Xinje DF3E Series User manual

- 1 -
DF3E series servo driver
User manual
Wuxi Xinje Electric Co., Ltd.
Data No. SF3 01 20210607 1.0

- 2 -
Basic explanation
⚫Thank you for purchasing Xinje DF3E series servo driver products.
⚫This manual mainly introduces the product information of DF3E series servo driver and MF series servo
motor.
⚫Before using the product, please read this manual carefully and connect the wires on the premise of fully
understanding the contents of the manual.
⚫Please deliver this manual to the end user.
This manual is suitable for the following users
⚫Designer of servo system
⚫Installation and wiring workers
⚫Commissioning and servo debugging workers
⚫Maintenance and inspection workers
Get the manual
⚫Please consult the supplier, agent and office who purchased the product.
Declaration of liability
⚫Although the contents of the manual have been carefully checked, errors are inevitable, and we cannot
guarantee complete consistency.
⚫We will often check the contents of the manual and make corrections in the subsequent versions. We
welcome your valuable comments.
⚫If there is any change to the contents introduced in the manual, please understand without further notice.
Contact information
⚫Tel: 400-885-0136
⚫Fax: 0510-85111290
⚫Address: Floor 4, building 7, creative industry park, No. 100, DiCui Road, Wuxi City
⚫Postcode: 214072
WUXI XINJE ELECTRIC CO., LTD. Copyright
Without explicit written permission, this material and its contents shall not be copied, transmitted
or used, and the violator shall be liable for the losses caused. All rights provided in the patent
license and registration including utility module or design are reserved. Jan. 2019

- 3 -
The problems that may arise during the use of the product are basically listed in the safety precautions, and all are
indicated by the two levels of attention and danger. For other unmentioned matters, please follow the basic
electrical operation rules.
Caution
When used incorrectly, there may be danger, moderate injury or minor injury, and
property loss.
Danger
When used incorrectly, it may cause danger, personal casualties or serious injuries,
as well as serious property losses.
Attention to Product Confirmation
1.Do not install damaged drives, drives that lack spare parts, or drives whose models do not meet the
requirements.
Installation Notes
1. Before installing wiring, be sure to disconnect the power supply to prevent electric shock.
2. It is forbidden to expose the product to water, corrosive gases, flammable gases and other
substances, causing electric shock and fire hazards.
3. Do not touch the conductive part of the product directly, which may cause misoperation and
malfunction.
Cautions for wiring
1. Please connect AC power to LN or L1/L2/L3 or R/S/T on the dedicated power terminal of the
driver. Do not connect the output terminals U, V, W of the driver to the three-phase power supply.
2. Please connect the ground wire correctly. Poor grounding may cause electric shock. Please use
2mm2wire to ground the ground terminal of the driver.
3. Please lock the fixed screw of the terminal, otherwise it may cause fire.
4. Be sure to disconnect all external power supply before wiring the driver.
Before using this product, please read this part carefully and operate after fully understanding
the use, safety and precautions of the product. Please connect the product correctly on the
premise of paying great attention to safety.
Be sure to review this section carefully before use this product. In precondition of security, wire
the product correctly.
Safety Precautions
PrePrecaPrecautio
ns

- 4 -
5. Wiring, please ensure that the encode line, power line is loose, do not tighten, lest cable damage.
Operation Cautions
1. Do not touch the rotating part of the motor after the driver is running. There is a danger of injury.
2. Please pay attention to the test run of the motor once, do not connect the motor with the machine,
there is the possibility of injury.
3. After connecting the machine, please set the appropriate parameters before running, otherwise it
may cause the machine out of control or failure.
4. In operation, do not touch the radiator, there is a risk of scald.
5. Under power-on condition, do not change the wiring, there is a risk of injury.
6. Do not switch power frequently. If you need to switch power many times, please control it once in 2
minutes.
Maintenance and inspection
1. Do not touch the inside of servo driver and servo motor, otherwise it may cause electric shock.
2. When the power is started, it is forbidden to remove the driver panel, otherwise it may cause electric
shock.
3. Within 10 minutes of power off, the terminal should not be contacted. Otherwise, the residual
voltage may cause electric shock.
Wiring attention
1. Do not cross the power line and the control signal line from the same pipeline, nor tie them together.
The power line and the control signal line are separated by more than 30 centimeters.
2. For signal line and encoder (PG) feedback line, please use multi-stranded wire and multi-core
stranded integral shielding line. For wiring length, the longest signal input line is 3 meters and the
longest PG feedback line is 20 meters.

- 5 -
Catalog
►► CONFIRMATION ON PRODUCT ARRIVAL ·········································································· 1
1 SELECTION OF SERVO SYSTEM ···························································································· 1
1.1 SELECTION OF SERVO DRIVER··································································································· 1
1.1.1 Model name ························································································································································1
1.1.2 Description of each part·····································································································································1
1.1.3 Performance specification··································································································································2
1.2 SERVO MOTOR SELECTION······································································································· 3
1.2.1 Model name ························································································································································3
1.2.2 Description of each part·····································································································································3
1.3 CABLE SELECTION················································································································ 4
1.3.1 Model name ························································································································································4
1.3.2 Description of each part·····································································································································5
1.4 SELECTION OF OTHER ACCESSORIES···························································································· 7
1.4.1 Selection of regenerative resistance ···················································································································7
1.4.2 Fuse selection ·····················································································································································7
2 INSTALLATION OF SERVO SYSTEM······················································································· 8
2.1 SERVO DRIVER INSTALLATION ·································································································· 8
2.1.1 Installation site···················································································································································8
2.1.2 Environment condition ·······································································································································8
2.1.3 Installation standard···········································································································································8
2.2 SERVO MOTOR INSTALLATION ·································································································10
2.2.1 Environment condition ·····································································································································10
2.2.2 Installation cautions ·········································································································································10
2.2.3 Installation environment···································································································································12
2.3 SERVO CABLE INSTALLATION ··································································································12
2.3.1 Cable selection ·················································································································································12
2.3.2 Xinje cable specification···································································································································13
2.4 SERVO DRIVER DIMENSION ·····································································································16
2.5SERVO MOTOR DIMENSION ·····································································································16
3 WIRING OF SERVO SYSTEM·································································································18
3.1 MAIN CIRCUIT WIRING ··········································································································18
3.1.1 Servo driver terminal arrangement ··················································································································18
3.1.2 CN4 terminals···················································································································································19
3.1.3 CN2 terminals and DIP switch·························································································································19
3.1.4 Communication port·········································································································································20
3.2 CLASSIFICATION AND FUNCTION OF CN0 SIGNAL TERMINALS ·····························································21
3.2.1 Pulse signal ······················································································································································21
3.2.2 SI input signal (without brake) ·························································································································21
3.2.3 SO output signal ···············································································································································22
4 OPERATION OF SERVO SYSTEM···························································································23
4.1 CONTROL MODE SELECTION AND SWITCHING ················································································23
4.1.1 Control mode selection·····································································································································23
4.1.2 Control mode switching····································································································································23
4.2 BASIC FUNCTION SETTING ······································································································24
4.2.1 Jog operation····················································································································································24
4.2.2 Servo enable setting··········································································································································25
4.2.3 Rotation direction switching·····························································································································25
4.2.4 Stop mode ·························································································································································26
4.2.5 Power-off brake················································································································································28
4.2.6 Braking setting··················································································································································30
4.3 POSITION CONTROL··············································································································32
4.3.1 General position control···································································································································32
4.3.2 Position control (external pulse command)······································································································41
4.3.3 Position control (Internal command) ···············································································································42
4.4 SPEED CONTROL ·················································································································50

- 6 -
4.4.1 Speed mode general control ·····························································································································50
4.4.2 Speed control (internal speed)··························································································································52
4.4.3 Speed control (pulse frequency command)·······································································································55
4.5 TORQUE CONTROL···············································································································56
4.5.1 Torque control (internal setting) ······················································································································56
4.6 BUS CONTROL····················································································································57
4.6.1 Object dictionary region assignment················································································································57
4.6.2 CiA402 motion control explanation··················································································································64
4.6.3 CIA402 motion control mode····························································································································74
4.7 ABSOLUTE VALUE SYSTEM ·····································································································95
4.7.1 Absolute system setting·····································································································································95
4.7.2 Replace the battery···········································································································································95
4.7.3 The upper limit of turns ····································································································································96
4.7.4 Read absolute position through communication·······························································································97
4.7.5 Reset absolute position ·····································································································································98
4.8 AUXILIARY FUNCTIONS ·········································································································98
4.8.1 Anti-blocking protection···································································································································98
4.8.2 Torque limit ······················································································································································99
4.8.3 Speed limit ······················································································································································100
4.8.4 I/O signal distribution ····································································································································100
4.8.5 Output terminal function·································································································································101
4.8.6 Input terminal function···································································································································105
4.8.7 Time limit curve of overload protection··········································································································107
5 SERVO GAIN ADJUSTMENT ······························································································· 108
5.1 OVERVIEW OF SERVO GAIN ADJUSTMENT··················································································· 108
5.1.1 Overview and process·····································································································································108
5.1.2 The difference of these adjustment modes ······································································································109
5.1.3 Model loop control ·········································································································································109
5.1.4 Torque disturbance observation·····················································································································111
5.2 ROTARY INERTIA PRESUMPTION ····························································································· 111
5.2.1 Overview·························································································································································111
5.2.2 Notes·······························································································································································111
5.2.3 Operation tool ················································································································································112
5.2.4 Operation steps···············································································································································112
5.3 FAST ADJUSTMENT ············································································································ 114
5.3.1 Overview·························································································································································114
5.3.2 Fast adjustment steps······································································································································114
5.3.3 Rigidity level corresponding gain parameters································································································114
5.3.4 Notes·······························································································································································115
5.4 AUTO-TUNING·················································································································· 116
5.4.1 Overview·························································································································································116
5.4.2 Notes·······························································································································································116
5.4.3 Operation tools···············································································································································116
5.4.4 Internal instruction auto-tuning steps·············································································································117
5.4.5 External instruction auto-tuning steps············································································································121
5.4.6 Related parameters·········································································································································125
5.5 MANUAL ADJUSTMENT ······································································································· 126
5.5.1 Overview·························································································································································126
5.5.2 Adjustment steps ·············································································································································126
5.5.3 Gain parameters for adjustment·····················································································································127
5.6 VIBRATION SUPPRESSION ····································································································· 129
5.6.1 Overview·························································································································································129
5.6.2 Operation tools···············································································································································129
5.6.3 Vibration suppression (PC software) ·············································································································129
5.6.4 Vibration suppression (manual setting)··········································································································130
5.6.5 Notch filter······················································································································································130
5.7 GAIN ADJUSTMENT ············································································································ 133
5.7.1 Load shaking ··················································································································································133
5.7.2 Vibration·························································································································································133
5.7.3 Noise·······························································································································································133
6 ALARM ···························································································································· 134

- 7 -
6.1 ALARM CODE LIST ············································································································· 134
6.2 ANALYSIS OF ALARM TYPES·································································································· 136
APPENDIX ·························································································································· 146
APPENDIX 1. GROUP PPARAMETERS ···························································································· 146
APPENDIX 2. UX-XX MONITORING PARAMETERS·············································································· 160
APPENDIX 3. MODBUS ADDRESS LIST···························································································· 163
APPENDIX 4. Q&A················································································································· 168
APPENDIX 5. GENERAL DEBUGGING STEPS······················································································ 170
APPENDIX 6. APPLICATION EXAMPLE ··························································································· 171
APPENDIX 7. SERVO GENERAL MODE PARAMETERS············································································ 173
Appendix 7.1 Basic parameters·······························································································································173
Appendix 7.2 External pulse position mode general parameters ············································································173
Appendix 7.3 Internal position mode general parameters·······················································································173
Appendix 7.4 Internal torque control general parameters ······················································································174
Appendix 7.5 Internal speed control general parameters························································································174
Appendix 7.6 External pulse speed control general parameters ·············································································174
APPENDIX 8. TORQUE-SPEED CHARACTERISTIC CURVE ······································································· 176
APPENDIX 9. LIST OF MODEL SELECTION AND CONFIGURATION······························································ 177
APPENDIX 10.SERVO SOFTWARE ································································································ 178
Appendix 10.1 Communication between servo software and servo driver ······························································178
Appendix 10.2 start [driver communication] ··········································································································178
Appendix 10.3 Close [driver communication]·········································································································178
Appendix 10.4 [Driver communication] interface···································································································179

1
►► Confirmation on product arrival
After the product arrives, please confirm the integrity of the product in the following aspects.
Items
Notes
Does the product on arrival match the
specified model?
Please confirm according to the nameplate of servo motor
and servo unit.
Does the servomotor shaft rotate
smoothly?
The servo motor shaft is normal if it can be turned
smoothly by hand. Servo motors with brakes, however,
cannot be turned manually.
Is there any damage?
Check the overall appearance, and check for damage or
scratches that may have occurred during shipping.
Are there any loose screws?
Check screws for looseness using a screwdrive.
Is the motor code the same with the
code in drive?
Check the motor code marked on the nameplates of the
servomotor and the parameter U3-70 on the servo drive.
If any of the above is faulty or incorrect, contact Xinje or an authorized distributor.

1
1 Selection of servo system
1.1 Selection of servo driver
1.1.1 Model name
1.1.2 Description of each part
Note: this driver has no panel, so it can't operate the panel. It needs to connect the cable of Xinje servo DB9 with
USB, and use the Xinje servo software.
DF
3
E
-
04
10
Z
Code
Product name
DF
Servo driver
Code
Rated output current
05
5
A
10
10
A
20
20
A
Code
Rated output power
01
100
W
02
200
W
04
400
W
07
750
W
Code
Product series
3
Series number
Code
Specification
Z
Servocan drive the brake
Servo cannot drive the brake
Code
Control function
E
Pulse, RS485, Canopen
、
C
EtherCAT
Power LED and alarm LED
Enable LED and Can communication LED
CN1: RS232 port
CN2: signal IO port
CN3: communication
encoder feedback
CN4: power supply input
Power cable output
CN0: Type E-CANopen&RS485
Type C-EtherCAT
DIP switch

2
Description of status indicator light:
➢Left upper power indicator: after power on, green is always on;
➢Left lower enable run indicator: after enable, green is always on;
➢Upper right alarm err indicator: after alarm, red is always on; Red flashing, need to power on again;
➢Lower right can communication indicator: green flashing after CAN communication.
1.1.3 Performance specification
Servo unit
DF3E series servo driver
Applicable encoder
Standard: 17-bit communication encoder
Input power supply
DF3E-□□□□: single phase DC48V
Control mode
Three phase full wave rectifying MOSFET controlled sine current
drive mode
Using
condition
Using
temperature
-10~+40℃
Storage
temperature
-20~+60 ℃
Environment
humidity
Below 90%RH (no condensation)
Vibration
resistance
4.9m/s2
Structure
Vertical or horizontal installation

3
1.2 Servo motor selection
1.2.1 Model name
MF3S –60 C S 30 B Z 1 –5 04
Series Inertia
MF3S Low inertia
MF3G Medium inertia
MF3H High inertia
Display Base No.
40 40 flange
60 60 flange
80 80 flange
Display Encoder type
C Magnetic encoder
TPhotoelectric encoder
Display Encoder resolution
S Single turn 17 bits
M Multi-turn 17 bits
L Multi-turn 23 bits
Display
15
20
Rated speed(rpm)
1500
2000
30 3000
Display Plug type
1 AMP plug
2 Aviation plug
Display Voltage level
2 24V
548V
660V
Display Power
01 100W
02 200W
04 400W
07 750W
15 1.5KW
Display Shaft
AWith key, no oil seal
BWith key and oil seal
CNo key, no oil seal
DNo key, with oil seal
Display Brake
No brake
Z With brake
1.2.2 Description of each part
Encoder
frame
flange
Output Shaft (Drive Shaft)

4
1.3 Cable selection
1.3.1 Model name
◼Encoder cable
CP-SP-M-01
Display Length (M)
01 1
Display Plug type
SP 9-core amp plug
Display Cable type
CP Normal
Display Plug type
M No battery box
CPT High flexibility
SV 7-core waterproof aviation plug
SC 10-core small aviation plug
02 2
03 3
05 5
BM With battery box
◼Power cable
Display Length (M)
Display Plug type
P4-core amp plug
V6-core waterproof small aviation
plug
Display Cable type
CM Normal
CMT High flexibility
L 4-core small aviation plug
CM-P15-01
Display Diameter(mm²)
07 0.75
15 1.5
20 2.0
01 1
02 2
03 3
05 5
◼Brake cable explanation
➢The cable model for motor/brake motor: CB-P03-length (common material) /CBT-P03-length (high flexible
material).
➢The standard wiring length of Xinje cable is 1m, 2m, 3m and 5m.

5
1.3.2 Description of each part
◼Encoder cable
(1) Pin definition of encoder on servo driver side
Connector appearance
Pin definition
No.
Definition
1
26
5
4
3
1
5V
2
GND
3
/
4
/
5
485+
6
485-
(2) Cable connection of encoder on motor side
Battery box description:
(1) The encoder including the cable definition of battery +, battery- is for the absolute motor, and the
non-absolute motor cable has no such pin.
(2) Only the cable of absolute value motor has external battery box, which contains a 3.6V/2.7Ah large
capacity battery, and has the function of replacing batteries when power cut. The using life is more than two
years. Please refer to chapter 4.6.2 change battery.
◼Power cable
(1) Pin definition of power cable on servo driver side
Connector
appearance
Pin definition
Color
Definition
Brown
U
Black
V
Blue
W
Yellow-green
PE
Connector pins
Pin definition
Suitable model
No.
Definition
1
2
3
4
5
6
7
8
9
1
Battery +
60 flange
2
Battery -
3
Shielded cable
4
485+
5
485-
6
/
7
5V
8
GND
9
/
1
34
5
6
72
No.
Definition
80 flange
1
GND
2
Battery +
3
Battery -
4
485+
5
485-
6
5V
7
Shielded cable

6
(2) Power cable connection on motor side
Connector pins
Pin definition
Suitable model
No.
Definition
1
2
3
4
1
U
60 flange
2
W
3
V
4
PE
13
4
2
No.
Definition
80 flange
1
PE
2
U
3
V
4
W
(3) Brake cable connection
Connector pins
Pin definition
Suitable model
No.
Definition
21
1
BK+
Motor with brake
2
BK-
Brake pins:
The cable including BK pin is used for the brake motor. The cable of the non-brake motor has no BK pin.

7
1.4 Selection of other accessories
1.4.1 Selection of regenerative resistance
When the servo motor is driven by the generator mode, the power returns to the servo amplifier side, which is
called regenerative power. The regenerated power is absorbed by charging the smooth capacitor of the servo
amplifier. After exceeding the rechargeable energy, the regenerative resistance is used to consume the
regenerative power.
The servo motor driven by regenerative (generator) mode is as follows:
➢The deceleration stop period during acceleration and deceleration operation;
➢Running vertically and axially;
➢When the external load drives the motor to rotate.
Servo driver model
Regenerative resistance connection terminals
DF3E-□□□□
Use external regenerative resistance, connect regenerative resistance to RB+
and RB- terminals, P0-25 = power value, P0-26 = resistance value.
The following table is the recommended specifications of external regenerative resistance for each type of motor.
Servo driver model
Rmin
(Not less than this value)
External regenerative
resistance
(Recommended power values)
DF3E-0103
27Ω
Above 100W
DF3E-0410
10Ω
Above 100W
DF3E-0720
5Ω
Above 100W
Note:
(1) The smaller the resistance is, the faster the discharge will be, but the smaller the resistance is, the easier the
breakdown resistance will be. Therefore, please close to the the lower limit but not be less than the lower limit
when choosing the type.
(2) When wiring, please use high-temperature flame-retardant wire, and the regenerative resistance surface can
not contact with the wire.
1.4.2 Fuse selection
The role of fuse in the circuit is over-current protection, also known as short-circuit protection.
When there is a short circuit, the current in the circuit is the largest, which undoubtedly far exceeds the rated
current of the equipment. If the circuit breaker is not cut off in time, the electrical equipment will soon be burned
due to the high current. Therefore, in order to cut off the circuit in time and protect the equipment from damage,
the fuse is used, the principle is that the fuse can be fused quickly before the equipment is damaged at the moment
when a large current is generated in the circuit, so as to cut off the circuit.
Fuse selection
Driver model
Driver power (W)
Fuse specification
DF3E-0103
100
20A/58VDC
DF3E-0410
400
20A/58VDC
DF3E-0720
750
40A/58VDC

8
2 Installation of servo system
2.1 Servo driver installation
2.1.1 Installation site
➢Please install it in the installation cabinet without sunshine or rain.
➢Do not use this product near corrosive and flammable gas environments such as hydrogen sulfide, chlorine,
ammonia, sulfur, chlorinated gas, acid, alkali, salt, etc.
➢Do not install in high temperature, humidity, dust, metal dust environment;
➢No vibration place.
2.1.2 Environment condition
Item
Description
Use ambient temperature
-20~60℃
Use ambient humidity
-10~40℃
Storage temperature
20~90%RH (no condensation)
Storage humidity
20~90%RH (no condensation)
2.1.3 Installation standard
Be sure to comply with the installation standard in the control cabinet shown in the figure below. This standard is
applicable to the situation where multiple servo drivers are installed side by side in the control cabinet (hereinafter
referred to as "when installed side by side").
> 10mm > 10mm > 10mm
Fan Fan Fan
> 50mm
> 50mm
> 50mm
> 50mm

9
◼Servo Drive Orientation
Install the servo drive perpendicular to the wall so the front panel containing connectors faces outward.
◼Cooling
As shown in the figure above, allow sufficient space around each servo drive for cooling by cooling fans or
natural convection.
◼Side-by-side Installation
When install servo drives side by side as shown in the figure above, make at least 10mm between and at least
50mm above and below each servo drive. Install cooling fans above the servo drives to avoid excessive
temperature rise and to maintain even temperature inside the control panel.
◼Environmental Conditions in the Control Panel
⚫Servo driver working ambient Temperature: -10~40 ℃
⚫Humidity: 90%RH or less
⚫Vibration: 4.9m/s2
⚫Condensation and Freezing: None
Note: when installing horizontally (mask facing the operator), it needs to use the frame provided by our company
(see chapter 2.4 the outline dimensions of servo driver).

10
2.2 Servo motor installation
MF series servomotors can be installed either horizontally or vertically. The service life of the servomotor can be
shortened or unexpected problems might occur if it is installed incorrectly or in an inappropriate location. Follow
these installation instructions carefully.
CAUTION
1.The end of the motor shaft is coated with antirust. Before installing, carefully remove all of the paint using a
cloth moistened with paint thinner.
2.Avoid getting thinner on other parts of the servo motor.
2.2.1 Environment condition
When used in places with water droplets or oil droplets, the protection effect can be achieved through the
treatment of motors. However, in order to seal the through part of the shaft, please specify the motor with oil seal.
Connectors should be installed downward.
MS series servo motors are for indoor use. Please use them under the following installation conditions:
Item
Description
Use ambient temperature
-20℃~60℃(relative humidity)
Use ambient humidity
-10℃~40℃(no freeze)
Storage temperature
20%~90%RH (no condensation)
Storage humidity
20%~90%RH (no condensation)
Protection level
IP66
2.2.2 Installation cautions
Item
Description
Antirust treatment
◆Before installation, please wipe the "rust-proof agent" of the extension end
of the servo motor shaft, and then do the relevant rust-proof treatment.
Encoder cautions
◆It is forbidden to impact the extension end of the shaft during installation,
otherwise the internal encoder will be broken.
Antirust
Through part of the shaft

11
Item
Description
◆When the pulley is installed on the servo motor shaft with keyway, the
screw hole is used at the end of the shaft. In order to install the pulley, the
double-headed nails are inserted into the screw holes of the shaft, the washer is
used on the surface of the coupling end, and the pulley is gradually locked with
the nut.
◆For the servo motor shaft with keyway, use the screw hole at the end of the
shaft to install. For shaft without keyway, friction coupling or similar methods
are used.
◆When the pulley is dismantled, the pulley mover is used to prevent the
bearing from being strongly impacted by the load.
◆To ensure safety, protective covers or similar devices, such as pulleys
installed on shaft, are installed in the rotating area.
Centering
◆When installing the servo motor, make it conform to the centering accuracy
requirement shown in the picture below. If the centering is inadequate, vibration
will occur, and sometimes the bearing and encoder may be damaged. When
installing the coupling, please do not directly impact the motor shaft, otherwise
the encoder installed on the opposite side of the load shaft will be damaged.
Installation
direction
◆Servo motor can be installed in horizontal or vertical direction.
Oil and water
solutions
When using in places where water droplets are dropping, please use it on the
basis of confirming the protection level of servo motor. (except for the
shaft-through part) When oil droplets will drip into the shaft-through part,
please specify the servo motor with oil seal.
Conditions for use of servo motors with oil seals:
◆Make sure the oil level is below the lip of the oil seal when using.
◆Please use the oil seal to keep the splash of oil droplets in good condition.
◆When the servo motor is installed vertically upward, please pay attention not
to oil accumulation on the lip of the oil seal.
Stress state of cable
◆Do not "bend" or apply "tension" to the wire, especially the core of the
signal line is 0.2mm or 0.3mm, very thin, so when wiring (using), do not make
it too tight.
Processing of
Connector Part
For the connector part, please pay attention to the following items:
◆When connecting the connector, please make sure that there is no foreign
matter such as garbage or metal sheets in the connector.
◆When connecting the connector to the servo motor, it is necessary to connect
the connector from the side of the main circuit cable of the servo motor first, and
the grounding wire of the main cable must be connected reliably. If one side of
The maximum and minimum deviations are
less than 0.03mm (rotated with the coupling)
measured at four locations in a circle.
The maximum and minimum deviations are less than 0.03mm
(rotated with the coupling) measured at four locations in a circle.

12
Item
Description
the encoder cable is connected first, the encoder may fail due to the potential
difference between PE.
◆When wiring, please make sure that the pins are arranged correctly.
◆Connectors are made of resin. Do not apply shock to avoid damaging the
connector.
◆When carrying out the operation under the condition that the cable remains
connected, it is necessary to grasp the main body of the servo motor. If only the
cable is seized for handling, it may damage the connector or pull the cable off.
◆If bending cable is used, full attention should be paid to the wiring operation
and stress should not be applied to the connector part. If the stress is applied to
the connector part, the connector may be damaged.
2.2.3 Installation environment
➢Do not use this product near corrosive and flammable gas environments such as hydrogen sulfide, chlorine,
ammonia, sulfur, chlorinated gas, acid, alkali, salt, etc.
➢In places with grinding fluid, oil mist, iron powder, cutting, etc., please choose motor with oil seal.
➢A place away from heat sources such as stoves;
➢Do not use motor in enclosed environment. Closed environment will lead to high temperature and shorten
service life of motor.
2.3 Servo cable installation
DF3E series servo motor adopts communication encoder, which may cause uncertain influence due to improper
use and environmental factors. When installing power cable and encoder cable, please pay attention to the
following instructions.
2.3.1 Cable selection
Our regular cable materials include ordinary cable and high flexible cable. The adapter cable connector for motors
with 80 flange or less is divided into aviation plug and amp plug.
The cable selected by the customer needs to define the operating conditions on site.
If the cable is used in general occasions, please select the cable from other manufacturers (2.3.2 specifications of
Xinje cable) in strict accordance with the specifications given by Xinje. If the cable is used in unconventional
occasions, please select the cable according to the actual working conditions to be superior to the existing
specifications of Xinje.
1. In normal situations, the following points should be noted:
⚫For pulse command signal cable, please ensure wiring less than 3m.
⚫The encoder cable shall be within 20 meters. It is recommended to select special cable if it is more than
20 meters. The wire diameter of encoder cable depends on the length of encoder cable used on site. The
longer the cable is, the greater the wire resistance is, and the more severe the voltage attenuation or
signal distortion is, which is likely to cause pulse loss or no signal can be detected. Therefore, in general,
the customized special cable should be selected if it is more than 20 meters.
⚫The power cable diameter depends on the current condition of the motor. Generally, the wire diameter is
1/10 of the maximum current of the motor. For example, the maximum current of the motor is 60A, and
the wire diameter of 6mm²is selected.
⚫In case of interference, it is necessary to separate strong and weak current. It is recommended to
separate power cable from encoder cable and signal cable.
⚫Ensure the correct grounding of servo driver and servo motor. The grounding resistance is not more than
4Ω, and the grounding depth is more than 2m. It is recommended to use 4*40 angle galvanized steel or
Table of contents
Other Xinje Servo Drive manuals
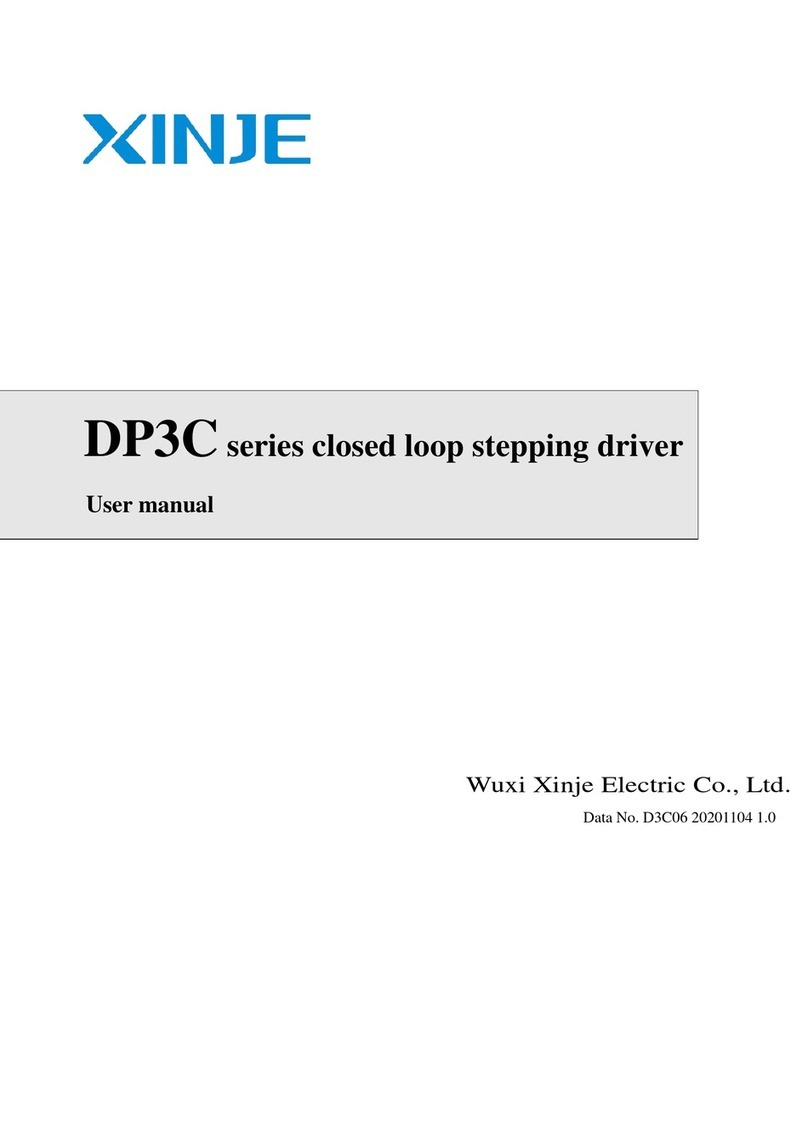
Xinje
Xinje DP3C Series User manual
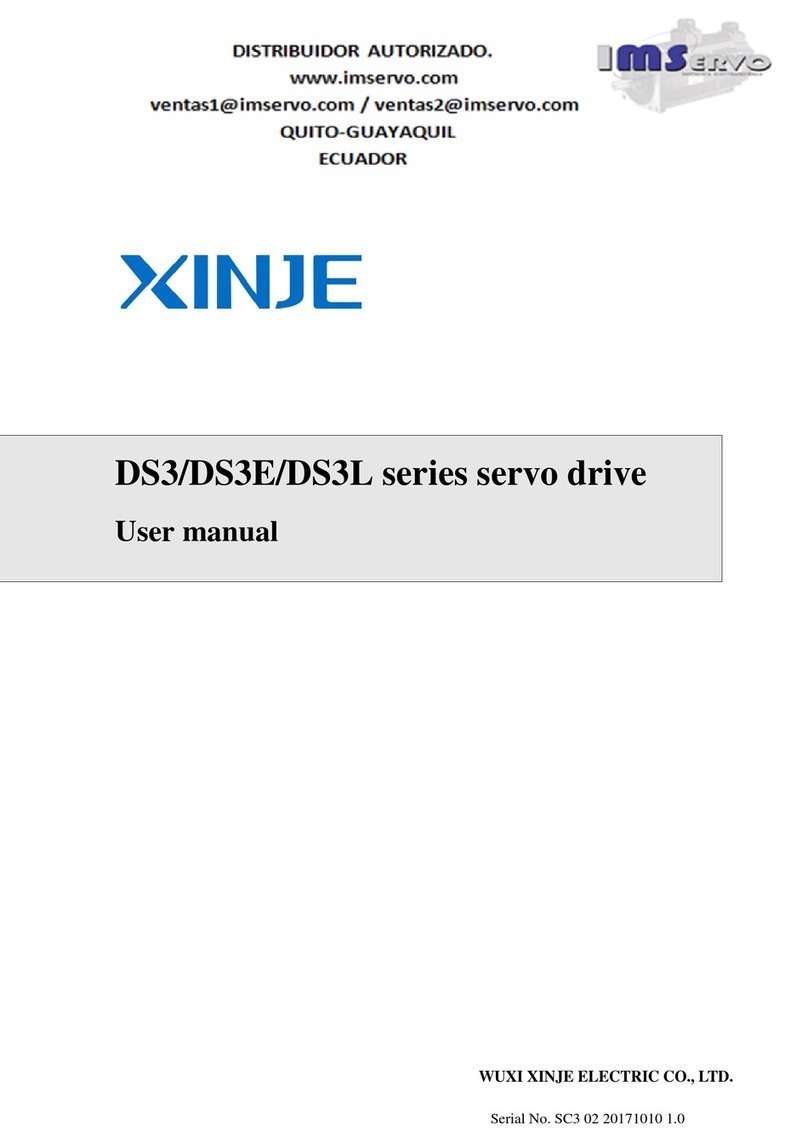
Xinje
Xinje DS3 series servo User manual
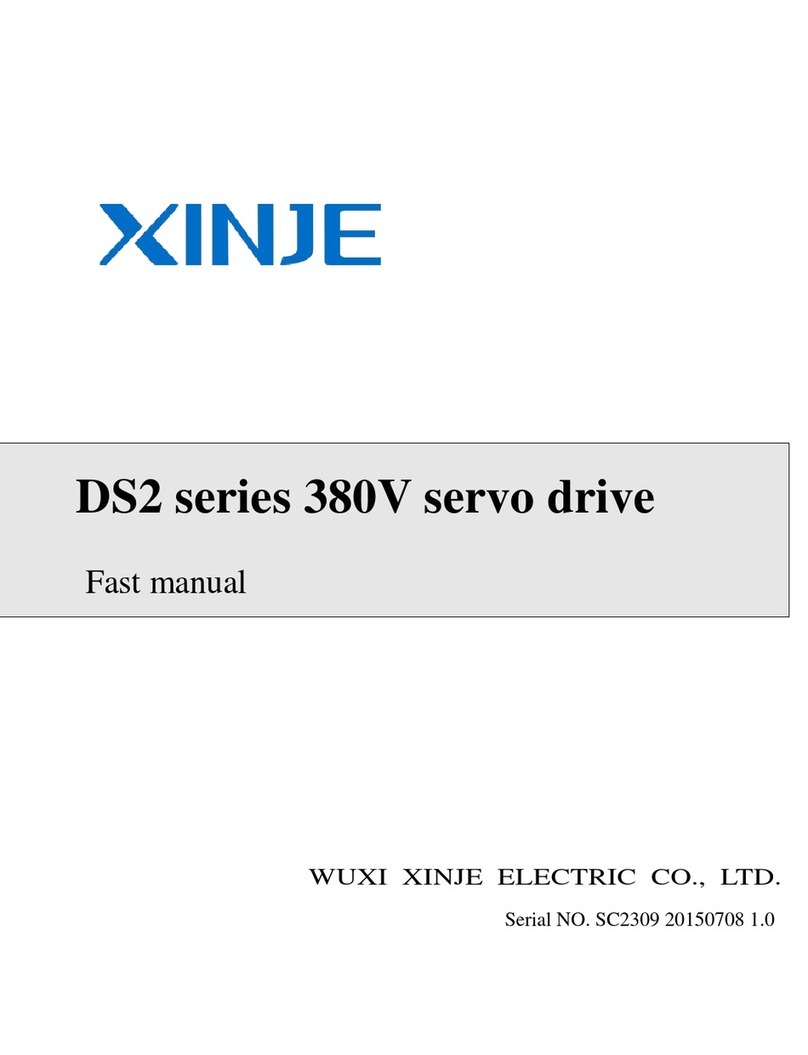
Xinje
Xinje DS2 series User manual
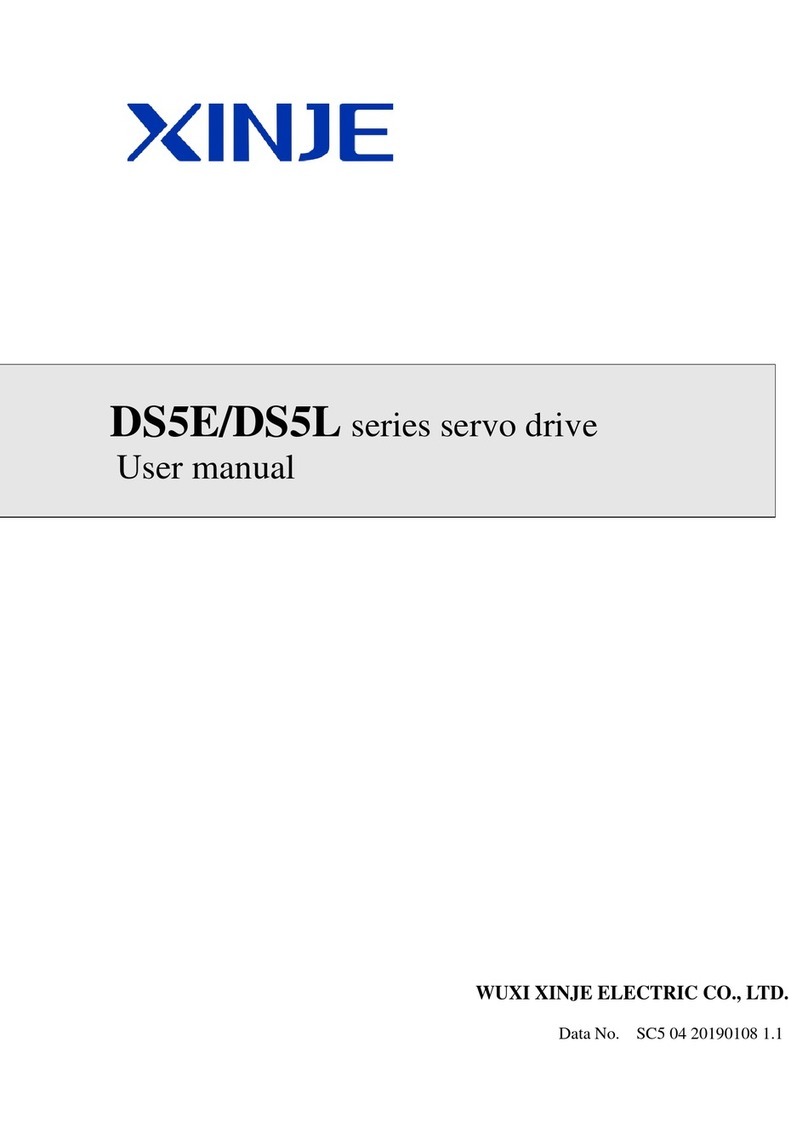
Xinje
Xinje DS5E Series User manual

Xinje
Xinje DP-708 User manual
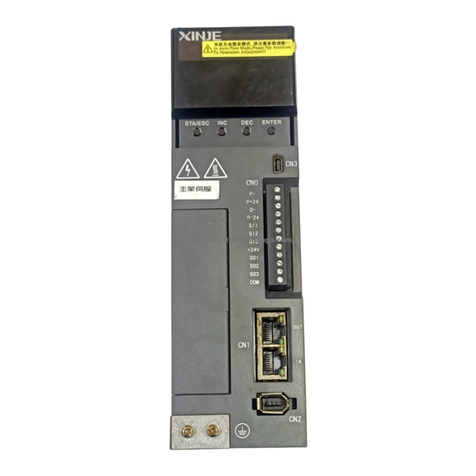
Xinje
Xinje DS5C Series User manual
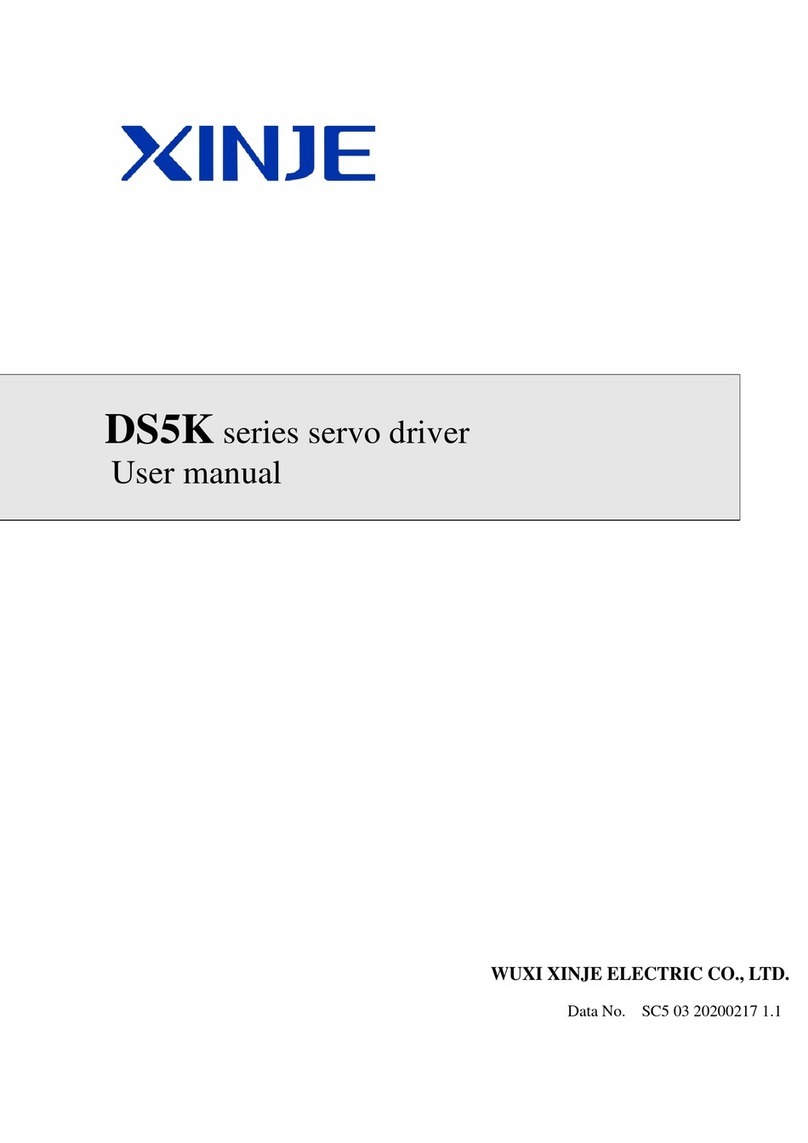
Xinje
Xinje DS5K Series User manual
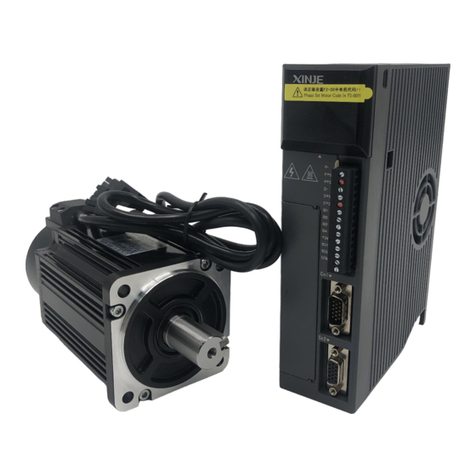
Xinje
Xinje DS2 series User manual
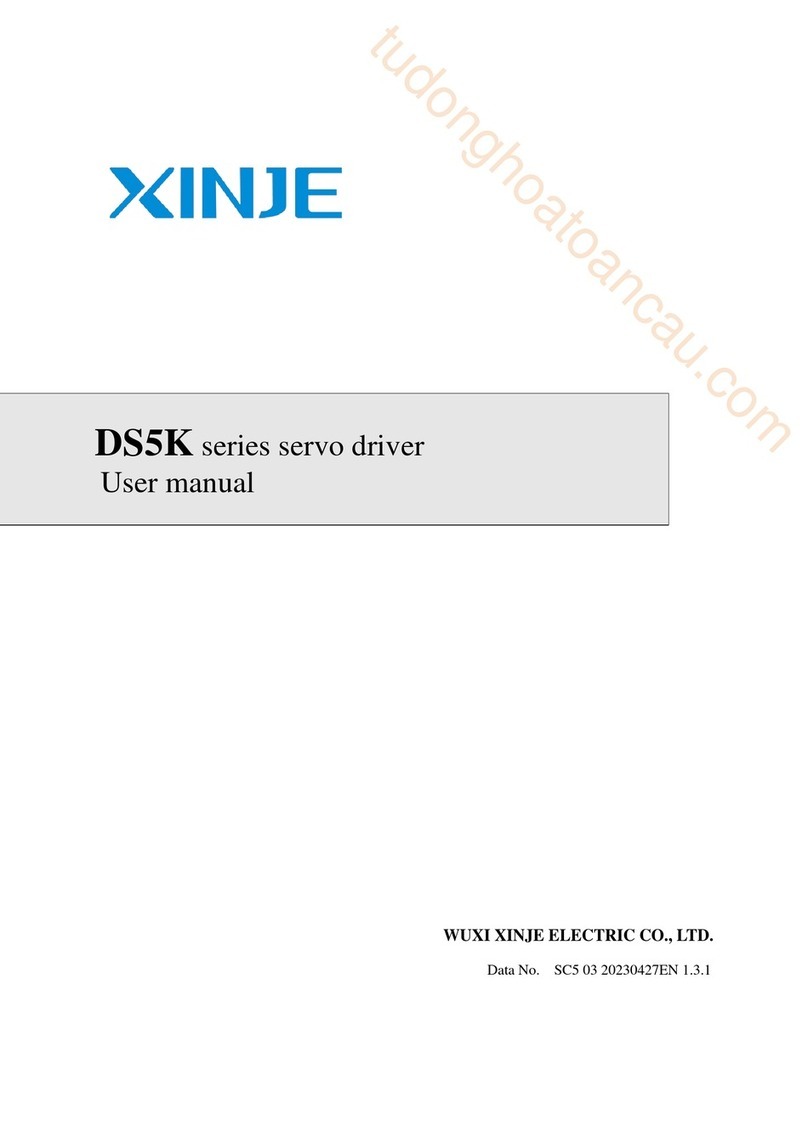
Xinje
Xinje DS5K Series User manual
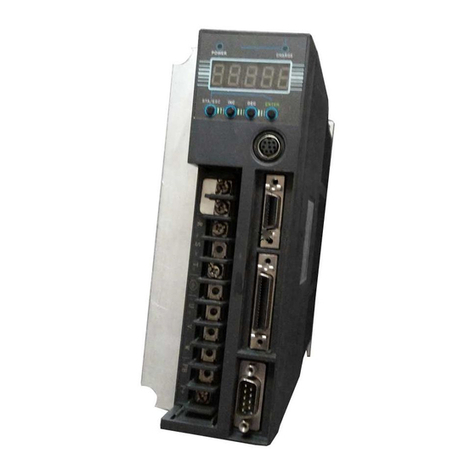
Xinje
Xinje DS3 series servo User manual
Popular Servo Drive manuals by other brands
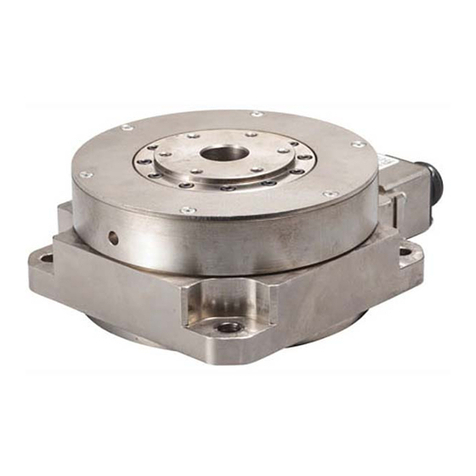
Mitsubishi Electric
Mitsubishi Electric TM-RFM Series user manual
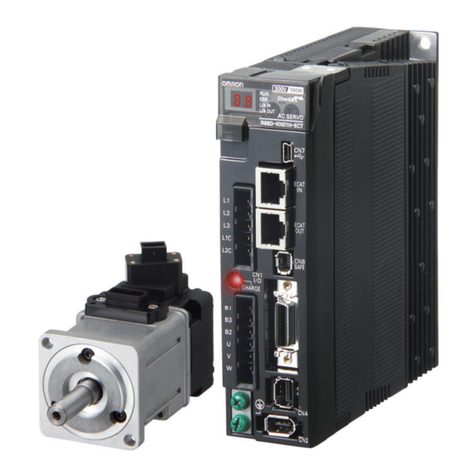
Omron
Omron OMNUC G5 Series user manual
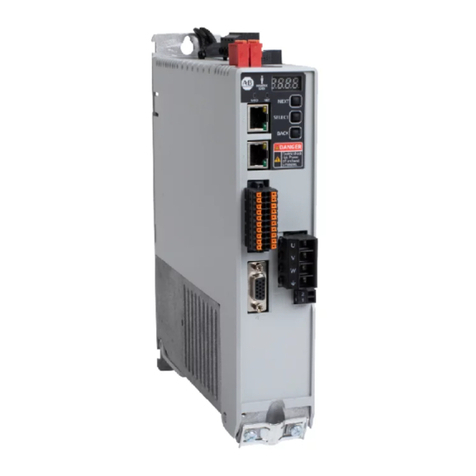
Rockwell Automation
Rockwell Automation Allen-Bradley Kinetix 350 Migration guide
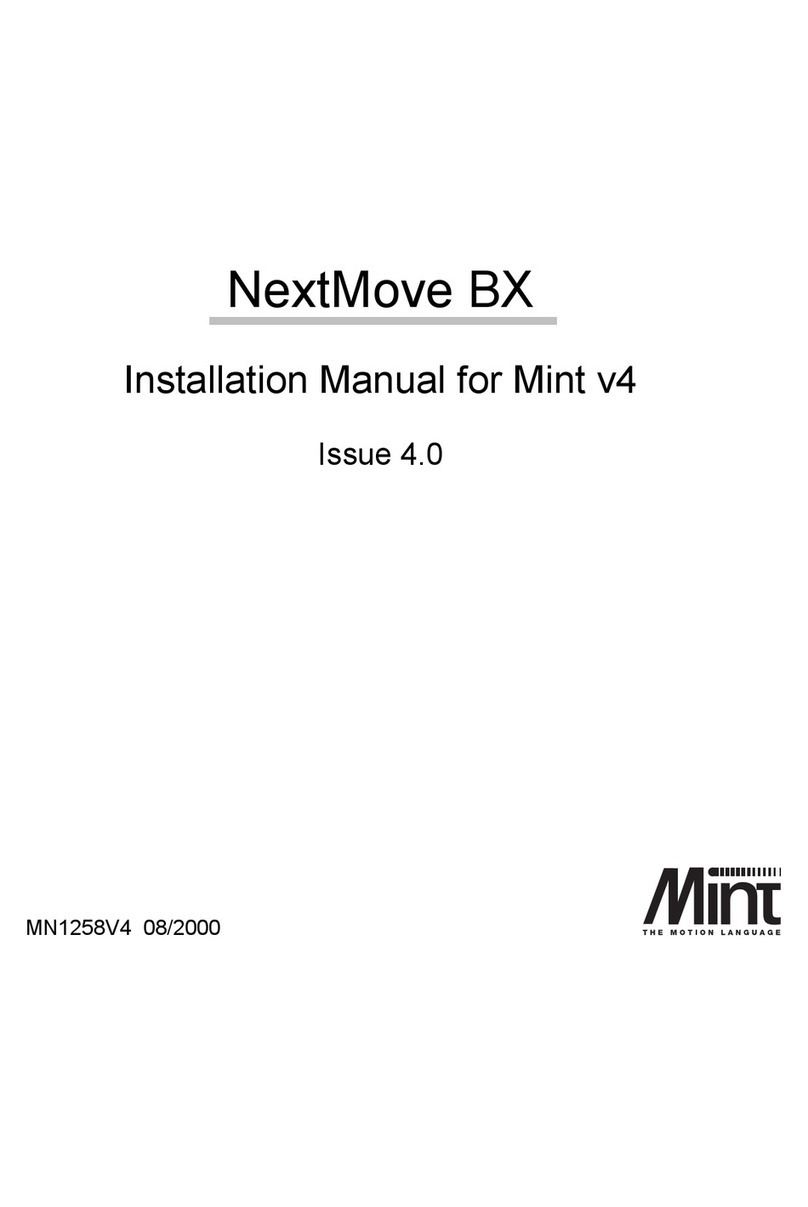
Baldor
Baldor NextMove BX installation manual
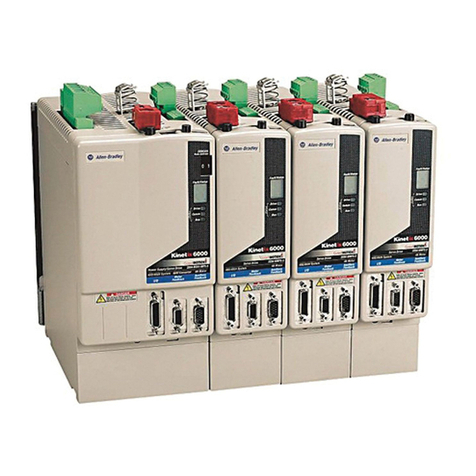
Rockwell Automation
Rockwell Automation Allen-Bradley Kinetix 6000 user manual
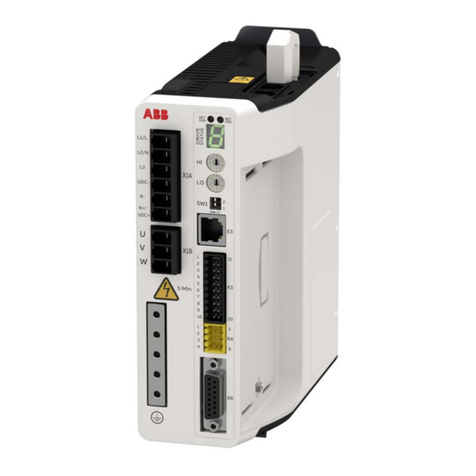
ABB
ABB MicroFlex e190 user manual