Hiwin EM1 Series User manual

MC03UE01-2305_V1.1
User Manual
EM1 Series AC Servo Motors
EM1-01-1-EN-2307-MA
www.hiwin.de

User Manual Imprint
EM1 Series AC Servo Motors EM1-01-1-EN-2307-MA Page 2of 80
Imprint
HIWIN GmbH
Brücklesbünd 1
D-77654 Offenburg, Germany
Phone +49 (0) 7 81 9 32 78 - 0
Fax +49 (0) 7 81 9 32 78 - 90
info@hiwin.de
www.hiwin.de
All rights reserved.
Complete or partial reproduction is not permitted without our permission.
These assembly instructions are protected by copyright. Any reproduction, publication in whole
or in part, modification or abridgement requires the written approval of HIWIN GmbH.

User Manual Contents
EM1 Series AC Servo Motors EM1-01-1-EN-2307-MA Page 3of 80
Contents
1About this Manual............................................................... 4
1.1 General precautions ............................................................. 4
1.2 Safety instruction ............................................................... 8
1.3 Copyright...................................................................... 10
1.4 Manufacturer information ....................................................... 10
1.5 Product monitoring ............................................................. 10
2Basic safety information........................................................ 11
2.1 Overview ...................................................................... 11
2.2 Basic safety notices ............................................................ 11
2.3 Reasonably foreseeable misuse ................................................. 11
2.4 Conversions and modifications .................................................. 11
2.5 Residual risks .................................................................. 12
2.6 Personnel requirements......................................................... 12
2.7 Protective equipment ........................................................... 12
2.8 Labels on servo motor .......................................................... 13
3Product description ............................................................ 14
3.1 Servo motor description ........................................................ 14
3.2 Main components of servo motor ................................................ 15
3.3 Order code .................................................................... 16
4Transport and setup ............................................................ 40
4.1 Delivery ....................................................................... 40
4.2 Transport to the Installation Site ................................................. 41
4.3 Requirements at the installation site ............................................. 41
4.4 Storage ....................................................................... 42
4.5 Unpacking and setup ........................................................... 42
5Assembly and connection....................................................... 43
5.2 Electrical installation ........................................................... 51
6Commissioning ................................................................ 59
7Maintenance and cleaning ...................................................... 61
7.1 Maintenance................................................................... 61
7.2 Cleaning....................................................................... 62
8Disposal....................................................................... 64
9Troubleshooting ............................................................... 66
10 Declaration of incorporation .................................................... 69
11 Appendix ...................................................................... 70
11.1 Glossary....................................................................... 70
11.2 Unit conversion ................................................................ 71
11.3 Tolerances and hypotheses ..................................................... 72
11.4 Supplementary formula ......................................................... 73
11.5 Optional accessories ........................................................... 74
11.6 Customer request form ......................................................... 77

User Manual About this Manual
EM1 Series AC Servo Motors EM1-01-1-EN-2307-MA Page 4of 80
1About this Manual
This manual explains the features of the product, possibilities for use, operating conditions and
operation limits of E1 series AC servo motor.
This manual is only intended for the use of trained specialists in automation and control
engineering who are familiar with the applicable national standards. It is the duty of the
technical personnel to use the manual published at the respective time of each installation and
commissioning.
The responsible staff must ensure the application or use of the products described satisfy all
the requirements for safety, including all the relevant laws, regulations guidelines and
standards.
Be sure to refer to this manual and to keep this manual in a location where it can be accessed
at any time.
Documents
For configuring, you require the catalog or manual as print version or online with the following
website.
https://www.hiwin.de/en/service/downloads
1.1 General precautions
Before using the product, please carefully read through this manual. HIWIN is not responsible
for any damage, accident or injury caused by failure in following the installation instructions and
operating instructions stated in this manual.
Before installing or using the product, check the package to see if it has been damaged or
broken. If there is any damage, please contact the sales representatives of HIWIN or agents
or dealers.
Check if the cables have been damaged and if they can be used for connection.
Read the performance specifications indicated on the label or in the enclosed document
before installation. Install the product based on the limit of the performance with
installation guide and only use genuine spare parts from HIWIN.
Please comply with the instructions and regulations when using the product.
AC servo motor must be operated within the specified performance limits (see technical
information and the approval drawing).
AC servo motor must only be used for the intended purpose as described. Any other use of
the AC servo motor shall be considered as improper usage. HIWIN is not responsible for any
product damage or personal injury caused by this.
For safe operation of the AC servo motor, appropriate safety precautions must be taken to
protect the motor against overload.
Servo motors must not be used outdoors or in potentially explosive environments.
Do not disassemble or modify the product by yourselves. The product has been designed
with structural calculations, computer simulations, and physical testing. Do not
disassemble or modify the product without the permission of professionals.
Children are not allowed to operate this product.
People who have physical or mental disease or who do not have experience with the use of
related products should not be allowed to use this product unless they are accompanied by
supervisors or personnel familiar with the product to ensure their safety.
Damaged products must not be installed or operated.
If the information of registration does not match with your purchasing or if there are any
questions related to the product, please contact the sales representatives of HIWIN or
agents or dealers.

User Manual About this Manual
EM1 Series AC Servo Motors EM1-01-1-EN-2307-MA Page 5of 80
HIWIN offers 1-year warranty for the product. The warranty does not cover damage caused by
improper usage (refer to the precautions and instructions stated in this manual) or natural
disaster.
Protective requirement
Table 1.1:
Operating Phase Personal Protective Equipment
Normal Operation In the vicinity of AC servo motor, the following personal protective
equipment is required:
Safety shoes
Protective helmet
Protective gloves
Cleaning When cleaning AC servo motor, the following personal protective
equipment is required:
Safety shoes
Protective helmet
Protective gloves
Protective goggles
Maintenance When carrying out maintenance and repairs, the following personal
protective equipment is required:
Safety shoes
Protective helmet
Protective gloves
Installation precautions
Warning! Risk of personal injury or damage to property.
Follow the technical instruction and install the AC servo motor at a location with bearable
load.
When installing, do not impact or strike the motor.
When installing, prevent foreign objects from entering the product.
The spacing for installing the AC servo motor, servo drive, controller and other machines
should follow specifications.
When installing, please set up an external emergency stop loop that can immediately stop
the product and cut off power.
Wiring precautions
Warning! Risk of personal injury or damage to property.
Ensure wiring is correctly performed. Otherwise, it may lead to product malfunction or
burn-out. There could be a risk of injury or fire.
Before using the product, carefully read through the specification noted on product label,
and ensure the product is used with power supply specified in product requirement.
Check if the wiring is correct. Incorrect wiring may make the AC servo motor operate
abnormally, or even cause permanent damage to the motor.
Select extension cable with shield. The shield must be grounded.
Caution! Risk of personal injury.
Ensure the AC servo motor is correctly grounded.
The resistance of grounding terminal connection shall be less than 10 Ωwhen the input
voltage of the drive is 400 V; less than 50 Ωwhen it is 220 V; less than 100 Ωwhen it is
110 V.

User Manual About this Manual
EM1 Series AC Servo Motors EM1-01-1-EN-2307-MA Page 6of 80
Operation precautions
Warning! Risk of personal injury or damage to property.
Please follow the requirements of installation direction.
Avoid excessive friction when the motor is running.
Ensure there is no object in the motion range of the system.
Before starting the AC servo motor, ensure the main switch is on.
Before transmitting electricity, ensure there is at least one ground wire connecting to all
electrical products.
Do not directly touch the motor parts after the AC servo motor is assembled.
Do not operate the product in an environment that exceeds its rated load.
If any abnormal odor, noise, smoke, temperature rise or vibration is detected, stop the AC
servo motor and cut off the power immediately.
Storage precautions
Caution! Risk of damage to property.
Follow the precautions of AC servo motor storage conditions.
Do not store the product in an inflammable environment or with chemical agents.
Do not store the product in a place with humidity, dust, harmful gases or liquids.
Clean and protect used AC servo motor before storage.
When storing AC servo motor, attach signs warning of magnetic fields.
Storage conditions must comply with EN 60721-3-1(Refer to the table below for Storage
conditions)
Motor can be stored for up to two years indoor with the following conditions:
–Dry
–Dust-free
–No vibration
–Good ventilation
–Resistance to extreme weather
–Indoor air does not contain corrosive gases
–Prevent motor vibration and moisture
If no dry storage environment is available, the following measures need to be taken:
–Wrap the motor with moisture-absorbing material, and then seal the motor.
–Put desiccant in the sealed package; the desiccant needs to be checked and replaced if
necessary.
Check the AC servo motor regularly.
Storage Conditions are listed as below:
Environmental parameter Unit Value
Air temperature (°C) -15 − 70
Relative humidity (%) 20 − 80
Rate of change of temperature (°C/min) 0,5
Air pressure kPa 70 − 106
Condensation - Not allowed
Formation of ice - Not allowed
Store the motor in an environment with good protection. (indoor/factory)

User Manual About this Manual
EM1 Series AC Servo Motors EM1-01-1-EN-2307-MA Page 7of 80
Transportation precautions
Caution! Risk of personal injury or damage to property.
Follow the precautions of AC servo motor transport conditions.
Carefully move the product to avoid damage.
Do not apply excessive force to the product.
Do not stack the product to avoid collapse.
Transport conditions must comply with EN 60721-3-1 (Refer to the table below for
transportation conditions).
Transportation Conditions
Environmental parameter Unit Value
Air temperature (°C) -15 − 70
Relative humidity (%) 20 − 80
Rate of change of temperature (°C/min) 0,5
Air pressure kPa 70 − 106
Condensation - Not allowed
Formation of ice - Not allowed
Store the motor in an environment with good protection. (indoor/factory)
Maintenance precautions
Warning! Risk of personal injury or damage to property.
Do not disassemble or modify the product.
If the product malfunctions, do not repair the product by yourselves, please contact HIWIN
for repairs.
Disposal precautions
Warning! Risk of personal injury or damage to property.
If it is not correctly performed, it may cause personal injury or damage to material.
If AC servo motor or related components (especially the rotor with strong magnets) are not
handled correctly, it may cause personal injury, death or property damage.
Please ensure that the AC servo motor and related components are disposed correctly.

User Manual About this Manual
EM1 Series AC Servo Motors EM1-01-1-EN-2307-MA Page 8of 80
1.2 Safety instruction
Carefully read through this manual before installation, transportation, maintenance and
examination. Ensure the product is correctly used.
Carefully read through electromagnetic (EM) information, safety information and related
precautions before using the product.
Safety precautions in this manual are classified into “DANGER”, “WARNING”and “
CAUTION”.
Danger!Imminent danger!
Indicates that death or severe personal injury will result if proper precautions are not taken.
Warning! Potentially dangerous situation!
Indicates that death or severe personal injury may result if proper precautions are not taken.
Caution! Moderate danger!
Indicates that minor personal injury can result if proper precautions are not taken.
Warning Signs
No access for people
with active implanted
cardiac devices!
Substance hazardous tot
he environment!
Warning!
Warning of crushing of
hands!
Warning of electricity!
Warning of hot surface!
Warning of magnetic
field!
Mandatory Signs
Wear head protection!
Refer to user manual!
Wear protective gloves!
Disconnect before
carrying out
maintenance or repair.
Wear safety footwear!
Lifting point.
Connect an earth
terminal to the ground!

User Manual About this Manual
EM1 Series AC Servo Motors EM1-01-1-EN-2307-MA Page 9of 80
Danger!Danger from operation!
Do not repair the product by yourselves if something abnormal occurs. The product can
only be repaired by HIWIN qualified technicians or sent back to HIWIN for repairs.
Do not apply the load exceeding the specification standards to the product.
Do not change product parts or remove product screws without authorization, or the
product will be damaged. HIWIN is not responsible for any damage, accident or injury
caused by this.
Do not touch the product’s keyway with hands.
Do not touch the rotating parts of the product when it is operating.
Danger! Danger from hot surface!
Do not place flammable materials around the AC servo motor, servo drive or regenerative
resistor.
Do not use the product in an environment with corrosive, flammable gases or flammable
materials.
Do not touch the surface of the AC servo motor, servo drive or regenerative resistor which
will be hot while operating.
Danger!Danger from electrocution!
To prevent risk of electric shock, do not use damaged cables with excessive pressure or
press and clamp the wire overly.
Do not remove the cover, cables, or connector from AC servo motor while the power is ON.
Do not touch wires or operate the equipment with wet hands.
Do not use when wires are in contact with oil or water.
Danger! Danger from strong magnetic fields!
Strong magnetic fields around AC servo motor pose a health risk to persons with implants
(e.g., cardiac pacemakers) that are affected by magnetic fields.
People with implants are affected by magnetic fields should maintain a safe distance of at
least 1 m from the AC servo motor.
Warning! Risk of personal Injury or damage to property.
Read this manual and follow it carefully before using the product.
If the product is used with excessive load, it may rise the temperature of the motor
housing.
There may be electromagnetic compatibility (EMC) problems in other environments.
Do not use the product in an environment where it may be shocked. Do not directly strike
the shaft or encoder, as hitting or pounding. HIWIN is not responsible for any damage,
accident or injury caused by this.
Do not pick up or place the motor only by pulling its cable or shaft.
Since AC servo motor contains a precision encoder, please take sufficient measures to
prevent electromagnetic interference or abnormal temperature change while using.
The absolute encoder has an attached magnetic sensor. Do not operate magnetic
equipment on the top of the encoder cover or around the encoder.

User Manual About this Manual
EM1 Series AC Servo Motors EM1-01-1-EN-2307-MA Page 10 of 80
Caution! Risk of personal injury or damage to property.
Please follow the requirements of installation direction.
Follow the technical instruction and install the AC servo motor at a location with bearable
load.
When installing, do not impact or strike the motor.
When installing, prevent foreign objects from entering the product.
The spacing for installing the AC servo motor, servo drive, controller and other machines
should follow specifications.
When installing, please set up an external emergency stop loop that can immediately stop
the product and cut off power.
Caution! Risk of physical damage to watches and magnetic storage media.
Strong magnetic force may destroy watches and magnetizable data storage media near the
AC servo motor!
Do not bring watches or magnetizable data storage media in the vicinity (<300 mm) of the
AC servo motor!
1.3 Copyright
This user manual is protected by copyright. Any reproduction, publication in whole or in part,
modification or abridgement requires the written approval of HIWIN.
Note
HIWIN reserves the right to change the contents of this manual or product specifications
without prior notice.
1.4 Manufacturer information
Company HIWIN GmbH
Address Brücklesbünd 1
77654 Offenburg
Tel +49 (0) 781 / 9 32 78 - 0
Fax +49 (0) 781 / 9 32 78 - 90
Technical Customer Service +49 (0) 781 / 9 32 78 - 77
Technical Customer Service Fax +49 (0) 781 / 9 32 78 - 97
Mail support@hiwin.de
Website www.hiwin.de
1.5 Product monitoring
Please inform HIWIN, the manufacturer of AC servo motor, of:
Accidents.
Potential sources of danger in AC servo motor.
Anything in this user manual which is difficult to understand.

User Manual Basic safety information
EM1 Series AC Servo Motors EM1-01-1-EN-2307-MA Page 11 of 80
2Basic safety information
2.1 Overview
This chapter explains safety notices and risk management approach of using the product.
2.2 Basic safety notices
Danger! Danger from strong magnetic fields!
Strong magnetic fields around AC servo motor pose a health risk to persons with implants
(e.g., cardiac pacemakers) that are affected by magnetic fields.
People with implants are affected by magnetic fields should maintain a safe distance of at
least 1 m from the AC servo motor.
Danger!Danger from operation!
If an abnormality occurs with this product, do not attempt to repair it yourself. This
product should only be repaired by this company’s qualified technical personnel or the
product should be sent back to this company for repairs.
Do not use the servo motor for loads that exceed its specification standards.
Do not change servo motor parts or remove motor screws on your own because this can
damage the servo motor. This company will not be responsible for any damage, accidents,
or injuries caused by products that have been improperly tampered with.
Do not touch the keyway of motor with hands.
Never touch the rotating parts of the motor when the motor is operating.
Danger! Danger from hot surface!
Do not place flammable materials around the AC servo motor, servo drive or regenerative
resistor.
Do not use the product in an environment with corrosive, flammable gases or flammable
materials.
Do not touch the surface of the AC servo motor, servo drive or regenerative resistor which
will be hot while operating.
Caution! Risk of physical damage to watches and magnetic storage media.
Strong magnetic force may destroy watches and magnetizable data storage media near the
AC servo motor!
Do not bring watches or magnetizable data storage media in the vicinity (<300 mm) of the
AC servo motor!
2.3 Reasonably foreseeable misuse
Warning! Risk of damage to property.
AC servo motors must not be operated:
Outdoors.
In potentially explosive atmospheres.
2.4 Conversions and modifications
Warning! Risk of personal injury or damage to property.
Conversions or modifications to AC servo motor are prohibited.

User Manual Basic safety information
EM1 Series AC Servo Motors EM1-01-1-EN-2307-MA Page 12 of 80
Modifications of AC servo motor are not permitted. Please contact HIWIN for special request.
2.5 Residual risks
Caution! Personal injury or damage to property.
During normal operation, there are no residual risks associated with AC servo motor
components. Warnings about risks that may arise during commissioning, maintenance and
repair work are provided in the relevant sections.
2.6 Personnel requirements
Operation staff are trained in the safe operation practices for linear actuator systems and
have fully read and understood this user manual.
Maintenance staff maintain and repair linear actuator systems in such a way that they pose
no danger to people, property or the environment.
Qualified personnel are those who, based on their training and experience, are capable of
identifying risks and avoiding potential hazards when working with these products.
Caution!
Only authorized and competent ones may carry out work on AC servo motor components.
They must be familiar with the safety equipment and regulations before starting work.
Activity Qualification
Commissioning Trained specialist personnel of the operator or manufacturer
Normal Operation Trained personnel
Cleaning Trained personnel
Maintenance Trained specialist personnel of the operator or manufacturer
Repairs Trained specialist personnel of the operator or manufacturer
2.7 Protective equipment
Possible safety equipment/measures:
Personal protective equipment in accordance with regional regulations.
Zero-contact protective equipment.
Mechanical protective equipment.

User Manual Basic safety information
EM1 Series AC Servo Motors EM1-01-1-EN-2307-MA Page 13 of 80
2.8 Labels on servo motor
Nameplate
1 Product name 6 Serial No.
2 Motor type 7 Company address
3 Part No. 8 CE mark
4 Input spec. 9 UL mark
5 Output spec. 10 QR mark
Location of Safety Symbols on Motor
1
2
3
4
5
6
7
8
9
10
Anti-knocking
Name plate
High

User Manual Product description
EM1 Series AC Servo Motors EM1-01-1-EN-2307-MA Page 14 of 80
3Product description
3.1 Servo motor description
AC servo motor is a high speed and low torque motor. It can control rotating motor, and control
the current, speed, and position through the servo drive. It has the characteristics of high
precision, low noise, high response, and high instantaneous output.
New developed AC servo motor can be applicable to FPD, semiconductor, laser cutting, PCB,
machine tool, 3C electronics, energy, automobile, measuring/inspection industry, and related
automation industry. Compared with the last generation of FR series, EM1 servo motor
enhances maximum speed, encoder resolution, compact size, and ensure speedy settling,
stability, tuneless function with dynamic payload by working with brand-new E1 servo drive, that
can effectively improve production efficiency.
50 W – 750 W AC servo motor appearance are as bellowing.
1 Encoder connector 8 Front cover
2 Encoder cable 9 Oil seal
3 Power cab 10 Shaft (rotor)
4 Encoder cab 11 Key
5 Encoder cover (encoder) 12 Power cable
6 Brake cover (brake) 13 Power connector
7 Motor cover (stator)

User Manual Product description
EM1 Series AC Servo Motors EM1-01-1-EN-2307-MA Page 15 of 80
1 kW – 2 kW AC servo motor appearance are as bellowing.
1 Power connector 7 Motor cover (stator)
2 Brake connector 8 Front cover
3 Encoder connector 9 Oil seal
4 Encoder cover (encoder) 10 Shaft (rotor)
5 Brake cover (brake) 11 Key
6 Back cover
3.2 Main components of servo motor
Combination of HIWIN AC servo motors and servo drives.
Servo Motor Model Rated Output Rated Torque Rated Speed Servo Drive Model
EM1-C-M-05-2-⎕-⎕-0-⎕50 W 0,16 Nm 3.000 rpm ED1⎕-⎕⎕-0422-A⎕
EM1-C-M-10-2-⎕-⎕-0-⎕100 W 0,32 Nm 3.000 rpm ED1⎕-⎕⎕-0422-A⎕
EM1-C-M-20-2-⎕-⎕-0-⎕200 W 0,64 Nm 3.000 rpm ED1⎕-⎕⎕-0422-A⎕
EM1-C-M-40-2-⎕-⎕-0-⎕400 W 1,27 Nm 3.000 rpm ED1⎕-⎕⎕-0422-A⎕
EM1-C-M-75-2-⎕-⎕-0-⎕750 W 2,39 Nm 3.000 rpm ED1⎕-⎕⎕-1022-A⎕
EM1-A-M-1K-2-⎕-⎕-0-⎕1 kW 4,77 Nm 2.000 rpm ED1⎕-⎕⎕-1022-A⎕
EM1-D-M-1A-2-⎕-⎕-0-⎕1,2 kW 5,73 Nm 2.000 rpm ED1⎕-⎕⎕-2032-A⎕
EM1-D-M-2K-2-⎕-⎕-0-⎕2 kW 9,55 Nm 2.000 rpm ED1⎕-⎕⎕-2032-A⎕

User Manual Product description
EM1 Series AC Servo Motors EM1-01-1-EN-2307-MA Page 16 of 80
3.3 Order code
3.3.1 Model explanations
3.3.1.1 E1 series AC servo motor
For further use with drive, cable, and accessory, please refer to chapter 5 and 11.
Number 1 2 3 - 4 - 5 - 6 7 - 8 - 9 - 10 - 11 - 12
Code E M 1 - C - M - 0 5 - 2 - B - E - 0 - A
1, 2, 3 EM1 Mode name
4 C Rated/Max.Speed:
A: 2.000 / 3.000 rpm
C: 3.000 / 6.000 rpm
D: 2.000 / 5.000 rpm
5 M Rotor Inertia:
M: Medium inertia
6, 7 05 Rated output:
05: 50 W
10: 100 W
20: 200 W
40: 400 W
75: 750 W
1K: 1.000 W
1A: 1.200 W
2K: 2.000 W
8 2 Input voltage:
2: 220 VAC
9
B
Brake option:
0: Without brake
B: With brake
10 E Encoder option:
E: 23bit incremental (battery is not required)
F: 23bit single-turn /16bit multi-turn absolute (battery is required)
11 0 Reserved:
0: Standard
1: Customized
12 A Shaft type:
A: Round shaft / without oil seal
B: Round shaft / with oil seal
C: Shaft with key / without oil seal
D: Shaft with key / with oil seal

User Manual Product description
EM1 Series AC Servo Motors EM1-01-1-EN-2307-MA Page 17 of 80
3.3.1.2 Servo Drive
For detailed functions of E1 series servo drive, please refer to “ED1 Series Servo Drive User
Manual”.
Number 1 2 3 4 - 5 6 - 7 8 9 10 - 11 12 - 13 14
Code E D 1 S - V G - 0 4 2 2 - 0 1 - 0 0
1, 2, 3 ED1 Mode name
4 S Type:
S: Standard
F: Fieldbus
5 V Control Interface:
V: Voltage command and pulse
E: EtherCAT (CoE)
H: mega-ulink (with HIWIN MoE HIMC motion controller or API/MPI motion control command library)
L: MECHATROLINK-III
P: PROFINET
6 G Special Function:
G: Gantry
N: No special function
7, 8 04 Rated output:
04: 400 W
05: 500 W
10: 1kW
12: 1,2 kW
20: 2 kW
40: 4 kW
50: 5 kW
75: 7,5 kW
9 2 AC Phase:
2: Single/Three-phase (For 400 W/ 500 W/ 1 kW/ 1,2 kW model)
3: Three-phase (For 2 kW/ 4 kW/ 5 kW/ 7,5 kW model)
10 2 AC Power:
2: 110 V/ 220 V (100 VAC –240 VAC)
3: 400 V (380 VAC – 480 VAC)
11 0 Applicable Category:
0: AC, LM, DM, and TM
A: AC only
T: GT
12 1 Safety Version:
1: STO function security approval
13, 14 00 Reserved
Note
Servo drive model no. 12 digits (ED1⎕- ⎕⎕ - ⎕⎕⎕⎕ - ⎕0): STO function without
security approval.
Servo drive model no. 14 digits (ED1⎕- ⎕⎕ - ⎕⎕⎕⎕ - ⎕1 - ⎕⎕): STO function with
security approval.
For the communication settings and details about fieldbus servo drive (ED1F-E), please
refer to “E1 Series Servo Drive EtherCAT(CoE) Communications Command Manual.”
For the communication settings and details about fieldbus servo drive (ED1F-L), please
refer to “E1 Series Servo Drive MECHATROLINK-III Communication Command Manual.”
For the settings and details about gantry function servo drive (ED1⎕- ⎕G), please refer
to “E1 Series Servo Drive Gantry Control System User Manual.”
When the 10th digit of the model number is 2 and the AC voltage is 100 – 120 VAC, only
single-phase input power can be used.

User Manual Product description
EM1 Series AC Servo Motors EM1-01-1-EN-2307-MA Page 18 of 80
400 V servo drives (ED1⎕- ⎕- ⎕⎕⎕ 3) and gantry function servo drives (ED1⎕-
⎕G) only support Thunder 1.6.11.0 or later versions.
If the 10th digit = 2, the following drives are supported: 400 W / 500 W / 1 kW / 1.2 kW /
2 kW / 4 kW. If the 10th digit = 3, the following drives are supported: 5 kW / 7,5 kW.
CoE is the acronym for “CANopen over EtherCAT”; MoE is the acronym for “mega-ulink over
EtherCAT.”
When using API/MPI library with servo drive, users should carefully read through “API/MPI
Library Reference Manual” to check if Windows system is supported.
ED1⎕- ⎕⎕-⎕⎕⎕⎕-T1- ⎕is a GT servo drive, its functions are as follows:
–Support nano precision function.
–Support 2D Error map (with ED1⎕- ⎕G-⎕⎕⎕⎕-T1- ⎕). Gantry function cannot be
used while users enable 2D Error map.
–Support DC 96-120 V.
3.3.1.3 Power cable
For combination of E1 series servo motors and servo drives, please refer to section 3.3.5.
Number 1 2 3 4 - 5 6 - 7 8 - 9 10 11 - 12
Code H V P S - 0 4 - A B - 0 3 M - B
1, 2, 3 HVP Mode name
4 S Capacity:
S: Small capacity (50 W–750 W)
M: Medium capacity (1 KW–2 KW)
5, 6 04 Pin assignment:
04: U / V / W / GND
06: U / V / W / GND / B+ / B-
7 A Motor connector
A: AMP connector
B: Straight military type connector
C: L shape military type connector
8 B Drive connector:
B: R-type terminal
9, 10, 11 03M Cable length:
03M: 3 meter
05M: 5 meter
07M: 7 meter
10M: 10 meter
15M: 15 meter
12 B Cable type:
B: Flexible type
Note
Cable length is not allowed to use exceeds 30 m.
Cable length can be customized for integer number, for example (1 m, 2 m, 3 m…30 m)
Pin assignment and connector specification can be referred to chapter 5.2.1.
Bending radius limitation of power cable can be referred to chapter 5.2.1.4.

User Manual Product description
EM1 Series AC Servo Motors EM1-01-1-EN-2307-MA Page 19 of 80
3.3.1.4 Encoder cable
For combination of servo motors and servo drives, please refer to section 3.3.5.
Number 1 2 3 - 4 5 6 - 7 8 - 9 10 11 - 12
Code H V E - 2 3 A - A B - 0 3 M - B
1, 2, 3 HVE Mode name
4, 5, 6 23A Encoder type:
23A: 23 bit multi-turn absolute encoder
23I: 23 bit single-turn absolute encoder
7 A Motor connector:
A: AMP connector
B: Straight military type connector
C: L shape military type connector
8 B Drive connector:
B: 3M SCR type connector
9, 10, 11 03M Cable length:
03M: 3 meter
05M: 5 meter
07M: 7 meter
10M: 10 meter
15M: 15 meter
12 B Cable type:
B: Flexible type
Note
Cable length is not allowed to use exceeds 30 m.
Cable length can be customized for integer number, for example (1 m, 2 m, 3 m…30 m)
Pin assignment and connector specification can be referred to chapter 5.2.1.
Bending radius limitation of power cable can be referred to chapter 5.2.1.4.

User Manual Product description
EM1 Series AC Servo Motors EM1-01-1-EN-2307-MA Page 20 of 80
3.3.1.5 Combination of E1 series AC servo motor, servo drive and cable
Servo motor Capacity Power cable Encoder cable Servo drive
EM1CM0520E0⎕50 W HVPS04AB⎕⎕MB HVE23IAB⎕⎕MB ED1⎕-⎕⎕-0422-A⎕
EM1CM052BE0⎕HVPS06AB⎕⎕MB
EM1CM0520F0⎕HVPS04AB⎕⎕MB HVE23AAB⎕⎕MB
EM1CM052BF0⎕HVPS06AB⎕⎕MB
EM1CM1020E0⎕100 W HVPS04AB⎕⎕MB HVE23IAB⎕⎕MB
EM1CM102BE0⎕HVPS06AB⎕⎕MB
EM1CM1020F0⎕HVPS04AB⎕⎕MB HVE23AAB⎕⎕MB
EM1CM102BF0⎕HVPS06AB⎕⎕MB
EM1CM2020E0⎕200 W HVPS04AB⎕⎕MB HVE23IAB⎕⎕MB
EM1CM202BE0⎕HVPS06AB⎕⎕MB
EM1CM2020F0⎕HVPS04AB⎕⎕MB HVE23AAB⎕⎕MB
EM1CM202BF0⎕HVPS06AB⎕⎕MB
EM1CM4020E0⎕400 W HVPS04AB⎕⎕MB HVE23IAB⎕⎕MB
EM1CM402BE0⎕HVPS06AB⎕⎕MB
EM1CM4020F0⎕HVPS04AB⎕⎕MB HVE23AAB⎕⎕MB
EM1CM402BF0⎕HVPS06AB⎕⎕MB
EM1CM7520E0⎕750 W HVPS04AB⎕⎕MB HVE23IAB⎕⎕MB ED1⎕-⎕⎕-1022-A⎕
EM1CM752BE0⎕HVPS06AB⎕⎕MB
EM1CM7520F0⎕HVPS04AB⎕⎕MB HVE23AAB⎕⎕MB
EM1CM752BF0⎕HVPS06AB⎕⎕MB
EM1AM1K20E0⎕1 kW HVPM04⎕B⎕⎕MB HVE23I⎕B⎕⎕MB
EM1AM1K2BE0⎕HVPM06⎕B⎕⎕MB
EM1AM1K20F0⎕HVPM04⎕B⎕⎕MB HVE23A⎕B⎕⎕MB
EM1AM1K2BF0⎕HVPM06⎕B⎕⎕MB
EM1DM1A20E0⎕1.2 kW HVPM04⎕B⎕⎕MB HVE23I⎕B⎕⎕MB ED1⎕-⎕⎕-2032-A⎕
EM1DM1A2BE0⎕HVPM06⎕B⎕⎕MB
EM1DM1A20F0⎕HVPM04⎕B⎕⎕MB HVE23A⎕B⎕⎕MB
EM1DM1A2BF0⎕HVPM06⎕B⎕⎕MB
EM1DM2K20E0
⎕
2 kW
HVPM04
⎕
B
⎕⎕
MB
HVE23I
⎕
B
⎕⎕
MB
EM1DM2K2BE0
⎕
HVPM06
⎕
B
⎕⎕
MB
EM1DM2K20F0⎕HVPM04⎕B⎕⎕MB HVE23A⎕B⎕⎕MB
EM1DM2K2BF0⎕HVPM06⎕B⎕⎕MB
Other manuals for EM1 Series
1
Table of contents
Other Hiwin Engine manuals
Popular Engine manuals by other brands

Fuji Imvac
Fuji Imvac BT-24M Operator's manual
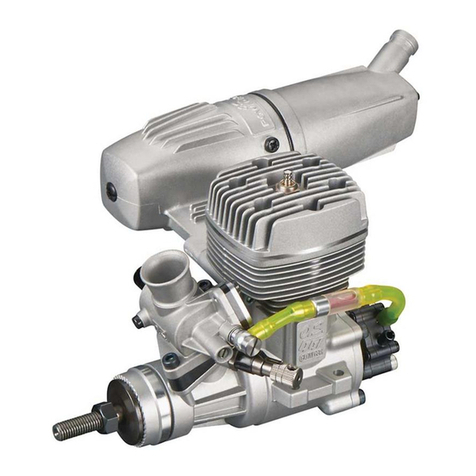
O.S. engine
O.S. engine GGT10 instruction manual

Lombardini
Lombardini 15 LD 225 Use and maintenance manual
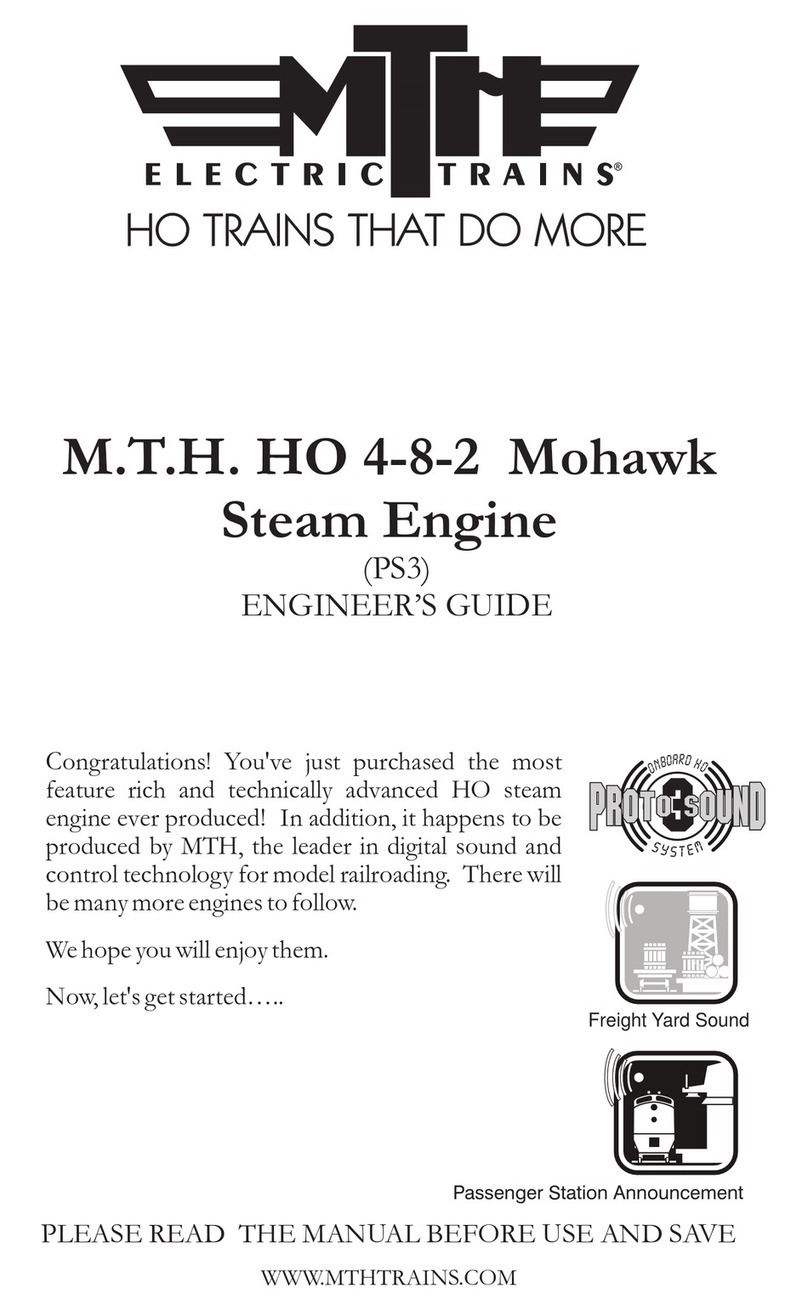
MTHTrains
MTHTrains HO 4-8-2 Mohawk Engineer's guide
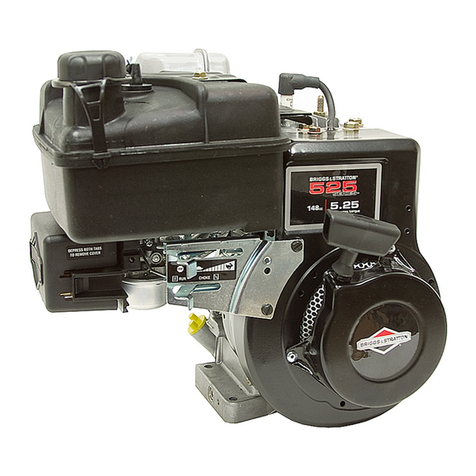
Briggs & Stratton
Briggs & Stratton 90000 series Operator's manual
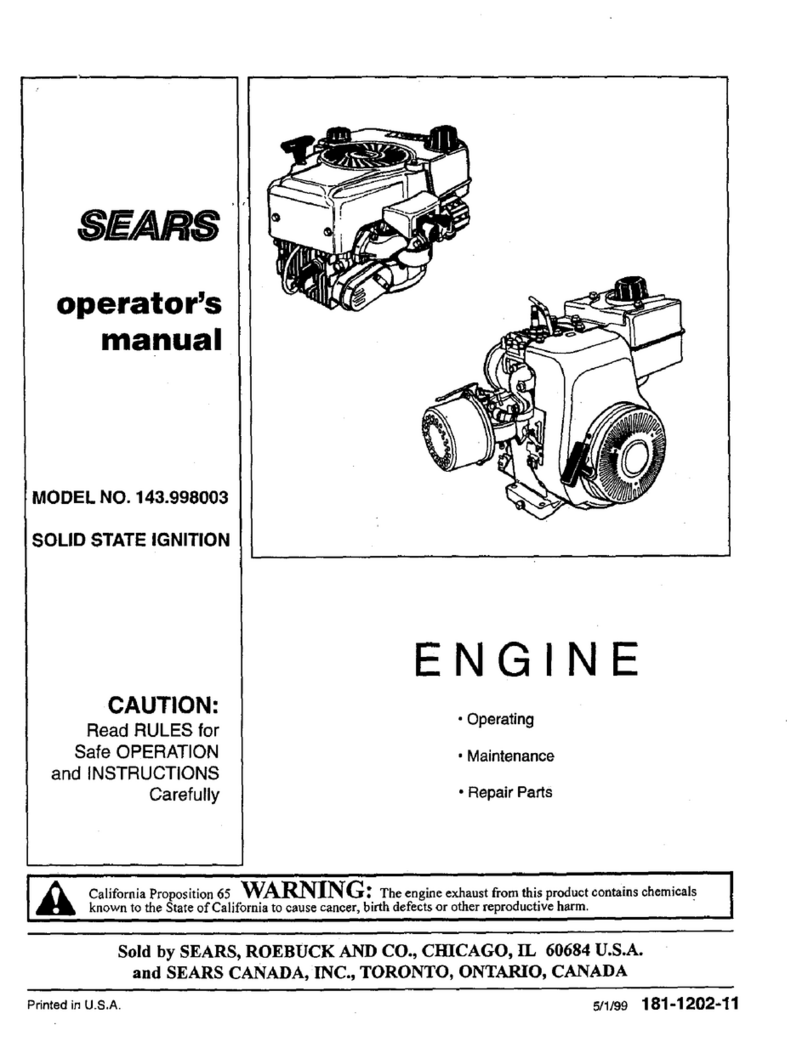
Sears
Sears 143.998003 Operator's manual