Glentek SMA7130 Installation and operating instructions

OPERATION
&
SERVICE MANUAL
Model SMA7130
Model SMA71075
Model SMA71100
Brush Type Amplifier System

Glentek Inc. 208 Standard Street, El Segundo, California 90245, U.S.A. (310) 322
-
3026
2
SMA7130, SMA71075 and SMA71100 MANUAL
Table of Contents
Page
Introduction.............................................................................................................................5
Chapter One: Description, Features and Specifications
1.1 Description.................................................................................................................6
1.2 Features.....................................................................................................................7
1.2.1 Stand Alone One Axis Amplifier (SMA7130, SMA71075 and SMA71100)...........7
1.3 Specifications.............................................................................................................8
1.3.1 Stand Alone Amplifier (SMA7130, SMA71075 and SMA71100)..........................8
1.3.1.1 Input and Output Power...............................................................................8
1.3.1.2 Signal Inputs ...............................................................................................8
1.3.1.3 Digital Inputs ...............................................................................................8
1.3.1.4 System........................................................................................................8
1.3.1.5 Outputs.......................................................................................................8
1.3.3.6Mechanical..................................................................................................8
Chapter Two: Theory of Operation
2.1 Introduction................................................................................................................9
2.2 Driving DC Servo Motors............................................................................................9
2.3 Servo Loops...............................................................................................................10
2.4 Brushed Motors vs Brushless Motors .........................................................................11-12
2.5 Operation of Output Switching Transistors..................................................................12
2.6 “ H ” Type Output Bridge Configuration.......................................................................12
2.7 Pulse-Width-Modulation (PWM)..................................................................................13-14
2.8 Current-Loop Operation..............................................................................................14
2.9 Velocity-Loop Operation.............................................................................................14
2.10 Protection Circuits.....................................................................................................14
Chapter Three: Model Numbering
3.1 Introduction.................................................................................................................15
3.2 Stand Alone Amplifier .................................................................................................15
Chapter Four: Installation
4.1 Introduction.................................................................................................................16
4.2 Mounting ....................................................................................................................16

Glentek Inc. 208 Standard Street, El Segundo, California 90245, U.S.A. (310) 322
-
3026
3
SMA7130, SMA71075 and SMA71100 MANUAL
4.3 Wiring.........................................................................................................................16-18
4.3.1 RFI/EMI and Wiring Technique..........................................................................16
4.3.2 Wire Size and Type...........................................................................................17
4.3.3 Connector Size and Type ..................................................................................17
4.3.3.1 The Power and Motor Connector of the SMA7130....................................17
4.3.3.2 The Power and Motor Connector of the SMA71075 and SMA71100 .........17
4.3.3.3 The Signal Connectors.............................................................................17
4.3.4 Amplifier Module Connections ...........................................................................18
4.3.4.1 The Power Connections for the SMA7130(TB1)........................................18
4.3.4.2The Power Connections for the SMA71075 and SMA71100......................18
4.3.4.3The Signal Connections (J1).....................................................................19
4.3.4.4The Encoder Input Connections (Factory Option) (J4)...............................19
Chapter Five: Configuration
5.1 Introduction.................................................................................................................20
5.2 Logic Input Configuration............................................................................................20
5.3Amplifier Configuration................................................................................................20
5.3.1 +15V/+5 Logic Level Configuration ....................................................................20
5.3.2 Velocity Mode and Current Mode Configuration.................................................20
5.3.3 Tach Lead.........................................................................................................20
5.3.4Tach Reverse (Encoder input option only) .........................................................20
5.3.5Encoder Reverse (Encoder input option only) ....................................................21
5.3.6Motor Reverse...................................................................................................21
5.3.7Coarse Balance.................................................................................................21
5.3.8Encoder Derived Tachometer Optimization (Encoder input option only) .............21
5.3.9Tach Pulse Width Table (Encoder input option only)..........................................21
Chapter Six: Start Up and Calibration
6.1 Introduction.................................................................................................................22
6.2 Initial Start Up.............................................................................................................22
6.3 Calibration of the Velocity Mode Amplifier...................................................................22-23
6.4 Calibration of the Current Mode Amplifier....................................................................24
6.5 Calibration Setup Record............................................................................................25
Chapter Seven: Maintenance, Repair, and Warranty
7.1 Maintenance...............................................................................................................26
7.2 Amplifier Faults...........................................................................................................26-27
7.2.1 Table of Fault LED Conditions........................................................................26
7.2.2High Speed Electronic Circuit Breaker (HS/ECB) Fault...................................27
7.2.3Low Speed Electronic Circuit Breaker (LS/ECB) Fault.....................................27
7.2.4Amplifier Over Temp Fault..............................................................................27
7.2.5Over Voltage Fault .........................................................................................27
7.2.6Resetting A Fault............................................................................................27
7.3 Amplifier Failure..........................................................................................................27
7.4 Factory Repair............................................................................................................28
7.5 Warranty.....................................................................................................................28

Glentek Inc. 208 Standard Street, El Segundo, California 90245, U.S.A. (310) 322
-
3026
4
SMA7130, SMA71075 and SMA71100 MANUAL
Appendix A: Amplifier Drawings
SMA7130 Installation Drawings (7030-1030)....................................................................30-31
SMA7130 Assembly Drawings (7030-1002)......................................................................32-33
SMA71075 Installation Drawing (7075-3030)....................................................................34
SMA71100 Installation Drawing (7075-3035)....................................................................35
SMA71075 & SMA71100 Installation Schematic (7075-3031)...........................................36
SMA71075 & SMA71100 Assembly Drawing (7075-3002)................................................37
Appendix B: Personality Module (Pre-Amp)
Standard -Tachometer Feedback Installation Drawing (8000-2402-002)...........................39
Standard -Tachometer Feedback Installation Schematic (8000-2435-002).......................40
Optional -Encoder Feedback Installation Drawing (8000-2402-003) .................................41
Optional -Encoder Feedback Installation Schematic (8000-2435-003)..............................42
Appendix C: European Union EMC Directives
Electromagnetic Compatibility Guidelines for Machine Design...........................................44-50

Glentek Inc. 208 Standard Street, El Segundo, California 90245, U.S.A. (310) 322
-
3026
5
SMA7130, SMA71075 and SMA71100 MANUAL
Introduction
Glentek's brush type and brushless DC servo motors and amplifiers offer the ultimate in low maintenance and
high performance motion control. Glentek offers a full line of matched motors and amplifiers to meet virtually every
motion control application.
This manual provides all the technical information necessary to install, configure, operate, and maintain our
TORQUE-SWITCH™ series, brush type servo amplifiers, model SMA7130, SMA71075 and SMA71100. There is
also an informative theory-of-operation chapter.
We suggest that you take the time to read this manual from cover-to-cover before attempting to work
with these amplifiers for the first time. If at any time you have questions, or have any special requirements,
please feel free to call and discuss them with a Glentek applications engineer. We are happy to provide both off-the-
shelf and custom products. With over three decades in the servo-motor/amplifier business, we have a vast pool of
applications knowledge waiting to assist you.
Thank you for selecting Glentek for your motion control needs. It is our goal to save you time, money, and to
provide you with a superior product.

Glentek Inc. 208 Standard Street, El Segundo, California 90245, U.S.A. (310) 322
-
3026
6
SMA7130, SMA71075 and SMA71100 MANUAL
Chapter One: Description, Features and Specifications
1.1 Description:
This brush type servo amplifier system has been designed to offer you, our customer, a large degree of
flexibility and customization with a standard, in stock product. The amplifier is of a modular, ‘open’ construction
for ease of installation and service.
The amplifier system is available in the following types of configurations:
•As a stand alone one axis amplifier, SMA7130-1A-1, SMA71075-1A-1 and SMA71100-1A-1, which contains
a DC power supply, cooling fan, soft start circuitry, fusing and a shunt regulator. Please see section 1.2.2
for more detailed information.
Each amplifier accepts a bipolar DC control input. The polarity of this signal determines the direction of
rotation. This signal may be used to control either the velocity (RPM) or the current (torque) of the motor (see
Servo Loops, section 2.3). The amplifier provides Pulse-Width Modulated (PWM) power to the motor in
proportion to the input signal.
Each amplifier has several ‘logic’ inputs to stop the motor in one or both directions. These inputs are very
useful for connecting to mechanical limit switches or digital equipment.
Each amplifier has several protection circuits to protect the amplifier, motor, and operator from almost any
kind of fault. LED’s show what fault has occurred, and a separate output can be used to signal other equipment.
1.2 Features:
1.2.1 Stand-Alone One Axis Amplifier (SMA7130, SMA71075 and SMA71100):
•Ergonomic design: Easy access to connections, adjustments, and test points.
•Complete isolation: Complete isolation from input to output.
•Dual signal inputs: One single-ended and one differential. Both single-ended inputs may be use
simultaneously. All inputs have up to 15,000A/V gain (velocity mode), and inputs
will accept up to ±13VDC for the differential input and ±50VDC for single-ended.
•Dual mode operation: The amplifier may be field configured for velocity (RPM) control or current torque)
control.
•Current limit: Maximum peak motor current is adjustable.
•Digital limit/enable Three separate logic inputs can stop the motor in either or both directions.
Inputs: Inputs may be configured for active-high or active-low, pull-up or pull-down
termination, and a 0 to +5VDC or 0 to+15VDC range. See Logic Input
Configuration, section 5.2.
•Fault input/output: Open-collector output goes low in the event of a fault. Externally forcing the
output low will inhibit the amplifier. This allows all fault outputs in a multi-axis
system to be connected together (wire-ORed) to shut down all amplifiers should
any amplifier have a fault.
•Silent operation: Carrier frequency is 20KHz for the SMA7130 and 9KHz for the SMA71075 and
SMA71100.
•Short circuit protection: Complete short circuit and ground fault protection.
•LED diagnostics: A Red LED flashes to display various fault conditions and a green LED illuminates
to indicate normal operating conditions.
•Tach or encoder A tachometer (standard) or encoder (optional) velocity feedback personality board.
feedback:
CHAPTER 1: DESCRIPTION, FEATURES AND SPECIFICATIONS

Glentek Inc. 208 Standard Street, El Segundo, California 90245, U.S.A. (310) 322
-
3026
7
SMA7130, SMA71075 and SMA71100 MANUAL
•Frequency response 750 Hz minimum.
(Velocity Loop):
•Frequency response 2 KHz minimum.
(Current Loop):
•External Aseparate input is provided to reset the amplifier after a fault.
fault reset:
•High-Speed Electronic Instantly shuts down the amplifier in the event of a short across
Circuit Breaker outputs and or ground fault condition.
(HS/ECB):
•Low-Speed Electronic Shuts down the amplifier if the amplifier is operated above the
Circuit Breaker maximum continuous current rating for 2seconds.
(LS/ECB):
•Over/under voltage These circuits constantly monitor amplifier power-supply
and over temperature: voltages, and amplifier-heatsink temperature. They will shut down the
amplifier in the event of any out-of-specification amplifier condition.
•Surface mount Constructed with surface mount components.
technology:
•Line operated AC power operation, 110-130VAC: Single or three phase AC input with in-rush current
protection at turn-on. No power isolation transformer is required.
•Regen clamp circuit (shunt regulator) with LED indicator and internal load resistor bank bleeds off excess
DC Buss voltage when decelerating a large load inertia (95 watts for the SMA7130 and 375 watts for the
SMA71075 and SMA71100). The regen clamp circuit is set to turn on at 225VDC.
•All faults can be monitored through isolated logic signals.
•Bridge rectifier(s) and filter capacitor(s).
•Cooling fans.
CHAPTER 1: DESCRIPTION, FEATURES AND SPECIFICATIONS

Glentek Inc. 208 Standard Street, El Segundo, California 90245, U.S.A. (310) 322
-
3026
8
SMA7130, SMA71075 and SMA71100 MANUAL
Signal Input Voltage
VDC
(maximum)
Impedance
(minimum)
ohms
Velocity Gain
Amp./Volt
Current Gain
Amp./Volt
Differential ±13 10,000 15,000 0-5
Single-ended ±50 4,000 15,000 0-5
Tachometer input ±50 10,000 7,000
1.3 Specifications:
1.3.1 Stand-Alone Amplifier (SMA7130-1A-1, SMA71075-1A-1, SMA71100-1A-1):
The amplifier requires external AC power. Forced air cooling is required to meet the maximum power
ratings specified below.
1.3.1.1 Input and Output Power:
1.3.1.3 Digital Inputs:
•±Limit, Inhibit and Reset: +24V max. Terminated by 10K ohms.
•Fault (as input): +40V/-5v max. Terminated by 10K ohms.
•Typical for all digital inputs: Digital inputs have hysteresis with thresholds at 1/3 and 2/3 of +5V or
+15V depending on range selected.
1.3.1.4 System:
•Drift offset over temperature reference to input: 0.01mV/ oC max.
•Frequency response (Velocity loop): 750Hz min.
•Frequency response (Current loop): 2KHz min.
•Dead band: None.
•Form factor: 1.01.
1.3.1.5 Outputs:
•Fault (as output): Active low. Open-collector output can sink 75mA max. through 10 ohms.
•Absolute motor current: Bipolar output. 1V=10Afor SMA7130; 1V=40A for SMA71075 &
SMA71100. 10mA max.
CHAPTER 1: DESCRIPTION, FEATURES AND SPECIFICATIONS
Amplifier
Model
AC
Input
Voltage
R.M.S. Peak
SMA7130-1A-1120 30A 60A
SMA71075-1A-1120 75A 150A
SMA71100-1A-1120 100A 150A
Output Power
(Current)
1.3.1.2Signal Inputs:
1.3.1.6 Mechanical:
Model L x W x H
(inches) Weight
(lbs)
SMA7130-1A-1 14.50 x 4.25 x 8.81 11.00
SMA71075-1A-117.63 x 5.75 x 12.40 28.00
SMA71100-1A-117.63 x 5.75 x 12.40 28.00

Glentek Inc. 208 Standard Street, El Segundo, California 90245, U.S.A. (310) 322
-
3026
9
SMA7130, SMA71075 and SMA71100 MANUAL
Chapter Two: Theory of Operation
2.1 Introduction:
This chapter contains the basic control theory of how brush type and brushless servo motors and amplifiers
operate. It also compares and contrasts the advantages and disadvantages of brushless and brush type motors
and amplifiers to help you select which is best suited for your application. The following is a summary of the
topics:
•The theory behind an amplifier driving DC servo motors.
•A comparison between brush type and brushless motors.
•Operation of output switching transistors.
•“H Type” output bridge configuration.
•Pulse-Width-Modulation (PWM).
•Current-Loop and Velocity-Loop operation.
•Protection circuits.
2.2 Driving DC Servo-Motors:
The torque of any DC motor is proportional to motor current: the stronger the magnetic field, the stronger the
pull. Motor current may be controlled in two ways: linear and PWM (Pulse-Width Modulation). Linear control is
achieved by simply inserting a resistance in series with the motor. This resistance is usually a partially turned on
transistor. The transistor is said to be in its "linear" region. Linear amplifiers are simple, accurate, and effective.
However, they are very inefficient and they generate a lot of heat. Linear amplifiers are used when low electrical
noise, high bandwidths (2KHz or higher) and or low inductance (less than 1mH) motors are used. In pulse-width
modulation the control devices (output transistors) are rapidly turned full on and full off. The ratio of the on time
(the pulse width) and off time determines the average motor current. Refer to figure 2.1. For example: if the
output is on 25% of the time and off 75% of the time, the average motor current is approximately 25% of
maximum.
A coil of wire, such as the windings of a motor, forms an inductor. Inductors resist changes in current. This
resistance to change, known as reactance, acts to dampen or average the high-current spikes that would
otherwise occur when the output devices are on. In fact, if motor inductance is low, external inductors may have
to be added in series with each motor lead to ensure proper operation.
A brush type motor may be run from a steady DC voltage since the brushes and commutator switch the
current from winding to winding. However, a brushless motor requires that the voltage be switched from winding
to winding externally; the voltage that drives a brushless motor is a constantly changing AC waveform. Section
2.5 discusses these waveforms.
Figure 2.1
Pulse Width Modulation Waveform
CHAPTER 2: THEORY OF OPERATION

Glentek Inc. 208 Standard Street, El Segundo, California 90245, U.S.A. (310) 322
-
3026
10
SMA7130, SMA71075 and SMA71100 MANUAL
CHAPTER 2: THEORY OF OPERATION
2.3 Servo Loops:
A basic velocity mode servo loop for a brush type motor is shown in figure 2.2a. An external controller
commands a given velocity (RPM). The velocity loop summing amplifier compares this command with the actual
motor velocity, supplied by a DC tachometer on the motor shaft, and produces an error voltage proportional to
the difference between the actual and commanded velocity.
The velocity error is used to command motor current in the inner servo-loop. The current loop summing
amplifier compares the command current (velocity error) with the actual current in the motor and produces an
error voltage proportional to the difference between the actual and commanded current.
Finally, the current error signal is used to produce an output (linear or PWM) to drive the motor.
The velocity loop may be bypassed, and an external current command fed directly to the current loop. In
this case, the external command signal controls the torque of the motor, rather than the velocity. This is known
as current-mode operation.
The servo-loops of a brushless amplifier (figure 2.2b) operate in much the same way,
except there are now three current loops, one for each phase of the motor.
Figure 2.2a
Velocity mode sevo loop
for a brush type motor
Figure 2.2b
Velocity mode sevo loop
for a brushless motor

Glentek Inc. 208 Standard Street, El Segundo, California 90245, U.S.A. (310) 322
-
3026
11
SMA7130, SMA71075 and SMA71100 MANUAL
Figure 2.3
Brush type and Brushless type Motors
2.4 Brushed Motors vs. Brushless Motors:
There are two basic types of motor design that are used for high-performance motion control systems: brush
type PM (permanent magnet), and brushless type PM. As you can see in figure 2.3, a brush type motor has
windings on the rotor (shaft) and magnets in the stator (frame). In a brushless type motor, the magnets are on
the rotor and the windings are in the stator.
To produce optimal torque in a motor, it is necessary to direct the flow of current to the appropriate windings
with respect to the magnetic fields of the permanent magnets. In a brush-type motor, this is accomplished by
using a commutator and brushes. The brushes, which are mounted in the stator, are connected to the motor
wires, and the commutator contacts, which are mounted on the rotor, are connected to the windings. As the
rotor turns, the brushes switch the current flow to the windings which are optimally oriented with respect to the
magnetic field, which in turn produces maximum torque.
In a brushless motor there is no commutator to direct the current flow through the windings. Instead, an
encoder, hall sensors or a resolver on the motor shaft senses the rotor position (and thus the magnet
orientation). The position data is fed to the amplifier which in turn commutates the motor electronically by
directing the current through the appropriate windings to produce maximum torque. The effect is analogous to a
string of sequencing Christmas lights: the lights seem to chase each other around the string. In this case, the
magnets on the rotor "chase" the magnetic fields of the windings as the fields "move" around the stator.
The relative advantages and/or disadvantages of a brush type motor/amplifier combination vs. a brushless
motor/amplifier combination can be significant. On the next page is a summary of advantages and
disadvantages of brush type motor/amplifiers and brushless type motor/amplifiers to help you decide which type
to select for your applications.
CHAPTER 2: THEORY OF OPERATION

Glentek Inc. 208 Standard Street, El Segundo, California 90245, U.S.A. (310) 322
-
3026
12
SMA7130, SMA71075 and SMA71100 MANUAL
Brushless Motors/Amplifiers Brushed Motors/Amplifiers
Advantages Disadvantages
No scheduled maintenance and no brush dust
is generated. Motor brushes must be checked periodically for
wear and excess brush dust.
Higher RPM limits. Approximately 3000RPM maximum.
Lower inertia/torque ratio. Higher inertia to torque ratio.
Dissipates heat more efficiently due to
windings being located in stator. Not as efficient at dissipating heat. Heat is
trapped at rotor and shortens bearing life.
Safer for explosive atmospheres. Quieter and
less electrical noise generated. Brushes spark and generate electrical and
audible noise.
Disadvantages Advantages
Amplifiers are complicated and expensive. Amplifiers are simpler and less expensive.
Higher torque ripple. Lower torque ripple.
No Industry standard packaging. Industry standard packaging.
2.5 Operation of Output Switching Transistors:
The output transistors, for all intents and purposes, operate in only two states. They are analogous to ON/
OFF switches. When an output transistor is OFF , there is no current flowing through it (its resistance is infinite).
When an output transistor is ON, current flows through it (its resistance is near zero). When the transistor is ON,
it is technically referred to as being in saturation.
2.6 “H” Type Output Bridge Configuration:
The output configuration of the amplifier is an “H TYPE” bridge (see figure 2.4 for schematic representation
of an output bridge with a motor connected).
Figure 2.4
Schematic representation of
an output bridge with a
motor connected.
The advantage of an “H TYPE” output bridge configuration is that by controlling the
switching of the opposite pairs of transistors, current can be made to flow through the motor
in either direction using a single-polarity power supply.
To provide motor current in one direction, transistor A and C are turned ON, while B and
D remain in the OFF state. To provide motor current in the other direction, B and D are
turned ON, while A and C remain in the OFF state.
CHAPTER 2: THEORY OF OPERATION

Glentek Inc. 208 Standard Street, El Segundo, California 90245, U.S.A. (310) 322
-
3026
13
SMA7130, SMA71075 and SMA71100 MANUAL
2.7 Pulse-Width-Modulation (PWM):
Pulse-width-modulation is the technique used for switching opposite pairs of output transistors ON and OFF
to control the motor drive current. When zero current is commanded to the current loop, the opposite pairs of
transistor are turned ON and OFF as shown in figure 2.5. Note that since the pulse widths are equal, the net DC
current in the motor is equal to zero.
When a non-zero current is commanded to the current loop, the transistor switching waveform is as shown in
figure 2.6A. Since there is a non-zero current command, the output transistor pulse widths will change and the
motor will see a net DC current flowing from A through C.
Figure 2.5
Transistor switching
waveform at zero
current
Figure 2.6A
Transistor switching
waveform when current
flows from A through C
If the input to the current loop had been changed in polarity, the output transistor switching waveform would
be as shown in figure 2.6B.
Figure 2.6B
Transistor switching
waveform when current
flows from B through D
If a larger current of the same polarity was commanded to the output transistor (see figure 2.6B) the ON-time
widths of B and D would automatically increase to provide more current.
From the previous examples it is easy to understand why this output transistor switching technique is
referred to as pulse-width-modulation.
To change the magnitude and polarity of the current flow in the motor, the pulse widths of the opposite pairs
of transistors are modulated. The frequency at which these output transistors are switched ON and OFF is
referred to as the ‘carrier frequency’.
CHAPTER 2: THEORY OF OPERATION

Glentek Inc. 208 Standard Street, El Segundo, California 90245, U.S.A. (310) 322
-
3026
14
SMA7130, SMA71075 and SMA71100 MANUAL
CHAPTER 2: THEORY OF OPERATION
Now that we have a good understanding of how the current is provided from an “H TYPE” pulse-width-
modulated (PWM) bridge, let’s analyze the operation of the current loop.
2.8 Current Loop Operation:
Please refer to figure 2.2A for a diagram of the current loop. In control electronics the symbol Sigma (with
the circle around it) is referred to as a ‘summing junction’. The manner in which this summing junction operates
is as follows:
The current-command signal (also referred to as the velocity error signal when received from the output of
the velocity loop, as shown in figure 2.2A) is added to the current feedback signal. The signal resulting from this
addition, is referred to as the “current error” signal. This current-error signal is fed into the current amplifier,
which in turn produces a current in the motor. A voltage which is proportional to the motor current is developed
across Rs (shunt resistor). This voltage is referred to as the “current feedback” signal. The current in the motor
increases until the current-command signal is equaled. At this point the current error signal drops to zero and
the actual current is equal to the commanded current. If anything happens to disturb either the current
command signal, or the current feedback signal, the same process occurs again until the current feedback signal
is equal in magnitude to the current command signal, but opposite in polarity.
The type of loop described above is referred to as a “servo loop” because the current servos about a
commanded value.
We are surrounded in our everyday lives by a multitude of servo loops. For example, many of today’s luxury
cars have what is called ‘automatic climate control’. To operate this servo loop, you set the climate control to the
temperature that you wish to be maintained in the interior of the car (current command signal). The selected
temperature is then summed with the actual temperature from a thermometer (current feedback), and the output
(current error signal) activates either the heater or the air conditioner until the actual temperature as measured
by the thermometer (current feedback signal) is equal in magnitude, but opposite in polarity, to the set
temperature.
2.9 Velocity Loop Operation:
Please refer to figure 2.2A for a diagram of a typical velocity loop. The velocity loop’s operational description
is analogous to the current loop description, except for the fact that the input signal is called the Velocity
Command and the feedback signal from the DC tachometer is called the Velocity Feedback.
2.10 Protection Circuits:
The High and Low Speed Electronic Circuit Breakers (HS/ECB and LS/ECB) protect the amplifier and motor
from being damaged by high motor current (specified max. peak and rms current values). The Over
Temperature and Over Voltage detection circuits will shut off the amplifier when the temperature of the amplifier
or the buss (B+) voltage exceeds a specified limit. Also, there are circuits which limit the motor from running in
either or both directions.

Glentek Inc. 208 Standard Street, El Segundo, California 90245, U.S.A. (310) 322
-
3026
15
SMA7130, SMA71075 and SMA71100 MANUAL
Chapter Three: Model Numbering
3.1 Introduction:
This chapter contains the model numbering system for the SMA7130, SMA71075 and SMA71100, stand
alone one axis amplifiers. The model numbering system is designed so that you, our customer,will be able to
create the correct model number of the product that you need quickly and as accurate as possible.
3.2 Stand Alone Amplifiers (SMA7130, SMA71075 and SMA71100):
Differential or Single-ended
Signal Inputs:
0 = Single; (Default)
1 = Differential.
Velocity or Current Mode:
(see section 2.8 and 2.9)
0 = Velocity; 1 = Current.
On Board Power Supply
+15V/+5V on pull-up:
0 = +15V; (Default)
1 = +5V.
Personality Board Type:
0 = Tachometer;(Default)
1 = Encoder
±Limit 0=L, 1=H
±Limit 0=U, 1=D
Inhibit 0=L, 1=H
Inhibit 0=U, 1=D
Reset 0=L, 1=H
Reset 0=U, 1=D
{See section 5.2}
Type A: U=0 & L=0
(Default)
Type B: D=1 & H=1
Type C: U=0 & H=1
Type D: D=1 & L=0
00
0000=0 1000=8
0001=1 1001=9
0010=2 1010=A
0011=3 1011=B
0100=4 1100=C
0101=5 1101=D
0110=6 1110=E
0111=7 1111=F
4-BIT Binary
to Digital
SMA71XXX -YYY -QQQ -1A -1 -ZZ
Amplifier Model Number Power Supply
Configuration Code
30 = SMA7130Optional Custom 00 = 110-130VAC
075 = SMA71075 Configuration Code 01 = SPECIAL
100 = SMA71100 (A numerical code will be
assigned by Glentek to amplifiers
Amplifier Configuration Code (Below) whose specifications vary from
the standard configuration.)
Amplifier Configuration Code
CHAPTER 3: MODEL NUMBERING

Glentek Inc. 208 Standard Street, El Segundo, California 90245, U.S.A. (310) 322
-
3026
16
SMA7130, SMA71075 and SMA71100 MANUAL
Chapter Four: Installation
4.1 Introduction:
This chapter provides the necessary information to make all the wiring connections for the amplifiers to
operate properly.
4.2 Mounting:
Appendix A contains all the wiring diagrams, assembly drawings, and mechanical information necessary to
install the amplifiers. The amplifier package should be mounted in a clean, dry enclosure, free of dust, oil, or
other contaminants.
NEVER INSTALL THE AMPLIFIER PACKAGE IN ANY LOCATION
WHERE FLAMMABLE OR EXPLOSIVE VAPORS ARE PRESENT.
IMPORTANT: Muffin fan(s) are mounted along one edge of the amplifier to provide cooling. At least 3 inches
must be allowed between the fan side and the side opposite the fans and any other surface. The clearance to
any other side of the amplifier package is not critical, although sufficient space should be allowed for easy wiring
and servicing.
4.3 Wiring:
DO NOT APPLY POWER UNTIL INSTRUCTED TO DO SO.
4.3.1 RFI/EMI and Wiring Technique:
IMPORTANT: All PWM equipment inherently generates radio-frequency interference (RFI), and
wiring acts as antennae to transmit this interference. In addition, motors inherently generate electromagnetic
interference (EMI). Unless the wiring is very short, some sort of shielding on the motor wires is necessary to
meet FCC RFI/EMI guidelines and to protect other equipment from the effects of RFI/EMI. We recommend
that shielded wire be used, or the wires should be run in metallic conduit. The shield or conduit should be
connected to the amplifier baseplate, which in turn must be earth grounded. In addition, a conductor of the
same gauge as the motor wires must be connected from the motor case to the amplifier baseplate to
provide protection from shock hazard. The earth grounding is necessary to meet National Electrical Code
(NEC) requirements as well as suppressing RFI/EMI.
Additional RFI suppression may be obtained by placing inductors in each motor lead near the
amplifier. Consult a Glentek applications engineer for inductor recommendations. Glentek stocks a complete
line of inductors for virtually every application.
IMPORTANT: The signal wiring to the tachometer, encoder (if used) and the signal inputs to the
amplifier are susceptible to noise pickup. Excessive noise pickup will cause erratic amplifier operation. We
urge that each signal input line each be run in separate, twisted-pair, shielded cable. In each case the shield
should be terminated at the amplifier end only to a common terminal. We also recommend that the signal
lines be kept as far as possible from any power or motor wires.
CHAPTER 4: INSTALLATION

Glentek Inc. 208 Standard Street, El Segundo, California 90245, U.S.A. (310) 322
-
3026
17
SMA7130, SMA71075 and SMA71100 MANUAL
4.3.2 Wire Size and Type:
IMPORTANT: To ensure safe operation, Glentek strongly recommends that all wiring conform to all local
and national codes.
Recommended Wire Size and Type:
•Motor Wires: 10AWG, shielded -SMA7130.
6AWG, shielded -SMA71075
4AWG, shielded -SMA71100
•Motor Case Ground: Same as motor wires, or use metallic conduit.
•Main Power: 12AWG, twisted -SMA7130.
8AWG, twisted -SMA71075
6AWG, twisted -SMA71100
•Fan Power: 16AWG, twisted.
•Signal,Tach, Encoder Input: 22AWG, twisted-pair, shielded.
•Logic Inputs/Outputs: 22AWG, shielded with its return lead.
4.3.3 Connector Size and Type:
4.3.3.1 The Power and Motor Connector of the SMA7130 Amplifier:
•MAGNUM Series A2000 (Magnum p/n A203508):
-Screw Size/Spacing: #6-32 on .375” centers.
-Number of Screw Terminals: 8.
-Color: Black.
4.3.3.2The Power and Motor Connector of the SMA71075 and SMA71100 Amplifiers:
•MAGNUM Series 1404 (Magnum p/n 14004-8):
-Screw Size/Spacing: #6-32 on .500” centers.
-Number of Screw Terminals: 8.
-Color: Black.
4.3.3.3The Signal Connectors:
The signal connector is supported by the Molex®KK 2695 Series .100" (2.54mm) Centerline Connector
System.
•J1 of the Main Amplifier:
Mating connector: Molex®2695 Series .100” (2.54mm) Center Crimp Terminal Housing (P/N 22-
01-3175):
-Red Nylon Housing.
-15 positions.
-With polarizing rib.
•J4 of the Personality Board (Optional Encoder Input):
Mating connector: Molex®2695 Series .100” (2.54mm) Center Crimp Terminal Housing (P/N 22-
01-3107):
-Red Nylon Housing.
-10 positions.
-With polarizing rib.
•Crimp Terminals for the above mating connectors: Molex®Crimp Terminals (molex P/N: 08-55-
0102):
-15 microinch select gold plated.
-brass.
CHAPTER 4: INSTALLATION

Glentek Inc. 208 Standard Street, El Segundo, California 90245, U.S.A. (310) 322
-
3026
18
SMA7130, SMA71075 and SMA71100 MANUAL
CHAPTER 4: INSTALLATION
4.3.4 Amplifier Module Connections:
4.3.4.1 The Power Connections for the SMA7130 -TB1:
Signal Name Terminal Notes
AC 1 TB1-1AC power input -1Ø
AC 2 TB1-2AC power input -1Ø
AC 3 TB1-3AC power input -3Ø
CHASSIS GND TB1-4Chassis ground
N/C TB1-5No connection
MTR B TB1-6Motor -
N/C TB1-7No connection
MTR A TB1-8Motor +
4.3.4.2The Power Connections for the SMA71075 and SMA71100:
Signal Name Terminal Notes
MTR B 1Motor -
N/C 2No connection
MTR A 3Motor +
N/C 4No connection
N/C 5No connection
AC 3 6AC power input -3Ø
AC 2 7AC power input -1Ø
AC 1 8AC power input -1Ø

Glentek Inc. 208 Standard Street, El Segundo, California 90245, U.S.A. (310) 322
-
3026
19
SMA7130, SMA71075 and SMA71100 MANUAL
Signal Name Terminal Notes
Encoder Input (J4):
N/C J4-1No Connection.
AJ4-2Phase A signal input.
AJ4-3Negative phase A signal input.
BJ4-4Phase B signal input.
BJ4-5Negative phase B signal input.
ZJ4-6Phase Z signal input.
ZJ4-7Negative phase Z signal input.
COM J4-8Common for Encoder.
COM J4-9Common for Encoder.
COM J4-10 Common for Encoder.
4.3.4.4The Encoder Input Connections -J4 (Factory Option):
Signal Name Terminal Notes
SIGNAL 1 (+) J1-1Differential signal input.
SIGNAL 1 (-) J1-2Differential signal return.
SIGNAL 2 (+) J1-3Single-ended signal input.
COMMON J1-4Common for all signals and shields.
TACH IN J1-5Tachometer input. Not used in current-mode.
COMMON J1-6Common for all signals and shields.
ABS I J1-7Scale factor: 1V=10A for the SMA7130;
1V=40A for the SMA71075, SMA71100.
LIMIT + J1-8Inhibits the motor in the + direction.
LIMIT -J1-9Inhibits the motor in the -direction.
INHBIT J1-10 Inhibits the motor in both directions.
FAULT J1-11 Goes low if there is a fault in the amplifier. May be
externally forced low to stop motor rotation in both
directions.
COMMON J1-12 Common for all signals and shields.
RESET IN J1-13 Resets the fault latch. May also be used as an inhibit
input.
MTR TEMP J1-14 Motor over temperature switch input.
N/C J1-15 No Connection.
4.3.4.3The Signal Connections -J1:
CHAPTER 4: INSTALLATION

Glentek Inc. 208 Standard Street, El Segundo, California 90245, U.S.A. (310) 322
-
3026
20
SMA7130, SMA71075 and SMA71100 MANUAL
Chapter Five: Configuration
5.1 Introduction:
Each amplifier has several configuration options. This chapter describes these options and how to
implement them. If desired, Glentek will be happy to pre-configure your amplifiers.
NOTE: Each amplifier module and multi-axis amplifier is configured and shipped according to the model
number (instructions to construct a model number is in chapter three) when the order is placed. It is important
for the user to realize that any changes to the jumpers (micro-shunts) by the user will result in discrepancies
between the model number and the actual configuration of the amplifier.
5.2 Logic Input Configuration:
There are five logic inputs: Limit +, Limit -, Inhibit, Reset In and Motor Temp. The first four may be configured
for active-high or active-low signals, and pulled-up or pulled-down termination (type A, B, C, and D). The
motor-temp may be configured for active-high or active-low signals, and is always pulled-up (type A and C).
All five logic inputs have a selectable 0 to +5VDC or 0 to +15VDC range.
Type "A": Requires grounding of input to disable the amplifier (pull-up, active-low).
Type "B": Requires a positive voltage at input to disable the amplifier (pull-down, active-high).
Type "C": Requires grounding of input to enable the amplifier (pull-up, active-high).
Type "D": Requires a positive voltage at input to enable the amplifier (pull-down, active-low).
5.3 Amplifier Configuration:
The following table shows the jumpers (micro-shunts) that need to be configured for the Type A, B, C, and D
configurations. The standard configuration is shown in bold.
5.3.1 +15V/+5V Logic Level Configuration (Default: JP8 = Omit):
+15V: JP8 = Omit.
+5V: JP8 = Jumper.
5.3.2Velocity Mode and Current Mode Configuration:
Velocity Mode: JP2 = Jumper, JP4 = Omit.
Current Mode: JP2 = Omit, JP4 = Jumper.
5.3.3 Tach Lead (Default: JP3 = Omit):
The tach lead jumper is added to add capacitance to the tach lead circuit. This may be needed if you
have a large one hook overshoot when monitoring tach out. This jumper should remain omitted unless
instructed to add by a Glentek engineer.
5.3.4 Tach Reverse Configuration (For encoder input option only; Default: JP6-3 = Jumper):
The tachometer reverse jumper is added to reverse the spinning direction of the motor or prevent the
motor from running away in case of incorrect polarity of the feedback signal.
Type A Type B Type C Type D
LIMIT± JP7-C -Omit
JP10-D -Jumper JP7-C -Jumper
JP10-D -Omit JP7-C -Omit
JP10-D -Omit JP7-C -Jumper
JP10-D -Jumper
INHIBIT JP7-B -Omit
JP10-C -Jumper JP7-B -Jumper
JP10-C -Omit JP7-B -Omit
JP10-C -Omit JP7-B -Jumper
JP10-C -Jumper
RESET IN JP7-A -Omit
JP10-B -Jumper JP7-A -Jumper
JP10-B -Omit JP7-A -Omit
JP10-B -Omit JP7-A -Jumper
JP10-B -Jumper
MTR TEMP JP10-A -Jumper not available JP10-A -Omit not available
FAULT standard not available not available not available
CHAPTER 5: CONFIGURATION
This manual suits for next models
2
Table of contents
Other Glentek Amplifier manuals
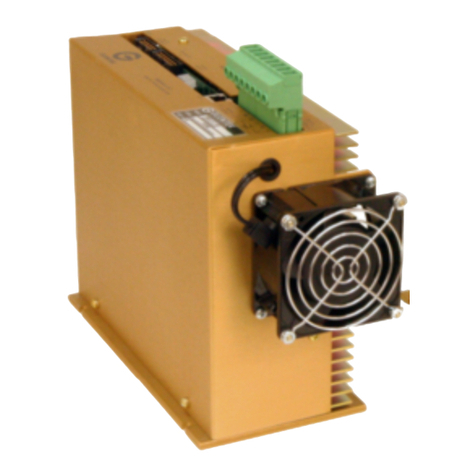
Glentek
Glentek Alpha Series User manual
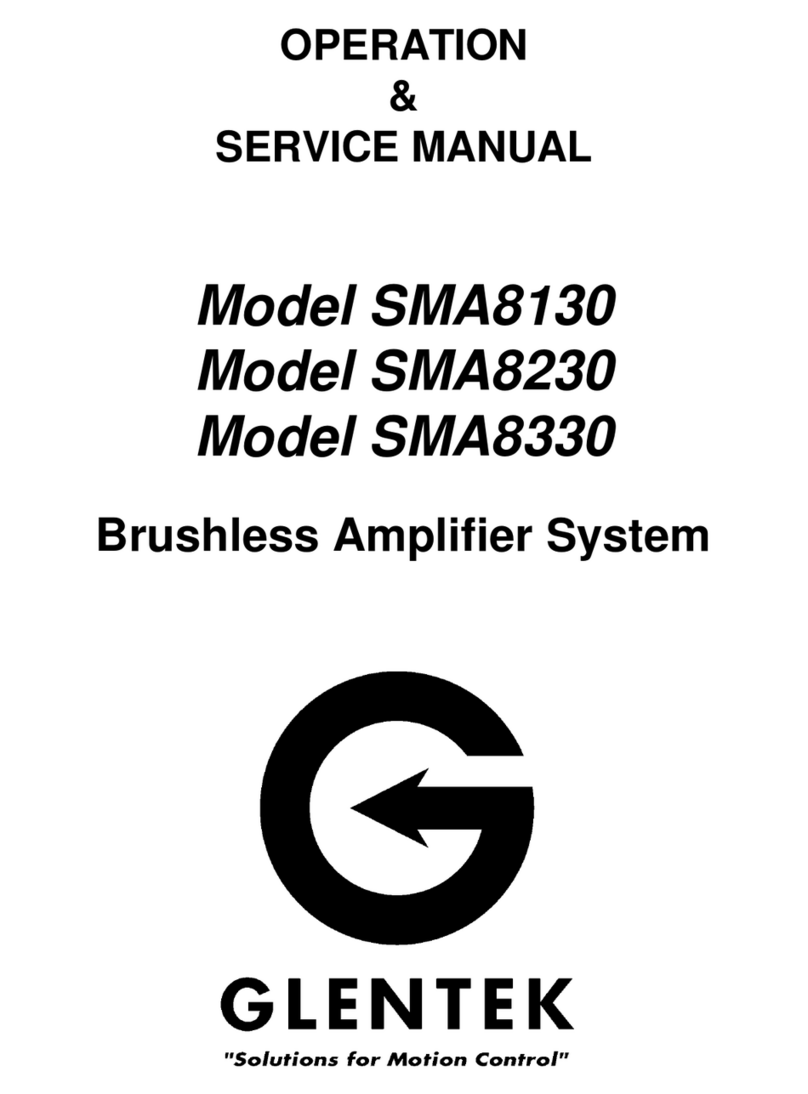
Glentek
Glentek SMA8130 Installation and operating instructions
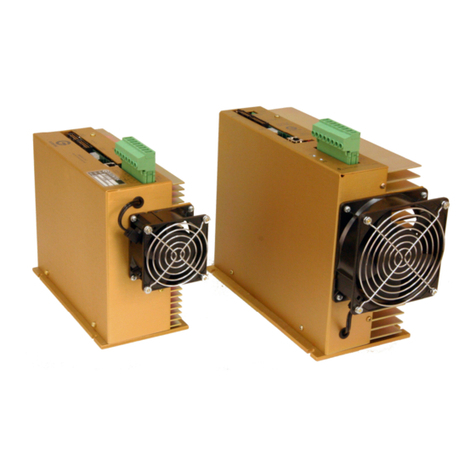
Glentek
Glentek Alpha Series User manual
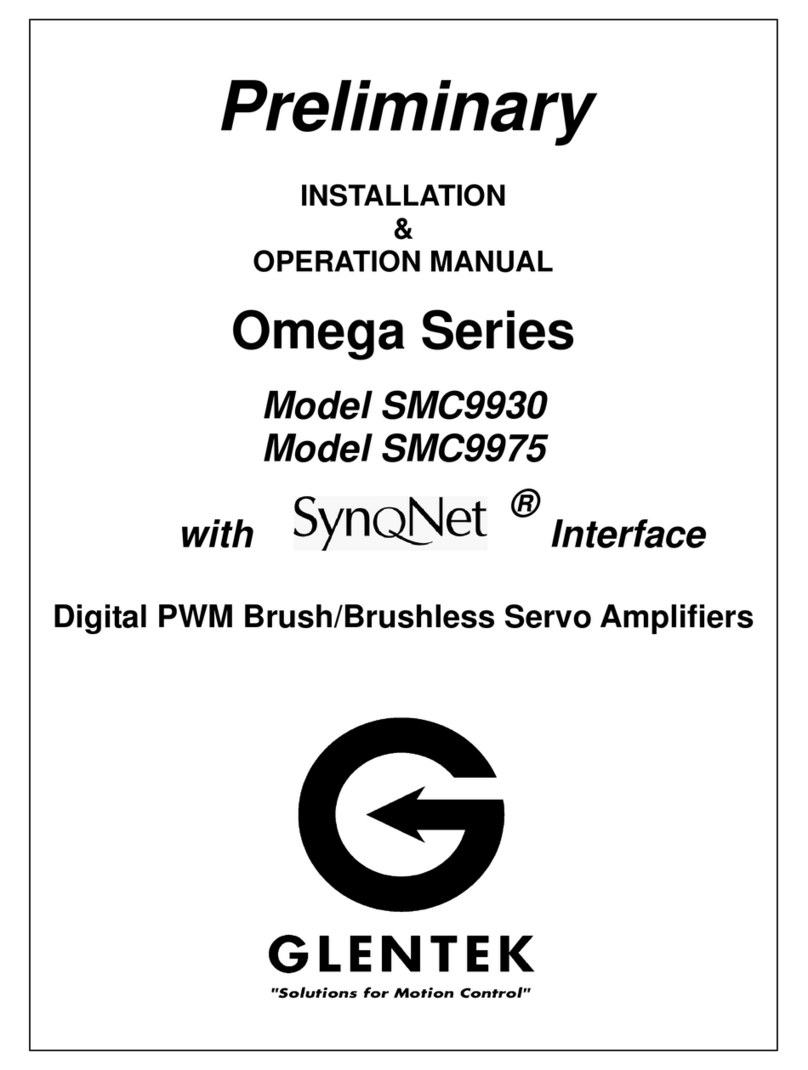
Glentek
Glentek Omega SMC9930 User manual
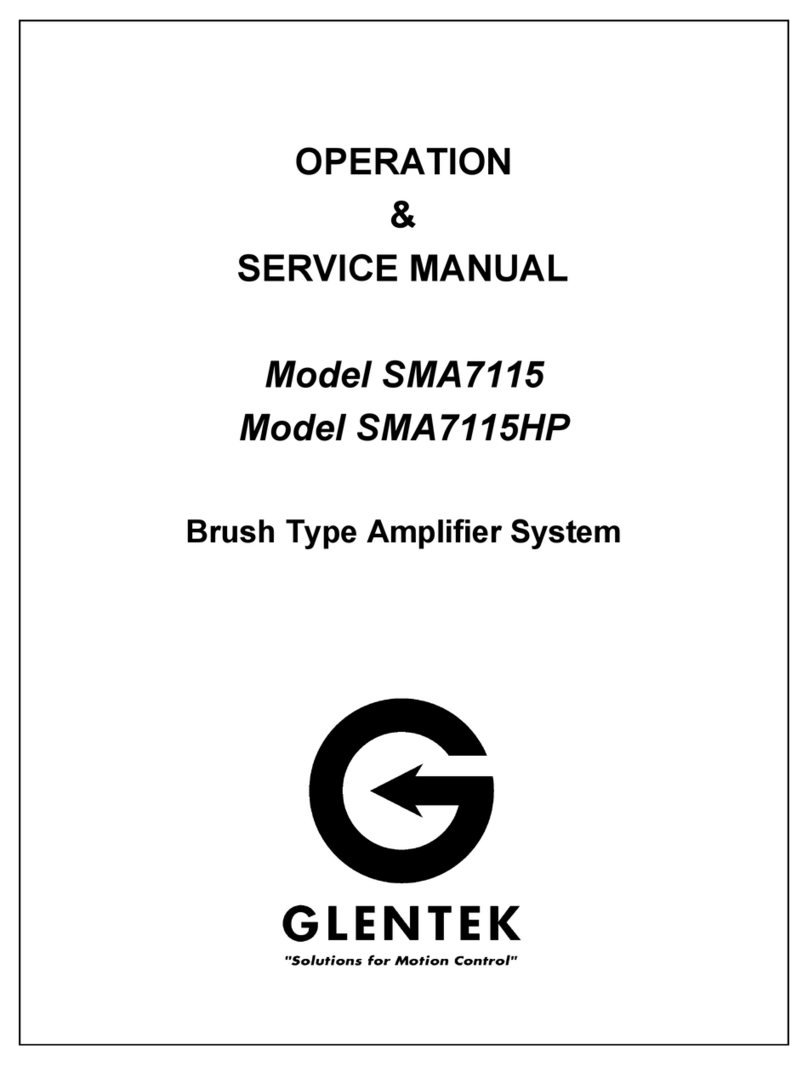
Glentek
Glentek SMA7115HP Installation and operating instructions
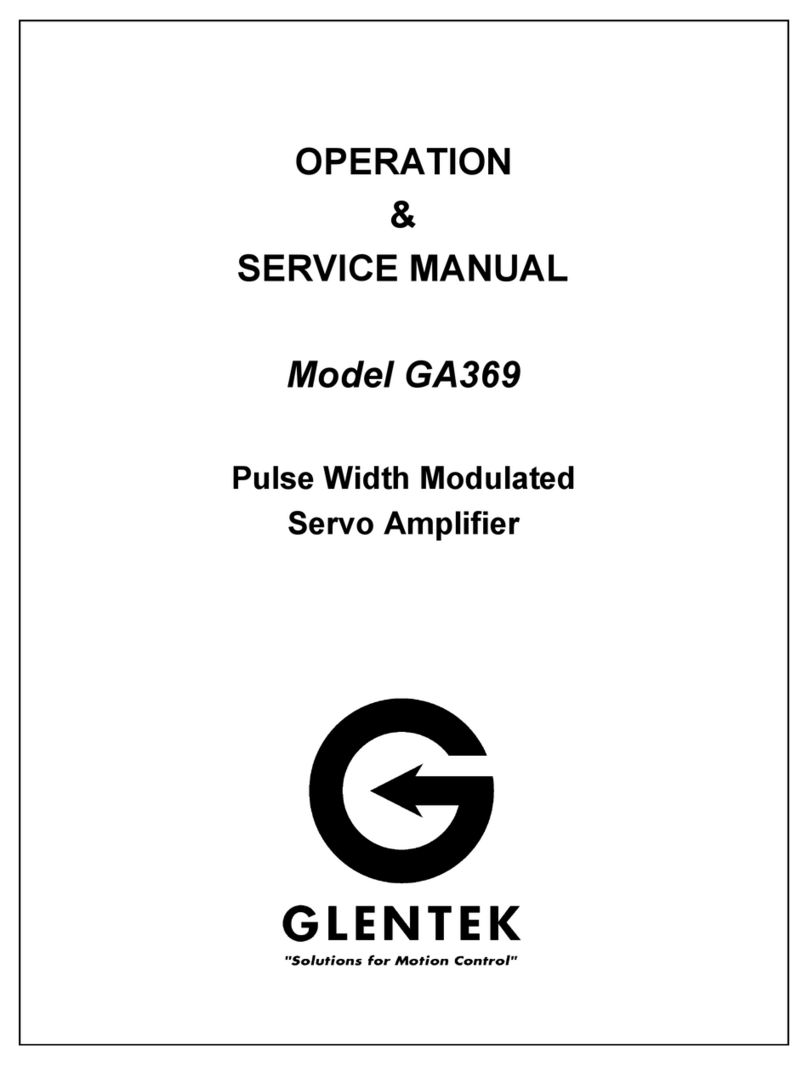
Glentek
Glentek GA369 Installation and operating instructions
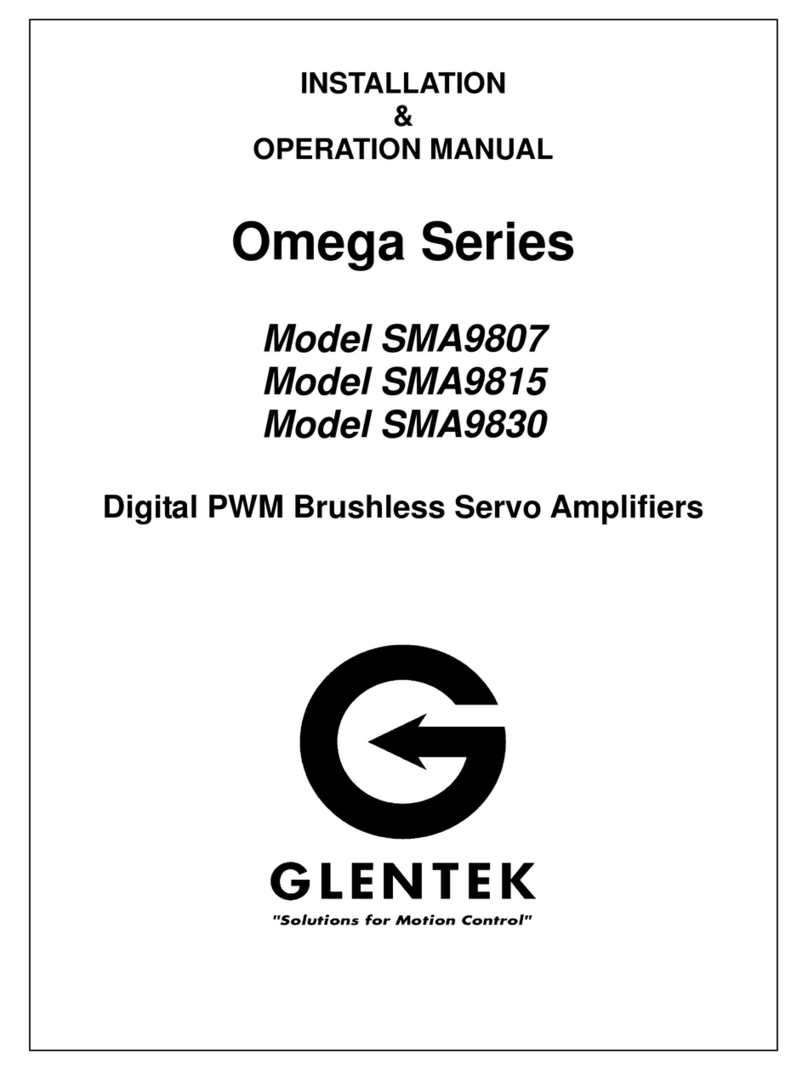
Glentek
Glentek Omega Series User manual
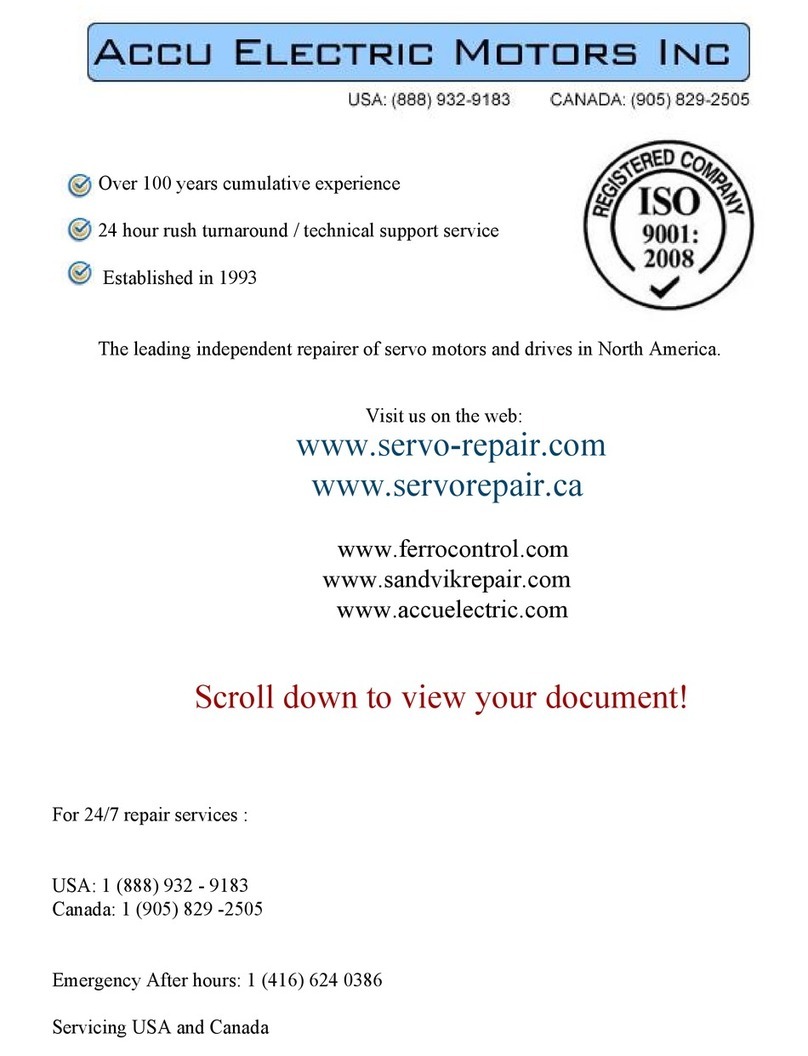
Glentek
Glentek SMA7105 Installation and operating instructions
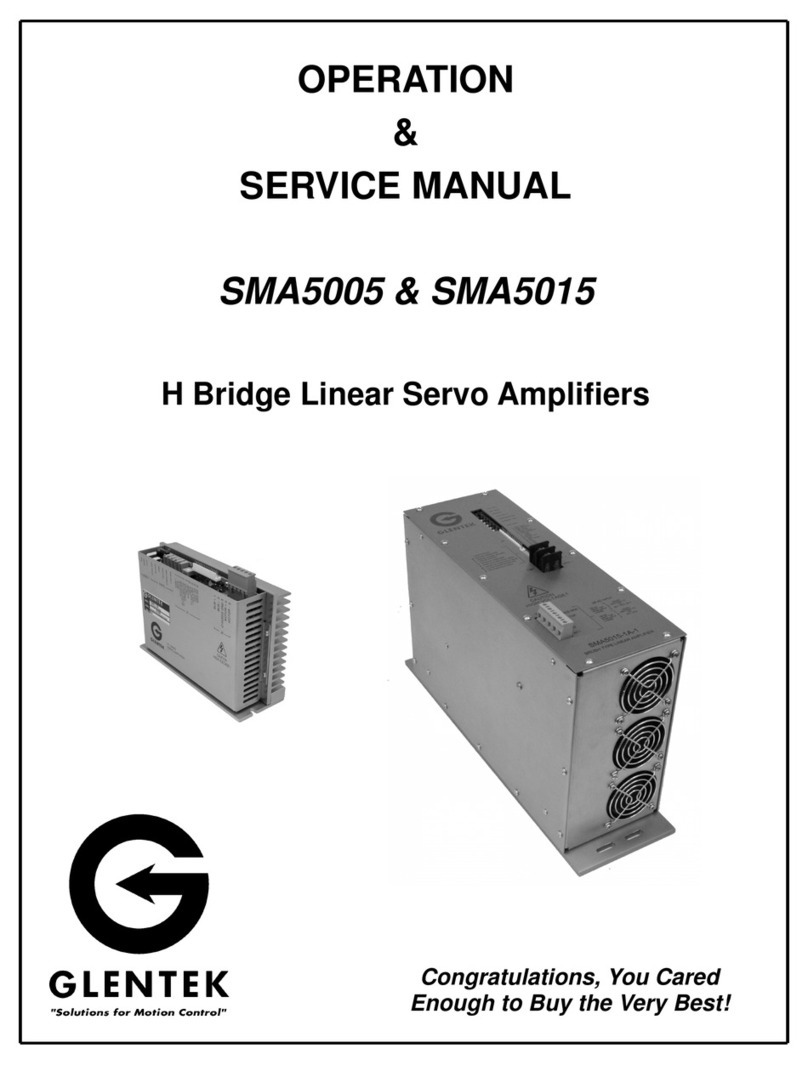
Glentek
Glentek SMA5005 Installation and operating instructions
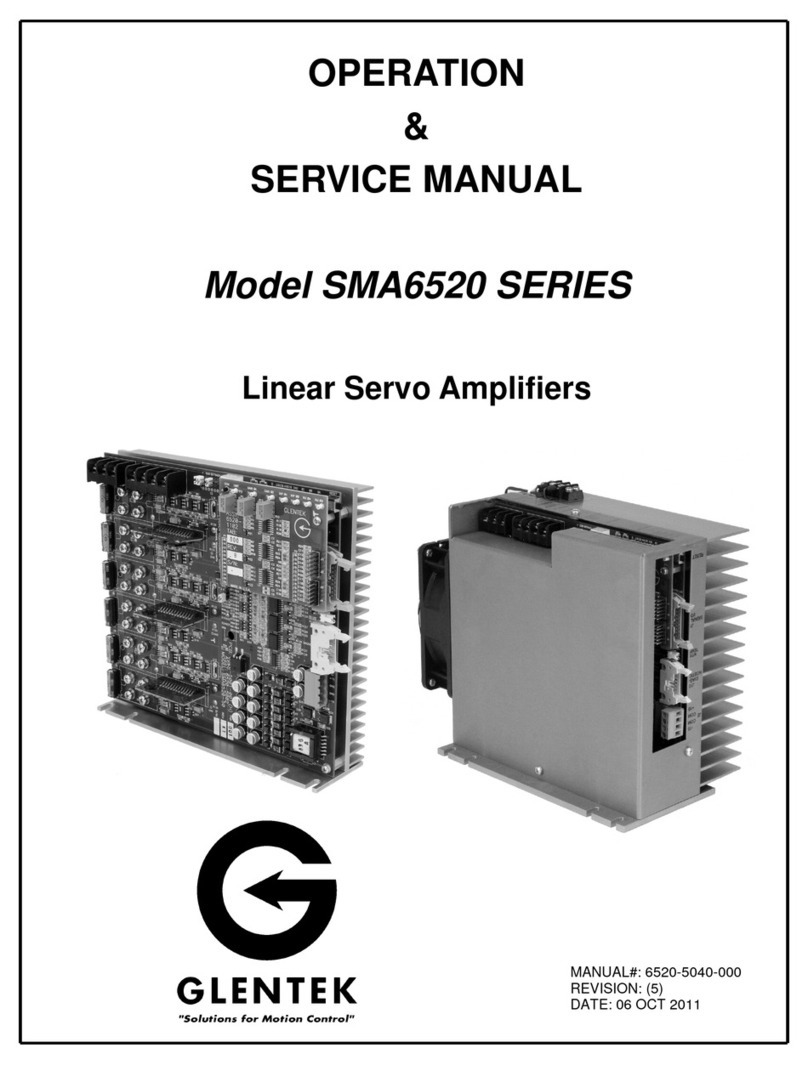
Glentek
Glentek SMA6520 SERIES Installation and operating instructions