Globe RM610 User manual

Manual
GLOBE RM610 Piston Air Motor
With optional auxiliaries
GLOBE Airmotors | Boerhaaveweg 9-11 | NL - 2408 AD Alphen a/d Rijn | Tel +31 172 426 608 | info@globe-benelux.nl
AIRMOTORS B.V.
GLOBE
globe-airmotors.com

2 · GLOBE RM610 PISTON AIR MOTOR MANUAL| INCLUDING AUXILIARIES
APPROVALS
CERTIFICATION
Contents
Warranty 3
Safety first 3
Installation Motor & Valve 4
Mounting to construction 6
Air supply 7
Installation Brake 9
Mounting to construction 10
Operation Motor & Valve 11
Performance regulation 14
Operational principle HCV 15
Operational priciple RCV 16
Operation Brake 17
Operation Principle Brake 18
Load Adjustment 22
Maintenance Motor & Valve 23
Shutdown and long storage 24
Servicing 26
Maintenance Brake 35
Trouble shooting 37
Dimensions, Performances & Spare
Parts 38
Main dimensions RM110 38
Main dimensions RM110 + Brake 39
Performance RM110 + Brake 40
Main dim. RM110 + Brake + HCV 41
Main dim. RM110 + Brake + RCV 42
Performance RM110 + HCV/RCV 43
Spare Parts List RM110 44
Spare Parts List Parking Brake 45
Spare Parts List HCV 46
Spare Parts List RCV 47
Ordering code 49
CE Certification 50
Options & Accessories 52
The GLOBE piston air motors and pneumatic
brakes are certified according to the following
(harmonized) standards:
EN-ISO80079-36:2016
EN-ISO80079-37:2016
Machinery directive 2006/42/EC
Supply of Machinery (Safety) Regulations
2008
Safety of machines – basic terminology-
EN-ISO 12100:2010
Preparation for using the instructions – structu-
re, content en presentation part 1:
General assumptions and detailed demands
EN-IEC 82079-1:2012
Pneumatics – general rules and safety regulati-
ons for systems and parts
EN-ISO 4414:2010

· 3GLOBE RM610 PISTON AIR MOTOR MANUAL| INCLUDING AUXILIARIES
Congratulations with your GLOBE air motor!
This product is made with quality materials to meet the highest standards.
This manual contains safety instructions for the use of your GLOBE air
motor. Please read and follow all recommended instructions for a trouble-
free use.
Warranty
The GLOBE Piston Air Motor and the GLOBE Pneumatic Brakes are designed to operate without
any problems. This is only guaranteed if the regulations with regards to installation, operation,
maintenance and repair are observed. Problems occurring during the guarantee period are
corrected in accordance to GLOBE Airmotors BV guarantee conditions. All results of unauthorised
opening and repairs carried out during the guarantee period may invalidate the warranty.
You can order your service kit at orders@globe-benelux.nl. Please ensure that maintenance is
carried out by certified staff.
STOP
Hazard
Possible consequences: dead or
severe injuries
Dangerous situation
Possible consequence: damage
to the drive of the environment
Wear hearing protection
Wear eye protection
Hazard Situation
Possible consequences: slight or
mild injuries
Safety first
Safety is important for you and other people. For the protection of you and others, we have several
warnings in this manual and on the product. Please always read carefully and follow the instructions.
A GLOBE Silencer is neccessairy for optimal reach of maximum power. Not instal-
ling a GLOBE Silencer will increase the risk of hearing damage, motor malfunctions
or loss of power. It is also essential that an FRL unit is incorporated into the airline to
prevent motor malfunctions. Our silencers and FRL units are designed specifically for
our motors to ensure maximum service life.

4 · GLOBE RM610 PISTON AIR MOTOR MANUAL| INCLUDING AUXILIARIES
Installation
Correct installation is your responsibility! Make sure you have the proper installation conditions.
Note! Damage by lack of lubrication will occur if motors are mounted shaft up or at an angle.
Please consult GLOBE Airmotors BV for other mounting options.
Note! When first running the motor some light oil should be injected into the inlet connection to
ensure adequate lubrication until the air line lubrication is established.
Install proper guard around the output shaft if needed.
WARNING - Injury hazard
Wear eye protection: Airflow from product may contain solid or liquid materials that can
result in eye or skin damage.
Failure to follow these instructions can result in serious injury or property damage.
In order to guarantee the maximum performance and service life of these motors it is essential that
the following points are strictly observed and obeyed. All the information in this chapter is also valid
in case a hand control valve (HCV) or remote control valve (RCV) is fitted to the motor or supplied
loose.
Installation | Motor & Valve
A GLOBE Silencer is neccessairy for optimal reach of maximum power. Not instal-
ling a GLOBE Silencer will increase the risk of hearing damage, motor malfunctions
or loss of power. It is also essential that an FRL unit is incorporated into the airline to
prevent motor malfunctions. Our silencers and FRL units are designed specifically for
our motors to ensure maximum service life.

· 5GLOBE RM610 PISTON AIR MOTOR MANUAL| INCLUDING AUXILIARIES
Installation Mounting positions
The motor is normally mounted in a horizontal position with the filler / breather plug towards the top
(Fig. 1) It may also be mounted with the shaft vertically downwards (Fig. 2). As supplied the motors
have been run up and tested using protective oil and then drained for transit. It is vital that each
motor is re-filled to the correct oil level as shown below. The RM110 - 310 motors have a dipstick
for vertical mounting (Fig. 2) and the lower mark on this dipstick provides the oil level. Oil levels are
achieved on motors in the horizontal position by filling to the plugs marked 60 (RM110-410 models)
and plug 26 (fitted in housing 3 RM510-610 models). (numbers indicate parts on exploded view)
The vertical oil level position for the RM410, RM510 and RM610 motors is a combined horizontal
drain and vertical level plug (part number 26) To fill motors with oil remove the combined breather
and oil filler plug part number 46. Ensure breatherplug is in the vertical position. It may be neces-
sary to fit an elbow between the breather plug and the motor (see Fig. 2).
Fitting
Mount motor in operating position. Check oil level, (as seen on Fig. 1). Before connecting to the
air supply blow out the air lines to remove any loose scale, swarf or abrasive dust which may be
present. Remove the red plastic dust-caps and the ‘O’ ring seal (45). For unidirectional operation
check the required direction of rotation and connect the air supply line to the appropriate port on the
inlet / exhaust adaptor plate (72) leaving the other port open or pipe downwards if exposed to the
atmosphere. The motor should not be allowed to race. Always operate within the catalogue speed
curves.
It’s important that no dust or debris can accumulate at the output shaft. This may
damage the shaft seal. The GLOBE Piston Motor is only allowed in horizontal
position or shaft pointing vertical downwards. It is not allowed for the shaft to point
in any angle upwards.

6 · GLOBE RM610 PISTON AIR MOTOR MANUAL| INCLUDING AUXILIARIES
Air Inlet
The motor is normally supplied with inlet / exhaust adaptor plate (72). All motors are reversible.
Mounting to construction
»Mount the unit to the construction. Care should be taken, when fitting drive components to the
shaft, that excessive force is not used. This will upset the shaft alignments which has been kept to a
minimum in order to give high motor performance.
»Use the proper sized fasteners.
»Axial loads must be kept to a minimum.
Maximum Working Pressure 8 bar - 120 psi
The air supply must be clean and free from moisture. An air line filter and mist lubricator should be
incorporated in the air supply line, located immediately before the motor. If the rated performance of
the motor is to be obtained all valves and pipework must be of adequate size. Valves should be
sited as close as possible to the motor. For short pipe runs e.g. up to 2 meters the supply line should
be the same size as the motor ports and larger for longer runs.
Use a puller to remove pulleys, pinions and couplings. Check if the tension on
the belt pulley matches the specifications of the manufacture. Do not exceed the
maximum radial and axial forces on the shaft. If the motor shaft is connected to the
part to be driven without a coupling, check that the radial offset and axial force
effect will not cause problems.
Do not exceed the maximum radial and axial forces on the shaft.
Use the proper size fasteners.
Use a puller to remove pulleys, pinions and couplings.
STOP

· 7GLOBE RM610 PISTON AIR MOTOR MANUAL| INCLUDING AUXILIARIES
»Air supply to the motor should always be
taken from non-hazardous area.
»Remove the plastic shipping plugs from the
ports. Save the plugs for the future, during
shutdown.
»Please make sure that the temperature of the
air used for air supply to the air motor don’t
exceed the following temperatures, -20°C to
+40°C.
»Install a filter (64 micron) to make sure the air
is clean and dry and install an air pressure
regulator to control motor speed and flow
control for speed regulation.
»A lubricator must be placed inside the main
air line near the motor. The lubricator unit
should have a bowl with enough oil for ope-
ration and should allow the user to control
the amount of oil drop per minute going
to the motor. Check air line oil every time
before starting. Air motor should be supplied
with oil of a viscosity of 32. This type of oil is
flammable at a temperature of 218°C.
»Air quality should meet ISO 8573-1:2010
class 4 for solid particles and ISO 8473-
1:2010 class 3 for water.
»For the most efficient power and control of
speed, all valves and the air lines should be
the same size as the air connections of the
motor. If the valves, air lines and other con-
nections have a longer distance than 2m (6
feet) of the motor we advise one size bigger.
»Before final connection to the motor, clean the
compressed air connection with low pressure
air to remove any dirt inside the line before
connecting to the ports of the air motor.
»When sillencers are installed, ensure that
condensation cannot run back into the motor
port. Mount the air motor with silencer point-
ed down or make extra piping on the silencer.
»If the motor unit is not used for a longer
period it is advisable to store the unit indoors
remove the silencer and plug the exhaust
port. See also shut down and long storage at
maintenance.
»Make sure that on all ports of the motor and/
or valve an air line or silencer is mounted,
appropriate to the situation.
Air supply

8 · GLOBE RM610 PISTON AIR MOTOR MANUAL| INCLUDING AUXILIARIES
Air line filtration
»Use a 64 micron air filter
»The air line filter should be drained regu-
larly and the element examined for signs of
clogging.
»Air quality should meet ISO 8573-1:2010
class 4 for solid particles and ISO 8473-
1:2010 class 3 for water.
Air line lubrication
»The air line lubricator should be replenished
when needed and set to give the following
required drop rate/min:
Drop rate/min
Motor Continuous Operation Intermittent Operation
RM110 3-4 6-8
RM210 4-5 8-10
RM310 5-6 10-12
RM410 6-8 12-16
RM510 6-8 12-16
RM610 8-10 16-20
»For normal ambient temperatures 0°C to 32°C. Use oil with viscosity VG32.
»For extremes of ambient temperature consult the manufactures.
Recommended Lubricants
For normal ambient temperature (0-32 deg. C.)
Brand Crankcase Air line
Shell TELLUS S2 VX100 TELLUS S2 A32
B.P. ENERGOLHLP-HM100 ENERGOL HLP-HM32
Esso NUTO H.100 -
Regent REGAL PE.RO -
Castrol HYSPIN AWH-M100 HYSPIN AWS 32
Mobil - ALMO 524
Texaco - RANDO 32
For extremes of ambient temperatures consult GLOBE
Lubricating oil capacities
Horizontal 75ml Vertical 150ml
Use a good quality hydraulic oil with a viscosity of around 100cSt (460SSU) at 40°C (104°F)

· 9GLOBE RM610 PISTON AIR MOTOR MANUAL| INCLUDING AUXILIARIES
Installation | Brake
Correct installation is your responsibility! Make sure you have the proper installation conditions.
Install proper guard around the output shaft if needed.
WARNING - Injury hazard
Wear eye protection: Airflow from product may contain solid or liquid materials that can
result in eye or skin damage.
Failure to follow these instructions can result in serious injury or property damage.
In order to guarantee the maximum performance and service life of these motors it is essential that
the following points are strictly observed and obeyed.
It’s important that no dust or debris can accumulate at the output shaft. This may
damage the shaft seal. The GLOBE Piston Motor is only allowed in horizontal position
or shaft pointing vertical downwards. It is not allowed for the shaft to point in any angle
upwards.

10 · GLOBE RM610 PISTON AIR MOTOR MANUAL| INCLUDING AUXILIARIES
Mounting to construction
»Mount the brake to the construction. Care should be taken, when fitting drive components to the
shaft, that excessive force is not used. This will upset the shaft alignments which has been kept to a
minimum in order to give high motor performance.
»The brake is pre-set to the maximum holding torque needed at the operating pressure of the
customer. The brake will not be released when the motor is running at a lower pressure than the
operating pressure given by the customer prior to delivery.
»Make sure that the air is dry and filtered with an air filter of 64 micron or better.
»The brake must be mounted to a GLOBE Piston Airmotor of equivalent size (for instance: RM110
Brake on RM110 Motor) including the correct piping and control valves supplied by GLOBE.
Do not exceed the maximum radial and axial forces on the shaft.
Use the proper size fasteners.
Use a puller to remove pulleys, pinions and couplings.
STOP

· 11GLOBE RM610 PISTON AIR MOTOR MANUAL| INCLUDING AUXILIARIES
Operation
WARNING - Injury hazard
Wear eye protection: Air stream from product may contain solid or liquid materials that
can result in eye or skin damage.
Failure to follow these instructions can result in serious injury or property damage.
Wear hearing protection: The noice level from the air motor may exceed 85 db (A)
Do not use combustible gases to drive this air motor
Correct operation is your responsibility! Make sure you have the proper operation conditions.
Operation | Motor & Valve
A GLOBE Silencer is neccessairy for optimal reach of maximum power. Not instal-
ling a GLOBE Silencer will increase the risk of hearing damage, motor malfunctions
or loss of power. It is also essential that an FRL unit is incorporated into the airline to
prevent motor malfunctions. Our silencers and FRL units are designed specifically for
our motors to ensure maximum service life.

12 · GLOBE RM610 PISTON AIR MOTOR MANUAL| INCLUDING AUXILIARIES
Do not run the air motor at high speeds with no load.
This will result in excessive internal heat that may cause motor damage.
STOP
Allowable speeds for motors (RPM)
RM110 RM210 RM310 RM410 RM510 RM610
Continious 1950 12 0 0 1800 135 0 900 11 0 0
Intermittent 0-2400 0-2400 0-2400 0-2000 0-2000 0-2000
»Check all connections before starting the air
motor. It is your responsibility to operate this
product at recommended speeds, loads and
ambient temperatures (-20°C to +60°C).
»Check if the air line filtration and air line
lubrication is OK. The air line filter should be
drained and/or cleaned regularly and the
filter element examined for signs of clogging.
»The maximum working pressure is 8 bar (120
PSI).
»Clean surface of air motor unit thoroughly of
all dustproofing products, contaminants and
other impurities. Clean only with damp cloth.
»Do not run the air motor at high speeds with
no load. This will result in excessive internal
heat that may cause motor damage.
»The starting torque is less than the running
torque. The starting torque will vary depen-
ding on the position of the pistons in relation
to the air intake port when the motor is being
started.
»During operation be aware if unfamiliar
sounds or vibrations occur. Stop the unit
immediately and investigate the source.
»In case that the motor is exposed to high
vibrations, during operation and when not
in operation, please contact GLOBE. High
vibrations might lead to increased inspection
interval of the bearings.
»The motor may run continuously at speeds up
to the rated running conditions shown in our
performance data sheets. In these sheets the
output power/torque is based on running
conditions with the actual pressure measu-
red at the motor port. Check the allowable
speeds below.
»Advisable is to use an air dryer with set point
of 20 degrees Celsius below lowest ambient
temperature.

· 13GLOBE RM610 PISTON AIR MOTOR MANUAL| INCLUDING AUXILIARIES
»Axial loads must be kept to a minimum.
»Max. radial load midway along shaft as shown in graph below:
»Check intake filter and silencer after the first 100 hours of operation.
»Clean filters and determine how frequently filters should be checked during future operation.
The oil level in the motor casing must be maintained. The frequency of replenishment
will depend on the application and usage. The motor case should be drained and
refilled after 25 hours of initial running and every 200 hours thereafter or sooner if
found necessary e.g. (contamination of oil by water from the air line.)
STOP
Allowable Radial Loads
RM110 RM210 RM310 RM410 RM510 RM610
N445 890 1330 1330 6500 6500
LBF 100 200 300 300 14 61 14 61
Air line filtration
»Use a 64 micron air filter
»The air line filter should be drained regu-
larly and the element examined for signs of
clogging.
»Air quality should meet ISO 8573-1:2010
class 4 for solid particles and ISO 8473-
1:2010 class 3 for water.
Air line lubrication
»The air line lubricator should be replenished
when needed and set to give the following
required drop rate/min:
»For normal ambient temperatures 0°C to 32°C. Use oil with viscosity VG32.
»For extremes of ambient temperature consult the manufactures.
Drop rate/min
Motor Continuous Operation Intermittent Operation
RM110 3-4 6-8
RM210 4-5 8-10
RM310 5-6 10-12
RM410 6-8 12-16
RM510 6-8 12-16
RM610 8-10 16-20

14 · GLOBE RM610 PISTON AIR MOTOR MANUAL| INCLUDING AUXILIARIES
Performance regulation
2. Air flow regulation
Air flow regulation is the best way to reduce
the output speed without the loss of torque.
The air flow can be regulated with a throttling
device. By throttling, the starting torque
remains essentially the same but the torque
curve is steeper. This means that under the
same load fluctuation, the speed fluctuation
is smaller in comparison with the pressure
regulation. There is a distinction made
between the following installation positions:
Exhaust air throttling
The exhaust air throttling is the less optimal
way of throttling relating to the durability
and the air consumption. The advantage of
this method is that the rotational speed can
be regulated constantly in the lower rotation
range. In the border area of the rotation
range, a combination of supply- and exhaust
air throttling should be used. The exhaust
throttling should be used for controlling low
speed of rotation.
Supply air throttling
The supply air throttling generates better
results in relation to the durability, the running
smoothness and the air consumption.
With the regulation of the inlet pressure and the flow rate, the performance can be adapted to the
individual application. This is done by pressure or air flow regulation or a combination of both.
The compressibility of the air generates a dampening effect in all ranges. This allows that the motor
also can be started, while it is loaded. With a load reduction, the motor reacts immediately with an
increase in speed.
0
100 12 0 14 0 160 18 0 200 220 240
1
2
3
4
5
6
Rotation speed
Torque
0
100 12 0 14 0 160 18 0 200 220 240
1
2
3
4
5
6
Rotation speed
Torque
Pressure regulation
Air flow regulation
0
100 12 0 14 0 160 18 0 200 220 240
1
2
3
4
5
6
Rotation speed
Torque
0
100 12 0 14 0 160 18 0 200 220 240
1
2
3
4
5
6
Rotation speed
Torque
Pressure regulation
Air flow regulation
1. Pressure regulation
With pressure regulation the output power
can be adjusted. When the supply pressure is
decreased, the torque and power is reduced
proportionally and the torque curve becomes
flatter. The forces inside the motor are also
reduced, which increases its durability.
For optimal power and speed control, we advise to use the com-
bination of pressure and air flow regulation.

· 15GLOBE RM610 PISTON AIR MOTOR MANUAL| INCLUDING AUXILIARIES
Operational principle RM610 Hand Control Valve
This range of bolt on valves offers very sensitive speed and directional control. One frictional
matched spool and sleeve assembly is offered with two alternative means of actuation.
Configuration
As standard these valves can be supplied with either EQUAL POWER OR BIASED POWER
spools, the latter is suitable for hoisting applications (normal power for lifting - reduced power for
lowering).
The direction of reduced power must be stated when ordering CW or CCW, when viewed on the
output shaft of the motor.
Hand Controlled (HCV) - The control valve spool is operated directly by a lver mechanism.
Speed increase is obtained as the lever is moved in either direction from the centre (neutral) position.
Pressure Drop - Minimal pressure drop will be experienced through the valves, having the effect
of maintaining the output torque whilst reducing the motor output speed by approximately 10-15%
at 6 bar (90 psi) at maximum power. The starting torque remains unaffected.

16 · GLOBE RM610 PISTON AIR MOTOR MANUAL| INCLUDING AUXILIARIES
Operational principle RM610 Remote Control Valve
This range of bolt on valves offers very sensitive speed and directional control. One frictional
matched spool and sleeve assembly is offered with two alternative means of actuation.
Configuration
As standard these valves can be supplied with either EQUAL POWER OR BIASED POWER spools,
the latter is suitable for hoisting applications (normal power for lifting - reduced power for lowering).
The direction of reduced power must be stated when ordering CW or CCW, when viewed on the
output shaft of the motor.
Remotely Controlled (RCV) - This option is usually controlled from a remote position by one
of the PC series or LC2 remote controllers. A variable air pilot signal is applied to either end of
the valve spool, depending on the required direction of motor rotation. The pilot pressure range is
between 1.4 bar (20 psi) and 4.8 bar (70 psi), increased pilot pressure gives increased speed. The
valve is spring centred to neutral.
Pressure Drop - Minimal pressure drop will be experienced through the valves, having the effect
of maintaining the output torque whilst reducing the motor output speed by approximately 10-15%
at 6 bar (90 psi) at maximum power. The starting torque remains unaffected.

· 17GLOBE RM610 PISTON AIR MOTOR MANUAL| INCLUDING AUXILIARIES
WARNING - Injury hazard
Wear eye protection: Air stream from product may contain solid or liquid materials that
can result in eye or skin damage.
Failure to follow these instructions can result in serious (eye) injury or property damage.
Wear hearing protection: The noice level from the air motor may exceed 85 db (A)
Do not use combustible gases to drive this brake
Correct operation is your responsibility! Make sure you have the proper operation conditions.
Operation | Brake

18 · GLOBE RM610 PISTON AIR MOTOR MANUAL| INCLUDING AUXILIARIES
Operating Principle Brake
The brake has a corresponding mounting interface, thus can be directly mounted on the motor. This
brake consists of two spring applied brake shoes (2) pressed against a central hub (1), which is
mounted on the output shaft of the motor. These shoes are released by applying air pressure to the
cylinder / piston assembly (3/4). The brake torque can be varied by means of two spring adjusters
(7).
The brake has a wide range of adjustment to match the requirements of each application (i.e.
torque and air pressure) but it is normally set to hold the motor torque plus 20%. Care must be taken
because it is possible to adjust the brake so tightly that it will not release , and conversely it can be
adjusted to the other extreme and not hold the load. Both adjusters must be screwed equally to the
required setting. If the brake is used within the “running torque plus 20%” range then it is working
within its safety limits and will give exceptional service over a long period of time when correctly
utilized as a parking brake. These conditions of “running torque plus 20%” are broadly similar to the
minimum starting torque of the RM motors at around 4 bar (60 psi) and adjustment to give full lift off
of the brake at around 4 bar (60 psi) will enable the load to be held initially on the brake with the
motor progressively engaging to hold the load as the pressure increases and gradually release the
brake.
Under no circumstances should these parking brakes be offered or used for dynamic braking appli-
cations; they have not been designed to meet the different criteria that apply in these cases.
A
A
5
4
1
2
7
8
6
3
B
B
5
3
1
1Brake wheel
2Brake shoe (2x)
3Brake release piston (2x);
brake force release
4Brake release cylinder; pressure chamber
5Pilot pressure connection
6Brake shoe spring (2x);
brake force actuator
7Brake force adjuster (2x)
8Brake force adjuster locknut (2x)

· 19GLOBE RM610 PISTON AIR MOTOR MANUAL| INCLUDING AUXILIARIES
Circuit A
Applies to braked motors supplied without control valving. The
unit will be fitted with a shuttle valve to allow brake operation
for dual rotation.
Circuit B
Units supplied with hand (HCV) proportional control reversible valve
(C). When the HCV (C) is operated a pneumatic signal will be pas-
sed onto the the shuttle valve (F) and the brake (B) is released.
Circuit C
Units supplied with remote (RCV) proportional control reversible valve (C).
When the RCV is actuated by one of the pilot lines (p2) a pneumatic signal
will be passed onto the shuttle valve (E) and the brake (B) is released.

20 · GLOBE RM610 PISTON AIR MOTOR MANUAL| INCLUDING AUXILIARIES
Range brake Torque
Type Running torque Max. Brake Holding Torque
Nm lbf/Ft. Nm lbf/Ft.
RM110 at 2000 rpm 4,5 Nm 3 5,4 Nm 4
RM210 at 2000 rpm 12 Nm 9 14,4 Nm 10,5
RM310 at 1800 rpm 28 Nm 20 33,6 Nm 25
RM410 at 1600 rpm 55 Nm 40 66 Nm 48,5
RM510 at 1100 rpm 125 Nm 92 150 Nm 110,5
RM610 at 1500 rpm 125 Nm 92 150 Nm 110,5
Operation
»Before use always remove any sediments on
the surface of the brake before starting-up.
»During operation be aware if unfamiliar
sounds or vibrations occur. Stop the unit
immediately and investigate the source.
»Air quality should meet ISO 8573-1:2010
class 4 for solid particles and ISO 8473-
1:2010 class 3 for water.
»Bear in mind the maximum allowable torque
of the brake. Do not exceed as this may result
slipping and damage of the brake.
The following figure can be used as a guide to using the brake, they are all based around an air
line supply pressure of 5.5 bar (80 psi). In each case the motor running torque has been taken at
the peak power condition of the motor, the rotational speed of the motor varying in each case, this
speed is specified against a particular motor. The maximum brake torque of the brakes is achieved
by applying the procedure described under Load Adjustment in this chapter.
Wear check
Check every 200 operating hours the thickness of the brake shoe liners. If the rivet heads which are
holding the shoes on the brake shoe assembly – item 26 – are within 0.5 mm of the surface new
brake shoe assemblies need to be fitted.
This manual suits for next models
2
Table of contents
Other Globe Engine manuals
Popular Engine manuals by other brands

Briggs & Stratton
Briggs & Stratton 90000 series Operator's manual

Toyota
Toyota 1CD-FTV manual
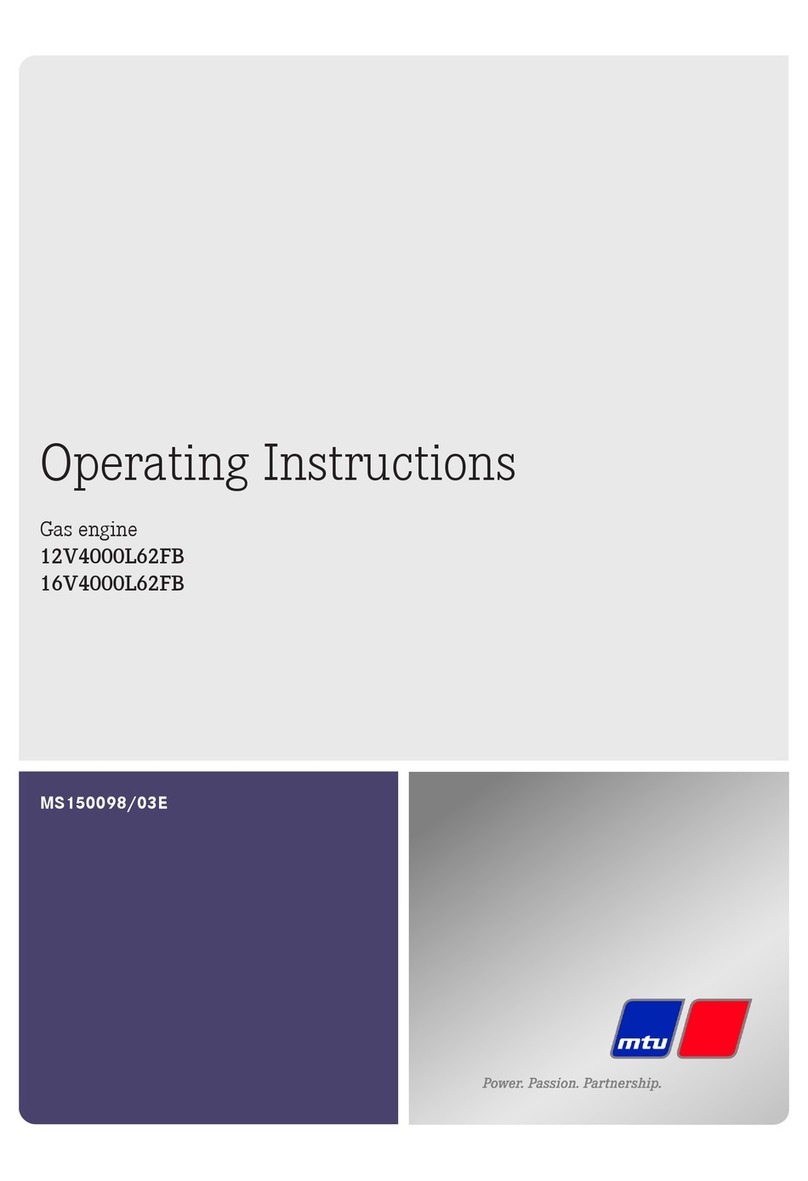
MTU
MTU 12V4000L62FB operating instructions
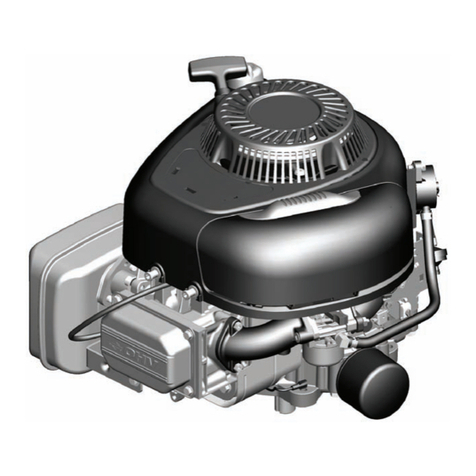
Briggs & Stratton
Briggs & Stratton Power Built Intek I/C 210000 Operator's manual
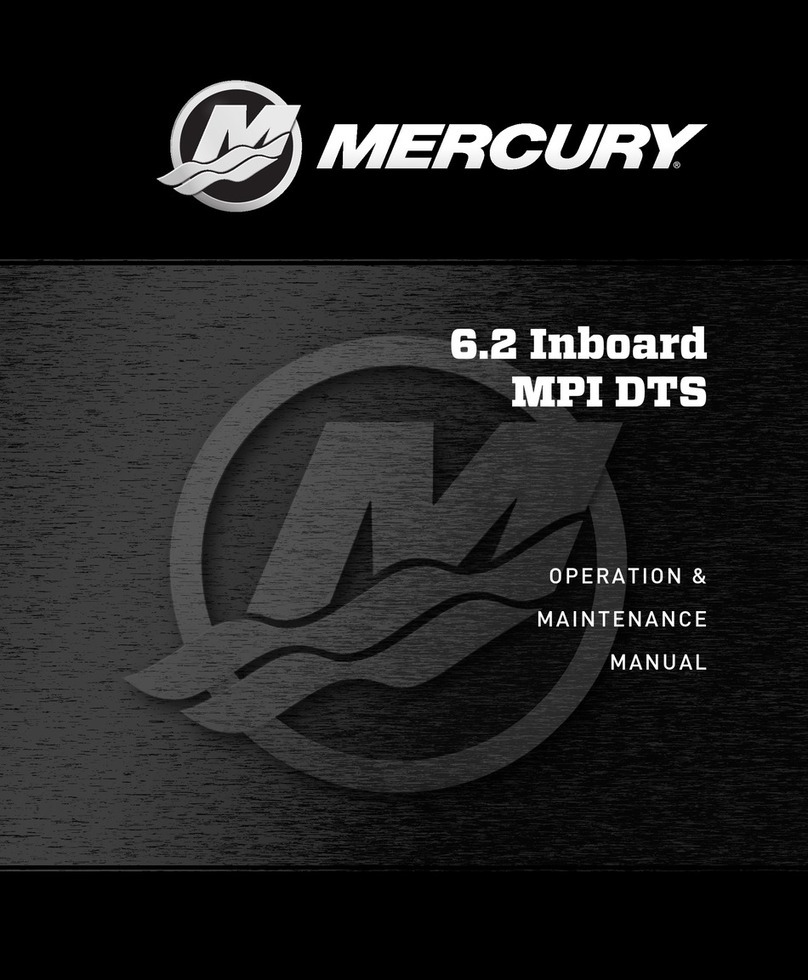
Mercury
Mercury 6.2 Inboard MPI DTS Operation & maintenance manual
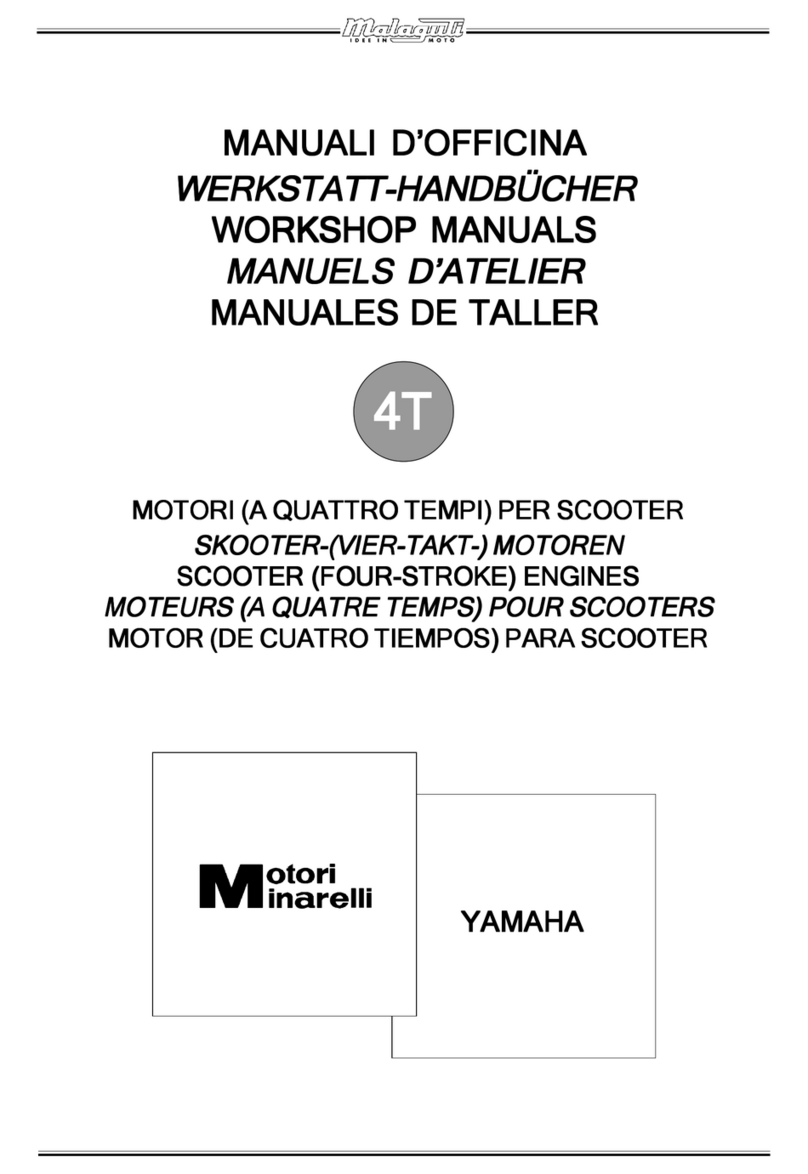
Malaguti
Malaguti 4T Series Workshop Manuals