Glasdon TURBOCAST 800 Installation and operation manual

TURBOCAST 800 ™
Operating & Maintenance Manual
ENGLISH (UK) VERSION
APRIL 2022 - ISSUE 5
ORIGINAL INSTRUCTIONS
Towable Grit/Salt Spreader
This manual must be read before operating the machine
Glasdon U.K. Limited
Preston New Road
BLACKPOOL
Lancashire
FY4 4UL
Tel: (01253) 600410
Fax: (01253) 792558
e-mail: [email protected]
www.glasdon.com

Operating & Maintenance Manual
CONTENTS PAGE
1
Thank you for purchasing a Glasdon Turbocast 800 Towable Grit/Salt Spreader.
This manual contains important information for the operation and future care of your product.
SECTION 1
SECTION 2
SECTION 3
SECTION 4
SECTION 5
SECTION 6
SECTION 7
INTRODUCTION
Important Information
General Description
Speed Restrictions
Towing: The Legal Requirements
BEFORE USE
Important Information
Fitting the Tow Bar
Information
USING THE MACHINE
A Step-by-Step Guide to Broadcast Spreading
Guide to Drop Spreading
SPREAD TABLES
Broadcast Spread
Drop Spread
CONTROLS
Spread Adjustment
Speed Adjustment
Jockey Wheel
Spread Limiters
TROUBLESHOOTING
MAINTENANCE
2
2
2
2
2
4
4
4
6
7
7
10
12
12
13
14
14
14
15
15
16
19

1 Introduction
The Turbocast 800 Towable Grit/Salt Spreader has a capacity of 200 litres (250 kg) and can
either broadcast or drop spread grit/salt. The rate of spread can be adjusted over a range
of speeds between 5-20mph. A variance in particle size and moisture content of the gritting
material will be tolerated because the spreader can spread white and brown rock salt either
wet or dry. However, certain materials such as pure salt and kiln-dried sand are too ne to
spread effectively.
The Turbocast 800 is supplied with either a ball hitch or a pin hitch as standard.
Hitch height range accommodated is 290 to 690mm.
! IMPORTANT INFORMATION !
ROUTINE MAINTENANCE
Routine cleaning and maintenance of the Turbocast 800 Grit/Salt Spreader is
essential to ensure its optimum performance and to prevent unnecessary damage.
Do NOT leave any grit/salt in the hopper, even when the Turbocast 800 is covered
or being stored internally. Being hygroscopic, salt will absorb moisture and then set
hard like 'concrete'.
Salt in solution with water is incredibly corrosive and will attack metalwork and
seize bearings. It is therefore very important to empty the hopper after each use
and closely follow the maintenance instructions contained in this manual.
ANNUAL SERVICING
An annual or end of season service is essential to ensure the optimum performance
of the Turbocast 800. We appreciate that some of our customers may not have a
facility to undertake such work and we therefore offer an Annual Service Scheme
for all existing and new customers across the UK. Please contact us by email on
information.
GENERAL USAGE
The Turbocast 800 is not designed for gritting extensive areas of public roads and
highways.
TOWING SPEEDS
The maximum towing speeds (page 3) for the Turbocast 800, when spreading and
not spreading, must be strictly adhered to at all times.
LOADING OF GRIT/SALT
Care must be taken when loading the hopper. It is recommended that
bagged or loose grit/salt is shovelled into the hopper. Drop loading must be
avoided as this may cause serious damage to the hopper and spreading mechanism.
POTHOLES AND SPEED HUMPS
If the area being gritted has potholes or speed humps, caution must be exercised
and driving speeds kept to a maximum of 5mph.
TOWING VEHICLE
A competent person must approve the suitability of the towing vehicle being used,
which must take account of the recommended towing height for the Turbocast 800.
2

Speed Restrictions
The tyres and machine have been designed to operate at between 5mph - 20mph.
NOTE: 1. Spread rates are calculated at 5 to 20mph (8-32kph) for optimum performance.
2. The maximum towing speed (including not spreading) = 20mph (32kph).
As the vehicle incorporates neither suspension nor brakes - the maximum towing speed for
the machine when spreading is 20mph and all spread rates have been calculated up to this
maximum speed.
Towing: The Legal Requirements on the Public Highway
The machine has been designed to conform to the Road Vehicles (Construction and Use)
Regulations 1986 relating to trailers and gritting trailers for use on the public highway. In the
case of light trailers, weighing less than 3500kg maximum laden weight, there is no specied
relationship in UK law between the weight of the towing vehicle and the weight of the trailer.
The machine incorporates lights which conform to the Road Vehicles Lighting Regulations
1989 as amended, and so make it legal for use on the public highway. It should be noted that
gritting trailers are exempt from certain regulations set out in the Road Vehicles (Construction
and Use) Regulations 1986.
Furthermore there is a European Directive 2007/46/EC, enforced in the UK by the Vehicle
Certication Agency (VCA). This Directive is a legal requirement that all vehicles used on the
road conform to a set of standardised design criteria - where vehicles such as trailers must be
Type Approved to demonstrate that they are t for safe use on the highway. Turbocast 800
has been issued a European Community Whole Vehicle Type Approval (ECWVTA).
M1 Category Vehicles
For M1 category vehicles (i.e. Motor vehicles used for the carriage of passengers and
comprising not more than eight seats in addition to the driver's seat) the maximum permissible
trailer weight is quoted by the vehicle manufacturer. Alternatively, the vehicle manufacturer
may provide a maximum gross train weight (train weight = the laden weight of the trailer plus
the laden weight of the towing vehicle). If this is exceeded it is possible that the Courts or
Insurance Companies may take the view that it constitutes a danger.
Light Goods Vehicles
The maximum laden weight of a trailer that may be towed by a light goods vehicle depends
on both the stated gross train weight of the towing vehicle and the vehicle manufacturer's
recommended maximum permissible trailer weight. Neither the maximum permissible trailer
weight or the maximum gross train weight (i.e. The laden weight of the trailer plus the laden
weight of the towing vehicle) should be exceeded. It is possible that the stated gross train
weight is less than the sum of the stated maximum permissible laden weight of the towing
vehicle and the stated maximum permissible laden trailer weight. In this case the towing
vehicle and the trailer must be loaded so that each does not exceed its individual maximum
limit and the sum of both does not exceed the maximum gross train weight.
Breakaway or Safety Cable
There are no service brakes on the machine so a safety cable has been tted so that in the
unlikely event of an accidental de-coupling the machine is retained to the towing vehicle.
3
1 Introduction

Check the proposed towing vehicle is suitable for towing the Turbocast 800.
• Is the towing vehicle tted with either a pin hitch or ball hitch attachment?
Pin Hitch Attachment Ball Hitch Attachment
• Check the hitch point on the towing vehicle is rated to carry a minimum load of 420kg.
• Check the towing vehicle has a towing capacity greater than the maximum laden weight
of the Turbocast 800, 420kg.
420
If any of these conditions are not met, the towing vehicle will be
unsuitable for towing the Turbocast 800!
PLEASE FIND AN ALTERNATIVE VEHICLE.
4
Measure the height of the hitch
point on the towing vehicle (to the
centre of the ball or midpoint of
the usable part of the pin). Use the
Hitch Height Table (see Table 1)
overleaf to determine which xing
position to set the tow bar in.
Example - If the towing vehicle is
tted with a ball hitch whose height
measures 400mm (16”) from the
ground, this falls within the height
range 370-450mm. In this instance
the tow bar should be tted into
position 2.
Fig. 1
2 Before Use - Fitting the Tow Bar
2 Before Use - Important Information

Position
1*
Position
2
Position
3
Position
4
Position
5
Fitting Location
Suitable Hitch Height
Range of Towing Vehicle
(mm)
290-370 370-450 450-530 530-610 610-690
*with Tow Bar mounted upside down.
If the hitch is not at the correct height for the towing vehicle, do not t the Turbocast 800 at
an angle (see Fig. 2). This will impair the proper performance of the product. Instead, the hitch
height will need to be adjusted so that the top of the hopper sits as parallel as possible to the
ground (see Fig. 3). The top of the hopper should be as level with the ground as possible for
optimal performance. In the rst instance, measure the height of the hitch point on the towing
vehicle and determine which position to t the tow bar in to using Table 1.
Fig. 2
5
2 Before Use - Fitting the Tow Bar
Hitch Height Table
Fig. 3
Table 1

2 Before Use - Fitting the Tow Bar
Fig. 4
Before tting rst determine which position
you intend to mount the tow bar in. Check
the correct tting position by referring to Table
1. The tow bar is supplied separately to the
chassis and must be tted prior to use. Before
attempting tting it will be necessary to rest
the machine on the rear stand (see Fig. 4).
Place the 4 x M10 xing bolts through the 4
xing holes in the tow bar and through the
matching xing holes in the chassis mounting
plate (see Fig. 5). Place the M10 nuts on the
back and tighten using 2 x 17mm spanners or
socket set.
6
Wheels & Tyres
With reference to the Road Vehicles (Construction and Use) Regulations 1986 relating to
trailers and gritting trailers for use on the public highway, the Turbocast 800 is restricted to a
maximum towing speed of 20mph on public highways.
Check that the tyres are the correct pressure before every use.
Tyre Specication
Jockey Wheel
The Turbocast 800 is equipped with an adjustable jockey wheel enabling the machine to free
stand with the hopper and hitch horizontal.
Lights
Road-legal lighting is attached to the back of the machine as standard. Please ensure the
electrical supply from the towing vehicle is connected to the spreader using the cable and
plugs supplied.
2 Before Use - Information
Size Model Max load Max speed Pressure
5.00 - 10 4PR STARCO S-252 355kg 130kph (80mph) 51psi (3.5 Bar)
Fig. 5

7
3 Using the Machine - A Step-by-Step Guide
Fig. 6
STEP 1. The drive mechanism is housed under
the drive cover ap on the near-side (red
sticker on the outside) (see Fig. 6). Disengage
the switch by icking the handle out towards
you. Check that the two clutches (the parts
with the teeth) have disengaged from one
another, although this is hidden one clutch
should spin freely without touching the other.
The outer clutch is spring loaded and so
should spring out when disengaged. If it does
not, this is normal, simply use your hand to
rmly pull on the outer clutch assembly until it
springs away from the inner clutch. Close the
drive mechanism cover.
Fig. 7
STEP 2. Wheel the machine so that the ball
hitch point on the Turbocast 800 rests over the
ball hitch of the towing vehicle (see Fig. 7). A
set of instructions is attached to the front of
the hopper (see above) and operatives are
advised to follow this sequence for every use.
1
STEP BY STEP GUIDE.
The Turbocast 800 includes a series of on-product instructions to help guide the
operator through using the product.
The guide listed here follows the same sequence. The numbers (e.g. )next to each
STEP in the guide here correlate with the number system as used on the on-machine
graphics. E.g. STEPS 2-5 relate to ‘Hitching the Machine’ - which is explained in
graphic 1 on the machine.
1

3 Using the Machine - A Step-by-Step Guide
STEP 3. First, place the security cable over
the ball on the towing vehicle, then lift the
security release lever on the ball hitch point
and press the nose of the machine down
rmly onto the ball hitch. It will be necessary
to rotate the jockey wheel handle to raise
the jockey wheel (to lower the nose of the
machine) to give sufcient ground clearance
to lock the hitch onto the ball. Release the
security release lever on the ball hitch point
and once it has been pushed down onto the
ball it should make an audible ‘click’ once
secured. Check that it cannot be pulled off
the ball by pulling up rmly on the hitch point
handle (without touching the release lever).
STEP 4. Raise the jockey wheel as far is it will
go to give at least 50mm ground clearance
(see Fig. 9). If necessary, unclamp the jockey
wheel attachment, move it higher up and re-
clamp in position so that sufcient clearance
is afforded. To unclamp the jockey wheel, turn
the locking handle anti-clockwise until the
clamp is sufciently loose to allow the jockey
wheel attachment to slide up.
Fig. 8 Fig. 9
Fig. 10 Fig. 11
STEP 5. Plug one end of the electrical
connection cable supplied with the unit into
the socket on the front of the machine. If a
7 Pin electrical socket has been tted to the
towing hitch of the towing vehicle, connect
the opposite plug from the connection cable
into the socket on the towing vehicle (see Fig.
10). Wind the slack from the cable around the
draw bar along its length to minismise the risk
of damage to the cable.
STEP 6. Set the spread adjustment wheel to
the Min. Output setting. Twist the handle
clockwise until reasonably tight. Do not
overtighten.
50mm
8
1
1 2
UNLOCK

Min.
Set the desired spread rate by
turning the Adjustment Wheel
to the desired position.
354
2
1
Max.
Max.
C
B
A
Min.
3 Using the Machine - A Step-by-Step Guide
STEP 7. Load the hopper with grit salt.
DO NOT SHOCK LOAD THE GRITTER! Open
bags inside the hopper or shovel in loose
grit. Spread the loose grit salt around in the
hopper to level it out.
STEP 8. Set the spread adjustment wheel
to the required position for the desired
output. Clockwise motion for minimum and
anticlockwise for maximum spread, turn until
tight (refer to Table 2 on Pg. 11).
Fig. 12 Fig. 13
ZONE ‘C’ ZONE ‘A’
ZONE ‘B’
STEP 9. Locate the rubber drive wheel which
drives the spinner plate at the rear of the
machine. Set this to give the desired spread
output given the speed you will tow the
vehicle at when up to speed. If it is not set
in the corect position you will need to move
the position of the drive wheel (see Fig. 14).
Choose the correct position based on the
output required (refer to Table 2).
STEP 10. The drive wheel is locked in position
via a pair of M8 bolts, one is tted in a slot in
the drive wheel shaft which keeps the drive
wheel aligned while another is located into
one of the three speed setting holes in the
drive wheel shaft (see Fig. 15). To set the drive
wheel into a different position, loosen the
xing tted into one of the setting holes using
a 12mm spanner or socket until the screw is
clear of the drive wheel shaft. The drive wheel
can then be slid along the shaft in to another
setting position. You may nd it useful to
loosen the xing which is in the alignment slot
in the drive wheel shaft rst to make moving
the wheel a little easier. Once the xing is
aligned with the desired setting hole in the
drive wheel shaft, re-apply the M8 through
bolt and tighten the nut until the bolt sits into
the setting hole.
Fig. 14 Fig. 15
9
2
3
The 3 setting positions are speed-specic.
Setting 1 - 15 to 20mph
Setting 2 - 10 to 15mph
Setting 3 - 5 to 10mph

Min.
Set the desired spread rate by
turning the Adjustment Wheel
to the desired position.
354
2
1
Max.
Max.
C
B
A
Min.
3 Using the Machine - A Step-by-Step Guide
STEP 11. Check that the spread limiters are
raised and locked in the ‘up’ position. The
limiter locking handles operate on a spring pin
and locate into holes in the limiters (see Fig.
16).
STEP 12. Tow the machine to the desired start
location. Open the drive mechanism cover
and engage the drive mechanism see Fig.
17). Double-check that the clutch teeth are
securely interlocked. If they are, close the
cover.
Fig. 16 Fig. 17
Fig. 18 STEP 13. Tow the machine at the correct
speed and the machine will broadcast
spread at a low spread rate, with a consistent
8m spread. Some ne tuning of the spread
adjustment wheel position may be necessary
to achieve the desired output given the
conditions of the day and the type of grit salt
being spread.
STEP 14. Complete STEPS 1-7. Set the spread
adjustment wheel to a position within the
‘Drop Spreading’ range as indicated on the
graphic. Refer to Table 3 on Pg. 13.
STEP 15. Drop the spread limiters into the drop
spread positions by unlocking the spring pin
locks on both arms and dropping them down.
(see Fig. 20).
Fig. 19
Min.
Set the desired spread rate by
turning the Adjustment Wheel
to the desired position.
354
2
1
Max.
Max.
C
B
A
Min.
3 Using the Machine - Drop Spreading
Fig. 20
10
4 5

11
Fig. 18
STEP 16. Complete STEPS 9-13 (excluding
11) to begin spreading. Tow the machine
at the correct speed and the machine will
drop spread with a dense 1m spread. Some
ne tuning of the spread adjustment wheel
position may be necessary to achieve the
desired output given the conditions of the
day and the type of grit salt being spread.
3 Using the Machine - Drop Spreading
Fig. 21
STEP 17. Complete STEPS 1-7. Complete STEP
14 to set the desired output. Set the spread
limiters in the desired position. For example,
to spread to the right the left hand limiter
should be lowered and the right raised and
vice versa for spreading to the left. Check the
orange limiter locking handles are hand-tight
before setting off (see Fig. 22).
STEP 18. Complete STEPS 9-13 (excluding
11) to begin spreading. Tow the machine
at the correct speed and the machine
will broadcast spread to the Left or Right
(depending on which limiters you have set).
Some ne tuning of the spread adjustment
wheel position may be necessary to achieve
the desired output given the conditions of the
day and the type of grit salt being spread.
Fig. 22 Fig. 23
3 Using the Machine - Directional Spreading

12
INPUTS OUTPUT
Towing
Speed
(m.p.h.)
Spread
Setting
Speed
Setting
Spread Width
(approx.)
Spread
Consistency
Spread
Density
*(g/m2)
5-10 A 3 8.0m EXCELLENT 15
5-10 A 2 4.0m GOOD 30
5-10 A 1 2.0m OK 60
5-10 B 3 8.0m EXCELLENT 30
5-10 B 2 4.0m GOOD 60
5-10 B 1 2.0m OK 120
5-10 C 3 8.0m EXCELLENT 60
5-10 C 2 4.0m GOOD 120
5-10 C 1 2.0m OK 240
INPUTS OUTPUT
Towing
Speed
(m.p.h.)
Spread
Setting
Speed
Setting
Spread Width
(approx.)
Spread
Consistency
Spread
Density
*(g/m2)
10-15 A 3 8.0m+ SCATTERED 10
10-15 A 2 8.0m EXCELLENT 15
10-15 A 1 4.0m GOOD 30
10-15 B 3 8.0m+ SCATTERED 20
10-15 B 2 8.0m EXCELLENT 30
10-15 B 1 4.0m GOOD 60
10-15 C 3 8.0m+ SCATTERED 40
10-15 C 2 8.0m EXCELLENT 60
10-15 C 1 4.0m GOOD 120
INPUTS OUTPUT
Towing
Speed
(m.p.h.)
Spread
Setting
Speed
Setting
Spread Width
(approx.)
Spread
Consistency
Spread
Density
*(g/m2)
15-20 A 3 8.0m+ SCATTERED 5
15-20 A 2 8.0m+ SCATTERED 10
15-20 A 1 8.0m EXCELLENT 15
15-20 B 3 8.0m+ SCATTERED 10
15-20 B 2 8.0m+ SCATTERED 20
15-20 B 1 8.0m EXCELLENT 30
15-20 C 3 8.0m+ SCATTERED 20
15-20 C 2 8.0m+ SCATTERED 40
15-20 C 1 8.0m EXCELLENT 60
* Spread Density is an estimate only and will vary depending upon the type of grit product used and the climatic conditions at the time of spreading.
4 Broadcast Spread
Table 2

13
4 Drop Spread
INPUTS OUTPUT
Towing
Speed
(m.p.h.)
Spread
Setting
Speed
Setting
Spread Width
(approx.)
Spread
Consistency
Spread
Density
*(g/m2)
5-10 A 3 1.0m EXCELLENT 120
5-10 A 2 1.0m GOOD 120
5-10 A 1 1.0m GOOD 120
5-10 B 3 1.0m EXCELLENT 240
5-10 B 2 1.0m GOOD 240
5-10 B 1 1.0m GOOD 240
5-10 C 3 1.0m EXCELLENT 480
5-10 C 2 1.0m GOOD 480
5-10 C 1 1.0m GOOD 480
INPUTS OUTPUT
Towing
Speed
(m.p.h.)
Spread
Setting
Speed
Setting
Spread Width
(approx.)
Spread
Consistency
Spread
Density
*(g/m2)
10-15 A 3 1.0m GOOD 120
10-15 A 2 1.0m EXCELLENT 120
10-15 A 1 1.0m GOOD 120
10-15 B 3 1.0m GOOD 240
10-15 B 2 1.0m EXCELLENT 240
10-15 B 1 1.0m GOOD 240
10-15 C 3 1.0m GOOD 480
10-15 C 2 1.0m EXCELLENT 480
10-15 C 1 1.0m GOOD 480
INPUTS OUTPUT
Towing
Speed
(m.p.h.)
Spread
Setting
Speed
Setting
Spread Width
(approx.)
Spread
Consistency
Spread
Density
*(g/m2)
15-20 A 3 1.0m GOOD 120
15-20 A 2 1.0m GOOD 120
15-20 A 1 1.0m EXCELLENT 120
15-20 B 3 1.0m GOOD 240
15-20 B 2 1.0m GOOD 240
15-20 B 1 1.0m EXCELLENT 240
15-20 C 3 1.0m GOOD 480
15-20 C 2 1.0m GOOD 480
15-20 C 1 1.0m EXCELLENT 480
* Spread Density is an estimate only and will vary depending upon the type of grit product used and the climatic conditions at the time of spreading.
Table 3

14
5 Controls
The spread adjustment wheel is located at the front of the hopper. In conjunction with the
speed adjustment drive wheel (see below) this controls the output of grit. By turning the wheel
counter-clockwise, the level of displacement which is afforded to the motion of the agitator
ngers is increased. The larger the displacement the more grit is icked out through the grit
aperture and onto the spinner plate. Conversely, when the wheel is turned clockwise, the
opposite occurs, with the displacement of the agitation ngers minimised to reduce the grit
output.
When broadcast spreading the whole of the range of movement of the adjustment wheel is
effective. The wheel can be rotated clockwise or anticlockwise and is divided into 3 spread
Zones, labelled ‘A’, ‘B’ and ‘C’ (see Fig. 24). The minimum output is given by turning the
wheel clockwise until stop through Zone ‘A’, whilst the maximum output requires full rotation
anticlockwise through Zone ‘C’ until stop. When drop spreading, the user need only set the
wheel within or beyond Zone ‘A’ (see Fig. 25). This is because when the spread limiters are
engaged, the density of the output of grit is increased eight-fold due to the limitation of the
spread width from 8m to 1m.
The drive wheel is locked in position via a pair of M8 bolts, to set the drive wheel into a
different position, remove the xing tted into one of the setting holes using a 12mm spanner
or socket until the bolt is clear of the drive wheel shaft. The drive wheel can then be slid along
the shaft into another setting position. You may nd it useful to loosen the xing which is in the
alignment slot in the drive wheel shaft rst to make moving the wheel a little easier.
Spread Adjustment
Speed Adjustment
When the new setting position
has been selected - 1, 2 or 3 (see
Fig. 26), simply align the bolt with
the corresponding hole in the
shaft and re-apply the M8 bolt
through the shaft and tighten
the M8 nut xing until it is fully
engaged with the shaft.
Fig. 24 Fig. 25
Fig. 26
Min.
Set the desired spread rate by
turning the Adjustment Wheel
to the desired position.
354
2
1
Max.
Max.
C
B
A
Min.
Min.
Set the desired spread rate by
turning the Adjustment Wheel
to the desired position.
354
2
1
Max.
Max.
C
B
A
Min.

15
5 Controls
The jockey wheel is adjustable to enable easier loading and unloading of the machine hitch
onto that of the towing vehicle. To raise the nose of the machine, turn the cranked handle
in a clockwise motion. To lower the nose of the machine, turn the handle anti-clockwise.
Particularly when operating the machine with towing vehicles with a low hitch height (hitch
positions 1 and 2), it may be necessary to unclamp and reset the position of the jockey
wheel once the machine has been connected to the towing vehicle to increase the ground
clearance. To do this, simply unclamp the locking handle on the clamp which holds the
jockey wheel to the tow bar (see Fig. 27). Shift the position of the jockey wheel up and then
re-clamp in place. In some cases it might be necessary to remove the jockey wheel entirely
whilst the machine is attached to the towing vehicle to give sufcient ground-clearance.
NOTE: The jockey wheel will need to be reattached BEFORE unhitching the machine from the
towing vehicle to ensure it can be safely manoeuvred when disconnected from the vehicle.
Fig. 27
The spread limiters are operated via a pair of spring pin locking handles, one for each limiter.
When pulled the handles disengage the retaining pin which holds the limiter arms up and
allows them to drop into position for drop spreading. The handles automatically engage the
pin on top of the limiter arm to ensure it stays locked down whilst drop spreading. The limiters
can be placed back in the raised position by pulling the lock handles to disengage the pin,
raising the limiter arm and then releasing the handle so that the pin re-engages with the hole
through the limiter arm itself to lock it in place.
Fig. 28

6 Troubleshooting
1. The machine is not spreading, or is spreading intermittently.
Quick Check:
Is there sufcient material in the hopper?
If not. Rell.
Is the aperture at the bottom of the hopper jammed or clogged up with material?
Use a tool to free up the compacted material.
Is the drive engaged?
Check the engagement between the clutches. If not properly spaced, screw the handle
clockwise until a position is reached where the clutches engage successfully and yet are still
clear of one another when the handle is icked into the disengaged position.
Am I towing at the speed which correlates to the settings chosen?
Re-check the spread settings. If not. Alter your towing speed accordingly.
Is the agitation mat lifting in a wave like pattern?
If not. Remove the agitation mat and check the condition of the cams. If the cams are worn,
they may need replacing.
Quick Check:
Am I towing at the speed which correlates to the settings chosen?
Re-check the spread settings. If not. Alter your towing speed accordingly.
Is the agitation mat lifting in a wave like pattern?
If not. Remove the agitation mat and check the condition of the cams. If the cams are worn,
they may need replacing.
Have I selected an appropriate spread setting?
Check that the output is not overloading the spinner plate with too much grit.
Probable Cause:
When the towing speed is lower than the speed setting the machine has been set in, it can
mean that the spinner plate is spinning more slowly than is required to dispense the grit
effectively. This can lead to the unusual pattern. Also, if the spread setting is set to give a very
high output (i.e. Zone ‘C’ or Max.) this can exacerbate the effect.
Fig. 29 Fig. 30
Fig 29. Shows a typical, evenly
distributed spread
Fig 30. Shows a skewed, linear
spread pattern
16
2. The machine is spreading, but it is spreading material more to one side and
leaving a ‘line’ of grit down one side of the spread pattern (see Fig. 29).
Note: This may occur in either broadcast or drop spread modes.

Remedies:
• Increase the towing speed to fall within the recommendations for the speed setting.
• If the towing speed is ok, move the speed adjustment drive wheel to a lower towing
speed setting. For example, if you are in setting 2, move it to setting 3. This will increase the
spinner speed and mean the spinner plate is better able to dispense the grit with an even
distribution given the amount of grit being ejected from the hopper.
• Decrease the spread output by turning the spread adjustment control. It is possible
that too much grit is being released from the hopper for the spinner plate to effectively
distribute.
3. The drive is engaged and yet no grit is being spread.
Quick Check:
Is there sufcient material in the hopper?
If not. Rell.
Is the aperture at the bottom of the hopper jammed or clogged up with material?
If so. Use a tool to free up the compacted material.
Is the drive engaged?
Check the engagement between the clutches.
If not properly spaced when engaged, screw the handle clockwise until a position is reached
where the clutches engage successfully and yet are still clear of one another when the
handle is disengaged.
Probable Cause:
The engagement handle which engages and disengages the machine has become loose
(through normal use) or has been loosened by turning the handle. The position of the handle
is factory-set, however has been designed with sufcient adjustment to allow the operator to
adjust the position if required.
Remedies:
• Reset the spacing between the clutches by tightening or loosening off the engagement
handle position.
Has the chain come off the drive train?
Remove the mudguard and protective plastic sheets covering the drive train on the near side
of the machine (UK). If either of the chains has come off it will need to be remounted. It will be
necessary to slacken off the chain tensioner(s) to allow the chain to be remounted. Always
remember to re-tension the chain afterwards by setting the tensioner in a position where the
nylon roller squeezes against the chain to keep it taught.
Probable Cause:
The machine has been used on uneven ground or over trafc calming measures which has
caused the chain to jump off the sprockets or the chain has become stretched and done so
of its own volition.
Remedies:
• Remount the chain and/or reset the chain tension by repositioning the chain tensioner(s).
• Ensure the chain tension is checked at least annually.
6 Troubleshooting
17

Has the clutch system been damaged in any way?
Check for signs of damage to the two white clutches which initiate the drive mechanism.
These have been designed so that they will break under unusual loading conditions. E.g. If
the machine becomes jammed by an impediment - such as a large stone jamming within
the aperture in the hopper. If signs of damage are visible to the clutches then one or both will
need to be replaced. This fail safe has been designed into the drive system to protect the rest
of the drive train, rather than causing more signicant damage elsewhere on the machine.
The clutches are easily accessible and can be replaced by removing the mudguard, then
disassembling the simple clutch assembly. Please contact Glasdon for details.
Probable Cause:
The machine has been used to spread a material which compacts readily (e.g. Soil). This has
resulted in a jamming of the hopper aperture and caused the agitation system to temporarily
seize up. In some instances, the clutches will break to prevent damage to the rest of the drive
/ agitation system.
Remedies:
• Replace one or both of the clutches from the drive mechanism assembly. Details on
replacement will be advised by one of our Technical Services team.
4. The tail lights are not working correctly.
Quick Check:
Is the plug correctly connected at both ends?
Reinstall to make sure.
Are there signs of damage to the cable?
If so cease use of the cable immediately and request a replacement.
Are any of the bulbs in need of replacement?
If so request a replacement.
Are any of the connections loose?
Open the plug(s) to determine if there are any loose connections to isolate the fault.
Are there signs that any of the connections are dirty or rusty?
Inspect the connections. Clean and spray any suspect connections with a lubricant such as
WD40.
6 Troubleshooting
18

7 Maintenance
19
Emptying the Hopper
To rapidly evacuate the hopper of grit, rst set the spread adjustment wheel to the maximum
setting (‘Max.’ or ‘Zone C’) (see Fig. 31). Engage the drive mechanism and tow the machine
around until the majority of grit has been dispensed (see Fig. 32). With the spread adjustment
at its maximum output, it will release the material rapidly - so choosing an area where a dense
spread is either benecial, or where it will cause minimal disruption is recommended when
doing this.
Min.
Set the desired spread rate by
turning the Adjustment Wheel
to the desired position.
354
2
1
Max.
Max.
C
B
A
Min.
Fig. 31
Storing the Machine
After Each Use
When storing the machine, the drive mechanism should be disengaged and the spread
adjustment wheel set in the Max. setting. This will put the least amount of strain on the
agitation mechanism as possible during storage. The machine should be thoroughly cleaned
after each and every use. Any material which is left in the hopper may set solid as grit/salt is
hygroscopic (moisture absorbing) and will harden like concrete if left. Cleaning after each
use is important and will extend the lifetime of the machine. If left uncleaned, the grit can set
and will damage the mechanics of the machine when next used.
Cleaning
To clean, use a hosepipe, or ideally a jet wash to rinse away any excess material that remains
after the hopper has been emptied. For particularly stubborn deposits, it may be necessary to
employ the use of a brush to sweep away any build ups. Pay particular attention to ensuring
the rubber agitation mat, the grit aperture through which grit exits the hopper and spinner
plate are all thoroughly cleaned and devoid of grit. The entire exterior of the machine can
be cleaned. Do not remove any of the machine’s protective covers before cleaning as these
areas should already be shielded from grit contamination. Care should be taken, particularly
when using a jet wash, not to focus the jet on any areas which must be greased (see Pg. 21).
This can remove the grease from moving parts - meaning more need be applied afterward.
The machine should be stored on its wheels with the tow bar attached, or can be rested on
the rear stand.
Fig. 32
Other manuals for TURBOCAST 800
1
Table of contents
Other Glasdon Spreader manuals
Popular Spreader manuals by other brands
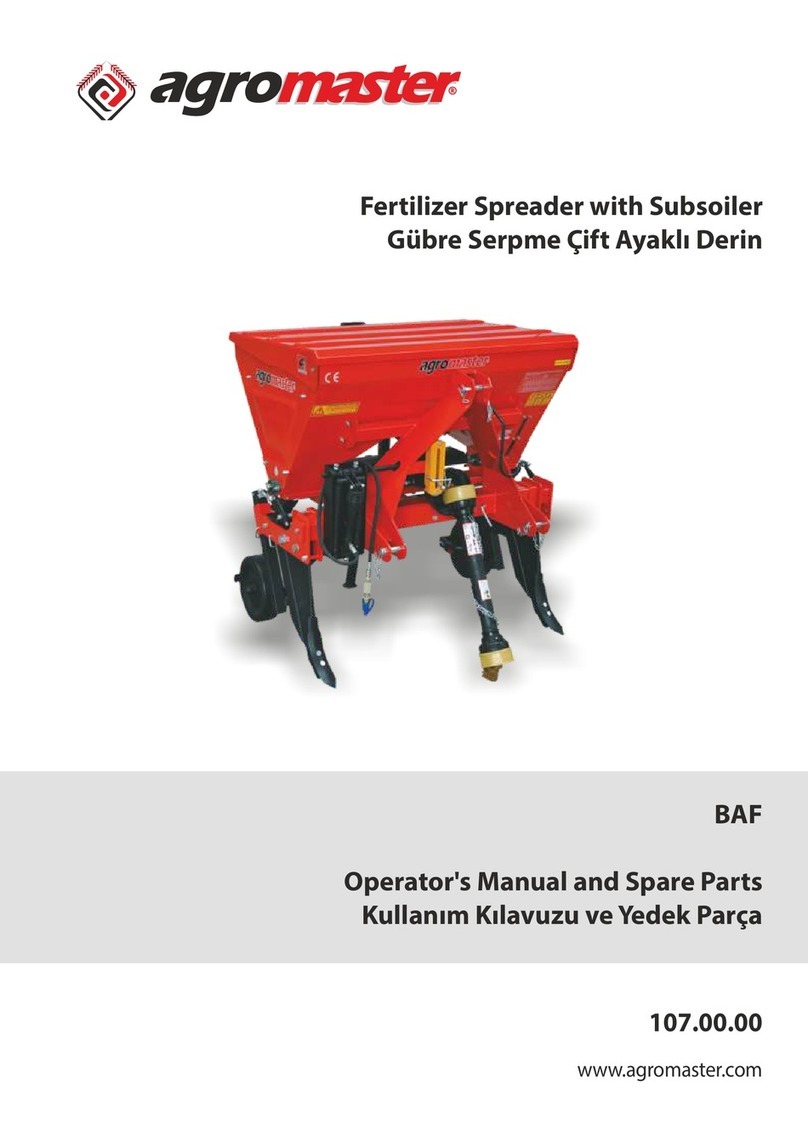
agromaster
agromaster BAF Series OPERATOR'S MANUAL AND SPARE PARTS
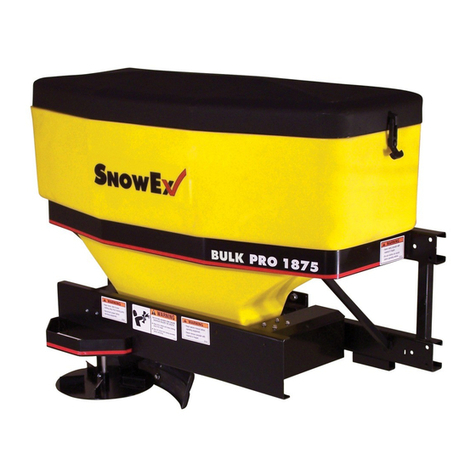
SnowEx
SnowEx Bulk Pro SP-1575 Owner's manual and installation instructions

Western
Western PRO-FLO 2 owner's manual
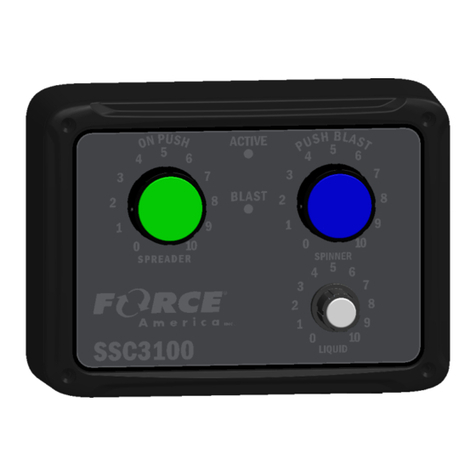
Force America
Force America SSC3100 Operation and calibration manual
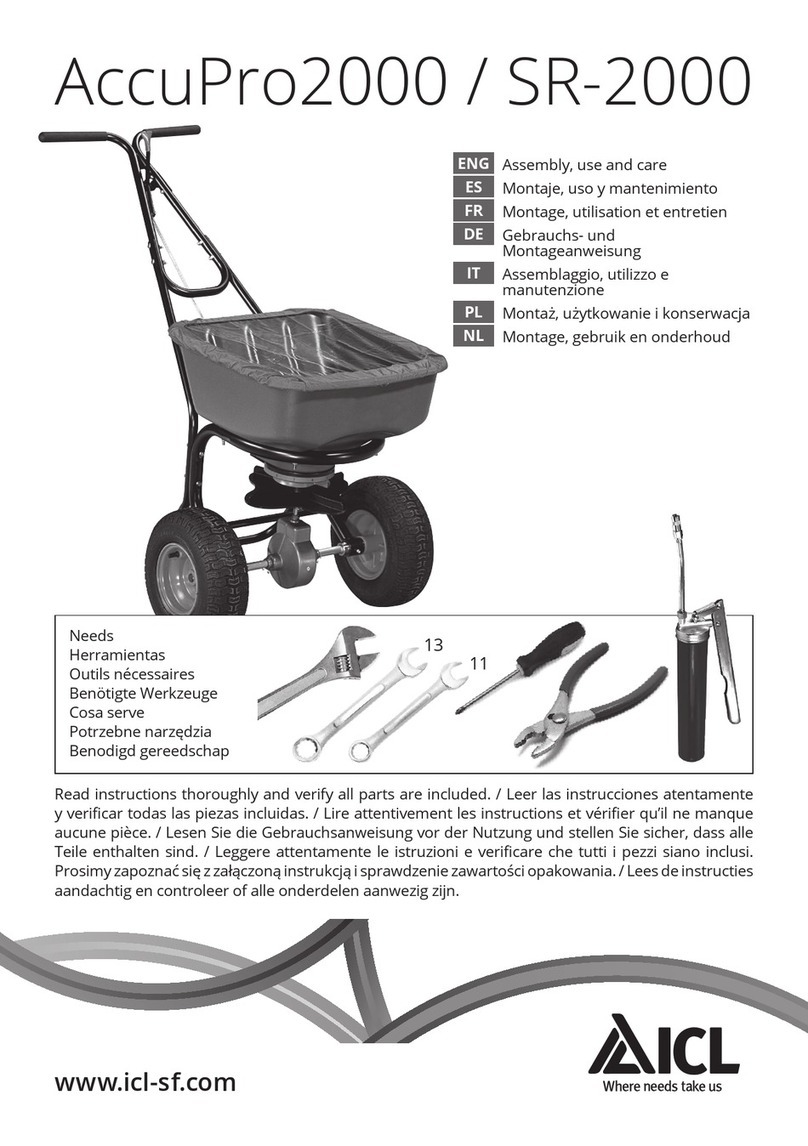
ICL
ICL AccuPro2000 Assembly, use and care
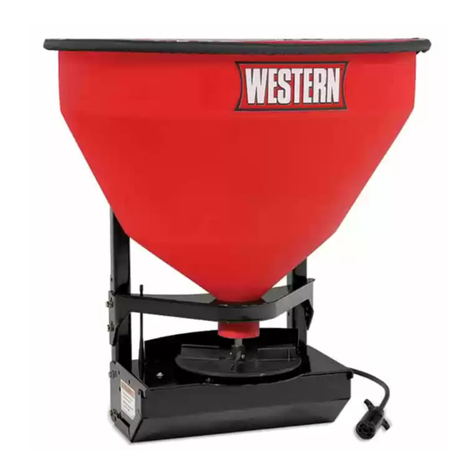
Western
Western PRO-FLO 300W Owner's manual and installation instructions
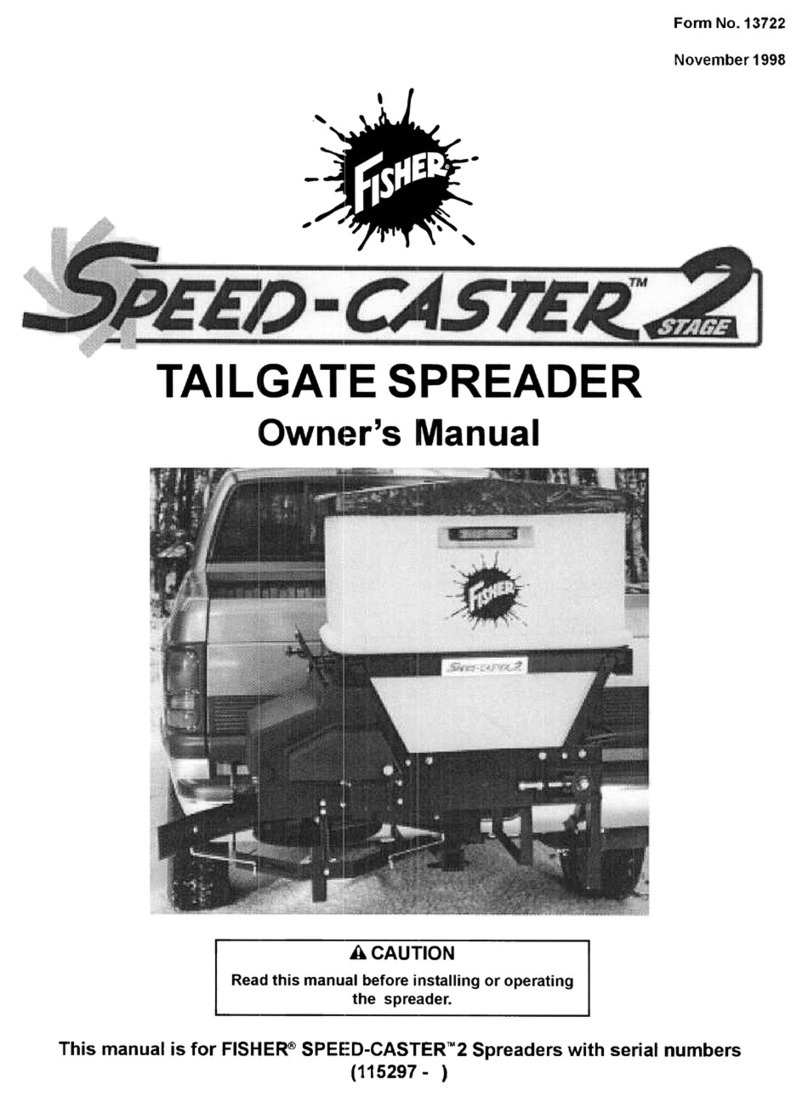
Fisher
Fisher M-Scope Gold Bug 2 owner's manual
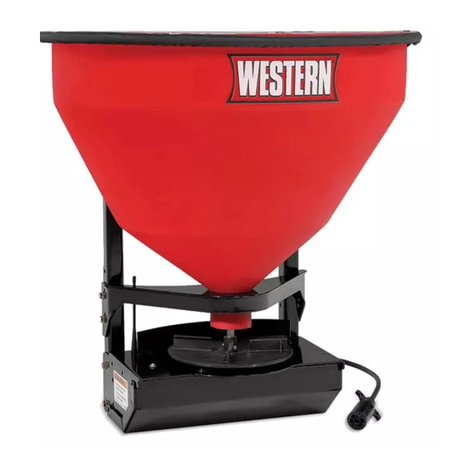
Western
Western LOW-PRO Owner's manual and installation instructions

Gardena
Gardena Classic 300 Assembly instructions
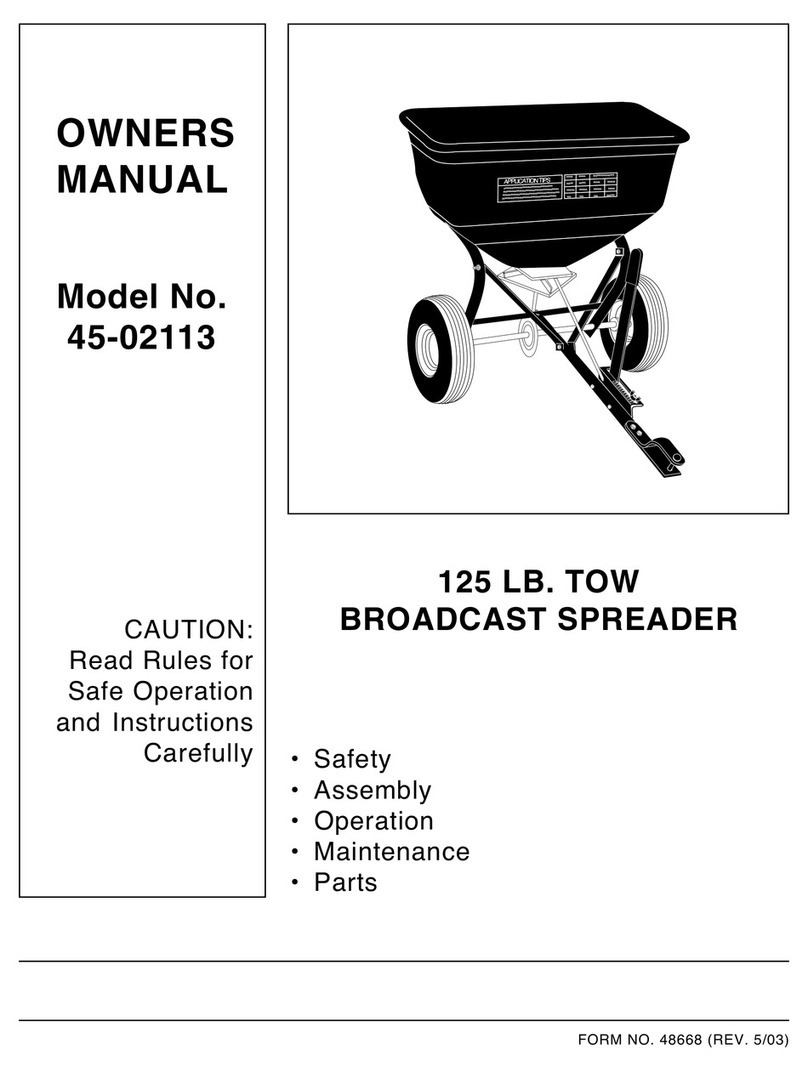
Agri-Fab
Agri-Fab 45-02113 owner's manual

Fisher
Fisher SWING AWAY installation instructions
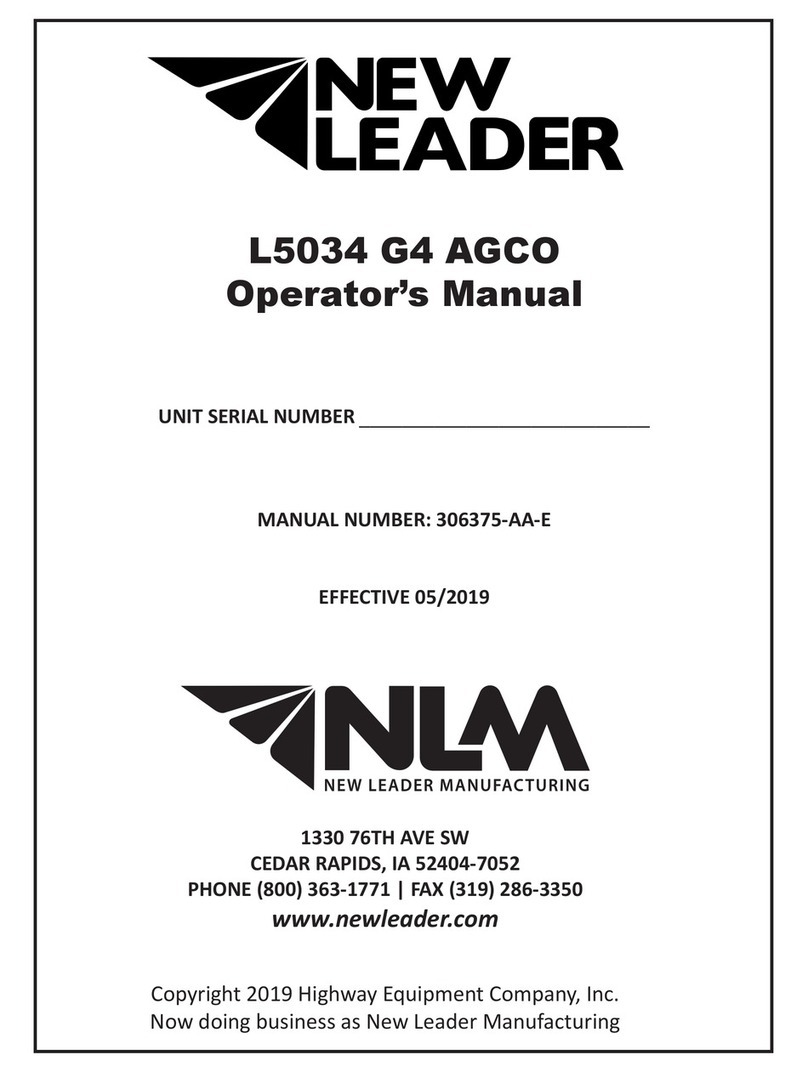
New Leader
New Leader L5034G4 AGCO Operator's manual