HANKISON SPX Flow FLEX Series User manual

FLEX Series
Refrigerated Type Compressed Air Dryers
Models: FLX 1.1, FLX 1.2, FLX 1.5-1, FLX 1.5, FLX 2.1, FLX 2.1-4, FLX 3.1, FLX 4.1, FLX 4.5, FLX 5.5
FORM NO.: 7440062 REVISION: 09/2018 READ AND UNDERSTAND THIS MANUAL PRIOR TO OPERATING OR SERVICING THIS PRODUCT.
INSTRUCTION MANUAL

Contents
INTRODUCTION .................................................................................................. 1
SAFETY............................................................................................................... 1
INSTALLATION ..................................................................................................... 1
HOW IT WORKS .................................................................................................. 3
CONTROLLER...................................................................................................... 3
START-UP/OPERATION........................................................................................ 4
MAINTENANCE................................................................................................... 6
FIELD SERVICE GUIDE......................................................................................... 7
ENGINEERING DATA ........................................................................................... 8, 9
DRAWINGS
General Arrangement
Model: FLX 1.1 ............................................................................................ 10
Model: FLX 1.2 ............................................................................................ 11
Models: FLX 1.5-1, FLX 1.5, FLX 2.1, FLX 2.1-4 ........................................... 12
Models: FLX 3.1, FLX 4.1 ............................................................................. 13
Models: FLX 4.5, FLX 5.5 ............................................................................. 14
Electrical Schematic
Models: FLX 1.1, FLX 1.2 (115V/1PH/60Hz)................................................ 15
Models: FLX 1.5-1 (115V/1Ph/60Hz) .......................................................... 16
Models: FLX 1.5, FLX 2.1, FLX 4.1 (230V/1Ph/60Hz) .................................. 17
Models: FLX 2.1-4, FLX 3.1, FLX 4.5, FLX 5.5 (460V/3Ph/60Hz).................. 18
Air and Refrigerant Flow Schematic ............................................................. 19
REPLACEMENT PARTS........................................................................................ 20, 21
MAINTENANCE KITS ........................................................................................... 22
NOTES................................................................................................................ 23
WARRANTY

1
INTRODUCTION
Compressed air is generated by compressing atmospheric air
of which contains moisture and other containments, into high
pressure air. After compression, the air is not saturated but when
it is cooled by the aftercooler, the RH remains 100%.
If it travels down the pipe line and cools further, moisture starts
to condensate into liquid water. Condensate water in the pipe
line is harmful to the manufacturing process as it causes rust
or sludge etc.
In order to avoid this problem, the only solution is to dry the
compressed air with an air dryer. Refrigerated compressed air
dryers are used as a cost effective and energy efficient solu-
tions for eliminating moisture from the compressed air system.
SPX Flow’s discovery of using Phase Change Material (PCM) as
a component in the refrigerated compressed air dryer to pro-
duce latent heat has encouraged great energy savings. Through
latent heat properties, it is able to save up to 99% of energy at
no load condition. This is indeed a breakthrough in refrigerated
compressed air dryer technology.
SAFETY
The dryers are designed and built with safety as a prime con-
sideration; industry accepted safety factors have been used in
the design. Each dryer is checked at the factory for safety and
operation. All necessary adjustments are made before shipment.
Follow the maintenance schedules outlined in this manual for
good performance and safe operation.
Only qualified personnel with proper tools should do mainte-
nance.
Safety instructions in this manual used to indicate hazard
seriousness levels are classified as follows:
Immediate hazard which WILL result in severe injury or
death.
Hazard or unsafe practice which COULD result in severe
injury or death.
Hazard or unsafe practice which COULD result in minor
injury or product damage.
Carefully read the following safety rules before proceed-
ing with installation, operation or maintenance. The rules
are essential to ensure safe dryer operation. Failure to
follow these rules may void the warranty or result in dryer
damage or personal injury.
1. Do not install or try to repair a dryer that has been damaged
in shipment. See Receiving and Inspection for instructions.
2. Compressed air and electricity have the potential to cause
personal injury or equipment damage. Before doing any
work on the dryer, be sure the electrical supply has been
locked and tagged and the internal pressure of the dryer
has been vented to the atmosphere.
3. Do not operate the dryer at pressures or temperatures
above the maximum conditions shown on the data plate.
4. Always supply electrical power that complies with the volt-
age shown on the data plate.
5. Do not readjust the dryer without factory authorization.
6. Do not operate the dryer with any dryer cabinet panel
removed.
Cooling air flow across the condenser may be reduced
if a dryer panel has been removed while the dryer
is operating, resulting in the dryer not functioning
properly and/or dryer failure. Failure to follow these
instructions may result in a non-warrantable dryer
failure.
7. Only a competent refrigeration mechanic works on the
refrigeration system.
8. Use only manufacturer’s genuine replacement parts. The
manufacturer bears no responsibility for hazards caused
by the use of unauthorized parts.
INSTALLATION
Inspect the dryer closely when it is received. Record any indica-
tion of damage on the delivery receipt, especially if the dryer
will not be immediately uncrated. Obtain the delivery person’s
signed agreement to recorded damages to facilitate future
insurance claims .
Since the dryer is shipped F.O.B. Factory, the manufacturer’s
responsibility for the shipment ceases when the carrier signs
the bill of lading.
If goods are received short or in damaged condition, notify the
carrier and insist on a notation of the loss or damage across
the face of the freight bill. Otherwise no claim can be enforced
against the carrier.
If concealed loss or damage is discovered, notify your carrier
at once and request an inspection. This is absolutely necessary.
Unless you do this, the carrier will not consider any claim for
loss or damage. The carrier will make an inspection and may
grant a concealed damage notation. If you give the carrier a
clear receipt for the goods that have been damaged or lost in
transit, you do so at your own risk and expense.
The manufacturer is willing to assist you in collecting claims for
loss or damage. Willingness does not make the manufacturer
responsible for collecting claims or replacing material. Claim
filing and processing is your responsibility.

2
Ambient Air Temperature
Locate the dryer indoors where the ambient air temperature will
be between 39°F (4°C) and 122°F (50°C). Intermittent operation
at ambient temperatures up to 122°F (50°C) will not damage the
dryer but may result in a higher dew point or dryer shutdown
due to high refrigerant discharge pressure (see Field Service
Guide). Call your local distributor if prolonged operation at
ambient temperatures above 122°F (50°C) or below 39°F (4°C)
is unavoidable.
Do not operate air-cooled dryers at ambient air temperatures
below 39°F (4°C). Such operation may result in low suction pres-
sure, causing freeze-up.
Location and Clearance
Mount the dryer on a level base and bolt down if the base vi-
brates. If the dryer is air cooled, install it in a clean, well-ventilated
area to reduce fouling of the condenser coils with dirt and dust.
Allow 39 inches (1000 mm) clearance on the sides and the front
of the dryer for cooling airflow on air-cooled dryers and for
service access on air-cooled dryers.
System Arrangement
Liquid water adversely affects dryer performance. To prevent
“slugging” the dryer with liquid water, locate the dryer down-
stream of an after cooler and a mechanical separator. Install
drain valves to discharge condensate that collects in these areas.
If the airflow is relatively constant and will not cause short term
overloading of the dryer, it is recommended that the dryer be
located downstream of the receiver tank. If the nature of the
application is such that the air demand regularly exceeds the
dryer flow rating, it is recommended that the dryer be located
upstream of the receiver.
For safety and convenience, install inlet and outlet shutoff
valves and depressurization valves at the locations indicated.
These valves allow the dryer to be isolated and depressurized
for servicing. Bypass piping may be installed around the dryer
for uninterrupted airflow when the dryer is serviced. If the com-
pressed air operation cannot tolerate wet air for short periods,
install a second dryer in the bypass line.
Compressed air systems commonly require filters to remove
compressor oils, particulates, condensed liquids and other
contaminants. When an oil-removal filter is used, install the
filter downstream of the dryer. At this location, the life of the
replaceable filter element is prolonged since the dryer removes
some of the entrained oil and drained through the separator.
Piping and Connections
The user must furnish piping unless otherwise specified. Con-
nections and fittings must be rated for the maximum operating
pressure given on the dryer data plate and must be in accor-
dance with applicable codes. Support all piping; do not allow
the weight of any piping to stress the dryer or filters. Inlet and
outlet shutoff valves and bypass valves are recommended. Pip-
ing should be at least the size of the inlet and outlet connections
to minimize pressure drop in the air system. See Specification
Table for dryer inlet and outlet connections.
Drains
Condensate must be drained from the dryer to prevent an influx
into outlet air. The FLEX dryers are equipped with an automatic
no loss drain valve and internal drain hoses up to the drain con-
nections on the dryer cabinets.
The automatic no loss drain valve uses two electrostatic capacity
sensors (high level, low level), so any condensate from com-
pressed air can be sensed correctly and discharged. Therefore,
the FLEX dryer can protect energy loss by discharging conden-
sate selectively.
The user must install a discharge line from the drain connection
and run it to a waste disposal collection system that meets ap-
plicable regulations. Pipe or copper tubing 1/2 inch or larger is
recommended for condensate discharge lines. Install the drain
lines so that condensate can be seen as it drains.
NOTE: Discharge is at system pressure. Drain line should be
anchored.
NOTE: Condensate may contain oil. Comply with applicable laws
concerning proper disposal.
Drain Valve Operation
A. Verify that isolation valves are open. If the drain fails to
discharge after the valve is energized, the electronic control
circuit will repeatedly energize the valve in an attempt to
clear the discharge port. If, after 60 seconds, the drain still
fails to discharge, the control circuit then switches to the
alarm mode. In this mode the valve is de-energized and the
red alarm light is activated on the drain. The valve is then
automatically energized every 4 minutes for 5 seconds.
Check the drain operation. Push drain (push-to-test) button
on the drain or the Electronic Controller (if equipped) to
energize drain. A flow of condensate and/or air should be
present at the drain outlet. The alarm mode automatically
clears after the drain returns to normal operation.
B. The condensate flows through the feed line (1) into the
condensate drain and accumulates in the housing (2). A
capacitive sensor (3) continuously registers the liquid level.
As soon as the container is filled, a fixed waiting period
begins during which more condensate accumulates. After
the waiting time has expired the pilot valve (4) is then ac-
tivated and the diaphragm (5) opens the outlet line (6) for
discharging the condensate.
When the condensate drain has been emptied, the outlet
line is closed again quickly and tightly without wasting
compressed air.
Figure 1.
Schematic diagram of the no loss drain valve

3
Electrical Connections
Operation of dryers with improper line voltage constitutes
abuse and could affect the dryer warranty.
The dryers are constructed according to NEMA Type 1 electrical
standards. Field wiring must comply with local and national fire,
safety and electrical codes. Installation must be in accordance
with the National Electrical Code. Confirm that your line voltage
is the same as the voltage listed on the dryer data plate. Refer
to Figures 6A, 6B, 6C, and 6D electrical schematics.
HOW IT WORKS
Phase Change Mechanism of the FLEX Dryer
1. When the refrigeration compressor and the condenser fan
are running, the cold refrigerant in the chiller (evaporator)
cools the liquid Phase Change Material (PCM) which gradu-
ally solidifies.
2. When the PCM is sufficiently cooled and solidified, the
refrigeration compressor and condenser fan will stop.
3. The compressed air is continuously cooled by the PCM
while the refrigeration compressor is inactive. No power
is consumed during this period.
4. The PCM gradually liquefies as it adsorbs heat from the
compressed air, and when fully melted, the refrigeration
compressor and condenser fan resume to cool the PCM.
Compressed Air flow
The dryers use refrigeration cooling to condense entrained
moisture out of the air stream. Warm saturated air enters the
air-to-air heat exchanger where it is cooled by outgoing cold
air. The inlet air is further cooled in the refrigeration chiller. The
condensate is removed from the air stream by an electronic
drain valve.
The cold, dry air is reheated by incoming warm air as it passes
back through the air-to air heat exchanger. Using the outgo-
ing air to pre-cool the inlet air condenses up to 65 percent of
the moisture out of the inlet air before it reaches the chiller.
Pre-cooling the inlet air reduces the heat load on the refriger-
ant compressor, permitting the use of a smaller refrigerant
compressor.
Figure 2.
Schematic diagram of the compressed air flow and
refrigerant
CONTROLLER
There are two kinds of Controllers, the Level 1 has basic functions
while the Level 2 has advanced functions like communication
and operating status data storage.
The Level 1 Controller is standard for models FLX 1.1 and FLX
1.2. The Level 2 Controller is standard for models FLX 1.5-1, FLX
1.5, FLX 2.1, FLX 2.1-4, FLX 3.1, FLX 4.1, FLX 4.5, and FLX 5.5.
Level 1
Level 2
Figure 3.
Controller
a: DRYER ON/OFF SWITCH
b: ALARM LIGHT
c: REFRIGERANT COMPRESSOR RUNNING LIGHT
d: DRYER RUNNING LIGHT
e: ENERGY SAVING RATIO (%)
f: DEWPOINT TEMPERATURE INDICATOR
g: RUNNING TIME SELECT BUTTON
h: DRYER RUNNING / REFRIGERANT COMPRESSOR RUNNING TIME
i: ENERGY SAVING (GRAPH)
j: TIMER BUTTON (LEVEL 2 ONLY)
k: MICRO-USB CONNECTION PORT (LEVEL 2 ONLY)
Functions
1. Level 1 Controller
(i) Dryer On/Off
(ii) Display energy saving ratio (%)
(iii) Display alarm signal
(iv) Display dryer and refrigerant compressor running
time
(v) Display dew point level by indicator

4
START-UP/OPERATION
Never use the disconnect switch to shut down the dryer
for an extended period of time (except for repair). Failure
to follow these instructions may result in a non-warrant-
able compressor failure.
IMPORTANT: For models FLX 1.5 through FLX 5.5, energize
dryer for 24 hours prior to starting refrigerator compres-
sor! Failure to follow these instructions may result in a
non-warrantable compressor failure.
Follow the procedure below to start your dryer. Failure to follow
the prescribed start-up procedure will invalidate the warranty.
If problems arise during start-up, call your distributor. Before
repair, vent the internal pressure of the dryer to atmospheric
pressure.
Before starting dryer
Drain connections must be made before the dryer can be op-
erated. The dryers are fully automatic and require no auxiliary
controls.
1. Turn the dryer on/off switch to off.
2. Check that the main electrical supply voltage matches the
voltage specified on the dryer data plate.
3. Check proper connection and support of compressed air
lines to the dryer; check bypass valve system, if installed.
4. SLOWLY pressurize the dryer. The outlet valves of the dryer
should be closed to prevent flow through the dryer.
5. Turn on the main electrical power to the dryer.
6. Ensure adequate ventilation for air cooled dryers.
7. Do not operate the dryer with any dryer cabinet panel
removed.
Cooling air flow across the condenser may be reduced
if a dryer panel has been removed while the dryer
is operating, resulting in the dryer not functioning
properly and/or dryer failure. Failure to follow these
instructions may result in a non-warrantable dryer
failure.
To start dryer
IMPORTANT: For models FLX 1.5 through FLX 5.5, energize
dryer for 24 hours prior to starting refrigerator compres-
sor! Failure to follow these instructions may result in a
non-warrantable compressor failure.
1. Turn the power switch to ON. The refrigerant compressor
will turn on.
2. Allow the dryer to run 15 minutes. Confirm that the tem-
perature indicators are in the green zone.
3. SLOWLY open the dryer outlet valves permitting flow
through the dryer.
4. Confirm that condensate is discharging from the drain valve
by pressing the “Push-to Test” button.
5. Confirm that the inlet air temperature, pressure and airflow
to the dryer meet the specified requirements (see Engi-
neering Data section).
2. Level 2 Controller
(i) Save the operating data
a. Refrigerant compressor on/off status, Alarm, Dew
point level, Inlet air temperature
b. Memory chip can save maximum 30 days
c. When there is no space to save, then erase the first
one
(ii) MICRO-USB connection port
a. Automatically download operating data
b. Automatically upgrade firmware program
(iii) Communication port
a. RS485: Modbus monitoring
Operation
1. The Controller indicates the energy saving %, dryer’s oper-
ating time, refrigeration compressor’s operating time and
dew point level.
2. To start the FLX dryer, turn on the (a) dryer on/off switch.
3. When the refrigeration compressor and the condenser fan
are running, the cold refrigerant in the chiller (evaporator)
cools the liquid Phase Change Material (PCM) which gradu-
ally solidifies. During this time, the refrigeration compressor
running light (c) is illuminated on the LCD window.
4. Energy saving percent (e) is displayed on the LCD window
by calculating dryer running time and refrigeration com-
pressor operating time.
5. Pressure dew point level (f) is displayed on the LCD window.
6. Dryer running time (h) is displayed on the LCD window,
when the power on or dryer running time select button (g)
is pressed, then refrigerating compressor running time is
displayed. When the (j) button is pressed over 10 seconds,
dryer running time is erased and displayed “0 H”. (timer
reset)
7. Check the dryer operating status when the alarm light (b)
blinks according to Table 1 below.
No. Alarm display Description
1 lamp (b) blinks rapidly
and “E01” is displayed
on (h)
Ref. compressor has
no signal
2 lamp (b) blinks and
“E02” is displayed on
(h)
Temperature sensor
signal open
3 lamp (b) light is on
“E03” is displayed on
(h)
Drain valve has some
trouble
Table 1. Alarm display mode

5
6. Confirm that the condensate lines from the drain valve
discharge into a collection tank or an environmentally ap-
proved disposal system.
The FLEX dryer is designed to run and stop repeatedly. Let the
FLEX dryer operate even when the demand for compressed air
is interrupted; the FLEX dryer will not freeze up.
Shutdown
When the dryer must be shutdown for maintenance or other
reasons, use the following procedure.
1. Turn off the power switch.
2. Disconnect the main power supply.
3. Lock out and tag the power supply in accordance with OSHA
requirements.
If mechanical repairs are to be made or service is performed,
vent the internal pressure of the dryer to atmospheric pressure.
Restart the dryer according to the start-up instructions.
Disconnect power supply and depressurize dryer before
servicing. Dismantling or working on any component of
the compressed air system under pressure may cause
equipment failure and serious personal injury.

6
MAINTENANCE
The FLEX Dryer requires little maintenance for satisfactory opera-
tion. Good dryer performance can be expected if the following
routine maintenance steps are taken.
General
For continued good performance of your refrigerated dryer,
all refrigeration system maintenance should be performed by
a competent refrigeration mechanic.
NOTE: Before corrective maintenance is done during the war-
ranty period, call your local distributor and proceed according to
instructions. Refer to the warranty for limits of your coverage.
Daily Maintenance
Check the operation of the no loss drain valve at least once
daily. See the Field Service Guide for remedies to drain valve
malfunctions.
Monthly Maintenance
It is recommended to inspect the condenser coils monthly.
If necessary, remove dirt or other particles with compressed
air from an OSHA-approved air nozzle that limits its discharge
pressure to 30 psig (2.1 kgf/cm
2
).
Yearly Maintenance
It is recommended to replace the drain service unit annually.
For units purchased with mounted filtration, replace prefilter
and afterfilter elements annually.
Maintenance kits are available to facilitate annual maintenance.
Models: FLX 1.1, FLX 1.2, FLX 1.5-1, FLX 1.5, FLX 2.1, FLX 2.1-4,
FLX 3.1, FLX 4.1
Head
Bowl O-Ring
Bowl
Element
Float Drain
Drain Line
Connection
Models: FLX 4.5, FLX 5.5
Head
Element
Bowl O-Ring
Bowl
Drain Connection
Figure 4.
Mounted Filtration

7
FIELD SERVICE GUIDE
PROBLEM SYMPTOM POSSIBLE CAUSE REMEDY
Water downstream of
dryer.
No discharge from no loss drain
valves.
Drain valve failure or accumulation
of dirt in drain valve strainer.
Dismantle drain valve: clean, repair or replace.
See maintenance section.
Inlet air temperature is too high. Aftercooler malfunction. Check aftercooler discharge temperature.
Reduce temperature to 122°F (50°C) max.; reduce
airflow if temperature is above 95°F (35°C).
Liquid water entering dryer. Aftercooler drain valve malfunction. Dismantle aftercooler drain valve; clean, repair or
replace.
Excessive airflow (may also cause
high pressure drop).
Dryer improperly sized. Check airflow and dryer capacity (See Engineering
Data Tables).
Reduce airflow or resize and replace dryer.
Compressor cuts out on internal
overload.
Inadequate ventilation of refriger-
ant compressor.
Ensure adequate ventilation of the condensing unit
(see Clearance).
Motor will restart automatically when compressor
is cool.
Leak in refrigeration system. Locate leak, repair and recharge. Motor will restart
automatically when compressor is cool.
Compressor windings read open or
shorted.
Compressor burned out. Have a refrigeration mechanic check and replace.
The dew point level is red on LCD
window.
Inlet air temperature too high. Reduce aftercooler discharge temperature to design
conditions (See Engineering Data Tables).
Excessive airflow. Check airflow and system capacity. Reduce airflow or
resize and replace system.
Condenser fouled or clogged. Clean or replace condenser.
Fan motor inoperative. Replace fan motor.
High ambient temperature. Ventilate area.
See Engineering Data Tables.
High pressure drop
across dryer.
Inlet air temperature is too low. Low ambient temperature. Consult your local distributor.
Excessive airflow (may also cause
water downstream of dryer).
Dryer improperly sized. Check airflow and dryer capacity. Reduce airflow or
resize and replace dryer.
Dryer icing up. Adjust operating conditions to meet sizing condi-
tions.
No condensate from
no loss drain valve.
Valve venting. But no condensate
from valve.
Accumulation of dirt in valve
strainer.
Dismantle valve strainer.
Strainer clean or replace.
Valve continuously venting. Clogged valve orifice. Replace valve.
Short in electrical component. Check and replace connector or controller assembly.
Valve not cycling. No electrical power. Check and correct power supply and connections.
Drain valve malfunction. Replace drain valve.
No response when test button is
pushed.
No electrical power. Check and correct power supply and connections.
Burn out fuse. Check solenoid coil and wiring cable and replace
fuse.

8
ENGINEERING DATA
SPECIFICATIONS
MODEL Rated Capacity1
(scfm)
Inlet /Outlet
Connections
Dimensions - inches (mm) Net Weight
lbs (kg)
Height Width Length
FLX 1.1 75 NPT 1” 29.6
(751)
14.3
(363)
23.7
(603)
120
(54.5)
FLX 1.2 100 NPT 1” 28.0
(711)
14.3
(363)
30.7
(781)
147
(66.5)
FLX 1.5-1 150 NPT 2” 30.0
(761)
17.4
(443)
35.5
(901)
203
(92)
FLX 1.5 150 NPT 2” 30.0
(761)
17.4
(443)
35.5
(901)
189
(85.5)
FLX 2.1 200 NPT 2” 30.0
(761)
17.4
(443)
37.8
(961)
217
(98.5)
FLX 2.1-4 200 NPT 2” 30.0
(761)
17.4
(443)
37.8
(961)
244
(110.5)
FLX 3.1 300 NPT 2” 35.9
(911)
19.4
(493)
43.7
(1,111)
324
(147)
FLX 4.1 400 NPT 2” 35.9
(911)
19.4
(493)
43.7
(1,111)
335
(152)
FLX 4.5 450 NPT 2” 40.6
(1,032)
19.5
(494)
49.3
(1,253)
366
(166)
FLX 5.5 550 NPT 2” 40.6
(1,032)
19.5
(494)
49.3
(1,253)
396
(180)
1Rated Flow Capacity - Conditions for rating dryers are in accordance with ISO 7183 (Option A2).
Compressed air at dryer inlet: 100 psig (6.9 barg) and 100°F (38°C); ambient air temperature: 100°F (38°C), operating on 60 Hz power
supply.
2Refer to dryer data plate for refrigerant charge.
ELECTRICAL DATA
MODEL
Power Supply Power
Consumption
(kW)
Refrigerant
Voltage Phase Hz
FLX 1.1 115 1 60 0.54
R-134a
FLX 1.2 115 1 60 0.62
FLX 1.5-1 115 1 60 1.04
R-407c
FLX 1.5 230 1 60 0.85
FLX 2.1 230 1 60 1.32
FLX 2.1-4 460 3 60 1.26 R-134a
FLX 3.1 460 3 60 1.99
R-407c
FLX 4.1 230 1 60 2.54
FLX 4.5 460 3 60 3.23
FLX 5.5 460 3 60 3.42

9
ENGINEERING DATA
MINIMUM - MAXIMUM OPERATING CONDITIONS ALL MODELS
Min.-Max. Inlet Air Pressure (compressed air at inlet to dryer) 43.5 - 232 psig (3 - 16 barg)
Min.-Max. Inlet Air Temperature (compressed air at inlet to dryer) 39°F - 122°F (4°C - 50°C)
Min.-Max. Ambient Temperature 36°F - 113°F (2°C - 45°C)
REFRIGERANT PRESSURE SWITCH SETTINGS
Refrigerant Compressor Control
High Pressure Switch Setting
Model Refrigerant Cut-Out
psig (barg)
Cut-In
(psig)
FLX 1.1
FLX 1.2
FLX2.1-4
R-134a 304 psig
(21 barg)
Manual
Reset
FLX 1.5-1
FLX 1.5
FLX 2.1
FLX 3.1
FLX 4.1
FLX 4.5
FLX 5.5
R-407c 406 psig
(28 barg)
Manual
Reset
CORRECTION FACTORS (MULTIPLIERS)
Air Inlet Temperature
°F (°C) Multiplier Air Inlet Pressure
psig (barg) Multiplier Ambient Air Temperature
°F (°C) Multiplier
80°F (27°C)
90°F (32°C)
100°F (38°C)
110°F (43°C)
120°F (49°C)
1.46
1.23
1.00
0.82
0.68
75 psig (5.2 bar)
100 psig (6.9 bar)
120 psig (8.3 bar)
150 psig (10.3 bar)
225 psig (15.5 bar)
0.86
1.00
1.04
1.09
1.15
80°F (27°C)
90°F (32°C)
100°F (38°C)
110°F (43°C)
120°F (49°C)
1.12
1.06
1.00
0.83
0.68

10
DRAWINGS: GENERAL ARRANGEMENT
Figure 5A
Model: FLX 1.1
MODEL
DIMENSIONS, INCHES (MM) INLET/OUTLET
CONNECTIONS
WEIGHT
Lb. (kg)
A B C D E F G H I J K
FLX 1.1 4.69
(119)
4.97
(126.2)
8.41
(213.5)
19.20
(487.7)
14.27
(362.4)
29.58
(751.2)
12.75
(324)
23.72
(602.5)
3.39
(86.2)
15.40
(391.2)
22.14
(562.4) 1" NPT 120
(54.5)
DRIED AIR OUTLET
WETTED AIR INLET
AIR FLOW
COOLING
C
D
E
F
GMAIN POWER CABLE
A B
4-Ø10 MOUNTING HOLES
DRAIN OUTLET
FOOT PRINT
FRONT VIEW REAR VIEWRIGHT SIDE VIEW
TOP VIEW
H
J
K
I

11
DRAWINGS: GENERAL ARRANGEMENT
Figure 5B
Model: FLX 1.2
MODEL
DIMENSIONS, INCHES (MM) INLET/OUTLET
CONNECTIONS
WEIGHT
Lb. (kg)
A B C D E F G H I J K
FLX 1.2 3.41
(86.5)
4.97
(126.2)
6.77
(172)
19.25
(489.2)
14.29
(363)
28
(711.2)
12.76
(324)
30.76
(781.3)
5.56
(141.2)
19.29
(490)
29.18
(741.2) 1" NPT 147
(66.5)
AIR FLOW
COOLING
DRIED AIR OUTLET
WETTED AIR INLET
F
E
C
D
A B
5-Ø10 MOUNTING HOLES
G
DRAIN OUTLET
POWER CORD
FOOT PRINT
FRONT VIEW REAR VIEWRIGHT SIDE VIEW
TOP VIEW
J
K
I
H

12
DRAWINGS: GENERAL ARRANGEMENT
Figure 5C
Models: FLX 1.5-1, FLX 1.5, FLX 2.1, FLX 2.1-4
MODEL
DIMENSIONS, INCHES (MM) INLET/OUTLET
CONNECTIONS
WEIGHT
Lb. (kg)
A B C D E F G H I J K
FLX 1.5-1 4.86
(123.5)
7.86
(199.6)
3.63
(92)
24.38
(619.2)
17.44
(443)
29.97
(761.2)
15.91
(404)
35.50
(901.3)
3.39
(86.2)
27.16
(690)
33.91
(861.2) 2" NPT 203
(92)
FLX 1.5 4.86
(123.5)
7.86
(199.6)
3.63
(92)
24.38
(619.2)
17.44
(443)
29.97
(761.2)
15.91
(404)
35.50
(901.3)
3.39
(86.2)
27.16
(690)
33.91
(861.2) 2" NPT 188.5
(85.5)
FLX 2.1 4.86
(123.5)
7.86
(199.6)
3.63
(92)
24.38
(619.2)
17.44
(443)
29.97
(761.2)
15.91
(404)
37.85
(961.3)
3.39
(86.2)
29.53
(750)
36.27
(921.2) 2" NPT 217
(98.5)
FLX 2.1-4 4.86
(123.5)
7.86
(199.6)
3.63
(92)
24.38
(619.2)
17.44
(443)
29.97
(761.2)
15.91
(404)
37.85
(961.3)
3.39
(86.2)
29.53
(750)
36.27
(921.2) 2" NPT 244
(110.5)
DRIED AIR OUTLET
WETTED AIR INLET
AIR FLOW
COOLING
C
D
E
F
G
MAIN POWER CABLE
A B
5-Ø10 MOUNTING HOLES
DRAIN OUTLET
FOOT PRINT
FRONT VIEW REAR VIEW
RIGHT SIDE VIEW
TOP VIEW
J
K
I
H

13
DRAWINGS: GENERAL ARRANGEMENT
Figure 5D
Models: FLX 3.1, FLX 4.1
DRIED AIR OUTLET
WETTED AIR INLET
AIR FLOW
COOLING
MAIN POWER CABLE
DRAIN OUTLET
5-Ø10 MOUNTING HOLES
E
F
G
C
D
A B
FOOT PRINT
FRONT VIEW REAR VIEWRIGHT SIDE VIEW
TOP VIEW
H
I
J
K
MODEL
DIMENSIONS, INCHES (MM) INLET/OUTLET
CONNECTIONS
WEIGHT
Lb. (kg)
A B C D E F G H I J K
FLX 3.1 4.86
(123.5)
7.86
(199.6)
8.31
(211.2)
25.59
(650)
19.41
(493)
35.88
(911.2)
17.88
(454)
43.75
(1111.3)
3.39
(86.2)
35.43
(900)
42.17
(1071.2) 2" NPT 324
(147)
FLX 4.1 4.86
(123.5)
8.58
(218)
8.35
(212)
25.56
(649.2)
19.41
(493)
35.88
(911.2)
17.88
(454)
43.75
(1111.3)
3.39
(86.2)
35.43
(900)
42.17
(1071.2) 2" NPT 335
(152)

14
DRAWINGS: GENERAL ARRANGEMENT
Figure 5E
Models: FLX 4.5, FLX 5.5
DRIED AIR OUTLET
WETTED AIR INLET
AIR FLOW
COOLING
4-Ø10 MOUNTING HOLES
E
F
C
D
A B
G
H
MAIN POWER CABLE
DRAIN OUTLET
FOOT PRINT
FRONT VIEW REAR VIEW
RIGHT SIDE VIEW
TOP VIEW
I
J
K
L
MODEL
DIMENSIONS, INCHES (MM) INLET/OUTLET
CONNECTIONS
WEIGHT
Lb. (kg)
A B C D E F G H I J K L
FLX 4.5 4.87
(123.8)
8.58
(218)
9.79
(248.6)
30.83
(783)
19.43
(493.5)
40.61
(1031.6)
17.72
(450)
19.30
(490)
1.97
(50)
43.70
(1110)
47.64
(1210)
49.32
(1252.8) 2" NPT 366
(166)
FLX 5.5 4.87
(123.8)
8.58
(218)
9.78
(248.6)
30.83
(783)
19.43
(493.5)
40.61
(1031.6)
17.72
(450)
19.30
(490)
1.97
(50)
43.70
(1110)
47.64
(1210)
49.32
(1252.8) 2" NPT 396
(180)

15
DRAWINGS: ELECTRICAL SCHEMATIC
Figure 6A
Models: FLX 1.1, FLX 1.2 (115V/1PH/60Hz)
NL E
Customer's installation
115V/1PH/60Hz
MC1
S1
M2
L1
N1
S0
F0
(16A)
M1
CS
C
SM
35
R
S2
CR 4
SOL.
S3
1
DIP SW
2 3 4
AC IN1 COMP1 ALARM1 DRAIN
COM.
N.O.
N.C.
COM
ON
R1 S1
FG S2 R2 COM ON COM RBRA
TS1 TS2
DRAIN
TRAP1
MC1
8 9 10 8
N1 L1
PCB
LEGEND
M1: Refrigerant Compressor
M2: Fan Motor
MC1: Magnetic Contactor
CR: Running Capacitor
CS: Starting Capacitor
R: PTC Relay
S1: Switch “On-Off”
S2: Overload Protector
S3: High Pressure Switch
TS1: Temperature Sensor 1
TS2: Temperature Sensor 2
SOL: No Loss Drain Valve
PCB: Control Board
S0: Main Switch (Customer’s installation)
F0: Main Fuse (Customer’s installation)

16
DRAWINGS: ELECTRICAL SCHEMATIC
Figure 6B
Models: FLX 1.5-1 (115V/1Ph/60Hz)
LEGEND
M1: Refrigerant Compressor
M2: Fan Motor
MC1: Magnetic Contactor
CR: Running Capacitor
CH: Crankcase Heater
S1: Switch “On-Off”
S2: Overload Protector
S3: High Pressure Switch
TS1: Separator Inlet Temp. Sensor
TS2: Heat Exchanger Inlet Temp. Sensor
TS3: Air Inlet Temp. Sensor
SOL: No Loss Drain Valve
PCB: Control Board
S0: Main Switch (Customer’s installation)
F0: Main Fuse (Customer’s installation)
NL E
Customer's installation
CH
115V/1PH/60Hz
MC1
S1
S
R
CR
M1
C
S2
L1
N1
S0
F0
(16A)
M2
SOL.
S3
1
DIP SW
2 3 4
AC IN1 COMP1 ALARM1 DRAIN
COM.
N.O.
N.C.
COM
ON
R1 S1
FG S2 R2 COM ON COM RBRA
TS1 TS2
DRAIN
TRAP1
MC1
8 9 10 8
N1 L1
PCB
TS3 RS232 RS485
RS232 RX
GND
RS232 TX
RS485 +
GND
RS485 -

17
DRAWINGS: ELECTRICAL SCHEMATIC
Figure 6C
Models: FLX 1.5, FLX 2.1, FLX 4.1 (230V/1Ph/60Hz)
NL E
Customer's installation
CH
230V/1PH/60Hz
MC1
S1
S
R
CR
M1
C
S2
L1
N1
S0
F0
(16A)
M2
SOL.
S3
1
DIP SW
2 3 4
AC IN1 COMP1 ALARM1 DRAIN
COM.
N.O.
N.C.
COMONR1 S1FG S2 R2 COM ON COM RBRA
TS1 TS2
DRAIN
TRAP1
MC1
8 9 10 8
N1 L1
PCB
TS3 RS232 RS485
RS232 RX
GND
RS232 TX
RS485 +
GND
RS485 -
LEGEND
M1: Refrigerant Compressor
M2: Fan Motor
MC1: Magnetic Contactor
CR: Running Capacitor
CH: Crankcase Heater
S1: Switch “On-Off”
S2: Overload Protector
S3: High Pressure Switch
TS1: Separator Inlet Temp. Sensor
TS2: Heat Exchanger Inlet Temp. Sensor
TS3: Air Inlet Temp. Sensor
SOL: No Loss Drain Valve
PCB: Control Board
S0: Main Switch (Customer’s installation)
F0: Main Fuse (Customer’s installation)

18
DRAWINGS: ELECTRICAL SCHEMATIC
Figure 6D
Models: FLX 2.1-4, FLX 3.1, FLX 4.5, FLX 5.5 (460V/3Ph/60Hz)
LEGEND
MC1: Magnetic Contactor
MC2: Magnetic Contactor
TH: Thermal Overload
F1: Fuse
S1: Switch “On-Off”
H.P.S.: High Pressure Switch
TS1: Separator Inlet Temp. Sensor
TS2: Heat Exchanger Inlet Temp. Sensor
TS3: Air Inlet Temp. Sensor
DRAIN TRAP: No Loss Drain Valve
PCB: Control Board
L3L1 L2
0V
480V
0V
120V
460V/3PH/60HZ
W1U1 V1 W2U2 V2
MAIN POWER
TB1 L3L1 EL2
F1(2A)
MOTOR
FAN
MC2
MC1
COMP.
TRANSFORMER
50VA
60Hz
S1
CRANK CASE HEATER
R1
T1
MC1
4
5
L1
L3
R2
T2
1
DIP SW
2 3 4
AC IN1 COMP1 ALARM1 DRAIN
COM.
N.O.
N.C.
COMONR1 S1FG S2 R2 COM ON COM RBRA
TS1 TS2
DRAIN
TRAP1
11 10 9 8
R2 T2
PCB
TS3 RS232 RS485
RS232 RX
GND
RS232 TX
RS485 +
GND
RS485 -
DRAIN
TRAP
H.P.S
TH
MC1
MC2
7
89
89
32 31
TH
This manual suits for next models
10
Table of contents
Other HANKISON Dehumidifier manuals

HANKISON
HANKISON HBP Series User manual
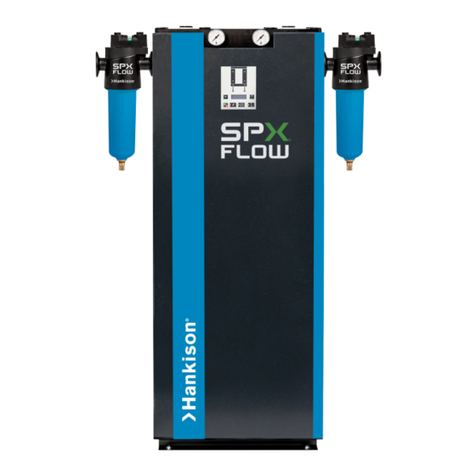
HANKISON
HANKISON SPXFLOW HSHD Series User manual
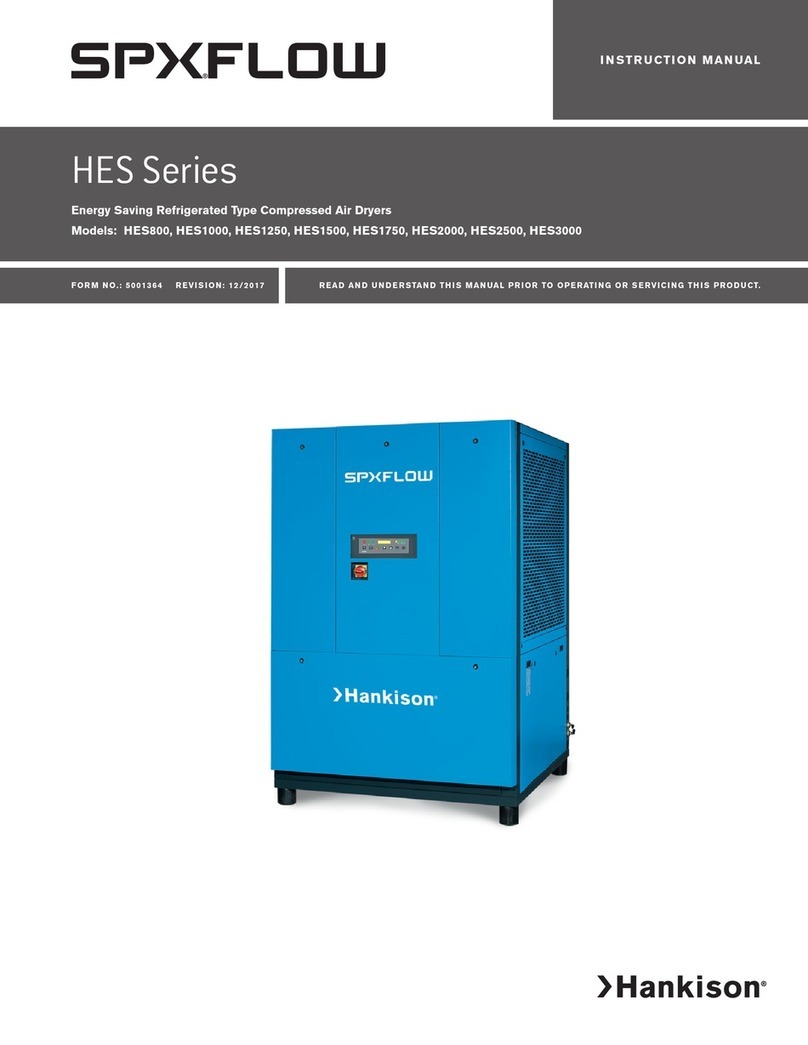
HANKISON
HANKISON SPX FLOW HES Series User manual
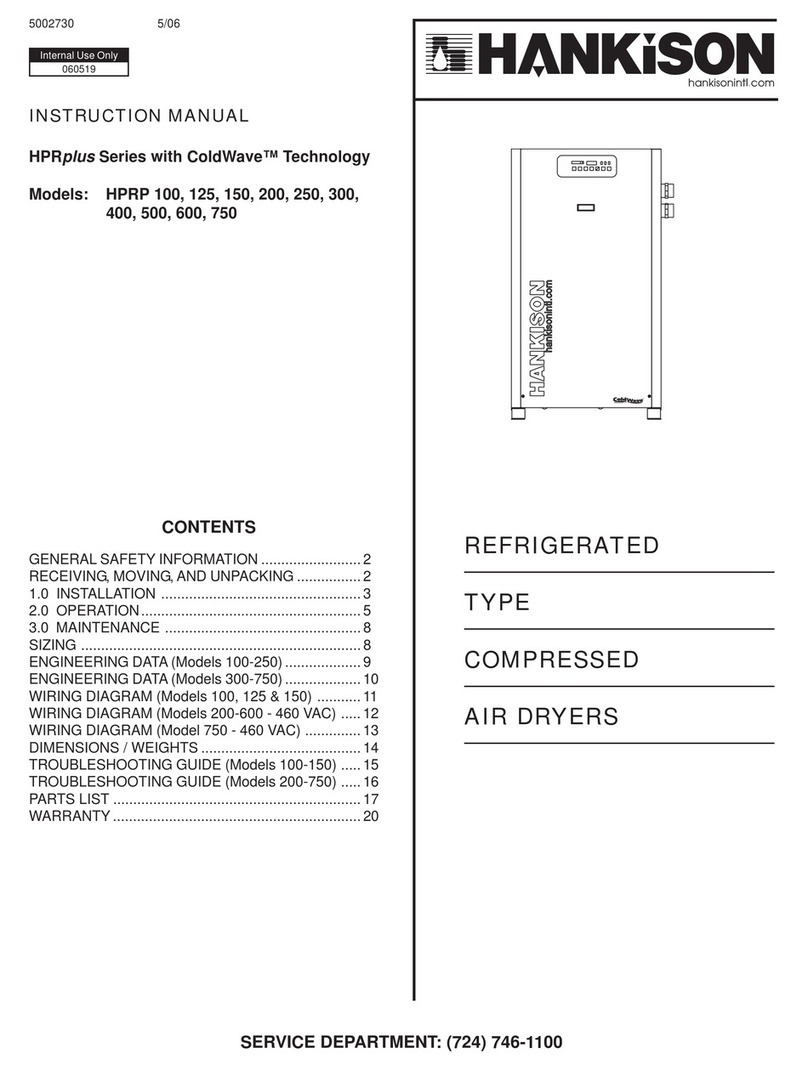
HANKISON
HANKISON HPRplus Series User manual

HANKISON
HANKISON HPET Series User manual

HANKISON
HANKISON SPX HES Series User manual

HANKISON
HANKISON HPRP 25 User manual
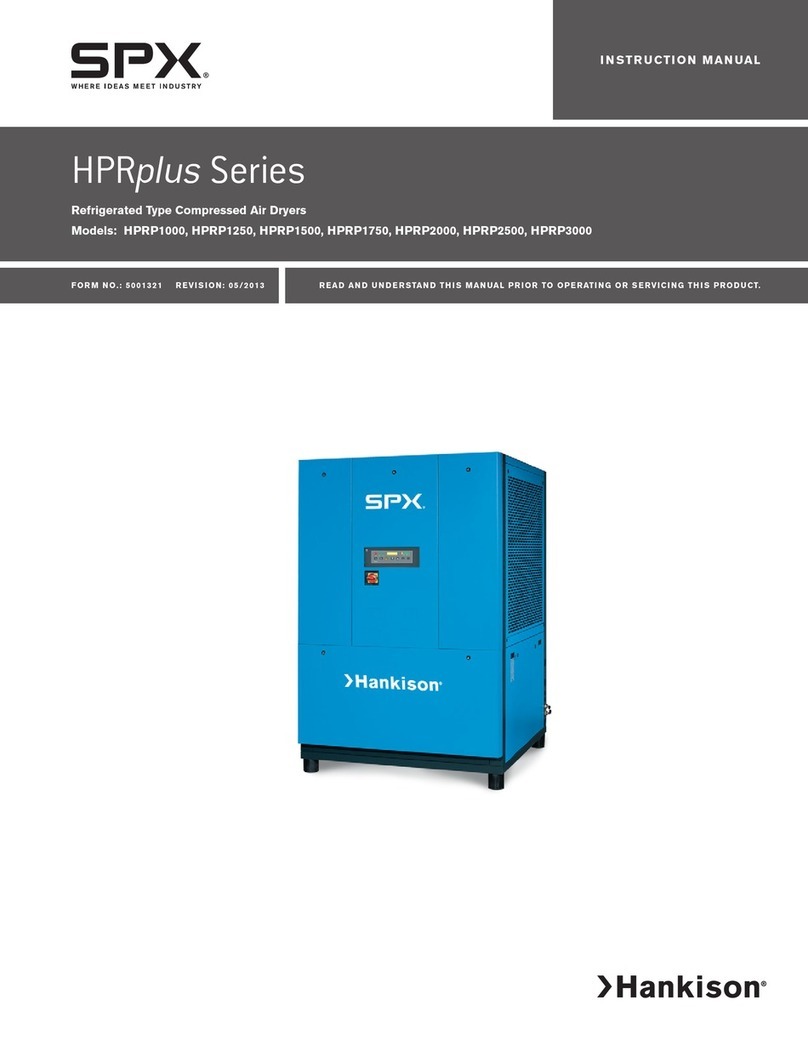
HANKISON
HANKISON HPRplus HPRP1000 User manual
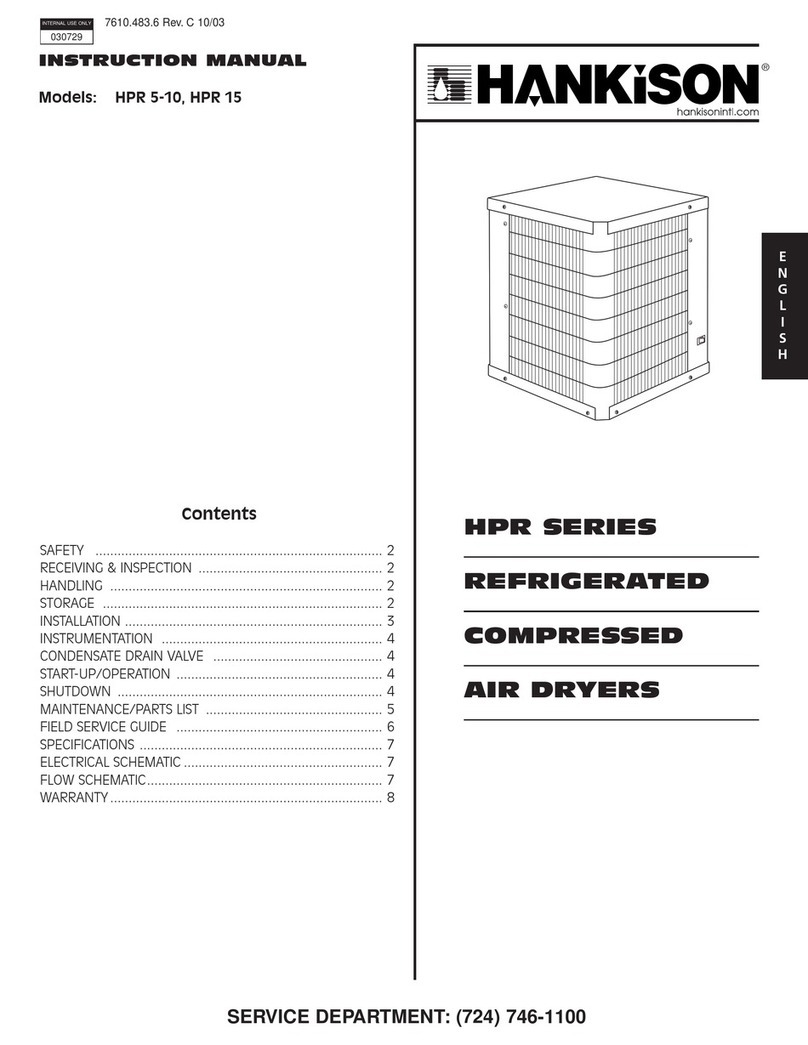
HANKISON
HANKISON HPR Series User manual
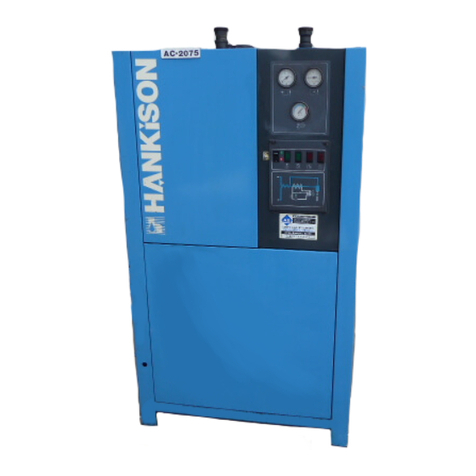
HANKISON
HANKISON PR500 User manual