GKD 3RCI+ User manual

M3000010 v1.1
3RCI+ Quick Start Guide
Covering both Standard and SpaceGuard Systems

2
GKD Technik LtdM3000010
Screen Layout
1Foreman Key
switch
Machine Controllers Switch (Foreman’s key switch) allows or denies access to the
user sengs and service menus. Used when there are slew and height limits in
use to avoid accidental changes by the operator.
2
3
4
5
Display Touchscreen colour display which provides user informaon and control of the
system.
Overload
warning LED RED LED illuminates to show when the machine is in an overload condion.
Rated Capacity
warning LED
AMBER LED illuminates to show when the machine is approaching the rated ca-
pacity and overload condion.
System power
Comms OK GREEN LED ashes connuously to indicate power and system operaon.
6Light Sensor Automacally dims or brightens the screen, depending on lighng condions.
1
2
3
4
5
6

3
GKD Technik LtdM3000010
Screen Layout connued...
1
2
3
4
5
6
ALO Symbol
3RCI+ SpaceGuard Systems that are cered to work Adjacent Line Open will
show the symbol “ALO √”, 3RCI+ systems that are not cered to work Adjacent
Line Open, or approved systems without operaonal slew limits or virtual walls,
will show “ALO X”.
In-gauge Shows green when the machine is within gauge to travel. Will also show red
when a slew limit is exceeded or a height limit is exceeded.
Dig Mode If the system is in dig mode this icon shows green and the moon cuts and
alarms on overload are disabled, the blue beacon is not illuminated.
Height Height of li point from ground level (road mode) or rail head (rail mode).
Acve Li
Point
The current acve li point is shown here. Possible opons are BP (Bucket Pin),
ALP (Auxiliary Li Point), QH (Quick hitch), or TLJ (demountable Tele-jib). If
nothing shown here then only one liing point is enable (Bucket Pin).
Radius Radius of current li point from the slew centre of the machine.
1
2
3
4
5
6
78910 11 12 13
14
15
16
17
18
Load Displays the current load on hook. This will include any aachments and the
quick hitch.
7
19

4
GKD Technik LtdM3000010
Logging
This icon shows the status of the on-board data logging system. There are four
states for the icon. 1) Not shown - logging is disabled. 2) Logging icon - no events
recorded but Logging On. 3) Exclamaon mark - Logging is on and an event has
been recorded. 4) Logging symbol with red cross - Log is inoperave or card full.
Screen Layout connued...
8
9
10
11
12
13
14
15
16
18
Status Bar This area shows machine informaon, error messages and current date and me.
Rated Capacity
Shows the maximum permied load for the current height an radius.
Note: when an * appears against this number, it will indicate that either the
machine is in hydraulic limit or the rang displayed is the maximum based on the
hydraulic limitaons of the machine.
Speed Shows the current speed of the machine in MPH.
Duty Indicator This symbol will indicate whether the RCI is switched to Rail dues, Road dues
or LUL (London Underground) dues.
Slew Shows the current slew angle in degrees. 0° is typically over the oscillang axle.
Menu buon
Allows access to user and service funcons.
Note: if the machine controllers key switch is o then the system will not allow
access to service menus or limit funcons.
RCI Status Bar
This bar lls from boom to top and provides a visual reference of the
relaonship between the applied load and the rated capacity. A warning will
occur between 92.5% and 97.5% of the rated capacity. This warning is an AMBER
LED and an audible alarm on the cab. If the applied load should exceed 104% of
the rated capacity then the RED LED is lit and a connuous external siren is
sounded. The machine will then be inhibited to prevent further unsafe
movements.
Axle Lock Icon
Shows the current state of the axle lock. A locked padlock indicates that the axle
locked, an unlocked padlock indicates that the axles are unlocked, and an
unlocked padlock with a cross through it indicates that the axles cannot be
unlocked as it is unsafe to do so as it would put the machine into an overload
condion.
Cant /
Gradient
Shows the current cant and gradient of the machine (rail dues only). Cant will
show as posive (right hand rail high at 0° of slew) or negave (right hand rail low
at 0° of slew), and gradient will show as posive (facing up gradient) or negave
(facing down gradient).
Movement These arrows indicate the safe direcon each piece of equipment can be moved.
GREEN indicates movement is safe. RED indicates movement is unsafe.
19
Rail Gauge Indicates the current rail gauge on use. This is set during the system installaon
by the converter.
17

5
GKD Technik LtdM3000010
Operator Display Guide connued...
Daily Checks
Before starng work, visually inspect the RCI sensors and wiring for damage, ensure that the RCI system is
in good working order and that the values for height, radius, slew posion and load shown on the RCI are
valid. Please refer to the User manual for daily check requirements.
System Start - Up
The 3RCI+ system should automacally start up when the ignion is turned on. Inially a green LED on the
front panel will blink on and o to indicate that the system is boong up, and then the screen will power
up. Once started up, the internal buzzer will sound connuously unl the operator acknowledges the
system by pressing the “OK” buon. The operator will then need to input his 8 digit PTS number. Where
the operator has a 6 digit Sennel card number, it is suggested that two zeros are typed in rst, followed
by the 6 digit Sennel number. The system will then go to the working screen shown on page 5.
Foreman Key
The RCI display incorporates a foreman key switch to the right of the display. When this key switch is in
the “Locked” posion, most of the buons behind the [MENU] buon will be greyed out and unavailable.
To make them available, turn the foreman key switch to the “unlocked” posion.
Li Point Selecon
Where mulple li points are available, the li point being used should be selected from the opons
programmed into the RCI. The acve li point is shown on the main screen under the Height value (see
item 5 on page 5). To change the acve li point, press the [MENU] buon, and cycle through the
available calibrated li points using the boom le buon.
Possible opons are:
BP (Bucket Pin)
ALP1 (Auxiliary Li Point)
ALP2 (secondary Auxiliary Liing Point)
QH (Quick Hitch)
TLJB (demountable tele jib)
Only those opons enabled within the soware will be available. Selecng the incorrect li point will not
compromise the safety of the system, but height, radius and load values may be inaccurate.

6
GKD Technik LtdM3000010
Operator Display Guide connued...
Liing a load
As a load is lied, the Load on Hook value as displayed on the screen (item 7 on page 5) will show the
weight of the load suspended from the hook. This load is compared to the Rated Capacity (item 9 on
page 5), the calculated value that the machine is allowed to li before an “overload” event occurs, and
the status bar (item 14 on page 5) will ll proporonal to the % of the Rated Capacity currently being
used. As the machine changes posion in terms of height, radius, cant, gradient or slew angle, the Rated
Capacity is connuously recalculated. Axle lock status and Road, Rail or LUL duty changes will also aect
the Rated Capacity value.
Overload
As the RCI detects that the Load on Hook value is approaching the Rated Capacity, the AMBER LED on the
side of the RCI display will light up and the internal buzzer will sound. As the Load on Hook value reaches
the full Rated Capacity value, the RCI will register an Overload state, which is signaled by the RED LED
being lit and the external pping alarm sounding. At the same me, any hydraulic service which will take
the machine further into overload will be cut, and the RCI screen will change the colour of the arrows
represenng available hydraulic services from green to red for any service that has been moon cut.
Any hydraulic service that will result in the load moving to a safer posion will sll be allowed, and the
arrows on screen represenng these services will stay green to signify that the services are sll available.
Axle Lock
The machine’s Rated Capacity will generally be lower with the oscillang axle unlocked than when it is
locked. When working with a locked axle (stac li) and a li and carry duty is required, the axle must be
unlocked. The RCI will monitor the Rated Capacity for both locked and unlocked dues, and if unlocking
the axle will put the machine into overload, the axle unlock signal will be interrupted by the RCI and the
axle will not be allowed to unlock. The axle lock symbol on screen will change to an unlocked padlock
with a red X through it, and the axle will remain locked unl the load is moved to a posion where the RCI
will not be in overload with the axle unlocked. At that point, the axle unlock interrupt will be released and
the axle will be allowed to unlock.
Travel Inhibit
The RCI will inhibit travel under the following condions:
When the machine is in an overload state - in rail mode only.
When the axle is locked - in rail mode only.
When a height limit has been reached.
When the air pressure is detected as being low (air brakes) - in rail mode only.

7
GKD Technik LtdM3000010
Operator Display Guide connued...
Dig Mode
When the machine is not being used as a crane, it may be permied for the system to operate in DIG
mode. In DIG mode all overload warnings and moon cut on overload is turned OFF, and no protecon
against overload will be present. The blue light on the roof will be turned o, and where red / white
indicator lamps are present the white lamp will switch OFF and the red lamp will switch ON. The data log
will record the use of DIG mode. In order to use DIG mode, the foreman key switch must be in the
unlocked posion.
To engage DIG mode, press the [MENU] buon, and press the [DIG IS OFF] buon. DIG mode will then be
turned on. The main screen will indicate that DIG mode is engaged by turning the DIG mode indicator to
green (item 3 on page 5), a yellow circle with an alarm symbol with a cross will be shown next to the
logging symbol top right of the screen and LOGGING DIG MODE will ash in the status bar (item 8 on
page 5).
To turn DIG mode o and return to LIFT mode, press the [MENU] buon and then press the [DIG RAIL
MODE] buon at the top right of the screen.
Backward Stability
The RCI system will monitor the state of the machine to prevent the machine falling over backwards
when working on a cant. With a reduced load on the hook and when working on a cant of more than
50mm with the turret facing up the cant, the RCI may restrict the movement of the stub boom back.
When the maximum boom angle is achieved in a potenally backwardly unstable condion the stub
boom li funcon will be moon cut and a “backward stability” message will be shown. If the boom is far
enough back to trigger a backwardly unstable condion and the machine is slewed towards a potenally
backwardly unstable condion, the “backward stability” message will be shown and the slew funcon
will be cut to prevent the machine reaching a backwardly unstable posion. To rotate the turret further,
lower the stub boom unl the message disappears and slew funcon is restored.
Height Limits
In order to set a height limit, the foreman key switch must be in the unlocked posion.
To set a height limit, press the [MENU] buon and then press the [HEIGHT LIMIT is o] buon.
The system will ask if you wish to Enter a height limit. To enter a height limit (in meters) press [YES].
To capture a height limit from the excavator current boom posion, press [NO] and you will be prompted
to move the excavator to the desired height limit and press [YES]. A height limit will be set that
corresponds with the highest point of the excavator at the moment it was set. Once set, the RCI will
monitor all booms against the set height limit, and will moon cut any hydraulic service that will cause a
boom to move through a set height limit. Services that cause machine movement away from the height
limit will always be allowed.
To turn o a set height limit press [MENU] and the [HEIGHT LIMIT IS ON].
The height limit will be turned o.

8
GKD Technik LtdM3000010
Operator Display Guide connued...
Height Limit connued…
When a height limit is set, you will see the following on the operator main screen.
Angular Slew Limits
In order to set a slew limit, the foreman key switch must be in the unlocked posion.
To set angular slew limits, press the [MENU] buon and then press the [Slew Angle is o] buon.
The system will ask if you wish to enter slew limits. To enter slew limits (in degrees) press [YES].
To capture slew limits using the excavator turret posion, press [NO] and you will be prompted to move
the excavator to the desired clockwise limit posion and press [YES], and then to the desired counter
clockwise posion and press [YES] again. Slew limits will be set as captured from the turret posion
relave to the undercarriage. Once set, the RCI will monitor turret posion against the set limits, and will
moon cut the appropriate hydraulic slew services the limit is reached. Slewing away from the set slew
limit will always be allowed.
To turn o a set slew limit press [MENU] and then [SLEW ANGLE IS ON]. The slew limits will be turned
o.
When a slew limit is set, you will see the following on the operator main screen.
Current highest point
of the machine.
Current set
height limit.
Current counter
clockwise limit.
Current clockwise
limit.

9
GKD Technik LtdM3000010
Virtual Walls
In order to set a slew virtual wall, the foreman key switch must be in the unlocked posion.
To set a virtual wall, press the [MENU] buon and then [VIRTUAL WALLS OFF]. To set the LEFT wall
distance, press [LEFT]. To enter the value for the le wall, in meters from the machine centre, select
[YES]. Alternavely, to capture the wall distance from the bucket pin posion press [NO], move slew le
of 0° of slew and posion the bucket pin at the desired le limit and press [YES]. The right wall is set in
the same way, but slewed to the right of 0° of slew to capture the wall posion. Select either LEFT, RIGHT
or BOTH to acvate the virtual wall/s as required.
To turn the virtual walls o, press the [MENU] buon and then [VIRTUAL WALLS ON], select CANCEL.
Virtual walls will then be turned OFF.
When a slew limit is set, you will see the following on the operator main screen.
Operator Display Guide connued...
Current le
Virtual wall distance
Current right
Virtual wall distance
Distance from bucket
pin to virtual wall
Tandem Li Duty
In order to use Tandem Li, the foreman key switch must be in the unlocked posion.
When using the machine as one of a pair of machines liing a load together, the Tandem Li mode must
be engaged. The eect of the Tandem Li mode is to reduce the li capacity of the machine to provide an
addional safety margin before an overturn occurs, as dictated by Network Rail Tandem Li guidelines.
To engage Tandem Li mode, press [MENU] and then [Tandem is o]. Tandem Li mode will be engaged,
the machine’s li capacity will be recalculated in line with Tandem Li regulaons, and on machines
cered to RIS1530 rev4 and above the blue RCI indicator lamp on the cab will blink on and o at 2
second intervals.
To turn Tandem Li mode OFF press [MENU] and then [Tandem is ON]. Tandem Li mode will be turned
o and the machine li capacity will return to standard li dues.

10
GKD Technik LtdM3000010
SpaceGuard and Safety Mismatch
If a SpaceGuard equipped RCI system detects a mismatch between the primary angle / slew sensors and
the Safety angle / slew sensors, a Safety Mismatch warning is displayed. The mismatch is oen related to
the slew count sensors, and slewing the machine back over the reset sensor at 0° of slew may well clear
the fault. If not, inspect the angle sensors for possible mechanical damage. If a fault sll exists,
an engineer visit may be required.
Troubleshoong
The 3RCI+ system connuously monitors the system components for correct operaon. In the event that
a problem is detected with the system, the li capacity is reduced to 700kg and an error message is
displayed next to the [MENU] buon indicang the nature of the error detected. In the event that more
than one error is present, only the top line error is indicated. Pressing the [MENU] buon and selecng
the [MORE] tab will bring up a list of all detected errors on the system.
Below is a link to the GKD Knowledge base where you can nd denions of all the error codes for the
3RCI+ System including SpaceGuard.
helpdesk.gkdtechnik.com/kb
GKD Contact Details
Contact GKD Technologies on:
+44 (0) 1202 861961
+44 (0) 1202 971971
service@gkdtec.com
www.gkdtec.com
GKD Technologies reserve the right to change these instrucons in line
with the policy of connuous improvement.
Operator Display Guide connued...
Other manuals for 3RCI+
1
This manual suits for next models
1
Table of contents
Popular Control Panel manuals by other brands

Axon
Axon Cerebrum CCP-4200B Operation manual
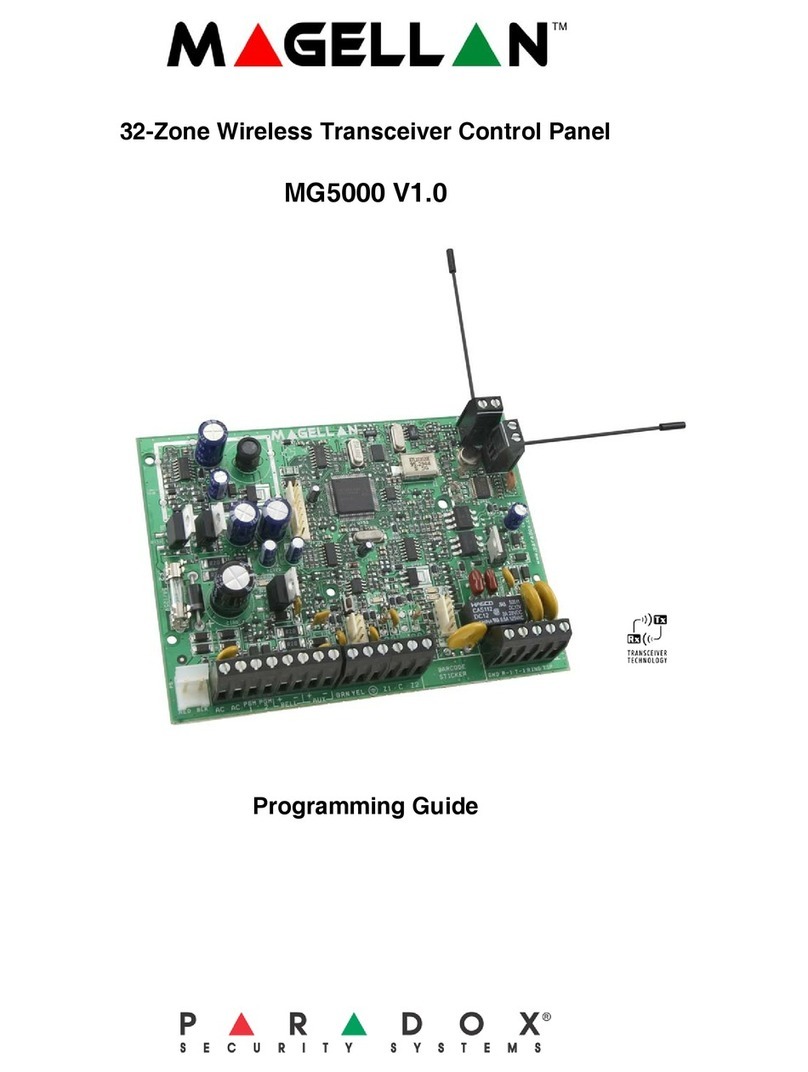
Magellan
Magellan MG5000 Programming guide
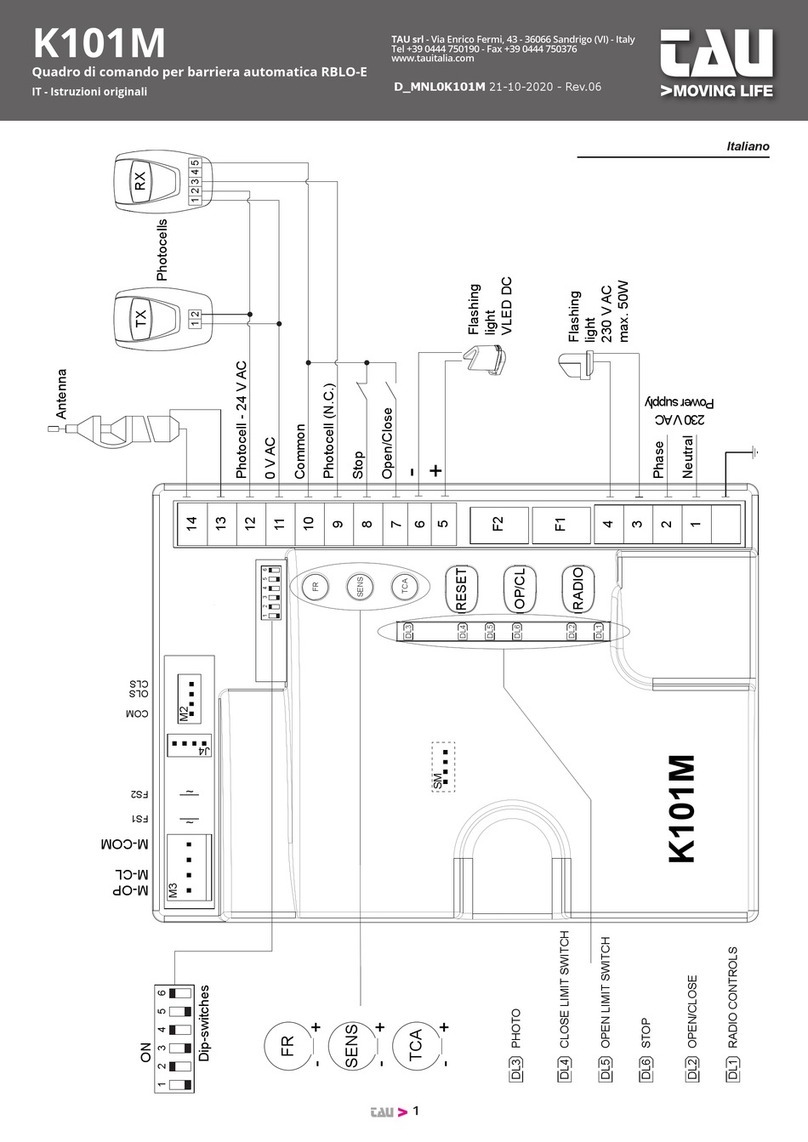
tau
tau K101M TRANSLATION OF ORIGINAL INSTRUCTIONS
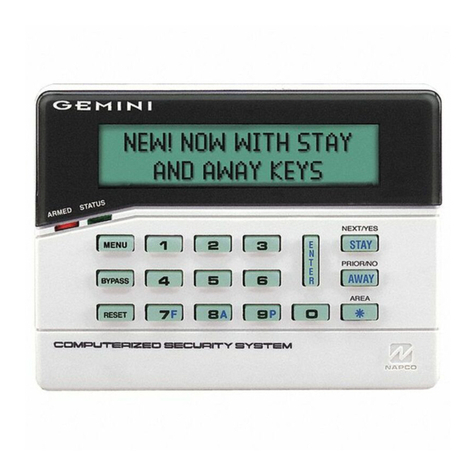
NAPCO
NAPCO Gemini GEM-P816 Programming instructions
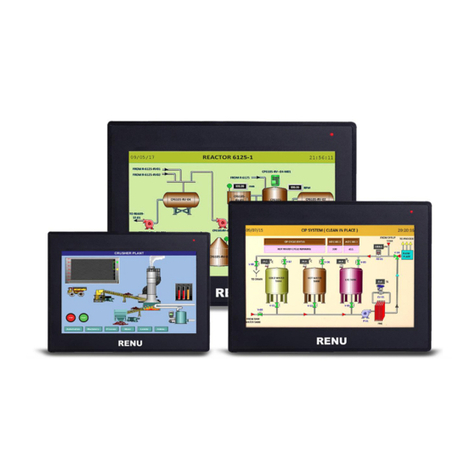
Renu Electronics
Renu Electronics FlexiPanels FP4 Series user manual
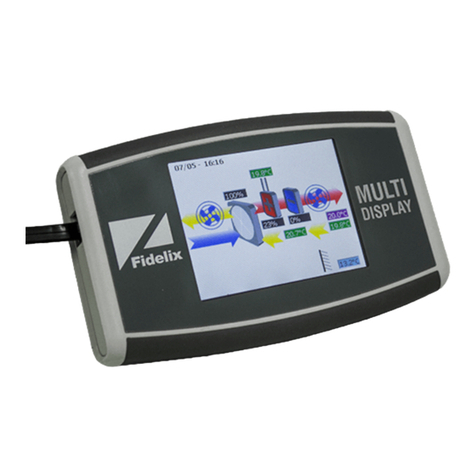
Fidelix
Fidelix multiDISPLAY FX-RP Series Programming manual
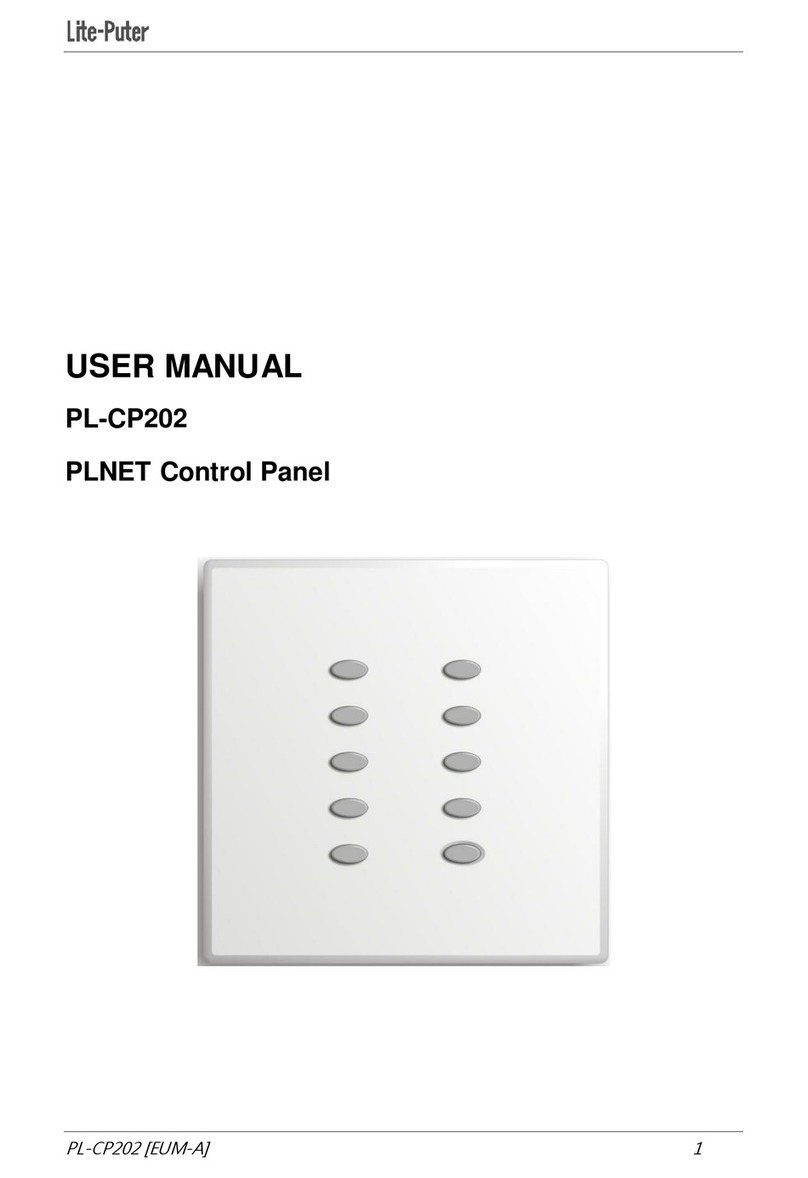
Lite-Puter
Lite-Puter PL-CP202 user manual
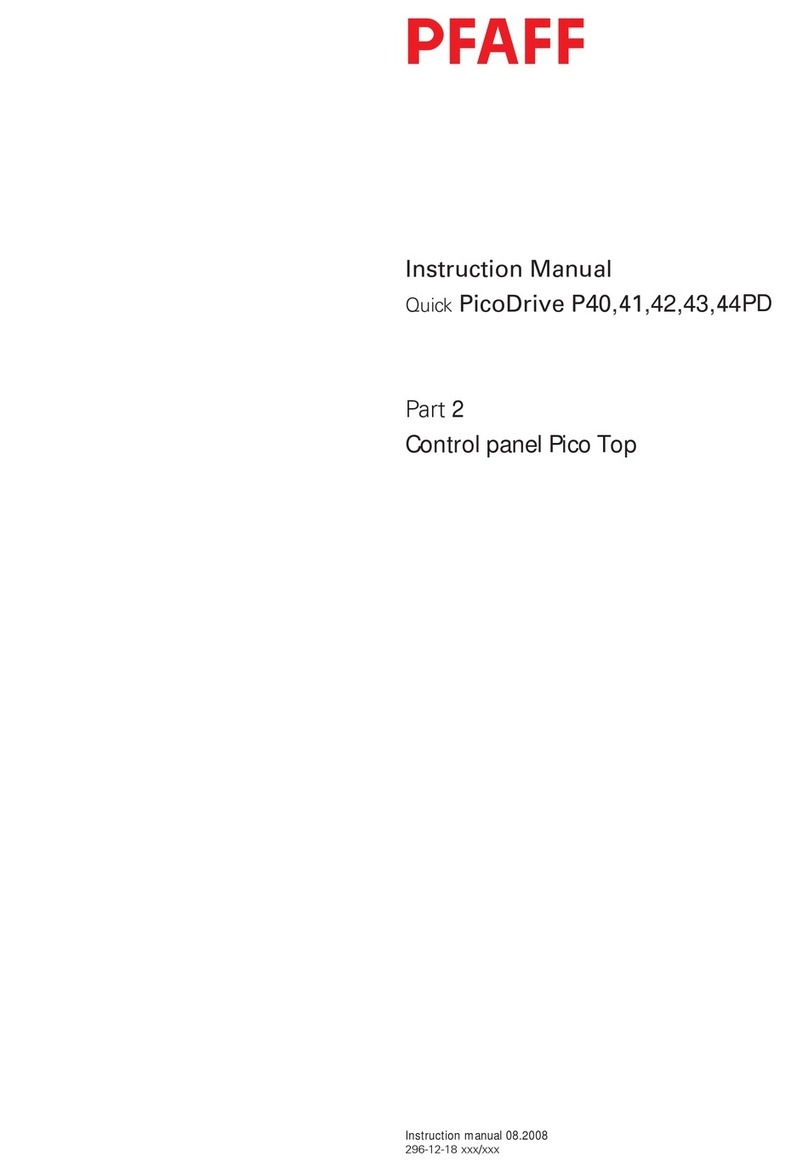
Pfaff
Pfaff PicoDrive P40PD instruction manual
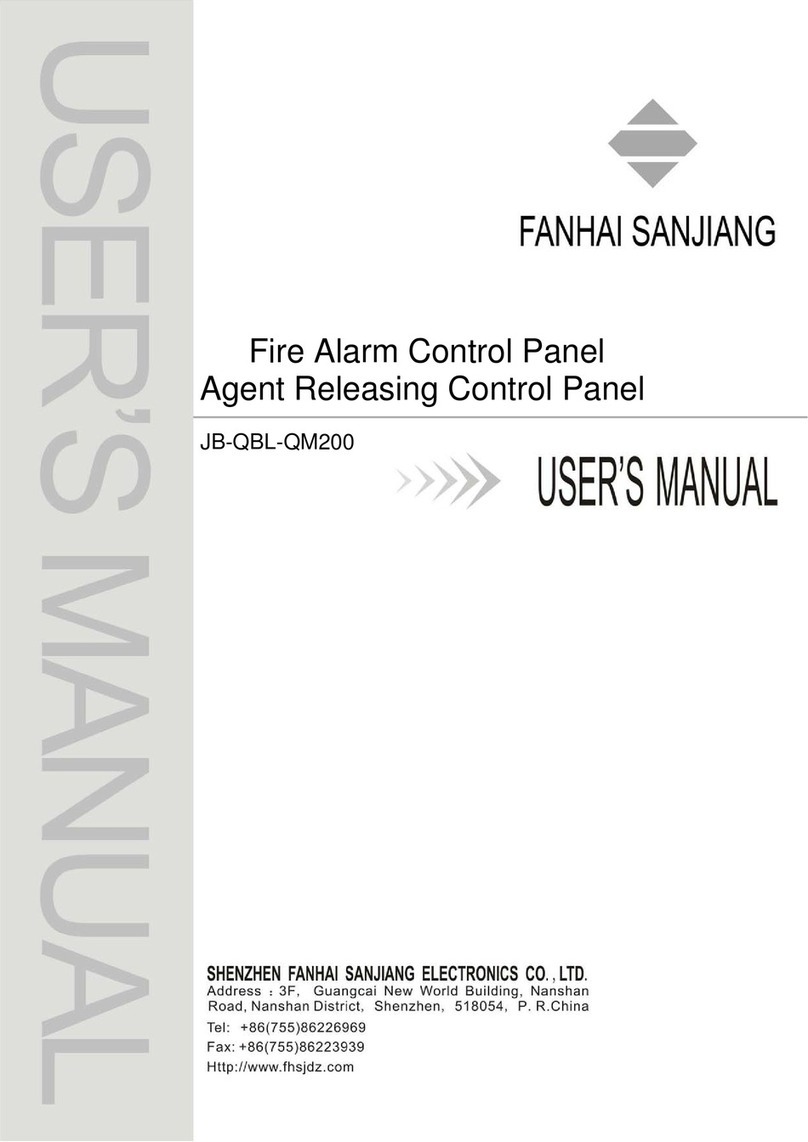
SHENZHEN FANHAI SANJIANG ELECTRONICS
SHENZHEN FANHAI SANJIANG ELECTRONICS JB-QBL-QM200 user manual
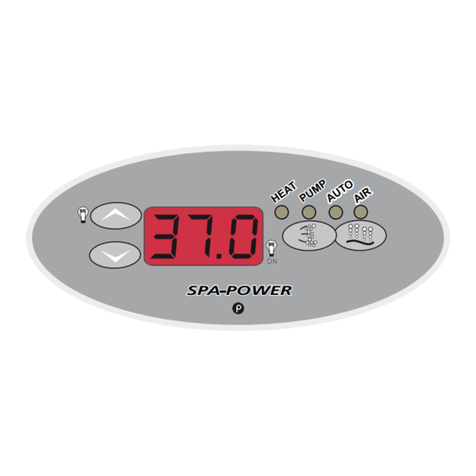
BWT
BWT SP601 operating instructions

Honeywell
Honeywell Notifier NFS-320 operating instructions
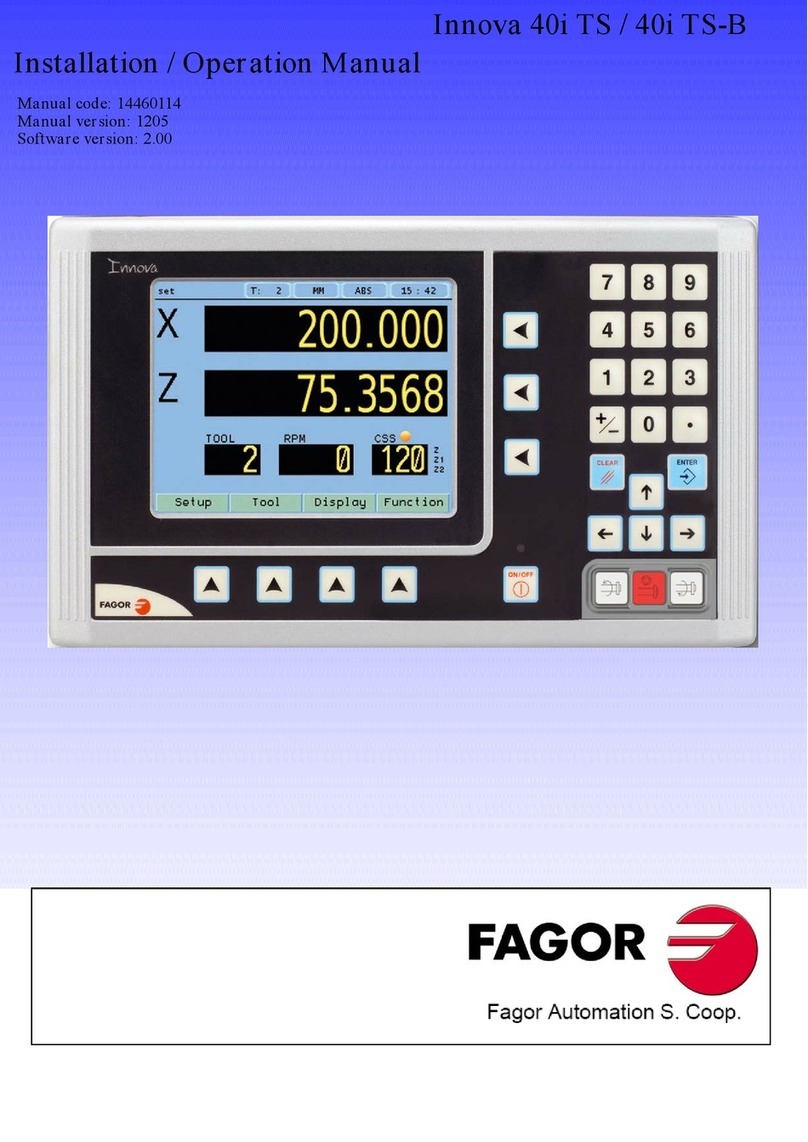
Fagor
Fagor Innova 40i TS Installation & operation manual