HOLEMAKER VERSADRIVE V100T User manual

Magnetic Drilling Machine
V100T
(Original Instructions)

2
V100T/July 2020/V1.1
Congratulations on your purchase of the Holemaker Technology VERSADRIVE V100TTransportable
Magnetic Drilling Machine.
Your model is designed to produce superior holes quickly and efficiently. Through years of
experience, constant innovation and development, HMT is committed to provide you with metal
cutting tools and products to help you be more productive.
Before operating your new magnetic drilling machine, please read all instructions first. These include
the Operators Manual and Warning Labels on the unit itself. With proper use, care and maintenance
your model will provide you with years of effective hole drilling performance
TO REDUCE THE RISK OF INJURY USER MUST READ AND UNDERSTAND ALL INSTRUCTIONS:
Holemaker Technology LTD,
Bridge House,
Pattenden Lane,
Marden,
Kent,
UK,
TN12 9QJ
www. holemaker-technology.com

3
V100T/July 2020/V1.1
1Table of contents
1
1Table of contents 3
2Safety 4
2.1 General safety instructions 4
2.1.1 Work Area 4
2.1.2 Electrical Safety 4
2.1.3 Personal Safety 5
2.1.4 Machine Use and Care 5
2.1.5 Service 5
2.2 Magnetic Drill Specific safety information 6
3Description 7
3.1 Intended use 7
3.2 Description and features 8
3.3 Packing List 9
3.4 Serial number 9
3.5 Technical data 10
3.6 Environmental 12
4Preparation & adjustment 13
4.1 Assembly 13
4.1.1 Fitting the feed handles 13
4.1.2 Mounting the drill guard 15
4.1.3 Fitting the cooling system 16
4.1.4 Fitting the safety strap 19
4.2 Prior to use 20
5Using the machine 21
5.1 Carrying handle 21
5.2 Control panel 22
5.2.1 Magnet Switch 22
5.2.2 Motor NVR Switch 23
5.2.3 Spindle Direction Switch 23
5.2.4 Magnet Protection Fuse 23
5.3 Speed and Torque Control 24
5.4 Electro-Magnet 26
5.5 Emergency Stop 27
5.6 Tool lubrication 28
6Working with operating tools 29
6.1 The Morse Taper arbor 29
6.2 VERSADRIVE Magnet Drill System 31
6.3 Annular cutters 32
6.4 Twist drills 36
6.5 Tapping 36
7Maintenance 37
8Trouble shooting 40
9Exploded views & Spare part lists 41
9.1 Motor exploded view 41
9.2 Motor spare part list 42
9.3 Stand exploded view 43
9.4 Wiring diagrams 45
10 HMT Warranty Statement 46
11 Certification 47

4
V100T/July 2020/V1.1
2Safety
2.1 General safety instructions
Do not use this power tool before you have thoroughly read and completely understood this
Instruction Manual and the “General Safety Instructions”, including the figures, specifications, safety
regulations and the signs indicating DANGER, WARNING and CAUTION.
WARNING: When using electrical tools basic safety precautions should always be followed to reduce
the risk of fire, electrical shock and personal injury including following.
Please also observe the relevant national industrial safety regulations. Non-observance of the safety
instructions in the said documentation can lead to an electric shock, burns and/or severe injuries.
This Operator’s Manual including the “General Safety Instructions” should be kept for later use and
enclosed with the power tool, should it be passed on or sold.
2.1.1 Work Area
1. Keep your work area clean and well lit.
2. Do not operate magnetic drilling machine in explosive atmospheres, such as in the
presence of flammable liquids, gases or dust.
3. Keep bystanders, children, and visitors away while operating a magnetic drilling
machine.
2.1.2 Electrical Safety
1. Power tool plugs must match the outlet. Never modify the plug in any way. Do not
use any adapter plugs with earthed (grounded) power tools.
2. Avoid body contact with grounded surfaces such as pipes, radiators, ranges and
refrigerators.
3. Do not expose magnetic drilling machines to rain or wet conditions.
4. Do not abuse the cord. Never use the cord to carry the magnetic drilling machine or
pull the plug from an outlet. Keep cord away from heat, oil, sharp edges or moving
parts. Replace damaged cords immediately.
5. When operating a magnetic drilling machine, use an extension cord suitable for
outdoor use.
6. If operating a magnetic drilling machine in a damp location is unavoidable, use a
residual current device (RCD) protected supply.

5
V100T/July 2020/V1.1
2.1.3 Personal Safety
1. Stay alert, watch what you are doing and use common sense when using a magnetic drilling
machine. Do not use machine while tired or under the influence of drugs, alcohol, or
medication.
2. Use personal protective equipment. Always wear eye protection.
3. Prevent unintentional starting. Ensure the switch is in the off-position before connecting to
power source and/or battery pack, picking up or carrying the tool.
4. Remove any adjusting key or wrench before turning the power tool on.
5. Do not overreach. Keep proper footing and balance at all times.
6. Dress properly. Do not wear loose clothing or jewellery. Contain long hair. Keep your hair,
clothing, and gloves away from moving parts.
7. If devices are provided for the connection of dust extraction and collection facilities, ensure
these are connected and properly used.
8. Do not let familiarity gained from frequent use of tools allow you to become complacent and
ignore tool safety principles.
2.1.4 Machine Use and Care
1. Do not force the power tool. Use the correct power tool for your application.
2. Do not use the power tool if the switch does not turn it on and off.
3. Disconnect the plug from the power source and/or remove the battery pack, if detachable,
from the power tool before making any adjustments, changing accessories, or storing power
tools.
4. Store idle power tools out of the reach of children and do not allow persons unfamiliar with
the power tool or these instructions to operate the power tool.
5. Maintain power tools and accessories. Check for misalignment or binding of moving parts,
breakage of parts and any other condition that may affect the power tool’s operation. If
damaged,
6. Check for misalignment or binding of moving parts, breakage of parts, and any other
condition that may affect the machine operation. If damaged, have the tool serviced before
using by an HMT Authorized Technician. Many accidents are caused by poorly maintained
tools.
7. Keep cutting tools sharp and clean.
8. Use the power tool, accessories and tool bits etc. that are recommended by HMT for your
model, in accordance with these instructions, taking into account the working conditions and
the work to be performed.
9. Keep handles and grasping surfaces dry, clean and free from oil and grease.
2.1.5 Service
•Tool service must be performed only by qualified repair personnel. Service or maintenance
performed by unqualified personnel could result in a risk of injury.

6
V100T/July 2020/V1.1
2.2 Magnetic Drill Specific safety information
•Keep your fingers well out of the drill/cutter area.
•Avoid touching the drilled core that is automatically ejected by the centering pin
when the working procedure is finished. Contact with the core when it is hot, or if it
falls, can cause personal injuries.
•Always use the drill guard. Before switching on machine ensure the guard is closed
securely.
•Always use the safety strap.
•The magnetic drilling machine is suitable for use on steel with a minimum thickness
of 10mm, with zero air gap between the magnet core surface and the mounting
surface. Curvature, coats of paint and surface irregularities will create an air gap.
Keep the air gap to a minimum.
•Always place the machine on a flat surface.
•Do not clamp the magnetic drilling machine on small or irregularly shaped objects.
•Always place the machine on a surface that is clear of shavings, chips, swarf and
surface dirt.
•Keep the magnet clean and free of debris and swarf.
•Do not switch on the machine until it has been securely mounted and installed
according to these instructions.
•Do not switch on the machine before having checked that the magnetic stand has
been tightened firmly and securely to the mounting surface.
•Adjust the table so cutter does not extend into the work piece before drilling. Do not
perform any design, assembly or construction activities on the work piece while the
machine is switched on.
•Before switching on the machine, make sure all accessories have been mounted
correctly.
•Always use the recommended speed for the accessories and the material.
•Do not use the machine on the same work piece on which electric welders are being
used.
•Use only an appropriate cutting fluid. We offer a range of premium cutting oils and
lubricants which are specially developed and selected for optimum performance and
maximum tool life.
•Do not use liquid cutting fluids while drilling vertically or overhead. Dip the cutter in
cutting paste or apply an appropriate spray for these applications.
•Do not pour cutting fluid into the reservoir while it is mounted in the bracket. Do not
allow cutting fluid to enter the drill motor.
•Before use, ensure movable cutter guard is fitted correctly and operates properly.
•Ensure that metal chips or resinous residue cannot lead to blockage of the function.
•In case of jammed cutter disconnect the machine from the power supply, remove
the reason for the jam before turning on the machine again.

7
V100T/July 2020/V1.1
RESIDUAL RISKS
In following the relevant safety regulations and the implementation of safety
devices, certain residual risks cannot be avoided.
These are:
•Impairment of hearing
•Risk of personal injury from flying particles
•Risk of burns due to accessories becoming hot during operation
•Risk of personal injury due to prolonged use.
Always try to reduce these risks further by the use safe working practices and the use of appropriate
PPE as much as possible.
3Description
3.1 Intended use
This magnetic drilling machine is intended for commercial/industrial use as a magnetic base drilling
machine for drilling materials with a magnetizable surface using annular cutters and twist drills.
The magnetic drilling machine can be used horizontally, vertically or overhead using the safety strap
provided, taking the precautions identified in this manual.
This magnetic drilling machine is IP20 and is intended to be used in a weather-protected
environment. Ambient operating temperatures of <-10 and >45°C should be avoided.
Use only HMT approved tools and accessories with this machine.
The machine should not be used beyond its stated capacities.
The machine should not be used for any purpose other than stated.
The machine should NEVER be used without a protective earth or ground connection.
The machine SHOULD NOT be used in a potentially explosive environment.
The machine should not be used as a lifting device, the magnetic base is for clamping only.

9
V100T/July 2020/V1.1
3.3 Packing List
Standard Machine
1 x Magnetic Drilling Machine
1 x Instruction Manual
1 x Standard Weldon Arbor
1 x VERSADRIVE RAPID LOCK Weldon Adaptor
1 x Drill Guard & 2 Thumbscrews
1 x Hex Key (3)
1 x Safety Strap
1 x Drill Drift
1 x Basic Carrying Case
1 x Bottle of Cutting Oil
Pro Machine
1 x Magnetic Drilling Machine
1 x Instruction Manual
1 x Quick Release –Weldon Coolant Arbor
1 x VERSADRIVE RAPID LOCK Weldon Arbor
1 x Drill Guard & 2 Thumbscrews
1 x Hex Key (3)
1 x Safety Strap
1 x Drill Drift
1 x Heavy Duty Carrying Case
1x Coolant Bottle, Tap and Tube
1 x Bottle of Cutting Oil
3.4 Serial number
The serial number is displayed on the machine on the motor housing.
The serial number will help you and your sales point validate and identify the machine.
As example: V100T11020205
This breaks down to:
V100T 110 20 205
Machine series
Voltage
Year of manufacture
Identification number

10
V100T/July 2020/V1.1
3.5 Technical data
VERSADRIVE V100T- 110V / 230V (Check machine markings)
Capacity Annular Cutters
Up to Ø100 mm (TCT cutters)
Capacity Twist Drills
Ø 1 –32 mm
Capacity Threading
M30 x 3.5
Capacity Countersinking
Ø 55mm (in S275)
Overall Length
350mm (with guard)
Overall Width
210mm 240mm (with coolant)
Overall Height
450mm Min - 780mm Max
Slide Stroke
280mm
Weight –(Machine only)
24.5 kg
Magnet dimensions
220 x 115x 60 mm (L x W x H)
Magnetic Adhesion Force
2200 Kg (25mm Thick Material)
Rated Voltage
110V AC / 230V AC
Rated Current
16 A / 7.8 A
Rated Input
1800 W
IP Rating
IP20
Insulation Class
Class 1
Rated Speeds I
No Load II
60-140 min-1
200-470 min-1
Spindle type
MT3 to 19,05mm Weldon
Sound Pressure Level
86 dBA Uncertainty 3 dBA
Sound Power Level
99 dBA Uncertainty 3 dBA
SPL at Operators Head Level
89 dBA Uncertainty 3 dBA
Hand-Arm Vibration
< 2.5 m/s2Uncertainty 1.5 m/s2
The vibration measurement was made under standard conditions in accordance with the
requirements of BS EN 62841-1:2015.
The actual vibration level during use will depend on the workpiece stability/rigidity and the condition
of the cutter used. These factors may increase the vibration experienced by the operator, each
individual application of the tool should be assessed for the effect of these application variable
factors, before exposure.

11
V100T/July 2020/V1.1
Symbols
Symbol
Term, meaning
Explanation
Read Documentation
You MUST read the enclosed documentation such
as the Instruction Manual and the General Safety
Instructions.
Wear ear protection
Use ear protection during operation.
Wear eye protection
Use eye-protection during operation.
Wear Gloves
Danger/warning/caution
Observe the information in the adjacent text!
Warning Electrical Enclosure
Danger - High voltage present inside enclosure.
European conformity symbol
Confirms the conformity of the power tool with
the directives of the European Community.
Class of protection I
Product with basic insulation and exposed
(touchable), conductive parts additionally
connected to the protective earth conductor.
mm
Millimeter
Unit of measure for length, width, height or depth
kg
Kilogram
Unit of measure for the mass
V
Volt
Unit of measure for the electric voltage
A
Ampere
Unit of measure for the electric current intensity
W
Watt
Unit of measure for the output
N
Newton
Unit of measure for the force
min
Minutes
Unit of measure for the time
no
No-load speed
Revolution speed at no-load
1/min min-1
per minute
Unit of measure for number of revolutions,
strokes, impacts or oscillations per minute.

12
V100T/July 2020/V1.1
3.6 Environmental
Separate collection. This product must NOT be disposed of with normal household waste.
Separate collection of used products and packaging allows materials to be recycled and used again.
Re-use of recycled materials helps prevent environmental pollution and reduces the demand for raw
materials.
Local regulations may provide for separate collection of electrical products from the household, at
municipal waste sites or by the retailer when you purchase a new product.

13
V100T/July 2020/V1.1
4Preparation & adjustment
4.1 Assembly
WARNING: To reduce the risk of injury, turn unit off and disconnect machine from power source
before installing and removing accessories, before adjusting or changing set- ups or when making
repairs. Be sure all switches are in the OFF position. An accidental start-up can cause injury.
4.1.1 Fitting the feed handles
Take the feed handle (x 3), and screw each one in turn into the pinion shaft.
Ensure the handles are fully secure before use.
[image 2]

14
V100T/July 2020/V1.1
To remove the feed handle from the machine, first lower the slide until it is at its lower most
position.
Unscrew the M6 cap screw (item 1) and remove the pinion shaft retainer (item 2). The pinion
shaft and feed handle assembly (item 3) can now be withdrawn.
[image 3]
It is possible to position the feed handle on either side of the machine (image 4).
Method of removal and refitting is as in 3.1.1 and 3.1.2 above.
IMPORTANT: If the feed handle is repositioned, the operator must have good access to the controls
at ALL times.
[image 4]

15
V100T/July 2020/V1.1
4.1.2 Mounting the drill guard
The drill guard protects against ejection of sharp and/or hot chippings, it also protects against
accidental contact with rotating parts and must always ALWAYS be mounted during operation.
1) Ensure the drill mounting bracket (1) is attached to the motor lower support and is secure.
2) Slide the drill guard (2) up to the bracket.
3) Fit the 6mm shoulder screw (4) with a nylon washer (3) between it and the face of the guard.
4) Fit M6 thumbwheel (5) with an M6 spring washer (6) and nylon washer to the guard face.
5) Tighten the shoulder screw and then adjust the thumbwheel to allow the guard to just slide.
6) The guard can be locked in position at any time using the thumbwheel.
[image 5]

16
V100T/July 2020/V1.1
4.1.3 Fitting the cooling system
Description of the cooling system.
The coolant system consists of the following items:-
1. Coolant bottle
2. Flow adjustment tap
3. Coolant tube
4. MT3 Arbor with integral coolant collar
5. Stay Bar
The coolant system has a cutter holder (4) with an integral collar which allows coolant to be fed
down through the centre of the cutter whilst rotating.
The collar is prevented from rotating by the stay bar (5).
Coolant is stored in the coolant bottle (1), the flow is regulated by the tap (2) and fed to the cutter
holder collar by means of a flexible tube (3).
The coolant bottle is attached to the main stand by means of a bracket.
[image 6] –Guard not shown.

17
V100T/July 2020/V1.1
Fitting the coolant system –Fit the coolant arbor by engaging the morse taper of the arbor into the
drill units morse taper socket.
The stay bar must be aligned to fit into one of the two slots in the motor support bracket.
See image 7 –inset below.
[image 7] –Guard not shown
The coolant bottle and tap assembly has a mounting bracket which is slotted to allow easy
removal. To fit the bottle, place the bracket over the 2x shoulder bolts then slide down to
lock in place. See image 8 below.
[image 8]

19
V100T/July 2020/V1.1
4.1.4 Fitting the safety strap
The safety strap should always be used during operation.
Use of the safety strap reduces the risk of personal injury if for some reason there is a loss of
magnetic adhesion and the magnet comes loose from the workpiece (such as loss of power supply).
The purpose of the safety strap is to prevent the machine from falling or spinning should there be a
loss of magnetic adhesion.
The safety strap should NOT be used as an alternative method of clamping to the magnet.
[image 11]- Upper inset shows strap slot - Lower inset shows cam buckle.
Position the machine on the item to be drilled and switch on the magnet.
Feed the free end of the strap through the strap slot on the machine and around the
workpiece.
Fit the free end through the cam buckle.
Pull on the free end to tighten the strap.
MAKE SURE the safety strap is securely fitted BEFORE using the drill.

20
V100T/July 2020/V1.1
4.2 Prior to use
Please make sure that the contacting surface for the magnet is level, clean and rust-free.
Remove any varnish or primer. When working on materials that are not magnetizable, suitable
fixation devices are obtainable as accessories from HMT, e. g. suction plate, vacuum plate or
pipe-drilling clamp must be used.
When working on steel materials with a material thickness of less than 5 mm, the work piece must
be reinforced with an additional steel plate in order to guarantee the magnetic holding power.
Check the machine for possible damage before using the machine, you must carefully check
protective devices or slightly damaged components to ensure they are operating perfectly and as
intended.
Check that moving are in perfect working order and do not jam and check whether parts are
damaged. All parts must be correctly installed and fulfill all conditions necessary to ensure perfect
operation of the machine.
Damaged protective devices and parts must be repaired or replaced according to specifications by
HMT of any authorized HMT dealer.
DO NOT use under wet conditions or in presence of flammable liquids or gases.
This magnetic drilling machine is a professional power tool.
DO NOT let children near the machine.
Supervision is required when inexperienced operators use this machine.
ELECTRICAL SAFETY
The electric motor has been designed for one voltage only.
Always check that the power supply corresponds to the voltage on the rating plate.
Your HMT MAGNETIC DRILLING MACHINE is designed in class I (grounded) according to
BS EN 62841-1. Earthing connection is required.
If the supply cord is damaged, it must be replaced by a specially prepared cord available through the
HMT service organization.
EXTENSION CABLE
If an extension cable is required, use an approved 3-core earthed extension cable suitable for the
power input of this tool (see technical data). Minimum conductor size is 1.5 mm²; the maximum
length is 30 metre. When using a cable reel, always unwind the cable completely.
TRY A FEW SIMPLE PROJECTS USING SCRAP MATERIAL UNTIL YOU DEVELOP A “FEEL” FOR THE
MACHINE
LET THE MACHINE RUN IN FOR A PERIOD OF 8-10 HOURS BEFORE STARTING WITH BIG OPERATIONS.
DO NOT LOAD THE MACHINE TOO MUCH DURING RUN-IN PERIOD
NEVER USE THE MACHINE IN SERIOUS OVERLOAD
KEEP THE MACHINE CLEAR FROM MOISTURE AT ALL TIMES TO PROTECT THE MACHINE, YOURSELF
AND OTHERS.
Table of contents
Other HOLEMAKER Drill manuals

HOLEMAKER
HOLEMAKER PRO 60 HP User manual
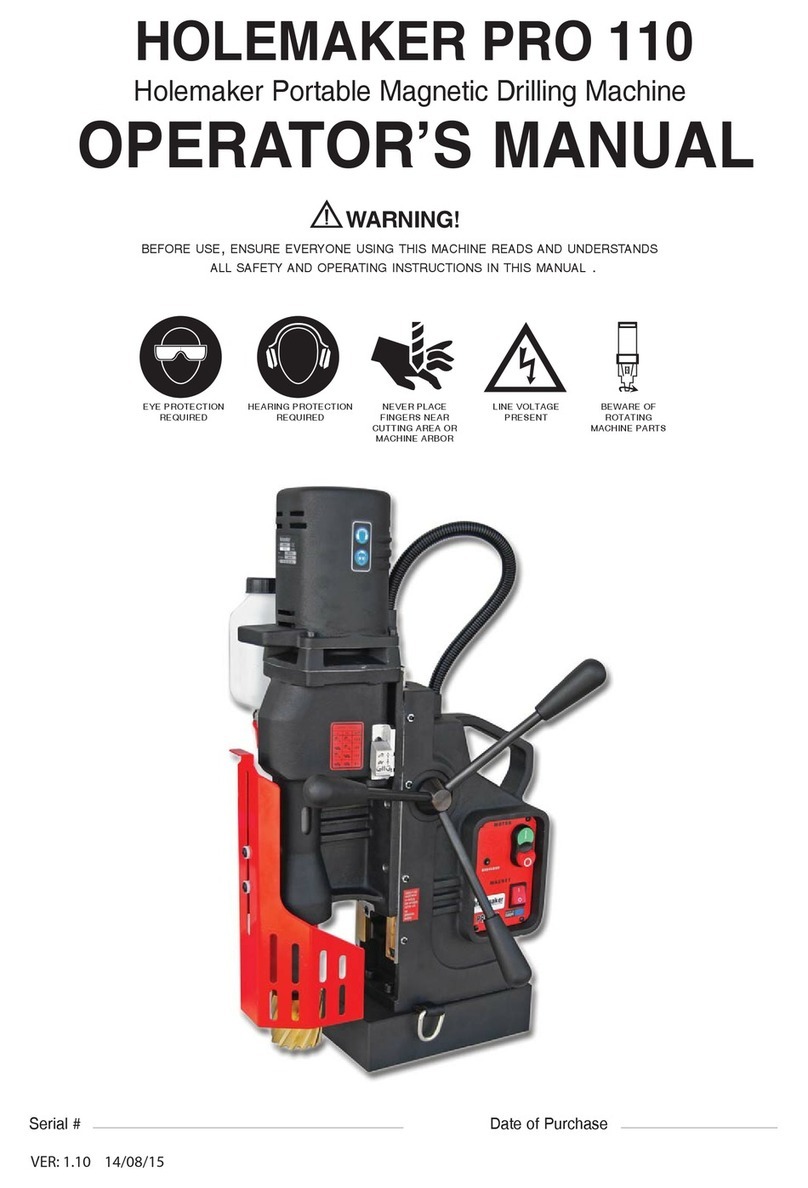
HOLEMAKER
HOLEMAKER PRO 100 User manual
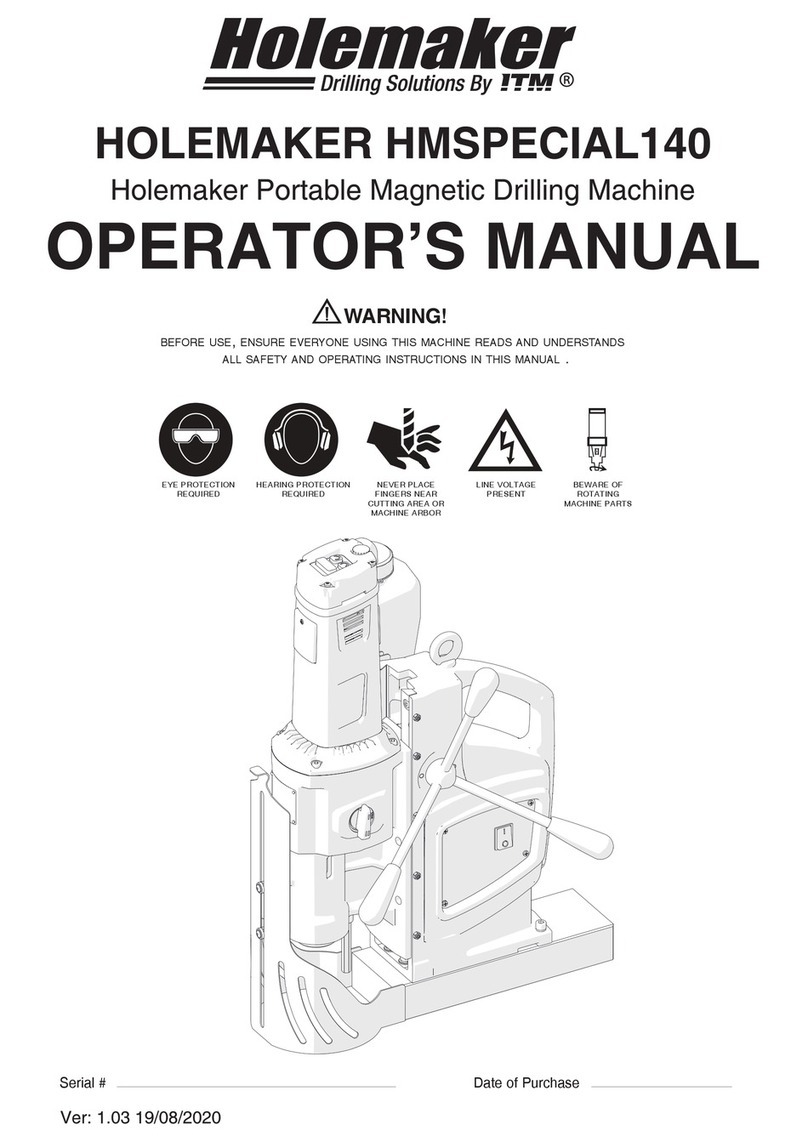
HOLEMAKER
HOLEMAKER HMSPECIAL140 User manual
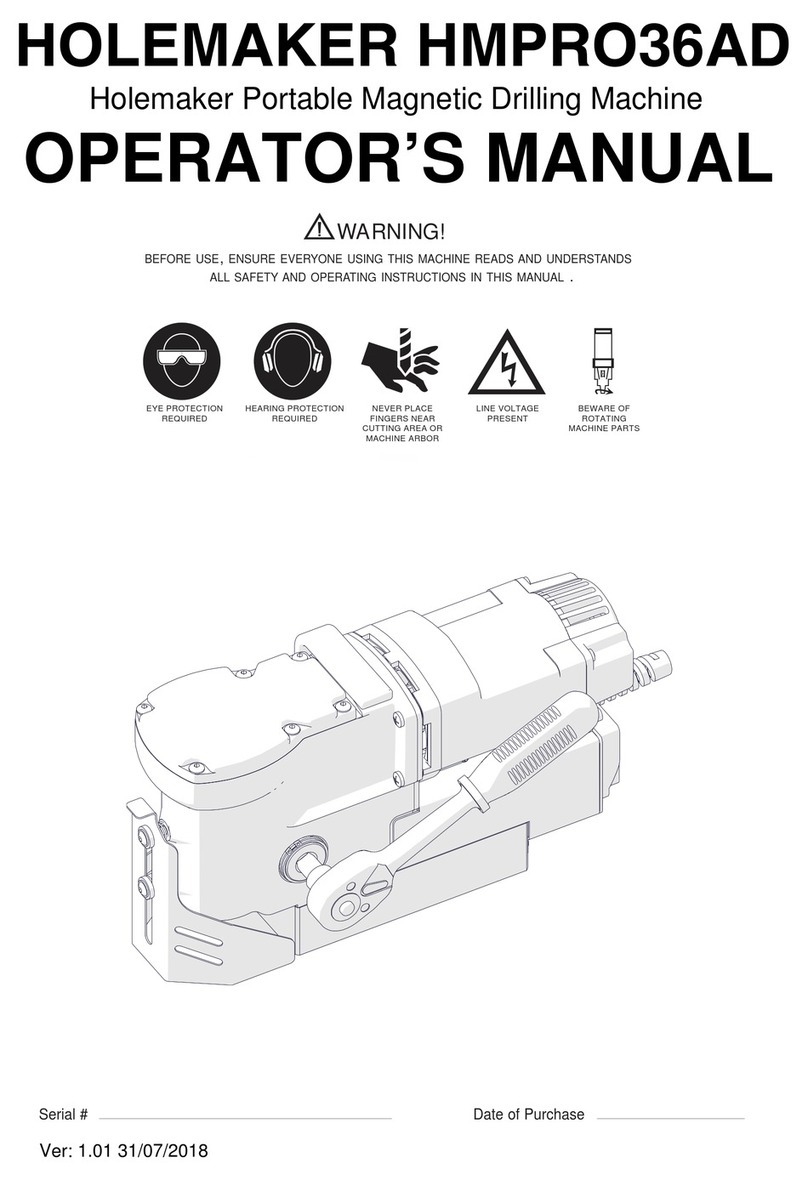
HOLEMAKER
HOLEMAKER HMPRO36AD User manual
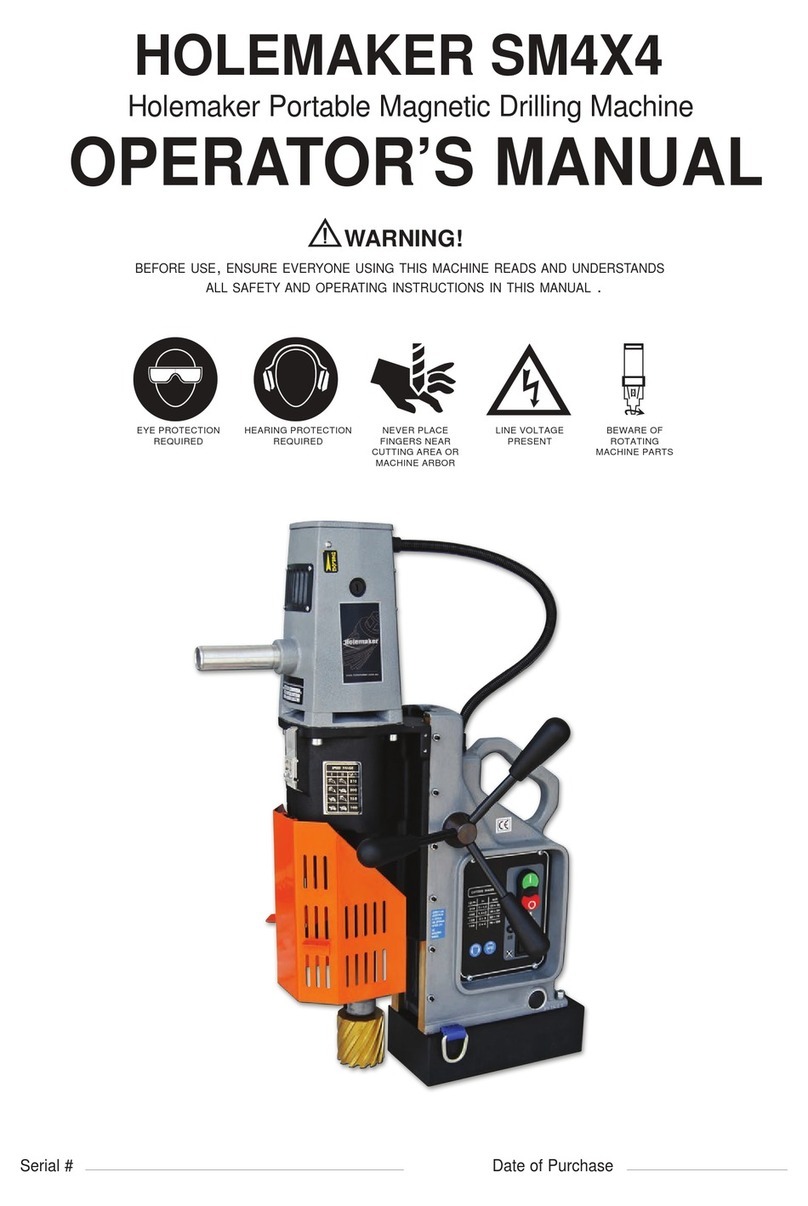
HOLEMAKER
HOLEMAKER SM4X4 User manual

HOLEMAKER
HOLEMAKER 35 User manual
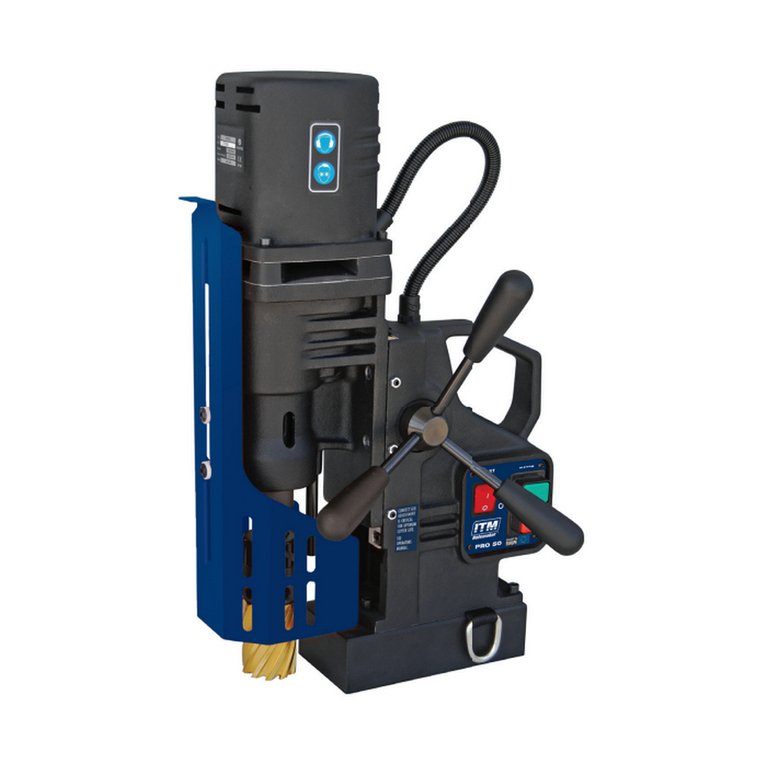
HOLEMAKER
HOLEMAKER HMPRO50 User manual
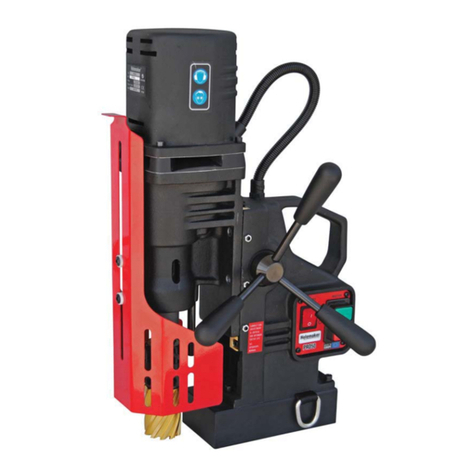
HOLEMAKER
HOLEMAKER PRO 50 User manual
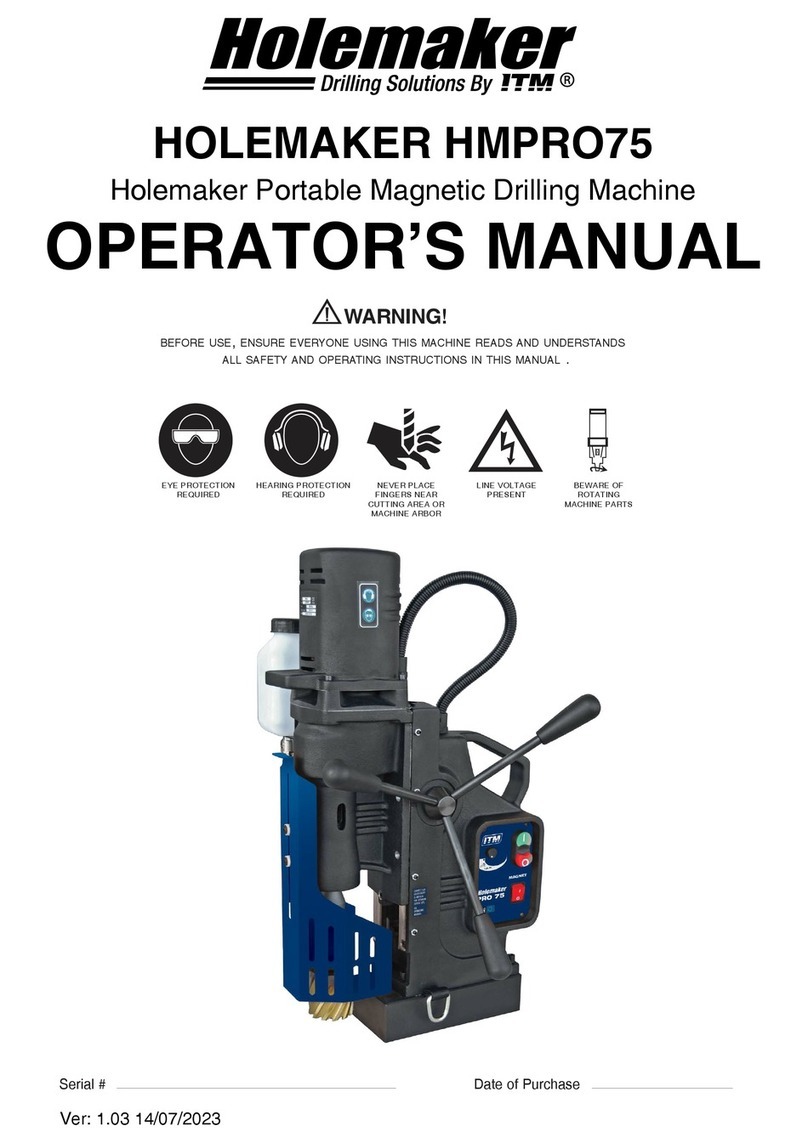
HOLEMAKER
HOLEMAKER HMPRO75 User manual
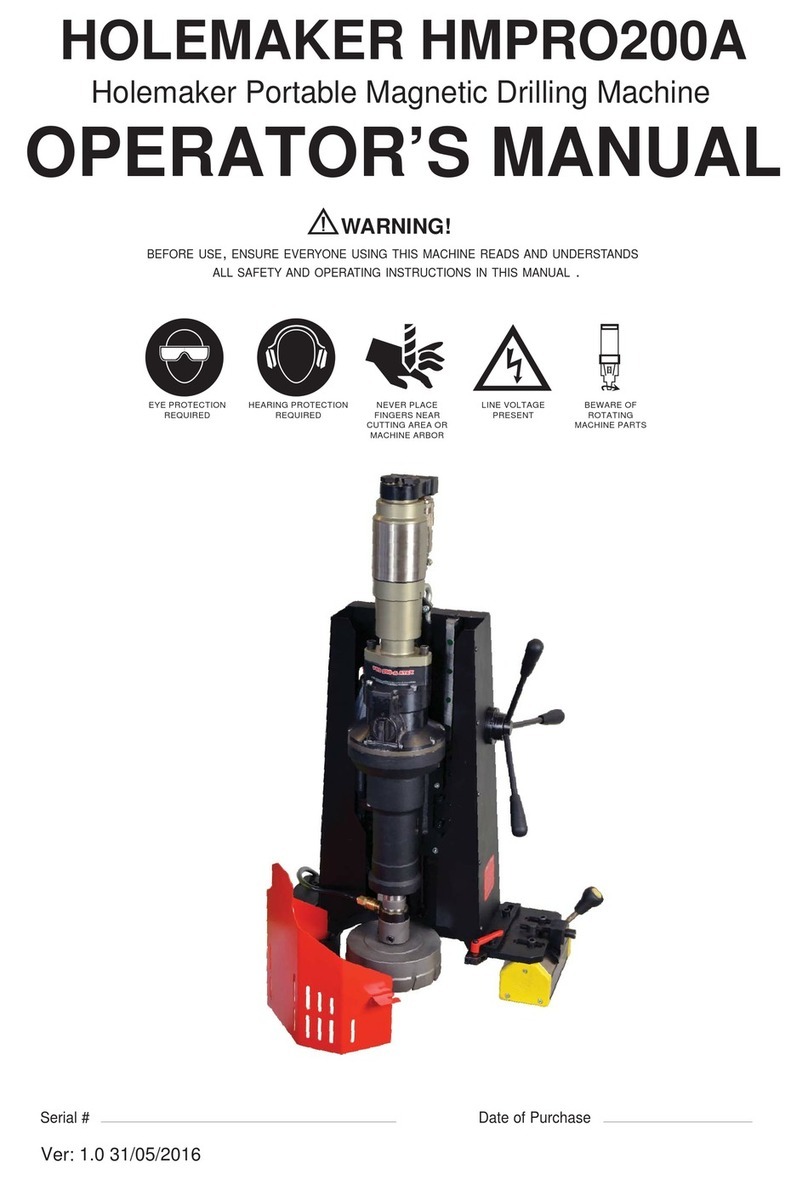
HOLEMAKER
HOLEMAKER HMPRO200A User manual