Hussmann KRACK MK Series User manual

MK/MV-Medium Profile Series Unit Coolers (E206993_J)
Part Number: E206993_M

MK/MV – Medium Profile Series Unit Coolers (E206993_M)
ANSI Z535.5 DEFINITIONS
•DANGER – Indicate[s] a hazardous
situation which, if not avoided, will
result in death or serious injury.
•WARNING – Indicate[s] a hazardous
situation which, if not avoided, could result
in death or serious injury.
•CAUTION – Indicate[s] a
hazardous situation which, if not
avoided, could result in minor or
moderate injury.
•NOTICE – Not related to personal injury –
Indicates[s] situations, which if not avoided,
could result in damage to equipment.
The information contained in this document is
the property of Hussmann Corporation and
shall not be used in whole or in part without
written permission.
Environmental Concerns
Hussmann recommends responsible
handling of refrigerants that contain
Chlorine, Fluorine and Carbon (CFCs)
and those that contain Hydrogen,
Chlorine, Fluorine, and Carbon
(HCFCs). Only certified technicians
may handle these refrigerants. All
technicians must be aware and follow
the requirements set forth by the
Federal Clean Air Act (Section 608) for
any service procedure being performed
on this equipment that involves
refrigerant. Additionally, some states
have other requirements that must be
adhered to for responsible manage-
ment of refrigerants.
BEFORE YOU BEGIN
Read these instructions completely and
carefully.
ANSI Z535.5 DEFINITIONS
• DANGER – Indicate[s] a hazardous situation
which, if not avoided, will result in death or serious
injury.
• WARNING – Indicate[s] a hazardous situation
which, if not avoided, could result in death or serious
injury.
• CAUTION – Indicate[s] a hazardous situation
which, if not avoided, could result in minor or
moderate injury.
• NOTICE – Not related to personal injury – Indicates[s]
situations, which if not avoided, could result in damage to
equipment.
Environmental Concerns
Hussmann recommends responsible handling of refrige-
rants that contain Chlorine, Fluorine and Carbon (CFCs) and
those that contain Hydrogen, Chlorine, Fluorine, and Carbon
(HCFCs). Only certified technicians may handle these
refrigerants. All technicians must be aware and follow the
requirements set forth by the Federal Clean Air Act (Section
608) for any service procedure being performed on this
equipment that involves refrigerant. Additionally, some
states have other requirements that must be adhered to for
responsible management of refrigerants.
This warning does not mean that Hussmann products
will cause cancer or reproductive harm, or is in
violation of any product-safety standards or
requirements. As clarified by the California State
government, Proposition 65 can be considered more of
a ‘right to know’ law than a pure product safety law.
When used as designed, Hussmann believes that our
products are not harmful. We provide the Proposition
65 warning to stay in compliance with California State
law. It is your responsibility to provide accurate
Proposition 65 warning labels to your customers when
necessary. For more information on Proposition 65,
please visit the California State government website.
Contractors shall strictly adhere to
specifications provided by the Engineer of
Record (EOR), as well as US Environmental
Protection Agency regulations,
OSHA regulations, and all other federal, state
and local codes. This work should only be done
by qualified, li- censed contractors. There are
numerous hazards, not limited to, but including:
burns due to high temperatures, high pressures,
toxic substances, electrical arcs and shocks,
very heavy equipment with specific lift points
and structural constraints, possible acid expo-
sure, food and product damage, public safety,
noise, and possible environmental damage.
Never leave operating compressors unattended
during the manual soft-start process. Always
power rocker switches off when unattended.
!
!
!
PERSONAL PROTECTION EQUIPMENT (PPE)
Only qualified personnel should install and service this
equipment. Personal Protection Equipment (PPE) is re-
quired whenever servicing this equipment. Wear safety
glasses, gloves, protective boots or shoes, long pants,
and a long-sleeve shirt when working with this equip-
ment. Observe all precautions on tags, stickers, labels
and literature attached to this equipment.
This manual was written in accordance with
originally prescribed equipment that is subject to
change. Hussmann reserves the right to change
all or part of the equipment for future stores such
as, but not limited to, controllers, valves and
electrical specifications. It is the installers
responsibility to reference the refrigeration
drawings supplied for each installation, as
directed by the Engineer of Record.
August 31, 2018
PERSONAL PROTECTION EQUIPMENT (PPE)
Only qualified personnel should install and service
this equipment. Personal Protection Equipment
(PPE) is required whenever servicing this
equipment. Always wear safety glasses, gloves,
protective boots or shoes, long pants, and a long-
sleeve shirt when working with this equipment.
Observe all precautions on tags, stickers, labels
and literature attached to this equipment.
Contractors shall strictly adhere to
specifications provided by the Engineer of
Record (EOR), as well as US Environmental
Protection Agency regulations, OSHA
regulations, and all other federal, state and
local codes. This work should only be done
by qualified, licensed contractors. There are
numerous hazards, not limited to, but
including: burns due to high temperatures,
high pressures, toxic substances, electrical
arcs and shocks, very heavy equipment with
specific lift points and structural constraints,
possible acid exposure, food and product
damage, public safety, noise, and possible
environmental damage. Never leave operating
compressors unattended during the manual
soft-start process. Always power rocker
switches off when unattended.

MK/MV – Medium Profile Series Unit Coolers (E206993_M)
— LOCK OUT / TAG OUT —
To avoid serious injury or death from
electrical shock, always disconnect the
electrical power at the main disconnect
when servicing or replacing any electrical
component. This includes, but is not limited
to, such items as controllers, electrical
panels, condensers, lights, fans, and
heaters.
This warning does not mean that Hussmann
products will cause cancer or reproductive
harm, or is in violation of any product-safety
standards or requirements. As clarified by the
California State government, Proposition 65
can be considered more of a ‘right to know’
law than a pure product safety law. When
used as designed, Hussmann believes that
our products are not harmful. We provide the
Proposition 65 warning to stay in compliance
with California State law. It is your
responsibility to provide accurate Proposition
65 warning labels to your customers when
necessary. For more information on
Proposition 65, please visit the California
State government website.
This manual was written in accordance
with originally prescribed equipment that is
subject to change. Hussmann reserves the
right to change all or part of the equipment
for future stores such as, but not limited to,
controllers, valves and electrical
specifications. It is the installer’s
responsibility to reference the refrigeration
drawings supplied for each installation, as
directed by the Engineer of Record.
Proper Field Wiring and Grounding Required!
Failure to follow code could result in death or
serious injury. All field wiring MUST be
performed by qualified personnel. Improperly
installed and grounded field wiring poses FIRE
and ELECTRO- CUTION hazards. To avoid
these hazards, you MUST follow requirements
for field wiring installation and grounding as
described in NEC and your local/state
electrical codes.
This equipment is prohibited from use in
California with any refrigerants on the
“List of Prohibited Substances”for that
specific end-use,perCalifornia Code of
Regulations, title 17, section 95374.
Use in other locations is limited to
refrigerants permitted by country, state,
or local laws and is the responsibility of
the installer/end-user to ensure only
permitted refrigerants are used.
This disclosure statement has been
reviewed and approved by Hussmann
and Hussmann attests, under penalty
of perjury, that these statements are
true and accurate.

MK/MV – Medium Profile Series Unit Coolers (E206993_M)
1
TABLE&OF& CO N TENTS !
1 RECEIPT OF EQUIPMENT ____________________________________________________________ 6
1.1 INSPECTION __________________________________________________________________ 6
1.2 LOSS OF GAS HOLDING CHARGE ___________________________________________________ 6
2 UNIT INFORMATION AND DIMENSIONS _______________________________________________ 6
2.1 MODELS COVERED _____________________________________________________________ 6
2.2 UNIT DIMENSIONS _____________________________________________________________ 7
3 UNIT LOCATION AND MOUNTING ____________________________________________________ 7
3.1 UNIT LOCATION _______________________________________________________________ 7
3.2 MOUNTING ___________________________________________________________________ 7
4 PIPING INSTALLATION _____________________________________________________________ 8
4.1 DRAIN LINE ___________________________________________________________________ 8
4.2 REFRIGERATION PIPING _________________________________________________________ 8
4.3 EVACUATION AND LEAK TEST ____________________________________________________ 10
4.4 MK HOT GAS DEFROST PIPING ___________________________________________________ 10
4.5 REFRIGERANT DISTRIBUTOR NOZZLES _____________________________________________ 12
4.6 EXPANSION VALVE ____________________________________________________________ 17
5 ELECTRICAL _____________________________________________________________________ 21
5.1 FIELD WIRING ________________________________________________________________ 21
5.2 ELECTRICAL DATA _____________________________________________________________ 21
6 AIR DEFROST SEQUENCE OF OPERATION _____________________________________________ 23
6.1 SEQUENCE OF OPERATION ______________________________________________________ 23
7 ELECTRIC DEFROST SEQUENCE OF OPERATION _________________________________________ 23
7.1 SEQUENCE OF OPERATION ______________________________________________________ 23
7.1.1 STEP A: NORMAL REFRIGERATION CYCLE _______________________________________ 23
7.1.2 STEP B: DEFROST CYCLE ____________________________________________________ 24
8 GAS DEFROST SEQUENCE OF OPERATION _____________________________________________ 29
8.1 HGE/HGG 3 PIPE HOT GAS DEFROST ______________________________________________ 29
8.2 SEQUENCE OF OPERATION ______________________________________________________ 29
8.3 KGE/KGG REVERSE CYCLE 2 PIPE KOOL GAS DEFROST _________________________________ 30
8.4 SEQUENCE OF OPERATION ______________________________________________________ 30
9 UNITS WITH KE2 EVAP OEM CONTROLLER ____________________________________________ 32
9.1 SEQUENCE OF OPERATION ______________________________________________________ 32
9.2 DEFROST OPERATION __________________________________________________________ 33
9.2.1 PUMP DOWN SETTINGS ____________________________________________________ 33
9.2.2 DEFROST SETTINGS ________________________________________________________ 34
9.2.3 DRAIN SETTINGS __________________________________________________________ 34
9.2.4 FAN DELAY SETTINGS ______________________________________________________ 34

MK/MV – Medium Profile Series Unit Coolers (E206993_M)
2
9.2.5 AIR DEFROST _____________________________________________________________ 34
9.2.6 ELECTRIC DEFROST ________________________________________________________ 38
9.2.7 HOT GAS DEFROST ________________________________________________________ 40
9.3 CONNECTIVITY (ENABLING SMART ACCESS SETUP) ___________________________________ 42
9.3.1 KE2 STANDARD REMOTE DISPLAY INTERFACE ___________________________________ 42
9.3.2 DIAGNOSTICS MODE _______________________________________________________ 43
9.3.3 POINT TO POINT LAN INTERFACE _____________________________________________ 43
9.3.4 NETWORK INTERFACE ______________________________________________________ 46
9.4 SMART ACCESS FROM A WEB BROWSER ___________________________________________ 47
9.4.1 HOME PAGE _____________________________________________________________ 47
9.4.2 LOGIN PAGE _____________________________________________________________ 48
9.4.3 SETTINGS PAGE ___________________________________________________________ 48
9.4.4 NETWORK SETUP PAGE _____________________________________________________ 49
9.4.5 SETPOINTS PAGE __________________________________________________________ 49
9.4.6 GRAPHS _________________________________________________________________ 50
9.5 BONDING ___________________________________________________________________ 50
10 START UP _____________________________________________________________________ 54
10.1 PRE-STARTUP ______________________________________________________________ 54
10.2 OPERATION CHECKOUT ______________________________________________________ 54
11 PREVENTATIVE MAINTENANCE ___________________________________________________ 55
12
TROUBLESHOOTING CHART ______________________________________________________ 56
13 KE2 OEM EVAP TROUBLESHOOTING CHART _________________________________________ 56
14 REPLACEMENT PARTS LIST _______________________________________________________ 63

MK/MV – Medium Profile Series Unit Coolers (E206993_M)
3
TABL E !OF!CHARTS!
Table 1 UNIT DIMENSIONS ........................................................................................................................... 7
Table 2 SUCTION CONNECTION .................................................................................................................. 11
Table 3 MK MEDIUM TEMPERATURE – AIR DEFROST ................................................................................. 13
Table 4-1 MK MEDIUM TEMPERATURE – AIR DEFROST .............................................................................. 14
Table 5-1 MK ELECTRIC OR GAS DEFROST ................................................................................................... 15
Table 6 MK ELECTRIC OR GAS DEFROST ...................................................................................................... 16
Table 7 MV LOW TEMPERATURE/HIGH VELOCITY - ELECTRIC DEFROST ...................................................... 17
Table 8 MK SERIES - AIR DEFROST .............................................................................................................. 18
Table 9 MK SERIES - ELECTRIC DEFROST ..................................................................................................... 19
Table 10 MV SERIES LOW TEMPERATURE - HIGH VELOCITY ........................................................................ 20
Table 11 MK MOTOR AMPS – 1/4 HP MOTOR ............................................................................................ 21
Table 12 MV MOTOR AMPS – 1/3 HP MOTOR ............................................................................................ 21
Table 13 MK & MV EC AMPS – 1/3 HP MOTOR ........................................................................................... 21
Table 14 MK HEATER AMPS ........................................................................................................................ 22
Table 15 MV HEATER AMPS ....................................................................................................................... 22
Table 16 UNIT TROUBLESHOOTING CHART ................................................................................................. 55
Table 17 KE2 TROUBLESHOOTING ............................................................................................................. 56
Table 18 REPLACEMENT PARTS .................................................................................................................. 64

MK/MV – Medium Profile Series Unit Coolers (E206993_M)
4
TABL E &OF& FIGURES!
Figure 1 UNIT DIMENSIONS ......................................................................................................................... 7
Figure 2 MULTIPLE UNIT COOLERS CONTROLLED BY A SINGLE SOLENOID ..................................................... 9
Figure 3 MULTIPLE UNIT COOLERS CONTROLLED BY MULTIPLE SOLENOIDS .................................................. 9
Figure 4 (H) HGE - 3 PIPE HOT GAS COIL WITH ELECTRIC DRAIN PAN DEFROST PIPING ................................ 10
Figure 5 (G) HGG - 3 PIPE HOT GAS COIL WITH HOT GAS DRAIN PAN DEFROST PIPING ............................... 10
Figure 6 (K) KGE - 2 PIPE REVERSE CYCLE KOOL GAS COIL WITH ELECTR. DP DEFROST PIPING ..................... 11
Figure 7 (K) KGG - 2 PIPE REVERSE CYCLE KOOL GAS COIL WITH KOOL GAS DP DEFROST PIPING ................. 11
Figure 8 AIR DEFROST WIRING 1 PH ........................................................................................................... 23
Figure 9 AIR DEFROST WIRING 3 PH ........................................................................................................... 23
Figure 10 DEFROST TERMINATION THERMOSTAT LOCATION FOR CARBON DIOXIDE (R744) ....................... 24
Figure 11 ELECTRIC DEFROST WIRING 208-230/60/1 .................................................................................. 25
Figure 12 ELECTRIC DEFROST WIRING 208-230/60/3 ................................................................................. 26
Figure 13 ELECTRIC DEFROST WIRING 460/60/3 ......................................................................................... 26
Figure 14 MULTIPLE UNIT COOLERS, ELECTRIC DEFROST 460/60/3 ............................................................. 27
Figure 15 MULTIPLE UNIT COOLERS, ELECTRIC DEFROST 208-230/60/3 ...................................................... 28
Figure 16 (H) HGE - 3 PIPE HOT GAS COIL AND ELECTRIC DRAIN PAN DEFROST WIRING .............................. 29
Figure 17 (G) HGG - 3 PIPE HOT GAS COIL AND HOT GAS DRAIN PAN DEFROST WIRING ............................. 30
Figure 18 (P) KGE - 2 PIPE KOOL GAS COIL AND ELECTRIC DRAIN PAN DEFROST WIRING ............................. 31
Figure 19 (K) KGG - 2 PIPE KOOL GAS COIL WITH KOOL GAS DRAIN PAN DEFROST WIRING ......................... 31
Figure 20 LATENT ENERGY RECOVERY ........................................................................................................ 32
Figure 21 RECOGNITION OF NECESSITY TO DEFROST .................................................................................. 33
Figure 22 AIR DEFROST CONTROLLER WIRE DIAGRAM ............................................................................... 35
Figure 23 AIR DEFROST SLAVE POWER DIAGRAM ....................................................................................... 36
Figure 24 AIR DEFROST SLAVE CONTROL DIAGRAM .................................................................................... 37
Figure 25 KE2 DEFROST CYCLE CHART ......................................................................................................... 38
Figure 26 ELECTRIC DEFROST CONTROLLER WIRING DIAGRAM ................................................................... 39
Figure 27 HOT GAS DEFROST WITH ELECTRICAL DRAIN PAN HEATER CONTROLLER WIRE DIAGRAM ........... 40
Figure 28 HOT GAS DEFROST NO ELECTRICAL DRAIN PAN HEATER CONTROLLER WIRE DIAGRAM .............. 41
Figure 29 CONNECTORS ON KE2 EVAP OEM ............................................................................................... 42
Figure 30 CONTROL PANEL ......................................................................................................................... 43
Figure 31 NETWORK AND SHARING CENTER ............................................................................................... 44
Figure 32 NETWORK CONNECTIONS ........................................................................................................... 44
Figure 33 ETHERNET PROPERTIES ............................................................................................................... 45
Figure 34 INTERNET PROTOCOL VERSION 4 PROPERTIES ............................................................................ 45
Figure 35 WEB BROWSER ........................................................................................................................... 46
Figure 36 IP ADDRESS ON KE2 EVAP HARDWARE ........................................................................................ 46
Figure 37 KE2 EVAP HOME PAGE ................................................................................................................ 47
Figure 38 KE2 EVAP LOGIN PAGE ................................................................................................................ 48
Figure 39 KE2 EVAP SETTINGS PAGE ........................................................................................................... 48
Figure 40 KE2 EVAP NETWORK SETTINGS PAGE .......................................................................................... 49
Figure 41 KE2 EVAP SETPOINTS PAGE
......................................................................................................... 49
Figure 42 KE2 EVAP GRAPHS PAGE ............................................................................................................. 50
Figure 43 CONTROLLING SYSTEM WITH 4 TO 8 KE2 EVAP CONTROLLERS .................................................... 50
Figure 44 HOME PAGE ................................................................................................................................ 51

MK/MV – Medium Profile Series Unit Coolers (E206993_M)
5
Figure 45 NETWORK SETUP SCREEN ........................................................................................................... 51
Figure 46 SETPOINTS SCREEN ..................................................................................................................... 52
Figure 47 REPLACEMENT PARTS ................................................................................................................. 63

MK/MV – Medium Profile Series Unit Coolers (E206993_M)
6
1RECEIPT OF EQUIPMENT
1.1 INSPECTION+
All equipment should be carefully checked for damage or shortages as soon as it is received.
Each shipment should be carefully checked against the bill of lading. If any damage or shortage is
evident, a notation must be made on the delivery receipt before it is signed and a claim should
then be filed against the freight carrier.
1.2 LOSS+OF+GAS+HOLDING+CHARGE+
Each unit cooler is leak tested, evacuated to remove moisture, and then shipped with a gas holding
charge. Absence of this charge may indicate a leak has developed in transit. The system should not be
charged with refrigerant until it is verified that there is no leak, or the source of the leak is located.
2UNIT INFORMATION AND DIMENSIONS
2.1 MODELS+COVERED+
MK Series medium profile unit coolers.
MV Series medium profile unit coolers - low temperature.
The MK and MV series are designed for walk-in coolers with ceiling heights of 10 to 14 feet
that require high airflow. MK/MV unit coolers draw air through the coil and discharge it into
the room via the unit fans.
The MK series handles medium to low temperature requirements and has three defrost options –
air, electric, and hot gas. The MV series is designed for low temperatures requiring extra high air
discharge velocities. The MV unit coolers are only available with electric defrost.

MK/MV – Medium Profile Series Unit Coolers (E206993_M)
7
2.2 UNIT+DIMENSIONS+
Figure 1 UNIT DIMENSIONS
Table 1 UNIT DIMENSIONS
Unit Size
“A”
“B”
“C”
“D”
1 FAN
38.4
27.0
_
19.2
2 FAN
63.4
54.0
_
32.7
3 FAN
92.4
81.0
54.0
46.2
4 FAN
119.4
108.0
54.0
59.7
3UNIT LOCATION AND MOUNTING
3.1 UNIT+LOCATION+
Unit coolers must be located to provide good air circulation to all areas of the cooler. The unit cooler
should be positioned to blow away from the wall and directed down an aisle rather than into and
through shelves. For best performance it is desirable to arrange the air discharge toward the door of
the cooler to minimize the entrance of warm moist air when the door is open. Light fixtures, shelving
and product boxes must be located so that they do not block the air intake or air discharge from the unit
cooler.
IMPORTANT:
The coil face must be located a minimum of 24” from walls to assure unrestricted air intake.
3.2 MOUNTING+
The unit cooler should be suspended with 3/8” diameter hanger rods or flush mounted against the
ceiling using 3/8” minimum lag screws with flat washers. Rods should have double nuts on the top and
bottom. Adequate support must be provided to hold the weight of the unit.
The unit must be level in all directions to insure proper drainage of the condensate. Suspended units
must have sufficient clearance above for cleaning the top.

MK/MV – Medium Profile Series Unit Coolers (E206993_M)
8
4PIPING INSTALLATION
4.1 DRAIN+LINE+
The drain line should be as short and as steeply pitched as possible with a minimum of ¼” drop per
running foot. A drain line trap should be installed to prevent warm moist air from migrating through the
drain line. If the temperature surrounding the drain line and trap is below freezing (32°) it must be
wrapped with a drain line heater and insulation. Be sure to also wrap the drain pan coupling. The drain
line heater must be energized continuously. Be sure to follow the manufacturer’s recommendation
when installing the drain line heat tape.
A union at the drain connection in the drain pan is recommended for ease of installation and future
servicing. The union should be located as close to the drain pan as possible. Use two wrenches when
tightening to prevent the drain fitting from twisting and damaging the unit.
Long runs of drain line i.e. more than a few feet should be supported by hangers to avoid damage to the
drain pan.
4.2 REFRIGERATION+PIPING+
System design must conform to all local and national codes, laws, and regulations applying to the site of
installation. In addition, the safety code for mechanical refrigeration, ASME B31.5, should be followed
as a guide to safe installation and operation practice.
Refrigerant line sizes and piping techniques should be obtained from the ASHRAE guide or equivalent
reference. Under no circumstances should the refrigerant connection size of the unit be used as the
basis for sizing the lines.
The horizontal suction line should slope away from the unit cooler toward the compressor. Vertical
suction risers may require a trap at the bottom of the riser for proper oil return.
When connecting multiple unit coolers using a common suction line, the branch suction lines must enter
the top of the common suction line. The branch lines must be sized for the evaporator capacity and the
common suction line to be sized for the total system capacity.
For units with hot gas defrost refer to section 4.4 and figures 2 through 5 for piping arrangement.
Refer to section 4.5 for refrigerant distributor nozzle selection.
Refer to section 4.6 for expansion valve selection.
For Food Service installations – seal any joint between unit cooler and cooler wall with a sealant Listed
by the National Sanitation Foundation.
Special Instructions for Units Using Carbon Dioxide (R744)
These unit coolers are intended to utilize carbon dioxide only in a secondary loop or a cascade
system. As such, unit installation must comply with the following instructions:
A. If the refrigeration system is de-energized, venting of the R744 through the pressure regulating
relief valves on the refrigeration system can occur. In such cases, the system may need to be
recharged with R744, but in any case, the pressure regulating relief valve(s) are not to be
defeated or capped. The relief setting shall not be altered.

MK/MV – Medium Profile Series Unit Coolers (E206993_M)
9
B. A sufficient number of pressure relief and pressure regulating relief valves may need to be
provided based on the system capacity and located such that no stop valve is provided between
the relief valves and the parts or section of the system being protected.
To properly protect and control systems using pumped liquid overfeed R744, the solenoid, isolation, and
pressure relief valves shall be arranged as shown in either Figure 2 or 3, according to the solenoid valve
arrangement. To handle the requirements of liquid R744 high pressure solenoid valves are to be used.
Figure 2 MULTIPLE UNIT COOLERS CONTROLLED BY A SINGLE SOLENOID
Figure 3 MULTIPLE UNIT COOLERS CONTROLLED BY MULTIPLE SOLENOIDS

MK/MV – Medium Profile Series Unit Coolers (E206993_M)
10
4.3 EVACUATION+AND+LEAK+TEST+
When all refrigeration connections have been completed, the entire system must be tested for leaks and
then evacuated. Refer to the instructions provided with your compressor system for information on
performing the leak test and evacuation.
4.4 MK+HOT+GAS+DEFROST+PIPING+
Figure 4 (H) HGE - 3 PIPE HOT GAS COIL WITH ELECTRIC DRAIN PAN DEFROST PIPING
Figure 5 (G) HGG - 3 PIPE HOT GAS COIL WITH HOT GAS DRAIN PAN DEFROST PIPING

MK/MV – Medium Profile Series Unit Coolers (E206993_M)
11
Figure 6 (K) KGE - 2 PIPE REVERSE CYCLE KOOL GAS COIL WITH ELECTR. DP DEFROST PIPING
Figure 7 (K) KGG - 2 PIPE REVERSE CYCLE KOOL GAS COIL WITH KOOL GAS DP DEFROST PIPING
Table 2 SUCTION CONNECTION
2, 3 CIRCUITS
4, 5 CIRCUITS
6,7,8,10,13,15 CIRCUITS
20 CIRCUITS
7/8”
1-1/8”
1-5/8”
2-1/8”
To identify number of circuits per model refer to tables 3, 4 and 5.

MK/MV – Medium Profile Series Unit Coolers (E206993_M)
12
4.5 REFRIGERANT+DISTRIBUTOR+NOZZLES+
Unit coolers are piped using a refrigerant distributor with a changeable nozzle design to equally
distribute refrigerant to each circuit of the evaporator coil. Distributor nozzles are included and are
packed in individual plastic envelopes along with a retainer ring and instruction card. The instruction
card tells what refrigerant the nozzle is to be used with. There may be 1, 2, or 3 envelopes with nozzles
located near the distributor.
The nozzles provided with the unit have been selected for design conditions of 9°F to 11°F T.D. and 90°F
(85°F electric and hot gas defrost) liquid refrigerant at the expansion valve inlet. If the unit will be
operated at conditions that are substantially different from these conditions, it may be necessary to
select a different size nozzle. Contact the factory for advice.
The nozzle must be installed in the distributor or the auxiliary side connector before installing the
expansion valve. There are nozzle identification numbers stamped on one side of the nozzle. Be sure to
insert the nozzle into the distributor with these numbers visible in case identification is required later.
The nozzle is held in place by a retainer ring that is easily inserted or removed with a pair of needle nose
pliers. Nozzle selections are listed in tables 3, 4, and 5.

MK/MV – Medium Profile Series Unit Coolers (E206993_M)
13
Table 3 MK MEDIUM TEMPERATURE – AIR DEFROST
MODEL
CFM
STANDARD
CIRCUITS
NOZZLE
R404A
NOZZLE
R407A
NOZZLE
R448A
MK14A-68
3245
2
L-3/4
L-1/2
L-3/4
MK14A-94
3060
3
L-1
L-3/4
L-1
MK14A-121
2960
3
L-1-1/2
L-1
L-1-1/2
MK24A-188
6120
5
L-2
L-1-1/2
L-2
MK24A-242
5920
5
L-3
L-2
L-2-1/2
MK34A-363
8880
13
J-4
J-2-1/2
J-3
MK44A-484
11840
13
J-5
J-4
J-5
MK16A-86
2985
2
L-3/4
L-3/4
L-1
MK16A-118
2815
3
L-1
L-1
L-1-1/2
MK16A-145
2725
4
L-1-1/2
L-1-1/2
L-1-1/2
MK26A-172
5970
4
L-2
L-1-1/2
L-2
MK26A-236
5630
5
L-2-1/2
L-2
L-2-1/2
MK26A-290
5450
8
L-3
L-2-1/2
L-3
MK36A-354
8445
10
J-4
J-3
J-4
MK36A-435
8175
13
J-4
J-4
J-5
MK46A-580
10900
13
J-6
J-5
J-6
MK18A-98
2860
2
L-1
L-3/4
L-1
MK18A-133
2710
3
L-1-1/2
L-1
L-1-1/2
MK18A-160
2625
4
L-1-1/2
L-1-1/2
L-2
MK28A-196
5720
5
L-2
L-1-1/2
L-2
MK28A-266
5420
6
L-3
L-2
L-2-1/2
MK28A-320
5250
10
J-3
J-2-1/2
J-3
MK38A-393
8130
10
J-4
J-3
J-4
MK38A-480
7875
13
J-5
J-4
J-5
MK48A-640
10500
13
J-8
J-5
J-6
Note: Air defrost distributor nozzle selections are based on +25°F suction temperature, 10°F T.D. and
90°F liquid temperature.

MK/MV – Medium Profile Series Unit Coolers (E206993_M)
14
Table 4 -1 MK MEDIUM TEMPERATURE – AIR DEFROST
MODEL
CFM
STANDARD
CIRCUITS
NOZZLE
R404A
NOZZLE
R407A
NOZZLE
R448A
MK14A-68
3245
2
L-1
L-3/4
L-1
MK14A-94
3060
3
L-1-1/2
L-1
L-1-1/2
MK14A-121
2960
3
L-2
L-1-1/2
L-2
MK24A-188
6120
5
L-3
L-2-1/2
L-2-1/2
MK24A-242
5920
5
L-4
L-3
L-3
MK34A-363
8880
13
J-6
J-4
J-5
MK44A-484
11840
13
J-8
J-6
J-6
MK16A-86
2985
2
L-1-1/2
L-1
L-1-1/2
MK16A-118
2815
3
L-2
L-1-1/2
L-2
MK16A-145
2725
4
L-2-1/2
L-2
L-2-1/2
MK26A-172
5970
4
L-4
L-2-1/2
L-2-1/2
MK26A-236
5630
5
L-5
L-4
L-4
MK26A-290
5450
8
L-6
L-5
L-5
MK36A-354
8445
10
J-8
J-6
J-6
MK36A-435
8175
13
J-10
J-8
J-8
MK46A-580
10900
13
J-12
J-10
J-10
MK18A-98
2860
2
-
-
-
MK18A-133
2710
3
-
-
-
MK18A-160
2625
4
-
-
-
MK28A-196
5720
5
-
-
-
MK28A-266
5420
6
-
-
-
MK28A-320
5250
10
-
-
-
MK38A-393
8130
10
-
-
-
MK38A-480
7875
13
-
-
-
MK48A-640
10500
13
-
-
-
Note: Air defrost distributor nozzle selections are based on +25°F suction temperature, 15°F T.D. and
90°F liquid temperature. 15°F T.D. application not recommended for 8 fins per inch models.

MK/MV – Medium Profile Series Unit Coolers (E206993_M)
15
Table 5-1 MK ELECTRIC OR GAS DEFROST
MODEL
CFM
STANDARD
CIRCUITS
NOZZLE
R404A
NOZZLE
R407A
NOZZLE
R448A
MK14( )-60
3245
4
L-3/4
L-1/2
L- 3/4
MK14( )-82
3060
5
L-1
L-3/4
L-1
MK14( )-105
2960
5
L-1
L-1
L-1-1/2
MK24( )-120
6490
10
J- 1-1/2
L-1
L- 1-1/2
MK24( )-164
6120
10
J-2
J-1-1/2
J-2
MK24( )-210
5920
13
J-2-1/2
J-2
J-2-1/2
MK34( )-246
9180
15
G-3
G-2
G-3
MK34( )-315
8880
20
G-4
G-3
G-4
MK44( )-420
11840
20
G-5
G-4
G-5
MK16( )-76
2985
4
L- 3/4
L-3/4
L-1
MK16( )-103
2815
5
L-1
L-1
L-1-1/2
MK16( )-127
2725
5
L-1-1/2
L-1-1/2
L-1-1/2
MK26( )-152
5970
10
J-2
J- 1-1/2
J-2
MK26( )-206
5630
10
J-2-1/2
J-2
J-2-1/2
MK26( )-254
5450
13
J-3
J-2-1/2
J-3
MK36( )-309
8445
15
G-4
G-3
G-4
MK36( )-381
8175
20
G-5
G-4
G-5
MK46( )-508
10900
20
G-6
G-5
G-6
Note: Electric or hot gas defrost distributor nozzle selections are based on 20°F suction temperature,
10°F T.D. and 85°F liquid temperature. ( )-E, G, H, K, P.

MK/MV – Medium Profile Series Unit Coolers (E206993_M)
16
Table 6 MK ELECTRIC OR GAS DEFROST
MODEL
CFM
STANDARD
CIRCUITS
NOZZLE
R404A
NOZZLE
R407A
NOZZLE
R448A
MK14( )-60
3245
4
L-1
L-3/4
L-1
MK14( )-82
3060
5
L-1-1/2
L-1
L-1-1/2
MK14( )-105
2960
5
L-1.5
L-1-1/2
L-2
MK24( )-120
6490
10
J-2
L-1-1/2
L-2
MK24( )-164
6120
10
J-2.5
J-2
J-3
MK24( )-210
5920
13
J-3
J-3
J-4
MK34( )-246
9180
15
G-4
G-3
G-4
MK34( )-315
8880
20
G-5
G-4
G-5
MK44( )-420
11840
20
G-6
G-5
G-6
MK16( )-76
2985
4
L-1-1/2
L-1
L-1-1/2
MK16( )-103
2815
5
L-1-1/2
L-1-1/2
L-2
MK16( )-127
2725
5
L-2
L-1-1/2
L-2
MK26( )-152
5970
10
J-2-1/2
J-2
J-2-1/2
MK26( )-206
5630
10
J-3
J-3
J-4
MK26( )-254
5450
13
J-4
J-3
J-4
MK36( )-309
8445
15
G-5
G-4
G-5
MK36( )-381
8175
20
G-6
G-5
G-6
MK46( )-508
10900
20
G-8
G-6
G-8
Note: Electric or hot gas defrost distributor nozzle selections are based on -20°F suction
temperature, 10°F T.D. and 85°F liquid temperature. ( )-E, G, H, K, P.

MK/MV – Medium Profile Series Unit Coolers (E206993_M)
17
Table 7 MV LOW TEMPERATURE/HIGH VELOCITY - ELECTRIC DEFROST
MODEL
CFM
STANDARD
CIRCUITS
NOZZLE
R404A
NOZZLE
R407A
NOZZLE
R448A
MV14E-73
4790
5
L-1
L-1
L-1-1/2
MV14E-100
4300
6
L-1-1/2
L-1-1/2
L-2
MV14E-128
4130
8
L-2
L-2
L-2-1/2
MV24E-146
9580
10
J-2-1/2
J-2
J-2-1/2
MV24E-200
8600
10
J-3
J-2-1/2
J-3
MV24E-256
8260
13
J-4
J-3
J-4
MV34E-300
12900
15
G-5
G-4
G-5
MV34E-383
12390
20
G-8
G-5
G-6
MV44E-512
16520
20
G-12
G-6
G-8
MV16E-93
4405
5
L-1-1/2
L-1-1/2
L-2
MV16E-126
3955
6
L-2
L-1-1/2
L-2
MV16E-155
3800
8
L-2-1/2
L-2
L-2-1/2
MV26E-186
8810
10
J-3
J-2-1/2
J-3
MV26E-252
7910
10
J-5
J-3
J-4
MV26E-310
7600
13
J-6
J-4
J-5
MV36E-378
11865
15
G-8
G-5
G-6
MV36E-465
11400
20
G-10
G-6
G-8
MV46E-620
15200
20
G-12
G-10
G-12
*Consult factory.
Note: Low temperature distributor nozzle selections are based on -20°F suction temperature, 10°F T.D.
and 85°F liquid temperature.
4.6 EXPANSION+VALVE+
Before mounting the unit, install the expansion valve and connect the equalizer tube. The expansion
valve should be installed directly to the distributor body or as close as possible with no elbows or bends.
Locate the expansion valve bulb on a horizontal length of suction line as close to the suction header as
possible. Position the bulb in a 3, 4, 8, or 9 o’clock position (do not position on the bottom side of the
pipe). Clamp the bulb down flush and tightly against the pipe and insulate. Never locate the bulb in a
trap or downstream from a trap.
Expansion valves are adjusted at the factory prior to shipment. The setting will be correct for many
applications, but in other applications adjustments may be needed. It is important that the operation of
the expansion valve be checked after the system has balanced out at the desired room temperature. If
the coil is being starved, it is necessary to reduce the superheat setting of the valve by turning the
adjusting stem counterclockwise. If the superheat is too low, it is necessary to increase the superheat
setting of the valve by turning the adjusting stem clockwise. It is recommended that for a 10°F to 12°F
T.D. system, the valve should be adjusted to maintain 5°F to 6°F superheat.
This manual suits for next models
46
Table of contents
Popular Cooling Box manuals by other brands
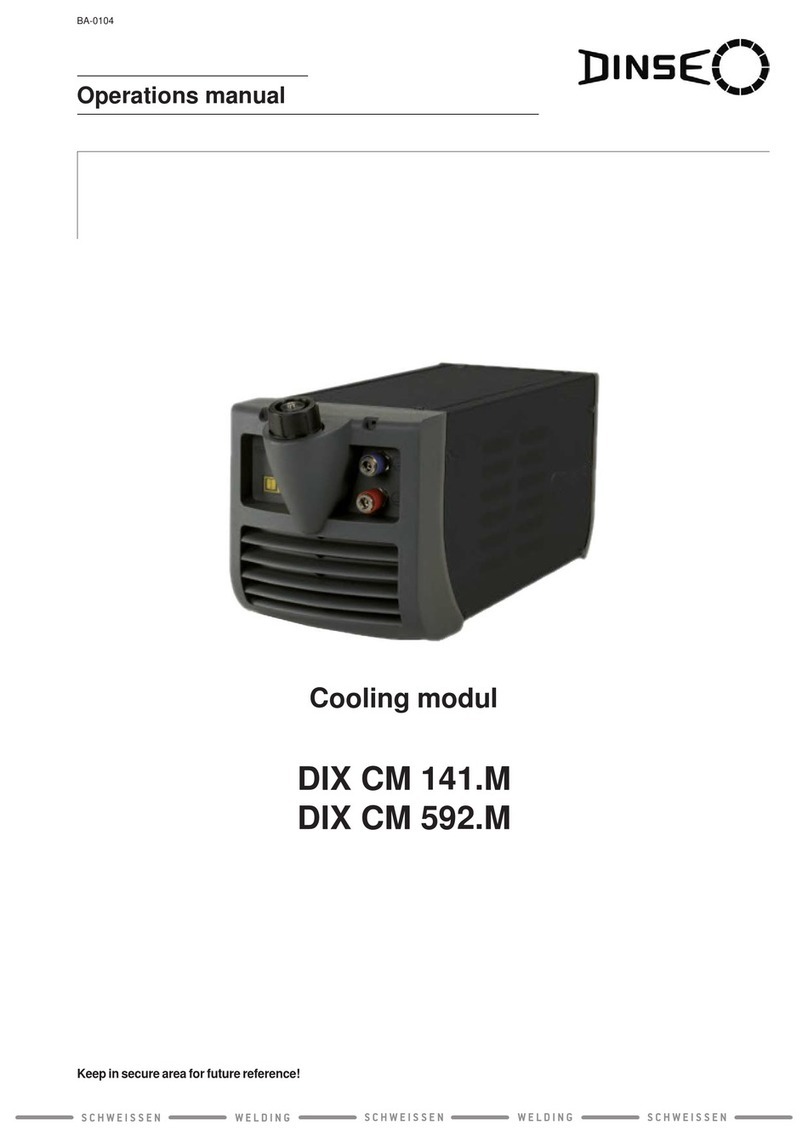
DINSE
DINSE DIX CM 141.M Operation manual
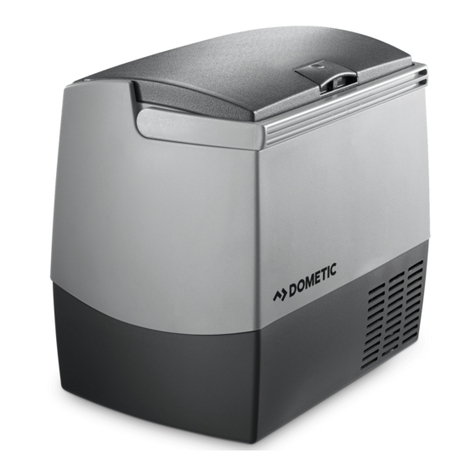
Dometic
Dometic CoolFreeze CDF-18 operating manual

Seifert
Seifert 43302101 user manual
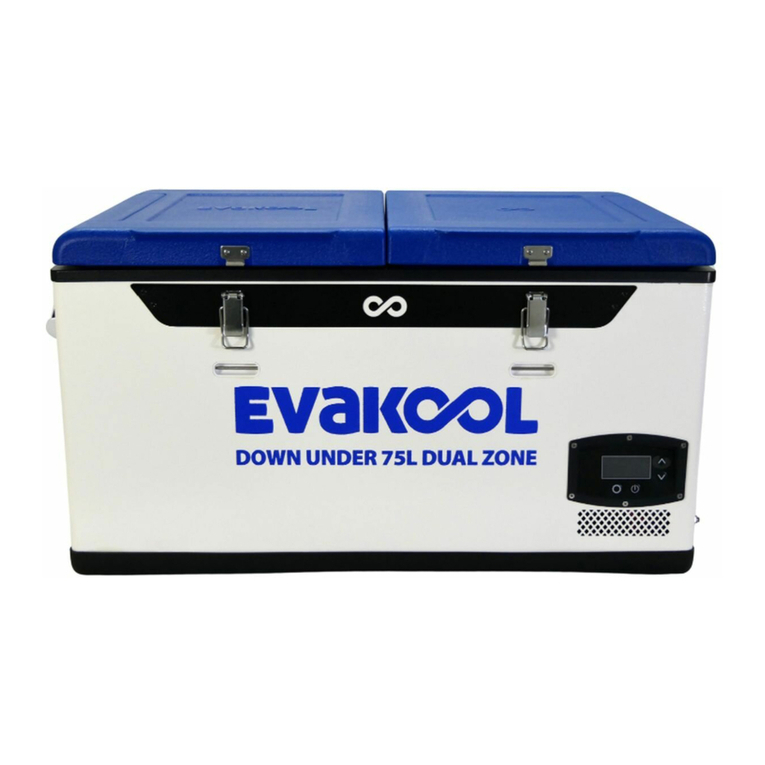
EvaKool
EvaKool DOWN UNDER Series instruction manual

Brandson Equipment
Brandson Equipment 305274 user manual
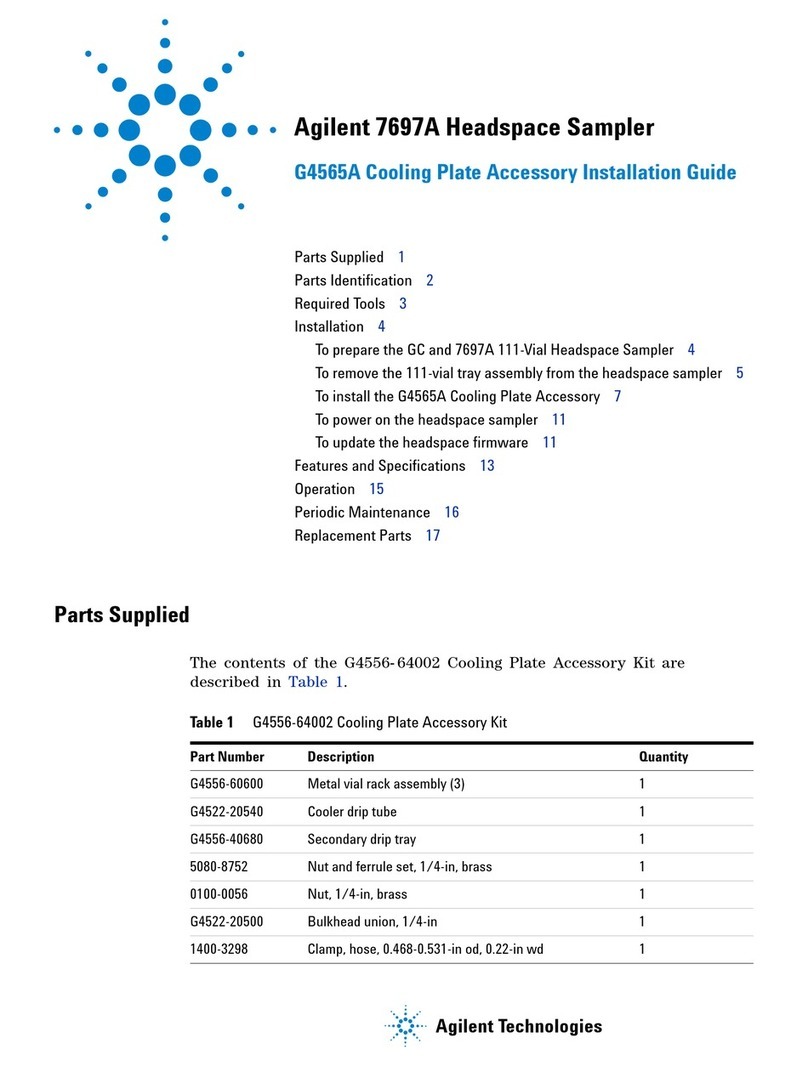
Agilent Technologies
Agilent Technologies G4565A Accessory installation guide
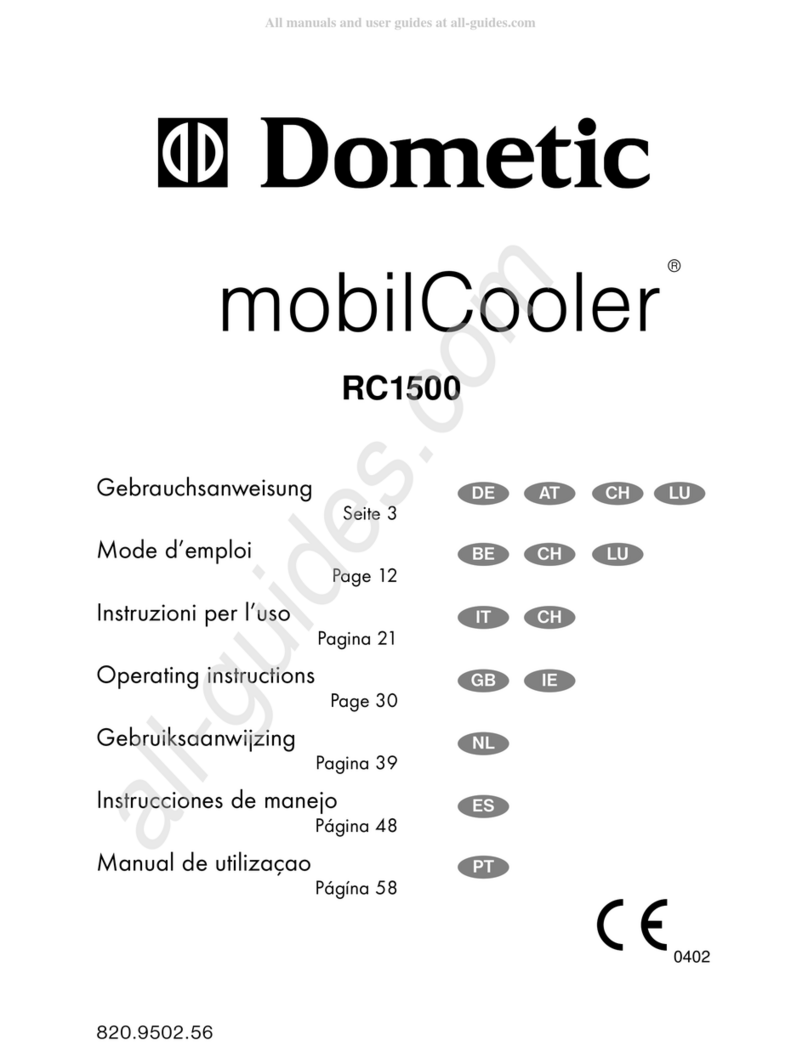
Dometic
Dometic mobilCooler RC1500 operating instructions
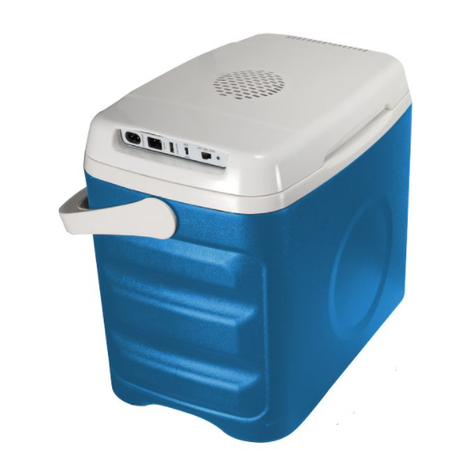
Guzzanti
Guzzanti GZ-26BW instruction manual
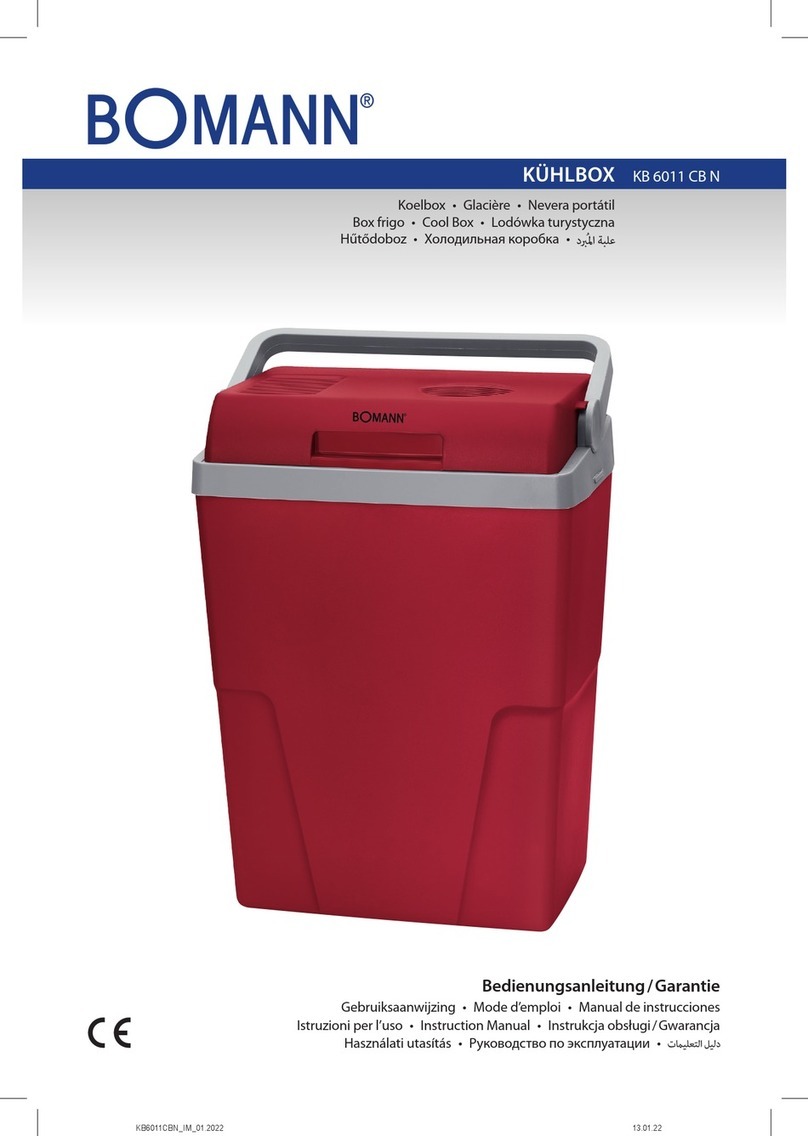
BOMANN
BOMANN KB 6011 CB N instruction manual
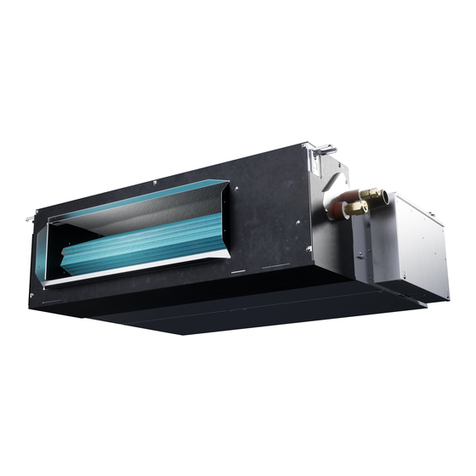
Hitachi
Hitachi RPIL-0.4FSRE Installation & operation manual
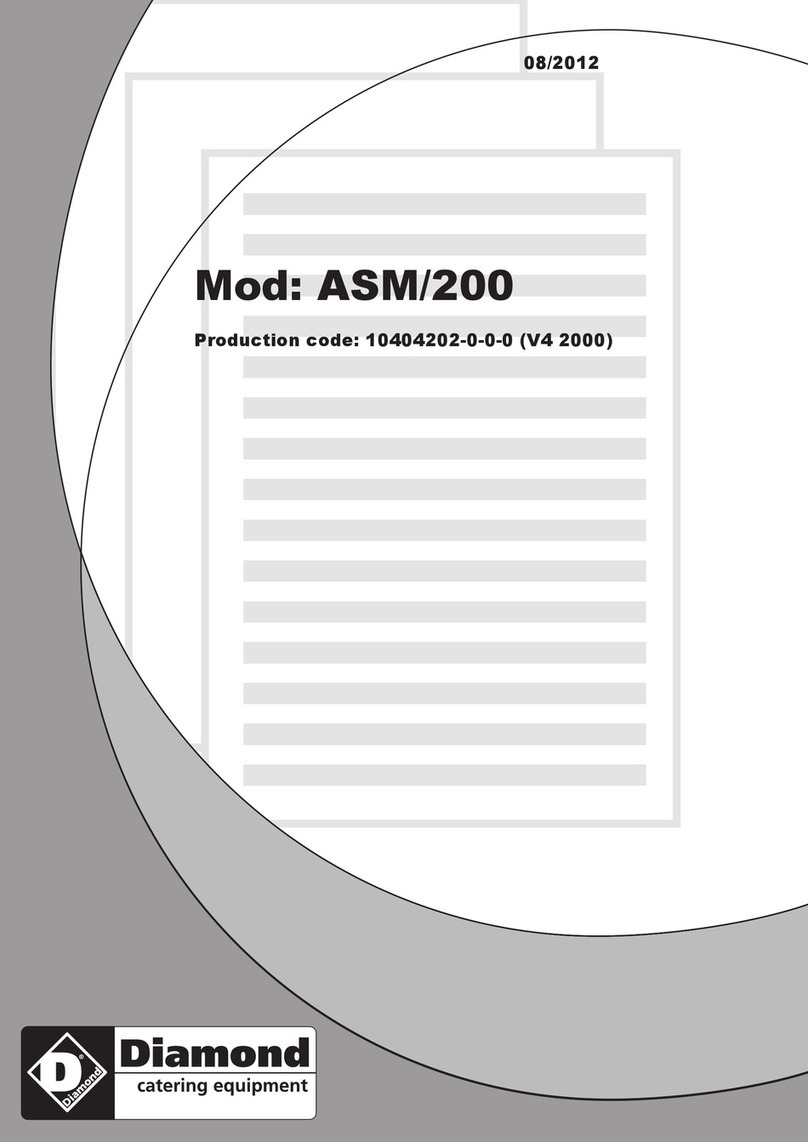
Diamond
Diamond ASM/200 Assembly instructions

FRIEDHELM LOH
FRIEDHELM LOH Rittal SK 3178800 Assembly and operating instructions