HORNER SmartBlock HE579DAC107 User manual

MAN0965-03-EN
Specifications/Installation
10/15/2013 No part of this publication may be reproduced without the prior agreement and written permission of Horner APG, LLC. Information in this document is subject to change without notice. Page 1of 6
SmartBlock I/O Module - HE579DAC107/HE579DAC207
8/4 Channel Current and Voltage Output
0-5V / 0-10V / 4-20mA / 0-20mA - CsCAN
1. SPECIFICATIONS / DIMENSIONS
ANALOG OUT
Number of Outputs
8 (207) or 4 (107)
Isolation
(Power to Analog Output)
1000V DC
IEC61010-1 300V RMS
Output Ranges
0-5V, 0-10V DC
4-20mA, 0-20mA DC
Isolation Method
Magnetic
Resolution
14 bits
Output Clamp
-.5/+24V, 600Wpk
Accuracy, 25°C
0.1%
Output Type
Sourcing
Load Resistance
V: 500 ohms Min
mA: 500 ohms Max
Register Value for
Nominal Full Scale
32000
GENERAL SPECIFICATIONS
Required Power @ 24 VDC
(Voltage Mode 2KΩ)
(207) 145mA
(107) 105mA
Cooling Method
Self-cooling
Relative Humidity
5 to 95% Non-condensing
Required Power @ 24 VDC
(Voltage Mode 2KΩ)
(207) 255mA
(107) 190mA
Altitude for use
Up to 2,000m
Pollution Degree
2 or lower
Voltage Input
10-30 VDS
Weight
12oz/340g
Operating Temperature
0⁰to 60⁰C
Atmosphere
Free from corrosive gases
and excessive dust
Storage Temperature
-25⁰to 70⁰C
DIMENSIONS
Width
4.48”
(113.7mm)
Length
4.56”
(115.8mm)
Height
2.16” (54.8mm)
Height w/ connector
2.84” (72.1mm)
2. TECHNICAL SUPPORT
North America:
Tel: 317 916-4274 Fax: 317 639-4279 Web: http://www.heapg.com Email: techsppt@heapg.com
Europe:
Tel: +353-21-4321266 Fax: +353-21-4321826 Web: http://www.horner-apg.com Email: tech.support@horner-apg.com
Status LEDs
J2 Outputs 5 -8
J1 Outputs 1-4
Network ID
Selector Switches
CAN and
power connector
Earth Ground Location

MAN0965-03-EN
Specifications/Installation
10/15/2013 No part of this publication may be reproduced without the prior agreement and written permission of Horner APG, LLC. Information in this document is subject to change without notice. Page 2of 6
3. WIRING

MAN0965-03-EN
Specifications/Installation
10/15/2013 No part of this publication may be reproduced without the prior agreement and written permission of Horner APG, LLC. Information in this document is subject to change without notice. Page 3of 6
4. NETWORK, POWER AND GROUNDING
A single, 5-pin connector is used to make both a network connection and power input. A quality, class-2 power supply should be
used for this product. If the power is run with the network cable, care must be taken such that the voltage does not drop below the
lower supply limit on longer runs. A separate supply for the controller and I/O is recommended for best noise immunity.
A quality earth ground is required for safe and proper operation. The best ground is achieved by screwing the lower left grounding
location into a grounded back plate. Alternately a ground can be connected to the spade lug.
Please see Horner manual MAN0799 for details on CAN wiring.
CAN Network & Power Connector
Torque rating 4.5 –7 Lb-In (0.50 –0.78 N-m)
CAN Network & Power Port Pin Assignments
Pin
Signal
Signal Description
Direction
1
V-
CAN and Device Ground - Black
2
CN_L
CAN Data Low - Blue
In/Out
3
SHLD
Shield Ground - None
4
CN_H
CAN Data High - White
In/Out
5
V+
Positive DC Voltage Input
(10-30VDC) - Red
5. CONFIGURATION
For most applications, the I/O scanner built into Cscape and the OCS firmware will
provide a fast, robust, and easy to use method to configure and scan the SmartBlock
I/O. For advanced operations, such as on-the-fly changes to the output type, please
see the following chapter on network data and the SmartStix and SmartBlock
programming guide.
To configure SmartBlock I/O from Cscape open the Hardware Configuration dialog
from the Controller | Hardware Configuration menu:
1. Select the option for CsCAN I/O.
2. Click Add.
3. Select the SmartStix Tab and select the device to be configured.
The DAC207 SmartBlock has the same configuration and network signature as the
SmartStix version. You can replace a SmartStix device with a SmartBlock in this
case with no programming changes. As of Cscape version 9.30, the configuration for
the DAC207 is found in the SmartStix tab. This will be added to the SmartBlock tab
in a future release for convenience.
To the right is the configuration for DAC207 device, configuration definitions are listed
below:
Configuration Type
Definition
Network ID
This should match the ID of the rotary switch on the SmartBlock unit and should be unique to the
network.
I/O Mapping
These registers define how the OCS controller registers are mapped to the data to and from the
SmartBlock I/O. These registers do not have to match the I/O types typically used for I/O such as %AI,
Q… Any standard controller registers may be used such as %R, %T and %M.
Input Update Method
This defines how often analog data is sent from the SmartBlock to the CsCAN network. Digital data is
transmitted on change of state.
Channel Configuration
This selects how each analog channel is configured including filtering.
Timeout
This sets the time a controller will wait before assuming the host OCS is off-line.

MAN0965-03-EN
Specifications/Installation
10/15/2013 No part of this publication may be reproduced without the prior agreement and written permission of Horner APG, LLC. Information in this document is subject to change without notice. Page 4of 6
6. NETWORK DATA
Consumed Digital Data –This data is sent from the controller to the SmartBlock. For typical applications the I/O configuration
setup in Cscape will automatically populate this data. For more advanced applications you may use NetPut functions to write this
data. Please see the advanced programming guide MAN0880 for more details.
Bit
Description
1-8
Mode Bit 1 bit per channel
0 = Voltage Mode 1 = Current mode
17-20
Scale Bit 1 bit per channel
0 = 10V or 20mA 1 = 5V or 4-20mA
73-80
Hold Last State
1 = Hold last State 0 = go to default value
Consumed Analog Data –This data is sent from the controller to the SmartBlock. For typical applications the I/O configuration
setup in Cscape will automatically populate this data. For more advanced applications you may use NetPut functions to write this
data. Please see the advanced programming guide MAN0880 for more details.
Word
Description
1-8
Analog Data
Data for analog output channels 1 to 8
9-16
Default Data
Analog output default state on error or stop (if selected)
Produced Digital Data –This data is sent from the SmartBlock to the controller. Normally this data is mapped into specific
registers in the I/O configuration in Cscape. For advanced applications NetGet functions can be used to obtain this data. Since this
data is broadcast to all controllers on the network additional controllers can use NetGet functions to obtain this data as well.
Bit
Description
1-32
Not Used
33-48
Status and Diagnostic Data
49-56
Firmware Version
57-64
Device Class –10 for the DAC207 68 for DAC107
7. SETTING ID SWITCHES
CsCAN Network IDs are set using the hexadecimal number system from 01 to FD. The decimal equivalent is 1-253. Refer to following
Conversion Table, which shows the decimal equivalent of hexadecimal numbers. Set a unique Network ID by inserting a small Phillips
screwdriver into the two identical switches.
NOTE: The CsCAN Baud Rate for SmartBlock I/O is fixed at 125KBaud

MAN0965-03-EN
Specifications/Installation
10/15/2013 No part of this publication may be reproduced without the prior agreement and written permission of Horner APG, LLC. Information in this document is subject to change without notice. Page 5of 6
Dec
Hex
Dec
Hex
Dec
Hex
Dec
Hex
Dec
Hex
Dec
Hex
Dec
Hex
Dec
Hex
Dec
Hex
HI
LO
HI
LO
HI
LO
HI
LO
HI
LO
HI
LO
HI
LO
HI
LO
HI
LO
1
0
1
29
1
D
57
3
9
86
5
6
114
7
2
142
8
E
170
A
A
198
C
6
226
E
2
2
0
2
30
1
E
58
3
A
87
5
7
115
7
2
143
8
F
171
A
B
199
C
7
227
E
3
3
0
3
31
1
F
59
3
B
88
5
8
116
7
4
144
9
0
172
A
C
200
C
8
228
E
4
4
0
4
32
2
0
60
3
C
89
5
9
117
7
5
145
9
1
173
A
D
201
C
9
229
E
5
5
0
5
33
2
1
61
3
D
90
5
A
118
7
6
146
9
2
174
A
E
202
C
A
230
E
6
6
0
6
34
2
2
62
3
E
91
5
B
119
7
7
147
9
3
175
A
F
203
C
B
231
E
7
7
0
7
35
2
3
63
3
F
92
5
C
120
7
8
148
9
4
176
B
0
204
C
C
232
E
8
8
0
8
36
2
4
64
4
0
93
5
D
121
7
9
149
9
5
177
B
1
205
C
D
233
E
9
9
0
9
37
2
5
65
4
1
94
5
E
122
7
A
150
9
6
178
B
2
206
C
E
234
E
A
10
0
A
38
2
6
66
4
2
95
5
F
123
7
B
151
9
7
179
B
3
207
C
F
235
E
B
11
0
B
39
2
7
67
4
3
96
6
0
124
7
C
152
9
8
180
B
4
208
D
0
236
E
C
12
0
C
40
2
8
68
4
4
97
6
1
125
7
D
153
9
9
181
B
5
209
D
1
237
E
D
13
0
D
41
2
9
69
4
5
98
6
2
126
7
E
154
9
A
182
B
6
210
D
2
238
E
E
14
0
E
42
2
A
70
4
6
99
6
3
127
7
F
155
9
B
183
B
7
211
D
3
239
E
F
15
0
F
43
2
B
72
4
8
100
6
4
128
8
0
156
9
C
184
B
8
212
D
4
240
F
0
16
1
0
44
2
C
73
4
9
101
6
5
129
8
1
157
9
D
185
B
9
213
D
5
241
F
1
17
1
1
45
2
D
74
4
A
102
6
6
130
8
2
158
9
E
186
B
A
214
D
6
242
F
2
18
1
2
46
2
E
75
4
B
103
6
7
131
8
3
159
9
F
187
B
B
215
D
7
243
F
3
19
1
3
47
2
F
76
4
C
104
6
8
132
8
4
160
A
0
188
B
C
216
D
8
244
F
4
20
1
4
48
3
0
77
4
D
105
6
9
133
8
5
161
A
1
189
B
D
217
D
9
245
F
5
21
1
5
49
3
1
78
4
E
106
6
A
134
8
6
162
A
2
190
B
E
218
D
A
246
F
6
22
1
6
50
3
2
79
4
F
107
6
B
135
8
7
163
A
3
191
B
F
219
D
B
247
F
7
23
1
7
51
3
3
80
5
0
108
6
C
136
8
8
164
A
4
192
C
0
220
D
C
248
F
8
24
1
8
52
3
4
81
5
1
109
6
D
137
8
9
165
A
5
193
C
1
221
D
D
249
F
9
25
1
9
53
3
5
82
5
2
110
6
E
138
8
A
166
A
6
194
C
2
222
D
E
250
F
A
26
1
A
54
3
6
83
5
3
111
6
F
139
8
B
167
A
7
195
C
3
223
D
F
251
F
B
27
1
B
55
3
7
84
5
4
112
7
0
140
8
C
168
A
8
196
C
4
224
E
0
252
F
C
28
1
C
56
3
8
85
5
5
113
7
1
141
8
D
169
A
9
197
C
5
225
E
1
253
F
D
8. LED INDICATORS
HE579DAC107 and HE579DAC207 provide diagnostic and status LED indicators
Diagnostic LED Indicators
Diagnostic LED
State
Meaning
MS
indicates fault status
of the Network
Solid Red
RAM or ROM test failed
Blinking Red
I/O test failed
Blinking Green
Module is in power-up state
Solid Green
Module is running normally
NS
Indicates fault status
of the Network
Solid Red
Network Ack or Dup ID test failed
Blinking Red
Network ID test failed
Blinking Green
Module is in Life Expectancy default state
Solid Green
Network is running normally
Status LED indicators –The Power Status LED illuminates RED when power is applied to the module. There are I/O status LED
indicators for each of the Digital I/O points, which illuminate RED when the I/O point is ON.

MAN0965-03-EN
Specifications/Installation
10/15/2013 No part of this publication may be reproduced without the prior agreement and written permission of Horner APG, LLC. Information in this document is subject to change without notice. Page 6of 6
9. NETWORK CABLE
Recommended Cable
Thick: (Max Distance = 500m)
Belden 3082A
Thin: (Max Distance = 100m)
Belden 3084A
NOTES: 1) 12-24 VDC must be supplied to the network
2) For detailed wiring information, refer to Chapter Two in the Control Station Hardware Manual (MAN0227),
where a checklist is provided that covers panel box layout requirements and minimum clearances.
10.INSTALLATION / SAFETY
WARNING: Remove power from the OCS controller, CAN port, and any peripheral equipment connected to this local system before adding
or replacing this or any module
a) All applicable codes and standards should be followed in the
installation of this product.
b) Shielded, twisted-pair wiring should be used for best
performance.
c) Shields are to be terminated to frame ground.
d) In severe applications, shields should be tied directly to the
ground block within the panel.
e) Ungrounded thermocouple sensors are preferred due to their
isolated electrical characteristics.
f) Interposing terminal strips between the sensor and the module
can cause errors due to cold-junction effect.
g) If interposing terminal strips must be used, use specially
constructed terminal blocks that match the material
characteristics of the thermocouple sensor.
h) Horner thermocouple input modules use a high impedance
differential circuit to support the use of grounded or ungrounded
thermocouples. For grounded thermocouples, the specified
Common Mode Range allows for ground potential differences
between the machine ground and the PLC ground within that
range. For ungrounded or floating thermocouples, the high
impedance inputs are subject to common mode noise pickup.
For noisy environments, it is recommended that one side of all
ungrounded thermocouples be grounded near the PLC. This
does not affect open thermocouple detection or measurement
accuracy and reduces the effect of common mode noise if
present. This PLC side ground connection must not be used
with grounded thermocouples or accuracy will be affected. Any
thermocouple should be grounded in one place at most.
When found on the product, the following symbols specify:
All applicable codes and standards need to be followed in the installation of this product.
For I/O wiring (discrete), use the following wire type or equivalent: Belden 9918, 18 AWG or larger.
Adhere to the following safety precautions whenever any type of connection is made to the module.
Connect the green safety (earth) ground first before making any other
connections.
When connecting to electric circuits or pulse-initiating equipment, open their
related breakers. Do not make connections to live power lines.
Make connections to the module first; then connect to the circuit to be
monitored.
Route power wires in a safe manner in accordance with good practice and
local codes.
Wear proper personal protective equipment including safety glasses and
insulated gloves when making connections to power circuits.
Ensure hands, shoes, and floors are dry before making any connection to a
power line.
Make sure the unit is turned OFF before making connection to terminals.
Make sure all circuits are de-energized before making connections.
Before each use, inspect all cables for breaks or cracks in the insulation.
Replace immediately if defective.
Pin
Description
1
V+
2
CAN_H
3
Shield
4
CAN_L
5
V-
WARNING: Consult user documentation.
WARNING: Electrical Shock Hazard.
WARNING: To avoid the risk of electric shock or burns, always connect the safety (or earth) ground before making any other connections.
WARNING: To reduce the risk of fire, electrical shock, or physical injury it is strongly recommended to fuse the voltage measurement inputs. Be sure to locate
fuses as close to the source as possible.
WARNING: Replace fuse with the same type and rating to provide protection against risk of fire and shock hazards.
WARNING: In the event of repeated failure, do not replace the fuse again as a repeated failure indicates a defective condition that will not clear by replacing the
fuse.
WARNING: Only qualified electrical personnel familiar with the construction and operation of this equipment and the hazards involved should install, adjust,
operate, or service this equipment. Read and understand this manual and other applicable manuals in their entirety before proceeding. Failure to observe this
precaution could result in severe bodily injury or loss of life.
RED
WHT
SHD
BLU
BLK
This manual suits for next models
1
Table of contents
Other HORNER Control Unit manuals
Popular Control Unit manuals by other brands

Inficon
Inficon VGC501 operating manual

Infosystem Technology Corporation
Infosystem Technology Corporation WM-112 user manual
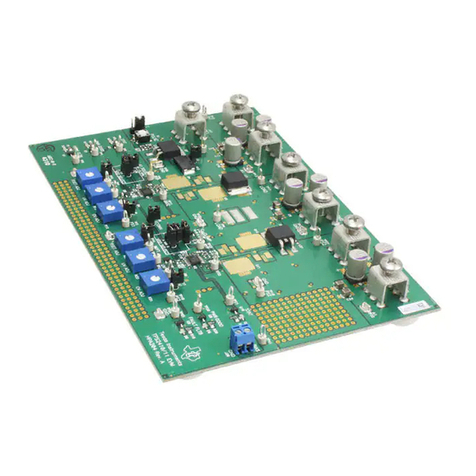
Texas Instruments
Texas Instruments TPS2410EVM user guide
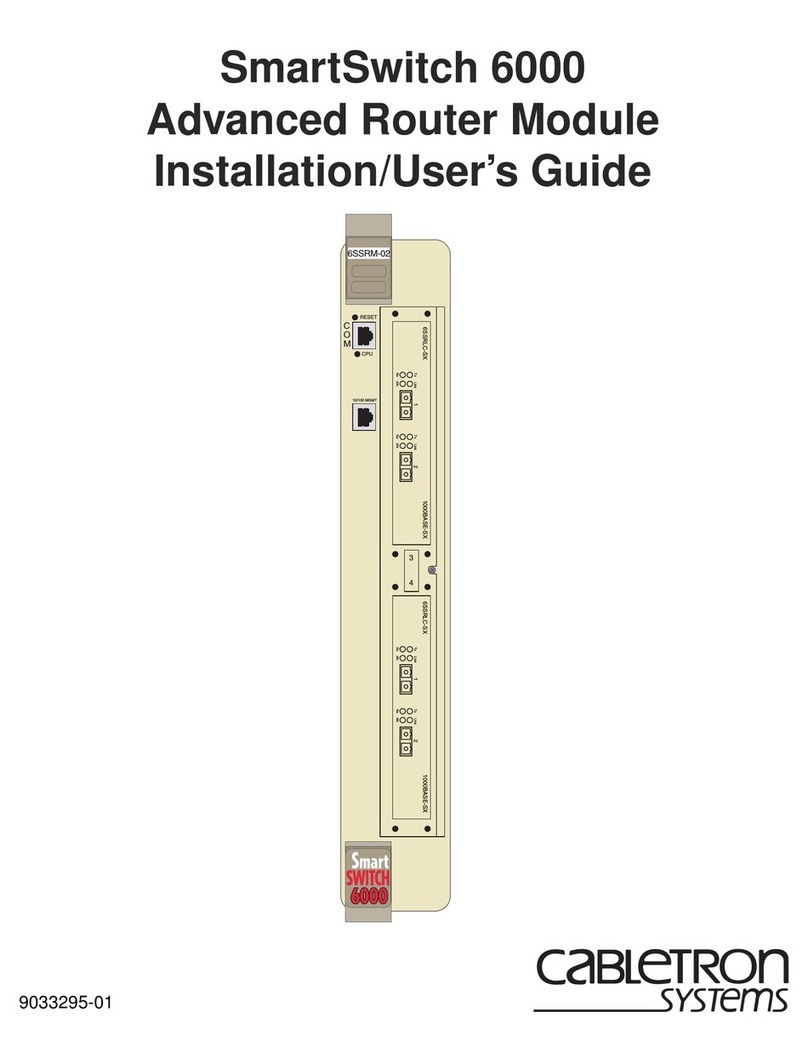
Cabletron Systems
Cabletron Systems SmartSwitch 6000 Installation & user guide
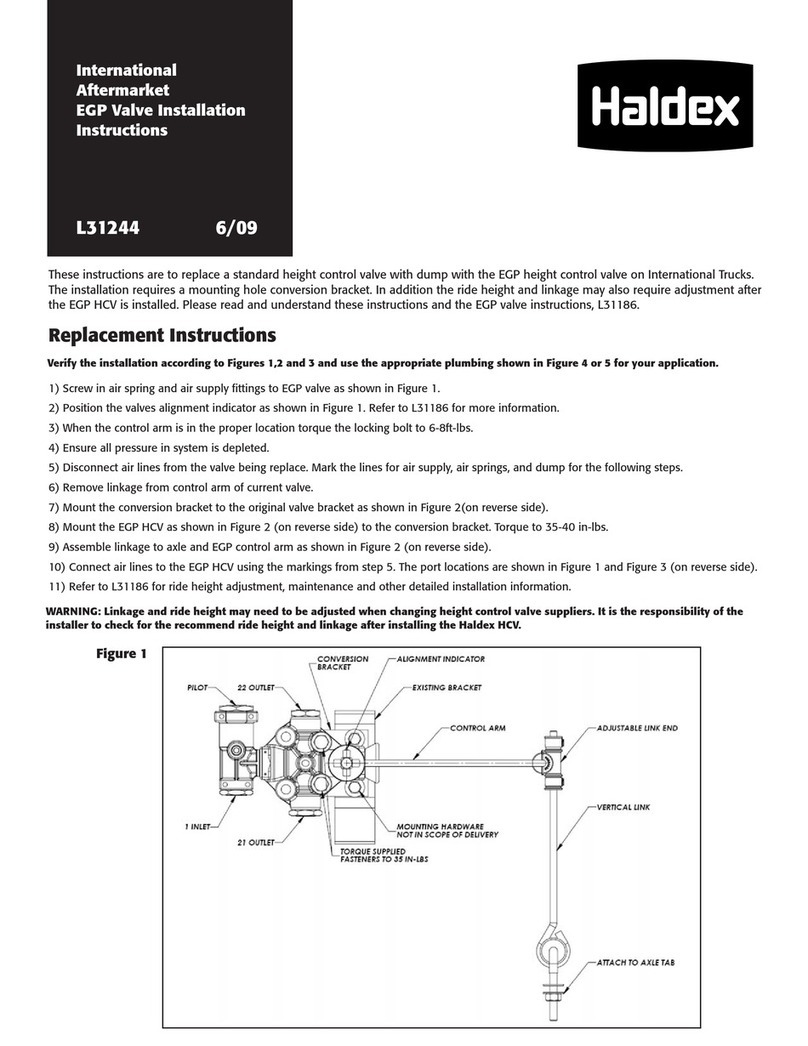
Haldex
Haldex EGP installation instructions
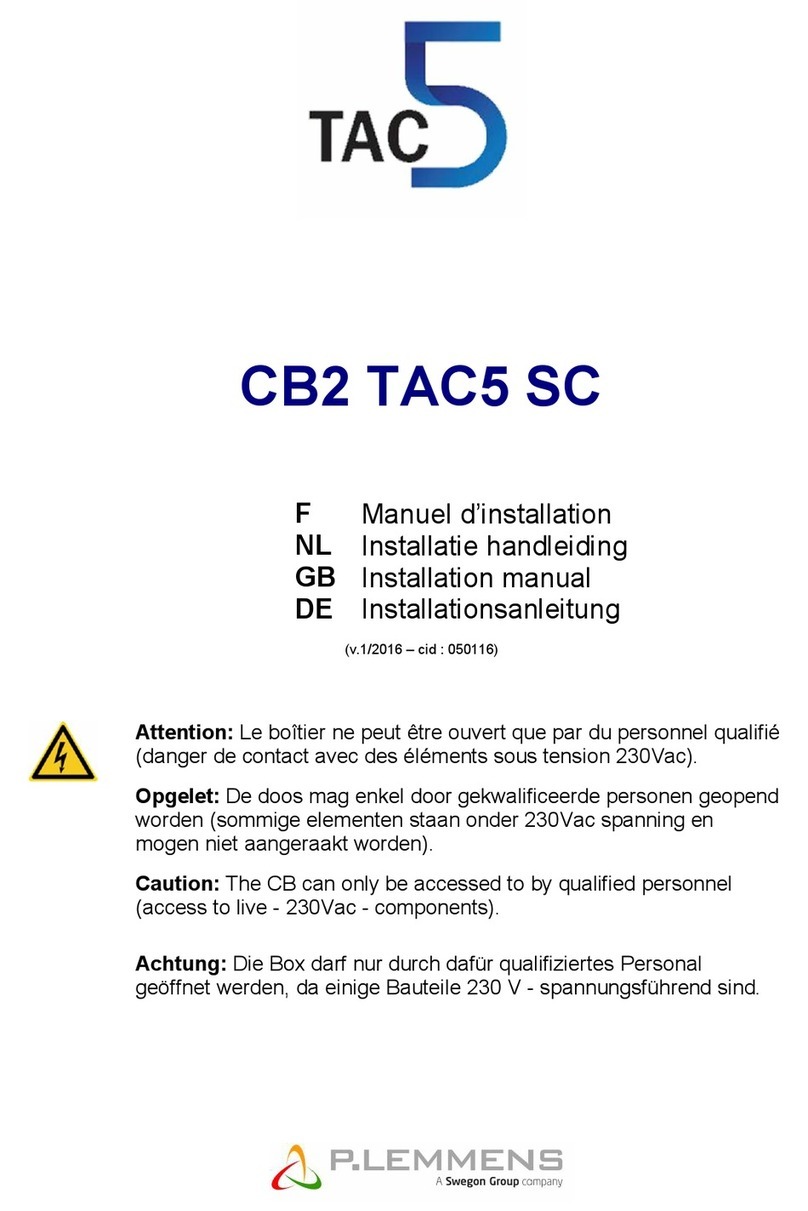
P.LEMMENS
P.LEMMENS CB2 TAC5 SC installation manual