HSB Beta 70-C-ZRS Quick guide

FM 239 Master MuW Manual Beta Type Z Rev.01
HSB Automation GmbH
In Laisen 74
72766 Reutlingen
Germany
Tel. +49 7121 14498-0
Fax +49 7121 14498-10
info@hsb-automation.de
www.hsb-automation.de
Distributor:
SCHUNK GmbH & Co. KG
Spann- und Greiftechnik
Bahnhofstr. 106 - 134
74348 Lauffen/Neckar
Germany
Tel. +49 7133-103-0
Fax +49 7133-103-2399
www.schunk.com
distributed by
Original
Assembly and
Maintenance Manual
Linear Unit
Types
Beta 60-ZSS
Beta 70-C-ZRS-ZSS
Beta 80-ZRS-ZSS
Beta 80-C-ZRS-ZSS
Beta 100-ZRS-ZSS
Beta 100-D-ZSS-ZSA
Beta 110-ZRS-ZSS
Beta 120-ZRS-ZSS
Beta 120-C-ZSS
Beta 140-ZRS-ZSS
Beta 140-C-ZSS
Beta 165-ZSS
Beta 180-ZSS
Beta 180-C-ZSSS


Safety
FM 239 MuW Beta Type Z Rev.01 2022-09-01 1
distributed by
Contents
1Safety........................................................................................................................3
1.1 Symbols used............................................................................................................ 3
1.2 Regulation use .......................................................................................................... 3
1.3 General safety........................................................................................................... 4
1.5 Use in explosive environments.................................................................................. 4
1.6 Technical condition of the linear unit.......................................................................... 5
1.7 Modifications to the linear unit ................................................................................... 6
1.8 Requirements for personnel....................................................................................... 6
1.9 Obligations of the operating company........................................................................ 7
2Warranty ...................................................................................................................7
3Technical data –Standard model...........................................................................8
4Product description...............................................................................................14
5Transportation and storage ..................................................................................17
6Installation and adjustment...................................................................................18
6.1 Installing the linear unit by mounting rails ................................................................ 18
6.2 Screwing the linear unit into place from below......................................................... 19
6.3 Setting maximum travel........................................................................................... 19
6.3.1 Setting the positions of the inductive limit switches ..................................20
6.3.2 Setting the positions of the mechanical limit switches...............................21
6.4 Mounting a drive unit ............................................................................................... 22
6.4.1 Mounting a motor.....................................................................................23
7Start-up...................................................................................................................24
8Operation................................................................................................................25
9Shutdown................................................................................................................26
10 Maintenance...........................................................................................................27
10.1 Lubrication............................................................................................................... 27
10.2 Replacing the timing belt ......................................................................................... 30
10.3 Replacing cover bands............................................................................................ 34

Safety
22022-09-01 FM 239 MuW Beta Type Z Rev.01
distributed by
About this manual
Applicability
This manual applies to the following linear units with timing belt drive:
•Beta 60-ZSS
•Beta 70-C-ZRS-ZSS
•Beta 80-ZRS-ZSS
•Beta 80-C-ZRS-ZSS
•Beta 100-ZRS-ZSS
•Beta 100-D-ZSS
•Beta 100-D-ZSA
•Beta 110-ZRS-ZSS
•Beta 120-ZRS-ZSS
•Beta 120-C-ZSS
•Beta 140-ZRS-ZSS
•Beta 140-C-ZSS
•Beta 165-ZSS
•Beta 180-ZSS
•Beta 180-C-ZSS
The drawings show the Beta 60-ZSS type and serve as examples for
all other types, though some of the details may differ.

Safety
FM 239 MuW Beta Type Z Rev.01 2022-09-01 3
distributed by
1 Safety
The Assembly and Maintenance Manual is a component element of the
product package, and must always be kept to hand as a reference
source.
The Manual must be passed on if the unit is sold on or given away.
If there is anything in this manual which you do not fully understand,
please be sure to contact the manufacturers.
1.1 Symbols used
This manual employs the following symbols to indicate hazards as well
as other types of symbol:
Indicates immediate danger.
Failure to observe this notice entails risk of death or very serious injury.
Indicates a danger carrying a medium to high risk.
Failure to observe this notice may result in death or serious injury.
Indicates minor risk.
Failure to observe this notice may result in light to moderate injury or
damage to property.
Note
Indicates tips on use of the machine and optimising its efficiency.
1.2 Regulation use
The mechanical linear unit is intended for installation in machines, and
is used solely for manipulating, positioning, transporting, palletising ,
loading, unloading, clamping, clocking, tensioning, testing, measuring,
handling and pushing workpieces or tools.
Pay attention to the basic applications of the linear unit set out in
sections 4 and 3.
In order to comply with the EU Directive governing Electromagnetic
Compatibility (EMC), the mechanical linear unit may only be used in
industrial environments.
Any other use, or use for purposes beyond those stipulated, will be
classed as illegitimate. The manufacturers accept no liability for any
loss thereby incurred. The risk is borne solely by the operators.

Safety
42022-09-01 FM 239 MuW Beta Type Z Rev.01
distributed by
1.3 General safety
Preconditions for
operation
The linear unit must not be put into operation until the machine or line
into which it is installed conforms to the following:
•Relevant accident prevention regulations
•Generally accepted safety standards
•EU directives
•Standards governing the electromagnetic compatibility of machinery
•Other applicable standards
•Applicable national legislation.
Safe operation
To ensure safe operation, refer to the following documents:
•This operating manual for the linear unit, particularly the technical
data
•The operating manual for the line into which it is installed
1.4 Use in clean rooms (ISO 14644)
The linear units used in clean rooms are fitted with a vent hole
(generally G1/2“) at the basic profile.
The following guidelines must be observed:
•The linear unit must be subjected to a negative pressure of 0.2 bar.
•The linear unit must be relubricated with a grease suitable for use
in clean rooms (basic lubrication carried out using Klübersynth
BEM 32-34).
1.5 Use in explosive environments
The linear units are suitable for use in potentially explosive
atmospheres, but the supplement to these assembly and maintenance
instructions " FM_319_Use-in-Atex-zones-MuW " must be observed.
The following applies to Beta 100-D-ZSA:
The linear unit is not suitable for use in potentially explosive
atmospheres.

Safety
FM 239 MuW Beta Type Z Rev.01 2022-09-01 5
distributed by
1.6 Technical condition of the linear unit
State of the art
The unit conforms to the current state of the art and applicable rules
and regulations. The unit conforms to the EU Machinery Directive,
harmonised European standards or corresponding national standards:
•Machinery Directive 2006/42/EC
•DIN EN ISO 12 100:2011-03 Safety of Machinery, General Design
Guidelines, Risk Assessment and Reduction
•DIN EN ISO 13850:2008-09: Safety of machinery; emergency-stop
devices
•DIN EN 60 204-1:2006: Electrical equipment for industrial machines
•2004/108/EC: EMC Directive
•EMVG: German law relating to the electromagnetic compatibility of
equipment dated 26.02.2008 (Federal Gazette I p. 220)

Safety
62022-09-01 FM 239 MuW Beta Type Z Rev.01
distributed by
1.7 Modifications to the linear unit
Modifications
The linear unit must not be modified, either in its basic design or in its
safety components, without our written consent. Any such unauthorised
modification will void our liability in respect of the unit.
The operating company may only carry out the maintenance and repair
work detailed in this operating manual. Any other measures, such as to
replace wearing parts and components, may be carried out only in
consultation with our service engineers, by the service engineers
themselves, or by us directly.
Installed safety devices must never be dismantled or disabled.
When fitting special attachments to the unit, follow the fitting
instructions provided by the manufacturers!
1.8 Requirements for personnel
The linear unit has been designed and built in accordance with the
state of the art and accepted safety standards. Hazards may
nevertheless be posed when operating it. Consequently, the unit may
only be installed and operated by trained, competent personnel.
All personnel assigned to install, operate, maintain, repair or dismantle
a linear unit must have read and understood this operating manual, and
in particular section 1, “Safety”.
Work on parts carrying live electrical current may be carried out only by
trained electricians. Such work includes:
•Installing safety limit switches
•Mounting a drive unit
•Checking the direction of rotation of the drive

Warranty
FM 239 MuW Beta Type Z Rev.01 2022-09-01 7
distributed by
1.9 Obligations of the operating company
Instruction of
personnel
In accordance with EU Health and Safety Directive 89/655/EEC articles
6(1) and 7 and with the Framework Directive 89/391/EEC articles 1(1)
and 6(1), the company operating the linear unit must provide personnel
assigned to install, operate, maintain, repair or dismantle the unit with
appropriate instruction, in particular with regard to safety.
We recommend that companies require their personnel to provide
written confirmation of having received such instruction.
Checking the unit
In accordance with EU Health and Safety Directive 89/655/EEC article
4a, the operating company must subject to the unit to thorough
checking prior to putting it into operation, after carrying out repairs, and
after malfunctions have occurred.
Legibility and
maintenance of
affixed notices and
labels
The operating company must ensure that all notices and labels
attached to the unit are fully legible (in particular details of the serial
number) and must ensure compliance with all instructions contained on
them. Damaged or illegible notices and labels must be replaced.
2 Warranty
The warranty conditions are laid down in the terms and conditions of
delivery and payment issued at time of order. Warranty cover will be
voided if:
•the unit is not operated in accordance with the stipulated regulation
use;
•the instructions set out in this operating manual are not followed;
•the unit is modified without the consent of the manufacturers;
•screws sealed by locking varnish are unlocked.
The manufacturer’s warranty in respect of maintenance and repair work
applies only if original replacement parts are used.

Technical data –Standard model
82022-09-01 FM 239 MuW Beta Type Z Rev.01
distributed by
3 Technical data –Standard model
Technical data
Linear unit
Sizes
Beta type with
timing belt drive
Beta
60
Beta 70-C
Beta 80
Beta 80-C
Beta 100
Beta
100-D
ZSS
ZRS
ZSS
ZRS
ZSS
ZRS
ZSS
ZRS
ZSS
ZSS
Drive element
Timing belt
Stroke per revolution [mm]
160
175
175
220
220
210
210
200
200
160
Velocitymax. [m/s]
5,00
8,00
5,00
8,00
5,00
8,00
5,00
8,00
5,00
5,00
Acceleration max. [m/s2]
30
30
30
40
40
40
40
40
40
60
No-load torque [Nm]
1,10
1,20
1,20
1,50
1,50
1,80
1,80
2,50
2,50
5,00
Maximum travel (standard) [mm]
7620
7640
6840
7600
7600
7580
7600
7420
7420
7720
Repeat accuracy [mm]
±0,08
±0,08
±0,08
±0,08
±0,08
±0,08
±0,08
±0,08
±0,08
±0,08
Operating temperature [°C]
(continuous operation)
0...80
0...80
0...80
0...80
0...80
0...80
0...80
0...80
0...80
0...80
Geometrical moment of inertia IY
[mm4]
400064
583502
563227
1274608
1330612
1304382
1374486
1784876
917778
Geometrical moment of inertia IZ
[mm4]
522090
852344
852687
1706029
1694165
1760119
1772461
3588262
2328902
Length of standard carriage [mm]
190
190
190
210
210
210
210
280
280
210
Length of long carriage [mm]
230
240
240
270
270
270
270
400
400
270
Weight (without travel) [kg]
4,55
3,10
3,40
5,50
6,10
5,30
7,80
9,50
9,10
6,80
Weight (per 100 mm travel) [kg]
0,59
0,59
0,38
0,60
0,85
0,65
0,98
1,10
1,45
0,75
Weight of standard carriage [kg]
1,22
1,30
1,65
2,10
1,80
3,00
2,75
4,10
3,80
3,50
Weight of long carriage [kg]
1,72
1,65
2,10
2,70
2,30
3,70
3,25
5,85
5,43
4,10
Noise emission max. [dB A] 1)
80
80
80
80
80
80
80
80
80
80
1) The figure will vary based on assembly with other system components

Technical data –Standard model
FM 239 MuW Beta Type Z Rev.01 2022-09-01 9
distributed by
Technical data - Linear unit
Sizes
Beta type with timing belt drive
Beta
100-D
Beta 110
Beta 120
Beta
120-C
Beta 140
Beta
140-C
ZSA
ZRS
ZSS
ZRS
ZSS
ZSS
ZRS
ZSS
ZSS
Drive element
Zahnriemen
Stroke per revolution [mm]
160
300
300
240
240
300
220
220
220
Velocitymax. [m/s]
5,00
8,00
5,00
8,00
5,00
5,00
8,00
5,00
5,00
Acceleration max. [m/s2]
60
60
60
60
60
60
60
60
60
No-load torque [Nm]
5,40
3,50
3,50
3,00
3,00
4,50
2,50
2,50
2,50
Maximum travel (standard) [mm]
7720
7520
7520
7520
7520
7500
7540
7540
8100
Repeat accuracy [mm]
±0,08
±0,08
±0,08
±0,08
±0,08
±0,08
±0,08
±0,08
±0,08
Operating temperature [°C]
(continuous operation)
0...80
0...80
0...80
0...80
0...80
0...80
0...80
0...80
0...80
Geometrical moment of inertia IY[mm4]
917778
4999522
4940967
3093457
7115871
3160259
3117373
Geometrical moment of inertia IZ[mm4]
2328902
6042239
5979329
7081517
8943087
9121665
9047121
Length of standard carriage [mm]
172
320
320
320
320
320
320
320
320
Length of long carriage [mm]
-
500
500
500
500
500
500
500
500
Weight (without travel) [kg]
11,70
15,70
18,00
12,50
13,0
0
21,00
13,50
15,0
0
15,00
Weight (per 100 mm travel) [kg]
0,75
1,50
2,10
1,30
1,70
2,40
1,30
1,70
1,70
Weight of standard carriage [kg]
2,70
4,80
5,20
6,00
6,50
8,00
7,00
7,50
7,50
Weight of long carriage [kg]
-
7,50
8,20
9,40
10,2
0
12,00
11,00
11,7
0
11,70
Noise emission max. [dB A] 1)
80
80
80
80
80
80
80
80
80
1) The figure will vary based on assembly with other system components
Technical data - Linear unit
Sizes

Technical data –Standard model
10 2022-09-01 FM 239 MuW Beta Type Z Rev.01
distributed by
Beta type with timing belt drive
Beta 165
Beta 180
Beta 180-C
ZSS
ZSS
ZSS
Drive element
Zahnriemen
Stroke per revolution [mm]
440
320
320
Velocitymax. [m/s]
5,00
5,00
5,00
Acceleration max. [m/s2]
60
60
60
No-load torque [Nm]
12,00
8,00
8,00
Maximum travel (standard) [mm]
6920
7500
7500
Repeat accuracy [mm]
±0,08
±0,08
±0,08
Operating temperature [°C] (continuous
operation)
0...80
0...80
0...80
Geometrical moment of inertia IY[mm4]
21411115
9351064
Geometrical moment of inertia IZ[mm4]
25986463
24300412
Length of standard carriage [mm]
400
380
380
Length of long carriage [mm]
600
600
600
Weight (without travel) [kg]
42,40
37,70
39,70
Weight (per 100 mm travel) [kg]
3,50
2,40
2,60
Weight of standard carriage [kg]
11,90
11,20
14,65
Weight of long carriage [kg]
17,90
15,70
15,75
Noise emission max. [dB A] 1)
80
80
80
1) The figure will vary based on assembly with other system components

Technical data –Standard model
FM 239 MuW Beta Type Z Rev.01 2022-09-01 11
distributed by
Forces and moments - Beta linear unit with timing belt drive
Type designation
Dynamic forces [Nm]
Dynamic moments [Nm]
FX
FY
FZ
-FZ
MX
MY
MZ
Mno-load
Beta 60-ZSS
850
500
1400
800
50
160
100
1,10
Beta 70-C-ZRS
1100
300
1000
400
35
120
50
1,00
Beta 70-C-ZSS
1100
600
1800
1200
60
180
120
1,20
Beta 80-ZRS
1350
500
1500
800
50
180
100
1,50
Beta 80-ZSS
1350
800
3000
2000
100
250
250
1,50
Beta 80-C-ZRS
2200
1000
1500
1500
100
300
180
1,80
Beta 80-C-ZSS
2200
1600
4000
3000
300
500
500
1,80
Beta 100-ZRS
2800
1000
2500
1200
200
250
200
2,50
Beta 100-ZSS
2800
1000
3000
2000
200
250
250
2,50
Beta 100-D-ZSS
2200
1800
4000
3000
350
750
750
5,00
Beta 110-ZRS
4000
2000
5000
2500
300
600
450
3,50
Beta 110-ZSS
4000
3000
8000
4000
400
800
600
3,50
Beta 120-ZRS
4000
2500
5000
3000
350
700
700
3,50
Beta 120-ZSS
4000
3000
8000
4000
400
800
600
3,50
Beta 120-C-ZSS
4800
4000
12000
6000
600
1500
1000
3,50
Beta 140-ZRS
4000
2500
5000
3000
350
700
700
4,50
Beta 140-ZSS
4000
2500
6000
4000
500
1000
1000
4,50
Beta 140-C-ZSS
4000
3200
7500
5000
600
1200
1200
4,50
Beta 165-ZSS
10000
5000
15000
8000
700
1400
1100
12,00
Beta 180-ZSS
6000
6000
12000
6000
1500
3000
1500
8,00
Beta 180-C-ZSS
6000
8000
15000
8000
1800
3600
1800
8,00
Figures in ( ) relate to the long carriage.
Mno-load = No-load torque ±30%
The forces and moments quoted are maximum values for the single load. In the event
of combined loading or simultaneous occurrence of multiple moments or forces, the
individual values must be reduced. In case of doubt consult Technical Support.

Technical data –Standard model
12 2022-09-01 FM 239 MuW Beta Type Z Rev.01
distributed by
Dynamic load ratings of rail guides - Beta linear unit
Model
Size
Number
of rails
Number
of
carriages
Load rating
per carriage
Cdyn [N]
THK / Rex*
Preten-sion
FV
[N]
THK / Rex*
Mt [Nm]
THK / Rex*
Guide
spacing in
direction x
(lx1) [mm]
Guide
spacing in
direction y
(ly) [mm]
Beta 60
15
1
2
11271 / 9860
564 / 620
60 / 74
106 (156)
Beta 70-C
15
1
2
11271 / 9860
564 / 620
60 / 74
124 (174)
-
Beta 80
20
1
2
17700 / 23400
885 / 1500
210 / 240
128 (188)
-
Beta 80-C
25
1
2
25160 / 28600
1258 / 1820
340 / 320
122 (182)
-
Beta 100
20
1
2
17700 / 23400
885 / 1500
210 / 240
152 (272)
-
Beta 100-D-ZSS
15
2
4
11271 / 9860
564 / 620
-
150 (210)
56
Beta 110
25
1
2
11271 / 9860
564 / 620
340 /320
203 (383)
-
Beta 120
25
1
2
25160 / 28600
1258 / 1820
340 / 320
144 (324)
-
Beta 120-C
30
1
2
25160 / 28600
1258 / 1820
580 /540
184 (364)
-
Beta 140
15
2
4
35558 / 36500
1778 / 2540
-
180 (330)
72
Beta 140-C-ZSS
20
2
4
11271 / 9860
564 / 620
-
200 (400)
76
Beta 165-ZSS
35
1
2
17700 / 23400
885 / 1500
985 / 890
198 (398)
-
Beta 180-ZSS
20
2
4
49448 / 51800
2472 / 3350
-
172 (392)
84
Beta 180-C-ZSS
25
2
4
17700 / 23400
885 / 1500
-
272 (492)
84
Figures in ( ) relate to the long carriage
The load rating and pre-tension figures relate to the standard linear guidance system with recirculating linear ball bearings
* Rex = Rexroth
Static and dynamic load ratings of roller guides - Beta linear unit
Model
Size
()
[mm]
Number
of load-
bearing
rollers
for Fz
Number
of load-
bearing
rollers
for Fy
Load
rating per
roller Cstat
[N]
Load
rating per
roller Cdyn
[N]
Guide spacing*
in direction x [mm]
Guide
spacing in
direction y
[mm]
lx1
lx2
ly
Beta 50-C
20
4
2
600
1.500
86 (136)
86 (136)
30,5
Beta 70
20
4
2
600
1.500
74 (124)
138,5 (188)
41
Beta 80
20
4
2
600
1.500
95 (155)
156,5 (216)
41,5
Beta 80-C
24
4
-
-
2
1240
2300
2750
4200
-
75
148,5
-
42
-
Beta 100
28
4
2
1.300
3.200
136 (256)
223 (343)
47
Beta 110
28
4
2
1.300
3.200
175 (355)
262 (424)
66
Beta 120
35
4
2
3.000
6.800
148 (328)
148 (328)
70
Beta 140
35
4
2
3.000
6.800
202 (352)
202 (389)
98
Beta 180
35
4
2
3.000
6.800
272 (492)
272 (492)
121
Beta 180-C
47
4
2
6550
13500
224 (444)
224 (444)
125
The pre-tension per roller is approximately 5%

Technical data –Standard model
FM 239 MuW Beta Type Z Rev.01 2022-09-01 13
distributed by
Tightening torques [Nm] for fixing screws
Fixing screws
M4
M5
M6
M8
M10
M12
The figures given are intended as
guides.
For shorter insertion depths, the
figures must be adjusted
accordingly.
DIN912/ISO4762-8.8
2,7
5,4
9,0
22,0
43,0
74,0
DIN912/ISO4762-10.9
3,0
5,7
9,0
22,0
43,0
74,0
DIN912/ISO4762-12.9
3,0
5,7
9,0
22,0
43,0
74,0
Tightening torques [Nm] for clutch with clamping hub
Size
14
19
24
28
38
Clutch diameter [mm]
30
40
55
65
80
Screw size
M3
M6
M6
M8
M8
Tightening torque [Nm]
1,34
10,50
10,50
25,00
25,00
Tightening torques [Nm] for clutch with clamping ring hub
Size
14
19
24
28
38
Clutch diameter [mm]
30
40
55
65
80
Screw size
M3
M4
M5
M5
M6
Tightening torque [Nm]
1,34
2,90
6,00
6,00
10,00

Product description
14 2022-09-01 FM 239 MuW Beta Type Z Rev.01
distributed by
4 Product description
Linear unit with
timing belt drive
Key
1
Bearing casing
4
Cover band
2
Carriage
5
Base profile
3
Lubricating nipple
6
Driver
Figure 1: Component assemblies of the Beta 60 linear unit with timing belt
drive

Product description
FM 239 MuW Beta Type Z Rev.01 2022-09-01 15
distributed by
Roller bearing and
linear guidance
system
Key
2
Carriage
8
Roller bearing guidance system
5
Base profile
9
Recirculating ball bearing
7
Timing belt
10
Guide rails
Figure 2: Guide elements
A mechanical linear unit converts rotational motion into linear motion
and is used to move loads quickly, safely and precisely from one
position to another. It consists of an aluminium base profile, a moving
carriage supported by a guide element (recirculating ball bearing or
roller bearing guidance system) and a drive element (screw or timing
belt drive).
Depending on its design, the carriage is able to absorb forces and
moments in all directions, and is positively connected to the guidance
and drive elements by way of the so-called drivers.
The base profile is self-supporting up to a certain length, and is
equipped with grooves for mounting.

Product description
16 2022-09-01 FM 239 MuW Beta Type Z Rev.01
distributed by
As an option, the linear unit can be equipped with accessories such as
a cover, screw supports, inductive or mechanical limit switches and
other fittings(see section 6.3).
The effective range can be flexibly configured. Multiple linear units of
the Alpha, Beta or Delta type can be arranged two-dimensionally (2
axes) or three-dimensionally (3 axes).
Driven linear units can be connected to non-driven units of the same
type by a plate, to be able to take large-area loads for example.

Transportation and storage
FM 239 MuW Beta Type Z Rev.01 2022-09-01 17
distributed by
5 Transportation and storage
The mechanical linear unit is a precision item. Its mechanism may be
damaged by heavy jolting, resulting in impairment of its functions.
Risk of damage by heavy jolting or bending!
Transport the assembled linear unit only with the transit protection
fitted.
To prevent damage during transportation and storage, protect the linear
unit against shaking and sliding as follows:
•Stow it in a box of sufficient size.
•Use packing.
Section 3 lists the unit weights.
Protect the unit against:
•dirt;
•corrosion;
•water;
•and aggressive atmospheres.

Installation and adjustment
18 2022-09-01 FM 239 MuW Beta Type Z Rev.01
distributed by
6 Installation and adjustment
The linear unit can be attached by the following methods:
•On mounting rails
•By screws inserted into the sliding blocks
•By screws inserted into the factory-fitted tapped hole rails
Install the linear unit on a flat surface. Unit parallelism < 0.2
mm/1,000 mm.
Mounting by the rails with tapped holes in them is the preferable
solution:
for highly dynamic applications;
where the linear unit has only two attachment points.
6.1 Installing the linear unit by mounting rails
Figure 3: Mounting rails (1)
The recommended maximum spacing between the mounting rails is
700 mm.
Procedure
1. Attach the mounting rails (1) loosely in position (figure 2).
2. Align the linear unit axially.
3. Tighten the mounting rails (1)
(for tightening torques see section 3).
This manual suits for next models
21
Table of contents
Other HSB DC Drive manuals
Popular DC Drive manuals by other brands
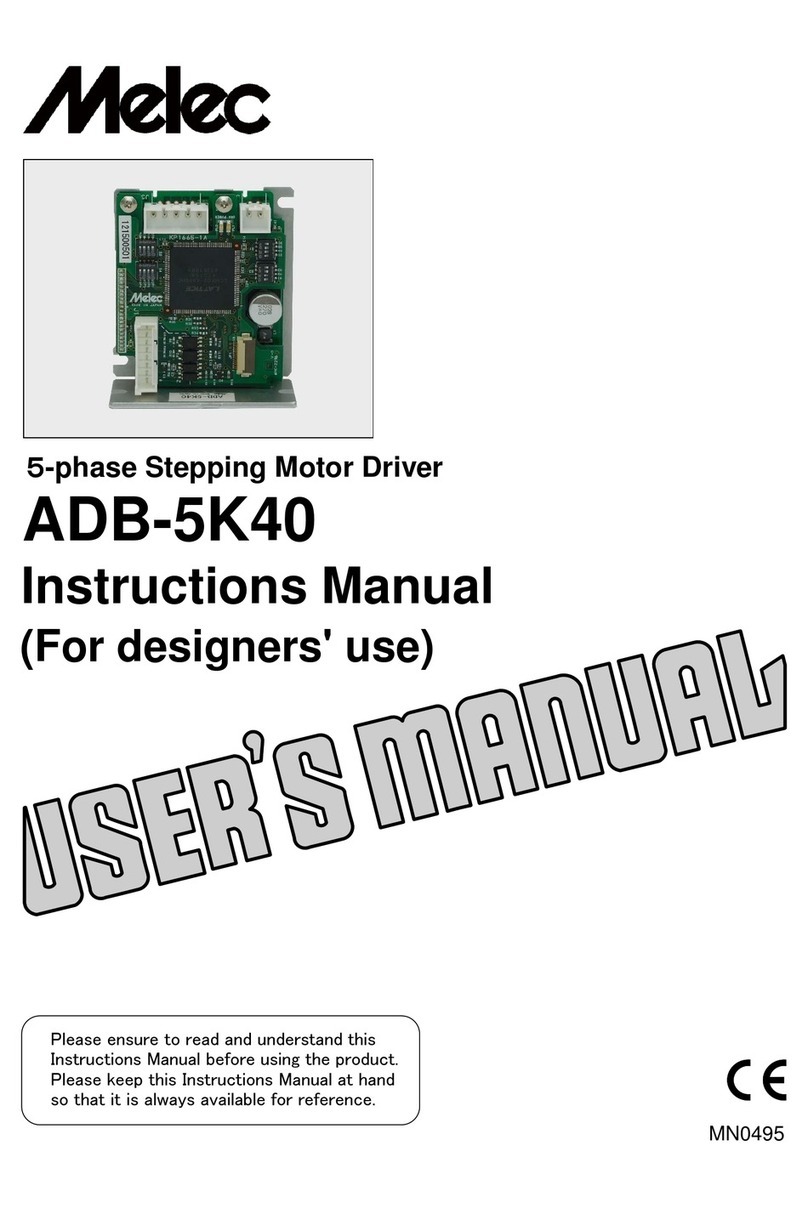
M-Elec
M-Elec ADB-5K40 instruction manual
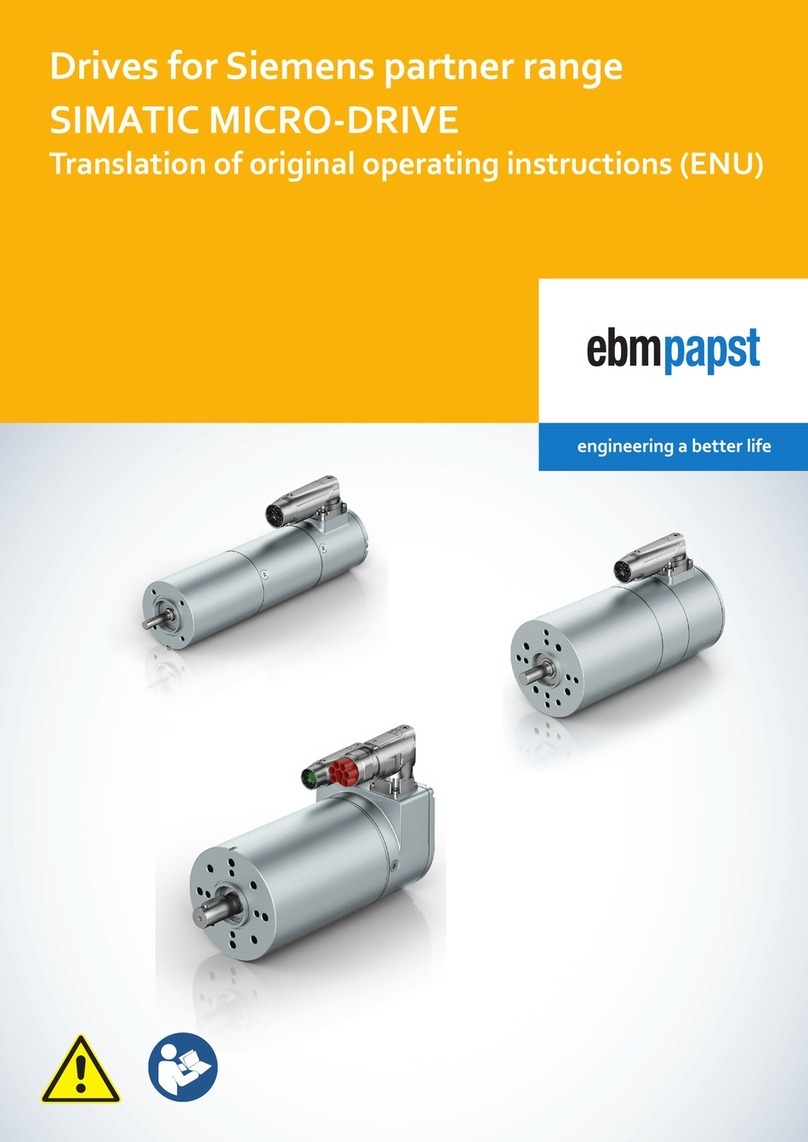
Ebmpapst
Ebmpapst ECI-42 K1 Series Translation of original operating instructions

KEBCO
KEBCO COMBIVERT G6 series Instructions for use
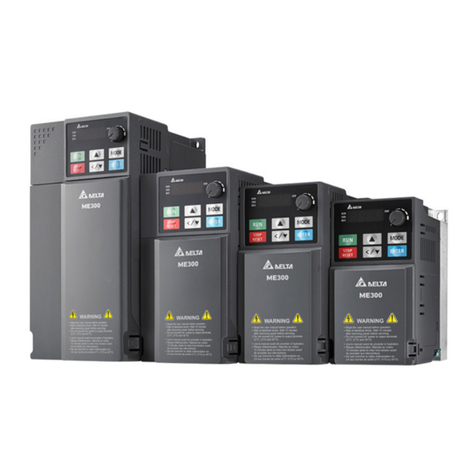
Delta
Delta VFD-ME300 Series Quick setup instructions
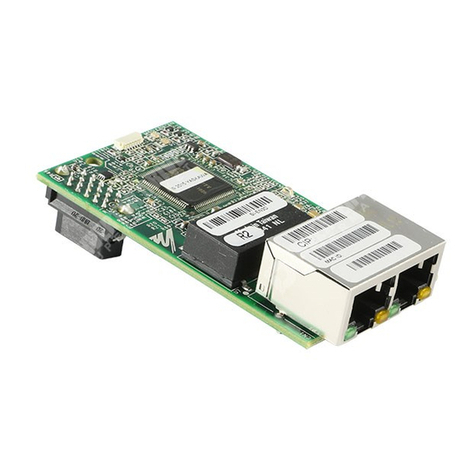
YASKAWA
YASKAWA 1000-Series installation manual
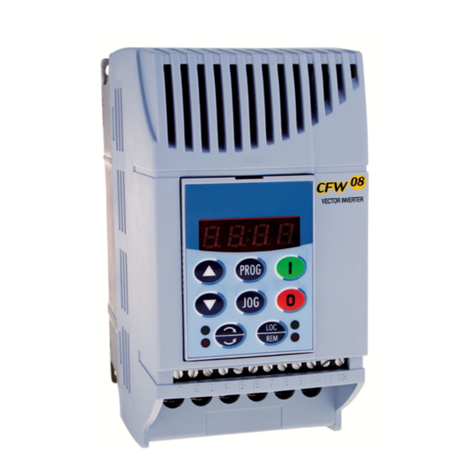
Eliwell
Eliwell EWCFW-08 user manual
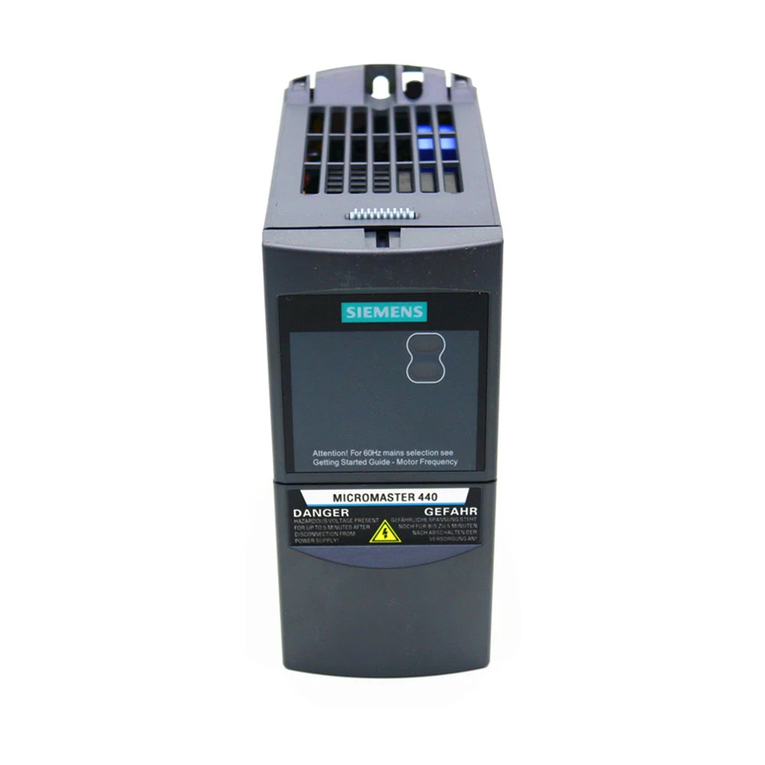
Siemens
Siemens MICROMASTER 440 operating instructions

Mitsubishi Electric
Mitsubishi Electric D700-SC Easy start guide
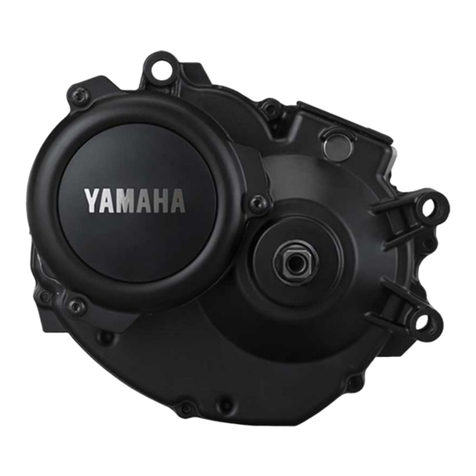
Yamaha
Yamaha PW-SE quick start guide

GFA
GFA ELEKTROMAT SI 45.7 WS-40,00 installation instructions
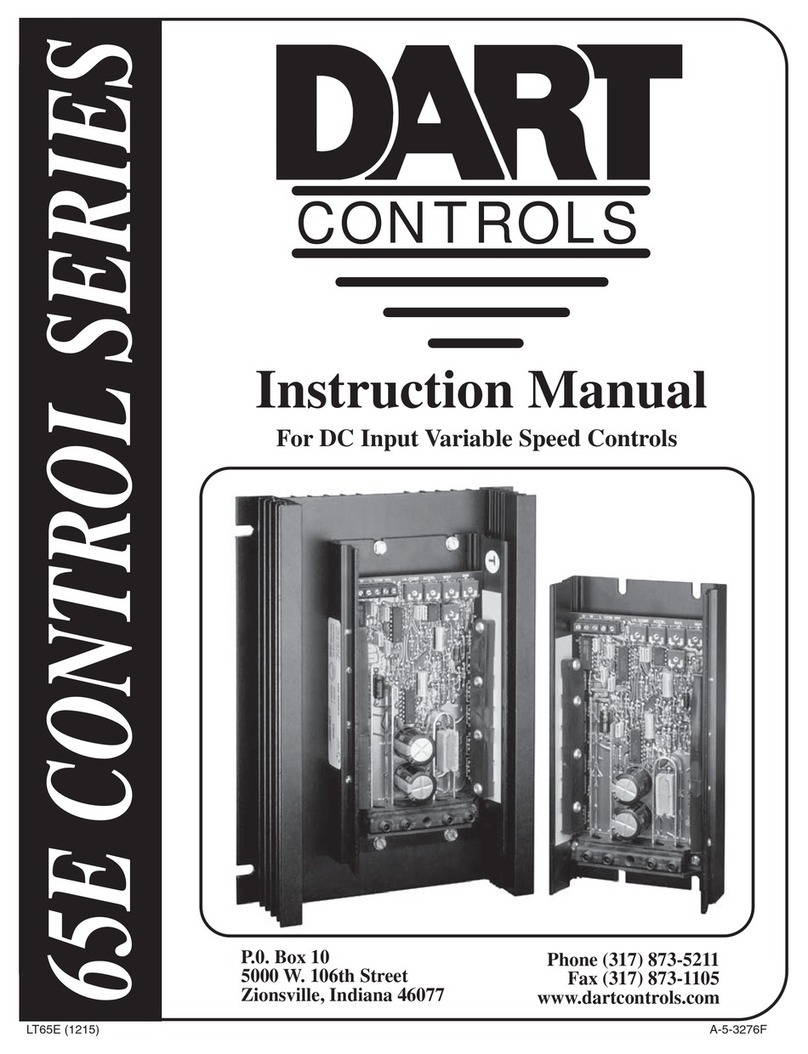
DART Controls
DART Controls 65E Series instruction manual
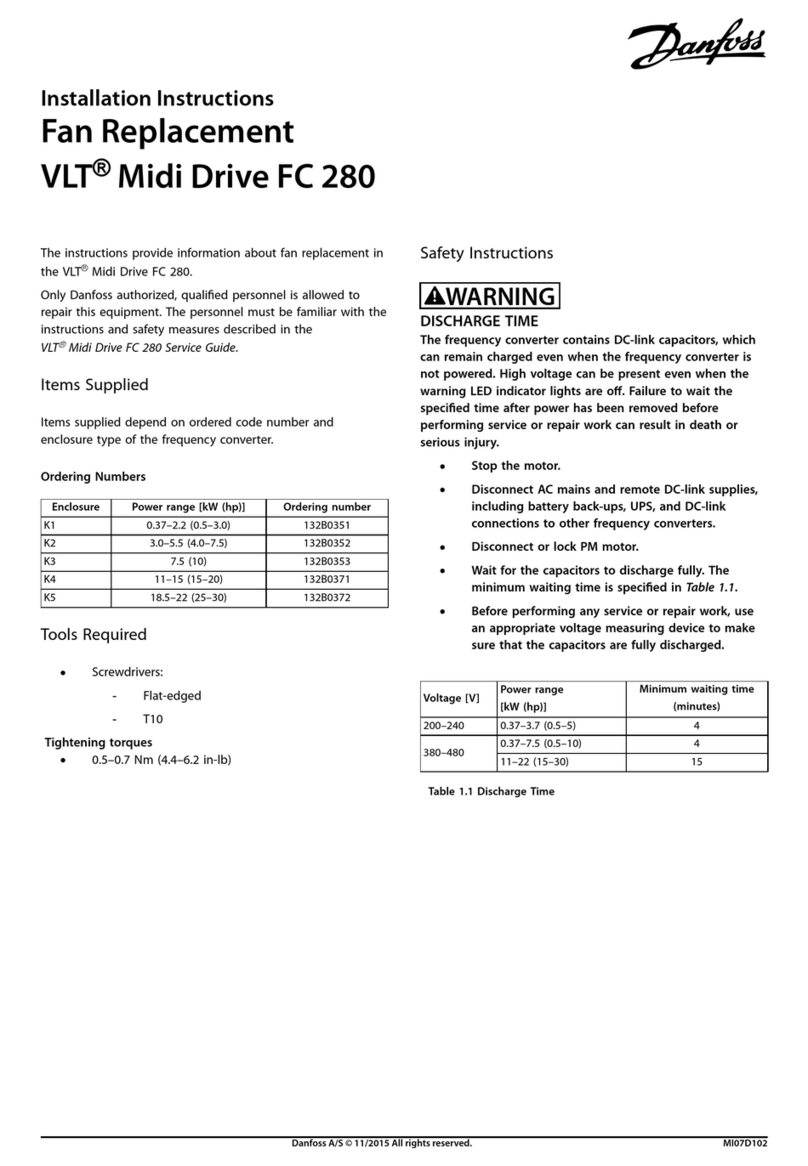
Danfoss
Danfoss VLT Midi Drive FC 280 installation instructions