Hägglunds CB 280 User manual

SC-2.3
2008-11-20
Assembly Instructions
Compact CB 280
Hägglunds Drives AB
SE-890 42 Mellansel
Sweden
Tel: +46 (0)660 870 00
E-mail:
www.hagglunds.com
This material is strictly for internal use within the Hägglunds Drives Group only

Page 2 For internal use only
Assembly Instructions CB 280
Important!
The highest cleanliness of the motor parts and
of the workplace is always the basics to ensure the
smooth functioning of the hydraulic motor!
A lifting capacity of 800 kg (1764 lb)
is required to perform this work!
Make a note in the service inspection report:
the motor type and individual number from the sign
on the motor. This is important when
you are ordering spare parts.
D-40063
Special tool needed
T-000022 T-000043D-30205
D-30204

Page 3 For internal use only
Assembly Instructions CB 280
Grind the cam ring surface
around the roll pin holes with
a fine grinding stone.
It is very important to
clean the cam ring good
before assembling!
Grind the spacer ring over the
roll pin holes with a fine grind-
ing stone on both sides of the
spacer ring. Do not grind on the
sliding surface for the roller.
The highest cleanliness of the motor parts and of the
workplace are basics to ensure the smooth functioning
of the hydraulic motor!
Make sure to minimise that contamination can enter
into the motor during the assembling.
Ensure that you have cleaned all motor parts thoroughly,
especially if you have re-machined, grinded or in some
other way worked up the motor parts.
After final cleaning of the motor parts, don’t leave the
parts too long before assembling.
When lubricating
• always use clean filtrated oil, recommended ISO class
16/13 according to ISO 4406, NAS.7,
• always use clean grease of type Texaco Multifac EP2
or equivalent.
Rust protection
Use Shell Ensis SX or equivalent rust protection fluid.
Always use new gasket set.
Sliding surface
Important preparation before assembly
Work to be done before
cleaning the motor parts:
Always treat the sliding
surfaces with care
Shaft end housing Connection block and valve plate

Page 4 For internal use only
Assembly Instructions CB 280
A1
Install the Ø 1 mm orifice in the flushing connection
(F1) in the shaft end housing.
Note! This orifice is only used when flushing of the seal
is needed, normally plugged.
A2
Install the flushing connection plug (F1) G 1/4".
Allen key 6 mm, torque 30 Nm (22 lbf·ft)
A4
Drawing shows the direction of the seals.
Dust
seal
Radial lip
seal
A3
Install the connection plug (D3) 1" in the shaft end
housing.
Allen key 12 mm. Torque 125 Nm (92 lbf·ft).

Page 5 For internal use only
Assembly Instructions CB 280
A5
Install the dust seal in to the shaft end housing.
Tool D-30204.
A6
Place the shaft end housing on supports (x3).
Equally devided. Tool D-30205.
A7
Tap down the radial lip seal, turn the seal according
to drawing A4. Tool D-30204.
Note! Be careful not to damage the seal lip.
A8
Lubricate the seal with grease, Texaco Multifac EP2
or equivalent.
Note! Use a brush of good quality and watch out
so hair doesn’t come loose.

Page 6 For internal use only
Assembly Instructions CB 280
A12
Lubricate the O-ring for the wear ring with oil
and install it on the shaft.
A9
Lubricate the O-ring with oil and install it in the shaft
end housing.
Note! The screw joint on the motor works as a frictional
connection, so no oil are allowed on the surface.
A11
Heat up the roller bearing to 110°C (230°F) in an oven.
Tap the bearing down with a brass or a plastic rod. The
bearing should be turned according to drawing A10.
Note! To awoid damages on the bearing only tap on the
inner race of the bearing.
A10
Note! The snap ring on the bearing shall be towards
the middle of the motor.
Position of
the snap ring

Page 7 For internal use only
Assembly Instructions CB 280
A14
Install the lock ring for the wear ring.
A13
Heat up the wear ring to 110°C
(230°F). Install it on the shaft.
Tap it down with a plastic hammer.
A15
Gently pull back the wear ring so that the lock ring no
longer is loose.
To keep the lock ring permanent, the wear ring has to
be kept in place against the lock ring, until it is shrinked.
A16
Turn the cylinder block and install it into the shaft end
housing. Be careful not to damage the radial seal.
Use two lifting eyes M12.

Page 8 For internal use only
Assembly Instructions CB 280
See Service Manual
SC-2 Piston ring Assembly
A17
The direction of the piston ring is important!
A18
Install the piston ring on the pistons.
Note! Turn the piston ring according to drawing A17.
A19
Lubricate the piston bores with oil.
Note! Oil cleanliness level important!
A20
Lubricate the piston balancing surface with oil.
Note! Oil cleanliness level important!

Page 9 For internal use only
Assembly Instructions CB 280
A23
Install the piston assembly into the cylinder block.
Note! Make sure to place the roller on top of the O-ring
to avoid damages to the sliding surface.
A22
Install the cam rollers into the pistons.
Check so the cam rollers slide easily.
A24
Position of cam ring mark, seal retainer and shaft end
housing.
Motor sign
!
!
Install above
the O-ring
A21
Check carefully that the cam roller not is damaged.
Flushing
connection
Cam ring mark

Page 10 For internal use only
Assembly Instructions CB 280
A25
Install the first cam ring. Use two lifting eyes M16.
Note! Before you install the cam ring, make sure
that the surfaces between the cam ring and the shaft
end housing is absolutely clean.
A26
Lubricate the holes for the balancing sleeves with oil.
A28
Install the balancing sleeves.
A27
Install the springs for the balancing sleeves.

Page 11 For internal use only
Assembly Instructions CB 280
A30
Install the valve plate gently, so no balancing pistons
are falling out when you turn the valve plate.
Allen key 5 mm. Torque 14 Nm (10 lbf·ft).
Always make sure to install a locating bolt with thread
locking. Thread locking can also be made by use of
middlestrong locking (Loctite No. 243).
A29
Lubricate the holes in the valve plate
with oil and install the balancing pistons.
Note! Always treat the sliding surfaces on the valve
plate with care.
!
!
A31
Check the valve plate spring function: check that the
valve plate can move up and down by pressing it down
by hand.
A32
Lubricate the O-ring with oil and install it.

Page 12 For internal use only
Assembly Instructions CB 280
A33
Lubricate the surface on the cylinder block with oil.
A34
Turn over the connection block and lift it on the top of
the motor. Use two lifting eyes M12. The roll pin holes
should correspond to the threaded holes in the shaft
end housing.
Note! Make sure that the surfaces between the cam
ring and connection block are absolutely clean.
Important!
Place the
lifting
arrangement
on the top
A36
Place the plugs at their places, to avoid that dirt comes
into the motor.
A35
Lubricate the threads and
tighten four screws firmly,
then open them half a turn
(90 degrees) or until it is loose.

Page 13 For internal use only
Assembly Instructions CB 280
A40
Install the bearing race, use a plastic mandrel
to knock it down.
Note! Cleanliness very important. Make sure
that the surfaces are absolutely clean.
!
!
A39
Position of the axial-radial bearing.
See Service information No. 8
A37
Lubricate the 2 roll pins and
install them with the slot in
tangential direction. Remove
grease that are superfluous.
A38
Drive down the roll pins 10 mm (0.4 in).
10 mm
(0.4 in)

Page 14 For internal use only
Assembly Instructions CB 280
A42
Knock down the radial bearing
with a plastic hammer.
Knock only on the inner race.
Note! Before use:
make sure that
the tool is clean!
A43
Place the tool T-000022 and the assembly plate
T-000043 on to the bearing. Make sure to center
the tool carefully attach the screws through the holes in
the assembly plate and to the cylinder block.
Tighten the screws thoroughly.
A44
Push down the axial-radial bearing all the way until the
tool is tight against the cylinder block. Leave the puller
like this.
A41
Install the axial bearing.
Lubricate with hydraulic oil.
Note! Oil cleanliness level important.

Page 15 For internal use only
Assembly Instructions CB 280
A48
Lubricate the O-ring with
grease and install it.
A47
Install the wear ring. Tap it
down against the bearing.
Use a plastic hammer.
A46
Lubricate the O-ring for the wear ring with oil
and install it.
A45
Rotate the cylinder block a couple of turns in order
to align the bearing.
Rotate the motor
a couple of turns

Page 16 For internal use only
Assembly Instructions CB 280
A49
Install the bearing retainer. Oil the threads.
A50
Lock the cylinder block according to the picture.
Tighten the retainer screws.
Allen key size 10 mm. Torque 136 Nm (100 lbf·ft).
A51
Install the G1" plug with a new O-ring into the bearing
retainer.
Allen key 17 mm. Torque 125 Nm (92 lbf·ft).
A52
Tighten the four cover screws firmly, then open them
half a turn (90 degrees) or until it is loose.

Page 17 For internal use only
Assembly Instructions CB 280
A53
Place a support for the puller on to the bearing retainer.
A54
Place and install the puller tool T-000022.
Tighten the bearing to a torque of 160–180 Nm
(118–133 lbf·ft).
A55
Lift up the motor slightly from the supports.
A56
Tap all around the motor (on the rear cover only).

Page 18 For internal use only
Assembly Instructions CB 280
A57
Lower down the motor.
A60
Place a dial indicator with magnetic shoe on the
centre of the bearing retainer. Place the tip on the flat
surface on the connection block according to the photo.
Adjust the clock to zero.
A59
Remove all the lifting arrangements and the puller.
Tighten the four M20 Hexagon head screws No. 1 to 4
in order (see drawing A58), to maximum torque.
Allen key 17 mm. Torque 540 Nm (398 lbf·ft).
A58
Drawing shows the tightening sequense.
3
2
1
4

Page 19 For internal use only
Assembly Instructions CB 280
A61
Rotate the cylinder block 360 degrees. The axial run
out between the bearing and the connection block
must not exceed 0.03 mm. If the axial run out is not
obtained, loosen the screws and make the adjustment
once again from A52.
A62
The drawing shows the correct position of the seal.
A64
Install the radial lip seal into the seal retainer and tap
it down with a plastic hammer. Turn the seal correctly
according to drawing A62.
A63
Grease the tool.
Place the radial lip seal
on the tool D-40063.
Note! Check so that the tool is free from damages
to avoid to distroy the sealing.
!
!
See Service information No. 15

Page 20 For internal use only
Assembly Instructions CB 280
A67
Protect the surfaces against rust. Use Shell Ensis SX
or equivalent rust protection fluid.
A68
Install the seal retainer.
A66
Install the O-ring into the seal retainer.
A65
Lubricate the radial seal lip with grease,
Multifac EP2 or equivalent.
Other Hägglunds Engine manuals
Popular Engine manuals by other brands

GEIGER
GEIGER GJ5606-DuoDrive Original assembly and operating instructions
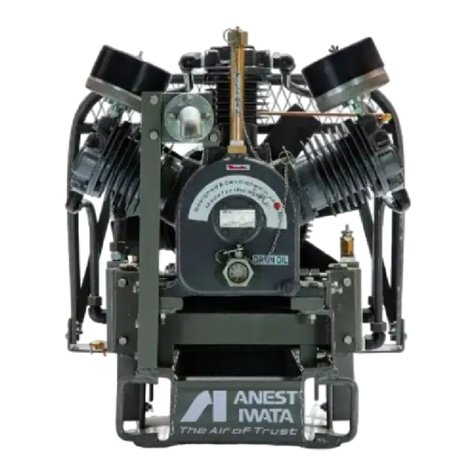
Anest Iwata
Anest Iwata SLVB-5 instruction manual

Hydro-Gear
Hydro-Gear HGM-C Service and repair manual
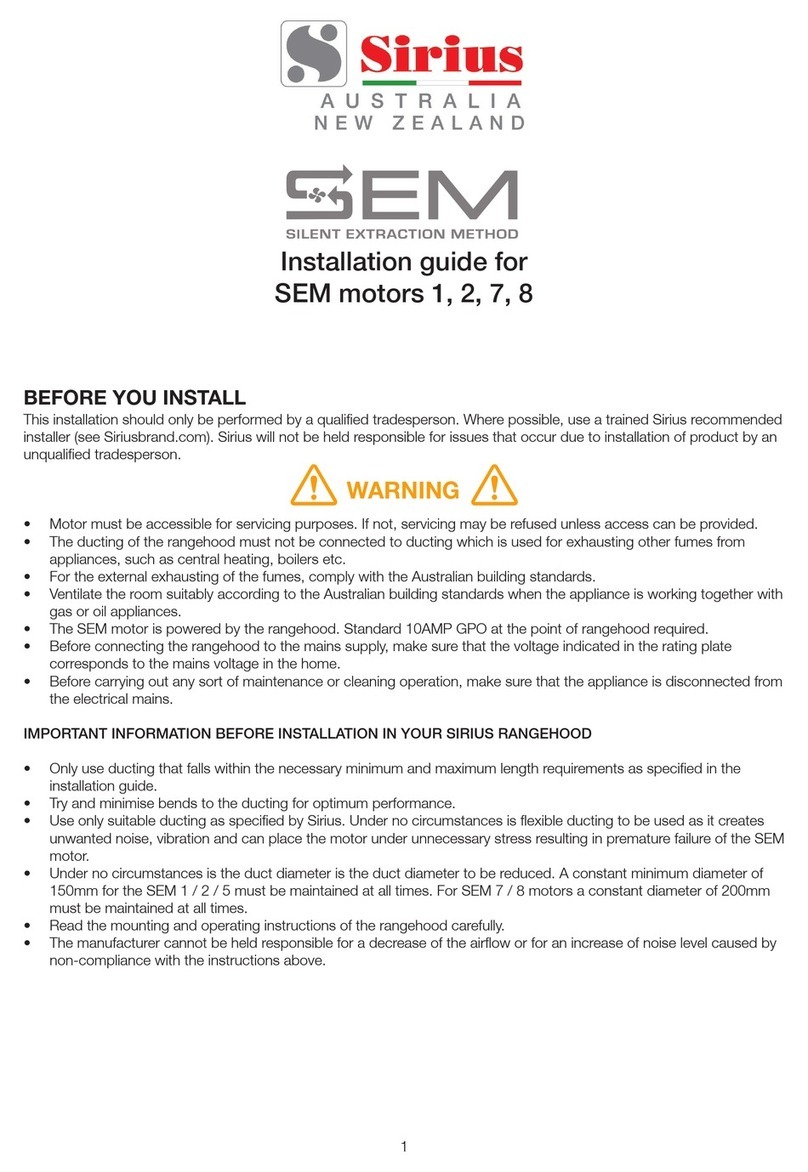
Sirius Satellite Radio
Sirius Satellite Radio SEM1 Installation guides
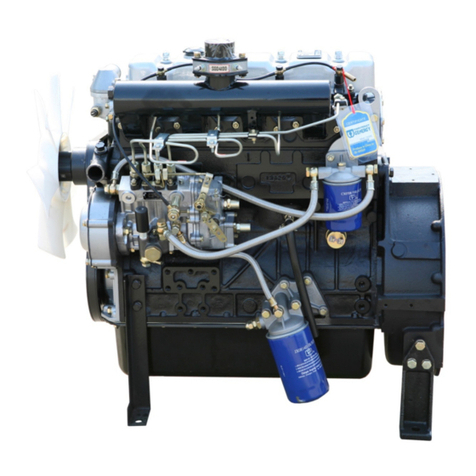
GENERGY
GENERGY SDE Series Instructions for use

Raider
Raider 50 HP TLDI Service manual
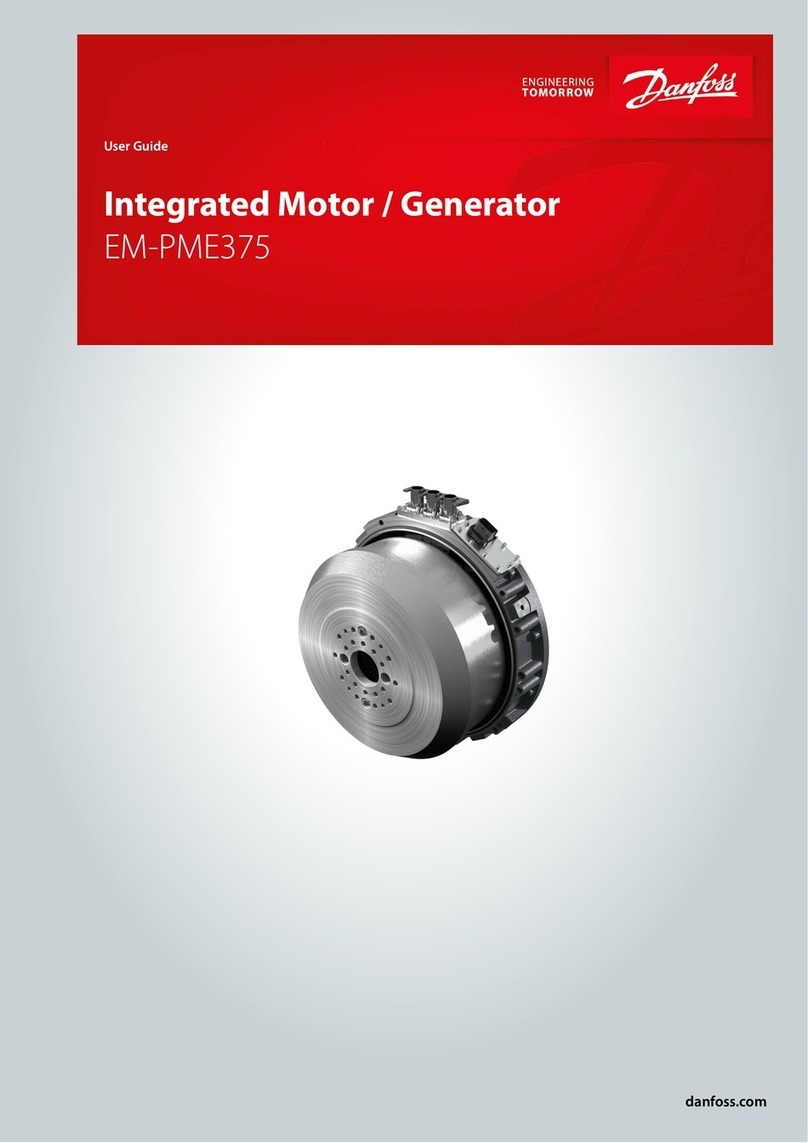
Danfoss
Danfoss EM-PME375 Series user guide

LinMot
LinMot PR01-52 installation guide
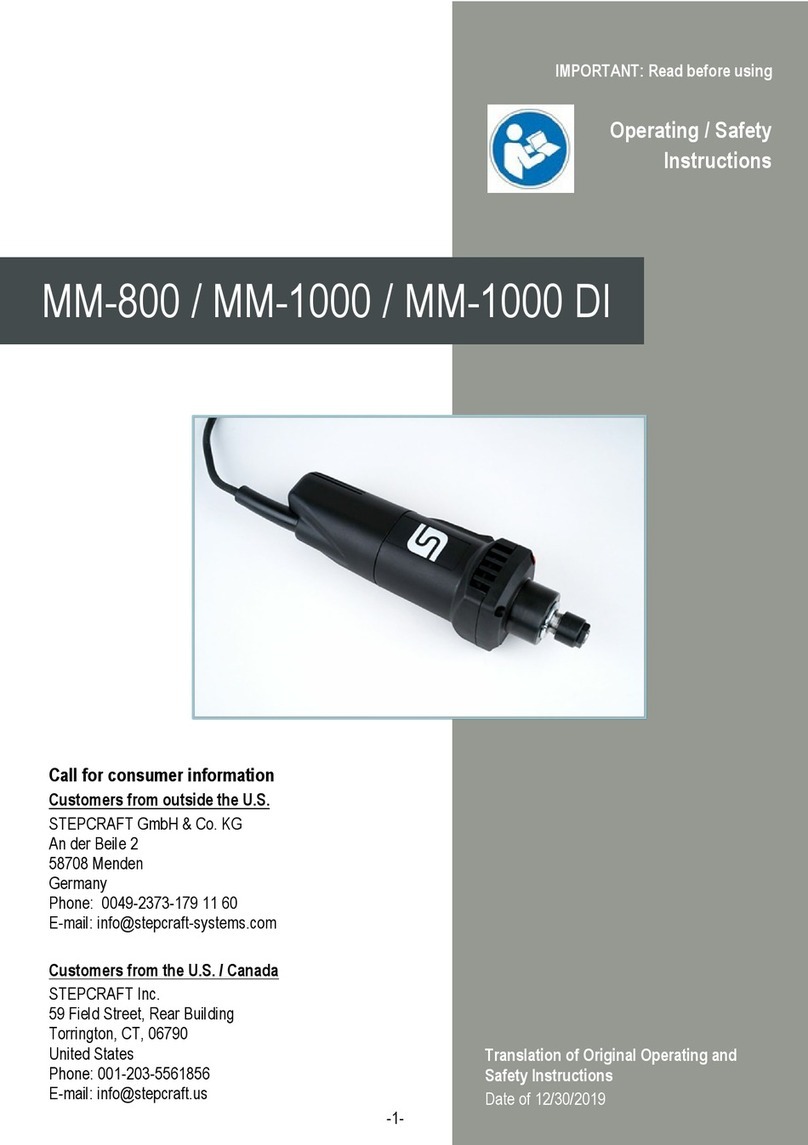
STEPCRAFT
STEPCRAFT MM-800 Operating and safety instructions
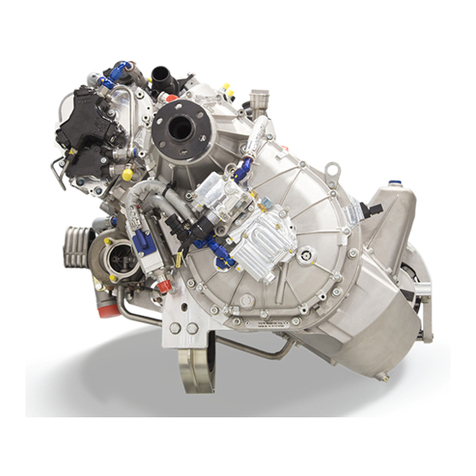
Technify Motors
Technify Motors CD-135 Operation and maintenance manual

Flux
Flux F 416 EX Original attachment

YewdaleDefiant
YewdaleDefiant 980003 Programming instructions