HOLEMAKER HMPRO36AD User manual

HOLEMAKER HMPRO36AD
Holemaker Portable Magnetic Drilling Machine
OPERATOR’S MANUAL
Holemaker Portable Magnetic Drilling Machine
OPERATOR’S MANUAL
WARNING!
BEFORE USE,ENSURE EVERYONE USING THIS MACHINE READS AND UNDERSTANDS
ALL SAFETY AND OPERATING INSTRUCTIONS IN THIS MANUAL .
esahcruPfoetaD#laireS
HOLEMAKER PRO 50
BEWARE OF
ROTATING
MACHINE PARTS
LINE VOLTAGE
PRESENT
NEVER PLACE
FINGERS NEAR
CUTTING AREA OR
MACHINE ARBOR
HEARING PROTECTION
REQUIRED
EYE PROTECTION
REQUIRED
Ver: 1.10 14/08/2015
Holemaker Portable Magnetic Drilling Machine
OPERATOR’S MANUAL
WARNING!
BEFORE USE,ENSURE EVERYONE USING THIS MACHINE READS AND UNDERSTANDS
ALL SAFETY AND OPERATING INSTRUCTIONS IN THIS MANUAL .
esahcruPfoetaD#laireS
HOLEMAKER PRO 50
BEWARE OF
ROTATING
MACHINE PARTS
LINE VOLTAGE
PRESENT
NEVER PLACE
FINGERS NEAR
CUTTING AREA OR
MACHINE ARBOR
HEARING PROTECTION
REQUIRED
EYE PROTECTION
REQUIRED
Ver: 1.10 14/08/2015
Ver: 1.01 31/07/2018
OPERATOR’S MANUAL
PRO 36
PRO 36 AD
AD
DRILLING MACHINE
WITH ELECTROMAGNETIC BASE
ul. Elewatorska 23/1, 15-620 Białystok, Poland
Phone: +48 85 678-34-00, Fax: +48 85 651-15-31
www.promotech.eu e-mail: office@promotech.eu

HMPRO36AD OPERATOR’S MANUAL
2
www.holemaker.com
LIMITED WARRANTY
Industrial Tool & Machinery Sales (hereinafter refered to as ITMS) will, within twelve (12)
months from the original date of purchase, repair or replace any goods found to be defective
in materials or workmanship.
This warranty is void if the item has been damaged by accident, neglect, improper service or
other causes not arising out of defects in materials or workmanship. This warranty does not
apply to machines and/or components which have been altered, changed, or modified in any
way, or subjected to overloading or use beyond recommended capacities and specifications.
Worn componentry due to normal wear and tear is not a warranty claim. Goods returned
defective shall be returned prepaid freight to ITMS or agreed repair agent, which shall be the
buyer’s sole and exclusive remedy for defective goods. ITMS accepts no additional liability
pursuant to this guarantee for the costs of travelling or transportation of the product or parts to
and from ITMS or the service agent or dealer, such costs are not included in this warranty.
Our goods come with guarantees which cannot be excluded under the Australian Consumer
Law. You are entitled to replacement or refund for a major failure and to compensation
for other reasonably foreseeable loss or damage. You are also entitled to have the goods
repaired or replaced if the goods fail to be of acceptable quality and the failure does not
amount to a major failure.
THE MANUFACTURER RESERVES THE RIGHT TO MAKE IMPROVEMENTS AND
MODIFICATIONS TO DESIGN WITHOUT PRIOR NOTICE.
PRODUCTS IMPORTED AND DISTRIBUTED NATIONALLY BY:
INDUSTRIAL TOOL & MACHINERY SALES
18 BUSINESS ST, YATALA QLD 4207
F: 07 3287 1115 W: www.industrialtool.com.au
CONTENTS
1. GENERAL INFORMATION 3
1.1. Application 3
1.2. Technical data 3
1.3. Equipment included 4
1.4. Dimensions 5
1.5. Design 5
2. SAFETY PRECAUTIONS 6
3. STARTUP AND OPERATION 7
3.1. Installing and removing the handle 7
3.2. Installing, removing, and operating the annular cutter 8
3.3. Preparing 10
3.4. Drilling 12
3.5. Replacing the motor brushes 13
4. WIRING DIAGRAM 15

HMPRO36AD OPERATOR’S MANUAL
www.holemaker.com
3
CONTENTS
1. GENERAL INFORMATION 3
1.1. Application 3
1.2. Technical data 3
1.3. Equipment included 4
1.4. Dimensions 5
1.5. Design 5
2. SAFETY PRECAUTIONS 6
3. STARTUP AND OPERATION 7
3.1. Installing and removing the handle 7
3.2. Installing, removing, and operating the annular cutter 8
3.3. Preparing 10
3.4. Drilling 12
3.5. Replacing the motor brushes 13
4. WIRING DIAGRAM 15
PRO 36 AD
1. GENERAL INFORMATION
1.1. Application
The PRO 36 AD is a drilling machine with electromagnetic base, designed to drill
holes with diameters of up to 36 mm (1-7/16’’) either to a depth of up to 20 mm
(13/16’’) by using HSS annular cutters or to a depth of up to 30 mm (1-3/16’’) by using
TCT annular cutters. When using twist drill bits with a 19 mm (3/4’’) Weldon shank you
can drill holes with diameters of up to 12 mm (1/2’’) to a depth of up to 20 mm
(13/16’’).
The electromagnetic base allows the drilling machine to be fixed to ferromagnetic
surfaces with a force that ensures operator safety and proper machine operation.
A safety strap protects the machine from falling in case of a power loss.
With an optional HSS quill assembly you can drill holes to a depth of up to 25 mm
(1’’) by using HSS cutters or twist drill bits with a 19 mm Weldon shank.
1.2. Technical data
Voltage 1~ 110–120 V, 50–60 Hz
1~ 220–240 V, 50–60 Hz
Total power 1000 W
Motor power 920 W
Tool holder 19 mm (3/4’’) Weldon
Maximum drilling diameter with annular cutter 36 mm (1-7/16’’)
Maximum drilling diameter with twist drill bit 12 mm (1/2’’)
Maximum drilling depth with HSS cutter or drill bit 20 mm (13/16’’)*
Maximum drilling depth with TCT cutter 30 mm (1-3/16’’)
Electromagnetic base holding force
(surface with the thickness of 25 mm and roughness Ra = 1.25) 8 900 N
Electromagnetic base dimensions 90 mm × 180 mm × 38.5 mm
3-9/16’’ × 7-1/16’’ × 1-1/2’’
Stroke 39 mm (1-1/2’’)
Rotational speed without load 550 rpm (for 115 V)
580 rpm (for 230 V)
Rotational speed under load 350 rpm (for 115 V)
370 rpm (for 230 V)
Minimum workpiece thickness 6 mm (1/4’’)
Protection class I
Noise level More than 85 dB
Required ambient temperature 0–40°C (32–104°F)
Weight 9.5 kg (21 lbs)
* Up to 25 mm (1’’) when used with an optional HSS quill assembly (ZSP-0521-04-00-00-0).
This document is protected by copyrights.
Copying, using, or distributing without permission of PROMOTECH is prohibited.
3

HMPRO36AD OPERATOR’S MANUAL
4
www.holemaker.com
PRO 36 AD
84 mm hex wrench 1
unit
–Operator’s Manual 1
unit
1.4. Dimensions
1.5. Design
This document is protected by copyrights.
Copying, using, or distributing without permission of PROMOTECH is prohibited.
5
176 mm (6-15/16’’)
147 mm (5-13/16’’) 380 mm (14-15/16’’)
MOTOR
stopbutton
Electromagnetic base
(MAGNET) switch
MOTOR
startbutton
Carrying handle
Electromagnetic base
Chip guard
Opening for safety strap
Control panel
TCT quill assembly including spindle with arbor
PRO 36 AD
1.3. Equipment included
1Drilling machine 1
unit
2Plastic box 1
unit
3Handle 1
unit
4Handle adapter 1
unit
5Pilot pin 7.98x85 for TCT cutters 1
unit
6Pilot pin 6.34x74 for HSS cutters 1
unit
7Safety strap 1
unit
This document is protected by copyrights.
Copying, using, or distributing without permission of PROMOTECH is prohibited.
4
1
2
3
4
5
6
7
8
PRO 36 AD
1.3. Equipment included
1Drilling machine 1
unit
2Plastic box 1
unit
3Handle 1
unit
4Handle adapter 1
unit
5Pilot pin 7.98x85 for TCT cutters 1
unit
6Pilot pin 6.34x74 for HSS cutters 1
unit
7Safety strap 1
unit
This document is protected by copyrights.
Copying, using, or distributing without permission of PROMOTECH is prohibited.
4
1
2
3
4
5
6
7
8
PRO 36 AD
1.3. Equipment included
1Drilling machine 1
unit
2Plastic box 1
unit
3Handle 1
unit
4Handle adapter 1
unit
5Pilot pin 7.98x85 for TCT cutters 1
unit
6Pilot pin 6.34x74 for HSS cutters 1
unit
7Safety strap 1
unit
This document is protected by copyrights.
Copying, using, or distributing without permission of PROMOTECH is prohibited.
4
1
2
3
4
5
6
7
8
PRO 36 AD
1.3. Equipment included
1Drilling machine 1
unit
2Plastic box 1
unit
3Handle 1
unit
4Handle adapter 1
unit
5Pilot pin 7.98x85 for TCT cutters 1
unit
6Pilot pin 6.34x74 for HSS cutters 1
unit
7Safety strap 1
unit
This document is protected by copyrights.
Copying, using, or distributing without permission of PROMOTECH is prohibited.
4
1
2
3
4
5
6
7
8

HMPRO36AD OPERATOR’S MANUAL
www.holemaker.com
5
"
G
176 mm (6-15/16’’)

HMPRO36AD OPERATOR’S MANUAL
6
www.holemaker.com
2. SAFETY PRECAUTIONS
Drilling machine must not be used when:
1. The operator has not read the Operator’s Manual.
2. The work to be done is not in agreement with the recommendations in this Manual.
3. Drilling machine is not complete or has been repaired with non-original parts.
4. Power supply parameters do not conform to those stated on the motor’s plate.
5. Machines operator has not checked condition of the drilling machine, condition of air hose,
control panel or cutting tool.
6. Machine is not secured with safety chain as a protection from falling down especially when
used at heights or in vertical or upside-down positions.
7. Bystanders are present in the immediate vicinity of machine.
Important rules of safe use of drilling machine
1. Before attempting to work with the machine check condition of air hose and coupling.
2. Make sure that the drill is supplied with purified air and oiled.
3. Machine can be used outdoors, but is not weatherproof. Do not expose to rain, snow or
frost.
4. Machine should not be used on: rusty surfaces, steel plates covered with paint, uneven
surfaces, or steel plate which is being welded on.
5. Do not use the machine in explosion hazard zones.
6. Do not start work if the machine has excessive play on guide slides.
7. Always wear safety goggles and ear protection.
8. Do not remove metal chips with bare hands, always use gloves.
9. Do not touch the spindle and cutting tool during work.
10.Cutting Tools must be fastened firmly.
11.Do not drill with blunt of damaged cutting tools.
12.Do not use annular cutters without a pilot pin, and arbors without an ejection spring.
Do not touch or replace the cutting tool with power source on
13.After use, always clean drilling machine from metal chips and cutting fluid.
14.Any maintenance and repair should be performed only when the machine is disconnected
from the air supply.
15.Before each use the machine should be checked for the presence of damage. Check
whether any of the parts are broken and all the that all parts are fasten properly.
16.In the case that the machine falls on a hard surface, from a height, is wet or is subjected
to other unfortunate events that could affect its technical state - work should be terminated
immediately and the machine should be sent to service for inspection as soon as possible.
This machine is not recommended to be used to drill on steel thinner than 10mm (3/8”).
On thin steel less than 10mm (3/8”) magnet’s adhesive power would be significantly
reduced which can cause machines failure or personal injury.
HMP45
OPERATORS MANUAL – HOLEMAKER HMP45 5
10) Do not touch the spindle and cutting tool during work.
11) Cutting Tools must be fastened firmly.
12) Do not drill with blunt of damaged cutting tools.
13) Do not use annular cutters without a pilot pin, and arbors without an ejection spring.
Do not touch or replace the cutting tool with power source on
14) After use, always clean drilling machine from metal chips and cutting fluid.
15) Any maintenance and repair should be performed only when the machine is
disconnected from the air supply.
16) Before each use the machine should be checked for the presence of damage.
Check whether any of the parts are broken and all the that all parts are fasten properly.
17) In the case that the machine falls on a hard surface, from a height, is wet or is subjected
to other unfortunate events that could affect its technical state - work should be
terminated immediately and the machine should be sent to service for inspection as
soon as possible.
This machine is not recommended to be used to drill on steel thinner
than 10mm (3/8”). On thin steel less than 10mm (3/8”) magnet’s adhesive power
would be significantly reduced which can cause machines failure or personal
injury.
The pneumatic motor used in Holemaker HMP45 drilling machine is ATEX II2 G/D C
IIC T6;T4 certified, which is required for usage in explosion risk zones.
CAUTION:
Never carry the drill by the motor's air supply hose!

HMPRO36AD OPERATOR’S MANUAL
www.holemaker.com
7
PRO 36 AD
3. STARTUP AND OPERATION
3.1. Installing and removing the handle
Install the handle by using the adapter as shown in Fig. 1. The handle can be installed
from the opposite side of the machine to allow working in places hard to reach or
using the machine by a left-handed person.
To remove the handle, pull it out.
Fig. 1. Installing the handle
This document is protected by copyrights.
Copying, using, or distributing without permission of PROMOTECH is prohibited.
8

HMPRO36AD OPERATOR’S MANUAL
8
www.holemaker.com
PRO 36 AD
3.2. Installing, removing, and operating the annular cutter
Unplug the machine from the power source, raise the chip guard, and then rotate the
handle to the left (1, Fig. 2) to access the set screws (2). Next, wear protective gloves,
insert the required pilot pin into the annular cutter (3), and then use a clean and dry
cloth to wipe the arbor and cutter. Next, place the cutter into the arbor (4) so that the
flats (5) are aligned with the set screws (2), and then use the 4 mm hex wrench to
tighten both set screws.
To remove the cutter, loosen the screws (2) with the 4 mm hex wrench.
Fig. 2. Installing the annular cutter
This document is protected by copyrights.
Copying, using, or distributing without permission of PROMOTECH is prohibited.
9
3
4
2
5
1

HMPRO36AD OPERATOR’S MANUAL
www.holemaker.com
9
PRO 36 AD
Fig. 3 shows how annular cutters work. As the cutter penetrates the workpiece, the
pilot pin recesses into the arbor and tightens the spring. As a result, after the cutter
goes through the entire thickness, the slug core is expelled from the cutter.
Fig. 3. Annular cutters work
Annular cutters are designed to make only through holes shown in Fig. 4. When
drilling incomplete through holes the pilot pin must not be used.
Fig. 4. Types of holes to make with annular cutter
This document is protected by copyrights.
Copying, using, or distributing without permission of PROMOTECH is prohibited.
10
Slug core
Spring
Pilot pin
Annular cutter
Arbor
Incomplete through holes
Complete through holes

HMPRO36AD OPERATOR’S MANUAL
10
www.holemaker.com
PRO 36 AD
3.3. Preparing
Before starting, clean steel parts, including the arbor, from anti-corrosion coating
used to preserve the machine for storage and transport.
Install the handle as described before.
Based on the hole size desired, select the proper annular cutter or drill bit with a
19 mm Weldon shank. Next, use a clean and dry cloth to wipe the arbor and cutter
(drill bit), and then install the cutter (drill bit) into the arbor as described before.
Position the machine on a flat ferromagnetic surface with a thickness of at least
6 mm (1/4’’). The workpiece must be clean, without rust or paint that decrease the
holding force. The force value depends also on the type, thickness, flatness, and
roughness of the surface, fluctuations of the supply voltage, and the wear of the
electromagnetic base bottom. Some types of steel are non-ferromagnetic (do not
conduct magnetic flux) and the machine is not capable to clamp onto them.
Connect the machine to the power source, and set the MAGNET switch to ‘I’ to
turn on the clamping of the electromagnetic base.
Use the safety strap to prevent the machine from falling and avoid possible injury
to the operator if the machine loses magnetic clamping in case of a power loss. To
protect the machine, insert the strap through the opening in the machine body and
attach the machine to a fixed structure. The strap must be tight, not twisted (except
standard twist for horizontal drilling from Fig. 5c), and must be replaced every single
time the machine hangs on the strap as a result of coming loose from steel. Never
insert the strap into the buckle from the front (Fig. 5d).
This document is protected by copyrights.
Copying, using, or distributing without permission of PROMOTECH is prohibited.
11

HMPRO36AD OPERATOR’S MANUAL
www.holemaker.com
11
PRO 36 AD
Fig. 5. Protecting the machine from falling by using the safety strap
Rotate the handle to the left to place the pilot pin (drill bit) above the workpiece.
Fill the coolant bottle (not included) with a cutting fluid. Do not use pure water as
the cutting fluid. However, using emulsions formed from mixing water and drilling oil
is satisfactory.
When drilling in vertical positions (Fig. 5a), apply the coolant manually into the
drilling area. When drilling in inverted or horizontal positions (Fig. 5b, 5c) use coolants
under pressure or in the form of spray or paste.
This document is protected by copyrights.
Copying, using, or distributing without permission of PROMOTECH is prohibited.
12
a) b)
Vertical drilling Inverted drilling
c)
Horizontal drilling
Maximum possible
twist of the strap
d)
INCORRECT
CORRECT
✓

HMPRO36AD OPERATOR’S MANUAL
12
www.holemaker.com
PRO 36 AD
3.4. Drilling
Start the motor with the green MOTOR button, and slowly rotate the handle to the left
to lower the tool to the workpiece, and start drilling.
When using annular cutter, drill holes in one pass.
When using drill bits, drill holes with diameters of 8–12 mm (5/16’’ – 1/2’’) in two
passes. Drill a first hole by using a drill bit with the 70% diameter of the hole size
desired, and then drill again by using a bit with the diameter equal to the hole size
desired.
After the hole is made, retract the tool from the workpiece and press the red
MOTOR button to stop the motor. Before moving the machine to another drilling spot,
set the MAGNET switch to ‘O’ to turn off the electromagnetic base.
After the work is finished, unplug the machine from the power source, clean
chips and excess coolant from the machine and tool, and then remove the machine
from the worksite.
Before inserting the machine into the box, remove the handle, and then wear
gloves to remove the tool from the holder.
This document is protected by copyrights.
Copying, using, or distributing without permission of PROMOTECH is prohibited.
13
When the annular cutter goes through the workpiece, the slug
core is expelled from the cutter with a significant force.

HMPRO36AD OPERATOR’S MANUAL
www.holemaker.com
13
PRO 36 AD
3.5. Replacing the motor brushes
Check the condition of the carbon brushes every 100 work hours. To do this, unplug the
machine from the power source, and unscrew the cover (1, Fig. 6). Next, unscrew the
pressing plate (2), and then remove the brush holder (3) and the brush (4). If the
length of the brush is less than 5 mm (3/16’’), replace both brushes with new ones.
To install brushes, proceed in reverse order. After the replacement, run the motor
without load for 20 minutes.
Fig. 6. Replacing the brushes
This document is protected by copyrights.
Copying, using, or distributing without permission of PROMOTECH is prohibited.
14
1
2
3
4

HMPRO36AD OPERATOR’S MANUAL
14
www.holemaker.com
PRO 36 AD
To install the assembly, unplug the machine from the power source, raise the cover,
and then rotate the handle to the left (1, Fig. 7) to lower the standard TCT quill
assembly as much as possible. Next, remove the handle, use pliers to remove the
retaining rings (2), and then push out the shaft (3) by 16 mm (10/16’’), which will expel
the TCT quill assembly (4). Insert the HSS quill assembly (5), push in the shaft (6), and
then place the retaining rings back in place (7).
Fig. 7. Installing the HSS quill assembly
This document is protected by copyrights.
Copying, using, or distributing without permission of PROMOTECH is prohibited.
16
1
7
2
3
4
56
2
7

HMPRO36AD OPERATOR’S MANUAL
www.holemaker.com
15
PRO 36 AD
5. WIRING DIAGRAM
This document is protected by copyrights.
Copying, using, or distributing without permission of PROMOTECH is prohibited.
17
PRO 36 AD
5. WIRING DIAGRAM
This document is protected by copyrights.
Copying, using, or distributing without permission of PROMOTECH is prohibited.
17

HMPRO36AD OPERATOR’S MANUAL
16
www.holemaker.com
HOLEMAKER ANNULAR CUTTER GUIDE
Cutter Type Features Diameter Available Cut Depth Available Applications
Silver Series Metric
• M2AL High Speed Steel
• Universal Shank
• Multi-Cut Geometry
• Step Hardened
• 12 to 60mm Metric • 25mm & 50mm • General Purpose
Silver Series Imperial
• M2AL High Speed Steel
• Multi-Cut Geometry
• Step Hardened
• 7/16" to 2-1/4" Imperial • 1", 2" & 3" • General Purpose
Gold Series Metric • M2AL High Speed Steel
• Titanium Nitride Coated
• Universal Shank
• Multi-Cut Geometry
• Step Hardened
• 12 to 60mm Metric • 25mm, 50mm & 75mm • General Purpose
Super-Cut • Made In U.S.A
• Highest Quality
• M2 High Speed Steel
• Multi-Cut Geometry
• 12 to 60mm Metric
• 7/16" to 2-1/2" Imperial
• 25mm, 50mm & 75mm
• 1", 2" & 3" • General Purpose
Super-Cut TICN
• Titanium Carbon
Nitride Coated
• Made In U.S.A
• M2 High Speed Steel
• Multi-Cut Geometry
• 12 to 32mm Metric • 25mm & 50mm • Stainless Steel
• Cast Iron
Super-Cut M42 Cobalt
• M42 High Speed Steel
• 8% Cobalt
• Titanium Nitride Coated
• Made In U.S.A
• Multi-Cut Geometry
• 1/2" to 1" Imperial • 1" • Truck Chassis
• Hardened Steels
Super-Cut M42 Chassis
• Stack Ground Geometry
• M42 High Speed Steel
• 8% Cobalt
• Titanium Nitride Coated
• Made In U.S.A
• 1/2" to 1" Imperial • 1" • Truck Chassis
• Multi-Layered Steel
Pro-Cut
• ASP Powder Steel
• Multi-Cut Geometry
• Incredible Performance
• 12 to 22mm Metric • 25mm & 50mm
• Rail Line
• Hard Materials
• Stainless Steel
• Wear Plate
Maxi-Cut
• Tungsten Carbide Tipped
• Increased Resistance
to Breakage
• Multi-Cut Geometry
• 14 to 150mm Metric
• 5/8" to 2-3/8" Imperial
• 50mm, 75mm
& 100mm
• Large Diameters
• Stainless Steel
• Hard Materials
• Wear Plate
Maxi-Rail
• Tungsten Carbide Tipped
• Increased Resistance
To Breakage
• Multi-Cut Geometry
• 18 to 35mm Metric • 25mm
• Rail Line
• Hard Materials
• Wear Plate

HM PRO 36 AD
1
6
2
5
4
3
1
6
2
5
4
3
ITEM
PART NUMBER
DESCRIPTION
Q-TY
1
SKR-000012
PLASTIC BOX
1
2
PAS-000007
SAFETY STRAP 250
1
3
PLT-0378-15-00-00-0
PILOT PIN
1
4
KLC-000007
4 MM HEX WRENCH
1
5
PRD-000002
TORQUE STICK
1
6
KLC-000048
RATCHET WRENCH 3-8
1

HM PRO 36 AD
52 53
54
55
49
4
25 26
42
45
18
19
40
39
51
57
59
38
50
17
48
44
37
41
56
46
30
36
16
35
20
34
21
47
33
22
32
31
43
58
23
15
14
29
13
28
27
3
24
9
8
7
12 11
10
3
6
5
2
1
ITEM
PART NUMBER
DESCRIPTION
Q-TY
1
WKR-000098
HEX SOCKET BUTTON HEAD SCREW M5x16
6
2
PKR-0521-02-00-00-1
GEARBOX COVER
1
3
KLK-000044
DOWEL PIN 5n6x10
3
4
KOL-0521-08-00-00-0
GEAR z63 ASSY
1
5
PRS-000223
EXTERNAL RETAINING RING 25z TYPE A
1
6
LOZ-000169
BALL BEARING 25x42x9
1

HM PRO 36 AD
ITEM
PART NUMBER
DESCRIPTION
Q-TY
7
KOL-0521-08-01-00-0
GEAR z63
1
8
LOZ-000100
BALL BEARING 30x42x7
1
9
PRS-000021
EXTERNAL RETAINING RING 30z TYPE A
1
10
SPR-000063
DISC SPRING fi27.99xfi21.74x0.3
1
11
WLK-0521-07-00-00-0
PINION SHAFT z16 z32 ASSY
1
12
LOZ-000038
BALL BEARING 12x28x8
2
13
PDK-000221
WASHER 20x28x0.1
2
14
PDK-0521-13-00-00-0
SETTING WASHER
1
15
SLN-0521-03-00-00-1
MOTOR ASSY - 120V
1
15
SLN-0521-03-00-00-3
MOTOR ASSY - 230V
1
16
NSD-000009
HANDLE COVER
1
17
UCW-0521-12-00-00-0
HANDLE
1
18
WKR-000101
HEX SOCKET BUTTON HEAD SCREW M6x16
2
19
PDK-000021
ROUND WASHER 6.4
4
20
PRS-000019
EXTERNAL RETAINING RING 28z
2
21
PRS-000259
SEAL 20x28x4
1
22
TLJ-000010
SELF-LUBRICATING SLEEVE 28.05x32x1
2
23
KRP-0521-01-01-00-1
BODY
1
24
WLK-0521-10-00-00-0
FEED SHAFT z20
1
25
WKR-000302
SELF-TAPPING SCREW 5x30
4
26
WKR-000395
HEX SOCKET ROUND HEAD SCREW WITH FLANGE M5x20
2
27
PDK-000151
NYLON WASHER 8.1x14x3
4
28
OSL-0521-09-01-00-0
CHIP GUARD
1
29
SPR-000030
SPRING 1x10x17.5
2
30
ZSP-0521-04-00-00-0
QUILL ASSY
1
31
PRS-000011
EXTERNAL RETAINING RING 20z
1
32
TLJ-0521-04-01-00-0
QUILL CARRIER
1
33
LOZ-000045
BALL BEARING 20x42x12
1
34
PRS-000026
INTERNAL RETAINING RING 42w
1
35
WRZ-0378-03-02-00-0
SPINDLE
1
36
WKR-000063
HEX SOCKET SET SCREW WITH FLAT POINT M8x8
2
37
SPR-0378-03-04-00-0
SPRING
1
38
WYP-0378-03-05-00-0
PLUNGER
1
39
PDK-0139-00-04-00-0
WASHER 18.8x10x1
1
40
PRS-000009
INTERNAL RETAINING RING 19w
1
41
PDS-0521-14-00-00-0
ELECTROMAGNETIC BASE ASSY
1
42
LOZ-000072
BALL BEARING 9x26x8
1
43
WLK-0521-06-00-00-0
PINION SHAFT z11 z26 ASSY
1
44
STR-0521-05-00-00-0
ELECTRONIC CONTROLLER ASSY – 120V
1
44
STR-0521-05-00-01-0
ELECTRONIC CONTROLLER ASSY – 230V (CEE)
1
44
STR-0521-05-00-02-0
ELECTRONIC CONTROLLER ASSY – 230V (AU)
1
44
STR-0521-05-00-03-0
ELECTRONIC CONTROLLER ASSY – 230V (INDIA)
1
45
SZN-0075-00-51-00-5
POWER CORD 120V 3x2.08 WITH STRAIN RELIEF ASSY (US)
1
45
SZN-0212-10-02-00-2
POWER CORD 230V 3x1.5 WITH STRAIN RELIEF ASSY (CEE)
1
45
SZN-0212-10-02-00-1
POWER CORD 230V 3x1 WITH STRAIN RELIEF ASSY (AU)
1
45
PWD-0212-10-02-00-6
POWER CORD 230V 3x1.5 WITH STRAIN RELIEF ASSY (INDIA)
1
46
DLW-000007
CABLE GLAND WITH STRAIN RELIEF PG11
1
47
WKR-000420
COUNTERSUNK HEAD SCREW M3x16
1
48
OBD-0521-05-01-00-0
ELECTRONIC CONTROLLER HOUSING
1
49
WKR-000208
PAN HEAD SCREW M4x10
1
50
PDK-000060
EXTERNAL TOOTH LOCK WASHER 4.3
1
51
NKR-000013
HEX NUT M4
1

HM PRO 36 AD
ITEM
PART NUMBER
DESCRIPTION
Q-TY
52
MDL-0378-14-04-00-4
ELECTRONIC MODULE SW=35A - 230V
1
52
MDL-0378-14-04-00-3
ELECTRONIC MODULE SW=35A - 120V
1
53
PDK-000041
SPRING WASHER 3.1
1
54
NKR-000009
HEX NUT M3
1
55
NKR-000040
STRAIN RELIEF NUT
1
56
WLC-000006
START-STOP SWITCH - 120V
1
56
WLC-000008
START-STOP SWITCH - 230V
1
57
PNK-000013
POWER SWITCH
1
58
WKR-000289
HEX SOCKET BUTTON HEAD SCREW M5x8
4
59
PDK-000043
SPRING WASHER 4.1
1
Table of contents
Other HOLEMAKER Drill manuals
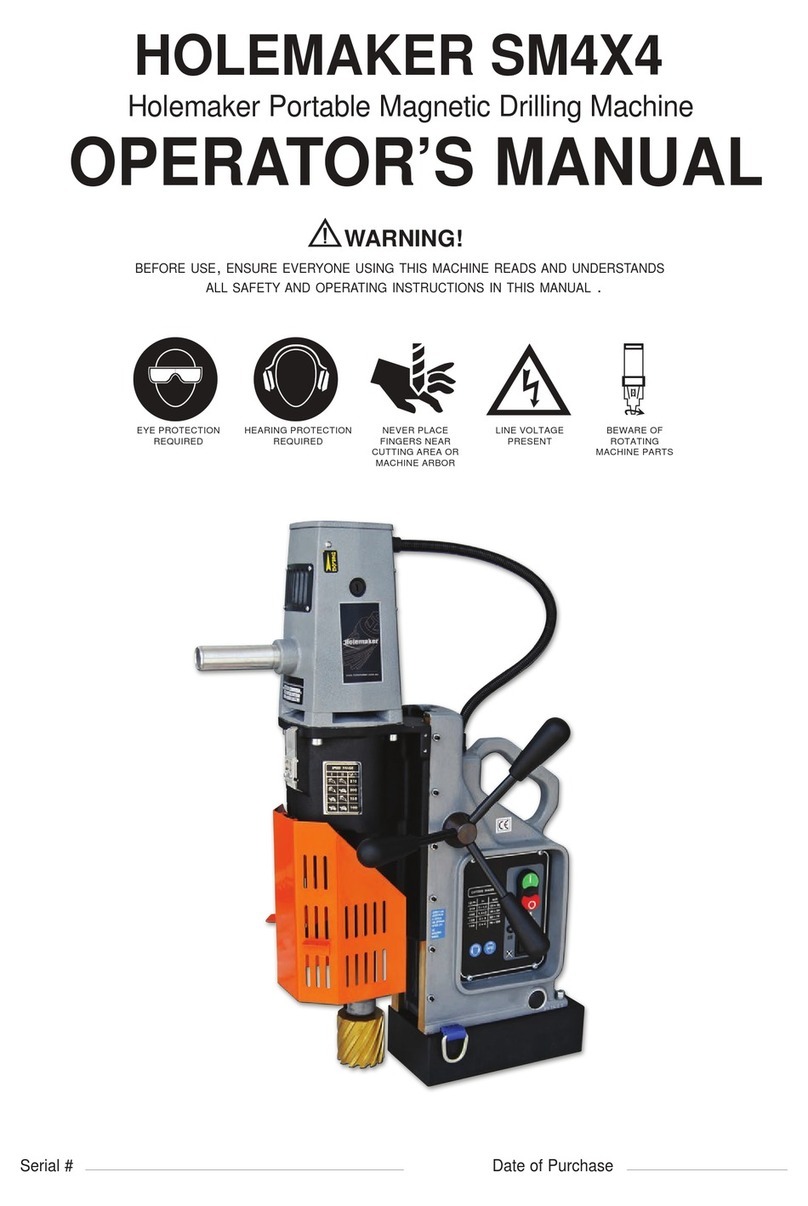
HOLEMAKER
HOLEMAKER SM4X4 User manual
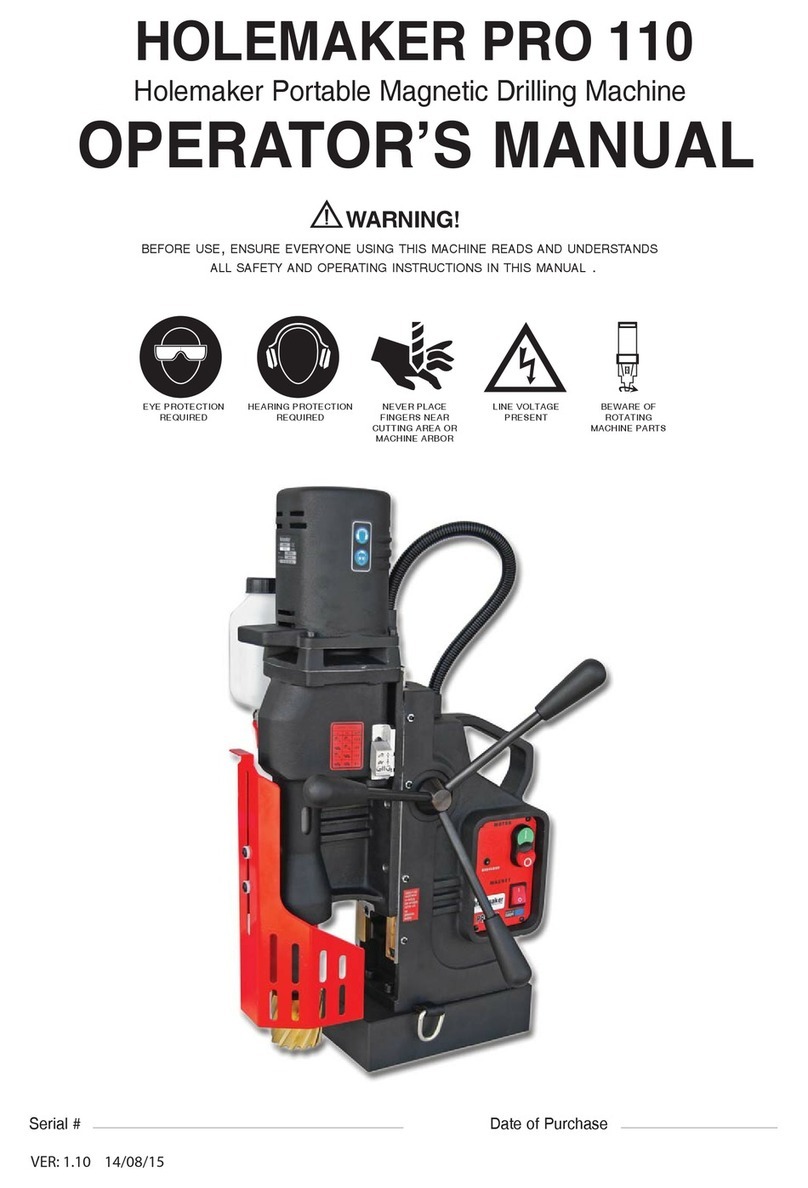
HOLEMAKER
HOLEMAKER PRO 100 User manual
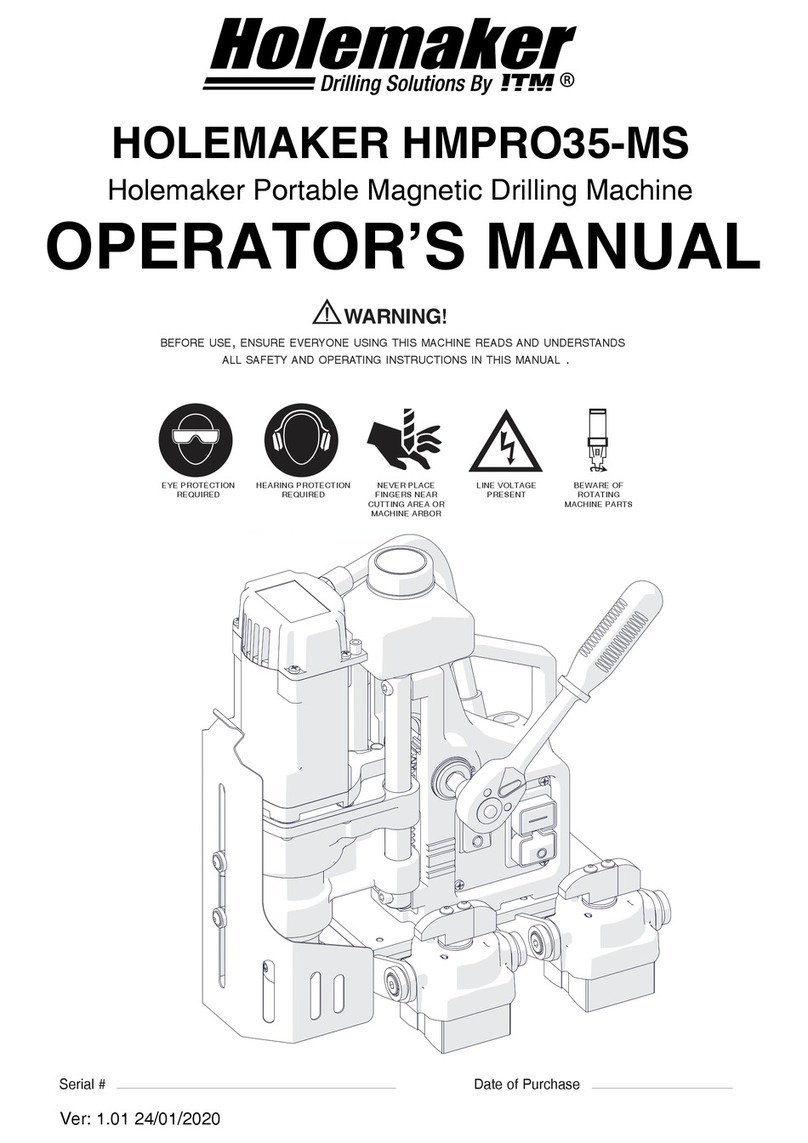
HOLEMAKER
HOLEMAKER HMPRO35-MS User manual
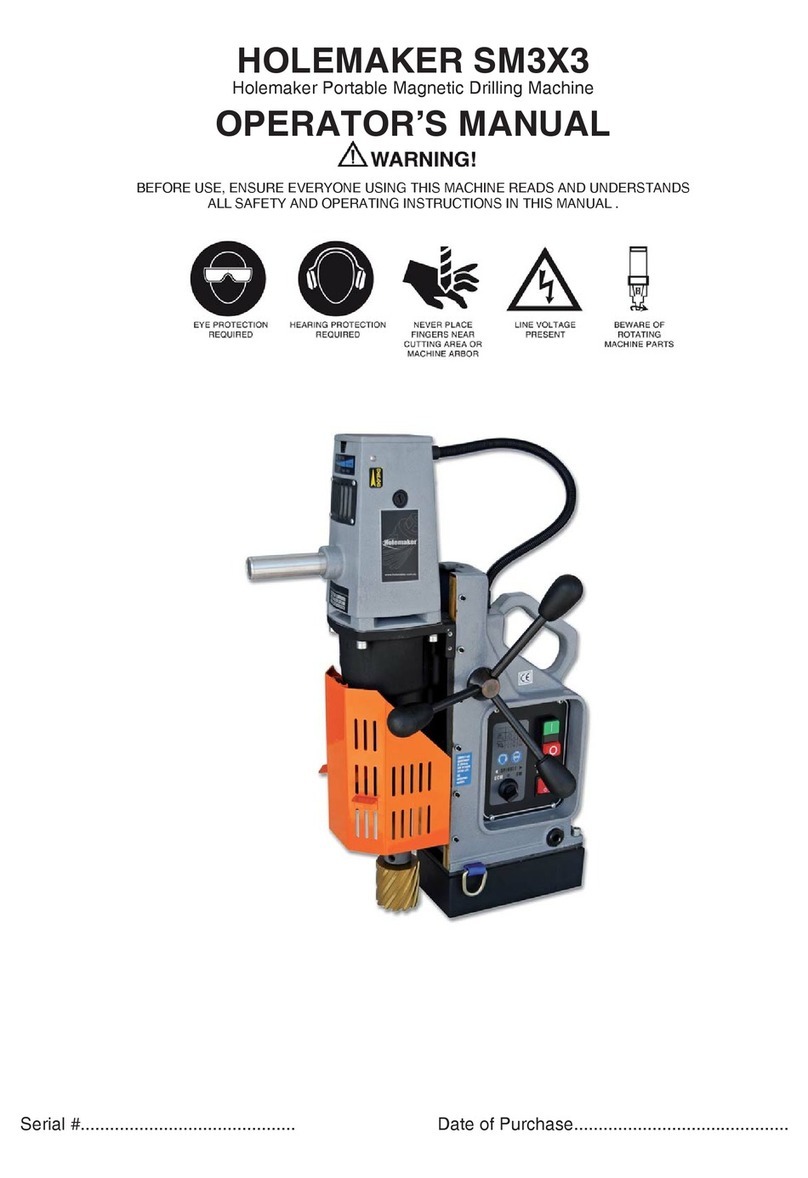
HOLEMAKER
HOLEMAKER Holemaker SM3X3 User manual

HOLEMAKER
HOLEMAKER Pro 35 Auto User manual
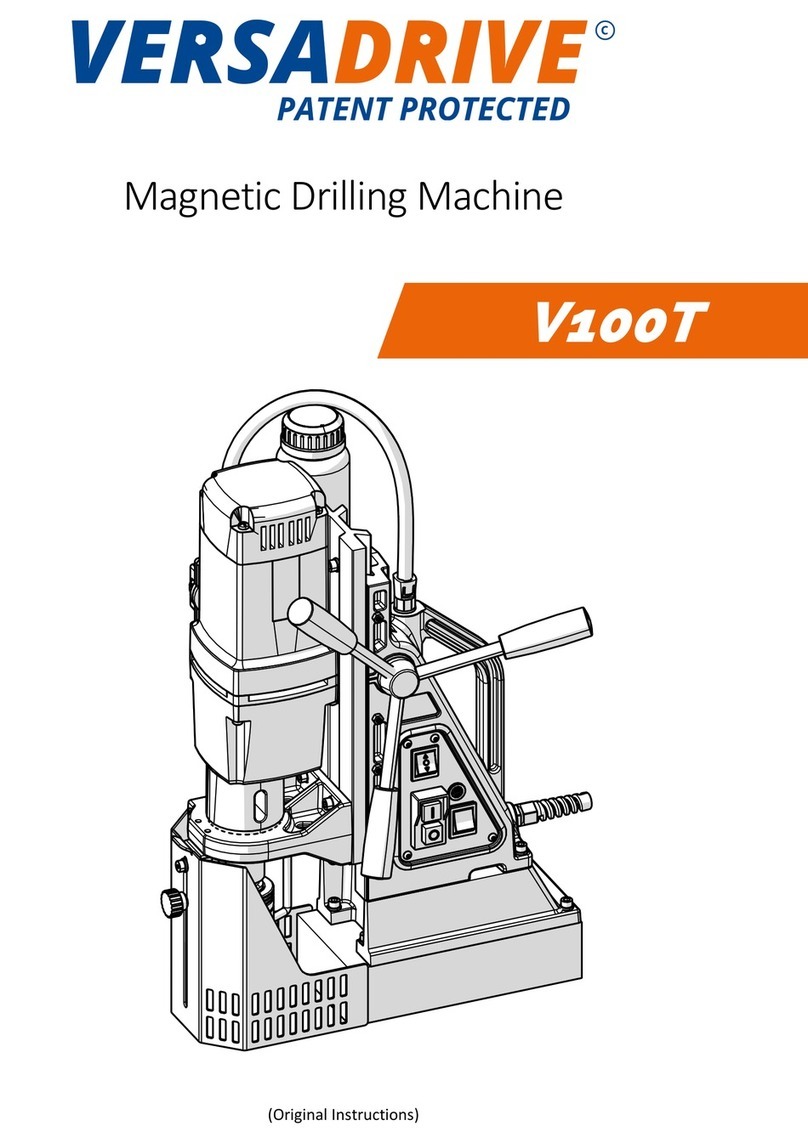
HOLEMAKER
HOLEMAKER VERSADRIVE V100T User manual

HOLEMAKER
HOLEMAKER 35 User manual
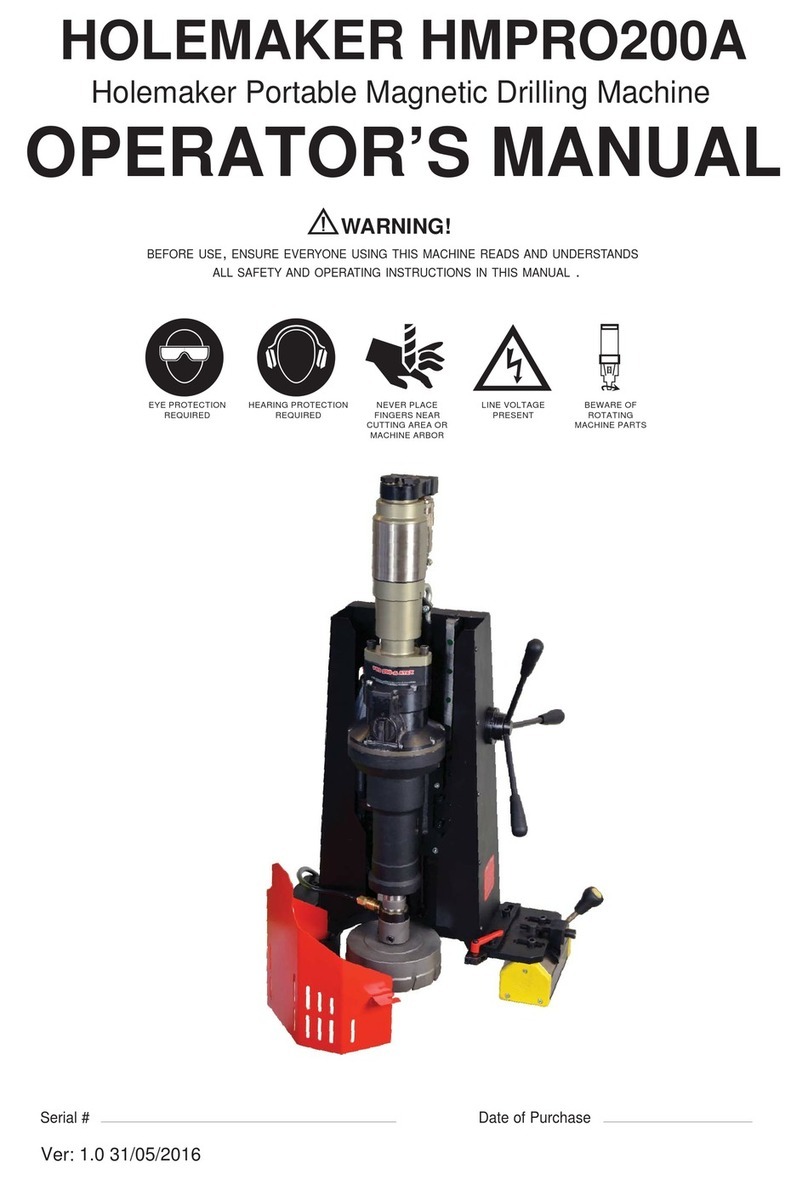
HOLEMAKER
HOLEMAKER HMPRO200A User manual
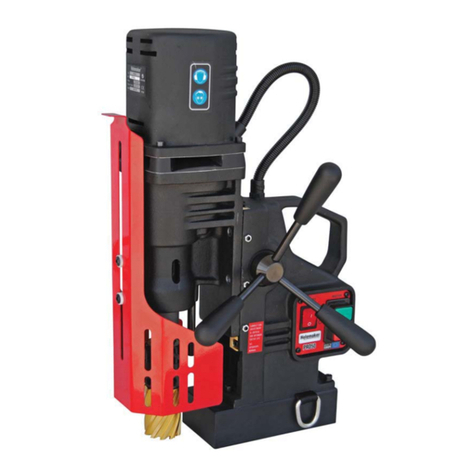
HOLEMAKER
HOLEMAKER PRO 50 User manual
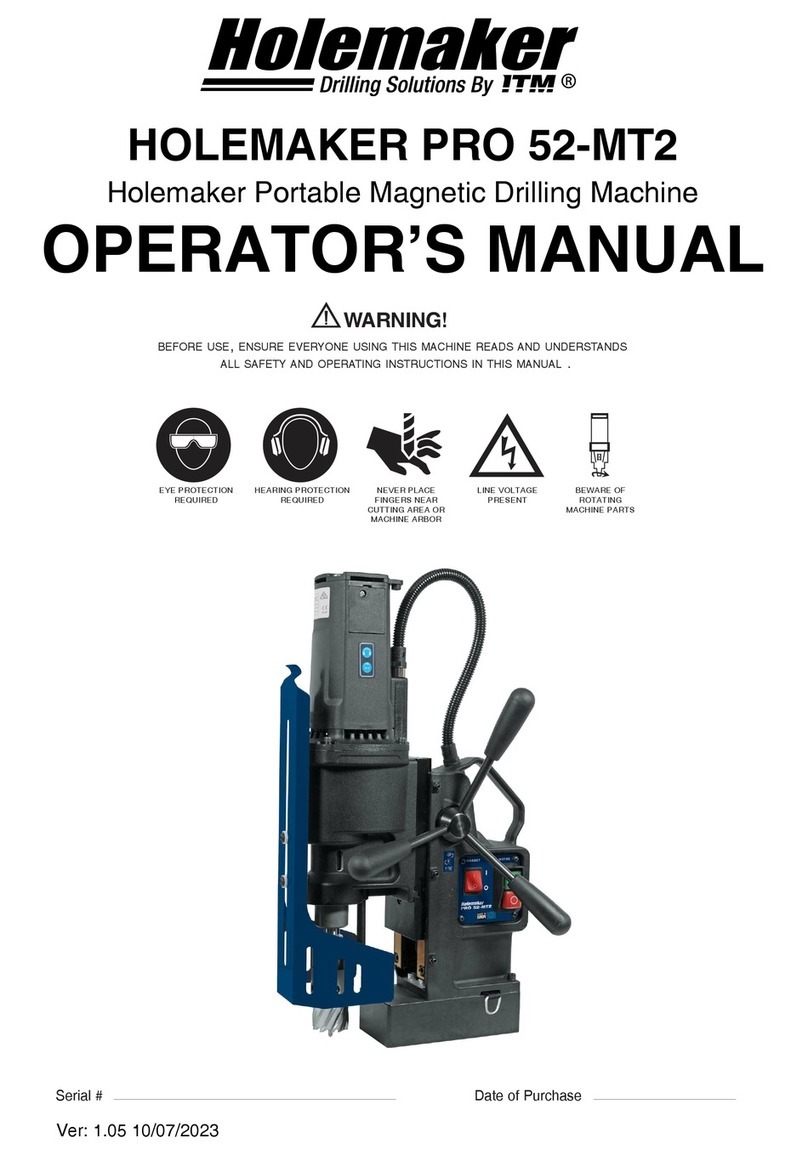
HOLEMAKER
HOLEMAKER PRO 52-MT2 User manual
Popular Drill manuals by other brands

Raider
Raider RDI-HD45 user manual
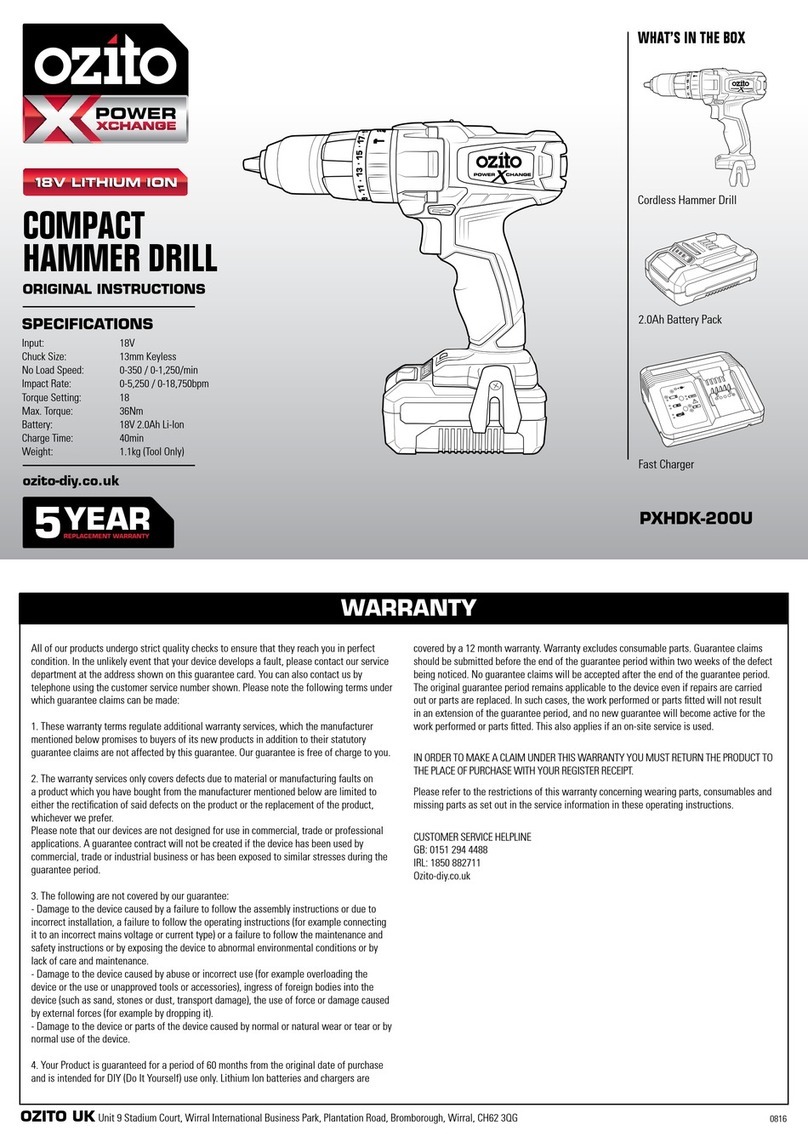
Ozito
Ozito PXHDK-200U Original instructions
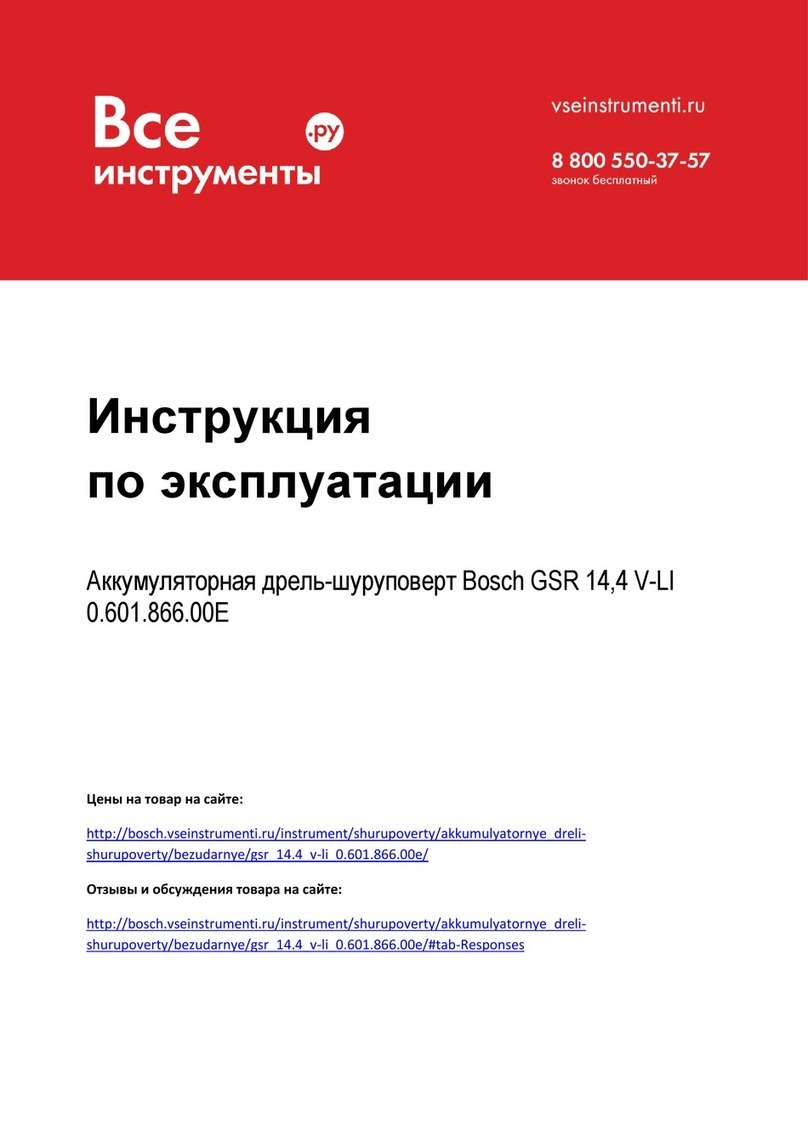
Bosch
Bosch Professional GSR 14,4 V-LI Original instructions
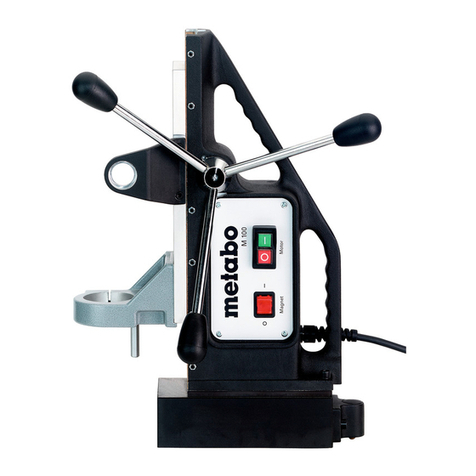
Metabo
Metabo M 100 Original instructions
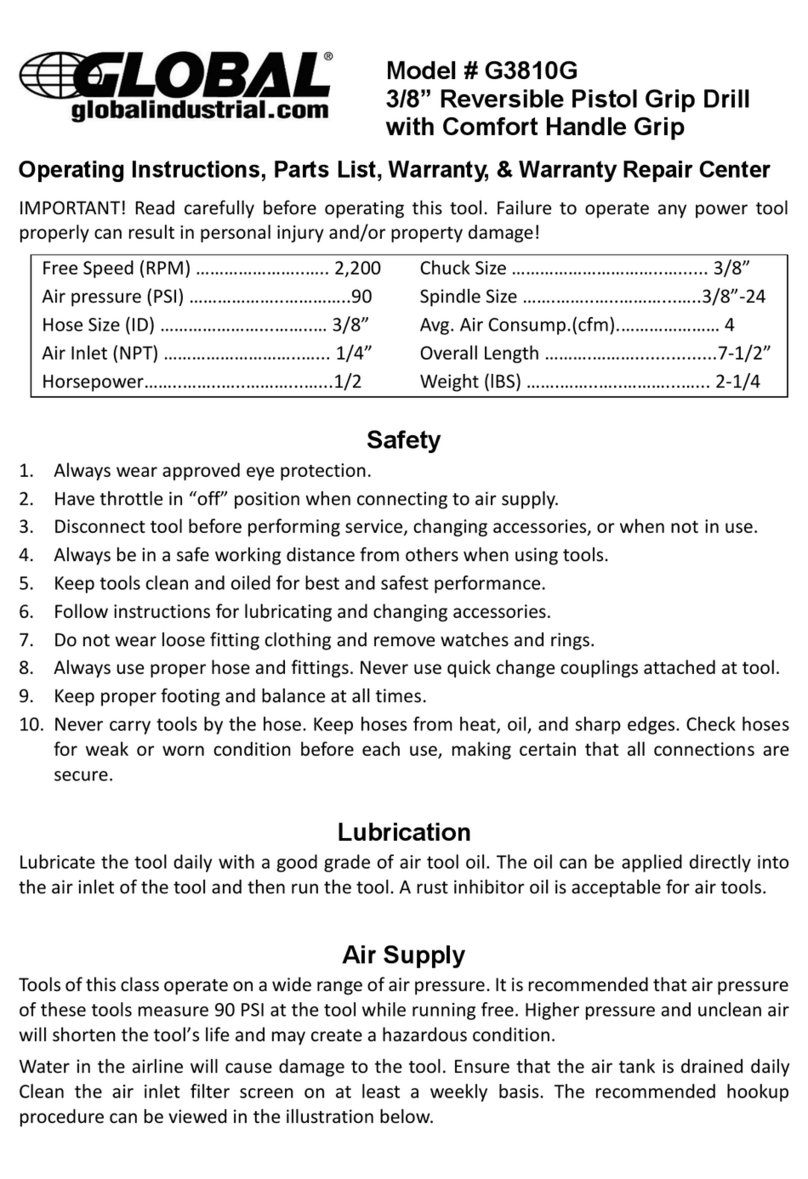
Global
Global G3810G Operating Instructions, Parts List, Warranty, & Warranty Repair Center
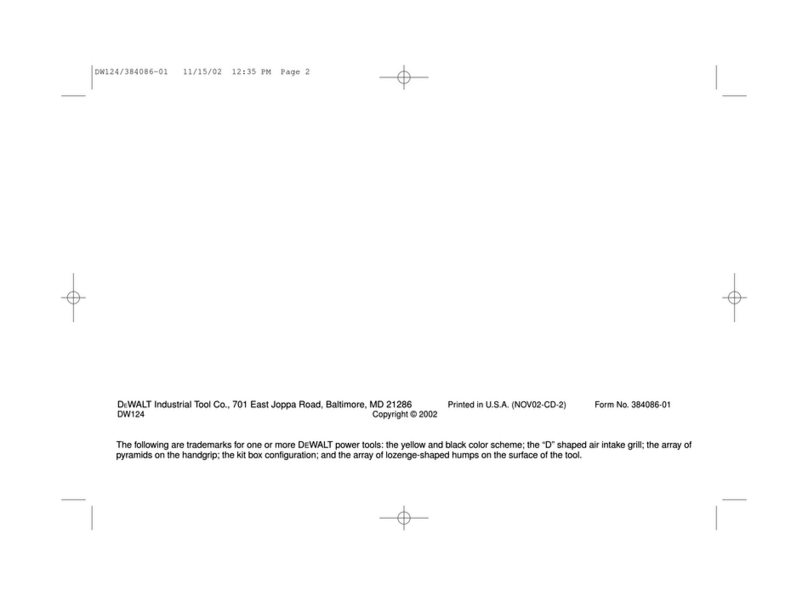
DeWalt
DeWalt DW124 instruction manual