HABONIM C47C User manual

Installation, Operating & Maintenance
Cryogenic Valves Series
WARNINGS & SAFETY INSTRUCTIONS
Habonim cannot anticipate all of the situations a user
may encounter while installing and using Habonim
valves. The user MUST know and follow all applicable
industry specifications on the safe installation and use of
these valves. Misapplication of the product may result in
injuries or property damage. Refer to Habonim product
catalogues, product brochures and installation, operating
and maintenance manuals for additional product safety
information or contact Habonim technical service.
1. Keep hands and objects away from the valve ports at
all times. Actuated valves could be accidentally
operated, resulting in serious injury or valve damage.
2. Before removing a valve from the line always make
sure the line has been depressurized and drained.
3. Utmost caution must be taken when handling a valve
that has toxic, corrosive, flammable or a contaminant
nature media flowing through its pipeline. The
following safety precautions are recommended when
dismantling valves with hazardous media:
a. Wear eye shield, protective headgear, clothing,
gloves and footwear.
b. Have available running water.
c. Have a suitable fire extinguisher when media is
flammable.
4. Do not try to operate a valve that exhibits any sign of
leakage. Isolate the valve and either repair or replace it.
5. Do not use or substitute non Habonim components or
parts in Habonim valves and assemblies.
1. GENERAL
This Installation, Operating & Maintenance manual covers the
instructions required for safe use of Habonim cryogenic ball valve.
Before using a valve, read the entire IOM carefully and make sure
you understand everything.
C47C, FC47C, FC47W
Fire-Safe (FC) and non Fire-Safe
Sizes included:
½” - 6” (DN15 - DN150)
Habonim ISRAEL
Tel: +972-4-6914911 / 6914903
Fax: +972-4-6914935
Habonim USA
Toll Free Phone: 1-866-261-8400
Toll Free Fax: 1-866-243-9959
Habonim China
Tel: + 86 21 64453190 *146
Fax: + 86 21 64453191
Habonim UK
Tel: +44-1633-484554
Fax: +44-1633-482252
Habonim Australia
Tel: +61 3 9556 5428
H-C47C-02/17
Inspired By Challenge

Cryogenic Valves
2
C47C, FC47C, FC47W
2. SIL
Under normal operating conditions the Habonim valve should be
inspected for proper functioning and signs of deterioration every
50,000 cycles or 6 months (whichever comes rst). Under severe
operating conditions inspection should be more frequently; detected
defects should be repaired promptly.
Severe operating conditions can be dened as:
• Application temperature less than -20 deg C
• Application temperature higher than +230 deg C
• Flow velocity higher than 5 m/sec for liquids, and 200 m/sec
for gaseous
• Acidic media PH < 5 or alkaline media PH > 9
Habonim recommend a proof test interval of 12 months; in case of
Fail to Open ESD system, a partial stroke is acceptable to conrm
that the installation is functioning properly.
For ESD systems with a Fail-To-Close demand, it is necessary to
plan a system shut-down; de-energize the system and inspect the
valve turning to its fully closed position.
It is essential to log-in the following parameters on site QA records
as a proof for preserving SIL capabilities: date, hour, name and
signature of the responsible engineer, air pressure on site, time to
close the valve, time to open the valve.
Habonim recommend valve full maintenance operation every
500,000 cycles or 4 years, whichever comes rst (refer to Para. 7 in
this IOM for maintenance instructions). The combined corrosion and
erosion allowance for the valve body wall thickness is 1 mm. When
this allowance has been eroded or corroded, mechanically removed
or otherwise, the valve should no longer be used. Inspect the valve
wall thickness every time the valve is maintained.
The estimated mean time to repair (MTTR) a valve, i.e. time net
(line draining or cooling down time excluded from the valve MTTR)
of replacing old valve with a new one is 60 minutes. Maintenance
team must read and understand the Habonim product IOM before
starting the operation. In case of a doubt please consult the Habonim
engineering team.
When a valve has been repaired or any maintenance was performed,
check the valve for proper function (proof testing). Any failures
affecting functional safety should be reported to the Habonim factory.
Client should consult the Habonim factory in order to obtain the
product assessment, FMEDA report, and other associated statistical
data to satisfy SIL level.
Special condition for safe use
When connected to an actuator the maximum rubbing speed of any
component within the valve must not exceed 1ms-1.
3. LIMITATIONS
The correct selection of materials of construction, seats and seals,
internal valve components and pressure/temperature ratings
determines the safe use of the valves and the particular performance
requirements for the application. This information can be found on
the nameplate welded to the valve body.
The combined corrosion and erosion allowance for the valve body
wall thickness is 1 mm. When this allowance has gone, the valve
should no longer be used. Inspect the valve wall thickness every
time the valve is maintained. Refer to Habonim Corrosion Data
Chart T-614 to determine the corrosion rate for your application.
As the variety of applications these valves can be used in is large,
it is impossible to cover all installation and maintenance instructions
for servicing the valves. It is the owner's responsibility to use the
valves as recommended and in accordance with the pressure and
temperature limits as stated in this manual. Where in doubt, please
consult with Habonim.
Any unstable uid or gas should be identied by its manufacturer
and must not be used with Habonim valves.
CAUTION:
The valves should be used in a well designed, adequately protected
system to ensure that pressure and temperature limits are not
exceeded.
Valve surface temperature may become extremely cold due to
operating conditions. Prevent any type of direct contact with the
valve that may harm the workers.
The valves should be used in a well designed, adequately supported
piping system such that it will not be subjected to undue forces or
hydraulic shocks during service.
The valves are not designed to operate during or after earthquakes
or under fatigue conditions. It is the responsibility of the owner to
determine if fatigue conditions exist.
4. STORAGE
Prior to storage, inspect the valve for shipping damage. The valves
are individually packed in a hermetically sealed polyethylene bag
lled with dry nitrogen. It is recommended to keep the valves in their
bags and in a clean and protective environment until ready for use.
Keep all protective packaging, ange covers and end caps attached
to the valves during storage.
5. LONG TERM STOREAGE
5.1. It is advisable to store the valves in waterproof conditions.
Ball valves should be protected to safeguard against
humidity, moisture, dust, dirt, sand, mud, salt spray, and sea
water.
5.2. Manual ball valves must remain in the open position during
the period of storage.
5.3. Actuated valves (fail to close position) remain in closed
position during this time.
5.4. Valves may be stored as shipped, provided the above
storage location and equipment orientation instructions are
followed
5.5. In order to prevent damage, protective covers on valve ends
should not be removed until immediately prior to installation.
5.6. Visual inspection should be performed on a semi-annual
basis and results recorded.
5.7. If the actuated valve (fail to close position) is planned for
long storage after dispatch it will be necessary to operate

Cryogenic Valves
3
C47C, FC47C, FC47W
6.1.3. All Habonim cryogenic valves are uni-directional and must
be installed for ow in one direction as indicated by the ow
arrow welded on the body and bonnet pad. Usually the arrow
points to the shutoff direction of the valve. In some cases
where it is not clear, relate to the arrow head as the low
pressure side and the arrow tail as the high pressure side.
BODY BALL
SEAT
PRES.SIZE
**** ****
**** ****
** ***
******************
Habonim logo
Body material
Seat material
Valve size
Valve description
Ball material
Work order
Max. pressure
INDUSTRIAL VALVES & ACTUATORS LTD
KFAR HANASSI, 1230500 IL
BODY
BALL
SEAT
BAR @ °C
1155
Habonim logo
Body material
Max. pressure @
Min. temperature Min. pressure @
Max. temperature
Valve description
CE mark
Ball material
Seat material
Valve size
Year manufacture
DN
P.O.
YR
BAR @ °C
once in 6 months for fully open/close position.
5.8. Ball valves should be operated for at least two complete
cycles before installing or returning to storage.
6. INSTALLATION
Caution: DO NOT install Cryogenic valves with the extended
bonnet tilted more than 450 from the upright vertical position.
(see gure 1)
FIGURE 1
Valve Tilting Limitation
6.1 General
6.1.1. Keep the valve in its polyethylene bag until ready for use.
Check the valve nameplate for identication of materials
(see Figure 2).
FIGURE
4.1.2. When the valve is in the closed position the ball relief hole
will be seen in the upstream port of the valve as indicated
by the arrow. The stem head has an engraved "T" mark
identifying the ball port and the pressure relief hole direction
(See Figure 3).
FIGURE 3
Valve Top View
4.1.4. When the valve is in the closed position the ball relief hole will
be seen in the upstream port of the valve as indicated by the
arrow. The stem head has an engraved "T" mark identifying
the ball port and the pressure relief hole direction (See
Figure 3).Inspect the valve interior through the end ports to
determine that it is clean and free from foreign matter.
6.1.5. Cycle the valve and inspect any functionally signicant
features.
6.1.6. Read all the literature, and note any special warning tags or
plates attached to the valve.
6.1.7. During installation, it is recommended that the valve ball be left
in the open position to prevent possible damage to the ball.
6.2 Threaded End Valves
6.2.1. Valves with screwed ends should be treated as a single unit
and should not be dismantled when installing to the pipeline.
6.2.2. Before installing the valve, make sure that the threads on the
mating pipe are free from excessive grit, dirt or burrs.
6.2.3. When tightening the valve, apply a pipe wrench or spanner
to the end connector closest to the pipe being worked, using
standard piping practices.
6.2.4. Use appropriate joint sealing materials in correct quantities.
6.2.5. If "back-welding" is required on screwed valves, refer to the
instructions for Weld End valves or to the "Habonim Welding
Instructions" bulletin.
6.3 In-line welding
6.3.1. Cryogenic valves suitable for in-line welding are designed
with extended ends. Habonim ends identication code XBW,
ETO. (Socket welding is not recomended for Cryogenic use)
6.3.2. Welding of valves shall be performed by a qualied welder
according to the ASME Boiler Construction Code Section
IX. For valves to be welded within the EEA, refer to the
requirements of ESR 3.1.2 of the Pressure Equipment
Directive 97/23/EC.
6.3.3. Valves must be in the fully open position to protect the ball
and seats from excessive temperatures during the welding
procedures.
6.3.4. Automated Valves in the "Fail Close" position should be

Cryogenic Valves
4
C47C, FC47C, FC47W
cycled to the open position.
6.3.5. Use a temperature stick and a wet cloth wrapped around
the center section to prevent overheating. DO NOT heat the
center section over 150°C (300°F).
6.3.6. Align valve to pipe line, ensuring proper t to minimize pipe
load. Tack weld only.
6.3.7. Complete welding in small segments. Allow enough time
for cooling between each segment.
6.3.8. After completing the welds, wait for the valve to cool below
90°C (200°F). Tighten the body bolts to torque gures and
tightening patterns according to Figure 5
6.3.9. It is recommended not to rotate the valve to the closed
position before ushing the line.
6.4 Weld End Valves not in-line
6.4.1. Valves that will be disassembled before welding carry a
packet with replacement body seals. Follow steps 2 to 6 of
the DISASSEMBLY section but to not discard the seat rings.
6.4.2. Prior to welding the ends to the pipe, ensure that the end
ats are aligned to the body ats.
6.4.3. Do not scratch or cut the seats and sealing surfaces of
the valves as this will cause valve leakage.
6.4.4. Assemble the valve without the ball and seats and follow
steps 1 to 7 for Weld End Valves.
6.4.5. After the valve cools, again follow steps 2 to 9 of the
DISASSEMBLY section and section 7 to 13 of the
ASSEMBLY section.
7. OPERATION
7.1. Flush the valves and pipeline with nitrogen, whilst preventing
the introduction of air, moisture or water into the cryogenic
valves and pipelines as this will freeze the valve and render
it inoperable.
7.2. Habonim Cryogenic Valves provide tight shut off when used
in accordance with Habonim published pressure/temperature
chart. If these valves are used in a partially open (throttled)
position, seat life may be reduced.
7.3. Valves are operated by turning the valve handle 90° anti-
clockwise to open, and turning 90° clockwise to close.
7.4. To prevent leakage or malfunctions resulting from internal
wear or seal degradation, the user must establish
apreventive maintenance and inspection program. This
program must include:
a. Inspection of parts to detect loss of wall thickness
which may result in decreased pressure capacity.
b. Routine replacement of seals and inspection for proper
operation.
7.5. Valve operating torques as published in the Habonim
literature are the normal expected maximum break-away
torques. These torques have been conrmed by laboratory
testing of each valve under controlled conditions. Highly
viscous or abrasive media could cause an increase in valve
torque.
Valve Marking and Labeling
All valve marking are on a nameplate which is spot welded to the
valve body. Valves for the European market and above 1" carry the
CE mark with the information required by the PED.

Cryogenic Valves
5
C47C, FC47C, FC47W
8. MAINTENANCE
8.5. GENERAL
8.1.1. HABONIM valves have a long and trouble free life, and
maintenance is seldom required. When maintenance is
necessary, valves can be refurbished on site.Rotate the
valve handle to the “open” position (see para. 5 for valve
handle position).
8.1.2. under normal operating conditions the HABONIM valve
should be inspected for proper functioning and signs of
deterioration every 50K cycles or 6 months (whichever come
rst)/ Under severe operating conditions inspection should
be more frequently.
8.1.3. Habonim recommended valve full maintenance operation
every 500 K cycles or 4 years (whichever come rst) . The
combined corrosion and erosion allowance for the valve
body wall thickness is 1 mm. when this allowance has been
eroded or corroded , mechanically removed or otherwise,
the valve should no longer be used.
8.1.4. To extend valve performance and reduce possible plant
problems, the following procedures should be followed:
àIf leakage at the stem is noted, tighten the gland
nut about a 1/8-turn as a routine maintenance procedure.
This will compensate for any wear or settling of the gland
packing.
Caution: Excessive tightening of the stem nut can result
in accelerated seal wear and high valve operating torque.
àIf the valve is removed from the line and disassembled,
replacement of all seats and seals is recommended
using the appropriate Habonim Repair kit. Examine all
metallic sealing surfaces such as ball, stem, and the
surfaces on the end connectors that contact the seats for
wear, corrosion or damage.
àOnly Habonim's spare parts should be used. A soft parts
repair kit from Habonim consists of the following:
• 2 x seats
• 1 x gland packing
• 1 x stem thrust bearing
• 1 or 2 x body seals
• 1 x bonnet seal
• 1 x stem bearing
àIn addition to soft parts kits, other spare parts available
from Habonim are: valve balls, stems, glands, bolts,
screws and nuts. Should additional parts be required, it is
recommended that the complete valve be replaced.
àWhen ordering repair kits, please provide the valve size
and full gure number code and series.
8.2. DISASSEMBLY
The following instructions are for off-line disassembly of
valves sizes 1 ⁄ 2” to 2-1/2” (or 2” full bore).
8.2.1. Cycle the valve with the line pressure fully relieved before
attempting to remove the valve from the pipeline, to insure
pressure has also been discharged from the valve cavity.
8.2.2. Bring the valve handle to the open position.
8.2.3. Remove all body bolts.
8.2.4. Cryogenic valve end connectors are interlocked to the body
(See gure 4). To overcome this feature it is necessary to
separate the ends from the body using a block of wood or
plastic mallet and swing the body out of the line. If the pipe
does not allow enough movement, remove the remaining
bolts and rotate the body through its port axis, enabling easier
access to the end connectors anges.
8.2.5. Bring out the body center section.
8.2.6. Remove and discard the seats, seat seals and body seals.
WARNING: Be careful not to damage the sealing surfaces.
8.2.7. Loosen the 4 cap screws and remove the extended bonnet
from the valve body.
8.2.8. Support the ball to prevent it from falling out of body. Set the
ball aside in a clean secure area for reuse.
8.2.9. Remove and discard the bonnet seal and the stem bearing.
8.2.10. Remove the handle nut, handle, locking clip, stem nut, two
disc springs, follower, anti-abrasion ring and stem seal. Place
all components removed, in a clean secure area.
Bare shaft valve
Remove locking clip, stem nut, two disc springs, follower, anti-
abrasion ring and stem seal. Place all components removed,
in a clean secure area.
8.2.11. Slide the stem and remove it from the extended bonnet.
8.2.12. Discard the stem thrust seal taking care not to scratch or nick
the stem or packing bore area of the bonnet.
The following instructions are for off-line disassembly of
valves sizes 2-1/2” to 8”.
8.2.13. Cycle the valve with the line pressure fully relieved before
attempting to remove the valve from the pipeline, to insure
pressure has also been discharged from the valve cavity.
8.2.14. Bring the valve handle to the open position. Warning: trying to
remove the valve body from the line in the closed position will
damage the ball.
8.2.15. Remove all body bolts.
8.2.16. Cryogenic valve end connectors are interlocked to the body
(See gure 4). To overcome this feature it is necessary to
separate the ends from the body using a block of wood or
plastic mallet and swing the body out of the line. If the pipe
does not allow enough movement, remove the remaining
bolts and rotate the body through its port axis, enabling easier
access to the end connectors anges.
8.2.17. Bring out the body center section.
8.2.18. Remove and discard the seats, seat seals, support ring and
body seals. WARNING: Be careful not to damage the sealing
surfaces.
8.2.10. 1

Cryogenic Valves
6
C47C, FC47C, FC47W
8.3. ASSEMBLY
The following instructions are for off-line assembly of valves
sizes 1 ⁄ 2” to 2-1 ⁄ 2” (or 2” full bore).
8.3.1. Clean valve parts completely using a cloth and IPA solution.
8.3.2. Lubricate the new stem thrust seal, bearing and packing,
with appropriate lubricant (Cassida grease EPS 2 or
equivalent - thin smear).
8.3.3. Place the stem thrust ring on the stem.
8.3.4. Slide the stem into the extended bonnet with the threaded
side rst and carefully guide it up through the bonnet bore.
8.3.5. Holding the stem up insert the new stem seal over the stem
and into the stem bore. Place the new anti-abrasion ring,
metal follower and the two disks spring (face to face) onto
the stem.
8.3.6. Thread the gland nut onto the stem. Tighten the gland nut to
the torque gures (table 1).
8.3.7. Place the locking clip on the gland nut by adjusting the
orientation of the nut (in the clockwise direction).
8.3.8. Insert the seal inside the extended bonnet bottom ange.
8.3.9. Insert the stem bearing into the valve body top platform.
8.3.10. Follow the welded arrow and place the ball inside the body
with the pressure relief hole towards the arrow's tail.
8.3.11. Holding the extended bonnet, slide the stem into the
ball. Note: the unique design will allow only one correct
engagement. (See gure 5)
8.3.12. With the bottom ange of the bonnet aligned with the valve
platform, and with the arrows on the body and bonnet
pointing in the same direction, hand tighten the bonnet bolts
and spring washers.
8.3.13. Tighten the bonnet bolts to the torque gures (table 3).
8.3.14. Place the handle, serrated washer and thread the wrench
nut on the stem. Holding the handle tighten the wrench nut
tight.
8.3.15. Place the new seats, seat seals and body seals in the valve
body.
8.3.16. Tighten the body bolts to the torque gures (table2), and
according to tightening pattern illustrated in gure 6.
TABLE 1
Gland Nut Tightening Torque For C47C, FC47C and
FC47W
C47C FC47C, FC47W
Valve size Stem thread Nm Lb-In Nm Lb-In
½”- ¾” 3⁄8”- 24 UNF 435 653
1”- 1¼” 7⁄16” - 20 UNF 9 80 11 97
1½”- 2”+2½"* 9⁄16” - 18 UNF 13 115 15 133
2½” M20 x 2.5 30 265 30 265
3” - 4” 1” - 14 UNS 60 530 60 530
6” - 8” 1½” - 12 UNF 120 1060 120 1060
* For Valve size 2 1/2" with stem 1 1/2"
8.2.19. Loosen the 4 cap screws and remove the extended bonnet
from the valve body.
8.2.20. Support the ball to prevent it from falling out of body. Set the
ball aside in a clean secure area for reuse
8.2.21. Remove and discard the bonnet seal and the stem bearing.
8.2.22. Remove the wrench bolt, wrench head and handle, stem
nut, stop plate, follower, bearing, anti-abrasion ring and
stem seal. Place all components removed, in a clean
secure area.
Bare shaft valve
Remove stem nut, two disc springs, location ring , tab lock
washer, follower, bearing, anti-abrasion ring and stem seal.
Place all components removed, in a clean secure area.
8.2.23. Slide the stem and remove it from the extended bonnet.
8.2.24. Discard the stem thrust seal taking care not to scratch or
nick the stem or packing bore area of the bonnet.
8.2.22.1.
8.3.17. Leave the valve in the open position for ushing the line.
The following instructions are for off-line
assembly of valves sizes 2-1/2” to 6”.
8.3.18. Clean valve parts completely using a cloth and IPA solution.
8.3.19. Lubricate the new stem thrust seal, bearing and packing,
with appropriate lubricant (Cassida grease EPS 2 or
equivalent - thin smear).
Warning: Stem thrust ring must be placed in the correct
orientation (See gure 7).
8.3.20. Place the stem thrust ring on the stem.
8.3.21. Slide the stem into the extended bonnet with the threaded
side rst and carefully guide it up through the bonnet bore
8.3.22. Holding the stem up insert the new stem seal over the stem
and into the stem bore. Place the new anti-abrasion ring,
metal follower, locking clip and the stop plate onto the stem.
Bare shaft valve
8.3.22.1.Holding the stem up insert the new stem seal over the
stem and into the stem bore. Place the new anti-abrasion
ring, follower, two disc springs, ,location ring and, tab lock
washer onto the stem.
8.3.23.Thread the gland nut onto the stem. Tighten the gland nut to
the torque gures (table 1).
8.3.23. Insert the seal inside the extended bonnet bottom ange..
8.3.24. Insert the stem bearing into the valve body top platform.
8.3.25. Follow the welded arrow and place the ball inside the body
with the pressure relief hole towards the arrow's tail.
8.3.26. Holding the extended bonnet, slide the stem into the
ball. Note: the unique design will allow only one correct
engagement. (See gure 5).
8.3.27. With the bottom ange of the bonnet aligned with the valve

Cryogenic Valves
7
C47C, FC47C, FC47W
FIGURE 5
Fool Proof Trim Design
platform, and with the arrows on the body and bonnet
pointing in the same direction, hand tighten the bonnet
bolts and spring washers.
8.3.28. Tighten the bonnet bolts to the torque gures (table 3).
8.3.29. Place the wrench head on the stem making sure it is
parallel to the stem groove for ball valve position. Insert
the handle through the wrench head and tighten with the
wrench bolt.
8.3.30. Place the new seats, seat seals, support ring and body
seals in the valve body.
8.3.31. Tighten the body bolts to the torque gures (table2), and
according to tightening pattern illustrated in gure 6.
8.3.32. Leave the valve in the open position for ushing the line.
Reduced
bore Full Bore Bolt
Thread
Tightening Torque
Nm in.lb
½” 1⁄4”, 3⁄8” M8 20 180
3⁄4” ½” M8 20 180
1" 3⁄4” M10 40 350
11⁄4” 1" M10 40 350
1 ½” 1 1⁄4” M12 65 575
2" 1 ½” M12 65 575
2½” 2" M12 65 575
3" 2 ½” M12 65 575
4" 3" M16 180 1590
4" M20 350 3100
6" M20 350 3100
8" M20 350 3100
* For M6 bolt use a suitable tool for hand tight close
Sizes ½” - 2½” Sizes 3" - 6"
TABLE 2
Body Bolts Tightening Torque
For C47C, FC47C and FC47W
TABLE 3
Bonnet Bolts Tightening
Torque For C47C, FC47C
Reduced
bore Full Bore Bolt
Thread Nm in.lb
½"-”3⁄4” ½" M5 6 55
1"-2" ”3⁄4”-1½” M6 9 80
2½” 2" M10 39 345
3"-4" 2½”-4" M12 65 575
6"" M16 160 1416

Cryogenic Valves
8
C47C, FC47C, FC47W
B
A
ø Ball port
G
C
H
D
S
ø W
TxL thread
F PCD
2
2
1
3
6
6
5
5
4
22
24
17
11
12
13
14
15
16
10
9
8
20
26
22
7a
18A
18
10A
7
21
28
28A
30
25
18A
18
½” & ¾”
without nut
1” - 2”
with nut
P
P
N thread
MStem flats
show valve
ball position
Preparation
for actuation
Item Description Material specications Qty.
14 Handle A240 430 1
15 Serrated washer A194 6 1
16 Handle nut DIN 3506 A4-80, A194 Gr 8M 1
17 Sleeve PVC 1
18 Body bolt EN 3506-1 A2-70, A193 Gr B8 8
18A Spring washer DIN 127 A2 8
20 Anti-static spring A313 302 1
21 Anti-static plunger A479 304 1
22 Arrow ow A167 304 2
23 Tag (not shown) A167 304 1
24 Bonnet seal PTFE, Graphite 1
25 Stem bearing PTFE 1
26 Bonnet A479 316L, A351 CF8M 1
28 Bolt A193 B8, DIN 912 A2-70 4
28A Spring washer DIN 127 A2 4
30 Dog tag A167 304 1
* Repair kit components
** Only with HermetiX™ re safe design
Item Description Material specications Qty.
1Body A351 CF8M, A494 M35-1, Bronze RG5 1
2End A351 CF8M, A494 M35-1, Bronze RG5 2
3Ball A351 CF8M, B574 N06022, Bronze RG5 1
4Stem A479 316/316L, A564 Gr.630 H1150D
17-4PH, B574 N06022 1
5* Seat CF PTFE, TFM, PCTFE (KEL-F) 2
6* Body seal PTFE, Graphite 2
7* Stem thrust seal CF PTFE(2), TFM(2), PCTFE (KEL-F) 1
7a* Anti-abrasion ring CF PTFE(2), TFM(2), PCTFE (KEL-F) 1
8Stop pin A582 303 1
9* Stem seal CF PTFE, TFM, Graphite(2) 1
10 Follower B783 316L 1
10A** Slide bearing TF316 1
11 Disc spring A693 631 17-7PH 2
12 Stem nut DIN 3506 A4-80, A194 Gr 8M 1
13 Locking clip A167 8, 8A 1
(1)
C47C series is Habonim's standard valve design without the HermetiX™
stem seal construction.
(2)
This material can only be used as part of the C47C design.
Size ¼" - 2"

Cryogenic Valves
9
C47C, FC47C, FC47W
B
A
ø Ball port
G
C
H
D
S
ø W
TxL thread
F PCD
M
M
QM
N thread N thread
DD
Stem groove
shows valve
ball position
Square
P
Preparation
for actuation
2
2
1
3
6A
6
5
5
4
22
24
17
14A
12
13
14
14B
16
10
9
820
26
22
7a
18A
18
10A
7
21
28
28A
30 25
18A
18
6
11
Size 2½" - 6"
Item Description Material specications Qty.
14 Handle C.St. Zinc plate, A240 316L 1
14A Stop plate A240 430 1
14B Wrench head A351 CF8M 1
16 Wrench bolt A194 B8, DIN 3506 A2-70 1
17 Sleeve PVC 1
18 Body bolt EN 3506-1 A2-70, A193 Gr B8 8
18A Spring washer DIN 127 A2 8
20 Anti-static spring A313 302 2
21 Anti-static plunger A479 304 2
22 Arrow ow A167 304 2
23 Tag (not shown) A167 304 1
24 Bonnet seal PTFE, Graphite 1
25 Stem bearing PTFE 1
26 Bonnet A479 316L, A351 CF8M 1
28 Bolt A193 B8, DIN 912 A2-70 4
28A Spring washer DIN 127 A2 4
30 Dog tag A167 304 1
* Repair kit components
** Only with HermetiX™ re safe design
Item Description Material specications Qty.
1Body
A351 CF8M, A494 M35-1, Bronze RG5
1
2End
A351 CF8M, A494 M35-1, Bronze RG5
2
3Ball
A351 CF8M, B574 N06022, Bronze RG5
1
4Stem A479 316/316L, A564 Gr.630
H1150D 17-4PH, B574 N06022 1
5* Seat CF PTFE, TFM, PCTFE (KEL-F) 2
6* Body seal PTFE, Graphite 2
6A Support ring A351 CF8M 1
7* Stem thrust seal CF PTFE(2), TFM(2), PCTFE (KEL-F) 1
7a* Anti-abrasion ring CF PTFE(2), TFM(2), PCTFE (KEL-F) 1
8Stop pin A582 303 1
9* Stem seal CF PTFE, TFM, Graphite(2) 1
10 Follower B783 316L 1
10A** Slide bearing TF316 1
11 Disc spring A693 Gr. 631 17-7PH 2
12 Stem nut DIN 3506 A4-80, A194 Gr 8M 1
13 Tab lock washer A240 304 1
(1)
C47C series is Habonim's standard valve design without the HermetiX™
stem seal construction.
(2)
This material can only be used as part of the C47C design.
This manual suits for next models
2
Table of contents
Other HABONIM Control Unit manuals
Popular Control Unit manuals by other brands

Aqua Systems
Aqua Systems SmartChoice II Wi-Fi quick start wi-fi setup
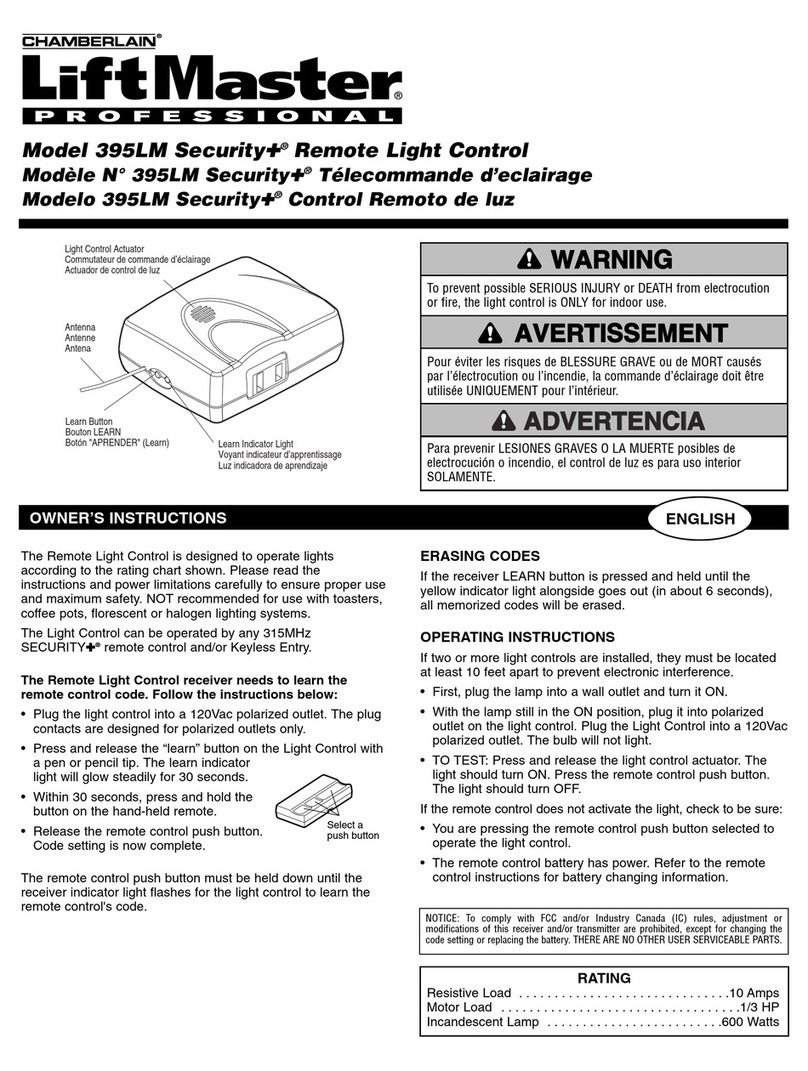
Chamberlain
Chamberlain LiftMaster Professional Security+ 395LM Owner's instructions
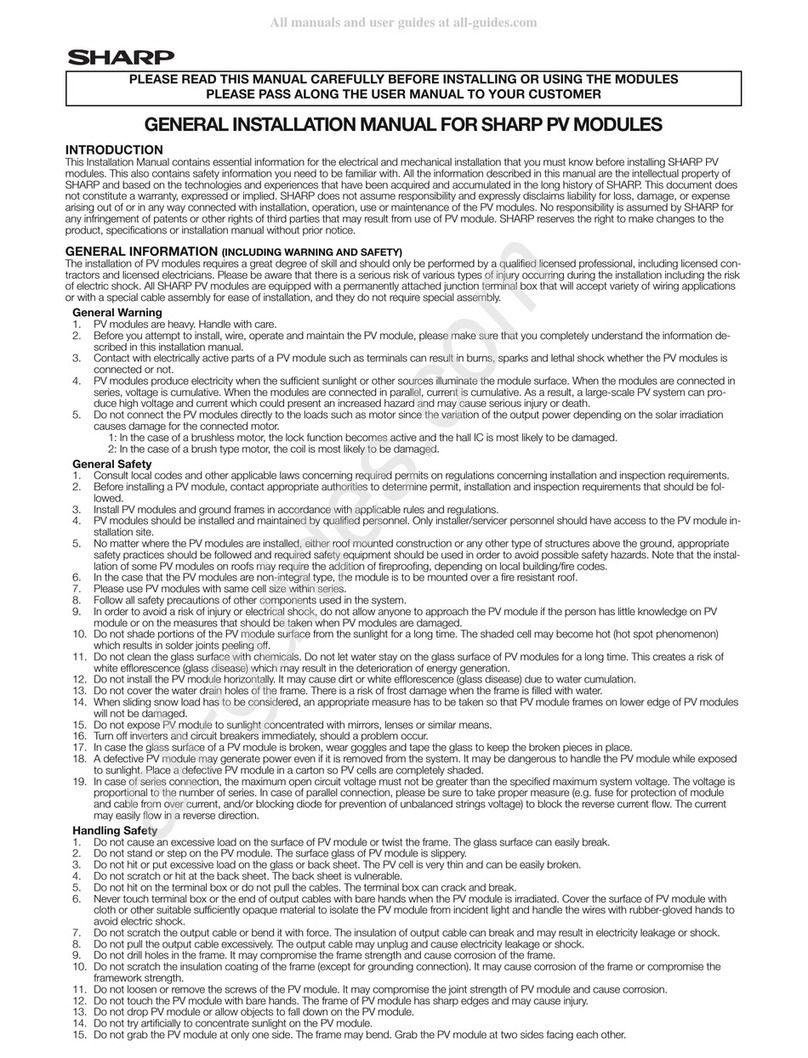
Sharp
Sharp ND-158E1F General installation manual
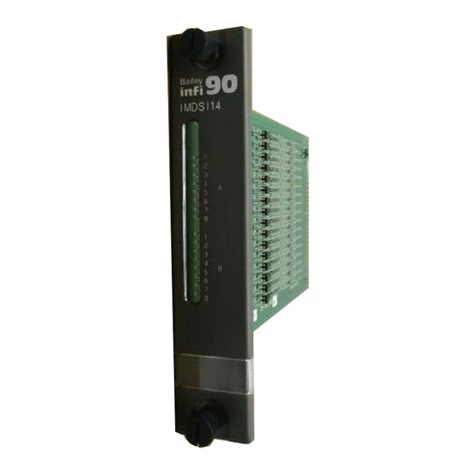
Bailey
Bailey Infi 90 IMDSI12 Instruction
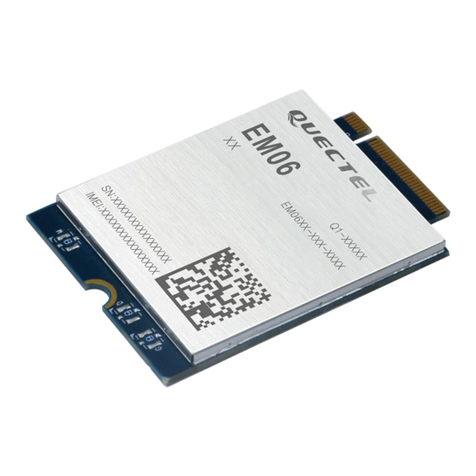
Quectel
Quectel EM06 manual
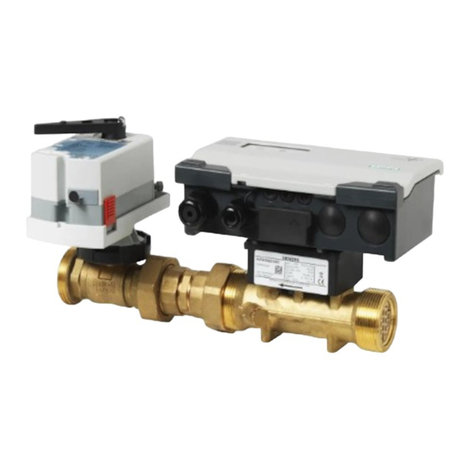
Siemens
Siemens EVG4U10E Series Mounting instructions