Glentek SMA8130 Installation and operating instructions

OPERATION
&
SERVICE MANUAL
Model SMA8130
Model SMA8230
Model SMA8330
Brushless Amplifier System

SMA8130, SMA8230, and SMA8330
2
Glentek Inc., 208 Standard Street, El Segundo, California 90245, U.S.A. (310) 322-3026
TABLE OF CONTENTS Page
Introduction........................................................................................................6
Chapter One: Description, Features and Specifications
1.1 Description...................................................................................................7-8
1.2 Features.......................................................................................................8-9
1.2.1 Amplifier Module (SMA8X30-1A-1)....................................................8-8
1.3 Specifications...............................................................................................10-11
1.3.1 Amplifier Module (SMA8X30-1A-1)..............................................10-11
1.3.1.1 Input and Output Power............................................................10
1.3.1.2 Signal Inputs.............................................................................10
1.3.1.3 Digital Inputs.............................................................................10
1.3.1.4 System......................................................................................11
1.3.1.5 Outputs.....................................................................................11
1.3.2 Mechanical.........................................................................................11
Chapter Two: Theory of Operation
2.1 Introduction..................................................................................................12
2.2 Driving DC Servo Motors.............................................................................12
2.3 Servo Loops.................................................................................................13
2.4 Brushed Motors vs Brushless Motors..........................................................14-15
2.5 Sinusoidal vs Trapezoidal............................................................................15
2.6 The Advantages and Disadvantages of a Trapezoidal Amplifier System....16
2.7 Current Mode vs Velocity Mode...................................................................16
2.8 Tachometer (Velocity Mode) Feedback Options .........................................17
2.9 Commutation Using A Resolver...................................................................17
2.10 Current Mode in Sine/Resolver or Trapezoidal Amplifier vs Two/Three
Phase Input Current Mode Amplifier..........................................................17
2.11 Protection Circuits......................................................................................17
TABLE OF CONTENTS

SMA8130, SMA8230, and SMA8330
3
Glentek Inc., 208 Standard Street, El Segundo, California 90245, U.S.A. (310) 322-3026
Page
Chapter Three: Model Numbering
3.1 Introduction..................................................................................................18
3.2 Amplifier Module..........................................................................................18-20
3.2.1 Trapezoidal Mode...............................................................................18
3.2.2 Sine/Resolver Mode...........................................................................19
3.2.3 Two/Three Phase Input Current Mode...............................................20
Chapter Four: Installation
4.1 Introduction..................................................................................................21
4.2 Mounting......................................................................................................21
4.3 Wiring...........................................................................................................21-23
4.3.1 RFI/EMI and Wiring Technique..........................................................21
4.3.2 Wire Size and Type............................................................................22
4.3.3 Connector Size and Type...................................................................22-23
4.3.3.1 The Power and Motor Connector - TB1 of Amplifier.................22
4.3.3.2 The Signal Connector...............................................................23
4.4 Amplifier Module Connections (SMA8X30-1A-1).........................................24-26
4.4.1 Power and Motor Connections - TB1.................................................24
4.4.2 Signal Connections for the Trap. and Sine/Resolver Mode - J1 ........24
4.4.3 Signal Connections for the 2/3 Phase Current Mode Amplifier..........25
4.4.4 Signal Connections for the Trapezoidal Mode Pre-amp.....................25
4.4.5 Signal Connections for the Sine/Resolver Mode Pre-amp.................26
Chapter Five: Configuration
5.1 Introduction..................................................................................................27
5.2 Logic Input Configuration.............................................................................27
5.3 Trapezoidal Mode Amplifier Configuration...................................................27-29
5.3.1 +15V/+5V Logic Level Configuration..................................................27
5.3.2 Standard Configuration ......................................................................28
5.3.3 Integrator Configuration......................................................................28
5.3.4 Hall-Sensor Configuration..................................................................28
5.3.5 Motor Reverse Configuration .............................................................28
TABLE OF CONTENTS

SMA8130, SMA8230, and SMA8330
4
Glentek Inc., 208 Standard Street, El Segundo, California 90245, U.S.A. (310) 322-3026
Page
5.3.6 Simulated Tach - Disable Configuration.............................................28
5.3.7 Simulated Tach - Reverse Configuration ...........................................29
5.3.8 Simulated Tach - Speed Configuration ..............................................29
5.4 Sine/Resolver Mode Amplifier Configuration...............................................29-31
5.4.1 +15V/+5V Logic Level Configuration...............................................29
5.4.2 Standard Configuration...................................................................29
5.4.3 Encoder Output Resolution Configuration ......................................30
5.4.4 Motor Pole Configuration ................................................................31
5.5 Two/Three Phase Input Current Mode Amplifier Configuration...................31
5.5.1 +15V/+5V Logic Level Configuration...............................................31
5.5.2 Standard Configuration...................................................................31
Chapter Six: Start Up and Calibration
6.1 Introduction..................................................................................................32
6.2 Initial Start Up ..............................................................................................32
6.3 Trapezoidal Mode Amplifier Calibration.......................................................32-34
6.3.1 Velocity and Simulated Velocity Mode Calibration Procedure.......33-34
6.3.2 Current Mode Calibration Procedure ..............................................34
6.4 Sine/Resolver Mode Amplifier Calibration ...................................................35
6.4.1 Velocity Mode Calibration Procedure.................................................35-36
6.4.2 Current Mode Calibration Procedure..................................................36-37
6.5 Two/Three Phase Input Current Mode Amplifier Calibration .......................37-38
6.5.1 Two Phase Input Current Mode Calibration Procedure .....................37
6.5.2 Three Phase Input Current Mode Calibration Procedure...................38
6.6 Calibration Setup Record.............................................................................39
6.7 Resolver Alignment Procedure....................................................................40-41
Chapter Seven: Maintenance, Repair and Warranty
7.1 Maintenance ................................................................................................42
7.2 Amplifier Faults............................................................................................42-45
TABLE OF CONTENTS

SMA8130, SMA8230, and SMA8330
5
Glentek Inc., 208 Standard Street, El Segundo, California 90245, U.S.A. (310) 322-3026
Page
7.2.1 Table of Fault LED Conditions ...........................................................42
7.2.2 Under Voltage Fault ...........................................................................43
7.2.3 Motor Over Temp Fault......................................................................43
7.2.4 High Speed Electronic Circuit Breaker (HS/ECB) Fault.....................43
7.2.5 Low Speed Electronic Circuit Breaker (LS/ECB) Fault ......................43
7.2.6 Over Temp Fault ................................................................................44
7.2.7 Over Voltage Fault .............................................................................44
7.2.8 Resetting A Fault................................................................................44
7.3 Amplifier Failure...........................................................................................44
7.4 Factory Repair.............................................................................................45
7.5 Warranty......................................................................................................45
Appendix A: Amplifier Drawings
SMA8030 Brushless Power Board Installation Schematic (8030-1037)...............47
SMA8030 Brushless Power Board Assembly Drawing (8030-1032)....................48
SMA8130 Trapezoidal Amplifier Module Installation (8030-1033)........................49
SMA8230 Sine/Resolver Amplifier Module Installation (8030-1034) ....................50
SMA8330 2Ø/3Ø Amplifier Module Installation (8030-1035)................................51
Appendix B: Personality Module (Pre-amp)
SMA8130 Trapezoidal Mode Installation Schematic (8000-1130)........................53
SMA8130 Trapezoidal Mode Assembly Drawing (8000-1131).............................54
SMA8230 Sine/Resolver Mode Installation Schematic (8000-1430) ....................55-56
SMA8230 Sine/Resolver Mode Assembly Drawing (8000-1431) .........................57
SMA8330 2Ø/3Ø Current Mode Installation Schematic (8000-1330)...................58
SMA8330 2Ø/3Ø Current Mode Assembly Drawing (8000-1331)........................59
TABLE OF CONTENTS

SMA8130, SMA8230, and SMA8330
6
Glentek Inc., 208 Standard Street, El Segundo, California 90245, U.S.A. (310) 322-3026
Introduction
Glentek's brushless DC motors and amplifiers offer the ultimate in low maintenance and high
performance motion-control. Glentek offers a full line of matched motors and amplifiers to meet
virtually every motion-control application.
This manual provides all the technical information necessary to install, configure, operate,
and maintain our TORQUE-SWITCH™series, brushless servo-motor amplifiers, models
SMA8130, SMA8230, SMA8330. These amplifiers combine the economy of trapezoidal drive
current or the high performance of sinusoidal motor current with the efficiency of pulse-width
modulation (PWM).
We suggest that you take the time to read this manual from cover-to-cover before
attempting to work with these amplifiers for the first time. If at any time you have questions
not addressed in this manual, or have any special requirements, please feel free to call and
discuss them with a Glentek applications engineer. We are happy to provide both off-the-shelf
and custom products. With over three decades in the servo-motor/amplifier business, we have a
vast pool of applications knowledge waiting to assist you.
Thank you for selecting Glentek for your motion-control needs. It is our goal to save you time
and money, and to provide you with a superior product.

SMA8130, SMA8230, and SMA8330
7
Glentek Inc., 208 Standard Street, El Segundo, California 90245, U.S.A. (310) 322-3026
Chapter One: Description, Features and Specifications
1.1 Description:
This brushless amplifier system has been designed to offer you, our customer, a large
degree of flexibility and customization with a standard, in stock product. Each amplifier
consists of a standard power output board with one of our three types of personality modules
mounted on it. (To help you understand the various brushless amplifier and motor system
combinations and their respective advantages and disadvantages, please refer to chapter
two of this manual which describes the theory of operation). Following is a brief description
of these three personality modules and their mode(s) of operation:
• Trapezoidal Mode (SMA8130) - In this mode of operation, which is also commonly
referred to as six step, the brushless motor is commutated by hall sensors or an encoder
which contains these commutation signals. This personality module can be configured for
the following three different types of operation:
• VELOCITY MODE - In this mode of operation, a velocity signal from a brushless or
brush type tachometer is used to close a velocity loop in the amplifier. Please see
section 2.3, 2.7, 2.8 of this manual for more detailed information.
• SIMULATED VELOCITY MODE - In this mode of operation, a circuit on the
personality module looks at the hall sensors and generates a simulated velocity
signal which is used to close a velocity loop in the amplifier. This mode of operation
offers an extremely cost effective velocity mode system for medium to high velocity
applications. Please see section 2.6 of this manual for more detailed information.
• CURRENT MODE - In this mode of operation, which is also commonly referred to as
torque mode, a current in the motor is produced which is directly proportional to the
input signal. Please see section 2.2, 2.5, 2.7 of this manual for more detailed
information.
• Sine/Resolver Mode (SMA8230) - In this mode of operation, a brushless motor with an
integral resolver is required. The personality module contains a resolver to digital
converter which provides the positional information to the amplifier that is required to
commutate the motor. This positional information is also used by the personality module
to emulate a quadrature encoder output. This personality module can be configured for
the following two different types of operation:
• VELOCITY MODE - In this mode of operation, the personality module generates a
tachometer signal which is used to close a velocity loop in the amplifier. Please see
section 2.3, 2.5, 2.8 of this manual for more detailed information.
• CURRENT MODE - In this mode of operation, which is also commonly referred to as
torque mode, sine wave currents in the motor are produced that are directly
proportional to the input signal. Please see section 2.5, 2.7, 2.9 of this manual for
more detailed information.
• Two/Three Phase Input Current Mode (SMA8330) - In the two phase current mode, the
amplifier generates three sine wave currents that are proportional to two input signals.
This third command is generated on the personality module as the negative sum of the
other two signals. In the three phase current mode, the amplifier generates three sine
wave currents that are proportional to three input signals. Please see section 2.5, 2.9 of
this manual for more detailed information.
CHAPTER 1: DESCRIPTION, FEATURES AND SPECIFICATIONS

SMA8130, SMA8230, and SMA8330
8
Glentek Inc., 208 Standard Street, El Segundo, California 90245, U.S.A. (310) 322-3026
CHAPTER 1: DESCRIPTION, FEATURES AND SPECIFICATIONS
1.2 Features:
1.2.1 Amplifier Module (SMA8X30-1A-1):
• Ergonomic design: Easy access to connections, adjustments, and test points.
• Wide operating 120-340VDC.
buss voltage:
• Complete isolation: Complete isolation from input to output.
• Dual signal inputs: Two single-ended or one differential. Both single-ended inputs
may be used simultaneously. All inputs have up to 15,000 A/V
gain, and all inputs will accept ±13VDC except single-ended,
which will accept ±10VDC.
• Dual mode operation: The standard amplifier may be configured for velocity (RPM)
(8130 & 8230 only) control or current (torque) control.
• Current limit: Maximum motor current is adjustable.
• Silent operation: Carrier frequency is 20KHz.
• Short circuit protection: Complete short circuit and ground fault protection.
• LED diagnostics: Red LED flashes to display various fault conditions and a
green LED illuminates to indicate normal operating conditions.
• Encoder emulation: Encoder emulation comes standard with line driver outputs,
(8230 only) quadrature and zero index.
• Frequency response: 750 Hz minimum.
(Velocity Loop)
• Frequency response: 2 KHz minimum.
(Current Loop)
• Digital limit/enable Three separate logic inputs can stop the motor in either or both
Inputs: directions. Inputs may be configured for active-high or active-
low, pull-up or pull-down termination, and a 0 to +5V or 0 to
+15V range.

SMA8130, SMA8230, and SMA8330
9
Glentek Inc., 208 Standard Street, El Segundo, California 90245, U.S.A. (310) 322-3026
• Pseudo tach. option: For medium and high-speed, unidirectional or bidirectional
(8130 only) applications, an option allows the hall sensor inputs to produce
a simulated tachometer voltage thus eliminating the need for an
external tachometer.
• Encoder outputs: Incremental (quadrature) position outputs with separate index.
(8230 only) 19 different encoder counts, from 125 to 4096 counts/revolution,
are available. Differential line-driver output devices sink and
source 40mA.
• Tachometer output: DC output proportional to motor RPM.
(8130 & 8230 only)
• Fault input/output: Open-collector output goes low in the event of a fault. This input
is configured so that externally forcing this output low will inhibit
the amplifier. This allows all fault outputs in a multi-axis system
to be connected together (wire-ORed) to shut down all amplifiers
should any amplifier have a fault.
• Manual and external Push button and a separate input is provided to reset the
fault reset: amplifier after a fault.
• High-Speed Electronic Instantly shuts down the amplifier in the event of a short across
Circuit Breaker the motor leads or a ground fault condition.
(HS/ECB): (i.e. amplifier exceeds 100A for 10 microseconds)
• Low-Speed Electronic Shuts down the amplifier if the amplifier is operated above the
Circuit Breaker maximum continuous current rating for a pre-determined
(LS/ECB): period(i.e. 3 seconds).
• Over/under voltage These circuits constantly monitor the amplifier power-supply
and over temperature: voltages, and the motor and amplifier-heatsink temperatures.
They will shut down the amplifier in the event of any out-of-
specification condition.
CHAPTER 1: DESCRIPTION, FEATURES AND SPECIFICATIONS

SMA8130, SMA8230, and SMA8330
10
Glentek Inc., 208 Standard Street, El Segundo, California 90245, U.S.A. (310) 322-3026
1.3 Specifications:
This section contains the specifications for the brushless trapezoidal, sine/resolver and
two or three phase input current mode D.C. Servo Amplifiers.
NOTE: All data in this section is based on the following ambient conditions: 120oF (50oC)
maximum. Forced air cooling.
1.3.1 Amplifier Module (SMA8X30-1A-1):
The amplifier module includes an integral DC power supply which includes a bridge
rectifier, buss capacitors, in rush current protection, cooling fans and a shunt regulator.
Forced air cooling is required to meet the maximum power ratings specified below.
1.3.1.1 Input and Output Power:
Input Power/
Buss Voltage(B+) Output Power
(current)
CONTINUOUS PEAK
120VAC/170VDC 30A 60A
240VAC/340VDC 30A 60A
Amplifier
Model Signal Input Maximum
Voltage
(VDC)
Minimum
Impedance
W
Velocity Gain
Amp./Volt Current Gain
Amp./Volt
8130/8230 Differential ±13 10,000 15,000(min.) 0-5
8130/8230 Single-ended ±10 10,000 15,000(min.) 0-5
8330 2/3 phase input ±13 10,000 0-5
1.3.1.2 Signal Inputs:
1.3.1.3 Digital Inputs:
• ±Limit, Inhibit & Reset: 40/-0.5V max. Terminated by 10,000W.
• Fault (as input): 40/-0.5V max. Terminated by 10,000W.
• Typical for all digital inputs: Digital inputs have hysteresis with thresholds at 1/3 and
2/3 of +5V or +15V depending on range select jumper.
CHAPTER 1: DESCRIPTION, FEATURES AND SPECIFICATIONS

SMA8130, SMA8230, and SMA8330
11
Glentek Inc., 208 Standard Street, El Segundo, California 90245, U.S.A. (310) 322-3026
1.3.1.4 System:
• Drift offset over temperature reference to input: 0.01mV/ oC max.
• Frequency response (Velocity loop): 750Hz min.
• Frequency response (Current loop): 2KHz min.
• Dead band: None
• Form factor: 1.01
1.3.1.5 Outputs:
• Fault (as output): Active low. Open-collector output can sink 500mA max.
• Abs. motor current: 10A/V.
• Tachometer : 1000Wsource impedance, a high input impedance meter must
be used (1MW/volt). Maximum Tachometer output voltage for
12 bit = 0.5V/KRPM, 14 bit = 2V/KRPM.
• Encoder outputs: Standard TTL levels with 20mA sink or source capability.
(8230 only)
1.3.2 Mechanical:
Model L x W x H
(inches) Weight
(lbs)
SMA8X30-1A-1(Amplifier Module) 4.25 x 8.81 x 14.50 15.00
CHAPTER 1: DESCRIPTION, FEATURES AND SPECIFICATIONS

SMA8130, SMA8230, and SMA8330
12
Glentek Inc., 208 Standard Street, El Segundo, California 90245, U.S.A. (310) 322-3026
Figure 2.1
Pulse Width Modulation Waveform
CHAPTER 2: THEORY OF OPERATION
Chapter Two: Theory of Operation
2.1 Introduction:
This chapter contains the basic control theory of how brush-type and brushless servo
motors and amplifiers operate. It also compares and contrasts the advantages and
disadvantages of brushless and brush type motors and amplifiers to help you select which is
best suited for your application. The following is a summary of the topics:
• The theory behind an amplifer driving DC servo-motors.
• A comparison between brush-type and brushless motors.
• A comparison between trapezoidal mode and sinusoidal mode amplifier system.
• The advantages and disadvantages of trapezoidal mode amplifier systems.
• A comparasion between velocity mode and current mode.
• Various kinds of velocity feedback.
• Commutation using resolver.
• Current mode in sine/resolver or trapezoidal amplifier vs two/three phase input current
amplifier.
• Protection circuits.
2.2 Driving DC Servo-Motors:
The torque of any DC motor is proportional to motor current: the stronger the magnetic
field, the stronger the pull. Motor current may be controlled in two ways: linear and PWM
(Pulse-Width Modulation). Linear control is achieved by simply inserting a resistance in
series with the motor. This resistance is usually a partially turned-on transistor. The
transistor is said to be in its "linear" region. Linear amplifiers are simple, accurate, and
effective. However, they are very inefficient and they generate a lot of heat. Linear amplifiers
are used when low electrical noise, high bandwidths (2KHz or higher) and or low inductance
(less than 1mH) motors are used. In pulse-width modulation the control devices (output
transistors) are rapidly turned full-on and full-off. The ratio of the on-time (the pulse width)
and off-time determines the average motor current. Refer to figure 2.1. For example: if the
output is on 25% of the time and off 75% of the time, the average motor current is
approximately 25% of maximum.
A coil of wire, such as the windings of a motor, forms an inductor. Inductors resist
changes in current. This resistance to change, known as reactance, acts to dampen or
average the high-current spikes that would otherwise occur when the output devices are on.
In fact, if motor inductance is low, external inductors may have to be added in series with
each motor lead to ensure proper operation.
A brush-type motor may be run from a steady DC voltage since the brushes and
commutator switch the current from winding to winding. However, a brushless motor requires
that the voltage be switched from winding to winding externally; the voltage that drives a
brushless motor is a constantly changing AC waveform. Section 2.5 dicusses these
waveforms.

SMA8130, SMA8230, and SMA8330
13
Glentek Inc., 208 Standard Street, El Segundo, California 90245, U.S.A. (310) 322-3026
2.3 Servo Loops:
A basic velocity-mode servo-loop for a brush-type motor is shown in figure 2.2a. An
external controller commands a given velocity (RPM). The velocity-loop summing-amplifier
compares this command with the actual motor velocity, supplied by a DC tachometer on the
motor shaft, and produces an error voltage proportional to the difference between the actual
and commanded velocity.
The velocity error is used to command motor current in the inner servo-loop. The current-
loop summing-amplifier compares the command current (velocity error) with the actual
current in the motor and produces an error voltage proportional to the difference between the
actual and commanded current.
Finally, the current-error signal is used to produce an output (linear or PWM) to drive the
motor.
The velocity loop may be bypassed, and an external current command fed directly to the
current loop. In this case, the external command signal controls the torque of the motor,
rather than the velocity. This is known as current-mode operation.
The servo-loops of a brushless amplifier (figure 2.2b) operate in much the same way, except
there are now three current loops, one for each phase of the motor.
Figure 2.2a
Velocity-mode sevo loop for a brush-type motor
Figure 2.2b
Velocity-mode sevo loop for a brushless motor
CHAPTER 2: THEORY OF OPERATION

SMA8130, SMA8230, and SMA8330
14
Glentek Inc., 208 Standard Street, El Segundo, California 90245, U.S.A. (310) 322-3026
Figure 2.3
Brush-type and Brushless-type Motors
2.4 Brushed Motors vs Brushless Motors:
There are two basic types of motor design that are used for high-performance motion
control systems: brush-type PM (permanent magnet), and brushless-type PM. As you can
see in figure 2.3, a brush-type motor has windings on the rotor (shaft) and magnets in the
stator (frame). In a brushless-type motor, the magnets are on the rotor and the windings are
in the stator.
To produce optimal torque in a motor, it is necessary to direct the flow of current to the
appropriate windings with respect to the magnetic fields of the permanent magnets. In a
brush-type motor, this is accomplished by using a commutator and brushes. The brushes,
which are mounted in the stator, are connected to the motor wires, and the commutator
contacts, which are mounted on the rotor, are connected to the windings. As the rotor turns,
the brushes switch the current flow to the windings which are optimally oriented with respect
to the magnetic field, which in turn produces maximum torque.
In a brushless motor there is no commutator to direct the current flow through the
windings. Instead, an encoder, hall sensors or a resolver on the motor shaft senses the rotor
position (and thus the magnet orientation). The position data is fed to the amplifier which in
turn commutates the motor electronically by directing the current through the appropriate
windings to produce maximum torque. The effect is analogous to a string of sequencing
Christmas lights: the lights seem to chase each other around the string. In this case, the
magnets on the rotor "chase" the magnetic fields of the windings as the fields "move" around
the stator.
The relative advantages and/or disadvantages of a brush-type motor/amplifier
combination vs. a brushless motor/amplifier combination can be significant. On the next page
is a summary of advantages and disadvantages of brush type motor/amplifiers and brushless
type motor/amplifiers to help you decide which type to select for your applications.
CHAPTER 2: THEORY OF OPERATION

SMA8130, SMA8230, and SMA8330
15
Glentek Inc., 208 Standard Street, El Segundo, California 90245, U.S.A. (310) 322-3026
Brushless Motors/Amplifiers Brushed Motors/Amplifiers
Advantages Disadvantages
No scheduled maintenance and no brush dust
is generated. Motor brushes must be checked periodically for
wear and excess brush dust.
Higher RPM limits. Approximately 3000RPM maximum.
Lower inertia/torque ratio. Higher inertia to torque ratio.
Dissipates heat more efficiently due to windings
being located in stator. Not as efficient at dissipating heat. Heat is
trapped at rotor and shortens bearing life.
Safer for explosive atmospheres. Quieter and
less electrical noise generated. Brushes spark and generate electrical and
audible noise.
Disadvantages Advantages
Amplifiers are complicated and expensive. Amplifiers are simpler and less expensive.
Higher torque ripple. Lower torque ripple.
No Industry standard packaging. Industry standard packaging.
2.5 Sinusoidal vs Trapezoidal:
Figure 2.4 shows the two most common waveforms used to drive a brushless motor.
Note that in each case, there are actually three different waveforms. Each waveform drives
a motor winding and is 120 o out-of-phase with the other two. Again, the waveform may be
generated from a DC source by linear or PWM techniques.
The first waveform is known as trapezoidal or six-step since the voltage is literally
stepped from winding to winding (like the Christmas-light analogy). This is the simplest and
least expensive method of driving a brushless motor. Its principal disadvantage is that the
large current steps produce high torque ripple. (Torque ripple is a repetitive fluctuation in
torque as the motor turns and is independent of load.) The SMA8130 trapezoidal mode
amplifier produces a trapezoidal output.
The second waveform is known as sinusoidal. To minimize torque ripple, the motor
current needs to be constantly varied according to the orientation of the magnets and
windings. As it happens, this is a sine function. In fact, a sine wave is defined as a rotating
radius (like a motor shaft) revolving through time (see figure 2.4). A sine wave is the most
natural way to drive a motor and produces the minimum torque ripple. The SMA8230
sine/resolver mode amplifier produces a sinusoidal output.
Figure 2.4
Trapezoidal and sinusoidal waveform used to drive brushless motor.
CHAPTER 2: THEORY OF OPERATION

SMA8130, SMA8230, and SMA8330
16
Glentek Inc., 208 Standard Street, El Segundo, California 90245, U.S.A. (310) 322-3026
2.6 The Advantages and Disadvantages of a Trapezoidal Amplifier
System:
A trapezoidal motor has three stator windings and together with the rotor magnets are
designed so that the magnetic flux coupling between them produce a constant torque. The
torque of the motor is proportional to the three stator phase currents which are 120 o
out-of-phase to the other two. Shaft position sensors are required to provide the
commutation signals to commutate the motor. The two most common sensor types are
Hall-effect sensors and an optical encoder with commutation tracks.
A common class of applications for trapezoidal amplifiers is for motor speed control.
Classically, this is implemented by adding a brushless DC tachometer to the motor shaft and
driving the motor through a velocity controlled servo loop. A high performance velocity loop
can be implemented in this manner.
Another way of implementing the motor speed control is by using a simulated digital
tachometer synthesized by the motor’s commutation signals. The commutation signals are
used to trigger a one shot signal at every transition of the commutation signals. After
smoothing, a voltage proportional to velocity (RPM) is obtained.
Two additional system features were implemented in the synthesized tachometer design:
1 At 100% of full RPM, the PSEUDO-TACH voltage is limited by the power supply
voltage. If an RPM is commanded above 100% RPM, the servo will run away. To prevent
this from occuring, the absolute value of the PSEUDO-TACH signal is compared to a 95% of
full RPM reference. If the PSEUDO-TACH signal exceeds this value, an over speed latch is
set and the servo is disabled.
2 The PSEUDO-TACH one shot pulse is buffered and brought to the control interface.
The controller can use this signal to determine the exact velocity (RPM) of the motor.
The SMA8130 is a trapezoidal brushless amplifier which contains the necessary
electronics for motor commutation and also has the PSEUDO-TACH option for better speed
control.
2.7 Current Mode vs Velocity Mode:
The fundamental difference between current mode and velocity mode is that in current
mode, an external command signal controls the torque of the motor, rather than the velocity.
In velocity mode, an external command signal controls the velocity (RPM) of the motor, rather
than the torque. In a current mode amplifier, the command signal is proportional to the motor
current, thus it is also proportional to the torque of the motor. In a velocity mode amplifier, the
current loop amplifier stage is preceded by a high gain error amplifier which compares the
command signal and the tachometer feedback signal.
Current mode amplifiers are usually used in Position Control Systems where no
tachometer feedback is required. While velocity mode amplifiers are usually used in Classic
Cascaded Contol Systems where there are position, velocity and current loops in the system.
Velocity loops tend to have a higher bandwidth and operate better near zero speed.
CHAPTER 2: THEORY OF OPERATION

SMA8130, SMA8230, and SMA8330
17
Glentek Inc., 208 Standard Street, El Segundo, California 90245, U.S.A. (310) 322-3026
2.8 Tachometer (Velocity Mode) Feedback Options:
The following is a list of ways one can choose to implement tachometer feedback in order
to drive the motor through a velocity controlled servo loop:
• Brush-type and brushless DC mechanical tachometer.
• Simulated tachometer using the motor commutation signals (PSEUDO-TACH).
• Sinusoidal resolver.
• Simulated tachometer using the encoder signals.
The simplest way to simulate the actual velocity of the motor is by installing a mechanical
brush-type or brushless DC tachometer on the motor shaft which converts the velocity of the
motor into DC voltage.
The second method is to synthesize a digital tachometer using the motor commutation
signals (refer to section 2.6). The SMA8130 provides this option.
In the third method, with a sine/resolver amplifier (SMA8230) an analog tachometer signal
is generated as part of the Resolver-to-Digital conversion process and is immediately available
for use thru the dip-switch options for velocity mode(S1-7).
The fourth method is to have an optical encoder installed on the motor shaft to determine
the direction and position of the motor as it runs. The incoming encoder signals are converted
into quadrature clock pulses. The frequency of this clock pulses changes with the velocity of
the motor and the up/down clock output signals change with the direction of which the motor is
running at. The frequency of the clock is then converted into the tach DC voltage signal using
the Frequency-to-Voltage converter.
2.9 Commutation Using A Resolver:
The Resolver-to-Digital converter in the SMA8230 generates the necessary excitation for
the resolver, and converts the resolver’s sine and cosine signals into position data. This
position information is used to amplitude modulate the velocity error signal into three-phase,
sinusoidal and current-error signals like the one in section 2.5.
2.10 Current Mode in Sine/Resolver or Trapezoidal Amplifier vs Two/Three
Phase Input Current Mode Amplifier:
The fundamental difference between the current mode in sine/resolver or trapezoidal
amplifiers and the two or three phase input current mode amplifiers is that in the former case,
the commutation of the command and feedback signals is done within the amplifier itself. The
latter case accepts two or three 120 o out of phase commutated drive signals. In other words,
the user’s controller has to do the commutation of the command and feedback signals
themselves. The user can either input two or three commutated drive signals. If the user has
chosen two phase input, the third phase is generated as the negative sum of the other two
inputs.
2.11 Protection Circuit:
The High- and Low-Speed Electronic Circuit Breakers(HS/ECB and LS/ECB) protect the
amplifier and motor from being damaged by high motor current(specified max. peak and rms
current values). The Over Temperature and Over Voltage detection circuits will shut off the
amplifier when the temperature of the amplifier or the buss(B+) voltage exceeds a specified
limit. Also, there are circuits which limit the motor from running in either or both directions.
CHAPTER 2: THEORY OF OPERATION

SMA8130, SMA8230, and SMA8330
18
Glentek Inc., 208 Standard Street, El Segundo, California 90245, U.S.A. (310) 322-3026
Chapter Three: Model Numbering
3.1 Introduction:
This chapter contains the model numbering system for the SMA8130, SMA8230 and
SMA8330 amplifier module applications. The model numbering system is designed so that
you, our customer will be able to create the correct model number of the product that you
need as quick and as accurate as possible.
3.2 Amplifier Module:
3.2.1 Trapezoidal Mode:
SMA8130 - YYYY - QQQ - 1A - 1 - ZZ
Amplifier Model Number Power Supply
00 = 110-130VAC
Optional Custom 01 = 208-240VAC
Configuration Code 02 = SPECIAL
(A numerical code will be
assigned by Glentek to amplifiers
Pre-amp Configuration Code whose specifications vary from
the standard configuration.)
Pre-amp Configuration Code
Differential or Single-ended input:
0 = Single-ended; (Default)
1 = Differential;
Velocity or Current Mode:
0=Velocity; 1=Current;
(see section 2.7)
Sensor Select:
0 = Off = 120o/240o; (Default)
1 = On = 60o/300o;
(see 5.3.2,5.3.4)
Motor Reverse:
0 = Off; (Default)
1 = On;
(see 5.3.2, 5.3.5)
±Limit 0=L, 1=H see sect.5.2
±Limit 0=U, 1=D see sect.5.2
Inhibit 0=L, 1=H see sect.5.2
Inhibit 0=U, 1=D see sect.5.2
Reset 0=L, 1=H see sect.5.2
Reset 0=U, 1=D see sect.5.2
On Board Power Supply,
+15V/+5V on pull-up:
0 = +15V; (Default)
1 = +5V
Motor Temperature:
(see section 5.2)
0=Type A; (Default)
1=Type C
¤¤ See section 5.2 ¤¤
Type A: U=0 & L=0
(Default)
Type B: D=1 & H=1
Type C: U=0 & H=1
Type D: D=1 & L=0
4 Bit Binary-to-
Digital Conversion
0000=0 1000=8
0001=1 1001=9
0010=2 1010=A
0011=3 1011=B
0100=4 1100=C
0101=5 1101=D
0110=6 1110=E
0111=7 1111=F
DC Buss Voltage
0 = 120 - 170 Vdc
1 = 170 - 340 Vdc
2 = Special
CHAPTER 3: MODEL NUMBERING

SMA8130, SMA8230, and SMA8330
19
Glentek Inc., 208 Standard Street, El Segundo, California 90245, U.S.A. (310) 322-3026
PLD Device
Code
(See 5.4.3)
Encoder Resolution
(See section 5.4.3)
0 0 0 ¡¡ 256 250 128 125
0 0 1 ¡¡ 1024 1000 512 500
0 1 0 ¡¡ 4096 4000 2048 2000
0 1 1 ¡¡ 3600 2160 720 360
1 0 0 ¡¡ NA NA NA 625
1 0 1 ¡¡ NA NA NA 1250
1 1 0 ¡¡ NA NA NA 2500
1 1 1 ¡¡ NA NA NA Special
¤¤ ¤¤ ¤¤ ¤¤
S1-1¡¡0 0 1 1
S1-2¡¡0 1 0 1
3.2.2 Sine/Resolver Mode:
Bit Resolution
(See 5.4.3)
0 0 ¡¡ 10 Bit
0 1 ¡¡ 12 Bit
1 0 ¡¡ 14 Bit
SMA8230 - YYYYYYY - QQQ - 1A - 1 - ZZ
Amplifier Model Number Power Supply
00 = 110-130VAC
Optional Custom 01 = 208-240VAC
Configuration Code 02 = SPECIAL
(A numerical code will be assigned by
Pre-amp Configuration Code Glentek to amplifiers whose specifications
vary from the standard configuration.)
Pre-amp Configuration Code
±Limit 0=L,1=H
±Limit 0=U, 1=D
Inhibit 0=L, 1=H
Inhibit 0=U, 1=D
Reset 0=L, 1=H
Reset 0=U, 1=D
+15V/+5V on pull-up:
0=15V,(Default); 1=5V
Motor Temperature:
0=Type A; (Default)
1=Type C
Diff./Single-ended input:
0=Single; (Default)
1=Differential
Velocity or Current Mode:
0=Velocity; 1=Current
see section 2.7.
Motor Reverse:
0=OFF, (Default); 1=ON
see section 5.3.5.
Tach Reverse
1=ON, (Default); 0=OFF
see section 5.3.7.
0
4 BIT Binary-to-
digital Conversion
0000=0 1000=8
0001=1 1001=9
0010=2 1010=A
0011=3 1011=B
0100=4 1100=C
0101=5 1101=D
0110=6 1110=E
0111=7 1111=F
Type A: U=0 & L=0 (Default)
Type B: D=1 & H=1
Type C: U=0 & H=1
Type D: D=1 & L=0
£See section 5.2 £
DC Buss Voltage
0=120 - 170 Vdc
1=170 - 340 Vdc
2=Special
Number of
Motor Poles S3-1 S3-2 S3-3 S3-4
See section 5.4.4
2 1 1 1 1
4 1 1 1 0
6 1 1 0 1
8 1 1 0 0
10 1 0 1 1
12 1 0 1 0
CHAPTER 3: MODEL NUMBERING

SMA8130, SMA8230, and SMA8330
20
Glentek Inc., 208 Standard Street, El Segundo, California 90245, U.S.A. (310) 322-3026
3.2.3 Two/Three Phase Input Current Mode:
SMA8330 - YYY - QQQ - 1A - 1 - ZZ
Amplifier Model Number Power Supply
00 = 110-130VAC
Optional Custom 01 = 208-240VAC
Configuration Code 02 = SPECIAL
(A numerical code will be assigned
by Glentek to amplifiers whose
Pre-amp Configuration Code specifications vary from the standard
configuration.)
Pre-amp Configuration Code
2/3 Phase Input Current:
0 = 2 Phase; (Default)
1 = 3 Phase;
see section 2.9.
Inhibit 0=L, 1=H
see section 5.2.
Inhibit 0=U, 1=D
see section 5.2.
Reset 0=L, 1=H
see section 5.2.
Reset 0=U, 1=D
see section 5.2.
On Board Power Supply
+15V/+5V on pull-up:
0 = +15V; (Default)
1 = +5V
see section 5.2.
Motor Temperature:
0 = Type A; (Default)
1 = Type C
see section 5.2.
4 Bit Binary-to-
digital Conversion
0000=0 1000=8
0001=1 1001=9
0010=2 1010=A
0011=3 1011=B
0100=4 1100=C
0101=5 1101=D
0110=6 1110=E
0111=7 1111=F
0
Type A: U=0 & L=0
Default
Type B: D=1 & H=1
Type C: U=0 & H=1
Type D: D=1 & L=0
£See section 5.2 £
DC Buss Voltage
0 = 120 - 170 Vdc
1 = 170 - 340 Vdc
2 = Special
CHAPTER 3: MODEL NUMBERING
This manual suits for next models
2
Table of contents
Other Glentek Amplifier manuals
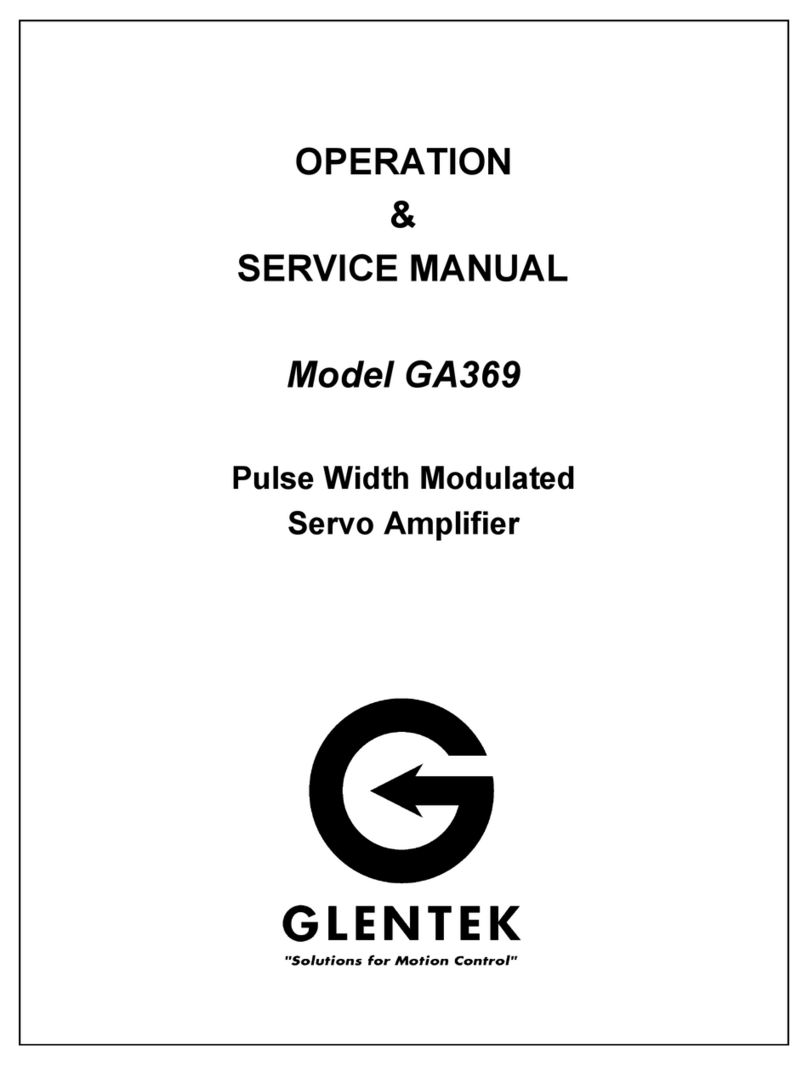
Glentek
Glentek GA369 Installation and operating instructions
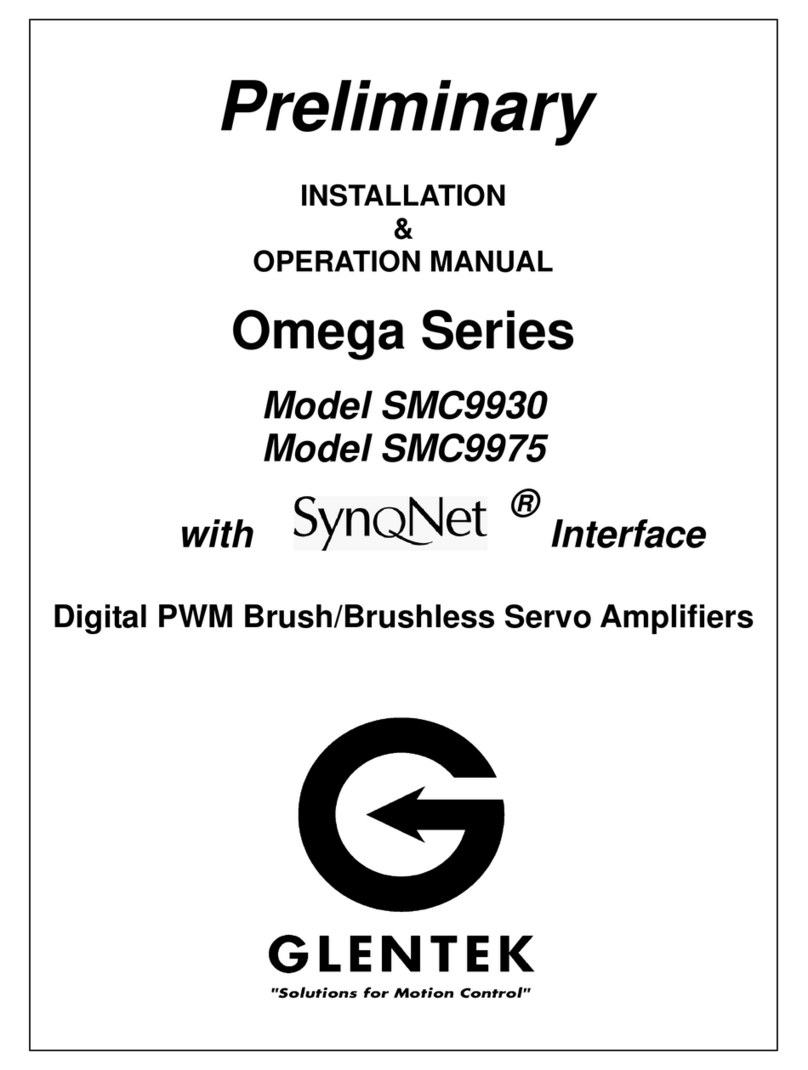
Glentek
Glentek Omega SMC9930 User manual
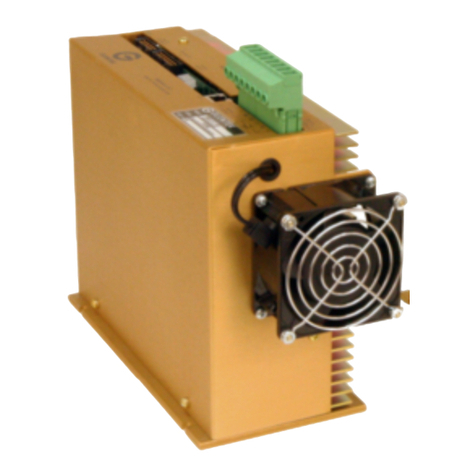
Glentek
Glentek Alpha Series User manual
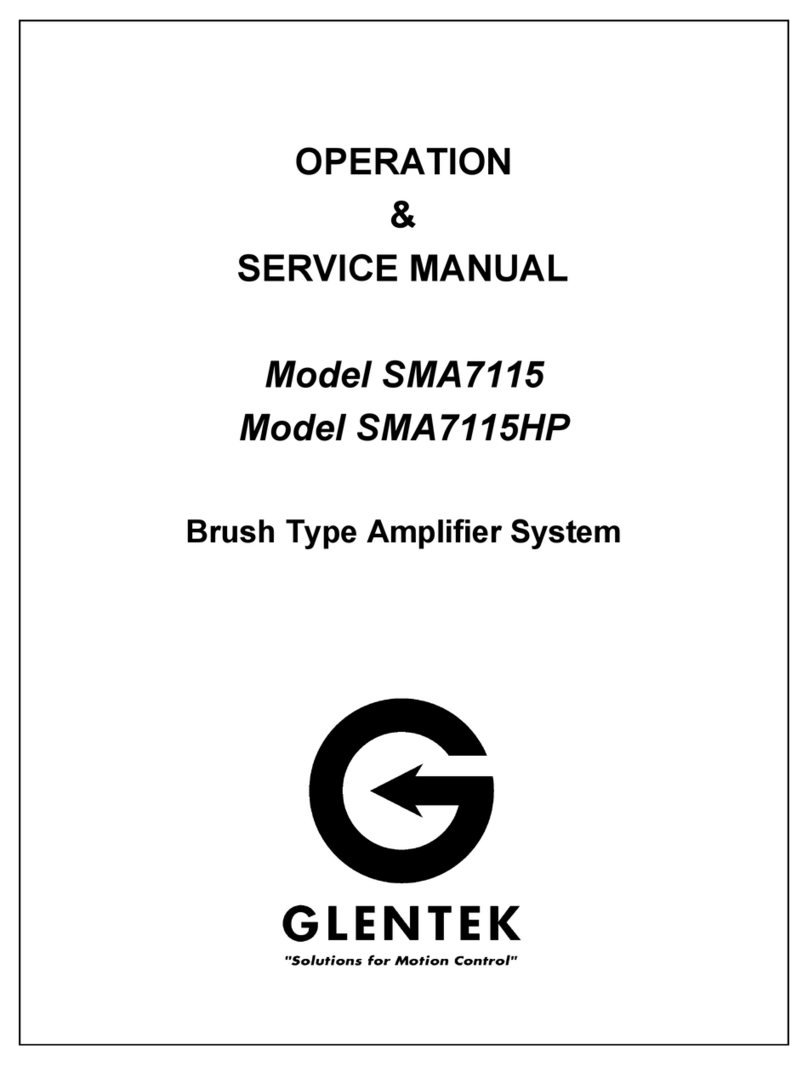
Glentek
Glentek SMA7115HP Installation and operating instructions
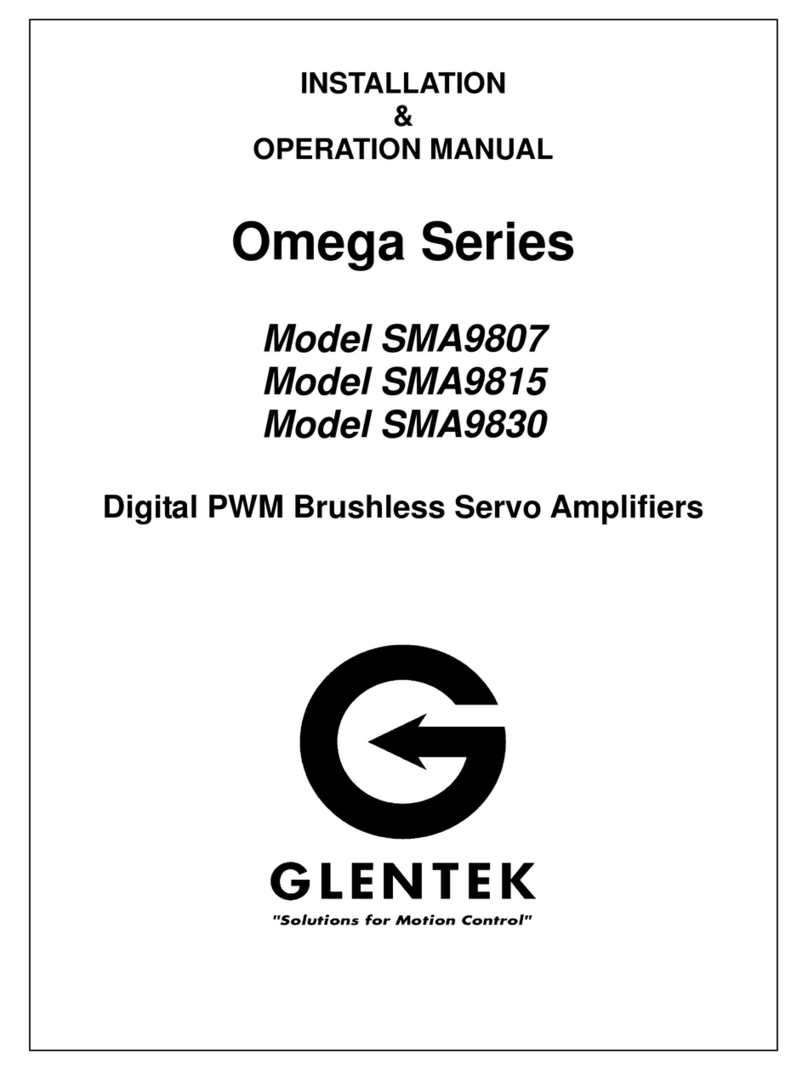
Glentek
Glentek Omega Series User manual
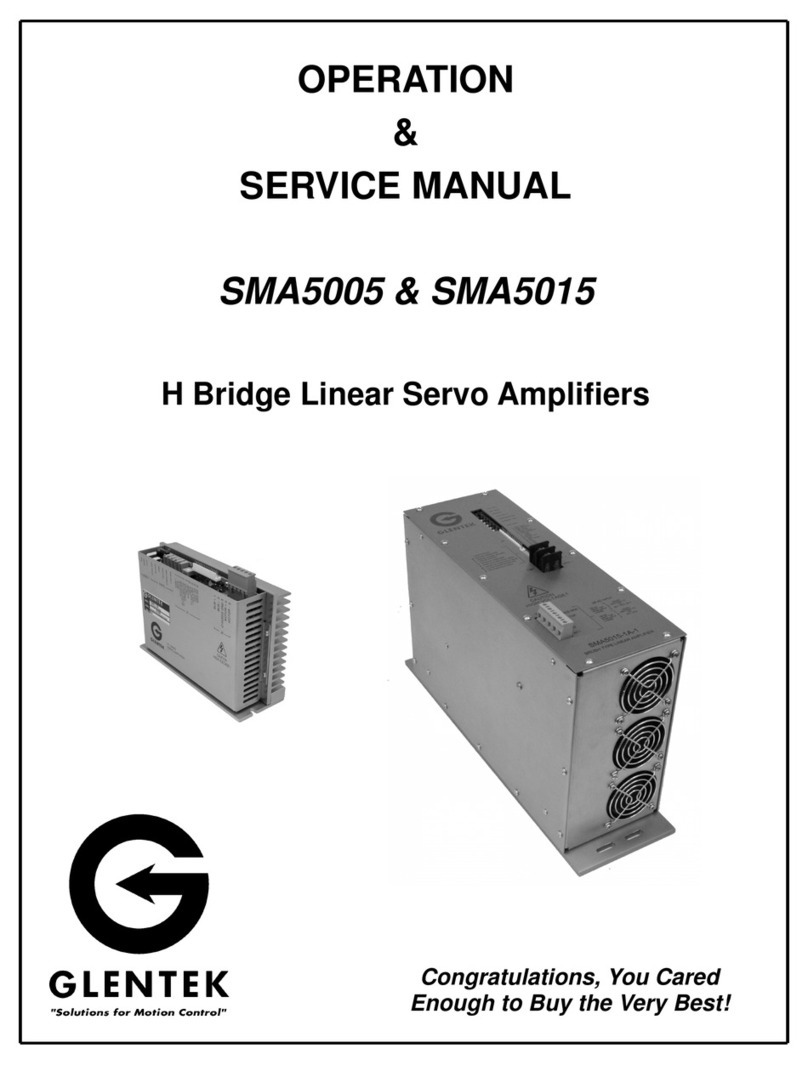
Glentek
Glentek SMA5005 Installation and operating instructions
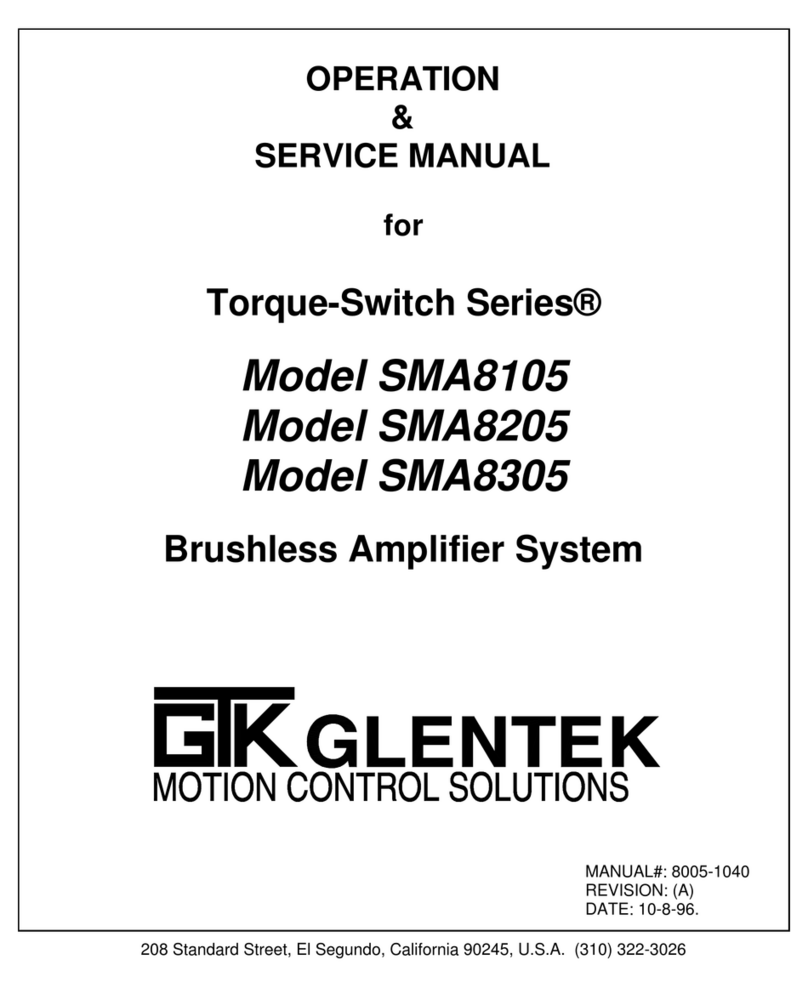
Glentek
Glentek SMA8105 Installation and operating instructions
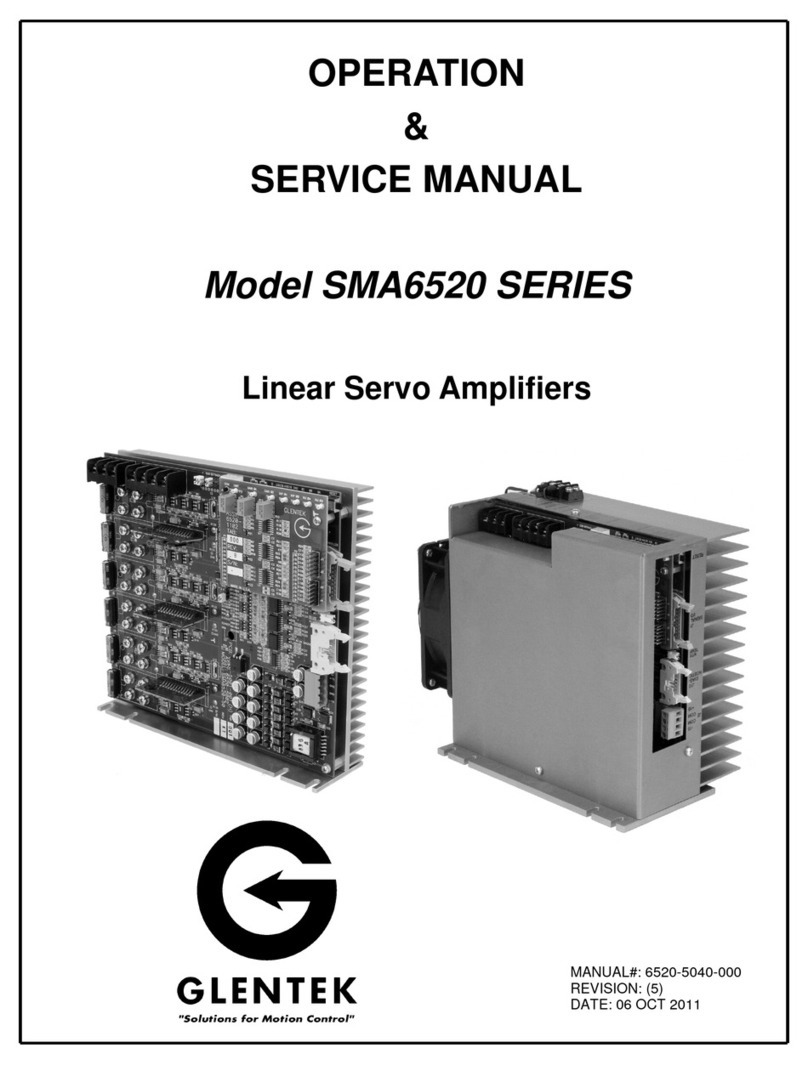
Glentek
Glentek SMA6520 SERIES Installation and operating instructions
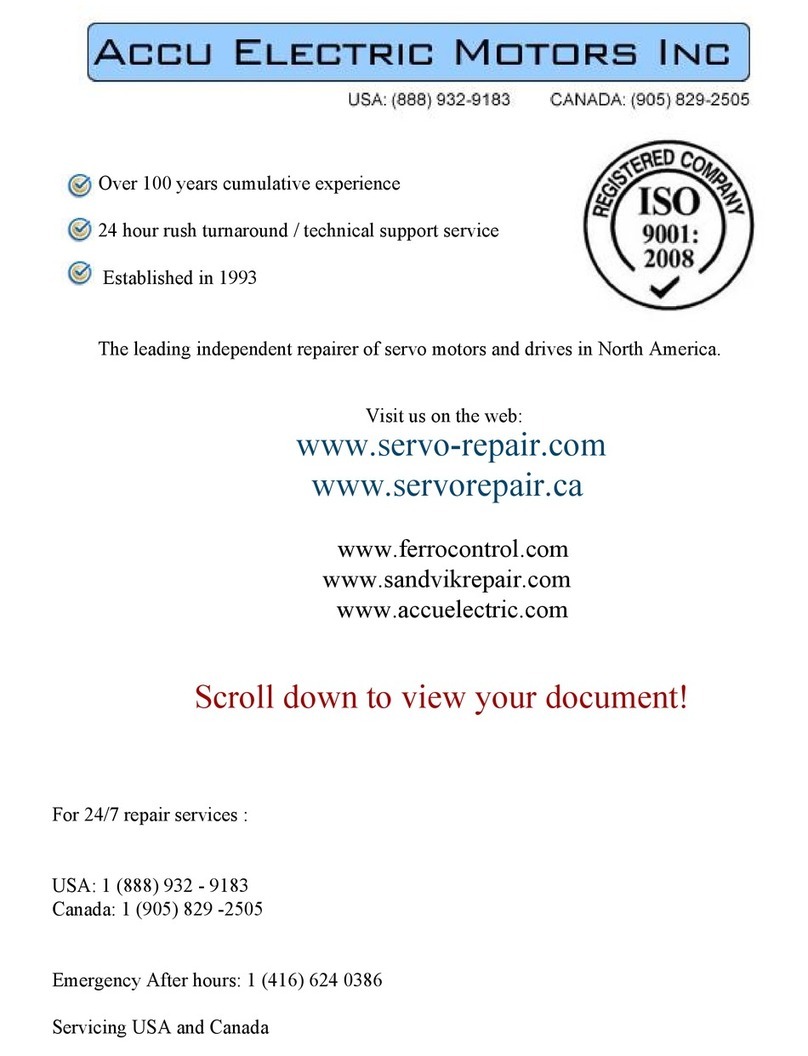
Glentek
Glentek SMA7105 Installation and operating instructions
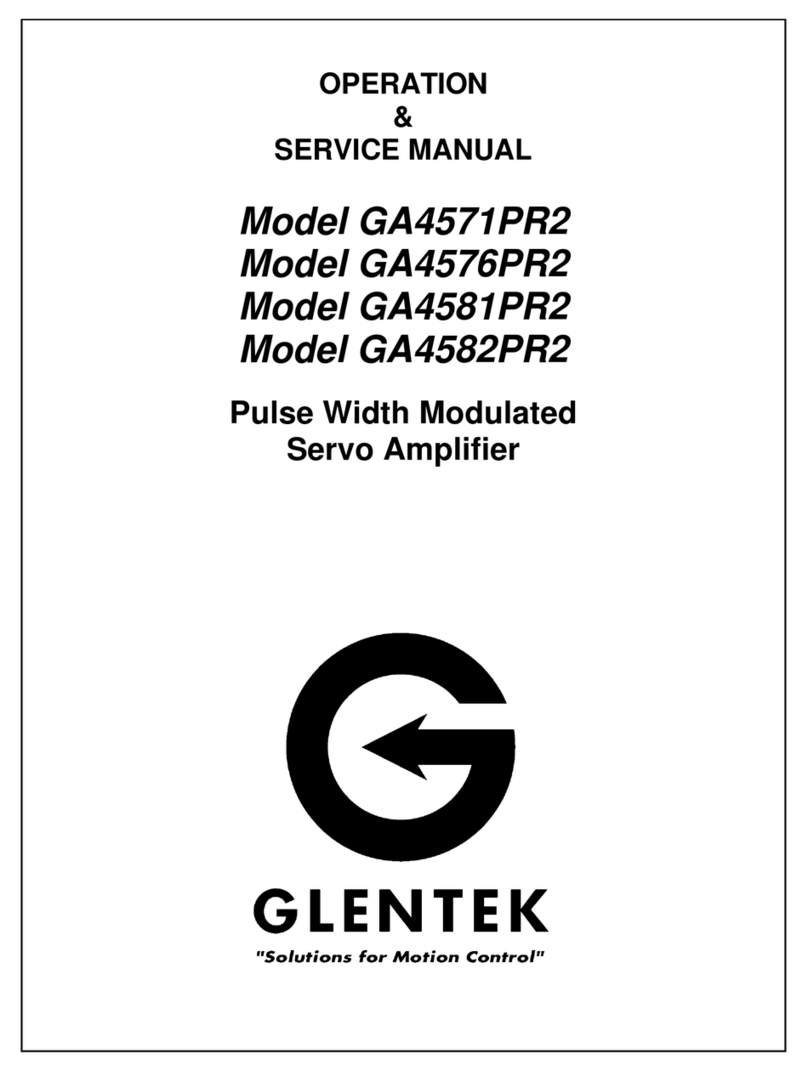
Glentek
Glentek GA4571PR2 Installation and operating instructions