HANKISON SPXFLOW HSHD Series User manual

HSHD Series
Desiccant Compressed Air Dryer
Models: HSHD-7, HSHD-13, HSHD-18, HSHD-21, HSHD-27, HSHD-40
FORM NO.: 7443487 REVISION: 10/2020 READ AND UNDERSTAND THIS MANUAL PRIOR TO OPERATING OR SERVICING THIS PRODUCT.
INSTRUCTION MANUAL

Contents
1.0 General Safety Information .............................................................................................................. 1
2.0 Receiving, Storing, and Moving ....................................................................................................... 1
2.1 Receiving and Inspection .............................................................................................................................................. 1
2.2 Storing ........................................................................................................................................................................... 1
2.3 Handling......................................................................................................................................................................... 1
3.0 Description ........................................................................................................................................... 2
3.1 Function......................................................................................................................................................................... 2
3.2 Operation ....................................................................................................................................................................... 2
4.0 Installation and Mounting................................................................................................................. 3
4.1 Location of Installation .................................................................................................................................................. 3
4.2 Service Clearance........................................................................................................................................................... 3
4.3 Mounting ....................................................................................................................................................................... 3
4.4 Connection to the Compressed Air System................................................................................................................. 3
4.5 Connection to the Dryer ............................................................................................................................................... 3
4.6 Pre- and After- Filter ..................................................................................................................................................... 3
4.7 Piping ............................................................................................................................................................................. 3
4.8 Electrical Connection..................................................................................................................................................... 3
4.8.1 Potential Free Contacts................................................................................................................................................. 3
4.8.2 Network Connection ..................................................................................................................................................... 4
4.9 Ambient Conditions ...................................................................................................................................................... 4
5.0 Initial Start-Up (Start up after prolonged inoperative periods) ................................................ 5
5.1 Preconditions ................................................................................................................................................................ 5
5.2 Switching ON the Dryer................................................................................................................................................. 5
5.3 Operation ....................................................................................................................................................................... 5
5.4 Switching OFF the Dryer ............................................................................................................................................... 5
6.0 Operation (Switching on, Switching off, Controls) ...................................................................... 5
6.1 Preconditions for Operation ......................................................................................................................................... 5
6.2 Switching ON the Dryer................................................................................................................................................. 5
6.3 Operation ....................................................................................................................................................................... 5
6.4 Switching OFF the Dryer ............................................................................................................................................... 5
6.5 Controls (Panel) ............................................................................................................................................................. 6
6.5.1 Start Screen ................................................................................................................................................................... 7
6.5.2 Message History............................................................................................................................................................. 7
6.5.3 Remote On/Off Settings................................................................................................................................................ 8
6.5.4 Setting Menu ................................................................................................................................................................. 8
6.6 Purge Air Consumption ................................................................................................................................................ 10
6.6.1 Maximum Purge Flow ................................................................................................................................................... 10
6.6.2 Average Purge Flow ...................................................................................................................................................... 10
6.6.3 Minimum Outlet Flow.................................................................................................................................................... 10
6.6.4 Timer Board Settings & Remote Control ...................................................................................................................... 10
7.0 Servicing and Maintenance............................................................................................................... 11
7.1 Nameplate ..................................................................................................................................................................... 11
7.2 Ordering Consumable Parts and Operating Materials.................................................................................................. 11
7.3 Weekly Maintenance...................................................................................................................................................... 11
7.4 Annual Maintenance...................................................................................................................................................... 11
7.5 Depressurize the Desiccant Dryer................................................................................................................................. 11
7.6 Replacement of Desiccant ............................................................................................................................................ 11
7.6.1 Replacement of Purge Solenoid Valves........................................................................................................................ 11
7.7 Prefilter/Afterfilter Maintenance .................................................................................................................................. 12
8.0 Troubleshooting Guide.................................................................................................................... 13
9.0 Technical Data................................................................................................................................... 15
9.1 Maximum Purge Flow................................................................................................................................................ 15
9.2 Ambient Temperature ............................................................................................................................................... 15
9.3 Electrical Data............................................................................................................................................................. 15
9.4 Desiccant.................................................................................................................................................................... 16
9.5 Condensate................................................................................................................................................................ 16
9.6 Measurements, Weights............................................................................................................................................ 16
9.7 Nominal Air Flow........................................................................................................................................................ 16
9.8 Correction Factors..................................................................................................................................................... 16
10.0 Replacement Parts & Maintenance Kits....................................................................................... 17
10.1 Replacement Parts
10.2 Maintenance Kits
11.0 Drawings ............................................................................................................................................ 18
11.1 General Arrangement: HSHD-7.................................................................................................................................. 18
11.2 General Arrangement: HSHD-13................................................................................................................................ 19
11.3 General Arrangement: HSHD-18................................................................................................................................ 20
11.4 General Arrangement: HSHD-21................................................................................................................................ 21
11.5 General Arrangement: HSHD-27................................................................................................................................ 22
11.6 General Arrangement: HSHD-40................................................................................................................................ 23
11.7 P&I Diagram ............................................................................................................................................................... 24
11.8 Electrical Schematic ................................................................................................................................................... 26
11.9 Electrical Schematic With Electronic Drain Option ................................................................................................... 27
Warranty ........................................................................................................................................................ 29

1
1.0 General Safety Information
This equipment is designed and built with safety as a prime
consideration; industry-accepted safety factors have been
used in the design. Each dryer is checked at the factory for
safety and operation. All pressure vessels which fall under
the scope of ASME Section VIII, are hydrostatically tested in
accordance with the latest addenda.
WARNING – The following safety rules must be observed
to ensure safe dryer operation. Failure to follow these
rules may void the warranty or result in dryer damage
or personal injury.
1. Never install or try to repair any dryer that has been
damaged in shipment. See the Receiving and Inspection
instructions in this manual for appropriate action.
2. This equipment is a pressure-containing device. Never
operate the dryer at pressures or temperatures above
the maximum conditions shown on the data plate.
Never dismantle or work on any component of the dryer
or compressed air system under pressure. Vent internal
air pressure to the atmosphere before servicing.
3. This equipment requires electricity to operate. Install
equipment in compliance with national and local electrical
codes. Standard equipment is not intended for installation
in hazardous environments.
Never perform electrical service on the dryer unless the
main power supply has been disconnected. Parts of the
control circuit may remain energized when the power
switch is turned off.
4. Air treated by this equipment may not be suitable for
breathing without further purification. Refer to OSHA
standard 1910.134 for the requirements for breathing
quality air.
5. Use only genuine replacement parts from the manufac-
turer. The manufacturer bears no responsibility for hazards
caused by the use of unauthorized parts.
Safety instructions in this manual are boldfaced for emphasis.
The signal words DANGER, WARNING and CAUTION are used
to indicate hazard seriousness levels as follows:
DANGER – Immediate hazard which will result in severe injury
or death.
WARNING – Hazard or unsafe practice which could result in
severe injury or death.
CAUTION – Hazard or unsafe practice which could result in
minor injury or in product or property damage.
The dryer data plate contains critical safety and identification
information. If the data plate is missing or defaced, immedi-
ately contact your local distributor for a replacement.
2.0 Receiving, Storing, and Moving
2.1 Receiving and Inspection
This shipment has been thoroughly checked, packed and
inspected before leaving our plant. It was received in good
condition by the carrier and was so acknowledged.
Immediately upon receipt, thoroughly inspect for visible loss or
damage that may have occurred during shipping. If this ship-
ment shows evidence of loss or damage at time of delivery to
you, insist that a notation of this loss or damage be made on
the delivery receipt by the carrier’s agent. Otherwise no claim
can be enforced against the carrier.
Also check for concealed loss or damage. When a shipment has
been delivered to you in apparent good order, but concealed
damage is found upon unpacking, notify the carrier imme-
diately and insist on his agent inspecting the shipment. The
carrier will not consider any claim for loss or damage unless an
inspection has been made. If you give the carrier a clear receipt
for goods that have been damaged or lost in transit, you do
so at your own risk and expense. Concealed damage claims
are not our responsibility as our terms are F.O.B. point of ship-
ment. Shipping damage is not covered by the dryer warranty.
2.2 Storing
Store the dryer indoors to prevent damage to any electrical
or mechanical components. All packaging material should be
left in place until the dryer is in position.
The storage temperature should be between 32°F (0°C) and
131°F (55°C). Frost or higher temperature can cause damage.
Contact the manufacturer for long term storage/commission-
ing periods greater than 6 months.
2.3 Handling
CAUTION – Never lift the dryer by attaching hooks or
slings to the compressed air inlet or air outlet connec-
tions. Severe structural damage could occur.
IMPORTANT: Allow handling only by personnel trained in the
safe movement of loads.

2
3.0 Description
3.1 Function
Dual tower regenerative desiccant dryers are utilized to dry
compressed air to dew points below the freezing point of
water or reduce the moisture content to low levels for use in
critical process applications.
Air is dried by using two identical towers, each containing a
desiccant bed. While one tower is on-stream drying the com-
pressed air, the other tower is off-stream being regenerated
(reactivated, i.e., dried out).
Desiccant dryers lower the dew point by adsorbing most of
the water vapor present onto the surface of the desiccant.
Adsorption occurs until an equilibrium is reached between
the partial pressure of the water vapor in the air and that on
the surface of the desiccant.
Desiccant can then be regenerated by desorbing the water
collected on its surface. Regeneration occurs by expanding a
portion of the dried air to atmospheric pressure. This very dry
air (called purge air) causes the moisture to desorb from the
desiccant and then carries the desorbed water out of the dryer.
3.2 Operation
The Drying Circuit: Up-Flow Drying
A. The incoming compressed air travels through the oil removal
pre-filter (1) and enters the top manifold assembly (2).
B. A shuttle valve and flow distributor direct the airflow down-
ward through a transfer tube (3) to the bottom manifold
assembly (4).
C. The dried compressed air moves through a flow distributor
to the dryer outlet (6).
D. The air travels through particle removal after-filter (7). The
clean, dry air is now ready use.
1) In the Class 2 fixed mode (-40°F pdp), the on-line car-
tridge dries the air for a period of 4 minutes.
2) In the Class 1 pdp mode (-94°F pdp), the on-line cartridge
dries the air for a period of 2 minutes.
1
2
3
6
7
5
4
Inlet Air
Outlet Air
Example above: Letower drying / Right tower regenerang
Up-Flow Drying
The Regeneration Circuit: Down-Flow Regeneration
A. A portion of the ultra-dry air is throttled to near atmo-
spheric pressure through a purge orifice (1) directing the air
through the right desiccant cartridge (2). The water vapor
is effectively desorbed from the desiccant.
B. The purge air then passes through flow distributor (3),
upward through purge valve (4) and purge air muffler (5),
then exhausted to atmosphere.
1) In the Class 2 (-40°F pdp) fixed dew point mode, the
dryer regenerates for 3 minutes and 20 seconds. The
purge valve then closes, slowing repressuring in the
right cartridge for 40 seconds to line pressure. With the
right cartridge fully regenerated, it is now prepared to
go online & dry the air.
C. After 40 seconds of repressurization, the left purge valve
opens (6) & depressurizes. The offline tower is now ready
to go back on-line.
D. This moves the inlet shuttle valve moves into position. The
incoming air now passes through the shuttle valve (via the
flow distributor) to the right desiccant cartridge, where it
is dried to the desired dew point.
1) In the Class 2 fixed mode, the full cycle time is 8 minutes
– 4 minutes drying & 4 minutes regenerating.
2) In the Class 1 fixed mode, the full cycle time is 4 minutes
– 2 minutes drying & 2 minutes regenerating.
5
3
1
4
Inlet Air
Outlet Air
Example above: tower drying / Right tower
2
6
Down-Flow Regeneration

3
4.0 Installation and Mounting
4.1 Location of Installation
The desiccant compressed air dryer should be installed in a
dry room indoors. Ample free space should be allowed for
the maintenance of the device.
The dryer is furnished in a cabinet for floor mounting.
The dryer is suitable for floor or wall mounting with a bracket
(see chapter "General Arrangement drawing“) (OPTION).
If supplied, install pre-filter and after-filter, which are packed
separately, in the pipe system. Please use the connector
adapters.
4.2 Service Clearance
>16in.
>12in.
>12in.
>12in.
4.3 Mounting
WARNING – When a valve is installed after the dryer an
appropriate safety relief valve should be installed to
prevent over pressurization of the dryer due to external
causes (fire).
CAUTION – When installing the dryer ensure all connec-
tions are even and no pressure is placed on inlet and
outlet connections.
CAUTION – Check all compressed-air connections to en-
sure that they are firm and free of leaks.
4.4 Connection to the Compressed Air System
The compressed air inlet and outlet line should be equipped
with shut off valves and a bypass system.
When installing a bypass, its function and influence on the
compressed air quality, must be known when used.
4.5 Connection to the Dryer
The dryer is shipped complete with desiccant and ready to
operate after filtration, compressed air piping, condensate
piping and electrical connections are made.
4.6 Pre- and After- Filter
IMPORTANT: In order to ensure correct functioning of the
desiccant dryer, an oil removal filter with a max. residual oil of
0.01 ppm must be installed. To protect the down-line system
from desiccant dust, a dust filter must be installed.
4.7 Piping
The piping between the preliminary filter and the dryer must
be short and corrosion-resistant.
4.8 Electrical Connection
The dryer is equipped with a plug.
Check to see that power supply to dryer is the same as the
power requirements indicated on the identification label. Install
plug into receptacle of proper voltage or hardwire to pigtails
and ground screw inside cabinet according to electrical draw-
ings in the back of this manual. Be sure to follow all applicable
electrical codes.
4.8.1 Potential Free Contacts
All externally connected cables (pot. free wiring) should be
fixed by means of cable ties as shown in the picture.

4
4.8.2 Network Connection
The network cable should be provided with a loop, be fixed
under the control using cable ties (see picture).
When opening the controller, the network cable must be pushed
carefully to avoid mechanical stress on the network socket.
4.9 Ambient Conditions
Locate the dryer under cover in an area where the ambient air
temperature will remain between 35°F (2°C) and 120°F (49°C).
NOTE: If dryer is installed in ambients below 35°F (2°C), low
ambient protection requiring heat tracing and insulation of the
prefilter bowls, and auto drains and/or sumps is necessary to
prevent condensate from freezing. If installing heat tracing,
observe electrical class code requirements for type of duty
specified. Purge mufflers and their relief mechanisms must
be kept clear from snow and ice buildup that could prevent
proper discharge of compressed air.

5
5.0 Initial Start-up
(Start up after prolonged inoperative periods)
5.1 Preconditions
The desiccant compressed air-dryer is ready for operation when:
• The device has been installed in accordance with section
4. "installation“.
• All inlet and outlet lines have been correctly connected.
• The required forms of energy (electricity, compressed air)
are available.
• A stable power supply must be available.
• The shut-off devices (e.g. butterfly valve, ball valve) in the
compressed-air inlet line are opened and in the outlet line
are closed (if installed).
• The compressed-air bypass is open (if installed).
• The appropriate operating voltage is supplied to the dryer.
• Filters are mounted.
• Condensate piping mounted.
IMPORTANT: The dryer is preset at the factory, see chapter 6.6.4.
5.2 Switching ON the Dryer
The device is to be switched on only when all the condi-
tions specified in section 5.1 have been fulfilled.
A. Dryer is under operating pressure.
B. Press the "I / 0“ button.
C. The dryer must regenerated for approx. 6 hours without
compressed-air being supplied to the network.
D. Open the shut-off device in the compressed-air outlet line
(if installed).
E. Close the compressed-air bypass (if installed).
5.3 Operation
IMPORTANT: Please note the information provided in Chapter 7.
"Servicing and Maintenance“.
5.4 Switching OFF the Dryer
A. Press the "I / 0“ button.
• Dryer is switched off.
CAUTION – The dryer is still pressurized!
To depressurize see Chapter 7. "Servicing and Mainte-
nance“.
6.0 Operation
(Switching on, Switching off, Controls)
6.1 Preconditions for Operation
The dryer is ready for operation when the following conditions
have been fulfilled:
• The installation of the dryer in accordance with section 4.
"Installation“.
• Dryer has been commissioned in accordance with section 5.
"Initial Start-Up“.
• All inlet and outlet lines have been correctly connected.
• The required forms of energy (electricity, compressed air)
are available.
• The compressed-air inlet and outlet line are pressurized.
• Shut-off devices (butterfly valve, ball valve) in the com-
pressed-air inlet and outlet lines are open.
• Bypass (if installed) in the compressed-air line up-line of
the desiccant compressed-air dryer is closed.
• The appropriate operating voltage is supplied to the dryer.
• Slowly pressurize the system up to working pressure.
6.2 Switching ON the Dryer
The dryer is to be switched on only when all the require-
ments specified in section 6.1 "Preconditions“ have been
fulfilled.
A. Press the "I / 0“ button.
• The dryer is now in operation.
If "remote control" is selected (see Section 6.6.4), the dryer can
be stopped via contact REM/GND (see diagram).
No connection means "Remote On".
Or if selected via Modbus:
When remotely controlled via Modbus, the dryer will remain in
its state (on / off) if the Modbus connection is disconnected.
6.3 Operation
IMPORTANT: Please note the information provided in Chapter 7.
"Servicing and Maintenance".
6.4 Switching OFF the Dryer
A. Close the shut-off devices in the compressed air line before
and after the desiccant dryer to avoid a flow through the
dryer when it is switched off. Close the condensate line to
the condensate drain to avoid flooding the desiccant dryer
with condensate in the event of internal pressure loss.
B. Press the "I / 0“ button. (Only possible on local operation.
De-energize at remote operation).
• Dryer is switched off.
CAUTION – The dryer is still pressurized!
To depressurize see Chapter 7. "Servicing and Mainte-
nance“.
IMPORTANT: The dryer is designed for continuous operation.
After prolonged inoperative periods, the desiccant compressed
air dryer is to be restarted as specified in section 5.2 "Switch-
ing ON the Dryer“.

6
6.5 Controls (Panel)
1. Left cartridge drying LED (green)
2. Right cartridge drying LED (green)
3. Left cartridge regenerating LED (yellow)
4. Right cartridge regenerating LED (yellow)
5. Left purge valve LED (green)
6. Right purge valve LED (green)
7. Mark / Scroll
8. Power On/ Off switch
9. Power On LED
10. LED Remote ON/OFF
11. LED Service/ Warning/ Alarm
12. Enter / Quit
13. Graphic display
14. Pressure gauge left cartridge
15. Pressure gauge right cartridge
Power On
white: Voltage applied
green: Dryer on
green flashes: Dryer (Remote) off
Dryer in Remote Operation green: at terminal
green flashing: at Modbus
Warning/Service/Alarm
yellow for service, for warning
yellow flashing, flashing has priority!
for alarm red, flashing has priority!
red by wire break PDP-Sensor
for PDP-Alarm red flashing

7
6.5.1 Start Screen
SP X FLO W
VX.X.X
Basic Menu
If there is a PDP sensor, the first line indicates the pressure dew
point; if there is no sensor, the first line is empty!
Dryer On, without PDP-Sensor
Dryer On, with PDP-Sensor (Option)
-5 8 °F
Dryer Off, without PDP-Sensor
Dryer Off, with PDP-Sensor (Option)
-5 8 °F
Press to move to:
Shows hours with operating voltage
4 8 h
Press to move to:
Shows the hours until the next service
1320 h
Press to move to:
Shows the software version
V 1 .0 .0
Press to move to:
Dryer On, without PDP-Sensor
or after approx. 1 minute without input.
6.5.2 Message History
By briefly pressing , you get to the message display.
Press again briefly to return to "Basic menu", or after
2 minutes and 30 seconds.
The messages are numbered at the top right (1 is the latest,
maximum 20 messages, fifo system)
Press to scroll through the messages .:
- Warnings cause the warning / service relay to drop.
- Alarms cause the alarm relay to drop.
Possible messages:
202 Drain Warning (deactivates the Relay warning /
service) yellow LED flashes
310 Service time expired
Relay warning / service) yellow LED glows
204 DTP alarm (deactivates the Relay Alarm)
red LED flashes
210 DTP sensor cable break deactivates the Relay
Alarm) red LED lights
If power failure message 204 is suppressed for 10 minutes,
message 202 is also suppressed.
Examples:
1st Message (newest)
Message 202, at 2891 hours with operating voltage
/
1
2 0 2 2 8 9 1 h
5. Message (5 newest)
Message 310, at 2602 hours with operating voltage
/
5
3 1 0 2 6 0 2 h
12. Message (12 newest)
Message 204, at 2001 hours with operating voltage
/
1 2
2 0 4 2 0 0 1 h
18. Message (18 newest)
Message 210, at 308 hours with operating voltage
/
1 8
2 1 0 3 0 8 h

8
6.5.3 Remote On/Off Settings
Mode A:
With Remote Off, the cycle is stopped, the solenoid valves are
switched off.
With Remote On, the cycle continues at the same point.
Optimized for reciprocating compressors!
Dip switch 6 on OFF.
Mode B:
With Remote Off, the half-cycle is stopped at the end, and the
solenoid valves are switched off.
With Remote On, the cycle continues at the same point.
Optimized for the desiccant dryer!
Dip switch 6 on ON.
Remote On Mode A
A
Remote On Mode B
B
Remote Off Mode A
A
Remote Off Mode B
B
6.5.4 Setting Menu
Press and hold button for approximately 3 seconds.
Target pressure dewpoint
Now appears (Set pressure dewpoint):
PDP sensor installed and activated
-4 0 °F
or
PDP sensor disabled
Pressing marks the number/symbol in the second line.
By further pressing the button, the scrolling will continue:
; -80°C/-112°F; -79°C/-110°F; …; -21°C/-5.8°F; -20°C/-4°F;
Meanings:
PDP control switched off
e.g. -40°C/-40°F Target PDP is -40°/-40°F C
Pressure dewpoint alarm
(if PDP sensor installed and activated)
By pressing , you move to (pressure dewpoint alarm):
-4 ° F
Pressing marks the number in the second line.
Press the button again to scroll through:
The setting range is between (target pressure dewpoint + 5°C/
41°F) and 0°C/32°F.
Example:
Target pressure dewpoint: -37°C/-34,6°F
Pressure dewpoint alarm setting range: -32°C/-25.6°F to 0°C/
32°F
The following options are available:
(-32°C/-25.6°F; -31°C/-23.8°F; …; -1°C/30.2°F; 0°C/32°F;
-32°C/-25.6°F)

9
Service Counter
Press to move to (Reset Service Counter):
no
Pressing marks „no“ in the second line.
By further pressing the button, you can choose between
"no/yes“.
no
y e s
If "Yes" is selected, the service time counter is set to the de-
fault value.
IP-Address
Press to move to (Enter IP address):
IP -A d d r e s s
1 6 9 .2 54.100 .0 95
Pressing marks number/symbol in the second line.
By further pressing the button the numbered block is
incremented:
IP -A d d r e s s
1 6 9 .2 54.100 .0 95
By pressing , you move to the next number block:
IP -A d d r e s s
1 6 9 .2 54.100 .0 95
If the mark disappears after a few seconds, the value is accepted.
The final transfer to the control memory only takes place when
the setting menu is exited via the button or via a cold start.
Subnet-Address
Press to move to (Enter Subnet Address):
S u b n e t
2 5 5 .2 5 5 . 0 0 0 .0 0 0
Pressing marks number/symbol in the second line.
By further pressing the button the numbered block is
incremented:
S u b n e t
2 5 5 .2 5 5 . 0 0 0 .0 0 0
By pressing , you move to the next number block:
S u b n e t
2 5 5 .2 5 5 . 0 0 0 .0 0 0
If the mark disappears after a few seconds, the value is accepted.
The final transfer to the control memory only takes place when
the setting menu is exited via the button or via a cold start.
Gateway-Address
Press to move to (Enter Gateway address):
G a te w a y
1 6 9 .2 54. 1 0 0 .1 00
Pressing marks number/symbol in the second line.
By further pressing the button the numbered block is
incremented:
G a te w a y
1 6 9 .2 54. 1 0 0 .1 00
By pressing , you move to the next number block:
G a te w a y
1 6 9 .2 54. 1 0 0 .1 00
If the mark disappears after a few seconds, the value is accepted.
Press again briefly to return to "Basic menu", or after 2
minutes and 30 seconds.
The final transfer to the control memory only takes place when
the setting menu is exited via the button or via a cold start.

10
Service Technician Menu
Keep the button pressed for approximately 5 seconds.
P a s s w o r d
0 0 0 0
By pressing , the 1st digit of the second line is marked.
By further pressing the button the marked digit is incre-
mented:
P a s s w o r d
0 0 0 0
Press to move to the next digit:
P a s s w o r d
0 0 0 0
If the marking disappears after a few seconds, the password
entered in this way is accepted.
If entered correctly, the default value of the Service Counter
and the operating hours can also be set in the Settings menu.
8760 h
0001 5 7h
Press again briefly to return to "Basic menu", or after 2
minutes and 30 seconds.
6.6 Purge Air Consumption
Dryer is designed to operate either in 8 minute (-40°F/-40°C)
or 4 minute (-94°F/-70°C) cycle.
6.6.1 Maximum Purge Flow
Maximum purge flow is the amount of purge flowing through
the off-stream tube when the purge/repressurization valve
is open. After the purge/repressurization valve closes the
purge flow will gradually decrease as the off-stream tube
repressurizes to line pressure.
6.6.2 Average Purge Flow
The average purge flow is the actual amount of flow aver-
aged over the entire purge/repressurization cycle. It in-
cludes the maximum purge flow for a set amount of the
purge/repressurization time and the volume of air used for
repressurization.
6.6.3 Minimum Outlet Flow
Determine minimum outlet flow available from dryer by
subtracting maximum purge flow from inlet flow to dryer
(specification by authorized dealer).
IMPORTANT: Air compressor should be adequately sized to
handle air system demands as well as purge loss. Failure to do
so could result in overloading air compressors and/or insuf-
ficient air supply downstream.
6.6.4 Timer Board Setting & Remote Control
With the dryer de-energized (disconnect plug), verify position
of the cycle time DIP switches. The DIP switches are located
on the timer board in the cabinet.
Dip-switches Meaning Dip-switch *
OFF
Dip-switch
ON
1 Selection of cycles see table see table
2 Selection of cycles OFF
3 Selection of cycles OFF
4 Local / Remote operation Local Remote operation
5 Remote Off via Modbus deactivated activated
6 Remote Off Mode A / B Mode A Mode B
7 °C / °F °C °F
8 Reserve OFF
* Factory setting: DIP Switch 7 is "ON". All other DIP switches are "OFF"
Scheme Dip 1 Dip 2 Dip 3
-40°C / -40°F ↔<10bar/ 145psig OFF OFF OFF
-70°C / -94°F ↔<10bar/ 145psig ON OFF OFF
-40°C / -40°F ↔>10bar/ 145psig OFF ON ON
-70°C / -94°F ↔>10bar/ 145psig ON OFF ON

11
7.0 Servicing and Maintenance
WARNING – The heatless desiccant dryer is a pressure
containing device. Depressurize the dryer before servic-
ing or repairing. (See section 7.5.)
ATTENTION!
Before starting any service work ensure all power is isolated
from the dryer. A power plug (if fitted) should be unplugged.
7.1 Nameplate
The nameplate contains all information to identify your dryer.
Please provide the information from the nameplate with every
enquiry and when ordering replacement parts.
7.2 Ordering Consumable Parts and Operating
Materials
Use only genuine replacement parts from the manufacturer.
The manufacturer bears no responsibility for hazards caused
by the use of unauthorized parts .
WARNING – There is risk of personal injury or damage to
the machine resulting from the use of unsuitable spares
or operating materials. Unsuitable or poor quality con-
sumable parts and operating materials may damage the
machine or impair its proper function. Personal injury
may result from damage.
For continued good performance of your dryer, all regular
dryer maintenance should be performed by an authorized
service technician.
7.3 Weekly Maintenance
NOTE: The components specified in parentheses (e.g. B006)
refer to the P&I-schematic diagram.
A. Check the residual pressure in the tubes (B006 and B007)
during the regeneration with the gauges (PI018 and PI019).
B. If the residual pressure level rises above 0.3 bar/ 4.4psi, the
purge mufflers must be replaced.
1) Switch off the dryer (see chapter 5. "Switching off the
dryer").
2) Replace the purge mufflers.
3) Switch on the dryer.
C. Check the differential pressure gauge from the pre- and
after filter (F001, F012) (see instruction manual filter).
Replacement filter elements (see section 7.4 "Annual
maintenance").
D. Check the automatically condensate drain at the pre-filter.
7.4 Annual Maintenance
NOTE: The components specified in parentheses (e.g. B006)
refer to the P&I-schematic diagram.
A. Replace the filter cartridges from the pre- and after filter
(F001 and F012).
1) Depressurize the dryer (see chapter 7.5 "Depressurizing
the desiccant dryer").
2) Switch off the dryer (see chapter 5. "Switching off the
dryer").
3) Replacing the filter cartridges see filter instruction
manual.
B. Replace condensate drain.
C. Replace the purge mufflers (see section 7.3 "Weekly main-
tenance").
7.5 Depressurize the Desiccant Dryer
NOTE: The components specified in parentheses (e.g. B006)
refer to the P&I-schematic diagram.
A. Close the shut-off devices in the compressed-air inlet- and
outlet line.
B. Let the desiccant dryer run through a complete tower
change cycle or until all air has been exhausted from the
dryer.
C. Check the residual pressure in the tubes (PI018 and PI019).
7.6 Replacement of Desiccant
A. Frequency Of Desiccant Replacement
Desiccant should be replaced whenever the required dew
point cannot be maintained while the dryer is being operated
within its design conditions and there are no mechanical
malfunctions.
NOTE: Desiccant life is determined by the quality of the
inlet air. Proper filtering of the inlet air will extend the life
of the desiccant. Typically desiccant life is 2 years.
B. Procedure for Desiccant Charge Replacement
1. Depressurize the dryer (see chapter 7.5 "Depressurizing
the desiccant dryer").
2. Switch off the dryer (see chapter 5. "Switching off the
dryer").
3. Remove the front panel of the dryer.
4. Loosen the nuts / washers of the upper manifold and
remove it.
5. Remove the gasket and metal mesh. Remove the
threaded rods.
6. Remove the aluminum profiles and remove the cartridge
with the aid of the attached knurled screw.
7. Replace the lower metal mesh and gaskets and reas-
semble the new threaded rods and profiles back.
8. Insert the cartridges and replace the upper metal mesh
and gaskets.
9. Mount the distributor block and the front plate of the
dryer.
10.Torque:
HSHD-7 - HSHD-21: 15Nm (nuts/ threaded rods)
HSHD-27 - HSHD-40: 20Nm (nuts/ threaded rods)
11.After replacing the desiccant, restart the dryer as de-
scribed in chapter 6.
IMPORTANT: Keep the desiccant cartridges with the new desic-
cant closed until they are used, to avoid moisture contamination.
7.6.1 Replacement of Purge Solenoid Valves
NOTE: The components specified in parentheses (e.g. B006)
refer to the P&I-schematic diagram.
A. Change solenoid purge valves (V014/V015) after 5 years of
full operation.

12
7.7 Prefilter/Afterfilter Maintenance
A. Element Replacement
1. For maximum filtration efficiency, replace element an-
nually or when pressure drop reaches 4.3 psi (0.3 bar)
(indicator in red area), whichever occurs first.
B. Procedure for Element Replacement
WARNING: THIS FILTER IS A PRESSURE CONTAINING DEVICE.
DEPRESSURIZE BEFORE SERVICING.
1. Isolate filter (close inlet and outlet valves if installed) or
shut off air supply.
2. Depressurize filter by slowly opening manual drain valve.
3. Remove bowl by unscrewing the bowl from the filter
head using hand, strap wrench or C spanner, and pulling
bowl straight down.
4. Clean filter bowl.
5. Replacing complete element.
a) Pull off old element and discard.
b) Make certain that the old and new element have the
same part number and the end caps are the same
color.
c) Wipe the wall inside the filter head to remove any
dirt.
d) Lubricate the new element o-ring on the element
top cap.
e) Align the slot in the element top cap with the projec-
tion inside the filter head.
Projection
Element Slot
O-Ring
f) Insert the element into the head making sure the
element slot and the projection inside the filter head
remain aligned.
NOTE: Handle all elements by bottom end cap only.
6. Replace housing o-ring (located at the top of the filter
bowl) if needed. Make certain o-ring is generously
lubricated (Use lubricant provided).
7. Reassemble bowl to head.
NOTE: Threaded bowl to head connection, generously
lubricate threads with a high grade/temperature lubri-
cant 150°F (66°C). (Use lubricant provided)
C. Auto Drain Mechanism Replacement
Prefilter only: It is recommended that drain mechanism be
replaced annually.

13
8.0 Troubleshooting Guide
NOTE: Refer to the P&I-schematic diagram and Dimensional Drawings for components specified in parentheses (e.g. B006).
WARNING – A POTENTIAL ELECTRICAL SHOCK HAZARD EXISTS. Some of the troubleshooting checks may require gain-
ing access to the dryer’s electrical enclosure while the power supply is energized and should be performed by a
qualified electrical technician
WARNING – Before performing any electrical or mechanical repairs or maintenance, or removing or disassembling
any component, be sure to de-energize and depressurize the dryer
Water in the compressed-air system
Possible Cause Remedy
Condensate residues which formed prior to
starting up the dryer are in the compressed-
air system
Blow out compressed-air system with dry air until no more moisture is con-
densed out. Open collection point at most remote position, if possible.
Bypass open. Close bypass.
Condensate from the prefilter not separated. Carry out check by trained staff and repair, if necessary.
The operating parameters have changed
since the desiccant dryer was installed.
Correct to the original operating parameters as the dryer was designed.
High pressure loss through the desiccant compressed air dryer
Possible Cause Remedy
The capacity of the pre and/or -after filter
cartridge are overload.
Replace the filter cartridge (see annex filter).
The operating parameters have changed
since the desiccant dryer was installed.
Restore the operating conditions for which the dryer was designed.
Display: 310
(LED Warning/ Service/ Alarm glows yellow)
(Service time expired, leads to deactivation of the relay warning / service)
Possible Cause Remedy
Service time expired Carry out maintenance and reset service counter.

14
Display: 202
(LED Warning/ Service/ Alarm flashes yellow)
(Drain warning, leads to deactivation of the relay warning / service)
Possible Cause Remedy
Condensate not separated. Press TEST-button on the condensate discharger (X001/ see chapter 12).
Condensate is not discharged:
- Check power supply to solenoid coil.
In case of power on this terminal replace printed circuit board.
- Check if dryer and condensate discharger are pressurized (min. 0.8bar
/11.6psi). If they are pressurized check if outlet pipe behind the conden-
sate discharger is blocked.
Yes: Clean pipe and remove any obstruction.
No: Disconnect dryer and condensate discharger from power supply
(main switch / fuse) and ensure that device is in a pressure-less state.
Dismantle solenoid diaphragm, remove any obstruction and examine
diaphragm. If diaphragm is damaged replace with new one. During this
procedure, it is possible to replace also all seals and the coil core.
Housing and sensors should be thoroughly cleaned at the same time.
Condensate and air are discharged, but ALARM -signal continues
- Disconnect dryer and condensate discharger from power supply (main
switch / fuse) and ensure that device is in pressureless state. Open con-
densate discharger and clean sensor thoroughly.
Display: 204
(LED Warning/ Service/ Alarm flashes red)
(PDP Alarm, leads to deactivation of the relay alarm)
Possible Cause Remedy
Desiccant dryer only switched on briefly. Operate desiccant dryer for some time with low load.
Desiccant dryer overload. Adapt the operating conditions to the permitted parameters.
Ambient temperature too high.
Air inlet temperature high.
Volumetric flow rate too high.
Operation pressure too low.
PDP sensor defective (PT029) Check the PDP sensor and replace, if necessary.
Display: 210
(LED Warning/ Service/ Alarm glows red)
(PDP Sensor cable break, leads to deactivation of the relay alarm)
Possible Cause Remedy
PDP Sensor cable break Check the electrical connection, replace if necessary.
PDP sensor not connected PDP-control switch off (see chapter 6.5.4)

15
9.0 Technical Data
Specification according to DIN ISO 7183 Option A2
IMPORTANT: Should any data change which is marked with an asterisk (*), all other data in that section may also change.
9.1 Maximum Purge Flow
HSHD-7 HSHD-13 HSHD-18 HSHD-21 HSHD-27 HSHD-40
Min. inlet temperature °F / °C + 35.6 / + 2
* Inlet temperature °F / °C +100 / + 38
Max. inlet temperature °F / °C + 122 / + 50
* Outlet temperature °F / °C +100 / + 38
* Air flow
(relating to +20°C compressed air
induction temperature and 1 bar
absolute)
scfm
m3/h
7
12
13
22
18
31
21
36
27
46
40
68
* Pressure dewpoint at working pressure °F / °C - 40 / - 40
Min. working pressure psi/bar 58 / 4
* Working pressure [ P0 ] psi/bar 100 / 7
Allowable pressure [ PS ] psi/bar 217.5 / 15
* Differential pressure inlet / outlet
(without filtration) psi/bar [2.18 / [0.15
Compressed air connection
(without filtration) NPT 1/2 3/4
9.2 Ambient Temperature
HSHD-7 HSHD-13 HSHD-18 HSHD-21 HSHD-27 HSHD-40
Ambient temperature °F / °C + 100 / + 38
Min. ambient temperature °F / °C + 35.6 / + 2
Max. ambient temperature °F / °C + 104 / + 40
9.3 Electrical Data
HSHD-7 HSHD-13 HSHD-18 HSHD-21 HSHD-27 HSHD-40
Voltage V 120 ±10% / 1 Ph
Frequency Hz 50 - 60
Nominal power W
BTU/hour 50 / 171
Nominal current A 0.7
Max. pre-protection A 16
Max. connection cross section mm² 3 x 1.5
* Noise level chart (Equivalent level of
continuous acoustic pressure in the
distance of 1m in a free field (Leq))
dB (A) 60 62 62 62 62 63
* Noise level chart (The level of short-
term sound pressure at the distance
of 1m in open space (LpA))
dB (A) 74 74 75 76 77 78

16
9.4 Desiccant
HSHD-7 HSHD-13 HSHD-18 HSHD-21 HSHD-27 HSHD-40
Desiccant Activated alumina
Volume profile gal 0.68 0.99 1.37 1.75 2.32 2.97
Charge per tower (Cartridge) lb 4.10 6.13 8.71 11.35 14.88 19.29
9.5 Condensate
HSHD-7 HSHD-13 HSHD-18 HSHD-21 HSHD-27 HSHD-40
Condensate separator connection (pre-filter) See filter instruction manual
9.6 Measurements, Weights
HSHD-7 HSHD-13 HSHD-18 HSHD-21 HSHD-27 HSHD-40
Height / Width / Depth inch See dimensional drawing
Weight lb 61.3 77.2 97.4 117.7 136.2 165
9.7 Nominal Air Flow
Model DTP [°F] Max. air flow inlet [scfm] 1
HSHD-7 - 40 7
HSHD-13 - 40 13
HSHD-18 - 40 18
HSHD-21 - 40 21
HSHD-27 - 40 27
HSHD-40 - 40 40
HSHD-7 - 94 5
HSHD-13 - 94 9
HSHD-18 - 94 12
HSHD-21 - 94 14
HSHD-27 - 94 18
HSHD-40 - 94 27
1) According to CAGI (Compressed Air and Gas Institute) standard
ADF-200, Dual Stage Regenerative Desiccant Compressed Air
Dryers - Methods for Testing and Rating. Conditions for rating
dryers are: inlet pressure - 100 psig (7 kg/cm2); inlet temperature
- saturated at 100°F (38°C)
9.8 Correction Factors
Correction factor for working pressure
Working pressure (psi) 58 72 87 100 116 131 145 160 174 189 203 218
Working pressure (bar) 4 5 6 7 8 9 10 11 12 13 14 15
K p(ü) 0.40 0.57 0.77 1.00 1.13 1.25 1.38 1.38 1.50 1.56 1.61 1.67
Correction factor for compressed air inlet temperature
Compressed air inlet temperature (°F / °C) 86 / 30 95 / 35 100 / 38 104 / 40 113 / 45 122 / 50
k Tin (DTP = -40°C/ °F) 1.07 1.07 1.00 0.93 0.82 0.72

17
10.0 Replacement Parts & Maintenance Kits
10.1 Replacement Parts
HSHD-7 HSHD-13 HSHD-18 HSHD-21 HSHD-27 HSHD-40
Filter Adapters 7443512 7443513
Plugs 7443514 7443515
Controller 7443516
Gauge 7443517
Top Block 7443518 7443519
Bottom Block 7443520 7443521
Solenoid Valve 7443522
Front Panel 7443523 7443524 7443525 7443526 7443527 7443528
Base Plate 7443529 7443530
Muffler Core 3116957
Orifice 7443531 7443532 7443533 7443534 7443535 7443536
Plastic Caps 7443537
Solenoid Adapters 7443538
10.2 Maintenance Kits
HSHD-7 HSHD-13 HSHD-18
Year 2 Maintenance Kit Filter Elements,
Muffler Cores, Drain
HSHDMK7-2-4
(7458608)
HSHDMK13-2-4
(7458609)
HSHDMK18-2-4
(7458610)
Year 3 Maintenance Kit
Filter Elements,
Muffler Cores, Drain,
Desiccant Cartridge
HSHDMK7-3-5
(7458602)
HSHDMK13-3-5
(7458603)
HSHDMK18-3-5
(7458604)
Year 4 Maintenance Kit Filter Elements,
Muffler Cores, Drain
HSHDMK7-2-4
(7458608)
HSHDMK13-2-4
(7458609)
HSHDMK18-2-4
(7458610)
Year 5 Maintenance Kit
Filter Elements,
Muffler Cores, Drain,
Desiccant Cartridge
HSHDMK7-3-5
(7458602)
HSHDMK13-3-5
(7458603)
HSHDMK18-3-5
(7458604)
HSHD-21 HSHD-27 HSHD-40
Year 2 Maintenance Kit Filter Elements,
Muffler Cores, Drain
HSHDMK21-2-4
(7458611)
HSHDMK27-2-4
(7458612)
HSHDMK40-2-4
(7458613)
Year 3 Maintenance Kit
Filter Elements,
Muffler Cores, Drain,
Desiccant Cartridge
HSHDMK21-3-5
(7458605)
HSHDMK27-3-5
(7458606)
HSHDMK40-3-5
(7458607)
Year 4 Maintenance Kit Filter Elements,
Muffler Cores, Drain
HSHDMK21-2-4
(7458611)
HSHDMK27-2-4
(7458612)
HSHDMK40-2-4
(7458613)
Year 5 Maintenance Kit
Filter Elements,
Muffler Cores, Drain,
Desiccant Cartridge
HSHDMK21-3-5
(7458605)
HSHDMK27-3-5
(7458606)
HSHDMK40-3-5
(7458607)
Phone: +1 724 745 1555
Email: ft.dehydration.order.entry@spxflow.com
Web: www.spxflow.com/hankison

18
11.0 Drawings
11.1 General Arrangement: HSHD-7
12345678
A A
B B
C C
D D
E E
F F
Maintenance
Space
13.5/8
9/16
19.3/8
4.1/4
6.3/8
6.9/16
15.7/8
1/2
Ø5/8
Ø3/8
2.3/8
1.1/2
2.3/4 2.3/4
10.13/16
13.3/8
4xØ3/8
12.3/4
5.9/16
6.3/8
18.1/2
1.1/2
7.7/8
24.1/4
5.5/16
21
1.1/2
CD
OPTION
2.3/16 4.75
15.1/2
200
2.3/8
1.25
4x Ø5/16 x 3.15/16
2x Ø5/16 x 3.15/16
>15.3/4
16.1/16
A
B
A
A
BB
A
B
C
D
NPT*
NPT*
NPT*
NPT*
1/2” NPT
1/2” NPT
1/2” NPT
1/2” NPT
* ANSI B1.20.1
This manual suits for next models
6
Table of contents
Other HANKISON Dehumidifier manuals
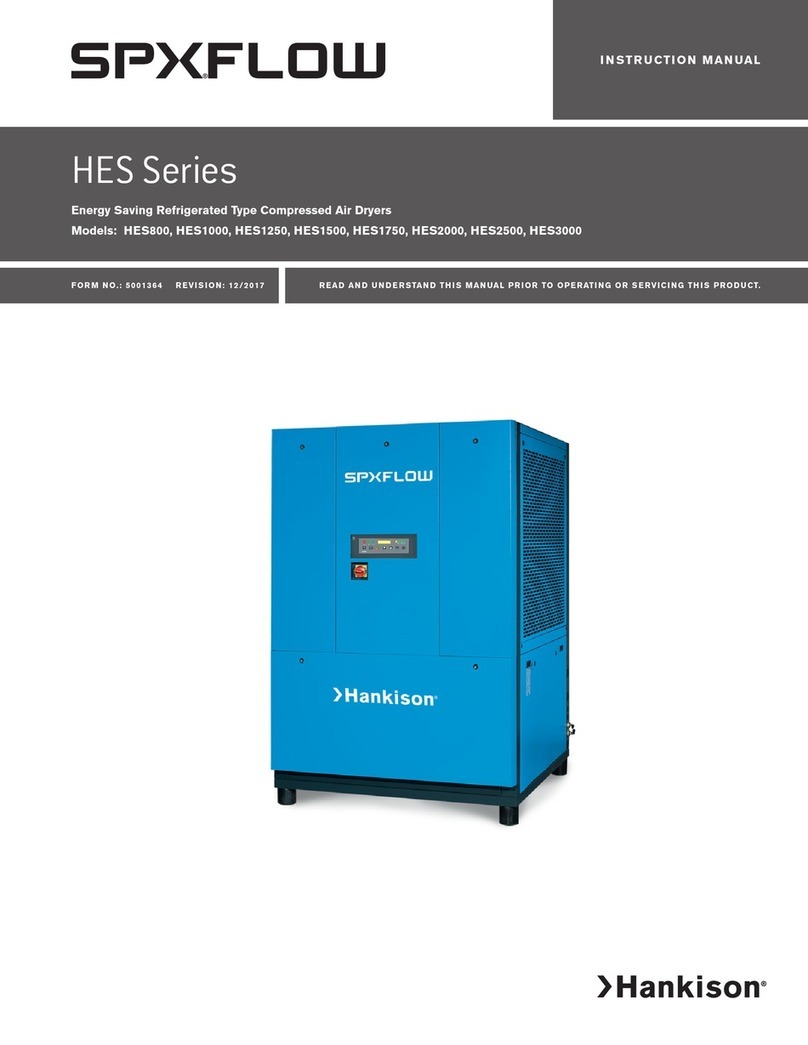
HANKISON
HANKISON SPX FLOW HES Series User manual

HANKISON
HANKISON SPX HES Series User manual

HANKISON
HANKISON HPRP 25 User manual

HANKISON
HANKISON H Series User manual
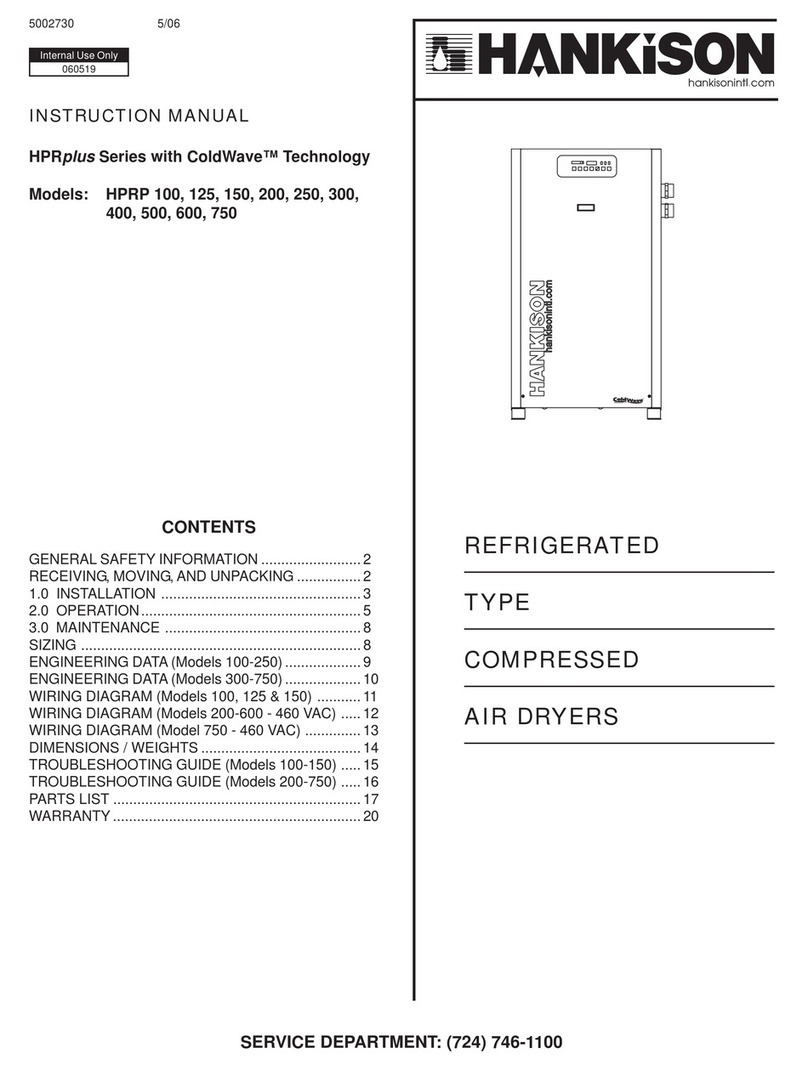
HANKISON
HANKISON HPRplus Series User manual

HANKISON
HANKISON HBP Series User manual
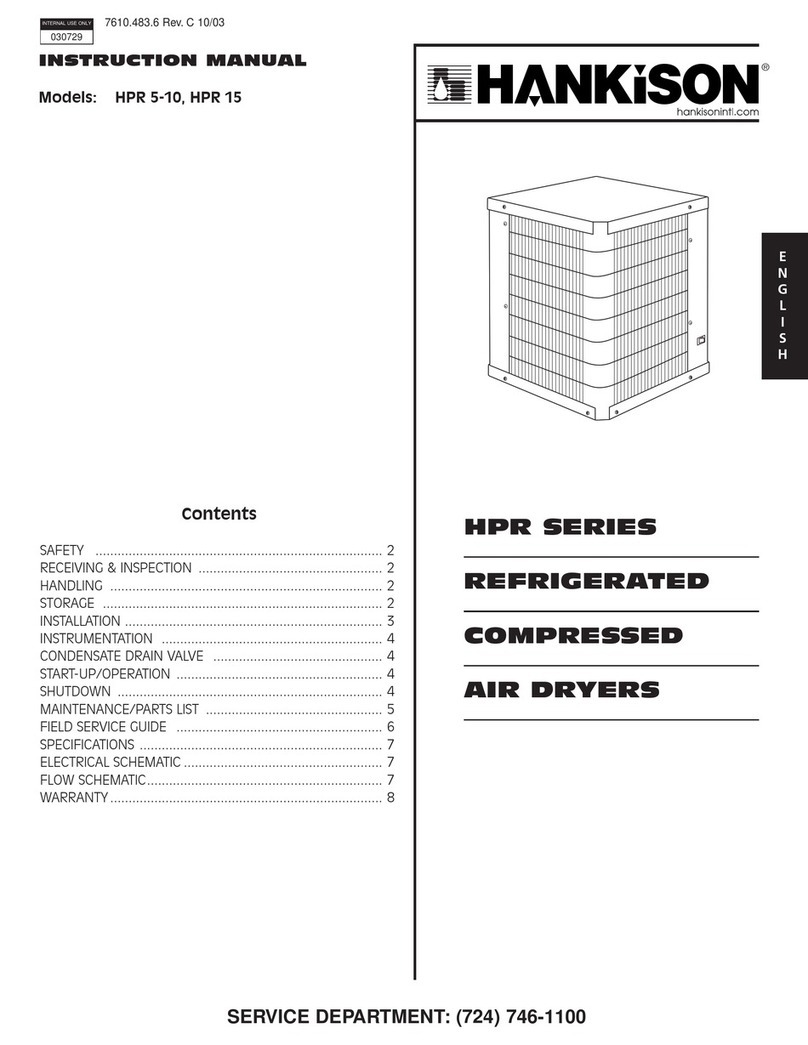
HANKISON
HANKISON HPR Series User manual

HANKISON
HANKISON HPET Series User manual
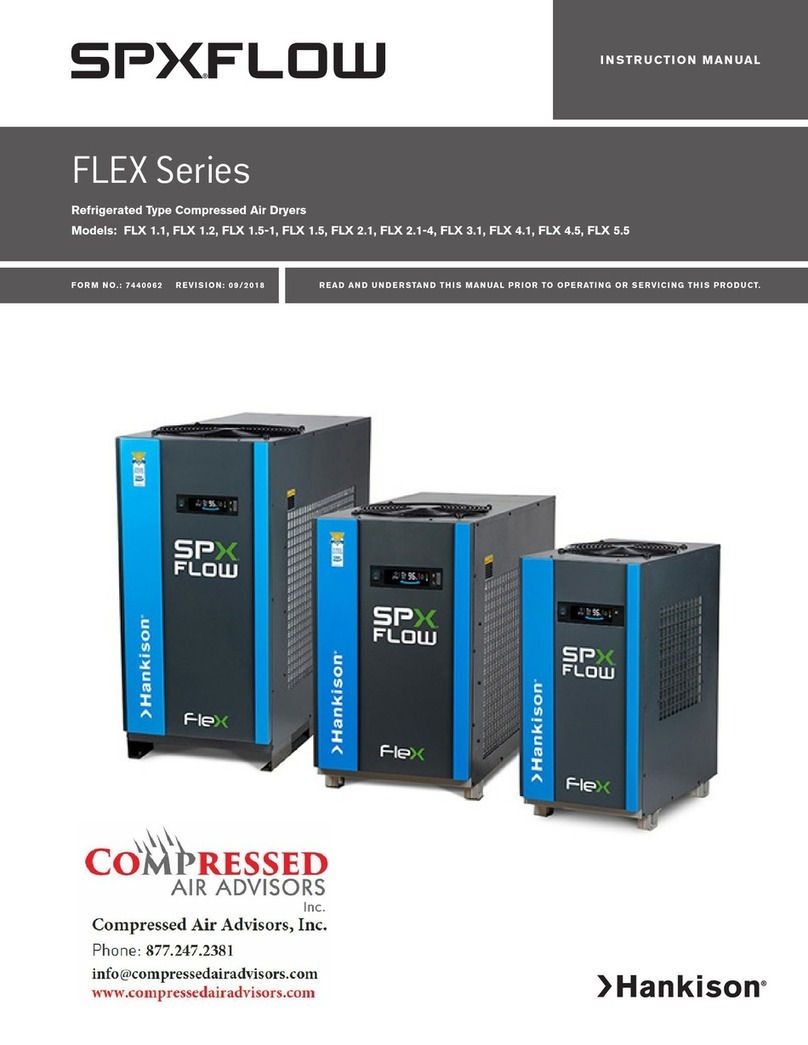
HANKISON
HANKISON SPX Flow FLEX Series User manual
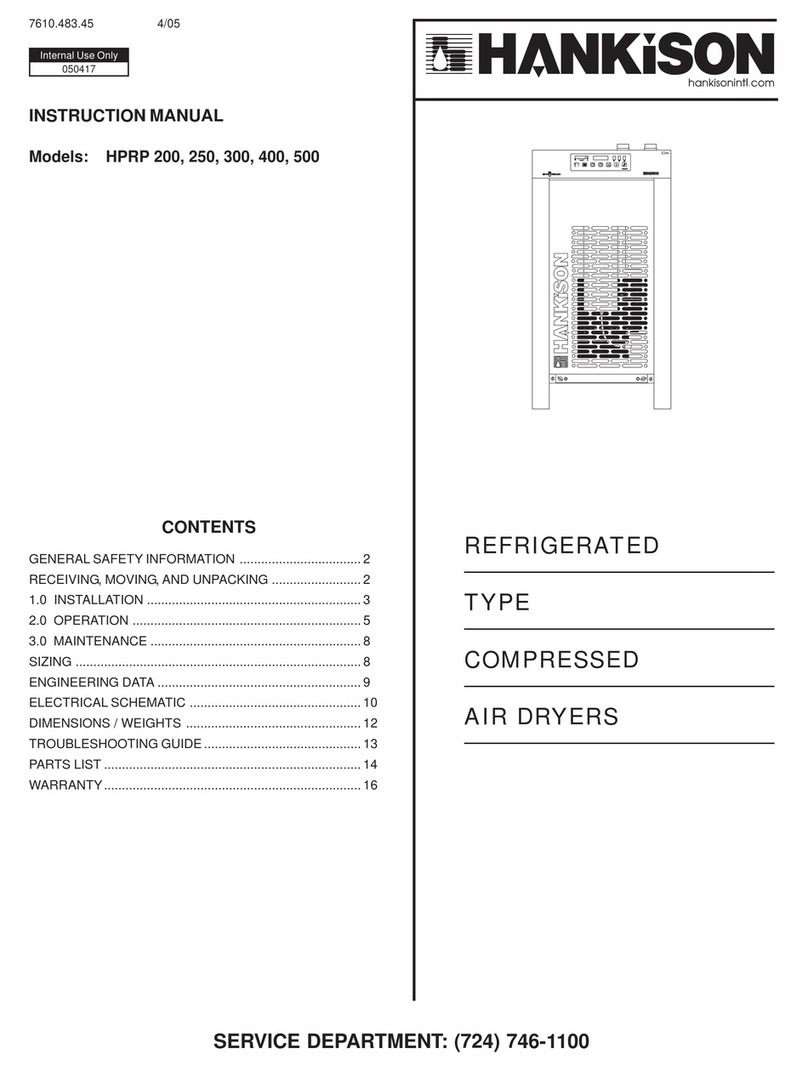
HANKISON
HANKISON HPRP 200 User manual