HBX CPU-1000 User manual

HBX Control Systems Inc.
Central Processing Unit 1000
Version 1.38
CPU-1000
General Installation Guide

Control Systems Inc.
Comfort
Control
Innovation
HBX CPU-1000 HVAC Controller
Version 1.34
© HBX Control Systems Inc. 2011 Tableof Contents 1/1 Page 1
Tableof Contents
TABLE OF CONTENTS
• Section 1 - Introduction 2-6
· Getting Started................................................................ 2
· Receiving Inspection and Storage................................ 2
· General Technical Data................................................. 3
· Nameplate Information................................................. 3
· Main Parts and Labels.................................................... 4-5
· Terminal Designations................................................... 6
• Section 2 - Installation and Wiring 7-8
· Installation Requirements.............................................. 7
· Safety Precautions........................................................... 7
· Control Terminal Colour Coding ............................... 8
· Wiring Options............................................................... 8
• Section 3 - Programming the Control 9-10
· Display Features............................................................. 9
· Navigating the Display.................................................. 10
· Programming and Setup............................................... 10
· Program Lock................................................................ 10
• Section 4 - Summary of Parameters 11-14
· Table and Factory Defaults........................................... 11-14
• Section 5 - Accessories and Options 15
• Section 6 - Troubleshooting Guide 16-17
• Glossary of Terms 18-22
· PMI Theory and Description........................................ 19
· Modulating Theory and Types...................................... 20-22
• Typical Design Outside Temperatures 23
• Temperature Conversion Charts 24
• Warranty Information 25

HBX CPU-1000 HVAC Controller
Version 1.38
Introduction 2/6 Page 2
GETTING STARTED
This manual will help with the installation, parameter
setting, troubleshooting and general maintenance
requirements for the Controller. To guarantee the safe
and reliable operation of this Control, you must first
read this manual in detail and take particular note to any
and all warnings or caution directives prior to
connecting to AC power.
Only suitably qualified individuals with
formal training in electrical and HVAC
controls should attempt the installation of
this equipment. Incorrect wiring and
installation will affect the warranty provided
with this unit. Wiring must be completed in
accordance with the codes and practices
applicable to the jurisdiction for the actual
installation.
The HBX CPU-1000 is a microprocessor
based controller and as such is not to be
regarded as a safety (limit) control. Please
consult and install the heating or cooling
appliance in accordance with the
manufacturer's recommendations.
SAFETY SYMBOLS:
RECEIVING, UNPACKING,
INSPECTION AND STORAGE
This CPU-1000 has gone through rigorous quality
control tests at the factory before shipment. After
receipt and before installation perform the following
checks:
Receipt
After receiving, inspect the unit for any possible
physical damage that may have occurred during
transportation.
Inspection
After unpacking the unit make sure the box contains:
• CPU-1000 Controller
• 1 Remote Outdoor Temperature Sensor
• 2 Universal Temperature Sensors
• 1 Terminal Screwdriver
• 2 Cable Ties
Make sure the part number on the unit corresponds to
the part number on the original box.
Storage
The CPU-1000 should be kept in its original shipping
carton prior to installation. In order to retain the
warranty coverage it should be stored properly:
• Store in a clean dry place
• Store within an ambient temperature range of
+10ºC to +40ºC
• If possible, store in an air-conditioned
environment where the relative humidity is less
than 95%
• Do not store in places where the unit may come
into contact with corrosive gases or liquids
• Do not store in an area or upon an unstable
surface where it may become damaged due to
falling
Extreme Hazard -
This action poses a serious threat that could result
in personal injury or death, as well as permanent
damage to the equipment. Proceed with caution.
Moderate Hazard -
This action may cause personal injury or have
adverse effects on the installation process if
handled incorrectly.
Disconnect Power Source -
The presence of low voltage(24VAC) or high
voltage(120VAC) could result in personal injury or
permanent damage to components or equipment.
Point of Interest -
This point clarifies pertinent information, or
brings your attention to an action that may have
adverse effects on the installation process.

HBX CPU-1000 HVAC Controller
Version 1.38
© HBX Control Systems Inc. 2012 Introduction 3/6 Page 3
GENERAL TECHNICAL DATA
Input Voltage:
120 VAC, ± 10%, 60Hz
3 x Optically Isolated Inputs:
20 - 240 VAC
3 x Thermistor Inputs:
Boiler/System Sensors/Outdoor
3 x Pump Output Relays:
240VAC 10A
2 x Auxiliary Output Relays:
240VAC 10A
Standard Communications:
RS-232
Real Time Clock Battery:
Lithium-Ion
Microprocessor:
16Bit, 20MHz
Languages:
English
Graphic Display:
128 x 64 pixels (55mm x 28mm viewable area)
Weight:
0.95 KG (2.1 lbs)
Dimensions:
190mm W x 170mm H x 70mm D
ETL Listings:
Meets CSA C22.2 No. 24
Meets UL Standard 873
ETL Control No. 3068143
Storage:
+10ºC to +40ºC
All I/O (inputs and outputs) are both colour
coded and keyed indexed for
non-interchangeability
Nameplate Information:
The exterior label contains specific information unique
to your HBX HVAC Control and identifies some of the
basic features. The label displays the serial number
which will match the serial number on your actual
Control, the lot number, the bar code and the product’s
ETL number.
CPU-1000
Central
Processing Unit
CPU-1000
Central Processing Unit
Made In
Canada
Lot Number: 0000001
Serial Number: 0004-1204
Date: 12/21/04
Lot Number:
Serial Number:
Date:
3068143
V1.28
V1.28
V1.28
V1.28
V1.28
Side View Side ViewFront View Rear View
72mm
70mm 20 75mm 75mm
190mm 190mm
172mm9
63.2
168.2
63.2
Top ViewBottom View

HBX CPU-1000 HVAC Controller
Version 1.38
Introduction 4/6 Page 4
Example:
Viewing from top left and moving right in a clockwise
direction:
1. Back-Lit Graphic Display:
The display is one of the key features of the Controller.
Depending upon which mode of operation is selected,
you will be able to view most common system values
simultaneously. It will also serve as a visual indicator
when in the programming mode.
2. Lockable Keypad Cover:
Once your system has been programmed and optimized
there should be little or no reason for further changes.
The Controller has been designed with the ability to
physically “hard-lock” the keypad to prevent tampering
with the settings.
3. Menu and Programming Buttons:
These buttons will be used to set up the Controller
during commissioning and for toggling between
displays or troubleshooting at a later date if necessary.
A. Moves screen or value down
B. Moves screen or value up
C. Enters a value, parameter, or setting, toggles Y/N
D. Return to last screen and access programming mode
•Reset- Protected from being accidentally pushed
2. Lockable
Keypad Cover
3. Menu /Reset /
Programming
Buttons
4. Serial Number /
Bar Code Tracking
5. Communication
Connection
6. 120 VAC
Pump Outputs
7. 120 VAC
Power Inputs
8. Miscellaneous
Relays
9. Thermistor /
Sensor Inputs
10. Demand
Inputs
11. Backup
Battery
1. Graphic
Display
MAIN PARTS AND LABELS
A
A
B
B
C
C
D
D
Input: 120VAC 60Hz 5A
Relays: 240VAC 10A
DdSl20240V
Certified to CSA C22 2No 24
1000

HBX CPU-1000 HVAC Controller
Version 1.38
© HBX Control Systems Inc. 2012 Introduction 5/6 Page 5
4. Serial Number and Bar Code:
This label will identify the entire factory ordered options
and the date of manufacture. It can also be used for re-
ordering and will be required in the event of factory
service assistance or warranty claim.
5. Communication Connection:
The standard communications port (RS-232) is found
immediately below the bar code label. Optional
communications software needs to be purchased to
enable a connection. Please consult factory or dealer.
Only a CAB-0100 can be inserted into this
connection without causing damage.
6. 120 VAC Pump Outputs:
There are three separate (3-wire) 120VAC output power
terminals designed to run either a pump or fan.
7. 120 VAC Power Input:
There is one (3-wire) terminal block for incoming
120VAC power.
8. Miscellaneous Relays:
There are two (2-wire) miscellaneous/auxiliary relay
terminal blocks. These can be used to wire a variety of
miscellaneous devices up to 10Amps.
9. Thermistor/Sensor Inputs:
There are three (2-wire) sensor/thermistor inputs.
Under no circumstance should power be
applied to these terminals! Permanent damage
to the Controller’s circuitry may result.
10. Demand Inputs:
There are three (2-wire) “demand” control inputs.
Control signals between 20-240VAC are designed to
trigger a variety of commands within the Controller, for
example run a heat demand, a setpoint demand and/or
a DHW demand.
11. Backup Battery:
The lithium-ion battery is purely a back-up supply for
the real time clock and will keep the clock refreshed
during a power interruption to the Control.
Prior to installation, please remove the
protective paper strip to activate the back-up
battery as shown below.

HBX CPU-1000 HVAC Controller
Version 1.38
Introduction 6/6 Page 6
21
SD
1
SD
1
43
SD
2
SD
2
65
SD
3
SD
3RG
021
82
N
L
7262
RG
021
52
N
L
4232
RG
021
22
N
L
1202
RG
021
91
N
L
8171
LR
2
LR
6151
2
LR
1
LR
4131
1
MT
3
MT
2111
3
MT
2
MT
019
2
MT
1
MT
87
1
v042-02 v042-02 v042-02
EREHREWOPTCENNOCTONOD
A01 A01
A01 A01A01
0001UPC
XBH TINUGNISSECORPLARTNEC
yaleR3P
yaleR2P
yaleR1P
CAV021rewoPylppuS
2yaleR:csiM
1yaleR:csiM
1langiSdnameD
2langiSdnameD
3
langiSdnameD
1rotsimrehT
2rotsimrehT
3rotsimrehT
0001UPCXBHrofsnoitangiseDlanimreT
Demand Signal 1 - Any heat demand signal powered by 20 -
240VAC. E.g. 24VAC Thermostat. This trigger will follow the
Outdoor Reset Curve calculated by the Control.
Demand Signal 2 - Any heat demand signal powered by 20 -
240VAC. E.g. 24VAC Thermostat. This trigger will not follow the
Outdoor Reset Curve but stage the boiler to its maximum boiler
temp programmed in the Control. Demand 2 has an alternative
function and can be programmed to be the default input for a flow
proof switch (only available with applications using pump
sequencing).
Demand Signal 3 - Any heat demand signal powered by 20 -
240VAC. E.g. 24VAC Thermostat/Aquastat. This trigger is
designed to stage the boiler temp to satisfy the DHW settings
programmed in the Control.
Thermistor 1 - Boiler Sensor
Thermistor 2 - System Sensor (alternative position for DHW
Sensor, Staging/DHW Systems only)
Thermistor 3 - Outdoor Sensor
TM1, TM2 & TM3 are designed for 10K Ohm
Thermistors and must never be subjected to any
external power supply (voltage or current)
P3 Relay - Any pump (or fan) output rated to a max of 10Amps
120VAC. This relay is pre-programmed to be the default DHW
pump supplying a DHW in-direct hot water tank. Its alternative
function is to be an Injection Pump relay when PMIp is the
injection mixing strategy.
P2 Relay - Any pump (or fan) output rated to a max of 10Amps
120VAC. This relay is pre-programmed to be the default (low
temp) system pump. When programmed for a mixing system.
P1 Relay - Any pump (or fan) output rated to a max of 10Amps
120VAC. This relay is pre-programmed to be the default boiler or
(High Temp) system pump.
P1 & P2 - The (2) dedicated relays when pump sequencing is
selected in the Controls program. P1 & P2 become the Hi Temp
system pumps in a commercial application requiring pump
sequencing.
Supply Power - The 3-wire 120VAC input to the control.
Protected by a 30Amp breaker or fuse.
Misc: Relay 2 - This relay is the default relay for bringing on the
2nd Boiler or Boiler stage. It has an alternative function and can
be used as an injection valve. This may be PMIv for radiant
mixing or a on/off valve for DHW indirect storage tanks.
Misc Relay 1 - This relay is the default relay for bringing on the
1st Boiler or Boiler stage.
Misc Relays 1&2 are Dry Contacts and rated for
a max of 10Amps

HBX CPU-1000 HVAC Controller
Version 1.38
© HBX Control Systems Inc. 2012 Page 7
INSTALLATION & WIRING
The CPU-1000 is designed to be wall mounted, DIN rail mounted, or installed
inside a separate electrical enclosure. The unit should be mounted inside and be
protected from falling water and high humidity conditions. With all the covers in
place it is designed to protect any individual from accidental electrical shock.
The Controller has a built in 5Amp fast acting fuse to protect the circuitry on the
Printed Circuit Board (PCB). The unit is designed to power up to 3 pumps and 2
auxiliary relays of 10Amps each. As such, an upstream customer supplied fuse or
circuit breaker rated at a maximum of 30 amps must be in circuit. It is the
installers responsibility to provide either a 3 pin (3ft max) grounded plug and cable,
or the unit must be wired directly to a breaker and terminated inside the control
box (terminals 17, 18 & 19).
All power wiring must be with a minimum of 18AWG wire.
Low power wiring ----------- insulated 18AWG (min.) wire to a max of 500ft.
Thermistor wiring ------------ insulated 18AWG (min.) wire to a max of 500ft.
It is recommended to use 18AWG Single Stranded Wire. It is also
recommended to run signal and power wiring in separate conduit.
Only suitably qualified individuals with formal training in electrical and
HVAC controls should attempt the installation of this equipment.
Incorrect wiring and installation will affect the warranty provided with this
unit. Wiring must be completed in accordance with the codes and practices
applicable to the jurisdiction for the actual installation.
Section Two
Installation and Wiring

HBX CPU-1000 HVAC Controller
Version 1.38
Page 8
Central Processing Unit
CPU-1000
WIRING OPTIONS
White Green Black Red Brown Blue Yellow Natural Black Red Blue Orange
DEMAND DEMAND DEMAND THERM THERM THERM RELAY RELAY PUMPPUMPPUMP
INPUT
POWER
1
13579111315246810121416 26232017 27242118 28252219
1122212333
White (1-2) Demand 1, 2-wire control input
20-240VAC
Green (3-4) Demand 2, 2-wire control input
20-240VAC
Black (5-6) Demand 3, 2-wire control input
20-240VAC
Red (7-8) Therm 1, 2-wire thermistor
Eg. boiler sensor
Brown (9-10) Therm 2, 2-wire thermistor
Eg. system sensor
Blue (11-12) Therm 3, 2-wire thermistor
Eg. outdoor sensor
Yellow (13-14) Relay 1, misc. auxiliary
10Amps
Natural (15-16) Relay 2, misc. auxiliary 10Amps.
Also becomes the default terminals
when selecting PMIv (valve injection).
Explained further on page 63.
Black (17-19) Input Power, 3-wire.
This is the main input power supply
connection. 17 is line, 18 is neutral and
19 is earth ground.
Red (20-22) Pump 1, 3-wire 120VAC output power
to pump or fan number 1. 20 is line, 21
is neutral and 22 is earth ground.
Blue (23-25) Pump 2, 3-wire 120VAC output
power to pump or fan number 2. 23 is
line, 24 is neutral and 25 is earth ground.
Orange (26-28) Pump 3, 3-wire 120VAC output power
to pump or fan number 3. 26 is line, 27
is neutral and 28 is earth ground. Also
becomes the default terminal when
using PMIp (pump injection).
Explained further in the manual.
Terminals 7-12 must not be subjected to any
external power source

HBX CPU-1000 HVAC Controller
Version 1.38
© HBX Control Systems Inc. 2012 Page 9
Section Three
Programming
PROGRAMMING
DISPLAY FEATURES
The HBX display is a 128 x 64 pixel, back-lit graphic display on a blue background.
In addition to displaying text and icons it has the ability to provide you with visual
graphing capabilities. These graphing capabilities will allow you to get
representative data and trending information of up to 2 independent feedback
values.
Standard Screen
Alternate Screen Showing Flow Proof Feature
Applicable only to a Staging Control with Pump Sequencer turned on.
System Status
STue Jan 4 2005 12:00:45
Boiler
System
Outdoor
Room
162
112
54
72
Target
ºF
ºF
ºF
ºF
170
120
Output
%
HD HTD DHW SP1 SP2 SP3
DHW Demand ON
Heat Demand
ON
Set Back Mode
ON
Warm Weather Shut Down
ON
Target
Temperature
Shown in
Column below
Real Time and Date Shown
Temperature Feedback
( deg. Fahrenheit shown)
WWSD
High Temp Demand ON Setpoint ON Indicator
System Status
STue Jan 4 2005 12:00:45
Boiler
Outdoor
Room
162
54
72
Target
ºF
ºF
ºF
170
Output
%
HD FLO DHW SP1 SP2 SP3 WWSD
Flow Proof ON

HBX CPU-1000 HVAC Controller
Version 1.38
Page 10
NAVIGATING THE CONTROL
The four large red buttons labeled “A”,
“B”, “C”, and “D” are used to make
your way through the programming
options within the Control.
Pressing the “A” or “B” button while
viewing the initial “System Status” and
“System Function” main screens will
toggle from screen to screen. Pressing
the “D” button will take you to the
“Programming Options” screen.
Pressing the “D” button again will
revert to the main system screens.
Once in the “Programming Options” menu you may move the selection indicator up and down by pressing the “A”
and “B” buttons, pressing the “C” button will enter the selected option.
Pressing the “C” button on options with limited choices (ie. on/off, yes/no) will toggle the selection.
Pressing the “A” and “B” buttons on options with variable numerical choices (ie. temperature values, time settings)
will increase and decrease the selected amount. Pressing the “C” button upon completion will forward you to the next
step.
The “D” button can be used to revert to the previous menu.
A
A
B
B
C
C
D
D
Input: 120VAC 60Hz 5A
Program Lock Feature
To minimize the potential for unauthorized tampering of your control after commissioning, you have the ability
to limit/lock the programming menus.
To lock the Control, use two fingers to press and hold down the A and B buttons simultaneously for
approximately 10 secs.
To unlock the Control, use two fingers to press and hold down the C and D buttons simultaneously for
approximately 10 secs.
If the display flashes erratically, remove your fingers from the buttons and try again by pressing both
buttons at the same time.
A
A
B
B
C
C
D
D
Input: 120VAC 60Hz 5A
Relays: 240VAC 10A
Demand Signal: 20 - 240V
Model: CPU - 1000
Certified to CSA C22.2No 24
Conforms to UL Standard 873
Central Processing Unit
1000
A
A
B
B
C
C
D
D
Input: 120VAC 60Hz 5A
Relays: 240VAC 10A
Demand Signal: 20 - 240V
Model: CPU - 1000
Certified to CSA C22.2No 24
Conforms to UL Standard 873
Central Processing Unit
1000
Lock Feature Unlock Feature

HBX CPU-1000 HVAC Controller
Version 1.38
© HBX Control Systems Inc. 2012 Page 11
SUMMARY OF PARAMETERS
Description Options Range Factory
Default
Main View
Screen(s)
View:
• Boiler Temp
• System Temp
• DHW Temp*
• Outdoor Temp
• Indoor Temp
(if sensor connected)
• Actual vs. Target
Temps
• Min/Maxs values for
each sensor
• Time and Date
• Setpoints
• Setbacks
• Separate Heat Demands
• WWSD
• 3 pumps run
condition
• Cycle Count
• Temperature Range
• Staging Control*
• Mixing Control*
• DHW Control*
• Dual System Control*
• Dual Mixing Control*
* Depending on
control type
selected.
(-40-225 ) ºC or ºF
(-40-225 ) ºC or ºF
(-40-225 ) ºC or ºF
(Open ) ºC or ºF
(Open ) ºC or ºF
ºC or ºF
ºC or ºF
24 hr clock
up to 3
up to 3
up to 3
0ºF to 100ºF
On/Off
0-65535 Cycles
ºC or ºF
ºF
ºF
ºF
ºF
ºF
ºF
ºF
Off
N
75ºF
ºF

HBX CPU-1000 HVAC Controller
Version 1.38
Page 12
Description Options Range Factory
Default
Control
Options
• Display Options
• Always HD?
• Use Room Thermistor
• Mins and Maxs
• Testing
• Stage Run Times
• Use Zone Module
Y/N
Y/N
Up to 6 sensors
c/w reset
Up to 17 relays
(w/ Exp. Modules)
Plus 5 x PWM
Up to 14
Y/N
N
N
N
Boiler
Options
(Staging
and DHW
Controls)
• Staging Options
• Hi/Lo Fire
• Fixed First
• Fixed Last
• Lo/Lo-Hi/Hi
• Boiler Differential
• Min Boiler Ontime
• # of Stages (14 w/Modules)
• Pump Options
• 1 Pump/Boiler
• Pump Sequencer
• Rotate Boilers
• Pumps Always On?
• Post Purge
• Rotate Time/Normal
• Use Flow Proof?*
• Mod out Setpoint
• 3- Standard Pumps
P1, P2, P3(PMIp)
Y/N
Y/N
Y/N
Y/N
Auto/40/30/20/10
3 Mins
1 to 2
Y/N
Y/N
Y/N
Y/N
Y/N
30 - 240 Sec
Y/N
Y/N
N
N
N
N
Auto
3-20 Mins
Single Stage
N (off)
N (off)
Y
N
30 Sec
N
N
• 2- Auxiliary Relays
P1 & P2 can be used
for pump sequencing
Boiler,
System, DHW

HBX CPU-1000 HVAC Controller
Version 1.38
© HBX Control Systems Inc. 2012 Page 13
Description Options Range Factory
Default
Mixing
Options
• Boiler Options
• Injection Type
“Same as
last section”
PMI Valve
PMI Pump
Floating Action
Modulating
“Same as
last section”
PMIv
‘Valve’
Change
Design
• Design Boiler Temp
• Design System Temp
• Design System Temp 2*
• Design Room Temp
• Design Room Temp 2*
• Design Outside Temp
• Design Outside Temp 2*
• Min Boiler Temp
• Min System Temp
• Min System Temp 2*
• WWSD
• Default Designs
Staging*
• Default Designs
Mixing*
0ºF to 225ºF
0ºF to 225ºF
0ºF to 225ºF
-50ºF to 100ºF
-50ºF to 100ºF
-50ºF to 100ºF
-50ºF to 100ºF
40ºF to 200ºF
0ºF to 150ºF
0ºF to 150ºF
0ºF to 100ºF
o Lo Efficient
Building
o Mid Efficient
Building
o Hi Efficient
Building
o Lo Temp Radiant
o Hi Temp Radiant
o Fancoil
o Baseboard
o Lo Temp Radiator
o Hi Temp Radiator
190ºF
135ºF
135ºF
70ºF
70ºF
-10ºF
-10ºF
120ºF
75ºF
75ºF
75ºF

HBX CPU-1000 HVAC Controller
Version 1.38
Page 14
Description Options Range Factory
Default
Setpoint
Options
• Setpoint 1
o Setpoint Temp
o Heating
o Cool Interlock
o Differential
o Lag Time
o Setpoint Demand
• Setpoint 2 and 3
Off/33ºF to 225ºF
Heat/Cool
Y/N
2ºF to 100ºF
0S to 600S
No/Lo/Hi Temp
As Above
OFF
Heating
N
2ºF
0S
Hi Temp
As Above
Setback
Options
• Use Setbacks
• Set Setbacks
o Start Time 1
o End Time 1
o Start Time 2
o End Time 2
o Start Time 3
o End Time 3
Y/N
0:00 – 24:00
0:00 – 24:00
0:00 – 24:00
0:00 – 24:00
0:00 – 24:00
0:00 – 24:00
N
Domestic
Setup
• Use DHW?
• DHW Valve
• DHW Priority
• Domestic Temp
• Differential
• DHW Interlock
• DHW Boiler Temp
Y/N
Valve/Pump
Y/N
32ºF to 225ºF
0ºF to 100ºF
Y/N
100ºF to 225ºF
N
Pump
N
100ºF
2ºF
N
150ºF
Graphing • Boiler Graph
• System Graph
Target vs. Actual
Target vs. Actual

HBX CPU-1000 HVAC Controller
Version 1.38
© HBX Control Systems Inc. 2012 Page 15
ACCESSORIES AND OPTIONS
The CPU-1000 Main Control has been designed to incorporate simple integrated Expansion Modules to provide and
accommodate even the most sophisticated control package. Each Expansion Module has a side ported 32-Pin input/output
connection.
When connected using the HBX
32-Pin male to male adapter, each
module can be joined together
(daisy chain style) and will butt
together with virtually no side
clearance. Due to the 32-pin
connector no external cross wiring
is necessary.
A maximum of 6
Expansion Modules can
be connected in series.
1) Additional Sensors:
• Universal Sensors part number 029-0022
• Indoor/Outdoor Sensors part number OUT-0100
2) Connectors
• 32-Pin Adapter Plug part number 033-0037
KEY/COLOUR
CODED CONNECTORS
To simplify the installation, the Control has been
designed to utilize dedicated terminal plugs. Each
terminal has non-interchangeable male and female
mating parts.
In addition each plug is colour coded as well as being
keyed/indexed. There are a combination of two and
three wire plugs.
INDOOR/OUTDOOR SENSOR
The HBX remote (Indoor/Outdoor) Temperature Sensor has 2
x 20mm knock out holes, 1 from the underside and 1 from the
rear. The HBX housing can accommodate up to four (4) 10K ohm
thermistors.
Outside sensors should be placed on the north facing wall of
the heated building to avoid any solar heating effect. The sensor
should also be located away from other non-ambient heat
sources such as exhaust fans, heat generating air conditioners or
refrigeration units.

HBX CPU-1000 HVAC Controller
Version 1.38
Lorem Ipsem Page 16
Page 16
TROUBLESHOOTING & FAULT CODES
Display does not come
on
Check power connection at terminals 17,18,19. If no power (120VAC) present
then trace power back to source. Cycle power to Control.
No heat demand Check that you have at least 20VAC being supplied to the heat demand trigger.
E.g. power to terminals 1&2 for a heat demand to follow the outdoor reset curve.
Power to terminals 3&4 for a Hi temp heat demand and power to terminals 5&6
are for a DHW demand.
Injection not working Make sure that in the mixing settings you have selected the appropriate device you
are using to mix with. If it is PMIp then your connection should be attached to
26 to 28 and if it is PMIv then connect the valve to 15,16.
Buttons do not respond
or cannot go into
Programming Mode
Hold down buttons C and D to unlock the buttons. Hold until display says
BUTTONS UNLOCKED.
Parameters set in
control do not seem to
be taking effect
Manually Reset Control by using a small blunt tool and gently press the reset
button.
Boilers not staging on Make sure in the boiler options that you have selected the appropriate amount of
stages for the system.
Domestic Hot water
demand not coming on
Make sure if you are using a Thermistor that it is hooked to terminals 9&10 on a
staging control or have your aquastat attached to terminals 5&6 with power.

HBX CPU-1000 HVAC Controller
Version 1.38
Lorem Ipsem Page 17 Page 17
Lack of Heat or no
response to a heat
demand
Control may be in Warm Weather Shut Down mode, see “System Status” display.
Is the acronym “WWSD” visible? If yes, check in “Change Designs” menu under
WWSD, factory default is 75ºF. Adjust accordingly to your own design
parameters.
Remember to check and install your Outside temperature sensor away from
direct sun or potential heat sources etc.
Cannot select more than
4 Boilers in Staging
Options
If you are using the DHW control type the maximum # of boiler stages is limited
to 4.
Staging and Mixing control types will allow you to program up to a
maximum of 14 stages but please note you must have the corresponding
number of Expansion Modules to effectively accomplish this
No Boiler Heat Demand
when Zone Module has
a call for Heat
Make sure you program ‘Use Zone Module’ to ‘Y’ in Control Options. Zone
Modules are currently under development.
© HBX Control Systems Inc. 2012

HBX CPU-1000 HVAC Controller
Version 1.38
Page 18
GLOSSARY OF TERMS
AI (Analog Input) – A control signal that varies in
magnitude, example 0-10 volts or 4-20mA. Usually
being supplied to the control source.
Aquastat – The name usually supplied to the
temperature sensing device immersed in water and
sending on/off control signals to its control source.
Closed Loop – This typically describes the control
strategy employed in a regulated system. Closed loop
controls always have feedback sensors giving signals
back to the control source allowing incremental
adjustments to be made, thus resulting in more precise
control.
Mixing Valve – A special type of valve that is
designed to temper water temperature by blending
hot water with cooler return water.
Can be 2-way, 3-way and even 4-way mixing.
Modulating Valve – A special type of
valve that has the ability to regulate or proportional
open or close dependent on the control signal supplied
to it.
Open Loop – Normally used to describe a type of
control strategy for a regulated system. Open loop
systems provide no feedback on temperature changes
and thus tend to work blind or unaware of actual
temperature conditions.
PID (Proportional, Integral, Derivative) –
This is an acronym to describe the control calculations
in automatic controls. In essence it decides when to
accelerate or decelerate a device and at the same time
measures and compensates for the rate of change and
how long it has been outside of its target range.
PWM (Pulsed Width Modulation) –
It is a control strategy that uses digital technology (1’s
and 0’s or 0 and 5 volts) to emulate an analog signal.
The longer the high value (e.g. 5 volts) is pulsed for
during a string of pulses, represents a higher analog
value.
Relay – Typically a small switching device that
aids or assists in the control of turning on/off larger
pieces of electrical equipment.
Thermistor – Is an electrical device that varies its
resistance in proportion to the temperature it is
exposed to. It is commonly used as a feedback signal
to a controller.
Thermostat – A temperature sensing device that
sends electrical signals back to a central controller to
turn on/off the heat/cooling supply.
WWSD (Warm Weather Shut Down) –
A control strategy used to turn the boiler off at times
when the temperature outside of the building exceeds
the design heat loss or heat exchange between the
internal and external walls. The strategy is designed to
provide energy savings from firing the boiler
unnecessarily and to improve the inside comfort of
uncontrolled zones.
Zone – An area, room or collection of rooms that
have independent heating and cooling control. Each
zone will usually have its own thermostat.
Zone Damper – The name usually given to the
sliding or rotating vane inside the air supply ducting or
plenum. The zone damper will either open or close to
meet the heat/cool demand.
Zone Valve – The name given to the isolation valve
that opens and closes the heat generating/cooling
source to the zone requiring temperature adjustment.

HBX CPU-1000 HVAC Controller
Version 1.38
© HBX Control Systems Inc. 2012 Page 19
Pulsed Modulated Injection Theory (PMI)
PMI uses all 3 (proportional, integral, derivative) functions of a PID Control algorithm to open and close 1 of 2
relays housed within the CPU-1000. The control can choose to use PMI on either a pump (PMIp) terminals 26, 27
& 28 or a valve (PMIv) terminals 15 & 16.
In the example of a pump, the PMI logic will determine how long the pump needs to be ON for and how long to
be OFF for to maintain adequate injection rates to stabilize the target temperature in the mixed (radiant) heat
emitter. In the case of pump injection, the pump is being held on (pulsed on) e.g. full speed, for a calculated period
of time and then held off (pulsed off) e.g. zero speed, for again a calculated period of time. The ON pulse and the
OFF pulse, time is continuously being monitored and compensated for by the Controls internal algorithm using PID
application theory.
* It is important to view this as a long on pulse or off pulse as opposed to a rapid series of pulses. The
duration of each pulse will likely be several seconds or even minutes before the beginning of a new cycle
length. It is also important to recognize that this control principle cycles the device on and off more frequently
than is customary. This has been taken into consideration and several safety features are built into the Control
to alleviate any potential adverse effects on the Control, the electrical environment, pump motors and valve coils.
In the case of PMIv or valve injection the theory is exactly the same. With regard to the slower and varying response time
of the valve the control PID will compensate and respond with timing changes accordingly.
HBX has tested this injection principle both in the lab and in extensive customer site locations with a variety of
manufacturers’ valves and pumps with exceptional control characteristics and no detrimental effects on either valve
motors/coils or pump motors etc.
The main advantages to employing this control strategy with mixing are:
i. Single Phase pumps up to 10 amps (1HP, 120VAC) can be used for injection
ii. Extra Controls do not need to be wired into the main Control
iii. The option exists for future mechanical system upgrades or modifications without changing
your primary controller
iv. Greater injection control using valves
PMIp is not recommended with split-phase motors. Premature failure of the start winding
and/or centrifugal starting contacts may occur.
PMI - Theoretical Representation
0 min 1 min 2 mins 3 mins 4 mins 5 mins
On
120V
P I T P
I
OV
A. Typical Short Cycle Runtime B. Typical Long Cycle Runtime
* In both examples, actual cycle time may be longer or shorter then shown
Table of contents
Other HBX Computer Hardware manuals
Popular Computer Hardware manuals by other brands
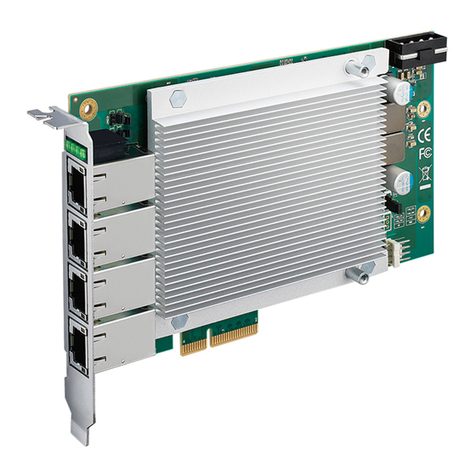
Vecow
Vecow PE-5000 Series user manual
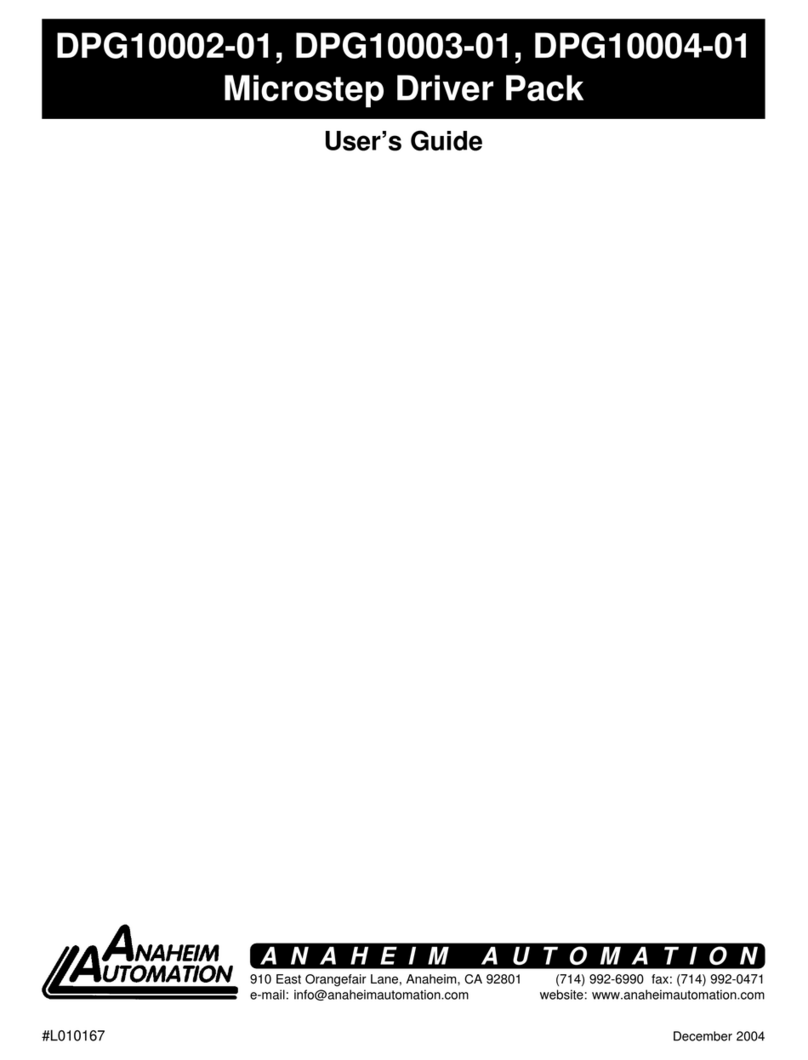
Anaheim Automation
Anaheim Automation DPG10002-01 user guide
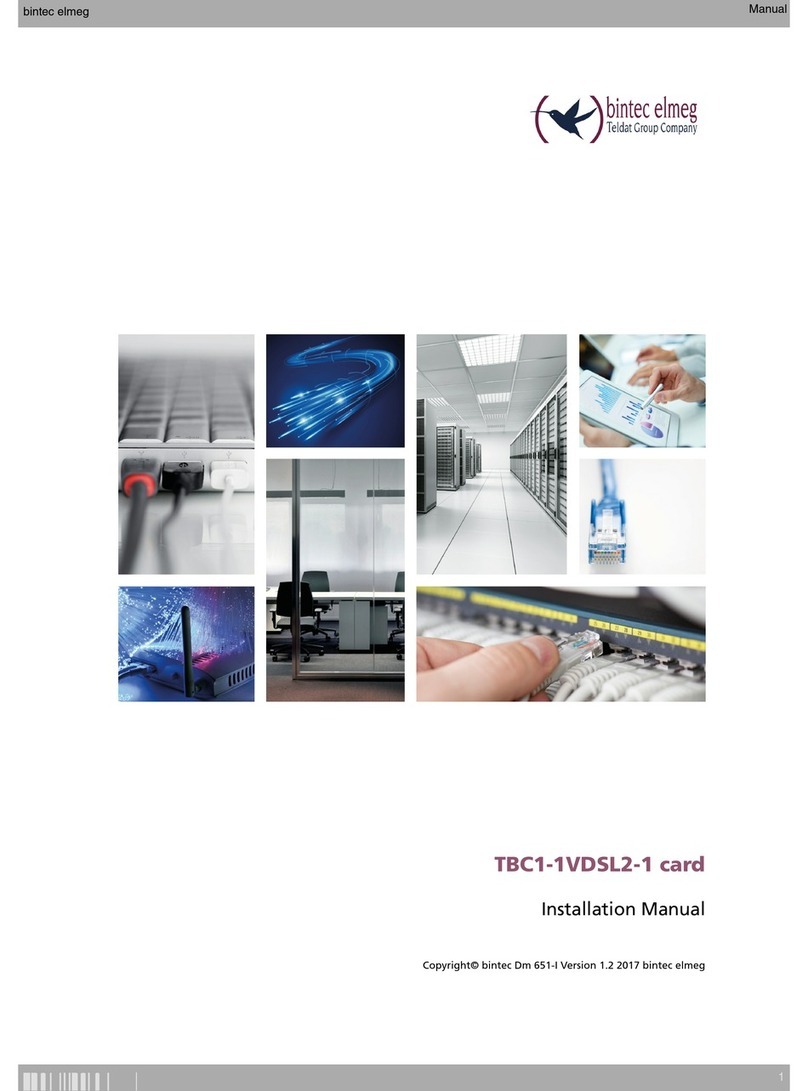
BinTec
BinTec TBC1-1VDSL2-1 installation manual
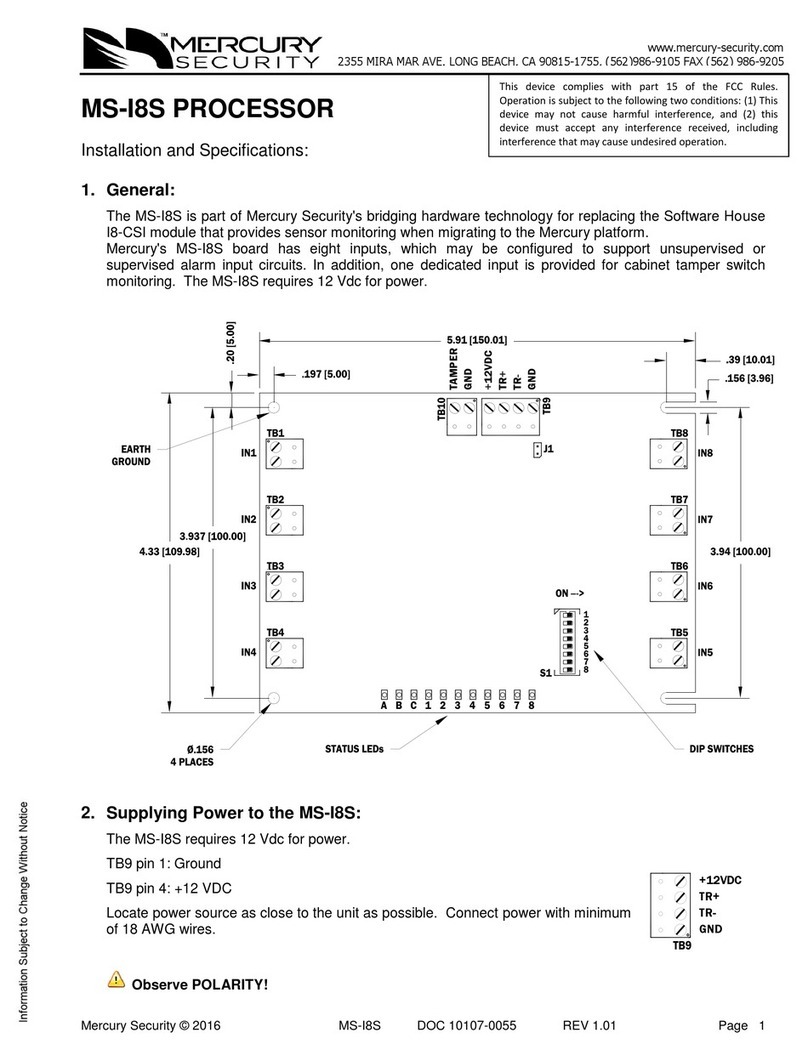
Mercury Security
Mercury Security MS-I8S Installations and specifications
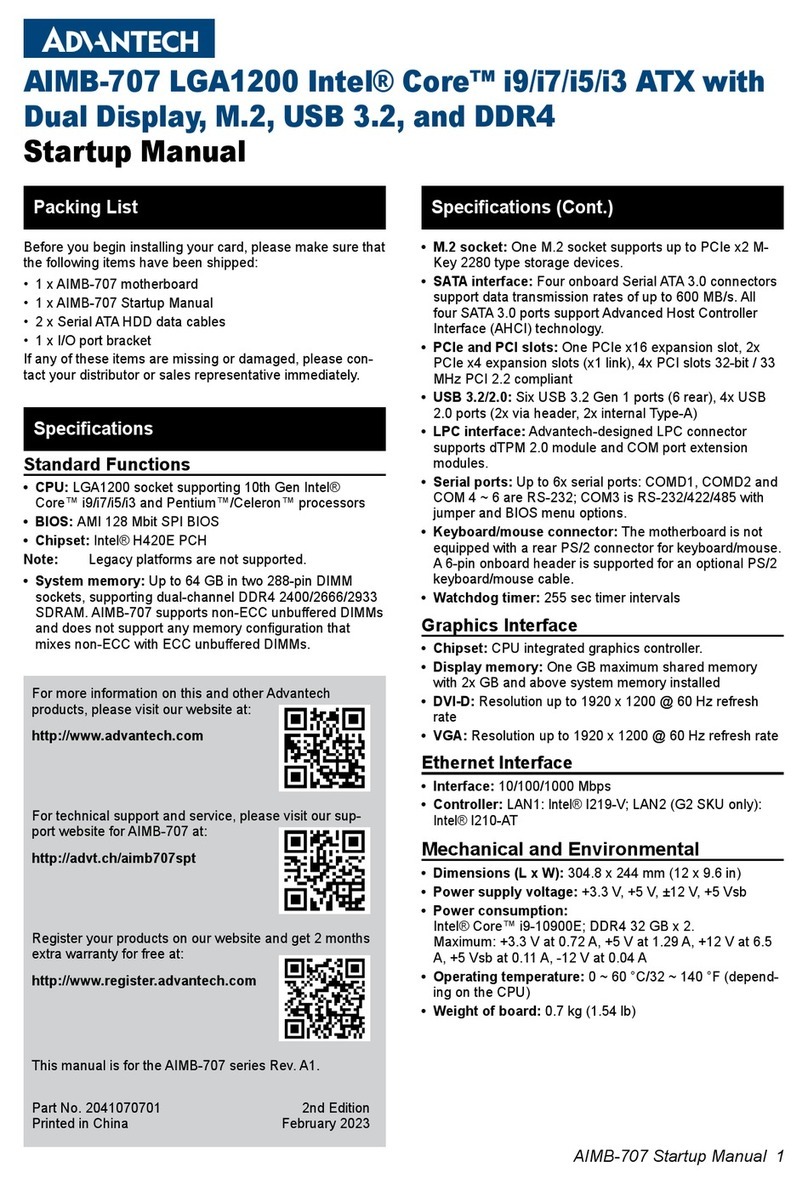
Advantech
Advantech AIMB-707 Startup manual

evertz
evertz 7825DSK2-LG-HD instruction manual