GORMAN-RUPP SM SERIES Operating instructions




















Other manuals for SM SERIES
2
This manual suits for next models
2
Other GORMAN-RUPP Water Pump manuals

GORMAN-RUPP
GORMAN-RUPP AMT 5586-H6 User manual

GORMAN-RUPP
GORMAN-RUPP S8A1-E95 460/3 Application guide
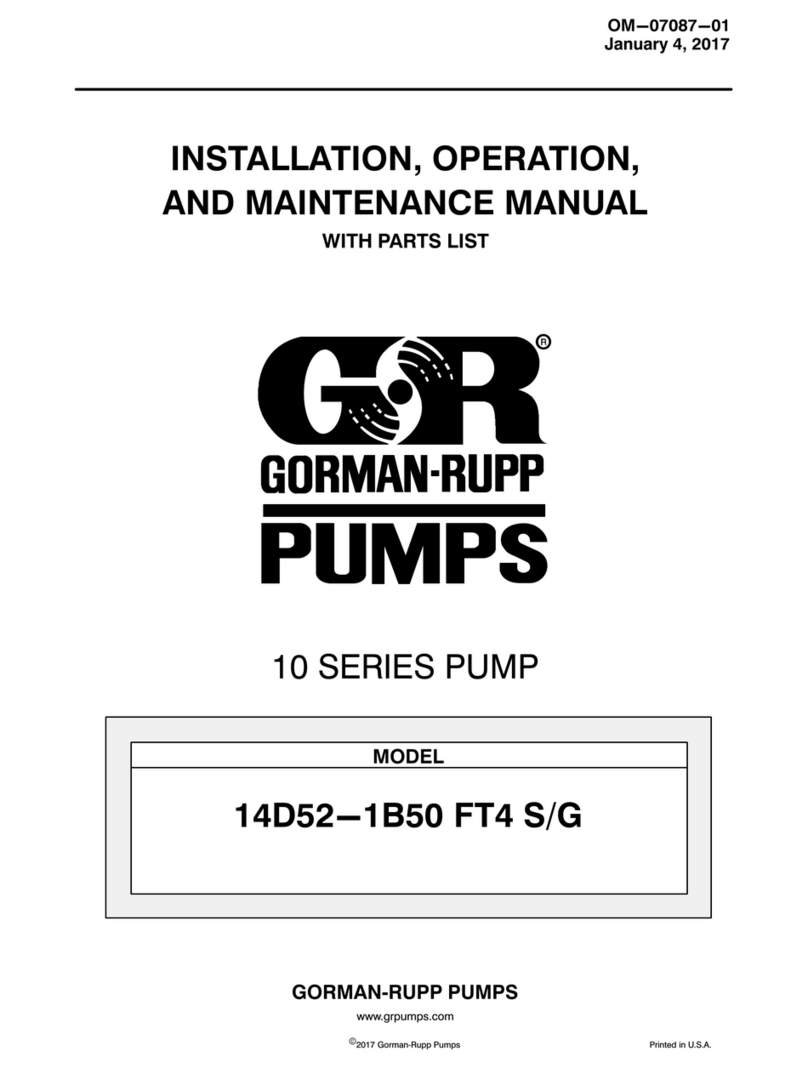
GORMAN-RUPP
GORMAN-RUPP 10 SERIES Application guide
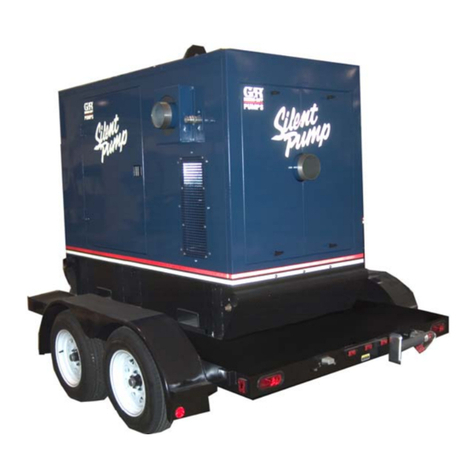
GORMAN-RUPP
GORMAN-RUPP T6A60S-4045T-ESP Installation and operating instructions

GORMAN-RUPP
GORMAN-RUPP PRIME-AIRE PA4B Series Operating instructions
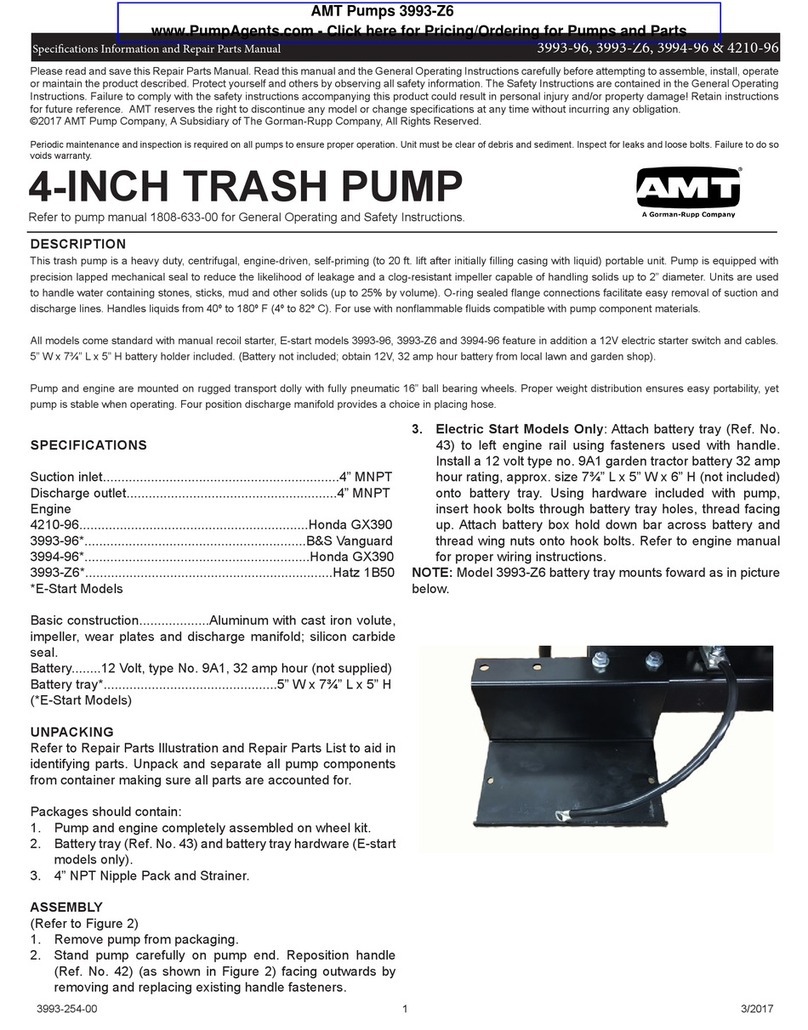
GORMAN-RUPP
GORMAN-RUPP AMT 3993-96 Assembly instructions
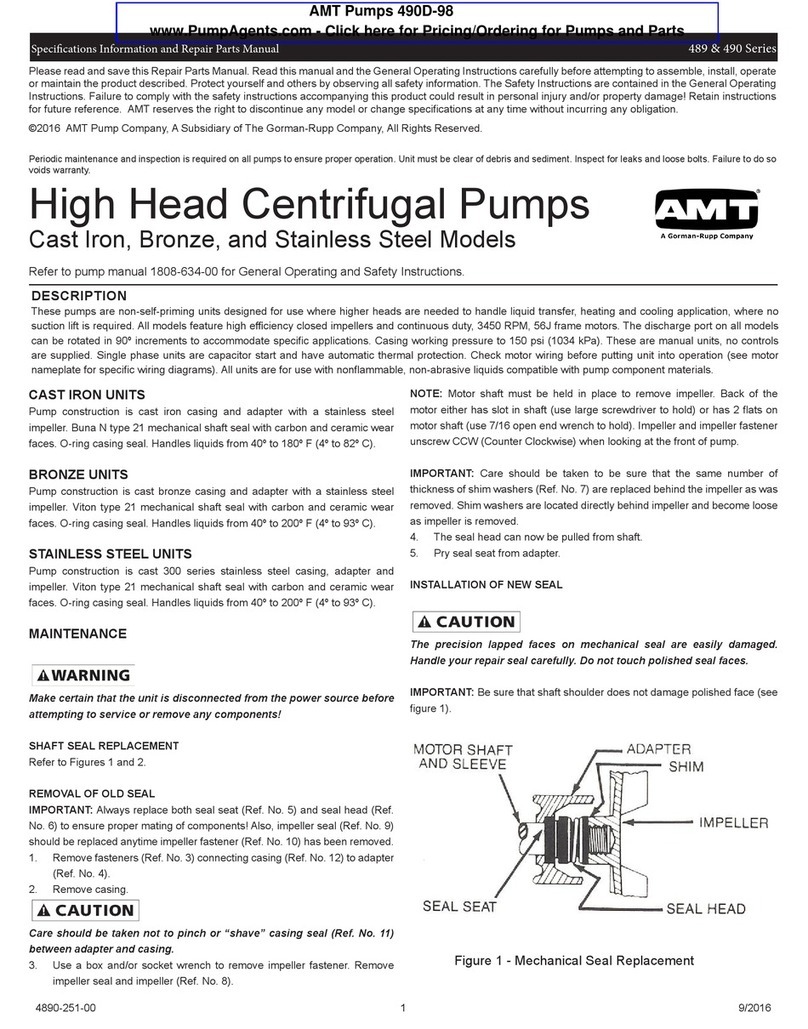
GORMAN-RUPP
GORMAN-RUPP AMT 489 Series Assembly instructions

GORMAN-RUPP
GORMAN-RUPP PA4C60-4045H General instructions
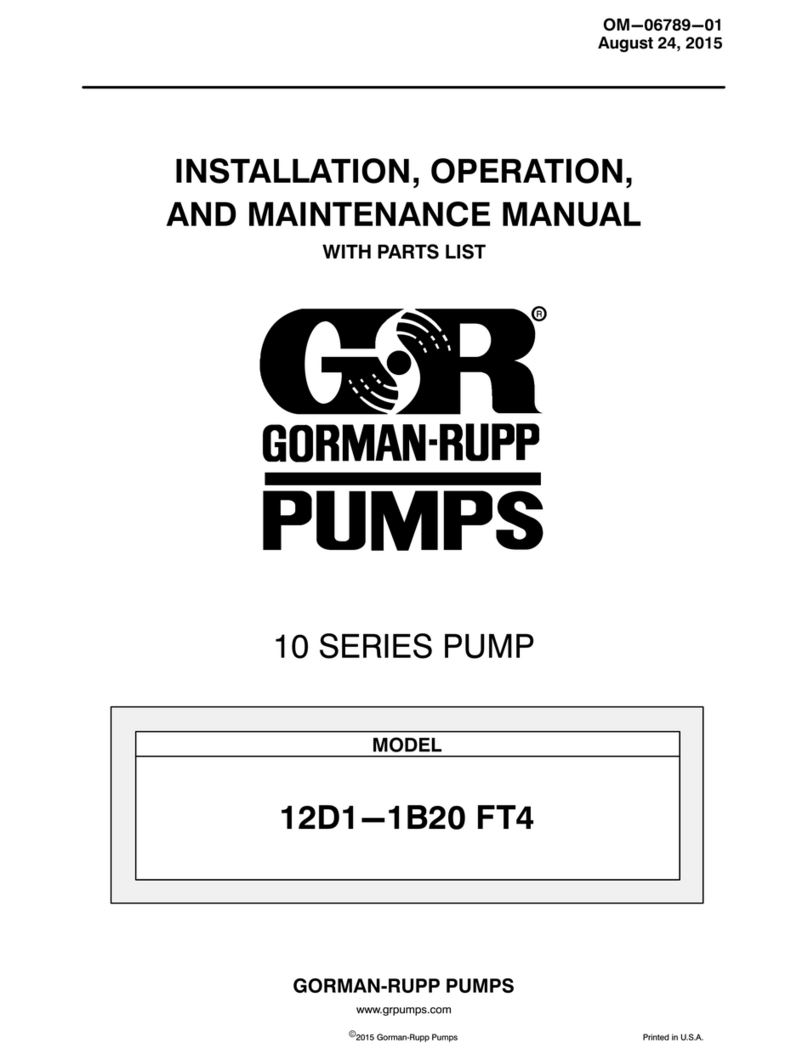
GORMAN-RUPP
GORMAN-RUPP 12D1-1B20 FT4 User manual
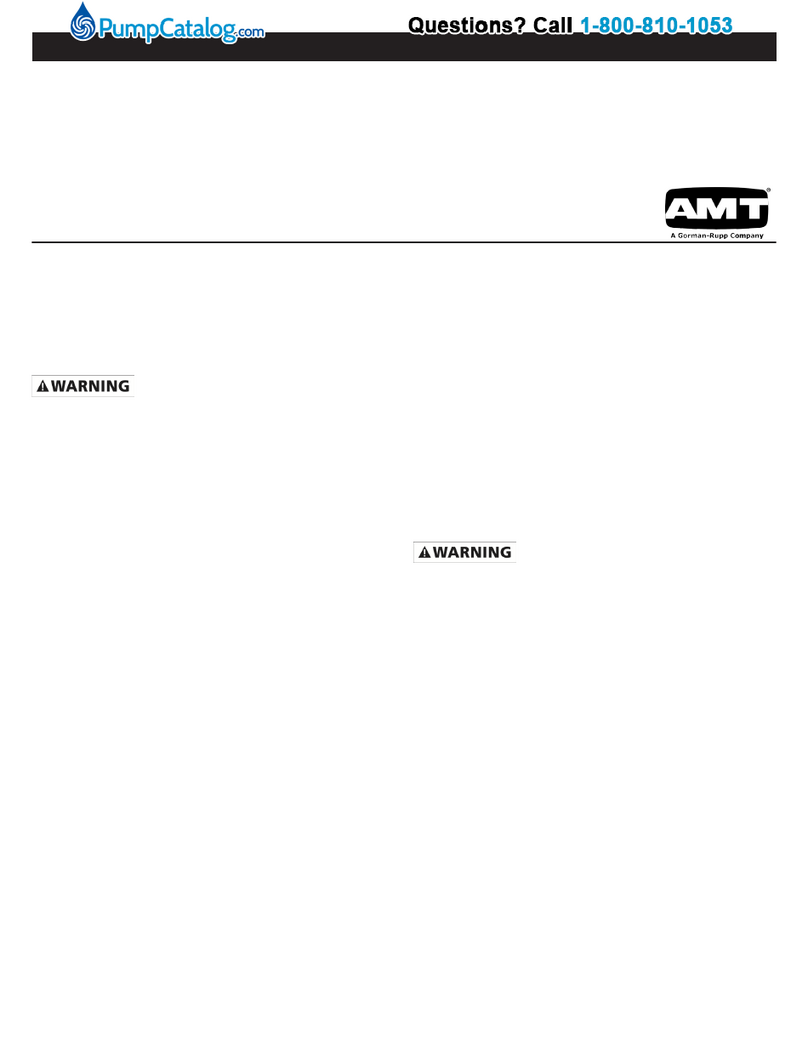
GORMAN-RUPP
GORMAN-RUPP AMT 4782-95 Assembly instructions
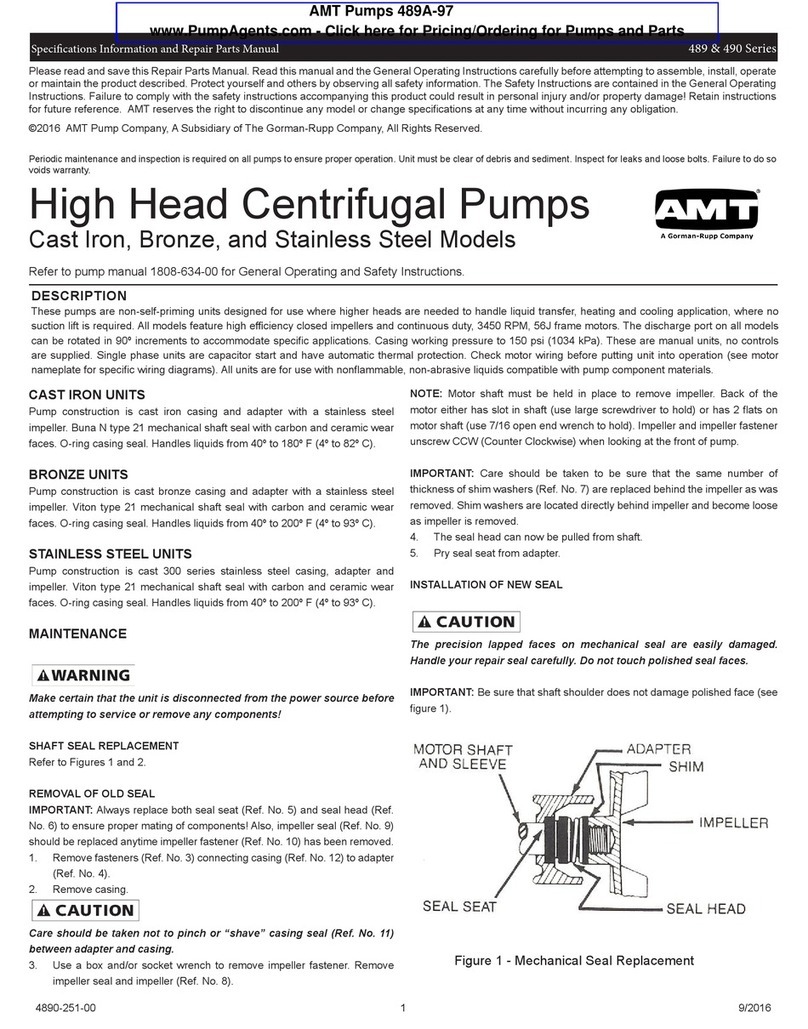
GORMAN-RUPP
GORMAN-RUPP AMT 489 Assembly instructions
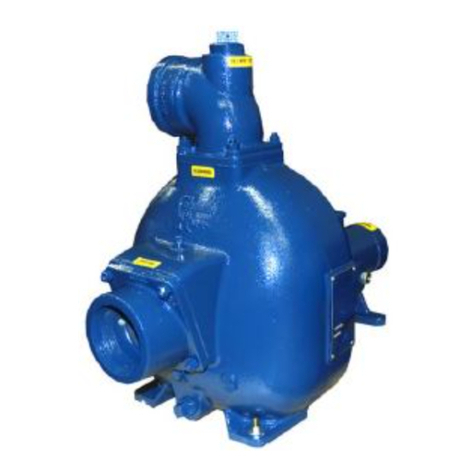
GORMAN-RUPP
GORMAN-RUPP 83A2-B Application guide
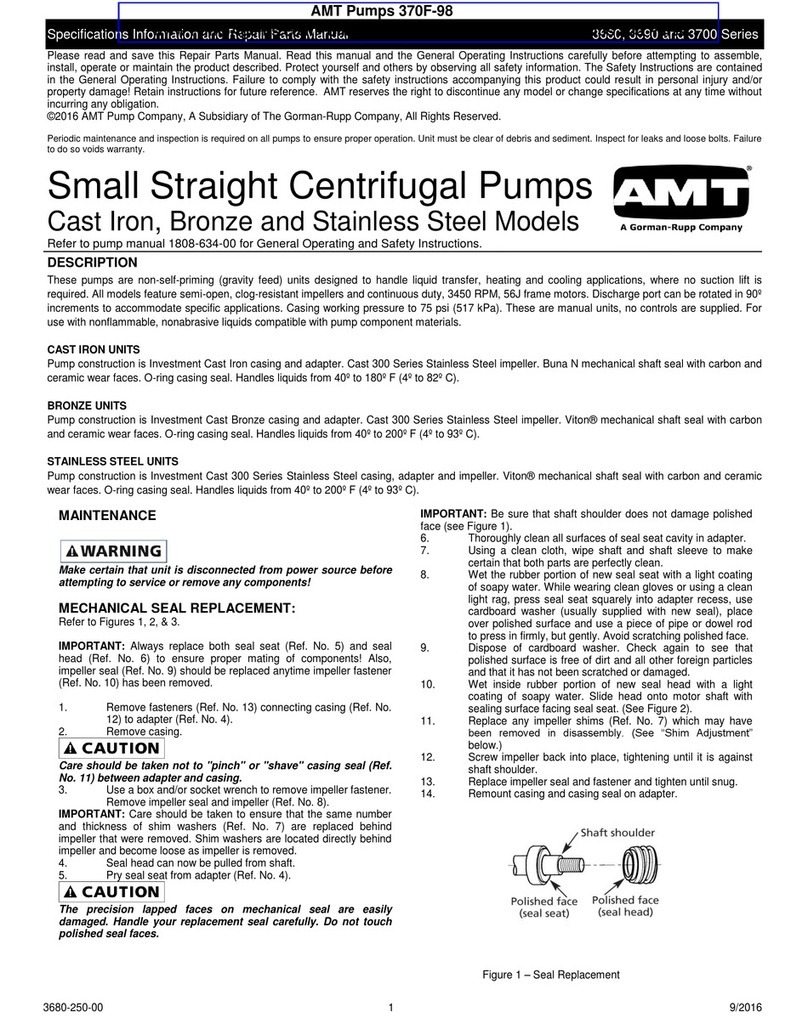
GORMAN-RUPP
GORMAN-RUPP AMT 370F-98 Assembly instructions
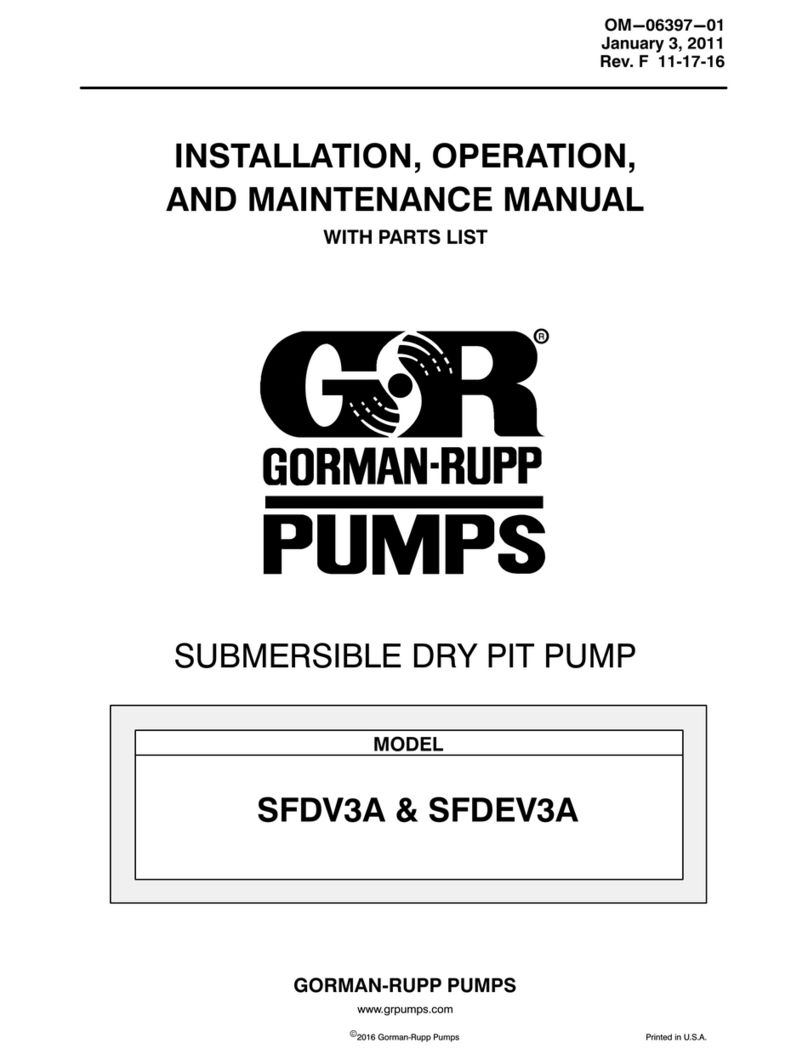
GORMAN-RUPP
GORMAN-RUPP SFDV3A Application guide
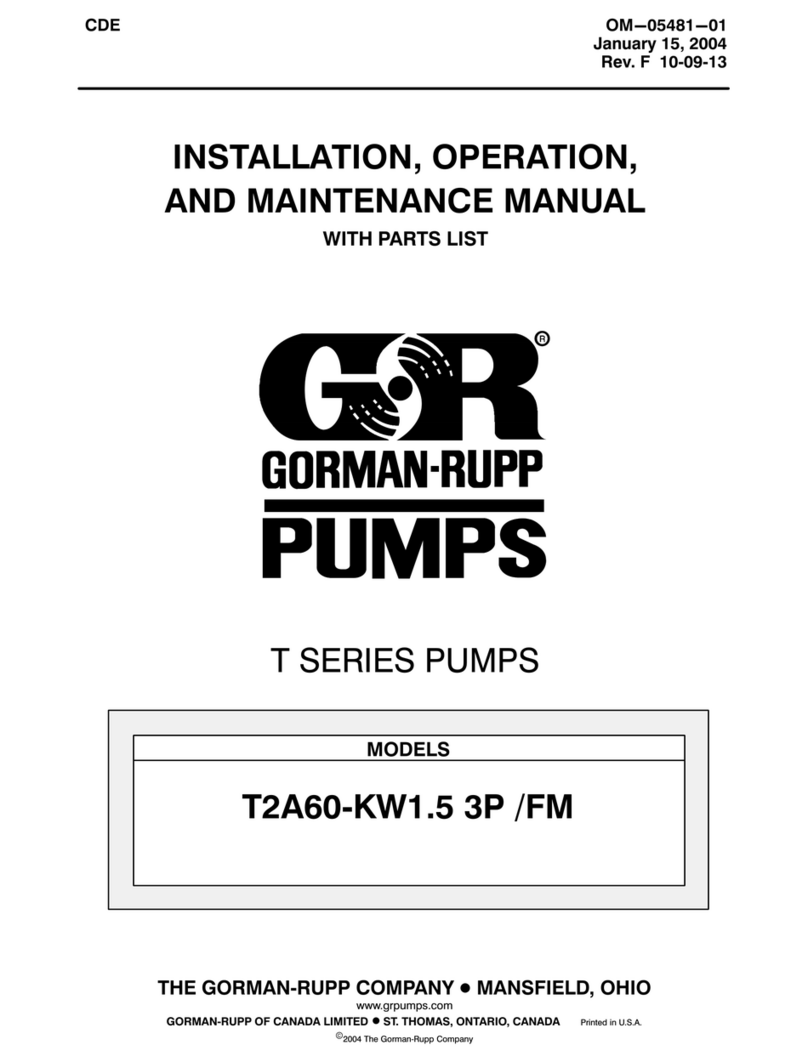
GORMAN-RUPP
GORMAN-RUPP SUPER T SERIES User manual
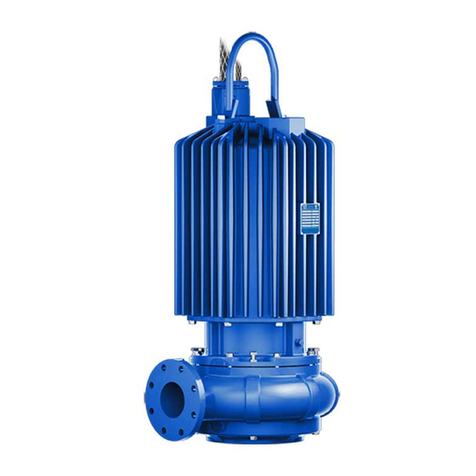
GORMAN-RUPP
GORMAN-RUPP SFV Series Installation and operating instructions
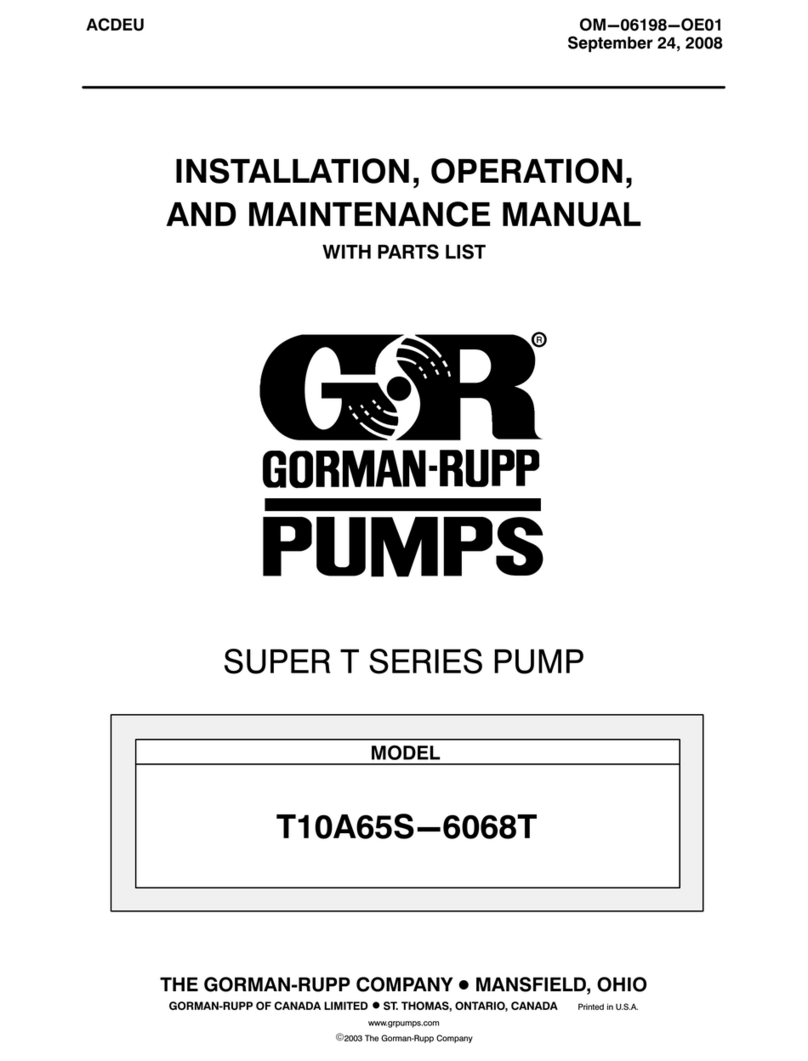
GORMAN-RUPP
GORMAN-RUPP SUPER T SERIES Installation and operating instructions

GORMAN-RUPP
GORMAN-RUPP PAH SERIES Application guide

GORMAN-RUPP
GORMAN-RUPP AMT 3680 Series Assembly instructions
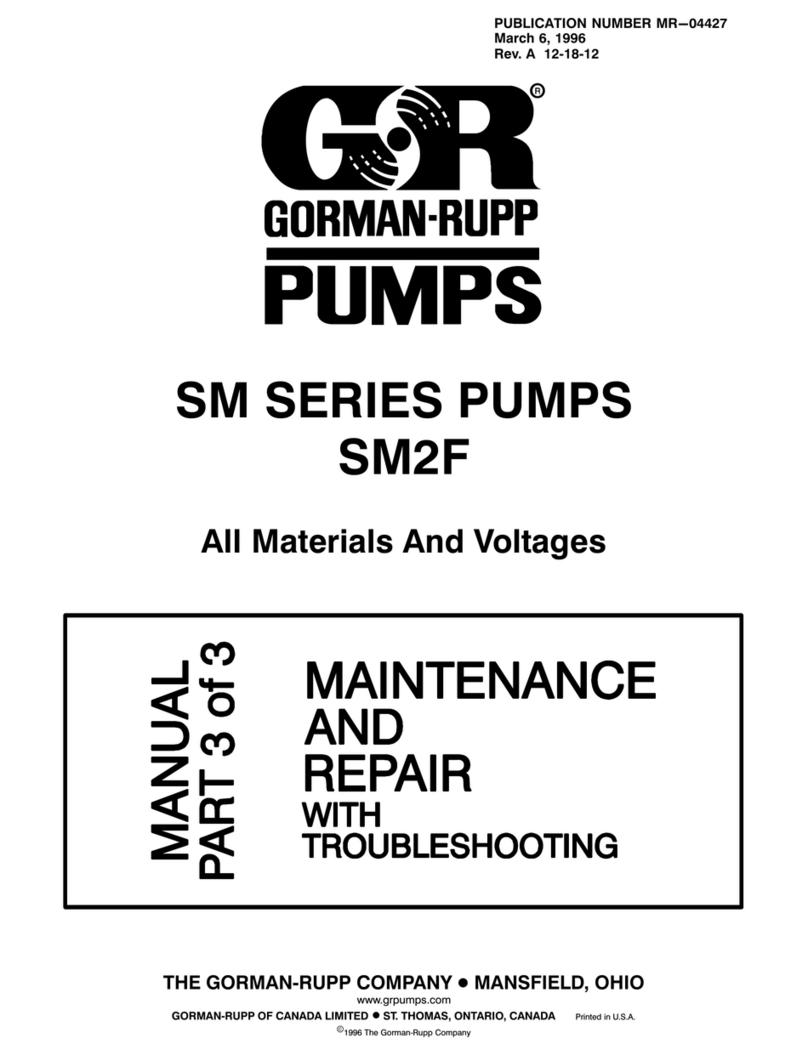
GORMAN-RUPP
GORMAN-RUPP SM SERIES User manual
Popular Water Pump manuals by other brands

Schmalz
Schmalz EVE-TR 250 AC3-F operating instructions

Watson-Marlow
Watson-Marlow MasoSine EC 25 manual
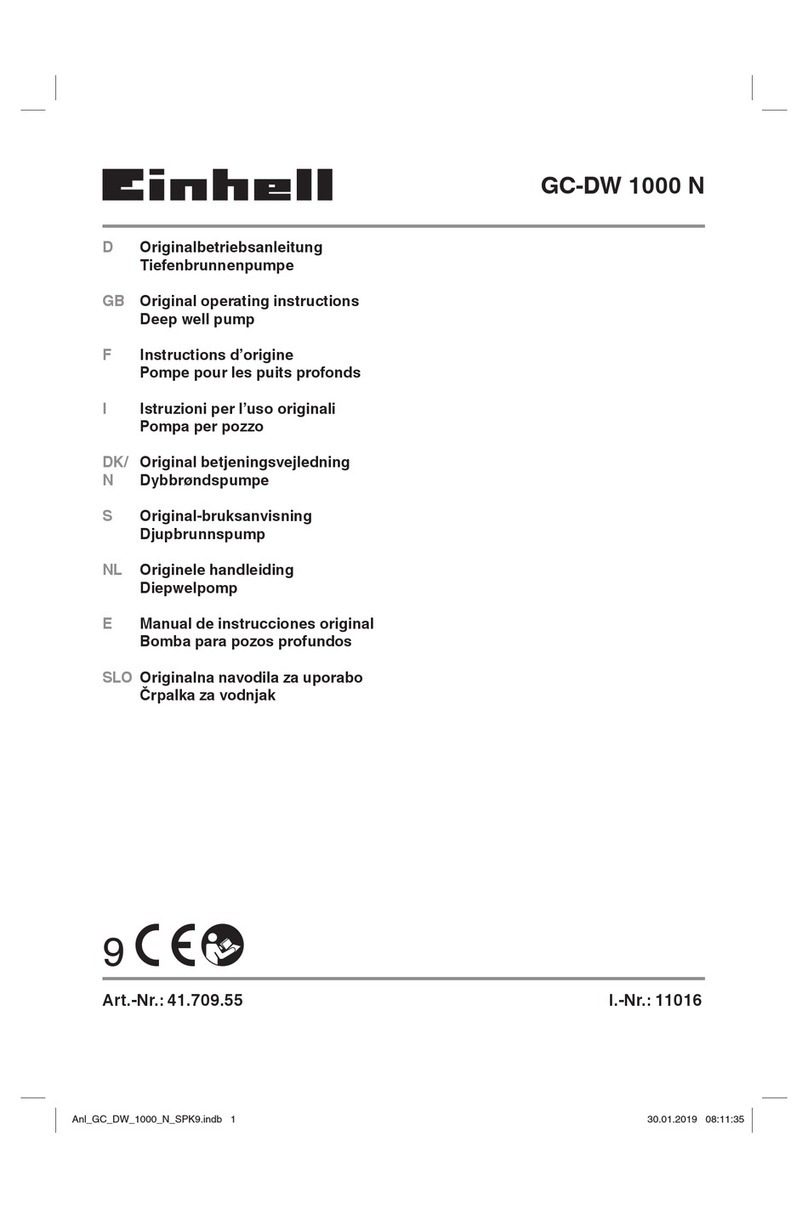
EINHELL
EINHELL GC-DW 1000 N Original operating instructions
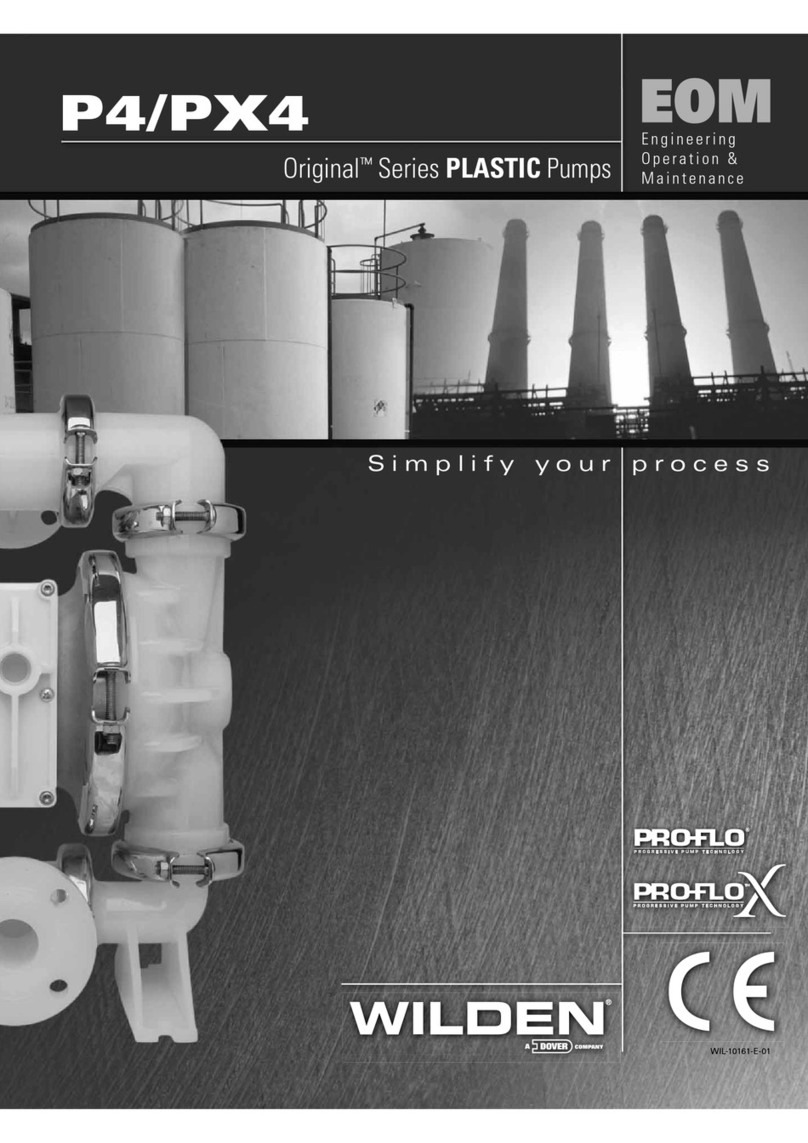
Dover
Dover Wilden Pro-Flo P4 Series Engineering, operation & maintenance

KINNEY
KINNEY KVA Series Operator's manual
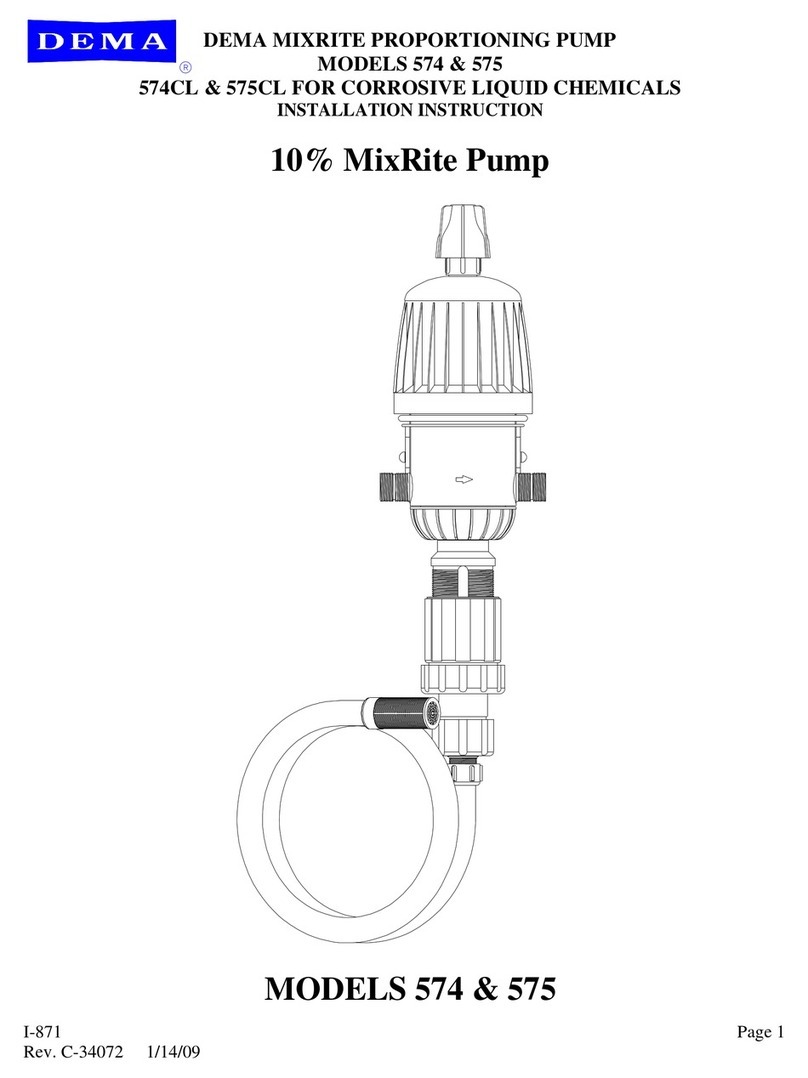
DEMA
DEMA 574 installation instructions