Harmonic Drive HA-675 Series User manual

HA-675 Series
AC Servo Driver Manual
●Thank you very much for your purchasing our HA-675 series
servo driver.
●Be sure to use sufficient safety measures when installing and
operating the equipment so as to prevent an accident resulting in
a serious physical injury damaged by a malfunction or improper
operation.
●Product specifications are subject to change without notice for
improvement purposes.
●Keep this manual in a convenient location and refer to it
whenever necessary in operating or maintaining the units.
●The end user of the driver should have a copy of this manual.
SOFTWARE Ver.2.1
ISO14001
ISO9001

1
SAFETY GUIDE
For actuators, motors, control units and drivers
manufactured by Harmonic Drive Systems Inc
Read this manual thoroughly before designing the application, installation, maintenance or inspection of the actuator.
Indicates a potentially hazardous situation,
which, if not avoided, could result in death
or serious personal injury.
Indicates a potentially hazardous situation, which, if
not avoided, may result in minor or moderate personal
injury and/or damage to the equipment.
LIMITATION OF APPLICATIONS:
The equipment listed in this document may not be used for the applications listed below:
Space equipment Automobile, automotive parts
Aircraft, aeronautic equipment Amusement equipment, sport equipment, game machines
Nuclear equipment Machine or devices acting directly on the human body
Household apparatus Instruments or devices to transport or carry people
Vacuum equipment Apparatus or devices used in special environments
If the above list includes your intending application for our products, please consult us.
Safety measures are essential to prevent accidents resulting in death, injury or damage of the equipment due to
malfunction or faulty operation.
CAUTIONS FOR ACTUATORS AT APPLICATION DESIGNING
Always use under followings conditions:
-Ambient temperature: 0℃to 40℃
-Ambient humidity: 20% to 80%RH (Non-condensation)
-Vibration: Max 24.5 m/S2
-No contamination by water, oil
-No corrosive or explosive gas
Follow exactly the instructions in the relating
manuals to install the actuator in the equipment.
-Ensure exact alignment of motor shaft center and
corresponding center in the application.
Failure to observe this caution may lead to vibration,
resulting in damage of output elements.
CAUTION FOR ACTUATORS IN OPERATIONS
Keep limited torques of the actuator.
-Keep limited torques of the actuator.
-Be aware, that if arms attached to output element hits
by accident an solid, the output element may be
uncontrollable.
Never connect cables directly to a power supply
socket.
-Each actuator must be operated with a proper driver.
-Failure to observe this caution may lead to injury, fire or
damage of the actuator.
Do not apply impacts and shocks
-Do not use a hammer during installation
-Failure to observe this caution could damage the
encoder and may cause uncontrollable operation.
Avoid handling of actuators by cables.
-Failure to observe this caution may damage the wiring,
causing uncontrollable or faulty operation.
CAUTIONS FOR DRIVERS ATAPPLICATION DESIGNING
Always use drivers under followings conditions:
-Mount in a vertical position keeping sufficient distance
to other devices to let heat generated by the driver
radiate freely.
-Ambient temperature: 0℃to 50℃
-Ambient humidity: less than 95% RH (Non
condensation)
-No contamination by water, oil or foreign matters
-No corrosive, inflammable or explosive gas
Use sufficient noise suppressing means and safe
grounding.
-Keep signal and power leads separated.
-Keep leads as short as possible.
-Ground actuator and driver at one single point, minimum
ground resistance class: D (less than 100 ohms)
-Do not use a power line filter in the motor circuit.
Pay attention to negative torque by inverse load.
–Inverse load may cause damages of drivers.
-Please consult our sales office, if you intent to apply
products for inverse load.
Use a fast-response type ground-fault detector
designed for PWM inverters.
-Do not use a time-delay-type ground-fault detector.
CAUTION FOR DRIVERS IN OPERATIONS
Never change wiring while power is active.
-Make sure of power non-active before servicing the
products.
-Failure to observe this caution may result in electric
shock or personal injury.
Do not touch terminals or inspect products at least
5 minutes after turning OFF power.
-Otherwise residual electric charges may result in
electric shock.
-Make installation of products not easy to touch their
inner electric components.
Do not make a voltage resistance test.
-Failure to observe this caution may result in damage of
the control unit.
-Please consult our sales office, if you intent to make a
voltage resistance test.
Do not operate control units by means of power
ON/OFF switching.
-Start/stop operation should be performed via input
signals.
Failure to observe this caution may result in deterioration
of electronic parts.
DISPOSAL OF AN ACTUATOR, A MOTOR,A CONTROL UNITAND/OR THEIR PARTS
All products or parts have to be disposed of as industrial waste.
-Since the case or the box of drivers have a material indication, classify parts and dispose them separately.
SYSTEMS
C
A
U
TI
O
N
CAUTION
CAUTION
WARNING
WARNIN
G
C
A
U
TI
O
NWARNIN
G
C
A
U
TI
O
N
CAUTION
CAUTION
C
A
U
TI
O
N
WARNIN
G
WARNING
C
A
U
TI
O
N
C
A
U
TI
O
N
CAUTION
WARNING

HA-675 series servo driver manual
HA-675_V3_02 - Contents 1 -
Contents
Chapter 1 Outlines of HA-675 driver·······················································································1
1-1 Main features·············································································································1
1-2 Models of HA-675 driver····························································································2
1-3 Combinations with actuators·····················································································3
1-4 Specifications of HA-675 driver·················································································3
1-5 External drawing of the HA-675 drivers ····································································4
1-6 Front panel················································································································5
1-7 Outlines of I/O ports ··································································································6
1-8 Operating display panel·····························································································7
1-8-1 Outlines of operation modes·····················································································7
1-8-2 Selecting a mode·······································································································7
1-8-3 Functions of each mode····························································································8
1-9 Teach-box··················································································································8
1-9-1 Specifications of the teach-box ·················································································8
1-9-2 External drawing of the teach-box·············································································9
1-9-3 Main blocks of the teach-box panel·········································································10
1-9-4 Operation keys········································································································11
1-9-5 Operation modes·····································································································13
1-10 Outlines of protection functions···············································································14
1-10-1 Alarms ·····················································································································14
1-10-2 Protection functions·································································································15
Chapter 2 Functions ···············································································································18
2-1 Control system of HA-675 driver·············································································18
2-2 Encoder system·······································································································19
2-2-1 Incremental encoder INC························································································19
2-2-2 Absolute encoder ABS····························································································19
2-3 Tuning Servo gains ·································································································20
2-3-1 Position control block and position loop gain··························································20
2-3-2 Speed control block, speed loop gain, and speed loop integral compensation······21
2-4 Motion control functions ··························································································22
2-4-1 Outlines of teach-box ······························································································22
2-4-2 Outlines of programming·························································································23
2-5 Other functions········································································································27
2-5-1 In-position range······································································································27
2-5-2 Manual JOG operation····························································································27
2-5-3 Monitoring inputs and operating outputs·································································27
2-5-4 Error count clear by S-ON·······················································································28
2-5-5 Speed limit and current limit····················································································28
2-5-6 Automatic actuator identification for HA-675-1 driver ·············································29
2-5-7 Automatic gain control at positioning for HA-675-1 driver·······································29
Chapter 3 I/O ports··················································································································30
3-1 I/O port layout··········································································································30
3-2 Models of I/O port connector CN2···········································································30

HA-675 series servo driver manual
HA-675_V3_02 - Contents 2 -
3-3 I/O port connections································································································31
3-3-1 Logical inputs ··········································································································31
3-3-2 Contact inputs··········································································································31
3-3-3 Outputs····················································································································32
3-3-4 Monitor outputs········································································································32
3-4 I/O port functions·····································································································33
3-5 Connection example································································································42
3-6 I/O ports for absolute position data ABS·································································44
3-6-1 General descriptions of absolute encoder·······························································44
3-6-2 Outputting position data from output port: CN2 ······················································45
Chapter 4 Installing the HA-675 driver··················································································46
4-1 Receiving Inspection·······························································································46
4-2 Notices on handling·································································································47
4-3 Location and installation··························································································48
4-3-1 Environment of location···························································································48
4-3-2 Notices on installation ·····························································································48
4-3-3 Installing ··················································································································49
4-4 Suppressing noise···································································································49
4-4-1 Devices for grounding ·····························································································49
4-4-2 Installing noise filter·································································································50
4-4-3 Instructions for cabling ····························································································51
4-5 Connecting power cables························································································52
4-5-1 Instructions for power supply ··················································································52
4-5-2 Allowable size of cables··························································································52
4-5-3 Connecting the power cable····················································································53
4-5-4 Insulation transformer······························································································53
4-5-5 Protecting power lines·····························································································54
4-6 Connecting a ground wire·······················································································54
4-7
Connecting motor and regeneration resistor cables
························································54
4-8 Connecting the encoder and the I/O cables····························································55
4-8-1 Preparing the encoder cable and the I/O cable·······················································55
4-8-2 Pin layouts of encoder connector (CN1)·································································55
4-8-3 Pin layouts of the I/O signal connector (CN2)·························································56
4-8-4 Connecting the encoder and the I/O signal cables·················································56
4-8-5 Recommendation of EIA-232C (RS-232C) cable for CN3······································56
4-9 Power ON and OFF sequences··············································································57
4-9-1 Power ON / OFF sequence circuit ··········································································57
4-9-2 Frequency of power ON / OFF operation································································57
4-9-3 Power ON sequence·······························································································57
4-9-4 Power OFF sequence ·····························································································58
Chapter 5 Operations ·············································································································59
5-1 Trial run ···················································································································59
5-1-1 Driving actuator only································································································59
5-1-2 Setting parameters··································································································68
5-1-3 Tuning servo parameters ························································································70
5-1-4 Operations of teach-box··························································································72
5-1-5 Setting parameter data····························································································73
5-1-6 End of trial run·········································································································76
5-2 Normal operation·····································································································77
5-2-1 Notices for normal operations ·················································································77

HA-675 series servo driver manual
HA-675_V3_02 - Contents 3 -
5-2-2 Daily maintenance···································································································77
Chapter 6 Operation of the display panel·············································································78
6-1 Summary of modes·································································································78
6-2 Selecting a mode·····································································································78
6-3 Functions of each mode··························································································79
6-4 Monitor mode ··········································································································80
6-4-1 Operation in the monitor mode················································································80
6-4-2 Functions of the monitor mode················································································81
6-5 Tune mode ··············································································································89
6-5-1 Operation in the tune mode·····················································································89
6-5-2 Functions of tune mode···························································································91
6-6 Parameter mode······································································································96
6-6-1 Operation in the parameter mode···········································································96
6-6-2 Functions of parameter mode ·················································································98
6-7 Test mode··············································································································107
6-7-1 Operation in the test mode····················································································107
6-7-2 Functions of test mode··························································································109
6-8 Defaults of parameters··························································································114
6-9 Parameters after automatic setting of the HA-675-1 driver···································117
Chapter 7 Operations of the teach-box ··············································································118
7-1 Outlines of the teach-box······················································································118
7-2 Attaching and detaching the teach-box·································································118
7-3 Operation keys······································································································119
7-4 Outlines of indications···························································································121
7-5 Operations of teach-box························································································122
7-5-1 Common operations······························································································122
7-5-2 Operations for absolute system ABS····································································124
7-5-3 Turing servo power ON and OFF··········································································125
7-6 Operation modes···································································································126
7-7 Program mode·······································································································127
7-7-1 Setting the program mode·····················································································127
7-7-2 Specifying an address···························································································128
7-7-3 Arranging address numbers··················································································128
7-7-4 Conditions in programming···················································································129
7-7-5 Programming of commands··················································································130
7-7-6 Examples of program····························································································131
7-7-7 Fine adjustment of positions ·················································································133
7-7-8 Functions of program mode··················································································134
7-8 Test mode··············································································································142
7-8-1 Servo-ON ··············································································································142
7-8-2 Originating·············································································································142
7-8-3 Operation in the test mode····················································································143
7-8-4 JOG operations·····································································································144
7-9 Parameter mode····································································································145
7-9-1 Operation in the parameter mode·········································································145
7-9-2 Commands in parameter mode·············································································146

HA-675 series servo driver manual
HA-675_V3_02 - Contents 4 -
Chapter 8 Troubleshooting··································································································154
8-1 Alarms and diagnostic tips ····················································································154
8-2 Troubleshooting for improper actuator motion······················································168
8-2-1 No rotation·············································································································168
8-2-2 Unstable rotation ···································································································169
8-2-3 Poor positioning accuracy·····················································································171
8-3 Exchanging batteries ABS ····················································································172
8-3-1 Duration of keeping a revolution count··································································172
8-3-2 Exchanging procedures ························································································172
Chapter 9 Options·················································································································173
9-1 Extension cables···································································································173
9-2 Connectors············································································································173
9-3 Software for setting up parameters·······································································174
9-4 Software for creating operating data·····································································174
9-5 Backup battery for absolute encoders ABS ·······················································174
9-6 Insulation transformer (single-phase)····································································175
Index ·······························································································································178

Chapter 1 Outlines of HA-675 driver
HA-675_V3_03 - 1 -
Chapter 1 Outlines of HA-675 driver
The HA-675 series are dedicated servo drivers with programmable motion control functions for the
FHA-C series actuators, which are axially compact and featured a large through-hole. The actuators
utilize Harmonic drive® gear components for precise motion control and super flat AC servomotors.
The HA-675 drivers provide many superior motion control functions to allow the FHA-C series
actuators to excel in performance.
1-1 Main features
◆Unique programmable motion control functions
Additionally to the AC servo drive functions, the HA-675 drivers provide programmable functions to
control position, speed, and acceleration, and logical functions such as repeat, jump and so on.
Specifying a motion starting address performs a complicated programmed motion profile.
◆Easy programming with the teach-box
You can create motion programs with the teach-box having operation keys and a LCD display with four
lines by 20 digits without any complicated operation.
◆For both absolute and incremental encoders
The FHA-C series actuators provide two kinds of encoders for detecting a position: the one is an
incremental encoder for general applications and the other is an absolute encoder for keeping its
current position data all the time, even in power failure. The HA-675 series drivers provide their
models to accept both types of encoders. In this document, INC is attached for the descriptions for the
incremental system only, and ABS is for the absolute system only.
◆Easy parameter setting
Parameters have been set to match the driver with the FHA-C series actuator you have ordered. No
setting for the actuator is necessary by users.
The HA-675 series provides four modes that can be adjusted by the end user: monitor mode, tune
mode, parameter mode, and test mode. Parameters of these modes are indicated on the front panel
using a 7-segment LED display and are easily set.
Load
HA-675driver
Servo
control
Position
Speed
Program control
Position command
Speed command
Program storing
Host
Specifying address
Starting
Stopping
Originating
TBX-670
or
PSF-670
Programming

Chapter 1 Outlines of HA-675 driver
HA-675_V3_03 - 2 -
PT1-200 04-200
Ins. transformer: PT1 series
2nd volt. 200: AC 200V
Prim. volt 100: AC100V
115: AC115V
200: AC200V
220: AC220V
2nd cur. 02: 2A
04: 4A
08: 8A
1-2 Models of HA-675 driver
Model number of The HA-675 driver is as follows
Note 1: The absolute system is not available for HA-675-1 (1A).
◆Extension cables (optional):
for HA-675-1
for HA-675-2 and -4
for a motor:
EWC - MB * * -A06 - TN
EWC - MB * * -M08 - TN
for an incremental encoder: INC
EWC - E* * - M06 - 3M14
EWC - E * * -B04 - 3M14
for an absolute encoder: ABS
-
EWC - S * * -B08 - 3M14
* * means cable length: 03: 3m, 05: 5m, 10: 10m (three kinds of length are available.)
Connectors (optional): CNK-HA65-S1/ CNK-HA65-S2
Software for setting up parameters (optional): PSF-650
(Downloading is possible from our home page [http://www.hds.co.jp/])
Software for creating operating data(optional): PSF-670
(Downloading is possible from our home page [http://www.hds.co.jp/])
Backup battery ABS (optional): HAB-ER17/33
(attached to the shipped driver)
Isolation single phase transformer (optional):
HA-675-2A-200
AC servo driver HAseries
675 series
Nominal current
2
2.4 A
4
4 A
Input voltage
Encoder
No
code
Incremental encoder INC
A
Absolute encoder ABS
1
1 A
200
200V
100
100V
See Note 1.

Chapter 1 Outlines of HA-675 driver
HA-675_V3_03 - 3 -
1-3 Combinations with actuators
Five HA-675 models are available for use with FHA-C actuators dealing with their nominal current and
encoder systems. The correct combinations are as follows:
Model
Volt.
Incremental system INC
Absolute system ABS
HA-675-1-200
HA-675-2-200
HA-675-4-200
HA-675-2A-200
HA-675-4A-200
200V
FHA-8C-xx-E200
FHA-11C-xx-E200
FHA-14C-xx-E200
FHA-17C-xx-E250
FHA-25C-xx-E250
FHA-32C-xx-E250
FHA-40C-xx-E250
FHA-17C-xx-S248
FHA-25C-xx-S248
FHA-32C-xx-S248
FHA-40C-xx-S248
Model
Volt.
Incremental system INC
Absolute system ABS
HA-675-1-100
HA-675-2-100
HA-675-4-100
HA-675-4A-100
HA-675-4A-100
100V
FHA-8C-xx-E200-A
FHA-11C-xx-E200-A
FHA-14C-xx-E200-A
FHA-17C-xx-E250-A
FHA-25C-xx-E250-A
FHA-32C-xx-E250-A
FHA-17C-xx-S248-A
FHA-25C-xx-S248-A
FHA-32C-xx-S248-A
1-4 Specifications of HA-675 driver
Model
Power supply: 200V
Power supply: 100V
Incremental INC
HA-675-1-200
HA-675-2-200
HA-675-4-200
HA-675-1-100
HA-675-2-100
HA-675-4-100
Absolute ABS
-
HA-675-2A-200
HA-675-4A-200
-
HA-675-2A-100
HA-675-4A-100
Driver’s nominal current
1.0 A
2.4 A
4.0 A
1.0 A
2.4 A
4.0 A
Driver’s maximum current
3.2 A
7.3 A
18.0 A
3.2 A
7.3 A
18.0 A
Power
supply
Main circuit
AC200 to 240V(1 / 3-phase) +10 to -15%
AC100 to115V(1-phase)+10 to -15%
Control circuit
AC 100 to 115V or AC200 to 240V(1-phase)
+10 to -15%
AC100 to 115V(1-phase)+10 to -15%
Power frequency
50/60Hz
Applicable position sensor
Incremental
Incremental or absolute
Incremental
Incremental or absolute
Allowed revolution (motor)
No limits
INC
+4095 to -4046
ABS
No limits
INC
+4095 to -4046 ABS
Power Control Method
Sinusoidal PWM control Switching function: 12KHz
Control mode
Uniaxial positioning
Allowed Environment
Operating temperature: 0 to 50C Storage temperature:-20 to 85C
Operating/storage humidity: below 95%RH (No condensation)
Vibration resistance: 4.9 m/s2(10 to 55Hz) Impact resistance: 98m/s2
Atmosphere: metal powder, dust, oil mist and corrosive gas are not allowed.
Ventilation
Self cooling
Installation
Base mount (Wall mount)
Encoder interface
Serial transmission line driver input type
Input signal
Clear, Servo-ON, Originating, Interlocking, Start, Stop,Addressing, Emergency stop,
Origin signal, FWD-limit, REV-limit, ABS position date request, ABS revolution counter clear
(Every signal is insulated by opt-isolators.)
Output signal
Ready, Motion finish, Originated,Alarm,Alarm code (4-bit), Current address
(Every signal is insulated by opt-isolators.)
Position signal output
ABS absolute data, Phase-A, -B, -Z; line driver output
Analog monitor
2ch: motor speed, current command
Front panel
Configuration
Display: 7-segment LED 6 digits (red)
Operation key: 4 keys
Monitor function
Motor speed (r/min), torque monitor (%), over load rate (%), error pulse, feedback pulse,
Input signal monitor, output signal monitor, alarm history (up to 8 alarms )
Parameters
System parameters Tune parameters
Protection function
Emergency stop inputs, FWD and REV limits, Over current, Overload, Over voltage,
Error counter overflow, Over speed, Regenerative failure/main power voltage failure, Encoder
failure, CPU failure, Memory failure, ABS revolution data error, ABS encoder system failure,
ABS encoder overflow, ABS battery low voltage, ABS absolute data transmitting rule error
Regeneration
By external
resister
Built-in resister (power: 40W Max)
External resistor is acceptable.
By external
resister
Built-in resister (power: 40W Max)
External resistor is acceptable.
Functions
Monitoring, Self diagnosis, JOG operation, Trapezoidal speed profile, S-curve speed profile,
Compound speed profile, Indexing, ABS backup battery for revolution counter
Parameter
Motor parameter, system parameter, tune parameter
Rush current suppressing
Rush current suppressing circuit is built-in
Operation mode
Monitor mode (for usual operations), Test mode, Tune mode, Parameter mode
Mass
1.5 kg
1.5 kg
1.7 kg
1.5 kg
1.5 kg
1.7 kg
Note: The specifications marked with (ABS) are valid for absolute systems only, with (INC) are for incremental
systems only, and specifications with no marks are valid for both systems.

Chapter 1 Outlines of HA-675 driver
HA-675_V3_03 - 4 -
1-5 External drawing of the HA-675 drivers
The external drawing is shown as follows: Unit: mm (Third angle projection method)
Note 1: When HA-675 drivers are installed in a cabinet, leave enough ventilation space as shown
below.
The dimensions marked with “※”
are applied for HA-675-4A only.
Heat sink
Ventilation holes
Base dimensions
Battery room
Name plate

Chapter 1 Outlines of HA-675 driver
HA-675_V3_03 - 5 -
1-6 Front panel
Names of front panel blocks
Functions
◆LED display
This indicates operating the HA-675 driver states, parameter values, alarms, by a 6-digit
7-segment-LED.
◆[UP],[DOWN],[ADJ],[SET] keys
These keys are used for changing indications, setting and tuning functional parameter values, and
manual JOG operation of actuators.
◆CN1: encoder connector
The connector accepts encoder cable connector.
◆CN2: I/O connector
This accepts I/O signals to/from host devices.
◆CN3: Serial port connector (compliant with the EIA-232C standard)
This is a connector with the teach box TBX-670 or the PC.
◆Power supply terminals: r, s, R, S, T
These terminals are provided for connecting the power supply. Control power is connected to [r,s]
terminals, and main power is connected to [R,S,T] terminals. (R,S –Single Phase; R,S,T –Three
Phase).
◆External regeneration resistor terminals: R1,R2
If the built-in regeneration resistor is insufficient in its capacity to handle frequent start/stop operations
of the actuator, an external resistor can be connected to these terminals.
◆Actuator terminals: U,V,W
An actuator cable is connected to the terminals. Connect the motor wires to the driver’s terminal have
the same symbols as the wire’s. If you confuse the symbols, the driver and the actuator may fail.
◆Ground terminals
Connect grounds here to prevent electrical shock.
HA-675-2
LED display
ADJ key
SET key
CN3: Serial port connector
(Teach-box connector)
CN2: I/O connector
CN1: Encoder connector
DOWN key
UP key
For control power: r,s
For main power: R,S,T
For regeneration resistor: R1,R2
For actuator: U,V,W
Ground terminals
Power supply terminal
Cover of battery room

Chapter 1 Outlines of HA-675 driver
HA-675_V3_03 - 6 -
1-7 Outlines of I/O ports
The CN2 connector provides input and output signals to and from the host devices. The 50 pins of the
connector are assigned to the following signals. Do not connect signals to pins marked “-“.
Pin No.
Signal
Symbol
I/O
Pin No.
Signal
Symbol
I/O
1
Input signal common
INPUT-COM
Input
26
+24V
+24V
Input
2
Clear
CLEAR
Input
27
-
-
-
3
Servo-ON
S-ON
Input
28
ABS Position data request
ABS-REQ
Input
4
Originating
ST-ORG
Input
29
-
-
-
5
Interlock
INTERLOCK
Input
30
ABS
Revolution counter clear
ABS-CLEAR
Input
6
Start
START
Input
31
-
-
-
7
Stop
STOP
Input
32
-
-
-
8
Input signal common
INPUT-COM
Input
33
Ready
READY
Output
9
Input bit 1
INPUT DATA 1
Input
34
Motion finish
FINISH
Output
10
Input bit 2
INPUT DATA 2
Input
35
At-origin
ORG-END
Output
11
Input bit 4
INPUT DATA 4
Input
36
Alarm
ALARM
Output
12
Input bit 8
INPUT DATA 8
Input
37
Output bit 1
OUT-DATA 1
Output
13
Input bit 16
INPUT DATA 16
Input
38
Output bit 2
OUT-DATA 2
Output
14
Input bit 32
INPUT DATA 32
Input
39
Output bit 4
OUT-DATA 4
Output
15
Emergency stop+
ESTOP+
Input
40
Output bit 8
OUT-DATA 8
Output
16
Emergency stop-
ESTOP-
Input
41
Output bit 16
OUT-DATA 16
Output
17
FWD limit+
FSTOP+
Input
42
Output bit 32
OUT-DATA 32
Output
18
FWD limit-
FSTOP-
Input
43
Output common
OUT-COM
Output
19
REV limit+
RSTOP+
Input
44
Phase-A+(LD)
A+
Output
20
REV limit-
RSTOP-
Input
45
Phase-A-(LD)
A-
Output
21
Origin+
ORG+
Input
46
Phase-B+(LD)
B+
Output
22
Origin-
ORG-
Input
47
Phase-B-(LD)
B-
Output
23
Speed monitor
SPD-MON
Output
48
Phase-Z+(LD)
Z+
Output
24
Current monitor
CUR-MON
Output
49
Phase-Z-(LD)
Z-
Output
25
Monitor Ground
GND
Output
50
Ground
FG
Output
Note 1: The pins marked with “ABS”(pin 28 & 30) are dedicated for absolute systems. Do not use them
for incremental systems.
Note 2: OC: open collector port, LD: line driver port
Note 3: Do not use the pins marked “-”. Using these pins may cause failure of interior circuitry.
Note 4: The [pin 38 to 41] output 4-bit alarm codes at an alarm state.

Chapter 1 Outlines of HA-675 driver
HA-675_V3_03 - 7 -
1-8 Operating display panel
The HA-675 driver provides a 6-digit LED display and four operation keys on the front panel. The
panel executes monitoring, tuning, setting, and JOG operation.
1-8-1 Outlines of operation modes
The HA-675 driver provides the following four modes: monitoring, tuning, setting, and operations.
◆Monitor mode
The HA-675 driver displays a current address number, motor speed, current position from a
motor-encoder, pulse count in an error counter, input and output signal states, load condition, alarm
history, and the code number for the actuator for which the driver is set. These are useful to diagnose
the driver if it fails or operates in an abnormal manner.
After applying power the [monitor mode] starts up. While the power is on, from the [monitor mode] as
the main screen it is possible to switch to and from other modes.
◆Tune mode
The [tuning mode] consists of various parameters to control the actuator motion. Setting the most
suitable value for each parameter obtains the optimum performance of the actuator.
◆Parameter mode
The [parameter mode] sets various parameter values relating to the fundamental operational functions
such as: limiting values of speed and torque, and parameters to communicate with a teach-box.
For the absolute system, the revolution counter is possible to be cleared in the parameter mode.
◆Test mode
The [test mode] consists of required functions for system test; such as JOG operation functions,
operations of pseudo output signals, and I/O signal monitors.
1-8-2 Selecting a mode
The figure shown below is an outline of mode selecting procedures. After turning on the driver the
[monitor mode] starts up automatically. The [ADJ] and [SET] keys select a mode.
Powering with pressing both [ADJ] and [SET] keys in same time jumps to the monitor mode followed
by leaving the fingers from the buttons. When an alarm occurs, the LED display converts to indicate
the alarm automatically, and no operations on the panel become impossible. For clearing the
revolution counter of the absolute system, the powering operation may be useful.
Powering
Monitor mode
Parameter mode
Tune mode
Test mode
ADJ
3 sec.
3 sec.
ADJ
SET
SET
3 sec.
SET
ADJ
SET
Powering

Chapter 1 Outlines of HA-675 driver
HA-675_V3_03 - 8 -
1-8-3 Functions of each mode
Each mode provides the following functions:
Mode
Code
Function
Setting & operation
Monitor mode
0
Current address
Setting is impossible.
1
Motor speed
3
Error pulse count (Low)
4
Error pulse count (High)
5
Torque monitor
6
Overload rate
7
Feedback pulse (Low)
8
Feedback pulse (High)
c
I/O monitor
d1 to d8
Alarm history
E
Actuator code
F
Connection actuator serial number (Low)
G
Connection actuator serial number (High)
H
Connection actuator serial number (Affix)
Tune mode
0
Speed loop gain
Setting is possible.
1
Speed loop integral compensation
2
Position loop gain
3
Reserved (out of use)
4
In-position range
Setting is possible.
A
Speed monitor offset
b
Current monitor offset
Parameter mode
5
Error count clear by Servo-ON
Setting is possible.
6
Position error allowance
A
Speed limit
b
Current limit
c
Signal logic
For J
ABS Revolution counter clear
Operation is possible
G
Mechanical origin
Setting is possible
H
ABS Send data timing
I
ABS Low battery voltage signal
n
Regenerative resistance
o
Automatic gain control
P
Alarm history clear
Test mode
Jo
JOG operation
Operation is possible
SP
JOG speed
Setting is possible.
Ac
JOG acceleration
rdy
Output port operation
Operation is possible
c
I/O port monitor
Setting is impossible.
An
Analog monitor manual output
Operation is possible
Note: The parameters marked with (ABS) are valid for absolute systems only, and parameters with no
marks are valid for both absolute and incremental systems.
1-9 Teach-box
1-9-1 Specifications of the teach-box
Model
TBX-670
Display
LCD, 4 lines by 20 digits
Operation key
5 rows by 8 lines and 4 keys
Emergency stop switch
Mushroom push-lock switch
Operation mode
Parameter mode, Program mode, Test mode
Max. number of address
64 addresses
Programmable functions
Originating, Shortcut motion, Indexing, Jump, Repeat, S-curve acceleration
profile, Software origin
Motion pattern
Individual positioning, Sequential positioning, Programmed positioning
Displacement and position unit
Pulse, Angle (1/1000), metric (1/100mm)
Speed unit
Pulse/sec, r/min
Allowed Environment
Service temperature/ storage temperature: 0 to 40℃/-20 to 60℃
Service/storage humidity: below 95%RH (No condensation)
Vibration resistance/impact resistance: 4.9 m/s2(10 to 55Hz)/ 98m/s2
External dimensions
200×87×25.5 mm
Mass
290 g

Chapter 1 Outlines of HA-675 driver
HA-675_V3_03 - 9 -
1-9-2 External drawing of the teach-box
The external drawing is shown as follows: Unit: mm (Third angle projection method)
It is possible to add a commercially available EIA-232C (RS-232C) cable to extend the 2-meter
teach-box cable. The extension cable should be less than 3 meters.
Recommended commercially available cable:
Classification: Straight fully-connected EIA-232C cable
Specification: D-sub 9pin female (inch screw) - D-sub 9pin male (inch nut)
Length: Less than 3 meters
S O N
E S T P
D E N B
ABSREQ
ABSCLR
120 (MAX)
50 (MAX)
27
235 (MAX)
201
L=2000

Chapter 1 Outlines of HA-675 driver
HA-675_V3_03 - 10 -
1-9-3 Main blocks of the teach-box panel
The teach-box panel consists of four blocks as follows:
The operating data can be set in the following unit.
Rotation unit: pulse/second, 1/100 r/min
Transfer unit: pulse, angle (1/1000), Distance (1/100mm)
◆LCD display
The LCD display indicates all information with alphanumeric letters with four lines by 20 digits.
Upper three lines indicate commands and data, and the lowest line indicates the operation mode, the
unit of the data and the address.
◆Mode LEDs
Three red LEDs indicate the current operation mode.
Left: Program mode
Center: Test mode
Right: Parameter mode
◆Operation keys
All programs are created with forty-four keys of 5 rows by 8 lines and 4. On the key faces, instruction
codes and numerals for operation are marked. Each code on a key face is same as the indicating
code. The details of the codes are described on the next chapter.
◆Emergency stop switch
The red mushroom switch is provided for emergency stop operation. Pressing the switch turns the
state of the HA-675 driver to the same state of signal inputting (OFF) to [CN2-15, -16: emergency
stop].
To recover from the emergency stop state, turn the switch to right (clockwise) to release the
emergency signal, and input [ON] signal to [CN2-2: clear] or regenerate the HA-675 driver.
LCD display
Emergency stop switch
Mode LED
Operation keys
SON
ESTP
DENB
ABSREQ
ABSCLR

Chapter 1 Outlines of HA-675 driver
HA-675_V3_03 - 11 -
1-9-4 Operation keys
The teach-box provides three operation modes: [program], [test] and [parameter]. The functions of a
key are different by the modes. The relation between keys and functions are as follows:
Key
Operation mode
Program mode
Test mode
Parameter mode
MODE
Specifies a mode from program, test, and parameter modes. Every pressing shifts the mode
cyclically like program⇒test⇒parameter⇒program⇒…The LCD display or the LED indications
indicate the current mode.
Program mode: DSET; Left LED
Test mode: TEST; Center LED
Parameter mode: PSET; Right LED
START
Starts the programmed actuator
motion at the displaying
address.
Starts the actuators motion in
parameter specified mode.
OPM-0: individual positioning
OPM-1: sequential positioning
OPM-2: programmed motion
ORG
The actuator starts for the origin. The originating speed and acceleration are set by [RSP:
originating speed 1] [RS2: originating speed 2] [RAD: originating accelerating time] of [parameter
mode].
Keeping the key pressing for 1 second or more sets the current position as the origin (incremental
encoder only). When the origin is set by this way, make the actuator free in rotation.
STOP
Stops the actuator.
ERASE
ALL
Pressing this key after [ENTER]
erases all command data in the
HA-675 driver. To cancel the
erasing after pressing the key,
press [CANCEL].
←CCW
CW→
Both keys adjust the position
precisely.
Moves the actuator by JOG
operation.
Both keys adjust the software
origin precisely.
SON
This turns the motor drive circuit for the HA-675 driver ON and
OFF. For the absolute system and the [system parameter] →[H:
data send timing] is set [0], transmitting the position data to a host
is required before turning on the servo power.
ESTP
DENB
Before disconnecting the teach-box from the HA-675 driver, it is required to press the
[ESTOP-DENB] and [ENTER] keys in the order. Without the operation, disconnecting the teach-box
causes the [alarm 01: emergency stop].
ABS
ABSREQ
[System parameter]→When the value of [H: data transmission timing] is “0”, operating this button
outputs the position data to “CN2- 44~49: A,B,Z phase output”. This operation is valid only once after
the power is turned on for HA-675.
ABS
ABSCLR
At the first power supplying after connecting with a FHA-C actuator or at events of alarms [Alarm53:
ABS system failure], [Alarm54: revolution counter overflow] and [Alarm55: revolution count error], the
key clears the revolution counter by pressing the key for around five seconds until making pee
sound. The operation is ignored during the servo power is active.
Careful attentions are required to the operation, because the absolute encoder loses position data by
the operation.
SPD
Sets actuator speed.
SLP
Sets acceleration time.
TIM
Delay time until the actuator
sends an operation completion
signal after the positioning
completion
JMP
Sets an address to jump.
NOP
No operation.

Chapter 1 Outlines of HA-675 driver
HA-675_V3_03 - 12 -
Key
Mode
Program mode
Test mode
Parameter mode
POS
INC increments,
ABS positions
CHP
Sets a speed changing position.
DIV
Divides equally a positional value of
POS command.
LOP
Repeats the motion from specified address
to the preceding address having LOP.
END
End of a motion program.
ABS
Indicates position by the absolute
system.
INC
Indicates position by the incremental
system.
INS
Inserts an address.
DATA
NO
Specifies an address.
Specifies an address when
[individual positioning] is
specified.
DEL
Pressing [ENTER] key after this [DEL]
key erases the command data at
indicating address.
To cancel the erasing operation after
pressing [DEL] key, press [CANCEL] key.
CANCEL
Cancels preceding operation.
0 to 9
Input numerals.
↑
NEXT
Steps forward by an address.
Steps forward by an
address when [individual
positioning] is specified.
↓
BACK
Steps backward by an address.
Steps backward by an
address when [individual
positioning] is specified.
↑↓
These [cursor keys] scrolls indications.
___
(CLR)
This works as the minus key or clears a
command.
Pressing [ENTER] key after this key
erases the command data under the
cursor.
To cancel the operation after pressing the
key, press [CANCEL] key.
ENTER
Defines command inputting, inserting
and erasing operation. While an
address and command data are
indicating, pressing this key stores the
data in the EEPROM of the HA-675
driver.
Note 1: Key operation except [STOP] key is ignored while the actuator is moving.
Note 2: Press keys one by one steadily. Pressing two or more keys may indicate “Over-run Error”on
the teach box, because of impossibility for processing, and key operations are ignored.
Note 3: Symbol INC and ABS indicates the methods for increments of the position command.
INC indicates the increments (relative position command) based on the current position.
ABS indicates the positions based on the command of the pre-allocated position (absolute
position).

Chapter 1 Outlines of HA-675 driver
HA-675_V3_03 - 13 -
1-9-5 Operation modes
Three modes are provided for teach-box operation as follows:
◆Program mode
In the mode you can create motion programs using commands of position, speed, acceleration time,
delay time, jump, indexing, repeat and so on.
◆Test mode
In the test mode you can verify the programs created in the program mode. It is possible to confirm
positions, to observe sequential motions at every address, and to test programs continuously.
◆Parameter mode
The mode allows setting parameters required for originating, units of speed and position, acceleration
profiles, an offset for backlash, a ball-screw lead, and availability of the shortcut motion.
The modes provide the following commands:
Mode
Command
Function
Default
Unit
Possible values
Program mode
SPD
Speed
p/s
1/100 r/min
pps: 500 to 1,000,000
The equivalent converted in p/s
POS
INC increments,
ABS positions
pulse
1/100mm
1/1000°
-2,000,000 to +2,000,000
The equivalent converted in p/s
-360,000 to +360,000
CHP
Speed changing position
pulse
1/100mm
1/1000°
-2,000,000 to +2,000,000
The equivalent converted in p/s
-360,000 to +360,000
SLP
Acceleration time
0.01 s
0 to 1000
DIV
Indexing
0 to 200
TIM
Delay time
0.01 s
0 to 9999
JMP
Jump
0 to 63
LOP
Repeat cycle
Number of repeat is 01 to 99.
NOP
No operation
END
End of motion
Parameter mode
ASP
Acceleration profile
0
0: Linear acceleration
1: S-curve acceleration
BLR
Backlash offset
0
pulse
0 to 9999
OPM
Motion profile
0
0: individual positioning
1: sequential positioning
2: programmed motion
RED
Ball screw lead
0
Code
0 to 19
MQU
Position unit
0
0: pulse
1: 1/1000°angular unit
2: 1/100mm
SPU
Speed unit
0
0: p/s
1: 1/100 r/min
RTD
Originating direction
0
0: CW viewed from output
1: CCW viewed from output
RS2
Originating speed 2
20,000
p/s
1/100 r/min
500 to 50,000
The equivalent converted in p/s
NRT
Software origin
0
pulse
-9999 to +9999
RAD
Originating acceleration
time
10
0.01 sec
0 to 1000
RSP
Originating speed 1
200,000
p/s
1/100 r/min
500 to 1,000,000
The equivalent converted in p/s
SCD
Pulse per revolution
Varies in
actuators
pulse
1000 to 9,999,999
SHC
Shortcut motion
0
0: unavailable
1: available
Note: Speeds and angles in above table are applied to output of actuators.

Chapter 1 Outlines of HA-675 driver
HA-675_V3_03 - 14 -
1-10 Outlines of protection functions
1-10-1 Alarms
HA-675 drivers provide various functions to protect actuators and drivers from the occurrence of
abnormalities. When a function detect faults, the actuator enters a free rotation state, a two-digit alarm
code is indicated on the display, and a set of 4-bit alarm signals is transmitted to the host.
[Monitor mode] →[d: alarm history] allows to check up to eight previous recorded alarms.
alarm
code
Alarm description
4-bit
code
CN2-41
CN2-40
CN2-39
CN2-38
alarm clear
01
Emergency stop
0011
OFF
OFF
ON
ON
Possible
02
FWD limit
0011
OFF
OFF
ON
ON
Possible
03
REV limit
0011
OFF
OFF
ON
ON
Possible
04
Programming error
0011
OFF
OFF
ON
ON
Possible
10
Over speed
1011
ON
OFF
ON
ON
Impossible
20
Over load
0001
OFF
OFF
OFF
ON
Possible
30
Over current
1001
ON
OFF
OFF
ON
Impossible
40
Over voltage
1011
ON
OFF
ON
ON
Impossible
41
Regenerative failure/main power
voltage failure
1010
ON
OFF
ON
OFF
Impossible
50
Encoder failure
1101
ON
ON
OFF
ON
Impossible
51
Abnormal encoder signal
1101
ON
ON
OFF
ON
Impossible
52
INC UVW failure
1101
ON
ON
OFF
ON
Impossible
53
ABS System failure
1101
ON
ON
OFF
ON
Impossible
54
ABS Revolution counter overflow
1101
ON
ON
OFF
ON
Impossible
55
ABS Revolution count error
1101
ON
ON
OFF
ON
Impossible
56
ABS Low battery voltage
1101
ON
ON
OFF
ON
Auto recov.
57
ABS Send data rule error
1101
ON
ON
OFF
ON
Impossible
60
Error counter overflow
0010
OFF
OFF
ON
OFF
Possible
70
Memory failure (RAM)
0101
OFF
ON
OFF
ON
Impossible
71
Memory failure (EEPROM)
0101
OFF
ON
OFF
ON
Impossible
76 or
Flickering [0]
CPU failure
0100
OFF
ON
OFF
OFF
Impossible
Note 1: The INC 52 is valid for incremental system only, and the ABS 53 through 57 are valid for
absolute system. Other codes are valid for both incremental and absolute systems.
Note 2: The lower code is displayed for plural alarms.
Note 3: When [alarm 56: low battery voltage] occurs, the servo power supply does not turn off. If
[parameter mode]→[I: low battery alarm] is set [1: no output], the alarm is indicated on the
LED display, but no alarm signals including 4-bit codes are transmitted to the host.
Note4: Flickering [0] means CPU failure.
Note 5: After troubleshooting the alarm of [alarm clear: impossible], turn the power off. And then, turn it
on again by following the sequence procedure.
This manual suits for next models
9
Table of contents
Other Harmonic Drive Servo Drive manuals
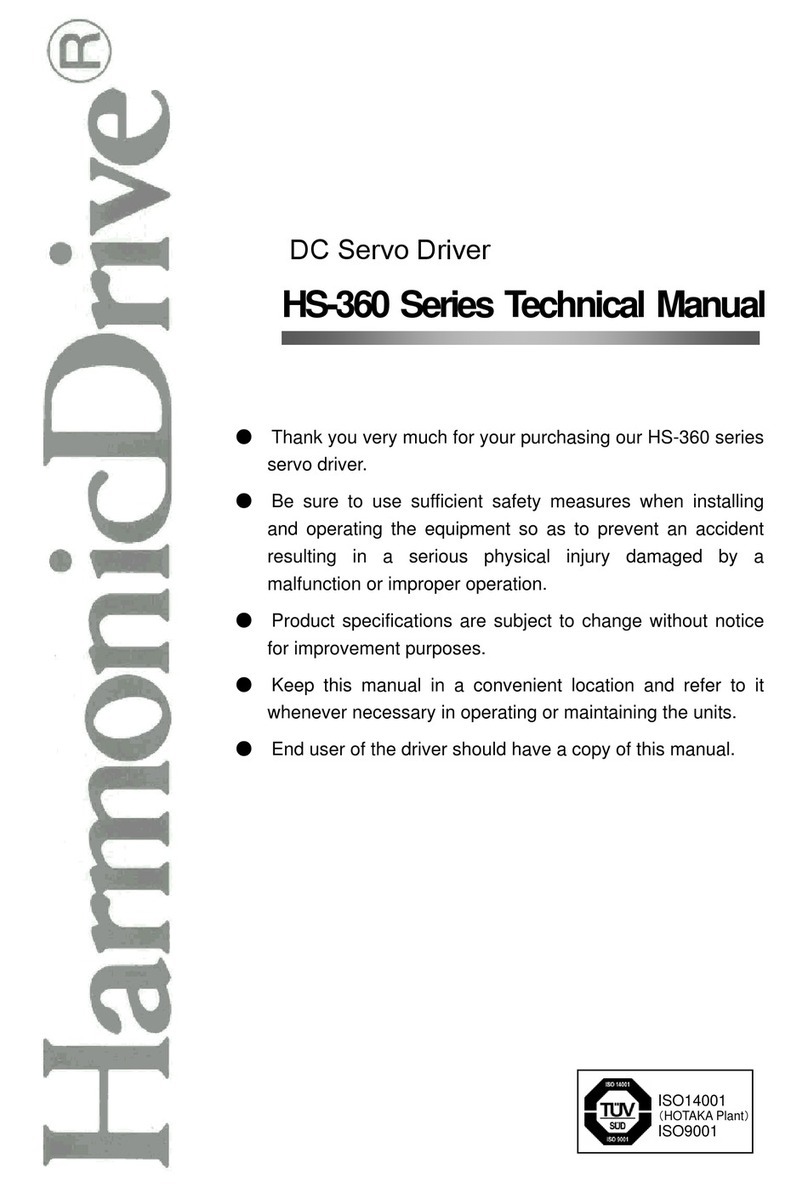
Harmonic Drive
Harmonic Drive HS-360 Series User manual
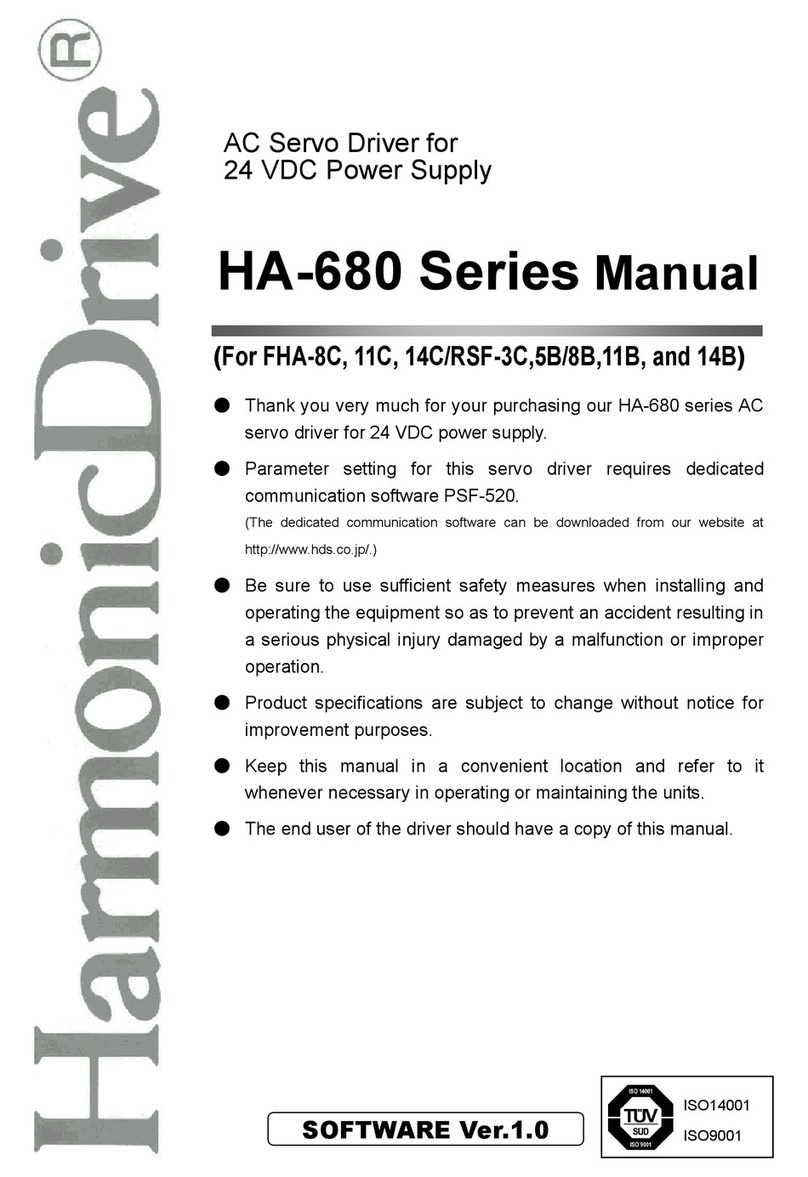
Harmonic Drive
Harmonic Drive HA-680 Series User manual
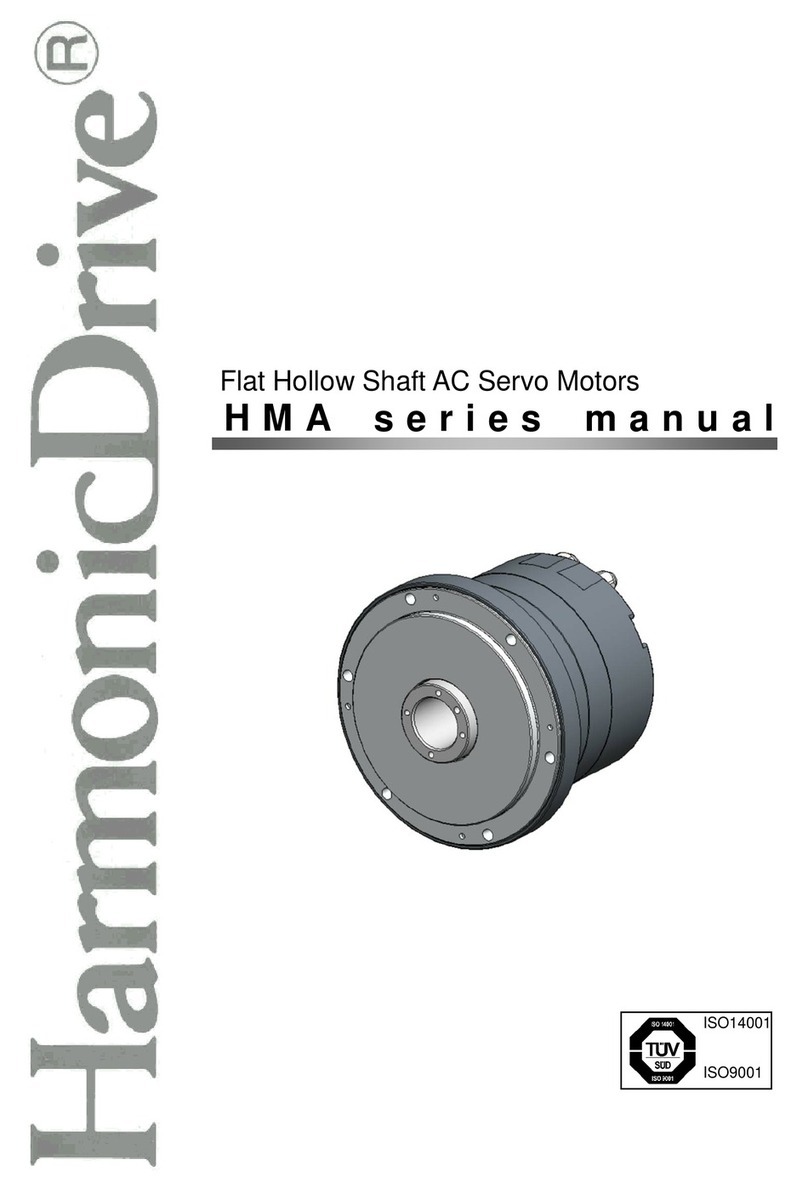
Harmonic Drive
Harmonic Drive HMA Series User manual

Harmonic Drive
Harmonic Drive LAH Series User manual
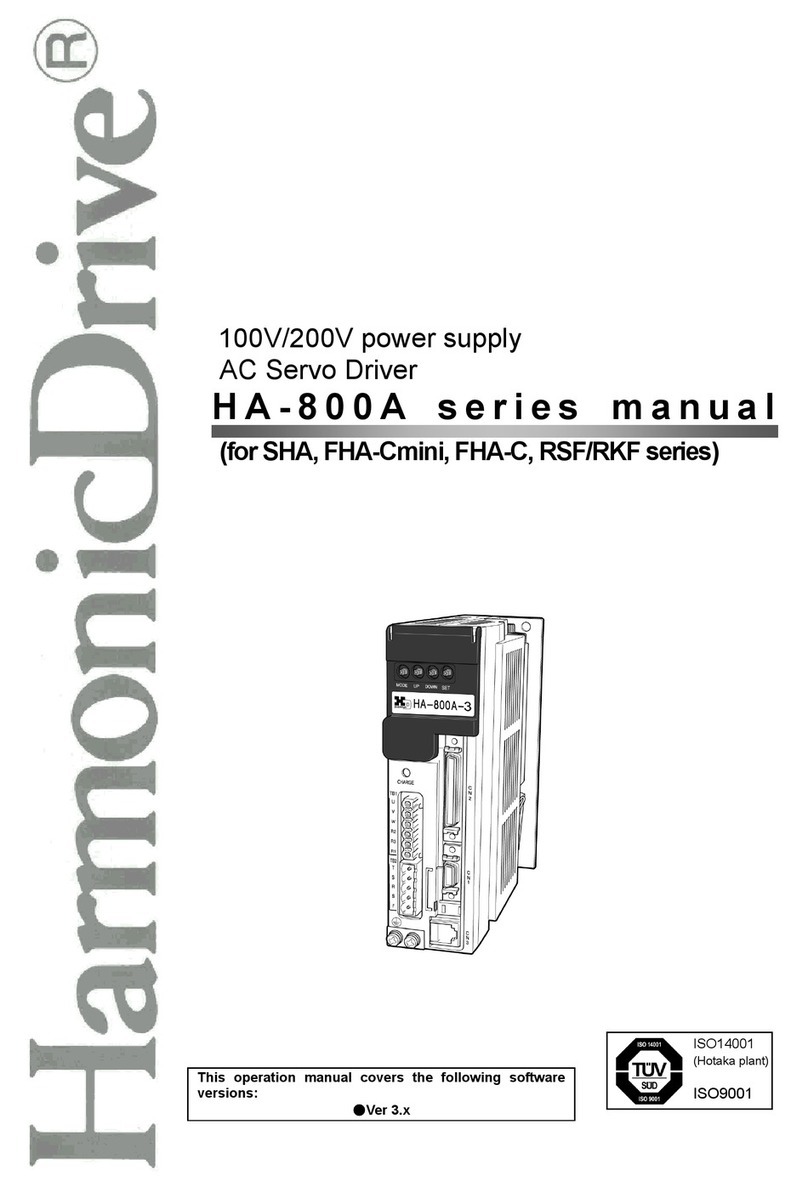
Harmonic Drive
Harmonic Drive H A - 800A User manual

Harmonic Drive
Harmonic Drive HA-520 Series User manual
Popular Servo Drive manuals by other brands

SEW-Eurodrive
SEW-Eurodrive CMP Series Addendum to the operating instructions
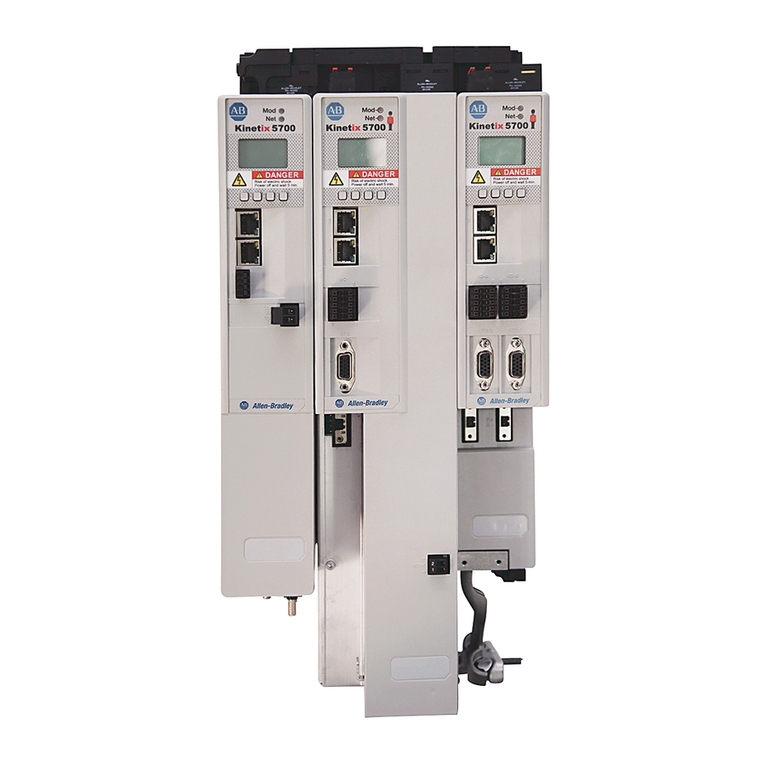
Allen-Bradley
Allen-Bradley Kinetix 5700 quick start guide
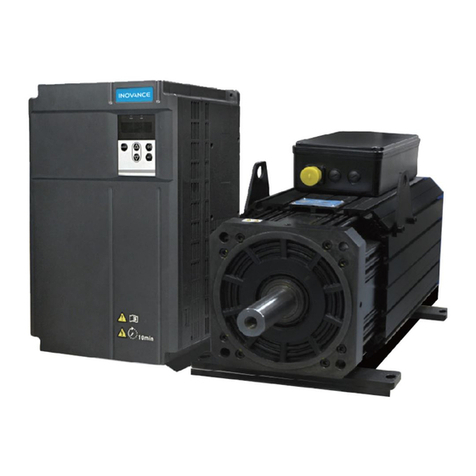
Inovance
Inovance IS650P Series user guide
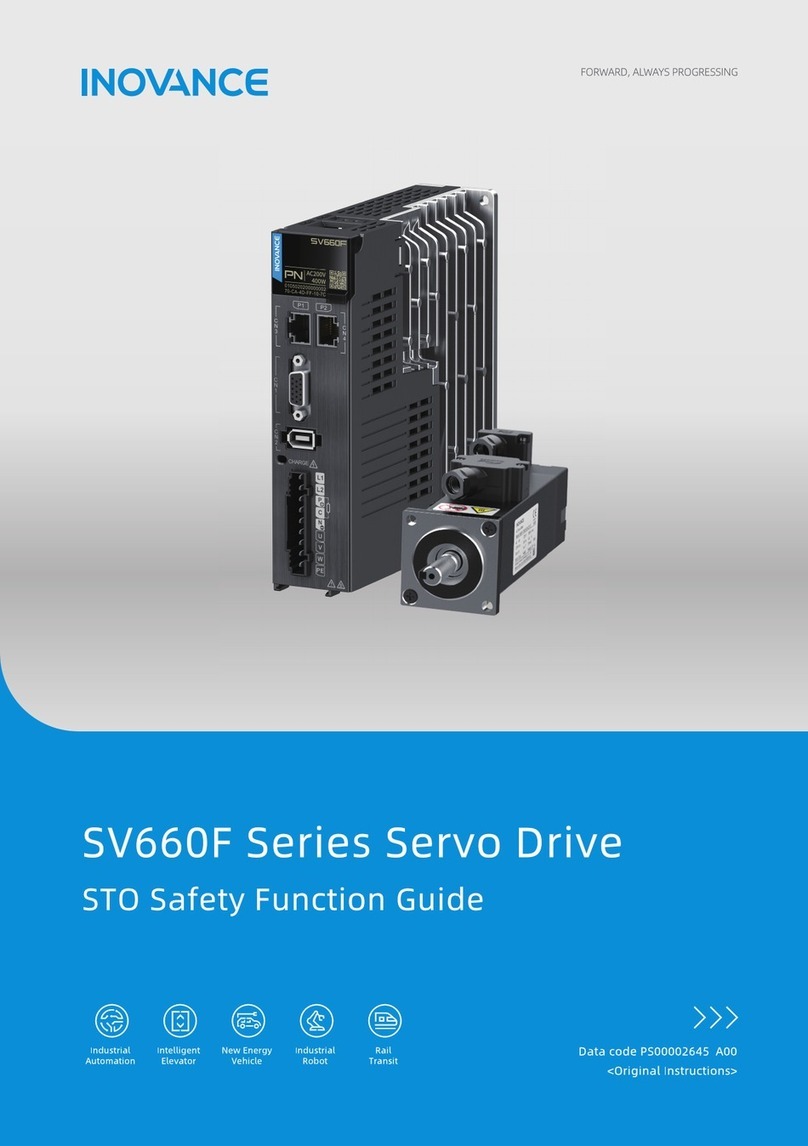
Inovance
Inovance SV660F Series Safety function Guide
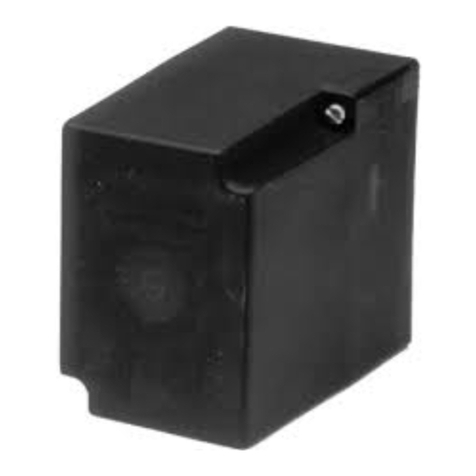
Fireye
Fireye NEXUS NX04-1 Installation
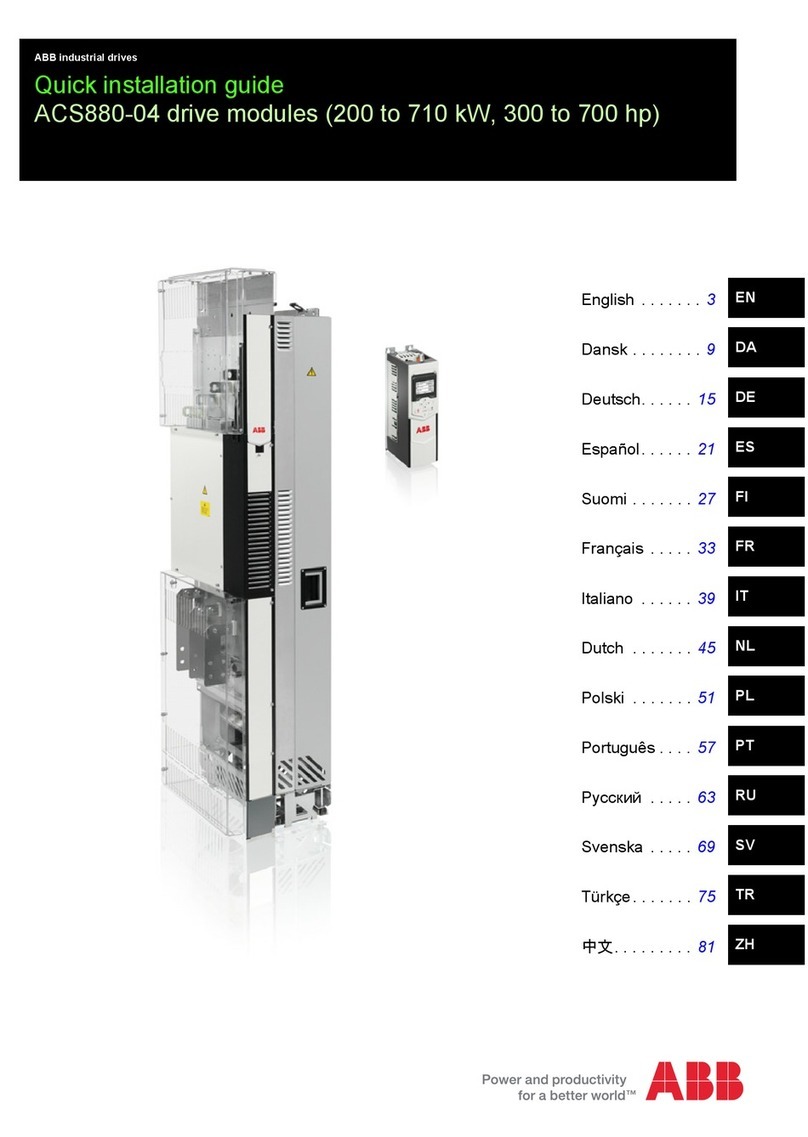
ABB
ABB ACS880-04 drive modules Quick installation guide