HABONIM 24/H24 Series User manual

Three Piece High Pressure Ball Valves –24/H24 Valves Series
Installation, Operating & Maintenance
Three Piece High Pressure Ball Valves
24/H24 Valves Series
REV00-03/23
Itemnumber: YP0005355

Three Piece High Pressure Ball Valves –24/H24 Valves Series
Three Piece High Pressure Ball Valves –24/H24 Valves Series
1
Contents
1.
General..............................................................................2
2.
Sil.......................................................................................2
3.
ATEX - Explosive Environment………………………………………3
4.
Limitations.........................................................................4
5.
Storage...............................................................................5
6.
Installation.........................................................................5
7.
Operating Instructions......................................................8
8.
Maintenance.....................................................................9
9.
Packages assembly & Disassembly.................................10
10.
Disassembly & Assembly Manual...................................13
Habonim cannot anticipate all of the situations user may encounter while installing and using Habonim
valves. The user MUST know and follow all applicable industry specifications on the safe installation and
use of these valves.
Misapplication of the product may result in injuries or property damage. Refer to Habonim product
catalogues, product brochures and installation, operating and maintenance manuals for additional
product safety information or contact Habonim.
Keep hands and objects away from the valve ports at all times. Actuated valves could be accidentally
operated, resulting in serious injury or valve damage.
Before removing a valve from the line, always make sure the line has been depressurized and
drained. Cycle the valve a few times to relieve any pressure that could be trapped in the body
cavity.
Utmost caution must be taken when handling a valve that has toxic, corrosive, flammable or a
contaminant nature media flowing through its pipeline.The following safety precautions are
recommended when dismantling valves with hazardous media:
Wear safety glasses, protective headgear, clothing, gloves and footwear.
Have available running water.
Have a suitable fire extinguisher when media is flammable.
Do not try to operate a valve that exhibits any sign of leakage. Isolate the valve and either repair or replace
it.

Three Piece High Pressure Ball Valves –24/H24 Valves Series
Three Piece High Pressure Ball Valves –24/H24 Valves Series
2
1. General
ThisInstallation,Operating&Maintenancemanualrepresentstheinstructionsrequired
forsafeuseof
Habonim ballvalve. Themanualrelatesto reduceand fullbore valves.
Before usinganyoftheseseries valves,read the entireIOMcarefully and makesure
everythingis clear.Where
in doubt, please consult with Habonim engineering team.
2. Sil
Undersevereoperating conditions inspection should be more frequently;detected
defectsshould be repairedpromptly.Severeoperating conditions can be definedas:
•
Application temperature less orabovethanspecifiedon thevalvetaglabel
•
Flow velocity higherthan 5m/sec for liquids, and 200m/secforgaseous
•
Acidic mediaPH < 5 oralkaline media PH> 9
Habonim recommend a prooftestintervalof 12 months; in case ofFailto Open ESDsystem,apartial
stroke
is acceptable to confirm thatthe installation is functioning properly.
ForESDsystemswith aFail-To-Closedemand, it is necessary toplan asystem shut-down; de-energize
the
systemand inspectthevalveturning to its fully closed position.
Itis essentialto log-in the following parametersonsiteQA records
as a proof for preserving SIL capabilities: date, hour, name andsignature of the responsible
engineer, air
pressure onsite,time to closethevalve, timeto open thevalve.
The combined corrosion anderosion allowanceforthevalvebody wallthicknessis 1mm. When this
allowance has been eroded orcorroded, mechanically removedorotherwise,the valveshould no
longerbe used. Inspect thevalvewallthickness every timethevalve is maintained.
The estimated mean time torepair(MTTR) a valve,i.e. timenet (line draining orcooling downtime
excluded fromthe valveMTTR) of replacingoldvalvewith anewoneis 60minutes. Maintenance
team mustread and understand the Habonim productIOM beforestartingthe operation.In case of
adoubt please consultthe
Habonimengineeringteam.
When avalve hasbeen repaired oranymaintenance was performed,check the valvefor proper
function
(proof testing). Anyfailuresaffecting functionalsafety should bereported totheHabonim
factory.
Proof testand maintenance
During a proof test operation, all the inner soft parts (seats, seals, stem packing and bearings) to
be examine andreplaced (onlyHabonim OEM repair kits can be used!) ininterval less than 5 years
to claim the valve assembly "as-good-as-new “.
Habonim recommendvalvefullmaintenanceoperation every 500,000cyclesor5years, whichever
comes first.
Client should consult the Habonim factory to obtain the product assessment, FMEDA report, and
other associated statistical data to satisfy SILlevel

Three Piece High Pressure Ball Valves –24/H24 Valves Series
Three Piece High Pressure Ball Valves –24/H24 Valves Series
3
3. ATEX –Explosive Environment
Pneumatic equipment shall complywith the requirements of ISO 4414.
The Compact can be installed in any appropriate potentially explosive hazardous area
as listed on the identification nameplate on the actuator. The Compact is certified to
category 1 according to the ATEX Directive 2014/34/EU (Equipment intended for use in
PotentiallyExplosive Atmospheres).
Special condition forsafe use.
1. Any electrical equipment (solenoidvalves/limitswitches)shallbe suitably certified
as specifiedby themanufacturer.
2. The air compressor must incorporatea filter on the intakesystem and contain only
lubricants that are resistant toignition orcarbonization at anticipatedtemperatures.
3. The air delivery must not beprovidedby hoses that aremanufacturedfrom
elastomeric materials that can carbonize and form glow particles inanticipated
temperatures.
4. The supply of air must come from a safe area and contain noexplosive gas or dust.
5. The temperature class is based on the maximum process temperature. The end
user must ensure that the process temperature does not exceed the temperature
classificationlimitations.
6. The ball valves havebeen assessed as simple equipment within the assessment
performed for the actuator. When used separately fromthe actuator, the ballvalves
shall be used within the parameterspermitted for theactuator.
7. No charging mechanism stronger than amanual rub shall be applied to external
non-metallicmaterials.
8. The actuator shallonly be usedin locations where a propagating brush dischargeis
not possible.
9. The actuators must have a cycle rate of ≤1 cycle per minute.
10. It is the user’s responsibility to ensure that the system/internal parts of the
actuator are suitably purged of explosive gas. In addition,before using the actuator,
the users must enter into the actuator non-explosive gas, to ensure thatthere is no
potentialfor ignition.
11. During maintenance, the end user shall ensure thatany lubricationused hasan
auto-ignition greater than50Kabove the maximum surface temperature (80°Cfor T6,
95°C for T5 and 130°C for T4) and shallalso beresistantto carbonization. Lubricated
seals
Habonim recommend replacing all seals every500,000cyclesor 5 years, whichever
comes first. All new seals should be lubricated. See “Lubricants” paragraph to identify
which lubricant touse.
Bearings/soft parts
Habonim recommend replacing all bearings and soft parts every 500,000cycles or 5
years, whichever comes first.
Springs
Habonim recommend replacing all springs every 500,000 cycles.
Drive –Air Supply
• Use clean dry air according to ISO 4414.
• The air compressor must incorporate a filter on the intake system and contain only
lubricants that are resistant toignition orcarbonization at anticipatedtemperatures.
• The air delivery must not be provided by hoses that are manufactured from
elastomeric materials that can carbonize and form glow particles inanticipated
temperatures.
• Supply Pressure for the Compact actuators are as follows:
Double-acting: 2-8 barg (30-120 psig).
Spring-return: 3-8barg (40-120 psig).
For IIB, other inert gases may be used such as nitrogen, argon and sweet natural
gas.
Thin hydraulicoil can also be used. Do not usewater asa supply medium.
Severe operation
The ATEX does not cover Severe operating conditions:
• Application temperature less than -50 deg C
• Application temperature higher than +120 deg C
Certificationstandards: EN ISO 80079-36:2016 & EN ISO
80079-37:2016
Earthing/grounding
Electrical earthing / grounding must be done during actuator
installation.
Use one of the actuator's bottommounting
screws to connectgroundingwire.
Special condition for spring return/airto spring
All spring return actuator models shall have a Namur breather block
or a solenoid valvethat acts asa breatherfitted tobothportA and B
as shown in the manufacturer’s drawings. When the solenoid valve is
used in place of the breather, it shall replicate the breather block in
terms of preventing an internal atmosphere only the solenoid is
directlyinstalled intoportA and B.
When the actuator is operated on start up or from being offwith no
pressurisation, the end user must purge the internal parts of the
actuator in accordance with the IOMmanualto ensure there has not
been a build-up of an internal explosive atmosphere; to enhance
safety a Specific Condition of use to that effect applies (Prior to
putting the equipment into operation, the internal chambers of the
actuator shell be purged with clean, dry air from a non –hazardous
area or an inert gas; refer to equipment IOMmanual). Once purging
has been completed,the end user shall startthe actuatorby supplying
air pressure toport A. At this point,a V-shapedgasket atthe breather
block device moves to the left and allows non-explosive
instrumentation air filling the inner chamber of the actuator. At the
same time the air, whichis in thespring chamber,willbe pushed out
by the piston’s movement through the actuator's port B and out to
the exit orifice. The outer atmosphere will no longer enter the
actuator and the actuator will only contain non-explosive
instrumentation air in both chambers.
Closing the actuator by stopping the pressure supply toportA. At this
point, the V-shaped gasket will move to the right due to the
instruments air pressure in the internalchamberand redirect itfrom
the inner chamber towards the exit orifice. At the same time the
outgoing air will fill the spring chambers.

Three Piece High Pressure Ball Valves –24/H24 Valves Series
Three Piece High Pressure Ball Valves –24/H24 Valves Series
4
4. Limitations
The correct selection ofmaterialsof construction,seats and seals, internalvalve
components and pressure/temperatureratings determinesthesafeuse of thevalvesand
the particularperformancerequirementsfor
the application.
This information can be found on thename platewelded to the valve body.
The combined corrosion and erosion allowanceforthe valvebodywallthicknessis
1(mm). When this allowance hasgone,
the valve should nolongerbeused. Inspectthe
valve wallthickness every time the valveis maintained.
Refer
toHabonim ChemicalCompatibility Chartto determinethecorrosion ratefor your
application.
As the variety of applications these valves can be usedin is large, it is impossible to
coverallinstallation
and maintenance instructions for servicing the valves.
Habonim's standard valves design is for relative humidity of 50% and SATP (Standard
AmbientTemperature andPressure)environmentconditions.
Itis the owner’sresponsibility to use the valves as
recommended and in accordance
withthe pressure/temperaturelimitsand chemicalcompatibility forboth inner&
outerparts asstatedin thismanual.
Where
in doubt, please consult with Habonim.
Any unstable fluid orgas should be identified by its manufacturer and must not beused
withHabonim valves.
CAUTION:The valves should be used in awell-designed, adequately protected system to
ensure that externaland internalpressure and temperature limitsdo not exceed the valve
limits.
The valve rating is definedas the lowerrating of the seatand valve body.
Valve surface temperature may become extremely hot or cold due tooperating conditions.
Prevent any type of direct contactwith the valve that may cause harm or injury .Avoid direct
contactwith the valve by wearing protective gloves.
The valves are not designedto operate duringor afterearthquakesorunderfatigue conditions.
It is the responsibility of the owner to determine if fatigue conditions exist.
The process fluid temperature shallnot exceed the ignition temperature of the dust.
WARNING:USEOF THEVALVEISAPPLICATIONSPECIFIC. BESURETHATTHEVALVEIS SUITABLE
FORITSINTENDED SERVICE. IF YOU HAVEANY QUESTIONS CONCERNING THE USE,
APPLICATION ORCOMPATIBILITY OF THE VALVE WITH THE INTENDED SERVICE,CONTACT
HABONIMFORMOREINFORMATION.
DO NOTEXCEEDTHE VALVEPERFORMANCELIMITATIONS!
EXCEEDING THEPRESSUREORTEMPERATURELIMITATIONSMARKED
ON THE VALVELABELPLATEMAY CAUSEDAMAGE AND LEADTO
UNCONTROLLEDPRESSURERELEASE. DAMAGEORPERSONAL
INJURYMAYRESULT.

Three Piece High Pressure Ball Valves –24/H24 Valves Series
Three Piece High Pressure Ball Valves –24/H24 Valves Series
5
5. Storage
Prior to storage, inspect the valve for shipping damage. Keep all protective
packaging, flange coversand end caps attached to the valvesduring storage. It is
recommended to keepthe valves in aclean anddry
environment untilit is ready
foruse.
Carbon Steel valveshavea“black oxide”and oildipped finish. Thisnontoxicprocess
is performed to retard rusting during storage. Itis not asubstituteforpaintor other
means of protectivecoatingtobe applied to the valveonce installed.
Stainless steel valves have their natural finish and do not need any additional protection once
installed.
5.1.
L ong Term Storage
5.1.1.
Itis advisable to store thevalves in waterproofconditions.Ballvalves
should be protected to safeguardagainsthumidity,Moisture,dust,dirt,
sand,mud,saltspray,andseawater.
5.1.2.
Manualball valves must remain in the open position during the period ofstorage.
5.1.3.
Actuatedvalves (failto close position) remainin closed position during this time.
5.1.4.
Valves may bestoredas shipped,providedthe abovestoragelocation and
equipment orientation
instructions are followed
5.1.5.
In order to prevent damage,protectivecoverson valve ends should
not be removed until
immediately prior to installation.
5.1.6.
Visualinspection should beperformed onasemi-annualbasis and results recorded.
6. Installation
The installation procedure forHabonim ballvalvesis criticaltoensuring both longlife
andsatisfying
performance.Valves stored on site,awaiting installation, should be
keptin theiroriginalpacking, in dry
conditions, wheredamagewillnot occur(See
Para. 4).
Before carrying out theinstallation, it is important to follow the basicprocedures described
below:
6.1.
G e ne ral
6.1.1.
Itis essentialto flush the line prior to assembling any valveontheline.
6.1.2.
Carefully unpack the valveandcheck valvenameplateforidentification of materials.
6.1.3.
Remove anyspecialpackingmaterialssurroundingthevalve.
6.1.4.
Check the valvefortheflowdirection indication marks. Appropriatecaremust be
taken, to installthe
valveforproperfloworientation.
6.1.5.
Inspectthe valveinteriorthrough theendports to determineit is cleanandfree
fromforeignmatter
accordingtoASMEG93-03E1.
6.1.6.
Cycle the valve and inspectany functionally significant features.
6.1.7.
Readallthe literature andnoteanyspecialwarningtagsorplates attached to thevalve.
6.1.8.
Before installation check toinsurethat theflowline balls are in the fully open
position in orderto prevent possible damagetothe ballsand seats.Thevalve
performance depends on itsoriginal
conditions. At any stagedonot leave the
valve in the partially open position oneitherofthe lines.

Three Piece High Pressure Ball Valves –24/H24 Valves Series
Three Piece High Pressure Ball Valves –24/H24 Valves Series
6
6.2.
V a lve M arkin g an d L abelin g
6.2.1.
All valves marking is ona nameplate which is spot weldedtothe valvebody.
6.2.2.
Valves for theEuropean market andabove1”carry the CEmark with theinformation
requiredby the
PED.
6.2.3.
The valve markings that are accordingto API-6D standardarepresentedin orderto
provide the user
fulltraceability andinformationregardingthevalve.Unlessotherwise
requested,nameplateswillbe securedto the valvebody andwillbe visible to user. The
information on the nameplateis as described below:
Standard Habonim Tag
Standard CE Tag
Standard ATEX Tag

Three Piece High Pressure Ball Valves –24/H24 Valves Series
Three Piece High Pressure Ball Valves –24/H24 Valves Series
7
Standard API-6D Tag
6.3.
Insta llation in a vibrating environm ent
When installing a cryogenic valve with an actuator in a normal vibrating environmentthe whole
unit MUST be fixed with a stable fixation to a rigid area.
When installing a cryogenic valve with an actuator in an inclination angle it is CRITICAL to do a
stable fixation to the whole unit to a rigid area.
For a non-cryogenicvalves it is recommended to dofixation in a normal vibrating environment.
When installing a valve in a high vibrating environment suchas foran off-road application -
please contact Habonim.
6.4.
T hr e aded End Valves
6.4.1.
Valves with threaded ends should betreated as a single unit and should not be
dismantled when installingtopipeline.
6.4.2.
Before installingthevalves,makesure thatthethreadsonthemating pipeare freefrom
excessivegrit,
dirt or burrs.
6.4.3.
When tighteningthe valve, apply apipe wrench orspannerto theend connector
closest tothe pipe beingworked,usingstandardpipingpractices.
6.4.4.
Useappropriatejoiningsealantsmaterialincorrectquantities.
6.4.5.
If“back-welding”is required onthreaded endvalves, refertotheinstructions forWeld
End valves orto
the “Habonim Welding Instructions” bulletin.

Three Piece High Pressure Ball Valves –24/H24 Valves Series
Three Piece High Pressure Ball Valves –24/H24 Valves Series
8
7. Operating Instructions
Habonim Valves providetight shutoff when used under normalconditions and in accordance with
Habonim’s
published pressure/temperature chart.
If these valvesare usedin a partially open (throttled)position,seat lifemaybereduced. Consult with
Habonimfor
theproperseatmaterialselection.
Onmanualoperatedvalves, thevalveoperationis done by turning thevalvehandle 90° clockwise toopen
(handle is parallelto flow line), and 90° counterclockwise toclose (handleis perpendicular to flow line).
Forunidirectionaldesignedvalves;aflowarrowindicates theflowdirectionofthevalveforproperinstallation.
A
silicone-based lubricant is applied to assist valve break in.The lubricant, if unacceptable, may beremoved by a
solvent wash.
If ashut-off valveis installed for end of line service,it mustbe ensuredthatit is closed with ablind end
connection and the valve is securedagainst being opened unintentionally.
WARNING: Never look into the valve bore while the valveis in a flow line. Pressure and
fluids could escape from the valve causing harm or injury.
To prevent leakage, malfunctions resulting from internal wear or seal degradation, the
user must establish a preventive maintenance and inspection program. This program
must include:
1. Inspection of parts to detect loss of wall thickness which may result in decreased
pressure capacity (see Para.3 foracceptable reduction ofwall thickness).
2. Routine replacement of seals and inspection for proper operation (See Para. 7 for
maintenance instructions).
Valveoperating torques, as published in the Habonim literature,are the normal
expected maximum break-out torques. These torques have been confirmed by
laboratory testing of each valve under controlled conditions. Highly viscous or
abrasive media, frequency of operation and temperature fluctuations could cause an
increase in valve torque.

Three Piece High Pressure Ball Valves –24/H24 Valves Series
Three Piece High Pressure Ball Valves –24/H24 Valves Series
9
8. Maintenance
HABONIM valveshave along andreliablelife,and maintenance is seldomrequired. Whenmaintenanceis
necessary,valvescan be refurbished onsite.
To extend valveperformanceand reduce possible plant problems, thefollowingprocedures should be followed:
7.1.
Ifleakage around the stem is noticed,check thestem nuttorqueaccordingto value in Table1in the
Disassembly and assembly manual. Ifthe leakcontinues, tighten thegland nutabout a 1/4-turn as a
routine maintenanceprocedure. Thiswillcompensateforany wearorsettling of thegland packing.
Caution: Excessive tightening of the stem nut can result in accelerated seal wear
and high valve operating torque.
7.2.
It is strongly recommended totightenthe stemnuttorqueaccordingto value in Table1in the
Disassembly andassembly manualevery 15,000cycles.
7.3.
Ifthe valveis removedfromthe lineand disassembled,replacementof allseatsandsealsis
recommended
usingthe appropriateHabonim Repairkit.Examineallmetallicsealingsurfacessuch as
ball, stem, andthe
surfaces on theendconnectorsthatcontacttheseats forwear,corrosionordamage.
7.4.
Only Habonim authorized spareparts should beused.DefaultrepairkitpartsfromHabonim canbe found
at"components&materials"inHabonim catalog.
7.5.
In addition torepair kits, otherspareparts areavailablefromHabonim, suchas stem,glands, bolts,
screws
andnuts.
7.6.
Should additionalparts be required,it is recommended that thecompletevalve bereplaced.
7.7.
When ordering repairkits, pleaseprovide thevalvesizeand fullfigure numbercodeand series,
engraved
onthe valve IDtag.

Three Piece High Pressure Ball Valves –24/H24 Valves Series
Three Piece High Pressure Ball Valves –24/H24 Valves Series
10
9. Packages Assembly and Disassembly
Disassembly
Do not attemptto maintain the actuator while it is still
connectedto the valve or to any ancillary device.
Verify thatthe actuator is not pressurized.
Checkthat the airports are vented and thatspring return
actuators are in the fail close position.
1. Remove the air hose or the solenoidvalve fromthe
actuator.
2. Release (one turn) the boltsconnectingthe bracket
and the actuator bottom plan.
3. Remove completely the bolts connectingthe bracket
and the actuator bottom plan.
4. Hold the actuatorand lift it away fromthe valve.
5. Remove the adaptor and place it in a secured place.
6. Remove the boltsconnectingthe bracket andthe
valve ISO5211 pad.
7. Keep all parts in a clean and secured place.
8. Follow the instructions detailed in the valve IOM
and the actuator IOM in conjunctionwith this
instructions.

Three Piece High Pressure Ball Valves –24/H24 Valves Series
Three Piece High Pressure Ball Valves –24/H24 Valves Series
11
Assembly
Spring return actuator
For Normally Closed (NC) valve (valve closed on air
failure), turn the valve to its closed position.
For Normally Open(NO) valve (valve opened onair
failure), turn the valve to its open position.
Double acting actuator
Valve position is irrelevant.
1. Smear grease (thin Layer) on the bolt’s threads,
valve stemflats and adaptorsquare.
2. Bolt (hand tight) the bracket to the valve ISO5211
pad.
3. Place the adaptor on the valve stem, checkthat the
adaptor fitssnugly onto the valve stemwithoutplay
and is in the correct angular relationshipto the
actuator gear shaft.
4. Make sure the adaptor sits on the valve stemtip, and
there is an air gap betweenthe stemnutlockclip and
the adaptor bottomplan.
5. Place the actuator on the bracket, making sure that
the indicator shows the correct valve position(openor
closed).
6. Assemble the bolts with theirwashersin their
positions, but do not tighten themfully.
7. Supply air to port A and check that the stroke of the
actuator matches the limits of the stroke of the valve.
Adjust as necessaryand tightenthe bolts fasteningthe
valve and the actuator.

Three Piece High Pressure Ball Valves –24/H24 Valves Series
Three Piece High Pressure Ball Valves –24/H24 Valves Series
12
8. Carry out an operatingcheckwith the air pressure
connected to port A, in the case of a spring-return
actuator, or to port B for a double-acting actuator.
Ensure that openingand closing of the valve is complete,
i.e. the ball and valve ports are correctly alignedwhen the
valve is open. If the valve openingis notcomplete, align
the ball port position by turning the actuator adjustment
screws. New actuatoradjustment screws are locked in
place
by usingLoctite221, any change of screws position, must
be repeated with renewalof the glue overthe screws
thread.
9. Tightenall bracket bolts with suitable spanner.
10. Hold the adaptorand lift it up anddown (up to 1 mm
recess), make sure notension exerted onthe valve
stem by the adaptor.
11. Connectthe air hose or solenoidvalve to the actuator.
Warning–Movingparts can cause seriousdamage to
employees. Remove handsand tools from the
bracket area and from the valve port area.
12. Pressurize the actuator(port A) with air pressure
adjusted tothe actuator spring configuration.
13. Inspectvalve and actuator quarterturn free
movement.
14. Depressurize the actuatorand inspectsafe returnto
start position.

Three Piece High Pressure Ball Valves –24/H24 Valves Series
Three Piece High Pressure Ball Valves –24/H24 Valves Series
13
Disassembly & Assembly Manual
Three Piece High Pressure BallValves
Series included:
24 Series
Sizesincluded:
¼” –1.5”(DN8 –DN40)

Three Piece High Pressure Ball Valves –24/H24 Valves Series
Three Piece High Pressure Ball Valves –24/H24 Valves Series
14
Contents
1.
General .............................................................................12
2.
Disassembly......................................................................12
3.
Assembly...........................................................................13
Habonim cannot anticipate all of the situations user may encounter while installing and using Habonim
valves. The user MUST know and follow all applicable industry specifications on the safe installation and
use of these valves.
Misapplication of the product may result in injuries or property damage. Refer to Habonim product
catalogues, product brochures and installation, operating and maintenance manuals for additional
product safety information or contact Habonim.
Keep hands and objects away from the valve ports at all times. Actuated valves could be accidentally
operated, resulting in serious injury or valve damage.
Before removing a valve from the line, always make sure the line has been depressurized and
drained. Cycle the valve a few times to relieve any pressure that could be trapped in the body
cavity.
Utmost caution must be taken when handling a valve that has toxic, corrosive, flammable or a
contaminant nature media flowing through its pipeline.The following safety precautions are
recommended when dismantling valves with hazardous media:
Wear safety glasses, protective headgear, clothing, gloves and footwear.
Have available running water.
Have a suitable fire extinguisher when media is flammable.
Do not try to operate a valve that exhibits any sign of leakage. Isolate the valve and either repair or replace
it.

Three Piece High Pressure Ball Valves –24/H24 Valves Series
Three Piece High Pressure Ball Valves –24/H24 Valves Series
15
1.
General
•
Itis strongly recommendedto reviewboth thedisassembly and assembly chaptersbeforegetting
started.
•
Forany discrepancies, please contact Habonim.
2.
Disassembly
•Cycle the valve withtheline pressurefully relievedbeforeattempting to removethe valvefrom the
pipeline, to ensure pressurehasalsobeen dischargedfrom thevalvecavity.
•Set the valve to open position.
•Remove the dowelpins.
•Carefully removetheends from thevalvebody.
•Remove anddiscard the seats,bodyseals and allthe valve parts.
•Set the valve to close position.
•Supportthe ballto prevent it fromfallingoutof the valve body andsetthe ballaside in a clean
secure areaforreuse.
•Remove stemnutand allthe stemassembly components.
•Place all the removedcomponents, inacleanand secure area.
•Push the stem down intothe bodyandremove it.
•Discardthe stem thrust seals, care taken notto scratchornick the stembore areaof the body.
•Cleanthe stemand the stembore area.

Three Piece High Pressure Ball Valves –24/H24 Valves Series
Three Piece High Pressure Ball Valves –24/H24 Valves Series
16
3.
Assembly
The followinginstructionsare for valvesof all sizes.
3.1.
Lubricate the stemthrust seal(7) and thestemseal(9)
withappropriate lubricant.
3.2.
Place the stemthrustseal(7) onthestem(4).
3.3.
Insertthe stem (4) horizontallyinto the centerbody (1) withthe
threaded side firstandcarefully guide itup through the stembore.
3.4.
Holding the stem (4) upinsert the stemseal(9) overthe stem
(4) andinto the stem bore. Place thefollower(10) andO-ring(10B –
forH24 design),slidebearing (10A),two discsprings (11),and Thread
the stemnut(12) onto the stem (4).
3.5.
Tighten the stem nutontothe stemaccording totable 1.
3.6.
Add the tab lock washer(13).
Handles assembly forall valvesizes
3.7.
Lubricate the stemthrustseal(7) and thestemseal(9)
withappropriate lubricant.
3.8.
Place the stemthrustseal(7) onthestem(4).
3.9.
Insertthe stem (4) horizontallyinto the centerbody (1) withthe threadedside firstand carefully
guide it upthroughthe stembore.
3.10.
Holding the stem (4) upinsert the stemseal(9) overthe stem
(4) andinto the stem bore. Place thefollower(10) andO-ring(10B–for
H24 design),slidebearing (10A), two-disc springs (11),and Thread the
stem nut (12) onto the stem (4).
3.11.
Tighten the stem nutontothe stem
accordingto table 1
3.12.
Add the tab lock washer(13).
3.13.
Place the handle (14) on the top of thetab
lock washer.
3.14.
Place the serrated washer(15) and tighten
the handle nut(16) ontothe stemaccording
to table 1
3.15.
Thread the stop pin(8)
Valve Size*
Stem Size
Stem Thread
HERMETIX
N-m
Lb-In
1/4”-3/4”
1/2”
3/8”-24UNF
6
53
1”-
1 1⁄4
”
1”
7/16”- 20 UNF
11
97
1 1⁄2 "
11⁄2”
9/16”- 18 UNF
15
133
Detail A:
Table 1:
Detail A:
Detail A:
*For full bore valves (B24) use one size up

Three Piece High Pressure Ball Valves –24/H24 Valves Series
Three Piece High Pressure Ball Valves –24/H24 Valves Series
17
The followinginstructionsare for off-line assemblyof valvesall sizes
3.16.
Bringthe valve handleto the close positionand insertthe ball(3).
3.17.
Place the ballintothe valve body (1)untilthe stem tongueis engagedand
turn the stem sothe valveisatopenposition,to preventthe ballfrom
fallingout.
3.18.
Assembleboth seals (6A &6B) andseats (5) onthe valve ends (2) andthread the assembledend
into the valve body (1).
3.19.
Tighten the endsto the valve bodyapplyingtorque accordingto table 2.
3.20.
Applysome lubricant on the dowelpins (8a) and place theminto thevalvebody, toprevent the
endsloose.
3.21.
Set the valve to openposition.
Valve Size*
Hexagon dimension
Tightening torque
[mm]
N-m
Lb-In
1/4”-1/2”
38
120
1060
3/4"
46
150
1330
1"
60
180
1600
1.25"
70
210
1860
1.5"
75
240
2100
Table 2:
*For full bore valves(B24) use onesize up
Table of contents
Other HABONIM Control Unit manuals
Popular Control Unit manuals by other brands
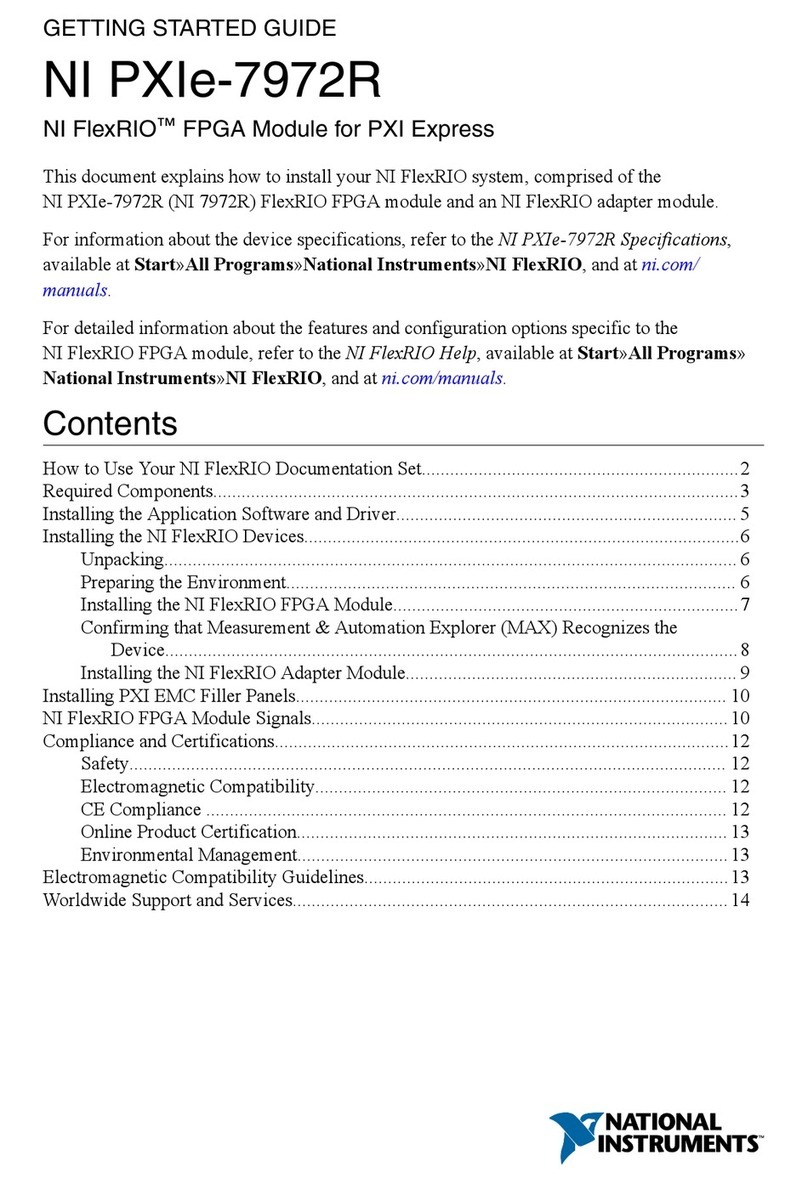
National Instruments
National Instruments NI PXIe-7972R Getting started guide
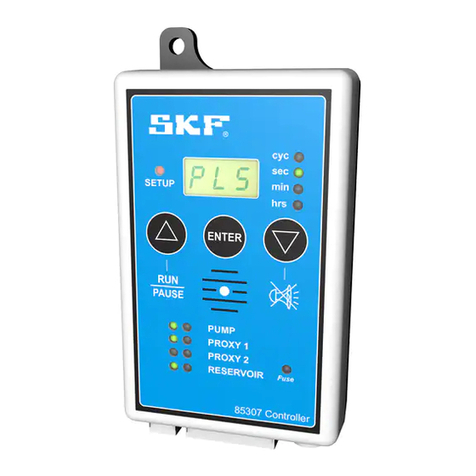
Lincoln
Lincoln SKF 85307 operating instructions
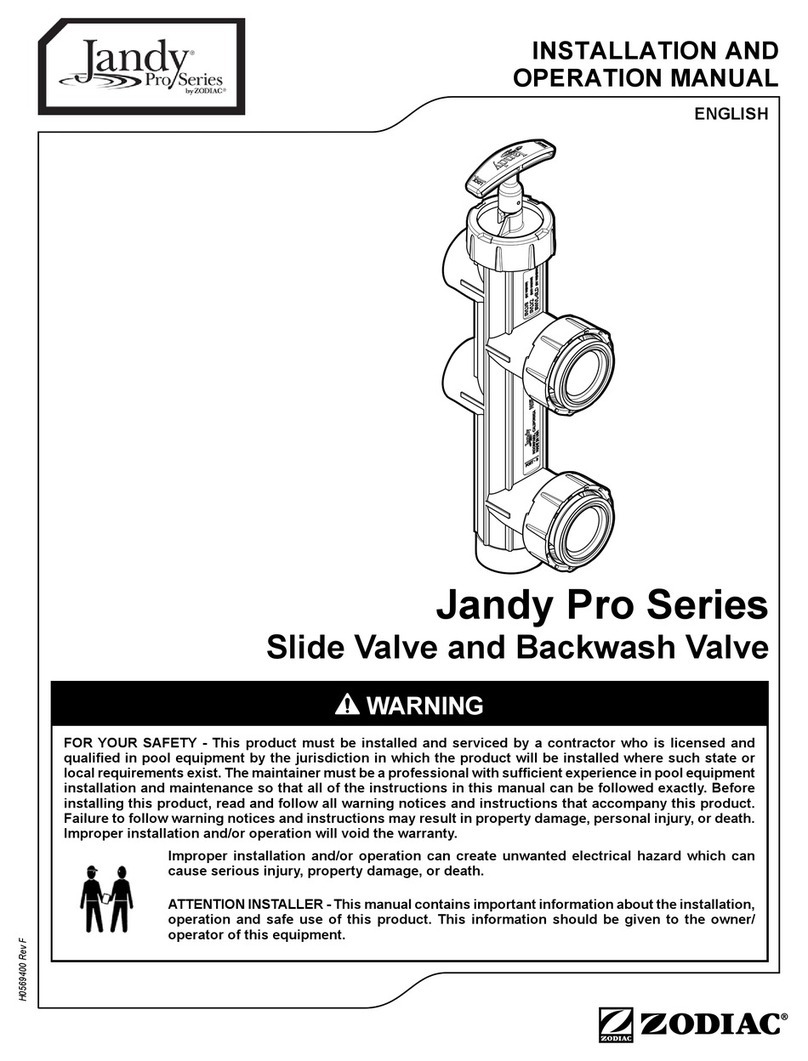
Zodiac
Zodiac Jandy Pro Series Installation and operation manual

jbc
jbc WSU instruction manual
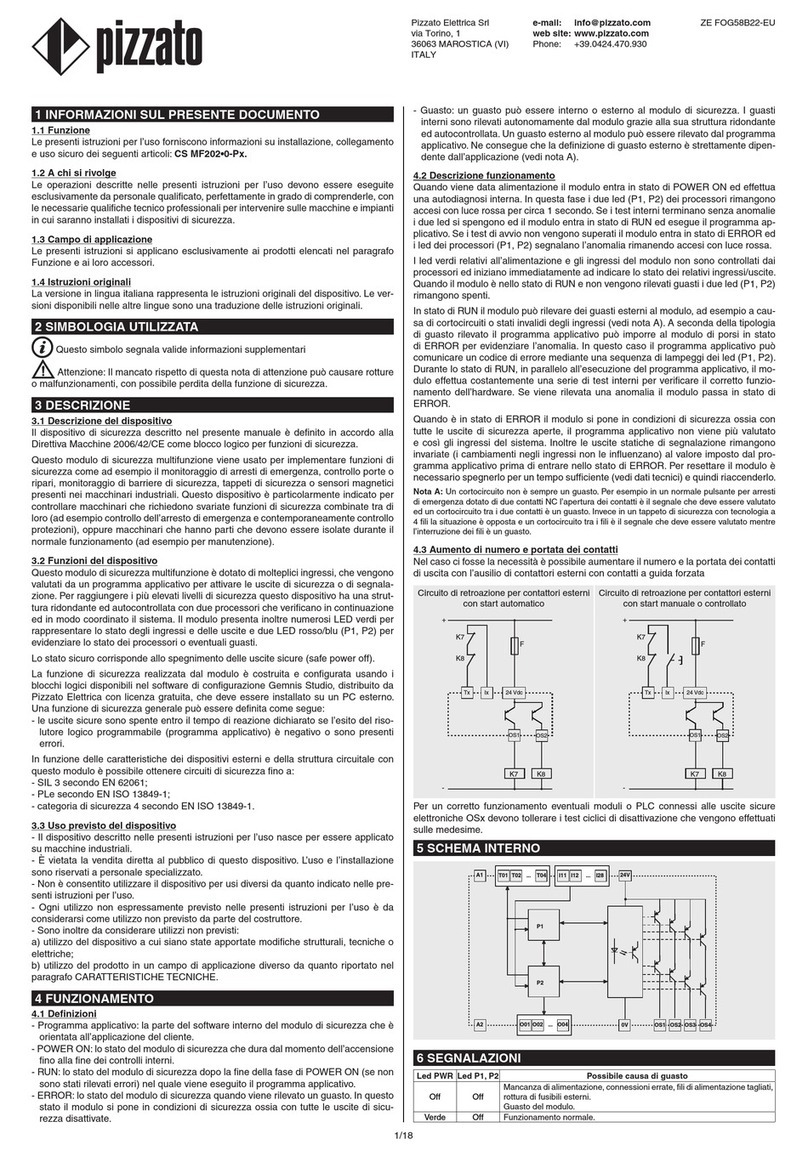
pizzato
pizzato CS MF2020-P Series operating instructions
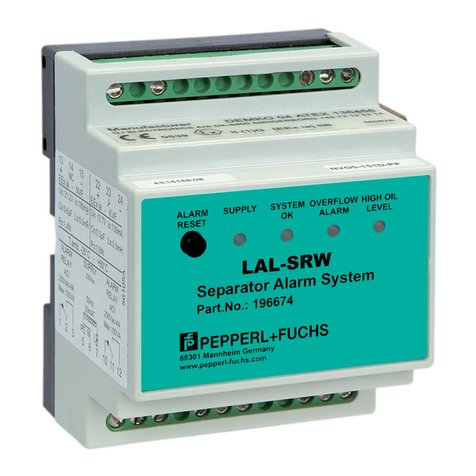
Pepperl+Fuchs
Pepperl+Fuchs LAL-SRW series manual
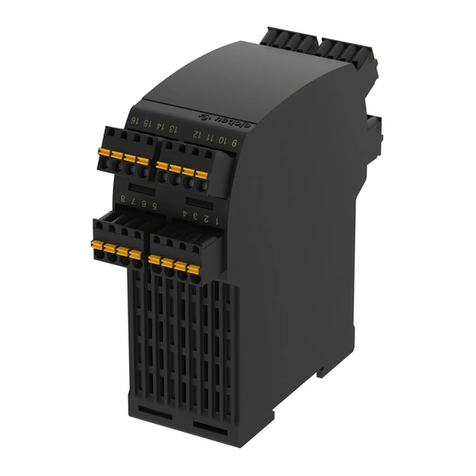
elobau
elobau eloFlex 471EFR Series Translation of the original operating instructions

BFT
BFT SIRIO FR-TMA Installation and user manual
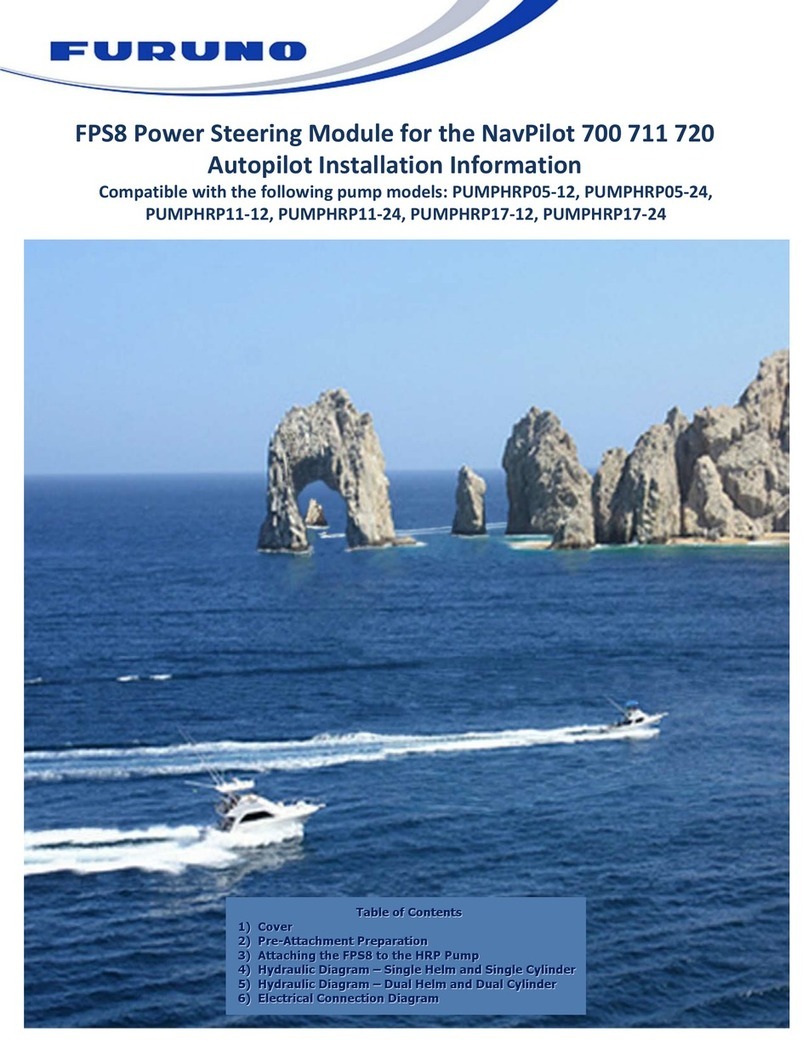
Furuno
Furuno FPS8 Installation information
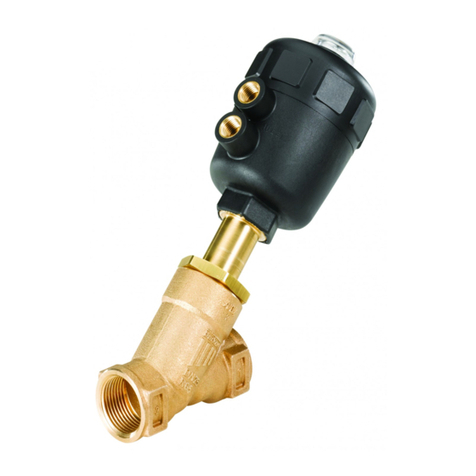
Burkert
Burkert Type 2000 operating instructions
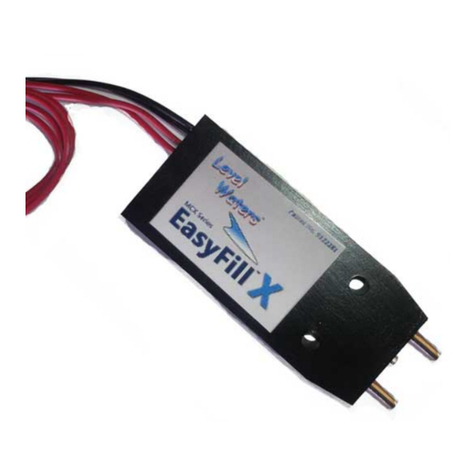
Level Waters
Level Waters EasyFill X MCX-11SW user manual
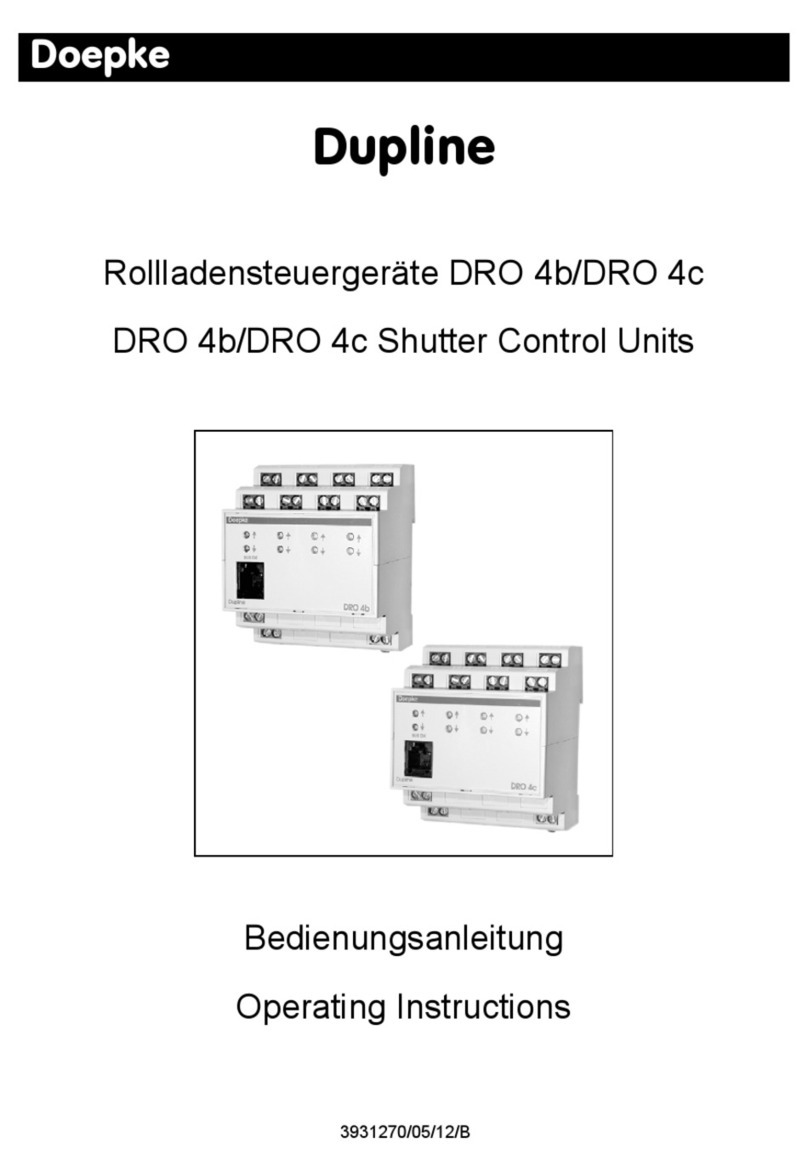
Doepke
Doepke Dupline DRO 4b operating instructions