Hiwin DMR User manual

Assembly Instructions
Torque motors DMR, TMRW, TMRI
www.hiwin.de

2
Assembly Instructions
Torque motors DMR, TMRW, TMRI
TM-Komponenten-03-2-EN-2011-MA
HIWIN GmbH
Brücklesbünd 1
77654 Offenburg
Germany
Phone +49 (0) 7 81 9 32 78-0
Fax +49 (0) 7 81 9 32 78-90
www.hiwin.de
All rights reserved.
Complete or partial reproduction
is not permitted without our permission.
These assembly instructions are protected by copyright.
Any reproduction, publication in whole or in part, modi-
fication or abridgement requires the written approval of
HIWIN GmbH.

3
Assembly Instructions
Torque motors DMR, TMRW, TMRI
TM-Komponenten-03-2-EN-2011-MA
Contents
Contents
1. General information............................................................ 4
1.1 About these assembly instructions 4
1.2 Depictions used in these assembly instructions 4
1.3 Warranty and liability 6
1.4 Manufacturer’s details 6
1.5 Copyright 6
1.6 Product monitoring 6
2. Basic safety notices ........................................................... 7
2.1 Intended use 7
2.2 Reasonably foreseeable misuse 7
2.3 Conversions and modifications 7
2.4 Residual risks 7
2.5 Personnel requirements 7
2.6 Protective equipment 8
2.7 Labels on torque motor components 8
3. Description of the torque motor components....................... 10
3.1 Field of application 10
3.2 Design of the torque motor components (example of TMRW) 10
3.3 Functional description 11
4. Transport and installation................................................. 15
4.1 Delivery of DMR, TMRW and TMRI 15
4.2 Transport to the installation site 16
4.3 Requirements at the installation site 17
4.4 Storage 17
4.5 Unpacking and installing 17
5. Assembly and connection ................................................. 18
5.1 Requirements to the adjacent construction 19
5.2 Assembling the torque motor 26
5.3 Electrical connection 32
5.4 Connecting liquid cooling (TMRW/TMRI linear motors) 38
6. Commissioning ................................................................ 42
6.1 Switching on the torque motor 42
6.2 Programming 42
7. Maintenance and cleaning................................................. 43
7.1 Cleaning 43
8. Faults ............................................................................. 44
8.1 Faults with the motor 44
8.2 Faults during operation with drive amplifier 44
9. Disposal.......................................................................... 45
10. Appendix 1: Type plate...................................................... 46
11. Appendix 2: Order codes ................................................... 47
11.1 Order code DMR 47
11.2 Order code TMRW 47
11.3 Order code TMRI 47
12. Declaration of Conformity ................................................. 50

4
General information
Assembly Instructions
Torque motors DMR, TMRW, TMRI
TM-Komponenten-03-2-EN-2011-MA
1. General information
1.1 About these assembly instructions
1.1.1 Version management
Version Date Notes
03-2 November 2020 Name change TMR to DMR, “Appendix 3: Data sheets” deleted
03-1 February 2019 Various adjustments, addition of series TMRI
03-0 March 2017 Update and various additions: New model TMRWG, new chapter “Con-
necting liquid cooling”, new data sheets
02-3 October 2016 Update of “Declaration of Conformity”
02-2 January 2016 Update of “Declaration of Conformity”
02-1 October 2015 Various adjustments, additions
02-0 November 2014 Various adjustments, additions
01-1 June 2014 Layout adaptation, additions
01-0 April 2014 Initial creation of common assembly instructions for TMR and TMRW
Table 1.1 Version management
1.1.2 Requirements
We assume that
operating personnel are trained in the safe operation practices for torque motors and torque motor components, and
have read and understood these assembly instructions in full;
maintenance personnel maintain and repair the torque motors and torque motor components in such a way that they
pose no danger to people, property or the environment.
1.1.3 Availability
These assembly instructions must remain constantly available to all persons who work with or on the torque motors and their
components.
1.2 Depictions used in these assembly instructions
1.2.1 Instructions
Instructions are indicated by triangular bullet points in the order in which they are to be carried out.
Results of the actions carried out are indicated by ticks.
Example:
Position the torque motor over the mounting holes.
Place the mounting bolts into the mounting holes and tighten in a spiral pattern to a torque of 10Nm.
Torque motor is mounted.
1.2.2 Lists
Lists are indicated by bullet points.
Example:
Torque motors and their components must not be operated:
Outdoors
In potentially explosive atmospheres
…

General information
5
Assembly Instructions
Torque motors DMR, TMRW, TMRI
TM-Komponenten-03-2-EN-2011-MA
1.2.3 Depiction of safety notices
Safety notices are always indicated using a signal word and sometimes also a symbol for the specific risk (see chapter 1.2.4,
Symbols used).
The following signal words and risk levels are used:
Imminent danger!
Noncompliance with the safety notices will result in serious injury or death!
DANGER!
Potentially dangerous situation!
Noncompliance with the safety notices runs the risk of serious injury or death!
WARNING!
Potentially dangerous situation!
Noncompliance with the safety notices runs the risk of slight to moderate injury!
CAUTION!
Potentially dangerous situation!
Noncompliance with the safety notices runs the risk of damage to property or environmental pollution!
ATTENTION!
1.2.4 Symbols used
The following symbols are used in these assembly instructions and on the components:
Warning of dangerous electrical voltage! Warning of hot surfaces!
Warning of magnetic fields! Warning of crushing!
Substance hazardous to the
environment!
Wear protective gloves! Isolate before work!
Table 1.2 Warning signs
Table 1.3 Mandatory signs
1.2.5 Information
Describes general information and recommendations.
NOTE

6
General information
Assembly Instructions
Torque motors DMR, TMRW, TMRI
TM-Komponenten-03-2-EN-2011-MA
1.3 Warranty and liability
The manufacturer’s “General conditions of sale and delivery” apply.
1.4 Manufacturer’s details
Address HIWIN GmbH
Brücklesbünd 1
77654 Offenburg
Germany
Phone +49 (0) 781 932 78-0
Technical customer service +49 (0) 781 932 78-77
Fax +49 (0) 781 932 78-90
Technical customer service fax +49 (0) 781 932 78-97
E-mail [email protected]
Website www.hiwin.de
Table 1.4 Manufacturer’s details
1.5 Copyright
These assembly instructions are protected by copyright. Any reproduction, publication in whole or in part, modification or
abridgement requires the written approval of HIWIN GmbH.
1.6 Product monitoring
Please inform the manufacturer of:
Accidents
Potential sources of danger in the torque motors
Anything in these assembly instructions which is difficult to understand

Basic safety notices
7
Assembly Instructions
Torque motors DMR, TMRW, TMRI
TM-Komponenten-03-2-EN-2011-MA
2. Basic safety notices
Danger from strong magnetic fields!
Strong magnetic fields around torque motor components (where the rotor or rotor and stator are supplied
separately) pose a health risk to persons with implants (e.g. cardiac pacemakers) that are affected by
magnetic fields.
Persons with implants that are affected by magnetic fields should maintain a safe distance of at least
0.3m from the torque motor components!
WARNING!
2.1 Intended use
Torque motors are components of a rotary drive system for the precise positioning in terms of time and location of fixed
mounted loads, e.g. system components, within an automated system.
Torque motors are designed for installation and operation in any position. The loads being moved must be solidly mounted to
the rotor.
Torque motor components must not be used outdoors or in potentially explosive atmospheres.
Torque motor components may only be used for the intended purpose as described.
Torque motors must be operated within their specified performance limits (see catalogue “Torque Motors”).
For the safe operation of torque motors, suitable safety precautions must be taken to protect the motor against over-
load.
Proper use of the torque motors includes observing the assembly instructions and following the maintenance and repair
specifications.
Use of the torque motor components for any other purpose shall be considered improper use.
Use only genuine spare parts from HIWIN GmbH.
2.2 Reasonably foreseeable misuse
Torque motors must not be operated:
Outdoors
In potentially explosive atmospheres
2.3 Conversions and modifications
Conversions or modifications to the torque motors are not permitted.
2.4 Residual risks
During normal operation, there are no residual risks associated with the torque motor components. Warnings about risks that
may arise during commissioning, maintenance and repair work are provided in the relevant sections.
2.5 Personnel requirements
Only authorised and competent persons may carry out work on the torque motor components. They must be familiar with the
safety equipment and regulations before starting work (see Table 2.1).
Risk of material damage!
Strong magnetic forces may destroy watches and magnetisable data storage media near to the torque motor
components.
Do not bring watches or magnetisable data storage media into the vicinity (
<
100mm) of the torque motors
components!
ATTENTION!

8
Basic safety notices
Assembly Instructions
Torque motors DMR, TMRW, TMRI
TM-Komponenten-03-2-EN-2011-MA
2.6 Protective equipment
Operating phase Personal protective equipment
Commissioning When in the vicinity of the torque motor components, the following personal
protective equipment is required:
Safety shoes
Normal operation When in the vicinity of the torque motor components, the following personal
protective equipment is required:
Safety shoes
Cleaning When cleaning the torque motor components, the following personal protective
equipment is required:
Safety shoes
Maintenance and repairs When carrying out maintenance and repairs, the following personal protective
equipment is required:
Safety shoes
Table 2.2 Personal protective equipment
Table 2.3 Warning symbols
2.7 Labels on torque motor components
Pictogram Type and source of danger Protective measures
Danger from strong magnetic fields!
Persons whose health may be endangered by strong
magnetic fields must keep a safe distance (1m) from the
torque motor components!
Danger of electric shock! Disconnect the power supply of the torque motor compo-
nents before maintenance or repairs!
Danger from hot surfaces! Let hot surfaces cool down before touching them!
2.7.1 Warning symbols
Activity Qualification
Commissioning Trained specialist personnel of the operator or manufacturer
Normal operation Trained personnel
Cleaning Trained personnel
Maintenance Trained specialist personnel of the operator or manufacturer
Repairs Trained specialist personnel of the operator or manufacturer
Table 2.1 Personnel requirements

Basic safety notices
9
Assembly Instructions
Torque motors DMR, TMRW, TMRI
TM-Komponenten-03-2-EN-2011-MA
2.7.2 CE mark on type plate
Fig. 2.1 Type plate

10
Description of the torque motor components
Assembly Instructions
Torque motors DMR, TMRW, TMRI
TM-Komponenten-03-2-EN-2011-MA
Fig. 3.1 Design of the torque motors
3. Description of the torque motor components
3.1 Field of application
Torque motors are components of a rotary drive system for the precise positioning in terms of time and location of fixed
mounted loads, e.g. system components, within an automated system.
Torque motors are designed for installation and operation in any position. The loads being moved must be firmly attached to
the rotor.
The torque motors are supplied as ready-to-install components. As supplied, the rotor and stator are secured with installa-
tion clamps.
3.2 Design of the torque motor components (example of TMRW)
Stator:
The stators of TMRW and TMRI motors comprise the outer ring with cooling channels for liquid cooling and the inner ring
with the laminations and the windings cast in epoxy resin.
The stators of DMR motors do not have cooling channels on the outer ring. The inner ring likewise comprises the laminations
and windings cast in epoxy resin.
Rotor:
On both DMR as well as TMRW and TMRI motors, the rotor consists of nickel-plated steel with rare-earth magnets. The rotor
is mounted on the rotatable part of the customer’s machine.
Number Description
1Rotor
2Stator
3Groove for O-ring
4Rare-earth magnets
5Cooling channels for water cooling (TMRW, TMRI)
6Motor winding
7Motor cable
8Temperature sensor cable
Table 3.1 Main components of a torque motor
[1]
[2]
[3]
[4]
[5]
[6]
[7]
[8]

Description of the torque motor components
11
Assembly Instructions
Torque motors DMR, TMRW, TMRI
TM-Komponenten-03-2-EN-2011-MA
3.3 Functional description
DMR, TMRW and TMRI series torque motors are ready-to-install motor elements consisting of a stator and rotor. In terms of
design, they are internal rotor motors. The rotor is in the form of a ring. Their high power density enables high acceleration
rates and hence short cycle times. In electrical terms, they are three-phase servo motors with a higher number of poles. The
TMRW and the TMRI series is equipped with cooling channels.
3.3.1 Characteristics
Brushless motor
Hollow shaft rotor
Wear-free
High power density
Maintenance-free
3.3.2 Advantages
High efficiency
Extremely dynamic
Low maintenance costs
Compact installation dimensions
Simple control
When integrating a direct drive, ensure high rigidity between torque transmission and recording the control
variable (usually position measurement).
Resonances within the control circuit bandwidth degrade performance, since the motor is free from backlash.
3.3.3 Specifications of torque motor components
NOTE
NOTE
Type Outer diameter
[mm]
Continuous torque
[Nm]
Peak torque
[Nm]
Installed in HIWIN rotary table
(see catalogue “Rotary Tables”)
DMR03 110 3.5 10.5 TMS0
DMR14 150 11.3 33.8 TMS1
DMR18 150 22.5 67.5 TMS1
DMR32 193 10.0 30.0 TMS3
DMR34 193 20.0 60.0 TMS3
DMR38(L) 193 40.0 120.0 TMS3
DMR3C(L) 193 60.0 180.0 TMS3
DMR74 291 50.0 150.0 TMS7
DMR76(L) 291 75.0 225.0 TMS7
DMR7C(L) 291 150.0 450.0 TMS7
Type Outer diameter
[mm]
Continuous torque
[Nm]
Peak torque
[Nm]
TMRW13(L) 160 18.8 35.6
TMRW15(L) 160 31.3 59.4
TMRW17(L) 160 43.8 83.1
TMRW1A(L) 160 62.5 118.8
TMRW1F(L) 160 93.8 178.1
Table 3.2 DMR torque motors
Table 3.3 TMRW torque motors (torque data with water cooling)

12
Description of the torque motor components
Assembly Instructions
Torque motors DMR, TMRW, TMRI
TM-Komponenten-03-2-EN-2011-MA
Type Outer diameter
[mm]
Continuous torque
[Nm]
Peak torque
[Nm]
Table 3.4 TMRI torque motors (torque data with water cooling)
Table 3.3 TMRW torque motors (torque data with water cooling) – continuation
Drawings of the available torque motor components are provided in the appendix to these assembly instructions, or in the
internet at www.hiwin.de.
TMRW23(L) 198 35.0 66.5
TMRW25(L) 198 59.0 112.0
TMRW27(L) 198 82.5 156.0
TMRW2A(L) 198 117.5 223.0
TMRW2F(L) 198 176.0 334.5
TMRW43(L) 230 63.5 120.0
TMRW45(L) 230 106.0 203.0
TMRW47(L) 230 148.0 280.0
TMRW4A(L) 230 205.0 390.0
TMRW4F(L) 230 307.0 583.0
TMRW73(L) 310 145.0 275.0
TMRW75(L) 310 240.0 456.0
TMRW77(L) 310 335.0 640.0
TMRW7A(L) 310 480.0 910.0
TMRW7F(L) 310 720.0 1,360.0
TMRWA3(L) 385 260.0 490.0
TMRWA5(L) 385 430.0 810.0
TMRWA7(L) 385 600.0 1,100.0
TMRWAA(L) 385 860.0 1,600.0
TMRWAF(L) 385 1,290.0 2,400.0
TMRWD3(L) 485 400.0 750.0
TMRWD5(L) 485 660.0 1,230.0
TMRWD7(L) 485 930.0 1,760.0
TMRWDA(L) 485 1,340.0 2,470.0
TMRWDF(L) 485 2,000.0 3,600.0
TMRWG3(L) 565 515.0 1,002.0
TMRWG5(L) 565 930.0 1,700.0
TMRWG7(L) 565 1,255.0 2,360.0
TMRWGA(L) 565 1,810.0 3,340.0
TMRWGF(L) 565 2,720.0 5,020.0
Type Outer diameter
[mm]
Continuous torque
[Nm]
Peak torque
[Nm]
TMRIA5 385 540 830
TMRIA7 385 750 1,100
TMRIAA 385 1,080 1,660
TMRIAF 385 1,600 2,490
TMRIG5 565 1,140 1,770
TMRIG7 565 1,597 2,480
TMRIGA 565 2,280 3,500
TMRIGF 565 3,400 5,300

Description of the torque motor components
13
Assembly Instructions
Torque motors DMR, TMRW, TMRI
TM-Komponenten-03-2-EN-2011-MA
3.3.4 Closed cooling jacket (option for TMRW and TMRI)
For easy integration of our water-cooled torque motors, we also supply them in a closed version. The connection to the
cooling unit is realised via 2 G⅛ threads in the stainless steel jacket. As in the version without a closed cooling jacket, the
alignment of the motor is realised easily via the fit of the stator. Available for the sizes TMRW7, TMRWA, TMRWD, TMRWG
(all other sizes upon request) as well as for the sizes TMRIA and TMRIG.
3
8
BA
2-G⅛
8
Torque motor Dimension A [mm] Dimension B [mm]
TMRW7 35 25
TMRWA 35 35
TMRWG 35 35
TMRWD 27 43
TMRIA 35 35
TMRIG 35 35
Table 3.5 Dimensions of steel cooling jacket

14
Description of the torque motor components
Assembly Instructions
Torque motors DMR, TMRW, TMRI
TM-Komponenten-03-2-EN-2011-MA
3.3.5 Cable outlet orientations of the TMRW torque motors
Standard:
Motor cables potted in the stator
Option 1:
Motor cables potted in the stator
Additional strain relief plate
Option 2:
Motor cables potted in the stator
Additional strain relief plate
PG screw connections
Option 3:
Motor cables potted in the stator
Additional strain relief plate
90° cable outlet
Table 3.6 Cable outlet orientations of the TMRW torque motors

Transport and installation
15
Assembly Instructions
Torque motors DMR, TMRW, TMRI
TM-Komponenten-03-2-EN-2011-MA
4. Transport and installation
4.1 Delivery of DMR, TMRW and TMRI
4.1.1 Delivery state
DMR, TMRW and TMRI torque motors are usually supplied pre-assembled. To avoid damage during transport, the rotor is
fixed in the stator using installation clamps (see Fig. 4.1 and Fig. 4.2).
Fig. 4.1 DMR torque motor with installation clamps
Fig. 4.2 TMRW/TMRI torque motor with installation clamps
Risk of crushing from strong attraction forces!
Risk of injury from crushing and damage to the forcer or stator due to very strong attraction forces with
unpacked rotors.
Make sure that the installation clamps are not removed until the rotor and stator are secured by means
of a bearing!
If the rotor is supplied separately, be sure to observe the strong magnetic fields!
WARNING!

16
Transport and installation
Assembly Instructions
Torque motors DMR, TMRW, TMRI
TM-Komponenten-03-2-EN-2011-MA
4.1.2 Packaging
As supplied, the torque motor components are wrapped in film inside padded cardboard packaging.
Do not remove the film wrapping until just before installation.
4.1.3 Scope of delivery
Rotor, which is secured in the stator by installation clamps
Stator with (TMRW, TMRI) or without (DMR) cooling channels, plus motor and temperature sensor cables with open
cable ends
2 O-rings (TMRW, TMRI)
Type plate
Safety notices
It is possible to have the rotor supplied separately.
4.2 Transport to the installation site
Damage to the torque motor components!
The torque motor components may be damaged by mechanical loading.
During transport, do not transport any additional loads on the torque motor components!
Before transport, secure the torque motor components against tilting!
ATTENTION!
There are no magnetic fields around components in their original packaging.
Transport torque motor components to the installation site using a suitable hoist (pay attention to weights – see ap-
pendix).
Ensure even load distribution while lifting.
NOTE
Danger from strong magnetic fields!
Strong magnetic fields around torque motor components (where the rotor or rotor and stator are supplied
separately) pose a health risk to persons with implants (e.g. cardiac pacemakers) that are affected by
magnetic fields.
Persons with implants that are affected by magnetic fields should maintain a safe distance of at least
0.3m from the torque motor components!
WARNING!
Risk of material damage!
Strong magnetic forces may destroy watches and magnetisable data storage media near to the torque motor
components.
Do not bring watches or magnetisable data storage media into the vicinity (
<
100mm) of the torque motors
components!
ATTENTION!

Transport and installation
17
Assembly Instructions
Torque motors DMR, TMRW, TMRI
TM-Komponenten-03-2-EN-2011-MA
Damage to the torque motor components!
The torque motor components may be damaged by mechanical loading.
During transport, do not transport any additional loads on the torque motor components!
Before transport, secure the torque motor components against tilting!
ATTENTION!
4.3 Requirements at the installation site
4.3.1 Ambient conditions
Ambient temperature +5°C to +40 °C
Installation site flat, dry, vibration-free
Atmosphere not corrosive, not explosive
4.3.2 Safety equipment to be provided by the operator
Possible safety equipment/measures:
Personal protective equipment in accordance with UVV (German accident prevention regulations)
Zero-contact protective equipment
Mechanical protective equipment
4.4 Storage
There are no magnetic fields around components in their original packaging.
Store the torque motor components in their transport packaging.
Do not store the torque motor in explosive atmospheres or in environments exposed to chemicals.
Only store the torque motor components in dry, frost-free areas with a corrosion-free atmosphere.
Make sure that the motors are not subjected to vibrations or impacts while in storage.
Clean and protect used torque motor components before storage.
The ambient temperature for storing the motors should be between –10 and +50 °C.
When storing the components, attach signs warning of magnetic fields.
4.5 Unpacking and installing
NOTE
The torque motor may only be installed and operated indoors.
Remove protective film.
Carefully transport components to the designated installation site.
Ensure that the maintenance points are easily accessible.
Dispose of packaging in an environmentally friendly way.
NOTE
Danger from strong magnetic fields!
Strong magnetic fields around torque motor components (where the rotor or rotor and stator are supplied
separately) pose a health risk to persons with implants (e.g. cardiac pacemakers) that are affected by
magnetic fields.
Persons with implants that are affected by magnetic fields should maintain a safe distance of at least
0.3m from the torque motor components!
WARNING!

18
Assembly and connection
Assembly Instructions
Torque motors DMR, TMRW, TMRI
TM-Komponenten-03-2-EN-2011-MA
5. Assembly and connection
Danger from electrical voltage!
Before and during assembly, disassembly and repair work, dangerous currents may flow.
Work may only be carried out by a qualified electrician and with the power supply disconnected!
Before carrying out work on the torque motor, disconnect the power supply and protect it from being
switched back on!
DANGER!
Risk of crushing from strong attraction forces!
Risk of injury from crushing and damage to the forcer or stator due to very strong attraction forces with
unpacked rotors.
Make sure that the installation clamps are not removed until the rotor and stator are secured by means
of a bearing!
WARNING!
The torque motor components may only be assembled by specialist personnel.
Do not use any spacers, shims or similar items when installing the torque motors.
For a closed control loop, a suitable position measuring system must be integrated.
For the safe operation of the torque motors, suitable safety precautions must be taken to protect the motor
against overload.
NOTE
NOTE
NOTE
NOTE
Danger from suspended loads or falling parts!
Lifting heavy loads may damage your health.
Use a hoist of an appropriate size when positioning heavy loads!
Observe the applicable occupational health and safety regulations when handling suspended loads!
CAUTION!

Assembly and connection
19
Assembly Instructions
Torque motors DMR, TMRW, TMRI
TM-Komponenten-03-2-EN-2011-MA
5.1 Requirements to the adjacent construction
5.1.1 Rotor
To rule out any problems with the motor’s operation resulting from the influence of the magnets, a gap of approx. 1mm
should be maintained between the adjacent construction and the magnets. In Table 5.1 and Table 5.2 you can also find the
maximum values for the external and internal diameter of the adjacent construction as well as the requirements for the
evenness of the assembly surface.
Adjacent
construction
A1mm
Ød max.
ØD max.
Rotor
Magnet
Fig. 5.1 Rotor with adjacent construction
Motor type ØD [mm] Ød [mm] Evenness A [mm] Evenness B [mm]
DMR0X 57.0 48.5 0.05 0.05
DMR1X 83.5 73.0 0.05 0.05
DMR3X 136.0 127.0 0.05 0.05
DMR7X 232.0 220.0 0.10 0.10
Motor type ØD [mm] Ød [mm] Evenness A [mm] Evenness B [mm]
TMRW1X 84.5 76.0 0.05 0.05
TMRW2X 118.0 110.0 0.05 0.05
TMRW4X 168.0 158.0 0.10 0.10
TMRW7X 232.0 217.0 0.10 0.10
TMRWAX 298.0 284.5 0.10 0.10
TMRWDX 383.0 370.0 0.15 0.15
TMRWGX 458.0 447.0 0,15 0,15
TMRIAX 298.0 284.5 0.10 0.10
TMRIGX 458.0 447.0 0.15 0.15
Table 5.1 Requirements for rotor installation – DMR
Table 5.2 Requirements for rotor installation – TMRW/TMRI
5.1.2 Stator
The recommended value for the tolerance of the housing internal diameter (and the stator mounting holes) is H7. Please
consult Table 5.1 and Table 5.2 (evenness B) for the values for the evenness of the stator mounting surface. To ensure that
the O-rings do not become damaged, which could cause leaks, we recommend applying a bevel to the housing (for dimen-
sions see Fig. 5.2).

20
Assembly and connection
Assembly Instructions
Torque motors DMR, TMRW, TMRI
TM-Komponenten-03-2-EN-2011-MA
5.1.3 Concentricity between rotor and stator
When installing HIWIN torque motors, ensure maximum concentricity between stator and rotor. Tolerance values for axial
offset lie between ±0.1 mm (DMR models and TMRW series TMRW1X, TMRW2X, TMRW4X and TMRW7X), ± 0.2 mm (TMRW
series TMRWAX, TMRWDX and TMRI series TMRIAX) and 0.25mm (TMRWGX and TMRIGX).
Stator
Housing
B
2mm
15– 30°
Fig. 5.2 Stator with housing
5.1.3.1 Radial forces between rotor and stator
Concentricity deviations result in radial forces between stator and rotor.
Offset LA
Fig. 5.3 Illustration of the radial forces generated by concentricity deviations between stator and rotor
Series FR_100 [N/m] Series FR_100 [N/m]
TMRW1X 2,184 DMR0X 1,346
TMRW2X 2,590 DMR1X 1,787
TMRW4X 2,946 DMR3X 1,878
TMRW7X 2,899 DMR7X 2,121
TMRWAX 3,574
TMRWDX 4,350
TMRWGX 5.158
Table 5.3 Overview of radial forces for a torque motor with an active length of 100 mm
= FR_100 (Radial force with an active
length of 100mm)
This manual suits for next models
123
Table of contents
Other Hiwin Engine manuals
Popular Engine manuals by other brands
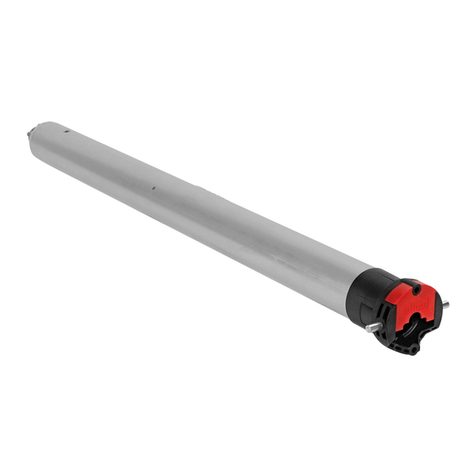
Simu
Simu T5 Hz.02 instructions
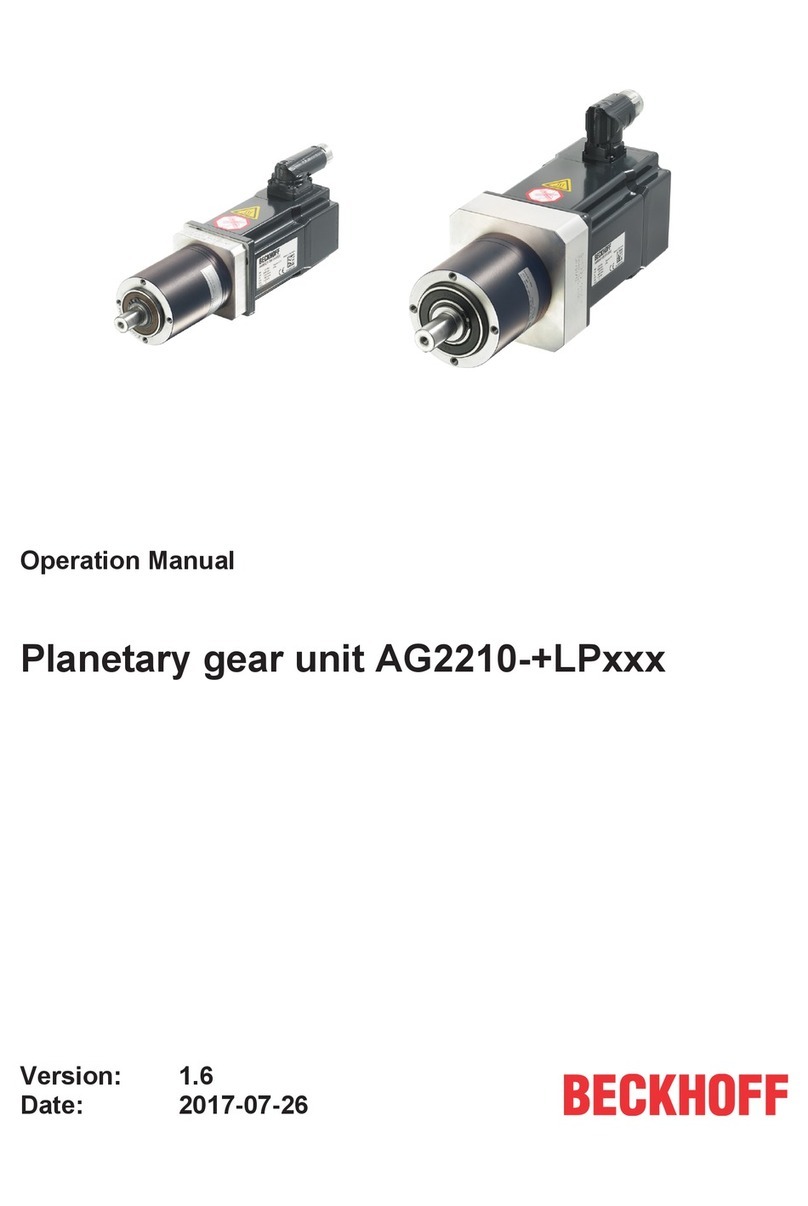
Beckhoff
Beckhoff AG2210-LP Series Operation manual

Nanni
Nanni T4.155 seriers Workshop manual

Schellenberg
Schellenberg ROLLODRIVE 65 PREMIUM manual
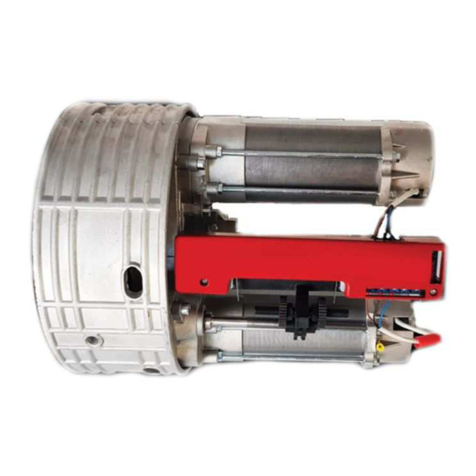
Aprimatic
Aprimatic Ro-Matic RS230 Mechanical installation, Use and Maintenance instructions

MOBILUS
MOBILUS M35 MR Installation and operating instructions