Heinzmann Pandaros-IV User manual

Copyright 2017 by Heinzmann GmbH & Co. KG.
All rights reserved. This publication may not be reproduced by any means whatsoever or passed on to any third parties.
Manual DG 01 003-e / 12-178155
Heinzmann GmbH & Co. KG
Motor- & Turbinenmanagement
Am Haselbach 1
D-79677 Schönau
Telefon +49 (0)7673 8208-0
Telefax +49 (0)7673 8208-188
E-Mail info@heinzmann.com
www.heinzmann.com
USt-IdNr.: DE145551926
HEINZMANN
Digital Electronic Speed Governors
Digital Basic System
PANDAROS - IV
DG 2005DP.6-01 up to -05
DG 2040DP.6-01 up to -05


Digital Governor Basic System PANDAROS IV
The appropriate manuals must be thoroughly studied before instal-
lation, initial start-up and maintenance.
All instructions pertaining to the system and safety must be followed in
full. Non-observance of the instructions may lead to injury to persons
and/or material damage.
HEINZMANN shall not be held liable for any damage caused through
non-observance of instructions.
Independent tests and inspections are of particular importance for all
applications in which a malfunction could result in injury to persons or
material damage.
All examples and data, as well as all other information in this manual
are there solely for the purpose of instruction and they may not be used
for special application without the operator running independent tests
and inspections beforehand.
HEINZMANN does not guarantee, neither expressly nor tacitly, that
the examples, data or other information in this manual is free from er-
ror, complies with industrial standards or fulfils the requirements of any
special application.
To avoid any injury to persons and damage to systems, the follow-
ing monitoring and protective systems must be provided:
Overspeed protection independent of the rpm controller
HEINZMANN shall not be held liable for any damage caused through
missing or insufficiently rated overspeed protection.
thermal overload protection
The following must also be provided for alternator systems:
Overcurrent protection
Protection against faulty synchronisation for excessively-large frequen-
cy, voltage or phase difference
Directional contactor
The reasons for overspeeding may be:
Failure of positioning device, control unit or its auxiliary devices
Linkage sluggishness and jamming
The following must be observed before an installation:
Always disconnect the electrical mains supply before any interventions
to the system.
Only use cable screening and mains supply connections that correspond
with the European Union EMC Directive
Check the function of all installed protection and monitoring systems

Digital Governor Basic System PANDAROS IV
Please observe the following for electronically controlled injection
(MVC):
For common rail systems each injector line must be equipped with a
separate mechanical flow-rate limiter
For unit pump (PLD) and pump-injector unit (PDE) systems, the fuel
enable is first made possible by the solenoid valve’s control plunger
motion. This means that in the event of the control plunger sticking, the
fuel supply to the injection valve is stopped.
As soon as the positioning device receives power, it can actuate the
controller output shaft automatically at any given time. The range of the
controller shaft or control linkage must therefore be secured against un-
authorised access.
HEINZMANN expressly rejects any implied guarantee pertaining to
any marketability or suitability for a special purpose, including in the
event that HEINZMANN was notified of such a special purpose or the
manual contains a reference to such a special purpose.
HEINZMANN shall not be held liable for any indirect and direct dam-
age nor for any incidental and consequential damage that results from
application of any of the examples, data or miscellaneous information
as given in this manual.
HEINZMANN shall not provide any guarantee for the design and planning
of the overall technical system. This is a matter of the operator its planners
and its specialist engineers. They are also responsible for checking whether
the performances of our devices match the intended purpose. The operator is
also responsible for a correct initial start-up of the overall system.

Contents
Digital Governor Basic System PANDAROS IV
Contents
Page
1 Safety instructions and related symbols.............................................................................. 1
1.1 Basic safety measures for normal operation.................................................................... 2
1.2 Basic safety measures for servicing and maintenance..................................................... 2
1.3 Before putting an installation into service after maintenance and repair works ............ 2
2 General................................................................................................................................... 3
3 Functions................................................................................................................................ 4
3.1 General functions............................................................................................................. 4
3.2 Variation specific additional functions............................................................................ 6
3.2.1 Variation DC 6-01 (Standard Generator)................................................................. 6
3.2.2 Variation DC 6-02 (Standard General).................................................................... 6
3.2.3 Variation DC 6-03 (Extended Generator)................................................................ 6
3.2.4 Variation DC 6-05 (Extended General, especially vehicle) .................................... 7
3.2.5 Variation DC 6-00 (ful flexibility)........................................................................... 8
3.2.6 Variation DC 6-06 (positioner)................................................................................ 9
4 Further information............................................................................................................ 10
5 Block diagram...................................................................................................................... 11
6 Sensors.................................................................................................................................. 12
6.1 Overview ....................................................................................................................... 12
6.2 Magnetic pick-up IA ..................................................................................................... 13
6.2.1 Technical data........................................................................................................ 13
6.2.2 Installation ............................................................................................................. 13
6.2.3 Tooth profile .......................................................................................................... 14
6.2.4 Clearance of magnetic pick-up .............................................................................. 14
6.2.5 Dimensions ............................................................................................................ 15
6.3 Coolanttemperature sensor TS 01-28-PT1000 (EDV- No.: 600-00-053-00).................. 16
6.4 Pressure sensors............................................................................................................. 17
6.4.1 Oil pressure sensor................................................................................................. 17
6.4.2 Boost pressure sensors........................................................................................... 18
6.4.2.1 Boost pressure sensor with plug..................................................................... 18
6.4.2.2 Boost pressure sensor with housing and terminal strip.................................. 19

Contents
Digital Governor Basic System PANDAROS IV
7 Setpoint adjusters................................................................................................................ 20
7.1 Setpoint potentiometer SW 01-1-b (1 turn) (EDV- No.: 600-00-041-01)..................... 20
7.2 Setpoint potentiometer SW 02-10-b (10 turn) (EDV- No.: 600-00-042-01)................. 20
7.3 Setpoint value adjustment by current signal.................................................................. 21
7.4 Digital presetting of setpoint values.............................................................................. 21
7.5 Setpoint value adjustment by pedal............................................................................... 21
7.6 Pneumatic setpoint adjuster........................................................................................... 21
8 Control unit DC 6-00 ... 05.................................................................................................. 22
8.1 Specification.................................................................................................................. 22
8.1.1 General................................................................................................................... 22
8.1.2 Inputs and outputs.................................................................................................. 23
8.2 Dimensions.................................................................................................................... 24
8.3 Mounting ....................................................................................................................... 25
9 Actuators.............................................................................................................................. 26
9.1 Design and mode of operation....................................................................................... 26
9.2 Installation ..................................................................................................................... 27
9.3 Specification.................................................................................................................. 28
9.4 Dimensions.................................................................................................................... 29
10 Electrical connection......................................................................................................... 31
10.1 Connection table for variation DG 6-00...................................................................... 31
10.2 Optional assignment of inputs and outputs, variation DG 6-00.................................. 32
10.2.1 Digital Inputs ....................................................................................................... 32
10.2.2 Analogue and PWM Inputs.................................................................................. 33
10.2.3 Digital Outputs..................................................................................................... 33
10.2.4 Analogue and PWM Outputs............................................................................... 33
10.3 Connection for variation DG 6-01 (standard generator) ............................................. 34
10.4 Connection for variation DG 6-02 (standard general)................................................. 35
10.5 Connection for variation DG 6-03 (extended generator)............................................. 36
10.5.1 Digital Inputs ....................................................................................................... 37
10.5.2 Analogue and PWM Inputs.................................................................................. 37
10.6 Connection for variation DG 6-05 (extended general)................................................ 38
10.7 Harness ........................................................................................................................ 39
11 Parametrization options ................................................................................................... 41
11.1 Parametrization at the factory...................................................................................... 41
11.2 Parametrization with the Hand Held Programmer HP 03 ........................................... 41
11.3 Parametrierung mit dem PC / Laptop.......................................................................... 41
11.4 Parametrization with user mask................................................................................... 42
11.5 Transferring data sets .................................................................................................. 42
11.6 Assembly line end programming................................................................................. 42

Contents
Digital Governor Basic System PANDAROS IV
12 Starting the engine - brief instruction............................................................................. 43
13 Ordering details................................................................................................................. 44
14 Download of manuals........................................................................................................ 45


1 Safety instructions and related symbols
Digital Governor Basic System PANDAROS IV 1
1Safety instructions and related symbols
This publication offers wherever necessary practical safety instructions to indicate inevitable
residual risks when operating the engine. These residual risks imply dangers to
- Personnel
- Product and machine
- The environment
The primary aim of the safety instructions is to prevent personal injury!
The signal words used in this publication are specifically designed to direct your attention to possi-
ble damage extent!
DANGER indicates a hazardous situation the consequence of which could
be fatal or severe injuries if it is not prevented.
WARNING indicates a hazardous situation which could lead to fatal injury
or severe injuries if it is not prevented.
CAUTION indicates a hazardous situation which could lead to minor inju-
ries if it is not prevented.
NOTICE indicates possible material damage.
Safety instructions are not only denoted by a signal word but also by hazard
warning triangles. Hazard warning triangles can contain different symbols
to illustrate the danger. However, the symbol used is no substitute for the
actual text of the safety instructions. The text must therefore always be read
in full!
This symbol does not refer to any safety instructions but offers important
notes for better understanding the functions that are being discussed. They
should by all means be observed and practiced.
In this publication the Table of Contents is preceded by diverse instructions that among
other things serve to ensure safety of operation. It is absolutely imperative that these
hints be read and understood before commissioning or servicing the installation.

1 Safety instructions and related symbols
2 Digital Governor Basic System PANDAROS IV
1.1 Basic safety measures for normal operation
The installation may be operated only by authorized persons who have been duly
trained and who are fully acquainted with the operating instructions so that they are ca-
pable of working in accordance with them.
Before turning the installation on please verify and make sure that
- only authorized persons are present within the working range of the engine;
- nobody will be in danger of suffering injuries by starting the engine.
Before starting the engine always check the installation for visible damages and make
sure it is not put into operation unless it is in perfect condition. On detecting any faults
please inform your superior immediately!
Before starting the engine remove any unnecessary material and/or objects from the
working range of the installation/engine.
Before starting the engine check and make sure that all safety devices are working
properly!
1.2 Basic safety measures for servicing and maintenance
Before performing any maintenance or repair work make sure the working area of the
engine has been closed to unauthorized persons. Put on a sign warning that maintenance
or repair work is being done.
Before performing any maintenance or repair work switch off the master switch of the
power supply and secure it by a padlock! The key must be kept by the person perform-
ing the maintenance and repair works.
Before performing any maintenance and repair work make sure that all parts of engine
to be touched have cooled down to ambient temperature and are dead!
Refasten loose connections!
Replace at once any damaged lines and/or cables!
Keep the cabinet always closed. Access should be permitted only to authorized persons
having a key or tools.
Never use a water hose to clean cabinets or other casings of electric equipment!
1.3 Before putting an installation into service after maintenance and
repair works
Check on all slackened screw connections to have been tightened again!
Make sure the control linkage has been reattached and all cables have been reconnected.
Make sure all safety devices of the installation are in perfect order and are working
properly!

2 General
Digital Governor Basic System PANDAROS IV 3
2General
The HEINZMANN Digital Governors of the PANDAROS series have been designed as speed
governors for diesel and gas engines with low and medium power. In addition to their primary
purpose of controlling speed, these governors are capable of performing some other tasks and
functions.
The control system consists of the control unit, the actuator, the setpoint adjusters, the sen-
sors, and the connection cables.
The control unit includes the control electronics. At the core of the control unit is a very fast
and powerful 16 bit microprocessor. The actual controller program on which the processor
operates, is permanently stored in a FLASH-EPROM.
The current engine speed is sensed bya magnetic pick-up on the flywheel or a measuringwheel.
One temperature sensor can measure the engine temperature and can cause changings of gov-
ernor parameters or alarm messages.
The speed setpoint, additional sensor inputs and the inputs for the analogue accessory are de-
pending on variations.
In the case of the DC 6-00 variant, which offers the largest functional scope and flexibility,
the user must configure all inputs and outputs themselves.
With regard to the other variants, no additional outputs are provided aside from the error mes-
sage output. In certain cases, the inputs are already specifically pre-configured and all pa-
rameters that are not required for the respective application are omitted so as to maintain a
clearer overview of the controller and to make start-up easier to perform.
With the serial interface ISO 9141 resp. RS 232 is communication to other devices possible.

3 Functions
4 Digital Governor Basic System PANDAROS IV
3Functions
The HEINZMANN digital controllers from the PANDAROS series are speed governors in
which, depending on the variant in question, further variant-specific functions are available in
addition to the speed control and the general functions.
3.1 General functions
a) Start fuel adjustment
For setting start fuel, minimum start quantity or maximum start quantity may alterna-
tively be selected. If necessary either can be configured in dependence of temperature.
Furthermore, variable start quantity can be provided, by which start quantity is automat-
ically increased during start-up.
b) Speed ramps
For applications where speed is not supposed to respond to changes of setpoint values
as fast as possible, a speed ramp is available. According to requirements, it may be par-
ametrized separately for increasing or decreasing speed. In addition, a separate speed
ramp is provided for start-up which will make the engine ramp slowly to operating
speed after starting.
c) All speed governing with adjustable droop
Several applications e.g. generators in parallel without HEINZMANN load measuring
unit might require speed control with droop (proportional band). The droop can be ad-
justed as desired. With droop adjusted to 0, the governor operates in isochronous mode.
d) Setting the speed range
The minimum and maximum speed adjustable by the (external) setpoint, can be para-
metrized.
e) Engine stop
When the switch input for engine shutdown is activated, the governor will cause the ac-
tuator to fully pull to stop direction until the engine has stopped.
f) Overspeed protection
An overspeed point can be parametrized. If this point is overcome, the governor will is-
sue an alarm and the actuator will fully pull to stop direction.
g) Gradient monitoring
The engine speed signal can be monitored for a permissible change speed (gradient).

3 Functions
Digital Governor Basic System PANDAROS IV 5
h) Correction of PID parameters
To optimize the dynamics for every operating point, the PID parameters may be cor-
rected in dependence of speed, temperature and load by means of freely programmable
stability maps.
i) Speed dependent fuel limitation
It is possible to program fuel limitation curves in dependence of speed so that for all
speeds there can be torque reduction as is admissible for the engine or desired by the us-
er.
j) Temperature dependent idling speed and fuel limitation
At low temperatures, the engine can be run at some higher idling speed. With the engine
warming up, idling speed is reduced to its normal value. It is possible to program fuel
limitation curves in dependence of temperature so that for every temperature there will
be torque reduction available as is admissible for the engine or desired by the user.
k) Operating hour meter
The operating hours when the engine is turning (speed is detected) will be added.
l) Failure diagnosis and display
If a sensor or the actuator is at fault, an alarm is issued and there will be a change-over
to emergency operation if so provided or an engine shutdown. Internal errors get detect-
ed also and they will be stored as all other failures. All failures can be read out with an
external hand programmer or with a communication program on a PC or laptop with
communication cable.
m)Communication
An ISO 9141 interface is provided to enable communication with a Heinzmann com-
munication tool.

3 Functions
6 Digital Governor Basic System PANDAROS IV
3.2 Variation specific additional functions
3.2.1 Variation DC 6-01 (Standard Generator)
(refer to connection diagram DC 6-01)
The speed setpoint is realized with two push buttons: increase speed and decrease speed.
3.2.2 Variation DC 6-02 (Standard General)
(refer to connection diagram DC 6-02)
The speed setpoint is given by an analogue setpoint source (voltage source 0 … 5 V,
current 4 … 20 mA or potentiometer 5 k) and one switch input for fixed speed.
3.2.3 Variation DC 6-03 (Extended Generator)
(refer to connection diagram DC 6-03)
The assignment of the function and the calibration of the inputs must be performed by
the customer themselves in this context. The following functions are also available, alt-
hough the limited number of inputs means that they cannot all be used simultaneously:
a) Free configurability of inputs
Five digital inputs are available in total, up to three of which can also optionally be
configured as analogue inputs featuring 0 … 5 V or 4 … 20 mA if required.
b) Speed offset selection
All analogue or digital control signals that are conventionally used on the market for
the purpose of generating a speed offset selection for a superordinate generator con-
trol may be applied. This naturally also includes signals from ComAp, Deapsea,
Deif, Kuhse, Stucke, etc. as well as analogue additional devices from Heinzmann.
c) Communication with Heinzmann generator management DGM-02
If the corresponding parameter settings have been made, the digital generator man-
agement from Heinzmann (THESEUS DGM-02) can be connected via CAN bus.
d) Idling speed
It is possible to switch to the idling speed for a warm-up or cool-down phase.
e) P-range changeover
It is possible to switch between two different P-ranges.
f) Speed range changeover
It is possible to switch between two different speed ranges.

3 Functions
Digital Governor Basic System PANDAROS IV 7
g) Manual/automatic mode
It is possible to switch between manual and automatic mode.
h) Generator switch
In order to make quicker adjustments when opening the power generator switch, it is
possible to activate a special function that queries the status of the power generator
switch. This status can be assigned to a digital input.
i) Deleting errors
The current errors can be deleted by pressing an assigned button at a digital input.
j) Automatic calibration of the actuator
After replacing the control device or the actuator, the feedback of the actuator can be
recalibrated by pressing an assigned button (actuator and control device are adjusted
in line with one another).
3.2.4 Variation DC 6-05 (Extended General, especially vehicle)
(refer to connection diagram DC 6-05)
a) Speed setpoint
The speed setpoint is given by an analogue setpoint source (voltage source 0 … 5 V,
current 4 … 20 mA or potentiometer 5k) and a switch input for fixed speed.
b) Boost pressure sensor
An analogue input is already specified for use with a boost pressure sensor. The input
can be configured for a 0 … 5 V or 4 … 20 mA signal.
For turbocharged engines, fuelling can be reduced to achieve smokeless operation
whenever there is no boost pressure (e.g., during start-up or on load changes). The
respective limit curves can be programmed accordingly.
c) Oil pressure sensor
An analogue input is already specified for use with an oil pressure sensor. The input
can be configured for a 0 … 5 V or 4 … 20 mA signal.
For the purpose of oil pressure monitoring, speed/pressure dependent limit curves
can be provided. If oil pressure is low, an alarm is issued; if oil pressure continues to
drop, the engine is shut down.
d) Idle-/Maximum speed governor
The governor may also be adjusted as an idle/max speed governor.

3 Functions
8 Digital Governor Basic System PANDAROS IV
3.2.5 Variation DC 6-00 (ful flexibility)
This variant is not pre-configured and contains all the previously described functions of
the different variants.
The only option that is not provided is that of communication with the digital generator
management THESEUS via CAN bus.
This variant continues to feature the following additional functions:
a) Second speed sensor
A digital input can be reconfigured in order to support the use of a second speed sen-
sor (featuring a Hall design).
b) Second fixed speed
It is possible to assign a second fixed speed.
c) Setpoint selection via notches
For simple applications for locomotive operation, the speed setpoint selection can be
performed via notches. In this context, the bit combinations of up to four digital in-
puts can be assigned to corresponding speed setpoints.
d) Changeover between limiting curves
It is possible to switch between two different limiting curves.
e) Jet Assist
A Jet Assist function can also be activated in order to perform quick adjustments for
load compensation at low levels of boost pressure.
f) Analogue outputs
The multifunctional ports (terminals 1 and 2) can also be configured as analogue
outputs featuring 4 … 20 mA. In this way, every available analogue measured value
or calculated setpoint can be output.
g) PWM outputs
The multifunctional ports (terminals 1 and 2) can also be configured as PWM out-
puts. In this way, every available analogue measured value or calculated setpoint can
be output.
h) Digital outputs
The multifunctional ports (terminals 1 and 2) can also be configured as digital out-
puts. This makes it possible for every digital measured value to be output.

3 Functions
Digital Governor Basic System PANDAROS IV 9
i) PWM inputs
The multifunctional ports (terminals 1 and 2) and digital input 3 can also be config-
ured as PWM inputs. In this way, every available analogue measured value or calcu-
lated setpoint can be output.
j) PE module adjustment
Via CAN bus, it is possible to communicate with an additional PE module of type
DC 6. This can then control a second actuator and provide additional inputs and out-
puts that can be configured from the speed governor. The typical application in this
regard is the control of V-type engines with two actuators.
3.2.6 Variation DC 6-06 (positioner)
This variant does not feature an integrated speed governor. In this context, the corre-
sponding actuator is controlled via an actuator setpoint position signal received from an
external source. This variant is described in a dedicated publication.

4 Further information
10 Digital Governor Basic System PANDAROS IV
4Further information
This publication describes in detail the technical data and connections of the control electron-
ics, of the sensors, of the setpoint adjusters and of the actuators.
The functions of the different adjustment parameters and characteristics are described in detail
in the manual
Basic Information Control device for conventional injection Manual DG 07 001-e
The mode of operation of the communication program DcDesk 2000 is described in detail in
the manual
Operation Instructions of Communication Program DcDesk 2000,
Manual-No. DG 00 003-e

5 Block diagram
Digital Governor Basic System PANDAROS IV 11
5Block diagram
Fig. 1: Block diagram
According to the different types, there are not all functions and inputs available!
-DC
24 V - Power Supply
Switch Inputs
Analogue Setpoint Adjuster
Interface RS 232
Pressure Sensors
Temperature Sensor
Micro Controler
Actuator
Drive
DC
EEP-
ROM
ISO9141
Speed Sensor
Watch-
dog 1 Watch-
dog 2 Watch-
dog 3
DC 6 Board
5 V
Actuator Position
Sensing
M
Integrated Hand Programmer
Failure Lamp
Analogue
Synchronizer
Analogue
Load Measuring Unit
LCD-Display
WINDOW
FUNCTION
ESCAPE
ENTER

6 Sensors
12 Digital Governor Basic System PANDAROS IV
6Sensors
6.1 Overview
Sensor
Speed
Coolant
Temperature
Oil Pressure
Boost Pressure
HZM - Designation
IA ..
TS 01-28-PT1000
DSO 01-6
DSO 01-10
DSL/G 0..-2
DSL/G 0..-5
DSL/G 0..-10
Connection
SV 6-IA-2K
2 pole
SV 6-IA-2K
2 pole
DIN 43650 A
2 line system
DIN 43650 A
2 line system
Measuring Procedure
inductive, active
PT1000, passive
active
active
Measuring Range
50 ... 9.000 Hz
-50 ... +150°C
0 ... 6 bar
0 ... 10 bar
0 ... 2 bar
0 ... 5 bar
0 ... 10 bar
Supply Voltage
Range
passiv
10 ... 34 V DC
12 ... 36 V DC
Output Signal Range
0 ... 10 V AC
ca. 700 ... 1500 Ohm
4 ... 20 mA
4 ... 20 mA
Operating Tempera-
ture Range
-55 ... +120°C
-50 ... +150°C
-25 ... +125°C
-40 ... +100°C
In order to ensure maximum flexibility with regard to the sensors, the minimum/ maximum
current values and the measuring ranges of the pressure and temperature sensors have been
provided programmable.
This manual suits for next models
4
Table of contents
Other Heinzmann Control Unit manuals
Popular Control Unit manuals by other brands
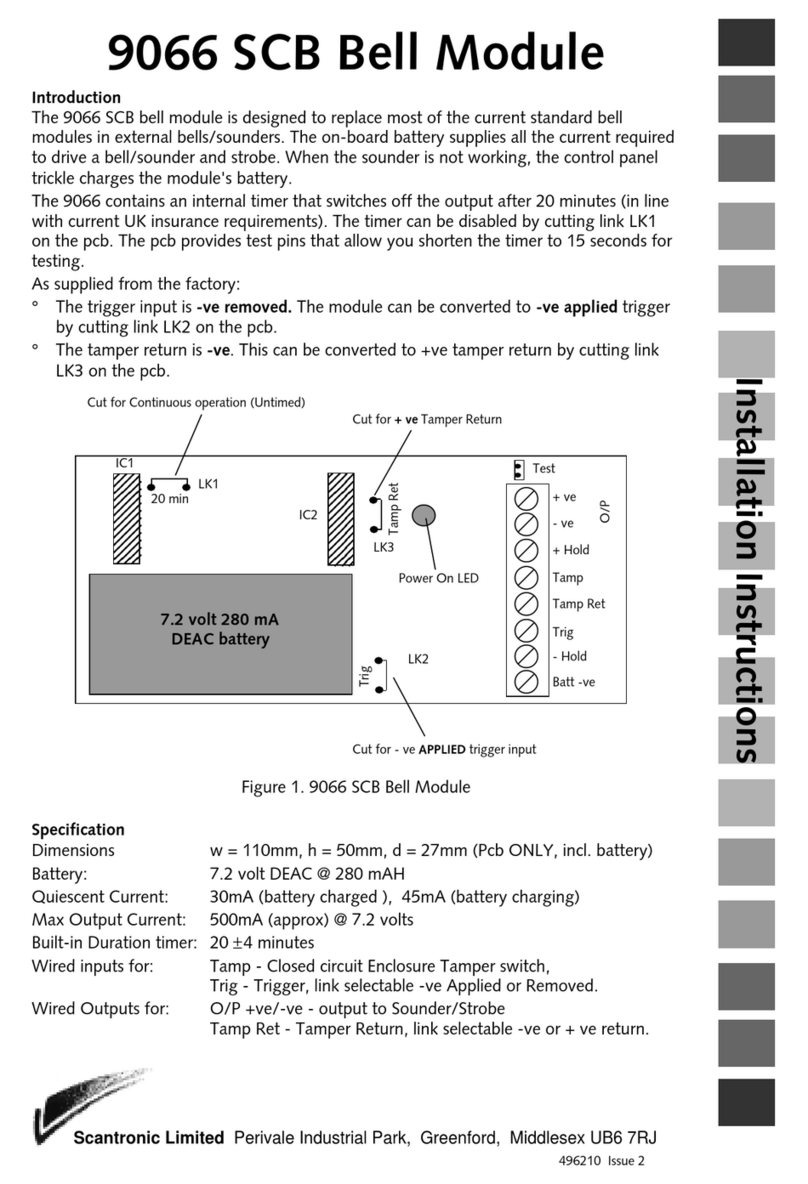
Scantronic
Scantronic 9066 SCB installation instructions
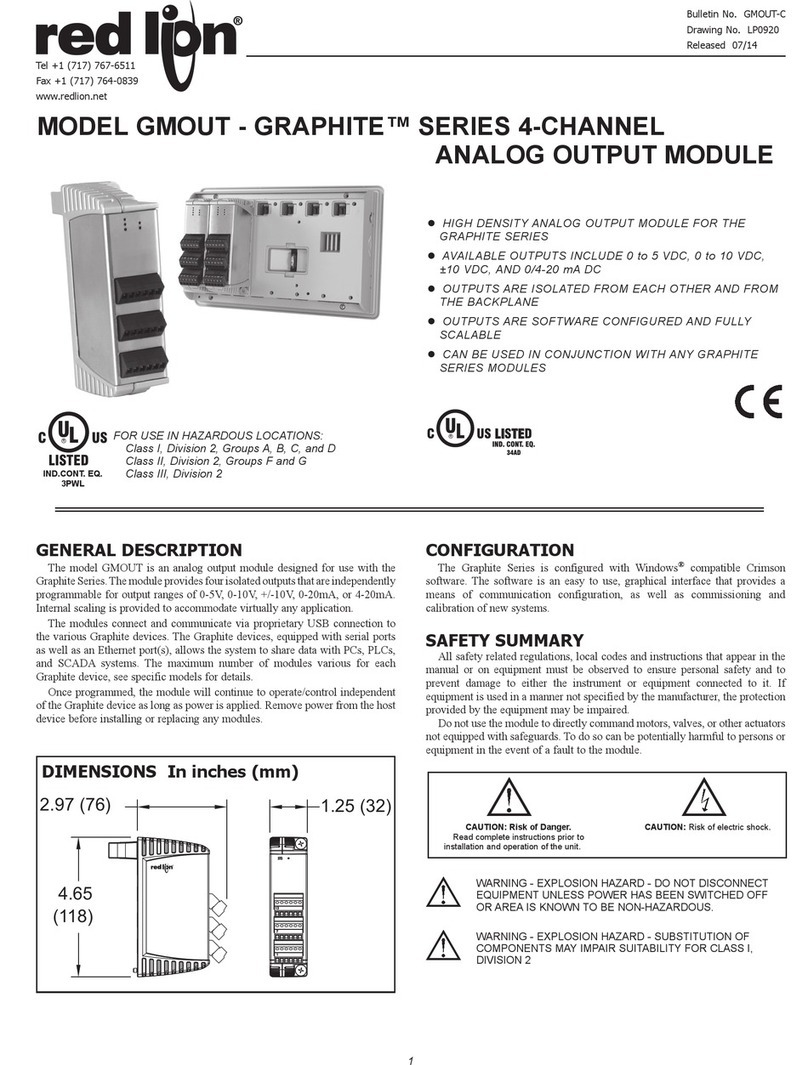
red lion
red lion Graphite Series General description

Flow Safe
Flow Safe F70U Series Installation, operation & maintenance manual
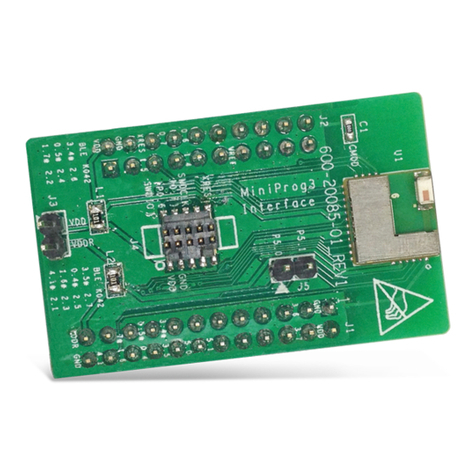
Cypress
Cypress EZ-BLE PRoC manual
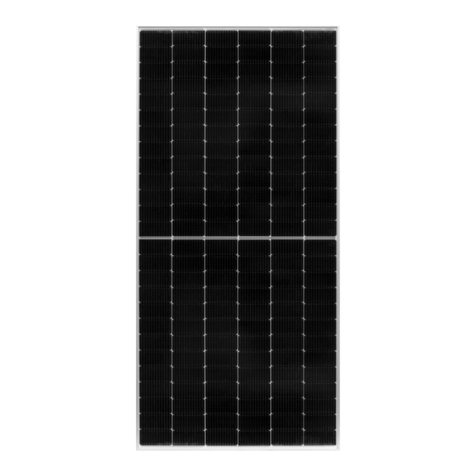
Qcells
Qcells Q.PEAK DUO-G10.X Series Operating and maintenance instructions
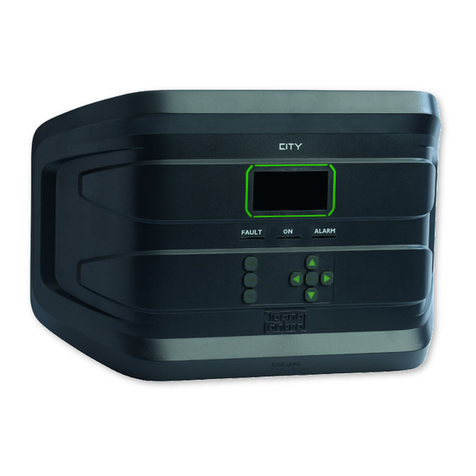
Tecnocontrol
Tecnocontrol CITY CE408P user manual
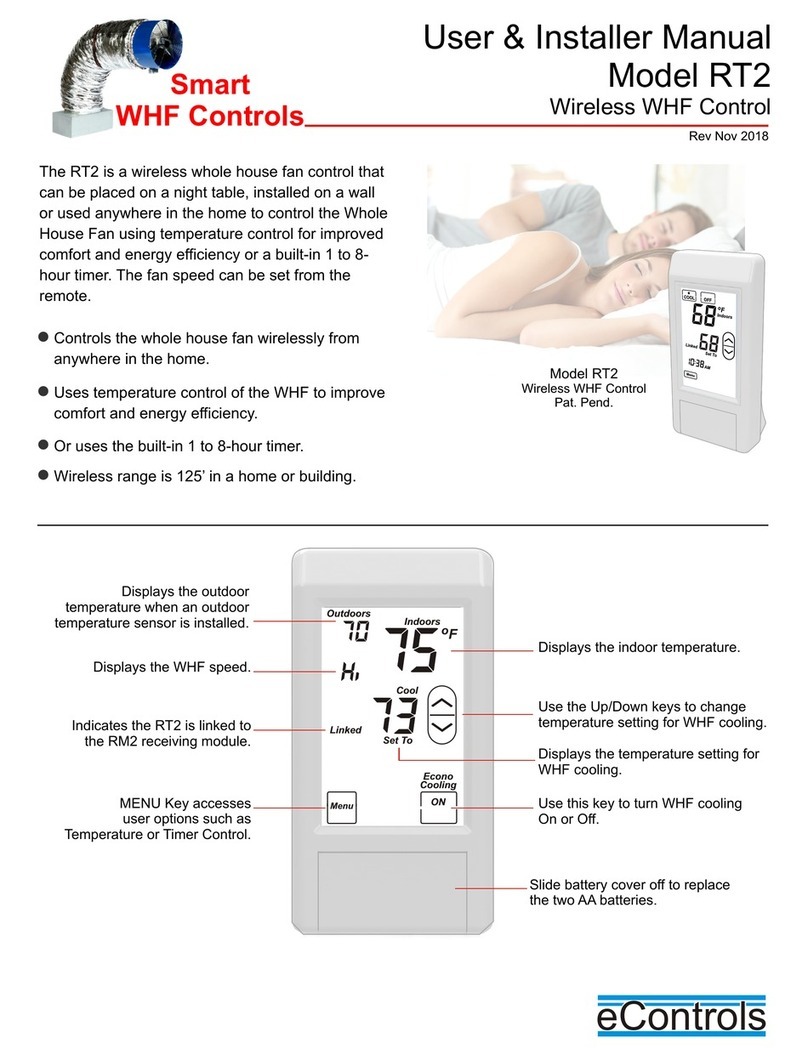
eControls
eControls RT2 User& installer's manual

System air
System air fantech ECO-FEEL 414729 Installation and operation instructions

flakt woods
flakt woods KSOM Installation and connecting instructions

Moe's
Moe's MS-104 user manual
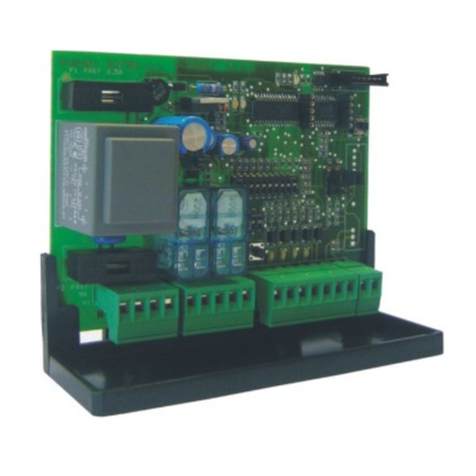
GiBiDi
GiBiDi SR100 Instructions for installations

EMU
EMU ProteusX Operation manual