GreenMech CS 100 User manual

CS 100
COMPACT 4-INCH
CHIPPER
Operator’s Manual

CS 100 CONTENTS 1
SECTION:
1. Introduction and Purpose
2. Technical Specifications, Dimensions, Noise Level, and
Lifting points
3. Safety and Symbols
3.1 Ensure!
3.2 Never!
3.3 Always!
3.4 Safety controls and switches
3.5 Control cut-outs
3.6 Symbols
4. Machine Preparation
4.1 Fuelling and parking
4.2 Infeed chute
4.3 Discharge chute
5. Operation
5.1 Pre-work checks
5.2 Starting machine
5.3 Stopping machine
5.4 Operating Hints
5.5 Preparing for Transport on completion of work
6. Maintenance
6.1 Routine Maintenance schedule and lubrication points
6.2 Engine Oil
6.3 Fuel level
6.4 Air cleaner
6.5 Drive belts
6.6 Infeed Chute Flaps
6.7 Cutting unit
6.8 Steam cleaning
6.9 Wheels and Tyres
6.10 Bearings and pivots
6.11 Mountings
7. Storage
7.1 Storage
7.2 Removal from storage
©GreenMechLtd - 1 - 06/09

CS 100 CONTENTS 2
8. Disposal
9. Appendix
9.1 Certificate of Conformity
9.2 Risk Assessment
9.3 Noise Assessment
9.4 Parts List
9.5 Transcript of HSE leaflet 604
©GreenMechLtd - 2 - 06/09

GM C/S100 1. INTRODUCTION AND PURPOSE 1-1
INTRODUCTION
This manual explains the proper operation of your machine. Read these instructions
thoroughly before operating and maintaining the machine. Failure to do so could result in
personal injury or equipment damage. Consult your GreenMech supplier if you do not
understand the instructions in this manual.
CAUTION! This symbol indicates important safety messages in this manual.
When you see this symbol, be alert to the possibility of injury to yourself or
others, and carefully read the message that follows.
We recommend that you keep this manual with the machine in the box provided. Note
here the serial number and quote it in any communications. This is important when
ordering spares. Remember to include all numbers and letters.
VIN Number…………………………………
Serial Number............................................
Write in the number!
Fig 1.1 Serial Number
Serial
Number
This manual covers the following models.
GM C/S100 Compact Chipper/ Shredder with interchangeable cassettes
Optional 14HP or 18HP (electric start) Briggs and Stratton Vanguard engines
The information in this manual is correct at the time of publication. However, in the course
of development, changes to the machine specification are inevitable. Should you find any
information to vary from the machine in your possession please contact your GreenMech
dealer for up to date information.
The manual may contain standard and optional features and is not to be used as a
machine specification.
PURPOSE
CAUTION! This machine is designed solely to chip wood and must not be
used for any other purpose. The machine should only be used by trained
operators who are familiar with the content of this instruction manual. It is
potentially hazardous to fit or use any parts other than genuine GreenMech
parts. The company disclaims all liability for the consequences of such use,
which in addition voids the machine warranty.
©GreenMechLtd 1-1 11/09

GM C/S100 2. SPECIFICATIONS 2-1
Fig 2.1 GM C/S100 Main Features
Engine controls
Drive cover
Sto
p
Button
Infeed chute
Chipper cassette
Discharge chute
Fuel tank
Stand
TECHNICAL SPECIFICATION GM C/S100-14 / GM C/S100-18
Chipping Capacity 4 to 6 m3 cuttings per hr depending on material
Guaranteed wood diameter 80mm (3”)
Permitted wood diameter 130mm (5”)
Chipping Blades 2 reversible and regrindable blades
Rotor cutting width 310mm
Power Unit Briggs and Stratton 4 stroke Vanguard V Twin 14hp
or 18hp with electric start
Fuel Petrol 95 octane (unleaded)
Fuel Consumption (continuous) 2 8 lt/hour
Length (Transport) 1725mm
Length (Work) 2183mm
Width 760mm
Height (Transport) 1245mm
Height (Work) 1468mm
Feed Height 840mm
Weight (Empty) 195Kg / 197Kg
©GreenMechLtd 2-1 11/09

GM C/S100 2. SPECIFICATIONS 2-2
Noise
Noise levels vary depending on type of material being processed. Also duration of
operation is variable. Noise emission tests have been carried out and the guaranteed
sound power level is displayed on the CE plate as follows: Lwa 120dB(A)
Minimise noise by slowing to idle or stopping the engine whenever chipping is not in
progress.
Full details are included in the Risk Assessment in the Appendix.
CAUTION! Operators must wear appropriate ear protection. Bystanders must be
kept away from proximity of machine.
Lifting Points
Ensure infeed chute is folded in and secured for transport. Sling from tubular handles of
fixed section of infeed chute and lifting point on discharge chute.
©GreenMechLtd 2-2 11/09

GM C/S100 3. SAFETY 3-1
3.1 ENSURE:
3.1.1 All Operators must be fully trained in
the use of their machine.
(Certificated Operator training courses are
available on request.)
3.1.2 The Operators Manual is read and
understood.
3.1.3 The enclosed HSE guidance notes
are read and understood.
3.1.4 The machine is positioned on level
ground and the machine must be level with
the infeed chute at no less than 600mm
(23.62 inches) above ground level (fig
3.4.3).
3.1.5 All guards are fitted and in good
condition.
3.1.6 Blades are in good condition and
secure.
3.1.7 All blades are sharpened or replaced
in “Sets”.
3.1.8 All fasteners are checked regularly
for tightness.
3.1.9 Only “WOODEN” materials free of
nails etc., are fed into the machine.
3.1.10 Correct First Aid Kit including large
wound dressing is available on site.
3.1.11 Fire extinguisher is available on site.
3.2 NEVER:
3.2.1 Work on the machine until the
chipper disc is stationary and engine has
stopped.
3.2.2 Operate the machine without
protective clothing (Eye protection,
Earmuffs, and Gloves), or high visibility
clothing when working on roadside.
3.2.3 Operate with loose articles of
clothing, including loose cuffs on gloves.
3.2.4 Work under a raised component
without adequate safety support.
3.2.5 Operate the machine with untrained
personnel or with individuals present who
are not involved in the chipping operation.
3.2.6 Leave the machine unattended with
engine running at full operating speed.
(See section 4)
3.2.7 Put any part of your body into the
infeed chute while the machine is running.
3.2.8 Operate the machine whilst under the
influence of alcohol or drugs.
3.2.9 Operate inside a building or confined
space.
3.2.10 Climb on the infeed chute.
3.3 ALWAYS:
3.3.1 Check machine before starting (see
Section 4 Preparation and Section 5.1
Operation: Pre-work checks).
3.3.2 Be aware of potential hazards in the
work area, i.e. uneven ground, tree roots,
trip/slip hazards, obstructions and type of
materials being fed into the machine.
3.3.3 Feed from the side.
3.3.4 Have a second trained operator
within easy reach of the machine.
3.3.5 Maintain strict discipline at all times.
3.3.6 Service machine at specified periods.
(see Section 6: Routine Maintenance).
3.3.7 Note direction of discharge chute and
if necessary note the wind direction to
prevent debris from being blown into
highway or where it could affect members
of the public.
3.3.8 Remove key before doing any
maintenance.
©GreenMechLtd 3-1 11/09

GM C/S100 3. SAFETY 3-2
Fig 3.4.1 Stop Button
Stop Button
3.4 Safety Controls and Switches
3.4.1 Emergency Stop (fig 3.4.1)
In the event of an emergency, push the
STOP button. This will lock in position to
stop the engine and machine.
3.4.1.1 Once the emergency has been
rectified the following sequence should be
carried out:
3.4.1.2 Check over machine for any
blockages.
3.4.1.3 To reverse the cutter, remove the
drive guard and, using a bar through the
hole in the cutter spindle, manually turn the
cutter to free the obstruction.
Fig 3.4.2 Engine Stop Switch
Stop switch or
key (elec start) 3.4.1.4 When clear, pull the stop button out
and restart the engine.
3.4.2 Engine stop switch
3.4.2.1 To stop the engine, push the cut-off
switch to the ‘0’ position. (fig 3.4.2), or
(electric start) turn key switch anticlockwise.
CAUTION! Do not restart engine until
hazard has been removed.
Fig 3.4.3 Infeed chute height
Infeed chute
height 600mm
min. (24")
3.5 Control cut-outs
An engine cut-out is installed under the
drive guard to stop and prevent restarting.
due to specific events. The drive guard has
to be removed first to access the cutter or
dismantle the chutes
©GreenMechLtd 3-2 11/09

GM C/S100 3. SAFETY 3-3
3.6 SYMBOLS on the MACHINE
These relate to operator safety, correct use and maintenance of machine. Check that all
personnel understand and are familiar with meanings before using the machine.
See engine manual for safety and control symbols on the engine.
Important Safety symbols
Take the correct action shown on the display below the stated hazard (see table)
Sound level
Ear defenders must be
worn
Important Operating Checks.
See engine manual.
Maintenance Information
See engine manual Grease point
40 hours / weekly
©GreenMechLtd 3-3 11/09

CS 100 4. MACHINE PREPARATION 4-1
Fig 4.1 Stand and Infeed Chute 4.1 Initial Fuelling and Parking
4.1.1 Position the machine on level ground
and ensure stand is secure (fig 4.1).
Hand nut
4.1.2 Fill the fuel tank with petrol.
4.1.3 Check the engine oil level.
4.1.4 Check that the stop button is
released.
Stand
4.2 Infeed Chute
4.2.1 Loosen hand nuts (fig 4.1) and swing
the infeed chute extension into work
position.
4.2.2 Tighten hand nuts ensuring that
nylon spacers pass through holes at ends
of slot.
.
CAUTION! Before transporting,
always fold up and secure the infeed chute.
Fig 4.3 Discharge Chute
Alternative position (either side)
4.3 Discharge Chute (Fig 4.3)
4.3.1 Release the spout clamp, remove
and reset the spout in the desired direction
and tighten the clamp.
Spout clamp
4.3.2 Set the flap at the desired height.
CAUTION! Observe wind direction -
avoid danger of discharge blowing towards
operator.
©GreenMechLtd 4-1 06/09

GM C/S100 5. OPERATION 5-1
5.1 Pre-Work Checks:
5.1.1 Check machine is stable with support
stand lowered with pin in place (fig 5.1.1).
Fig 5.1.1 Support Stand
5.1.3 Check engine oil level (fig 5.1.2 - See
also 6.2 and Engine instruction manual).
Support stand
and pin 5.1.4 Check engine air filter. (see Section
6.4)
5.1.5 Check fasteners for tightness.
5.1.6 Check cutter is free to turn.
5.1.6.1 If blocked, remove the drive guard
and, using a bar through the hole in the
cutter spindle, manually turn the cutter until
free of obstruction.
5.1.6.2 Check tightness of blade bolts and
condition of blades. See 6.7 for cutter
blade servicing.
5.1.6.3 Remove any loose material.
Fig 5.1.2 Engine Oil and Fuel
5.1.7 If any bolts are loose, refer to
maintenance section for further action.
Fuel Filler 5.1.8 Check discharge chute and flap is in
desired position and all clamps are tight.
(see Section 4.3)
5.1.9 Check infeed chute is folded out.
5.1.10 Check infeed rubber flaps are intact.
5.1.11 Check work area and erect signs
and cone off discharge area if necessary.
5.1.12 Check ALL safety procedures have
been followed.
5.2 Starting Machine:
5.2.1 Check all other personnel are clear of
machine.
5.2.2 Check that machine stop button is pulled
out to start.
5.2.3 Turn engine start switch to position I. (fig
5.2)
5.2.4 Open fuel tap by putting the vane to
vertical.
5.2.5 Set throttle to Slow and pull out choke.
5.2.6 Turn key or pull starter cord to start
engine.
5.2.7 Push choke back in.
5.2.8 Set throttle to Fast.
5.3 Stopping Machine
5.3.1 Push the STOP button.
5.3.2 Switch start key to position 0.
5.3.4 Wait for engine and cutter to stop.
CAUTION! The cutter may take
several seconds to stop due to its inertia.
Fuel tap Dipstick
Fig 5.2 Engine controls
Start -
Stop Throttle
Choke
Oil Filler
©GreenMechLtd 5-1 11/09

GM C/S100 5. OPERATION 5-2
5.4 Operating Hints
5.4.1 Reduce the engine throttle to Slow
whilst further material is collected for
chipping.
5.4.2 Take care when feeding wood into
the machine to allow for awkward shapes to
“KICK” when contacting the cutter.
CAUTION! Do not adjust discharge
chute when chipping is in progress.
Fig 5.5 Infeed chute folded in
CAUTION! A build up of debris risks
overheating of the engine and a risk of fire.
CAUTION! Keep working area around
the machine clear at all times and check
only authorised personnel are present.
Hand nut
5.5 Preparing For Transport On
Completion Of Work
5.5.1 Check that engine has stopped and
cutter is stationary.
5.5.2 Shake the machine and remove
surplus material from infeed chute and
machine surfaces.
5.5.3 Lift up infeed chute to transport
position and secure with hand nuts (fig 5.5)
ensuring spacers pass through holes at
ends of slots.
©GreenMechLtd 5-2 11/09

GM C/S100 6. MAINTENANCE 6-1
ROUTINE MAINTENANCE SCHEDULE
CAUTION! Always press stop button, switch engine to 0 and check for rotation before
carrying out any maintenance.
Action Section Page
DAILY
Check engine oil level (ref: engine manual) 6.2 – 6.3 6-3
Check fuel level 6.2 6-3
Clean air cleaner 6.4 6-3
Check drive belt 6.5 6-3
Check condition of infeed chute rubber flaps 6.6 6-3
Check condition of cutter blades and retaining bolts 6.7 6-4
First 50 hours
Check drive belt tension 6.5 6-3
Check wheel and tyre condition and pressures 6.9 6-5
Check all mountings 6.11 6-5
Check battery levels 6.12 6-5
Service engine Refer to engine manual
Weekly in addition to Daily actions
Check drive belt tension 6.5 6-3
Steam clean machine 6.8 6-5
Clean air cleaner 6.4 6-3
Check wheel and tyre condition and pressures 6.9 6-5
Grease all bearings and pivots 6.10, 6.1 6-5
Check all mountings 6.11 6-5
Check battery levels 6.12 6-5
250 hours in addition to Daily and Weekly actions
Check condition of bearings and pivots 6.10 6-5
Service engine Refer to engine manual
Check axle mounting bolts for tightness 6.11 6-5
Check and grease wheel spindles 6.10 6-5
ENGINE MAINTENANCE REFER TO ENGINE MANUAL
Tyre Pressure 1.4 bar (20 lb/in2)
Recommended lubricants Specification
Grease Complex grease EP2 (high temperature)
Engine SAE 15W-40 APICD
©GreenMechLtd 6-1 11/09

GM C/S100 6. MAINTENANCE 6-2
6.1 Lubrication Points (see 6.14)
Fig 6.1 Lubrication points GM C/S100
6.1.2 6.1.36.1.1
Grease except where stated
6.1.1 Cutter bearing (remove guard) 1 nipple
6.1.2 Cutter bearing (non-drive end) 1 nipple
6.1.3 Wheel spindles Remove wheel - smear with grease
Note. Do not overgrease bearings as damage to seals may occur.
©GreenMechLtd 6-2 11/09

GM C/S100 6. MAINTENANCE 6-3
6.2 Engine Oil
6.2.1 Check daily (fig 6.2). Refer to
engine manual to refill.
Fig. 6.2 Engine Dipstick and Filler
Engine Oil Filter
Fuel Filler
Refer to engine manual for replacement.
Oil Filler
6.3 Fuel Level
6.3.1 Check daily before work and fill as
required (fig 6.2).
CAUTION! Use clean 4-stroke petrol
fuel only. If in doubt, use a funnel with a
filter.
Dipstick
Fig. 6.4 Engine Air Cleaner
6.4 Air Cleaner
Weekly
Cover 6.4.1 Remove cover (fig 6.4).
6.4.2 Unscrew nut to slide out element and
either blow out with air-line or gently tap on
smooth ground to release debris.
6.4.3 Replace element and cover.
Air Cleaner 6.4.4 Ensure hand nuts are secure.
6.5 Drive Belts (Fig 6.5)
Check daily, before work.
6.5.1 Remove guard and inspect.
Fig 6.5 Drive Belt
Tension
Desired belt tension is 400N.
Pulley Bolt 6.5.2 Check with tension meter (available
as an option.)
6.5.3 Release pulley bolt and adjust
locknuts on tensioning screw to set tension.
6.5.4 Tighten pulley bolt.
Replacement
6.5.5 Release pulley bolt and slacken
tensioning screw to allow belts to be
removed.
Tensioner
6.5.6 Fit new belts, ensuring they lie snugly
in the pulley grooves.
6.5.7 Tension belts, tighten pulley bolt and
replace guard securely.
Fig. 6.6 Infeed Chute Rubber Flaps Note: Re-tension new belts after 5
working hours.
Rubber Flaps 6.6 Infeed Chute Flaps (Fig 6.6)
Two slitted flaps protect the operator from
material thrown back up the infeed chute.
6.6.1 Replace flaps if damaged.
CAUTION! Do not operate with
missing or damaged flaps.
©GreenMechLtd 6-3 11/09

GM C/S100 6. MAINTENANCE 6-4
6.7 Cutter Blade Servicing
The cutter cassette is removed as a unit to
service the cutter blades.
Cassette removal (fig 6.7.1)
6.7.1 Check engine is switched off.
6.7.2 Remove drive belts as 6.5 above
Fig 6.7.1 Cassette Removal
6.7.3 Fold the infeed chute in for transport
and secure.
6.7.4 Tip machine back onto infeed chute
and remove stand.
6.7.5 Tip machine forward to rest on feet of
cassette.
Cassette
on fe 6.7.6 Remove 2 front bolts and 2 rear
bolts.
6.7.7 Carefully tilt machine back to release
cassette and rest machine on infeed chute.
et
Blade servicing (Fig 6.7.2)
Drive guard and
stand removed CAUTION! Take care. Blades are
extremely sharp.
6.7.8 Slacken blades bolts with Torx tool
supplied and remove.
6.7.9 Turn blades round and refit to use
opposite edge.
Fig 6.7.2 Blade removal
6.7.10 Tighten blade bolts to 35Nm.
6.7.11 Check clearance to anvil is 0.5mm.
Blade Note: If blades have been reground the
anvil will need readjusting to 0.5mm.
6.7.12 Reassemble cassette and refit to
machine by reversing procedure above.
6.7.13 Refit belts as 6.5 above.
6.7.14 Replace and secure drive guard.
Blade regrinding
Bearing Both edges of each blade must be ground
on front at 27˚angle and on back 10˚angle
over 4mm to ensure correct clearances.
When less than 48mm minimum width
blades may be raised by a suitable shim.
CAUTION! Blades must only be
sharpened by grinding on a bench grinder.
Do not sharpen with hand held equipment.
Always sharpen in sets to maintain balance
of cutter assembly.
©GreenMechLtd 6-4 11/09

GM C/S100 6. MAINTENANCE 6-5
6.8 Steam Cleaning
weekly and every 250 hours
6.8.1 Check all covers are fitted and
closed
6.8.2 Steam clean machine surfaces.
6.8.3 Clean electrical components with a
damp rag, spray with WD40 and then wipe
with dry rag.
Fig 6.12 Battery (If fitted)
CAUTION! Do not steam clean
directly on to electrical components.
6.9 Tyres and Wheels
50 hours and 250 hours
6.9.1 Check condition of tyres.
6.9.2 Check pressures and inflate to 1.4bar
(20lb/in2) pressure as required.
Bolt each side 6.9.3 Check wheel nuts are tight.
6.10 Bearings and Pivots
weekly
See paragraph 6.1 for routine lubrication.
250 hours
6.10.1 Check rotating components for
excessive movement and noise in
operation.
6.10.2 Replace as required.
6.11 Mountings
250 hours
6.11.1 Check that all mounting bolts are
tight.
6.12 Battery (If fitted) (Fig 6.12)
First 50 hours and weekly
6.12.1 Check electrolyte level and top up if
required.
CAUTION! Gases are explosive.
Electrolyte is corrosive. Avoid sparks and
spillage.
6.12.2 Removal of battery
6.12.2.1 First disconnect negative (-) cable
(black cap).
6.12.2.2 Disconnect positive (+) cable (red
cap).
6.12.2.3 Remove bolts to allow tray to
drop and lift out battery.
6.12.2.4 Replace by connecting positive
cable before negative.
©GreenMechLtd 6-5 11/09

GM C/S100 6. MAINTENANCE 6-6
6.12 Fault finding
Fault Check Action Page
Stop button Pull out to release
Engine stop switch push to I - start position 6-3
Fuel Fill tank - check tap on 6-3
Oil pressure Check Oil level 6-3
Engine will not start
Drive guard Fit to engage cut-out switch 6-3
Engine not at correct speed Engine throttle Check operation 5-1
Blockage Clear 5-1Cutter not rotating Drive belt tension Re-tension or replace 6-3
Discharge chute Check for blockage 5-1Discharge does not flow Cutter unit Check for blockage 5-1
Unusual noise(s) Bearings Check and replace 6-10
©GreenMechLtd 6-6 11/09

CS 100 7. STORAGE 7-1
7.1 Storage
7.1.1 Thoroughly clean machine and note any replacement parts required.
7.1.2 Carry out 250 hour service if not already done. Refer to Section 6
7.1.3 Fit replacement parts when available.
7.1.4 Drain fuel
7.1.5 If machine is to be stored for more than 3 months, place on axle stands to remove
weight from wheels.
7.2 Removal from Storage
7.2.1 Check tyre pressures Refer to 6.9
7.2.2 Carry out machine preparation as necessary Refer to Section 4
©GreenMechLtd 7-1 06/09

CS 100 8. DISPOSAL 8-1
When the machine is finally scrapped, the following items should be disposed of only at
authorised waste disposal facilities.
Engine oil. Tyres. Rubber components
If in doubt, consult the Local Authority environmental department.
©GreenMechLtd 8-1 06/09
Other manuals for CS 100
1
Table of contents
Other GreenMech Chipper manuals
Popular Chipper manuals by other brands

Vermeer
Vermeer BC160XL Operating and safety instructions
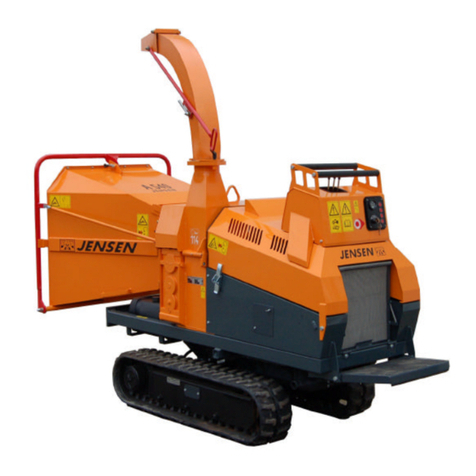
Jensen
Jensen A540 DiXL D-1703 Track operating instructions
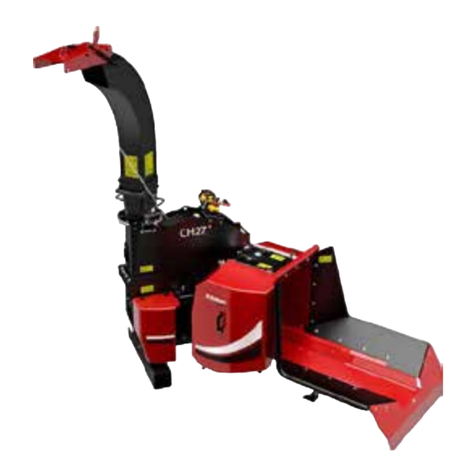
Farmi Forest
Farmi Forest CH27 ACR OPERATION, MAINTENANCE AND SPARE PARTS MANUAL
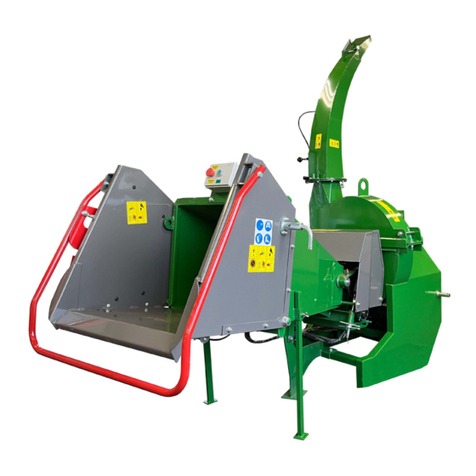
Kellfri
Kellfri 13-WC17H2 operating instructions
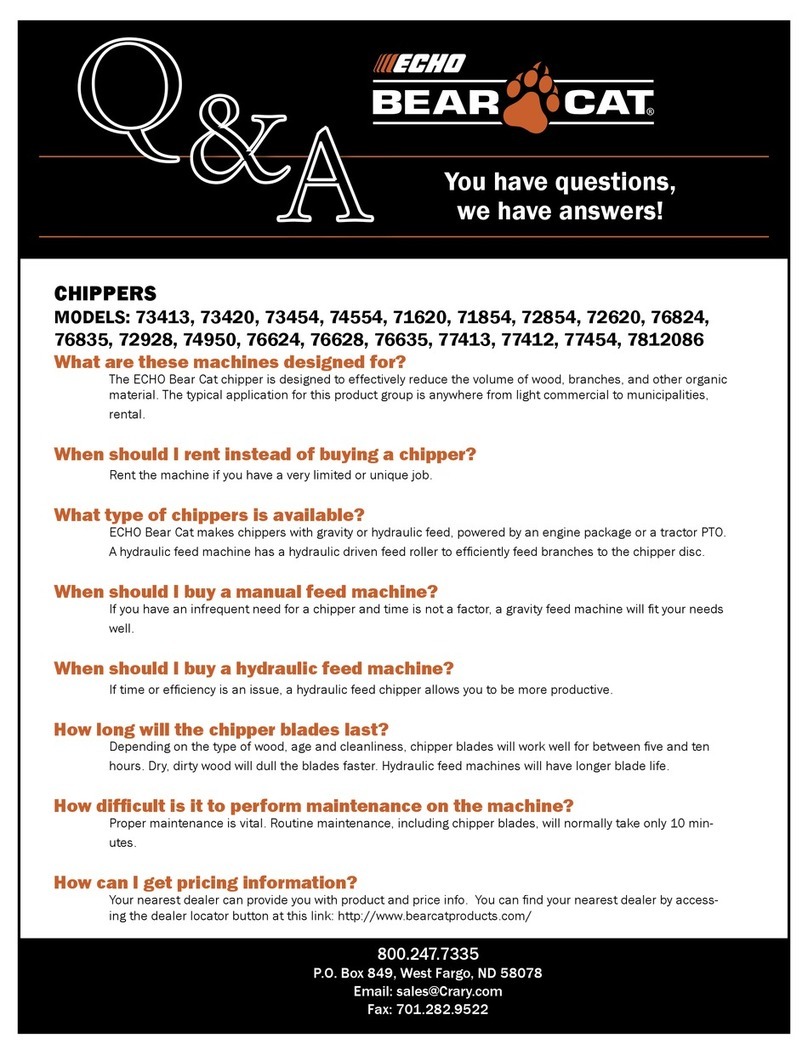
Echo
Echo Bear Cat 76824 Faq
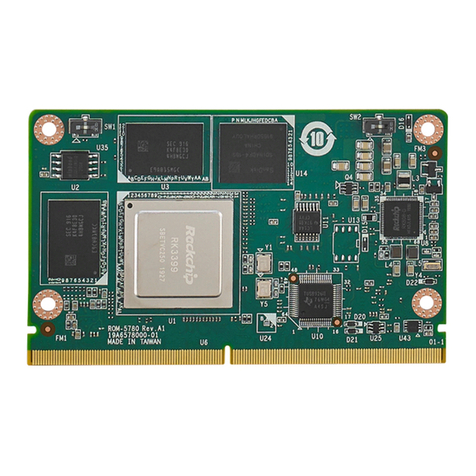
Advantech
Advantech ROM-5780 user manual