Hiwin TMRW Series User manual

TMRW Series Torque Motor
Installation Manual
www.hiwinmikro.tw

TMRW Series Torque Motor Installation Manual Table of Contents
Table of Contents
1. Introduction ...................................................................................................................................................... 1-1
1.1 General precautions............................................................................................................................ 1-2
1.2 Safety symbols.................................................................................................................................... 1-2
1.3 Safety instructions............................................................................................................................... 1-3
1.3.1 Wiring precautions ................................................................................................................. 1-3
1.3.2 Operation precautions............................................................................................................ 1-4
1.3.3 Maintenance and storage precautions................................................................................... 1-4
2. Motor Basic Structure....................................................................................................................................... 2-1
3. Motor Sizing ..................................................................................................................................................... 3-1
3.1 Torque motor selection........................................................................................................................ 3-2
3.2 Thermal calculation ............................................................................................................................. 3-7
3.2.1 Heat loss ................................................................................................................................ 3-7
3.2.2 Continuous operating temperature ........................................................................................ 3-8
3.3 Thermal time constant......................................................................................................................... 3-9
3.4 Water cooling system calculation...................................................................................................... 3-10
4. Motor Installation Design.................................................................................................................................. 4-1
4.1 Water cooling design........................................................................................................................... 4-2
4.1.1 Water cooling channel position .............................................................................................. 4-2
4.1.2 Water cooling channel dimension .......................................................................................... 4-3
4.1.3 Water cooling channel configuration...................................................................................... 4-4
4.1.4 O-ring features ....................................................................................................................... 4-5
4.1.5 Fixture dimension................................................................................................................... 4-5
4.2 Rotor installation design...................................................................................................................... 4-7
4.3 Stator installation design..................................................................................................................... 4-8
4.4 Air gap and assembly concentricity .................................................................................................... 4-9
4.5 Force between stator and rotor......................................................................................................... 4-10
4.5.1 Radial force .......................................................................................................................... 4-10
4.5.2 Axial force .............................................................................................................................4-11
4.6 Screw tightening torque .................................................................................................................... 4-12
4.7 Motor cable ....................................................................................................................................... 4-13
4.7.1 Power cable specification .................................................................................................... 4-13

TMRW Series Torque Motor Installation Manual Table of Contents
Table of Contents
4.7.2 Temperature sensor cable specification .............................................................................. 4-14
4.7.3 Bend radius of cable ............................................................................................................ 4-16
4.8 Parallel operation design .................................................................................................................. 4-17
4.9 Temperature sensor .......................................................................................................................... 4-21
5. Thermal Protection Device............................................................................................................................... 5-1
5.1 Features .............................................................................................................................................. 5-2
5.2 Wiring of temperature module............................................................................................................. 5-3
6. Motor Installation.............................................................................................................................................. 6-1
6.1 Install stator and rotor together ........................................................................................................... 6-2
6.2 Install stator and rotor separately........................................................................................................ 6-4
7. Troubleshooting................................................................................................................................................ 7-1
8. Technical Term s ............................................................................................................................................... 8-1

TMRW Series Torque Motor Installation Manual Table of Contents
(This page is intentionally left blank.)

1. Introduction
1. Introduction ...................................................................................................................................................... 1-1
1.1 General precautions............................................................................................................................ 1-2
1.2 Safety symbols.................................................................................................................................... 1-2
1.3 Safety instructions............................................................................................................................... 1-3
1.3.1 Wiring precautions ................................................................................................................. 1-3
1.3.2 Operation precautions............................................................................................................ 1-4
1.3.3 Maintenance and storage precautions................................................................................... 1-4

TMRW Series Torque Motor Installation Manual Introduction
1-2 HIWIN MIKROSYSTEM Corp.
MR01UE01-1904
HIWIN TMR(W) series torque motor, with the constitution of a stator and a rotor, can be directly drove
without decelerator. With servo drive control, excellent acceleration and good uniformity of movement can
be easily achieved. Due to the hollow shaft design, cable systems or mechanical parts can easily feed
through the motor.
1.1 General precautions
Before using the product, please carefully read through this manual. HIWIN Mikrosystem (HIWIN) is not
responsible for any damage, accident or injury caused by failure in following the installation instructions
and operating instructions stated in this manual.
Before installing or using the product, ensure there is no damage on its appearance. If any damage
is found after inspection, please contact HIWIN or local distributors.
Ensure the wiring is not damaged and can be normally connected.
Do not disassemble or modify the product. The design of the product has been verified by structural
calculation, computer simulation and actual testing. HIWIN is not responsible for any damage,
accident or injury caused by disassembly or modification done by users.
Keep children away from the product.
People with psychosomatic illness or insufficient experience should not use the product alone. The
supervision of managers or product docents is definitely needed.
If the login information does not match your order, please contact HIWIN or local distributors.
1.2 Safety symbols
Symbol Meaning
Warning of dangerous high voltage!
Warning of magnetic fields!
Warning of hot surfaces!
Environmentally hazardous substance!

TMRW Series Torque Motor Installation Manual Introduction
HIWIN MIKROSYSTEM Corp. 1-3
MR01UE01-1904
1.3 Safety instructions
When taking or placing the product, do not just pull the cable and drag it.
Do not subject the product to shock.
Ensure the product is used with rated load.
Do not repair the product by yourself when it malfunctions. The product can only be repaired by
qualified technician from HIWIN.
HIWIN motor certification test meets the following standards.
CE
LVD Safety:
2014/35/EU reference standard EN 60034-1:2010
EMC (Including EMI+EMS):
2014/30/EU reference standard
EN 61000-6-4:2007+A1:2011
EN 61000-6-2:2005
EN 61000-4-2:2009
EN 61000-4-3:2006
EN 61000-4-3:2008
EN 61000-4-3:2010
EN 61000-4-8:2010
UL Rotating Electrical Machines reference standard 1004-1
1.3.1 Wiring precautions
Before using the product, carefully read through the specification noted on product label, and ensure
the product is used with power supply specified in product requirement.
Check if the wiring is correct. Incorrect wiring may make the motor operate abnormally, or even cause
permanent damage to the motor.
Select extension cord with isolation net. The isolation net must be grounded.
Do not connect power cable and temperature sensor cable to the same extension cord.
Power cable and temperature sensor cable contain isolation net. The isolation net must be grounded.

TMRW Series Torque Motor Installation Manual Introduction
1-4 HIWIN MIKROSYSTEM Corp.
MR01UE01-1904
1.3.2 Operation precautions
Avoid excessive friction when the motor is running.
Ensure there is no object in the motion range of the system.
Before starting the motor, ensure the water cooling system works properly.
Before starting the motor, ensure the main switch is on.
Before transmitting electricity, ensure at least one ground wire is connected to all electrical products.
Do not directly touch motor parts as the motor stops operating.
If the current exceeds the maximum specified current, magnetic components in the motor may be
demagnetized. When it happens, please contact HIWIN or local distributors.
Do not operate the product in an environment that exceeds its rated load.
When the motor is running, its temperature must be within the specification.
If any abnormal odor, noise, smoke, temperature rise or vibration is detected, stop the motor and turn
off the power immediately.
Ambient temperature: +5°C ~ +40°C
1.3.3 Maintenance and storage precautions
Do not store the product in an inflammable environment or with chemical agents.
Store the product in a place without humidity, dust, harmful gases or liquids.
Install the product in location with less vibration.
The storage and transportation temperature of the product: -10°C ~ +50°C
The way to clean the product: wipe with alcohol (70%)
The way to discard the damaged product: recycle it according to local laws and regulations

TMRW Series Torque Motor Installation Manual Motor Basic Structure
2-2 HIWIN MIKROSYSTEM Corp.
MR01UE01-1904
TMRW series can get its best performance through water cooling. Bearing, position feedback device and
other related parts are excluded from shipment. Motor basic structure is shown in Figure 2.1.
Stator
Stator in TMR series does not contain water cooling channel, while stator in TMRW series does. The
outer casing is made of aluminum alloy or silicon steel, and the inner part is composed of iron core
and coils, covered with epoxy. There are two cable outlets on one side, motor power cable and
temperature sensor cable. Stator should be installed on the fixed part of customer’s machine.
Rotor
The main structure is a steel ring with attached magnets. Rotor should be installed on the rotating
part of customer’s machine. Due to its strong magnetic suction, well protection is needed during
assembly and handling. To avoid danger, keep it away from magnetic conductors (e.g. iron objects).
Figure 2.1 Motor basic structure for TMRW series
Rotor
Stator
Magnet
O-ring
Motor power cable
Temperature sensor cable
Water cooling channel
Iron core & Coil

3. Motor Sizing
3. Motor Sizing ..................................................................................................................................................... 3-1
3.1 Torque motor selection........................................................................................................................ 3-2
3.2 Thermal calculation ............................................................................................................................. 3-7
3.2.1 Heat loss ................................................................................................................................ 3-7
3.2.2 Continuous operating temperature ........................................................................................ 3-8
3.3 Thermal time constant......................................................................................................................... 3-9
3.4 Water cooling system calculation...................................................................................................... 3-10

TMRW Series Torque Motor Installation Manual Motor Sizing
3-2 HIWIN MIKROSYSTEM Corp.
MR01UE01-1904
3.1 Torque motor selection
The way to select a suitable motor based on speed, moving distance, and loading inertia is described in
the following contents. The basic process for sizing a motor is as below.
Requirement
Operating environment
Installation (horizontal or vertical)
Driving method
Load conditions (loading inertia, friction and cutting force)
Speed condition (maximum acceleration and velocity)
Duty cycle
Torque calculation
Calculate the torque corresponding to the speed under
each operation condition
Calculate equivalent torque
Motor sizing and T-N curve confirmation
Select the appropriate motor from HIWIN’s catalogue in accordance with calculated
maximum torque, equivalent torque and speed.
Ensure the speed and the corresponding torque under all operating conditions are
within the range of torque-speed curve of the motor.
Confirm the equivalent torque is within the continuous torque of the motor.
Torque (Nm)
Speed (rpm)
Tp
(Peak Torque)
Tcw
(Continuous torque
for water cooling)
Tc
(Continuous torque
for air cooling)
Torque Motor
T-N curve

TMRW Series Torque Motor Installation Manual Motor Sizing
HIWIN MIKROSYSTEM Corp. 3-3
MR01UE01-1904
Symbol
θAngular displacement (rad) IpPeak current (Arms)
t Moving time (sec) IeEquivalent current (Arms)
αAngular acceleration (rad/s2) IcContinuous current (Arms)
ωAngular velocity (rad/s) ω0 Initial angular velocity (rad/s)
J Load inertia (kgm2) m Loading Mass (kg)
JmRotor inertia (kgm2) R Outside diameter of loading Mass (m)
TpPeak torque (Nm) r Inside diameter of loading Mass (m)
TcContinuous torque (Nm) a、b Side length of loading Mass (m)
TiInertia torque (Nm) S D
istance from gravity center to rotary
center (m)
KtTorque constant (Nm/Arms)
STEP 1 Requirement
To select a proper motor, the following formula of load inertia and motion must be understood before
selection.
Calculation of load inertia
Load inertia can be determined by 3D drawing software or the formula. Basic formula is as below.
moment of inertia of a hollow cylinder: J=mR+r
2+S2
moment of inertia of a rectangular: J=ma+b
12 +S2
rotary center rotary center

TMRW Series Torque Motor Installation Manual Motor Sizing
3-4 HIWIN MIKROSYSTEM Corp.
MR01UE01-1904
Determine motion speed and parameters
Basic kinematics equations are described as below.
ω=ω0+αtθ=ω0t+1
2αt2
Where ω is angular velocity, αis angular acceleration, t is moving time and θis angular displacement.
Users can choose two of the four parameters (ω, α, t and θ) as designed parameters. The left two
parameters can be calculated by above equations.
※Motion velocity profile
Motion profiles for torque motor can be classified into “Trapezoid profile” and “Triangle profile”. Trapezoid
profile is usually used in scanning applications. Its motion profile can be divided into acceleration, constant
velocity and deceleration. The maximum angular acceleration can be determined by the basic kinematics
equations mentioned above. Triangle profile is usually used in point-to-point applications. Its motion profile
can be divided into acceleration and deceleration, and its motion profile and formula can be simplified as
below.
or

TMRW Series Torque Motor Installation Manual Motor Sizing
HIWIN MIKROSYSTEM Corp. 3-5
MR01UE01-1904
STEP 2 Torque calculation
The maximum torque can be calculated by the following equation.
Tmax =(J+Jm)×αmax +Tf=Ti+Tf
Where Tiis inertia torque, Tfis the torque caused by friction torque, cutting force or external force.
In most cases, the motions are cyclic point-to-point movements. The equivalent torque of a cyclic motion
with a dwell time of t4second can be calculated as below.
Te=(Ti+Tf)2×t1+Tf
2×t2+(TiTf)2×t3
t1+t2+t3+t4

TMRW Series Torque Motor Installation Manual Motor Sizing
3-6 HIWIN MIKROSYSTEM Corp.
MR01UE01-1904
STEP 3 Motor sizing and T-N curve confirmation
With the help of HIWIN’s motor specification, users can select the appropriate motor from peak torque and
equivalent torque, and ensure speed and torque under all operating conditions is within the range of the
motor’s T-N curve.
Motor sizing is determined as follows.
Tmax <Tp
Te<Tc
Users need to consider the ratio of equivalent torque and continuous torque. Generally, the ratio (Te/Tc) is
recommended to be within 0.7. Continuous torque for TMRW series can be classified into air cooling and
water cooling. If the motor is operated with water cooling, the water cooling continuous torque can be taken
as the guideline for comparison.
Peak current Imax and effective current Iecan be calculated by bring motor torque constant into the following
equation. (To know more about Kt, please refer to Chapter 8.)
Imax =Tmax
Kt
Ie=Te
Kt
Torque (Nm)
Speed (rpm)
Tp
(Peak Torque)
Tcw
(Continuous torque
for water cooling)
Tc
(Continuous torque
for air cooling)
Torque Motor
T-N curve

TMRW Series Torque Motor Installation Manual Motor Sizing
HIWIN MIKROSYSTEM Corp. 3-7
MR01UE01-1904
3.2 Thermal calculation
3.2.1 Heat loss
When the motor converts electric energy into kinetic energy, copper loss, iron loss and mechanical loss
are inevitable. Copper loss is the loss generated by the resistance when the current flows through the
stator coil of the motor. Iron loss, which can be classified into hysteresis loss and eddy current loss, is
generated by the conversion of the magnetic field between stator iron core and rotor magnet. As for
mechanical loss, it is generally much less than copper loss and iron loss; therefore, it can be ignored.
Copper loss under continuous torque is calculated as below.
( )
[ ]
{ }
2
cc25c
I25θ0.003931R
2
3
P⋅−⋅+⋅⋅=
Pc = copper loss at coil temperature θc[W]
R25 = line-to-line resistance at coil temperature 25°C [Ω]
Ic = continuous current at coil temperature θc[Arms]
θc = coil temperature [°C] (120°C for TMRW series; as for TMR series, refer to the drawing)
Iron loss is mainly caused by the change of magnetic flux during the commutation process and is
influenced by the frequency a lot. Since rotational speed is directly proportional to frequency, iron loss will
be larger at high speed. However, rotational speed for HIWIN torque motor is low, so iron loss is relatively
less than copper loss. Rotational speed value indicated by HIWIN drawing and specification is the
maximum peak speed that the motor can reach. Under the continuous operation of high speed, iron loss
must calculate extra heat given to rotor. At this time, motor loss increases rapidly. To avoid overheating,
users need to appropriately adjust operating conditions or apply heat dissipation on rotor.
Iron loss is mainly generated by eddy current and frequency. The faster the speed, the more the iron loss.
2
f∝
Fe
P
Fe
P
= iron loss [W]
f
= frequency [Hz]

TMRW Series Torque Motor Installation Manual Motor Sizing
3-8 HIWIN MIKROSYSTEM Corp.
MR01UE01-1904
Definition of frequency:
60
p
n⋅
=
f
n = rotational speed [rpm]
p = Number of poles pair
Heat loss mainly transmits the loss of coil and iron core to motor outer casing via heat conduction. Take
natural air cooling for example. Lost heat source will be transmitted from the surface of outer casing
contacted by the air to external environment via heat convection, and from the customer’s installation
surface via heat radiation and heat conduction. As for water cooling, lost heat source will be transmitted
from center of heat source to cooling water via heat conduction. Since the heat-conduction coefficient of
cooling water is much higher than that of air, the effect that heat source transmits to the air via convection
can be ignored. TMRW series is available to either water cooling or air cooling. Ensure parameters you
use fit the specification, and keep coil temperature from exceeding 120°C.
3.2.2 Continuous operating temperature
Steady state temperature of motor coil is determined by the proportion of copper loss and iron loss. When
rotational speed is low, iron loss may not be considered. Both total loss and rated continuous torque (Tc)
are defined when coil temperature is 120°C. When equivalent torque (Te) is less than rated continuous
torque (Tc), steady state temperature of motor coil under various operating conditions can be known by
the following formula.
When operating current is lower than rated current (Ieff < Ic), the relationship between temperature and
torque is as below.
( )
25θ
T
T
θ
θc
2
c
e
surre−⋅
+=
e
θ
= steady state temperature of coil under equivalent torque [°C]
surr
θ
= ambient temperature [°C]
e
T
= equivalent torque under actual operation [Nm] (when coil temperature is
e
θ
)
c
T
= rated continuous torque [Nm] (when coil temperature is
c
θ
)

TMRW Series Torque Motor Installation Manual Motor Sizing
HIWIN MIKROSYSTEM Corp. 3-9
MR01UE01-1904
3.3 Thermal time constant
During the operation of motor, coil temperature is related to thermal time constant. The definition of thermal
time constant is the time that the initial temperature reaches 63% of steady state temperature (as Figure
3.3.1 shows). The time to reach steady state is approximately five times the thermal time constant.
Figure 3.3.1 Curve of temperature rising
The relationship between thermal time constant and temperature is
( )
−⋅
−+
=
−
th
T
t
ici e1θθθtθ)(
( )
tθ
= coil temperature [°C] (at the operating time t)
i
θ
= initial coil temperature [°C]
t = operating time [sec]
th
T
= thermal time constant [sec]
When operating current is between rated current and peak current (Ic< Ie< Ip), power off time should be
set to cool the motor. The thermal time constant mentioned above can be applied to calculate the time for
load cycle. Refer to Section 3.2 to get steady state temperature of coil under equivalent torque (θe) through
equivalent torque under actual operation (Te). Then, get the relative maximum operating time via the
following formula.
The relationship between steady state temperature of coil under equivalent torque (θe) and maximum
operating time is
0
20
40
60
80
100
120
05000 10000 15000 20000
Temperature (℃)
Time (sec)

TMRW Series Torque Motor Installation Manual Motor Sizing
3-10 HIWIN MIKROSYSTEM Corp.
MR01UE01-1904
−
−
−⋅−=
ie
ic
th0
θθ
θθ
1lnTt
t0 = maximum operating time [sec]
Note: Coil temperature (θc) here cannot exceed the specification’s upper limit. (120°C for TMRW series; as
for TMR series, refer to the drawing)
The relationship between coil temperature and power off time is
( )
−
−
⋅−=
surrc
surrb
thbθθ
θtθ
lnTt
)
(
b
t
θ
= coil temperature to be cooled [°C] (after power off time tb)
tb = power off time [sec]
The time allocation of load cycle during motor operation can be determined by the two formulas above.
3.4 Water cooling system calculation
The features of motor indicated in HIWIN water-cooling motor drawing and specification are suitable for
water cooling condition, and coolant temperature is 20°C. Taking oil as coolant is also acceptable. Just
properly modify the performance of motor based on the features of coolant. The cooling condition indicated
in specification: coil temperature should be under 120°C when motor stator continuously operates under
continuous torque. If equivalent torque of actual operation is lower than continuous torque indicated in
specification, reduce cooling water flow to avoid consuming excess pump. The cooling condition can be
properly adjusted based on the following formulas.
Adjust the boundary conditions of water cooling system according to the motor power loss:
When equivalent torque is lower than continuous torque (Te< Tc), get the corresponding coolant flow from
the following formulas.
2
e
c
c
e
T
T
P
P
=
Δθq69.7P
ee
⋅⋅=
e
P
= Total loss of motor under equivalent torque [W]
Δθ = Temperature difference between motor inlet and outlet [°C]
e
q
= Coolant flow [l/min] (under equivalent torque)
Other manuals for TMRW Series
1
This manual suits for next models
70
Table of contents
Other Hiwin Engine manuals
Popular Engine manuals by other brands
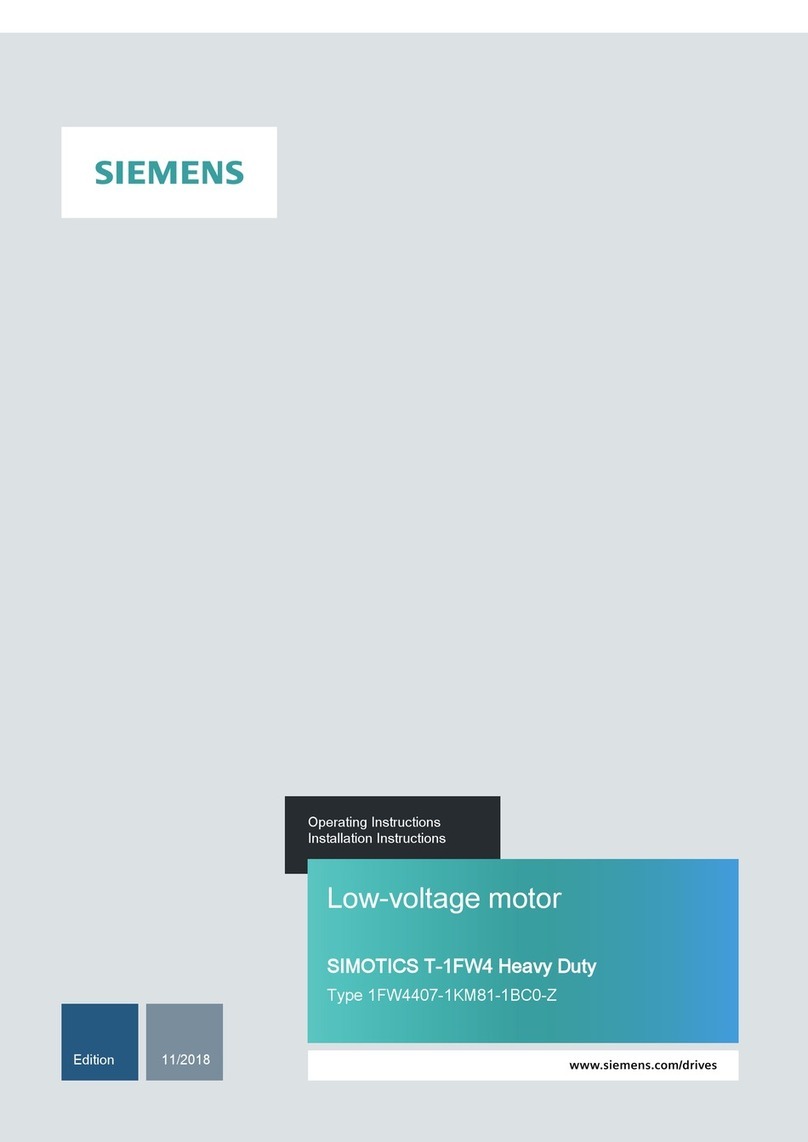
Siemens
Siemens SIMOTICS T-1FW4407-1KM81-1BC0-Z operating instructions

Tecumseh
Tecumseh TVT691 Operator's manual
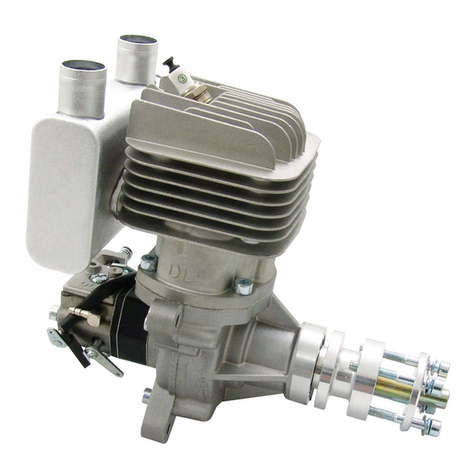
DLE
DLE DLE55RA user manual
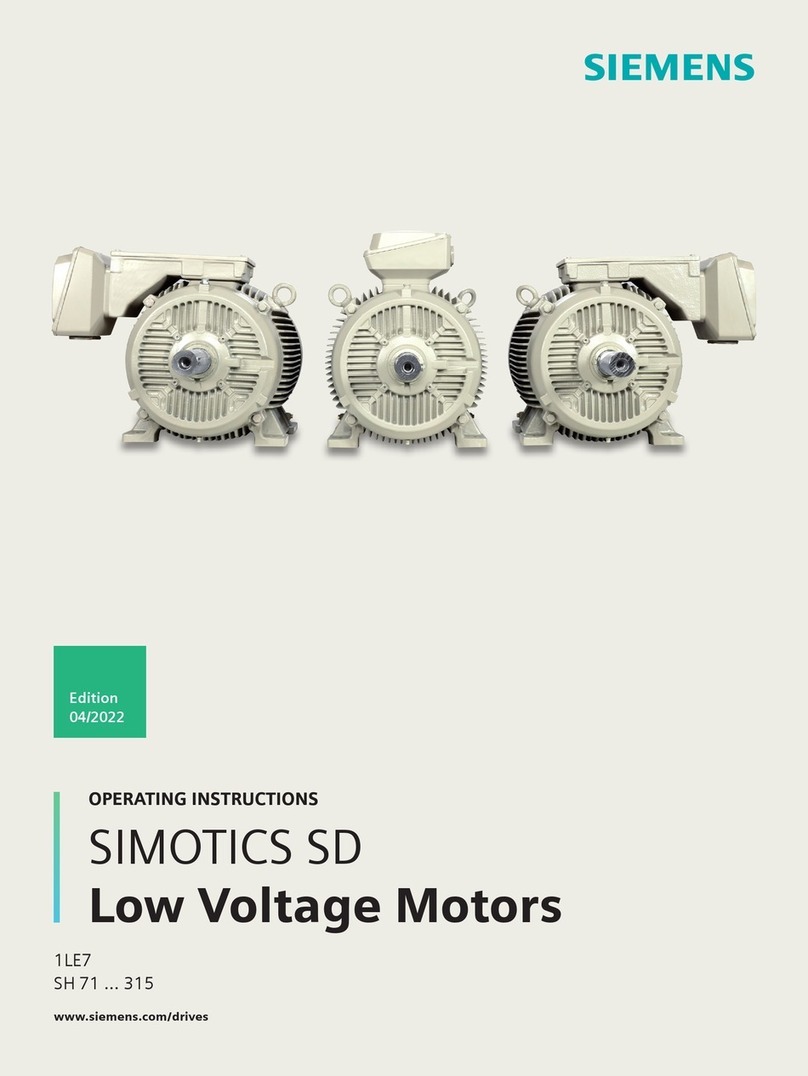
Siemens
Siemens SIMOTICS SD SH 71 315 Series operating instructions
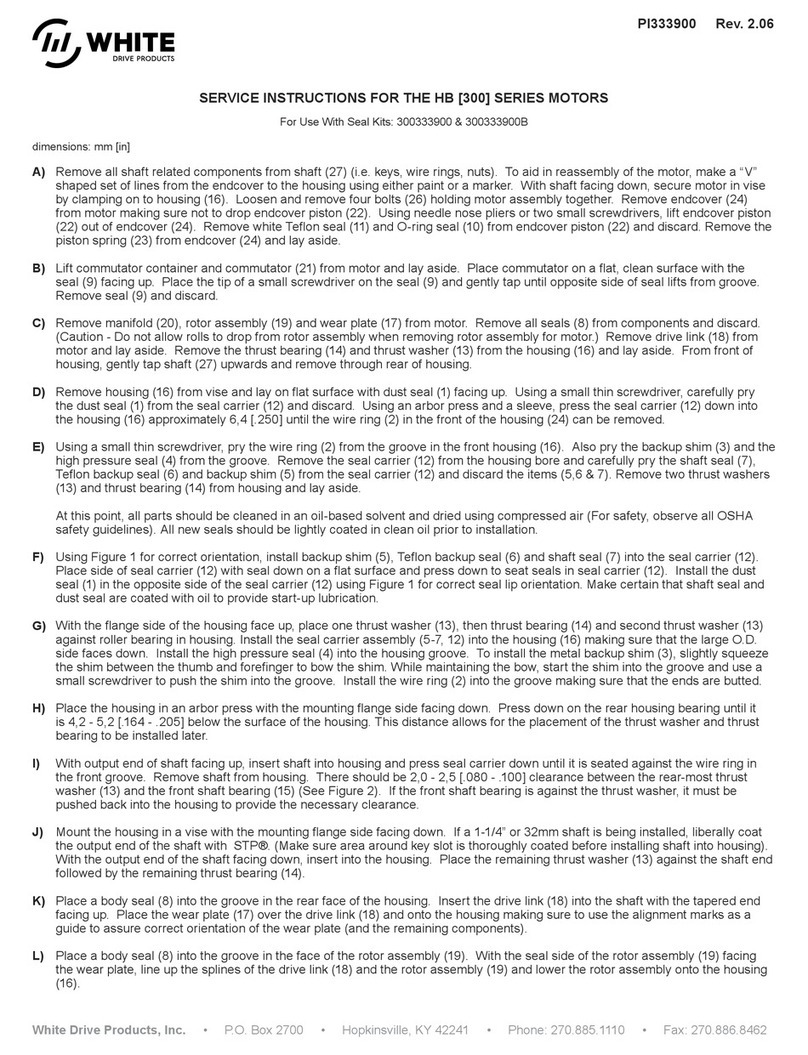
White
White HB 300 Series Service instructions
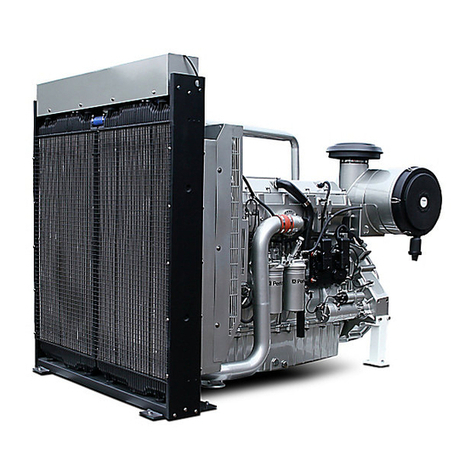
Perkins
Perkins 2806C-E18TA Operation and maintenance manual