 0.1.
●
Some sensors can go as low as 0.03.
16

● The noise level magnitude is usually under 0.01.
When dealing with false errors, do the following in order:
1. Make sure the node threshold is the default one.
2. Make sure the sweep you have configured covers the range of the sensor.
3. Try a custom sweep that fits the range of the sensor better.
4. Lower the threshold to fit the magnitude given by the sensor.
5. In extreme cases, set the threshold to 0. This will disable sensor detection.
Once the configuration is finished the app will show the option of taking a sample. Taking a
sample will show the parameters measured and allow you to check the consistency of the
readings.
Figure 4: WS app screenshot taking a sample.
17

Barometric Measurements
As the data logger includes a barometer. It is important to avoid placing the data logger inside
any type of container. This would aect the readings the barometer makes through the gore
valve.
If the vibrating wire sensor requires barometric pressure compensation (such as for
piezometers installed in locations that may be aected by changes in barometric pressure), the
current pressure readings from the barometer are usually used directly. Note that the
transformation of the data (compensated by the barometric pressure) is done on the gateway
in the Engineering Units drop-down menu from the particular node.
If you want to use sea level atmospheric pressure (as commonly used in meteorology), you will
need to correct the barometric readings using this formula:
𝑝
0 = 𝑝
( 1 − 𝑎𝑙𝑡𝑖𝑡𝑢𝑑𝑒
44330 ) 5 . 255
Where:
p
0 = pressure at sea level in mbars.
p = current pressure reading.
altitude = altitude in meters above sea level.
18

Safely Closing the Vibrating Wire Logger
This is important to ensure water tightness and the durability of the node. Close the
cover by cross-screwing the 2.5 Nm/2Nm torque as indicated. Please see the
Watertightness document for detailed information.
The Loadsensing vibrating wire data loggers have undergone water tightness testing by
an external laboratory and are rated at IPX7 (one meter for 30 minutes).
To guarantee water tightness, make sure to do the following:
●
Properly adjust the cable glands. Please note that the cable glands are closed
and
held with a 19 mm open spanner (e.g. a Bahco 19 mm single-ended open spanner,
RS Amidata code 717-8992).
Figures 5, 6 Pictures show how to properly close and hold cable glands with the open spanner.
●
Seal the unused cable glands with the piece of rubber rod provided in each box.
●
Lock the box by tightening screws crosswise on the lid after connecting
the
sensor. Adjust the screws using a torque wrench. If not, the base faces and cover
may not be parallel, screwing may become more dicult and the screw threads
or
the Helicoil inserts may be damaged. Moreover, the O-ring (seal) may not
be
19
This manual suits for next models
1
Table of contents
Other Geosense Measuring Instrument manuals
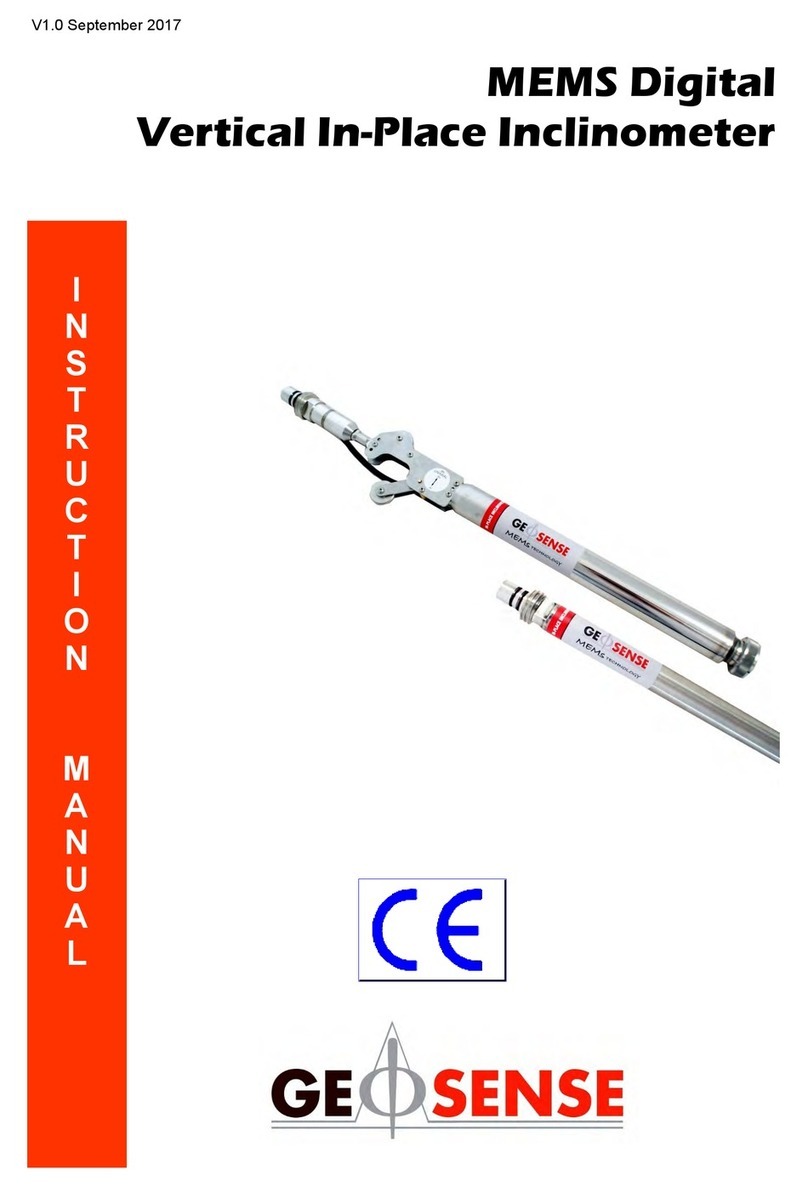
Geosense
Geosense IPI-V-1 User manual
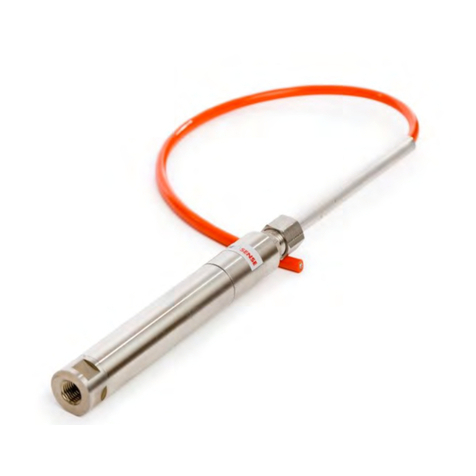
Geosense
Geosense VWPHT-3600 Series User manual
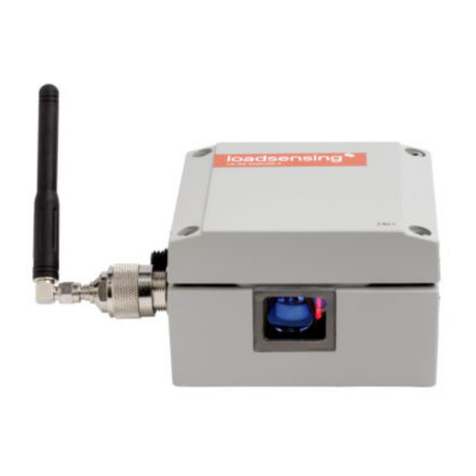
Geosense
Geosense WI-SOS 480 User manual
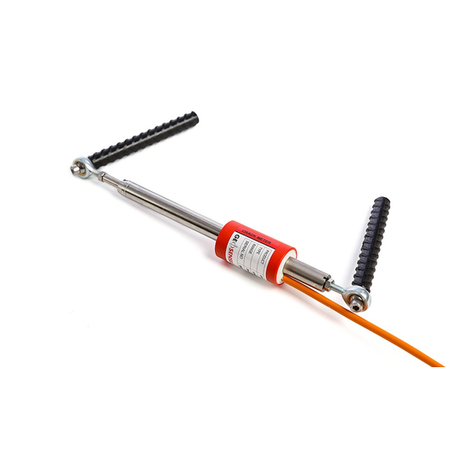
Geosense
Geosense VWCM-4000 User manual
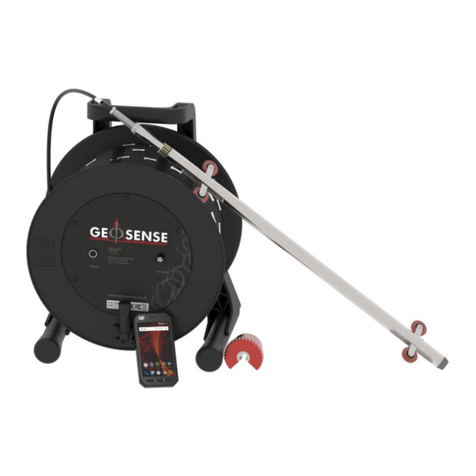
Geosense
Geosense MEMS DPI I User manual
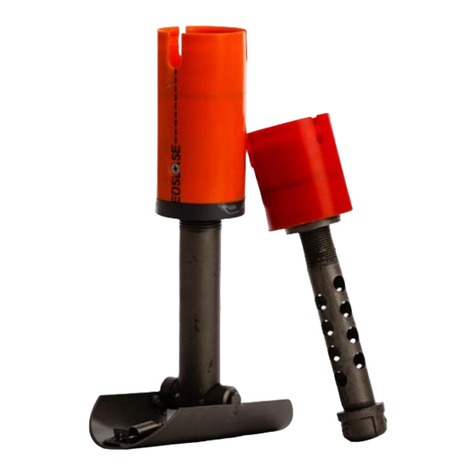
Geosense
Geosense Quick Joint User manual
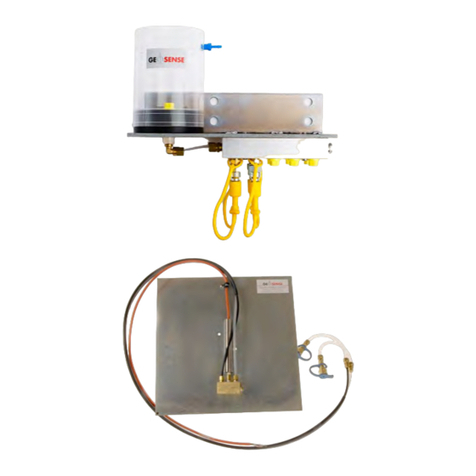
Geosense
Geosense VWLSS-200 User manual
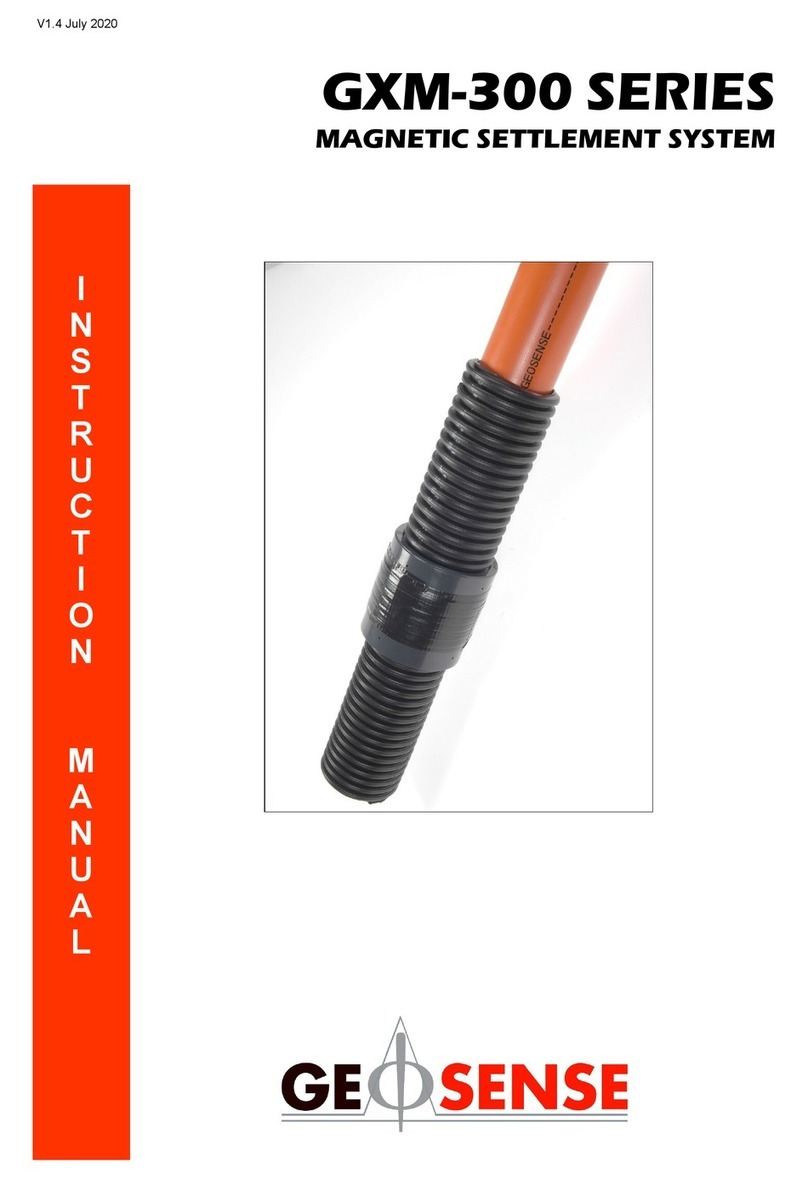
Geosense
Geosense GXM-300 Series User manual
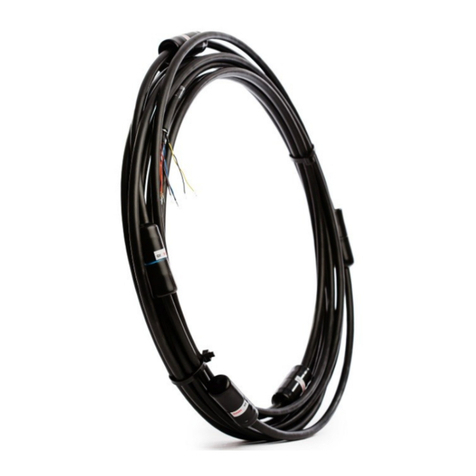
Geosense
Geosense TP-1 User manual