GOM ATOS COMPACT SCAN 5M User manual

GOM mbH
Mittelweg 7-8
D-38106 Braunschweig E-Mail: info@gom.com
Germany www.gom.com
Tel.: +49 (0) 531 390 29 0 Fax: +49 (0) 531 390 29 15
atos_cs_rev01_en_rev-c. 2012-09-03
ATOS
User Manual - Hardware
ATOS COMPACT SCAN 5M, 2M
With Camera Supports 300 mm, 500 mm and SO
COMPACT
SCAN

Important Notes
Page 2 (40)
atos_cs_rev01_en_rev-c 2012-09-03
Important Notes
Symbols
In this user manual the following standard signal words may be
used:
This label points to a situation that might be
dangerous and could lead to serious bodily
harm or to death.
This label points to a situation that might be
dangerous and could lead to light bodily harm.
This label points to a situation in which the
product or an object in the vicinity of the product
might be damaged.
This label indicates important application notes
and other useful information.
Safety and Health Hazard Notes
•Do not look directly into the laser light with optical instru-
ments.
The used laser meets laser class 1 M according to DIN EN
60 825-1.
•Do not use equipment connected to AC power during heavy
thunderstorms. Due to voltage variations and transient volt-
ages in the low-voltage network, malfunctions and danger-
ous voltages between housing and other components may
occur.
•In extreme positions, stands with horizontal extension arms
may fall over. Avoid such positions. Use the product only on
a safe and steady ground.
•When measuring large objects, make sure you comply with
the respective valid accident prevention regulations.
•Do not use the ATOS system in explosion-hazardous areas!
•Operate the equipment only with the operating voltages
printed on the housing. Using an incorrect operating voltage
may cause malfunctions or the risk of fire.
•
Artificial optical radiation (projector light). When operating,
do not look into the light source for a longer time. Directly
looking into the light source may be harmful for your eyes!
(See also 2 Technical Data).
•Check cables and, if damaged, replace them by all means.
Protect the cables from mechanical load (squeezing, ten-
sion, etc.). Damaged cables may cause short-circuits and
the risk of fire.
•AC power connection of the unit must comply with the valid
regulations of the respective countries.
•Replace fuses only with components having the same spec-
ifications.
•During scanning, stroboscopic light patterns are generated.
These light patterns might cause epileptic seizures for sen-
sitive persons.
•Never unplug or connect cables during operation!
•The devices must not come into contact with water. For
cleaning, use a moist cloth but first disconnect the power
plug.
•The ambient temperature must be between +5 and +40 °C.
Make sure no rapid temperature variations occur that might
cause condensation.
•The housing may only be opened when no voltage is ap-
plied.
•Do not stick any strange objects into the housing.
•Never cover the venting slots.
•Never operate the sensor without the corresponding air fil-
ter, see section 11.
Legal Notes
No part of this publication may be reproduced in any form or by
any means or used to make any derivative work (such as
translations, transformations or adaptations) without the prior
written permission of GOM.
GOM reserves the right to revise this publication and to make
changes in content from time to time without obligation on the
part of GOM to provide notification of such revision or change.
GOM provides this manual without warranty of any kind, either
implied or expressed, including, but not limited, to the implied
warranties of merchantability and fitness for a particular pur-
pose.
GOM may improve or change the manual and/or the product(s)
described herein at any time.
Copyright © 2011
GOM mbH
All rights reserved!

Table of Contents
Page 3 (40)
atos_cs_rev01_en_rev-c 2012-09-03
Table of Contents
Important Notes __________________________________ 2
Symbols_______________________________________________ 2
Safety and Health Hazard Notes ___________________________ 2
Legal Notes ____________________________________________ 2
Table of Contents_________________________________ 3
1. Introduction _______________________________ 5
2. Measuring System Types ____________________ 5
2.1 Types for Stationary Operation_____________________ 5
2.2 Types for Mobile Operation________________________ 6
3. Sensor Types ______________________________ 7
3.1 Sensor Types and Technical Data __________________ 7
4. Information About the Sensor ________________ 8
4.1 Sensor Configurations____________________________ 9
4.2 Definition of Terms Referring to ATOS COMPACT SCAN
300 and 500 ____________________________________ 10
4.3 Definition of Terms Referring to ATOS COMPACT SCAN
SO____________________________________________ 10
5. Lenses___________________________________ 11
5.1 Lenses ________________________________________ 11
6. Standard Control Elements and LED Indicators_ 12
6.1 Web Interface __________________________________ 13
7. Operation of 3D Ball Head___________________ 14
7.1 Positioning of Sensor ___________________________ 14
7.2 Sensor Fixture__________________________________ 14
7.2.1 Mechanism of Sensor Fixture_______________________ 14
7.2.2 Mounting Direction of Sensor on Locking Mechanism ____ 15
7.2.3 Fixture of Sensor on Locking Mechanism _____________ 16
8. Sensor Setup _____________________________ 17
8.1 General _______________________________________ 17
8.2 Measuring Volume ______________________________ 17
8.3 Changing the Camera Positions (Step by Step) ______ 17
8.3.1 Initial Situation: Sensor in Position 300 _______________ 18
8.3.2 Loosen Cameras from Support _____________________ 18
8.3.3 Remove Camera Screws and Loosen Support _________ 19
8.3.4 Remove Camera Support 300 ______________________ 19
8.3.5 Insert Camera Support SO _________________________ 20
8.3.6 Fix Camera Support SO ___________________________ 20
8.3.7Insert Camera Screws ____________________________ 21
8.3.8 Fix Cameras ____________________________________ 21
8.3.9 Changed Sensor with Camera Support SO ____________ 22
8.4 Set Up Sensor with ATOS V7 Software _____________ 23
8.4.1 Camera Angle___________________________________ 24
8.4.2 Adjust the Laser Pointers __________________________ 25
Steps to adjust the laser pointers ________________________25
9. Wireless Remote Control ___________________ 26
9.1 Preparing the Remote Control ____________________ 26
9.2 Explanation of the Function Keys__________________ 27
10. Sensor Calibration_________________________ 28
10.1 How to Handle Calibration Objects_________________ 28
10.2 Calibration Conditions ___________________________ 29
10.2.1 When is Calibration Required?______________________ 29
10.2.2 Prerequisites____________________________________ 29
10.3 Calibration Using Calibration Panel CP 40___________ 29
10.3.1 Handling Instructions for Calibration Panel CP 40 _______ 30
10.3.2 Loading the Calibration Data _______________________ 31
10.3.3 Preparing the Calibration Process ___________________ 31
10.3.4 Calibration Process_______________________________ 32
10.3.5 Calibration Result ________________________________ 32
10.4 Calibration Using Calibration Cross CC 30 __________ 33
10.4.1 Handling Instructions for Calibration Cross CC 30 _______ 34
10.4.2 Entering Calibration Data into ATOS _________________ 34
10.4.3 Preparing the Calibration Process ___________________ 35
10.4.4 Calibration Process_______________________________ 35
10.4.5 Calibration Result ________________________________ 36
10.4.6 Quick Calibration_________________________________ 36
11. Checking and Cleaning the Air Filter __________ 37
11.1 Removing the Air Filter __________________________ 37
12. Cabling, Network Port_______________________38
12.1 Cabling________________________________________ 38
12.1.1 Cabling with Laptop ______________________________ 38
12.1.2 Cabling with 19" PC ______________________________ 39
12.2 Network Port ___________________________________ 40
12.2.1 Notes for Network Administrators ____________________ 40

Table of Contents
Page 4 (40)
atos_cs_rev01_en_rev-c 2012-09-03

Introduction
Types for Stationary Operation
Page 5 (40)
atos_cs_rev01_en_rev-c 2012-09-03
1. Introduction
This user information is intended for qualified personnel who is not or
just a little familiar with the coordinate measurement technique but
who has basic PC knowledge (windows-based programs and operat-
ing systems). This user information is configured to the transfer of
knowledge of system installation, sensor settings, changing the cam-
era support and other hardware relevant information.
This user information is divided into the following sections:
•The first page informs about important safety aspects.
•Section 1 - Introduction
•Section 2 and 3 describe the system variants.
•Section 4 contains general information about the sensor.
•Section 5 informs about how to handle the lenses.
•Section 6 describes the control elements and LED indicators of the
sensor.
•Section 7 describes the control elements of the optional 3D pan and
tilt head.
•Section 8 describes the setup of the sensor.
•Section 9 explains the wireless remote control.
•Section 10 describes the calibration of the sensor.
•Section 11 informs about cleaning the air filter.
•Section 12 shows the cabling of the system as laptop and 19" PC
variants and contains notes for network administrators.
2. Measuring System Types
ATOS COMPACT SCAN systems are available in connection with ex-
tensive equipment. The two following versions only show a selection
of possibilities.
2.1 Types for Stationary Operation
Stationary System

Types for Mobile Operation
Measuring System Types
Page 6 (40)
atos_cs_rev01_en_rev-c 2012-09-03
•ATOS sensor with stereo cameras, fringe projector, controller and
power supply.
•Stand for secure and steady hold of the ATOS sensor.
Please only use stands which are released by GOM for this sen-
sor type. Otherwise the stand with the sensor may fall over!
•Calibration panel for high-precision calibration.
•High-performance PC system with Microsoft Windows 7 operating
system and separate network interface card for the Gigabit data
link.
The factory settings of the separate network interface card are op-
timized for the Gigabit data link and must not be changed! For
more information see section 12.2.1.
•ATOS application software (Windows) as of V7.5
2.2 Types for Mobile Operation
Mobile ATOS COMPACT SCAN - Out-of-the-box system
•Transport case
•Carbon fiber tripod stand and foldable calibration cross to guaran-
tee high mobility
•Manual rotation table
When using the carbon fiber tripod stand it may probably fall over!
•Foldable calibration cross
When calibrating using the foldable calibration cross, the highest
possible accuracy will not be achieved! For more information see
section 9.

Sensor Types
Sensor Types and Technical Data
Page 7 (40)
atos_cs_rev01_en_rev-c 2012-09-03
3. Sensor Types
This user manual describes two types of ATOS COMPACT SCAN
sensors. Mainly, the sensors are constructed similarly and differ in the
cameras and in the length of the camera support.
3.1 Sensor Types and Technical Data
System
ATOS COMPACT SCAN 2M
Rev. 01
ATOS COMPACT SCAN 5M
Rev. 01
Measuring points per individual
scan
or camera resolution
approx. 2 000 000 points
1624 x 1236 pixels
approx. 5 000 000 points
2448 x 2050 pixels
Camera position 500
Measuring volume:
250 x 190 x 190 mm
to
1000 x 750 x 750 mm
300 x 230 x 230 mm
to
1200 x 900 x 900 mm
Measuring point distance:
156 - 615 µm
124 - 481 µm
Camera position 300
Measuring volume (in mm):
125 x 90 x 90 mm
to
500 x 380 x 380 mm
150 x 110 x 110 mm
to
600 x 400 x 400 mm
Measuring point distance:
75 - 309 µm
62 - 250 µm
Camera position SO
Measuring volume (in mm):
35 x 30 x 20 mm
to
125 x 90 x 90 mm
40 x 30 x 20 mm
to
150 x 110 x110 mm
Measuring point distance:
21 - 79 µm
17- 63 µm
Transfer of image and control
signals
Using a Gigabit data link via an Ethernet interface (GigE)
Projector light
Artificial optical radiation, blue (400-500 nm)
(Medium risk according to DIN EN 62471,
issue March 2009, when looking into the light source)
Ambient conditions
+5 °C to +40 °C
(non-condensing)
Voltage range (typical)
90 - 240 V, 50 - 60 Hz
Power consumption
Typically 120 W
max. 200 W
Power Factor Correction
≥ 95%
Max. cable length between
sensor and PC, laptop
10 m
Application software,
Operating system
ATOS v7.5 and higher for Windows 7
For further information see http://www.gom.com

Sensor Types and Technical Data
Information About the Sensor
Page 8 (40)
atos_cs_rev01_en_rev-c 2012-09-03
4. Information About the Sensor
Each configured ATOS sensor, in scan direction, has defined 3D areas
within which a measuring object can be scanned. In the following,
such a 3D area is called "measuring volume" (MV).
The measuring volume determines the distance between sensor and
measuring object and the set of lenses to be used.
In practice, depending on the measuring task, different measuring
volumes might be required.
Ideally, you have camera and projector lenses that are preadjusted to
your measuring volume. In this case, you need to perform no or just
very few steps for adjusting the sensor.
A complete sensor setup is only required if the corresponding set of
lenses has never been adjusted before or is decalibrated (wrong ad-
justments).
For a complete sensor adjustment, you need to adjust the angle rela-
tions of the cameras and set the focus and aperture of the lenses.
Then, the complete system is calibrated by means of calibration
panels or calibration crosses. If the measuring volume is adjusted
successfully by calibration, you may start a measuring project.
The sensor adjustment is supported by the software. The software de-
termines all necessary parameter settings.
In order to achieve large, medium and small measuring volumes, the
sensors can be adapted to the camera positions SO (Small objects)
for small measuring volumes, 300 for medium measuring volumes and
500 for large measuring volumes, see table 4.1, with the help of ex-
changeable camera supports.

Information About the Sensor
Sensor Configurations
Page 9 (40)
atos_cs_rev01_en_rev-c 2012-09-03
4.1 Sensor Configurations
Sensor
Camera position
Name
Measuring volume
(MV)
(L x W x H) in mm
Measuring point dis-
tance
Recommended refer-
ence points mm Ø
Measuring distance
Camera angle
Focal length
camera lenses
Focal length
projector lens
Standard calibration objects,
Alternative calibration objects
(CP = Panel, CC = Cross)
[mm]
[mm]
[mm]
[mm]
[mm]
[°]
[mm]
[mm]
ATOS COMPACT SCAN 5M
Rev. 01
500
1
200
1200 x 900 x
900
0.481
8
1170
24
8
6
CP40/MV1000, CC30/MV1000x1000
800
800 x 600 x 600
0.325
3
1170
24
12
8
CP40/MV700, CC30/MV700
600
600 x 450 x
450
0.243
3
1170
24
17
12
CP40/MV560, CC30/MV500x500
300
300 x 230 x
230
0.124
1.5
1170
24
35
23
CP40/MV320, CC30/MV300
300
600
600 x 450 x
450
0.250
3
590
25
8
6
CP40/MV560, CC30/MV500x500
300
300 x 230 x
230
0.124
1.5
590
25
17
12
CP40/MV320, CC30/MV300
150
150 x 110 x
110
0.062
0.8
590
25
35
23
CP40/MV170
SO
150
150 x 110 x
110
0.063
0.8
420
23
17
16
CP40/MV170
70
70 x 50 x
50
0.029
0.4
420
23
35
28
CP40/MV100
40
40 x 30 x
20
0.017
0.4
420
23
50
50
CP40/MV60
ATOS COMPACT SCAN 2M
Rev. 01
500
1000
1000 x 750 x
750
0.615
8
1170
24
8
6
CP40/MV1000, CC20/MV1000x800
500
500 x 380 x
380
0.308
5
1170
24
17
12
CP40/MV560, CC20/MV500x400
250
250 x 190 x
190
0.156
3
1170
24
35
23
CP40/MV320, CC30/MV300
300
500
500 x 380 x
380
0.309
5
570
25
8
6
CP40/MV560, CC20/MV500x400
250
250 x 190 x
190
0.153
3
570
25
17
12
CP40/MV320, CC30/MV300
125
125 x 90 x
90
0.075
1.5
570
25
35
23
CP40/MV170
SO
125
125 x 90 x
90
0.079
1.5
420
23
17
17
CP40/MV170
60
60 x 50 x
50
0.037
0.8
420
23
35
35
CP40/MV60
35
35 x 30 x 20
0.021
0.4
420
23
50
50
CP40/MV38
Definitions:
Camera position 500 Camera position 300 Camera position SO

Definition of Terms Referring to
ATOS COMPACT SCAN 300 and 500 Information About the Sensor
Page 10 (40)
atos_cs_rev01_en_rev-c 2012-09-03
4.2 Definition of Terms Referring to
ATOS COMPACT SCAN 300 and 500
4.3 Definition of Terms Referring to ATOS COMPACT SCAN SO
Camera angle
Measuring distance (from ATOS label
to the center of the measuring volume)
Camera lens right R
Camera lens left L
Center of the measuring volume
Height H(measuring volume)
Width W(measuring volume)
Length L(measuring volume)
Projector lens P
Camera position (approx. distance in mm)
Camera angle
Measuring distance (from ATOS label
to the center of the measuring volume)
Camera lens right R
Camera lens left L
Center of the measuring volume
Height H(measuring volume)
Width W(measuring volume)
Length L(measuring volume)
Projector lens P
Camera position (approx. distance in mm)

Lenses
Lenses
Page 11 (40)
atos_cs_rev01_en_rev-c 2012-09-03
5. Lenses
The lenses shown in this example may, in some cases, differ from
those delivered in practice. Therefore, the statements made here have
to be used correspondingly.
All lenses are marked with L (left) or R (right) or P (projector). Left and
right are defined from the sensor view in normal operating position.
Never switch on the sensor if the projector lens still is equipped with
the lens cap! Due to the high light output, the lens cap and the pro-
jector lens may be damaged!
5.1 Lenses
For the projector lenses, the aperture value is fixed and cannot be
changed.
Select a set of lenses matching the required measuring volume and
camera positions (e.g. SO, 300, 500), and screw it into the cameras
and the projector.
To avoid getting dirt into the cameras and the projector, always equip
the devices with lenses or blind caps, even when they are switched
off. When changing the lenses, fix the new lenses in place immedi-
ately.
Screw in the lenses carefully by hand, lock the focus locking ring, if
necessary, to ensure screwing in without any problems.
Camera lens left L
Camera lens right R
Projector lens P
Screw thread; tighten carefully by hand in
the housing!
While doing so, lock focus locking ring!
Focus locking ring with hex socket head
locking screw
Focal length.
In this example 17 mm.
Aperture setting ring with manual locking screw. If no
screw exists, locking is done by means of three hex
socket head screws in the aperture ring. Note: In the
example shown, aperture value 11 means aperture
closed and aperture value 1.4 means aperture open.

Lenses
Standard Control Elements and LED Indicators
Page 12 (40)
atos_cs_rev01_en_rev-c 2012-09-03
6. Standard Control Elements and LED Indicators
a
•
Shows green light if the sensor is ready for operation.
•Shows orange light while the operating system of the sensor starts.
•Shows red light in the moment of being switched on or in case of a failure. You
will find additional status information on the Web interface of the sensor, see 6.1.
b
•Yellow LED, illuminates in case of active Gigabit transmission at interface CAM L.
c
•Green LED, illuminates in case of data transmission at interface CAM L.
d
•
Power switch to switch the sensor on and off.
a
b
c
d

Standard Control Elements and LED Indicators
Web Interface
Page 13 (40)
atos_cs_rev01_en_rev-c 2012-09-03
6.1 Web Interface
You reach the Web interface in the ATOS software under Help ►Sys-
tem Analysis ►ATOS Sensor ►Analyze System ►Sensor
Status ►...
Prerequisite:
The sensor must be switched on and connected to the computer.
The ATOS software is running but the sensor is not initialized ( )!
Start screen of the Web interface
Alternatively, you may also use the installed Firefox web browser. In
factory-adjusted measuring computers, a corresponding bookmark is
available.

Positioning of Sensor
Operation of 3D Ball Head
Page 14 (40)
atos_cs_rev01_en_rev-c 2012-09-03
7. Operation of 3D Ball Head
7.1 Positioning of Sensor
Always position the sensor using both of your hands (see figure be-
low), one hand at one of the sensor handles and the other hand at
the locking screw of the 3D ball head.
Only this way you can position the sensor safely.
Adjustment of sensor on stand
7.2 Sensor Fixture
7.2.1 Mechanism of Sensor Fixture
A wedge plate eholds the sensor in the locking mechanism f.
Clamped sensor fixture (front view)
Always make sure that the wedge plate ereally holds the sensor
correctly and firmly in the locking mechanism f !
e
f
f

Operation of 3D Ball Head
Sensor Fixture
Page 15 (40)
atos_cs_rev01_en_rev-c 2012-09-03
Functional principle of the clamping mechanism
You may adjust the clamping force any time with the knurled thumb
screw g.
7.2.2 Mounting Direction of Sensor on Locking Mechanism
Mounting direction of sensor
g

Sensor Fixture
Operation of 3D Ball Head
Page 16 (40)
atos_cs_rev01_en_rev-c 2012-09-03
7.2.3 Fixture of Sensor on Locking Mechanism
Steps for fixing the sensor
Loosen the locking lever h, unlock the mechanism using the latch i
and move the sensor with the wedge plate kto the stop.
Clamp the wedge plate again with the help of the locking lever h.
View of a correctly fixed sensor.
h
g
k
k
i
h

Sensor Setup
General
Page 17 (40)
atos_cs_rev01_en_rev-c 2012-09-03
8. Sensor Setup
8.1 General
In order to adjust the sensor, the complete system including the
ATOS software needs to be installed and the sensor must be
equipped with a set of lenses matching the measuring volume and
the camera position. For achieving all camera positions, three differ-
ent camera supports can be used.
Camera position 500 Camera position 300 Camera position SO
For each measuring volume (MV), the set of lenses are factory-
preadjusted.
If you have the respective set of lenses for each measuring volume,
setting up the sensor is easy as you do not need to carry out all the
steps referring to adjusting the focus and aperture!
You always need to perform a complete sensor setup if, for example,
the corresponding set of lenses has never been adjusted before or is
decalibrated.
8.2 Measuring Volume
Use the table in section 4.1 to determine a measuring volume.
You create larger measuring volumes with camera positions 500 and
300 and smaller measuring volumes with camera position SO (see ta-
ble 4.2).
Please check whether the cameras are in the correct position. How to
change the camera positions is described in section 0.
8.3 Changing the Camera Positions (Step by Step)
In the following, we describe how to change the camera distance from
300 to SO.
When you are changing the distance from SO to 300 or when you
are changing to camera position 500, please proceed corresponding-
ly. All camera supports have identical connecting elements.
The length of the camera connection cables are matched to the
camera support when the system is delivered.
If you received the support for camera position 500 or SO later, the
connection cables might not be long enough. In that case, contact
the GOM support or your local distributor.

Changing the Camera Positions (Step by Step)
Sensor Setup
Page 18 (40)
atos_cs_rev01_en_rev-c 2012-09-03
All camera supports have factory-adjusted stops for the required
camera angles.
Never loosen these stops!
8.3.1 Initial Situation: Sensor in Position 300
ATOS COMPACT SCAN sensor without connection cable (front view)
8.3.2 Loosen Cameras from Support
View from below

Sensor Setup
Changing the Camera Positions (Step by Step)
Page 19 (40)
atos_cs_rev01_en_rev-c 2012-09-03
8.3.3 Remove Camera Screws and Loosen Support
View from below
8.3.4 Remove Camera Support 300
View from below

Changing the Camera Positions (Step by Step)
Sensor Setup
Page 20 (40)
atos_cs_rev01_en_rev-c 2012-09-03
8.3.5 Insert Camera Support SO
Sensor view from below, SO camera support view from top
8.3.6 Fix Camera Support SO
View from below
This manual suits for next models
1
Table of contents
Other GOM Scanner manuals
Popular Scanner manuals by other brands
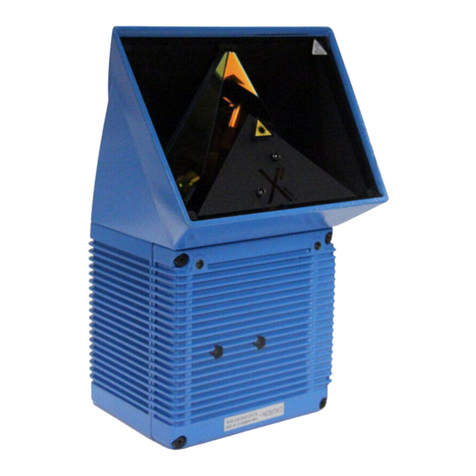
SICK
SICK Omni CLX490 Series operating instructions

Rangevision
Rangevision Smart manual
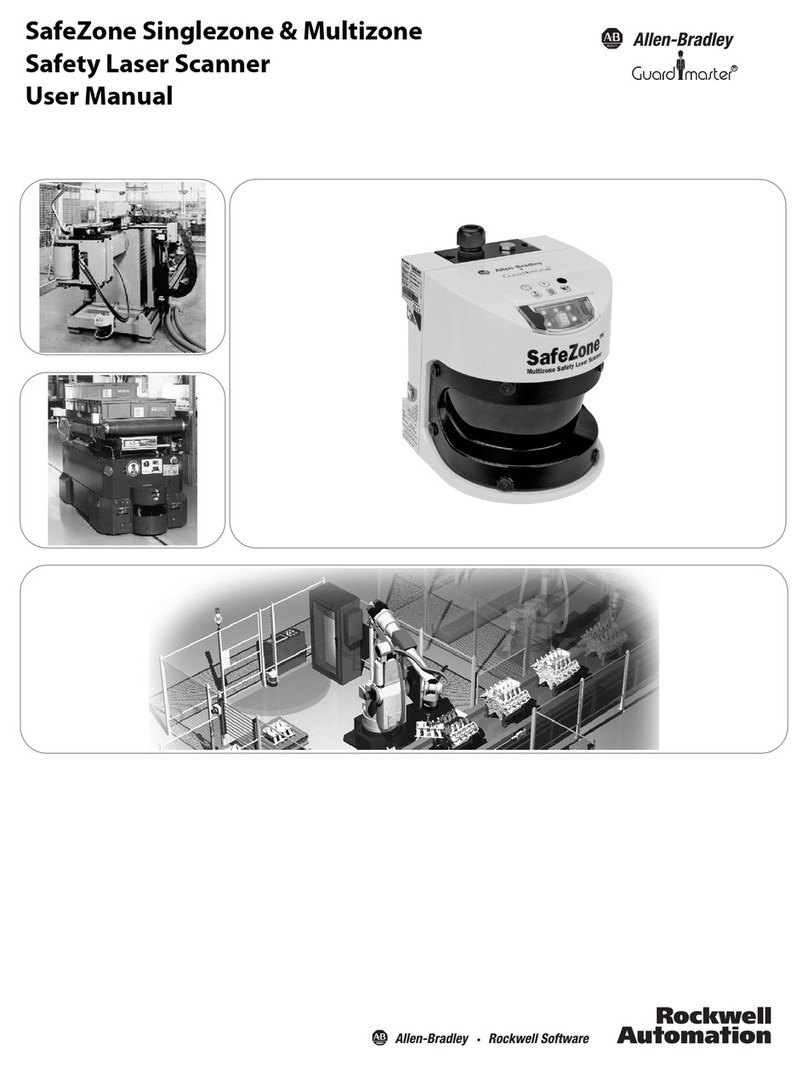
Rockwell Automation
Rockwell Automation Allen-Bradley Guard Master SafeZone user manual
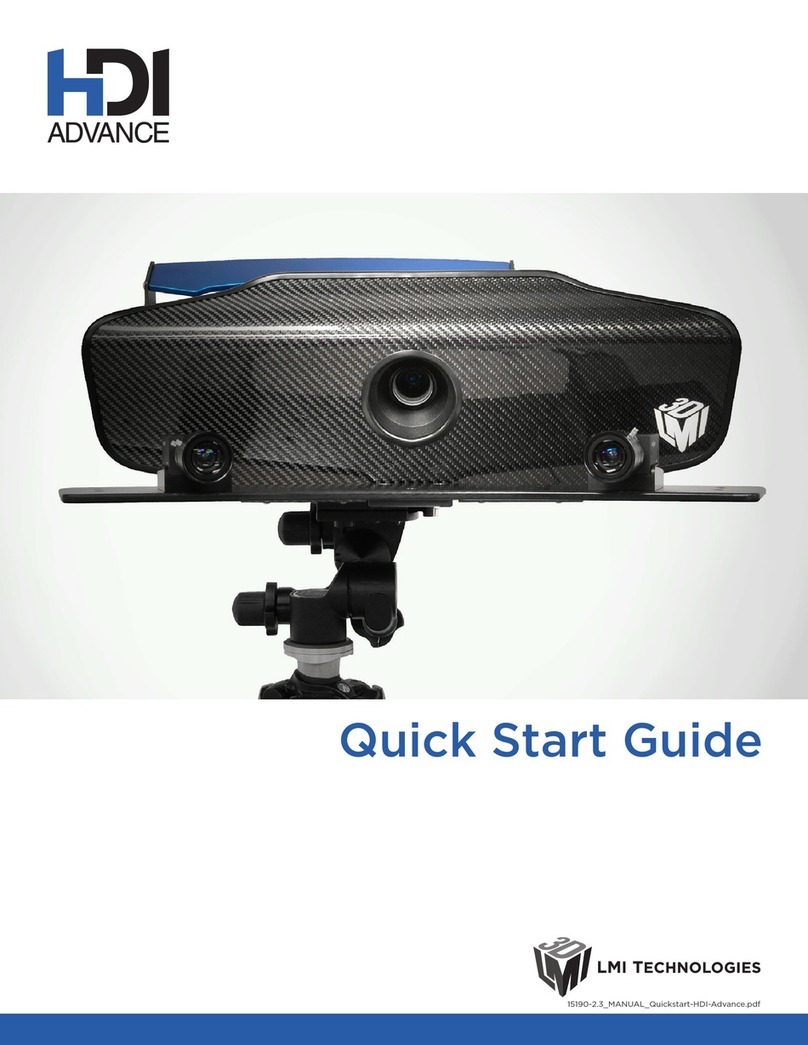
HDI
HDI Advanced 3D Scanner quick start guide
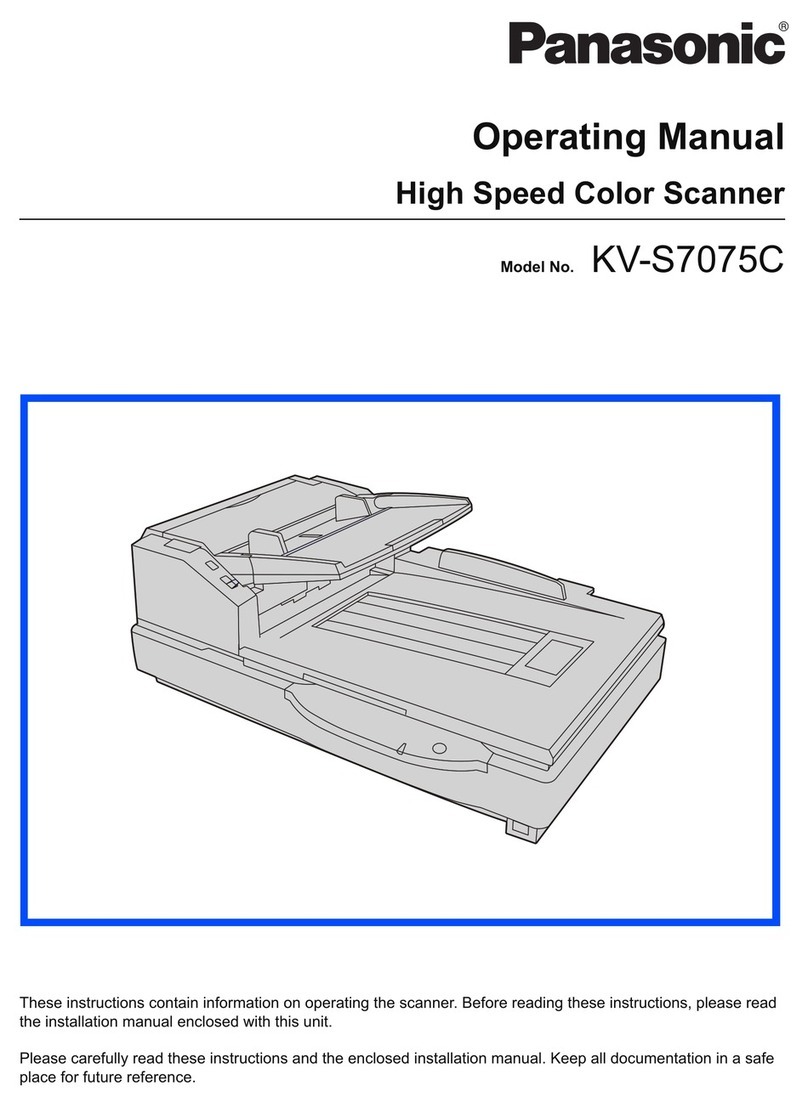
Panasonic
Panasonic KV-S7075C operating manual
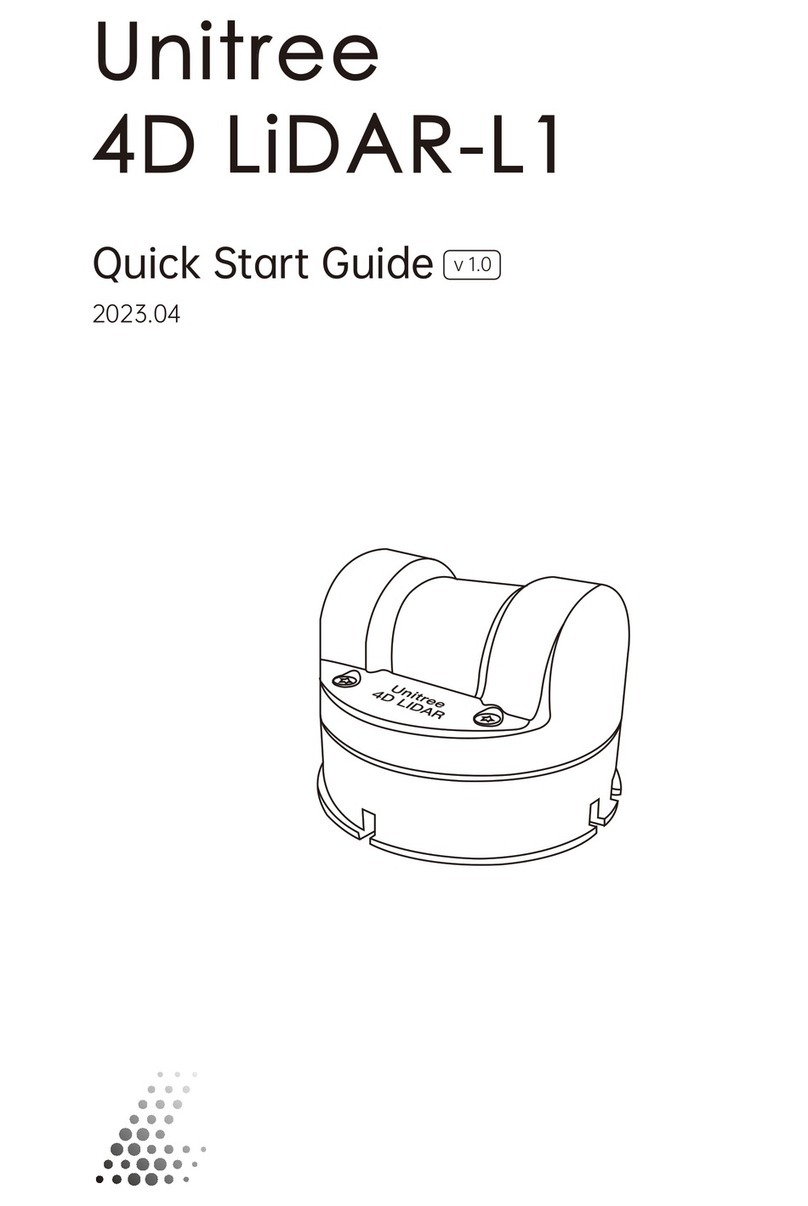
Unitree
Unitree 4D LiDAR-L1 quick start guide